Engle to embark on a new adventure after 32 years of service
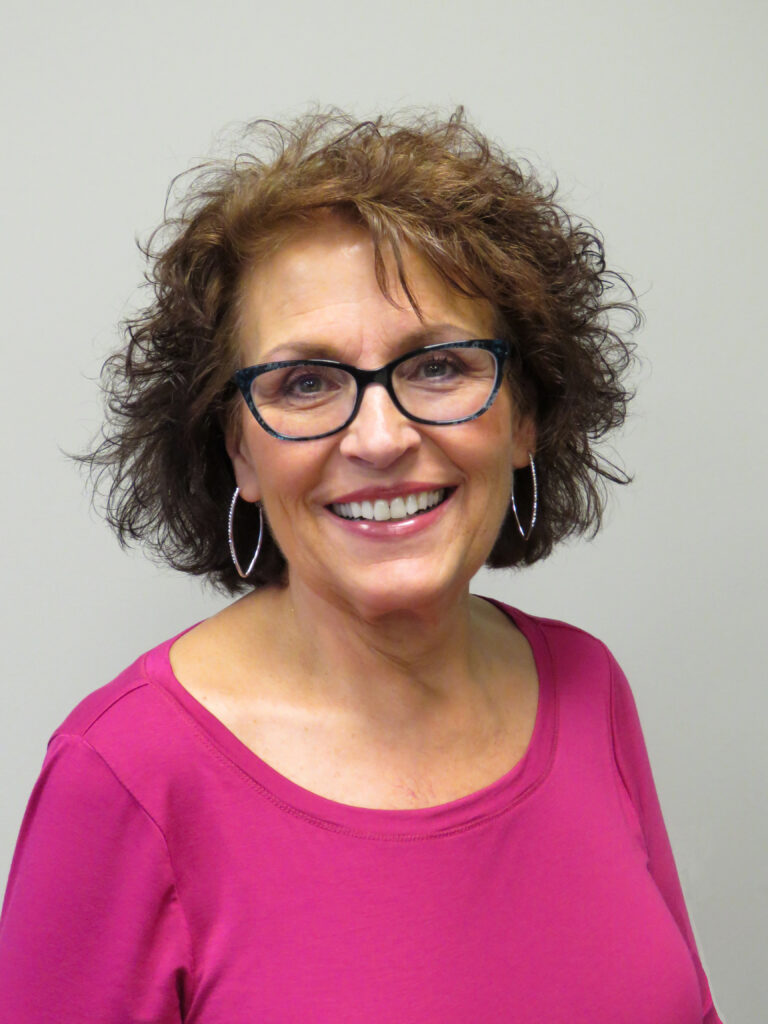
Laurie Engle, Felling Trailers’ Inside Trailer Sales Consultant, has lived and breathed trailers for thirty-two years. Laurie’s trailer tale started in the fall of 1991; Merle and Kathy Felling (founders of Felling Trailers) were in the midst of an office expansion. The local contractor running the expansion was Laurie’s husband. Like many family-owned businesses, Laurie was lending a hand to complete the project, working on painting and staining. “I was painting in the office one day, and the phones were ringing off the hook. I asked the secretary at the time if they (Felling) ever needed help answering phone calls, and she replied sure do,” said Laurie. Not knowing much about trailers but willing to learn, she spoke with Merle later that day and expressed her interest in working for Felling Trailers. After a bit of conversation, Merle said, “Yes, certainly, but we’ll start you off in the Parts room, selling axles, brakes, sheet steel, etc., then transition into trailer sales.” Merle believed strongly that having a good foundation of knowledge about the components and construction of a trailer makes for a better salesperson.” That was the best thing he ever did! Within six months, I sold my first trailer to Landscape Designs out of Alexandria, MN, and when I was asked about the components on the trailer, I had the answers right away with my experience in parts sales,” said Laurie. In the early 90’s, Felling Trailers did not have the extensive dealer network it does today; with a few dealers in the upper Midwest, Felling sold directly to end users. “We also sold livestock/horse and enclosed cargo trailers at that time. We were very busy; my phone was ringing off the hook. I’ve never looked back. Over the years, our product line grew dramatically; we now have 240 plus trailer models compared to the 8-10 different models we once offered. We never turned down a trailer deal, though; if a customer/dealer wanted something longer, shorter, taller, or different material, we’d make it happen,” said Laurie. With each decade that passed, the company never ceased to grow in one way or another. Merle strived to maintain an ongoing process of improving efficiencies with new equipment and cutting-edge technologies, expanding production space, and increasing the workforce. “When I started, we (Felling) had only 4 or 5 bays, and trailers were painted across town. A few years down the road, more bays were added, along with paint and blast booths and finishing. Merle and Kathy were very busy raising a family while putting in many hours throughout the day at the shop. They were constantly looking ahead, building for their future and their children’s futures,” said Laurie. Today, the company is now owned and operated by Merle & Kathy’s daughters, Brenda (Jennissen) and Bonnie (Radjenovich). Felling Trailers has always been a very family-orientated business, “I watched the girls grow, right alongside my own three children, as they created their lives and started families,” said Laurie. Through the years, Laurie has built many working relationships with dealers and customers, solving transport problems other manufacturers said were unsolvable. Felling’s Trailer Experts (Sales Team) work with dealers/customers to configure a trailer to meet the desired specifications and provide a custom solution. “Laurie has been a fixture of Felling Trailers for a long time. Her experience and customer service skills will be sorely missed. Felling Trailers is a better place because of Laurie Engle!” said Pat Jennissen, VP of sales and marketing. “I am truly humbled by the trust and confidence placed in me over the years. The loyalty and support from dealers and customers has been the driving force behind my success, and for that, I am forever grateful,” said Engle. From the many standard-built trailers to those that have been highly customized, certain ones stand out from the rest. One such trailer was for an amusement park ride company located on the East Coast. They needed a mobile platform trailer that could be paired with their Ferris wheels. Taking the specs and information provided by the amusement ride company, Laurie worked internally with Felling’s engineering team and custom fabricators to design and build a lightweight, high-quality trailer to meet the company’s needs. The trailer was exactly what the amusement company needed; Felling built seven more trailers over the next five years. Another series of even more unique trailers were flare trailers that would burn waste gases generated from pipelines, well sites, landfills, storage facilities, and maintenance activities. The trailer was configured with hydraulic outriggers to stabilize the unit during use and a hydraulic telescoping flare unit powered by a gas-powered engine mounted to the trailer’s deck. “Laurie has been a strong asset to our team. In addition to her deep trailer knowledge and excellent customer relationships, Laurie’s bright smile and tremendous personality will be missed in the office! I wish her the best retirement, making memories with her family!” said Brenda Jennissen, President/CEO. Laurie will hang up her headset and power down her system for the last time as a trailer sales consultant in late May of this year. “After 32 years of dedicated service in the trailer manufacturing and sales industry, the time has come for me to embark on a new chapter in my life as I transition into retirement. While I am excited for the opportunities ahead, I am also grateful for the incredible journey we have shared.” Passing on a few words of wisdom to those who follow, Laurie said, “Work hard, no matter what your job is, whether it’s on the phone getting the next sale or doing a fantastic job welding, painting, or finishing a trailer.” “Congratulations on your retirement, Laurie! Your many years of hard work and dedication have inspired us all. We will miss your presence, but we’re so happy for you as you embark on this new journey. We wish you all the best for this new chapter in your life!” said Nathan Uphus, sales manager. Her retirement plans are to “remember that
U.S. Rail Traffic report for the week ending May 25, 2024
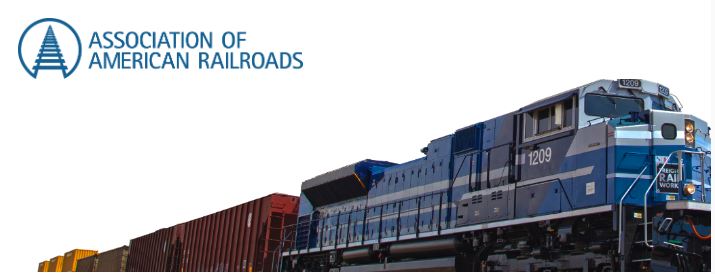
The Association of American Railroads (AAR) has reported U.S. rail traffic for the week ending May 25, 2024. For this week, total U.S. weekly rail traffic was 485,232 carloads and intermodal units, up 1.2 percent compared with the same week last year. Total carloads for the week ending May 25 were 217,744 carloads, down 6.9 percent compared with the same week in 2023, while U.S. weekly intermodal volume was 267,488 containers and trailers, up 8.9 percent compared to 2023. Three of the 10 carload commodity groups posted an increase compared with the same week in 2023. They were petroleum and petroleum products, up 2,073 carloads, to 11,337; chemicals, up 1,540 carloads, to 33,439; and farm products excl. grain, and food, up 600 carloads, to 17,091. Commodity groups that posted decreases compared with the same week in 2023 included coal, down 12,617 carloads, to 50,216; nonmetallic minerals, down 4,158 carloads, to 30,981; and metallic ores and metals, down 2,361 carloads, to 21,689. For the first 21 weeks of 2024, U.S. railroads reported a cumulative volume of 4,477,274 carloads, down 5.0 percent from the same point last year; and 5,324,623 intermodal units, up 8.6 percent from last year. Total combined U.S. traffic for the first 21 weeks of 2024 was 9,801,897 carloads and intermodal units, an increase of 1.9 percent compared to last year. North American rail volume for the week ending May 25, 2024, on 10 reporting U.S., Canadian, and Mexican railroads totaled 320,227 carloads, down 4.2 percent compared with the same week last year, and 350,485 intermodal units, up 5.7 percent compared with last year. Total combined weekly rail traffic in North America was 670,712 carloads and intermodal units, up 0.7 percent. North American rail volume for the first 21 weeks of 2024 was 13,821,331 carloads and intermodal units, up 2.0 percent compared with 2023. Canadian railroads reported 84,882 carloads for the week, down 1.3 percent, and 70,899 intermodal units, down 5.6 percent compared with the same week in 2023. For the first 21 weeks of 2024, Canadian railroads reported a cumulative rail traffic volume of 3,385,766 carloads, containers, and trailers, up 0.7 percent. Mexican railroads reported 17,601 carloads for the week, up 24.3 percent compared with the same week last year, and 12,098 intermodal units, up 12.3 percent. Cumulative volume on Mexican railroads for the first 21 weeks of 2024 was 633,668 carloads and intermodal containers and trailers, up 11.2 percent from the same point last year. View reports here
Episode 490: Addressing warehousing labor challenges with Inviscid Consulting
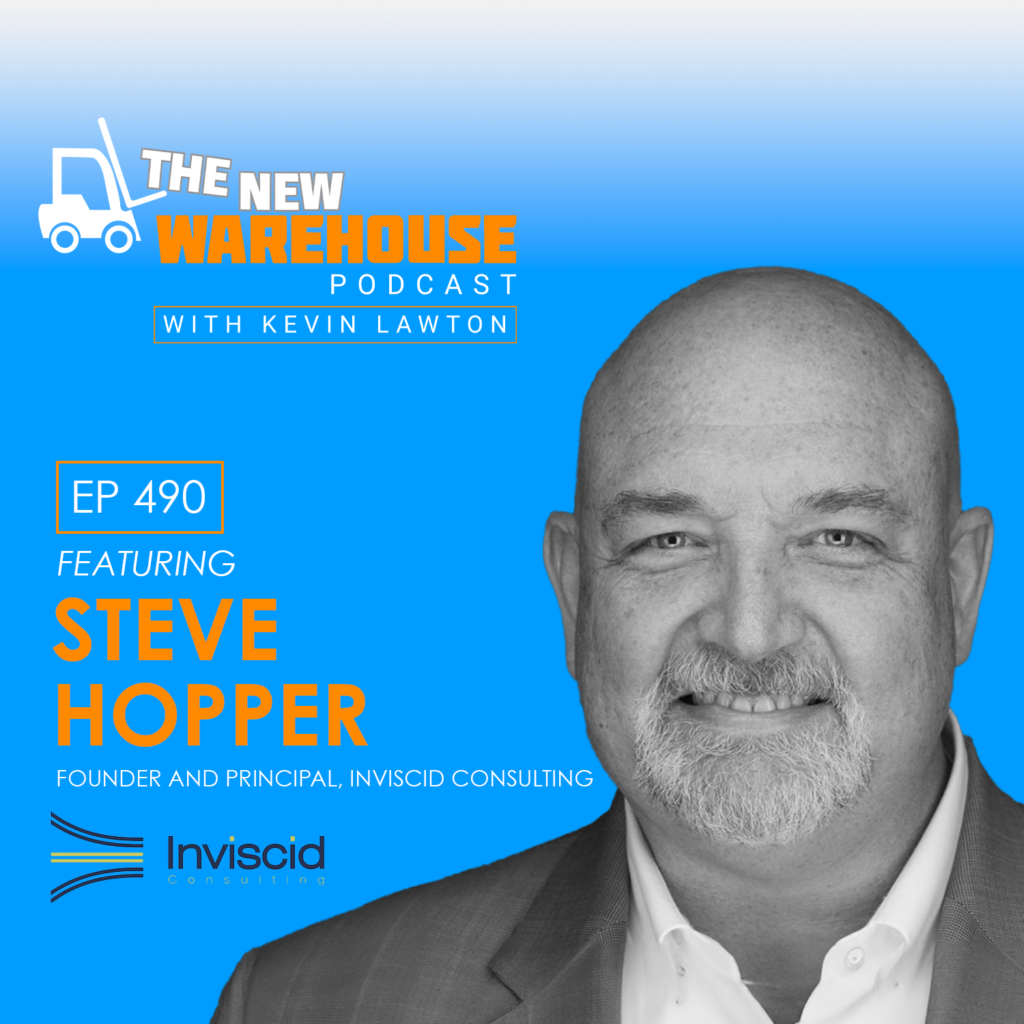
In episode 490 of The New Warehouse Podcast, Steve Hopper, founder and principal of Inviscid Consulting, joins the show to discuss the ever-pressing topic of labor. With decades of experience in the industry, Hopper brings a wealth of knowledge in optimizing warehousing, distribution, and logistics operations. Inviscid Consulting specializes in streamlining processes to reduce costs and enhance service levels. In this episode, Hopper delves into the persistent labor challenges in the warehousing sector, the nuances between labor performance and productivity, and innovative approaches to addressing workforce shortages without solely relying on increased staffing. Navigating Labor Challenges in Warehousing Labor shortages have been a longstanding issue in the warehousing industry, exacerbated by recent events like the pandemic and an aging workforce. Hopper explains that many view warehousing work as unappealing due to its physical demands and repetitive nature. This negative perception, evolving worker qualifications, and language barriers create a perfect storm for labor shortages. Despite these challenges, Hopper emphasizes, “You can’t just throw bodies at the problem. You must look at alternatives to get more out of your existing workforce.” Enhancing Productivity Through Strategic Measures Hopper discusses the critical distinction between productivity and performance in warehousing operations. Productivity is a raw metric of output divided by input, such as units per hour. Performance, however, encompasses a broader range of factors, including the pace of work, the methods used, and the overall utilization of time. “Many businesses overlook simple yet effective strategies to improve productivity,” Hopper says. He suggests that instead of immediately turning to automation, companies should focus on optimizing their current resources. Implementing best practices, improving worker training, and ensuring effective use of time can significantly enhance performance. Hopper uses a vivid analogy: “Think of Michael Jordan. His performance was a combination of pace, method, and utilization. It’s the same with your workforce.” Addressing Labor Shortages without Increasing Headcount Inviscid Consulting helps businesses tackle labor shortages by optimizing existing processes and resources. Hopper explains that many companies fail to manage and measure their workforce actively, leading to inefficiencies and high turnover. “Many are just throwing people into the warehouse and hoping for the best,” he observes. By conducting thorough operational assessments, Inviscid Consulting identifies areas for improvement. Hopper stresses the importance of setting realistic goals, managing workforce engagement, and fostering a positive work environment. He highlights innovative solutions like gamification and flexible working hours to attract and retain younger workers. Key Takeaways Addressing labor shortages requires more than just hiring more workers. Productivity and performance are distinct metrics; improving both involves optimizing pace, methods, and utilization. Implementing best practices and active workforce management can significantly enhance productivity. Innovative approaches, such as gamification and flexible working hours, can help attract and retain workers. The New Warehouse Podcast Episode 490: Addressing Warehousing Labor Challenges with Inviscid Consulting
SkyTrak® 8042 Telehandler offers more features and capabilities
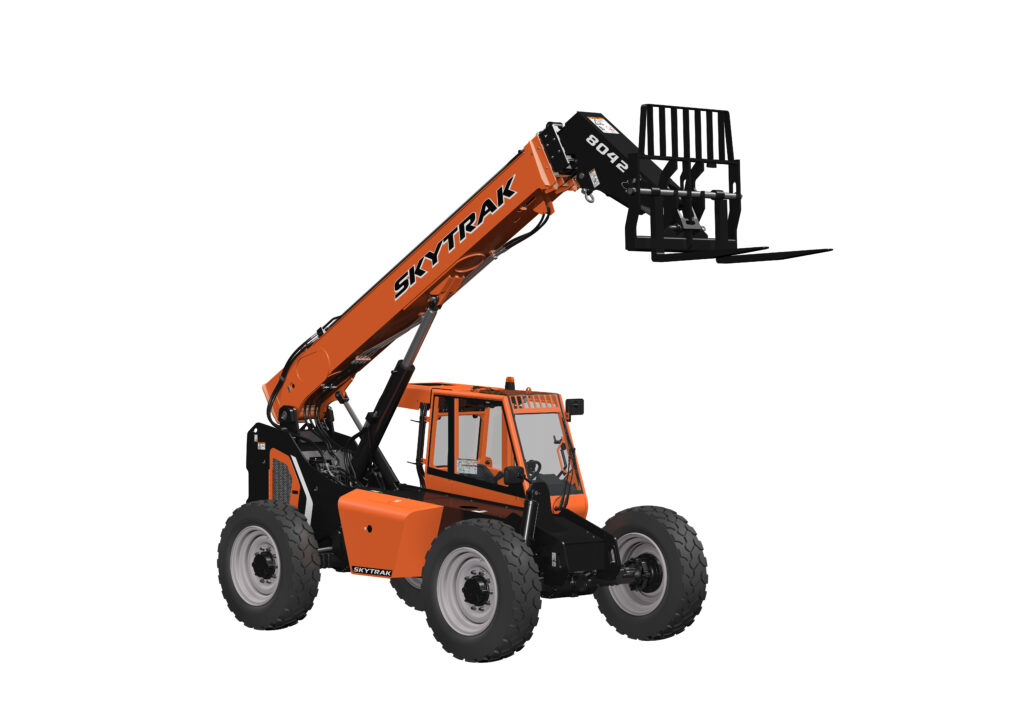
Innovative updates inspired by customer requests JLG® Industries, Inc. has introduced the all-new SkyTrak® 8042 telehandler, remastered to maintain the performance and reliability customers expect from the SkyTrak brand. Building on the legacy of its predecessor, this next-generation model comes with innovative updates that include a lightweight design, hydrostatic transmission, advanced control system, electric-over-hydraulic joystick and data at-a-glance. With the relaunch of the 8042, JLG continues the process of redesigning its popular SkyTrak telehandler line, which also includes the all-new 6034 and 6042 models introduced in 2023. “JLG redeveloped this model from the ground up with enhanced technology and functionality to meet the needs of today’s job sites and zero sacrifices,” says John Boehme, senior product manager – telehandlers, JLG. “We listened closely to our customers’ most requested features and capabilities to improve the efficiency and serviceability of the 8042, without any compromises. This model is designed to increase productivity and boost overall job performance in pick-and-place applications, such as handling, loading and unloading bulk materials on demanding residential, commercial, urban and suburban job sites across America.” Redesigned Build Keeping job site efficiency in mind, the updated 8042 features a lightweight design with an optimized boom and frame structure to make transportation much easier. Now two JLG 8042 telehandlers can fit on a single flatbed trailer. These updates did not compromise the machine’s key attributes; it still boasts the same maximum capacity and same all-steel construction it’s known for. The improved cab styling on the 8042 provides a larger LCD display and single-page load charts to deliver the data operators need, while allowing them to stay focused on the job at hand. The SkyTrak 8042 telehandler offers a maximum lift height of 42-ft 4-in, a maximum reach of 29-ft 6-in, and a 21,200-lb operating weight. The enclosed cab on this model is available with optional air conditioning for comfortable operation on hot or humid job sites. Reworked Functionality The hydrostatic transmission on the newly remodeled 8042 provides operators with greater control and ease of operation while allowing for inching — the ability to run the boom at high speeds without shifting into neutral — for faster delivery of materials at height. A multifunctional, electric-over-hydraulic joystick on this unit includes auxiliary hydraulic functions and attachment tilt capabilities, single-handedly elevating job site efficiency. Improved boom speed is complemented by auxiliary hydraulic connections on the side of the boom head for quick, efficient attachment changes. More than a dozen different attachments are offered for the 8042, including a variety of carriages, forks, buckets, hooks and trusses. Reimagined Technology A new, advanced control system on the upgraded 8042 provides more options like load stability indication (LSI), which senses forward load capacity and displays color-coded visuals to help operators work with higher confidence. Seatbelt engagement and operator presence (SEOP) technology is also available, which combines a high visibility orange seatbelt and visual and audible alarms, as well as limiting machine functions, to enhance safe machine operation. Other optional essentials on this model include: Multi-reverse camera system which displays left, right and rear views from behind the machine during day or night operation on a single, tri-view monitor. Reverse sensing system that provides an audible in-cab alarm to alert the operator of any rear obstructions when driving in reverse. White noise back-up alarm that emits a directional alarm when driving in reverse Remote diagnostics and richer telematics connectivity through JLG’s ClearSky Smart Fleet system improve data collection and streamline troubleshooting to help maximize uptime and increase return on investment (ROI). Refocused Serviceability This model is equipped with a 74-hp, 2.9L Deutz diesel engine which does not require diesel exhaust fluid (DEF), reducing maintenance costs. The single compensation and lift cylinder boom design relies on fewer components streamlining maintenance, while the top-mounted telescope cylinder makes the boom more accessible to maintain. A 30% reduction in hydraulic hoses and connections results in fewer potential leak points for improved serviceability.
ORBIS Corporation Partners with Blessings in a Backpack Waukesha County
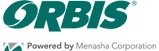
Partnership unites community members and resources to provide supplementary weekend food to students in the Kettle Moraine School District ORBIS® Corporation partners with Blessings in a Backpack of Waukesha County (BIAB) to provide weekend nutrition to students at Magee Elementary School who may lack access to nutritious food on the weekends. While the students are provided meals on the free and reduced lunch programs at school during the week, they often lack resources on Saturday and Sunday. Lack of nutrition can result in physical health problems, shortened attention spans, lower IQs and poorer grade achievements. This school year, Blessings in a Backpack Waukesha County Chapter is working to feed over 3,400 children at 42 schools in Waukesha, Oconomowoc, Sussex, Hartland Lakeside, Kettle Moraine and Menomonee Falls districts. As more than 11,000 children struggle with hunger on the weekends in Waukesha County alone, ORBIS hopes its lead sponsorship of Magee Elementary will increase awareness and inspire other businesses and community members to get involved, ultimately decreasing the number of hungry children to zero. “ORBIS has been working with Blessings in a Backpack Waukesha County Chapter since 2015, and with our headquarters being in Waukesha County, this cause hits close to home for a lot of our people,” said Norm Kukuk, president at ORBIS and board member of Blessings in a Backpack of Waukesha County. “It’s been inspiring to see ORBIS employees unite around this cause, donating their time and expertise, and we hope our support can empower others to give back to their own communities.” As a leader in the movement to end childhood hunger, Blessings in a Backpack offers many ways to get involved, including partnerships, event sponsorships, corporate employee engagement events and volunteer opportunities to help feed children in our community. “Corporate partnerships are critical in sustaining the Blessings in a Backpack program of feeding kids on the weekend. When we receive support from a company like ORBIS, it makes an immense impact in the community,” said Susan Reed, managing director at Blessings in a Backpack of Waukesha County. “The consequences of food insecurity are more than just a growling stomach, so whether it’s involvement through donations or partnerships with our chapter, it makes all the difference.” It takes $5 to feed one child for one weekend and $175 for the entire school year. To learn more about how you can support Blessings in a Backpack Waukesha County Chapter.
Unirope’s Brown elected to OIPEEC Management Board
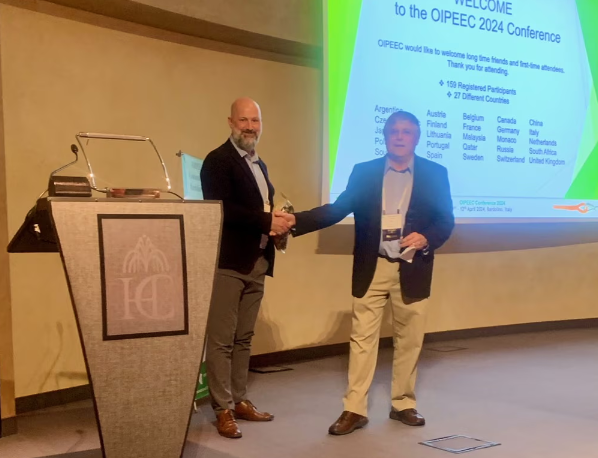
Unirope Ltd. president Justin Brown has been nominated to the board of the International Organization for the Study of Ropes (OIPEEC). Brown has served as a co-opted member of the board since February 2023, and was elected as a full member at last month’s (April) OIPEEC conference in Bardolino, Italy. Also elected to the OIPEEC management board were Amy Jenkins, of Teijin Aramid; and Prof. Dr. Ing. Ulrich Briem, of OTH Regensburg. Other executive changes included Bill Putnam, of Yale Cordage, finishing his term as president; and Sven Winter, of Rotec GmbH, moving into the president role from vice president. Elizabeth Huntley, meanwhile, of Whitehill Manufacturing, was elected vice president. OIPEEC organizes conferences every second year to discuss issues of relevance to ropes. These conferences are open to members and non-members alike. Past conferences covered varied topics, such as ‘Simulating rope applications’, ‘The non-destructive testing of ropes’, ‘Rope terminations and fittings’, ‘Wire rope discard criteria’, ‘How to get the most out of your ropes’, ‘Trends for ropes’, ‘Innovative ropes and rope applications’, and ‘Challenging rope applications’. The OIPEEC appointment adds to Brown’s ongoing industry work, including standards writing with the CSA Group’s tower (CSA Z248) and mobile crane (CSA Z150) committees (both as a member); and American Society of Mechanical Engineers (ASME) B30.30 Ropes (alternate member), where he sits alongside colleague Knut Buschmann, engineered product development (member). Brown is also president of Associated Wire Rope Fabricators (AWRF). He said: “We believe that it is not enough to participate in the fruits of an industry without giving an equal amount back. That is why we have taken the approach of being very active in our sector and contribute wherever we can. We sit on various boards and standards writing organizations and are involved with — and contribute to — many technical committees.” Unirope is actively involved with the Association of Crane and Rigging Professionals (ACRP), where Scott Fleming, director, and sales/rigging training manager, is chair of the board. Fleming is also secretary and treasurer, and technical committee member, at the Web Sling and Tie-Down Association (WSTDA). The company is a working member of the Cordage Institute, an international association of rope, twine, and related manufacturers, their suppliers, and affiliated industries; and the Infrastructure Health and Safety Association (IHSA), Ontario’s trusted health and safety resource. Unirope is a full member of the Lifting Equipment Engineers Association (LEEA) and is certified to ISO 9001.
Carolina Handling named 2023 Modula Top Performer of the Year
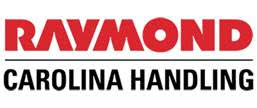
Carolina Handling has been named the 2023 Top Performer of the Year by Modula, Inc., a manufacturer of vertical lift modules and automated storage solutions. An authorized Modula dealer since 2021, Carolina Handling sells, installs and services Modula’s advanced vertical storage and retrieval systems designed to reduce storage space and boost productivity in order picking. Built on the “parts to picker” principle, the automated system has been proven to dramatically increase accuracy, reduce storage space and enhance worker safety and job satisfaction. “As Carolina Handling continues its evolution from a forklift-only company to a provider of end-to-end integrated warehouse solutions, products like Modula enhance our broad portfolio of equipment and technologies to help companies achieve greater speed, safety, accuracy and efficiency in their operations,” said Carolina Handling Chief Operating Officer Joe Perkins. “In addition to sales and implementation, we continue to add Modula Certified Technicians to provide the same elite level of aftermarket support for automation solutions that we’re known for on the forklift side of material handling.” Carolina Handling surpassed 91 percent of its sales quota on Modula units in 2023. Also, 13 Carolina Handling Field Service Technicians were certified in the installation and service of the automated storage and retrieval systems, with another 16 in the process of receiving certification. Carolina Handling also stocks Modula parts and has installed a Modula unit for demonstration and training in its customer experience center in Greenville, South Carolina. The 2023 Top Performer of the Year award includes a gold award for achieving the highest score in Modula’s Dealer Incentive Program and a bronze award for total units sold.
Episode 489: Elevating Warehouse Safety Management with Elokon Group
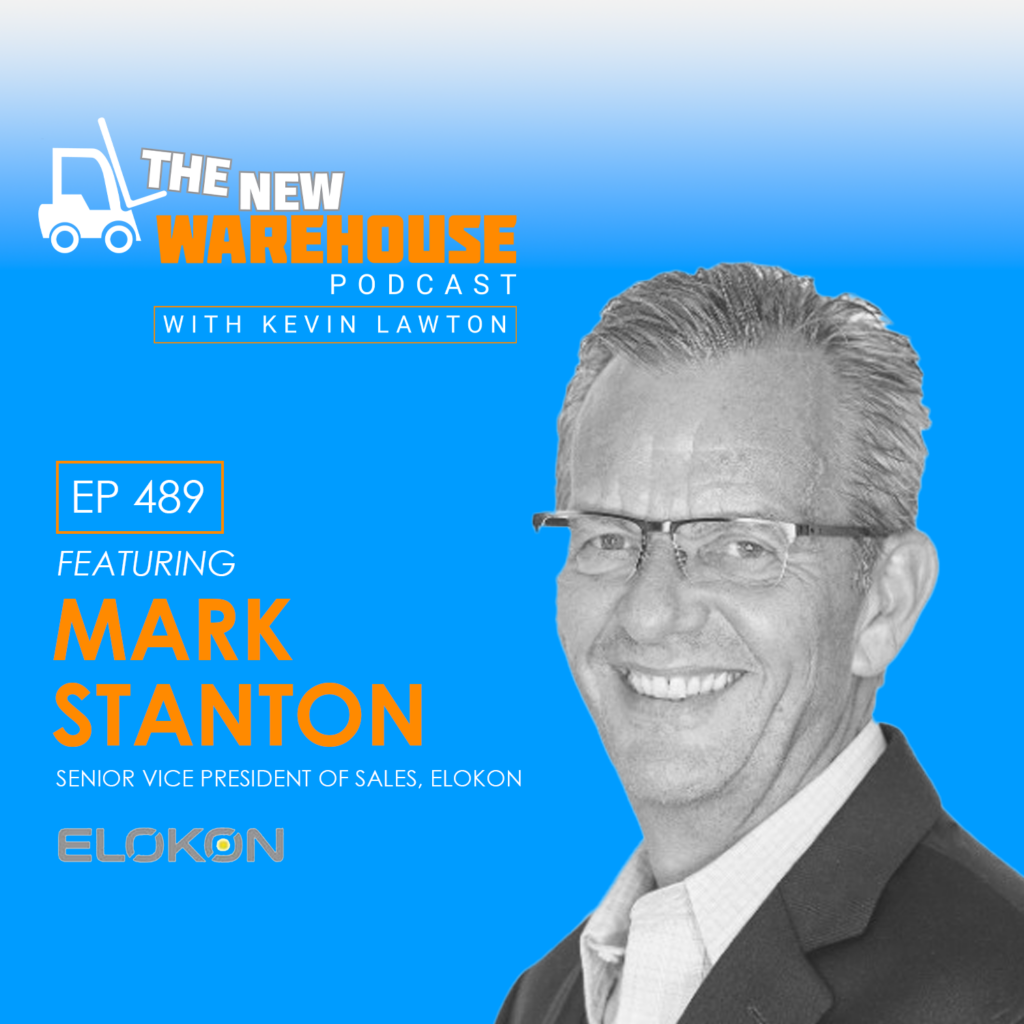
In episode 489 of The New Warehouse podcast, Mark Stanton, President and General Manager of Elokon Group, joins to discuss improving warehouse safety management. Elokon Group, with over 38 years of experience, specializes in enhancing safety for material handling equipment (MHE) and fire safety systems. This episode explores the integration of safety tech, the balance between passive and active measures, and the challenges of demonstrating ROI in safety investments. Integrating Safety Tech in Warehouses Mark emphasizes the significance of combining passive and active safety measures in warehouse environments. While passive measures, such as signage and barriers, are crucial, they often need the support of active technology. He noted, “You can have all the best tech in the world, but if you don’t implement the protocols and procedures and the management and supervision around that tech, there’s no guarantee that it’s going to work or improve anything.” Elokon’s safety solutions, such as the ELOshield system, utilize proximity detection to alert operators and pedestrians to potential hazards, enhancing real-time decision-making and reducing accident likelihood. The Role of Data in Elevating Warehouse Safety Management Data collection and analysis are pivotal in improving warehouse safety management. Elokon’s ELOfleet system exemplifies this by offering comprehensive fleet management through access control, safety checklists, and monitoring operator behavior. There’s so much data just floating around within a warehouse, but how do you take action on that? How do you use that to make better decisions? Stanton believes, “If we can give that human a little bit more information in a timely manner so that he or she can make a better-informed decision, the likelihood is you will get to or close to a zero-incidence operation.” By capturing near-miss incidents, companies can prevent future accidents. Stanton adds,“Whether that event is just a near miss or something more significant, people want to come in with 10 fingers and 10 toes, and they need to leave with the same quantity, you know. And anything we can do to improve and drive that on a daily, weekly, hourly basis and really push that envelope.” Analyzing data helps identify high-risk areas and implement targeted interventions, fostering a safer work environment. Overcoming ROI Challenges in Safety Investments One of the significant challenges in adopting safety technology is demonstrating a clear return on investment (ROI). Stanton shared insights on navigating this challenge, emphasizing the value of pilot programs and peer networking. He explained, “You haven’t had an incident at this point, so go and spend 50 grand, 100 grand just in case. They’re going to come back and say, ‘Well, that seems a little unnecessary.’”By implementing pilot programs, companies can evaluate the effectiveness of safety systems in real-world settings. Additionally, learning from the experiences of other organizations can provide valuable insights and build a compelling case for safety investments. Key Takeaways Combining passive and active safety measures is crucial for comprehensive warehouse safety. Data-driven insights help identify high-risk areas and guide targeted safety interventions. Pilot programs and peer networking can effectively demonstrate the ROI of safety technology investments. The New Warehouse Podcast Episode 489: Elevating Warehouse Safety Management with Elokon Group
Hamilton’s announces new Director of Sales and Business Development
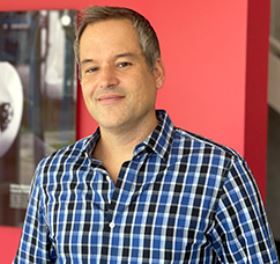
Hamilton Caster has announced that Andy Stamp will serve as their new Director of Sales and Business Development. Stamp has been in the industry for over 26 years. “Over my 26-year career, I’ve honed my expertise in developing new business and expanding existing sales and marketing platforms across various industries supported by Hamilton Caster, said Stamp. My proficiency in leveraging CRM systems to analyze data and drive strategies will be a key benefit.” Mark Lippert, president at Hamilton Caster said, “Andy possesses the hard-to-find ‘biz dev gene.’ It’s that rare genetic makeup of someone who thrives on the hunt for new business while also possessing incredible energy and focus to be successful. More importantly, he’s a heck of a nice guy.” Andy looks forward to growing business at Hamilton. “Profitable and sizable growth in all product groups. The goals include expanding into new customer bases, increasing Hamilton’s footprint nationwide, and ensuring that we are the #1 preferred heavy-duty caster and the “only” choice for heavy-duty carts and trailers”, said Stamp. Andrew holds a Bachelor’s degree in Business Management from Ohio State University and is an active member of professional associations such as AICC and PMMI. He is also a patent holder for innovative adhesive dispensing technologies. “I am thrilled to join Hamilton and be a part of such an innovative team,” said Andrew. “I am committed to driving growth and delivering unparalleled value to our customers. With our focus on innovation and customer satisfaction, I am confident that together, we will achieve new heights of success.”
New Age Industrial announces retirement of Bob Brackle
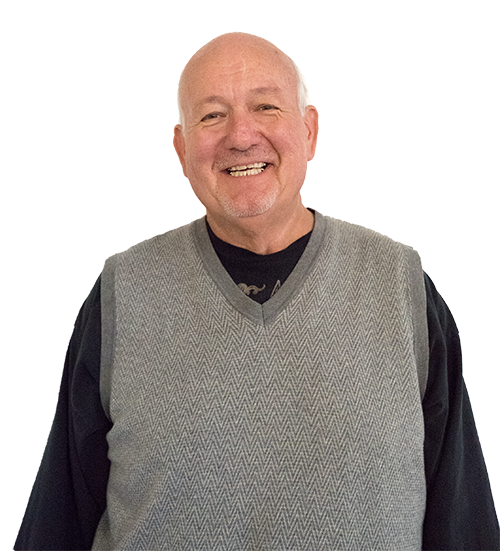
New Age Industrial, a designer and manufacturer of aluminum storage and transport, has announced the retirement of Bob Brackle, National Sales Manager for the Material Handling Division, effective May 25, 2024. Bob has dedicated 15 years and 5 months of service to New Age Industrial, playing a pivotal role in the growth and success of the Material Handling Division. His passion, dedication, and industry expertise have been instrumental in forging strong customer relationships and exceeding sales targets for the company’s innovative aluminum material handling equipment. Under Bob’s leadership, the Material Handling Division significantly increased sales. During this time, we successfully introduced and promoted New Age Industrial’s innovative line of aluminum equipment, revolutionizing how to boost efficiency, optimize workflow, and streamline operations in warehouses, distribution centers, and other material handling facilities. “Bob Brackle is one of a kind,” said Tom Sharp, Vice President at New Age Industrial. “His larger-than-life presence and unwavering dedication to building relationships have made him a legend at trade shows. We’ll miss his ability to captivate a room and generate excitement for New Age Industrial.” He continued, “We are incredibly grateful for his contributions and the lasting impact he has made on New Age Industrial and the entire industry. We wish Bob all the best in his well-deserved retirement.”
Urbx introduces robotic inventory storage and retrieval system for rapid retail fulfillment
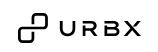
High-density system delivers speed and integration flexibility for e-commerce warehouses, retail and grocery fulfillment Urbx launches its robotic inventory storage and retrieval system capable of fulfilling complex, multi-SKU orders at unprecedented speeds. The system builds on the principles of traditional automated storage and retrieval systems (AS/RS) and uses a combination of robotics, software and storage racking to deliver key advantages in speed, height, density and scalability in goods-to-person order fulfillment workflows. The system uses a fleet of proprietary Urbx TowerBots driven by AI to find the shortest 3D path through a dense storage grid to retrieve totes and bring them out to a pick station. TowerBots move across the top of racking and drop down through strategically located columns to access inventory. This storage grid design requires no navigating aisles or digging to access totes below top storage layers, enabling access to inventory at all levels – stacked up to 75 totes high – in seconds. TowerBots then move totes down through those same columns to built-in conveyor tiles for transport to order fulfillment and consolidation. In practice, the Urbx system enables exceptional fulfillment speeds, capable of fulfilling a 50-line order in less than 2.5 minutes. “We started Urbx to satisfy the demand for speed in retail order fulfillment that just wasn’t being met by existing solutions. We concepted, tested and iterated on a system that really pushes the limits of what automation can do, and in turn, of what fulfillment operations can achieve,” says Lincoln Cavalieri, Founder and CEO, Urbx. “And that goes beyond revolutionizing warehouse environments. Delivering inventory at such high rates also has the near-term potential to address the needs of grocery fulfillment and even consumer-facing retail applications.” The Urbx system offers double-deep storage built up to industry-leading heights for maximum possible density and capacity, while maintaining a small horizontal footprint. This space efficiency is a particularly strong fit for supply chains pushing to locate distribution points closer to consumers in urban centers, where pressure from high real estate costs incentivizes building up, rather than out. The ability to handle up to 100 pounds per tote allows the system to accommodate a broad range of inventory, including heavy, dense items. Urbx is designed with the needs of integrators in mind, without rigid software requirements and specialized hardware components, and is sold and supported by a global network of material handling automation systems integrators. The company uses Beckoff for standard controls and sources totes from Utz.
LEEA Leads High Quality #GLAD2024
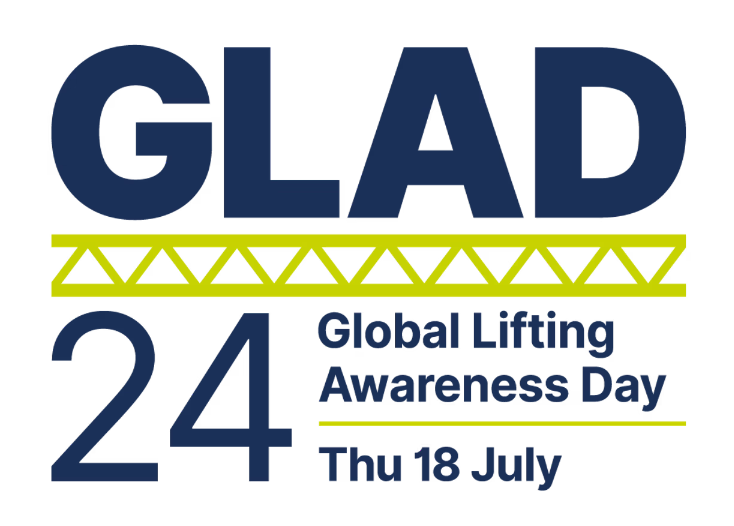
The Lifting Equipment Engineers Association (LEEA) has moved products, inspection, and training to the front of its Global Lifting Awareness Day (GLAD) campaign. As #GLAD2024 approaches on Thursday 18 July, LEEA is sharpening its focus on the importance of surrounding these three cornerstones of lifting with high quality. GLAD is an established event where its members, manufacturers, and suppliers lead those sharing material that promotes safe and high-quality load lifting across the world. Social media posts, videos, articles, and in-person activity are bound together by the hashtag, #GLAD2024. Ross Moloney, CEO at LEEA, said: “It’s about the ongoing battle between cost and quality. We all know that buying decisions are made for a multitude of reasons, but we want people to make sure those choices are always based on quality. It is perhaps easy for some not to think there’s any difference in quality and that all equipment and services are the same; we’re saying this isn’t the case. It’s why we constantly refer to skills, standards, and high levels of competency. This is a specialist industry, where high quality is a minimum requirement.” LEEA has already circulated three graphics based on high-quality products, inspection, and training, all of which attach the trifecta to existing #GLAD2024 publicity. The message chimes with LEEA’s organizational vision to eliminate accidents, injuries, and fatalities, placing further emphasis on skills and employment, which had emerged as front-running themes when the fifth GLAD drive was launched. Moloney added: “We are in a risky industry, and these are three key ways by which we can eliminate risk; accidents occur when these three things fail. Product matters, but because it was once compliant doesn’t mean it always will be, hence the need for ongoing inspection, and this must be conducted by a high-quality individual, who has been trained to the highest standards. “This is where the LEEA logo fits,” Moloney continued. “Joining our association means you become associated with high-quality providers. Our members go through an audit where we help them to check and improve their processes and practices. And on an ongoing basis, our members access training developed and devised by 1,000 members worldwide. We’re not making this content up ourselves — it’s written by the industry, for the industry. Above and beyond GLAD, it’s a clear market signal to end users: if you are involved in lifting, look for the LEEA logo.” Moloney delivered a well-received presentation, centered on GLAD, to the Associated Wire Rope Fabricators (AWRF) Spring General Meeting in Nashville, Tennessee last month (April). It was a delegation united in the understanding that there is no low-risk job in the lifting industry, and the entire global community must be trained and competent. Further, it is a sector that offers work opportunities, especially to younger people looking to become trained and qualified. “Skills in our industry pay the bills,” roared Moloney. “You get trained and qualified, and there are work opportunities in our high-tech, high-quality industry. A perception endures that lifting is all about heft and physicality, but our people fight gravity and do dangerous things. They all need to be trained and competent, so there are no unskilled occupations. We provide training and we strongly encourage end users to make sure that anyone they work with is trained and work-ready. Look at our TEAM card initiative for evidence.”
Trew® named Top workplace by employees for second consecutive year
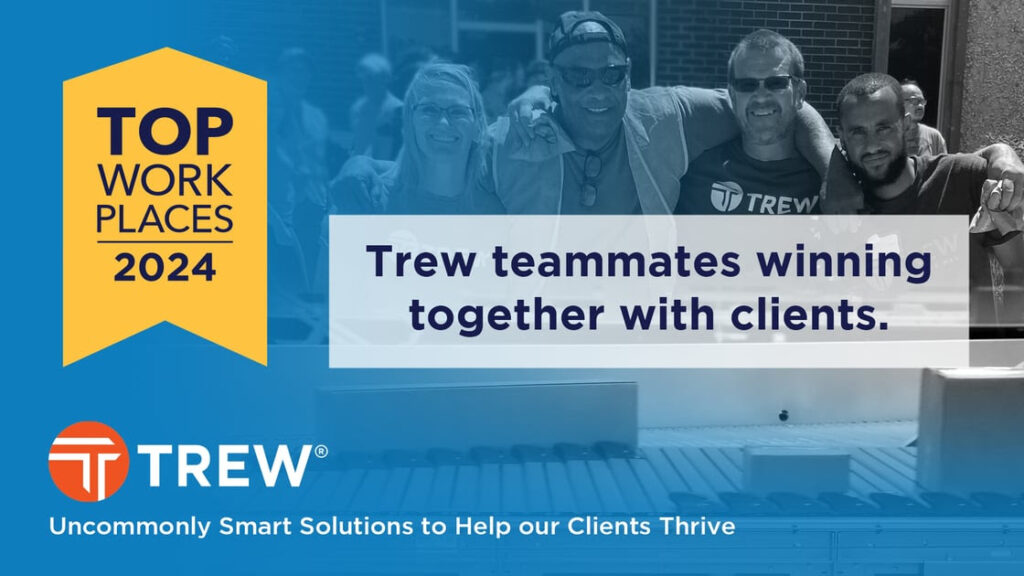
The award recognizes top companies in the Greater Cincinnati region based on employee feedback. Trew, LLC has been recognized as a 2024 Top Workplaces Regional winner, receiving the award for the second consecutive year. Trew’s team includes a wide range of roles that work together to create client value and deliver on-time projects. Roles within the business include solutions development, project management, software, engineering, manufacturing, installation, sales, marketing, and other general corporate services. “Trew has an environment where team members consistently go the extra mile to deliver exceptional service to our customers,” said Alfred Rebello Trew Chief Executive Officer. We are thankful that our people who form the bedrock of the company and who continually strive for excellence have awarded this honor.” The Top Workplace Award is based entirely on employee feedback gathered by a third-party survey administered by Energage, LLC. The confidential survey uniquely measures fifteen culture drivers that are critical to success of any organization such as alignment, execution, and connection. The award highlights organizations that stood out among their peers, demonstrating a commitment to employee satisfaction, organizational excellence, and building a thriving workplace culture. Trew won 2024 Cultural Excellence awards in the following categories: • Innovation • Purpose & Values • Leadership • Work-Life Flexibility • Compensation & Benefits Eric Rubino, Energage CEO, commented, “The Top Workplaces award is a badge of honor and something companies should be very proud to showcase. The people-first cultures they have built and nurtured will set them apart in a highly competitive market. These organizations represent the best of the best.” Trew was formed in January 2019 by warehouse automation veterans and has quickly become a solutions leader in the industry. The company is anchored in Cincinnati, with a diverse hybrid workforce and additional facilities in Milwaukee, Wisconsin and the greater Toronto, Canada area.
Crown SP 1500 Series delivers visibility that enhances safety
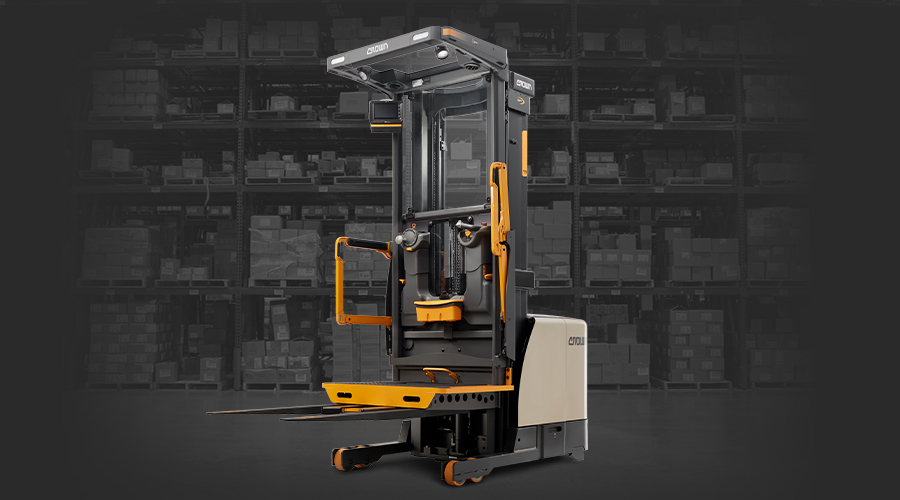
Crown Equipment Corporation has announced the availability of the Crown SP 1500 Series order picker. The lift truck introduces innovative design features, such as the industry’s first mid-platform window and industry-leading lift and lower speeds, that enhance operator safety and make order picking easier and more efficient. Visibility is a foundation of operator confidence and productivity and the Crown SP 1500 Series provides exceptional views even when fully elevated. The industry’s first mid-platform window, centered between the operator controls, provides a view of the floor below when the platform is raised. This is combined with a large upper window that offers a wide view of pedestrians, objects and other equipment, as well as openings in the center and on each side of the floorboard to provide clear views directly below. An optional large panoramic window above the operator provides clear sightlines to pick locations and overhead obstructions, resulting in clear all-around visibility for the operator. “Every element of the Crown SP 1500 Series is designed to work together with the operator to optimize the order picking process. By enabling seamless interaction between operator and lift truck, the lift truck’s design helps boost safety, efficiency and productivity,” said Chris Grote, senior product manager, Crown Equipment. “We do this by providing unmatched visibility at height, industry-leading lift and lower speeds, and intuitive blending of truck functions within a customizable, operator-centric compartment we call Op-Zone.” The SP 1500 Series also offers exceptional stability at height and outstanding lift and lower performance to complete tasks quickly and confidently. The lift truck is capable of traveling at 7.5 mph, with standard lift speeds of 71 fpm for the 24v, 115 for the 36v and 140 for the 48v. The Xpress Lower™ option raises lowering speeds from 80 fpm up to 205 fpm for the 36v and 48v lift truck options, and 110 fpm for the 24v lift truck. Op-Zone, the operator-centric compartment, can be customized to meet individual operator preferences and application requirements and to boost operational efficiency. Newly designed ergonomic controls allow for seamless blending of truck functions combined with an optional capability to provide independent height adjustability so operators can adjust control height to their individual preferences. Together with the dual-position tiller knob, they allow operators the flexibility to work from an optimal position throughout their shifts. The compartment also can be fitted with a variety of Work Assist accessories to support operators as they tackle a wide variety of tasks in a dynamic order picking environment. An underlying force supporting the Crown SP 1500 Series’ operator-centric experience is the Gena® operating system. This transformational lift truck operating system delivers a customizable, interactive, data-rich user experience to enhance supply chain performance. The intuitive system provides users with real-time, actionable data relevant to the task at hand, including safety reminders accompanied by illustrations and widgets that display key operating metrics like battery state of charge, hour meter and height indicator. “Crown helps its customers understand that implementing an integrated, holistic approach to lift truck safety is key to creating and maintaining a culture where safety is top of mind,” said Grote. “As the Crown SP 1500 Series demonstrates, equipment design is a significant component of this comprehensive approach.” The Crown SP 1500 Series includes Crown’s patented OnTrac® anti-slip traction control system that reduces slippage or wheelspin whenever the lift truck is accelerating, plugging or braking on wet or dusty floors. Customized energy solutions for the order picker are available, based on a range of V-Force® lead acid or lithium-ion batteries and chargers, to meet customer application and infrastructure requirements.
U.S. Rail Traffic report for the week ending May 18, 2024
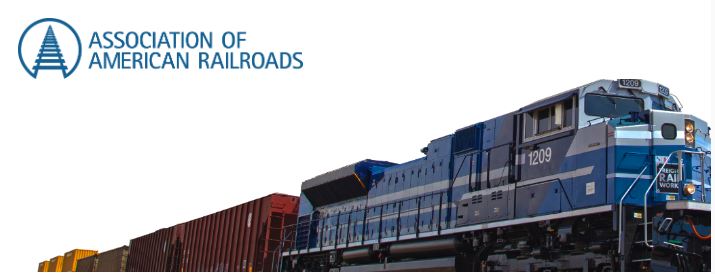
The Association of American Railroads (AAR) has reported U.S. rail traffic for the week ending May 18, 2024. For this week, total U.S. weekly rail traffic was 474,886 carloads and intermodal units, up 0.9 percent compared with the same week last year. Total carloads for the week ending May 18 were 214,092 carloads, down 4.8 percent compared with the same week in 2023, while U.S. weekly intermodal volume was 260,794 containers and trailers, up 6.2 percent compared to 2023. Five of the 10 carload commodity groups posted an increase compared with the same week in 2023. They included grain, up 2,004 carloads, to 19,917; petroleum and petroleum products, up 1,007 carloads, to 10,330; and chemicals, up 714 carloads, to 32,294. Commodity groups that posted decreases compared with the same week in 2023 included coal, down 12,113 carloads, to 50,520; metallic ores and metals, down 1,872 carloads, to 20,570; and nonmetallic minerals, down 1,137 carloads, to 31,798. For the first 20 weeks of 2024, U.S. railroads reported a cumulative volume of 4,259,530 carloads, down 4.9 percent from the same point last year; and 5,057,135 intermodal units, up 8.5 percent from last year. Total combined U.S. traffic for the first 20 weeks of 2024 was 9,316,665 carloads and intermodal units, an increase of 2.0 percent compared to last year. North American rail volume for the week ending May 18, 2024, on 10 reporting U.S., Canadian, and Mexican railroads totaled 323,396 carloads, down 1.4 percent compared with the same week last year, and 346,036 intermodal units, up 4.5 percent compared with last year. Total combined weekly rail traffic in North America was 669,432 carloads and intermodal units, up 1.6 percent. North American rail volume for the first 20 weeks of 2024 was 13,150,619 carloads and intermodal units, up 2.1 percent compared with 2023. Canadian railroads reported 92,669 carloads for the week, up 5.7 percent, and 72,537 intermodal units, down 2.6 percent compared with the same week in 2023. For the first 20 weeks of 2024, Canadian railroads reported a cumulative rail traffic volume of 3,229,985 carloads, containers, and trailers, up 0.9 percent. Mexican railroads reported 16,635 carloads for the week, up 7.9 percent compared with the same week last year, and 12,705 intermodal units, up 15.8 percent. Cumulative volume on Mexican railroads for the first 20 weeks of 2024 was 603,969 carloads and intermodal containers and trailers, up 10.9 percent from the same point last year. View reports here
Episode 488: Taking a Collaborative Approach with Rocrich AGV Solutions
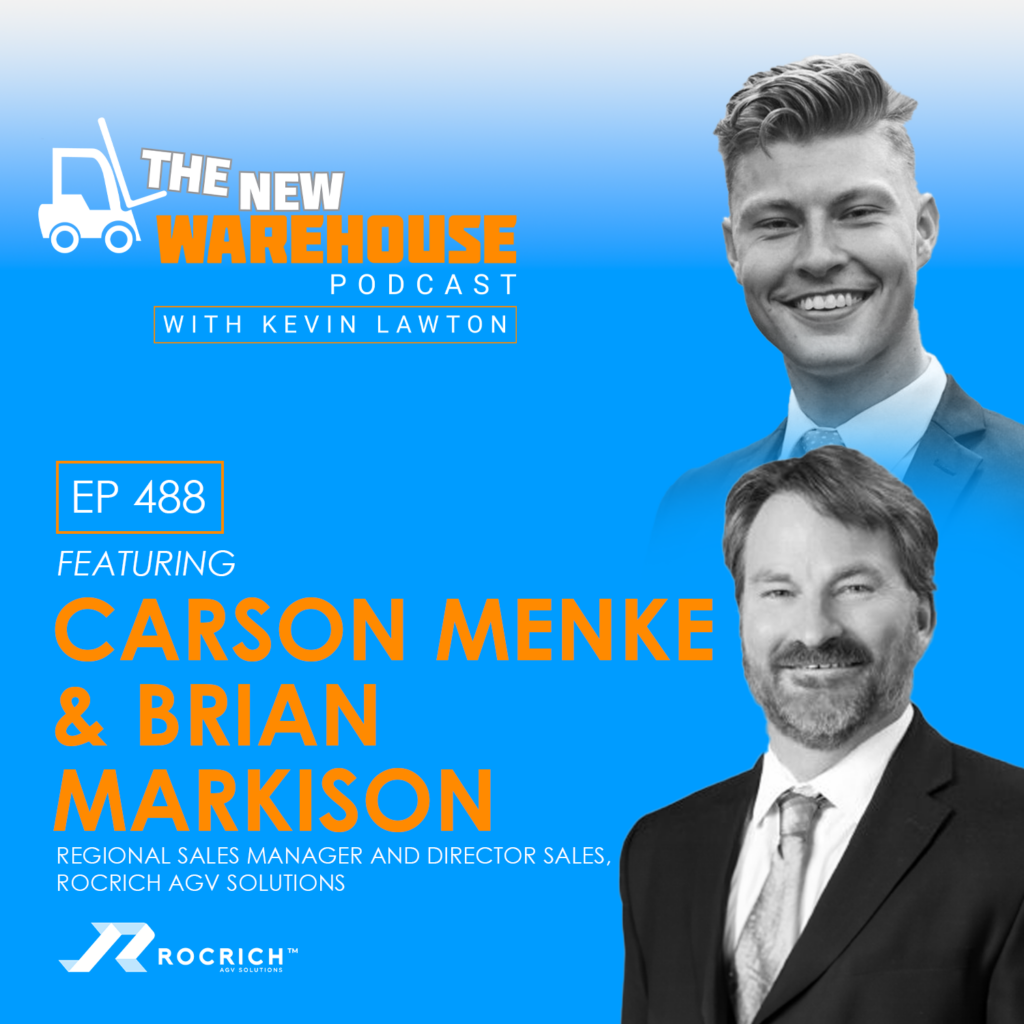
The New Warehouse Podcast welcomes Carson Menke, Regional Sales Manager, and Brian Markison, Director of Sales, from Rocrich AGV Solutions. The episode delves into the unique collaboration between Jungheinrich and Rocla in North America, the extensive automation solutions offered by Rocrich, and the broader implications of automation in the warehousing industry. Be sure to tune to hear Carson and Brian share their expertise on the evolution and future of warehouse automation. Rocrich AGV Solutions: Bridging Proven Brands Rocrich AGV Solutions stands out by combining the strengths of two established brands, Jungheinrich and Rocla. Carson explains, “Rocrich is the North American sales implementation and engineering of those two product lines.” He adds, “any challenge that approaches us that a customer may be having, we can put them first and really provide a solution that works for them.” This strategic combination allows Rocrich to offer a comprehensive range of solutions tailored to meet diverse customer needs. Brian Markison adds, “It allows us to blend those and handle more use cases and a single source from that perspective.” By leveraging the robust capabilities of both brands, Rocrich provides flexible and scalable automation solutions. Tailored Automation Solutions for Varied Challenges Rather than focusing solely on product specifications, Rocrich adopts a solutions-oriented approach to automation. Carson emphasizes, “When you’re looking at AGVs, it’s a little bit different. You wanna look at it from a solutions approach.” This means understanding the specific challenges faced by customers and providing customized solutions. Rocrich’s offerings range from standardized AGVs based on existing forklift models to more specialized units for niche applications. As Carson explains, “We have a very large offering under the two brands,” ensuring that they can meet the unique needs of each customer. Efficiency and Safety in Warehousing The discussion highlights the critical role of automation in addressing labor shortages and improving operational efficiency. Brian notes, “One of the biggest challenges that warehouses are facing today is just having enough labor on staff.” Automation not only helps mitigate labor shortages but also enhances safety and reduces costs. Carson adds, “Efficiency and dependability are big reasons why people are moving towards automation.” By automating repetitive and dangerous tasks, warehouses can improve safety and productivity, allowing human workers to focus on more value-added activities. Key Takeaways Strategic Brand Combination: Rocrich leverages the strengths of Jungheinrich and Rocla to offer comprehensive automation solutions. Solutions-Oriented Approach: Focus on addressing specific customer challenges rather than just product specifications. Labor and Efficiency Benefits: Automation helps mitigate labor shortages, improve safety, and enhance operational efficiency. The New Warehouse Podcast Episode 488: Taking a Collaborative Approach with Rocrich AGV Solutions
Longtime ASSP member earns Prevention through Design Award
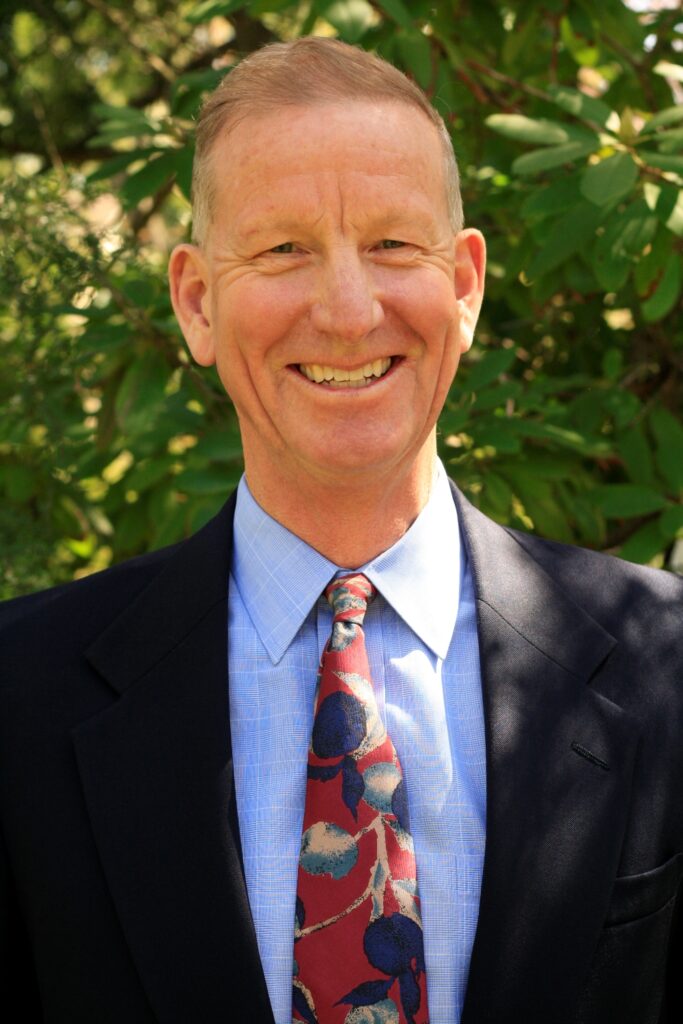
Bruce Main, P.E., CSP, a longtime member of the American Society of Safety Professionals (ASSP), earns the 2024 Prevention through Design (PtD) Award. The honor is presented to those who demonstrate outstanding leadership in reducing workplace hazards through design methods. The award is a collective effort of ASSP, the National Institute for Occupational Safety and Health (NIOSH), the National Safety Council (NSC) and the American Industrial Hygiene Association (AIHA). Main, president of Design Safety Engineering in Ann Arbor, MI, was recognized for his decades of proactive workplace safety contributions. He was a founding member of NSC’s Institute for Safety Through Design in 1995 and first-ever vice chair of the ANSI/ASSP Z590.3 Prevention through Design standard committee in 2011. An ASSP member since 1992, Main currently chairs the Z244 standards committee that establishes requirements for controlling hazardous energy through lockout/tagout measures and alternative methods. “Assessing workplace environments and designing out hazards is an innovative and long-term approach to business sustainability and preventing worker injuries, illnesses and fatalities,” said ASSP President-Elect Pam Walaski, CSP, FASSP, who spoke at the awards ceremony at the AIHA Connect conference in Columbus, OH. “Bruce has trained thousands of engineers and professionals in risk assessment and has elevated prevention through design principles and practical applications.” Main’s safety and health experience covers many technical areas, including mechanical design, machine guarding, control of hazardous energy, accident reconstruction and product safety evaluation. He is a consultant, researcher, author and highly sought-after instructor and speaker at universities and industry conferences. Main earned ASSP’s Thomas F. Bresnahan Standards Medal in 2015 for his extensive work in developing and advocating voluntary national consensus standards in occupational safety and health. “Bruce has been instrumental in keeping prevention through design principles in the forefront of safety efforts for more than 35 years,” Walaski said. “His enthusiastic approach to risk mitigation and worker safety has saved countless lives across many industries.” The annual PtD Award honors individuals, teams, businesses and other organizations that have eliminated or reduced hazards through designs or redesigns – or have contributed to the body of knowledge that enables PtD solutions. It reflects how proactive efforts can target hazards to safeguard people, property and the environment.
LEIBINGER wins the “German Innovation Award” for IQJET and is also recognized as “Innovator of the Year”
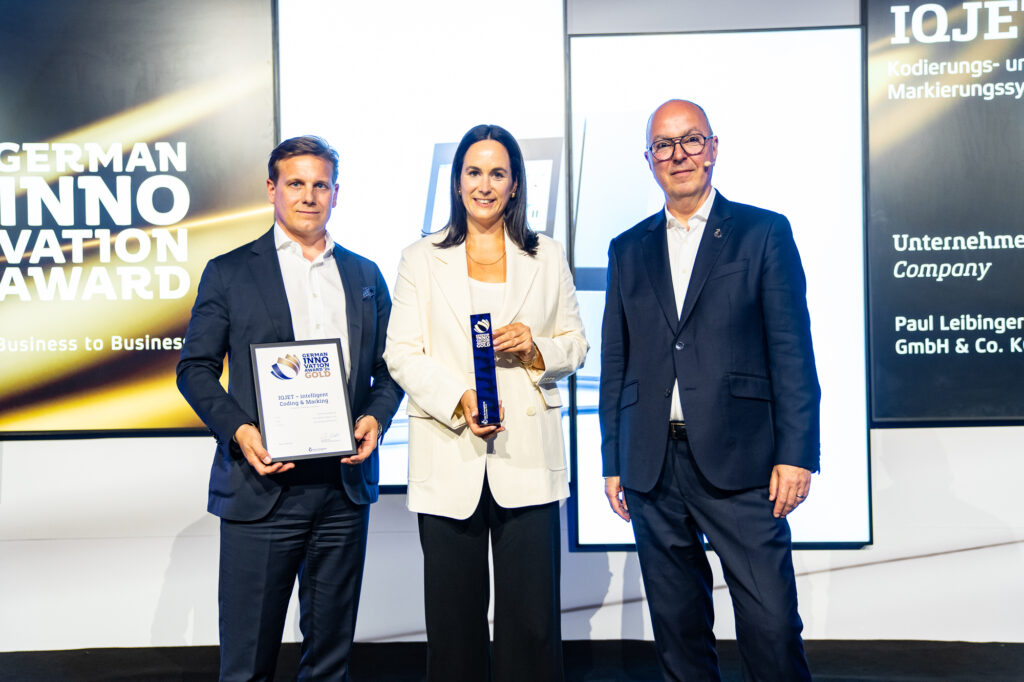
The German Design Council has honored LEIBINGER’s innovative, high-performance industrial printer, IQJET, with the Gold German Innovation Award on May 14th in Berlin. Additionally, the marking system specialist was named Innovator of the Year 2024. The interdisciplinary expert jury of the German Design Council awarded IQJET in the category “Excellence in Business to Business: Machines & Engineering” with the Gold German Innovation Award. The award is based on criteria such as sustainability, quality, and economic efficiency for outstanding products, projects, and pioneering achievements. About 300 guests from politics, business, and media attended the festive event at the Berlin Futurium. Revolutionary industrial printer IQJET Wherever production and packaging occur, marking plays a crucial role. Printed information ensures reliable compliance with legal requirements, enables seamless traceability along the entire value chain, and creates transparency as well as user interaction opportunities for consumers. With the new industrial printer, IQJET, LEIBINGER revolutionizes continuous inkjet printing (CIJ) and offers users from numerous industries an optimal solution for marking their products. IQJET, for instance, prints texts, logos, and codes on a variety of surfaces such as metal, plastic, glass, and paper. The device guarantees high performance, exceptional print quality, and efficiency with reliable continuous operation and no need for cleaning. Users benefit from the unique “Plug&Print” performance, easy operation, and five years of maintenance-free operation. Compared to conventional printers, IQJET reduces operating costs by up to 30 percent. Furthermore, companies optimize their ecological footprint through the low consumption of energy, ink, and solvents. Christina Leibinger, CEO of LEIBINGER, and COO Jan van het Reve personally accepted the award. Leibinger summarizes, “We have set a goal to continuously optimize industrial CIJ printing and take a leading role as a provider of innovative coding & marking technology. We are proud that our innovative strength has also impressed the jury.” Van het Reve adds, “Our developments are always focused on benefiting the customer, meaning that with the LEIBINGER printers we aim to make a significant contribution to operating cost optimization, sustainability, and efficiency in manufacturing and packaging lines worldwide.” LEIBINGER also awarded as a company The nomination committee also recognized LEIBINGER as Innovator of the Year 2024. Renowned business, science, and media experts consider LEIBINGER to be the pioneer in its field. The award is the largest audience award in German business, honoring companies of every size and industry as well as innovative ideas from all areas of business. Over 70,000 entrepreneurs, CEOs, and other business enthusiasts also choose the winners of the audience awards online in various categories.
Orion announced Kelly Watterworth as East Coast Regional Sales Manager
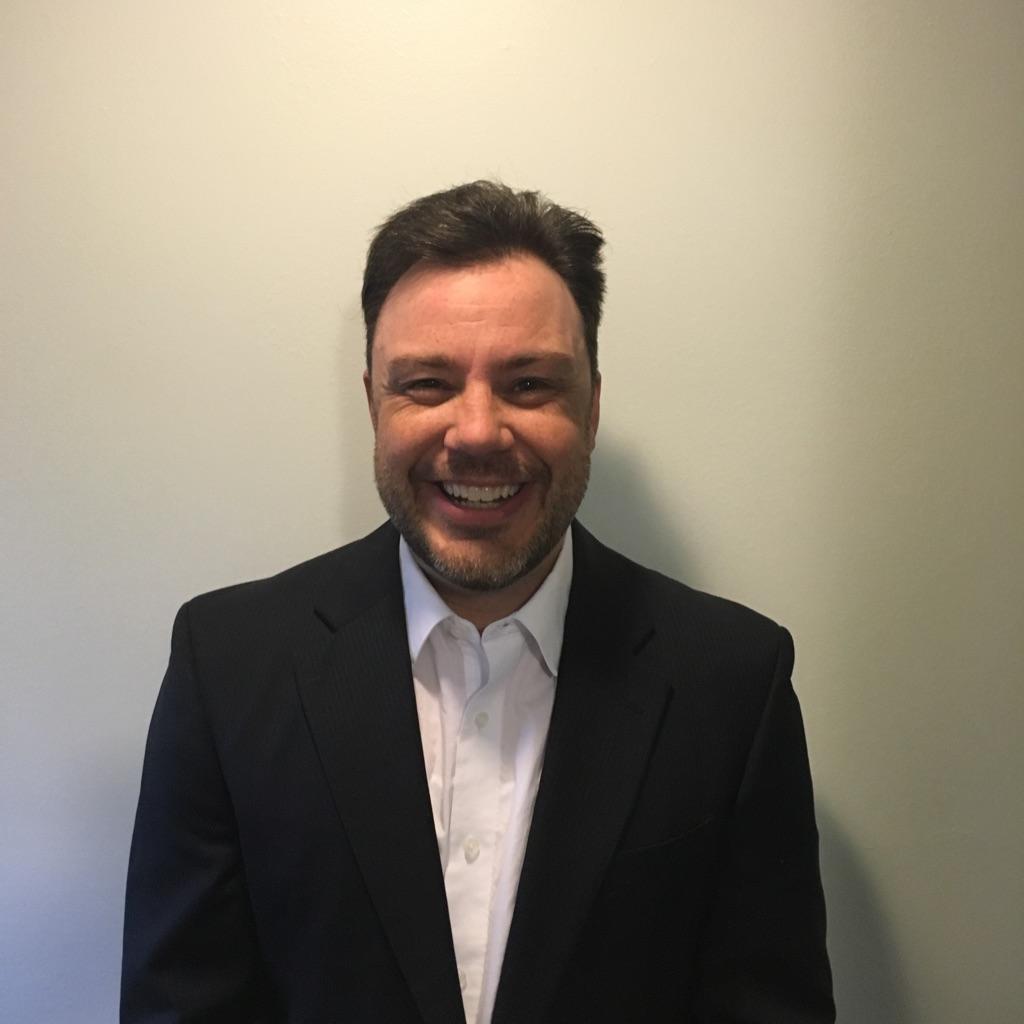
In his new role, Watterworth will be working directly with Orion channel partners to build relationships, train staff and provide support to the sales team to grow the company’s stretch-wrapping machinery. “I’m excited to once again build relationships with local channel partners as I’m transferring from a National Sales position where I worked mainly with direct sales accounts, integrators, and OEMs,” Watterworth said. Watterworth has held various managerial and sales roles with Orion since 2016. He has a bachelor’s degree from Michigan State University.
Mitsubishi Electric Automation, Inc. hosts its first Robot Roadshow event in Ohio
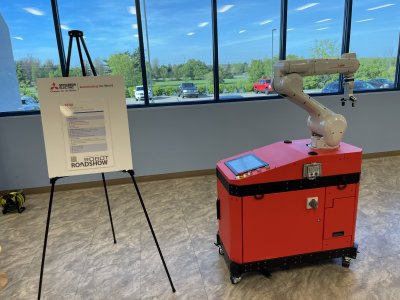
The Robot Roadshow allows attendees eager to learn, experience, or purchase automation to have hands-on interactions with Mitsubishi Electric Automation’s latest robots and robotic innovations. Mitsubishi Electric Automation, Inc. hosted its first-ever Robot Roadshow in late April 2024 to bring newly launched robots and robotic solutions to the Midwest. The two-day event, held at the Mitsubishi Electric Automotive America office in Mason, Ohio, brought in over 75 OEMs, System Integrators, Distributors, End-Users, engineers, education partners, and Mitsubishi Electric Automation channel partners. At the event, several demonstrations showcased the customizability of our LoadMate™ Plus engineered solution based on the robot series and size necessary for an application. Other demonstrations included machine tending and standard base options for Mitsubishi Electric Automation’s newest robotic-engineered solution, ARIA (Automated Robotic Industrial Assistant). Mitsubishi Electric Automation presented its newly released large robots, the RV-12 and RV-80, which created much excitement for attendees. In support of this event, ICONICS, a group company of Mitsubishi Electric, demonstrated real-time data and analytics visualization for robotic applications. “Thank you to all the customers who attended this event to learn more about our robotic automation and digital transformation offerings. Our demonstrations of our newly released modular ARIA platforms and robots were all a huge hit. I extend our gratitude to Mitsubishi Electric Automotive America for allowing us to host this event at your facility as well as the ICONICS and Mitsubishi Electric Automation team for making this show a great success. Stay tuned for more events from us!” said Britt Davis, regional sales manager (central) at Mitsubishi Electric Automation.