Vestil Manufacturing announces major expansion
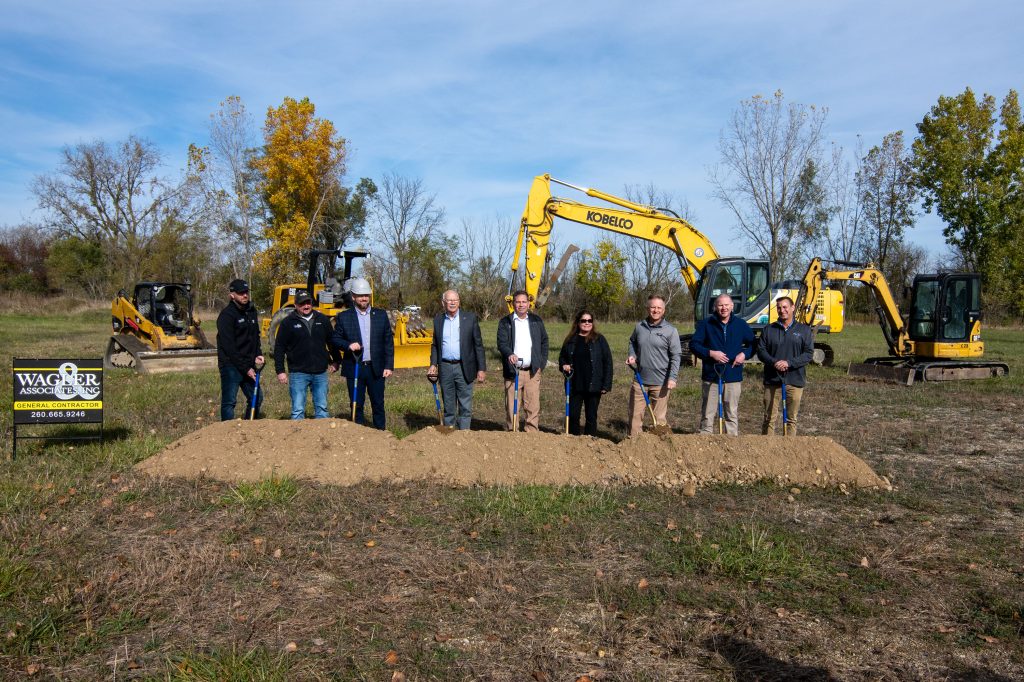
Vestil Manufacturing, a manufacturer of industrial and safety products market, just announced a major expansion project. The development will include a building expansion, cutting-edge capital equipment, and adding at least 20 jobs, further strengthening Vestil’s role as an industry leader. The expansion, set to add approximately 120,000 square feet of operational space at 351 Pokagon Trail, will enable Vestil to meet increasing demand, particularly for its plastic product lines. With the installation of advanced rotational molding equipment and a larger, highly skilled workforce, Vestil is positioned to serve customers better and to continue leading in the industrial product marketplace. Additionally, the project represents a significant investment in advanced technology and production resources, including a fiber tube laser, two robotic welders, additional lift trucks, and a sophisticated ERP software system. These investments aim to boost production capacity, streamline operations, and advance the company’s technological capabilities. “This expansion reflects our commitment to innovation, quality, and growth,” said Barry Trine, Vestil president. “By investing in our facilities, our technology, and our team, we’re not only positioning ourselves to meet future demand but are also creating opportunities for employment and contributing to the economic development in our community,” added Trine. The groundbreaking came two months after the passing of Ralph Trine, who had run Vestil since the company moved to Angola in the early 1980s. A moment of silence was held in Mr. Trine’s memory at the start of the ceremony. Vestil has partnered with Wagler & Associates, a locally owned & operated business, as the construction company leading this project. The expansion is scheduled for completion by September 2025. The project at Pokagon Trail includes a $1.5 million 120,000-square-foot addition and $3.2 million in new equipment, such as robotic welders and an enterprise resource planning system.
KION Group achieves strong results and increases profitability in the first nine months of FY 2024
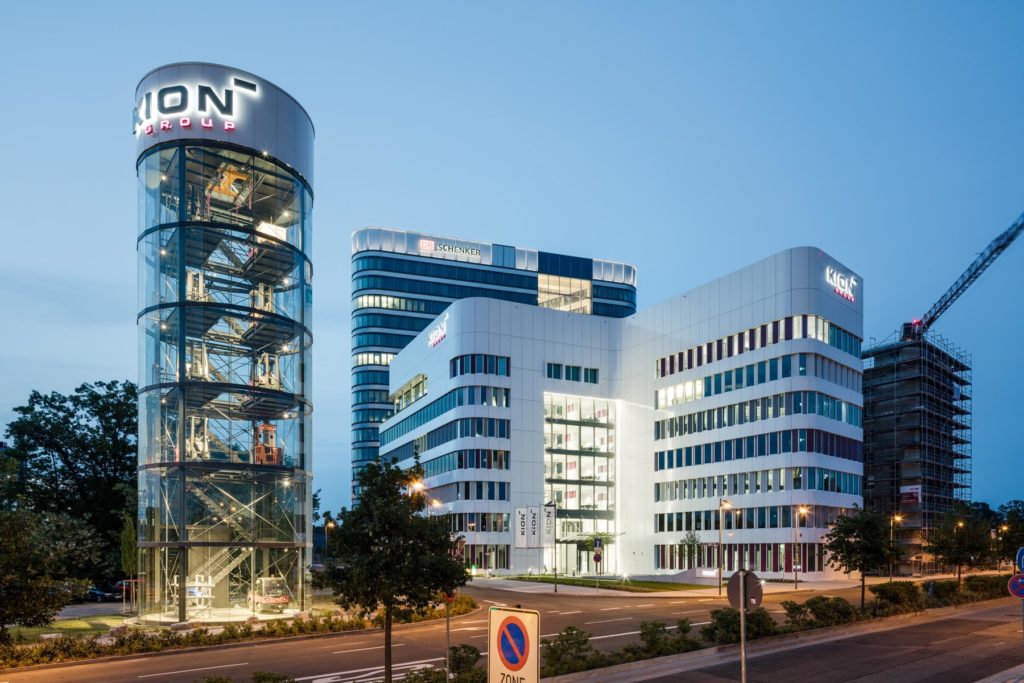
KION Group achieves strong results and increases profitability in the first nine months of FY 2024 Revenue up 1.1 percent to € 8.435 billion (2023: € 8.347 billion) Adj. EBIT improves 16.6 percent to € 666.7 million (2023: € 571.9 million) Adj. EBIT margin increases to 7.9 percent (2023: 6.9 percent) Free cash flow rises to € 431.3 million (2023: € 329.3 million) Outlook for 2024 confirmed with further narrowed bandwidths The KION Group significantly improved its profitability in the first nine months of the financial year. The company achieved an adjusted EBIT of € 666.7 million (2023: € 571.9 million) on the back of € 8.435 billion (2023: € 8.347 billion) in revenues. Consequently, the adjusted EBIT margin increased 1.0 percentage point year-on-year to 7.9 percent. “Macroeconomic and political uncertainties continue to affect the business climate in the major economies of Europe, Asia, and the Americas throughout 2024. Against the backdrop of this challenging environment, we are well on track to achieve our targets for the financial year,” said Rob Smith, Chief Executive Officer of KION GROUP AG. ”With the confidence of a strong performance in the first nine months, we are narrowing the target bandwidths further and confirm our outlook for the year.” Total revenue in the Industrial Trucks & Services segment increased by 2.4 percent to € 6.305 billion (2023: € 6.160 billion), mainly driven by higher unit sales and improved prices. The service business grew revenues by 2.2 percent and accounted for 48.0 percent of external segment revenue – which was in line with the previous year (48.1 percent). In the Supply Chain Solutions segment, revenues came in at € 2.161 billion (2023: € 2.216 billion). The project business revenue declined by 12.1 percent, and the higher-margin service business grew significantly by 15.8 percent. The service share of external segment revenue grew to 41.5 percent (2023: 34.9 percent). The adjusted EBIT of the Industrial Trucks & Services segment rose significantly to € 672.9 million (2023: € 613.6 million). Revenue growth and stable material costs led to a significantly increased gross margin and an adjusted EBIT margin of 10.7 percent (2023: 10.0 percent). Adjusted EBIT also improved significantly in the Supply Chain Solutions segment, doubling year-on-year to € 70.5 million (2023: € 30.7 million). Higher earnings contribution from the service business, efficiency measures in project implementation and the progress in completing lower-margin legacy orders were the key drivers of adjusted EBIT improvement. The adjusted EBIT margin improved to 3.3 percent (2023: 1.4 percent). At € 255.6 million, net income was higher year-on-year (€ 228.3 million). This corresponds to undiluted earnings per share of € 1.90 (2023: € 1.70). At € 431.3 million, free cash flow was significantly higher than in the previous year (€ 329.3 million). Outlook confirmed with further narrowed bandwidths In the quarterly statement for the period ended September 30, the Executive Board of KION GROUP AG confirms the outlook. It has further narrowed the ranges for the Group and the two operating segments: A new member of the Supervisory Board appointed Dr. Sun Shaojun has been appointed to the Supervisory Board for the period until the end of the Annual General Meeting in May 2025. He succeeds Tan Xuguang, who retired from the Supervisory Board on September 16, 2024. Dr. Sun is an experienced leader with deep expertise in mechanical engineering and in the intralogistics industry. Since 2007, he is a member of the Board of Directors of Weichai Holding Group Co., Ltd. in Weifang, People’s Republic of China. “I would like to express our sincere thanks to Tan Xuguang. He has contributed his considerable expertise, strategic vision, and industrial foresight to our Supervisory Board during his tenure,” said Hans Peter Ring, Chairman of the Supervisory Board of KION GROUP AG. “At the same time, we are glad that Sun Shaojun and I have found a successor who is familiar with the business and KION’s markets in EMEA thanks to his many years of professional experience in Germany.” Since 2013, Dr. Sun has been a member of the Management Board of Hydraulics Drive Technology Beteiligungs GmbH in Aschaffenburg, Germany. He started his career in 1998 at Weifang Diesel Engine Works in Weifang, People’s Republic of China. Dr. Sun holds a PhD in Engineering from Tianjin University in Tianjin, People’s Republic of China. Continuity in the Executive Board – Ching Pong Quek appointed until 2030 The Supervisory Board of KION GROUP AG has extended the appointment of the incumbent CTO & President, KION ITS Asia Pacific, Ching Pong Quek, by a further five years until June 30, 2030. Quek began his career at the KION Group in 2006 as CEO of Linde (China) Forklift Truck Corp. based in Xiamen. Since 2008, he has been responsible for the Asian business of the Industrial Trucks & Services segment, and from 2021 until the end of 2023, he has been acting as President of ITS Americas as well. In 2024, he took on the role of Chief Technology Officer of the KION Group in addition to the Asian business. Quek has been a member of the Executive Board of KION GROUP AG since 2013. “Ching Pong Quek is the longest-serving member of the KION Group Executive Board and has been shaping the company for 19 years with his in-depth expertise in the material handling industry,” said Hans Peter Ring, Chairman of the Supervisory Board of KION GROUP AG. “CP will continue to play a key role in driving forward both ITS’s Asian business and the further development of the CTO organization.” Key performance indicators for the KION Group and its two operating segments for the first nine months of 2024 and for the third quarter ending September 30, 2024 in € million Q3/2024 Q3/2023 Diff. Q1-Q3/2024 Q1-Q3/2023 Diff. Revenue Industrial Trucks & Services Supply Chain Solutions 2,699 1,999 710 2,730 2,025 719 -1.1% -1.3% -1.3% 8,435 6,305 2,161 8,347 6,160 2,216 1.1% 2.4% -2.5% Adjusted EBIT [1] Industrial Trucks & Services Supply Chain Solutions 219.6 202.3 28.4 223.6 234.7 15.8 -1.8% -13.8% 79.6% 666.7 672.9 70.5 571.9 613.6 30.7 16.6%
Episode 533: Humanoids in warehousing with Zion Solutions Group
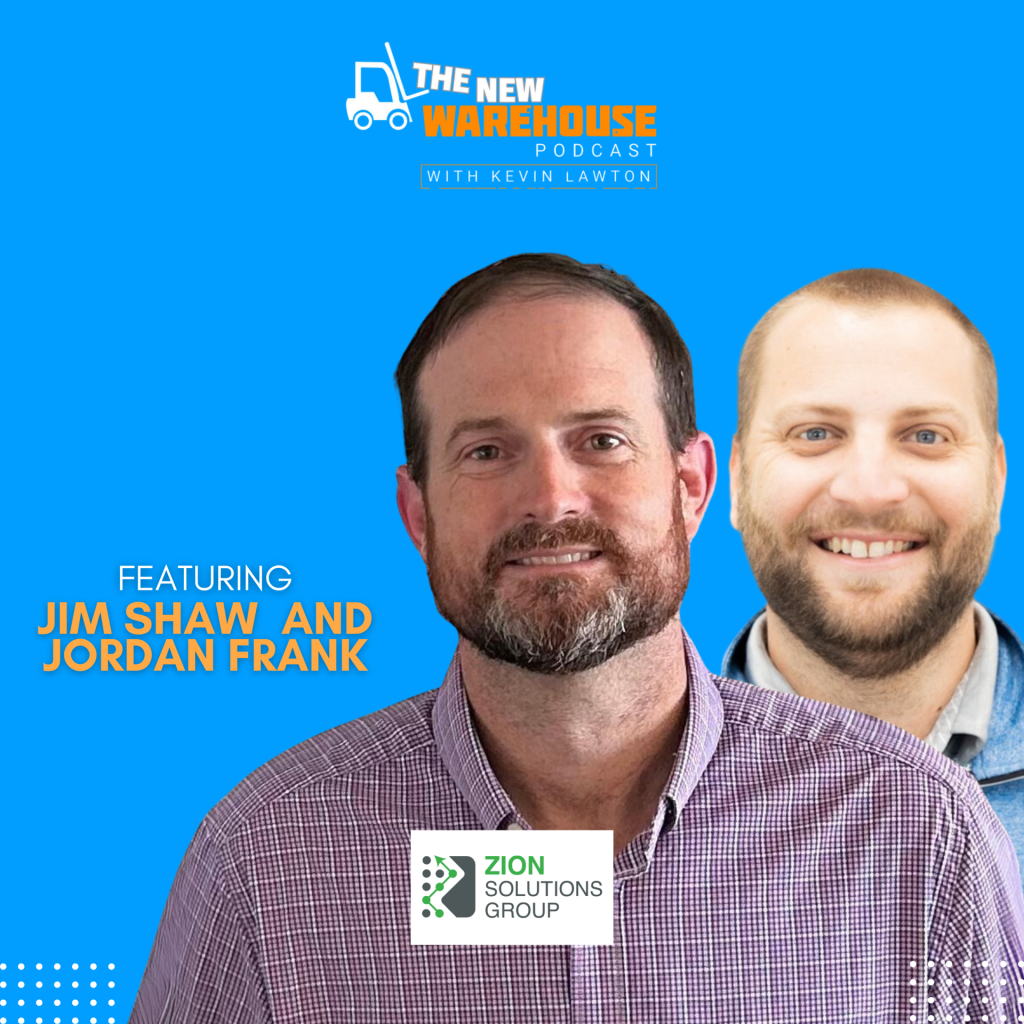
Welcome to this episode of The New Warehouse Podcast, where we dive into the impact of humanoids in warehousing with Zion Solutions Group’s President and Co-founder, Jim Shaw, and Executive Vice President and Co-founder, Jordan Frank. Zion Solutions, a leading systems integrator in warehouse automation, recently became the first to partner with Agility Robotics, marking a bold step toward incorporating humanoids into everyday operations. Today, Jim and Jordan discuss their approach to this collaboration, their focus on real-world solutions, and their long-term vision of how humanoid robots can help solve labor shortages and optimize warehouse tasks. Zion’s strategy offers a new look at how technology and human expertise can work together to redefine warehousing. A Collaborative Future of Humanoids in Warehousing Zion Solutions Group’s partnership with a leading humanoid robotics company highlights the potential for humanoids to play a supportive role in warehousing. “We’re the first systems integrator to work with a humanoid company actively deployed in warehouses,” Jim shared. Unlike conventional automation, these humanoids are designed to complement human workers, taking on repetitive, physically demanding tasks. Jordan explained, “They’re not here to replace people. Instead, they free up our team members to focus on more impactful work.” Testing Humanoids with a Step-by-Step Approach Zion Solutions and its robotics partner are testing humanoids with a measured, phased approach. Jordan describes it as a “crawl, walk, run” method, where each stage gathers insights and feedback from real-time applications. “It’s not about replacing a human’s speed just yet,” Jordan said, “but about deploying these robots responsibly to assist and support human efforts.” Early pilot programs have shown success in areas like tote handling, a repetitive but essential task in warehouse operations. Jim shared, “This technology allows us to reassign people to roles that require quick decision-making and adaptability—things robots can’t do as well.” With this approach, Zion ensures that humanoids will be used where they can add the most value. Zion’s Broader Vision for Technology in Warehousing At Zion Solutions Group, integrating humanoids is just one part of a larger strategy to redefine warehousing through innovative technologies. “Our goal is to leave a positive impact on the lives we touch,” Jim explained. The company’s extensive partner program ensures they stay at the forefront of new solutions, from robotics to software. “We strive to make our clients’ lives easier and more efficient,” Jordan added. For Zion, the goal is not just automation but intelligent, human-centered systems. This vision underscores Zion’s commitment to helping warehouses navigate the future with the right blend of people and technology. Key Takeaways on Humanoids in Warehousing Zion Solutions Group is the first systems integrator to partner with a humanoid robotics company focused on warehousing. Humanoids can handle repetitive tasks, allowing human workers to focus on higher-value roles. Zion and its partner employ a “crawl, walk, run” approach to humanoids in warehousing, ensuring that they are deployed safely and effectively. The New Warehouse Podcast Episode 533: Humanoids in Warehousing with Zion Solutions Group
AAR Reports Rail Traffic for the week ending October 26, 2024
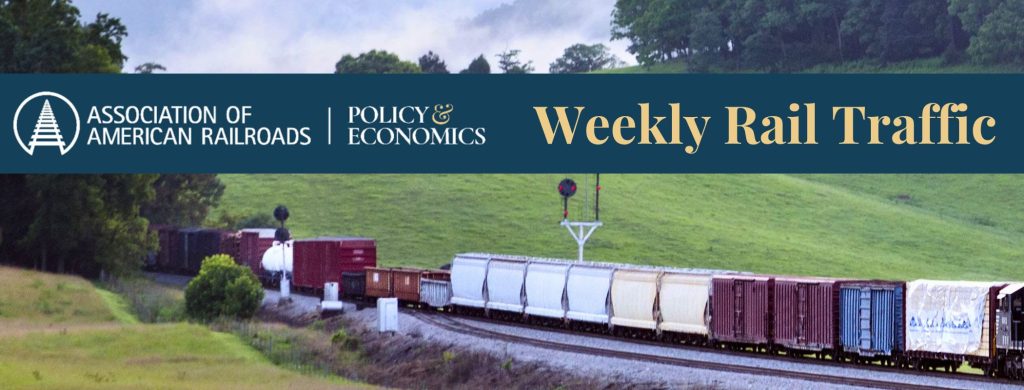
Today, the Association of American Railroads (AAR) reported U.S. rail traffic for the week ending October 26, 2024. This week’s total U.S. weekly rail traffic was 519,415 carloads and intermodal units, up 4.2 percent compared with the same week last year. Total carloads for the week ending October 26 were 228,829, up 0.9 percent from the same week in 2023, while U.S. weekly intermodal volume was 290,586 containers and trailers, up 6.9 percent from 2023. Seven of the ten carload commodity groups posted an increase compared with the same week in 2023. They included motor vehicles and parts, up 2,408 carloads, to 16,444; chemicals, up 1,506 carloads, to 32,838; and farm products excl. grain, and food, up 1,308 carloads, to 18,091. Commodity groups that posted decreases compared with the same week in 2023 were coal, down 3,132 carloads, to 59,981; metallic ores and metals, down 2,341 carloads, to 18,085; and nonmetallic minerals, down 332 carloads, to 32,084. For the first 43 weeks of 2024, U.S. railroads reported a cumulative volume of 9,371,430 carloads, down 3.2 percent from the same point last year, and 11,333,580 intermodal units, up 8.9 percent from last year. Total combined U.S. traffic for the first 43 weeks of 2024 was 20,705,010 carloads and intermodal units, an increase of 3.1 percent compared to last year. North American rail volume for the week ending October 26, 2024, on nine reporting U.S., Canadian, and Mexican railroads totaled 340,775 carloads, up 0.2 percent compared with the same week last year, and 376,589 intermodal units, up 6.0 percent compared to the previous year. Total combined weekly rail traffic in North America was 717,364 carloads and intermodal units, up 3.1 percent. North American rail volume for the first 43 weeks of 2024 was 28,794,945 carloads and intermodal units, up 2.3 percent compared with 2023. Canadian railroads reported 97,007 carloads for the week, up 0.7 percent, and 71,773 intermodal units, up 2.0 percent compared with the same week in 2023. For the first 43 weeks of 2024, Canadian railroads reported a cumulative rail traffic volume of 6,846,120 carloads, containers, and trailers, down 0.0 percent. Mexican railroads reported 14,939 carloads for the week, down 12.1 percent compared to last year, and 14,230 intermodal units, up 8.0 percent. Cumulative volume on Mexican railroads for the first 43 weeks of 2024 was 1,243,815 carloads and intermodal containers and trailers, up 2.6 percent from last year.
Bobcat Company donates $885,000 in equipment to support The Salvation Army’s Disaster Relief Efforts
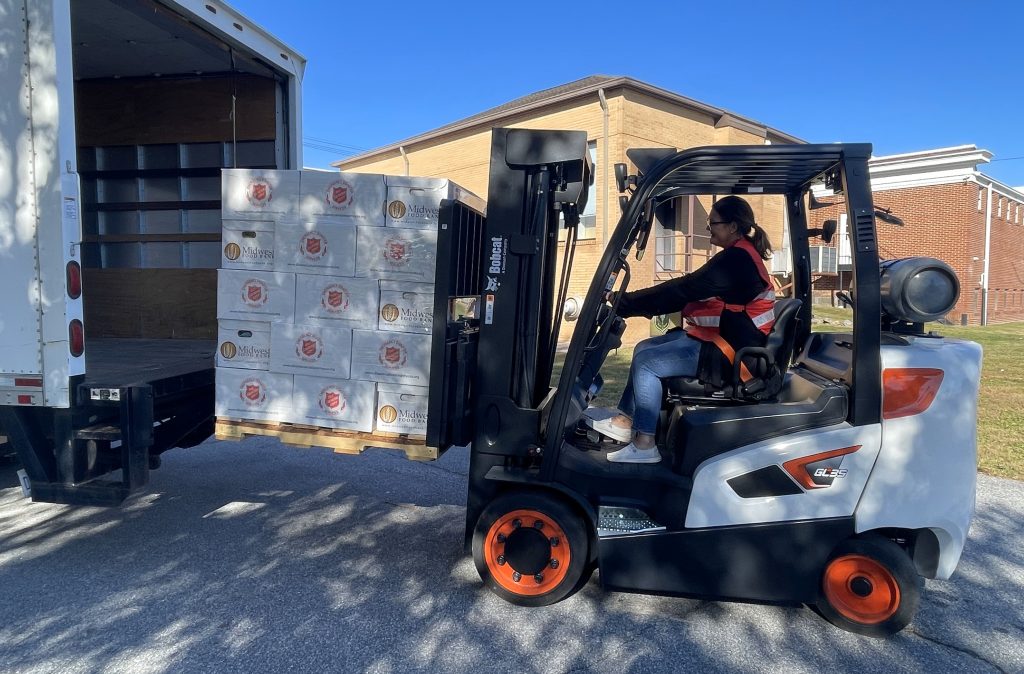
Donations of forklifts, portable generators, and light towers will enhance The Salvation Army’s disaster response efficiency and capacity The Salvation Army has received a significant equipment donation from Bobcat Company, a global equipment and worksite solutions brand, to support ongoing relief efforts in the aftermath of Hurricanes Helene and Milton and beyond. This donation, valued at $885,000, includes 23 essential pieces of equipment, such as forklifts, portable generators, and light towers, all vital for aiding communities impacted by natural disasters. These assets will be stored at The Salvation Army’s Emergency Disaster Services (EDS) warehouses and deployed across the Southeast, ensuring rapid and effective response to both the current and future disasters. The Salvation Army has often needed to rent much of this equipment in times of disaster, a costly and logistically challenging necessity, particularly during times of high demand following disasters. With Bobcat’s support, The Salvation Army can respond immediately without needing to source critical equipment during emergencies, enhancing its capacity to serve affected communities effectively. “This equipment will not only help with our immediate response efforts to Hurricanes Helene and Milton but will also save valuable time and money responding to future disasters,” said Commissioner Kenneth Hodder, National Commander of The Salvation Army. “Service delivery is severely impacted when critical equipment is unavailable during disaster operations, and this significant addition of operational equipment in our warehouses and the field is essential to ensuring the safety of our workers and in providing crucial services to survivors.” The Salvation Army’s EDS teams have provided emotional and spiritual care to more than 130,000 survivors throughout the Southeast since the hurricanes made landfall, as well as providing the following support: 580,000 meals and 370,000 snacks, 115,000 Ready-to-Eat meals, 88,000 food boxes, 280,000 drinks, 87,000 cases of water, and 86,000 clean-up kits. With Bobcat’s support, these critical services will continue as long as needed. Moreover, as The Salvation Army has a presence in many impacted areas, residents can rely on ongoing support as they rebuild their lives. “Bobcat equipment is often at the forefront of helping communities rebuild after natural disasters,” said Mike Ballweber, president of Doosan Bobcat North America. “Our collaboration with The Salvation Army allows Bobcat and our equipment to make an even greater impact, empowering The Salvation Army to maximize their efforts in doing the most good.” With this generous donation, The Salvation Army is better equipped to serve communities across the Southeast as they recover from the devastation of Hurricanes Helene and Milton and for rapid deployment in future disaster situations to help individuals and families in need. To learn more about how Bobcat is supporting communities, please visit bobcat.com. For more information on The Salvation Army’s hurricane relief efforts, please visit salvationarmyusa.org.
Motion enters into agreement to purchase hydraulics manufacturer
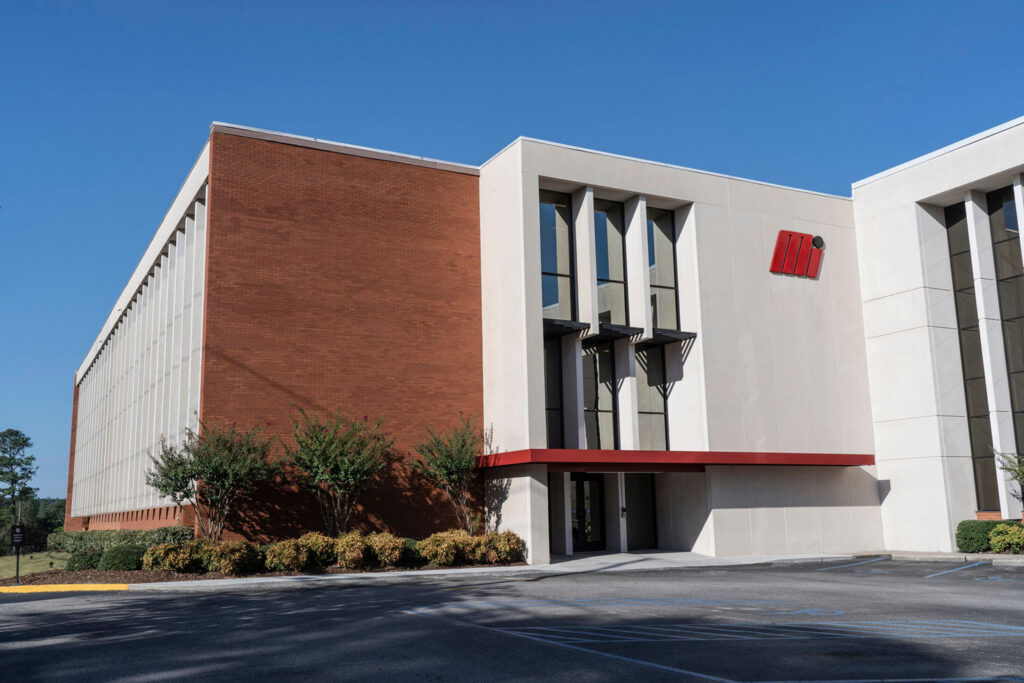
Motion Industries, Inc. signed a definitive purchase agreement to acquire the operating assets of Canadian-based Stoney Creek Hydraulics. The transaction is expected to close at the end of October, subject to customary closing conditions. Founded in 1998, Stoney Creek Hydraulics specializes in hydraulic and pneumatic cylinder manufacture/repair. Cylinders are built according to customer blueprints or designed by the engineering team to meet a customer application’s specific requirements. Repair services include cylinder inspection, machining and testing with precision. The company is named for its location in Stoney Creek, Ontario. “We are excited to begin a new chapter as part of the Motion team,” said Patrick Gauthier, Owner of Stoney Creek Hydraulics. “It is a great fit—both companies are customer-focused and share the same high values and service standards. The future is very bright for us and our customers as we combine resources and deepen our offerings.” James Howe, President of Motion, added, “As we continue to execute our acquisition strategy to grow our services, we are pleased to welcome Stoney Creek Hydraulics employees to Motion. Their skills and capabilities will bolster our hydraulic offering in Canada and complement our mechanical repair services in the region.”
NORD DRIVESYSTEMS complete packaging drive solutions at PACK EXPO
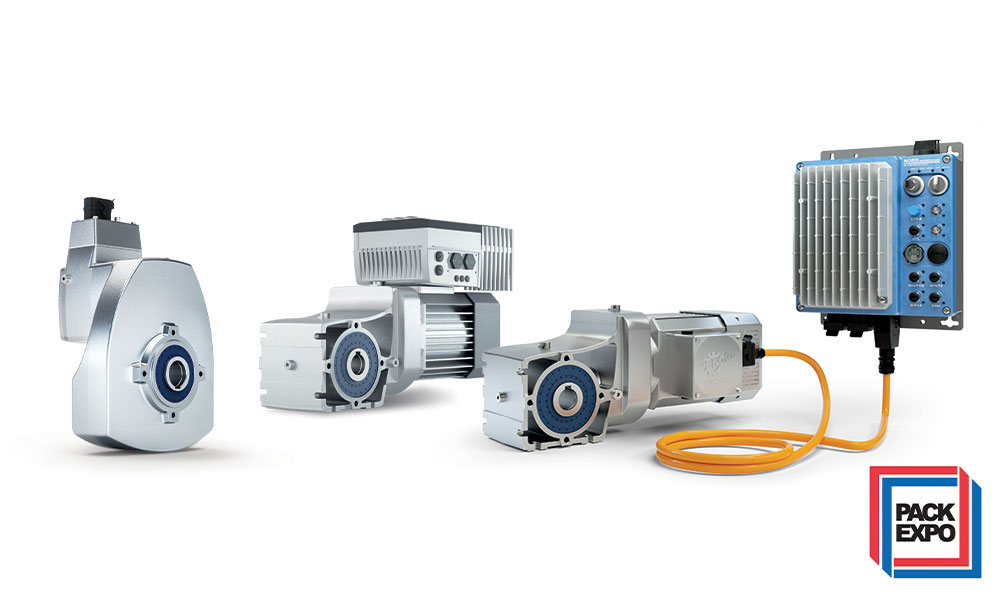
NORD offers intelligent, reliable, and cost-efficient solutions for the entire packaging process including primary packaging, secondary packaging, end-of-line packaging, and higher-level applications. PACK EXPO is one of the largest packaging and processing conventions in North America with over 45,000 expected attendees and 2,600 exhibitors registered to attend this year’s convention on November 3 – 6, 2024 in Chicago, IL. With the industry constantly changing, the show enables attendees to experience innovative solutions in action, learn from experts hosting educational sessions, and enjoy networking and idea-sharing in person. NORD DRIVESYSTEMS will be attending this year’s event showcasing their modular drive solutions engineered for high-volume packaging applications. Visit NORD at Booth N-5024 to view these innovative, intelligent packaging solutions first-hand. IE5+ Permanent Magnet Synchronous Motors IE5+ synchronous motors deliver consistently high operational efficiency, even at partial loads and low speeds. Their constant torque over a wide speed range enables variant reduction, significantly reduces operating costs, and produces a fast Return on Investment (ROI). A smooth surface version is available for high corrosion resistance and easy cleaning (TENV design) as well as a finned, ventilated version for optimized heat dissipation in heavy traffic systems (TEFC design). IE5+ motors are fully matched with NORD’s modular products to form a complete drive solution. NORDAC ON/ON+ Variable Frequency Drives NORDAC ON/ON+ variable frequency drives were developed to meet the special requirements of horizontal conveyor technology. Two versions of the VFD are available; NORDAC ON is compatible with IE3 motors while the NORDAC ON+ is optimized for use with high-efficiency IE5+ synchronous motors. These drives provide an economic solution for IIoT environments with an integrated industrial Ethernet interface, integrated PLC for drive-related functions, and firmware updates via Ethernet. Full Plug & Play capabilities make commissioning quick and simple whether for wall or motor mounting. Additionally, POSICON integrated positioning mode and high precision control ensure smooth, precise operation for packaging systems. LogiDrive Complete Drive Solution LogiDrive® is a complete drive solution from NORD that reduces planning and commissioning efforts through a standardized, service-friendly system configured precisely to application requirements. Basic versions are available with economic IE3 electric motors while advanced versions include IE5+ PMS motors for increased efficiency and reduced system variants. When combined with a decentralized variable frequency drive such as NORDAC FLEX, NORDAC LINK, or NORDAC ON/ON+, the drives reliably convey packaging material, drive tools, form and seal packages, and more. DuoDrive Integrated Gear Unit and Motor DuoDrive is an ultra-modern integrated gear unit/motor concept with a smooth body design. It combines a high-efficiency IE5+ permanent magnet synchronous motor with a single-stage helical gear unit in one compact housing. The drive features an extremely high system efficiency of up to 92% – resulting in a significantly reduced Total Cost of Ownership (TCO) compared to other drive systems. This solution is well suited for packaging systems thanks to its simple Plug & Play commissioning, high power density, and quiet operation. DuoDrive additionally offers flexible attachment options, a wide variety of motor connectivity options, and IP69K surface treatment for wash-down environments. Condition Monitoring for Predictive Maintenance The Industrial Internet of Things (IIoT) focuses on internet usage in industrial processes and utilizes intelligent, connected devices for attaining and accessing data. Condition monitoring solutions for predictive maintenance systems are directly integrated into NORD variable frequency drives to record drive and status data continuously or periodically. Important information can then be derived from the data analysis to proactively maintain systems, reduce downtime, and increase operational efficiency of the entire plant.
Women In Trucking Association names 2024 Top Companies for Women to Work in Transportation
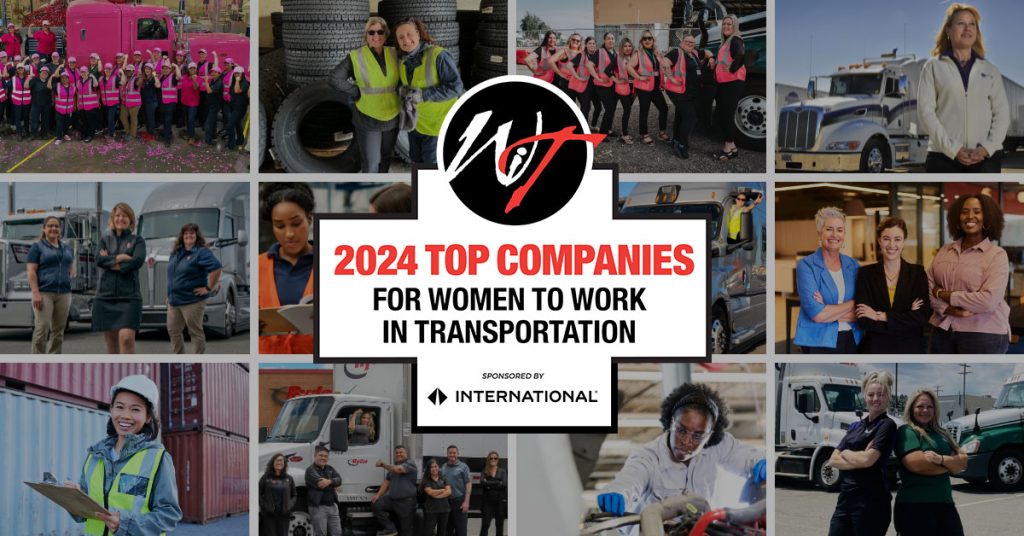
Redefining the Road magazine, the official magazine of the Women In Trucking Association (WIT), announced today the recipients of the 2024 “Top Companies for Women to Work in Transportation.” The magazine created the award in 2018 to support an element of WIT’s mission: to promote the accomplishments of companies that are focused on the employment of women in the trucking industry, according to Jennifer Hedrick, president and CEO of WIT. There are a number of characteristics that distinguish the companies recognized on this list, according to Brian Everett, publisher of Redefining the Road. These characteristics include corporate cultures that foster gender diversity; competitive compensation and benefits; flexible hours and work requirements; professional development opportunities; and career advancement opportunities. Qualified companies also must meet minimum requirements of what they report through the WIT Index, the industry barometer that benchmarks and measures the percentage of women who make up critical roles in transportation. The list includes a diverse range of trucking company types, including motor carriers, third-party logistics companies, and original equipment manufacturers. These companies will be recognized at the upcoming WIT Accelerate! Conference & Expo, which will be held Nov. 10-13 in Dallas, Texas. International Motors, formerly Navistar, is the sponsor of this year’s program. “Companies named to this prestigious list must demonstrate corporate attributes that are essential to any successful enterprise committed to gender diversity as part of their corporate strategy,” said Everett. “Qualifying companies to this list involves a two-step process. First, nominations by companies are carefully reviewed to ensure they meet a minimum threshold of qualifications. Then, the final ballot of companies is voted on by individuals in the industry. This is the seventh year of this prestigious recognition program, and it garnered a record number of more than 31,000 votes to identify and validate the final companies named to the list.” Companies generating the largest number of votes are named to the “Elite 30” of the 2024 Top Companies for Women to Work in Transportation. They are Air Products, ArcBest, Averitt, Cummins Inc., Daimler Truck North America, Epes Transport System, Estes Express Lines, FedEx, Great Dane, International Motors, J.B. Hunt Transport, Kenan Advantage Group, Landstar System, Old Dominion Freight Line, Penske Transportation Solutions, Peterbilt Motors Co., Premier Truck Group, Quality Carriers, Roehl Transport, RXO, Ryder System, Schneider, Sysco, The Goodyear Tire & Rubber Company, TravelCenters of America, UPS, Volvo Group North America, Walmart, WM, and XPO. Companies named to the overall 2024 Top Companies for Women to Work in Transportation list are 4Refuel, ADM Trucking, Aim Transportation Solutions, American Expediting Logistics, America’s Service Line, Ancora Training, Arrive Logistics, Arrow Truck Sales, Aurora Parts, Bay & Bay Transportation, Bennett Family of Companies, Bob’s Discount Furniture, Boyle Transportation, Brenny Transportation, Bridgestone Americas, Cargomatic, Carter Express, Centerline Drivers, Certified Express, CJ Logistics America, Clean Harbors, ContainerPort Group, Conversion Interactive Agency, Covenant Logistics Group, CrossCountry Freight Solutions, Crowley, Day & Ross, Dot Transportation, Dupré Logistics, Dynacraft (a PACCAR Company), Echo Global Logistics, Excargo Services, FStaff, Garner Trucking, Giltner Logistics, GLT Logistics, Great West Casualty Company, Halvor Lines, Highway Transport Logistics, Interstate Billing Service, ISAAC Instruments, J.J. Keller & Associates, JoyRide Logistics, JX Truck Center, Kenworth Truck Co., Koch Companies, Leonard’s Express, LGT Transport, Marathon Petroleum Co., May Trucking Co., McLeod Software, Michelin North America, MOTOR Information Systems, Musket Transport, National Carriers, National Shunt Service, New West Truck Centres, NFI Industries, OOIDA, Orica – USA, PACCAR Inc., PACCAR Leasing Co., PACCAR Parts, Palmer Trucks, Pennsy Supply, PepsiCo Foods North America, Polaris Transportation Group, Purolator, RE Garrison Trucking, Red Classic, Reliance Partners, Rihm Family Companies, Saia LTL Freight, Savage, Southeastern Freight Lines, Southwest International Trucks, Standard Logistics, Stericycle, Suburban Propane, Sun State International, Sunset Transportation, SWTO, TA Dedicated, The Erb Group, The Evans Network of Companies, The Pete Store, Thomas E. Keller Trucking, Total Transportation of MS, TRAC Intermodal, TRAFFIX, Trimac, Tri-National, Trinity Logistics, Triumph Financial, Truckstop, Tucker Freight Lines, Tyler Technologies, U.S. Xpress, Uber Freight, USAL, Venture Logistics, Werner Enterprises, Wilson Logistics, and Zonar Systems
Toyota Material Handling partners with Bastian Solutions on 100th AutoStore installation
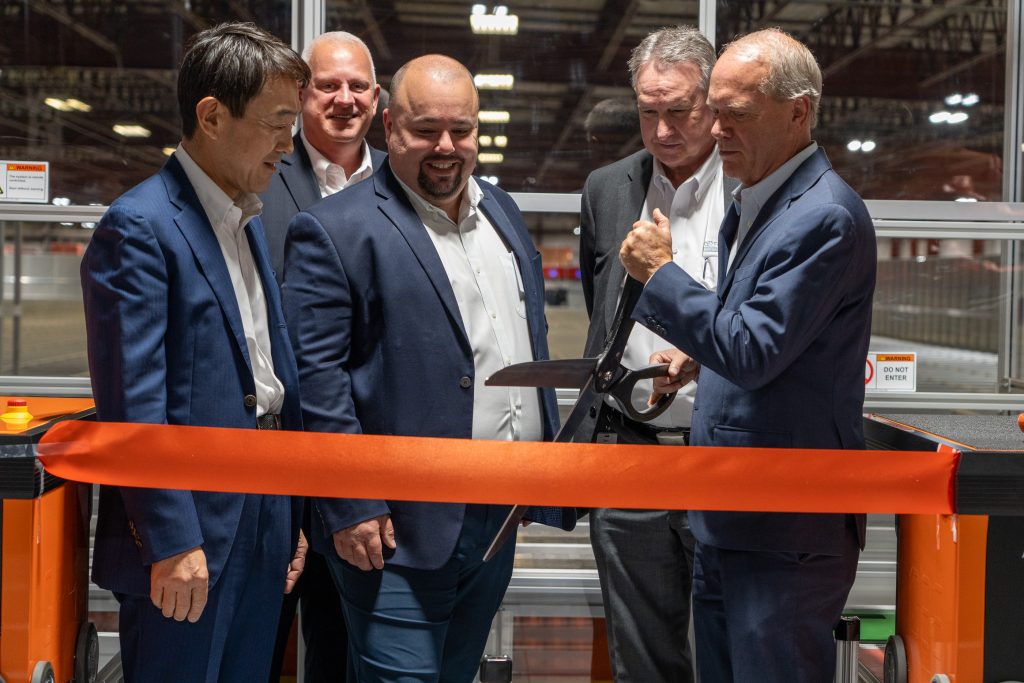
Toyota enhances its world-class parts distribution center with advanced AutoStore integration Toyota Material Handling unveiled a significant upgrade to its parts distribution center (PDC) at its Indiana headquarters on October 28 in collaboration with Bastian Solutions, part of Toyota Automated Logistics. This milestone marks Bastian’s 10oth AutoStore system installation, underscoring its automation expertise and enhancing Toyota’s capacity to process and deliver parts efficiently. “At Toyota, we will always be driven by what is best for our customers. This AutoStore integration will allow us to deliver parts to customers across North America faster than ever before, ensuring their forklift fleets are up and running when they need them most,” said Bret Bruin, Toyota Material Handling Vice President of Aftermarket Operations. “It’s amazing to see this project come together, in partnership with the teams at Bastian and AutoStore, to eliminate unnecessary waste and add efficiencies for the benefit of our customers.” The AutoStore integrates cutting-edge robotics, automation, and artificial intelligence into Toyota’s operations. In alignment with Toyota’s 2050 Vision for sustainability, the AutoStore system operates on rechargeable battery-powered robots, consuming energy only when in motion. The innovative system leverages vertical storage, maximizing unused space within the PDC. While the facility typically stocks an average of 55,000 stock-keeping units (SKUs), the new system dramatically increases storage capacity—from 40,000 to more than 128,000 storage locations—allowing Toyota to house more parts. This contributes to operational cost savings and indicates Toyota’s philosophy of Kaizen – or continuous improvement. “Today, we can reach over 80% of our customers with two-day shipping. Our goal is to reach 98% of our customers with next-day ground by 2030,” Bruin said. “This new AutoStore integration and enhanced Parts Distribution Center will play a significant role in helping us achieve that goal.” The AutoStore system minimizes manual labor by utilizing 28 autonomous robots that operate on a grid. These robots retrieve and deliver totes to four picking ports, each capable of processing up to 175 totes per hour. The system can fulfill up to 700 orders per hour, ensuring faster and more accurate order processing. AI-driven software strategically positions high-volume inventory for quicker access and provides real-time visibility to enhance operational efficiency further, ensuring Toyota Genuine Parts are readily available. The natural slotting system places low-volume parts at the bottom of the grid while keeping high-demand parts easily accessible to expedite order processing time. With the AutoStore system, Toyota ensures reliable order fulfillment, faster turnaround times, and improved customer satisfaction from its industry-leading North American dealer network. “Bastian is proud to support Toyota Material Handling in their efforts to deliver even greater customer service through an innovative, sustainable automation system,” said Aaron Jones, President and CEO of Bastian Solutions. “That focus on continuous improvement and quality solutions is at the heart of everything we do as Toyota group companies, and leveraging an incredible partner such as AutoStore is that final connection to ensure success now and into the future.” While robots and AI handle repetitive tasks, Toyota’s commitment to Jidoka—or automation with human touch—ensures associates spend their time on more strategic tasks. This allows Toyota to focus on problem-solving, innovation, and quality control, emphasizing the importance of human insight in driving operational excellence. During Toyota’s ribbon-cutting event at its Indiana headquarters, executives hosted guided tours to give stakeholders an exclusive firsthand look at the cutting-edge innovations and capabilities of the new AutoStore capabilities.
H&E Rentals reports third quarter 2024 results with revenue off by 4%
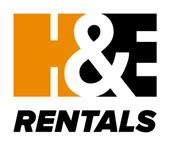
Today, H&E Equipment Services, Inc. reported financial results for the third quarter, which ended on September 30, 2024. The report includes the Company’s branch expansion achievements, with the addition of eight new locations in the third quarter, expanding the Company’s branch network to 157 locations across 32 states. THIRD QUARTER 2024 SUMMARY WITH A COMPARISON TO THIRD QUARTER 2023 Revenues declined 4.0% to $384.9 million compared to $400.7 million. Net income was $31.1 million compared to $48.9 million. The effective income tax rate was 28.3% compared to 26.1%. Adjusted EBITDA totaled $175.3 million, a decrease of 8.4% compared to $191.4 million. Adjusted EBITDA margins were 45.6% of revenues compared to 47.8%. Total equipment rental revenues were $326.2 million, an increase of $10.4 million, or 3.3%, compared to $315.8 million. Rental revenues were $288.1 million, an increase of $7.8 million, or 2.8%, compared to $280.3 million. Rental equipment sales decreased 47.3% to $27.8 million compared to $52.7 million. Gross margin declined to 44.5% compared to 47.0%. Total equipment rental gross margins were 45.3% compared to 47.4%, and rental gross margins were 51.2% compared to 53.3%. Average time utilization (based on original equipment cost) was 67.6% compared to 70.0%. Based on original equipment cost, the Company’s rental fleet closed the third quarter of 2024 at slightly below $3.0 billion, an increase of $220.1 million, or 8.1%. Average rental rates declined 0.1% compared to the third quarter of 2023 and fell 0.6% compared to the second quarter of 2024. Dollar utilization was 39.4% compared to 41.5% in the third quarter of 2023 and 38.6% in the second quarter of 2024. The average rental fleet age on September 30, 2024, was 40.8 months, compared to an industry average of 47.9 months. Paid regular quarterly cash dividend of $0.275 per share of common stock. “Industry fundamentals in the third quarter continued to trail year-ago measures,” said Brad Barber, chief executive officer of H&E Rentals. “Physical fleet utilization averaged 67.6%, or 240 basis points below the third quarter of 2023, evidence of the lower customer demand and a lingering modest oversupply of equipment. On a sequential quarterly basis, utilization improved 120 basis points. In addition, rental rates declined 0.1% compared to the prior-year quarter and were down 0.6% from the second quarter of 2024. Despite weakness in these key metrics, rental revenues grew 2.8% compared to the year-ago quarter due largely to the steady expansion of our branch count since the close of the third quarter of 2023. Finally, gross fleet expenditures in the quarter were $131.3 million, resulting in gross expenditures through the first nine months of 2024 of $327.8 million. We concluded the third quarter with a fleet original equipment cost of slightly below $3.0 billion.” Mr. Barber acknowledged the Company’s impressive expansion achievements, noting, “A record number of eight branches were added in the third quarter, while a ninth branch was opened in the month of October. The strong outcome reflected the outstanding execution of our accelerated new location program, which has achieved a record 16 additional locations in 2024, exceeding our stated expansion expectation. Through September 30, 2024, our U.S. geographic coverage improved to 157 locations across 32 states. When accounting for both new locations and branches added through acquisition, our branch count is up more than 14% in 2024 and approximately 54% since the close of 2021. Both measures are dominant accomplishments in our industry.” With the final quarter of 2024 underway, Mr. Barber provided updated expectations for the rental equipment industry, stating, “Construction spending in the U.S. continues to demonstrate the slowing rate of growth observed over the first half of 2024. We believe a trend of moderating activity will persist through the remainder of the year, with physical fleet utilization and rental rates below year-ago measures. Beyond the fourth quarter, the developing outlook for our industry is more encouraging into 2025. The Dodge Momentum Index (DMI), a leading indicator of construction spending, has exhibited gains for five of the last six months, while construction employment remains on a steady upward trajectory. Also, a cycle of easing interest rates is expected to have positive implications for local construction activity as projects are reevaluated under more favorable lending conditions. Finally, the strong expansion of mega-projects remains a significant growth driver for our industry, both today and in the future. Our branch expansion has led to greater and more diverse exposure to mega projects, including a growing presence on data centers, solar and wind farms, and LNG export facilities.” FINANCIAL DISCUSSION FOR THIRD QUARTER 2024 Revenue Total revenues were $384.9 million in the third quarter, a decline of 4.0% compared to $400.7 million in the third quarter of 2023. Total equipment rental revenues of $326.2 million improved 3.3% compared to $315.8 million in the third quarter of 2023. Rental revenues of $288.1 million increased 2.8% compared to $280.3 million in the third quarter of 2023. Rental equipment sales totaled $27.8 million, a decrease of 47.3% compared to $52.7 million in the third quarter of 2023. New equipment sales of $14.1 million increased 11.2% compared to $12.6 million in the same quarter of 2023. Gross Profit Gross profit totaled $171.5 million in the third quarter of 2024, a decrease of 9.0% compared to $188.4 million in the third quarter of 2023. Gross margin declined to 44.5% for the third quarter of 2024 compared to 47.0% for the same quarter in 2023. On a segment basis, the gross margin on total equipment rentals was 45.3% in the third quarter of 2024 compared to 47.4% in the third quarter of 2023. Rental margins were 51.2% compared to 53.3% over the same comparison period. Rental rates in the third quarter of 2024 declined 0.1% compared to the third quarter of 2023. Time utilization (based on original equipment cost) was 67.6% in the third quarter of 2024 compared to 70.0% in the third quarter of 2023. Gross margins on rental equipment sales improved to 60.2% in the third quarter of 2024 compared to 58.5% in the third quarter of 2023. Gross margins on new equipment sales were 19.8% in the third quarter of 2024 compared to
AutoScheduler adds Vice President of Customer Success to reinforce focus on successful customer implementations
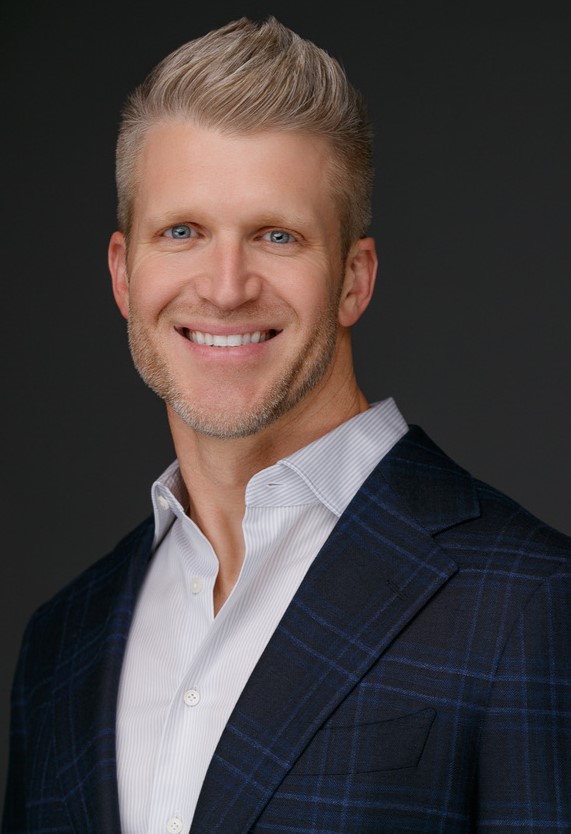
AutoScheduler.AI, an innovative Warehouse Orchestration Platform and WMS accelerator, announces that. He will replace Stephen Zujkowski, who is retiring. Ian has over a decade of experience in supply chain operations, logistics management, and strategic leadership. He will use his expertise to help AutoScheduler’s customers gain value and success from deploying AutoScheduler solutions. He will be the face of success for all AutoScheduler’s customers, ensuring the talented implementation team continues delivering exceptional services and fostering true partnerships. “As a leader within Amazon, Ian has demonstrated a deep understanding of operational planning and championed many technology implementations that enabled transformative changes within numerous operations,” says Keith Moore, CEO of AutoScheduler.AI. “His rich and diverse experience in leading and supporting innovation and a keen understanding of driving customer excellence make him a perfect fit for this pivotal role at AutoScheduler.AI.” “I am looking forward to setting new benchmarks for excellence in customer success with the best project delivery experiences, clear communications, and robust customer relationships, enabling AutoScheduler.AI to be the market leader in warehouse orchestration,” says Ian Johnston, Vice President, Customer Success, AutoScheduler.AI. “I am dedicated to driving value for clients through our innovative solutions and aligning AutoScheduler’s capabilities with customer needs.” As Vice President of Customer Success, Ian oversees the strategy, execution, and management of all customer deployment and satisfaction aspects. He will ensure that customers derive maximum value from AutoScheduler, leading to improved fulfillment, better labor utilization, and lower costs. As the leader in the Customer Success organization, he will drive measurable positive business outcomes, customer satisfaction, retention, and expansion across the customer base. Before joining AutoScheduler.AI, Ian served as Director of Supply Chain at Amazon, overseeing North America’s largest heavy, bulky logistics network, which included managing demand forecasting, capacity management, and product development for the U.S. and Canada. Ian’s leadership contributed to significant advancements in operational efficiency, including developing several novel planning products that enhanced forecast accuracy and capacity flexibility, reducing Amazon’s service cost and improving delivery speeds. Before Amazon, Ian served as a Marine Infantry Officer, leading combat operations in Afghanistan and deterrence operations in Southeast Asia. He later served at the White House, supporting two administrations and several high-profile events. Ian holds an MBA from the University of Virginia’s Darden School of Business and a BA in Political Science with a minor in Spanish from The Citadel. He is pursuing a Master of Science in Real Estate at the University of San Diego.
Inaugural jobs report shows how industry careers deliver for America’s Railroaders
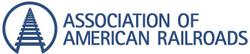
Today, the Association of American Railroads (AAR) released the “Rail Jobs Report: The Value and Opportunities in Railroading,” which provides a comprehensive review of the benefits and opportunities associated with freight rail careers. Featuring various employee testimonials, the report spotlights railroaders throughout the industry with stories of advancement, family legacy, and career impact. “Railroaders are the lifeblood that powers our industry and supports every facet of the economy,” said AAR President and CEO Ian Jefferies. “Rail work is not only a source of pride; it is a pathway to stability, growth, and opportunity that often spans generations. Combining data and employee testimonials, this report demonstrates the value of a railroading job – and the reasons why so many railroaders turn these jobs into careers.” The jobs report features statistics that distinguish freight rail jobs from those across other industries, highlighting railroading’s strong wages, world-class benefits, and hundreds of career paths and advancement opportunities: The median tenure of railroad employees is 13 years (compared to 3.9 years for other private sector workers). The average Class I railroad employee’s annual pay and benefits package is valued from $135,000 to almost $190,000. Effective Jan. 1, 2025, unionized freight rail employees’ monthly health care premiums will decrease by more than 10%, from $309.21 to $277.54 (compared to the national average monthly premium of more than $500 for employer-provided family coverage). Career railroaders (those 60+ who have served at least 30 years) receive more than two times as much retirement income as the average Social Security recipient. Veterans account for about 1 in 6 rail employees. Railroading isn’t just a job; it’s one of the best careers in industrial America. Learn more about the industry’s commitment to competitive compensation, robust benefits, and a strong focus on safety and professional development in the “Rail Jobs Report: The Value and Opportunities in Railroading.”
Alabama Park wins $100,000 Park Makeover from Bobcat Company
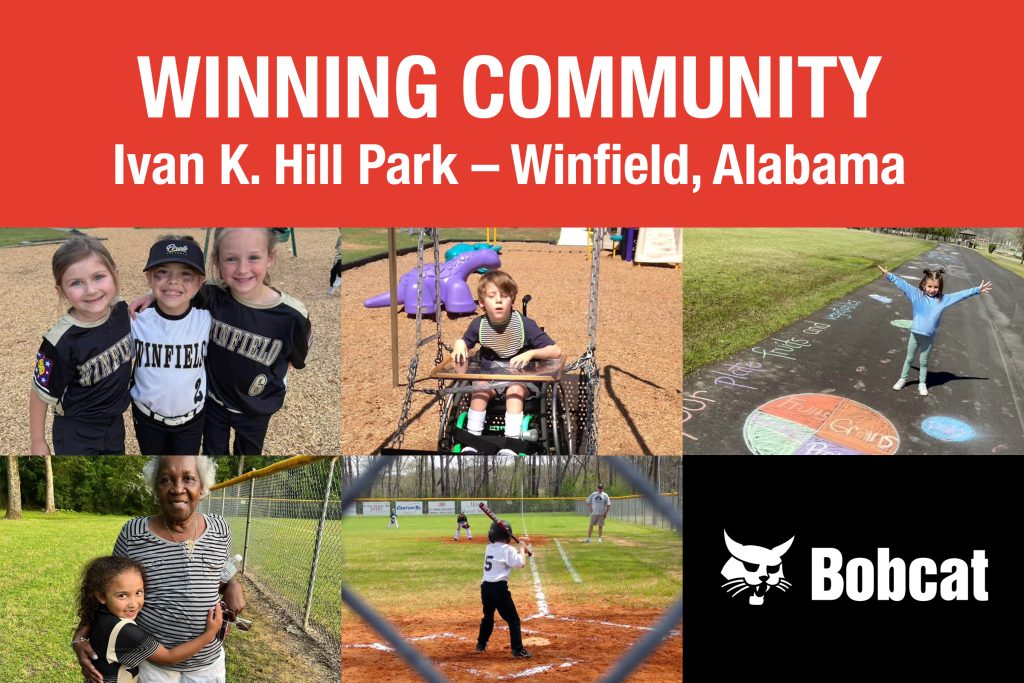
Ivan K. Hill Park in Winfield, Alabama, won the $100,000 Bobcat Park and Rec Makeover Contest hosted by Bobcat Company. The prize package will fund improvements at the park, which will focus on revitalizing a youth recreation space. Ivan K. Hill Park is a multi-use area featuring ballfields, playgrounds, and a senior center. It was nominated because of updates needed to improve user safety and accessibility. The $100,000 prize will go toward replacing the original 1960s fencing and ballfield backstop and enhancing access to the fields and restrooms. “This gift from Bobcat will allow our community to accomplish more by supplementing our funds to renovate a facility that will increase our ability to accommodate persons with disabilities in a safe environment. So many hearts will be touched immediately by offering hope and a promise of better playing facilities and just knowing that they are truly included,” said Gina Bryant, Winfield Park and Recreation director. “This award will help us continue to move forward with our goals and mission. It is proof that dreams can come true!” Bobcat kicked off the contest in July by teaming up with brand ambassador and renovation expert Chip Gaines for a baseball field makeover in Waco, Texas. Together, they aimed to inspire communities to see the potential in their own hometowns. Bobcat also partnered with the National Recreation and Park Association (NRPA) to promote the contest and review the submissions, focusing on the parks’ demonstrated need, sustainability impact, and long-term community benefit. Ivan K. Hill Park was selected as the winner based on NRPA’s criteria, which was coupled with strong public support for the park during the finalist voting period. “Bobcat equipment is best known for building on worksites around the world, but projects like this allow us to build something even greater together. We’re forging a community and helping build a legacy for the city of Winfield that will be treasured for generations to come,” said Laura Ness Owens, Bobcat vice president of global brand and marketing. Park enhancements at Ivan K. Hill Park are expected to be completed by April 2025. To stay updated on the park’s progress, please visit winfieldparkandrec.org or follow updates on the Winfield Park and Recreation Facebook page. In addition to the grand prize, Bobcat will also award the runner-up community with a new zero-turn mower to enhance their park and recreation space. Aaron Perry Park in Pontiac, Michigan, will be presented with a new mower in the next few weeks. Other finalists included Chestnut Street Park in Henderson, North Carolina; City of Purcell in Purcell, Oklahoma; and Jones Park in Galveston, Texas.
Handling Specialty Manufacturing Ltd. announces new president
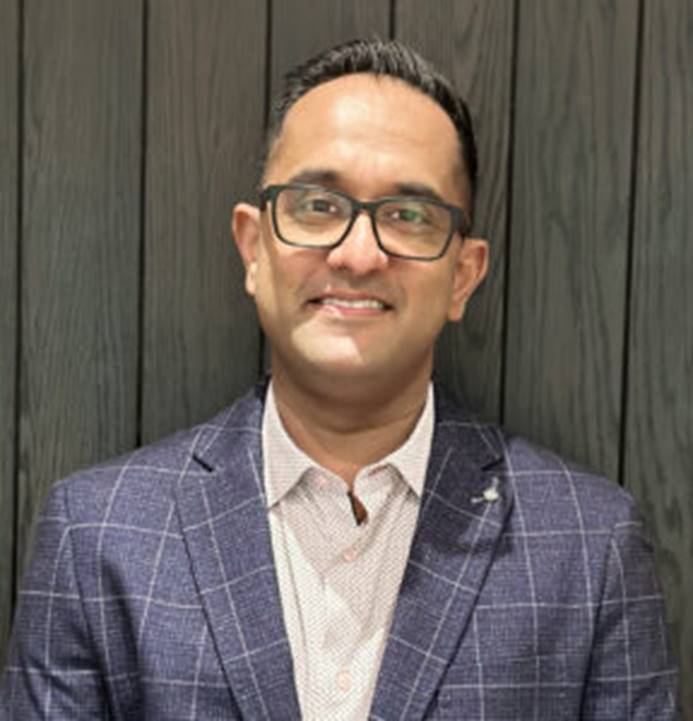
Handling Specialty Manufacturing Ltd., a provider of custom engineering solutions and specialized manufacturing, has announced the appointment of Ben D’Souza as its new president. With over 20 years of experience in the manufacturing sector, Ben brings a wealth of knowledge and a proven track record of driving innovation and operational excellence. Ben most recently served as Assistant General Manager at Massiv Automated Systems, Magna International, where he successfully led initiatives that increased production efficiency and innovation and enhanced on-time delivery. His leadership has consistently resulted in substantial revenue growth and improved customer satisfaction. “We are thrilled to have Ben join our team,” said Dave Ried, VP of Operations of Handling Specialty. “His deep understanding of the industry and commitment to excellence align perfectly with our mission to deliver top-notch custom solutions to our clients. We believe his vision will be instrumental in taking Handling Specialty to new heights.” Ben is known for his strategic approach to leadership, focusing on building strong teams and fostering a culture of innovation. He holds a Bachelor of Engineering from Toronto Metropolitan University (Formerly Ryerson), a Masters of Business Law from Osgood Hall (York University), and an MBA from the Schulich School of Business (York University). “I am excited to join Handling Specialty and to work alongside such a talented and innovative team,” said Ben. “Together, we will continue to push the boundaries of what is possible in our industry and provide our customers with exceptional value.” Handling Specialty Manufacturing Ltd. looks forward to Ben’s innovative ideas and leadership as the company continues to expand its offerings and strengthen its position in its diverse markets.
Episode 532: Tech-Driven logistics with Transfix
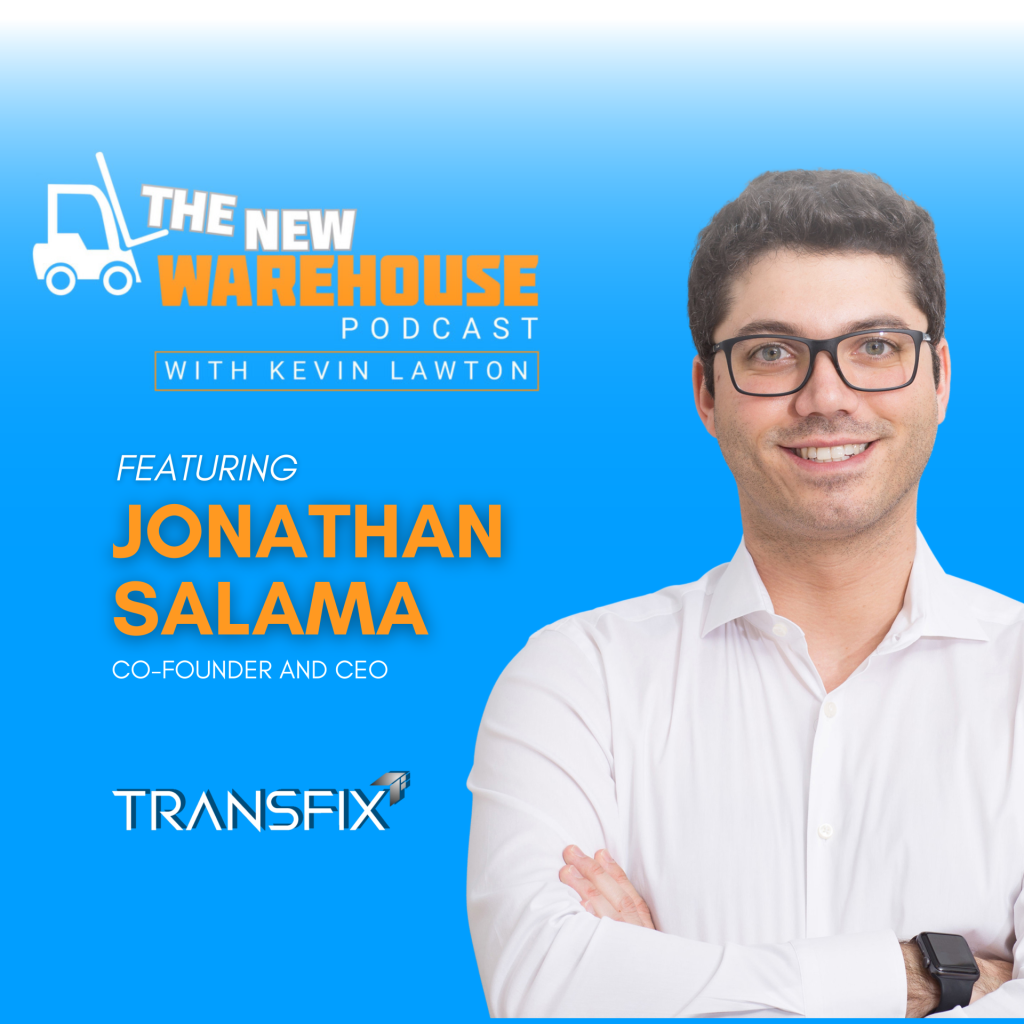
In this episode of The New Warehouse Podcast, we dive into tech-driven logistics with Jonathan Salama, co-founder and CEO of Transfix. Jonathan shares the journey of Transfix, including their recent shift to focus solely on technology. We explore technology’s key role in optimizing freight operations as Transfix evolves from a brokerage to a tech-driven solutions provider. The conversation covers the importance of automation, predictive data models, and how Transfix aims to reshape the future of logistics. From Brokerage to Tech-First: The Evolution of Transfix Transfix started as a brokerage to automate various freight processes. Early on, the company created tools to simplify tasks like shipment tracking and delivery scheduling. Jonathan explains, “We wanted to automate every step… anything that could be automated, we did.” This focus on automation contributed to the company’s growth and eventually led Transfix to sell its brokerage to NFI, redirecting efforts solely to technology. Today, Transfix’s tech platform, refined over the years, serves as its core product. With data-driven tools, the company aims to enhance workflows for both shippers and carriers. “The real value was the tech… that’s where we’re focusing all our efforts now,” Jonathan notes. Tech Advancements Driving Industry-Wide Transformation The logistics industry has seen a surge in tech adoption, but as Jonathan pointed out, it wasn’t always this way. “There was almost no conversation about technology in logistics back then,” he remarked, recalling the early days of Transfix. Tools like data science models and automation platforms are standard, but there’s still room for improvement. Transfix’s platform goes beyond basic tracking—it helps companies optimize their freight strategies in real-time. Jonathan highlighted how they used data to help shippers, stating, “We can predict when your truck will hit detention… so you can adjust and avoid unnecessary costs.” With this level of predictive capability, Transfix empowers companies to make better decisions, streamline operations, and reduce inefficiencies across the supply chain. What the Future Holds for Logistics Tech As logistics evolves, Jonathan sees even more room for technological innovation. From automated trucks to AI-driven models, the future is full of possibilities. “The next decade is going to be completely different… we’re just scratching the surface of what tech can do,” he said. Transfix’s forward-thinking approach positions them at the forefront of these innovations. Their current focus includes refining their machine learning algorithms to provide even more accurate freight rate predictions and expanding their suite of automation tools. Once fragmented and lagging in tech adoption, the industry is embracing digital transformation’s power—a trend Jonathan is confident will continue to accelerate. Key Takeaways Transfix shifted from a brokerage to focus solely on technology, selling its brokerage business to NFI. Their platform automates key freight processes, offering tools for predictive cost models and automated scheduling. Tech adoption in logistics is growing, but Transfix is pushing the boundaries of what’s possible with data and automation. Jonathan Salama envisions a future where technology plays an even more significant role in the logistics industry, with automated trucks and AI models leading the way. The New Warehouse Podcast Episode 532: Tech-Driven logistics with Transfix
Port of Long Beach awarded $2.6 Million Security Grant
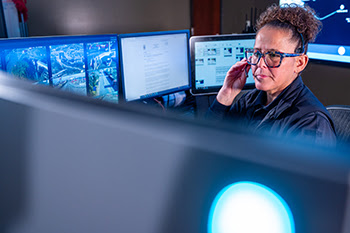
The Port of Long Beach has been awarded more than $2.6 million by the U.S. Department of Homeland Security’s Federal Emergency Management Agency to protect critical infrastructure and ensure the safe movement of trade at the nation’s second-busiest seaport. As the nation’s third-largest recipient of the agency’s Port Security Grant Program, the Port of Long Beach will invest the funding into strengthening cybersecurity, improving drone detection capabilities, and upgrading network infrastructure that supports the efficient flow of cargo. The Department of Homeland Security also awarded $4.2 million to six terminals within the Port of Long Beach, the Long Beach Police Department’s Port Police Division, and the Long Beach Fire Department. “These investments are vital in safeguarding our port’s operations and ensuring the secure movement of trade,” said Long Beach Mayor Rex Richardson. “This grant underscores our commitment to maintaining the highest standards of safety and efficiency at one of the nation’s busiest seaports.” “We thank the Department of Homeland Security for driving innovative security practices and heightening the Port’s ability to protect the people and the infrastructure responsible for moving cargo valued at more than $200 billion annually,” said Port of Long Beach CEO Mario Cordero. “This grant will bolster the Port’s existing security systems and enhance the resiliency of our operations in the event of an emergency.” “This grant will elevate our ability to protect the harbor with state-of-the-art technology and secure the livelihoods of more than 2.6 million people whose jobs depend on Port operations,” said Long Beach Harbor Commission President Bonnie Lowenthal. “We are grateful for this federal funding to strengthen this critical gateway for trans-Pacific trade.” “The Port of Long Beach is essential to our economy, serving as one of the country’s busiest hubs for trade and commerce,” said Sen. Alex Padilla. “This crucial investment in port security from FEMA will strengthen our port infrastructure, while protecting jobs and safeguarding our supply chains and national security.” “We’re very excited the Port of Long Beach was able to secure such critical new funding through the Port Security Grant Program, which will improve our port’s security and protect our communities,” said Rep. Robert Garcia. “As the top economic driver in our community, I will always make sure our Port has the necessary resources to be safe, sustainable, and green, with the most up-to-date technology. I was proud to advocate for the funding of this program in Congress, and I want to thank FEMA for making this grant money available in order to improve our port-wide risk management activities.”
Signode unveils new Transit Packaging Innovations and Integrated Automation Solutions at PACK EXPO 2024
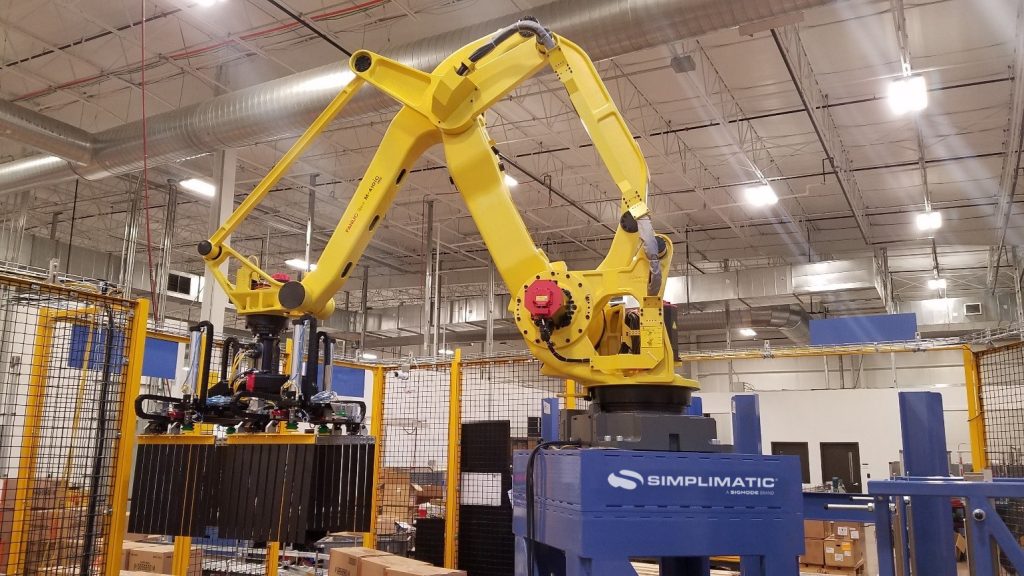
Signode, a global manufacturer of a broad range of transit packaging equipment, tools, consumables, automation, and support solutions, highlights new equipment and industry-leading technologies at PACK EXPO International 2024. The show is held at McCormick Place in Chicago, Illinois, from November 3-6; visitors to booth S-3100 will have the opportunity to see live equipment demonstrations and explore the latest additions to the expansive Signode portfolio of end-of-line transit packaging solutions. “At PACK EXPO 2024, we are excited to demonstrate how innovation drives every aspect of our end-of-line packaging solutions, from automated equipment to packaging consumables,” said Mike Wolf, Senior Director of Signode Technologies. “The new solutions we’re introducing at the show highlight our commitment to creating easy-to-use, adaptable systems that align with the evolving challenges facing today’s manufacturers.” New Innovative Products Highlights at PACK EXPO For the first time at PACK EXPO, Signode will debut several new innovations in its portfolio of plastic strapping solutions, including equipment, tools, and consumables. Representatives will be on-site to demonstrate how these advancements can add efficiency and improved productivity to your unique operation. Among these innovations is the fully automated SGP-5330 strapping bundler. The latest addition to the SGP series expands on its predecessor’s capabilities, now offering a smart touchscreen HMI and advanced IoT integration for real-time equipment monitoring and proactive maintenance. Live Integrated Solution Demonstrations Signode will also host live demonstrations of an integrated packaging system featuring the new GCU-3 strapping unitizer and the fully automatic Octopus® S Series stretch wrapping machine. This combination streamlines end-of-line operations while improving load integrity throughout the distribution cycle. Equipped with up to six modular heads for enhanced flexibility and maximum throughput, the GCU-3 uses sensitive compression and variable head tension to enable the strapping of highly delicate loads. The Octopus S Series uses an “S” wrap pattern to optimize load containment and minimize film usage, enabling it to wrap up over 100 loads per hour. The integrated demo will incorporate custom protective packaging through Signode Engineered Solutions, such as leading Multi-Wall™, PDM™, and Reddi-Pac™ brands. Lightweight, durable, and fully customizable, Signode’s turn-key packaging solutions aim to improve output, minimize waste, and maximize efficiency for the most demanding jobs. Signode will also run live demos of its fully customizable Simplimatic® Robotic Palletizing Systems and Simpli-flex® Conveying Systems. Engineered for ultimate versatility, these systems provide flexible options for loading single or multiple pallets, with multi-axis and collaborative configurations that adapt to various product lines. Integrating a Simpli-flex conveyor system upstream in your operation helps set the stage for a continuous flow of materials throughout each phase of the distribution cycle, enhancing overall throughput and operational efficiency. Signode’s comprehensive approach is further strengthened by a diverse portfolio of protective packaging, dunnage, and transit packaging solutions designed to elevate our customers’ operations and reinforce our commitment to their ongoing success. These and all Signode offerings are backed by industry-leading service and support. Customizing solutions to meet transit packaging needs, Signode has expanded its offering to include total support through its Packaging Plus Reliability Services programs, leveraging IoT capabilities for remote monitoring and service alongside on-site support from the Customer Experience Center in Roselle, IL.
Port of Long Beach honored for Small Business Support
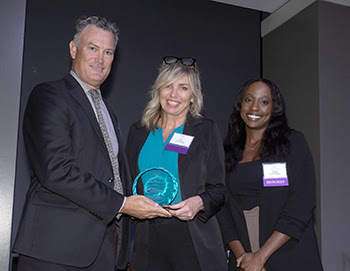
The Port of Long Beach has been recognized for supporting small businesses by connecting them to port-related construction and professional services contracts. The Port received the “Champion of Small Business” award during a recent awards banquet hosted by the Los Angeles County chapter of the American Council of Engineering Companies of California, an organization of engineering and land surveying firms. “Our engagements with the vendor community allow us to open the lines of communication with small businesses and reduce barriers for their participation in Port business,” said Port of Long Beach CEO Mario Cordero. “We thank the ACEC Los Angeles County chapter for this recognition.” “Our Small Business Enterprise Program creates significant economic opportunities by opening the door to a diverse set of local contractors and vendors,” said Long Beach Harbor Commission President Bonnie Lowenthal. “The SBE’s quarterly meetings and focus groups provide us with the feedback that allows us to create a more level playing field for small businesses.” In the 2023 fiscal year, 41.8% of Port funds spent on eligible contracts through the Port’s Small Business Enterprise Program went to purchase needed services and materials from companies defined as “small business enterprises” and “very small business enterprises,” exceeding the Port’s goal of 27%.
American Staffing Association names 2025 Board of Directors Officers
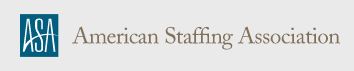
Today, the American Staffing Association announced its newly elected officers for the 2025 board of directors. The board voted on the leaders during the association’s annual Staffing World® convention and expo, which is taking place this week in Nashville, TN. The 2025 ASA board officers are: Chair: Janette Marx, Airswift First Vice Chair: Tom Gimbel, LaSalle Network Second Vice Chair: Jeff Bowling, Four Piers Advisors Treasurer: Ken Taunton, CSC, The Royster Group Secretary: Dana Baughns, Allegis Group Immediate Past Chair: Joanie Bily, Employbridge At the annual membership meeting, ASA members elected the following board members for three-year board terms: Andrea Brenholz, ATR International W. Benjamin “Ben” Elliott, Randstad Tom Gimbel, LaSalle Network Karenjo Goodwin, Exact Staff Inc. Ranjini Poddar, Artech LLC Mark Toth, CSP, ManpowerGroup Steve Wehn, AMN Healthcare DeLibra Wesley, National Recruiting Consultants Other directors currently serving on the board include Threase Baker, TSC, CSP, Abbtech Professional Resources, Inc.; Jeffrey S. Burnett, CSP, Labor Finders International Inc.; James A. Essey, CSP, TemPositions Group of Cos.; Jeff Harris, Workforce Unlimited; Jason Leverant, TSC, CSP, CSC, CHP, AtWork Group; Laura MacNeel, Aya Healthcare; Kelly McCreight, CSP, Hamilton-Ryker; Robin Mee, MeeDerby; Peter W. Quigley, Kelly; and Joyce Russell, Adecco Group US Foundation. “I’m deeply honored to have the opportunity to give back to the staffing industry through my role as chair of the ASA board,” Marx said. “Along with my colleagues, we’re excited to ensure our industry continues to innovate and lead the way in the labor market and the economy.” “The world of work and recruiting is undergoing an era of transformative change. Our association is fortunate to have forward-looking leaders who will advance the interests of the staffing, recruiting, and talent solutions industry in the coming year,” said Richard Wahlquist, chief executive officer of ASA. “Under Janette’s leadership, ASA and the board of directors will continue to play a key role in shaping the future of our industry and the world of work.” The complete list of ASA board members can be found at americanstaffing.net.
Holland Industrial & Prestige Auctions to conduct Auction of Complete Honeywell Intelligrated Manufacturing Facility
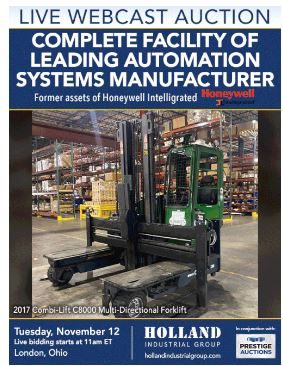
Holland Industrial Group, in partnership with Prestige Auctions, will conduct a live webcast auction of a complete 280,000 SF manufacturing facility of Honeywell Intelligrated, an automation systems manufacturer. The live webcast auction will be held on Tuesday, November 12th, 2024, at 11:00 AM ET, featuring a comprehensive range of late model production equipment, including precision CNC sheet metal fabrication and forming equipment, profile rolling, tube re-cut & finishing equipment, welding, material handling systems, a well-equipped machine shop, over 250 + sections of heavy duty pallet racking, 50+ sections of cantilever racking, 17+ forklifts and more. This sale presents a rare opportunity to acquire top-quality assets from one of the industry’s leading manufacturers. Featured Assets Include: 2013 Pivatic PCC60 TTHD CNC Punch Center with Uncoiler and Straightener 2014 Trumpf TruPunch 3000 CNC Punch 2015 Trumpf 7036 Electric Press Brake 2008 Trumpf 3180 CNC Press Brake 2007 Cincinnati 175MX 14’ CNC Press Brake and Cincinnati 60CBII CNC Press Brake 2016 Haven 873 HF Tube Cut-Off Line with Haven 960 Double End Deburring Machinery Late Model Kone & Gorbel Freestanding Crane Systems Miller & Lincoln Welders 2017 Combi-Lift C8000 Multi-Directional Forklift (17) CAT & Hyster Forklifts, machine shop equipment, air compressors, shop support, and more “At Holland Industrial Group, we are proud to offer our clients access to best-in-class fabricating and finishing equipment from one of the most respected names in the industry,” said Alex Holland, Senior Vice President of Holland Industrial Group. “This sale will be the fourth auction event that Holland and Prestige have conducted on behalf of Honeywell Intelligrated, and once again provides an excellent opportunity for businesses to secure premium industrial assets at a discount, with the convenience of a webcast auction.” Adam Herman, Vice President of Prestige Equipment, added, ” This is an impressive offering of precision metal fabrication and forming equipment previously used in the production of industry-leading conveyor and sortation systems, as well as a wide variety of general plant and production support equipment available for sale.” Participants are encouraged to register early to access the full auction catalog and ensure a smooth bidding experience. On-site inspections will be available by appointment before the auction.