Synergy Logistics listed in the Top 100 IT Providers by Inbound Logistics for the ninth consecutive year

The committee selected the Top 100 Logistics IT Providers based on those offering the innovations their customers need to streamline supply chain operations. Synergy’s Tier 1 warehouse management system (WMS), SnapFulfil, and multi-agent orchestration software, SnapControl, were considered essential solutions in an era of fast-paced warehouse automation and robotics functionality. The recognition for SnapFulfil and SnapControl has been well received by the innovative company as it underpins how its leading-edge warehouse technology continues to evolve and remain relevant to the Inbound Logistics audience of top manufacturers, distributors, and retailers. Synergy’s Chief Commercial Officer, Brian Kirst, said: “It’s no coincidence that Synergy has been recognized for nine consecutive years as a top 100 logistics IT provider. In a fast-paced world, we continue to invest in R&D and adapt our software to meet the ever-changing demands of our global customer base as well as introduce new products. “SnapControl is our latest solution, which is taking off as it tackles the need for seamless control of robotics and automation in the warehouse. It acts as a conductor of warehouse orchestration, otherwise known as multi-agent orchestration (MAO). Being vendor agnostic, it prioritizes work, allocates tasks and workflows, and ultimately enables companies to automate their operations on a much shorter timeline. But the real added value is the complete data picture it brings, which can facilitate tangible labor savings, accurate asset management decisions, and rapid time to value.”
PTDA Foundation welcoming nominations for 2024 Leadership Awards
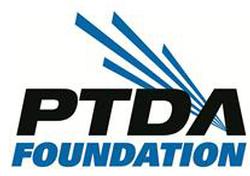
Wendy B. McDonald Woman of the Year Award and Robert K. Callahan Advancing Leaders Award nominations open through June 8 The PTDA Foundation is seeking nominations for its Wendy B. McDonald Woman of the Year Award and Robert K. Callahan Advancing Leaders Award. The Wendy B. McDonald Woman of the Year Award celebrates a woman who, regardless of her career stage, has made significant contributions to her company and the PT/MC industry in 2023. The award is presented annually, when merited. Nominations will be accepted through June 8, 2024. The Robert (Bob) K. Callahan Advancing Leaders Award acknowledges the dedication and ambition of young individuals committed to advancing within the PT/MC industry. Nominations are due by June 8, 2024. Both awards will be presented at the PTDA 2024 Industry Summit at The Broadmoor in Colorado Spring, Colo. in October.
Why a strong brand isn’t a luxury but a necessity
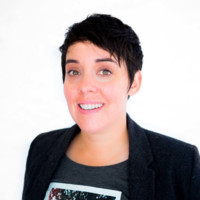
Who invented the light bulb? Of course, you’d say Thomas Edison. But what you may not realize is that Edison did not invent the light bulb. It was actually invented by Joseph Wilson Swan and Henry Woodward. What Edison did really well was commercialize the invention. But why do we always think of Thomas Edison first? Of course, he was a prolific inventor, but more importantly, he built a recognizable and resonating brand. Edison branded everything he did with his name, face, and signature. He built a massive publicity machine behind him. He forged close personal relationships with journalists who could be trusted to write adoring (but not always strictly accurate) copy. He was a relentless self-promoter. He used multiple public demonstrations to highlight and promote his technologies. Edison didn’t just do a lot of marketing but rather build a brand he could leverage. For example, his main laboratory, Menlo Park, was famous for generating more than 400 patents in just six years. But Edison worked with a team of 14 or so engineers, machinists, and physicists who were rarely if not at all mentioned, building and amplifying the narrative of Edison as a “sole inventor”. Only those inventors who left the lab and branched out on their own (i.e., Nikola Tesla) had a chance to gain broader recognition. Edison, while positioning himself this way, spent over half his time dealing with clients and investors, and speaking to the press. Edison also knew what stories and sound bites would resonate with the public. He’s well known for saying, “I have not failed 10,000 times—I’ve successfully found 10,000 ways that will not work.” But actually, he failed 2,774 times according to his records. We all know the 10,000 times quote, and there’s no question it wouldn’t be the same if he had said 2,774. The bottom line here is that while we want to believe that an amazing invention or innovative solution will sell itself, it’s far from the case. Building a brand and identity intentionally, and shaping a narrative provides you the best opportunity to succeed. This doesn’t mean simply promoting your product or your company but creating a brand around it that’s engaging, unique, interesting, and different. How crucial, after all, is the brand of Steve Jobs to the image of Apple? Or of Larry Page and Sergey Brin to our perception of Google? Even though many companies today are cutting back on branding and marketing investments, it’s funny how the companies we admire, were not built simply by new products but achieved their level of success through investing and architecting a great brand. Edison knew this – even 100 years ago. Andrea Belk Olson is a keynote speaker, author, differentiation strategist, behavioral scientist, and customer-centricity expert. As the CEO of Pragmadik, she helps organizations of all sizes, from small businesses to Fortune 500, and has served as an outside consultant for EY and McKinsey. Andrea is the author of three books, including her most recent, What To Ask: How To Learn What Customers Need but Don’t Tell You. She is a 4-time ADDY® award winner and host of the popular Customer Mission podcast. Her thoughts have been continually featured in news sources such as Chief Executive Magazine, Entrepreneur Magazine, Harvard Business Review, Rotman Magazine, World Economic Forum, and more. Andrea is a sought-after speaker at conferences and corporate events throughout the world. She is a visiting lecturer and startup coach at the University of Iowa, a TEDx presenter, and TEDx speaker coach. She is also an instructor at the University of Iowa Venture School. More information is also available on www.pragmadik.com and www.andreabelkolson.com.
Dorner to showcase innovative automation technologies at Automate 2024
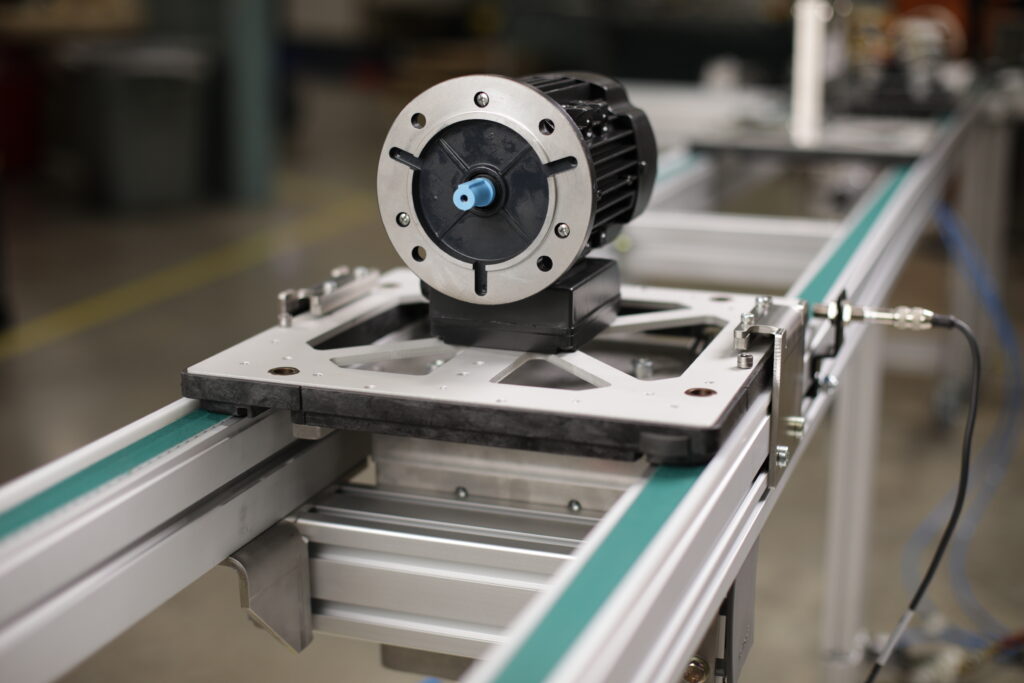
Dorner and its partner company montratec are set to unveil its latest innovations in assembly technology in booth 1224 at Automate 2024, May 6-9, at McCormick Place in Chicago. With a focus on enhancing efficiency and reliability in production environments, both Dorner and montratec will present a lineup of demo conveyors designed to meet the diverse needs of various industries. The newly released DualMove Pallet System will lead off Dorner’s collection. The DualMove features twin-strand timing belts that glide pallets precisely from one stop to the next. It also features three accessory modules: lift and transfer, lift and rotate, and lift and locate. DualMove’s reliability, flexibility, and easy integration make it a great fit for numerous assembly applications. Among the featured conveyors is the ERT150, an industry-ready solution engineered to convey medical and cleanroom-based product assembly. Boasting a versatile, low back-pressure platform, the ERT150 offers seamless and adaptable performance for various appliance, electronics, automotive, and consumer goods assembly applications. Its simple and effective design, including non-contact zoning and slip roller accumulation capability, ensures safe and efficient operation while minimizing downtime. With ISO Class 4 verification for cleanroom applications, the ERT150 sets a new standard for precision and reliability. Also on display will be Dorner’s FlexMove Pallet System, a versatile conveyor engineered for product routing, control, and inspection in small- to medium-size assembly automation applications. The FlexMove line is sold as completed assemblies or as kits. It offers users layout flexibility and the ability to implement easy conveyor system design changes to adapt to their business’s evolving needs. Modules include merge and divert modules, lift and locate stations, cushioned pallet stops, and a unique pin tracking system to guide pallets through 90° turns – all of which attach directly to the conveyor frame without modifications. Columbus McKinnon’s newest acquisition, montratec, will feature their montrac mono-rail solution at our booth. montratec’s intralogistics solutions for manufacturing, assembly, and production processes minimize cycle times and maximize customer operational throughput. Asynchronous movement enables products to be moved independently in multiple directions at varying speeds to balance production lines, increasing flexibility and productivity. montratec also brings a higher level of cleanroom certification that expands market access in the EV, life sciences, electronics, and semiconductor industries. Lastly, Dorner will feature its renowned 2200 industrial series conveyor solution. The 2200 series loop showcases the uniquely low-profile industrial line of conveyors and their ability to seamlessly transfer products from one conveyor to the next.
Haver & Boecker Niagara offers Rhino Hyde Liners
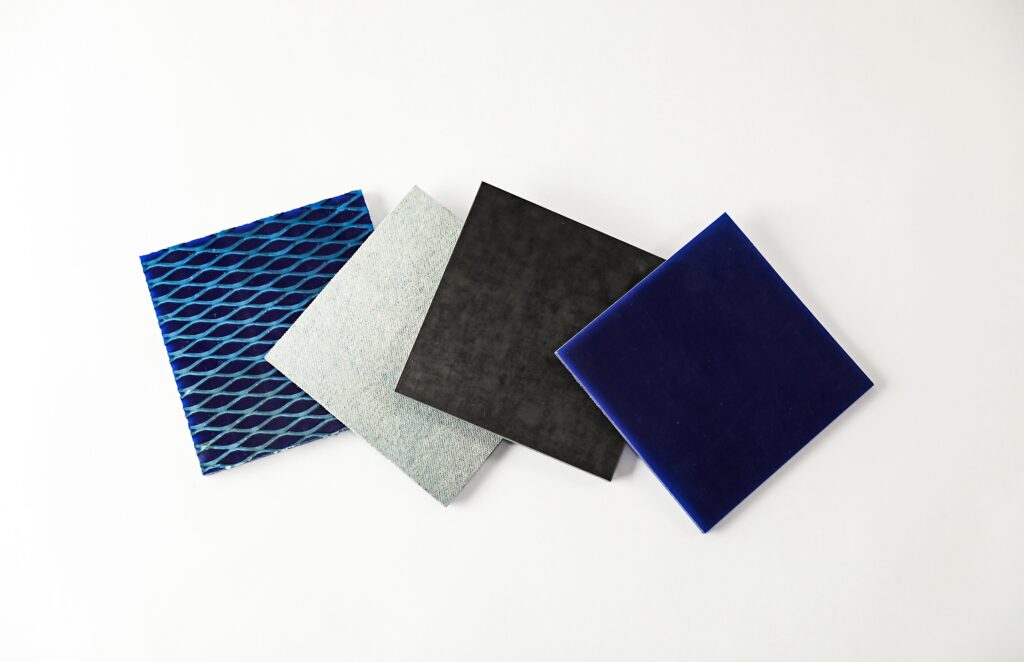
Haver & Boecker Niagara presented Rhino Hyde liners to enhance the wear life of a full range of equipment. The company’s custom-blend liners are strategically formulated and installed on key wear, material handling and impact areas of chutes, hoppers, vibrating screens and more. Rhino Hyde, constructed from thermoset polyurethane, boasts superior abrasion resistance, durability and chemical resistance compared to alternatives like thermoplastic polyurethane, rubber, or metal. “Haver & Boecker Niagara consistently seeks innovative solutions that elevate our customers’ operations,” said Karen Thompson, president of Haver & Boecker Niagara’s North American and Australian operations. “Offering Rhino Hyde liners underscores our commitment to delivering products and services that go well beyond the ordinary or expected. They aren’t just off-the-shelf products; they’re meticulously tailored solutions developed through collaboration with our partners and customers. It’s this dedication to personalized excellence that sets us apart.” Rhino Hyde liners are formulated and proven to outperform rubber, plastics, and even metals in rough weather. Producers can enjoy more durability with reduced wear in high-abrasion or high-impact areas. Additionally, Rhino Hyde liners offer a simple fix to seal worn spots. Polyurethane liners are a cost-effective solution and have the unique characteristic of being higher wear but are also a lighter-weight product with reduced maintenance and replacement costs. Rhino Hyde liners are designed for applications such as screening, material handling and hauling. They can be fully customized to the required size and are available in multiple different styles and attachment systems including the classic Rhino Hyde Blue, magnetic, urethane-backed ceramic, polyurethane blades, belt skirting and weldable liners. The original Rhino Hyde Blue liners boast high abrasion and impact resistance, along with reduced noise and vibration. Additionally, they won’t expand or contract in environments with fluctuating temperatures. Rhino Hyde Blue liners can be custom-made with several different backings, including solid steel, plain, expanded metal, fabric, and ceramic chip embedded. Magnetic Liners Magnetic liners are strong, durable liners featuring rare-earth magnets that easily fasten to steel without welding or bolting. Users can simply place the liner and remove as needed, saving both time and labor. They reduce material sticking, lessen noise and provide superior protection in even the most demanding applications. Magnets stay secure regardless of climate and withstand high levels of vibration and impact. Urethane-Backed Ceramic Liners Urethane-backed ceramic liners are the ultimate solution in applications where severe abrasion is an issue. The highly abrasion-resistant panels have replaced plain or weldable ceramic tile for decades in aggregate, coal, fly ash, glass, grain, gravel, cement and other industries. Urethane- backed panels require no fabrication, cutting or machining to install, and their durability and ease of installation reduces downtime, labor costs and waste. They combine the cut and abrasion resistance of ceramic, and the impact resistance and resiliency of Rhino Hyde polyurethane. Polyurethane Blade System Made with genuine Rhino Hyde polyurethane, Blade Systems provide thorough and even belt cleaning in both wet and dry conditions with exceptional resistance to cuts and tears. Rhino Hyde developed the Rhino Blade Tensioning System for excellent, cost-effective belt cleaning. The system has fewer moving parts than others in the industry, increasing reliability and offering a virtually maintenance-free experience. Furthermore, Rhino Hyde Blade Systems are compact in nature with minimal required space for installation. Complete Blade Systems can be installed in less than 30 minutes, and the Rhino Blade can be replaced in under 10 minutes by workers of all experience levels. Weldable liners Standard Rhino Hyde weld-in liners are easily installed with tack welding and have weld plates every 15-20 centimeters (about 6-8 inches) to ensure stability and rigidity. Rhino Armor weldable liners feature backing made entirely of perforated steel plate. These liners excel in heavy-duty applications, particularly those with heavy load drops.
H2C’s warehouse-in-the-sky is the first to pinpoint drone delivery
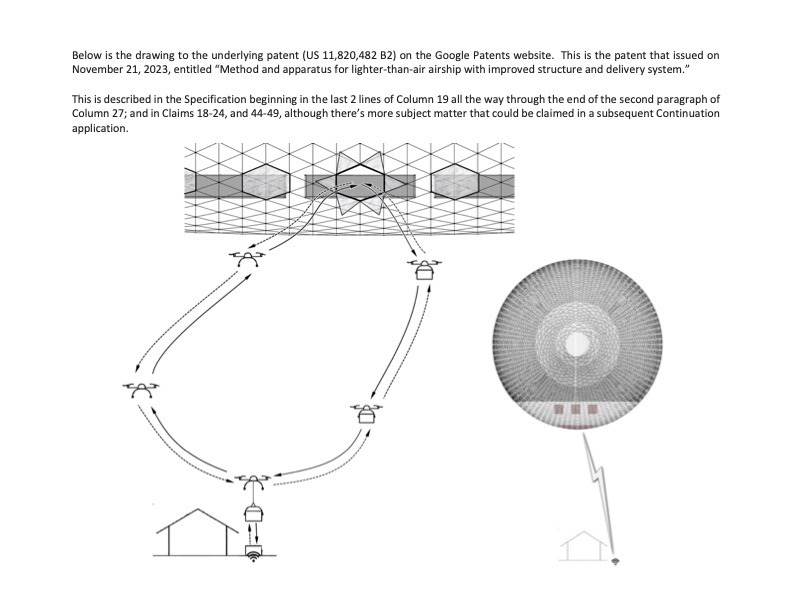
H2 Clipper, Inc. (“H2C”), an aerospace and alternative energy company developing uniquely capable hydrogen-powered dirigibles, has announced that it was granted a new U.S. patent for its warehouse-in-the-sky that includes the integration of aerial drones for picking up, transporting, and delivering packaged goods and other payloads. The technology incorporates: the use of a beacon, which can be a dedicated device or one’s cell phone, that enables package delivery by drone for companies like Amazon/FedEx/UPS/DHL etc., particularly in remote locations. Uniquely, the beacon also permits package returns from rural areas and remote global villages to put those items into international commerce; the ability to launch drones from a dirigible, allowing the drones to use all on-board energy to lift heavier packages rather than using that same energy to fly to the drop-off or pickup zone, resulting in efficient use of every route; charging bays for the aerial drones to recharge between short flights, which further reduces package delivery and retrieval time and trips; an on-board camera with each drone which provides proof of delivery, and is particularly important when using drone delivery in rural areas. With this patented technology, H2C’s warehouse-in-the-sky is the only airship technology that allows for pinpoint pick-up and delivery accuracy for commercial, consumer, and humanitarian use. “With the continued increase in online purchasing, the speed, convenience, and cost of local delivery are essential considerations for the supply chain,” said H2C Founder and CEO Rinaldo S. Brutoco. “By utilizing airships for delivery, shipments can bypass the exceedingly crowded and inefficient port facilities and airports, and eliminate the need for multiple intermodal transfers, handling steps, and ground-based facilities—minimizing delays and reducing costs.” US Patent 11,820,482 B2, entitled “Method and Apparatus for Lighter-Than-Air Airship with Improved Structure and Delivery System,” was issued by the United States Patent and Trademark Office (USPTO) and focuses on enhancements over previous airship designs and operating modes. Methods such as those described in H2C’s latest patent are focused on improving the “last mile” of delivery. The enhanced aerodynamic characteristics of the improved airship will enable it to travel at significant speeds, making door-to-door overnight delivery from a few regional warehouses and second-day door-to-door delivery of goods a possibility across the world. This ability to rapidly serve end-users directly from the factory or a few large regional distribution centers will resolve the last-mile challenges and provide a strong competitive advantage. The improvements represent a continuation of the work that H2C began in 2008 when it filed for its initial patent, which was issued in 2012. This news follows H2C’s January 2024 announcement that it was awarded a foundational robotics patent for using advanced “swarm robotics,” which achieves radical reductions of cost and quantum advances in manufacturing techniques for a wide variety of applications—including large scale lighter than air airships. H2C is represented in intellectual property matters by John C. Serio, a Partner in the Boston Intellectual Property and Technology Group at Withers Worldwide.
GRI expands product portfolio with 23 new SKUs in agriculture and construction tires
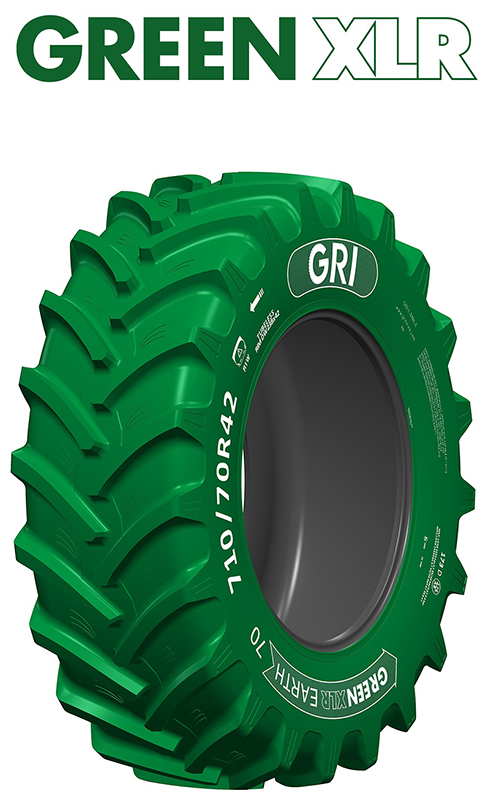
GRI has announced an expansion of its product portfolio with the addition of 23 new SKUs across its agriculture and construction tire segments. This strategic move underscores GRI’s commitment to meeting the evolving needs of its customers worldwide, as well as its dedication to innovation and excellence in tire manufacturing. The newly introduced SKUs encompass better load and speed indexes in the existing sizes to carry more weight with safety. These SKUs offer better options to the customers to choose the best fit for their machines. The expanded product portfolio includes tires designed for agricultural machinery such as tractors, implements, and sprayers, as well as tires tailored for construction equipment such as telehandlers, graders, and light trucks. Each SKU has been meticulously developed and tested to ensure optimal performance, durability, and reliability in demanding operating conditions. “We are excited to introduce these new additions to our product lineup, which reflect our ongoing efforts to provide comprehensive solutions to our customers,” said Dr. Mahesha Ranasoma, CEO of GRI. “With these new SKUs, we aim to further enhance our offerings and address the diverse needs of our global clientele.” The introduction of these 23 new SKUs further solidifies GRI’s position as a leader in the global specialty tire industry. With a focus on customer satisfaction, technological advancement, and sustainability, GRI continues to drive progress and deliver value to its customers worldwide.
Advanced Illumination introduces Light Hub for Zebra Smart Cameras
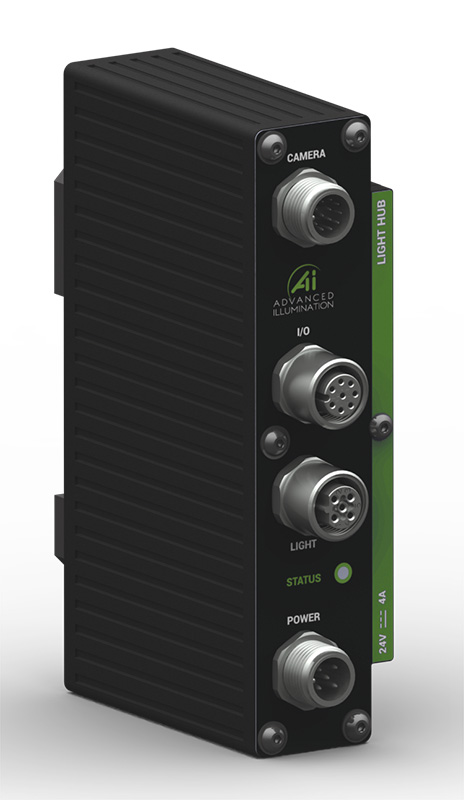
Advanced Illumination, the originator of LED lighting for machine vision, has announced the release of a new class of LED lighting controllers, aimed at revolutionizing machine vision system building through the simplification of camera, light, and I/O accessory interconnectivity. This machine vision solution cuts down on cost and setup time by operating as the connection “hub” between essential machine vision components. Starting with a variant that connects to Zebra’s popular line of Iris GTX Smart Cameras (previously part of Matrox Imaging), Advanced Illumination has developed the Light Hub for Zebra Iris GTX Smart Cameras. Also known as the HCS-150-ZEB (ZEB for Zebra), this Light Hub is capable of directly powering its connected Zebra camera while providing essential I/O functionality like triggering and analog dimming control between the connected light head, the Zebra camera, and any connected I/O accessories. Because this SignaTechTM-enabled controller can supply 4 amps of continuous output and up to 10 amps of overdrive strobe, users don’t need to compromise their machine vision lighting. With the HCS-150-ZEB, users can choose from hundreds of thousands of Advanced Illumination lighting configurations for unparalleled flexibility. The Light Hub is compatible with any new or existing C1 connection configured light heads. Whether users are looking to connect to a small, collimated backlight, or overdrive strobe a large, high-intensity bar light from their Zebra smart camera, the HCS-150-ZEB does so seamlessly. The HCS-150-ZEB is built for the rigors of industrial environments. Its IP67-rated enclosure ensures protection from dust and water ingress. The controller offers multiple mounting options, including a DIN rail clip for easy integration into controller cabinets, and M4 mounting channels for secure, custom positioning.
Saino doors marks 125 Years in the industrial door market
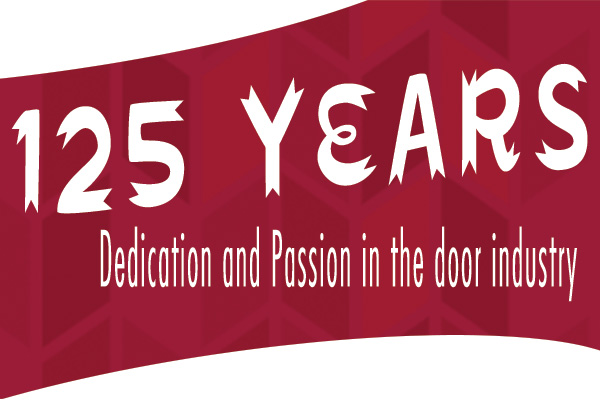
Saino Doors, a member of the Senneca family of brands, has announced to commemorate 125 years of unwavering dedication and passion in the industrial door industry. Since 1899, Saino has been at the forefront, setting the standard for unparalleled quality and reliability with its sliding fire and service door systems across various industries. As part of the Chase Doors brand, Saino offers a comprehensive line of door systems designed for a wide range of applications, including warehouses, distribution centers, industrial environments, processing plants, manufacturing facilities, parking garages, convention facilities, and pharmaceutical facilities. As Saino marks this significant milestone, they extend heartfelt gratitude for the unwavering support and trust in Saino door systems. The company’s dedication to providing innovative solutions tailored to meet their customer’s specific needs and surpass expectations remains unwavering. “Saino: Opening Doors to Possibilities for 125 Years and Counting. With a legacy built on great people, loyal customers, and exceptional products, we continue to thrive and grow,” Rick Paterni, Vice President of product and Marketing shared. “We expect the trend of satisfied customers to continue for decades to come, as we remain committed to excellence in every aspect of our business.” With a steadfast commitment to exceptional customer service and advanced manufacturing capabilities, Saino has earned a well-deserved reputation for delivering high-quality products. The company appreciates the partnerships formed over the years and eagerly anticipates another 125 years of success together.
Synergy North America Inc. has partnered with supply chain BEST to expand their WMS implementation
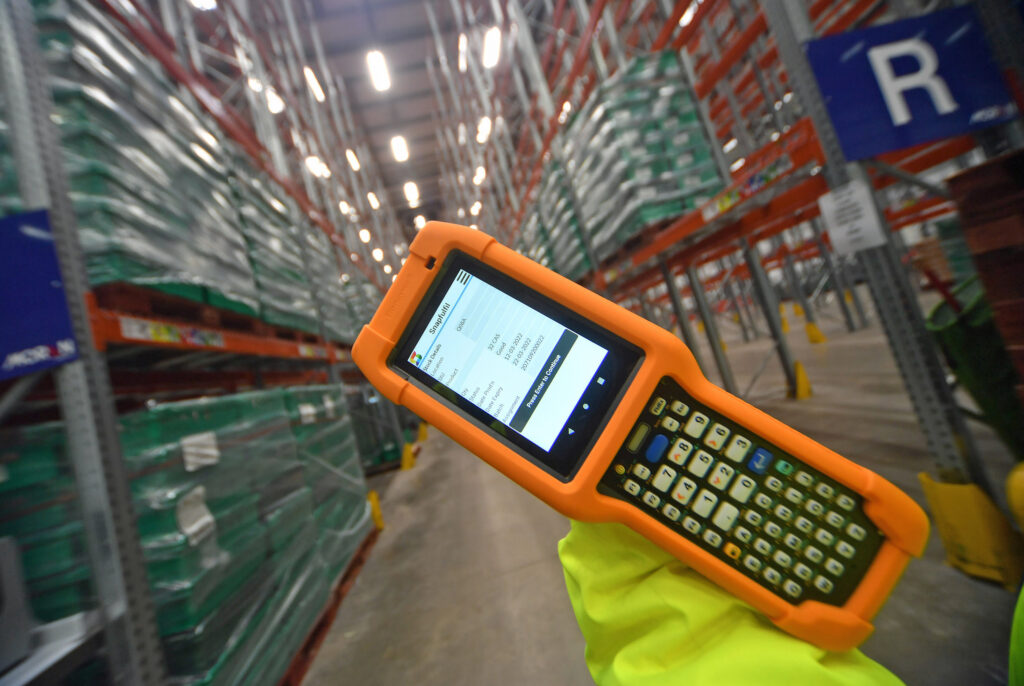
Working together as preferred channel partners, rapidly expanding Synergy will leverage access to Florida-based Supply Chain BEST’s end-to-end system implementation and project management expertise. This partnership is the latest in a fast-growing ecosystem of partners, vendors, and integrations for SnapFulfil, and builds upon Supply Chain BEST resources in the US, Canada, UK, and Hong Kong. Supply Chain BEST President, Joe Huss, said: “I am delighted to be partnering with Synergy and am excited by the prospect of working together as we share a mission to deliver the very best in customer supply chain solutions. Having worked with various WMS solutions over the years, SnapFulfil stands out in terms of its technologically advanced rules engine, flexibility, and configurability. The build process is configured as part of the solution, so there is minimal additional development and coding for each deployment, which historically adds to complexity and cost. “SnapFulfil is so customizable we can also instruct our customers to self-configure the WMS and help them understand how the system can get them to the next operational level, which is a real point of difference for those needing to flex and adapt to ever-changing market demands.” At 40+ companies strong, Synergy’s partnership network covers a broad spectrum of integration categories, such as ERP, iPaaS, Marketplace, Robotics, Shipping, and other channel partners. Synergy Logistics Chief Commercial Officer, Brian Kirst, added: “It’s a mutually beneficial partnership, with the Supply Chain BEST team a great fit to match our domain expertise. They share the same comprehensive yet flexible approach to implementation, as well as an ethos that integrated software solutions should be about rapid time-to-value and strong return on investment. As business opportunities increase for both companies, we can scale and grow together and secure and develop more of the right kind of business.”
Hamilton expands Nylast® wheel line to accommodate heavy-duty industries
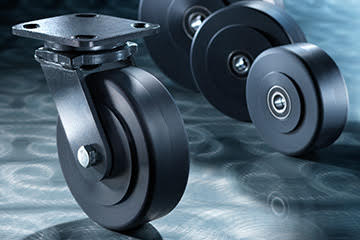
Hamilton Caster, manufacturer of heavy-duty industrial casters, wheels, carts, and trailers, has announced the expansion of its Nylast® wheel line to include sizes up to 24 inches in diameter, tripling its current load capacity of the series. This expansion not only broadens the scope of its offerings but also allows for the enhancement of several caster series for heavy manufacturing industries. Hamilton Nylast® wheels, crafted from solid-cast high-performance nylon, have long been synonymous with durability and resilience. Unlike conventional injection-molded nylon wheels, Nylast® boasts superior impact strength, making it the top choice for industries requiring robust performance under demanding conditions. Hamilton’s Nylast® material is meticulously formulated with finely divided particles of molybdenum disulfide (MoS2), enhancing load-bearing capability while preserving the impact resistance inherent to nylon. Every aspect of Nylast® wheels, from the face to the bore, undergoes CNC machining to strict tolerances, ensuring consistency and quality in every product. With the introduction of larger Nylast® wheel diameters, Hamilton is even more poised to cater to the evolving needs of heavy manufacturing industries such as aerospace and defense, ship and bridge building, and construction. The larger Nylast® wheel sizes enable Hamilton’s Super Duty and Extreme Duty Caster series to handle heavier loads, provide enhanced versatility, and perform in demanding industrial environments. “This expansion allows us to provide our customers with more solutions to tackle even the most demanding tasks with confidence,” said Jodi Fritsch, director of marketing. “We are committed to continuously innovating and improving our product offerings to meet the evolving needs of our customers.” Nylast® wheels are more desirable in specific applications over forged steel and polyurethane due to their ability to withstand a higher load capacity without damaging floors. Because Nylast® wheels are much lighter in weight than forged steel or polyurethane, the overall PSI on the contact area of the floor is significantly less. Nylast® also has a higher degree of chemical and moisture resistance. Chemical resistance of wheel materials depends upon many variables including the manner and length of exposure, temperature, and chemical concentration. Check out the Nylast® Chemical Resistance Chart to learn the chemicals that play nice with Nylast®. Nylast® wheels have very low rolling resistance while moving heavy loads. This feature enhances energy efficiency and minimizes friction, which in turn can extend equipment lifespan and improve overall performance. Low rolling resistance not only saves energy and ensures smoother workflows, but it can also contribute to a more sustainable and cost-effective operation. Last year, Hamilton introduced its new U-Grooved Industrial Track Wheels, offering Nylast® as a wheel option due to its ability to withstand chemicals and moisture. Nylast® U-Grooved Wheels provide a great alternative for customers in industrial environments where crane cables, pulleys, rolling gates, and doors are prevalent, and sanitary and wash-down conditions are imperative.
March 2024 Logistics Manager’s Index Report® LMI® at 58.3
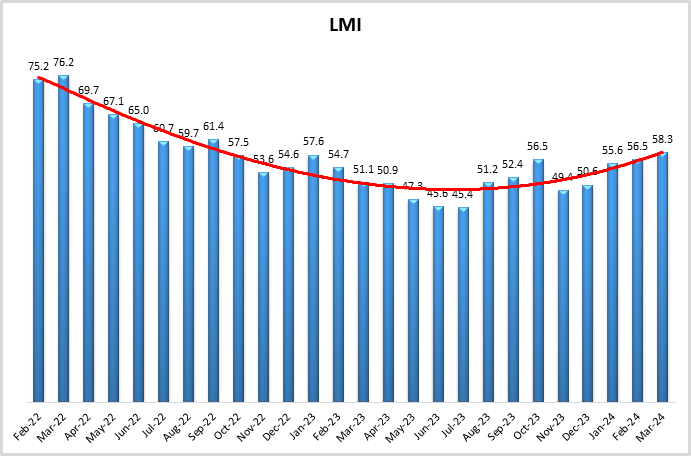
Growth is INCREASING AT AN INCREASING RATE for inventory levels, inventory costs, warehousing prices, and transportation utilization. Growth is INCREASING AT A DECREASING RATE for warehousing utilization, transportation capacity, and transportation prices. Warehousing capacity is CONTRACTING The Logistics Manager’s Index reads in at 58.3 in March 2024. This is up (+1.8) from February’s reading of 56.5. This is the fastest rate of expansion in the overall index since the reading of 61.2 from 18 months ago in September of 2022. The logistics industry is at a healthier place than it was then however. That reading from 18 months ago was largely inflated by unwanted inventories and high Warehousing Costs along with an anemic freight market. March of 2024 is a different story as we are seeing long-planned inventory expansions, along with more efficient levels of utilization in both warehousing and transportation as the drivers of growth. The level of 58.3 is within half a standard deviation from the all-time average of 62.2, suggesting that the overall logistics industry is now at the low end of what we would consider healthy and normal growth. Other signs of this health are that the growth has been consistent for Upstream (57.9) and Downstream (60.8), and also smaller (59.1) and larger (58.1) firms. The change this month was primarily driven by a continued rebuilding of Inventory Levels (+5.3) which at 63.8 are at their highest level since October 2022. This growth has had cascading effects on tightening Warehousing Capacity (-8.2) which is back into contraction territory for the first time since January 2023. These changes suggest that firms are building up inventories in anticipation of continued consumer spending and suggests that the economy will continue to grow in the near-term. Transportation Capacity is down (-1.3), but at 59.6 is still higher than Transportation Prices (53.0), meaning that we are not yet ready to call an end to the freight recession. Although it is much less severe than it was six months or a year ago. Researchers at Arizona State University, Colorado State University, Florida Atlantic University, Rutgers University, and the University of Nevada, Reno, and in conjunction with the Council of Supply Chain Management Professionals (CSCMP) issued this report today. Results Overview The LMI score is a combination of eight unique components that make up the logistics industry, including: inventory levels and costs, warehousing capacity, utilization, and prices, and transportation capacity, utilization, and prices. The LMI is calculated using a diffusion index, in which any reading above 50.0 indicates that logistics is expanding; a reading below 50.0 is indicative of a shrinking logistics industry. The latest results of the LMI summarize the responses of supply chain professionals collected in March 2024. The LMI read in at 58.3 in March, up (+1.8) February’s reading of 56.5. This is the seventh time in the last eight months that the LMI has shown expansion. This growth is driven by the buildup of inventories, the subsequent tightening of warehousing, and the ongoing slow yet steady recovery in transportation. The overall index is now at the low end of healthy levels of growth, closing in on the all-time average of 62.2 and is pointing towards steady economic growth in the near term. The broader optimism of our respondents is reflected in the University of Michigan’s Index of Consumer Sentiment which is up (+3.3%) to 79.4 in March and is 28.1% higher than a year ago. Consumers are confident about both the current state of the economy, and that inflation will continue to slow down[1]. Wall Street seems to be confident as well as the S&P 500 ended the first quarter up 10%. With growth coming from all 11 sectors of the index, this is the best opening to a year for the index since 2019. Historically, first quarters this strong have portended strong growth through the rest of the year[2]. It will be interesting to see if this momentum holds through the rest of 2024. Underlying this is continued job growth and slowing inflation. The U.S. added 275,000 jobs in February on the back of 229,000 jobs added in January. On the flip side, with more people entering the labor force the unemployment rate is up to 3.9%, which is higher bust still historically low as the U.S. has now seen unemployment under 4% for 25 consecutive months[3]. Evidence that the uptick in the unemployment rate is due more to a growing labor force than to job losses can be seen in jobless claims dipping down to only 210,000 new claims in the last week of March[4]. This is a continuation of the end of 2024 as U.S. economic growth in Q4 2023 was revised up from 3.2 to 2.4%. The Atlanta Federal Reserve estimates that it is growing at a rate of 2.1% in Q1 2024, but at this point that is still a speculative number[5]. As for inflation, many analysts are predicting that interest rates will need to come down by June or July for the Fed to meet its forecast of three rate cuts in 2024. Citi expects hiring to slow in Q2, which would leave an opening for the Fed to begin cooling rates [6]. As is often the case, inventories are the straw that stirs the drink in the logistics industry. Inventory Levels were up (+5.3) to 63.8 in March, which is their highest level since October of 2022 when firms were desperate to slash inventories. Since this time, Inventory Levels have largely registered in the 50’s and 40’s, including contracting in seven of eight months from May to December of 2023. They have been increasing steadily since then and moving back into the mid-60’s in March suggests that many firms are now back to business as normal. This normalcy has returned in part due to continued consumer activity. Consumer spending was up 0.6% in February as U.S. consumers continue to spend past analyst expectations of post-covid “revenge spending”. While a significant chunk of this spending is on services such as flights and meals,
Versatile and easy to use in-house sign and label print system

DuraLabel has announced the immediate availability of its new Kodiak Max, industrial sign and label print systems. Kodiak Max allows companies to bring multi-color, industrial-strength sign and label production in-house. Users can instantly create messaging to their exact specifications; alter or append messages at a moment’s notice; create permanent safety signs or temporary/seasonal signage; and save time and money versus outsourcing. All Kodiak Max Print Systems come with LabelForge PRO design software pre-installed. This easy-to-use tool has thousands of pre-made sign templates and symbols that can be printed as-is or customized as needed. Users can even design their own signs from scratch. LabelForge PRO supports 14 languages and multiple keyboard layouts. The uses for Kodiak Max are limitless. Typical uses include Arc Flash/Electrical Warnings, OSHA Notices, Chemical Labels, Equipment Labels, Pipe Marking, NFPA Labels, Wayfinding, Rack/Bay Identification and more. Regulatory compliance labels are also preloaded and automatically updated if regulations change. A stand-alone system, the Kodiak Max is ready to use out of the box. It features Wi-Fi connectivity, a responsive touchscreen display, and a wireless keyboard. Setup is fast and easy. An intuitive user interface guides users through the sign/label printing process. The Kodiak Max Print System uses thermal transfer technology to ensure durability, vibrant colors, and sharp, 300 DPI text, graphics, barcodes, and QR codes. Signs and labels can be printed in two colors in sizes up to 10” wide x 100” long. Quick-load ribbon cartridges make color changes fast and easy. Seven ribbon colors and 17 vinyl tape colors allow for a wide range of color schemes. Exactly what companies need for ANSI/OSHA compliance. DuraLabel Premium Vinyl is water, petroleum, UV light, and chemical resistant. It has ultra-aggressive adhesive and provides exceptional performance in outdoor environments and even in extreme conditions like cold storage warehouses and non-climate-controlled facilities. To ensure performance, reliability, and durability Kodiak Max Print Systems are designed, built, and tested in the United States. They carry a five-year warranty on the printer and premium vinyl supplies. DuraLabel also provides lifetime customer support, service, setup, and design guidance.
Nucor introduces new hot-rolled coil spot pricing
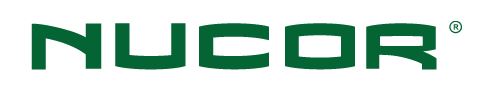
Nucor Corporation announced today that it is introducing a weekly Nucor Consumer Spot Price (CSP) to provide its customers with consistent and transparent communications regarding the Company’s hot-rolled coil spot pricing. Nucor will issue the first CSP on Monday, April 8, 2024. “We are constantly looking for better ways to serve our customers, not only with quality products and services, but also with timely information that will help them make informed decisions for their businesses. The CSP will give our customers relevant and current information about Nucor’s sheet business in a rapidly changing marketplace, which we believe will reduce their reliance on speculation and reduce risk,” said Rex Query, Executive Vice President of Sheet Products for Nucor Corporation. The CSP will be released every Monday, communicating Nucor’s hot-rolled spot price for the week to Nucor customers. It will remain in effect until the next weekly publication. Nucor CSP pricing will be derived from both quantitative and qualitative data. Lead times for all spot orders will be offered between three and five weeks to assist customers with their planning. “Over the last six decades, Nucor has continued to differentiate itself by innovating and finding new ways to provide solutions to our valued customers,” said Query. “The CSP is yet another tool that will help our customers succeed over the long term and strengthen our status as one of America’s most diversified and efficient industrial manufacturers.”
Cyclonaire welcomes John Elliot as Business Development Manager – Cement Sector
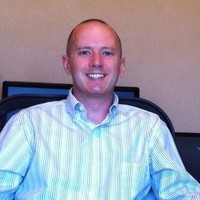
Cyclonaire Corporation has announced the appointment of John Elliot as Business Development Manager – Cementitious Materials. Elliot assumes this critical role as Zach Turner, the current Business Development Manager – Cementitious Materials, will be departing. Zach Turner has graciously agreed to stay on through May 17th, working closely with John to allow for the successful transition of all key accounts and opportunities. Elliot brings significant expertise in business development, client relationship management, and market analysis. He has a proven track record of driving growth and delivering value to clients through innovative solutions and strategic initiatives. “We are excited to welcome John Elliot to the Cyclonaire team as our new Business Development Manager – Cement,” said Mike Colella, Vice President Sales and Marketing at Cyclonaire Corporation. “His extensive experience and deep understanding of Bulk Material Handling will be instrumental in expanding our market presence and strengthening relationships with our valued clients.” In his role, Mr. Elliot will be responsible for identifying new business opportunities, fostering strategic partnerships, and managing growth in the Cement Sector. His leadership and industry knowledge will play a vital role in driving Cyclonaire’s position as a trusted partner in the cement sector. “I am thrilled to join Cyclonaire and contribute to the company’s continued success in the cement industry,” said John Elliot. “I look forward to working closely with the talented team at Cyclonaire to capitalize on new opportunities, exceed customer expectations, and continue to drive sustainable growth.” “We extend our gratitude to Zach Turner for his dedication and contributions to Cyclonaire and wish him all the best in his future endeavors,” added Mike Colella.
Fleet team expands with strategic acquisition of Forklift Training Systems
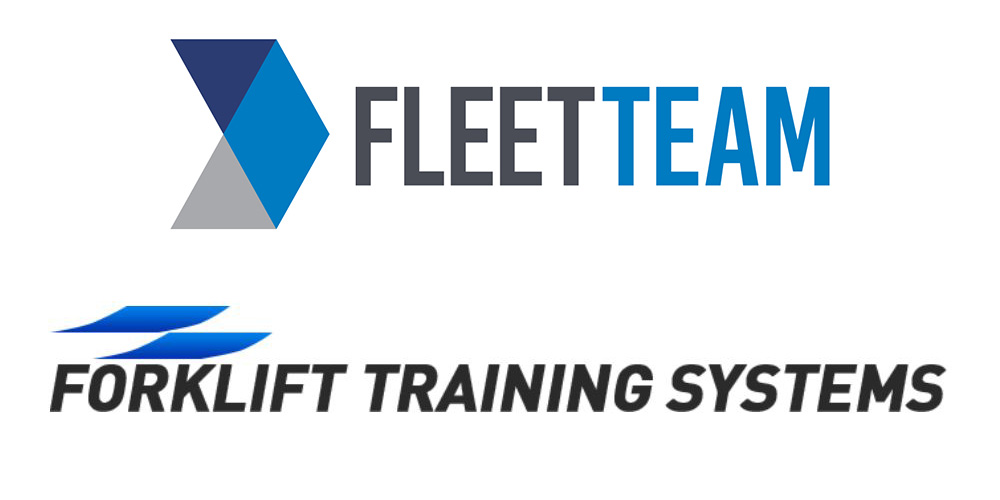
Fleet Team, fleet management and consulting company, has announced its acquisition of Forklift Training Systems, headquartered in Newark, Ohio. This transaction further diversifies Fleet Team to include operator/trainer training programs and cutting-edge safety products that complement the company’s existing client solutions portfolio. The acquisition, which closed on March 28, 2024, aims to leverage the strengths of both companies while maintaining the individual identities that have contributed to their respective successes. The decision to acquire Forklift Training Systems was driven by its exceptional reputation in the training and safety services space with Fortune 500 companies. The addition of Forklift Training Systems will allow Fleet Team to take a more holistic approach to fleet management and reinforce its commitment to meeting the evolving needs of its client base. Doug Riddle, President of Fleet Team, said, “With safety being top-of-mind for us and our clients, acquiring Forklift Training Systems is the beginning of a symbiotic partnership. We are ecstatic to bring the Forklift Training Systems team on board and look forward to the opportunities this change will bring.” David Hoover, President of Forklift Training Systems, will play a key role in providing safety and training leadership for both companies. “I am thrilled to build on the legacy I’ve established for Forklift Training Systems by gaining access to additional resources and collaboration from Fleet Team. With this change, our clients can still expect to receive the same exceptional service they know and trust, but now with access to additional resources.”
Iowa Hawkeyes Basketball heading to Cleveland Bobblehead unveiled for the Final Four
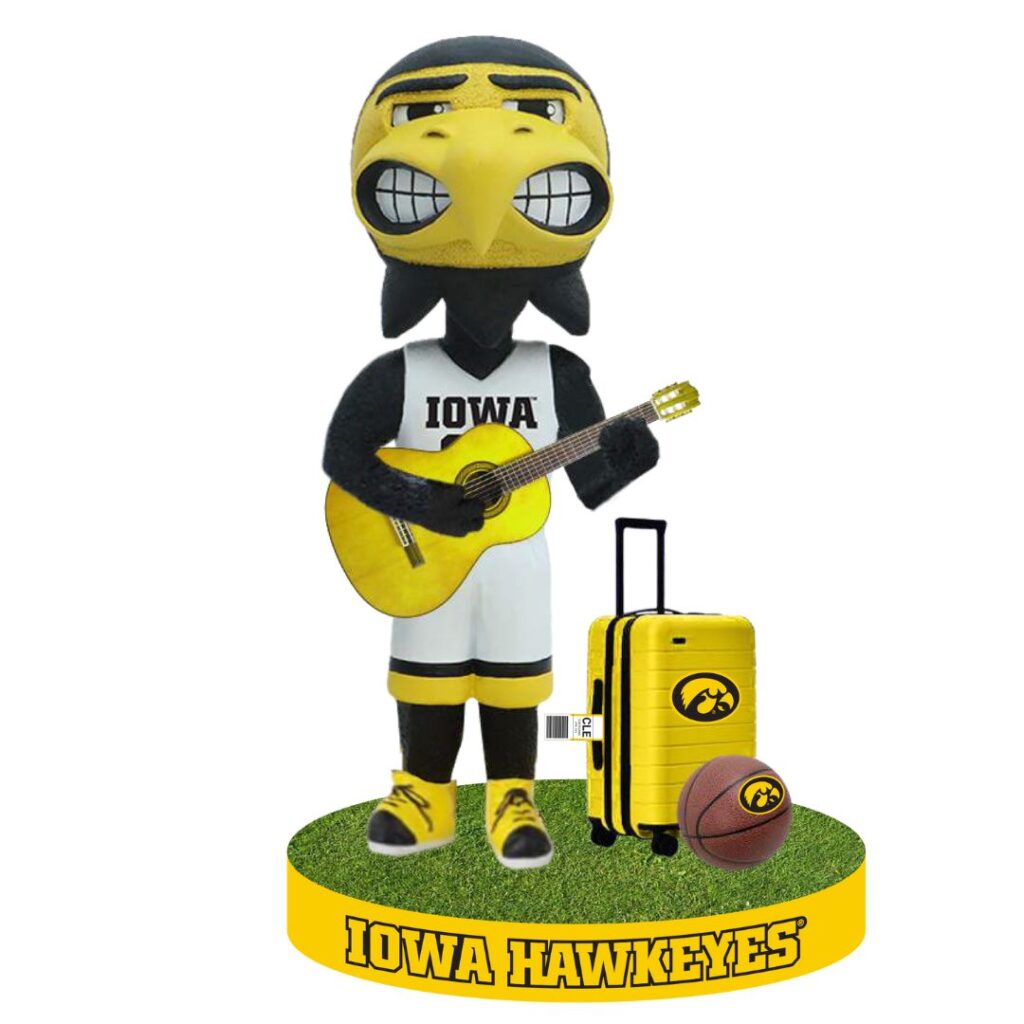
The unveiling of the Iowa Hawkeye Basketball bobblehead was this morning and is available in the National Bobblehead Hall of Fame and Museum’s online store. As Iowa heads to Cleveland after defeating National Champion and 3rd-seeded LSU in the Elite Eight on Monday to head to the Final Four for the third time in program history. Iowas will be looking for the school’s first title as the team and its fans make the trip to Cleveland. The bobbleheads, which are expected to ship in September, are $40 each plus a flat-rate shipping charge of $8 per order. Each bobblehead will be individually numbered to 2,024. The bobblehead features Iowa’s mascot, Herky the Hawk, playing a guitar with Iowa’s colors and logo. Next to Herky is a suitcase decked out in Iowa’s colors and logos with a Cleveland 2024 tag and an Iowa basketball. “We’re excited to unveil this Iowa Hawkeyes Bobblehead celebrating Iowa’s run to the Final Four as the team and its fans head to Cleveland,” National Bobblehead Hall of Fame and Museum co-founder and CEO Phil Sklar said. “This bobblehead is the perfect way for Iowa fans, alumni, students, faculty, and staff to celebrate the school’s trip to the Final Four in Cleveland!” The Iowa Hawkeyes Bobblehead joins the South Carolina Gamecocks, UConn Huskies, and NC State Wolfpack in the Headed to Cleveland Bobblehead Series.
U.S. Rail Report for the Week Ending March 30, 2024
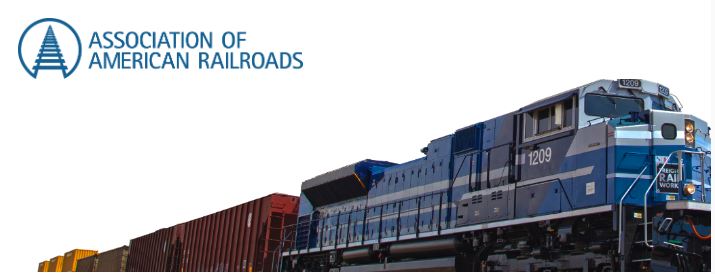
The Association of American Railroads (AAR) today reported U.S. rail traffic for the week ending March 30, 2024, as well as volumes for March 2024. U.S. railroads originated 866,865 carloads in March 2024, down 3.5 percent, or 31,101 carloads, from March 2023. U.S. railroads also originated 1,022,321 containers and trailers in March 2024, up 11.7 percent, or 106,903 units, from the same month last year. Combined U.S. carload and intermodal originations in March 2024 were 1,889,186, up 4.2 percent, or 75,802 carloads and intermodal units from March 2023. In March 2024, 11 of the 20 carload commodity categories tracked by the AAR each month saw carload gains compared with March 2023. These included: grain, up 8,475 carloads or 11.4 percent; chemicals, up 7,248 carloads or 5.7 percent; and petroleum & petroleum products, up 5,249 carloads or 15.0 percent. Commodities that saw declines in March 2024 from March 2023 included: coal, down 49,315 carloads or 18.6 percent; crushed stone, sand & gravel, down 5,434 carloads or 6.7 percent; and metallic ores, down 1,573 carloads or 8.9 percent. “Large swaths of rail traffic reflect broader economic changes,” stated Dr. Rand Ghayad, Chief Economist at the Association of American Railroads. “The recent announcement by the Institute for Supply Management that its manufacturing sentiment index turned positive in March aligns with rail carloads, excluding coal, showing a healthy 2.9% growth. This growth was driven largely by chemicals, petroleum products, and autos, critical components of our economy. Conversely, coal volumes continue to decline due to ongoing shifts in electricity generation markets. Intermodal was again a bright spot in March, reflecting stable consumer spending, increasing port activity, and a reduction in inventory destocking.” Excluding coal, carloads were up 18,214 carloads, or 2.9 percent, in March 2024 from March 2023. Excluding coal and grain, carloads were up 9,739 carloads or 1.7 percent. Total U.S. carload traffic for the first three months of 2024 was 2,773,827 carloads, down 4.2 percent, or 122,088 carloads, from the same period last year; and 3,268,647 intermodal units, up 9.1 percent, or 272,238 containers and trailers, from last year. Total combined U.S. traffic for the first 13 weeks of 2024 was 6,042,474 carloads and intermodal units, an increase of 2.5 percent compared to last year. Week Ending March 30, 2024 Total U.S. weekly rail traffic was 472,651 carloads and intermodal units, up 3.2 percent compared with the same week last year. Total carloads for the week ending March 30 were 218,733 carloads, down 3.2 percent compared with the same week in 2023, while U.S. weekly intermodal volume was 253,918 containers and trailers, up 9.3 percent compared to 2023. Eight of the 10 carload commodity groups posted an increase compared with the same week in 2023. They included grain, up 1,849 carloads, to 20,934; motor vehicles and parts, up 1,387 carloads, to 16,260; and chemicals, up 1,319 carloads, to 33,508. Commodity groups that posted decreases compared with the same week in 2023 were coal, down 13,750 carloads, to 51,603; and metallic ores and metals, down 1,279 carloads, to 21,129. North American rail volume for the week ending March 30, 2024, on 10 reporting U.S., Canadian and Mexican railroads totaled 328,007 carloads, down 4.1 percent compared with the same week last year, and 335,908 intermodal units, up 8.2 percent compared with last year. Total combined weekly rail traffic in North America was 663,915 carloads and intermodal units, up 1.8 percent. North American rail volume for the first 13 weeks of 2024 was 8,462,498 carloads and intermodal units, up 1.8 percent compared with 2023. Canadian railroads reported 92,728 carloads for the week, down 5.0 percent, and 71,047 intermodal units, up 8.0 percent compared with the same week in 2023. For the first 13 weeks of 2024, Canadian railroads reported a cumulative rail traffic volume of 2,050,973 carloads, containers, and trailers, down 0.8 percent. Mexican railroads reported 16,546 carloads for the week, down 10.4 percent compared with the same week last year, and 10,943 intermodal units, down 11.0 percent. Cumulative volume on Mexican railroads for the first 13 weeks of 2024 was 369,051 carloads and intermodal containers and trailers, up 5.1 percent from the same point last year. View the report here.
ASSP takes position opposing exploitative child labor
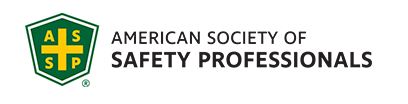
As the world’s oldest professional safety organization, the American Society of Safety Professionals (ASSP) has adopted a formal position on child labor. The statement from the board of directors declares that ASSP opposes all forms of exploitative child labor and calls on governmental and nongovernmental entities to combat such practices in the U.S. and worldwide. “While it is known that child labor is a significant issue in many developing countries, it sadly is also an issue in the United States that is seldom recognized,” said ASSP President Jim Thornton, CSP, CIH, FASSP, FAIHA. The International Labor Organization estimates that 22,000 children are killed at work every year. However, because much of child labor is hidden, it is difficult to obtain accurate data on how children are being affected. As part of ASSP’s position statement, the Society supports legislation and regulation that prohibit exploitative child labor practices; specific language in global standards that facilitates prevention; and actions by occupational safety and health professionals to implement policies and programs that better protect children in the workforce. “ASSP is the community that protects people, property, and the environment, so our mission reflects our role as guardians of worker safety,” Thornton said. “Safety, health, and well-being are inherent rights of every worker.” ASSP has heard from many of its 35,000 global members who feel strongly about the child labor issue, and the Society has received valuable insights from its Governmental Affairs and Standards Development committees. “There has been a focus to loosen U.S. child labor laws to help industry combat labor shortages,” Thornton said. “Wages for young workers are generally less than workers 18 and older based on the premise they are learning or less productive. The reality is those arguments are hyperbole to allow youth to be treated as lesser people.” While ASSP opposes exploitative child labor practices, the Society supports reasonable approaches to young people working and realizing the associated benefits and responsibilities of having a job. “We fully acknowledge the advantages of working as part of an individual’s maturation process,” Thornton said. “Our position is not meant to take a stand against young people working appropriate hours or in settings such as the family farm where experiences do not subject youth to hazards associated with farming and agriculture.” ASSP’s position statement specifically notes exploitative child labor practices such as: Full-time hours or an accumulation of hours that interferes with a child’s ability to attend school. Exposure to hard physical labor, hazardous conditions, or toxic environments. Agriculture tasks involving dangerous equipment are known to cause injuries and fatalities to young workers. Work activities that don’t allow a child to grow to become a healthy and productive adult. Any endeavor that demeans or exploits children harmfully or inappropriately. With its child labor position set, ASSP will now pursue next steps that include: Publishing articles and hosting webinars to educate the occupational safety and health community. Advocating for the prohibition of exploitative child labor in global standards such as the ANSI/ASSP/ISO 45001 and ANSI/ASSP Z10 occupational health and safety management systems standards. Using ASSP’s consultative status with the United Nations to support efforts to raise awareness. Encouraging ASSP members to help address the issue through supply chain requirements and environmental, social, and governance (ESG) practices. Working with other occupational safety and health organizations to help prohibit exploitative child labor. “This isn’t an issue we can solve alone, but entities working together can begin to turn the tide,” Thornton said.
BSL Battery receives certification for LiFePo4 forklift batteries
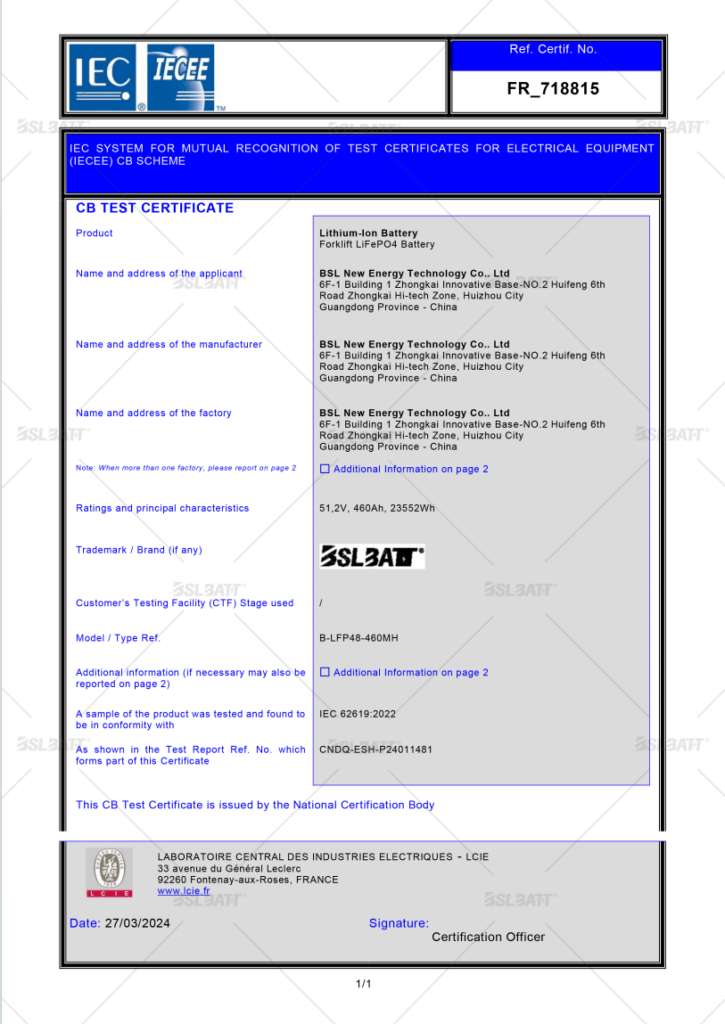
Innovation, quality, and safety have always been fundamental factors in the design and manufacture of BSL Battery – Industrial’s Lithium Iron Phosphate batteries. With the breakthrough of UL2580 and IEC 62619 certifications, BSL Battery-Industrial’s commitment to safety and design excellence remains unmatched. This milestone solidifies BSL Battery-Industrial’s position as a leader in the power industry. BSL Battery – Industrial, a recognized manufacturer of lithium-ion forklift batteries, has announced that the B-LFP24-205MH, B-LFP36-820MH, B-LFP48-460MH, B-LFP48-615MH, and B-LFP80-460MH lithium-ion (Li-ion) battery portfolios have received UL2580 and IEC 62619 certifications. UL2580 is the standard provided by UL, the global safety science organization, for battery products at the cell, module, and battery pack level to ensure safe use in a variety of power or transportation-related applications. IEC 62619 specifies requirements and tests for the safe operation of rechargeable batteries and battery packs in industrial applications. This prestigious certification will now apply to BSL Battery – Industrial Forklift Lithium Batteries. The UL2580 and IEC 62619 safety testing of forklift lithium-ion batteries has several benefits: By complying with the requirements and tests specified in the standard to ensure product safety, manufacturers can ensure that consumers use their batteries safely. It is well known that lithium-ion batteries can catch fire or explode if not properly designed, manufactured, or used. UL2580 and IEC 62619 mechanical testing and electrical testing help identify potential safety hazards and reduce the risk of accidents. Many countries have regulations that require products containing lithium-ion batteries to meet certain safety standards. Testing UL2580 and IEC 62619 can help manufacturers meet these requirements in the global marketplace. Consumers are becoming more aware of the potential safety hazards associated with lithium-ion batteries. By testing UL2580 and IEC 62619 and complying with the standards, manufacturers can gain consumer trust and differentiate their products from competitors. The mechanical testing, electrical testing, environmental testing, and test procedures for tolerance to battery failure specified in UL2580 and IEC 62619 can help identify potential quality issues with lithium-ion batteries, thereby improving product quality, design, manufacturing, and performance.