SEARCH OUR SOURCE DIRECTORY
Is your Dealership equipped for the Future of Customer Experience?
Back in March of this year, after attending and exhibiting at this year’s record-breaking ProMat Show in Chicago, one thing…
Tech-savvy managers: The cornerstone of modern warehousing
Warehouses are evolving into hubs of cutting-edge technology, but without the right leadership even the best tools can fall short.…
The Isolation Process: A powerful path to more sales
Psst — hey — c’mere! I’ve got a secret to tell you…Sometimes prospects will stall you, sometimes they will lie…
GAAP out—Free Cash Flow in
I know I am as guilty as anyone of stating that CASH IS KING. Must have included that statement at…
Three things you must know about selling to younger buyers
Salespeople are getting older. Buyers are getting younger. You have a disconnect. In raw terms, the average age of a…
Revolutionizing Distribution with AI
AI, in its next generation, could be a step-change for distribution, not so much on its evolutionary path, but with…
Gebrüder Weiss renews scholarship program for Rutgers Business School
Gabriel Godoi De Lima, Jun Pak, and Nikhil Walia are 2025 scholarship recipients Gebrüder Weiss has announced a five-year undergraduate scholarship…
PTDA welcomes MANTIS Conveyor Products and Allen Bearings & Technologies Limited
The Power Transmission Distributors Association (PTDA) welcomes new manufacturer member MANTIS Conveyor Products and welcomes back distributor member Allen Bearings &…
PLASTICS Economic Analysis: Steady Consumer Spending Signals Growth for Plastic Packaging
Plastics Industry Association (PLASTICS) Chief Economist, Dr. Perc Pineda, has released a new U.S. economic analysis, highlighting steady consumer demand…
U.S. rail traffic reports for the week ending May 31, 2025
The Association of American Railroads (AAR) has reported U.S. rail traffic for the week ending May 31, 2025. For this…
Final Speakers announced National Forklift Safety Day 2025
Tuesday, June 10, 2025 | 9:00 AM – 11:00 AM Live Streamed Event at the National Press Club – Virtual…
U.S. Army Reserve kicks off exercise at Port of Long Beach
Operation Mojave Falcon trains soldiers to support large-scale deployments The U.S. Army Reserve is partnering with the Port of Long…
Free Magazine & eNewsletter
Printed Monthly Magazine
Published monthly, Material Handling Wholesaler offers feature columns and special coverage of relevant industry issues and products.
Digital Monthly Magazine
Published on the fourth Thursday of each month, Material Handling Wholesaler offers feature columns and special coverage of relevant industry issues and products.
Material Handing Wholesaler Weekly Newsletter
Our Weekly newsletter is emailed every Tuesday and contains the latest Industry Events and People News, Source Directory, and important Industry Links.
Forklift International Weekly Hot Sheet Newsletter
Published every Monday morning with the latest material handling equipment
available for sale.
Plezia named Port of Long Beach Engineering Managing Director
The Port of Long Beach has promoted Suzanne Plezia, P.E., to Managing Director of Engineering Services to succeed Sean Gamette,…
Ati Motors introduces the Sherpa 10K: High-capacity Autonomous Tug designed for demanding industrial workflows
New heavy-duty vehicle sets a new standard for autonomous material movement Ati Motors, a global provider of autonomous robotics and…
NY/NJ Foreign Freight Forwarders & Brokers Association Announces 2025 “Captain of Industry” Award Recipient
Charlene Riley to be Honored at June 25th Dinner Cruise Co-Hosted with the Traffic Club of New York The NY/NJ…
MHEFI awards record $278k in scholarships to Future Supply Chain Leaders
The Material Handling Education Foundation, Inc. (MHEFI) has announced it has awarded an unprecedented $278,000 in scholarships to 71 exceptional…
Herc Holdings completes acquisition of H&E Equipment Services
Herc Holdings Inc. has announced that it has completed its acquisition of H&E Equipment Services, Inc. “The acquisition of H&E…
ASSP honors five visionaries for revolutionizing worker safety
The American Society of Safety Professionals (ASSP) has bestowed its highest honor – the Society’s Fellow distinction – upon five…
Arnold Magnetic Technologies highlights the PLASTIFORM® High Energy Flexible Magnets, Made in America
Arnold Magnetic Technologies Corporation (Arnold), a subsidiary of Compass Diversified and a global manufacturer of high-performance magnets and precision thin…
Signode to Feature New Innovations and Complete Packaging Solutions at PACK EXPO 2025
Signode is highlighting its integrated solutions and new packaging innovations at PACK EXPO 2025. Held at the Las Vegas Convention…
Exide Technologies to present latest energy storage solutions for data center applications at Data Centre World Frankfurt
Exide to exhibit at Data Centre World Frankfurt on 4th and 5th June Comprehensive energy storage solutions and…
ELOKON launched a dual-layered safety system for maximum forklift and pedestrian protection – ELOshieldAI
New solution combines ultra-wideband (UWB) proximity detection and AI-powered, tagless vision technology to prevent collisions in high-risk industrial environments ELOKON,…
AMT launches Flexible CRX-Based Collaborative Palletizing Solution
Applied Manufacturing Technologies’ FANUC CRX-30iA-based system features a custom user interface, compact design, and sub-12-month ROI for flexible case handling…
Advance Lifts highlights Palletizer & Self Leveling Lifts
Advance Lifts, a North American manufacturer of industrial scissor lift tables and dock lifts, highlights its comprehensive range of palletizer…
Episode 596: Warehouse orchestration with AutoScheduler
In this episode of The New Warehouse Podcast, Keith Moore, CEO of AutoScheduler AI, shares valuable insights into how warehouse…
Episode 595: Warehouse automation solutions without the sales pitch
Welcome to this episode of The New Warehouse Podcast, featuring Allison Myers and Dan Gilmore from MHI’s Solutions Community. MHI is a leading…
Episode 594: A skinny pallet jack, big savings, and the power of innovation
In this episode of The New Warehouse Podcast, Kevin chats with Dan Betz, Executive Vice President of Operations at Andrews…
Junttan selects Volvo Penta as engine partner in next-generation equipment
Junttan has partnered with Volvo Penta to power its next-generation machines, starting with the new DR5 drilling rig uniting shared…
Felling Trailers delivers custom mobile solution for FireLake Manufacturing’s incinerator unit
FireLake Manufacturing of Hutchinson, MN, manufactures incinerators and crematoriums, serving the medical, veterinary, and law enforcement sectors. FireLake’s product line…
Choosing the right strapping materials for your product
When it comes to securing your products for shipment, selecting the right strapping materials is critical. This decision impacts not…
Our Current Issue
Magazine & eNewsletter
Our magazine is published and mailed monthly, Material Handling Wholesaler offers feature columns and special coverage of important industry issues.
Weekly Newsletter – Get the latest industry events and people news in this weekly e-newsletter as well as direct access to Wholesaler’s Source Directory and link.
Current Supplements
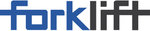
Back in March of this year, after attending and exhibiting at this year’s record-breaking ProMat Show in Chicago, one thing…
Warehouses are evolving into hubs of cutting-edge technology, but without the right leadership even the best tools can fall short.…
Psst — hey — c’mere! I’ve got a secret to tell you…Sometimes prospects will stall you, sometimes they will lie…
I know I am as guilty as anyone of stating that CASH IS KING. Must have included that statement at…
Arnold Magnetic Technologies Corporation (Arnold), a subsidiary of Compass Diversified and a global manufacturer of high-performance magnets and precision thin…