NRF statement on proposed Warehouse Safety Bill
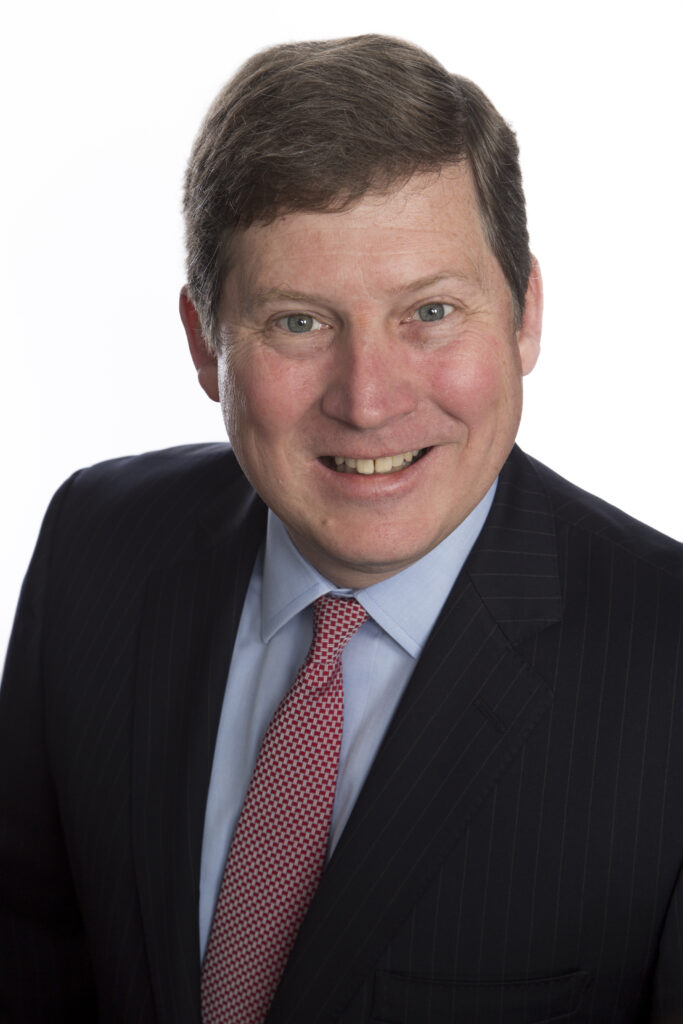
The National Retail Federation today issued the following statement from Executive Vice President of Government Relations David French after members of Congress announced plans to introduce the “Warehouse Worker Protection Act.” “Data from the Occupational Safety and Health Administration (OSHA) have consistently shown that warehouse workplaces are safe workplaces. NRF member companies are continually investing in better practices, more modern equipment, and innovative employee engagement efforts to make these workspaces as safe as possible. “Despite that, this legislation would overturn decades of employment and labor law, erode employers’ private property rights and unjustifiably expand the federal government’s intrusion into American workplaces. “The bill mandates that OSHA promulgate an ergonomics standard, despite a 2001 law passed by bipartisan majorities in both houses of Congress that permanently barred OSHA from regulating ergonomics for numerous reasons, including the impossibility of separating workers’ pain from away-from-work life activities, a lack of clear scientific evidence to support such a standard and the massive costs. There is no new rationale for undoing Congress’ prohibition, and NRF strongly opposes this bill.” As the leading authority and voice for retail, NRF will continue to advocate for workplace rules that promote workplace flexibility and economic growth.
NORD introduced gear motor QR codes
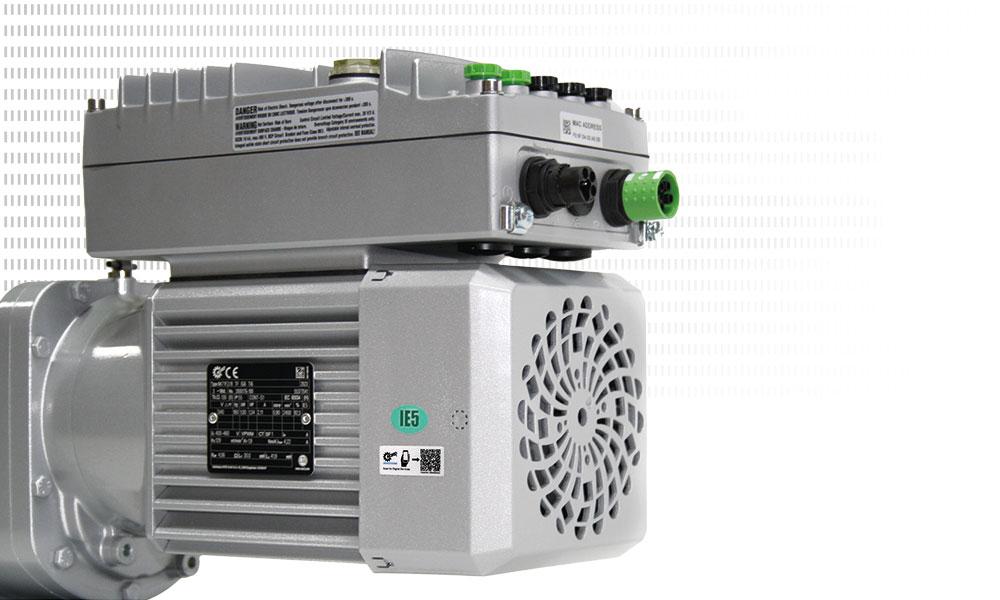
NORD’s new gear motor QR codes link to convenient digital services for unit documentation, service and sales contact requests, and order information. If you’ve recently purchased a NORD DRIVESYSTEMS gear motor, you may have noticed a new sticker with a QR code located on the unit. Quick Response (QR) codes can store a wide range of data and enable the user to access information almost instantly. These stickers are a new development in NORD’s expansive digital services and provide users quick access to product specifications, documentation, and service requests on-the-spot via their mobile device. The codes can be scanned using a photo app or QR code app and will bring the user to NORD’s digital service webpage with their respective country’s language and contacts. NORD’s existing digital services include the Documentation Center, a resource for product-specific manuals and literature, the Spare Parts Shop for fast online ordering of stock components and replacement parts, and the myNORD Customer Portal, a comprehensive tool that allows users to select and configure their NORD drive systems online. The QR codes extend these services with a defined service request contact form, as well as the ability to easily contact local sales and service departments. When a unit’s code is scanned, the form will automatically populate with the specified unit’s equipment/serial number and the proper documentation including spare parts list, manuals, Declaration of Conformity (DoC), 2D/3D drawings. Order details can also be accessed, saving time and ensuring the correct unit information is being referenced. QR code stickers are now in use at NORD USA’s four facilities in Waunakee, Wisconsin, Corona, California, Charlotte, North Carolina, and McKinney, Texas. On all gear motors and solo motors, the sticker is located on the motor cooling fin near the nameplate or on the terminal box if the motor is smaller than case Size 80. For gear units only, the sticker is located under the nameplate and for units with variable frequency drives, the sticker is located underneath the nameplate.
Longtime safety expert honored as ASSP Fellow
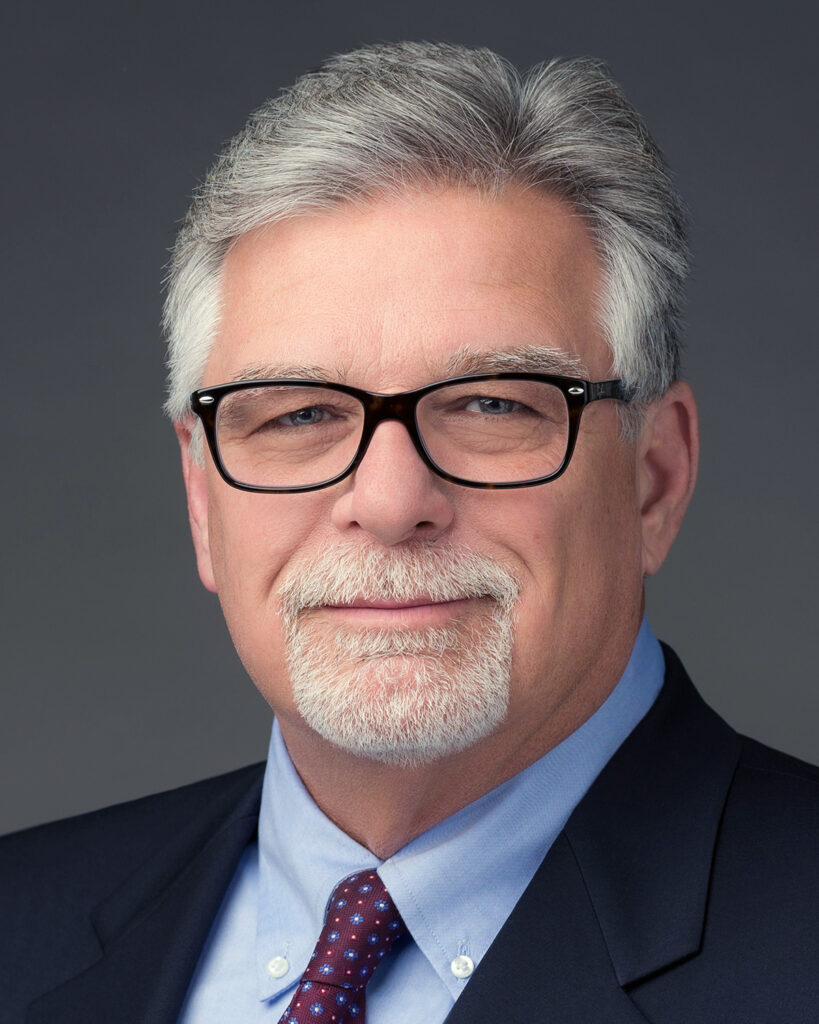
The American Society of Safety Professionals (ASSP) has bestowed the honor of Fellow on Daniel G. Hopwood, who has made significant contributions to the occupational safety and health profession for decades. He is the 2024 recipient of the Society’s highest honor, becoming the 147th Fellow since the world’s oldest professional safety organization was founded in 1911. “ASSP Fellows are an elite group of influential safety leaders who have played key roles in improving workplace environments as well as the safety and health profession overall,” said ASSP President Jim Thornton, CSP, CIH, FASSP, FAIHA. “Dan is a highly respected expert who has broadly helped prevent injuries, illnesses and fatalities on the job.” Hopwood, M.P.H., CSP, SMS, ARM, CBCP, FASSP, is vice president and director of risk control field services at Sompo, North America. An ASSP member since 1978, Hopwood has worked throughout his distinguished career as a risk manager, instructor, keynote speaker, author, technical expert and occupational safety and health advocate. He is an expert at developing methodologies for crisis management and business continuity planning. He also serves on the board of directors for the Board of Certified Safety Professionals. “As a senior member of our team, Dan develops safety programs, conducts incident investigations and provides extensive safety and health training,” said Christine Sullivan, CSP, ARM, former ASSP president and current executive vice president and head of risk control at Sompo. “He is a true collaborator who is always willing to share his expertise with colleagues and mentor industry newcomers.” Hopwood has taught undergraduate and graduate safety courses for 25 years, including time at Cuyamaca Community College, San Diego City College and San Diego State University, all in California. As a result, he has advanced the workplace safety and health profession and has profoundly impacted the careers of many students. Hopwood has guided thousands of professionals through his many writings and by leading dozens of educational and training sessions at national conferences and seminars. He authored the book “Safety & Health Management: Essential Considerations for Human Resources and Allied Professionals” and co-authored “Workplace Safety: A Guide for Small and Midsized Companies.” He also has written chapters in several other books and has been published in more than 25 journals, magazines and professional publications. As an ASSP volunteer leader, Hopwood has served at the local, regional and Society levels. He is past president of the San Diego Chapter and former Region I vice president. He was the San Diego Chapter Safety Professional of the Year in 2012 and earned ASSP’s Charles V. Culbertson Outstanding Volunteer Service Award in 2017. “Dan is a constant advocate who serves our profession with impartiality and a moral compass that makes the world a better place,” said Jose Perez, CSHM, CIT, SMS, OHST, CHST, an area director in ASSP Region I. “Many have experienced the value he brings to the humanity of our profession through his equitable and inclusive leadership. His exemplary approach and positive influence make others feel welcome, visible and heard.”
OZ Lifting launches stainless steel lever hoist
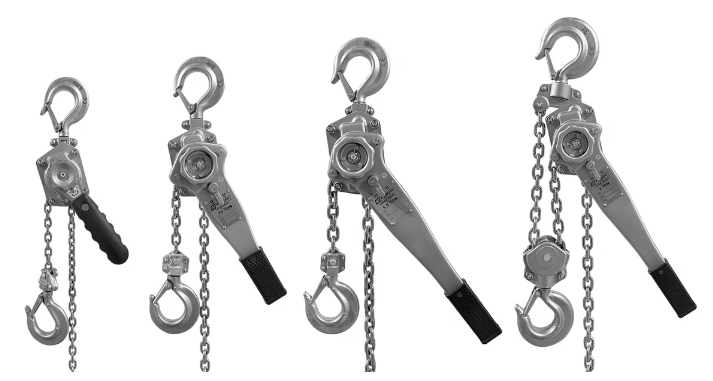
OZ Lifting Products LLC has launched North America’s first stainless steel lever hoist, in 0.25- to 3-ton capacities. The hoist is available in 0.25-, 0.75-, 1.5-, and 3-ton versions; and each one can be provided with 5 ft., 10 ft., 15 ft., and 20 ft. lengths of lift, but custom rigging is available. It joins three other products — chain hoist, push beam trolley, and beam clamp — in the company’s Type 304 stainless steel range. It is also the fourth lever hoist, in addition to an industrial model, in 0.25- to 9-ton capacities; a premium version, in 0.75 to 9-ton; and, in the same capacity range, the dynamometer-equipped Dyno-Hoist. The stainless steel version closely mirrors the industrial product but is designed for more demanding sectors. The benefits of Type 304 are many and varied. It is widely accepted as the most versatile stainless steel, which is why it is commonly the manufacturing product of choice for use in demanding markets. The smooth, non-porous surface makes it easier to clean and maintain, which is especially important in environments where hygiene is a concern. Most notable however for excellent corrosion resistance, Type 304 stainless steel is lauded by many end-user sectors, including water treatment; pharmaceutical and food production; and mining. It is suited though to any environment that has corrosion issues, such as those around saltwater, rain, snow, or high humidity. Steve Napieralski, president at OZ Lifting, said: “Our stainless manual hoists have been very successful, so it was a natural next step to extend the line to include lever hoists. The hoist offers increased resistance to wear and tear, meaning it has a longer lifespan, reducing replacement costs, even when subject to repeated use. “This capacity range will likely suit most applications but, as always, we will listen to the supply chain, and if we get inquiries for larger sizes, we will certainly add them.” The hoists are lightweight and easy to operate; they are ideal for use in confined and enclosed spaces, while the effort required on the lever to lift a full load is 20.20 lbs., 28.10 lbs., 41.50 lbs., and 42.70 lbs. respectively. Lever hoists can be used for lifting or pulling but, like the standard line, they will most commonly be found in tensioning applications. Similar to OZ Lifting’s stainless steel trolleys and manual chain hoist, the lever hoist features food-grade grease, that meets NSF H1 standards, for end users looking for tensioning or lifting in areas that cannot have any contamination around food. The way the hoist is configured means that the brake is not near where the gearing is located. The owner’s manual outlines proper maintenance procedures. Other key features include a freewheel for quick adjustment; 360-degree handle rotation; and a Weston-style brake system. They will be supplied with forged hooks and stainless steel riveted identification tags. Napieralski also pointed to the twin-pawl design; sealed roller bearing; and rubber grip. He added: “We anticipate interest in individual units and multiples thereof. We do a fair amount of custom rigging on many of our products so we will be prepared to quickly meet requests for custom lengths. We will continue to bring innovative products to the market; we have several on the horizon.” The stainless steel lever hoist will be available for delivery to OZ Lifting’s network of regional dealers in June.
Hyster-Yale Group provides students with real-world AI experience in 2024 Kellogg Design Challenge
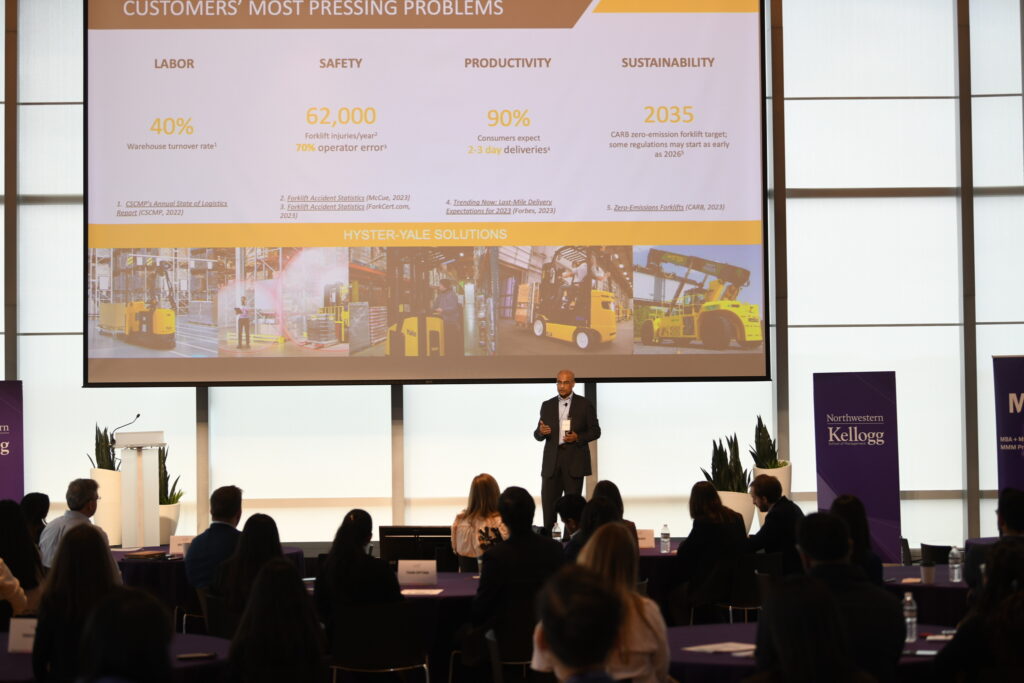
Representatives from HYG and Northwestern University judged submissions from 16 teams of MBA and engineering students in multi-stage innovation competition Representatives from Hyster-Yale Group joined Northwestern faculty from the Kellogg School of Management and Segal Institute for Design Innovation and industry leaders like IDEO, PwC and IA Collaborative to facilitate the 2024 Kellogg Design Challenge. As the platinum sponsor, Hyster-Yale provided the theme for this year’s competition, AI x Design, which emphasizes the use of artificial intelligence to enhance the design and development process of new products, potentially reducing the time and effort involved by up to 50%. “Our focus is fostering innovation to push forward how materials are moved and help address the most pressing challenges facing supply chain operations,” says Ed Stilwell, Chief Technologist of Innovation, Hyster-Yale. “As we pursue that mission, the Kellogg Design Challenge is an outstanding opportunity to tap into some of the brightest young minds. Not only is this an important step to harnessing the power of leading-edge technology to drive change, it supports our approach of hiring the best talent and developing them into the future leaders of tomorrow.” Approximately 90 graduate students from Northwestern, Parsons, Carnegie Mellon, University of Chicago, Imperial College London, Cornell, UCLA and Dartmouth competed in the multi-stage event. Throughout the month of April, the competition included a Q&A with Hyster-Yale innovation representatives, workshops with innovation partners and the main Kellogg Design Challenge Day, featuring presentations from all competitors, speaker sessions and networking opportunities. Students from Cornell University Johnson School of Business won first place for their exceptional “EZ Requirement Assistant,” showcasing a deep understanding of user needs and innovative problem-solving, while also demonstrating the potential for real time and cost savings. In addition to awarding cash prizes to the first, second and third place teams, this year’s edition included a bonus prize for the most human-centric and inclusive design, which was awarded to students from Northwestern Kellogg. Members of the Hyster-Yale innovation team, together with the other competition judges, evaluated the semi-finalists on their design research, solution design, business impact and innovation pitch. “We want to thank the Kellogg Design Challenge team, and the graduate students from reputed universities for their outstanding engagement in making the Kellogg Design Challenge an incredible success,” says Dr. Gopi Samayajula, Senior Vice President of Global Product Development, Hyster-Yale. “This year’s competition pushed them to build around the challenges of tomorrow’s technology-driven solutions and make a real impact on the design and development process of new products by leveraging emerging AI technologies – potentially reducing the effort involved by up to 50%.” The Hyster-Yale innovation team focuses on developing advanced technologies for materials handling operations and accelerating the adoption of these technologies in commercial applications. Between the Yale® and Hyster® lift truck brands, the company’s deployed emerging technology base includes over 500 automated lift truck units and more than 6,000 lift trucks with the company’s patented operator assistance technology. In addition to the Kellogg Design Challenge, Hyster-Yale has several longstanding collaborations with academic and career development programs across the country. The company’s Innovation Lab operates at the Shiley-Marcos Center for Design and Innovation at the University of Portland, and is a model for other industry-university cooperation, immersing students in real-world engineering and product development projects. The company also works with colleges in communities where it operates, such as East Carolina University, Berea College, Eastern Kentucky University and the University of Kentucky, to sponsor senior capstone projects and provide mentorship and internship opportunities. Hyster-Yale also serves alongside companies such as Lockheed Martin and Lexmark on the Eastern Kentucky University engineering advisory council.
Supervisory Board Extends CEO Rob Smith’s contract
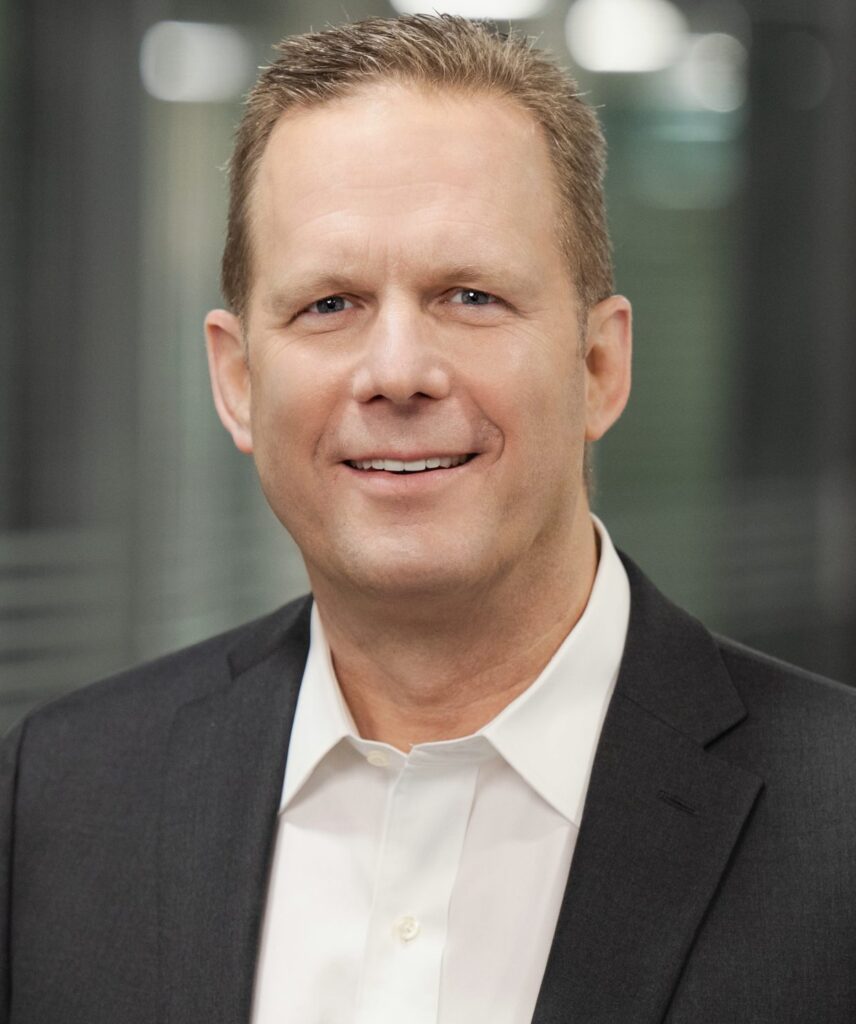
Contract extended by five years until end of 2029. Hans Peter Ring, Chairman of the Supervisory Board: “Under Rob Smith’s proven leadership we will open the next chapter of the success story of KION.” The Supervisory Board of KION GROUP AG has extended Chief Executive Officer Rob Smith’s (58) contract by five years, ensuring his leadership until December 31, 2029. This decision underscores the Board’s unwavering confidence in Smith’s strategic vision, operational expertise, and ability to drive sustained value for the shareholders, customers, and employees. “On behalf of the Supervisory Board I am glad that we can continue our trusted relationship with Rob Smith. I am confident that under Rob‘s proven leadership we will open the next chapter of the success story of KION”, says Hans Peter Ring, Chairman of the KION Supervisory Board. “I would like to thank the Supervisory Board for placing trust in me. I look forward to continuing to lead KION Group’s path to sustainable and profitable growth”, says Rob Smith. “Together with our team of the Executive Board and our more than 42,000 employees around the world, we want to shape the future of supply chains globally. We will keep delivering on our business priorities and seize the opportunities offered by our markets and technological innovation.” Before joining KION, Rob Smith was President & CEO of the publicly listed Finnish group Konecranes, a leading international manufacturer of industrial cranes and container port automation. From 2013 to 2019, he was Senior Vice President & General Manager Europe, Africa and Middle East of the global agricultural machinery company AGCO Corporation. Prior to that, he held management positions in automotive supply and capital goods companies in the U.S., France and Germany. Smith holds a BSE in Systems Engineering from Princeton University, an MBA in International Operations & Finance from the University of Texas at Austin – Red McCombs School of Business. He earned his Diplom-Kaufmann and Dr. rer. pol. degrees from the WHU – Otto Beisheim School of Management in Koblenz, Germany and wrote his dissertation on Global Supply Chain Performance and Risk Optimisation.
Global Shop Solutions Ilya Dynkin reaches 25-year milestone
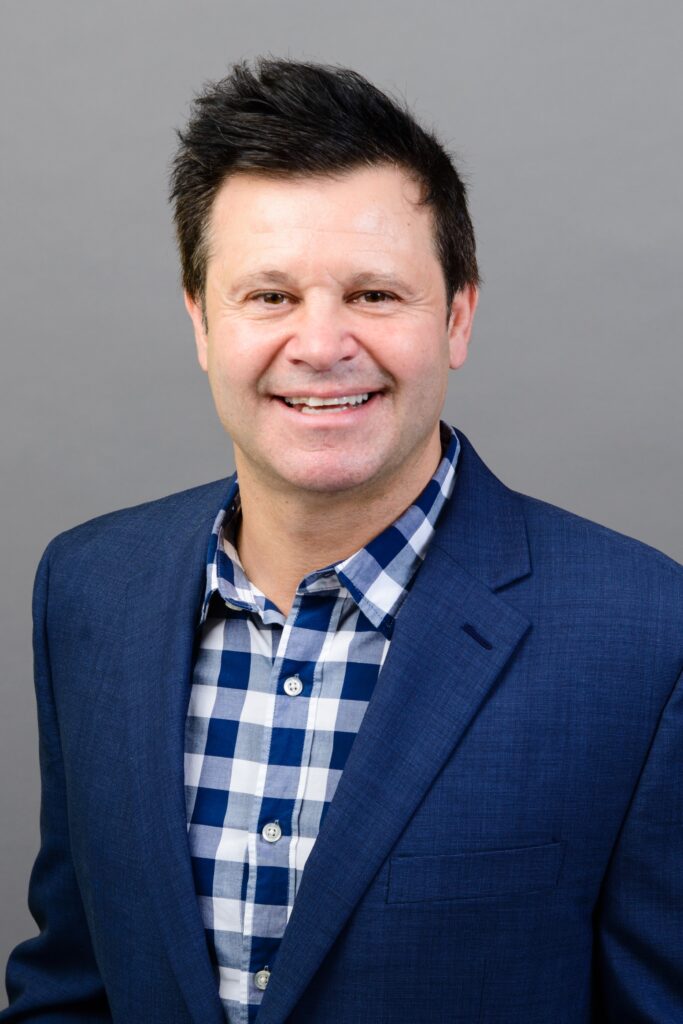
Working at the same company for 25 years is a rare occurrence these days. Global Shop Solutions has announced the latest addition to the Quarter Century Club, Ilya Dynkin, VP of Sales. When Dynkin joined Global Shop Solutions early in his career, he had no experience with ERP or manufacturing software. What he did have was enthusiasm, motivation, and the ability to find and win new opportunities, bringing in new customers. The love and care he shows to each person he works with isn’t just in the sale – it’s in the long-term relationships he builds. “We knew from the start we had a special person in Ilya because of the way he connects with manufacturers on a personal basis, understands their problems, and demonstrates how ERP software can correct them,” says Dusty Alexander, President and CEO of Global Shop Solutions. “He truly enjoys his work, and his spirit and enthusiasm for helping our customers simplify their manufacturing rubs off on all who work with him.” Dynkin prides himself on demonstrating how ERP software can help transform manufacturing companies and improve their processes. What he finds most rewarding is when customers have enough faith in him and trust in the company to want to become a lifetime partner. “At Global Shop Solutions our customers are buying software that will run their entire company from quote to cash, and I want to make sure they understand the importance of partnering with the right company,” says Dynkin. “Telling them who we are, the type of relationship they can expect, and the lifelong partner we want to be is an integral part of the process.” Dynkin believes that when a company shows loyalty to its employees, values and mission, it will keep its people engaged and performing their best. “I am proud of the growth Global Shop Solutions has achieved, but even more so the fact that we haven’t become corporatized,” says Dynkin. “The company’s principles and family atmosphere haven’t changed since I first came here 25 years ago. It continues to be a place where we support each other and can have open conversations with anyone, anytime. The family ownership truly cares about the people who work here, and always put them at the front of their decision-making process.” “I love the work,” adds Dynkin. “It’s gratifying to see the impact Global Shop Solutions has on our customers’ businesses, and I feel like I have a measurable impact on our company.”
Barcoding to expand North American presence through planned combination with DecisionPoint Systems
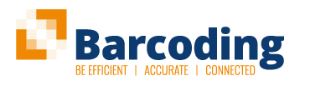
Barcoding, Inc. (“Barcoding”), a supply chain automation and innovation company, together with Graham Partners, has announced that an affiliate of Barcoding has entered into a definitive merger agreement with DecisionPoint Systems, Inc. (“DecisionPoint”). DecisionPoint is a mobility-first enterprise services and solutions company and a leading provider of retail in-store solutions and services centered on Point-of-Sale systems headquartered in Del Ray Beach, FL with additional locations in California, North Carolina, Colorado, Utah, and Pennsylvania. The combination of Barcoding and DecisionPoint will create a business of scale and a leader in supply chain automation by expanding Barcoding’s existing value proposition into the adjacent point-of-sale technologies space while establishing a national footprint with strongholds in the Southeast and West Coast. “With our planned combination with DecisionPoint, Barcoding continues to focus on growth that will directly and positively impact our customers and partners. Combining Barcoding and DecisionPoint will enhance our offerings and allow us to better serve enterprise customers in retail, supply chain, and other sectors with a more comprehensive set of solutions and services. We look forward to welcoming the DecisionPoint team into the Barcoding family,” said Shane Snyder, CEO and president of Barcoding.
H&E Equipment Services completes acquisition of Lewistown Rental and affiliated companies
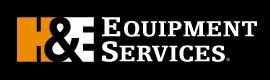
H&E Equipment Services, Inc. has announced the completion of its acquisition of Montana-based Lewistown Rental and three of its affiliated companies located in Havre, Glasgow, and Great Falls, Montana. The acquisition adds a comprehensive mix of equipment with an original equipment cost of approximately $28.5 million. Brad Barber, chief executive officer of H&E, stated, “With the addition of these four locations, H&E now has six locations in the state of Montana, addressing customer needs across the state. The acquisition is our third in the last six months and is indicative of our continued focus on expanding our geographic reach in the U.S. We are encouraged by the growing prospects for non-residential, industrial, infrastructure, and agricultural projects in Montana and look forward to establishing a strong presence in this vibrant state.” With the close of the transaction, H&E now operates 145 branch locations across 30 states.
Carolina Handling celebrates anniversary with 58 for 58 giveaway
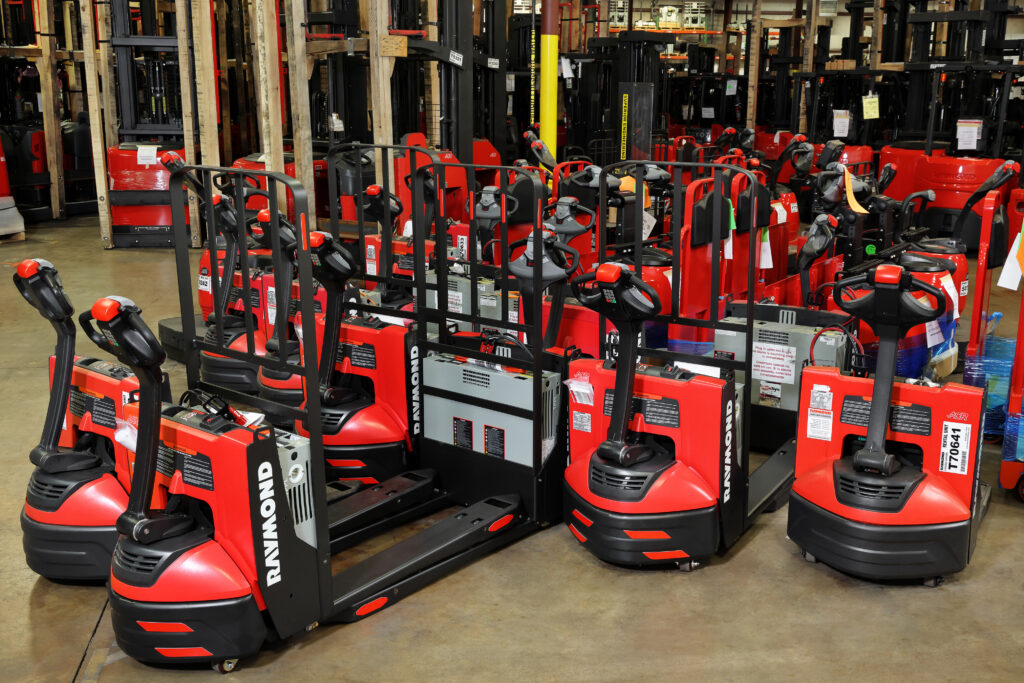
Carolina Handling is celebrating its 58th anniversary in 2024 with a yearlong campaign entitled “Handling Hunger Together” to assist hunger relief organizations throughout the company’s five-state footprint. According to Feeding America, more than 44 million people in the U.S. face hunger each year, including 1 in 5 children. In 2022, 49 million people turned to food banks and other charitable organizations to help feed their families. About 8 million pounds of food was collected and delivered to feeding organizations in 2023, according to Move for Hunger, with food banks in need of pallet jacks, lift trucks and other material handling equipment to move non-perishables and fresh produce. “There are numerous organizations throughout the Southeast that receive, store and distribute thousands of pounds of food each year to feed the hungry in their communities,” said Carolina Handling President & CEO Brent Hillabrand. “The logistics of that can be overwhelming to organizations that don’t have applicable, reliable equipment. That’s where companies like Carolina Handling can help.” In celebration of Carolina Handling’s 58 years in business in 2024, the Charlotte, NC-based intralogistics company is giving away 58 motorized pallet jacks to hunger relief organizations throughout its territory, which includes North Carolina, South Carolina, Georgia, Alabama and Florida’s Central time zone. The Raymond 8210 electric pallet jacks are used 2016 and newer models with battery packs. They will be awarded on a first-requested basis to qualifying organizations completing a submission form on the Carolina Handling website. Equipment will be delivered to all recipients at no charge.
KEEN Utility’s Evanston Work Boot with an energetic sole
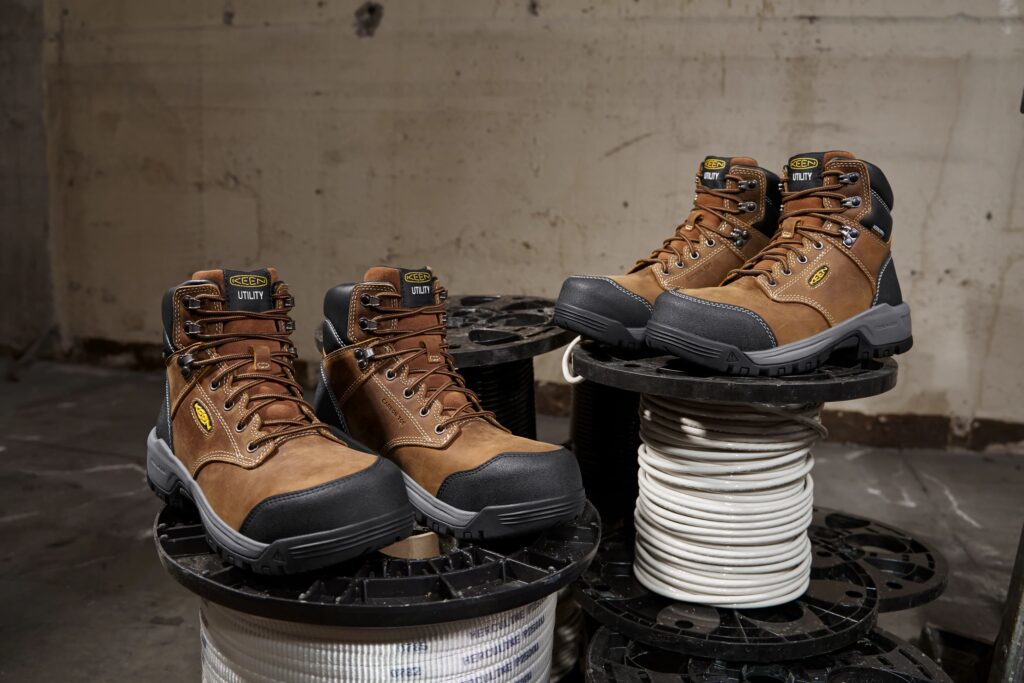
New for Spring ‘24, the Evanston from KEEN Utility offers the burly protection of a work boot with the athletic feel and flexibility of a sneaker. Product highlights include a responsive KEEN.ReGEN cushioning provides up to 50% energy return with every step as well as carbon-fiber safety toes that are unobtrusive and 15% lighter than steel. Other standout features include a KEEN.DRY waterproof, breathable membrane and full-grain Barnyard Resistant leather upper to keep you shielded from jobsite messes. A tough worker with an energetic sole, the Evanston is available for both men and women.
U.S. Rail Traffic report for the week ending April 27, 2024
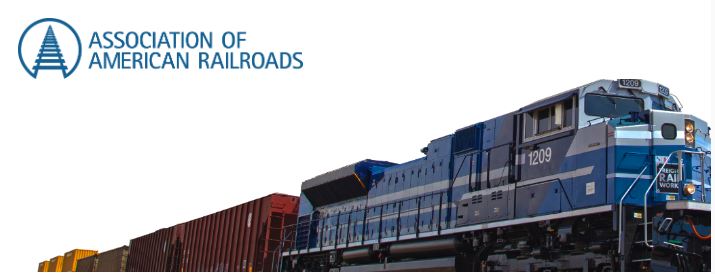
The Association of American Railroads (AAR) has reported U.S. rail traffic for the week ending April 27, 2024, as well as volumes for April 2024. U.S. railroads originated 848,882 carloads in April 2024, down 6.5 percent, or 58,751 carloads, from April 2023. U.S. railroads also originated 1,018,569 containers and trailers in April 2024, up 8.6 percent, or 80,471 units, from the same month last year. Combined U.S. carload and intermodal originations in April 2024 were 1,867,451, up 1.2 percent, or 21,720 carloads and intermodal units from April 2023. In April 2024, nine of the 20 carload commodity categories tracked by the AAR each month saw carload gains compared with April 2023. These included: motor vehicles & parts, up 7,191 carloads or 12.1 percent; petroleum & petroleum products, up 4,967 carloads or 13.8 percent; and chemicals, up 3,686 carloads or 2.9 percent. Commodities that saw declines in April 2024 from April 2023 included: coal, down 71,885 carloads or 28.0 percent; metallic ores, down 4,113 carloads or 16.9 percent; and crushed stone, sand & gravel, down 3,856 carloads or 4.4 percent. “U.S. rail carloads declined in April primarily due to decreased coal shipments,” said Rand Ghayad, Chief Economist at the Association of American Railroads. “Excluding coal, year-over-year carload volumes have experienced a three-month consecutive increase. In April, out of the 20 carload categories monitored, 9 showed growth, with several experiencing marginal declines. Additionally, sustained consumer spending and heightened port activity contributed to the eighth consecutive year-over-year rise in intermodal traffic for April. Excluding coal, carloads were up 13,134 carloads, or 2.0 percent, in April 2024 from April 2023. Excluding coal and grain, carloads were up 9,541 carloads, or 1.7 percent. Total U.S. carload traffic for the first four months of 2024 was 3,622,709 carloads, down 4.8 percent, or 180,839 carloads, from the same period last year; and 4,287,216 intermodal units, up 9.0 percent, or 352,709 containers and trailers, from last year. Total combined U.S. traffic for the first 17 weeks of 2024 was 7,909,925 carloads and intermodal units, an increase of 2.2 percent compared to last year. Week Ending April 27, 2024 Total U.S. weekly rail traffic was 476,302 carloads and intermodal units, up 0.7 percent compared with the same week last year. Total carloads for the week ending April 27 were 214,414 carloads, down 6.4 percent compared with the same week in 2023, while U.S. weekly intermodal volume was 261,888 containers and trailers, up 7.5 percent compared to 2023. Seven of the 10 carload commodity groups posted an increase compared with the same week in 2023. They included motor vehicles and parts, up 1,552 carloads, to 17,067; chemicals, up 1,227 carloads, to 33,800; and nonmetallic minerals, up 953 carloads, to 34,184. Commodity groups that posted decreases compared with the same week in 2023 were coal, down 18,156 carloads, to 45,832; metallic ores and metals, down 1,557 carloads, to 20,117; and forest products, down 80 carloads, to 8,341. North American rail volume for the week ending April 27, 2024, on 10 reporting U.S., Canadian and Mexican railroads totaled 325,396 carloads, down 5.3 percent compared with the same week last year, and 350,692 intermodal units, up 6.6 percent compared with last year. Total combined weekly rail traffic in North America was 676,088 carloads and intermodal units, up 0.5 percent. North American rail volume for the first 17 weeks of 2024 was 11,142,754 carloads and intermodal units, up 2.0 percent compared with 2023. Canadian railroads reported 93,258 carloads for the week, down 3.6 percent, and 75,832 intermodal units, up 5.2 percent compared with the same week in 2023. For the first 17 weeks of 2024, Canadian railroads reported cumulative rail traffic volume of 2,725,737 carloads, containers and trailers, up 0.3 percent. Mexican railroads reported 17,724 carloads for the week, down 0.8 percent compared with the same week last year, and 12,972 intermodal units, down 1.1 percent. Cumulative volume on Mexican railroads for the first 17 weeks of 2024 was 507,092 carloads and intermodal containers and trailers, up 8.4 percent from the same point last year.
Cromer Material Handling earns Diamond Award from Bobcat Company
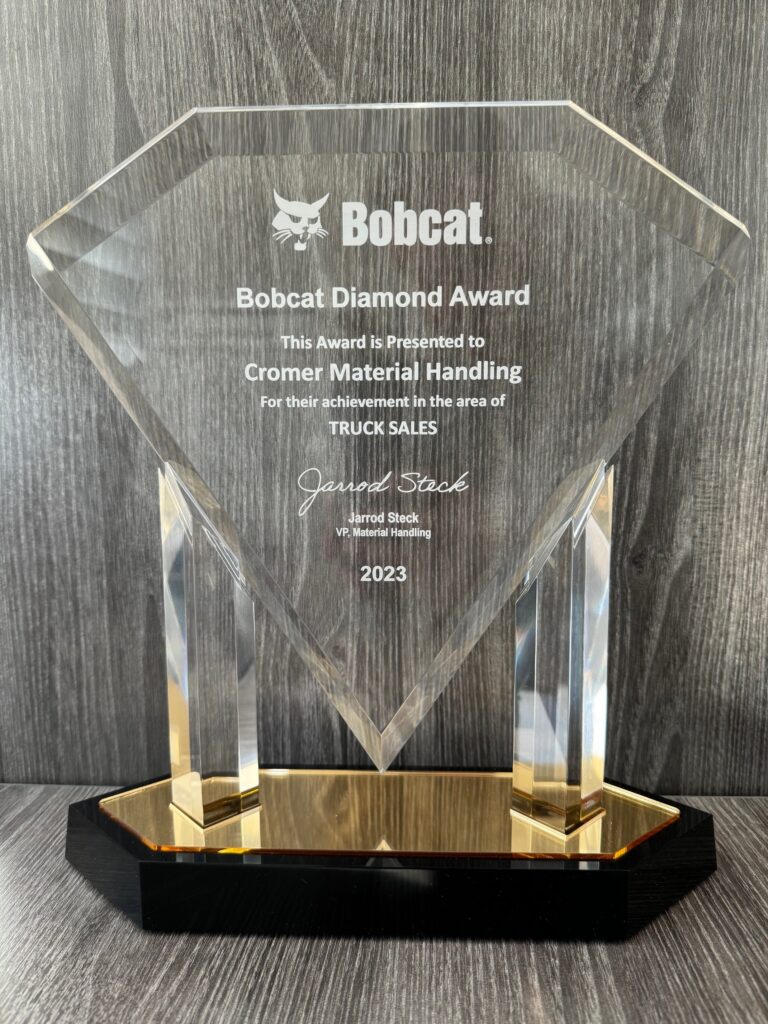
Bobcat Company recognized Cromer Material Handling as a top-performing material handling equipment dealer with a Diamond Award at MODEX 2024. The Diamond Award is presented annually to select dealers by Bobcat Company for outstanding efforts and commitment within their respective regions. This year, Bobcat recognized 21 material handling dealers based on sales, volume and other dealer engagement metrics. Cromer Material Handling was recognized at a reception held during MODEX 2024, the premier supply chain experience trade show in Atlanta, Georgia. “We are pleased to recognize such a deserving group of dealerships for their efforts and achievements,” said Jarrod Steck, Bobcat vice president of material handling products. “While forklifts are a new product offering within the Bobcat portfolio, these dealerships bring years of expertise and experience within the material handling industry, and we are thrilled to award these top performers and valued dealer partners.” Brent Poulton, President of Cromer Material Handling, accepted the award on behalf of the entire organization. “We are honored to be recognized by Bobcat Material Handling as one of the top-performing dealers,” Poulton said. Combining our talented team of parts, service, rental, and sales associates with a world-class product has proven to be a winning formula for us, Bobcat Material Handling, and our customers. We proudly represent the Bobcat brand and are committed to long-lasting partnerships with them and our customers.” Bobcat’s lift truck, materials handling products and organization were rebranded to Bobcat, from the former name of Doosan this past year.
Episode 482: Warehouse fire suppression systems with Telgian
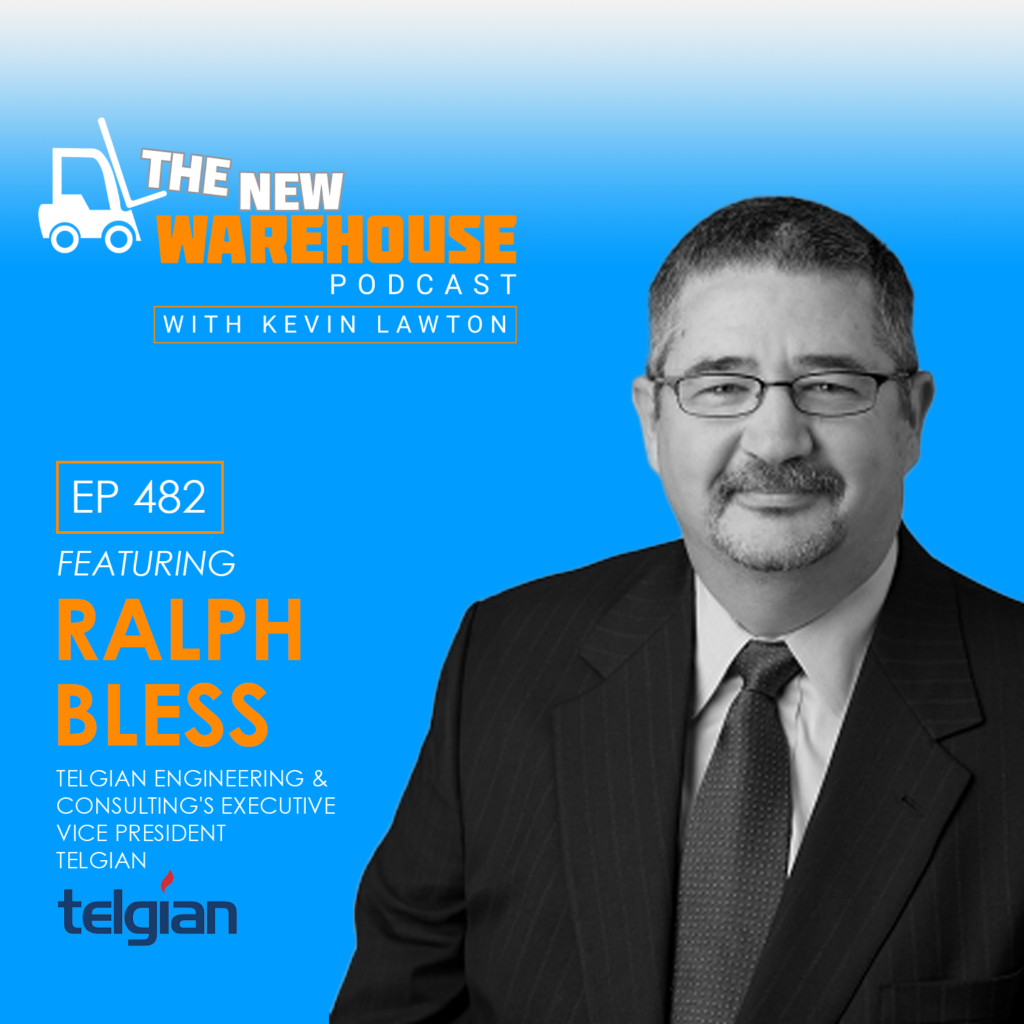
Welcome to another fiery episode of The New Warehouse Podcast! Today, we’re joined by Ralph Bless, Executive Vice President at Telgian, a company with a 39-year legacy in engineering fire protection systems. In this episode, Ralph unpacks the complexities of fire safety in warehousing, emphasizing the challenges introduced by modern automated systems such as ASRS and the struggle to keep fire codes current and warehouse fire suppression systems effective. Fundamentals of Warehouse Fire Suppression Systems Ralph clarifies the basic types of fire suppression systems found in warehouses: “There are two basic types that are most common in these warehousing environments. One is a wet pipe fire sprinkler system, and another one is a dry pipe fire sprinkler system.” He debunks a common myth, explaining, “A lot of people have the perception that sprinklers are like what you see in the movies, where one activates; they all activate. That’s just not the case.” Keeping Pace with Automation Discussing the intersection of automation and fire safety, Ralph notes, “The real challenges with these new automation systems, particularly the ASRS, is they’re evolving so fast.” He details the rigorous testing needed as “traditional sprinkler setups may not suffice” for these dense configurations. Ralph highlights regulatory hurdles: “when a jurisdiction is using an older set of the codes…they’re really looking and working off technology that is 10, 15 years old…we are not keeping up with that necessarily.” Anticipating Changes in Fire Safety Norms As warehousing technologies evolve, Ralph anticipates ongoing adjustments in fire safety approaches, “What we are seeing…is this focus on testing because that way we know we’ve got the proper protection.” Ralph expects a continued emphasis on testing. Pointing out, “most people thing that sprinklers put fires out, but they really don’t. In most cases, they either control the fire so the firefighters can show up and extinguish them.” It’s imperative to consider how small changes, such as narrowing distances between aisles, can impact how the sprinklers operate and their performance capabilities. Key Takeaways on Warehouse Fire Suppression Systems Automated warehousing systems like ASRS introduce complex fire safety challenges that require innovative testing and adaptation. Future fire safety standards will increasingly rely on dynamic testing to align with rapid technological advances in warehousing. Sprinklers don’t put fires out in most cases but control the fire until firefighters arrive to put it out. The New Warehouse Podcast Episode 482: Warehouse Fire Suppression Systems with Telgian
H&E Equipment Services reports first quarter 2024
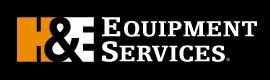
H&E Equipment Services, Inc. announced results for the first quarter ended March 31, 2024, with disciplined growth objectives contributing to double-digit improvement in rental revenues. FIRST QUARTER 2024 SUMMARY WITH A COMPARISON TO FIRST QUARTER 2023 Revenues increased 15.2% to $371.4 million compared to $322.5 million. Net income totaled $25.9 million compared to $25.7 million. The effective income tax rate was 26.5% compared to 26.1%. Adjusted EBITDA (earnings before interest, taxes, depreciation, and amortization) increased 13.1% to $161.7 million compared to $143.0 million. Adjusted EBITDA margin was 43.6% compared to 44.4%. Total equipment rental revenues were $295.3 million, an increase of $33.3 million, or 12.7%, compared to $262.0 million. Rental revenues were $261.7 million, an increase of $29.7 million, or 12.8%, compared to $232.1 million. Sales of rental equipment increased 49.8% to $48.1 million compared to $32.1 million. Margins improved to 62.9% compared to 58.6%. Sales of new equipment totaled $10.4 million, an increase of 33.2% compared to $7.8 million. Gross margin improved to 44.4% compared to 43.8%. Total equipment rental gross margins were 43.3% compared to 43.6%. Rental gross margins were 48.5% compared to 48.4%. Average time utilization (based on original equipment cost) was 63.6% compared to 67.3%. The Company’s rental fleet, based on original equipment cost, increased $383.0 million, or 15.7% to just over $2.8 billion. Average rental rates improved 2.9% from the year-ago quarter and declined 0.2% on a sequential quarterly basis. Dollar utilization was 37.0% compared to 38.6%. Average rental fleet age on March 31, 2024, was 39.9 months compared to an industry average age of 48.9 months. Paid regular quarterly cash dividend of $0.275 per share of common stock. Summarizing the Company’s first quarter results, Brad Barber, chief executive officer of H&E stated, “Rental revenues grew 12.8% on a year-over-year basis, supported by a modest improvement in rental rates and successful growth activities. Rental rates advanced 2.9% when compared to the year-ago quarter, while on a sequential quarterly basis, rates experienced a negligible decrease of 0.2%. Average physical utilization in the quarter was 63.6% compared to 67.3% in the year-ago quarter, with the decline due to lower than anticipated construction activity, as well as project delays resulting from recurring unfavorable weather conditions, with the work interruptions most pronounced across our western operations. Our continued focus on branch expansion and fleet growth led to further financial gain in the quarter. On a year-over-year basis, our branch network grew 17%, including 15 locations resulting from our accelerated branch expansion program and five other locations added through acquisitions. Our rental fleet closed the first quarter with an original equipment cost (OEC) in excess of $2.8 billion, or 15.7% larger than our OEC on March 31, 2023.” Providing an updated view on industry prospects, Mr. Barber noted, “Our current outlook for the equipment rental industry indicates a transitioning business environment, with moderating growth levels compared to the exceptional rate of growth in construction spending and strong business dynamics experienced over the past 24 months. We believe the easing in the progression of construction spending is in part the result of a ‘higher for longer’ interest rate environment and generally tighter lending standards, which have contributed to a greater supply of rental equipment. Even though non-residential and industrial project backlogs remain solid, the rate of new project starts has slowed in early 2024. We note several factors that are expected to be instrumental in maintaining, or possibly improving upon an environment currently exhibiting moderate growth and steady industry fundamentals. These factors include the continued escalation of mega projects, an expected increase in infrastructure projects, favorable trends in rental penetration and the steady growth in construction employment. These critical factors reinforce non-residential construction and industrial project activity and serve as the foundation in support of elevated long-term industry growth.” Mr. Barber addressed the Company’s planned capital expenditures while reiterating branch expansion objectives, stating, “We have reduced our 2024 guidance for gross fleet investment, with the steadying of industry fundamentals justifying a more balanced approach to capital spending over the year. Capital investment in our fleet is now expected to range from $350 million to $400 million, down from our initial guidance for 2024 of $450 million to $500 million. With the availability of equipment from manufacturers returning to normal, we could quickly increase our spending range should industry demand accelerate. The revised spending range will adequately address the planned growth in 2024 across our branch network, which remains at 12 to 15 new locations as we continue to demonstrate strong execution of our accelerated branch expansion strategy. Also, additional branch growth in 2024 could be achieved through the acquisition of attractive rental operations, as demonstrated by the acquisition of Precision Rental, which closed in the first week of 2024, and the recently announced pending acquisition of four locations in the state of Montana. Following the expected close of this latest transaction in the second quarter of 2024, H&E will operate 145 branches across 30 states, including eight branch additions since the close of 2023.” FINANCIAL DISCUSSION FOR FIRST QUARTER 2024 Revenue Total revenues increased 15.2% to $371.4 million in the first quarter of 2024 from $322.5 million in the first quarter of 2023. Total equipment rental revenues increased 12.7% to $295.3 million compared to $262.0 million in the year-ago quarter. Rental revenues increased 12.8% to $261.7 million compared to $232.1 million in the same period of comparison. Sales of rental equipment increased 49.8% to $48.1 million compared to $32.1 million in the first quarter of 2023. Sales of new equipment increased 33.2% to $10.4 million compared to $7.8 million in the same quarter of 2023. Gross Profit Gross profit increased 16.6% in the first quarter of 2024 to $164.9 million compared to $141.4 million in the first quarter of 2023. Gross margin of 44.4% for the first quarter of 2024 compared to 43.8% over the same period of comparison. On a segment basis, gross margin on total equipment rentals was 43.3% in the first quarter of 2024 compared to 43.6% in the first quarter of 2023. Rental margins were 48.5% compared to 48.4%. On average, rental rates in the first quarter of 2024 improved 2.9% when compared to rates in the first quarter of 2023. Time utilization (based on original equipment cost) was 63.6% in the first quarter of 2024 compared to 67.3% in the year-ago quarter. Gross margins
Cimcorp has announced new VP of Operations
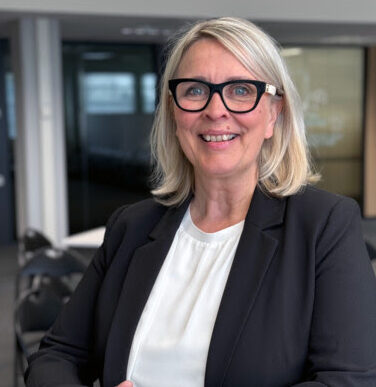
Leveraging three decades of expertise in managing international projects, Anne Happonen will support the company’s global initiatives and will support project leadership Cimcorp has appointed Anne Happonen as the company’s new Vice President of Operations. With an extensive career in helping global organizations navigate the intricate landscape of international business, Happonen is passionate about leading diverse teams and fostering strong customer relationships—a passion that aligns with Cimcorp’s ethos. Today, Cimcorp offers a comprehensive range of automated solutions—including automated storage and retrieval systems (AS/RS), picking and sortation, automated guided vehicles (AGVs), and a Warehouse Control System (WCS)—that enable tire factories and grocery distributors to tackle their biggest warehousing and distribution challenges, like energy efficiency, waste, and overall supply chain operations. “I’m excited for the opportunity to spearhead innovative automation projects as the new Vice President of Operations at Cimcorp,” said Happonen, “As a globally known company, Cimcorp has superb solutions, and I’m thrilled to be a part of a company that is a profitable, proud leader in their field and shows care for employees and partners alike.” With over three decades of experience in leading successful organizations, including global brands Cargotec, Sandvik, and Patria, Happonen’s philosophy is grounded in the principles of transparency, collaboration, and adaptability. “Successful leadership is about enabling the ease of work for others and fostering a culture of openness and trust. In this role, my wish is to provide the team with the best possible conditions to thrive. I strive to inspire teams to achieve goals, and my own inspiration stems from seeing people do their work with pride,” said Happonen. “This philosophy also translates to customers. It’s important to understand the big picture and realize that any negotiation is about the people. Honesty and humanity are essential in international business.” With nearly 500 employees globally, Cimcorp is passionate about optimizing material flows and has developed unique robotic solutions for order fulfillment and storage for leading companies in food and beverage, retail, e-commerce, consumer goods, and tire manufacturing. Additionally, Cimcorp offers Success Services for continuous maintenance and support to help customers secure a lifecycle of 20 years or more for their automation technology. As she embarks on this new chapter at Cimcorp, Happonen brings her a stellar track record and a genuine commitment to making a difference in the world—one project at a time.
Kassow Robots launches the world’s first 7-axis cobot series with a controller integrated into the base
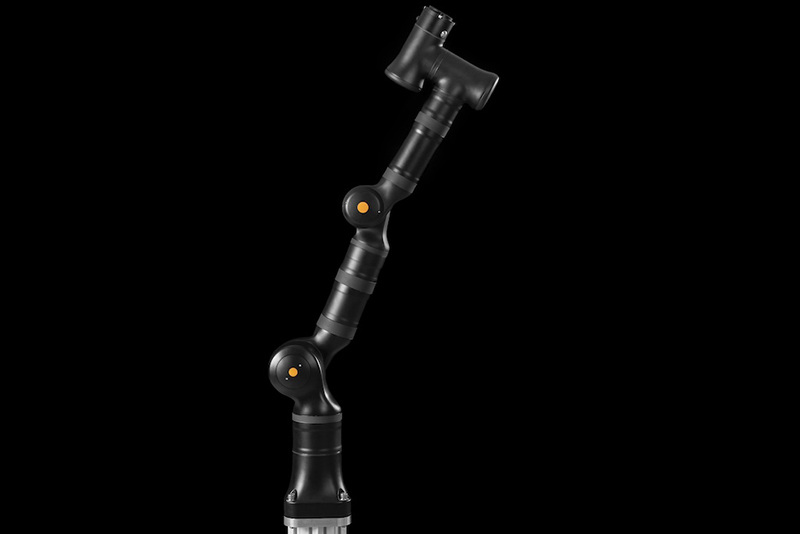
Greater flexibility for mobile solutions & additional space savings for cramped facilities With its Edge Edition, Kassow Robots has launched the world’s first 7-axis cobots in which the controller is integrated into the base of the robot. All five of the 7-axis cobots are now available in two versions: the classic variant with a separate controller, and the Edge Edition. Kristian Kassow and his engineering team have succeeded in miniaturizing the controller so that it now only occupies around 10% of the volume of the external controller. The footprint of the Edge edition’s base is extremely compact, measuring only 160 by 200 millimeters. These cobot models are powered by direct current, meaning that they can be directly connected to any DC power supply, for example, a battery of mobile robots. There are also easily accessible 60 IO connections. With these new models, the Copenhagen-based cobot manufacturer is making it easier for industrial companies to automate their operations. At the same time, their lightweight robots open up new opportunities for mobile cobot AMR and cobot AGV applications and various space-saving solutions. “The Edge Edition of our 7-axis cobots is a world first, enabling industrial customers to take a quantum leap in terms of flexible automation. Integrating the controller into the robot’s base delivers additional space savings and simplifies integration at the same time. The Edge Edition is ideal for simplifying mobile cobot applications—not least because it can be connected directly to the power supply of AGVs or AMRs. These mobile solutions hold tremendous potential for industrial automation,” highlights Kristian Kassow, founder and CEO of Kassow Robots. The five 7-axis cobot models, which the co-owner had developed especially for industrial use, were launched in 2019 and 2020. To this day, the company remains true to its motto of “strong, fast, simple.” The end customers use their 7-axis robots for applications such as CNC solutions and for machine tending, palletizing, labeling, dispensing, packaging, sanding, and more. More flexibility for SMEs “Additional floor space in production facilities comes with a heavy price tag and is sometimes not available at all. We make sure that automation can be implemented more flexibly in less space for companies of all sizes,” says Dieter Pletscher, Global Sales Manager at Kassow Robots. Companies that cannot expand or reconfigure their production facilities also benefit from the capabilities offered both by the Edge Edition and the five existing 7-axis cobots. Kassow Robots believes that these are especially useful for established SMEs with no additional production space that would prefer to avoid the costs of expansion. “Compactness can be a decisive advantage when it comes to process automation. Our Edge Edition allows for greater flexibility, not only thanks to the 7th axis featured by all of our robots but also by the controller integrated into the cobots‘ base,” explains Dieter Pletscher. SMEs can benefit from installing Edge Edition on mobile carts that allow employees to operatively move them to whichever location they are needed. Presentation at Automate 2024 in Chicago Kassow Robots presented a prototype of the Edge Edition at last year’s Automatica. In May 2024, one of the five Edge variants now available for ordering will be presented at North America’s biggest automation trade show, Automate, in Chicago (Booth 4250): the KR1410 Edge Edition, mounted on an AMR from Morrell Group.
Queen City Robotics Alliance Spring and Summer Events
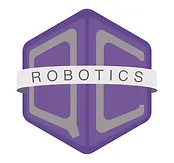
Summer is almost here… The volunteers and teams at Queen City Robotics Alliance (QCRA) are having a busy spring. Our FRC teams were in action at FIRST® FRC tournaments and we have two special events – SIM Tech on the Tees and Hops & Bots – happening in May. Here is a rundown: Team YETI goes to FRC Worlds For the second year in a row, FRC Team 3506 YETI Robotics® qualified for the FIRST FRC World Championships, which took place in Houston April 17-21. The team competed with 600 national and international teams and was the team’s 6th appearance in total. After two days of competition, Team YETI finished 8th qualifying them as the 8th seed Alliance captain in the playoffs, the highest ranking at FRC Worlds in the team’s 14-year existence. The team also competed for the Impact Award for the first time. The highlight of the event was a meet and greet with FIRST Robotics founder entrepreneur Dean Kamen. Congratulations to Team YETI! SIM Charlotte partners with QCRA for two events in May QCRA sponsor Charlotte Chapter of the Society for Information Management (SIM) is holding their Q2 meeting at The Zone on May 2 with the theme “Connecting Tech Leaders with the Future of Robotics.” Hosting meetings and other events at The Zone is one of the perks of QCRA Adopt-a-room sponsorship. This event is only open to members of SIM Charlotte. QCRA is also thankful to SIM Charlotte for including us in their SIM Tech on the Tees charity golf tournament on Monday, May 20, at Ballantyne Country Club. SIM organized this event to support STEM education organizations and programs raising over $850,000 over the last 10 years. SIM Charlotte has been a vital partner in QCRA’s mission. “The way QCRA fosters interest and access to technology for our area’s youth,” says Chris Long, SIM Charlotte President, “is a great example of the kind of non-profit that SIM supports in our mission to grow and develop a diverse pool of future technology leaders.” QCRA Hops & Bots fundraiser May 31 Hops & Bots, QCRA’s annual fund-raising event, will be Friday, May 31, from 5-7:30 PM at The Zone, 2102 Cambridge Beltway Dr., Suite B. This networking and robot demonstration event brings together businesses, people, and parents to raise money and learn how QCRA helps area robotics students. This will be the first time this event has been held in QCRA’s home facility, The Zone. QCRA robotics students will be giving robot demonstrations and tours of the facility and light hors d’ oeuvres, local craft beer, and soft drinks will be served. The highlight of the evening will be keynote speaker Stephen Saucier, M.Ed., President of Sullenberger Aviation Museum.
Mazzella wins award contributing with #GLAD2024
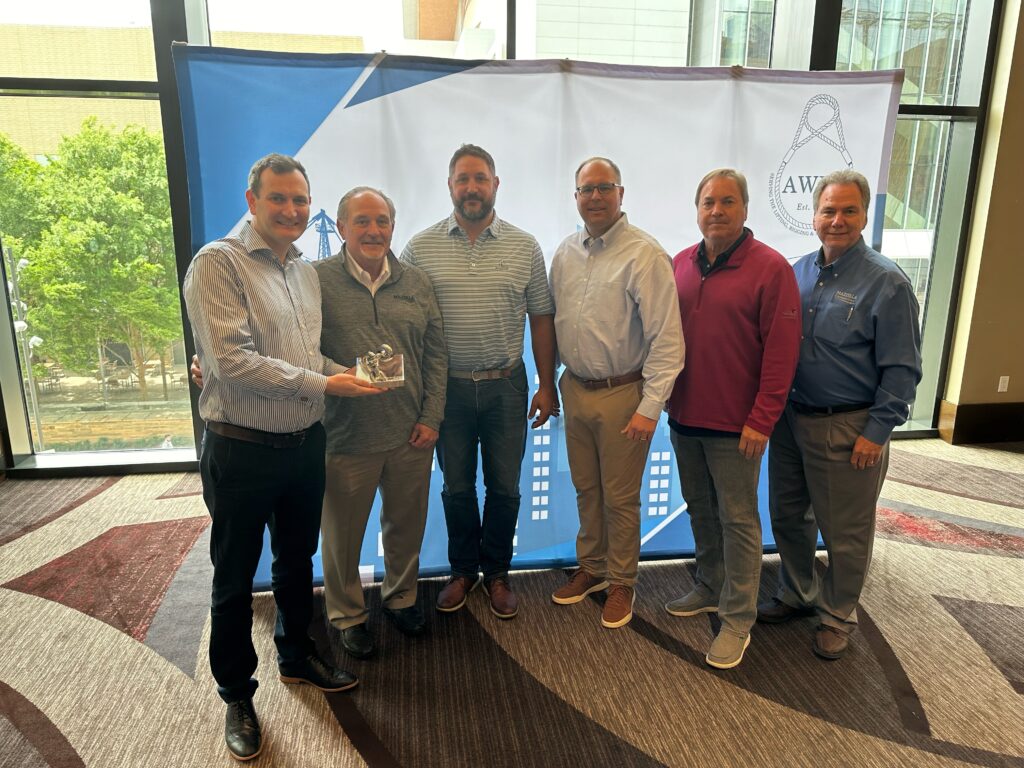
Mazzella Companies has been presented with an award for its contribution to last year’s Global Lifting Awareness Day (GLAD), by the Lifting Equipment Engineers Association (LEEA). Mazzella was unanimously voted by a judging panel to have provided the best contribution from a company or individual to #GLAD2023. Fittingly, the award was presented by Ross Moloney, CEO, LEEA, to Mazzella representatives attending this week’s Associated Wire Rope Fabricators (AWRF) Spring General Meeting in Nashville, Tennessee. Mazzella, like AWRF, has been a loyal campaigner since GLAD’s conception in 2020. Kindred Spirits, AWRF runs an accreditation program, powered by LEEA’s third-party audits. Mike Close, corporate marketing and communications manager, Mazzella, said: “Winning this award was both surprising and affirming. Last year marked our most significant involvement in GLAD to date. We dedicated our efforts to a comprehensive campaign that spanned multiple media, including articles, videos, and a podcast. These initiatives were aimed at supporting the vision of LEEA and GLAD, to raise overall awareness of the lifting and rigging industry. “This award is recognition for the whole marketing team. We were motivated by the increasing participation we observed in the industry and inspired by partners, like Kito Crosby, who received a similar award for their efforts in 2022. This appreciation of our peers spurred us to enhance our involvement and create an engaging and impactful awareness campaign.” Central to Mazzella’s contribution was welcoming Moloney on an episode of the company’s Safety Factor podcast, launched on the cusp of #GLAD2023. Each podcast episode is available in two formats: audio-only, available on traditional podcast platforms; and a video version on YouTube, allowing viewers to watch the conversation between the host and guests. The episode above, titled, “How Global Lifting Awareness Day Addresses the Labor Shortage in the Lifting Industry,” received 370 plays across both formats. Moloney has already been invited back to appear on a pre-#GLAD2024 episode. Mazzella also published two key articles: “How is Technology Changing the Lifting and Rigging Industry?” and, “How Does Global Lifting Awareness Day Promote the Lifting Industry?” and populated social media channels with engaging content. Moloney said: “GLAD messaging has always been underpinned by raising awareness — and Mazzella sets an outstanding example of what can be achieved. I was honored to feature on the Safety Factor podcast, but that was just one component of a wider commitment to #GLAD2023 that was humbling and empowering. While we are growing a legion of supporters, none were more deserving of recognition than Mazzella — and what a place to celebrate with them here with the AWRF community.” #GLAD2024 to be biggest ever The fifth Global Lifting Awareness Day — #GLAD2024 — will take place on Thursday 18 July, represented by a new logo. Once more, Mazzella will be among the leading stakeholders delivering the message emphatically to the point of use. This year’s campaign trail is already advanced, with the two pillars of earlier announcements being that LEEA will focus its strategy on skills and employment. It encourages everyone to contribute by using graphics and the hashtags to celebrate their involvement with the industry, at all levels of the supply chain. Cranes, hoists, rigging gear, and height safety hardware is central to safe operations in a myriad of end-user sectors, including civil engineering, construction, material handling, metals, military, offshore, subsea, and renewables, to select just a handful. Close added: “The new logo is very cool — the design elements of the crane and the use of safety yellow [color version], convey its relevance to the lifting and rigging industry. I think if you see it and don’t know what GLAD is, or the movement behind it, it effectively communicates its purpose of supporting and enhancing the industry. For #GLAD2024, we plan to continue our multi-medium approach, using articles, videos, and podcasts to spread awareness and share key messages. “Our goal is to leverage our partnerships, particularly with a leading training company in the industrial sector, to focus on professional development and highlight its significance. There’s always so much more that can be done to promote best practices and safety within our industry, so I sense that will be a big theme for us this year as well. On the day, we’ll have a schedule built out to post links on social media to relevant and supporting content and information each hour of the day.” Close called skills and employment “foundational in our industry.” He added: “As AI [artificial intelligence] and automation reshape our work environment, we have to be proactive in developing new skills in our teammates. It’s not just about adapting for tomorrow but planning for the next decades. This will be critical to remain competitive in attracting and retaining top talent. Additionally, the need for skilled craftsmen — welders, fabricators, riggers, operators, and technicians — remains as vital as ever. They transform ideas into tangible solutions, something that’s irreplaceable in our industry.”
Robroy Industries® appoints Alex Erwin as Business Development Manager
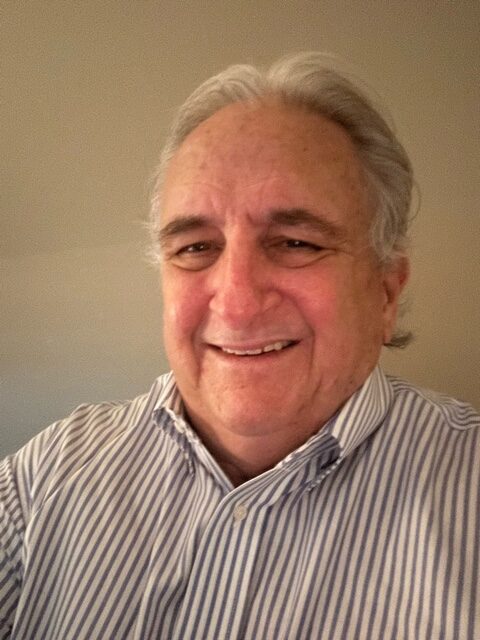
Robroy Industries® Enclosures Division has announced the appointment of Alex Erwin as its Central Region Business Development Manager. Erwin has been involved in the electrical product industry his entire professional life. A graduate of Georgia State University he provides more than 40 years of expertise as an electrician, serving as lighting manager for a wholesale supply house, and as a field sales representative for a manufacturers’ agent. “Alex is an ideal addition to our organization,” states Craig Mitchell, President of Robroy Industries®Enclosures Division. “He represents extensive experience that encompasses all aspects of our sales channel providing him the ability to understand and satisfy the diverse application needs of our enclosure customers.” Through its two brands, Stahlin® and AttaBox®, Robroy Enclosures offers the most extensive selection of non-metallic enclosures available for meeting the needs of diverse industries, interior and exterior applications, appealing aesthetics, and physical property performance standards including NEMA 4X and NEMA 6P integrity. Stahlin Enclosures delivers time and laborsaving solutions, non-stop innovation, and superior product performance. AttaBox Enclosures, manufacturers of high-performing non-metallic electrical and industrial enclosures, leads the way in providing application-specific solutions for installations within continuously demanding environments.