AAR reports Rail Traffic for the week ending October 19, 2024
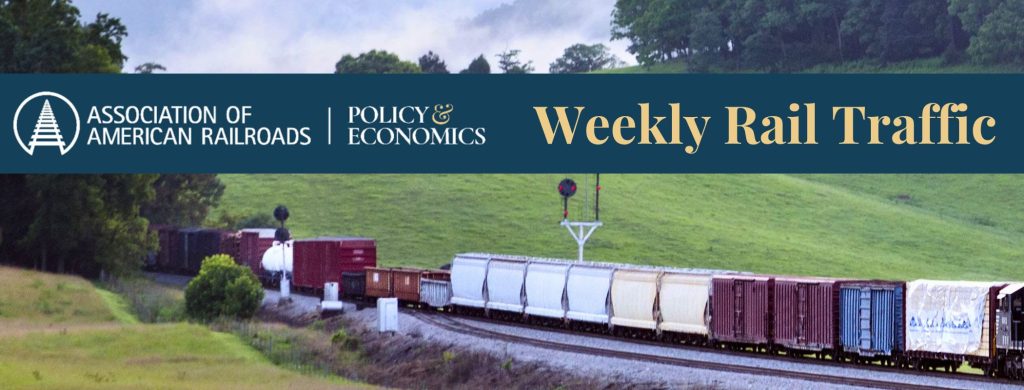
Today, the Association of American Railroads (AAR) reported U.S. rail traffic for the week ending October 19, 2024. This week’s total U.S. weekly rail traffic was 510,730 carloads and intermodal units, up 1.1 percent compared with the same week last year. Total carloads for the week ending October 19 were 223,278, down 4.6 percent from the same week in 2023, while the U.S. weekly intermodal volume was 287,452 containers and trailers, up 6.0 percent from 2023. Five of the ten carload commodity groups posted an increase compared with the same week in 2023. They included grain, up 3,052 carloads, to 23,372; miscellaneous carloads, up 1,015 carloads, to 9,992; and farm products excl. grain, and food, up 898 carloads to 18,082. Commodity groups that posted decreases compared with the same week in 2023 included coal, down 8,261 carloads, to 58,350; nonmetallic minerals, down 3,771 carloads, to 30,281; and metallic ores and metals, down 3,551 carloads, to 18,884. For the first 42 weeks of 2024, U.S. railroads reported a cumulative volume of 9,142,601 carloads, down 3.3 percent from last year, and 11,042,994 intermodal units, up 9.0 percent from last year. Total combined U.S. traffic for the first 42 weeks of 2024 was 20,185,595 carloads and intermodal units, an increase of 3.1 percent compared to the previous year. North American rail volume for the week ending October 19, 2024, on nine reporting U.S., Canadian, and Mexican railroads totaled 333,360 carloads, down 4.4 percent compared with the same week last year, and 368,573 intermodal units, up 3.1 percent compared with last year. Total combined weekly rail traffic in North America was 701,933 carloads and intermodal units, down 0.6 percent. North American rail volume for the first 42 weeks of 2024 was 28,077,581 carloads and intermodal units, up 2.3 percent compared with 2023. Canadian railroads reported 95,182 carloads for the week, down 2.1 percent, and 67,489 intermodal units, down 7.1 percent compared with the same week in 2023. For the first 42 weeks of 2024, Canadian railroads reported a cumulative rail traffic volume of 6,677,340 carloads, containers, and trailers, down 0.0 percent. Mexican railroads reported 14,900 carloads for the week, down 13.8 percent compared to last year, and 13,632 intermodal units, down 1.5 percent. Cumulative volume on Mexican railroads for the first 42 weeks of 2024 was 1,214,646 carloads and intermodal containers and trailers, up 2.7 percent from last year. To view the U.S. Rail Traffic charts, click here.
Mitsubishi Electric Automation, Inc. has launched a low-cost Robot with largest reach
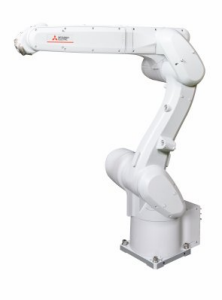
The MELFA RV-12CRL vertically articulated robot has the largest reach of any robot in Mitsubishi Electric’s low-cost robot series, at 1,504mm, and a 12kg payload capacity, making it a candidate for machine tending, case packing, and pick-and-place applications. Mitsubishi Electric Automation is reputable for its flexible and high-performance robots available in diverse payloads, reaches, and price ranges to accommodate customers’ unique needs. New to Mitsubishi Electric’s low-cost series of robots, the MELFA RV-12CRL vertical articulated robot offers a 1,504mm reach and 12kg payload capacity to cover a large work envelope, eliminating the need for a vertical life of an additional axis. Built-in features provide enhanced safety, streamlined implantation, and an overall reduction in downtime. The RV-12CRL features internal cables and air hoses for end-of-arm tooling, including 30 pins of signal cabling. Mitsubishi Electric has eliminated the need for encoder batteries that may cause tedious, expensive maintenance by adding MELSERVO-J5 servo motors, known for their battery-less encoder nature. Safety is a forethought, not an afterthought, with this robot launch through added safety via its CR800 controller to support safety monitoring functionality. The RV-12CRL series of robots possess versatile EOAT configurations, giving customers flexibility when selecting end-of-arm-tooling for the robot, making this series of robots appropriate for machine tending, case packing, and pick-and-place applications. When asked about the customer benefit of this launch, Product Manager (Robot) Curtis Sylliaasen stated, “The launch of the RV-12CRL robot marks an exciting opportunity for our customers to experience the quality and performance known by our industrial robot lineup at the price of a collaborative robot.”
Wauseon Machine introduces the redeployable automation module
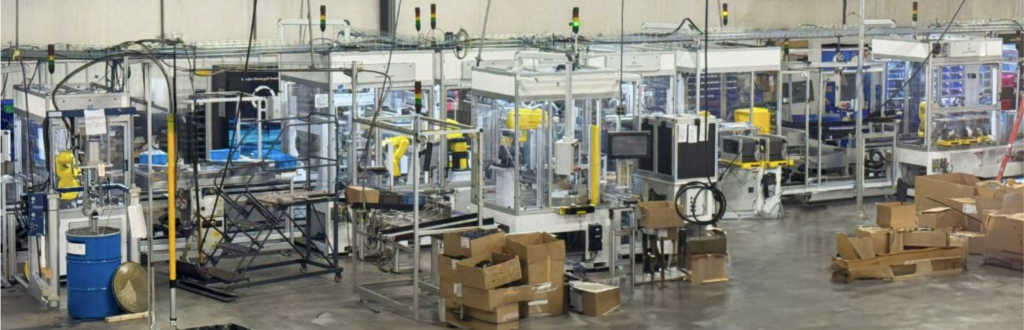
Innovative Solution for streamlined production and flexibility across industries Wauseon Machine highlights its Redeployable Automation Module, a transformative solution designed to enhance automation efficiency across industries. Engineered for versatility and cost-effectiveness, this platform integrates seamlessly into various manufacturing processes, offering flexibility from manual to fully automated operations. Its modular design allows for easy customization and redeployment, adapting to changing production needs such as assembly, sorting, testing, and handling tasks. This innovative platform represents WM’s commitment to advancing manufacturing technologies, reducing initial investment costs, and accelerating deployment timelines. Recent implementations have demonstrated remarkable results, including a significant reduction in labor requirements and a notable 28% increase in production output. Whether used in a single-cell configuration or integrated into a larger assembly line, the Redeployable Automation Module empowers businesses to optimize their operational efficiency. Wauseon Machine, offering extensive fabrication capabilities, ensures every component of the Redeployable Automation Module meets stringent quality and performance standards. With over four decades of experience, Wauseon Machine continues to innovate in automation and precision machining, driving industry standards and meeting the evolving needs of its customers. Founded in 1983, WM has grown from a small machine shop to a leader in robotics automation and precision machining. The introduction of the Redeployable Automation Module underscores WM’s commitment to delivering cutting-edge solutions that enhance productivity and operational flexibility in manufacturing environments.
Episode 531: Deus Robotics Delivering End-to-End Warehouse Automation
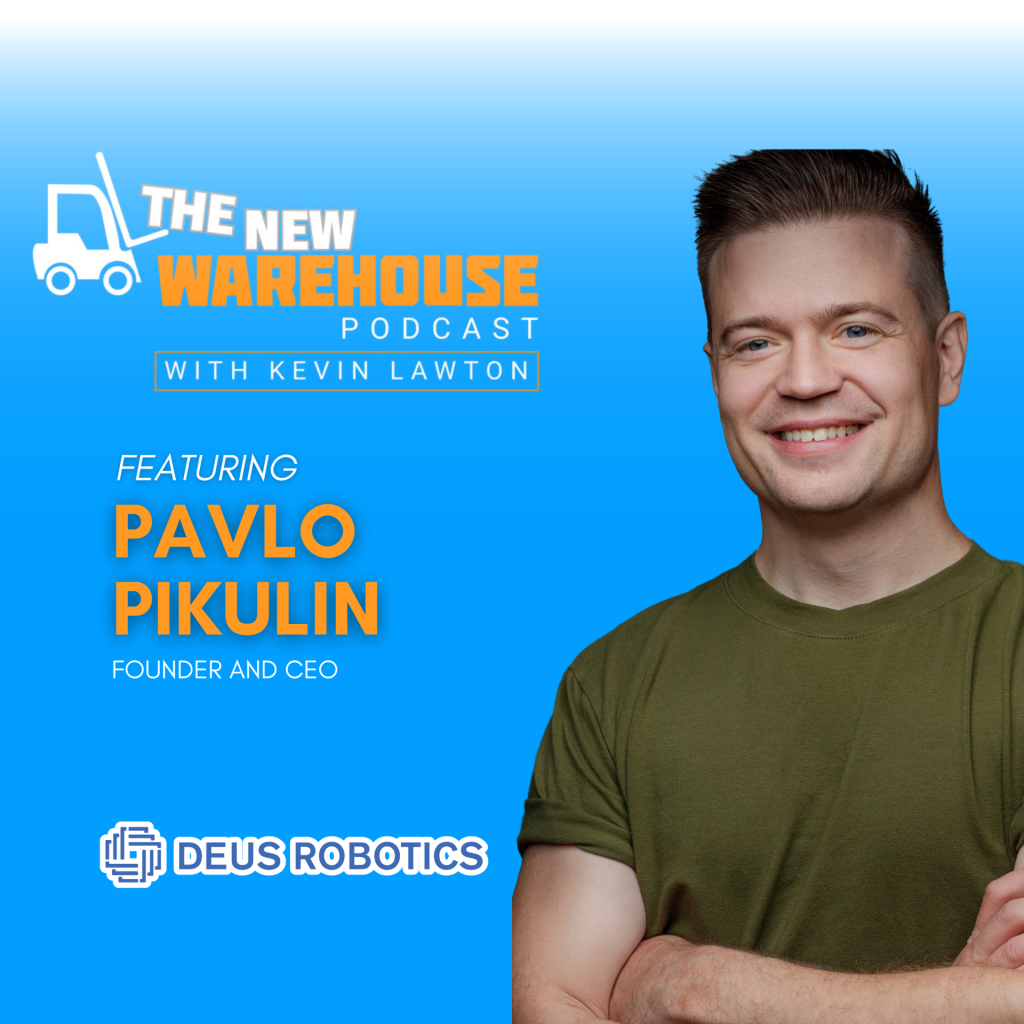
The New Warehouse Podcast welcomes Pavlo Pikulin, Founder and CEO of Deus Robotics, to discuss his passion for robotics. Pavlo’s passion for robotics traces back to his childhood dream of building robots to improve lives. With a background in AI and gaming, he founded Deus Robotics, focusing on providing end-to-end robotic solutions for warehouse operations. The discussion dives into how Deus Robotics integrates diverse robotic systems, utilizing AI to enhance automation efficiency. Pavlo also explores the unique challenges of robotic automation and the company’s approach to overcoming them. Transforming Warehouses with AI Pavlo’s early experience in gaming led to the development of advanced AI technologies, which are now the backbone of Deus Robotics’ solutions. By leveraging AI, Deus Robotics connects different robotic systems, ensuring seamless communication and coordination between hardware from multiple providers. “Our AI platform connects all systems,” Pavlo explains, “we can provide robots from different manufacturers, and they can work together in one system.” The integration of diverse robotic systems is critical in modern warehouses. Rather than relying on a single provider, Deus Robotics’ AI platform facilitates a unified approach to automation, enabling flexibility and reducing business costs. Overcoming Automation Challenges Integrating automation can be daunting for many warehouse operators, often due to concerns about cost and complexity. Pavlo recognizes that the biggest challenge for warehouse managers is understanding how to integrate robotic solutions effectively. He advises a phased approach: “Automate step by step, make small pilots in a small space… after that, you can scale it to a bigger part of the warehouse.” Deus Robotics’ end-to-end solutions address these concerns by offering project planning, simulations, and ongoing support. They ensure a smooth transition to automation without disrupting current operations. This step-by-step method helps warehouse managers test solutions on a smaller scale, minimizing risk while maximizing efficiency. The Future of Robotic Automation Pavlo predicts that robotic automation will continue to expand, driven by AI and sensor technology advancements. He highlights that robots are not just about hardware but the AI driving them, which will revolutionize the industry. “In the future, it will be easier to integrate robots, like buying a vacuum cleaner robot today,” Pavlo asserts. Deus Robotics is positioning itself as a leader in this space by offering flexible, modular solutions that cater to various operational needs. From large-scale warehouses to smaller facilities, their AI-driven systems will become increasingly accessible and offer significant operational cost reductions. Key Takeaways on End-to-End Warehouse Automation Deus Robotics’ AI platform enables seamless integration between robots from different manufacturers, optimizing warehouse operations. A phased approach to automation helps mitigate risks and ease the transition for warehouse operators. Robotic automation, powered by AI, is becoming more accessible and offers significant cost reductions for large and small operations alike. The New Warehouse Podcast EP 531: Deus Robotics Delivering End-to-End Warehouse Automation
Kito Crosby announces appointment as official supplier to The Ocean Cleanup
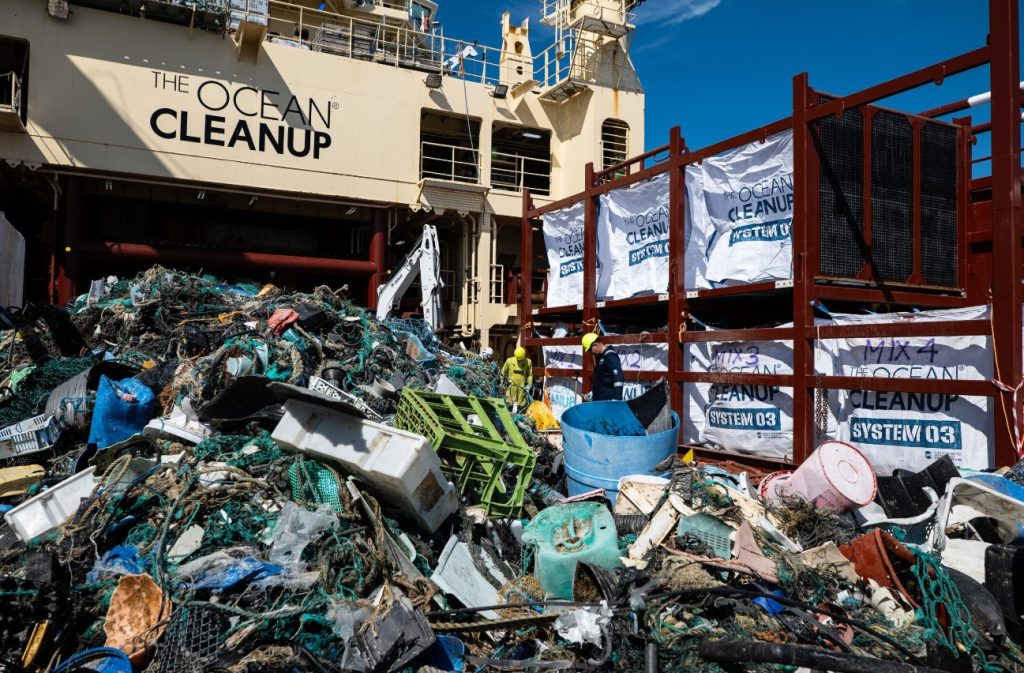
The Ocean Cleanup, a global nonprofit, and Kito Crosby, an international manufacturer in the lifting and securement industry, just announced Kito Crosby as the Ocean Cleanup’s Official Supplier of lifting and securement hardware. Through this partnership, Kito Crosby will provide high-quality lifting and securement products, expert training, and technical support to help The Ocean Cleanup remove plastic waste from the world’s oceans and rivers. Combining Kito Crosby’s innovative equipment with The Ocean Cleanup’s cutting-edge technology, this collaboration aims to enhance efficiency in ocean waste removal efforts and make significant strides toward a cleaner, healthier environment. “Through this partnership with The Ocean Cleanup, we are proud to contribute with our products made especially for safe & long-lasting use in marine environments, engineering support, training and expertise, and decades of experience in the maritime industry to help make a real difference in tackling ocean plastic pollution. By combining our capabilities with The Ocean Cleanup’s groundbreaking work, we aim to create lasting, positive change for the planet,” said Robert Desel, CEO of Kito Crosby.
Matthews Automation welcomes Christian Schauer as new Business Development Manager for EMEA
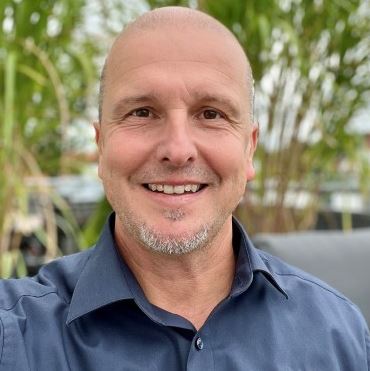
Matthews Automation has announced the appointment of Christian Schauer as the new Business Development Manager for the EMEA region. Christian will oversee sales and manage the growing interest and installations of Matthews’ advanced warehouse automation solutions across Europe, the Middle East, and Africa. Christian will be responsible for driving the adoption of Matthews’ innovative warehouse automation technologies, including NEXUS warehouse execution system (WES) software, controls for material handling equipment, robotics, and Lightning Pick paperless order picking systems. These solutions enhance distribution centers’ efficiency, productivity, and quality, especially for omnichannel order fulfillment. Matthews Automation, a U.S.-based company located in Cincinnati, Ohio, Waukesha, Wisconsin, and now Estenfeld, Germany, has been a trusted material handling automation and software provider for over 30 years. With thousands of installations in distribution centers worldwide, Matthews Automation continues to expand its global footprint. Recent international projects include new installations in Canada, China, the U.K., and several sites across Europe. It should be noted that Matthews Automation is a division of Matthews International, which has several successful industrial automation brands already established in Europe for decades. These include Matthews Engineering, a global provider of calendars, rotary processing systems, turnkey production lines for industries such as automotive and energy, and Matthews Marking Systems, an international provider of cutting-edge technology and equipment for the marking and coding industry. Christian will be based in their EMEA headquarters in Estenfeld, Germany, now offering sales, service, and support for both Matthews’ industrial printing and warehouse automation technologies. With previous strategic business development roles at other industrial automation providers, Christian has successfully built new markets and applications for manufacturing process improvement technologies, including 3D machine vision, lasers, and collaborative robotics, for over twenty years. “I’m thrilled to join Matthews Automation as the new Business Development Manager for EMEA,” said Christian. “With my extensive background in providing advanced industrial technologies, I look forward to helping customers transform their distribution centers with our state-of-the-art material handling automation to drive greater productivity, quality, and success.” “For decades, global brands have optimized e-commerce and omnichannel order fulfillment in their North American distribution centers with our software, controls, and picking systems, and now adoption is quickly growing in locations worldwide,” shares Gary Cash, Senior Vice President and General Manager of Matthews Automation. “We’re excited to have Christian’s expertise to communicate and deliver innovative warehouse automation solutions to brands in the EMEA region seeking to take their supply chain operations to the next level.”
Herc Holdings reports Nine Months 2024 results and updates 2024 Full Year Guidance
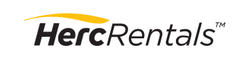
Record equipment rental revenue of $866 million, an increase of 13% Record total revenues of $965 million, an increase of 6% Rental pricing increased 2.3% year-over-year M&A and greenfield openings offset the impact of decelerating local-market revenue growth Net income increased 8% to $122 million, or $4.28 per diluted share Adjusted EBITDA of $446 million increased 9%; adjusted EBITDA margin of 46.2% Free cash flow of $218 million for the nine months ended September 30, 2024 Herc Holdings Inc. has reported financial results for the September 30, 2024 quarter. “In the third quarter, we significantly outpaced overall industry growth on both a total rental revenue basis and from an organic revenue perspective,” said Larry Silber, president and chief executive officer. “By capitalizing on our broad end-market coverage, diversified product and services offering, and expanding share in resilient urban markets, we continue to deliver strong volume and a solid price/mix performance. “We increased third quarter rental revenue by 13% to a new quarterly record, primarily reflecting the continued robust growth from mega projects and contributions from our increased branch network and recent acquisitions. This growth was achieved despite a tough year-over-year comparison and a challenging interest rate environment for local project starts,” said Silber. “As we manage the complexities of disparate levels of demand across geographies, end markets, and project types, our team is agile and remains focused on aligning costs and balancing fleet while continuing to support the growth of our business and deliver outstanding customer service.” 2024 Third Quarter Financial Results Total revenues increased 6% to $965 million compared to $908 million in the prior-year period. The year-over-year increase of $57 million was primarily related to an increase in equipment rental revenue of $101 million, reflecting positive pricing of 2.3% and increased volume of 10.7%. Sales of rental equipment decreased by $43 million during the period. Fleet rotation in the prior-year period was accelerated due to the easing of supply chain disruptions in certain categories of equipment. Dollar utilization increased to 42.2% in the third quarter compared to 42.1% in the prior-year period. Direct operating expenses were $334 million, or 38.6% of equipment rental revenue, compared to $288 million, or 37.6% in the prior-year period. The increase related primarily to the business’s growth, with personnel and facilities costs associated with greenfields and acquisitions. Rental equipment depreciation increased by 4% to $174 million due to a higher year-over-year average fleet size. Non-rental depreciation and amortization increased 14% to $33 million, primarily due to the amortization of acquisition intangible assets. Selling, general, and administrative expenses were $123 million, or 14.2% of equipment rental revenue, compared to $115 million, or 15.0%, in the prior-year period due to the continued focus on improving operating leverage while expanding revenues. Interest expense increased to $69 million compared with $60 million in the prior-year period due to increased borrowings primarily to fund acquisition growth and investment in rental equipment. Net income was $122 million compared to $113 million in the prior-year period. Adjusted net income increased 9% to $124 million, or $4.35 per diluted share, compared to $114 million, or $4.00 per diluted share, in the prior-year period. The effective tax rate was 24% compared to 23% in the prior-year period. Adjusted EBITDA increased 9% to $446 million compared to $410 million in the prior-year period, and adjusted EBITDA margin was 46.2% compared to 45.2% in the prior-year period. 2024 Nine Months Financial Results Total revenues increased 7% to $2,617 million compared to $2,450 million in the prior-year period. The year-over-year increase of $167 million was primarily related to an increase in equipment rental revenue of $229 million, reflecting positive pricing of 3.5% and increased volume of 8.4%, partially offset by an unfavorable mix driven primarily by inflation. Sales of rental equipment decreased by $63 million during the period. Fleet rotation in the prior year period was accelerated due to the easing of supply chain disruptions in certain categories of equipment. Dollar utilization increased to 41.0% compared to 40.8% in the prior-year period. Direct operating expenses were $967 million, or 41.1% of equipment rental revenue, compared to $851 million, or 40.1% in the prior-year period. The increase is primarily related to the business’s growth and personnel and facilities costs associated with greenfields and acquisitions. Additionally, delivery expenses were higher due to internal equipment transfers to branches in higher-growth regions to drive fleet efficiency. Finally, insurance expenses increased, primarily related to increased self-insurance reserves due to claims development attributable to unsettled cases. Rental equipment depreciation increased by 4% to $499 million due to a higher year-over-year average fleet size. Non-rental depreciation and amortization increased by 11% to $92 million, primarily due to the amortization of acquisition intangible assets. Selling, general, and administrative expenses were $358 million, or 15.2% of equipment rental revenue, compared to $332 million, or 15.7%, in the prior year due to the continued focus on improving operating leverage while expanding revenues. Interest expense increased to $193 million compared with $162 million in the prior-year period due to increased borrowings primarily to fund acquisition growth and investment in rental equipment. Net income was $257 million compared to $256 million in the prior-year period. Adjusted net income increased 2% to $265 million, or $9.30 per diluted share, compared to $260 million, or $9.03 per diluted share, in the prior-year period. The effective tax rate was 23% compared to 21% in the prior-year period. Adjusted EBITDA increased 7% to $1,145 million compared to $1,070 million in the prior-year period, and adjusted EBITDA margin was 43.8% compared to 43.7% in the prior-year period. Rental Fleet Net rental equipment capital expenditures were as follows (in millions): Nine Months Ended September 30, 2024 2023 Rental equipment expenditures $ 753 $ 1,100 Proceeds from disposal of rental equipment (198 ) (231 ) Net rental equipment capital expenditures $ 555 $ 869 As of September 30, 2024, the Company’s total fleet was approximately $7.1 billion at OEC. The average fleet at OEC in the third quarter increased by 12% compared to the prior-year period. The average
Hangcha Canada celebrates five-year milestone
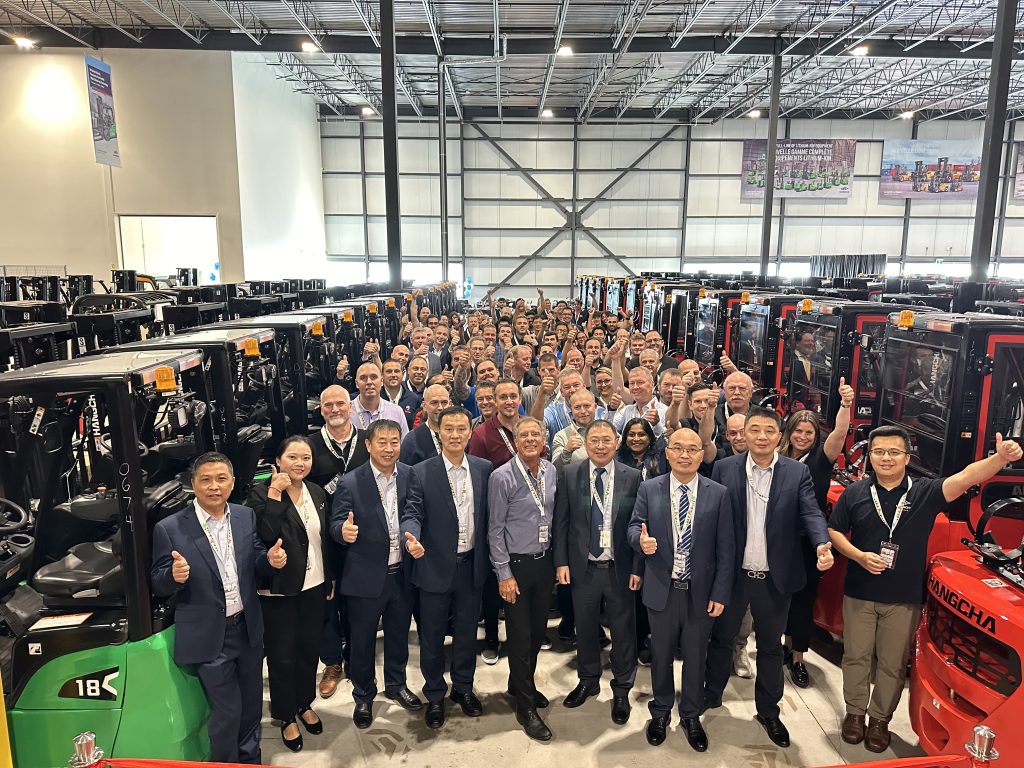
Hangcha Forklift Canada is celebrating a significant milestone—five years since its establishment. Officially launched on October 18, 2019, with an investment of USD 3 million, Hangcha Canada was built to bring a direct distribution model to the Canadian market. Fast-forward to today, and the company has coast-to-coast service capabilities through a network of 17 dealers. By cutting out intermediaries, Hangcha Canada is more agile and responsive in doing business with its dealers, offering personalized support and solutions that fit the unique needs of each Canadian market. In 2023 alone, Hangcha Canada sold 2,463 units across Class 1 to Class 7 forklifts, supplying relatively small operations to Fortune 500 companies in the automotive, warehousing, cosmetics, and food industries. At its recent 4th annual Canadian Dealers’ Conference, which coincided with its 5th anniversary, Hangcha Canada brought together all 17 dealers under the theme “Engage, Empower, and Elevate.” The conference focused on strategies for the future, such as expanding rental fleets and enhancing service capabilities.
Sales Engineering Co. welcomes Derek Anderson as Territory Sales Manager for New England
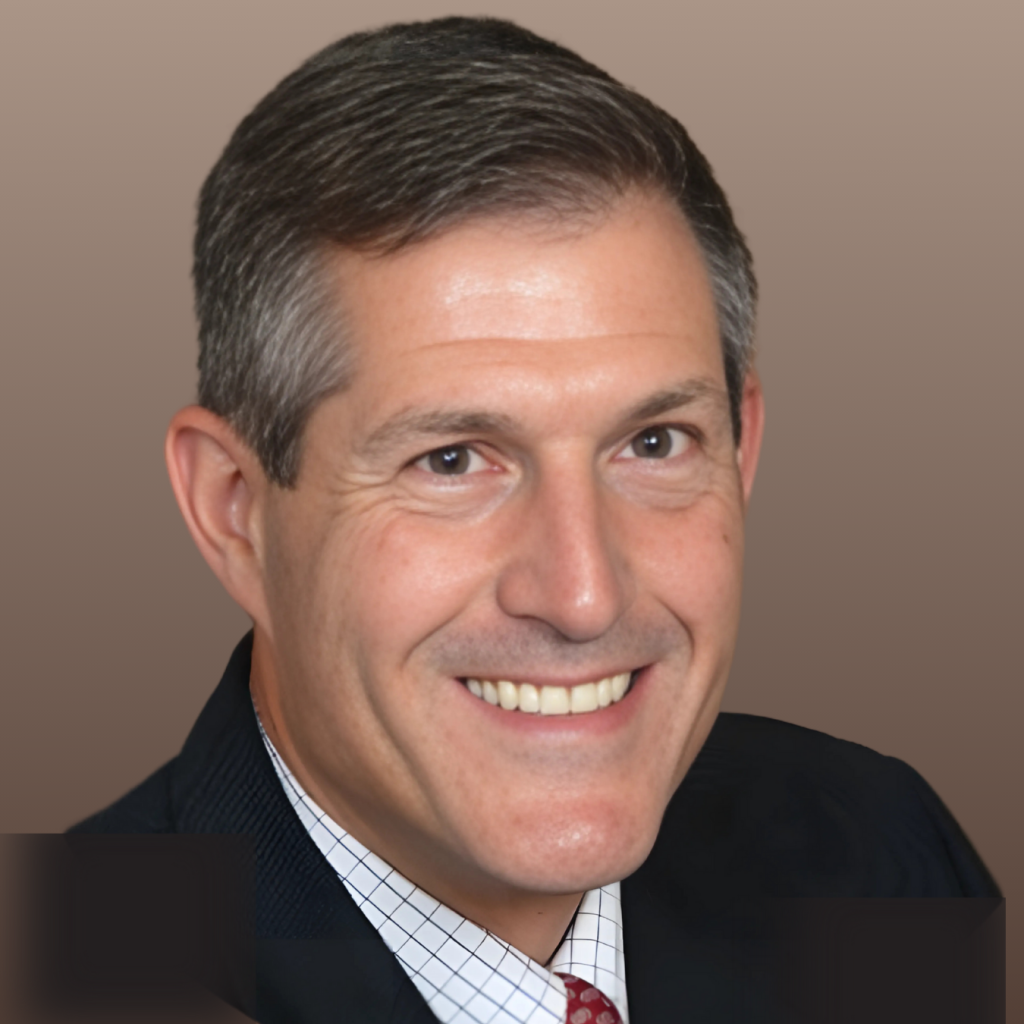
Sales Engineering Co., a manufacturers’ representative in the New England electronics market, has announced Derek Anderson’s appointment as New England’s new Territory Sales Manager. With over 28 years of sales leadership experience and a robust background in the electronics and semiconductor industries, Derek drives growth and strengthens partnerships across the region. Derek, a Worcester Polytechnic Institute graduate with a degree in electrical engineering and an MBA from the Olin School at Babson College, has led sales teams on both regional and national scales. His proven track record in sales strategy and team development will enhance Sale Engineering’s offerings to its technology partners and clients. “Derek Anderson’s wealth of experience and strategic vision make him a tremendous asset to our team,” said Tim Kilfoil, president of JF Kilfoil, the parent company of Sales Engineering. “His expertise will be invaluable as we continue to expand our reach and strengthen our offerings to our technology partners, customers, and distribution partners. We are thrilled to have him on board and are confident in the positive impact he will bring.” Derek will lead and mentor a dynamic team of manufacturing partners and account managers in his new role. He will focus on matching customers with Sales Engineering’s trusted supplier partners and their value-added technology solutions. His leadership is expected to foster continued growth and cultivate strong relationships with Sales Engineering’s customers and distribution networks.
Carolina Handling continues 58th anniversary celebration with 58 for 58 Season of service
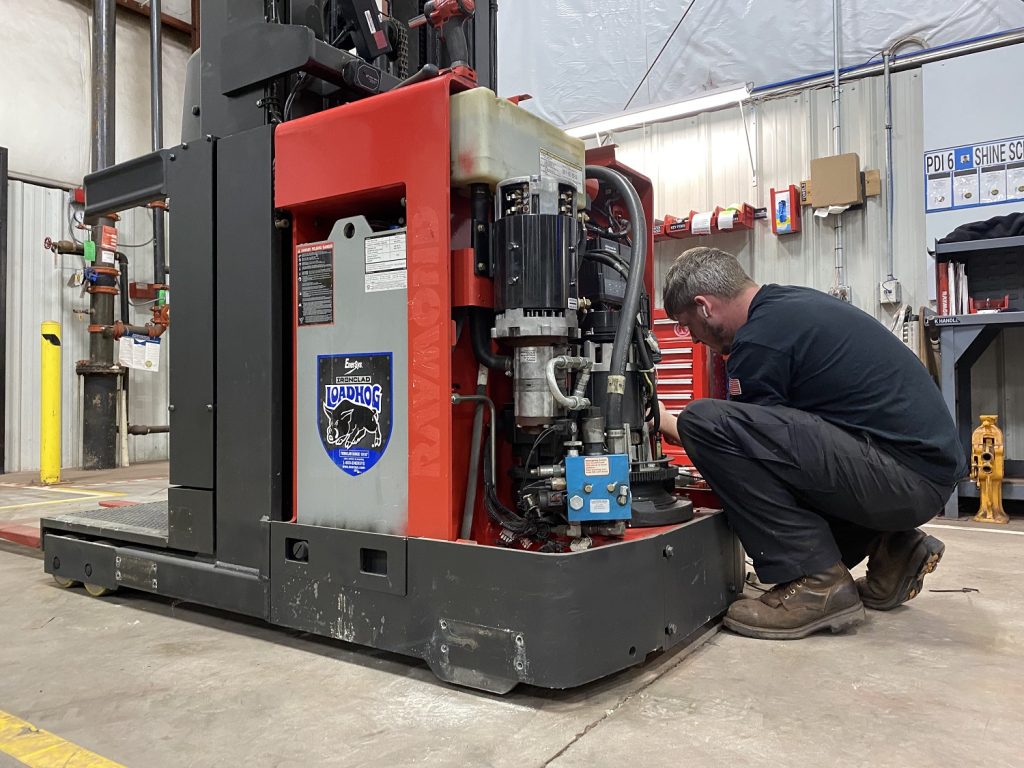
In 2024, to celebrate its 58th anniversary in business, Carolina Handling donated 58 Raymond motorized pallet jacks to hunger relief organizations throughout the Carolinas, Georgia, and Alabama. The company is extending its anniversary celebration by donating 58 hours of service to qualifying nonprofits with material handling equipment needing repair. “Many of the nonprofits we visited over the past few months while delivering pallet jacks have forklifts or pallet trucks that no longer operate, but there are no resources to cover repairs,” said Carolina Handling Chief Operating Officer Joe Perkins. “With a team of more than 425 technicians who maintain all lift truck brands and models, service is our specialty, so we’re expanding our 58th-anniversary celebration by donating 58 hours of service to hunger relief organizations throughout our territory.” In its new fiscal year, which began April 1, Carolina Handling turned its philanthropic focus to hunger relief, launching a 58-for-58 motorized pallet jack giveaway to help lighten the load for those who receive, store, and distribute thousands of pounds of food each year in their communities. The 58 organizations that received a pallet jack from Carolina Handling combine to serve 11.2 million individuals each year throughout the Carolinas, Georgia, Alabama, and the panhandle of Florida, distributing 290 million pounds of food. “The logistics of moving thousands of pounds of food can be overwhelming to organizations that don’t have reliable, safe equipment and processes,” Perkins said. “That’s where companies like Carolina Handling specializing in material handling solutions can help.” For more information on Carolina Handling’s 58 for 58 Season of Service and to apply for a no-cost service call, excluding parts, please visit carolinahandling.com/community/58-for58.
Johnson Electric and Aegis Sortation announce distribution partnership
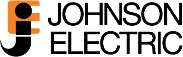
Aegis Sortation becomes exclusive technology distributor for Johnson Electric in the North American market Johnson Electric has announced an exclusive distribution agreement in partnership with Aegis Sortation. Under the agreement, Aegis will become the technology distributor for Johnson Electric TrueDrive™ and VersaSort™ products in North America. The decision to formulate the strategic partnership builds upon Aegis’ brand recognition in the material handing industry and Johnson Electric’s 65 years of expertise in motion system solutions. “As e-commerce sales continue to grow in the United States, we’re thrilled to embark on this partnership with Aegis Sortation, which is trusted for its proven solutions in the material handling industry,” said Stephen Pennington, vice president, IPG Americas, for Johnson Electric. “Their leadership in the freight and parcel and warehouse and distribution industries is second to none. We’ve worked together for over a decade and are happy to build upon our combined expertise to bring even more value to our collective customers with this agreement.” Aegis Sortation will be exclusively distributing two Johnson Electric products: TrueDrive, an innovative motorized drive roller conveyor system, as well as VersaSort, a compact steerable wheel table that allows diverting functions to operate up to twice as fast in small- to larger-sized sortation systems. Although not part of the distribution agreement, Aegis will also leverage Solligence™, a fast rotary actuator designed for divert motion in sliding shoe sorters. The rotary’s artificial intelligence monitors motion profiles and adjusts for wear, maintaining consistent speed and preventing performance degradation over time. “We’re committed to delivering transformative innovation with solutions that address the growing challenges in the material handling industry, especially around labor shortages and operational efficiency,” said Tony Young, CEO of Aegis Sortation. “By leveraging Johnson Electric’s cutting-edge solutions, we’re creating sortation modules that solve our customers’ variable package mix challenges, like irregular parcels, which are typically processed manually. This new technology also allows our customers to double their throughput while simultaneously reducing costs through improved asset utilization.”
Recession-Proofing your business with automation: A Strategic Approach
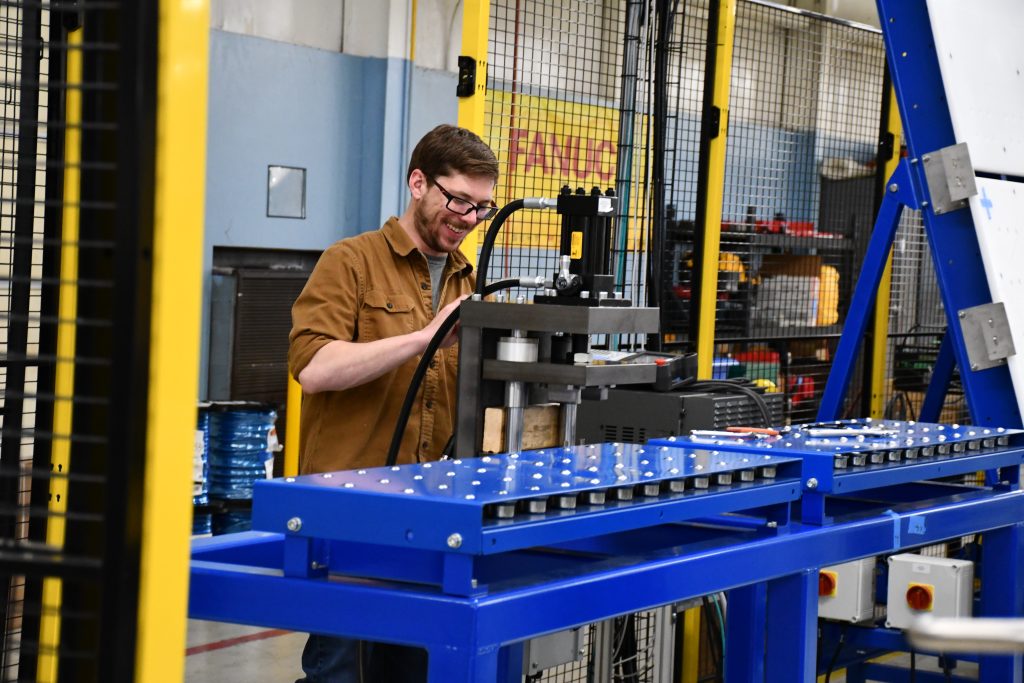
In uncertain economic times, businesses face numerous challenges that can hinder their efficiency, safety, and sustainability. One key strategy companies can deploy to withstand recessionary periods is to consider the holistic impact automation can have on their business. This article explores how companies ensure safe, consistent operations, and position themselves for sustainable growth once the economic storm passes. What Does It Mean to Recession-Proof a Business? Recession-proofing involves positioning your company to remain resilient and stable even when market conditions are unfavorable. Typically, this includes some combination of improving cash flow, optimizing resources, and trimming unnecessary expenses. But recession-proofing can, and should, go beyond managing mere financials; it also means ensuring your company is adaptable and flexible, utilizes data-driven decision-making, and is prepared to compete in an environment of reduced demand and fierce competition. Investing in automation is one-way businesses can streamline their processes, reduce labor dependency, and boost productivity—all critical factors in weathering an economic downturn. Mitigating the Domino Costs of Labor Turnover Recession-proofing a business should include taking action to address the manufacturing industry’s biggest pain points in your company before an economic downturn. In an industry where labor shortages can severely disrupt production, manufacturers are increasingly turning to automation as a strategic solution. On average, there are between 500,000 and 700,000 job openings in the U.S. manufacturing sector at any given time, with many positions going unfilled due to the undesirability of repetitive, low-skill jobs. Automation can fill this gap by taking over monotonous tasks, allowing companies to redirect their human resources to higher-level, skilled roles. This not only improves efficiency but also opens up new opportunities for employees who can now focus on more complex tasks, such as machine operation and maintenance. Automated systems can operate 24/7 without the need for breaks or holidays, significantly maximizing uptime while providing labor consistency. It’s also important to remember that labor costs extend far beyond mere wages. The cost of benefits like health care and disability insurance continues to rise, driving labor costs up. Plus, recruiting and training new or replacement workers requires more onboarding effort and resources than businesses can extend. Unfortunately, higher turnover combined with too few resources often results in inadequately trained employees and lower-quality products over time. Inconsistency in product quality will negatively impact brand reputation and consumer loyalty, reducing market share and impacting your bottom line. Plus, inconsistency in employee training protocols because of a lack of resources can seriously impact safety, leading to preventable accidents. Automation offers companies consistent, reliable output that can improve facility safety and mitigate high turnover rates and the associated costs of recruitment, training, and beyond. For businesses that produce essential consumer goods, ensuring that products can get to market quickly and reliably is critical. Labor shortages can disrupt this flow, leading to loss of market share. Plus, in a recessionary environment, competition will inevitably increase as demand decreases. Ensuring your company has solidified consumer loyalty within its market segment should be a key focus area. By investing in automation, companies can safeguard their production capacity, ensuring they can meet market demand regardless of labor constraints. Beyond filling the labor gap, automation ensures consistency in output, enhances product quality, and helps safeguard against the rising costs associated with employee turnover. Accuracy, Scalability, and Standardization: The Benefits of Holistic Automation Automation offers substantial benefits including higher production output, enhanced precision and consistency, and increased employee safety. While it’s easy to make the case for the financial benefits of automation, improved workplace safety and product quality should not be overlooked as these factors have wide-reaching implications across organizations. “There is nothing more important than safety to any organization, any factory,” says Carl Doeksen, Global Robotics Automation Director at 3M. “We find that the safest factories are also the most efficient and are putting out the highest quality products. Quality lies in precision and repeatability.” The key to sustainable and consistent cost-minimization lies in safety and quality assurance. One of the main facets of quality, as Doeksen says, is precision and repeatability. This is where having adaptable manufacturing lines offers a huge advantage. Automation systems can be designed for reuse across different production lines, making them a flexible and cost-effective solution for driving consistency across products. Plus, by standardizing the mechanical, electrical, and software components of their machines, businesses can simplify maintenance and lower the total cost of ownership over time. The key to efficiency is streamlining operations—making the equipment you use as widely applicable as possible. As such, deployable modules can be powerful tools for recession-proofing. These adaptable, standardized systems can be rapidly implemented to enhance operations across various sectors. In warehousing, for instance, deployable modules might include automated order fulfillment systems that integrate robotics and software to streamline processes. Their key advantages lie in their ability to be quickly adapted to existing infrastructures, minimizing the time and cost of overhauls. Moreover, the scalability of deployable modules allows businesses to flexibly adjust to market demands without requiring large capital investments, making them both cost-effective and efficient. For example, incorporating robotics into business operations can maintain an extremely high accuracy level on the first pass, significantly reducing errors and waste. Robots, particularly in warehouse settings, perform tasks such as picking, packing, and transporting goods. These automated systems increase productivity by operating continuously, reducing cycle times, and optimizing labor utilization. This high level of precision is especially valuable for tasks requiring exact measurements, such as working within 10-millimeter tolerances—something challenging for humans but routine for robots. Automation not only drives financial gains through higher production output and reduced operational costs but also plays a pivotal role in ensuring safety and efficiency within the workplace. By minimizing human involvement in repetitive and hazardous tasks, automation reduces the risk of workplace injuries while enhancing overall productivity. As Doeksen emphasizes, the safest factories are often the most efficient, consistently producing the highest quality products. The precision and repeatability offered by automated systems not only improves product quality, but also contributes to long-term cost savings through
Nucor reports results for the Third Quarter of 2024
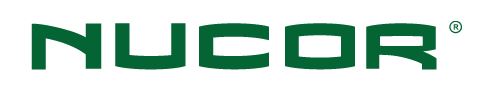
Consolidated net earnings attributable to Nucor stockholders of $249.9 million, or $1.05 per diluted share Adjusted net earnings attributable to Nucor stockholders of $353.0 million, or $1.49 per diluted share Net sales of $7.44 billion Net earnings before noncontrolling interests of $302.8 million; EBITDA of $869.0 million Nucor Corporation announced consolidated net earnings attributable to Nucor stockholders of $249.9 million, or $1.05 per diluted share, for the third quarter of 2024. Excluding non-cash impairment charges taken during the quarter, Nucor’s third quarter of 2024 adjusted net earnings attributable to Nucor stockholders were $353.0 million, or $1.49 per diluted share. By comparison, Nucor reported consolidated net earnings attributable to Nucor stockholders of $645.2 million, or $2.68 per diluted share, for the second quarter of 2024 and $1.14 billion, or $4.57 per diluted share, for the third quarter of 2023. Reflected in the third quarter of 2024, losses and impairments of assets are non-cash charges of $83.0 million, or $0.27 per diluted share, and $40.0 million, or $0.17 per diluted share, related to the impairment of certain noncurrent assets in the raw materials and steel products segments, respectively. In the first nine months of 2024, Nucor reported consolidated net earnings attributable to Nucor stockholders of $1.74 billion, or $7.22 per diluted share, compared with consolidated net earnings attributable to Nucor stockholders of $3.74 billion, or $14.83 per diluted share, in the first nine months of 2023. “Thank you to our Nucor teammates for continuing to set new records for safety performance while generating over $1.30 billion of cash from operations for the quarter,” said Leon Topalian, Nucor’s Chair, president, and Chief Executive Officer. “Nucor’s market leadership, product diversity, and strong balance sheet enable us to provide meaningful returns to shareholders and execute our growth strategy even in the face of market uncertainty.” Selected Segment Data Earnings (loss) before income taxes and noncontrolling interests by segment for the third quarter and first nine months of 2024 and 2023 were as follows (in thousands): Three Months (13 Weeks) Ended Nine Months (39 Weeks) Ended September 28, 2024 September 30, 2023 September 28, 2024 September 30, 2023 Steel mills $ 309,123 $ 882,614 $ 2,056,689 $ 3,124,549 Steel products 313,972 806,731 1,266,922 2,788,322 Raw materials (66,332) 71,367 (17,355) 267,918 Corporate/eliminations (168,490) (212,630) (794,479) (986,141) $ 388,273 $ 1,548,082 $ 2,511,777 $ 5,194,648 Financial Review Nucor’s consolidated net sales decreased 8% to $7.44 billion in the third quarter of 2024 compared with $8.08 billion in the second quarter of 2024 and decreased 15% compared with $8.78 billion in the third quarter of 2023. Average sales price per ton in the third quarter of 2024 decreased 6% compared with the second quarter of 2024 and decreased 15% compared with the third quarter of 2023. Approximately 6,196,000 tons were shipped to outside customers in the third quarter of 2024, a 1% decrease compared with the second quarter of 2024 and the third quarter of 2023. Total steel mill shipments in the third quarter of 2024 decreased 3% compared with the second quarter of 2024 and were comparable to the third quarter of 2023. Steel mill shipments to internal customers represented 19% of total steel mill shipments in the third quarter of 2024, compared with 21% in the second quarter of 2024 and 20% in the third quarter of 2023. Downstream steel product shipments to outside customers in the third quarter of 2024 decreased 6% compared with the second quarter of 2024 and decreased 11% compared with the third quarter of 2023. In the first nine months of 2024, Nucor’s consolidated net sales of $23.66 billion decreased 12% compared with consolidated net sales of $27.01 billion in the first nine months of 2023. Total tons shipped to outside customers in the first nine months of 2024 were approximately 18,709,000 tons, a decrease of 3% compared with the first nine months of 2023, and the average sales price per ton in the first nine months of 2024 decreased 10% compared with the first nine months of 2023. The average scrap and scrap substitute cost per gross ton used in the third quarter of 2024 was $378, a 5% decrease compared to $396 in the second quarter of 2024 and a 9% decrease compared to $415 in the third quarter of 2023. The average scrap and scrap substitute cost per gross ton used in the first nine months of 2024 was $399, a 7% decrease compared to $429 in the first nine months of 2023. Pre-operating and start-up costs related to the Company’s growth projects were approximately $168 million, or $0.54 per diluted share, in the third quarter of 2024, compared with approximately $137 million, or $0.43 per diluted share, in the second quarter of 2024 and approximately $101 million, or $0.31 per diluted share, in the third quarter of 2023. In the first nine months of 2024, pre-operating and start-up costs related to the Company’s growth projects were approximately $430 million, or $1.36 per diluted share, compared with approximately $273 million, or $0.83 per diluted share, in the first nine months of 2023. Overall, operating rates at the Company’s steel mills were 75% in the third quarter and second quarter of 2024 and 77% in the third quarter of 2023. Operating rates in the first nine months of 2024 decreased to 77%, compared to 80% in the first nine months of 2023. Financial Strength At the end of the third quarter of 2024, we had $4.86 billion in cash and cash equivalents and short-term investments on hand. The Company’s $1.75 billion revolving credit facility remains undrawn and does not expire until November 2026. Nucor continues to have the strongest credit ratings in the North American steel sector (A-/A-/Baa1), with stable outlooks at Standard & Poor’s and Fitch Ratings and a positive outlook at Moody’s. Commitment to Returning Capital to Stockholders Nucor repurchased approximately 2.5 million shares of its common stock during the third quarter of 2024 at an average price of $156.07 per share (approximately 11.0 million shares year-to-date
FMH Material Handling Solutions joins Towlift family
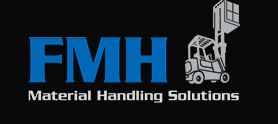
In 2022, FMH Material Handling Solutions changed ownership and remained under local management in El Paso, Denver, and Albuquerque. FMH officially joined the Towlift family, one of the country’s largest full-service material handling dealerships. It specializes in new and pre-owned equipment, rentals, industrial racking and storage, parts, service, and operator training. With locations across Ohio, Pennsylvania, and California, Towlift operates with the motto, “It’s the dealer that makes the difference!” and has been named a Dealer of Excellence over twenty times. With the addition of El Paso, Denver, and Albuquerque to the Towlift family, FMH Material Handling can offer an expanded portfolio of material handling solutions with a seamless customer experience. Towlift is in its third generation of family ownership, with sales and service locations in multiple states. It is one of the industry’s most experienced material-handling dealers and industrial equipment distributors. This experience gives Towlift the expertise to offer customers a full range of material handling solutions that improve their business operations. Bob Kwieciak currently serves as Towlift president.
Four New Power Transmission/Motion Control Categories introduced for PIE Technology Platform™
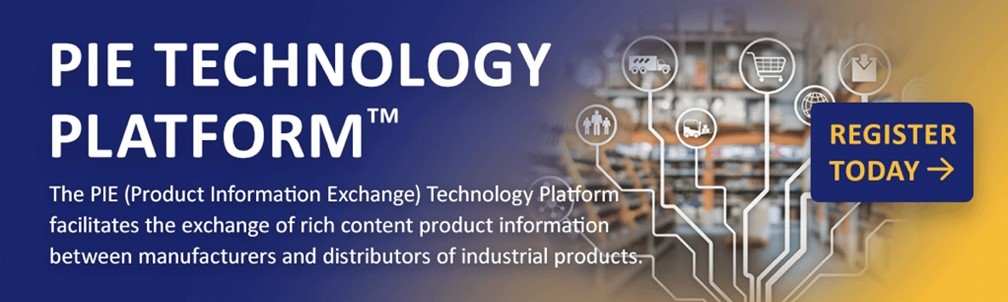
Bearing Specialists Association (BSA) and the Power Transmission Distributors Association (PTDA) announce the introduction of conveyors/material handling, couplings, motors, and linear bearings (round shaft) to the PIE Technology Platform™ (PIE). These additional product categories bring the total number of bearing and power transmission/motion control (PT/MC) categories available to 32. Additional categories in development include open gearing, enclosed gearing, and adjustable/variable speed drives. The essential tool for channel partners, PIE is a cloud-based platform that gives manufacturers and distributors of industrial products access to the most comprehensive catalog for the exchange of rich-content product information. Providing efficient, seamless, accurate, real-time data communication strengthens channel partner collaboration and advances online sales. Whether a distributor offers a simple online catalog or a full e-commerce experience, PIE ensures end customers have the most current and reliable product information. With data reliability at its core, PIE builds the trust that fosters customer loyalty and long-term success. With 24/7/365 access to PIE-compliant manufacturer partner content, distributors can map rich product data to their company-specific PIM system, website, or end-user digital communication using an automated tool. The single, secure, and standard platform is only accessible to authorized distributor partners, ensuring manufacturers can protect and maintain product data ownership. Both manufacturers and distributors benefit from reduced errors and staff time spent correcting inaccurate or outdated content. Learn more and register your company to participate at pietechnologyplatform.org.
Women In Trucking Association releases 2024-25 WIT Index Data
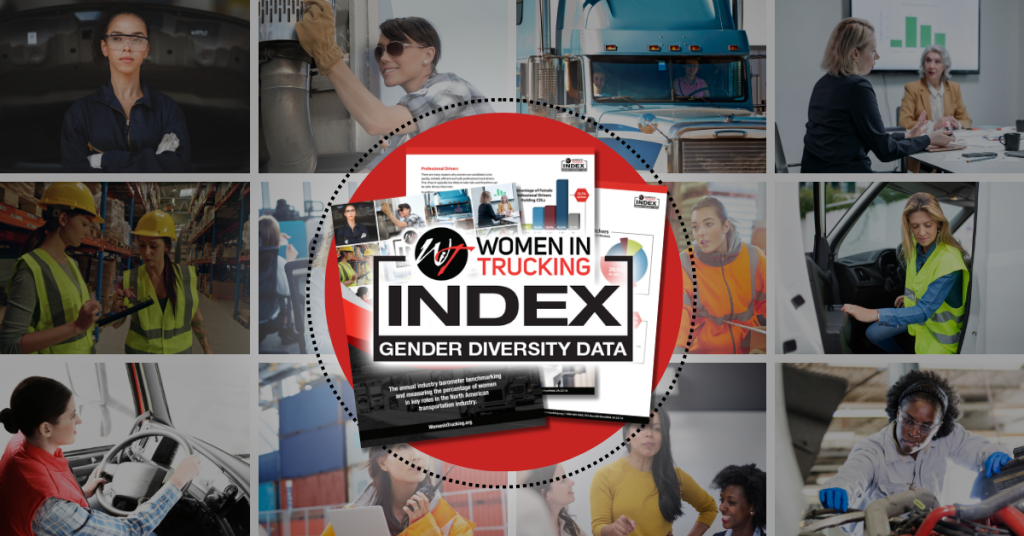
The Women In Trucking Association (WIT) recently released the findings of its 2024-25 WIT Index. This unique research is the industry’s barometer to benchmark and measure the percentage of women who hold critical roles in transportation. These roles include corporate management (C-Suite), those who serve on boards of directors, management and supervisory roles, and functional roles such as operations, technicians, HR/talent management, safety, and professional drivers. From August 2023 through April 2024, WIT conducted a survey of transportation organizations of all sizes to gather percentages of women in their workforce. The respondents were asked to report data that included demographics, the status of the company’s diversity and inclusion policy, and percentages of females in various roles within the company. Approximately 350 respondents reported their organizations’ gender diversity statistics in the WIT Index (2024-25) survey. Most (51.5%) represent for-hire motor carriers or companies with private fleets as part of the organization’s operations. Of those respondents representing organizations with fleet assets, 38% are for-hire motor carriers of various types (full truckload, less-than-truckload, refrigerated, flatbed, expedited, and liquid), and 13.5% are manufacturers, retailers, distributors, and other company types with private fleets. Another 13.5% of respondents are intermediary companies, including third-party logistics companies, truck brokers, and intermodal marketing companies (IMCs). The 2024-25 WIT Index survey found many women in influential leadership roles. Approximately 28% of those in C-Suite/executive positions are women, 34.5% of those in supervisory leadership roles are women, and 29.5% of those who serve on boards of directors are women. A significant percentage of women also hold roles in these functions: 74.5% in human resources/talent management, 38.5% in dispatcher roles, and 38.5% in safety. However, only 4% of truck diesel technicians are women. It has been a common assumption for years that the size of companies with for-hire or private fleets correlates to the percentage of professional truck drivers who are women. For the first time, the 2024-25 WIT Index reported a percentage of female professional truck drivers based on company workforce size. According to this year’s WIT Index, micro/small companies with less than 500 employees report that 12.5% of their professional driver population holding CDLs are women. Large/medium enterprises with 500 to 4,999 employees report that approximately 10.5% of their professional driver workforce holding CDLs are women. Giant/major enterprises with more than 5,000 employees report that approximately 7% of their truck driver population who hold CDLs are women. Notably, these percentages reflect professional truck drivers who hold CDLs and are driving medium- to heavy-duty commercial trucks, not last-mile or delivery vans or other vehicles that are not heavy-duty trucks. Percentages of company types Percentages of C-Suite/executives Percentages of supervisory leadership Percentages of boards of directors Percentages of HR/talent management Percentages of dispatchers Percentages of safety professionals Percentages of technicians Percentages of female professional drivers
AMH launches new stainless-steel series of chain and fittings
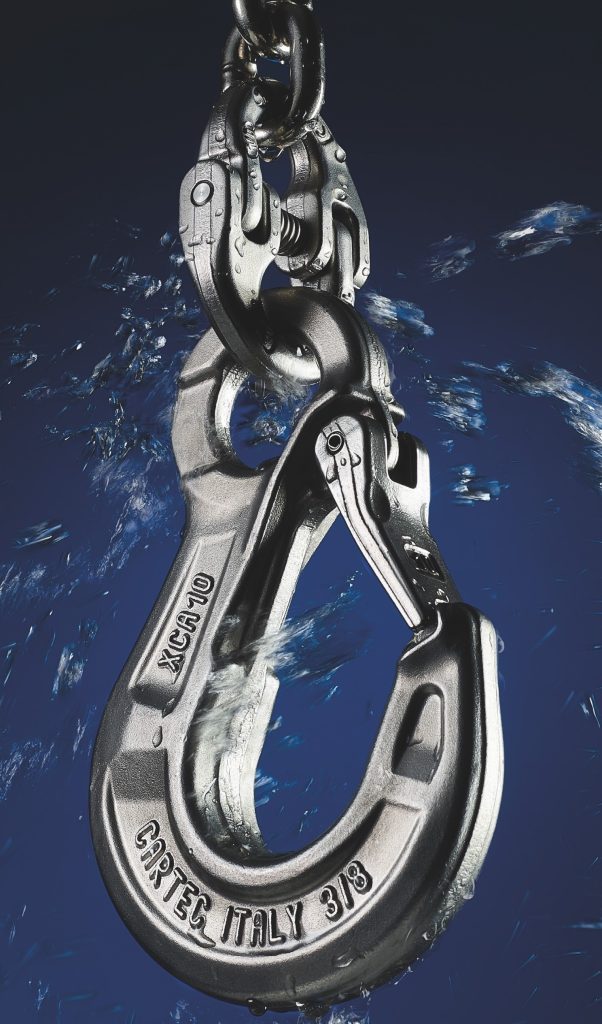
All Material Handling (AMH) is expanding its product offering with a new range of stainless-steel lifting chains and fittings. The high-quality, Italian-forged CARTEC Grade 60 stainless steel series is designed for lifting applications in marine and offshore environments, water and sewage, and even operations such as food production and pharmaceuticals. It is now available from AMH across North America. It completes AMH’s CARTEC offering, which already imports and supplies the CARTEC grade 100 and 80 steel chain fittings and lifting points such as swivel hoist rings and rotating eyebolts. Jim Canfield, National Sales Manager at AMH, said: “CARTEC is increasingly popular with lifting professionals because of the quality of these Italian-forged products. Expanding our range to include CARTEC stainless steel chain, sub-assemblies, and fittings enables us to bring these benefits to industries operating in more demanding environments.“ Stainless steel offers better corrosion protection in harsh conditions. It is also a more durable material and typically requires less maintenance in lifting applications. The comprehensive CARTEC range from AMH includes chains, master links, shackles, shortening clutches, hooks, links, and eyebolts.
Op-ed: Limiting plastic production leads us backwards
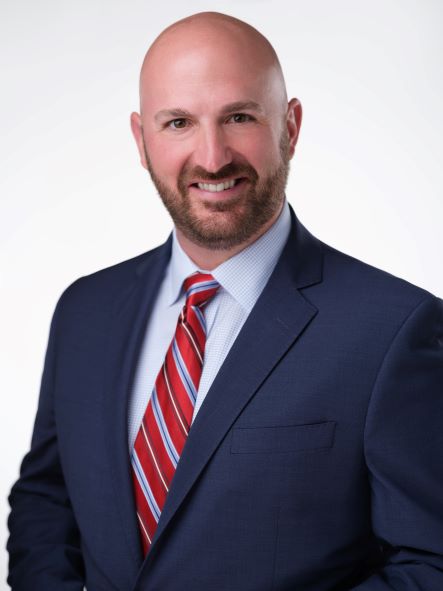
Matt Seaholm is the President and CEO of the Plastics Industry Association. Opinions are the author’s own. As political campaigns double down on the importance of American manufacturing, October brings real attention to this irreplaceable segment of the economy through the celebration of Manufacturing Month. Manufacturing Month provides an opportunity to acknowledge a miracle material that is integral to nearly every manufacturing process worldwide and the segment of our workforce that provides it. This material constitutes the majority of electric vehicles by volume, protects and preserves our food, insulates the wires connecting our homes and businesses, and is critical in producing solar panels and wind turbines. This material is plastic. Yet, despite its significance, the Biden administration has announced support for limiting global plastic production. In August, Reuters was the first to report that the administration is backing a global treaty to limit the amount of new plastic produced each year. In just the past ten years, plastic has become a bit of a political football, targeted by fringe activist organizations as a public enemy. Interestingly, and perhaps as an election-year gesture, the White House recently and somewhat quietly, announced its support for limiting the global production of this material—one that is essential to practically all American manufacturers. For over three years, leaders within this administration have rightly emphasized the importance of preserving and growing U.S. manufacturing jobs. However, support for manufacturing and the limitation of an essential material for the industry cannot go hand-in-hand. If the administration is successful in advocating for this new position as part of the global plastic pollution treaty discussions, it could send a detrimental shockwave through the manufacturing supply chain. While we strongly share the goal of eliminating plastic waste, limiting the production of a material that is an essential building block across manufacturing is not the solution. Beyond industry-wide damage, this policy poses the risk of moving manufacturing offshore. Publicly, Commerce Secretary Gina Raimondo has stressed the need to strengthen domestic supply chains — a challenge when the administration is simultaneously restricting access to crucial materials produced here in the U.S. Limiting domestic plastic production could result in job losses and force manufacturing to relocate to countries with less stringent regulations, including environmental standards. We expect that polyethylene production in Asia will continue to rise over the next five years, particularly in China. Do we want to give China, who will likely disregard production limits, a competitive edge while potentially undermining global environmental standards? The pandemic and the war in Ukraine have taught us that stable supply chains are crucial, and increasing reliance on foreign manufacturers would make the U.S. more vulnerable to disruptions. Vice President and Democratic presidential nominee Kamala Harris has announced a framework for her manufacturing agenda aimed at “making sure America, not China, wins the competition for the 21st century.” Her plan includes increasing investment in aerospace, biomanufacturing and other emerging technologies. Isn’t this position contradictory to supporting policies that limit the production of materials necessary for manufacturing in these industries? Manufacturing jobs currently make up over 8.5% of the U.S. workforce, driving the economy, with $1.4 trillion in manufactured goods exported in 2021, according to the National Association of Manufacturers. According to the Plastics Industry Association’s recently released Size and Impact Report, the plastics industry alone is the eighth-largest manufacturing sector in the U.S., supporting over one million jobs across a diverse range of skills. In fact, plastics manufacturing employment grew 1.1% per year from 2013 to 2023, outpacing total manufacturing. These are not just statistics; they represent stable employment that sustains families and communities nationwide. The new White House stance threatens the livelihoods of millions of Americans, undermining sectors that depend on plastic materials including automotive, consumer goods, construction and healthcare. Our country is a global leader in manufacturing quality, innovation and efficiency. Let’s not take away the materials that make this possible. Every day, engineers work to make products lighter, thinner, and more sustainable — all while improving performance. Restricting the availability of new plastics would stifle this growth, limiting the development of advanced materials and processes that benefit numerous other industries and support a circular economy. And then there is the environmental impact. Plastic is preferred by many industries for its unparalleled safety, protection and efficiency and potential for reuse and recycling, but also for the reduction in overall resource consumption. According to a 2024 report in Environmental Science & Technology, plastics have a lower total greenhouse gas contribution than alternatives. Capping production in favor of alternatives could ultimately increase harm to the environment. Manufacturing rarely occurs solely within the four walls of a factory. It happens as a collaboration between suppliers, designers, engineers, machinists, the customers and the list goes on. If you break that chain, the stability of manufacturing is put at risk. Restricting the supply of plastics to domestic manufacturing will threaten American jobs and diminish the nation’s global competitiveness — all without advancing our shared environmental goals. Actions must align with words. The plastics industry is committed to strengthening U.S. manufacturing — let’s create policies together to truly achieve these goals.
Boston Dynamics, Toyota Research Institute partner to advance robotics research
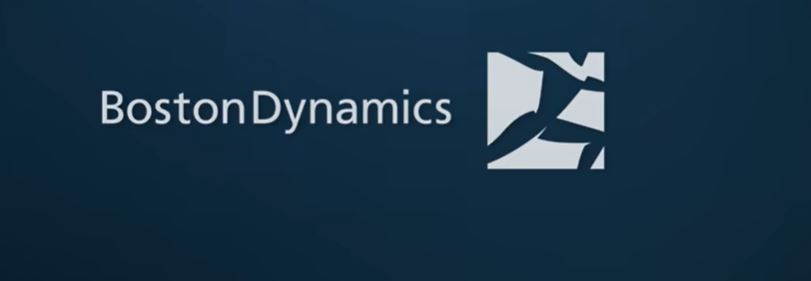
Boston Dynamics and Toyota Research Institute (TRI) announced that they will merge, combining two of the world’s leaders in artificial intelligence and robotics. The research partnership aims to accelerate the development of general-purpose humanoid robots by utilizing TRI’s large behavior models and Boston Dynamics’ Atlas robot. The partnership looks to push humanoid research further Boston Dynamics has a longstanding reputation for advances in humanoids, from extreme mobility to bimanual manipulation. The latest generation of Atlas results from years of hardware/software co-design aimed at building the most capable humanoid platform regarding physical capability and software interfaces for authoring whole-body behaviors. According to the companies, this combination makes it an ideal platform for advancing the science of AI-based manipulation skills. Boston Dynamics and Toyota Research Institute (TRI) announced they will merge, combining two world leaders in artificial intelligence and robotics. The research partnership aims to accelerate the development of general-purpose humanoid robots by utilizing TRI’s large behavior models and Boston Dynamics’ Atlas robot. “There has never been a more exciting time for the robotics industry, and we look forward to working with TRI to accelerate the development of general-purpose humanoids,” said Robert Playter, CEO of Boston Dynamics. “This partnership is an example of two companies with a strong research-and-development foundation coming together to work on many complex challenges and build useful robots that solve real-world problems.” Concurrently, TRI is widely recognized as a leader in rapidly advancing large behavior models (LBMs) for robotics. This includes work on diffusion policy, which, according to the company, pioneered the successful application of generative AI to advance dexterous manipulation capabilities in robotics. TRI has also played a leading role in developing open-source robot AI models and datasets. Leveraging additional strength in computer vision and large-language model training, TRI’s work on LBMs aims to achieve multi-task, vision-and-language-conditioned foundation models for dexterous manipulation. “Recent advances in AI and machine learning hold tremendous potential for advancing physical intelligence,” said Gill Pratt, chief scientist for Toyota and CEO of TRI. “The opportunity to implement TRI’s state-of-the-art AI technology on Boston Dynamics’ hardware is game-changing for each of our organizations as we work to amplify people and improve quality of life.” Scott Kuindersma, senior director of Robotics Research at Boston Dynamics, and Russ Tedrake, vice president of Robotics Research at Toyota Research Institute, will co-lead the Boston-based research partnership. The project is designed to leverage the strengths and expertise of each partner equally. The physical capabilities of the new electric Atlas robot, coupled with the ability to programmatically command and teleoperate a broad range of whole-body bimanual manipulation behaviors, will allow research teams to deploy the robot across a range of tasks and collect data on its performance. This data will, in turn, be used to support the training of advanced LBMs, utilizing rigorous hardware and simulation evaluation to demonstrate that large, pre-trained models can enable the rapid acquisition of new robust, dexterous, whole-body skills. The joint team will also research to answer fundamental training questions for humanoid robots, the ability of research models to leverage whole-body sensing, understanding of human-robot interaction, and safety/assurance cases to support these new capabilities.
Episode 530: Maximizing efficiency with Voice Technology in warehousing
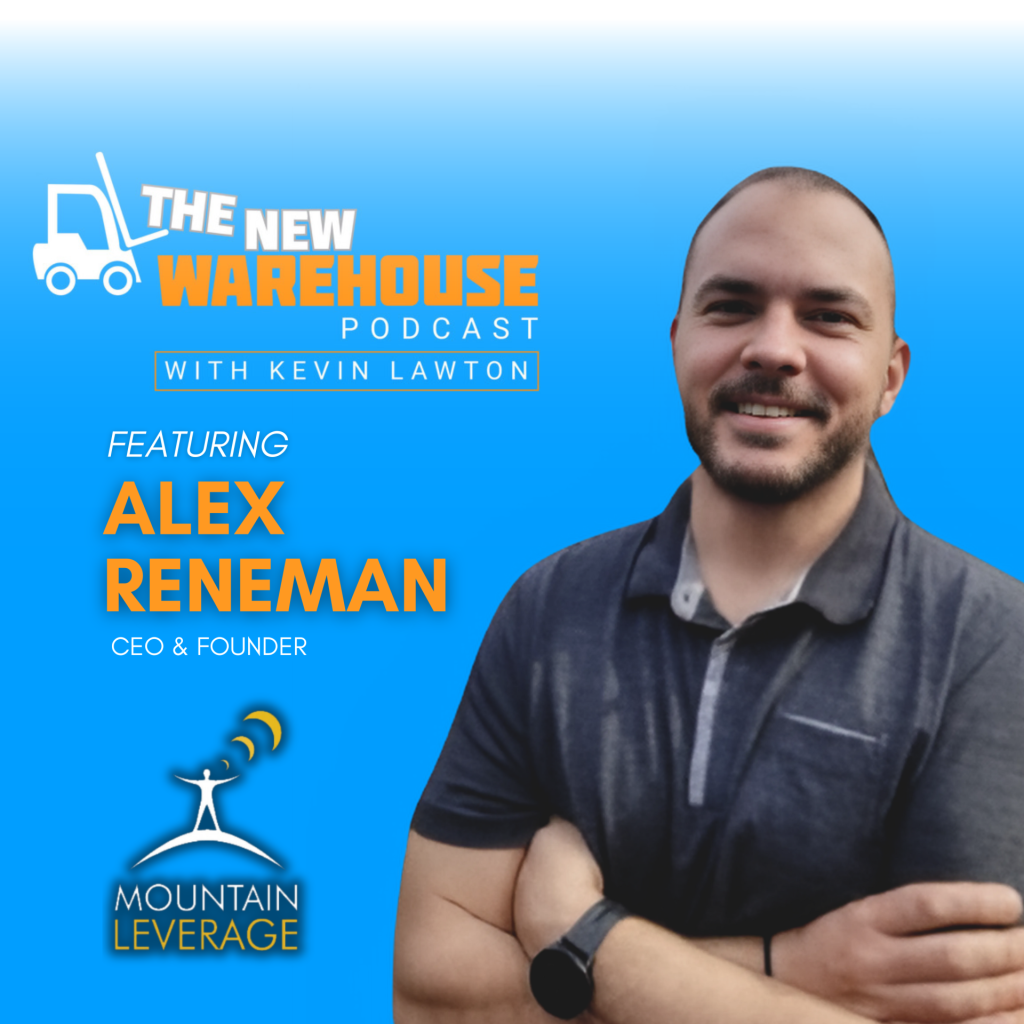
In this episode of The New Warehouse Podcast, our guest is Alex Reneman, a fellow podcaster, president, CEO, and founder of Mountain Leverage. Mountain Leverage, a leader in voice technology, is transforming how warehouses operate by integrating innovative voice-directed systems. Alex shares insights into the company’s journey, the impact of voice technology on warehouse operations, and its potential future. They dive into how voice interfaces improve efficiency, productivity, and worker satisfaction while addressing the role of company culture in the success of Mountain Leverage and its clients. Why Voice Technology in Warehousing is a Natural Fit Reneman emphasizes that voice technology is “a native interface” for workers, allowing for more fluid and efficient warehouse operations. In warehouse settings, tasks like picking, packing, and confirming orders become more streamlined with hands-free, voice-guided workflows. Reneman explains, “It’s a workflow solution on the edge that allows workers to be more efficient, more productive, and more accurate because their hands and eyes are free.” This technology keeps workers safe, reducing distractions and improving overall workflow accuracy. Implementing voice-directed systems is not just about efficiency but also worker satisfaction, making it a win-win for both employees and companies. Addressing Labor Challenges with Voice Solutions As labor challenges persist in the warehousing industry, voice technology has proven adaptable to many workers, including those for whom English is not the first language. Reneman highlights, “There are a lot of clever ways to implement that in some cases, where workers can hear instructions in English but respond in their own language.” This flexibility ensures that workers can adapt to voice-guided workflows quickly, reducing training time and increasing productivity. Additionally, the technology’s intuitive nature resonates with younger, tech-savvy generations entering the workforce, ensuring smooth transitions for all. Building a Strong Culture: The Heart of Mountain Leverage Reneman attributes the success of Mountain Leverage to the company’s strong internal culture, which he calls “the P.A.C.T.” This pact includes critical values such as Possibility, Accountability, Championship, and Trust. “It matters not just internally but to our customers,” Reneman explains. These values shape how Mountain Leverage works with its clients, ensuring that the focus is on optimizing performance and creating a positive and enjoyable partnership. By integrating this culture into every aspect of their work, the company builds long-lasting relationships and helps customers thrive in an ever-evolving industry. Key Takeaways on Voice Technology in Warehousing Voice technology boosts efficiency by allowing hands-free, eyes-free operations, increasing productivity and safety. The technology is adaptable to diverse workforces, bridging language barriers and engaging younger generations. A strong company culture built on trust and accountability enhances customer relationships and drives successful implementations. The New Warehouse Podcast Episode 530: Maximizing Efficiency with Voice Technology in Warehousing