New ASSP report aims to help create safer workplaces
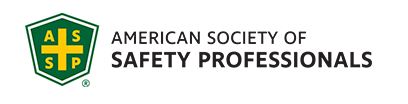
Occupational safety and health (OSH) professionals use collaboration and key insights to make smart decisions that can drive change across the industry. The American Society of Safety Professionals (ASSP) is helping that effort to improve worker safety and health by producing new online reports that contain firsthand views and experiences of business leaders from all industries. This valuable feedback and context from seasoned executives is being summarized through ASSP’s Corporate Listening Tour, an activity that helps inform and direct both ASSP and corporate initiatives that advance worker safety and health. The project is led by CEO Jennifer McNelly, CAE, who meets individually with a broad range of safety executives each year to discover trends impacting their companies and the safety and health profession. “While federal and state efforts have improved environments over the past few decades, more must be done to protect workers,” McNelly said. “The latest data from the U.S. Bureau of Labor Statistics shows that nearly 5,500 fatal work injuries occurred in 2022 – a 5.7 percent increase from the previous year. This means a worker died every 96 minutes. That’s simply not acceptable. On-the-job fatalities and serious injuries are preventable.” ASSP’s 2024 report from the Corporate Listening Tour highlights five key findings: Focus on What Matters. Prioritize the prevention of serious injuries and fatalities over minor incidents to avoid spreading resources too thin. This might mean accepting a slight increase in less severe incidents, but it’s ultimately about spending valuable time and resources where they count the most. Manage Workforce Changes and Safety Priorities. With unpredictable shifts in the workforce and a shortage of skilled labor, keeping everyone safe becomes more challenging. High turnover and the struggle to attract and keep good employees increase the risk of incidents and employee burnout. OSH professionals must influence how new employees are trained and provide input on retention strategies. Embrace OSH-Related Applications of AI. Technology, particularly artificial intelligence, is constantly reshaping how we work. While this brings opportunities for safety improvements, it also introduces new risks. OSH professionals should focus on using AI to enhance safety while ensuring the organization doesn’t neglect traditional safety practices that have proven to be effective. Manage Cultural Shifts and Governance in Uncertain Times. Economic and political uncertainties affect how businesses operate. OSH professionals can drive changes in organizational culture – making sure leaders take accountability for safety – and demonstrate its importance even in uncertain times. Empower Influential OSH Leaders in the Changing Workplace. OSH professionals must maintain their technical skills and certifications while seeking organizational support to become better leaders who can drive operational excellence. “The report proposes a set of questions to help spark discussions among safety teams as well as with their colleagues and corporate leaders,” McNelly said. “It’s through proactive conversations about trends and potential risks that we can better integrate program improvements to reduce worker injuries, illnesses and fatalities.”
Bill Vining joins KPI Solutions
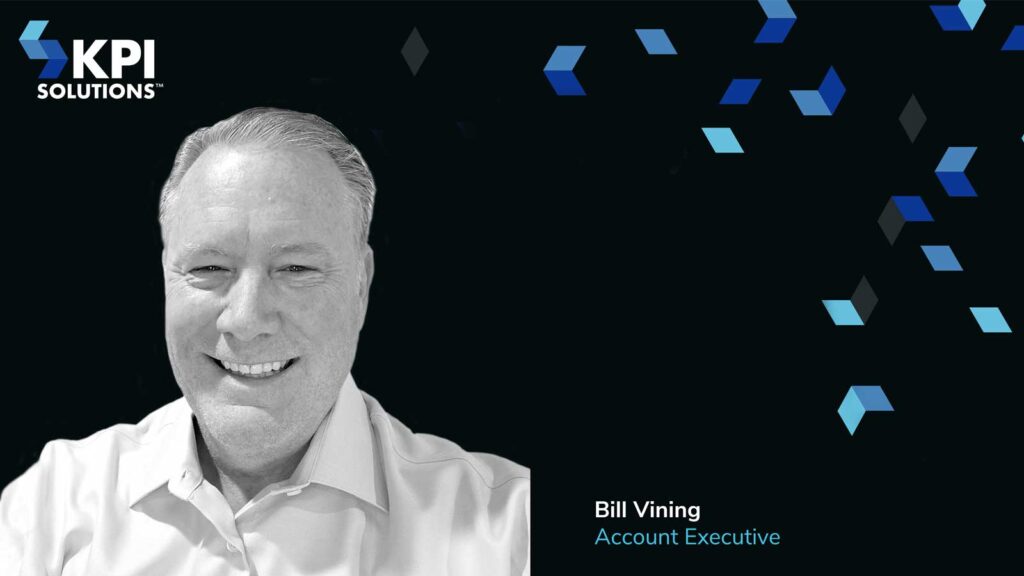
Bill brings 30 years’ experience working with clients to evaluate, design, and implement innovative solutions to solve complex supply chain challenges and boost productivity KPI Solutions (KPI) has announced that Bill Vining has joined the company as Senior Account Executive. In this role, Bill will work directly with companies to address operational challenges and develop best-in-class solutions using warehouse automation and intelligent software to reduce labor reliance and build resilience. “I’m excited to join the KPI Solutions sales team and partner with our clients to deliver tailored distribution solutions that blend leading technologies with world-class warehouse execution software,” said Bill. “KPI is unique in the industry for providing an unbiased end-to-end solution that allows clients to realize desired business results and drive value throughout the supply chain.” “We’re happy to welcome Bill as our solutions continue to transform operations and elevate performance, always focusing on being accountable for our client’s business case,” said Roger Counihan, Senior Vice President of Sales. “His experience in leading-edge automation and robotics will undoubtedly bring value to our clients, allowing them to not only meet today’s labor and productivity challenges but also prepare for future distribution demands.” Bill joins KPI Solutions from NEXUSiQ, provider of supply chain AI, analytics, and advanced visualization systems, where he served as Chief Revenue Officer. Throughout his extensive career in the supply chain industry, he has worked with several leading technology and software providers including Skydio, 6 River Systems, Dematic Reddwerks, Optoro, Red Prairie, and Manhattan Associates. He holds a Bachelor of Science, Economics degree from the University of Connecticut and resides in Atlanta.
GRI announces the appointment of Ydo Doornbos
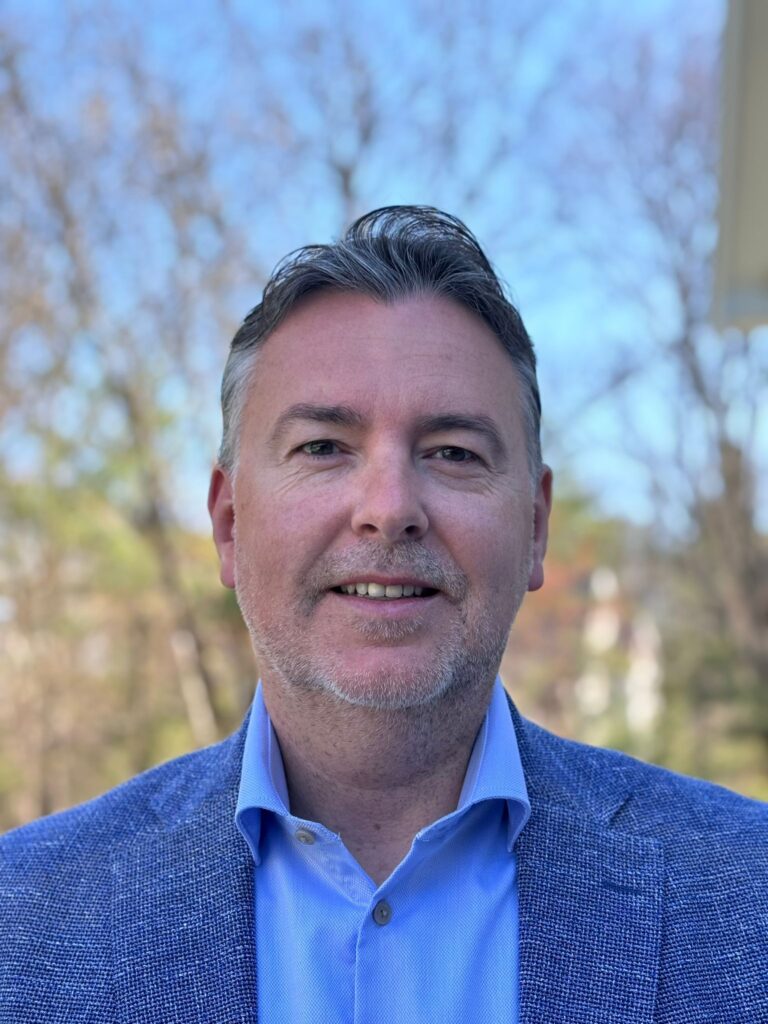
GRI has announced the appointment of Ydo Doornbos as Director of North America. With an illustrious career spanning 29 years in the tire industry in various management roles, Ydo brings with him a wealth of expertise and leadership to GRI’s North American business operations. Doornbos’ journey in the tire industry began in 1995 with a 6-month internship at Monarch Industrial Tires in the USA, after which he commenced his extensive career at Trelleborg Wheel Systems (TWS) as the Regional Sales & Operations Manager in Europe for the Monarch brand. He was then promoted to Marketing Manager Europe for the TWS Industrial Tires division. In 2005, Ydo returned to the United States, where he served as Director of Marketing, Customer Service & OEM Sales at TWS before being appointed Managing Director & Product Area President for Industrial and Construction tires. Over thirteen years, he spearheaded strategic initiatives that enhanced product integration and service excellence. In 2019, Ydo was promoted to Regional President North & Central America – AG/MH/CON, where he steered the company through unprecedented challenges posed by the global pandemic. In 2022, Ydo embarked on a new chapter in his career, assuming the role of VP Business Development at American Pacific Industries (API), a renowned tire engineering company. His strategic vision and business acumen contributed to API’s growth and expansion in the automotive and commercial tire sectors. Now, Ydo returns to his roots in Specialty Tires with GRI, driven by a commitment to sustainability and innovation. As Director of North America, he will lead GRI’s efforts to expand and drive GRI’s success in delivering sustainable Agriculture, Material Handling, and Construction tires to the North American market. Commenting on his appointment, Ydo Doornbos expressed his enthusiasm stating, ” I am thrilled to join GRI, a company synonymous with excellence and innovation in the tire industry. I look forward to leveraging my experience to drive growth and success in North America.”
Sunbelt Rentals acquires ABC Equipment Rental
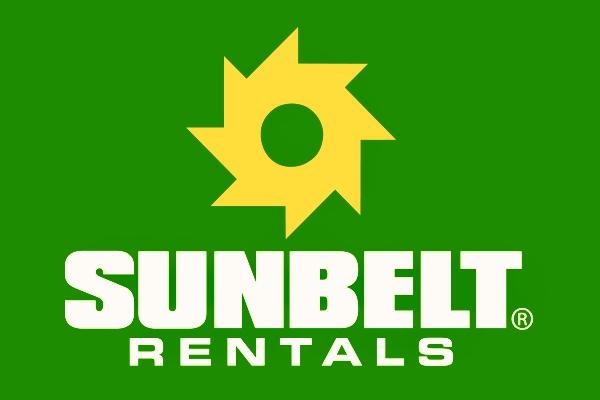
Sunbelt Rentals has acquired ABC Equipment Rental, a multi-branch independent equipment rental provider in the Baltimore and Washington D.C. markets. “We are pleased to join forces with the Sunbelt Rentals team,” said Lee Lightner, President of ABC Equipment Rental. “Sunbelt’s national brand, extensive general tool and specialty equipment fleet, and deep roots in the Baltimore and Washington markets will make this a great combination for our customers and employees.” Catalyst Strategic Advisors served as the exclusive transaction advisor to ABC Equipment Rental.
Atlas Companies acquires Badger Toyotalift
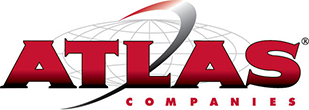
The Atlas Companies has acquired Badger Toyotalift of New Berlin, WI, effective October 1, 2023. In a memo from Atlas president and CEO Al Rawson welcomed the team members of Badge Toyotalift to the Atlas Companies. Badger ToyotaLift opened for business in 1969 and services the forklift and material handling needs of Southern Wisconsin. Since its inception, they have expanded its services and product offerings to create a comprehensive forklift dealership that allows it to fulfill the needs of its customers. Atlas Toyota Material Handling is an authorized Toyota Forklift Dealer committed to providing quality service, premium equipment, and innovative solutions for companies of all sizes. Supplying Illinois (Chicagoland), Minnesota, Wisconsin, and Northwest Indiana with the largest inventory of forklifts in the nation, Atlas Toyota is a complete resource for all your material handling needs. On July 1, 2020, the Atlas Companies acquired Minnesota material handling company Toyota-Lift of Minnesota, Inc.
MHEFI awards record-breaking $231,700 in scholarships to 61 students
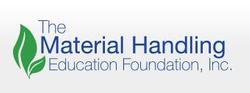
The Material Handling Education Foundation, Inc. (MHEFI) has announced the distribution of $231,700 in scholarships to 61 material handling, supply chain, and logistics students for the 2024/2025 academic year. This marks the highest amount ever awarded by MHEFI, reflecting its commitment to supporting education in material handling, logistics, and supply chain management. The scholarships, ranging from $1,500 to $6,000, were granted to undergraduate students who demonstrated outstanding academic performance, maintaining a “B” grade point average or higher in their major. Recipients were selected based on their dedication to these fields of study and their potential to make a positive impact in the industry. In response to this record-breaking scholarship amount, Brian Neuwirth, MHEFI President, stated: “We are immensely grateful to our sponsors whose generous contributions make these scholarships possible. These students show incredible potential and dedication, and we are honored to support their journey into the material handling and supply chain industry.” MHEFI would like to congratulate the following scholarship recipients: • William Fish, North Dakota State University, Crane Manufacturers Association of America (CMAA) Honor Scholarship, $6,000 • Sarosh Ahmed, University of Toledo, Crane Manufacturers Association of America (CMAA) Honor Scholarship, $6,000 • Ethan O’Connor, Oklahoma State University, Al Wurz Memorial Scholarship, $5,000 • Rahul Sah, Mississippi State University, Al Wurz Memorial Scholarship, $5,000 • Kayleigh Bednar, Kansas State University, Automated Storage & Retrieval Systems (ASRS) Honor Scholarship, $5,000 • Seth Thibodeau, Oklahoma State University, Conveyor & Sortation Systems (CSS) Honor Scholarship, $5,000 • Daniela Elenes, California Polytechnic, Dan Clapp Memorial Scholarship Sponsored by Rack Manufacturers Institute (RMI), $5,000 • Meredith DePuy, Virginia Tech, Frazier Industrial Honor Scholarship, $5,000 • Kyra Glenn, University of NorthTexas George W. Prest Honor Scholarship, $5,000 • Rushang Patel, Texas A&M University, Liz Richards Honor Scholarship Sponsored by MHEDA, $5,000 • Meher Syed, Texas A&M University, Liz Richards Honor Scholarship Sponsored by MHEDA, $5,000 • Justin Anetone, University of Nebraska, Kearney Liz Richards Honor Scholarship Sponsored by MHEDA, $5,000 • Addison Kiteley, Michigan State University, Material Handling Education Foundation, Inc. Honor Scholarship, $5,000 • Chase Hakerem, North Carolina State University, Material Handling Education Foundation, Inc. Honor Scholarship, $5,000 • Maleigha Long, Iowa State University, Material Handling Education Foundation, Inc. Honor Scholarship, $5,000 • Thomas Dean Mount, North Dakota State University, Material Handling Education Foundation, Inc. Honor Scholarship, $5,000 •Joan Jaiyeoba, Texas Tech University, Material Handling Education Foundation, Inc. Honor Scholarship, $5,000 • Matthew Offerman, Bradley University, Material Handling Education Foundation, Inc. Honor Scholarship, $5,000 • Katherine Maciejewski, Maine Maritime Academy, Material Handling Education Foundation, Inc. Honor Scholarship, $5,000 • Daniel Dandreo, Kansas State University, Material Handling Education Foundation, Inc. Honor Scholarship, $5,000 • Vinithra Seshan, California Polytechnic San Luis, Material Handling Education Foundation, Inc. Honor Scholarship, $5,000 • Bretton Hall, Oklahoma State University, Material Handling Education Foundation, Inc. Honor Scholarship, $5,000 • Christopher Bohm, Lake Superior State University, Richard Dilling Memorial Scholarship, $5,000 • Withanage Praveen Perera, University of Florida, Richard Dilling Memorial Scholarship, $5,000 • Emma Grace Woolsey, Virginia Tech, Rack Manufacturers Institute (RMI) Honor Scholarship Sponsored by ASG, $5,000 • Rae Williamson, Oklahoma State University, Rack Manufacturers Institute (RMI) Honor Scholarship Sponsored by ASG, $5,000 • Matthew Moore, University of Texas Arlington, Rack Manufacturers Institute (RMI) Honor Scholarship Sponsored by ASG, $5,000 • Genevieve Rasmussen, Bradley University, Rack Manufacturers Institute (RMI) Honor Scholarship Sponsored by ASG, $5,000 • Stephen Farley, Penn State University, Willard P. Heddles Memorial Scholarship, $4,800 • Abbey Kirk, Oklahoma State University, Mobile Automation Group (MAG) Honor Scholarship, $4,000 • Austin Yarbrough, University of Missouri-Columbia, The Robotics Group (TRG) Honor Scholarship, $4,000 • Samantha Chiang, Kettering University, The Robotics Group (TRG) Honor Scholarship, $4,000 • Peter Kronebusch, University of Illinois Urbana Champagne, Crane Manufacturers Association of America (CMAA) Honor Scholarship, $3,100 • Elijah Griego, New Mexico State University, Automation Controls Electrification (ACE) Honor Scholarship, $3,000 • Garrett Dickinson, University of Maine, Automation Controls Electrification (ACE) Honor Scholarship, $3,000 • Sydney Herring, Michigan State University, Ergonomics Assist Systems Equipment (EASE) Honor Scholarship, $3,000 • Gabriela McSwieney, Clarkson University, Gorbel Inc. Honor Scholarship, $3,000 • Samuel Sweat, Kansas State University, Protective Guarding Manufacturers Association (ProGMA) Honor Scholarship, $3,000 • Asif Ahmed, Texas Tech University, Protective Guarding Manufacturers Association (ProGMA) Honor Scholarship, $3,000 • Rashed Amad, Virginia Tech, Scan Label Apply Manifest (SLAM) Honor Scholarship, $3,000 • Matthew Carlesi, Worcester Polytechnic Institute, Storage Manufacturers Association (SMA) Honor Scholarship, $3,000 • Madison Harmon, Virginia Tech, Irving M. Footlik, PE Memorial Scholarship, $2,850 • Mollie McKee, Virginia Tech, Loading Dock Equipment Manufacturers (LODEM) Honor Scholarship, $2,850 • Evan Bennett, University of Wisconsin-Superior, LIFT Manufacturers Honor Scholarship, $2,600 • Margaret Stoving, Michigan State University, Bastian Family Scholarship, $2,500 • Ulises Navarro-Luviano, North Carolina State University, Bastian Family Scholarship, $2,500 • Matthew Wells, University of Arkansas, Conveyor & Sortation Systems (CSS) Honor Scholarship, $2,500 • Anna Sidoti, University of Tennessee, Solutions Community Honor Scholarship, $2,500 • Ivan Latinovic, Purdue University, Solutions Community Honor Scholarship, $2,500 • Carolina Remond, University of Arkansas, Southworth International Group Honor Scholarship, $2,500 • Philip Klim, North Carolina State University, St. Onge Company Honor Scholarship, $2,500 • Elan Preis, California Polytechnic San Luis, Seizmic, Inc./LAMHMS Honor Scholarship, $2,300 • Lucas Greazel, University of Mississippi, Expert Crane Honor Scholarship, $2,250 • Kush Patel, University of Tennessee Knoxville, UNEX Manufacturing Honor Scholarship, $2,250 • Blake Bollow, University of Wisconsin, Platteville, Hoist Manufacturers Institute (HMI)/Monorail Manufacturers Association (MMA) Honor Scholarship, $2,100 • Eamon Walsh, George Washington University, Hanel Storage Systems Honor Scholarship, $2,000 • Joel Chon, Rutgers University, Ridg-U-Rak Honor Scholarship, $2,000 • Alexis Denny, Michigan State University, Steel King Industries Honor Scholarship, $2,000 • Julia Fitzgerald, University of Pittsburgh, Brian McNamara Honor Scholarship Sponsored by Southworth International Group, $1,800 • Bryce Bullard, Oklahoma State University, James Galante Memorial Scholarship Sponsored by Southworth International Group, $1,800 • Ashton Parkey, Oklahoma State University, James Indelicato Material Handling Scholarship, $1,500 If you would like to support MHEFI’s mission to provide financial support for educational programs to engage and retain talent for the material handling, logistics and supply chain industry, please donate
IDENTCO highlights automation capabilities and PCB labeling at PCB East
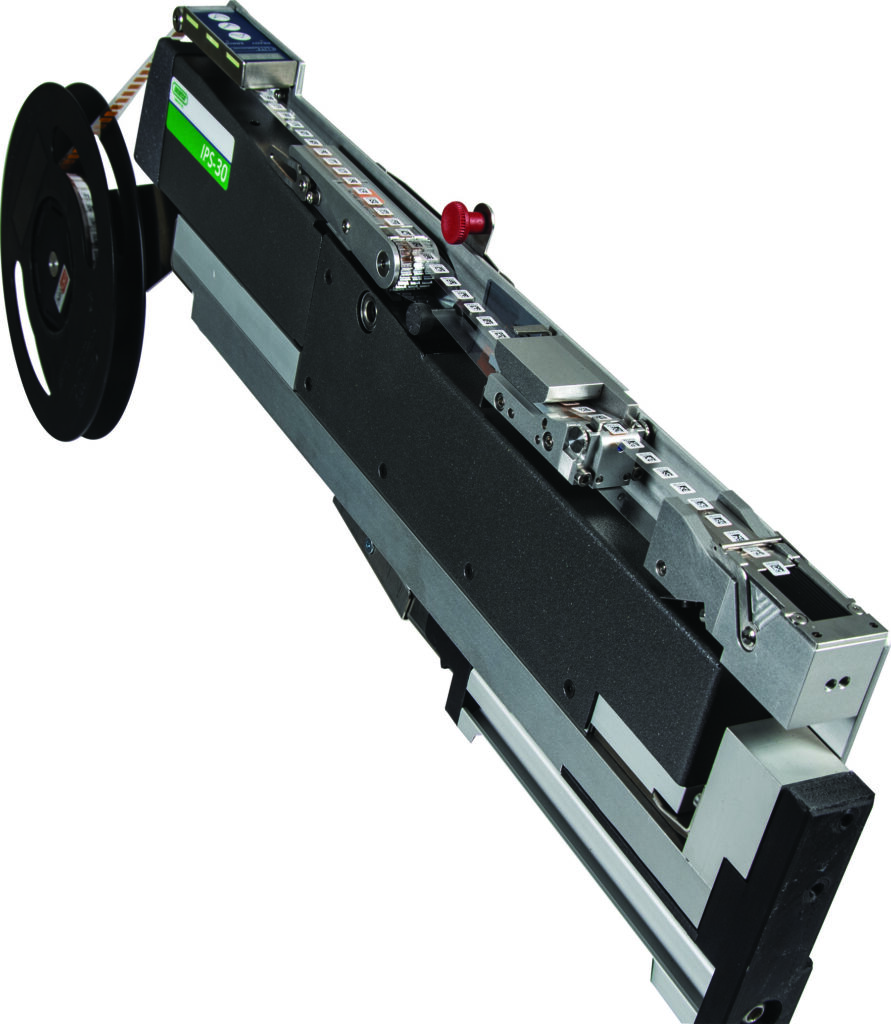
Company to showcase label feeders and product solutions to simplify automation. IDENTCO will highlight its automation capabilities and PCB labeling solutions at PCB East, June 4-7 in Boxborough, MA, Booth #301. With automation a key theme, IDENTCO’s commitment to simplifying the automation process for PCB manufacturers is evident through the company’s comprehensive label and equipment packages. Designed for hassle-free integration, IDENTCO’s automation products offer plug-and-play functionality with most SMT equipment brands. Attendees of the show will have the opportunity for a live demonstration of the IPS-30 Slimline Label Feeder. At a mere 30mm (1.18 in.) wide – half the size of conventional feeders – the IPS-30 requires only one feeder position on pick-and-place machines, freeing up valuable space along congested SMT production lines. Providing precise and accurate placement, it can also feed labels or die-cut parts as small as 2mm x 2mm. The company will also be exhibiting its robust label solutions for printed circuit board (PCB) applications, including DuraTrack. This label series provides printed circuit assemblies with comprehensive traceability – an increasingly attractive internal quality control and supply chain transparency feature for brand owners producing high-leverage electronics. Engineered for use in surface mount technology and throughout the entire assembly process, DuraTrack thermal transfer printable labels can endure harsh fluxes, the latest cleaning chemistries, and high temperatures encountered in today’s circuit board assembly processes, on both sides of the board.
Vertical reciprocating conveyors elevate AGVs and AMRs to new levels of efficiency
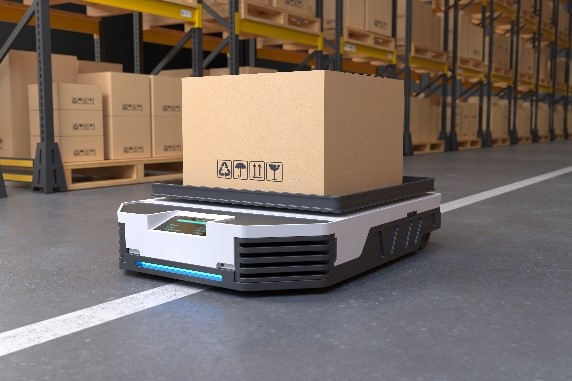
Vertical reciprocating conveyors (VRCs) act as the pivotal link between two major trends in warehouse operations that are dramatically increasing efficiency and profitability: Mobile Robots — The widespread adoption of Automated Guided Vehicles (AGVs) and Autonomous Mobile Robots (AMRs) is transforming the horizontal movement of materials across facilities, revolutionizing logistics and material handling processes. Vertical Space Utilization — Driven by the pursuit of logistics efficiency, along with escalating real estate costs and last-mile distribution demands, warehouses and production facilities are optimizing “cube space utilization” by expanding upwards rather than outwards. Vertical reciprocating conveyors seamlessly integrate the horizontal and vertical material handling processes, facilitating the smooth automated flow of material in three dimensions. These flexible and compact systems can be incorporated into a wide variety of layouts and serve a multitude of different applications. Combining VRCs with mobile robots and other manual and automated equipment often represents the most efficient, safest, and cost-effective solution for accessing taller racking, pick modules, mezzanines, and multiple floor levels, in virtually any type of warehouse or production environment. Rapid Adoption of Mobile Robots AGVs and AMRs are revolutionizing logistics across many industry sectors. In factories, these technological advancements automate material handling and assembly line tasks. This not only boosts production rates but also improves workplace safety by taking over hazardous or repetitive tasks from human workers. Automated Guided Vehicles adhere to predetermined paths, whereas Autonomous Mobile Robots employ sophisticated sensors and artificial intelligence for flexible navigation. AGVs, with their lower initial costs, are sometimes preferred by production and packaging operations in obstacle-free routes where predictable timing of material delivery is paramount. Conversely, AMRs offer unparalleled adaptability in dynamic and chaotic settings, making them ideal for large warehouses and distribution centers. Mobile robots are crucial to the advancement of Industry 4.0, boosting efficiency, flexibility, and automation within manufacturing landscapes. Their capacity for autonomous navigation and task execution across diverse scenarios renders them indispensable in the drive towards more intelligent and interconnected factory ecosystems. In warehouses, the impact of these robots is even more visible and transformative. Several factors are driving the swift adoption: E-commerce Growth: As E-commerce continues to experience explosive growth, with next-day-delivery expectations and direct-to-consumer marketing models, AGVs and AMRs are key to meeting the demand for quicker order fulfillment and inventory management. Complexity of Modern Distribution: The modern warehouses and distribution centers need to rapidly evolve from classic distribution models to an omni-channel model with the agility to pick case packs, fill retail store orders, pick and pack single consumer orders, and process customer returns and product refurbishments. Labor Shortages and Rising Costs: With ongoing labor shortages, particularly in logistics and manufacturing, AGVs and AMRs offer a solution by automating repetitive tasks. Technological Advancements: Enhanced sensors, AI, and better batteries have made AGVs and AMRs more adaptable and efficient, capable of performing complex tasks autonomously. Safety and Efficiency: Compared to forklifts and manual material handling equipment, AGVs and AMRs improve workplace safety and operational efficiency, handling hazardous tasks and operating 24/7 with precision. Vertical Cube Utilization Two to three decades ago, distribution centers typically featured clear heights of 24 to 32 feet – the vertical space from the floor to the ceiling. Today, driven by the scarcity and increased costs of land, especially near urban centers, and advances in fire protection and material handling technology, the industry standard for clear heights has shifted to 36 and 40 feet, with demand growing for even taller structures. The shift towards taller buildings is also fueled by the rapid growth in multi-level facilities, specifically designed to optimize last mile distribution, accommodating the increasing demand for faster and more efficient delivery systems in densely populated areas. Leveraging the “vertical cube” not only maximizes storage but also streamlines operations, improving material handling, increasing productivity, and ensuring safety without necessitating horizontal expansion. The utilization of upper levels also frees up prime dock-level real estate for crucial shipping, receiving, or re-packaging processes. Furthermore, the concept of cubic utilization in warehouse and factory design marks a significant shift towards sustainability and energy efficiency. By maximizing cubic space while minimizing the square footage of the building’s exterior envelope, facilities significantly reduce HVAC costs. This approach not only lowers initial investment in land and construction but also yields long-term savings in maintenance, operations, and even property taxes. VRCs are Ideal for Automated Material Handling The symbiotic relationship between these two trends — mobile robots and the utilization of vertical space — mediated through Vertical Reciprocating Conveyor technology, exemplifies how the strategic adoption of advanced automation technologies and space utilization concepts can revolutionize warehousing and manufacturing. A VRC functions like an elevator, with one fundamental difference — VRCs are intended to move material loads, not people. They are regulated as a conveyor (under ASME B20.1) and not people-moving elevators, making them less costly to install and maintain than an elevators. VRCs have an enclosed platform that prevents loads from falling as they are lifted and lowered. This makes them far safer to operate than forklifts or scissor lifts. VRCs safeguard employees from injuries incurred while transporting items on staircases and deter the misuse of forklifts beyond their safe mast lift height limits. Flexibility VRCs are a versatile solution that can be installed next to mezzanines, in existing elevator shafts, or through floors, and they can also be installed outdoors. Vertical Reciprocating Conveyors (VRCs) stand out for their exceptional versatility and adaptability, opening a myriad of automated material handling opportunities. They seamlessly integrate with mobile robots and automated conveyor systems, or they can be manually loaded and unloaded. AGVs, AMRs and driverless forklifts can travel with the load on the VCR and continue travel when they arrive at the destination floor. Alternatively, they can efficiently transfer loads onto the VRC at one level, and then another system —whether it’s another AGV, AMR, or a different automated or manual material handling method — can take over at a different level. Furthermore, VRCs can effortlessly connect with automated horizontal conveyor systems, facilitating the smooth flow of
LOBO Systems supports No Falls Week 2024
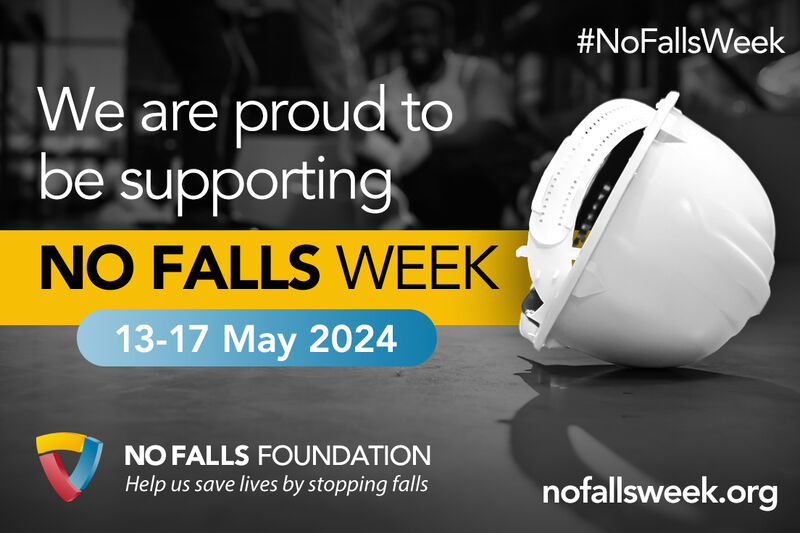
Safety in working at height environments LOBO Systems has announced its commitment to the No Falls Week Foundation’s upcoming event, No Falls Week, between 13th and 17th May 2024. With a resolute dedication to enhancing safety in working at height environments, LOBO Systems aligns with the Foundation’s mission to decrease the injuries stemming from inadequate training and inappropriate systems. No Falls Week, an initiative created by the No Falls Foundation, serves as a reminder of the critical importance of proper safety measures in preventing falls at worksites. This year’s event, scheduled for May 2024, aims to raise awareness and promote best practices for mitigating the risks associated with working at height. “Unfortunately, there has been a recent rise in workplace accidents in relation to falls,” said Robert Bokros, CEO of LOBO Systems. “Statistics show, 40 people lost their life due from a fall from height between 2022-2023, with the added statistic of 30% of all workplace deaths were due from falls from height” Robert adds. “No one should leave for work and fail to return home, our mission here at LOBO Systems is to increase safety whilst working at height, while providing a bespoke advanced system that is cost-effective and efficient.” No Falls Week 2024 will feature a series of educational initiatives, interactive workshops, and informational resources geared towards equipping workers and employers with the knowledge and tools necessary to mitigate fall-related risks. By leveraging its expertise and innovative solutions, LOBO Systems will actively contribute to these efforts, reinforcing its commitment to advancing safety standards within the industry.
Plastics Industry association packs over 21k meals for charity at NPE2024
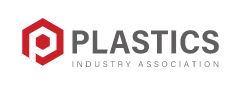
The Plastics Industry Association announced over 21,000 meals were packed at the first-ever community service event at NPE2024: The Plastics Show, exceeding the association’s goal of 20,000 meals. The event, in partnership with Alliance Specialties and Laser Sales and U.S. Hunger, saw over 70 volunteers, including NPE attendees and exhibitors, come together to make a difference in the fight against hunger. All meals were donated to Orlando’s Second Harvest Food Bank for distribution to the local community. “I’m thrilled we were able to surpass our goal for this event,” said Whitney Taveras PLASTICS’ Director of Industry Engagement (Equipment). “We are grateful for the amazing team of volunteers who packed over 21,000 meals for those in need. The plastics industry is dedicated to supporting local communities and this initiative was a true testament to that mission.” “We were able to accomplish an amazing act of service at NPE2024,” said Tony Demakis, President of Alliance Specialties and Laser Sales. “The event brought people together from across the plastics industry to serve others and make a difference for people in need in the local Orlando area. I’m so proud we exceeded our goal for this event and am thankful to PLASTICS and to all the volunteers.” “We are so grateful to the Plastics Industry Association for choosing to make an impact through U.S. Hunger,” said U.S. Hunger CEO Rick Whitted. “Together, we’ve packed over 21,000 meals for Central Florida families in need, illustrating the power of partnership and community spirit. This extraordinary act of generosity not only addresses immediate hunger relief but also underscores the profound impact we can achieve when industries unite for a common cause.” U.S. Hunger is a 501(c)(3) that has activated more than 950,000 volunteers to distribute over 160 million meals across the globe. We address hunger by engaging volunteers, educating on the root causes of food insecurity, and creating access to nutritious meals for low-income families.
Nucor Executive VP Douglas J. Jellison to Retire and Randy J. Spicer to be promoted
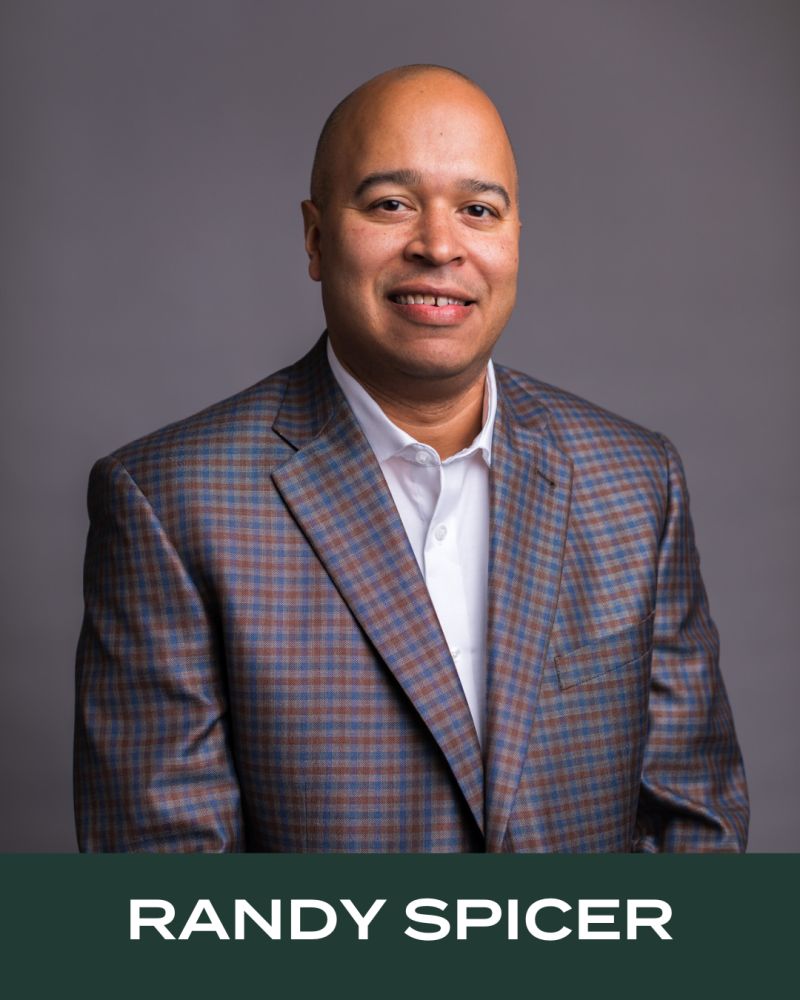
Nucor Corporation has announced that Executive Vice President Douglas J. Jellison plans to retire on June 8, 2024 after more than 33 years of service with Nucor. Jellison began his Nucor career in 1990 as Materials Manager at Nucor Bearing Products and has worked in various positions and businesses, including several controller and business development roles. Mr. Jellison served as General Manager of Nucor Bearing Products; Vice President and General Manager of Nucor Steel Seattle, Inc.; Vice President and General Manager of Nucor-Yamato Steel Company; President of Nucor Tubular Products; and President of Skyline Steel LLC. He was promoted to Executive Vice President in 2021. Leon Topalian, Nucor’s Chair, President and Chief Executive Officer commented, “I am incredibly grateful for Doug’s contributions over the last three decades. Throughout his career, he influenced a broad spectrum of Nucor’s businesses. He successfully led significant facilities, oversaw international operations, integrated and shaped acquisitions and spearheaded key enterprise strategies. His unyielding ability to drive change, overcome challenges and seek out the best outcomes is unparalleled. Most importantly, he lives Nucor’s culture in developing teammates and making everyone around him better. He is one of a kind. On behalf of all teammates, I want to thank Doug for his leadership and wish him a long and happy retirement.” Effective May 12, 2024, Randy J. Spicer will be promoted to Executive Vice President. Mr. Spicer began his Nucor career in 2004 as Accounting Supervisor at Nucor Steel Indiana. In 2006, he joined the start-up team at Nucor Steel Memphis, Inc. as Controller and subsequently served as Controller and Hot Mill Manager at Nucor Steel Gallatin LLC. He was promoted to General Manager of Nucor Tubular Products North in 2020 and elected to Vice President in 2022. He currently serves as President of Nucor Tubular Products. “Randy is a talented leader whose 20 years of Nucor experience help make him well-positioned to take on this challenging role. We look forward to his contributions to the executive leadership team,” said Mr. Topalian. “Doug’s retirement and Randy’s promotion are the product of the robust and thoughtful succession planning process that has been a top strategic initiative throughout Nucor.”
ALAN opens nominations for 2024 Humanitarian Logistics Awards
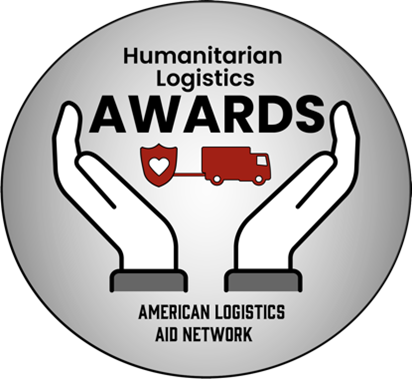
Annual awards honor extraordinary supply chain relief efforts The American Logistics Aid Network (ALAN) has officially opened nominations for its eighth annual Humanitarian Logistics Awards, and it’s asking for your help in identifying some of this year’s most deserving honorees. “There’s a lot of amazing work that the commercial supply chain community does to facilitate humanitarian relief efforts. But all too often, it goes unrecognized,” said ALAN Executive Director Kathy Fulton. “Our awards were created to spotlight the industry’s generosity and to honor its most compassionate companies and individuals. While ALAN works closely with a lot of these organizations to aid disaster relief efforts, there are still many deserving honorees that we won’t be made aware of – and able to honor – unless someone takes the time to nominate them.” Nominations (including self-nominations) can be made via ALAN’s website between now and June 28th. Winners will be announced this fall at the annual CSCMP Edge Conference. ALAN’s Humanitarian Logistics Awards are open to any logistics professional, academic, organization or department. They are awarded in four key categories, each of which can have multiple honorees: Outstanding Contribution To Humanitarian Logistics Employee Engagement Research And Academic Contributions Lifetime Achievement For a full list of rules and nomination criteria visit https://www.alanaid.org/wp-content/uploads/2018/06/HULA-2024-Nomination-Info-1.pdf Established in 2017, ALAN’s Humanitarian Logistics Awards recognize companies and individuals who exemplify the best that the supply chain profession has to offer by assuring that aid and comfort are rapidly delivered to communities in crisis. Previous winners have included United States Cold Storage, Flexport.org, CEVA Logistics, Palmer Logistics, ARPCO Transport Services, Scotlynn, Vector Global Logistics, Tucker Company Worldwide, Truckstop.com, Dr. Diego Vega, Professor Maria Bessiou, and the students on ALAN’s intern teams from the W.P. Carrey School of Business at Arizona State University, the University of Tennessee, Knoxville, and the University of Wisconsin Madison.
NFI strengthens Spin Master’s Supply Chain Solutions with New Mississippi Facility

Spin Master is a leading global children’s entertainment company that creates exceptional play experiences through its three creative centers: toys, entertainment, and digital games. Since its founding in 1994, Spin Master has grown from a small toy manufacturer to become the home of iconic brands, such as Rubik’s Cube, which is celebrating its 50th anniversary, the powerhouse preschool franchise, Paw Patrol, and the award-winning Toca Boca digital game. “This location is ideal and allows us to better service our retail customers,” said Steve Radewych, SVP of Supply Chain Operations at Spin Master. “We’re happy to continue working with NFI to strategically position our supply chain as business continues to grow.” NFI and Spin Master began their partnership in 2018 when Spin Master was looking to expand its supply chain throughout the Northeast. That same year, Spin Master acquired another company, which increased their need for faster solutions. NFI’s distribution team was able to help establish this East Coast presence in their Kutztown, Pennsylvania campus. As Spin Master’s business continued to evolve and expand, requiring additional flex space within the campus and the larger Lehigh Valley network, NFI was able to accommodate this overflow need. In early 2024, the relationship expanded further with the addition of an ideally located warehouse in Olive Branch, Mississippi, situated in the heart of the Central United States. While continuing to fulfill Spin Master’s distribution needs, NFI’s port services capabilities will also be utilized for drayage services inbound to the new distribution center. Additionally, NFI’s ILS team will manage the transfer of products from California to the new facility in 2024 and to Pennsylvania in 2025. “We’re really excited to expand our relationship with Spin Master for at least the next five years and utilize other services for this very strategic customer,” said Bill Mahoney, CCO and EVP at NFI. “We’ve celebrated five years of a great partnership and look forward to growing together.” NFI is committed to tailoring solutions for each unique customer and growing alongside the businesses it partners with. With expert knowledge, technology, scale, and dedicated people, NFI offers innovative, integrated, and customized solutions that span customer’s entire supply chain.
PLASTICS Industry Association releases 2024 Bioplastics Market Watch Report
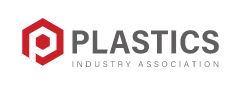
The Plastics Industry Association (PLASTICS) released its 2024 Bioplastics Market Watch Report today during an education session at NPE2024: The Plastics Show that ran from May 6-10th in Orlando, Florida, and attracted thousands of attendees from around the globe. “Bioplastics manufacturing is growing and consumers’ familiarity with bioplastics has increased, based on PLASTICS consumer survey,” said PLASTICS’ Chief Economist Dr. Perc Pineda. “Overall, the outlook for this industry is positive.” Among the highlights found in the 2024 Bioplastics Market Watch Report: Bioplastics manufacturing revenue is now projected to grow at a Compound Annual Growth Rate (CAGR) of 1.9% to reach $1.2 billion by 2028. The size of the U.S. bioplastics market will continue to vary depending on the different metrics used to quantify it. Nevertheless, the production capacity of bioplastics in North America, predominantly concentrated in the U.S., is estimated to account for 18.7% of the global production capacity. Although consumer perceptions of bioplastics continue to evolve, familiarity with bioplastics has increased significantly over a five-year period. In last year’s survey, 68% of consumers expressed a net familiar response, with just 14% indicating unfamiliarity. This marks a notable shift from the 2018 survey, where the net familiarity was 63%, with 31% indicating unfamiliarity. Competition within bioplastics manufacturing is expected to increase within and outside U.S. borders, driven by new materials development and new applications.
Marsh Bellofram re-organizes sales territories
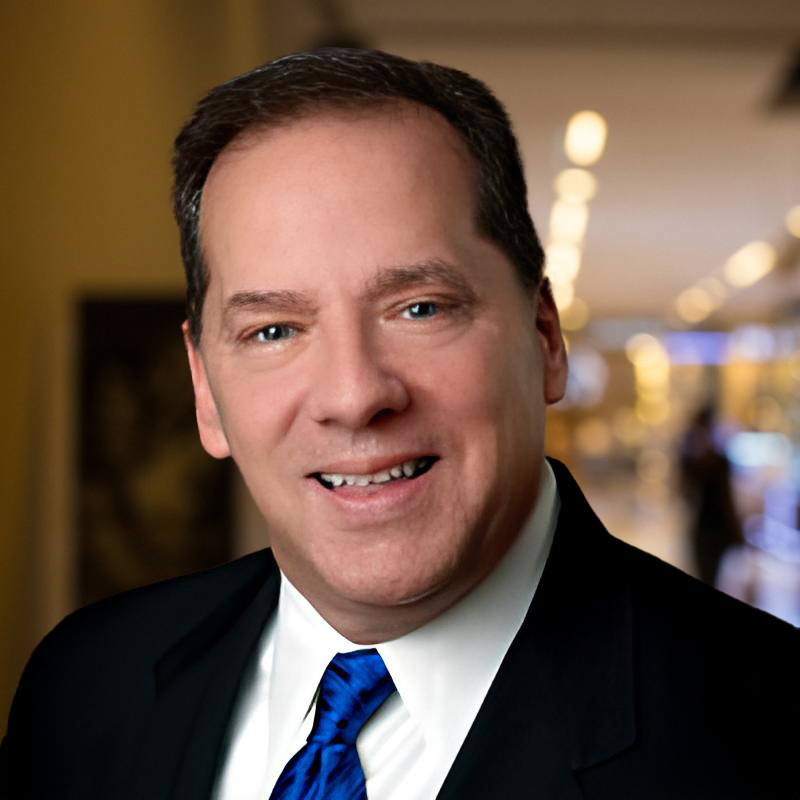
The Marsh Bellofram Group of Companies has announced a reorganization of its sales territories and a new, more holistic approach to sales across its 12 business units. As part of this effort, an existing manufacturers’ representative agency that already handles Marsh Bellofram products is expanding its territory, and a new rep group is being brought on. In addition, several internal territories are being reshuffled. EMPOWER Sales will expand its Marsh Bellofram territory to include Texas and Oklahoma. EMPOWER’s sales for Marsh Bellofram will be personally overseen by EMPOWER co-founder, principal, and general manager Bill Carroll. Carroll has nearly a decade of experience with Marsh Bellofram’s vast product lines, and will bring his expertise to these important expanded markets. EMPOWER’s main responsibility will be over the products of Automatic Timing & Controls (ATC), ATC Diversified Electronics (DEI), and Bellofram Precision Controls. In addition, Dan Weis and his company, Fluid in Motion (FIM), will represent these same products in three states in the upper Midwest for ATC/DEI and four states for Bellofram Precision Controls. Weis is a past sales manager for Bellofram Precision Controls in the same territory. His knowledge of the products and the market is expected to help customers achieve maximum impact from Marsh Bellofram solutions. Fluid in Motion has spent the past 35 years building strategic partnerships, industry knowledge, and product expertise to provide customers with a one-of-a-kind sourcing solution that is unparalleled in the industry. The sales re-organization brings other changes as well. Jon Staniszewski takes on a new role as sales manager for BelGAS (he previously served in the same position within Bellofram Precision Controls). Tony DeSimone will manage ATC/DEI for Illinois as well as all products in six other states. Meanwhile, longtime ATC/DEI sales manager Phil Storey remains covering the East Coast region down through mid-South states. Nick Kerpsack handles the same territory for Bellofram Precision Controls. A goal of the sales reorganization is to enable sales reps to sell broad product lines across multiple business units of the Marsh Bellofram family of brands, with support from product experts available to aid customers.
Compact light switch handle
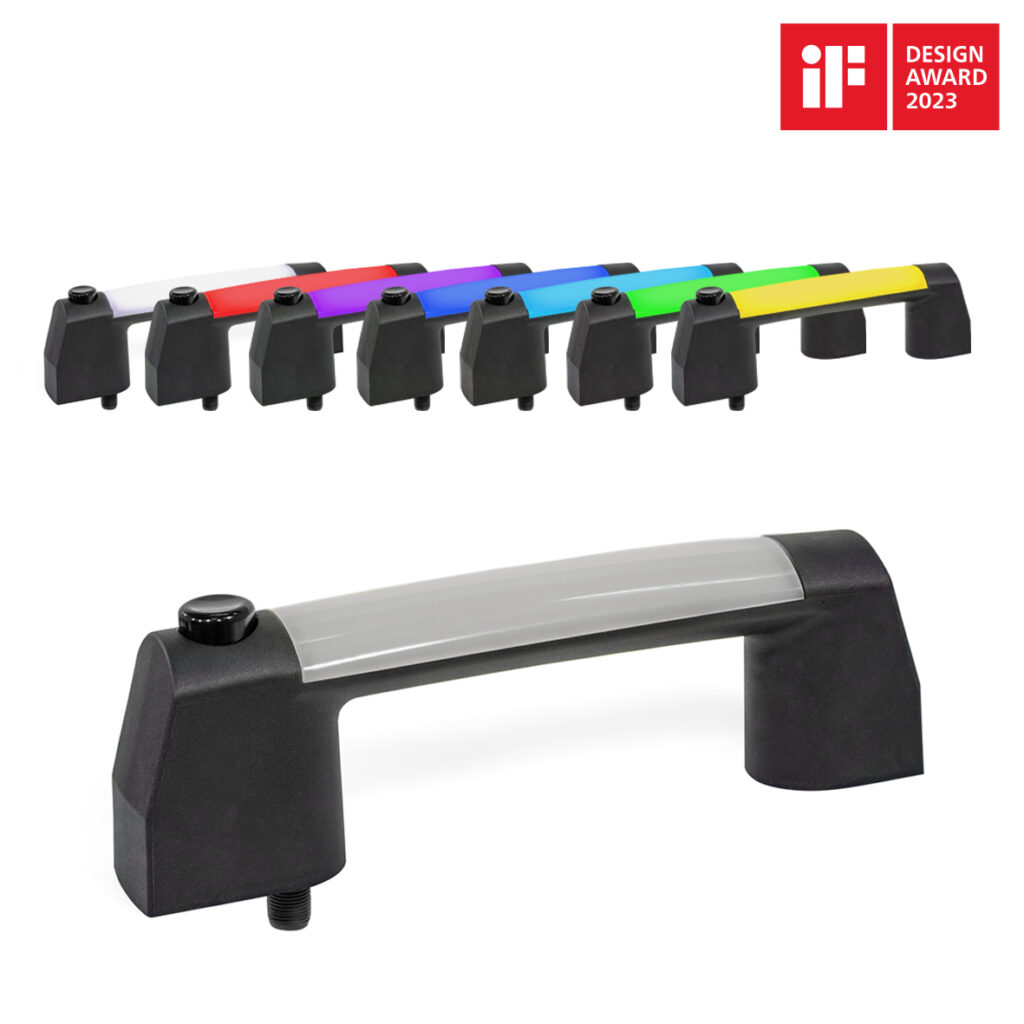
Signaling and indicator lights, switches, and buttons – elements that hardly any machine can do without. The new JW Winco cabinet U-handle EN 6284 integrates all these functions into a single, compact element. The U-handle is designed to enhance the operation of systems and machines. It features an integrated button and a large, colored, backlit area on the back of the handle. These elements can be used individually or in combination, providing a versatile tool for system control and process monitoring. The EN 6284 prioritizes safety in its design. The two-channel switch element, available in different contact configurations, enhances operational safety. It can handle a wide range of applications with DC and AC voltages from 24 to 240 volts and currents of up to 3 amperes, ensuring compatibility with various systems and machines. The light element on the back of the handle comprises a form-fitting diffusor made of robust polycarbonate that is tightly attached with an IP 67 protection rating. It homogenously diffuses the light produced by the interior LED module in a variety of colors and brightness levels depending on the activation of the 24-volt RGB matrix. This transforms the handle into a visible status indicator even from the side or from a distance – ideal for large systems operating with small crews. Depending on how it is wired, the light signal can indicate problems in the process, signal regular operation, or show that the system is ready to be opened. The colors and functions can be allocated individually. The extensive documentation and the video tutorial on the JW Winco website offer several possibilities. JW Winco has taken a holistic approach and provided the illuminated cabinet U-handle with a passive counterpart. The EN 6284.1 has the same shape and material (glass fiber- reinforced polyamide) as its active sibling, allowing for consistent machine design. Speaking of design: This combination of multifunctionality, design, ergonomics, and versatility was awarded the prestigious iF Design Award 2023.
Episode 484: Diving into the e-commerce transaction at Jay Group
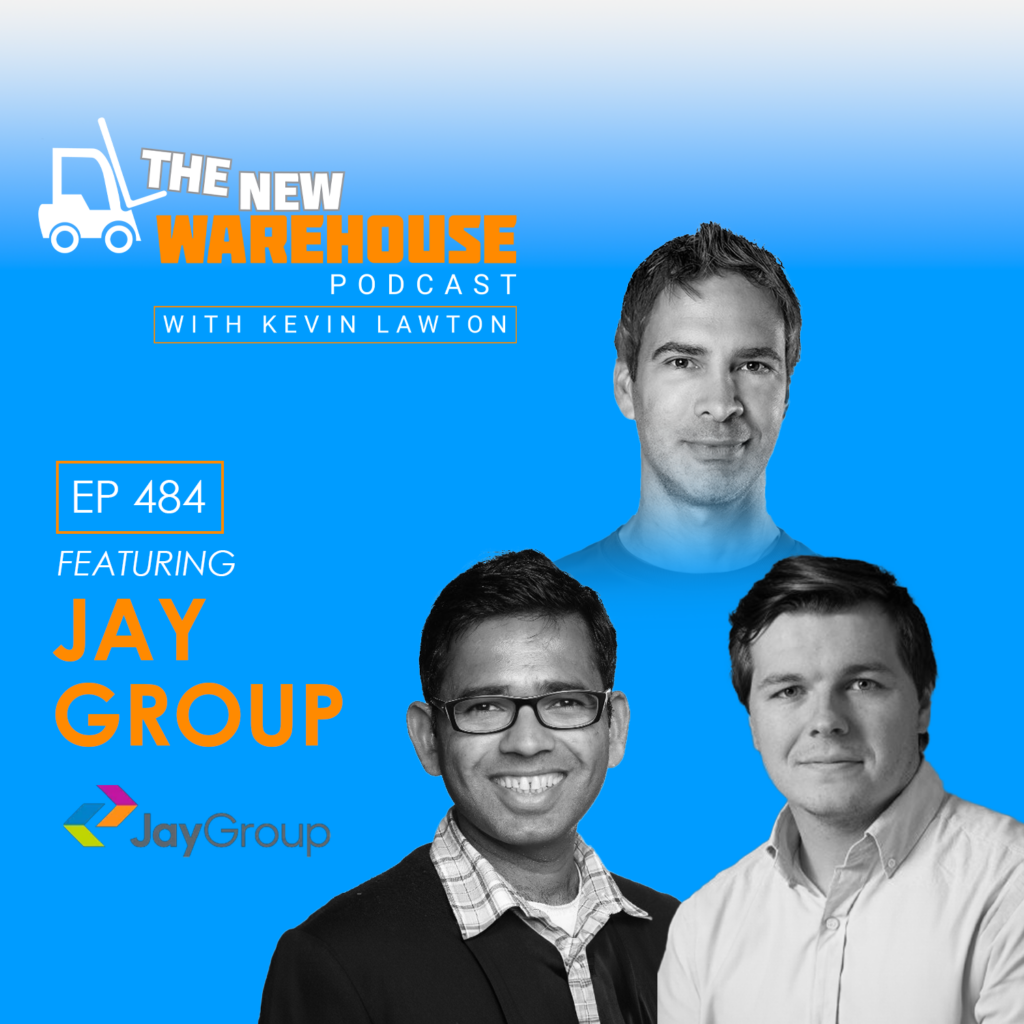
For The New Warehouse podcast, we had the pleasure of being on site and recording on location at Jay Group in Lancaster, PA. Kevin sat down with their President and COO, Blake Dudek as well as Ryan Millman of UnDigital and Akhilesh Srivastava of Fenix Commerce to discuss the end to end e-commerce order and how all of their solutions play a part to improve the customer experience and drive further value for brands. Giving the Consumer the Information They Need Consumers are constantly buying products online creating tons of data points but consumers desire to have as much information as possible to make their buying decisions easier. Fenix Commerce aims to capture this data and allow brands to leverage to help give these consumers the information they need. In the episode, Akhilesh discusses one example where the consumer is able to know exactly when to expect their package to arrive and they can get that information as early as on the Google search results page. Now, they have created value for the consumer at one of the earliest points. The data is being captured but then also flowing through the entire transaction feeding off of Jay Group’s shipping capabilities. This becomes your digital retail clerk and gives extra touch points for the consumer during the e-commerce transaction. Getting the Order to the Consumer When it comes to the physical process of getting the product to the customer, Jay Group steps in and handles the fulfillment process. With a long-standing history of servicing customers for multiple generations, they have built an outstanding fulfillment business that has its roots in promotional items. Fun fact, Blake’s Grandfather Jay started the company and was the one who came up with the idea for the Crown Royal bag. Focused on the customer experience, it is apparent that they are constantly looking to improve and provide additional value to their clients and their client’s customers. Part of that is partnering with smart technologies like Fenix Commerce and UnDigital to make that transaction a better experience for everyone involved. Creating a Personalized Unboxing Experience With more consumers focusing on online transactions and not going into physical stores, brands need to find a way to still give their customers a personalized shopping experience. They have the experience on their website but what happens when they get their product? In some cases, it may just be a product thrown into a plain brown box but some brands are upping that experience by making sure it is an actual experience and not something forgettable. UnDigital is providing a very personal and customized solution to help with this experience. Based on data known about these consumers and their buying habits they are able to provide customized labels, offers, and inserts into each individual package. From an operations perspective, the customized marketing material automatically comes out with the order so there is no manual intervention needed on the fulfillment provider side. Key Takeaways E-commerce shopping is going nowhere but consumers are still desiring a great experience. They want to know when they will get their order and they want to still have a great experience like they were going to the store to make a purchase. Tools can help you to drive value for all parties involved. In this discussion, all three solution providers are strong on their own but when they come together they can really elevate the overall consumer experience smartly and cost-effectively. A small cost per order can be an investment in immense long-term value. As you look at different tools and solutions to help provide more value to your customers, the cost may come into play but for small additional costs per order you can be creating a ton of long-term value. Retaining a customer for the long term is much better then losing them from a bad experience. The New Warehouse Podcast Episode 484: Diving into the E-commerce Transaction at Jay Group
U.S. Rail Traffic report for the week ending May 4, 2024
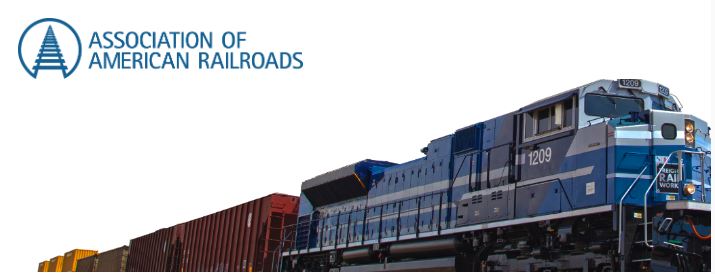
The Association of American Railroads (AAR) has reported U.S. rail traffic for the week ending May 4, 2024. For this week, total U.S. weekly rail traffic was 463,106 carloads and intermodal units, up 0.0 percent compared with the same week last year. Total carloads for the week ending May 4 were 213,410 carloads, down 5.1 percent compared with the same week in 2023, while U.S. weekly intermodal volume was 249,696 containers and trailers, up 4.9 percent compared to 2023. Seven of the 10 carload commodity groups posted an increase compared with the same week in 2023. They included petroleum and petroleum products, up 1,611 carloads, to 10,628; miscellaneous carloads, up 1,610 carloads, to 8,184; and grain, up 1,193 carloads, to 21,725. Commodity groups that posted decreases compared with the same week in 2023 were coal, down 15,611 carloads, to 46,928; nonmetallic minerals, down 1,615 carloads, to 32,965; and farm products excl. grain, and food, down 731 carloads, to 15,381. For the first 18 weeks of 2024, U.S. railroads reported a cumulative volume of 3,836,119 carloads, down 4.8 percent from the same point last year; and 4,536,912 intermodal units, up 8.7 percent from last year. Total combined U.S. traffic for the first 18 weeks of 2024 was 8,373,031 carloads and intermodal units, an increase of 2.1 percent compared to last year. North American rail volume for the week ending May 4, 2024, on 10 reporting U.S., Canadian and Mexican railroads totaled 324,302 carloads, down 0.9 percent compared with the same week last year, and 337,489 intermodal units, up 5.3 percent compared with last year. Total combined weekly rail traffic in North America was 661,791 carloads and intermodal units, up 2.2 percent. North American rail volume for the first 18 weeks of 2024 was 11,813,804 carloads and intermodal units, up 2.1 percent compared with 2023. Canadian railroads reported 94,801 carloads for the week, up 7.4 percent, and 76,026 intermodal units, up 5.7 percent compared with the same week in 2023. For the first 18 weeks of 2024, Canadian railroads reported a cumulative rail traffic volume of 2,896,564 carloads, containers, and trailers, up 0.6 percent. Mexican railroads reported 16,091 carloads for the week, up 12.9 percent compared with the same week last year, and 11,767 intermodal units, up 13.4 percent. Cumulative volume on Mexican railroads for the first 18 weeks of 2024 was 544,209 carloads and intermodal containers and trailers, up 10.5 percent from the same point last year. View reports here
Lucas Systems announced 100 Billion warehouse picks
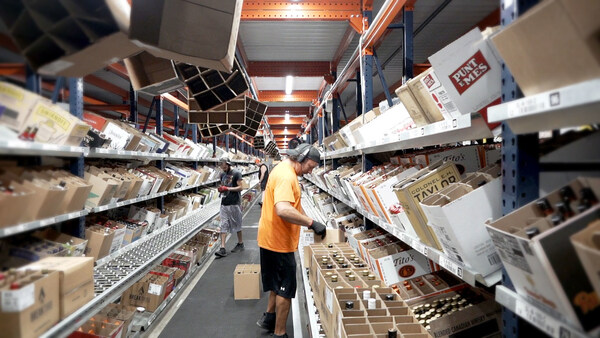
Credits continuous innovation of technologies centered around workers Warehouse workers made 100 billion warehouse picks using Lucas Systems software, according to an announcement today from Lucas Systems, a distribution center technology company. Lucas Systems, which provides software to workers in more than 400 warehouses across four continents, says the 100-billion milestone is a culmination of industry longevity combined with tens of thousands of workers using its sophisticated speech-recognition and optimization software, powered by Jennifer™. Jennifer™ provides in-the-moment voice and visual guidance for warehouse tasks such as picking, replenishment, putaway, loading, and cycle count. “Workers make nearly 17 million picks each day with Lucas technologies,” says Lucas Systems Founder and CEO Rick Brown. “For 26 years, we’ve been helping to improve the quality of work-life for warehouse workers while dramatically boosting productivity, accuracy, and safety.” Warehouse workers value technology so much that they are willing to make important trade-offs to access it. According to a recent market study commissioned by Lucas Systems, which polled 500 U.S. on-floor warehouse workers, nearly three out of four on-floor workers would consider a pay cut at another company for an opportunity to use technology if it helps them in their job. Lucas Systems says its technologies gain favor for key reasons: No voice training required with industrial grade dual engine speech recognition Flexibility for workers to work in their own language with more than 30 languages available Multimodal worker interaction using voice, visual and scanning options Built-in optimization that can reduce worker travel by up to 50% while improving picking accuracy Software that runs on a wide variety of Android devices including tablets, wearable devices and mobile computers Reaching 100 billion picks required adaptability, says Lucas executives. “Innovation has been key to our longevity and growth,” Brown says. “We have been at the forefront of leading change in the distribution industry, which is now occurring at an accelerated rate.” Notable market shifts have significantly raised the bar for technology companies. These changes include growth in direct-to-consumer volume and high expectations for near perfect accuracy and shorter order-to-delivery times. Henry Schein has benefitted from Lucas’ commitment to continuous innovation. “In pursuit of consistently fulfilling our customer commitment, we forged a partnership with Lucas Systems in 2006,” said Ed Igrisan, Vice President, U.S. Distribution West, South, and Canada, Henry Schein. “Since implementing Lucas Systems’ voice and AI optimization technologies, Henry Schein has achieved significant growth, exceeding $12 billion in revenue. This strategic partnership has helped to transform our distribution centers, driving substantial improvements in worker productivity, operational agility, and overall satisfaction for both our Team Schein Members and customers.”
PTDA Foundation launches student and employee scholarships
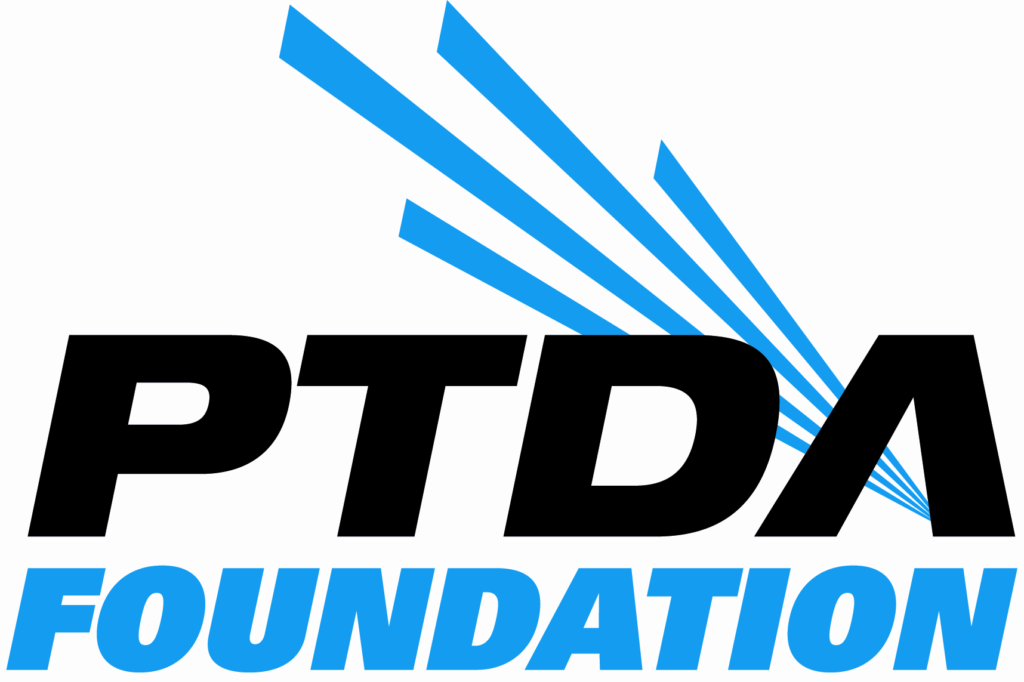
The demand for skilled professionals in the power transmission and motion control (PT/MC) industry has never been more urgent. Committed to helping PT/MC employers nurture current and upcoming talent, the PTDA Foundation has launched two new scholarships to empower individuals who are passionate about pursuing PT/MC careers. “By providing financial support by way of scholarships, we want to build the robust pipeline of talent needed to foster employee growth and ensure the industry has the expertise it needs to thrive,” says 2024 PTDA Foundation President Matt Pavlinsky, Applied Industrial Technologies. “We believe targeting individuals with a demonstrated interest or commitment to pursuing work in PT/MC-related fields will help ease some of the burden of employers struggling to find qualified candidates.” The new student scholarship provides financial support to those who are considering or currently pursuing an education in PT/MC related fields. Applicants must be currently enrolled or recently accepted as a student at a trade school, technical school, community college or four-year university in fields relevant to the PT/MC industry. Up to five $3,000 scholarships will be awarded. The employee scholarship provides financial support to individuals currently employed full-time at a PT/MC distributor or manufacturer in North America. Applicants must also be currently enrolled or recently accepted as a student at any level at a trade school, technical school, community college or university, and must be studying PT/MC related fields in engineering, technology or business. Up to five $2,500 scholarships will be awarded. Applications for both scholarships can be found online at ptworkforce.org/scholarships The application deadline is July 1, 2024. Awardees will be selected in August.