Are you a sales leader or a sales chaser?
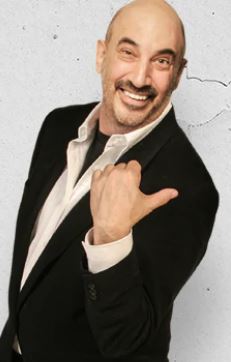
I grew up in Haddonfield, New Jersey. We lived at the corner of the busiest intersection in town. I was 15 years old when we got a puppy named “Thing-a-ma-jig.” The cutest, friendliest mutt-puppy you ever saw. One morning, about a week later, I opened the front door to get the paper — and the puppy got loose. She started running as fast as she could — right for the traffic. I started chasing her — hopelessly for five blocks, across busy streets — my little dog was gone — I was panicked (and out of breath). I decided to run back home and ask my dad to use the car and find the dog. I ran straight to my parent’s bedroom. “Dad — dad,” I panted, “The — dog’s — run — away — car — chase — it!” “OK son,” he said,” “Let’s jump in the car and find your puppy.” I turned to run out the door – took one step and tripped over the dog. You see, as soon as I started to run the other way, the dog chased me! Chasing your prospects too hard? Trying to push too hard for the sale? Follow up with a thinly disguised: “Is the money ready? Can I come over and get the money?” You figure that the best way is to be assertive and tell him why your company and product (or service) are the greatest. Right? — Wrong, sales breath! Try the opposite approach. Try running the other way by being attractive through your value. Create the law of attraction, and — let the prospect chase you. It’s the best sales and follow-up technique you’ve ever experienced. And the easiest way to sell is to buy. EARLY WARNING SIGNAL: No returned phone call. If prospects are not returning your call — whose fault is that? You’re chasing too hard. They’re running away. You couldn’t get their interest — you couldn’t get them (they aren’t interested enough) to chase you. Other tell-tale symptoms that the chase is going the wrong way: You are still cold calling (or direct emailing) to get prospects. You’re uncomfortable about calling. You are unprepared, or you have not established the needs of the prospect and are unsure of their status, or you don’t have much rapport with the prospect, or some of each. You are having trouble making appointments Prospects just won’t decide, and you keep hounding them. You’ve followed up a few times, and now you’re searching for a reason to call them — but you can’t think of one. The prospect is giving you a bunch of lame excuses. And worse, you are accepting them. If chasing people too hard makes them run away, why are you continuing to do it? The way I got my puppy-dog to come home was — I led the dog home. You can either lead the field or be in the field (some people are in left field). Your challenge is to lead your prospects so they will follow you — and turn into customers. Here’s the simple solution: (NOTE: I didn’t say easy, I said simple. There are no easy solutions.) Create a better market position for yourself. Are your prospects and customers reading about you – or getting information they can use written by you — in their social media accounts? Are they gaining helpful information on your web site? Have you recently spoken at their annual meeting? Or are you thinking “brochure,” “appointment,” and “product demo” or “corporate video.” Wrong thoughts. Those are competitive thoughts and lead to a dissertation by you and your competition as to who is better – and always lead to a battle over price. A battle that everyone who fights in it, loses. To create the position you seek: Getting qualified people to call you – you’d better get beyond the typical marketing materials. ASK YOURSELF: Where are people seeing you or talking about you? TELL YOURSELF: It takes time to create position. REWARD YOURSELF: But once you do, people call you to buy, instead of you calling them to sell. The secret formula? The magic potion? Real simple… whatever you do with your outreach, always have a prime objective at your core. Here is the one that has worked for me: PRIME OBJECTIVE: Put yourself in front of people that can say “yes” to you and deliver value first. About the Author: Jeffrey Gitomer is the author of twelve best-selling books including The Sales Bible, The Little Red Book of Selling, and The Little Gold Book of Yes! Attitude. His real-world ideas and content are also available as online courses at www.GitomerLearningAcademy.com. For information about training and seminars visit Are you a sales leader or a sales chaser? or email Jeffrey at salesman@gitomer.com or call him at 704 333-1112.
The innovative Movu escala 3D bin shuttle system took 1st place and receives “Product of the Year 2024” award
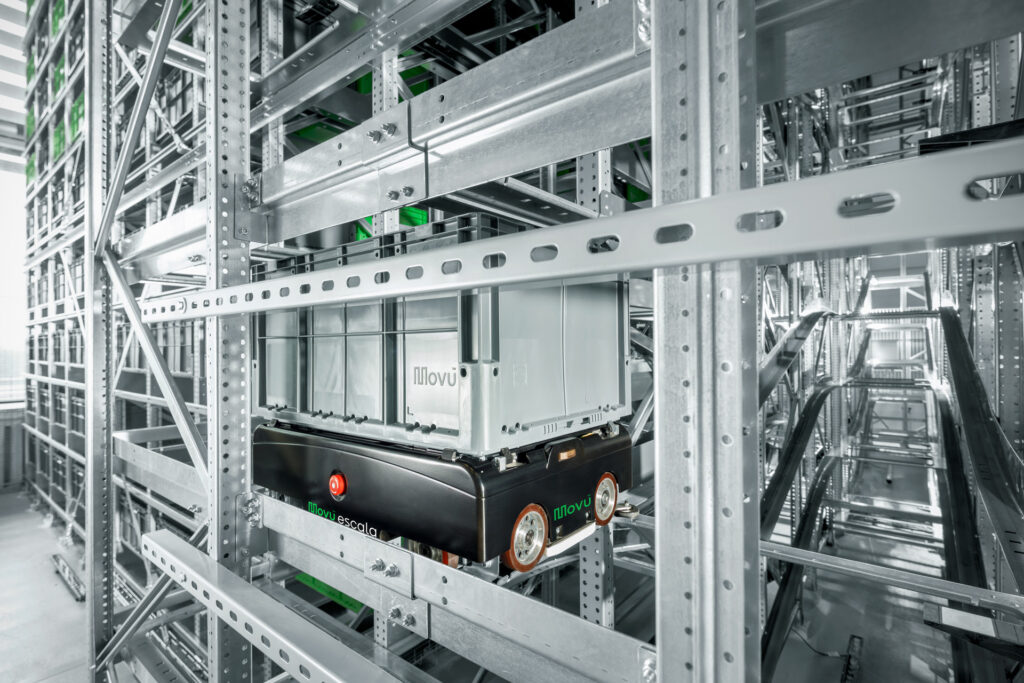
The Movu 3D shuttle system “escala” has been awarded “Product of the Year 2024” by the readers of the logistics trade magazine Materialfluss. After the Movu ifollow and the Movu atlas, the next family member from the Movu portfolio has now also received an important award. Votes were cast for products and solutions in five categories, with Movu escala took 1st place in the ‘Picking technology”, which was judged on three main criteria. First, the product is technically mature and available on the market. Secondly, it stands out significantly from its market competitors thanks to innovative features. Finally, the entry offers customers a clearly recognizable benefit. The award-winning Movu escala is the next-generation, flexible robotic automated bin storage and retrieval sub-system – for even the smallest applications of bin-compatible products. Robots move along a sophisticated rail track that connects every location point within the dense storage and retrieval rack – from fellow stow Group company, stow Racking – transferring between levels via ramps. This eliminates the need for maintenance-intensive conveyors, lifts, service aisle access, and sequencers. Intelligent management software, combined with the innovative rack design, allows the sequencing of bins at multiple points within the system and at the goods-to-person workstations. Jos De Vuyst, CEO of stow Group, said: “We are delighted to have received this award and would like to thank all readers who voted in our favor. The award confirms the innovative strength of the stow Group and of Movu Robotics and motivates us even more in our endeavors to develop advanced and accessible logistics automation solutions for all customers, regardless of whether they are starting in automation or expanding further.”
Loftware unveils enhanced cloud labeling platform at LogiMat 2024
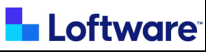
Loftware Cloud enables companies to conquer supply chain complexities, ensure supplier compliance, and improve traceability Loftware has unveiled Loftware Cloud at LogiMAT 2024. The cloud-based labeling platform harnesses the power of the company’s state-of-the-art technologies and is designed to help businesses of all sizes conquer diverse supply chain complexities, ensure supplier compliance, and improve traceability. The powerful and intuitive solution empowers organizations to adapt to changing demands across the global supply chain by providing users with the ability to easily design, manage, and print millions of accurate labels per day. This level of standardization and automation transforms legacy manual error-prone processes, facilitating high-performance supply chain label printing and enabling scale. Loftware Cloud is a robust and secure platform designed to meet the needs of all businesses no matter their size or industry focus. With fast deployment times, lower upfront costs, easy access, high availability, unmatched scalability, and impressive flexibility, the innovative solution helps companies meet a full range of business challenges. This includes addressing increasing customer requirements and evolving regulatory compliance. “2024 marks a pivotal point for global supply chains as automation becomes increasingly prevalent. Many organizations have historically struggled to keep up with this pace of change, risking lost opportunities and revenue,” said Michelle Northey, Loftware EVP Product. “However, for companies looking to transform their digital supply chain, Loftware Cloud offers a powerful, versatile, and cutting-edge solution that adheres to critical regulatory and customer standards while saving companies time, money, and resources.” Evolving customer demands, industry standards, and regulations define how products are developed, shipped, and disposed of across the global supply chain. Maintaining supplier compliance is a vital part of ensuring this is done seamlessly and accurately. Using Loftware Cloud, suppliers and co-packers can seamlessly print labels using pre-approved templates and data. Businesses can regulate access to the platform, gaining a meticulous record of each label printed and guaranteeing that labels meet compliance and brand standards. By doing so, companies can eliminate relabeling, save time, and reduce costs. In a bid to foster a sustainable enterprise, Loftware Cloud also brings unprecedented visibility and transparency across the global supply chain network by supporting track and trace and serialization initiatives. The benefits are varied – from minimizing costs and enhancing operational efficiency to improving agility and eliminating redundancies. Organizations leveraging Loftware’s solution also experience reduced rework, lower scrap rates, and a decreased need for relabeling, resulting in significant inventory loss prevention, and removing the need for costly product recalls. Additionally, Loftware’s certified SAP labeling solutions – designed to integrate with any SAP landscape – allow companies to drive their labeling seamlessly no matter where they are on their journey to S/4HANA. Loftware Cloud offers market-leading integration with SAP, S/4HANA, SAP Business Suite on HANA, and SAP ECC, allowing businesses to reduce costs, improve agility, and minimize costly errors. Existing Loftware customers, regardless of their current Loftware platform, will enjoy a seamless transition to a more powerful and integrated solution that delivers on our promise of innovation and excellence.
AIT Worldwide Logistics promotes three leaders to new executive roles
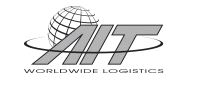
Ben Naro, Bill Fallon and Mike Tegtmeyer will guide growing sales, strategic accounts and infrastructure teams AIT Worldwide Logistics has announced promotions for three executive team members. Ben Naro and Bill Fallon have been named chief sales officer and chief commercial officer, respectively. They are the seventh and eighth members of the company’s C-level team. Meanwhile, Mike Tegtmeyer has been promoted to the role of executive vice president, of global infrastructure and security. Naro and Fallon report to President and Chief Operating Officer, Keith Tholan. Tegtmeyer reports to Chief Information Officer, Ray Fennelly. “Ben, Bill, and Mike have made outstanding, unique contributions to the company’s growth,” said AIT Chairman and Chief Executive Officer, Vaughn Moore. “I feel incredibly grateful and confident knowing that our sales, strategic accounts, and infrastructure teams are guided by the leadership of these three professionals whose accomplishments have raised the bar for high performance.” Chief Sales Officer, Ben Naro As AIT’s Chief Sales Officer, Naro is responsible for managing the global territory and field sales team. He is also tasked with aligning the sales organization to AIT’s overall global strategy while collaborating with all stakeholders to ensure strategic goals and initiatives are fulfilled. Finally, Ben will work diligently to drive growth through team building that connects and coordinates sales strategies amongst the AIT network’s primary geographic regions. “More than two decades ago, Ben came to AIT with just three years of freight forwarding sales experience,” Tholan said. “Since then, he has continually earned career advancement opportunities by performing in just about every sales role imaginable. He is a champion for AIT’s sales strategy, working diligently to upgrade processes and build high-performing teams of sales professionals across the network.” Chief Commercial Officer, Bill Fallon In his new role, Fallon sets the strategy and manages the set-up for a diverse array of vertical markets in AIT’s strategic account program. He also supports the entire organization by establishing solutions for broader strategic opportunities requiring a highly specialized, customized approach and he will focus on extending these niche, high-touch solutions to new markets in the AIT network. “Bill has more than 41 years of transportation experience, including 10 years with AIT, spanning from his early days in operations to becoming one of the best solutions design professionals in the forwarding industry,” Tholan said. “He reinvented himself early on at AIT and soon became the company’s number one sales professional and he has worked hard to assemble a team of highly diversified experts in the strategic account program.” Executive Vice President, Global Infrastructure and Security, Mike Tegtmeyer In his new role, Tegtmeyer continues leading the organization towards a next-gen level of quality in the worldwide management of AIT’s technology infrastructure and hardware platforms. With a priority emphasis on the networks in Asia and Europe, he is supporting the company’s path to an enhanced and expanded global infrastructure strategy. He will also maintain his focus on process improvements for the business, especially the expansion of AITConnect, a ticketing system that his team successfully rolled out for AIT’s compliance, human resources and IT help desk groups. “Over the course of his five years with AIT, Mike has deeply matured the company’s infrastructure strategy by leading the deployment of a modern, high-quality cloud-based environment,” Fennelly said. “On behalf of the entire organization, I’d like to acknowledge how much we appreciate his intellect, leadership and personal expression of AIT’s core values.”
Bobcat Company named to Fast Company’s 2024 Most Innovative Companies list
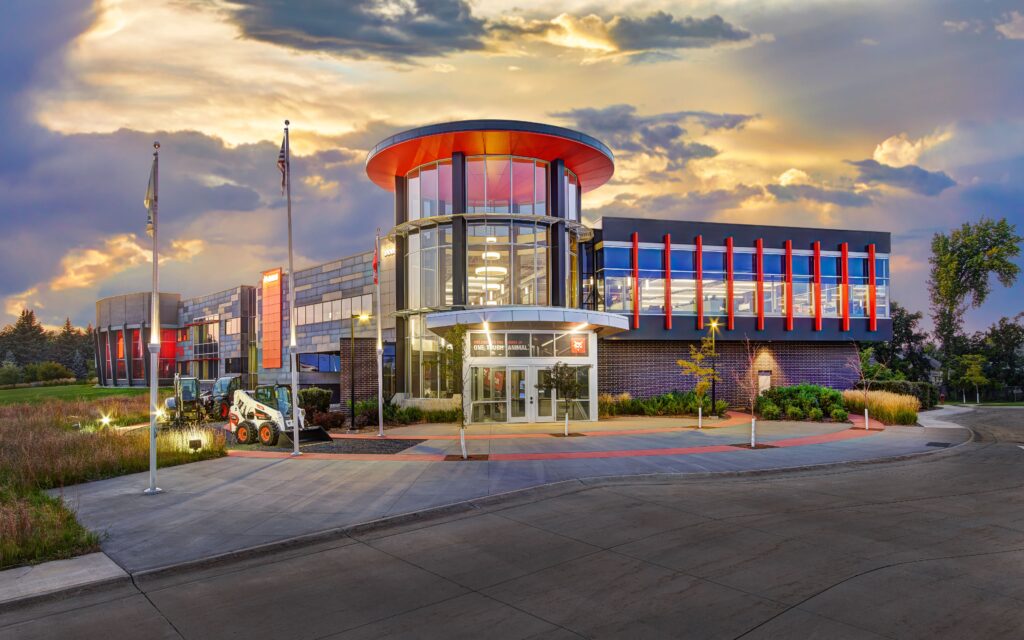
Brand recognized as stand-out industry leader in manufacturing, equipment design and automation Bobcat Company has been recognized as one of Fast Company’s 2024 Most Innovative Companies. The Most Innovative Companies honor places Bobcat in the spotlight among other organizations that are transforming industries and shaping society. “With innovation being at the core of our legacy, Bobcat is driving the industry forward reaching new heights,” said Joel Honeyman, Doosan Bobcat vice president of global innovation. “We believe that embracing technology and innovation is vital to long-term success, and we are thrilled to be recognized on Fast Company’s Most Innovative Companies list.” Since 1958, Bobcat has been looking forward in all aspects of its business to transform how the world works, build cities, and support communities for a more sustainable future. Advancing Manufacturing for Efficiency and Precision Bobcat is recognized in Fast Company’s Most Innovative Companies’ manufacturing awards category. Bobcat has advanced its manufacturing facilities—both in terms of its footprint and the technology within its many global locations. Recent updates to its facilities have included a $9.3 million automated press system in its Gwinner, N.D., manufacturing facility; technology in its Statesville, N.C., facility that streamlines component inspection; and a new robotic forming press in its Johnson Creek, Wis., location that minimizes operators’ manual labor while improving precision. All of these advancements have led to improved efficiencies, greater precision and more ergonomic worksites for its employees. Inventions for the Job Site of Tomorrow With a focus on innovation, Bobcat is paving the way for electrification and autonomy in equipment design and development. Since 2022, the brand has launched several industry-first machines, including the all-electric T7X compact track loader, the all-electric concept S7X skid-steer loader, and the fully electric and autonomous concept pair of loaders, the RogueX and the RogueX2. These new machines have garnered many new patents and patents pending, signifying how Bobcat is defining a new work experience while bringing sustainable solutions to the marketplace. Recognition, Optimism in Moving the World Forward This year’s Most Innovative Companies program showcases 58 industry categories—with manufacturing, health, climate, energy and AI among its popular categories. A panel of Fast Company editors and writers identified the companies driving progress around the world and across industries, evaluating thousands of submissions through a competitive application process. The result is a globe-spanning guide to innovation today, from early-stage startups to some of the most valuable companies in the world. “Our list of the Most Innovative Companies is both a comprehensive look at the innovation economy and a snapshot of the business trends that defined the year,” said Fast Company editor-in-chief Brendan Vaughan. “We saw extraordinary innovation across the board in 2023, but we also saw a handful of clear patterns: the growing footprint and impact of AI, the triumphant return of live events, and great leaps forward in climate tech. We face daunting challenges on many fronts, but the solutions we celebrate in MIC give me plenty of hope about the future.”
Dorner and Garvey partner on New AquaGard GT Stainless Steel Conveyor
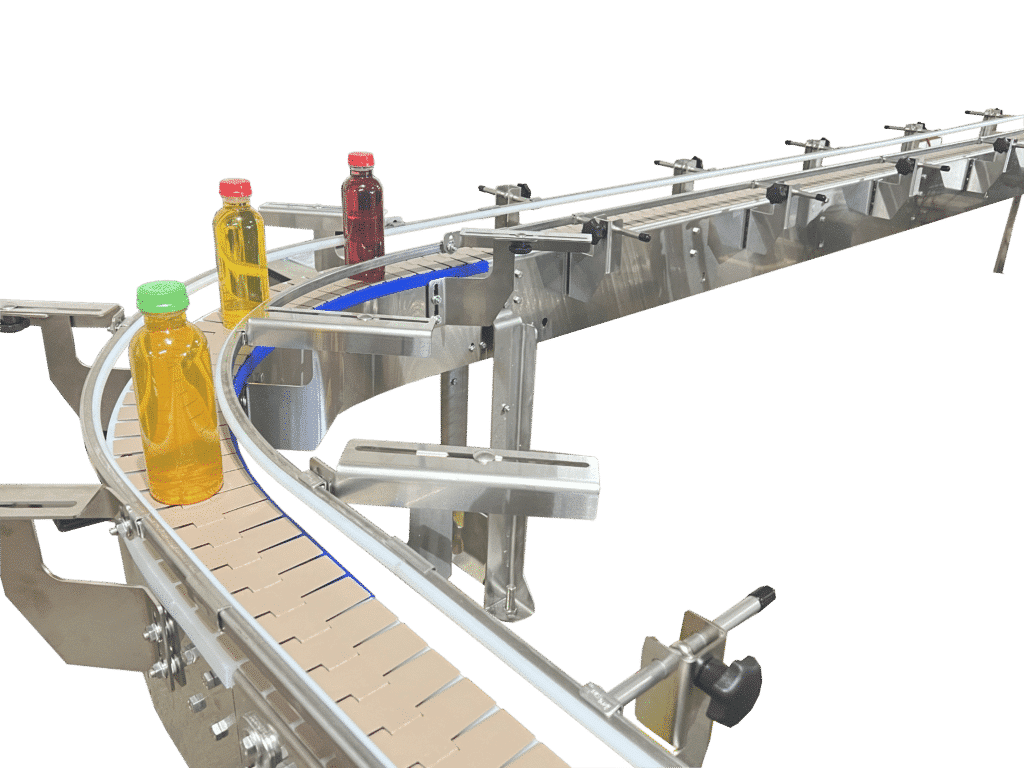
Dorner and Garvey are well-established brands with decades of proven success. But now, they are combining their strengths to write a new chapter together with the recent launch of its AquaGard GT Stainless Steel conveyor. This new line combines the best conveyance expertise of both brands to develop a platform with an attractive price point that integrates with accumulation systems and other machinery to create a fully automated processing line for bottling, canning, and food processing applications. The AquaGard GT merges the strengths of Garvey’s GT Series conveyor with Dorner’s AquaGard 7100 Series sanitary stainless steel conveyor. The AquaGard GT is a meticulously designed infeed and outfeed conveyor ideal for accumulation-type applications to prevent bottlenecks in industries such as packaging, bottling, dry food processing, and part handling. All components (except motors) are either stainless steel or FDA-approved plastics, which are ideal for operating in environments that require wipe-down or occasional washdown cleanings of the conveyor. Simple Design and Function The AquaGard GT conveyor system is designed to be as simple as possible, ensuring the highest level of reliability. These conveyors are engineered for flexibility and can be inserted virtually anywhere in the system, making line expansions or complete changeovers fast and efficient. With Dorner’s best industry lead time, conveyors can be custom-engineered and shipped out quickly to minimize downtime and get a production line up and running in no time. Versatility in Applications The AquaGard GT conveyor is a versatile solution suitable for an array of applications across a wide variety of industries. Primarily designed for packaged goods transport, its robust construction and advanced engineering ensure seamless movement of goods with precision and reliability. Its adaptability shines in integrated solutions by navigating through machines for efficient processing. Moreover, its seamless integration extends to end-of-line packaging and palletizers as well where it ensures smooth transitions and optimized throughput, enhancing overall operational efficiency. The AquaGard GT integrates features and benefits such as powered transfer units, flush side tails, and pre-engineered transfer modules, among others that in-house machine builders cannot match. The conveyor is competitively priced and comes with a short 10-day lead time.
ARA’s updated economic forecast
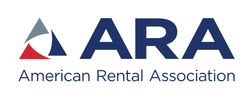
The updated forecast released at The ARA Show™, the American Rental Association (ARA) indicates that the United States equipment rental industry’s growth has a fairly positive outlook. Last quarter, the year-over-year growth was expected to be 7.6% in 2023 and 3.1% in 2024. The most current projections indicate a 7.9% increase in 2024 totaling $77.3 billion in construction and general tool rental revenue. “The ARA Rentalytics™ quarterly forecast reinforces the strength of the rental industry,” says Tom Doyle, ARA vice president, program development. “Rental should benefit with tailwinds from interest rates, inflation, improving supply, a preference to rent, and government and private spending. Rental revenue is again forecasted to increase.” Looking more granularly at construction and industrial equipment (CIE) growth in the United States, $60.9 billion is the projected revenue in 2024, which is 7.5% growth. In the coming years, 2025, 2026, and 2027, 3% growth is projected. The difference is smaller but still appreciable and more in line with a steadily growing economy. “We see a slowing of growth this year compared to last year but bear in mind, we have a slowing of inflation this year as well,” says Scott Hazelton, managing director at S&P Global. “The growth rates tail off in the future years, with growth of 4.3% in 2025 and 3.9% in 2026.” The current forecast for total Canadian equipment rental revenue shows a 3.1% growth to $974 million in 2024. 2024 growth is stronger in Canada than in 2023 growth due to inflation and resilient demand. In addition, Canada’s housing market and non-residential structure construction are both improving. While CIE investment will decline from previous years, a 7.2% increase is forecasted. The stark contrast from previous years is attributed to the lack of post-COVID investments in 2024. As businesses choose rental over ownership, the CIE rental penetration rate follows. The 2023 estimate of 56.4% is near the pre-pandemic peak. General tool investment in the United States is not quite as positive of an outlook. There is muted investment growth at 6.8%. Manufacturing is driving the growth and housing is still the weak spot. “ARA’s quarterly member survey showed conflicting results amongst members with just over half of respondents saying they saw a revenue increase in quarter four, a slight improvement over quarter three which saw an even split between those an increase and decrease,” says Mike Savely, ARA director, program development. It is worth noting that in current forecasts, no state in the United States has a decline in rental revenue growth in the next five years. There are states with weaknesses, but there is still growth.
Lift and Tilt table lowers to floor level for hand pallet truck accessibility
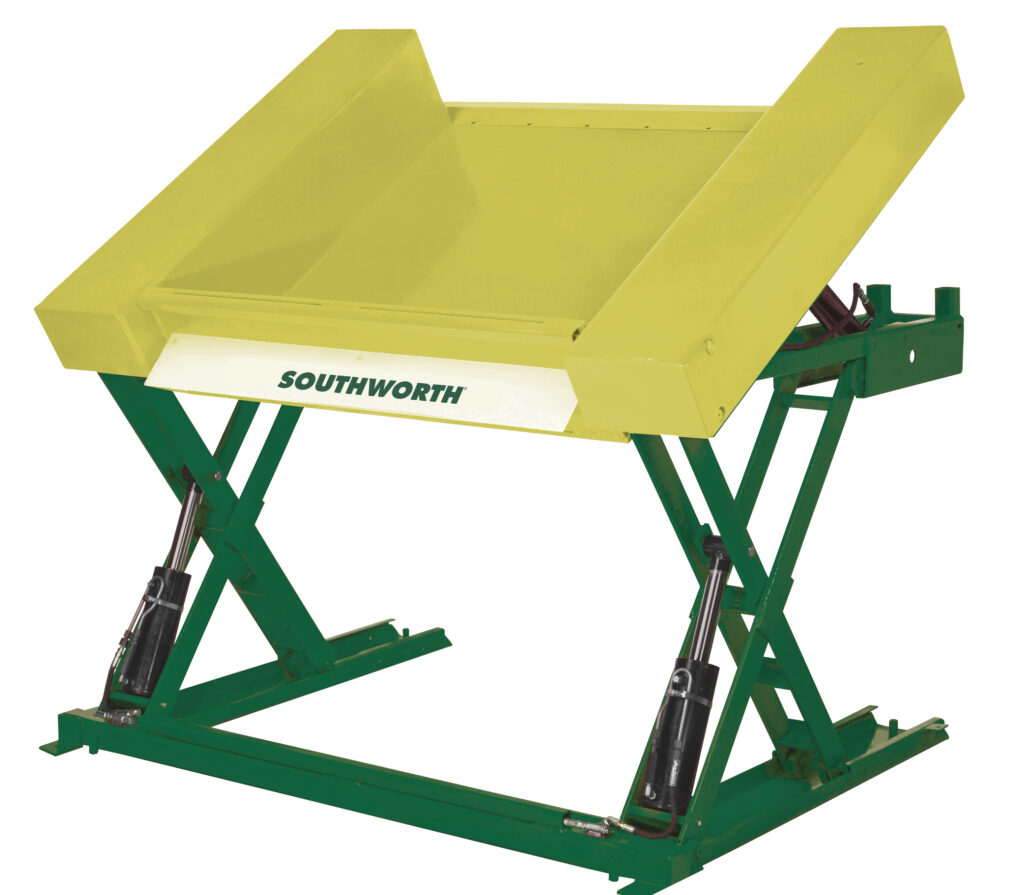
An extension of the popular ZLS line of floor height lifts, the new ZLS-T from Southworth is a combination lifter and tilter designed for accessing items stored in containers, totes, or gaylords. Its unique pan-style platform sits essentially flush with the floor when lowered allowing it to be loaded and unloaded by a hand pallet truck. It is ideal for use in facilities without forklifts or stackers or in areas where forklifts are prohibited. Lift and tilt are controlled independently so operators can precisely position loads at the most convenient height and angle for easy access without bending, reaching, or stretching. As the level of items in the container changes, the operator adjusts the height, angle, or both to maintain optimal ergonomic positioning throughout a shift. The ZLS-T tilts loads up to 30˚ while at any height from floor level to 33½” making it ideal for use with tall- or short-sided containers and drop gate containers. The operator controls lift and tilt position from either a hand pendant or foot control switch. Capacities of 2,000 or 4,000 pounds are available. The platform is 50” x 48”. A single-power unit with a 1 HP motor that operates on 115/1/60 power is used for both lift and tilt functions. ZLS-T models can be equipped with a wide range of safety and convenience options including bellows accordion skirting, photo-eye toe protection, portability chains, three-phase power units, custom platform sizes, and corrosion-resistant finishes.
Configura wins best IT Innovation Award at MODEX 2024
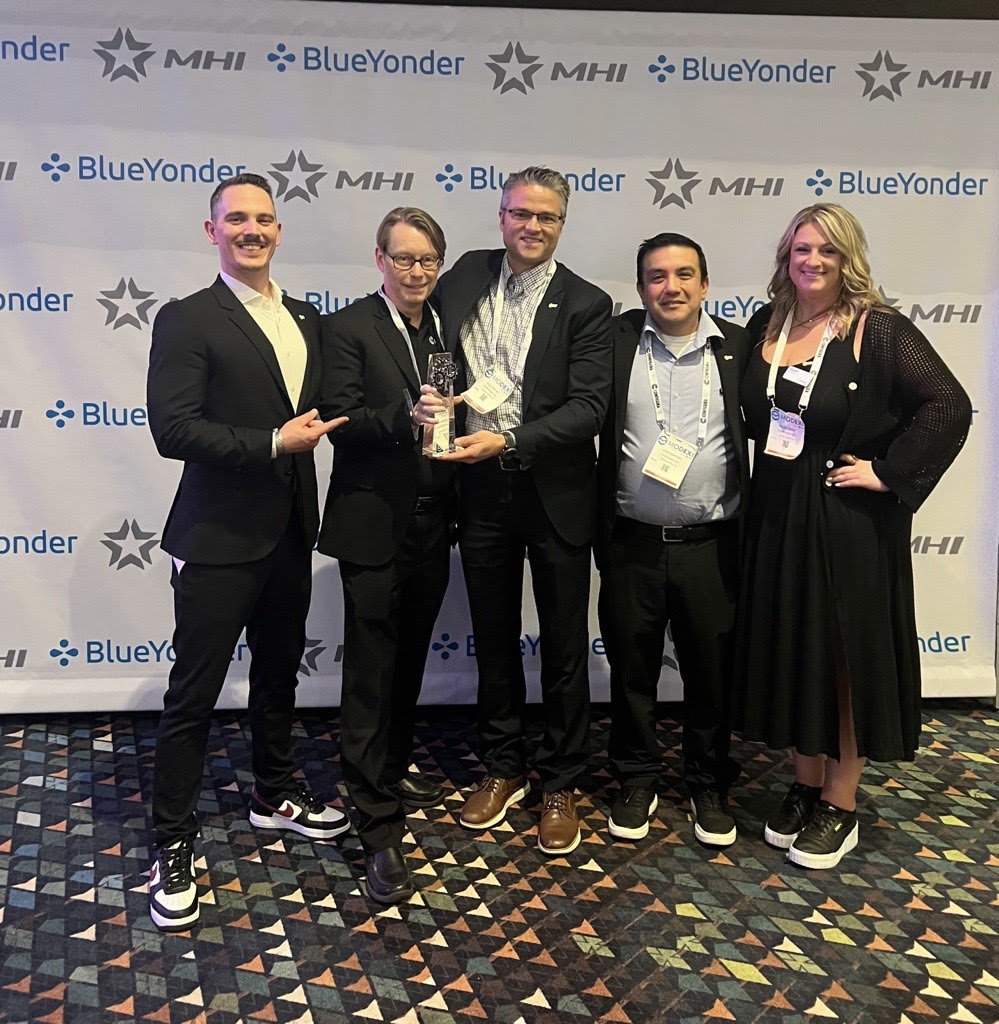
Recognition underscores the platform’s ability to help users design, envision, and implement the future warehouse. Configura, a design-oriented software solutions, was honored with the MHI Innovation Award for Best IT Innovation for its CET Material Handling product. This prestigious award was announced at MODEX 2024, North America’s largest material handling and supply chain conference, with more than 1,200 exhibitors in Atlanta, Georgia. The MHI Innovation Awards educate MODEX attendees and provide valuable insights on the latest manufacturing and supply chain products and services. Out of nearly 200 submissions for this year’s awards, MHI recognized Configura for its dedication to creating revolutionary software for intralogistics, warehousing, and distribution center design. CET Material Handling sets a new standard in material handling system design. CET operates seamlessly in 2D and 3D and utilizes Parametric Graphical Configuration (PGC) technology to eliminate errors, improve efficiency and streamline the design process. Real-time Bill of Materials, pricing, and comprehensive documentation creation contribute to error reduction and overall project success. “I’m so proud and happy to be a part of this great team and the work we have accomplished to position Configura at the forefront of the material handling industry,” said Stefan Persson, CEO of Configura. “After more than 30 years, we continue to produce innovative products and services for the global design community and remain committed to listening to our customers and developing our products to best suit their needs.” MODEX 2024 exhibitors were invited to submit a new product, product line, technology, service or new application of existing products or technology that creates quantifiable and sustainable results regarding ROI, cost savings, customer satisfaction, etc. The event brought together thousands of industry experts, professionals, and businesses from around the world to showcase the latest technologies, products, and solutions in the field of automation and material handling. Conference attendees witnessed live demonstrations of CET Material Handling to see how easy it can be to design a full-blown warehouse, including anything from racking to conveyors, with instant visualization and an automatic bill of materials. “We’re grateful for this recognition from the material handling community and appreciate MHI for putting together such a fantastic event,” said Rich Trahey, VP of Sales and Marketing at Configura. “We’re excited to keep pushing boundaries in the industry and continuing to be a resource for all material handling design needs.”
ORBIS enters into agreement for manufacturing plant in Texas
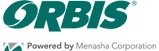
ORBIS® Corporation has announced it is entering into a lease-to-own agreement for manufacturing space in Greenville, Texas, with EPM Partners of New York. ORBIS Corporation is a wholly owned subsidiary of 175-year-old Menasha Corporation, based in Neenah, Wis. The agreement includes 420,000 square feet of manufacturing space that will be used to produce reusable pallets, totes, and bulk containers. Improvements and infrastructure will be required to prepare the space for ORBIS’ manufacturing activities. ORBIS will also enter a lease agreement with EPM Partners for 240,000 square feet of warehousing space in the same building. “We are excited to see this investment come to life and support our customers’ growth,” stated Norm Kukuk, president of ORBIS Corporation. “This plant enables ORBIS to expand its geographic footprint and increase production capacity to serve our customers with industry-leading solutions while making an impact in the community.” ORBIS expects to add more than 190 employees within two years of the lease commencement in order to support operations at the new plant. “ORBIS is bringing great new manufacturing jobs to Hunt County and we are very excited to partner with this world class leader for the long term,” states Hunt County Judge, Bobby Stovall. This plant is projected to begin some operations by the end of 2024. “We are so pleased to join the Greenville business community, where many investments have been made to create a strong business climate,” states Lynn Hediger, vice president of product management at ORBIS. This plant is located about fifty miles northeast of Dallas. According to Jerry Ransom, City of Greenville, Tex. Mayor, “We are excited to expand our business community with this world-class manufacturer who is focused on providing sustainable packaging solutions for the supply chain.” As a steward of sustainability, ORBIS is committed to driving the circular economy and a better world for future generations through reuse with environmentally friendly designed products, end-of-life recycling, material innovations and sustainable operations.
Google, Microsoft, and Nucor announced a new clean electricity technology initiative
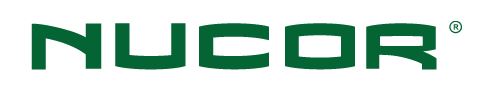
Google LLC, Microsoft Corporation, and Nucor Corporation have announced they will work together across the electricity ecosystem to develop new business models and aggregate their demand for advanced clean electricity technologies. These models will be designed to accelerate the development of first-of-a-kind (FOAK) and early commercial projects, including advanced nuclear, next-generation geothermal, clean hydrogen, long-duration energy storage (LDES), and others. As a first step, the companies will issue an RFI in several US regions for potential projects in need of offtake, and encourage technology providers, developers, investors, utilities, and others interested in responding to get in touch here. According to the International Energy Agency (IEA), firm, dispatchable clean electricity technologies and advanced energy storage systems are needed to cost-effectively decarbonize grids and help the world meet its growing electricity demand with carbon-free energy sources. These advanced clean electricity technologies can fill gaps in wind and solar production and support grid reliability – needs that today are still being met by fossil fuel generation. Yet, these advanced clean electricity technologies face challenges, in part because the novelty and risk of early projects make it difficult to secure the financing they need. By developing new commercial structures and aggregating demand from three of the world’s largest energy buyers, this approach aims to reduce the risks for utilities and developers considering early commercial projects and enable the investments that are needed – ultimately helping to bring these projects online by the early 2030s and reducing technology costs through repeated deployment. The companies will initially focus on proving out the demand aggregation and procurement model through advanced technology pilot projects in the United States. The companies will pilot a project delivery framework focused on three enabling levers for early commercial projects: signing offtake agreements for technologies that are still early on the cost curve, bringing a clear customer voice to policymakers and other stakeholders on broader long-term ecosystem improvements, and developing new enabling tariff structures in partnership with energy providers and utilities. In addition to supporting innovative technologies that can help decarbonize electricity systems worldwide, this demand aggregation model will bring clear benefits to large energy buyers. Pooling demand enables buyers to offtake larger volumes of carbon-free electricity from a portfolio of plants, reducing project-specific development risk, and enables procurement efficiencies and shared learnings. To ensure that the project delivery framework that they develop is transparent and scalable, Google, Microsoft, and Nucor will share their lessons learned and the roadmap from their first pilot projects, and encourage other companies to consider how they can also support advanced clean electricity projects.
Episode 470: Perpetual Power in warehousing with CaPow
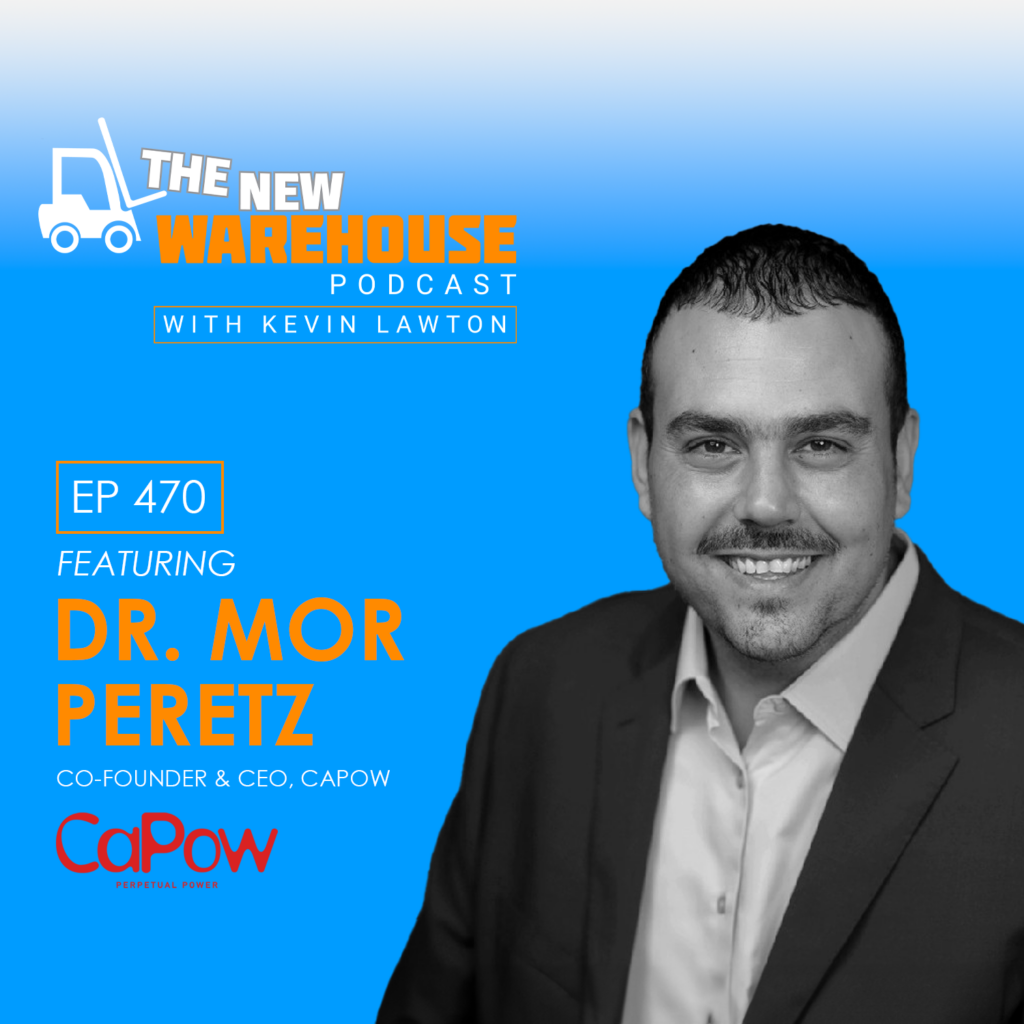
This episode of The New Warehouse Podcast features Dr. Mor Peretz, CEO of CaPow. CaPow, short for capacitive power, is transforming charging and power delivery technologies for the warehouse industry. CaPow aims to solve operational efficiency problems within warehouses, focusing on the energy issues that hinder productivity. Dr. Peretz shares insights into the inception of CaPow, its core technology, and how it promises to redefine energy solutions for automated systems and vehicles in warehousing. Understanding Perpetual Power: A Game-Changer for Warehousing Perpetual power, as Dr. Peretz explains, is the ability to provide power to vehicles, robots, and machines while they are in motion, contrasting the traditional stationary charging methods. This innovative approach allows for the downsizing or eliminating onboard batteries, paving the way for more efficient and sustainable operations. “So in the tagline perpetual power, what we’re trying to convey is the fact that we’re supporting power for vehicles, robots, machines while they’re on the ground…able to support the delivery of power or energy while in motion,” Dr. Peretz notes, highlighting the flexibility and efficiency it brings to warehouse operations. Why Perpetual Power Matters in Warehousing The introduction of perpetual power significantly impacts the warehousing industry by minimizing downtime associated with charging, thus enhancing operational efficiency. Dr. Peretz elaborates on the substantial time savings and operational improvements, stating, “Now what we’re after is finding the best way to have the robots work 100 percent of the fleet would work 100 percent of the time without compromise…taking the energy issue out of the equation.” The Impact of Perpetual Power on Warehouse Efficiency The adoption of perpetual power technology by CaPow leads to a noticeable reduction in the fleet size required for operations due to decreased downtime. Dr. Peretz shares insights from over 100 discovery talks with customers, revealing a potential efficiency increase of 20-35%, depending on various factors such as cluster size and work-to-charge ratios. “We can quantify the benefit of CaPow anywhere from 20 percent to 35 percent… in some cases even more,” he asserts, emphasizing the direct correlation between CaPow’s technology and improved operational metrics. Sustainability and Environmental Benefits of Perpetual Power CaPow’s technology not only boosts efficiency but also offers significant environmental benefits by reducing reliance on lithium-ion batteries, known for their sustainability challenges. Dr. Peretz discusses a research project estimating a reduction of 55.0 megatons of CO2 equivalent by 2027 due to CaPow’s interventions. “We end up that in 2027 we would save 55.0 megatons of CO2 equivalent…by 2050 we will be way beyond one gigaton,” he explains, underscoring CaPow’s commitment to environmental sustainability. Key Takeaways CaPow’s perpetual power technology enables continuous energy delivery to warehouse robots and vehicles, eliminating the need for stationary charging. Adopting this technology can lead to significant operational efficiency improvements, with potential savings of 20-35% in fleet operational costs. Beyond operational benefits, CaPow’s solution contributes to environmental sustainability by reducing the dependency on lithium-ion batteries and minimizing CO2 emissions. The New Warehouse Podcast Episode 470: Perpetual Power in Warehousing With CaPow
Kardex launches fastest order fulfillment per sq ft with FulFillX powering AutoStore at MODEX 2024
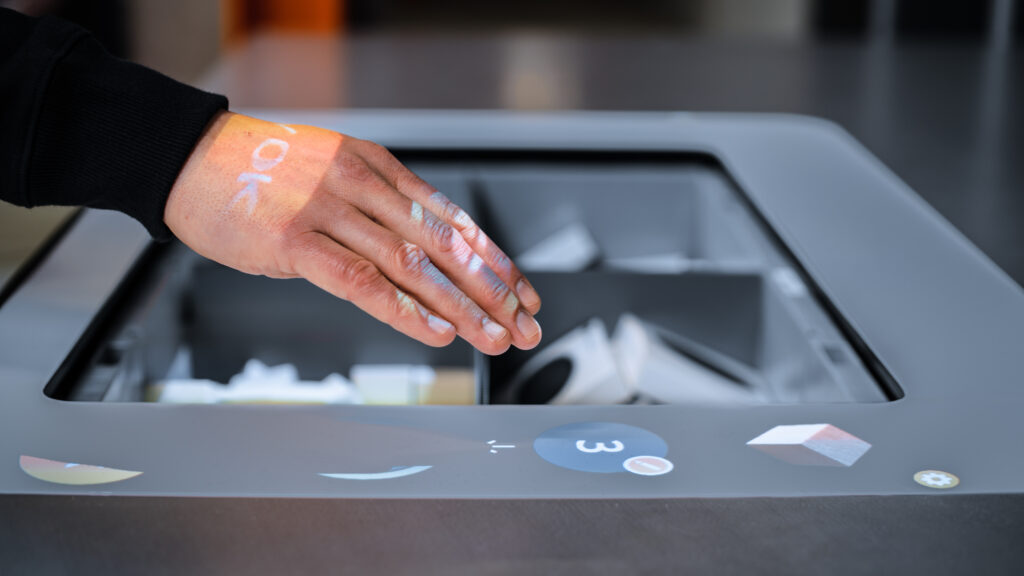
Kardex appeared at MODEX 2024 where it unveiled its FulfillX solution, specially designed by expert automation engineers to maximize the capabilities of AutoStore robotic cube storage systems and deliver the fastest order fulfillment solution per square foot on the market. The latest development in automated storage and retrieval systems (ASRS), AutoStore powered by Kardex allows new systems to ramp up faster and takes the unexpected surprises out of go-live, with systems capable of meeting or exceeding business cases in as little as 6 months. Kardex teamed up with cube storage pioneer AutoStore to launch FulfillX, demonstrating how the innovative warehouse execution system (WES) can maximize the potential of automation and robotics. Bringing together the right automation with the right global AutoStore partner, the flexible FulfillX WES is tailored to optimize picking and packing, maximizing the capabilities of AutoStore to complete orders for fulfillment while also streamlining putaway and other inventory processes. With Kardex FulfillX, users get a real-time overview of their whole operation, viewing and managing work in a simple window, receiving downtime estimates, and rapidly deploying enhancements, supported by Kardex’s dedicated AutoStore support team. Cutter & Buck harnesses the power of AutoStore with FulfillX With retail customers becoming more demanding when it comes to delivery times and efficient order fulfillment, conventional solutions are falling behind. Kardex FulfillX for AutoStore can ramp up to full capacity in as little as 6 months. Iconic US clothing retailer Cutter & Buck was able to reinvent its omnichannel business by harnessing the capabilities of AutoStore powered by Kardex’s precise FulfillX WES. The company needed a system to help it handle rising online and bricks-and-mortar sales, and growing inventory levels. The company opted to install an AutoStore system with Kardex FulfillX at its site in Renton, WA. The speed and density of the AutoStore robotic cube solution and the FulfillX-focused ‘pick to pack’ solution were ideal for Cutter & Buck’s existing fulfillment center near Seattle. Combined with Cutter & Buck’s commitment to leverage automation to address business challenges and its forward-looking approach, the project successfully optimized inventory and order fulfillment processes to deliver streamlined results. Kardex at Modex 2024 Visitors to the Kardex booth (B6410) at MODEX 2024 were able to see how Kardex combines its software know-how with the capabilities of AutoStore cube storage solutions to create user-friendly, highly configurable and focused ASRS solutions. In addition to new developments in warehouse software, visitors experienced live demonstrations of Kardex’s Intuitive Pick Assistant. With a user-friendly picking display, the innovative warehouse solution responds to movements and projects relevant picking information directly onto the surface of the access opening. It is compatible with both Kardex Remstar and AutoStore ports to facilitate accurate, ergonomic picking. Using digital tools and augmented reality, Kardex brought to life its full portfolio of solutions, including vertical lift modules, vertical carousel modules, vertical buffer modules, and AutoStore systems. Mitch Hayes, President of Kardex Solutions AutoStore, comments: “It was great to be able to demonstrate the capabilities of our portfolio of automation solutions at MODEX 2024, including Kardex FulFillX for AutoStore, our Intuitive Pick Assistant, and our wide range of modules, software packages and concepts. At Kardex, we assess each customer and understand their needs to develop a tailored solution designed to transform their warehouse operations. “MODEX 2024 was also the ideal opportunity to showcase the real-world success leading apparel company Cutter & Buck has had in North America with FulFillX. FulFillX has been designed to enhance the power of AutoStore, helping companies meet and exceed their business cases quickly by providing exceptional results within months. The modern microservices backend and simple window have been developed by our team of experienced automation engineers with extensive experience of AutoStore and complementary technologies.” Commenting on the capabilities of FulFillX, AutoStore Partner Sales Manager, Matt Savoie, adds, “We are delighted to work in partnership with Kardex on its innovative FulfillX warehouse execution system. AutoStore solutions are built for the future and Kardex has successfully pushed the boundaries of what cube storage can achieve to deliver the fastest order fulfillment system per square foot on the market.”
New SolarShield™ HMI clear cover excellent visibility when closed and locked
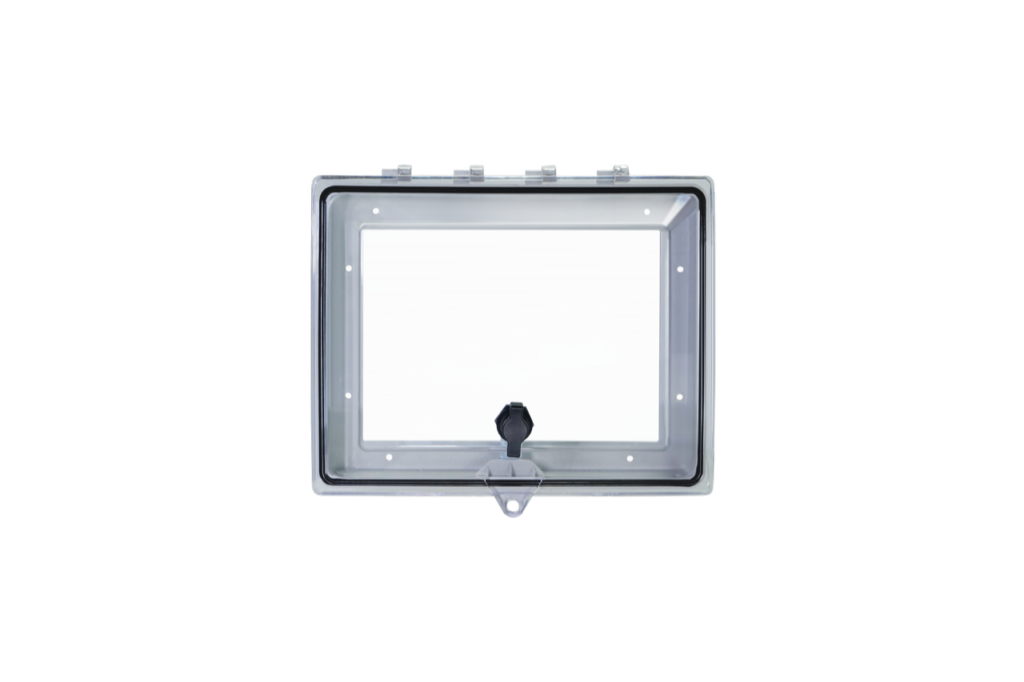
Stahlin® Enclosures, manufacturers of high-performing non-metallic electrical and industrial enclosures, has introduced Stahlin SolarShield™ HMI Covers, providing the ultimate HMI screen protection in the harshest of environments. Now, Stahlin is adding the option of a clear cover configuration that allows for excellent visibility of the HMI screen while the cover is closed. “Our new SolarShield HMI Clear Cover brings the convenience and efficiency of hands-free viewing,” says Craig Mitchell, President of Stahlin Enclosures. “No longer do you need to unlock and open a cover to take readings from your HMI. At the same time, this configuration, as with our patented opaque cover, provides rugged protection for HMI devices against environmental conditions.” The new Stahlin SolarShield Opaque and Clear HMI Covers offer the most innovative, durable, non-metallic HMI protection solution for use with all enclosure material types. The opaque covers are ideal for protecting HMI Screens from UV and harsh environmental conditions and are the industry’s only non-metallic HMI covers with side shields. Stahlin SolarShield HMI Clear and Opaque Covers fit standard 8” and smaller HMI screens and maintain NEMA 4X rating of the enclosure when paired with a NEMA 4X HMI device. These universal covers can be used with either non-metallic or metallic enclosures. Stahlin SolarShield HMI Clear and Opaque Covers perform reliably in demanding applications in non-hazardous industrial and commercial markets including industries such as oil and gas, equipment manufacturing, industrial machines, water/wastewater, marine, and food and beverage. Extremely tough and durable, Stahlin SolarShield HMI Covers can be used in both outdoor and indoor applications. They provide superior protection of Human Interface (HMI) screens from the sun*, dust, water (rain, sleet, snow), sand, flames, oils, chemicals, grease, dirt, foreign objects, and other environmental conditions that cause corrosion and damage. Among the many performance benefits of Stahlin SolarShield Clear and Opaque HMI Covers: Simple and functional: they are easy to use. A hinged design includes supporting inner doors for hands-free use and better visibility of the HMI screen in the sun*. Superior Protection: Maintains NEMA 4 and 4X rating when paired with a NEMA 4 or 4X HMI device. Stahlin SolarShield HMI Covers protect HMI screens and electrical equipment from corrosion and damage due to UV*, oils, dirt, and sand and greatly reduce equipment replacement cost. Strength: Impact resistant but light-weight polycarbonate cover and base construction with UV inhibitors provide long dependable life in harsh conditions. Reliable sealing featuring a robotically applied foam-in-place seamless polyurethane gasket. Stahlin SolarShield HMI Covers come with stainless steel hardware kit included and are padlock-able for increased security. Installation is simple and easy with the use of common tools. Stahlin SolarShield HMI Covers maintain UL’s best rating: an “f1” per UL 746C (resin has passed tests for UV exposure and water immersion). They also conform to the following standards: cURus Listed, UL50e, UL508A, Type 1, 3R, 4, 4X, 12. They provide an Operating Temperature Rating of -40°F to +248°F (-40°C to +120°C) and are Outdoor UV Exposure (UL 746C) (f1) Rated. Stahlin® Enclosures offers the most extensive selection of non-metallic enclosures available for meeting the needs of diverse industries, delivering time- and labor-saving solutions, non-stop innovation, and superior product performance in interior and exterior applications. *Clear version does not contain inner doors, or offer additional protection from UV.
Miner Limited acquires Dependable Dock & Door
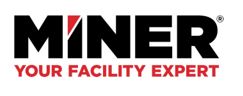
Acquisition Expands Miner’s Service Presence Across Central North Carolina Miner Ltd., the dock and door division of OnPoint Group, has announced the acquisition of Dependable Dock and Door, Central North Carolina’s leading high-speed door and loading dock specialists. Since 2003, Dependable Dock and Door has provided exceptional service and support to an impressive list of blue-chip customers throughout Central North Carolina, including Winston-Salem and Greensboro. Adding Dependable Dock and Door to Miner’s nationwide network of professionals further supports the company’s mission to be North America’s industry-leading facility expert in docks and doors. “This further expansion in the North Carolina and greater Southeast region reflects our commitment to building a nationwide service network to best serve customers from coast to coast. We’ve been thoroughly impressed with the team at Dependable Dock and Door and their reputation for quickly delivering exceptional service to their customers, and we are excited to welcome them to the Miner team,” said Miner President, Dave Wright. Following an extensive tenure as a technician and installer in commercial and residential sectors, Mark Harper started Dependable Dock and Door 21 years ago. He is a dock and door industry veteran and board member of the Institute of Door Dealer Education and Accreditation. Miner looks forward to implementing Mark’s expertise, further strengthening our capabilities in the Southeast United States. “Miner shares our commitment to providing exceptional service to our North Carolina neighbors, and we’re excited to take this opportunity to become part of their team,” said Mark Harper, owner of Dependable Dock and Door. “We’ve spent many years building our reputation and trust with customers as experts in creating systems that operate efficiently and safely year-round, and we’re grateful to expand our footprint further as we join the nationwide leader in our field.” The Dependable Dock and Door team has experienced impressive growth, credited in large part to their unwavering commitment to outstanding sales and service. They are the preferred dealer for Door Engineering and are the top choice in their region for the sale, installation, and service of commercial doors and dock equipment. Their service mindset and sense of urgency align with Miner’s mission to keep customers’ supply chains safe and operational.
RAVAS unveils cutting-edge mobile weighing solutions at LogiMAT
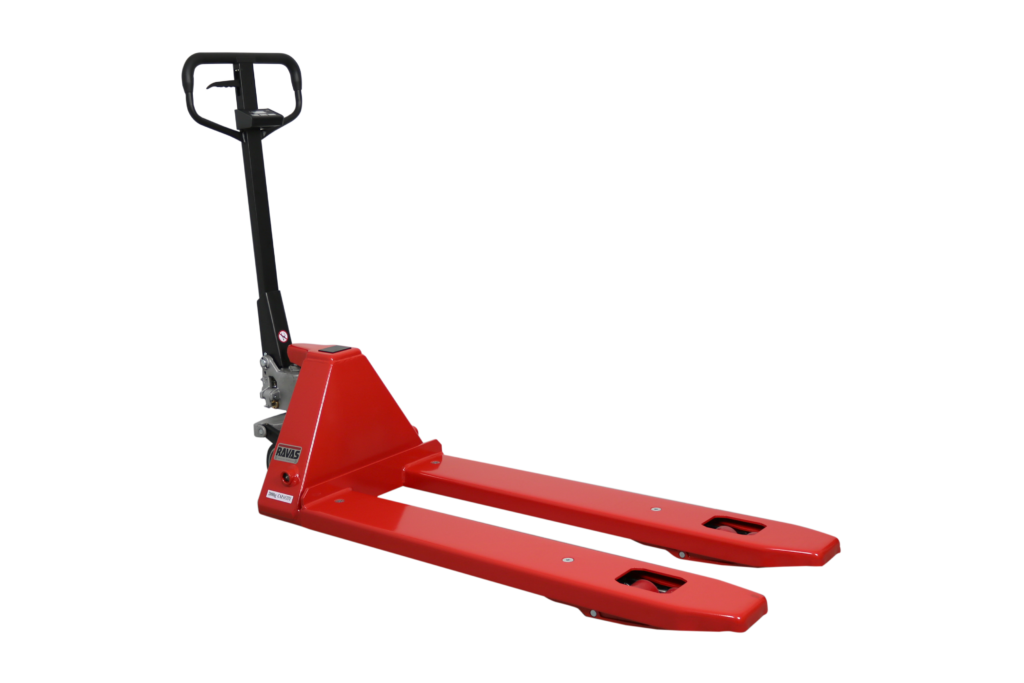
RAVAS invites you to visit our booth at LogiMAT 2024 in Stuttgart. Located in Hall 10, Booth 10F76, they will showcase via a personal tour our pioneering weighing technologies and recently awarded products. The new, ergonomic RAVAS iPT Essential One of the highlights at the booth is the introduction of the brand-new RAVAS iPT Essential. This advanced hand pallet truck, equipped with the award winning RedBox technology, represents a new generation in mobile weighing and is designed with ease of use, reliability, ergonomics, uptime and innovation in mind, allowing end-users to benefit from an advanced mobile weighing solution that optimizes their logistics processes and enhances efficiency. The patented innovative display on the handle of the RAVAS iPT Essential provides graphic information on essential parameters, including gravity adjustment, overload warnings, truck tilt, and load cell malfunctions. Discover RAVAS’ Weigh in Motion technology Additionally, the RAVAS iCP-WiM 2500 with the new Weigh in Motion technology is showcased at the booth, which is currently nominated for the esteemed International Forklift Truck of the Year (IFOY) Award. The Weigh in Motion technology on an intelligent carriage plate (iCP) ensures accurate and reliable weight determination while a forklift is moving. This results in significant time savings, and thus cost savings, as the driver can weigh without stopping. It also prevents unnecessary additional transport movements and manual activities, contributing to higher efficiency, lower chances of accidents, better sustainability, and increased employee satisfaction compared to traditional weighing methods. Moreover, the calibrated value provided by the Weigh in Motion technology can be used for direct billing. The seamless integration of Weigh in Motion technology with TMS, WMS, or ERP systems enables real-time weight control, optimization of loads, and prevention of over- or under-loading of trucks, ensuring streamlined operations and maximum productivity. Forklift scales with Weigh in Motion technology are particularly suitable for situations where large amounts of palletized goods need to be moved within a limited time. Ideal for logistics, storage, reweighing, and LTL shipments. Work smarter, not harder Another innovation in booth #10F76 is the new and improved RAVAS Ergo-Truck 2. A weighing electric pallet truck, capable of moving, weighing, and lifting loads up to 1,500 kg. The latest edition boasts a larger and improved battery along with a more powerful and stable electric scale truck. It seamlessly integrates RAVAS’ efficient weighing scales, a lithium-ion battery, and Bluetooth technology. The Ergo-Truck 2 is the ultimate solution for warehouses, outperforming hand pallet trucks and floor scales. Bert de Greeff, Global Manager Marketing, Communication & Product Management of RAVAS, states, “We are delighted to present our latest innovations at LogiMAT. Our focus on advanced weighing technologies enables businesses to improve their logistics processes, increase efficiency, and reduce costs. The recognition received by the RAVAS iCP with Weigh in Motion in Poland is a testament to the impact our products have on the industry. LogiMAT visitors are invited to visit our booth, where the expert team is available to answer questions, provide demonstrations, and thoroughly explain the benefits of RAVAS products.”
Trade rises at Port of Long Beach in February
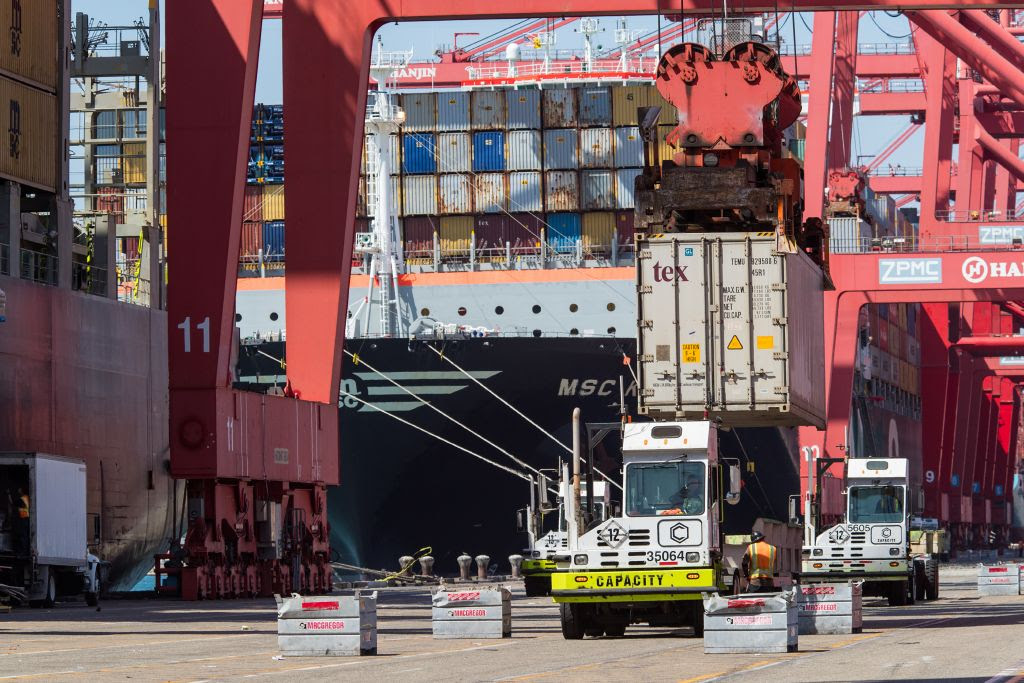
Increase boosted by growing consumer confidence, market share Cooling inflation, rising consumer confidence and an ongoing effort to recapture market share boosted cargo shipments moving through the Port of Long Beach in February. Dockworkers and terminal operators moved 674,723 twenty-foot equivalent units (TEUs) last month, up 24.1% from February 2023. Imports were up 29.4% to 329,850 TEUs and exports declined 21.1% to 87,474 TEUs. Empty containers moving through the Port increased 44.8% to 257,400 TEUs. “Our top-notch customer service and ongoing efforts to attract business back to the West Coast are paying off,” said Port of Long Beach CEO Mario Cordero. “We continue to invest in infrastructure projects that will keep us competitive and sustainable for decades to come.” “Our highly skilled workforce has helped us achieve year-over-year increases in cargo for the last six months,” said Long Beach Harbor Commission President Bobby Olvera Jr. “Customers are taking notice that our infrastructure projects and environmental programs make us the Port of Choice.” The Port has moved 1,348,738 TEUs during the first two months of 2024, a 20.7% increase from the same period in 2023.
Toyota Material Handling North America will establish an advanced energy storage solutions research and development facility
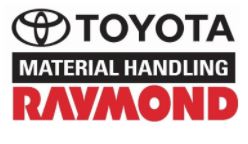
Toyota Material Handling North America (TMHNA), comprised of two main companies, Toyota Material Handling and The Raymond Corporation, will establish an advanced energy storage solutions development, prototyping, and test center in Henrietta, New York. The forward-thinking research and development center, located at 1565 Jefferson Road, will see TMHNA collaborate with Rochester area energy storage resources to further support its own and Toyota Industries’ advanced energy solutions technology efforts, including lithium-ion batteries and fuel cells. As a result, TMHNA has committed to creating up to 40 new jobs. The company expects to begin preparational activities at the site immediately and be operational at the testing center in the spring. Currently, TMHNA employs 2,560 workers statewide. Empire State Development President, CEO & Commissioner Hope Knight said, “Governor Hochul and ESD remain laser-focused on expanding New York State’s green economy by supporting the creation of 21st century research and development and manufacturing jobs. Toyota Material Handling North America’s continued commitment to driving alternative energy applications for the lift truck industry is truly commendable, and we are thrilled that they are moving full speed ahead with all the opportunities that the state and Finger Lakes region have to offer.” TMHNA is a trusted source of quality and reliable products and is committed to being a total material handling solutions provider from forklifts to energy solutions to automation technology. Toyota Material Handling and The Raymond Corporation have a combined 150 years in the industry, providing total solutions, including the latest research and advancements in alternative energy and forklift battery technology, being the first U.S. manufacturer to establish UL certification for an integrated lithium-ion battery and forklift solution. President and CEO of Toyota Material Handling North America and Senior Executive Officer at Toyota Industries Group Brett Wood said, “We look forward to working alongside ESD to establish an energy storage and fuel cell development and testing center in Henrietta, New York. We are honored to contribute to the growth of this community while advancing innovation in sustainable technology. This initiative signifies our commitment to excellence and underscores our dedication to environmental stewardship. Through this venture, we aim to create new jobs, empower individuals and drive progress toward a better and brighter future.” ESD is assisting the company with the project by providing up to $1.5 million through the performance-based Excelsior Jobs Tax Credit program. County of Monroe Industrial Development Agency and Greater Rochester Enterprise also provided support for the venture. The total project cost has been placed at a little more than $2 million. The company had considered locating its new, state-of-the-art R & D facility elsewhere, but selected the Finger Lakes region due to its world-renowned reputation for available top-notch talent and its innovative technology base. State Senator Jeremy Cooney, said, “With Toyota Material Handling North America’s new facility, cutting edge energy innovations will be happening in Henrietta. Our region’s workforce talent continues to attract businesses to Monroe County, and I am looking forward to seeing the impact this project will have for our workers and our community’s continued economic growth.” State Assembly member Harry Bronson, said, “Rochester’s connection to the auto industry runs deep and Toyota Material Handling North America is continuing this tradition in our region and connecting to our new status as a green energy leader and tech hub. This investment is critical to expanding our workforce in the advanced manufacturing and technology sectors, and ensuring good jobs are made available to hardworking people throughout our area. Thank you ESD and Governor Hochul for your work to bring this new industry to Henrietta.” Monroe County Executive Adam Bello, said, “Toyota Material Handling North America’s decision to establish an advanced energy storage solutions research and development facility in the Town of Henrietta is a pioneering leap into the future of our green economy. I applaud TMHNA for their vision and leadership and for recognizing Monroe County’s strength as a hub for high-tech innovation. We’re grateful to Empire State Development and Gov. Kathy Hochul for their commitment to our economy, job creation, and advancing sustainability in our region.” Henrietta Town Supervisor Stephen Schultz, said, “The Town of Henrietta is excited that Toyota will have a presence in town working on innovative technologies regarding sustainable energy efforts. Henrietta has made a significant push for sustainable energy, including upgrading all of its streetlights to energy-efficient LED lamps, a project that is currently underway. Henrietta also is home to RIT and its Battery Prototyping Center, which also works in close collaboration with Empire State Development. Between Toyota, RIT, and energy research companies, Henrietta and Monroe County are becoming hubs for leading the way to a cleaner energy future.” Greater Rochester Chamber of Commerce President and CEO and Finger Lakes Regional Economic Development Council Co-Chair Bob Duffy, said, “As a storied company with roots in Upstate New York, Toyota Material Handling North America’s commitment to growth in Greater Rochester underscores the vitality of our region, including an exceptional talent pool and innovative technology ecosystem. Congratulations to president and CEO Brett Wood and his team, and we look forward to collaborating with Toyota Material Handling and The Raymond Corporation to unlock even more opportunities for growth.” Matt Hurlbutt, President and CEO, Greater Rochester Enterprise, said, “As a leader in the energy innovation sector, the Greater Rochester, NY region is the perfect location for Toyota Material Handling North America to establish an energy storage and fuel cell development center. GRE helped connect TMHNA leaders to economic development partners and the battery and energy storage expertise and integrated ecosystem available in the Greater Rochester, NY region to support the company’s growth plans.”
Nucor Warehouse Systems begins rack supported AS/RS cold storage project
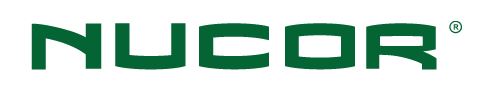
Nucor Warehouse Systems has been selected to provide a structural rack for a hundred-foot-tall, rack-supported building using an advanced AS/RS for a cold storage warehouse that houses dairy products on the East Coast. This new project is part of the company’s strategy of increasing automation projects and leveraging its internal expertise for rack-supported buildings where temperature, precision, and engineering are paramount. What makes this project unique is its need to connect to an existing structure that is also a cold-storage environment. Due to the height of the building, the flexibility of the new system is key to allow for both structures to work independently and ensure the safety of the structure and its temperature-sensitive products during usage. With more than 7,600 pallet positions planned for this warehouse, the AS/RS will also include two, three pallet-deep cranes as well as pick tunnels to allow for human intervention for fast picking and loading onto trucks as needed. “Nucor Warehouse Systems made a commitment last year to continue to invest in projects that would leverage our expertise of planning, engineering, and executing on rack-supported buildings,” said Daniel Aguirre, national sales manager at Nucor Warehouse Systems. “As we go into production on this large-scale project, we are working with the customer to ensure all challenges are met with confidence and a proactive approach.” The project goes into production this spring and the system is expected to be delivered onsite as the building begins construction in the summer 2024
Bobcat recognizes dealers for superior performance
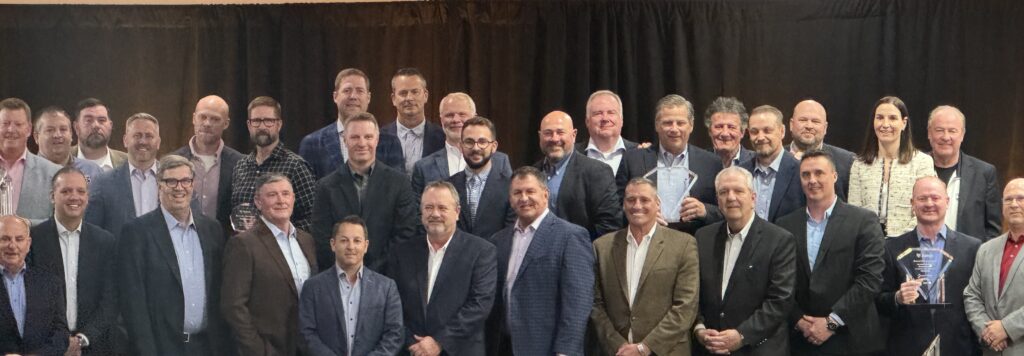
Awards given to top-performing material handling equipment dealers Bobcat Company has recognized 21 material handling dealers for superior performance within their respective regions. The dealers were recognized based on sales, volume and other dealer engagement metrics. “We are pleased to recognize such a deserving group of dealerships for their efforts and achievements,” said Jarrod Steck, Bobcat vice president of material handling products. “While forklifts are a new product offering within the Bobcat portfolio, these dealerships bring years of expertise and experience within the material handling industry, and we are thrilled to award these top performers and valued dealer partners.” Bobcat recognized these dealerships at a reception held during MODEX 2024. Its top recognition for “Dealer of the Year” went to ASCO Equipment. Additional awards were also presented including: Summit awards as the premiere category of recognition, followed by Diamond Awards, and finally the Platinum Awards recognition. Summit Awards: ASCO Equipment, Morrison Industrial Equipment, Connell Material Handling, Alliance Material Handling Diamond Awards: Alliance Material Handling, ASCO Equipment, Bacon Universal Co., C & B Material Handling – Sioux Falls, C & B Material Handling – St. Albans, Connell Material Handling, Cromer South, Florida Forklift, Forklifts Group, Mid Columbia Forklift, Morrison Industrial Equipment Co., Summit Handling Systems, Valley Industrial Trucks, W.D. Mathews Machinery Platinum Awards: Anderson Forklift; Bobcat of Casper; Hugg & Hall Equipment; Atlantic Forklift Services; Delta Materials Handling; Lift Truck Center, Inc.; Dedicated Material Handling Solutions