Talon trailer restraint provides safety for loading docks
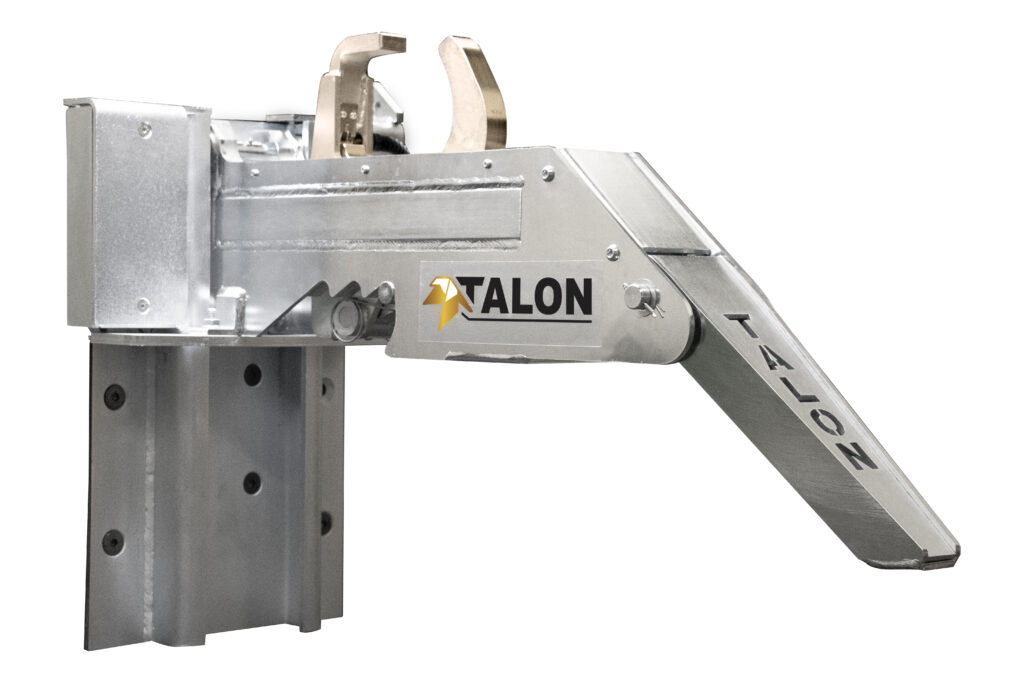
Innovative design delivers an all-new approach to safer, more effective trailer loading and unloading. 4Front Engineered Solutions has announced the introduction of the Talon™ trailer restraint, the company’s newest innovation in loading dock safety equipment. Offered under both the Kelley and Serco brands, Talon is a next-generation approach to securing docked trucks, delivering great improvements in safe and effective trailer loading and unloading. Due to pending National Highway Traffic Safety Administration (NHTSA) regulations affecting the design of trailer rear impact guard (RIG) bars, many trailer restraints are no longer compatible or are simply less effective at restraining and releasing trailers. Newer-style five-sided RIG bars with pentagonal cross-sections or tilted configurations require a different approach to trailer restraint design. To keep redesigned RIG bars more secure during loading and unloading trailers, the Talon trailer restraint’s additional upper hook provides true four-sided RIG bar capture, which is much more effective than two or three-sided capture. The four-sided capture also prevents the RIG bar from hopping over the hook and releasing the trailer from the dock. Talon is unique in that it accomplishes all of this as a powered restraint that does not use powered hydraulics or a motor, resulting in lower maintenance costs and a lower total cost of ownership. “The addition of Talon really cements Kelley and Serco as the leaders in loading dock safety solutions. Its clever design means that it works better with a wider range of trailers, cutting down on complexity while making it the most advanced trailer restraint system out there,” said Ryan Talbot, Vice President of Sales and Marketing at 4Front Engineered Solutions. Instead of a trailer restraint’s hook contacting only two or three sides of a RIG bar, and much like the talons on a bird of prey, the Talon trailer restraint makes complete contact with and surrounds all five surfaces of the pentagonal RIG bar while also eliminating restraint release failure, ensuring the trailer can be released at the appropriate time, thanks to a proprietary locking mechanism. Many trailer restraints have excessive play (running room) between the restraint and RIG bar during forklift movement. To eliminate running room issues, as a trailer moves toward the loading dock bumpers and engages with the Talon trailer restraint, the three-position slide lock limits trailer movement for a more stable loading environment. External red and green LED indicators inform the driver whether the restraint is still engaged or disengaged so the trailer can safely depart.
Menasha Corporation awards $6 Million in grants to nonprofit organizations in its 175th anniversary year
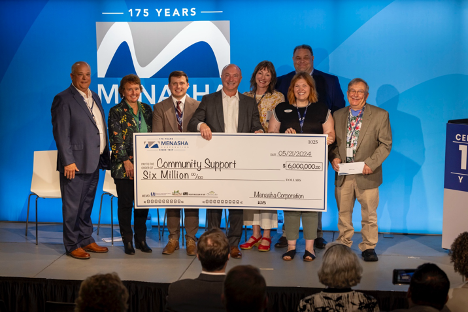
Menasha and Neenah Mayors declare May 21st as ‘Menasha Corporation Day’ in honor of ongoing community support In celebration of its 175th anniversary, Menasha Corporation, a sustainable corrugated and reusable plastic packaging manufacturer and supply chain services provider for over 2,500 leading global brands in North America and the parent company of ORBIS Corporation, announced it will grant $6 million to nonprofits in 2024, of which nearly $4 million will be donated to organizations in the Fox Valley where Menasha Corporation was founded. Chris Drees, Menasha Corporation President and CEO, announced the Fox Valley grant recipients on May 21, 2024, which included declarations by Menasha Mayor Austin Hammond and Neenah Mayor Jane Lang to proclaim May 21 as ‘Menasha Corporation Day’ for both cities. “Giving back is deeply rooted in Menasha Corporation’s legacy. It’s a philosophy that began with the extraordinary generosity of our founder, Elisha D. Smith,” Drees said. “Today, a fundamental tenet of our shareholders and our company is to continue that tradition of philanthropy. In our 175th year of business, we couldn’t think of a more fitting and worthy celebratory activity than to honor our milestone by supporting our community.” Through the company’s philanthropic arm, Menasha Corporation Foundation, the following Fox Valley organizations were chosen as grant recipients: Christine Ann Domestic Abuse Services Elisha D. Smith Public Library Trout Museum of Art Jefferson Park in Menasha The four grant recipients support causes that fall in the following four areas where Menasha Corporation Foundation focuses its support: Safe & Healthy Citizens, An Educated Society, Community Betterment, and Environmental Sustainability. The remaining donation dollars will be distributed across all of Menasha Corporation’s locations in the United States and include $350,000 in honor of the company’s anniversary and approximately $2 million in typical annual donations. “We are incredibly honored to be recognized by both cities of Menasha and Neenah with the proclamations presented today,” Drees said. “Our roots are here in the Fox Valley. Our partnership with Menasha and Neenah enriches our community. These proclamations demonstrate our commitment to supporting these two communities for years to come.” Awarded Manufacturer of the Year in 2024 by Wisconsin Manufacturers & Commerce, Menasha Corporation is the third oldest continuously operating company in Wisconsin, and the 76th oldest family business in America. Today, it employs more than 7,800 people in 108 facilities throughout North America and Europe. Headquartered in Neenah, Menasha Corporation employs more than 1,500 employees in 12 facilities throughout the state of Wisconsin.
CP&A advises on container crane procurement peer reviews
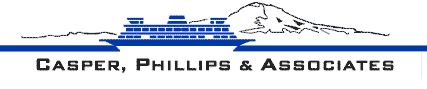
Casper, Phillips & Associates Inc. (CP&A) has delivered a presentation to port authorities titled, ‘Peer Review of Container Cranes’, to assist in future procurement processes. CP&A offers a wide variety of services, including specification, design, manufacturing review, modification, and accident investigation; and it is well-positioned to remind terminal operators and fellow stakeholders of the risks involved with container crane procurement. Including transport and offloading in the peer review scope is a good way to manage some of these risks — but that’s just the start. Richard Phillips, mechanical engineer at CP&A, said: “The procurement process for container cranes is somewhat unique and presents many challenges. Unfortunately, some procurement decision makers believe buying container cranes is the same as acquiring any other piece of equipment, such as a forklift or a company van.” As should be unanimously accepted by crane manufacturers, a peer is someone with approximately equal qualifications to the design team. While there is no universal set of criteria as to what makes an engineer a peer, a good starting point is professional licensure and relevant design experience in the appropriate disciplines. The team should have an expert in the prevailing hazards such as high wind, seismic, or other location dependent hazards. A peer review is when a neutral third party checks the design for compliance with the performance specification. A performance specification states what the crane needs to do — rated load, hoist and travel speeds, operating wind speed, etc. — but it does not specify how the crane manufacturer needs to meet the specification. Importantly, a design review is about compliance; it is not about the design reviewer’s preference for how he or she would have designed the crane. There is a level of professionalism expected for design reviews. While there will always be debate, comments that are not backed up by analysis, specification, or code requirements should be avoided. Phillips said: “It’s a big red flag if a large number of comments are generated without supporting calculations or citations of specification requirements. It’s not constructive for the designer to have to refute a large volume of comments that may not be contractually required or may be speculation since they are not supported by calculations. The reviewer should be performing enough analysis to back up their comments.” Custom port equipment Container cranes are custom designed to meet the unique requirements of each port. Some of these requirements may include being in a hurricane or earthquake zone; exposure to extreme temperatures; or proximity to other geological hazards. Sometimes a container terminal is located near an airport, or a crane may need to pass under a bridge during delivery, resulting in height restrictions. A naval architect provides the sea states and predicted voyage motions for the designers to analyze and brace the crane accordingly. The crane manufacturer owns the cranes until handover. Some crane manufacturers own their own fleet; others subcontract this work. It can be beneficial for the design reviewer to check the voyage bracing prior to shipping. There are other operational considerations, such as where hatch covers are stored; the use of dual trollies; and how many containers the crane can lift: single 40 ft., twin 20 ft., tandem 40 ft., quad 20 ft., etc. All things considered the planning phase has great variance. Sometimes it starts at the wharf design stage, other times the wharf is already designed, and existing cranes are being replaced. Depending on the level of customization, once a crane is awarded, it can be up to three years before delivery. Phillips, who himself conducts peer reviews of contractors’ crane designs, including some of the largest container cranes in the world, pointed to CP&A’s crane base anti-seismic isolation system (BASIS), which is built on nonlinear time history analysis (NLTHA) and can protect a crane’s main structure from damage even in contingency level earthquakes. “We are always improving our software,” said Phillips. “Our crane analysis software can be thought of as a custom workbench specifically made for cranes. There is a much larger market for buildings and bridge design, so the commercial software packages tend to focus on larger markets such as those [see below]. That led CP&A to create our own crane code-checking software. One example is that we have incorporated wind tunnel test data into our pre-processor, which develops the wind load forces on a crane. Obviously, a commercial building will not have integrated wind tunnel data for container cranes.” Cranes are significant structures Interestingly, due to the geological and environmental hazards, cranes should be treated more like bridges and skyscrapers instead of mass produced cars and airplanes. However, for cars and airplanes, there are crash tests and full-scale testing, which is impractical with cranes. ASCE 7-16 1.3.1.3.4 covers minimum design loads and associated criteria for buildings and other structures; this particular clause covers peer reviews for significant structures. Phillips added: “When you start thinking about how bridges, stadiums, and skyscrapers are designed it starts to become clear. For significant structures the [AISC 7] code requires a peer review. Are cranes significant structures? In our opinion they are; however, it is up to the local jurisdiction to make that decision.” Even at the time of going to press, CP&A was wrapping up peer review and procurement assistant projects related to rubber-tired gantry, rail-mounted gantry, and ship-to-shore cranes. Are your procurement processes for these hulking container cranes up to standard?
Motion enters agreement to purchase electrical/automation company
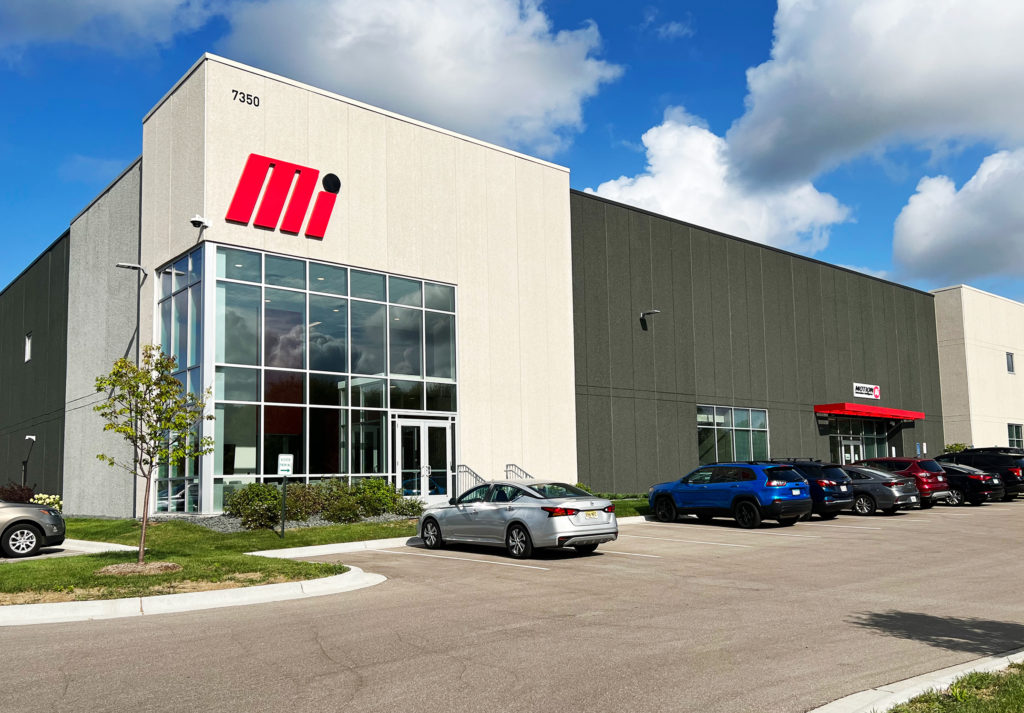
Motion’s automation market to expand in the Mid-Atlantic Motion Industries, Inc. has signed a definitive purchase agreement to acquire Allied Circuits, an electrical and automation firm. The transaction is expected to close later this month, subject to customary closing conditions. Located in Buffalo, New York, Allied Circuits designs, manufactures and services industrial control panels, electro-mechanical assemblies, robotic automation and integrated solutions. Founded in 1987, the company serves customers in the Western and Upstate New York markets and into Ontario, Canada, due to its proximity to the border. End markets include aerospace, automotive, filtration, fluid systems & plumbing, food & beverage, oil & gas, pharmaceutical, process industries, semiconductor and water & wastewater treatment facilities. The company will join Motion’s business unit, Motion Automation Intelligence (Motion Ai). The addition of Allied Circuits will provide an exceptional workforce of highly skilled teammates, ATEX certification capabilities and over 20,000 square feet of additional production space to bolster Motion Ai’s existing presence in the area. Motion Ai’s total region size will expand to over 100,000 square feet of production space and 150 people dedicated to serving existing and new customers. Chris Scinta, Partner at Allied Circuits, said, “It’s a great match—including the business culture and core values—and we’re very excited about our customers’ expanded access to even more products and services. Motion is an industry leader, and we are pleased to integrate employee talents and contribute to the company’s growth.” “Our customers are growing, and we’re committed to growing with them,” said James Howe, President of Motion. “By combining our engineering teams, we can leverage highly experienced technical resources needed to design, program, and support increasing automation needs within the region. This strategic acquisition will create new opportunities for our customers, teammates, and supplier partners.”
Diana Mueller joins KPI Solutions as Senior Account Executive
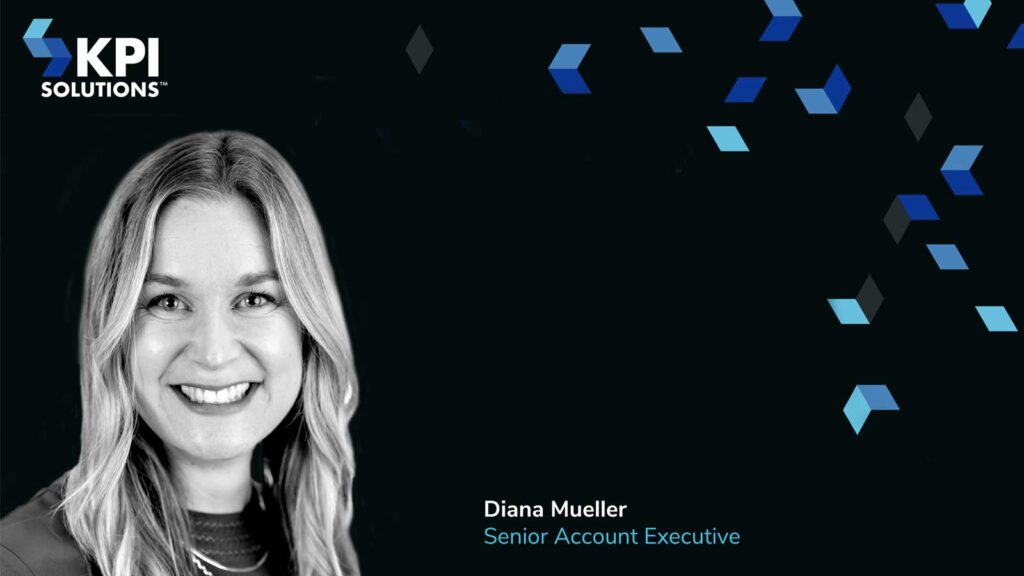
With 15+ years of experience in the logistics and supply chain industry, she specializes in architecting transformational distribution solutions that deliver business results KPI Solutions (KPI) has announced that Diana Mueller has joined the company as Senior Account Executive. In this role, Diana will partner with clients to understand their distribution objectives, and then enable and facilitate value-based strategic initiatives that support growth and build resilience. She brings particularly deep experience in developing omnichannel solutions for the retail, apparel, and footwear industries. “I’m thrilled to join the KPI Solutions sales team to help our clients solve complex supply chain challenges and navigate the many alternatives for warehouse design and automation,“ said Diana. “My background in large-scale, omnichannel distribution projects allows me to offer a fresh perspective to clients as we build a customized, total solution that boosts productivity and enables agility.” “Diana’s experience in business case rationalization and supply chain transformation will bring value to our clients as we continue to couple innovative engineering with leading automation technologies,” said Roger Counihan, Senior Vice President of Sales. “KPI’s clients will benefit from her focus on exceeding their business goals by leveraging creative designs with world-class automation and robotics, powered by intelligent software.” Diana joins KPI Solutions from Fortna, where she was an Account Executive. Prior experience includes working as a Solutions Manager and Transportation Analyst at OHL (now Geodis). She holds a Bachelor of Business Administration, Logistics, Materials, and Supply Chain Management degree from Auburn University and resides in Florida.
Orbital Stretch Wrapper manufacturer introduces upgraded safety control package
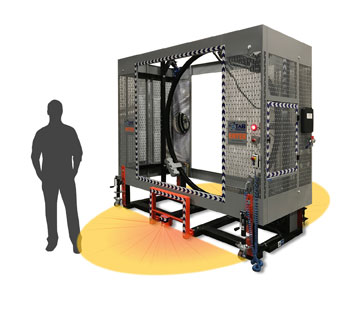
New package adds automated safety scanners to TAB Wrapper Tornado Orbital wrapper manufacturer TAB Industries, LLC, has introduced an upgraded safety control package. Available as an option on the company’s TAB Wrapper Tornado Smart Controls orbital wrapping machines, the new upgraded safety control package adds the company’s automated Safety Scanners, bumper guards, and accessories at a discounted price versus the individual add-ons. The Safety Scanners create an invisible field emanating in a 180-degree arc from both the front and back of the machine that allows forklifts to pass but automatically stops the wrapping machine if a worker enters the field. The scanners are set within the bumper guards, which protect the stretch wrapper from accidental contact with lift trucks. Available on TAB Wrapper Tornado Smart Controls models with the standard 80-inch, 100-inch, and 115-inch wrapping rings, the Upgraded Safety Control Package accommodates 480V electrical service and may be retrofit onto Smart Controls wrapping machines in the field. The patented smart controls pallet wrapping machines automatically apply stretch wrap 360 degrees around and under a pallet and load to create a stable, secure, unitized load in 30 seconds or less without boxes, crates, or banding. The stretch wrap machines are designed and manufactured at the company’s Reading, Pa. headquarters and delivered with the worker safety upgrade pre-installed, tested, and ready to operate. A full warranty is included.
MHS Lift named Top Workplace for Fifth Consecutive Year
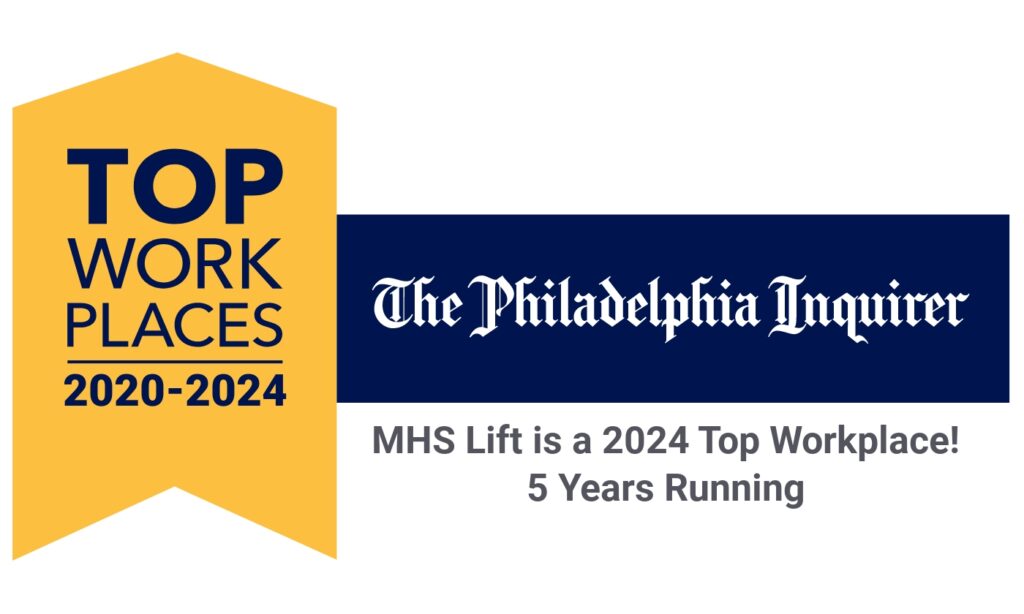
For the fifth consecutive year, MHS Lift, Inc. has been honored as one of the 2024 Top Workplaces in the Greater Philadelphia area by The Philadelphia Inquirer. For the last 15 years, The Philadelphia Inquirer has partnered with Exton-based company Energage to rank the region’s Top Workplaces through a scientific survey of employees who rate their workplace culture. Any organization with at least 50 employees based in the Delaware Valley area is eligible to participate. MHS Lift was additionally honored with Energage’s 2024 National Culture Excellence Award, a national recognition for Top Workplaces. The workplaces are divided into groups based on the number of employees and calculated scores. MHS Lift was honored for its excellence in the categories of leadership, innovation, compensation and benefits, purpose and values, and work-life flexibility. “We are very proud of the work environment that we’ve built here at MHS Lift,” said Andy Levin, co-president, MHS Lift. “We owe this award entirely to the hard work and outstanding performance of our talented employees, as well as our dedicated customers and associates.” “Each year, we strive to make MHS Lift an even greater place to work, emphasizing our company’s competitive benefits and salaries, while also staying committed to providing our employees with ongoing training and advancement opportunities,” said Brett Levin, co-president, MHS Lift. “Our goal is to consistently recruit highly skilled and smart people to join our growing workforce.” Committed to fostering a thriving company culture, MHS Lift has taken “having fun at work” to the next level with its one-of-a-kind Fun Committee. This group is dedicated to ensuring that MHS Lift employees enjoy their time on the job. The Fun Committee meets monthly to organize parties, fundraisers and community events, as well as brainstorm new and exciting ways to make the MHS Lift social scene vibrant and fun.
Hy-Brid Lifts announced Director of Sales for South-Central USA
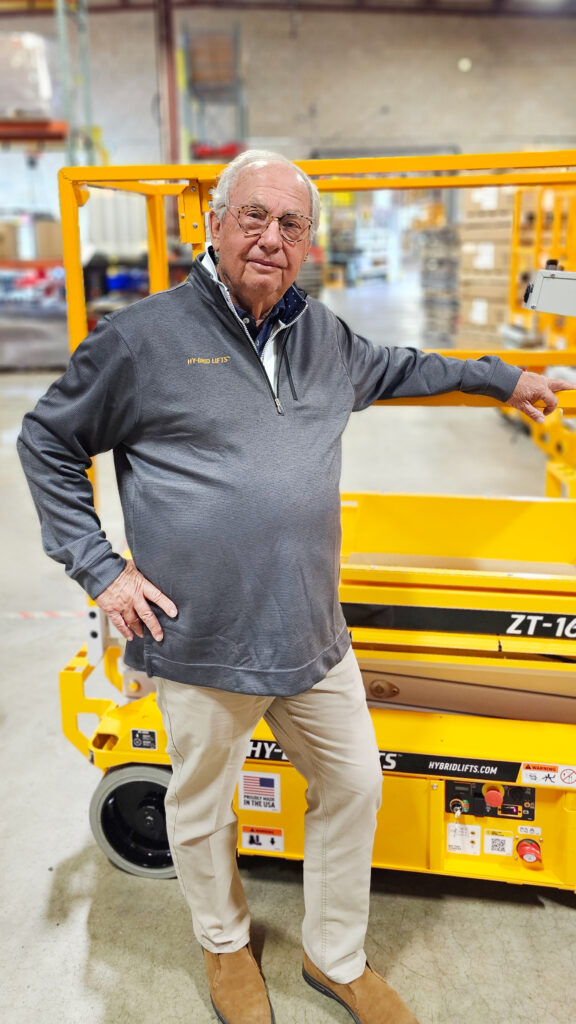
Hy-Brid Lifts has announced Gary Coke as director of sales covering the south-central United States. Coke’s responsibilities include providing customer support as well as continuing the growth and channel development of the Hy-Brid Lifts line of low-level scissor lifts. “I am excited to join this team and look forward to the opportunity to work with past and future customers. Coming from equipment manufacturing, I understand the importance of quality equipment and customer service backed by a solid service department,” said Coke. “After meeting the Hy-Brid Lifts team and seeing all of the new products in the pipeline, it’s no surprise that this company is continuing to grow, and I look forward to being a part of that growth.” Coke brings 19 years of industry experience to his new role, largely derived from his time in equipment manufacturing with SkyJack. He spent a majority of his career in sales with a strong emphasis on customer relationships and going above and beyond for every customer. “The entire Hy-Brid Lifts team is excited to have Gary on board to serve the south-central United States. Gary has a wealth of sales and rental industry knowledge that will strengthen our ability to serve our customers,” said Dave Wanta, Custom Equipment LLC vice president of sales. “Gary Coke is a valuable addition to the team, and we look forward to the contributions that he will provide for our company’s continued growth.”
H&E opens new branch in Arkansas
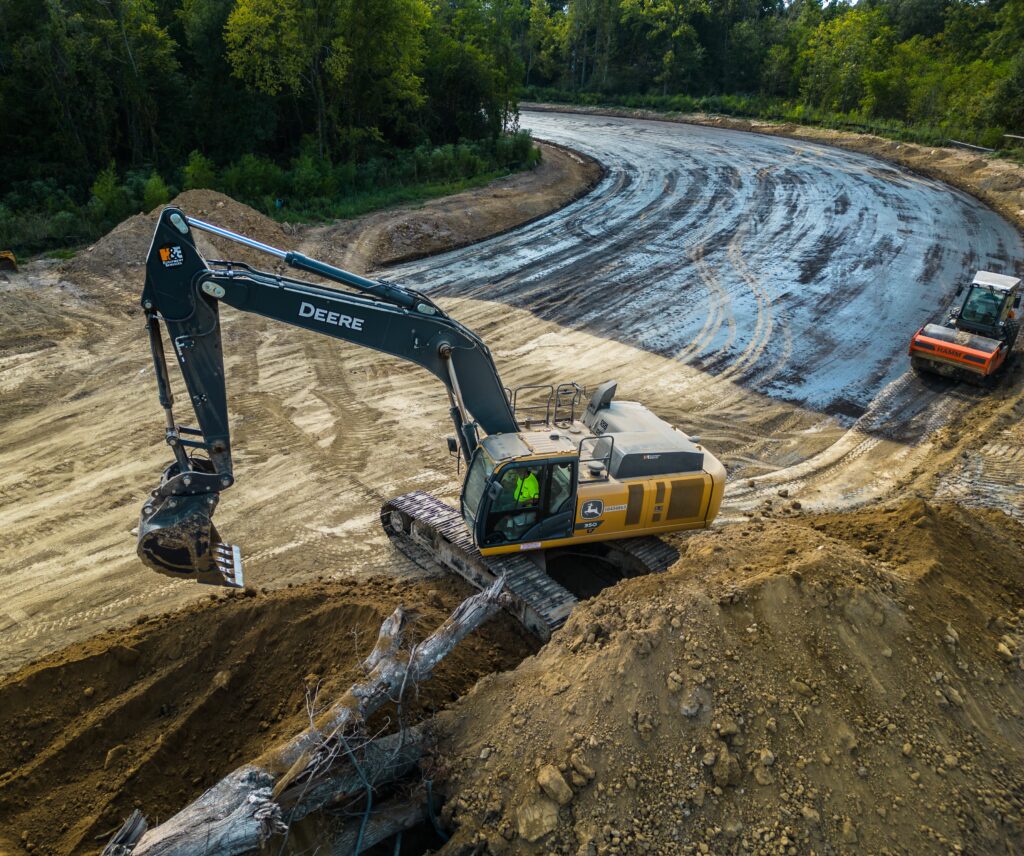
H&E Rentals has announced the opening of its Jonesboro branch, the third general rental equipment location in the state of Arkansas. Since the second quarter of 2023, H&E has opened 18 new branches across the country and acquired nine others. The facility is located at 2400 Dr MLK Jr Drive, Jonesboro, AR 72401-9228, phone 870-604-1100. It includes a fully fenced yard area, offices, and a repair shop and carries a variety of construction and general industrial equipment. “H&E has extended its coverage in northeast Arkansas, northwest of Memphis, Tennessee, and into the southeast tip of Missouri. With additional fleet in the area and quick access to I-555, state highways 49 and 63, and major roadways that branch off in all directions, we can get rental equipment to job sites quickly and efficiently,” says Branch Manager Wesley Creasey. “This new location bridges the gap between our existing Little Rock and Memphis branches, and we look forward to helping new and existing customers secure the right equipment for their projects.” The Jonesboro branch specializes in the rental of aerial lifts, earthmoving equipment, telescopic forklifts, compaction equipment, generators, light towers, compressors, and more and represents the following manufacturers: Allmand, Atlas Copco, Bomag, Case, Club Car, Cushman, Doosan, Gehl, Generac Mobile, Genie, Hamm, Hilti, Husqvarna, JCB, JLG, John Deere, Kobelco, Kubota, LayMor, Ledwell, Lincoln Electric, Link-Belt Excavators, MEC, Miller, Multiquip, Polaris, Sany, Skyjack, SkyTrak, Sullair, Sullivan-Palatek, Tag, Towmaster, Unicarriers, Wacker Neuson, Yanmar, and others.
Hyster-Yale Group appoints ICON Equipment as official Hyster Dealer
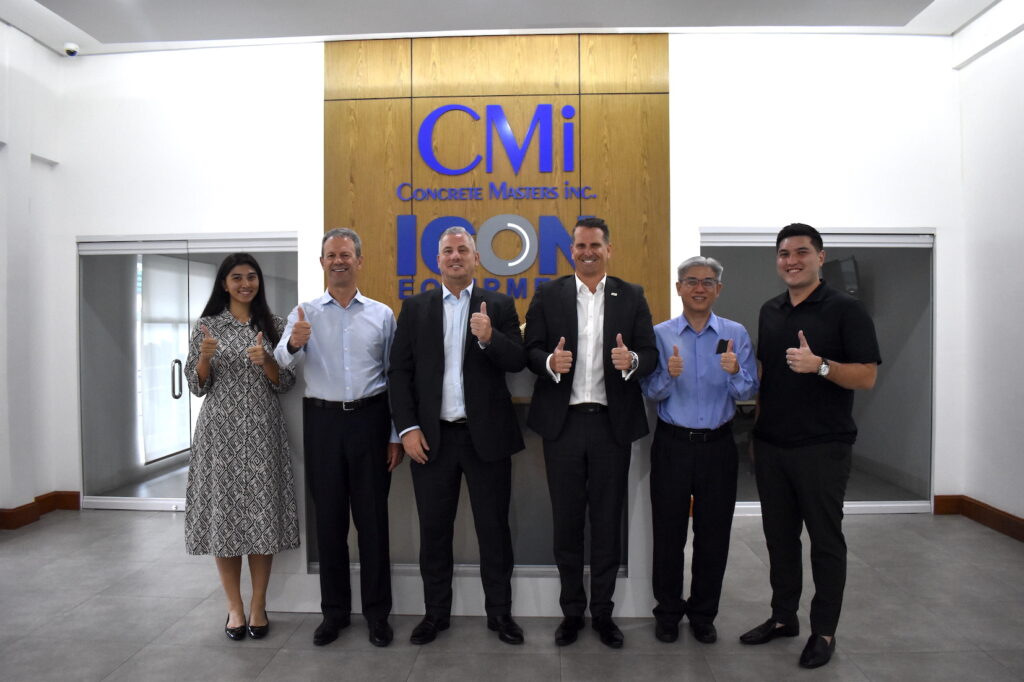
Hyster-Yale Group (HYG), an integrated full-line lift truck manufacturer, has appointed ICON Equipment Solutions Philippines Inc. (ICON) as its official dealer for the company’s Hyster® material handling solutions in the Philippines. This partnership signifies a strategic move to enrich material handling solutions in the region, leveraging ICON’s expertise and Hyster’s renowned technology. HYG’s decision to appoint ICON stems from the latter’s impressive track record and deep industry experience, positioning the Group ideally to tackle new challenges and foster growth in the Philippine market. ICON’s extensive sales coverage with four offices and two equipment yards nationwide, coupled with plans for upcoming branches, provides comprehensive customer reach and support. “We are thrilled to welcome ICON to our network of esteemed dealers,” said Mr. Simon Munn, Vice President, Dealer Development, JAPIC, Hyster-Yale Group. “Their dedication to delivering top-quality machinery, high spare parts availability, and efficient service aligns perfectly with HYG’s values. Together, we look forward to elevating the material handling industry and setting new benchmarks for excellence in customer service throughout the Philippines.” Commenting on the partnership, Mr. Chris Imperial, President at ICON highlighted the significance of partnering with HYG, “Partnering with HYG presents an advantageous opportunity in the material handling industry. Their commitment to delivering top-tier solutions, coupled with their comprehensive range of lift trucks, allow us to provide our customers with the highest quality products, further solidifying our position in the market.” The addition of Hyster products enriches ICON’s offerings, particularly in markets like the Philippines, where demand for reliable material handling equipment is on the rise. With e-commerce giants expanding their warehouse operations, the need for efficient logistics solutions has reached unprecedented levels. Additionally, with the continuous evolution of mining activities in the country, there is a growing need for robust equipment to facilitate smooth operations. Imperial added, “Hyster’s renowned reliability and advanced technology position us well to meet this demand, enabling efficient warehouse operations and smooth logistics for businesses across various industries.”
Episode 487: Inside Nucor Warehouse Systems and the Journey from Steel to Racks
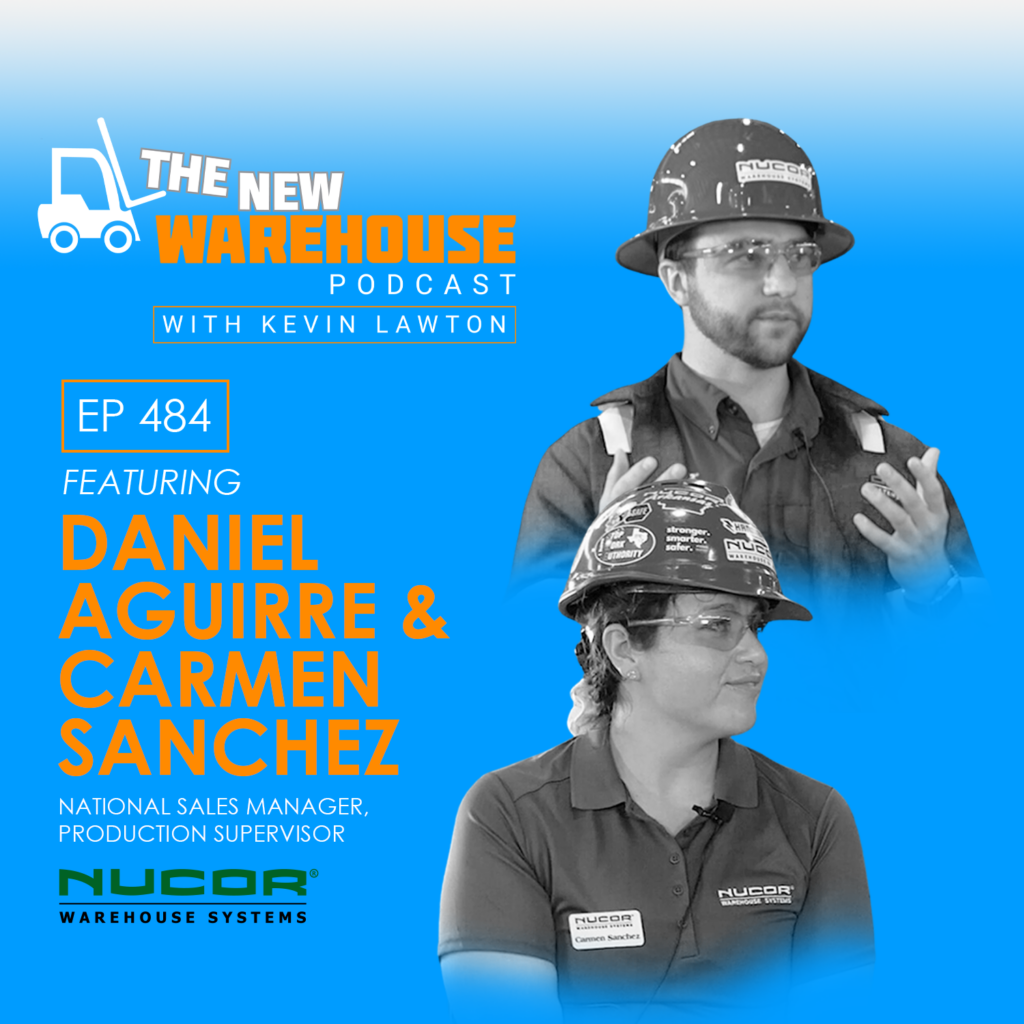
Episode 487 takes The New Warehouse Podcast on the road to the heart of industrial innovation at the Nucor Warehouse Systems (NWS) facility in Houston, Texas. Joining us are Daniel Aguirre, a seasoned guest, and Carmen Sanchez, the production supervisor on site. Nucor, renowned as the largest steel producer and recycler in the United States, showcases its end-to-end manufacturing process, transforming raw steel into the racking systems integral to modern warehouses. This episode delves into Nucor’s commitment to safety, efficiency, and sustainability in their production processes. The Core Value of Safety at Nucor Warehouse Systems Daniel emphasizes, “Safety to Nucor and to NWS is our core value. Without us being safe, none of this is possible.” The emphasis on safety is evident from the moment one enters the facility and every interaction with the Nucor team. Carmen explains, “We have 150 teammates that make everything possible. Our main priority is to work safely every day. Our main goal is for them to return to their families.” They integrate safety into the culture through daily safety meetings and empowering team members to speak up about potential hazards, fostering a community that isn’t just physically well and psychologically safe. Teamwork Makes The Dreamwork for End-to-End Pallet Racking Manufacturing Nucor’s Houston facility epitomizes a seamless end-to-end manufacturing process, turning raw steel into finished pallet-racking products. Daniel explains: “We’re taking steel coil, slitting it, and roll-forming it into beams or columns as standard roll-form racking.” The process continues with welding, painting, and preparing the racking for installation. Carmen highlights the teamwork involved: “Our talented team makes anything possible. We always find ways to be safer daily, make quality material, and be productive.” This integrated approach ensures high-quality products and the flexibility to meet diverse customer needs efficiently. Sustainability and Supply Chain Security Nucor’s commitment to sustainability is evident in its recycling efforts and secure supply chain. Daniel notes, “Nucor is the largest recycler in the United States. We can take old racking, melt it down, and produce new raw material.” This recycling process underscores Nucor’s dedication to environmental responsibility. Moreover, by controlling the entire supply chain, Nucor ensures on-time delivery and flexibility in production. Daniel explains, “Having a secure supply chain ensures on-time delivery and allows us to operate flexibly, adapting to customer needs without compromising quality.” This capability is crucial in today’s dynamic market, providing a reliable foundation for business operations. Key Takeaways from Nucor Warehouse Systems Nucor’s commitment to safety fosters a culture of mutual care and responsibility. The end-to-end manufacturing process at Nucor ensures high-quality, efficient, and flexible production of racking systems. Sustainability is integral to Nucor’s operations. Extensive recycling efforts and a secure supply chain enhance environmental responsibility and operational reliability. The New Warehouse Podcast Episode 487: Inside Nucor Warehouse Systems and the Journey from Steel to Racks
Cimcorp honored for proactive safety culture
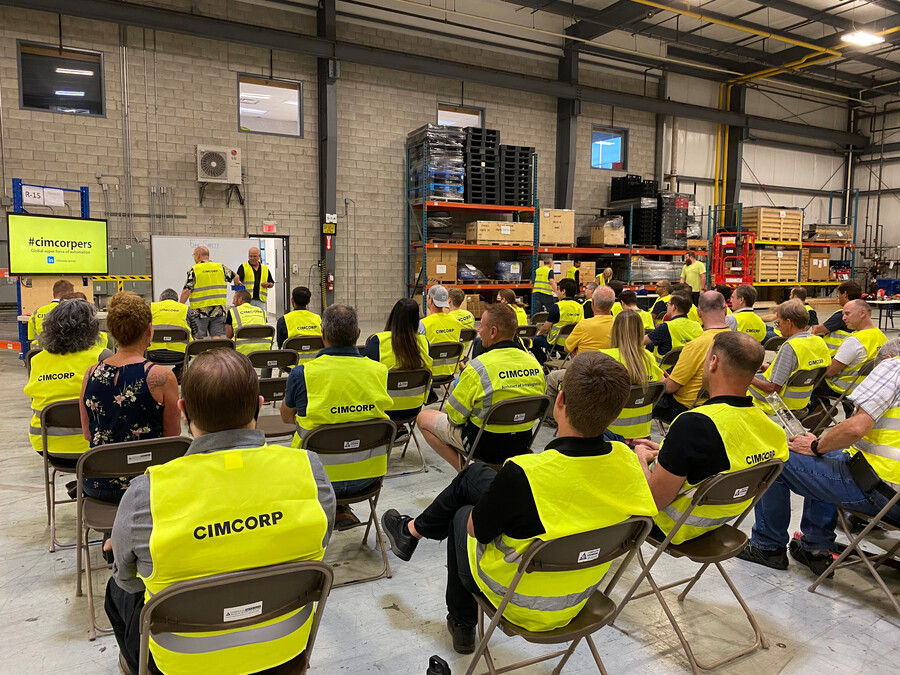
Cimcorp has been awarded the highest occupational safety level classification in the Vision Zero Forum, led by the Finnish Institute of Occupational Health. The Vision Zero Forum is a network of workplaces aimed at motivating and encouraging companies to strive towards a high level of occupational safety, occupational health and well-being at work. This accomplishment highlights Cimcorp’s dedication to workplace safety, and also reflects its commitment to fostering a culture where safety is a continuous journey, not merely a goal. With “Caring” one of its core company values, Cimcorp is committed to the well-being of its employees, partners, and customers. Cimcorp strives to provide healthy working conditions with the target of zero work-related injuries in all activities. Taking a preventative approach to safety, Cimcorp focuses on identifying and controlling risks and continuously developing the safety of its operations and products. Cimcorp’s journey towards zero accidents is driven by both collective effort and individual dedication. Every employee is encouraged to consider the safest way to complete each task before starting, fostering a reflective practice that supports a safe workplace. This mindset encourages each individual to care for their own safety, as well as the safety of others. “By developing our employee safety, we’re investing in the future,” said Tero Peltomäki, CEO, Cimcorp. “Each step taken towards safety is a step towards our shared success. When we care for each other’s safety as if it were our own, we embody the essence of our safety philosophy.” Cimcorp’s proactive approach to safety does more than prevent accidents; it builds trust and satisfaction among employees and customers. The company’s core value of reliability is evident in its operations, from fulfilling promises to being a trustworthy partner for both customers and staff. Cimcorp’s efforts to elevate workplace safety standards carry into installation sites and thorough risk assessments. Every reported safety observation is a step towards a safer, more efficient workplace and reflects continuous improvement.
Women In Trucking Association announced continued Gold Partnership with WM
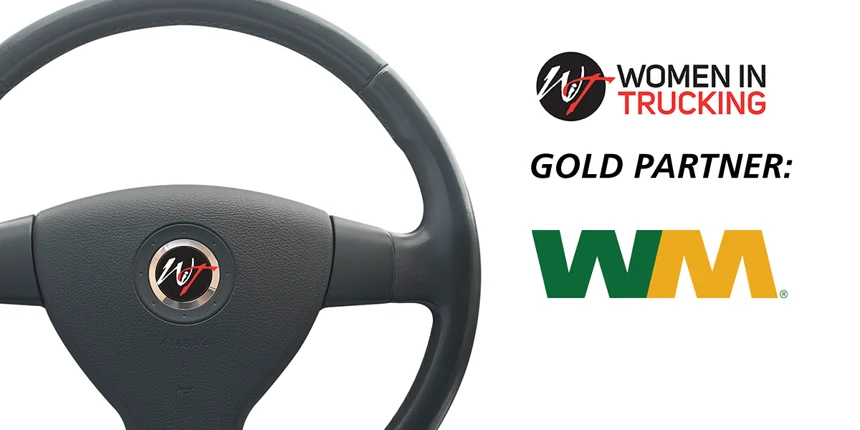
The Women In Trucking Association (WIT) has announced that WM has renewed its Gold Level partnership continuing the company’s support of the nonprofit association and its mission. Since 2018, WM has been a valuable partner of WIT contributing to the nonprofit’s efforts to encourage the employment of women in the trucking industry, promote their accomplishments, and minimize the obstacles they face. As part of those efforts, WM was a platinum sponsor at the 2023 Accelerate! Conference & Expo. Additionally, Domenica Farmer, Area Vice President at WM, serves on the WIT board of directors. “I am delighted to announce that we (WM) are renewing our partnership with Women in Trucking,” said Farmer. “It’s a fantastic partnership that we are proud to continue supporting. Here’s to another successful year of empowering and championing women in the trucking industry.” “We’re grateful for WM’s commitment to creating a more gender-diverse culture in transportation,” said Jennifer Hedrick, WIT president and CEO. WIT’s valuable partnerships with companies such as WM allow us to enhance engagement and opportunity within the trucking profession.” Founded in 2007, the Women In Trucking Association is a resource for more than 8,000 corporate and individual members located in the United States, Canada and Mexico, as well as Japan, Australia, Sweden, South Africa and New Zealand. Recent accomplishments include: releasing the 2023 WIT Index, the official barometer to benchmark and measure the percentage of women who make up critical roles in transportation each year, which had more than 300 company participants; awarding a deserving member a 2018 Volvo VNL670 in collaboration with Arrow Truck Sales, Inc.; honoring 300-plus leaders in transportation through several programs; and more than 1,900 registered attendees at the 2023 Accelerate! Conference and Exhibition.
U.S. Rail Traffic report for the week ending May 11, 2024
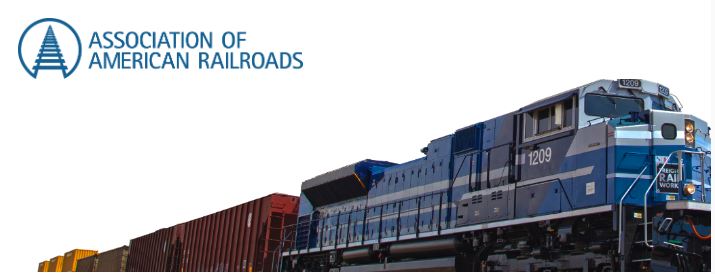
The Association of American Railroads (AAR) has reported U.S. rail traffic for the week ending May 11, 2024. For this week, total U.S. weekly rail traffic was 468,748 carloads and intermodal units, up 0.6 percent compared with the same week last year. Total carloads for the week ending May 11 were 209,319 carloads, down 7.0 percent compared with the same week in 2023, while U.S. weekly intermodal volume was 259,429 containers and trailers, up 7.7 percent compared to 2023. Six of the 10 carload commodity groups posted an increase compared with the same week in 2023. They included chemicals, up 1,668 carloads, to 33,045; petroleum and petroleum products, up 1,505 carloads, to 10,996; and miscellaneous carloads, up 1,132 carloads, to 8,639. Commodity groups that posted decreases compared with the same week in 2023 included coal, down 16,549 carloads, to 46,715; nonmetallic minerals, down 2,291 carloads, to 31,457; and grain, down 1,610 carloads, to 17,226. For the first 19 weeks of 2024, U.S. railroads reported a cumulative volume of 4,045,438 carloads, down 4.9 percent from the same point last year; and 4,796,341 intermodal units, up 8.7 percent from last year. Total combined U.S. traffic for the first 19 weeks of 2024 was 8,841,779 carloads and intermodal units, an increase of 2.0 percent compared to last year. North American rail volume for the week ending May 11, 2024, on 10 reporting U.S., Canadian and Mexican railroads totaled 321,482 carloads, down 2.6 percent compared with the same week last year, and 345,901 intermodal units, up 7.4 percent compared with last year. Total combined weekly rail traffic in North America was 667,383 carloads and intermodal units, up 2.3 percent. North American rail volume for the first 19 weeks of 2024 was 12,481,187 carloads and intermodal units, up 2.1 percent compared with 2023. Canadian railroads reported 94,624 carloads for the week, up 5.1 percent, and 73,591 intermodal units, up 4.1 percent compared with the same week in 2023. For the first 19 weeks of 2024, Canadian railroads reported a cumulative rail traffic volume of 3,064,779 carloads, containers and trailers, up 0.9 percent. Mexican railroads reported 17,539 carloads for the week, up 15.8 percent compared with the same week last year, and 12,881 intermodal units, up 21.4 percent. Cumulative volume on Mexican railroads for the first 19 weeks of 2024 was 574,629 carloads and intermodal containers and trailers, up 10.9 percent from the same point last year. View reports here
US Cutting Tool Orders totaled $212.4 Million in March 2024, bringing the Year-to-Date total up 2% from 2023
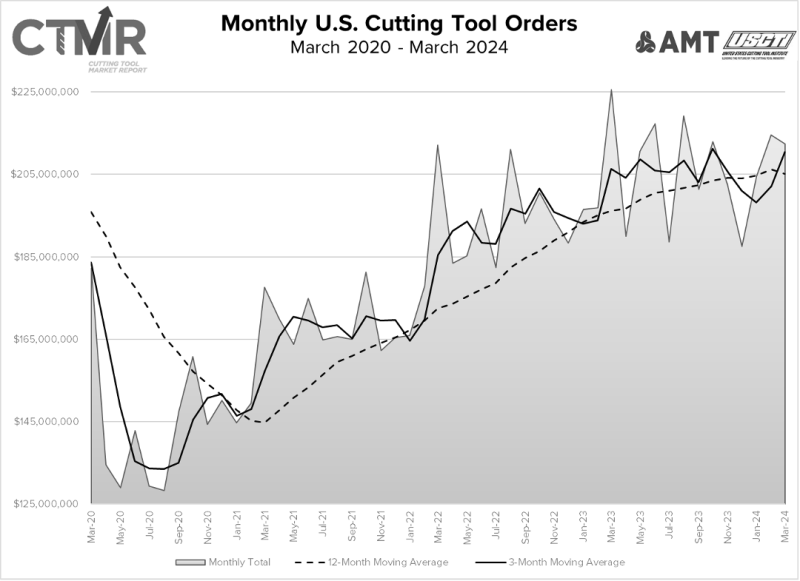
March 2024 U.S. cutting tool consumption totaled $212.4 million, according to the U.S. Cutting Tool Institute (USCTI) and AMT – The Association For Manufacturing Technology. As reported by companies participating in the Cutting Tool Market Report collaboration, this total was down 1.1% from February’s $214.6 million and down 5.8% compared with the $225.6 million reported for March 2023. With a year-to-date total of $631.5 million, 2024 is up 2% compared to the same period in 2023. “Despite the troubles at Boeing, cutting tool shipments to aerospace and defense-related manufacturing remain quite strong,” declared Jack Burley, chairman of AMT’s Cutting Tool Product Group. “First quarter data indicates that consumption of cutting tools and tooling remains on pace with current industrial production at a modest level. This may be an indicator of somewhat sluggish activity. “New projects are available in most industries, but many customers are reluctant to move forward, possibly because they are worried about inflation and election results. Despite the downward trend in new machine tool orders, I find it very interesting that cutting tools and related accessories to keep shops running are still performing reasonably well.” Steve Stokey, executive vice president and owner of Allied Machine and Engineering, agreed that inflation remained an industry concern. “The first quarter of 2024 is up slightly over the first quarter of 2023, but the long-run trend has turned negative for the first time since March 2021, when the industry began to recover from the COVID-19 downturn,” Stokey said. “Stubbornly high inflation appears to be a drag on the industry as the number of units shipped has shown a more sluggish trend than the value of shipments. If these patterns continue, the remainder of the year could end flat or slightly down from 2023.” The Cutting Tool Market Report is jointly compiled by AMT and USCTI, two trade associations representing the development, production, and distribution of cutting tool technology and products. It provides a monthly statement on U.S. manufacturers’ consumption of the primary consumable in the manufacturing process – the cutting tool. Analysis of cutting tool consumption is a leading indicator of both upturns and downturns in U.S. manufacturing activity, as it is a true measure of actual production levels. Historical data for the Cutting Tool Market Report is available dating back to January 2012. This collaboration of AMT and USCTI is the first step in the two associations working together to promote and support U.S.-based manufacturers of cutting tool technology. The graph below includes the 12-month moving average for the durable goods shipments and cutting tool orders. These values are calculated by taking the average of the most recent 12 months and plotting them over time.
Felling Trailers, Inc. names the 2024 Trailer for a Cause beneficiary

Felling Trailers, Inc. names Backing the Blue Line as the beneficiary of the twelfth annual 2024 Trailer for a Cause auction. Felling Trailers has hosted an online auction of an FT-3 Utility trailer for over a decade, donating 100% of the winning bid to the selected nonprofit organization. Felling Trailers’s goal is to bring awareness to various nonprofits that are making a difference and choosing a new beneficiary each year. Previous Trailer for a Cause auction have raised over $44,000 for nonprofit organizations such as ACT on ALZ-Alzheimer’s, Lymphoma Research Foundation, Minnesota Fire Fighters Foundation, Eagle’s Healing Nest, and Pockets of Hope to name a few. The 2024 Trailer for a Cause auction beneficiary, Backing the Blue Line, was selected by the Felling Trailers’ employees. “For several years, we put the decision of selecting the benefitting organization in the hands of our team members in the form of a vote. A list of organizations and corresponding information is given to team members to select from,” said Brenda Jennissen, President/CEO of Felling Trailers. “We respect and appreciate our local and state law enforcement officers and recognize what they lay on the line each day they put on their uniform and leave home for their shift to protect our communities. We’re thankful to live and work in communities that are protected by these professional men and women who choose to wear the badge. ‘Blessed are the Peacemakers; for they will be called Children of God.’ – Matthew 5:9.” Backing the Blue Line (BtBL) is a nonprofit organization dedicated to supporting the law enforcement community in Minnesota. BtBL unites the power of members and the generosity of donors to honor and support Minnesota law enforcement officers and families; they mobilize to provide services, labor, and assistance during times of illness, injury, or tragedy, as well as join in celebrating life milestones. BtBL supports the Minnesota law enforcement community by providing resources and emotional support to law enforcement officers and their families and serving as a positive voice in the community. Together, they are backing those who represent the thin blue line. An early Fall 2024 auction is being planned for Trailer for a Cause. Leading up to the auction, Felling Trailers will work with Backing the Blue Line to generate awareness about the work they do for the officers and families they serve with the programs and support services they offer. Backing the Blue Line is a 100% volunteer-run organization. Their donations directly support their vision to expand their reach to all Minnesota counties by increasing their supporters, volunteers, and means to assist. They want their interactions to drive a high standard for how law enforcement officers and their families are treated during times of crisis and need, offering family support services through programs like Christmas in June, Injured Officer Support, Not so Blue Christmas, and Fallen Officer Memorial Roses.
Kardex appeared at Automate 2024 showing manufacturers the fastest order fulfilment per sq ft
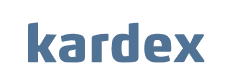
Kardex demonstrated to manufacturers at Automate 2024 the huge potential offered by Automated Storage and Retrieval System (ASRS) technology to reduce their intralogistics footprint, cut workloads, manage spikes in demand, and enhance productivity. Intralogistics solutions provider Kardex appeared at Automate 2024, North America’s largest robotics and automation event in Chicago (May 6-9), demonstrating the fastest order fulfillment solution per square foot on the market. Kardex FulfillX is a warehouse execution system (WES) purpose-built to allow new AutoStore systems to ramp up faster and is capable of meeting or exceeding business cases in as little as six months. It has been specifically created by experts at Kardex, a global AutoStore partner, to maximize the capabilities of AutoStore robotic cube storage systems for manufacturing customers. Kardex solutions offer manufacturers efficiency, flexibility, and short training times Visitors to stand #4681 at Automate 2024 saw FulfillX in action, with demonstrations of how it can create user-friendly, highly configurable AutoStore systems. FulfillX optimizes picking and packing, while also streamlining putaway and other inventory processes. It provides a real-time overview of the whole operation in a simple window. Enhancements can be rapidly deployed by Kardex’s dedicated AutoStore support team and digital twins enhance planning and commissioning. As well as promoting the benefits of FulfillX, Kardex’s booth used digital tools and augmented reality to bring to life the Kardex Intuitive Picking Assistant and its range of smart intralogistics solutions. Kardex’s Intuitive Picking Assistant solution is suitable for a wide range of industrial manufacturing applications, including spare parts picking, visual direction, and kitting. It uses digital tools and augmented reality to enhance picking processes by responding to movements and projecting relevant picking information directly onto the surface of the access opening. The Intuitive Pick Assistant is compatible with both and AutoStore ports to facilitate accurate, ergonomic picking, and can be tailored to specific customer requirements. In addition, it can be used to direct operators through kitting processes. As US manufacturers increasingly turn to warehouse automation technology, AutoStore empowered by Kardex FulfillX provides them with the opportunity to slash their facility footprint, reduce workload, manage spikes in demand, and address labor and skills shortages. Commenting on Kardex’s appearance at Automate 2024, Mitch Hayes, President of Kardex Solutions AutoStore, said, “Automate offered the ideal opportunity to introduce US manufacturers to AutoStore empowered by Kardex FulfillX. FulfillX represents the next evolution of ASRS technology. At Kardex, we are committed to pushing the boundaries of what is possible with intralogistics automation. Our advanced software solutions provide manufacturers with the flexible, convenient, and efficient capabilities they need to meet industry challenges now and in the future.” Real-world case studies MAHLE As a leading global parts and solutions provider to the Independent Aftermarket, MAHLE Aftermarket saw a shift in customer order profiles from larger pallet orders to smaller package orders in higher frequency. This resulted in an increasing number of shipping points per customer and shipping smaller quantities to more locations. To accommodate this shift, MAHLE Aftermarket implemented an AutoStore system from Kardex in their Olive Branch, MS location to automate small parts handling. Stay tuned for the official release of the MAHLE case study in mid-May 2024. Anyseals One company benefiting from AutoStore empowered by Kardex is Anyseals, a global wholesale sealing supplier. Anyseals provides their distribution customers with services including just in time delivery, bar coding, kitting and custom labeling. The company was moving from a completely manual to an automated operation and implementing a new WMS at its main US facility in Ohio. They turned to Kardex for a space-efficient, flexible solution to increase efficiency in small parts handling and facilitate growth. The Anyseals AutoStore system went live in October 2023 and Anyseals described working with Kardex as “a great experience”, with employees happy with how the technology assists them with their work, 100% uptime at the facility and average picking time reduced from up to 15 minutes per pick to seconds, with substantial time saved on putaway as well. Rush orders are prioritized to ship on time and Anyseals is still learning what is possible with Kardex and AutoStore to enhance its processes further. “The AutoStore solution will enable us to continue our strong growth trajectory and will enhance our ability to meet and exceed the high level of fulfilment execution for our customers”, says Toby Rose, COO at Anyseals USA.
PAC Machinery celebrates the end of an era and the beginning of an exciting new chapter in major leadership transition
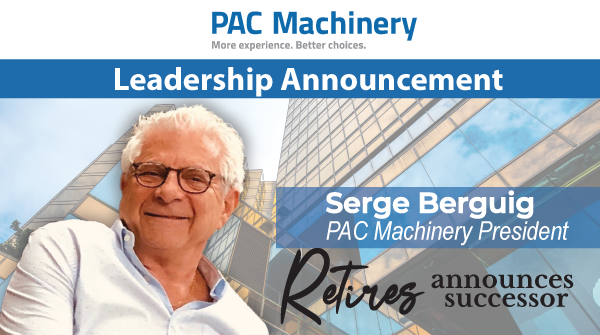
PAC Machinery (“PAC”) has announced the retirement of its President, Serge Berguig after 40+ years with the company. Serge is moving into a strategic advisory role, and will support the businesses as needed. Mr. Berguig also named Greg Berguig, as the new company President, effective May 1, 2024. Greg was serving as Vice President, leading sales, marketing, and commercialization efforts. The announcement was shared internally with employees on April 30, 2024. “As I reflect on my time leading this organization, I am proud of the growth realized across our locations, as well as the hard work and dedication from all our employees,” said Serge Berguig. “I know that our strong leadership team will continue to guide PAC Machinery into the future as a leading manufacturer of packaging equipment and bag materials,” Berguig said. Serge went on to thank employees for their contributions over the years as he reflected on what’s next for him and the leadership transition to his son Greg. “On behalf of everyone in our organization, I’d like to extend our appreciation and gratitude to Serge for 40 years of service to the company,” said Greg Berguig, President PAC Machinery,. During his time, Serge established this business as an industry leader in packaging, growing our product offerings through new developments and acquisitions, to keep PAC Machinery as a strong player in our space. We have a trusted brand reputation and are positioned to continue developing packaging solutions that customers require. Serge’s entrepreneurial spirit, engineering knowledge and focused leadership over the past four decades has earned him the utmost respect of our employees, customers, and partners. He will be missed as he transitions from his role.”
Bobcat installs stationary fuel cells from HyAxiom at two of its facilities
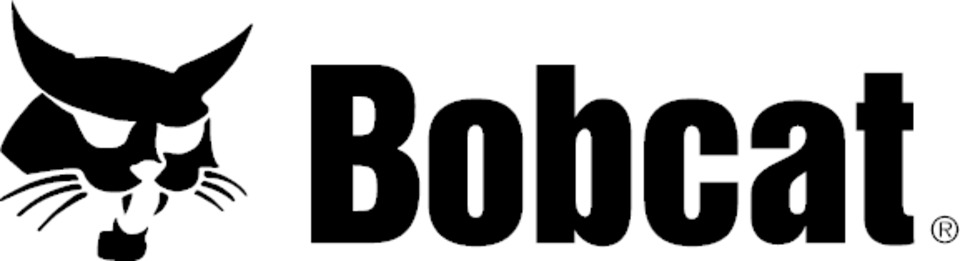
HyAxiom’s pureCell Ⓡ M400 units diversifies power sources, reduces energy consumption Bobcat Company has enhanced two of its North Dakota manufacturing facilities with the installation of 14 stationary, natural gas-powered fuel cells from HyAxiom, Inc., a leading global fuel cell and hydrogen solutions provider. These units will operate in parallel with the commercial power grid while carving a pathway to decarbonization by producing clean energy for the facilities operations. The three fuel cells at the Bismarck facility and the 11 units at the Gwinner location are the first commercial installations of stationary fuel cells in the state. The recently commissioned fuel cells allow Bobcat to diversify its energy sources by supplying a majority of the annual power and heat needs of the Bismarck facility and about half the needs of the Gwinner facility. “We are proud to be at the forefront of sustainable energy solutions with the installation of these new stationary fuel cells,” said Mike Ballweber, president, Doosan Bobcat North America. “This is just one example of our commitment to advancing our facilities today for a better tomorrow.” “HyAxiom’s stationary fuel cell solutions provide efficient combined heat and power that will help Bobcat improve its operations and continue innovating for the smart job site of the future,” said David Alonso, chief commercial officer at HyAxiom. Utilized in a wide range of applications, HyAxiom’s PureCell ® M400 is a proprietary phosphoric acid fuel cell (PAFC) that can use natural gas, hydrogen, LPG or a blend of fuels to produce rapidly deployable baseload electricity and heat that are also resilient, sustainable and affordable. While this is the first installation of fuel cells in North Dakota, HyAxiom’s fuel cells are in operation nationwide and globally, providing power and heat for commercial and industrial uses. With load- following capabilities, they have fast become a resilient source of energy for microgrid applications, providing the ability to switch between grid-connected and grid-independent modes, facilitating the ease of accessibility to reliable and clean electricity. In Bismarck, Bobcat is able to provide power back to the grid as a registered power producer. This reduces the demand on Bismarck energy providers and ensures there is enough power on the grid. Thanks to the useable heat produced by the fuel cells, Bobcat has also been able to reduce its overall energy use by eliminating two boilers previously required to produce heat on its paint line.
Combilift renews three-year sponsorship of Monaghan Ladies Gaelic Football Team
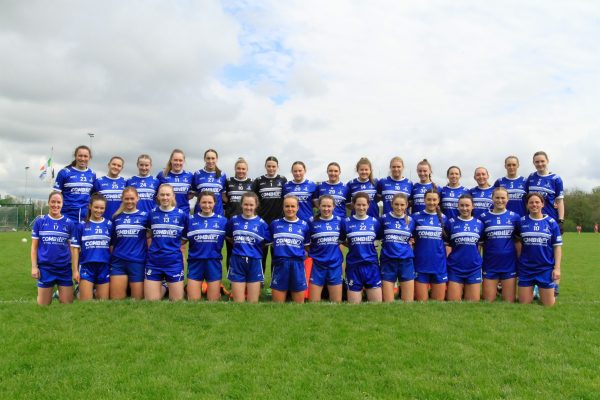
Combilift, a manufacturer of multi-directional forklifts and straddle carriers, has announced the renewal of its sponsorship with the Monaghan Ladies Gaelic Football Team for another three years. This extension underscores Combilift’s commitment to supporting local sports and fostering community spirit. Monaghan Ladies Gaelic Football has been a cornerstone of sporting excellence in the region, promoting athleticism, teamwork, and community engagement. Combilift’s renewed sponsorship will provide essential funding to support the team’s activities, including training programs, equipment, Programmed S&C Support, GPS and Sports Science, Performance Analysis, and Video Analysis. This partnership aims to enhance the development of players at all levels and strengthen the team’s presence in national and international competitions. Martin McVicar, Managing Director and Co-Founder of Combilift expressed his enthusiasm for the renewed partnership: “We are thrilled to continue our support for the Monaghan Ladies Gaelic Football Team. Their dedication, hard work, and passion for the sport resonate with Combilift’s values. We look forward to their continued success and growth over the next three years.” Team manager, Darren Greenan, also shared his appreciation: “The Monaghan Ladies are delighted that Combilift has chosen to renew their sponsorship partnership for the next 3 years. This financial support helps create the best possible environment for our intercounty players, boosts the team profile, and allows management the resources to prepare the teams to the higher levels expected. We strive to make intercounty football an attractive opportunity for girls in the county, and this goes a long way to helping us reach this goal”.