2024 MHEDA Convention & Exhibitor Showcase
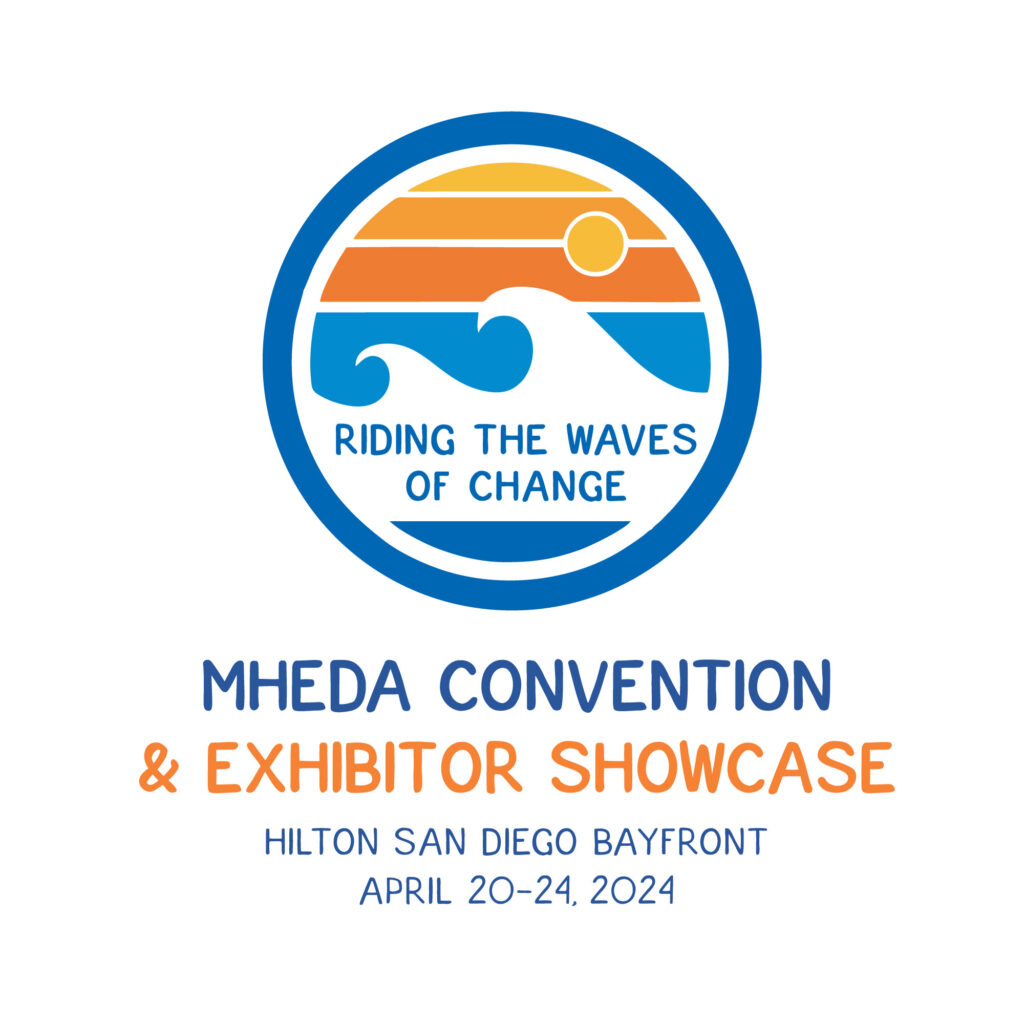
According to Albert Einstein, “The measure of intelligence is the ability to change.” Change is all around us, what are you doing to prepare your team, your business and yourself? If you are looking to stay connected with hundreds of your material-handling peers and in tune with the latest industry trends, then be sure to join MHEDA April 20-24 for the 2024 Annual Convention in San Diego, California. This year’s theme, “Riding the Waves of Change” is designed to help you navigate the often-difficult waves of endless changes in our world and in the material handling business community. Learn and connect with experts on topics critical to running your business: economic uncertainty, emerging technologies, shifting generations, artificial intelligence, leading teams, keeping your business cyber-safe, and more. MHEDA’s Convention is also a great way to learn about the latest products and services in our industry. Enjoy meeting with nearly 90 different companies at the Exhibitor Showcase, which will take place on Monday, April 22. The convention destination is ideally located at the beautiful Hilton San Diego Bayfront, rising above the stunning San Diego Bay and steps from the Gaslamp Quarter and Petco Park. Discover San Diego’s most exciting attractions within steps of the hotel – including fabulous shopping, dining, and nightlife. Look at all we have planned for you and then register today. We can’t wait to see you this spring! Memorable Main Stage Presentations Challenge of Change NFL Legend Joe Theismann knows how to deal with the “Challenge of Change.” On November 18, 1985, he was on top of his game–a two-time Pro Bowl player and the most productive quarterback in the history of the Washington Redskins. Later that evening, he found himself in a hospital bed with a compound fracture to his leg, shattering both his career and his boyhood dream. In this stirring presentation, Joe will help you tackle change by keeping a positive outlook and committing to a vision that guides you to the top. The Power of Choice In a workplace filled with endless possibilities, the choices we make define our journey. In this breathtaking journey, international speaker and author Sylvie di Giusto unveils the profound impact of intention on personal, professional, and organizational growth. Drawing from her expertise in behavioral psychology and her more than twenty-year-long corporate career, Sylvie reveals how the choices we make shape our interactions, relationships, and ultimately, the outcome of every encounter. Embrace It: Generative AI and Your Future Ready to feel excited about your new AI-powered future? Join Sam Richter, CEO of SBR Worldwide, for a humorous, high-content, and high-learning program. Artificial intelligence (AI) and machine learning are nothing new. However, with the introduction of Generative AI programs like ChatGPT, Claude, Llama, and other large language models, for the first time in history, everyone has equal access to the knowledge and advanced technology that will transform business, communications, jobs, and everyday lives. The Economy: Finishing 2024 and Looking Beyond The macroeconomic landscape is uneven, with some markets performing well and others struggling. ITR Economist Brian Beaulieu will look at the economic drivers for the rest of 2024 to clear away the noise and provide a clearer view of what lies ahead. We will examine the leading indicator signals to determine what they are telling us about 2025. Ten Business Sessions to Choose From Selling Through Tough Times Whether it’s a recession, industry disruption or downturn, a tough competitor, or an extended sales slump, every seller faces tough times. This practical message by sales trainer and author Paul Reilly is your go-to guide to growing your profits and mental resilience in any downturn. Recruiting, Retaining, and Developing Great Employees People hate change, but employees will leave a company if they are unhappy. Chris Czarnik, an award-winning speaker, and author will help you understand the demographic shift that has caused the talent shortage and examine the cost of an open position. 2024 Material Handling Business Trends Roundtable Discussions Discuss the 2024 Trends with fellow attendees during the Roundtable Discussions. Great way to connect, network and share your own ideas and experiences. Automation Solutions: A Beginner’s Guide This session provides insights from MHEDA Members on this emerging market. Learn about the capabilities, process, and resources required to integrate automated solutions. Presented by MHEDA Members Darin Boik, President, Advanced Equipment Company; Jordan Frank, EVP and Co-Founder of Zion Solutions Group; and Mitch Smith, Chief Revenue Officers, Hytrol. Making Higher Profit Permanent During the last two years, MHEDA members have experienced unprecedented levels of profitability. Dr. Al Bates, Principal in the Distribution Performance Project, will help you plan for your financial future and understand findings from the MHEDA’s benchmarking report. Rapid Growth in the Face of Uncertainty With real-world examples and case studies from a diverse range of industries, small business advocate Matthew Pollard explains why changing economic times, new technologies, and ever-growing competition are nothing to fear. For sustained momentum and growth in the face of external factors, businesses need only turn to Matthew’s proven, time-tested principles. Better Together: How To Build a Culture of Belonging Building a culture of belonging is more than top-down leadership and operating on the mindset that it’s someone else’s responsibility. Thought leader and TEDx speaker Princess Sarah Culberson uses her personal experience as an adopted child growing up in a bi-racial family, as well as understanding a whole new culture when she discovered that she was a real-life princess in Sierra Leone. Leading through Change Change is constant and not always fun. With her trademark wisdom, insights and engaging storytelling, speaker, and author AmyK Hutchens shares the psychological mindset of change from initial resistance to intrinsic acceptance all the way through to forward-focused action. You Just “Friended” a Thief: Simple Ways to Protect Your Data, Your Client’s Data, and Ultimately Your Business It’s shocking how vulnerable we all are to Personal Identity Theft and Business Identity Theft – in ways you might not think about. CEO of SBR Worldwide Sam Richter will help you protect your business.
Daubert Cromwell announces leadership changes at Daubert Mexico
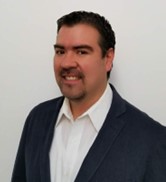
Daubert Cromwell, a provider of anti-corrosion packaging for industry, has named Rodrigo Martinez to succeed retiring Luis Jacome as Daubert Mexico Country Manager. Martinez has been the Mexico Regional Sales Manager for nearly seven years, working closely with Jacome at the subsidiary headquarters in Aguascalientes, Mexico. With this promotion, he takes on additional leadership for technical sales, customer service, marketing, and all operations in Mexico. In addition to recognition as a corrosion prevention expert for metalworking industries, Martinez has a broad background in manufacturing and project engineering. He holds a bachelor’s degree in manufacturing engineering and operation management from Universidad Panamericana in Aguascalientes. He studied SMT Manufacturing at George Brown College in Toronto. He is a certified auditor for ISO9001, ISO 14001, and APQP. During years as a Supplier Quality Engineer for a major OEM, he gained insight into corrosion problems of automotive markets and has since applied that knowledge to help Daubert Mexico customers reduce their costs of corrosion by adopting his recommended solutions. As Daubert Mexico Country Manager, Martinez will work closely with the company’s sales and technical teams in the US, Europe, Brazil, and China to coordinate packaging and process improvements that protect metal surfaces during all stages of production, storage and export
DAC Robotics selects OSARO’s robotic depall to automate receiving thru replenishment
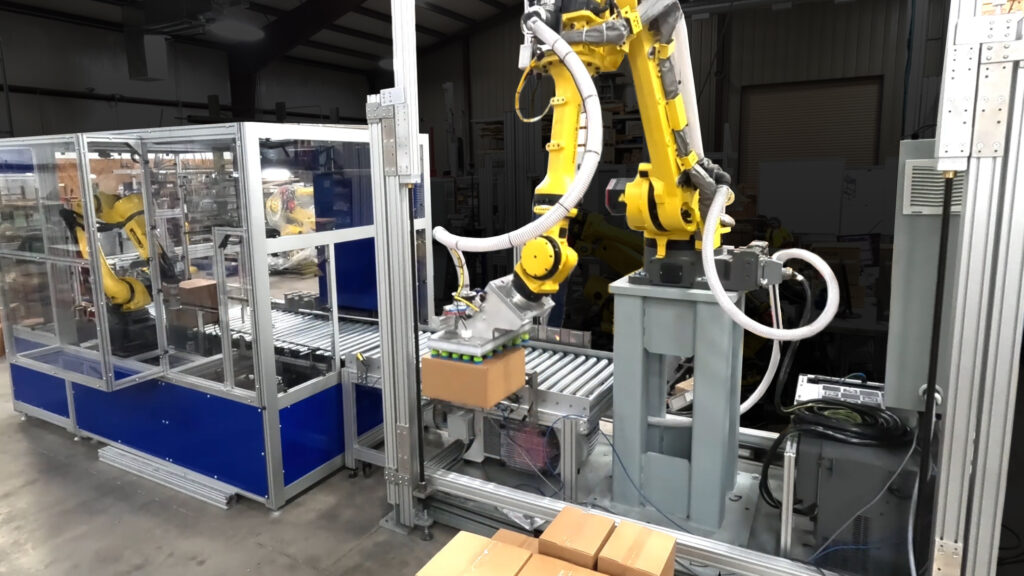
DAC Robotics has selected OSARO’s depall system for inclusion in its new three-step robotics system that handles depalletization, box opening, and decanting. The system uses OSARO’s SightWorks Perception software to run the depall robot, which then hands off boxes to DAC’s latest automatic box-opening ABOT and its decant robot. The system therefore handles everything from pallet to tote — from receiving to replenishment. CONTEXT While many other tasks downstream from the loading dock have been automated, the hazardous manual tasks of unstacking, sorting, scanning, opening, and transferring (decanting) master pack box contents into standard totes are often still performed by humans. To automate the entire process, DAC Robotics needed a high-performance depalletizing system capable of unloading a wide variety of box sizes and shapes from a pallet and then handing off each box to an automated box-opening robot in preparation for decant. The OSARO Robotic Depalletization System is equipped with OSARO SightWorks™ Perception Software, which enables the robot to recognize, select and successfully grasp the varied sizes and materials of unevenly stacked packages commonly found on mixed-case pallets that arrive at a loading dock. The system can depalletize the most technically challenging mixed-case pallets at rates that provide cost-effective automation of replenishment and reverse logistics. “Today’s technology announcement is the culmination of more than three years of development, engineering, and testing to integrate all automated work cells in the receiving and decanting process for warehouse intralogistics automation,” said Mark Ganninger, president of DAC Robotics. “With OSARO’s SightWorks Perception Software, we were able to design and deploy a system that met our exacting specifications.” WHAT WE’RE ANNOUNCING The fully integrated system being demonstrated at MODEX includes: A DAC Robotics mixed-case depalletizing system, powered by OSARO SightWorks™ Perception. The system can rapidly depalletize the most technically challenging mixed-case pallets. A DAC Robotics ABOT (automated box opening technology), which features the most advanced box metrology and dimensional capture to ensure precision opening of the widest range of box sizes and types before decanting. A DAC Robotics Precision Decanting System. DAC offers the widest, most advanced solutions in decant — from fully automated precision handling of the most delicate glassware and foil packs to semi-automated designs that allow for necessary operator re-pack and consolidation functions or additional process work to optimize and utilize the highest percentage of a re-packed tote’s capacity. “In today’s busy e-commerce and fulfillment warehouses, thousands of different SKUs arrive on mixed or homogenous pallet loads every day. The variance and multiplicity of pallet stacks, mixed pallet stacks, box construction, and box conditions can easily exceed millions of possibilities,” said OSARO CEO Derik Pridmore. “OSARO’s robotic depal system is the perfect teammate for DAC’s robotic box opener and decant system because it can maintain a high rate of inbound merchandise, 24×7.” Here’s a video that shows how it all works.
Precision, productivity, and progress: Intech’s inventory transformation journey with Kardex Remstar and ZOLLER
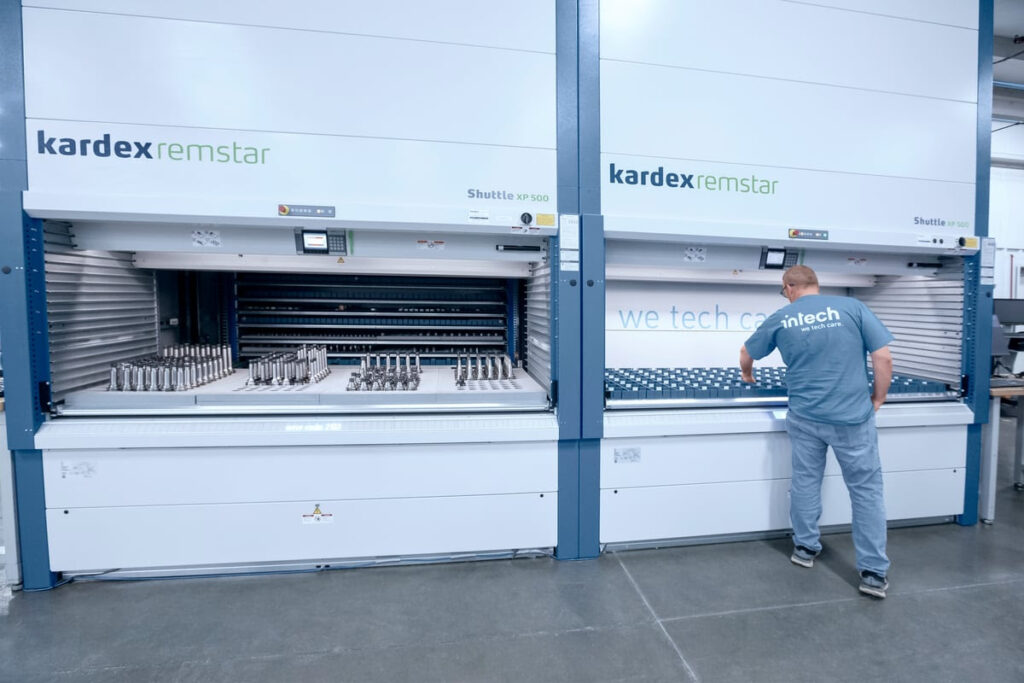
By integrating Kardex Shuttles with ZOLLER TMS Tool Management Solutions Software, Intech Athens has taken a monumental leap in streamlining inventory management processes, positioning them at the forefront of efficiency and precision in their industry. Through their dedication to delivering exceptional services and driving innovation, Intech has grown into a global leader in orthopedic contract manufacturing. One of nine global facilities, the Intech contract manufacturing facility in Athens, Alabama (formerly known as Turner Medical) specializes in the meticulous manufacturing of complex medical device instrumentation. As a distinguished medical device job shop, Intech Athens contracts for the production and manufacturing of medical device instruments essential for orthopedics, from complex hip and knee robotics devices to expandable spinal implants. Working at the intersection of medical science and engineering, Intech Athens plays a critical role in medical device innovation and production. Physicians, entrusted with the care of their patients, collaborate with industry-leading medical device Original Equipment Manufacturers (OEMs) such as Stryker and Medtronic. These medical professionals provide invaluable feedback—whether it’s developing a new surgical technique or a desire for a screw to fasten more swiftly, a tool to be more lightweight, or a design alteration to enhance accessibility during surgical procedures. The OEMs, armed with this feedback, turn to Intech Athens to make it happen. The team at Intech Athens uses their expertise and creativity to meticulously prototype the envisioned instrument for physicians to test on cadavers, ensuring utmost precision and safety. It’s amazing to watch an idea transform: from a prototype birthed within prototype dedicated cells (branded The Prototype Garage®) at Intech Athens, through the initial production stages, to its eventual market launch. The pinnacle of this journey is the patient whose quality of life has improved thanks to an implant or instrument crafted in this very facility—it’s an unparalleled reward. This is where the real essence of Intech’s work shines through, where every effort becomes profoundly meaningful. The Challenges of Rapid Growth To support this endeavor, Intech Athens boasts a 100,000-square-foot facility including a robust production area with over 70 CNC machines as well as engineering, quality assurance, regulatory compliance, and customer service – all supported by just over 220 employees (proudly known as Intechers). Intech’s commitment to innovation and investment in new technologies is paying off – Intech Athens has experienced an extraordinary 150% growth in the past decade. Amidst the rapid growth at Intech Athens, a new challenge became increasingly evident: the intricacies of inventory management. As the business expanded and the facility dove further into sophisticated manufacturing, inventory complexities multiplied. Transitioning from manual machining to CNC (Computer Numerical Control) machine manufacturing impacted the volume and variety of tools and supplies required. Each piece of CNC machinery had its own ecosystem: the cutting tool, its collar, the holder it sits in, the nut fastening it together and the retention knobs on the holder anchoring it into the machine. Beyond this, there is the work holding – including quick-change fixturing, vices, clamps, and an array of other components. Additionally, to ensure each product meets rigorous standards, very specific and elaborate gauging systems are essential. What appeared as a single manufactured component was, in reality, a culmination of 100+ manufacturing tools, gages, and supplies. Initially, Intech Athens used the traditional approach to manage inventory. Cabinets were grid-organized for less valuable smaller items while standard industrial shelving held larger items like fixtures and vices. Items were cataloged on clipboards and checked out manually, and it was expected that staff would conscientiously return them post-use. But as is often the challenge with manual systems, reliance on individual discipline and manual organization proved to be unreliable. Tools weren’t always returned to their designated spots, making it increasingly hard to locate specific items or determine their condition. Regular maintenance became an uphill battle. Recognizing the need for enhanced control, Intech Athens installed a vending machine system for cutting tools. These smart vending cabinets would vend specific tools based on several inputs, streamlining the process to a degree. However, this only addressed a fraction of the inventory. It wasn’t just about having the necessary tools—it was about knowing their exact location, quality, and readiness for use. “We were like any other job shop, we had the necessary items, but often didn’t know their location or condition. We knew we needed to do better,” said Joseph Forsyth, the Director of Advanced Manufacturing at Intech. Despite their growth and successes, Intech Athens found itself grappling with inventory control, a challenge they were determined to overcome. Revolutionizing Inventory Management To get control of their inventory, Intech had planned to leverage the ZOLLER Tool Management System software solution just as the Intech Toulon facility in France had done. But Intech Athens went a step further by integrating the ZOLLER TMS solution with high-density automated storage solution from Kardex Remstar. Stepping into the future of inventory management, they replaced their traditional racking systems and most of the cabinets with two state-of-the-art Vertical Lift Module Kardex Shuttles. Working in harmony with the ZOLLER TMS software, this complete solution not only provided better inventory control but also delivered significant space savings and increased manufacturing productivity. “From cutting tools to collars, vise jaws to sandpaper, and even dead blow hammers, we store them in the Kardex Shuttles. Through the ZOLLER TMS software, we’ve cataloged over 10,000 different part numbers. We now have unwavering clarity on our inventory—knowing precisely what we have and, more crucially, its exact location,” said Forsyth. Inventory Control Increases Speed to Market When it comes to medical device manufacturing, ‘speed to market’ is more than a catchphrase—it’s a determining factor of success. Particularly in prototyping, where swift turnarounds can be the difference between seizing an opportunity and missing out. For Intech Athens the reliability of their inventory control system is critical. “It’s not just about having the necessary items on hand. The real challenge is the speed at which we can access accurate data about the inventory. It’s about answering questions like, ‘Do we have the required tool for
Emerson upgrades LED Industrial Luminaires to support drive to lower energy requirements and minimize light pollution
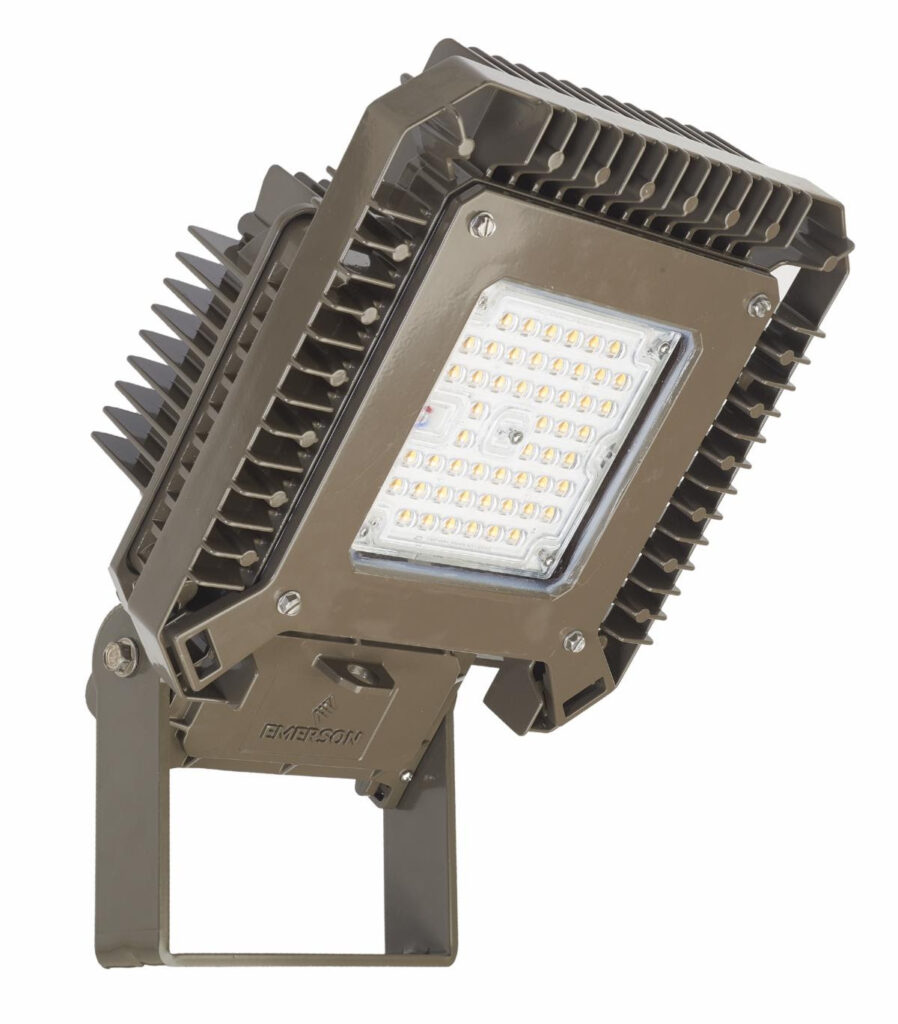
Appleton Baymaster and Areamaster now equipped with new energy-saving dimming option, warm color temperatures Emerson is upgrading two flagships of its Appleton™ LED lighting portfolio with new technology that underscores the company’s commitment to environmental sustainability. For the first time, Appleton Baymaster™ LED high bay luminaires and Areamaster™ LED floodlights will be equipped with energy-saving 0-10Vdc dimming as a standard feature, along with new color temperatures (CCT) that minimize light pollution. In addition, the luminaires now boast a cold start option for ambient temperatures as low as -55° C (-67 F), and a new pre-wired design for easier, less time-consuming installation. Upgrades apply to both the hazardous rated (CID2) and harsh industrial versions of Appleton Areamaster and Baymaster LED luminaires. BENEFITS OF LED DIMMING Adding a two-wire, 0-10Vdc variable dimming input port takes the energy efficiency of Baymaster and Areamaster LED luminaires to a new level. Dimming allows adjustment of the rated lumen output from 100% to 10%, resulting in greater flexibility and reduced costs. By optimizing the brightness of the luminaires in the workplace, plant managers can also supply a more comfortable and productive environment. Besides working as stand-alone dimmable fixtures, up to ten Baymaster or Areamaster luminaires can be daisy-chained to an Appleton Mercmaster Connect LED luminaire to further enhance energy and cost savings. In this configuration, the Mercmaster Connect acts as a “controller” and shares its motion sensing, daylight harvesting, and scheduling capabilities with the daisy-chained group. This enables the group to collectively lower light levels when no workers are present or when light isn’t required, thus eliminating 24/7 operation and maximizing product lifetime. Furthermore, when the Emerson Plantweb™ Insight Connected Lighting Application and WirelessHART network platform are added to this mix, plant operators have an Industrial IoT solution capable of remotely optimizing, monitoring, and analyzing their facility’s lighting performance. REDUCING LIGHT POLLUTION Light pollution is a growing concern in urban areas worldwide, affecting both the environment and human health. To combat this problem, the Areamaster and Baymaster have been upgraded with two warmer color temperatures, Amber (56 CRI) and 1800K (70 CRI) that emit far less blue light that causes sky glow. Warmer temperatures complement the luminaires’ robust optics designed to precisely distribute light only where it is needed, therefore preventing excess light from scattering, especially outdoors. OPERATION DOWN TO -55° C Bitter cold conditions, such as oil exploration sites in western Canada that reach -30° C or lower, are within the new temperature range of Areamaster and Baymaster luminaires. Both are certified instant-on and cold start capable in temperatures as low as -55° C (-67° F), unlike an HID fixture that can take several minutes in cold weather to reach full lumen output. Rugged Areamaster and Baymaster luminaires also eliminate many of the maintenance problems HIDs are prone to experience due to exposure to snow, ice, and freezing winds.
U.S. Cutting Tool Orders totaled $204.5 Million in January 2024 up 9.1% From December 2023
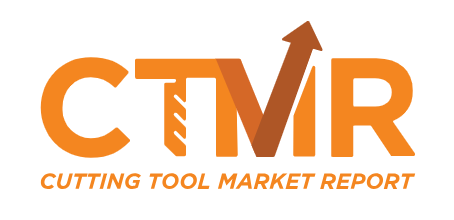
January 2024 U.S. cutting tool consumption totaled $204.5 million, according to USCTI and AMT. This total was up 9.1% from December’s $187.5 million and up 4.1% when compared with the $196.5 million reported for January 2023. January 2024 U.S. cutting tool consumption totaled $204.5 million, according to the U.S. Cutting Tool Institute (USCTI) and AMT – The Association For Manufacturing Technology. This total, as reported by companies participating in the Cutting Tool Market Report collaboration, was up 9.1% from December’s $187.5 million and up 4.1% when compared with the $196.5 million reported for January 2023. “January cutting tool shipments are a good start to 2024 and indicate that the expected decline will not be as severe as some fourth-quarter predictions that were based on the contraction in durable goods spending,” asserted Jack Burley, chairman of AMT’s Cutting Tool Product Group. “Job shops are reporting business activity, and quoting has slowed down some; however, large original equipment manufacturers in automotive, truck, and aerospace are still investing in new production lines. Overall, there is optimism within the industry for continued growth this year.” Tom Haag, president at Kyocera SGS Precision Tool, elaborated further, stating: “January activity started quite slow after the holidays but appeared to recover as the month progressed and carried into February. We are hopeful that the inventory depletions at the close of 2023 are now being replenished to prepare for a solid manufacturing year in 2024. Commercial aerospace has a 10-year backlog to address, and if automotive manufacturing can sort out whether to produce electric vehicles or internal combustion engines, 2024 could prove to be a strong year in metalworking. With 2023 being an exception, we expect the first three months of 2024 to set the tone for the year, barring any geopolitical interruptions.” The Cutting Tool Market Report is jointly compiled by AMT and USCTI, two trade associations representing the development, production, and distribution of cutting tool technology and products. It provides a monthly statement on U.S. manufacturers’ consumption of the primary consumable in the manufacturing process – the cutting tool. Analysis of cutting tool consumption is a leading indicator of both upturns and downturns in U.S. manufacturing activity, as it is a true measure of actual production levels. Historical data for the Cutting Tool Market Report is available dating back to January 2012. This collaboration of AMT and USCTI is the first step in the two associations working together to promote and support U.S.-based manufacturers of cutting tool technology. The graph below includes the 12-month moving average for the durable goods shipments and cutting tool orders. These values are calculated by taking the average of the most recent 12 months and plotting them over time.
ASSP announces sessions for Safety 2024 in Denver
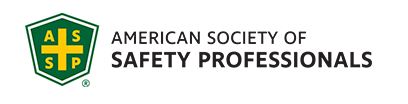
The American Society of Safety Professionals (ASSP) has published the concurrent sessions lined up for its signature workplace safety education event this summer at the Colorado Convention Center in Denver. More than 200 continuing education sessions will be available to occupational safety and health professionals who attend the Safety 2024 Professional Development Conference and Exposition from Aug. 7-9. In addition, ASSP reminds safety professionals who have yet to register that time is short to get the best rate for Safety 2024. Register online to get the discounted early rate through March 21. Safety 2024 is a dynamic learning and networking experience that highlights best practices, industry trends, and the latest product innovations. The continuing education sessions are considered the heart of the conference, providing practical information that safety professionals can immediately put to use at their organizations. The one-hour sessions are presented by safety experts with real-world experience. Topics include risk management, workplace violence, artificial intelligence, safety, and health management systems, infectious disease exposure, heat stress, ergonomic assessments, emergency preparedness, prevention through design, fall protection, and the safety aspects of diversity, equity, and inclusion. Thousands of safety and health professionals from around the world look to ASSP’s annual conference – now in its 63rd year – to advance their careers and take advantage of networking opportunities that can help elevate safety at their companies. Attendees will also be inspired, entertained, and informed by popular general sessions.
TrewSort sliding shoe sorter
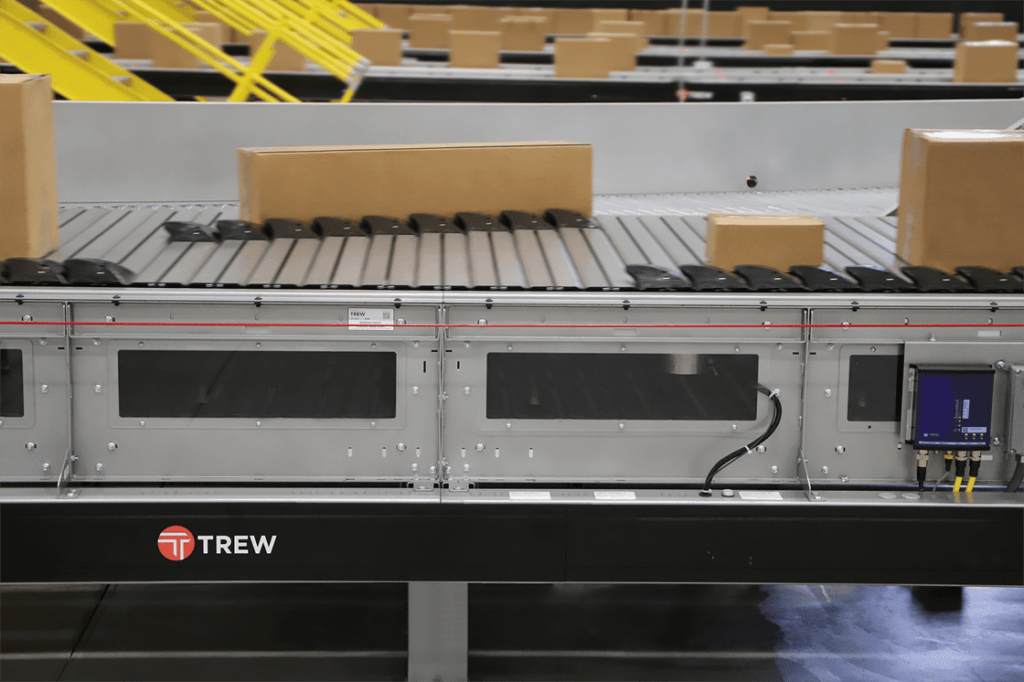
TrewSort sliding shoe sorter provides retail, e-commerce, and warehouse operations with high-capacity reliable throughput with the added benefits of AI-enabled technology Trew, LLC, an automated materials handling solutions provider, has announced the latest in high-throughput, high-accuracy sortation for retail and e-commerce fulfillment operations. The TrewSort™ Sliding Shoe Sorter incorporates “AI inside” high-performance, self-learning actuators with mechanical and control design elements that deliver high-rate, accurate, and reliable line sortation of cartons, parcels, totes, poly bags, and other items. TrewSort delivers industry-leading sortation rates with inventive design elements that allow it to handle a wide variety of items with reliability and accuracy. Features include intelligent high-density product spacing, catch-free transportation surface and divert elements, and the use of high-performance materials that eliminate problems caused by product impact, snag points, and “walls” seen in other designs. “The AI uses machine learning built into the divert actuator allowing the sorter to maintain accuracy by self-identifying issues before they become problems,” said Trew Product Manager, Andrew Herchenbach. “There is deep thinking in every detail of the sorter. It is designed to perform at the highest standards now and flex and grow with customers.” The TrewSort system is manufactured for heavy use in facilities running three shifts per day, with forward-thinking features like nearly infinitely adjustable divert switch locations, modular machine sections, expandable electrical design, and adjustable after-sort lane connections that allow the sorter to fit buildings easily today and expand in the future. “When you need reliable operational throughput and performance, the TrewSort sliding shoe sorter delivers results,” said Herchenbach. “This system offers companies incredible levels of reliability and flexibility to have confidence now and as your business grows.”
Mitsubishi Logisnext Americas launches Logisnext Financial Services through partnership with DLL
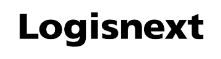
Simplifies acquisition process, provides added flexibility Mitsubishi Logisnext Americas (Logisnext), a manufacturer and provider of material handling, automation, and fleet solutions, has announced the launch of Logisnext Financial Services, providing customers with one single point of contact for equipment purchasing and financing. The new service is offered through Logisnext’s strategic partnership with DLL, a global asset finance company for equipment and technology. Under Logisnext Financial Services, customers will have direct access to proven and reliable lease and purchase options across all Logisnext material handling and warehouse products in the United States, including Mitsubishi forklift trucks, Cat® lift trucks, Jungheinrich®, UniCarriers® Forklifts and Rocla AGVs. Customers will also have added flexibility and control of their business and capital requirements. This approach provides efficient and effective operating costs to meet business goals – all with the latest material handling technology. “DLL has had a longstanding history and close relationship with Logisnext for more than 15 years,” said Mike Kinka, president of Construction, Transportation and Industrial at DLL. “This, in combination with the experience of DLL in the materials handling market, will help bring Logisnext’s equipment financing solutions to the next level.” This collaboration further expands on Logisnext’s dedication to providing customers with a complete portfolio of solutions – from site-specific consultation and fleet management to financing and comprehensive product support. “The launch of Logisnext Financial Services, and our partnership with DLL, allows us to better serve our customers,” said Jerry Sytsma, executive vice president of sales and Aftermarket Services at Logisnext. “Through Logisnext Financial Services, customers will have one point of contact for managing their acquisition needs – from equipment purchasing to financing. Our goal is to help our customers succeed, and by offering a wide range of financing options, we make it easy for customers to get the right equipment when they need it most.”
Charles Thompson has been named a winner in the Supply & Demand Chain Executive 2024 Pros to Know award.
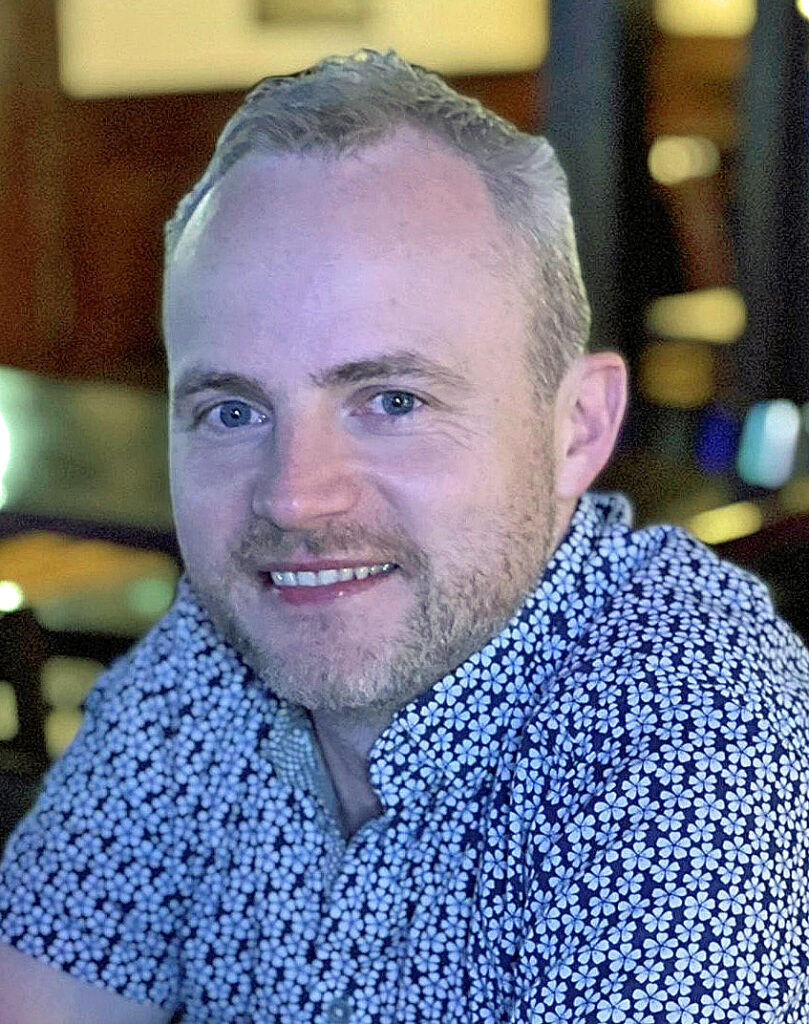
This recognition is in the ‘Rising Stars’ category and makes Charles, age 38 from Denver, Colorado, one of only 25 up-and-coming industry achievers listed globally. The Pros to Know award recognizes outstanding executives whose accomplishments offer a roadmap for other leaders looking to leverage the supply chain for competitive advantage. Charles is a highly successful project manager thanks to both his strong technical knowledge and direct experience. Coming from a warehouse background, his industry knowledge is second to none and his primary focus has long been on WMS implementations, from an end-user and service-provider perspective. Consequently, he is adept in recognizing and defining key industry practices for different warehouse environments, which is key in providing an elevated level of service and solution delivery to customers. Smitha Raphael, Chief Product & Delivery Officer of Synergy Logistics, said: “This accolade is very much deserved. Charles is a key player in Synergy’s new agile implementation solutions, which resolve the need for rapid deployment in larger, more complex enterprise integrations. He skillfully adapts and tailors his knowledge and experience on each project he is involved with, to not only solve customer challenges but to also secure improvements and margin gains across their operations.” As the continued growth of automation needs increases the demand for adaptability in the supply chain and customer operations, Charles is continually improving his skillset with additional exposure to change management methodologies. In the last 12 months, Charles has also been the lead project manager in Synergy’s maiden implementation of SnapControl, a game-changing and award-winning multi-agent orchestration (MAO) solution that orchestrates all automation devices and robotic systems within warehouses from one centralized and convenient platform. The project, with a rapidly expanding US-based e-tailer, resulted in a sixfold increase in productivity thanks to SnapControl determining the quality of manual versus automated pick tasks and identifying the manual picks required in areas serviced by AMRs. This has translated into labor savings of over half a million dollars and the company now saves over $40,000 per week, with an impressive investment payback period of just 23 weeks.
Episode 469: Insights on warehouse software solutions from Embassy Data Logistics’ CEO Lee Rector
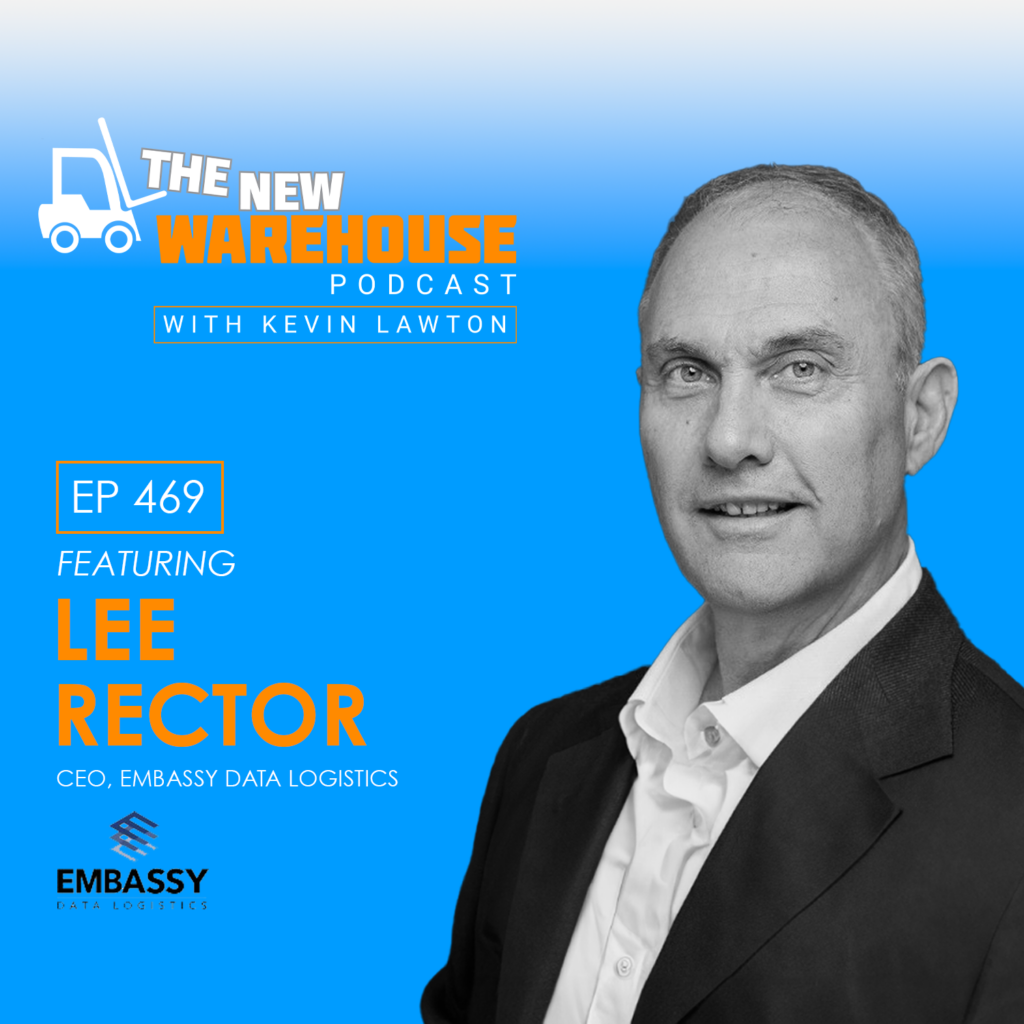
In this episode of The New Warehouse Podcast, Lee Rector, CEO of Embassy Data Logistics, joins Kevin for an informative episode about warehouse software solutions. With a rich background in warehousing and supply chain technology, Rector shares his journey from founding his company to addressing the challenges of data utilization in warehouses. This episode dives into the innovative solutions offered by Embassy Data Logistics, the common hurdles in the industry, and valuable industry insights drawn from Rector’s book, “Warehousing 101.” Empowering Warehouses with Data-Driven Solutions Embassy Data Logistics stands out in the warehouse space by offering low-cost, easily implementable technology that transcends industry boundaries. Rector’s goal with Emassy was to build a technology that could be implemented anywhere that isn’t bound to a specific industry. Rector highlights how his company uses accumulated data and lookup tables for various touchpoints within a warehouse to create efficient operations. This approach allows for a quick analysis of simple data like orders and SKU characteristics, answering the universal question of operational averages. “It’s generalized to the point where…it can run in essentially any country on the planet,” Rector explains, underscoring the global applicability of their solutions. Addressing Industry Challenges with Innovative Technology The industry faces numerous challenges, notably in labor management and data analysis. Rector’s ambition was to create a solution that didn’t require extensive services or integrations, making it accessible to a broader market. He explains how Embassy Data Logistics’ products can improve labor efficiency and provide operational benchmarks without costly implementations. “We didn’t wanna have a solution that required engineering labor…which eliminates 98% of those customers on the market that need this,” Rector states, emphasizing the need for accessible and practical solutions. Harnessing Industry Insights for Future Success Drawing on his extensive experience and the lessons compiled in his book, “Warehousing 101,” Rector discusses the importance of understanding the science of warehousing. He stresses the gap in education for warehouse management and the necessity of bridging the language divide between executives and operations. His book is a comprehensive guide to warehouse operations, offering foundational knowledge crucial for the next generation of warehouse managers. “The book is designed to be that entry-level understanding…it’s really the entry-level to the science,” Rector comments, highlighting the educational aspect of his work. Key Takeaways on Warehouse Software Solutions Empowering Warehousing Operations: Embassy Data Logistics leverages extensive data analysis to offer universally applicable, cost-effective solutions. Innovative Solutions to Industry Challenges: The company addresses the gap in accessible technology for labor management and operational efficiency, avoiding the need for expensive and complex integrations. Educating the Next Generation: Through his book “Warehousing 101,” Rector provides invaluable insights into the foundational aspects of warehousing, advocating for a data-driven approach to management and operations. The New Warehouse Podcast Episode 469: Insights on Warehouse Software Solutions from Embassy Data Logistics’ CEO Lee Rector
Movu Robotics and Morel Robotics Forge strategic alliance to bring seamless plug-and-play robotic solutions to Turkey
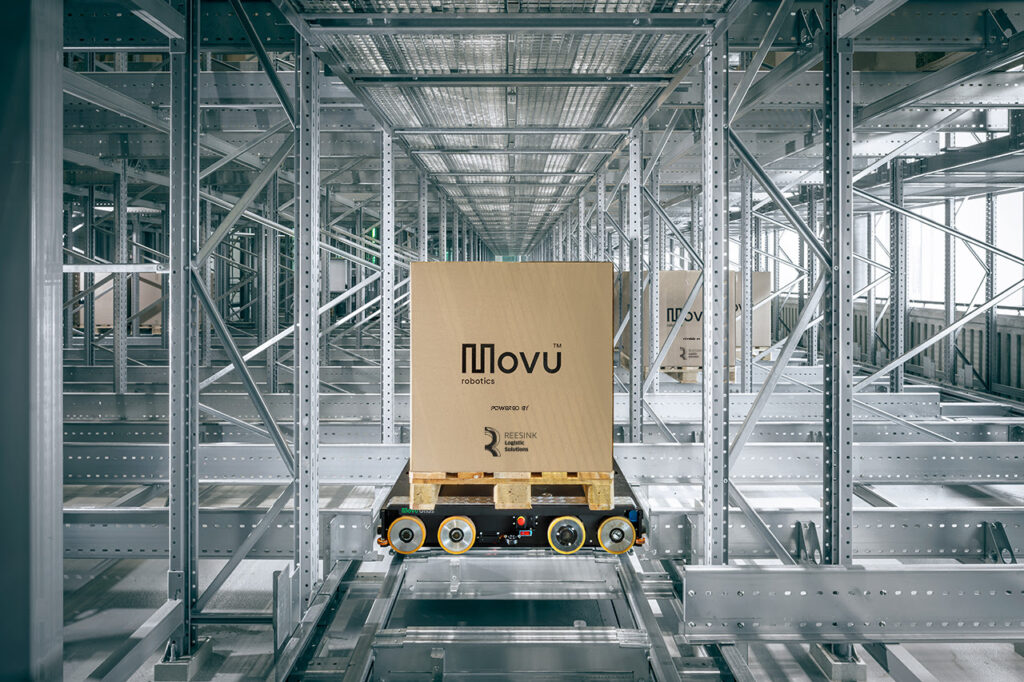
Movu Robotics, a warehouse automation solution that stands out by bringing easier logistics automation technologies to the world’s warehouses, has announced Morel Robotics as its premier integrator in Turkey. This collaboration aims to revolutionize the country’s automation landscape by bringing accessible and cutting-edge robotic technologies to businesses across various sectors. Movu aims to redefine the future of automation with its seamless plug-and-play solutions to drive efficiency, productivity, and safety in industries worldwide. Through this partnership, Movu Robotics will leverage Morel Robotics’ extensive expertise and market presence in Turkey to introduce its advanced robotic solutions to businesses seeking to optimize their operations. Movu escala bin shuttle, Movu atlas pallet shuttle, and Movu ifollow autonomous mobile robot (AMR) will be installed in Morel Robotics’ showroom as a demo center for the clients. The installation will include 4000 pallet positions, 19000 tots, and 8 ifollow robots. The demo center will showcase how to upgrade warehouses with Movu’s accessible automation. “Morel Robotics brings a lot of experience and a deep understanding of the Turkish market,” said Stefan Pieters, Co-CEO at Movu Robotics. “Their commitment to excellence aligns perfectly with our mission to deliver easier, modular, and flexible solutions that empower businesses to thrive in an increasingly automated world.” “We are excited to partner with Movu Robotics to bring accessible plug-and-play automation to our clients in Turkey,” said Hakan Aksoy, co-founder at Morel Robotics. “Together, we aim to drive technological innovation and empower businesses to achieve operational excellence via automation,” added Emir Altaras, another co-founder at Morel Robotics. With Movu’s state-of-the-art robotic solutions and Morel Robotics’ robust integration capabilities, businesses in Turkey can expect unparalleled opportunities to enhance their operations, streamline processes, and achieve greater competitiveness in the global market. This partnership underscores Movu Robotics’ commitment to expanding its global footprint and delivering impactful solutions to businesses worldwide. Both companies are determined to redefine the future of automation in Turkey, setting new standards for efficiency, productivity, and innovation.
U.S. Rail Traffic Reports for the Week Ending March 9, 2024
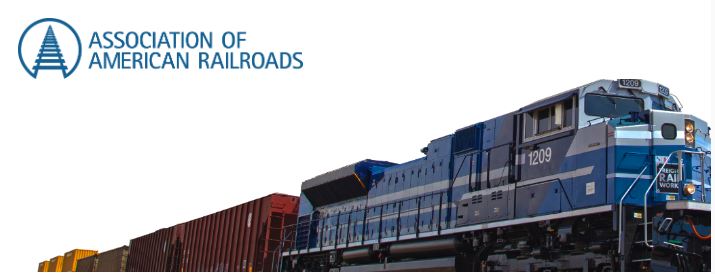
The Association of American Railroads (AAR) today reported U.S. rail traffic for the week ending March 9, 2024. Total U.S. weekly rail traffic was 472,662 carloads and intermodal units, up 5.0 percent compared with the same week last year. Total carloads for the week ending March 9 were 214,585 carloads, down 3.7 percent compared with the same week in 2023, while U.S. weekly intermodal volume was 258,077 containers and trailers, up 13.5 percent compared to 2023. Five of the 10 carload commodity groups posted an increase compared with the same week in 2023. They included chemicals, up 1,916 carloads, to 33,713; petroleum and petroleum products, up 1,399 carloads, to 9,930; and metallic ores and metals, up 685 carloads, to 18,882. Commodity groups that posted decreases compared with the same week in 2023 included coal, down 8,963 carloads, to 55,963; nonmetallic minerals, down 2,691 carloads, to 28,505; and miscellaneous carloads, down 726 carloads, to 7,791. For the first 10 weeks of 2024, U.S. railroads reported a cumulative volume of 2,125,301 carloads, down 4.5 percent from the same point last year; and 2,504,403 intermodal units, up 8.5 percent from last year. Total combined U.S. traffic for the first 10 weeks of 2024 was 4,629,704 carloads and intermodal units, an increase of 2.1 percent compared to last year. North American rail volume for the week ending March 9, 2024, on 12 reporting U.S., Canadian, and Mexican railroads totaled 321,441 carloads, down 3.2 percent compared with the same week last year, and 342,181 intermodal units, up 12.0 percent compared with last year. Total combined weekly rail traffic in North America was 663,622 carloads and intermodal units, up 4.1 percent. North American rail volume for the first 10 weeks of 2024 was 6,467,217 carloads and intermodal units, up 1.4 percent compared with 2023. Canadian railroads reported 89,470 carloads for the week, down 1.8 percent, and 71,752 intermodal units, up 7.2 percent compared with the same week in 2023. For the first 10 weeks of 2024, Canadian railroads reported a cumulative rail traffic volume of 1,554,602 carloads, containers, and trailers, down 1.9 percent. Mexican railroads reported 17,386 carloads for the week, down 4.3 percent compared with the same week last year, and 12,352 intermodal units, up 11.0 percent. Cumulative volume on Mexican railroads for the first 10 weeks of 2024 was 282,911 carloads and intermodal containers and trailers, up 8.8 percent from the same point last year. View the report here.
EnerSys® shows customer-driven solutions at MODEX 2024
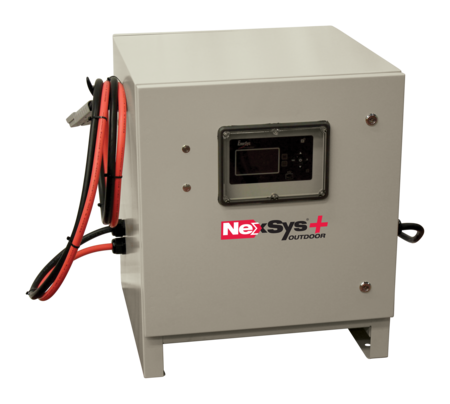
EnerSys ® has outlined its commitment to providing customers with solutions to achieve true optimization during an onsite press conference at MODEX 2024. Opening with remarks from Lisa Hartman, Vice President Investor Relations & Corporate Communications at EnerSys, and the company’s President of Motive Power Global, Chad Uplinger, both leaders briefly commented on current market trends and customer challenges, how these trends have influenced product development and 2024 (FY25) growth initiatives for its Motive Power line of business. “Helping customers tackle change and its subsequent challenges drives everything we do – from the development of our advanced technologies, to how we align with OEMs on integration, to how we work with customers to identify and help achieve their goals,” said Uplinger. “Ultimately, our success rests on that of our customers – developing and offering optimized power solutions that enable them to address market headwinds and keep their operations productive and resilient.” Noting some of the key market drivers mentioned by Chad Uplinger during the press conference, Harold Vanasse, Senior Director of Marketing, Motive Power Global at EnerSys, also discussed a few of the company’s newest solutions being showcased by EnerSys ® at MODEX in booth B8032. “Labor is a big challenge our customers have been facing – even before the pandemic. With a roughly 43% turnover rate in warehousing 1, many customers are looking to become more resilient by automating their operations as much as possible,” said Vanasse. “To help achieve true automation, we are showcasing our NexSys ® AIR wireless charger that eliminates the need for workers to monitor and maintain mechanical charging connections. While compatible with all our major battery technologies, it’s a perfect match with our NexSys ® maintenance-free batteries to help AGV fleets operate more productively and autonomously.” The NexSys ® AIR wireless charger features contact-free charging pads – eliminating the maintenance and wear associated with physical connections. It integrates into a range of AGV applications with charging stations that can be installed in a variety of locations throughout facilities. Each NexSys ® AIR wireless charger station offers intuitive touchscreen controls with added safety features that include Foreign Object Detection (FOD) and Live Object Detection (LOD). “Between price volatility for fossil fuels and 67% of companies planning to hold supply chains responsible for environmental KPIs 2 , customers running outdoor fleets or specialized attachments are looking for alternatives to internal combustion engine-powered equipment,” added Vanasse. “As a powerful option, we’re featuring our new 80-volt NexSys ® iON battery and NexSys ® + Outdoor charger. Whether alone or used together, these provide many traditional Class 4 and 5 internal combustion engine fleets the ability to go electric – reducing emissions and carbon footprint. In addition to being highly energy efficient, our entire line of maintenance-free NexSys ® batteries does not require watering, which results in water savings as well.” Designed for high-demand applications, the 80-volt version of the NexSys ® iON battery offers the same UL2580 and ISO26262 ratings as the rest of the NexSys ® iON line of batteries – providing rugged, dependable power for indoor/outdoor equipment and applications involving specialized attachments. The new IP54-rated NexSys ® + Outdoor charger brings the advanced performance of the popular NexSys ® + charger to equipment operating at building material yards, airports, farms, rental facilities, ports, cargo terminals, and other working environments exposed to the weather. “We’re always trying to understand customer needs and apply a ‘total systems approach’ to achieving their goals. These new products expand our ability to apply that approach for customers deploying AGVs and electrifying outdoor equipment,” concluded Vanasse. “Our full array of options enables us to address a lot of our end-users application challenges – whether indoors or outside, human-driven or automated.”
HWArobotics introduces its reliable, customizable shuttle systems at MODEX 2024
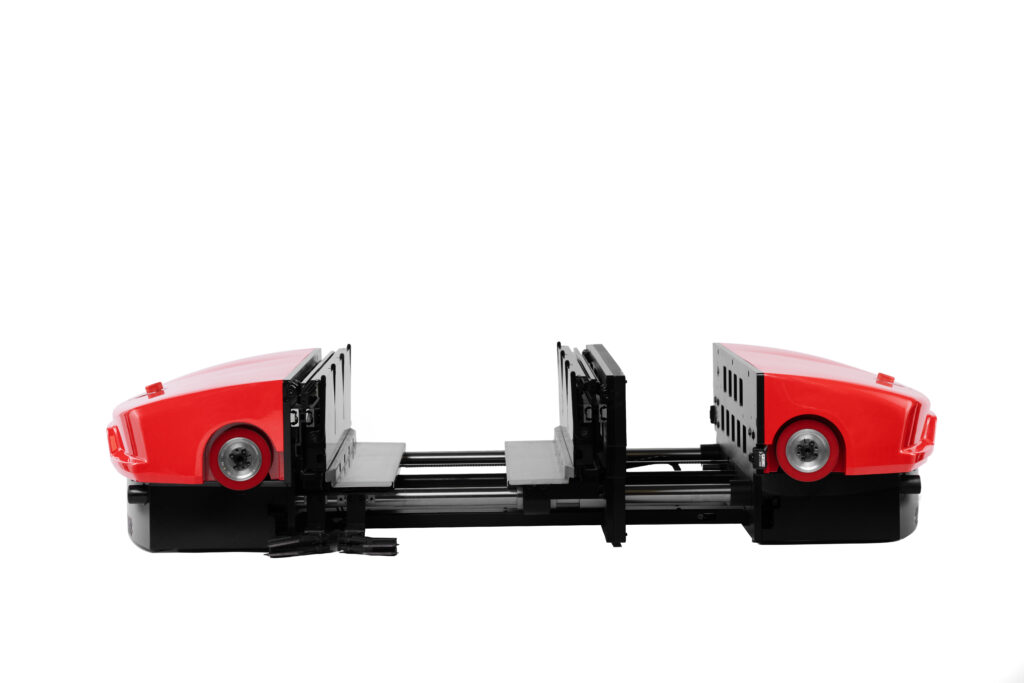
Shuttle systems from HWArobotics are now available to companies across North America after the ASRS pioneer demonstrated its technology – based on 20 years’ experience – at MODEX 2024. HWArobotics showcased its high quality, reliable, and efficient shuttle automated storage and retrieval systems (ASRS) technology at the MODEX 2024 supply chain show, in Atlanta, Georgia (March 11-14). The warehousing and logistics robot company has 20 years of experience in developing and building shuttle robot systems and appeared at MODEX to introduce its comprehensive range of ASRS technology to a North American audience. HWArobotics is looking to expand its customer base in the region and develop new partnerships with distributors, following the successful deployment of its solutions by Canadian 3PL business Darwynn. Designed to optimize logistics and supply chain management operations, four key HWArobotics product lines were launched in North America at Modex 2024, including three tote shuttles and one pallet shuttle, as well as associated cargo lifts, racking, and control software. With system availability of more than 99%, excellent reliability, accuracy, and scalability, HWArobotic’s customizable shuttle robot systems deliver high throughput for a wide range of industry sectors and can be deployed fast to deliver results quickly. A whole process intelligent logistics solution HWArobotics’ warehouse automation experts were on hand at Booth C3885 at this year’s Modex to demonstrate the company’s products, which use high-performance components from European suppliers, including Siemens (Germany), Voestalpine (Austria) and Hilti (Lichtenstein). The stand featured the SLS300, SLS400, and SLS600 series tote shuttles and the FPSS1500 pallet shuttle. Manufactured using durable, long-lasting core components to create a stable structure, the SLS300 series standard tote shuttle storage system delivers high efficiency and up to 24 hours of continuous operation. Capable of speeds of up to 4 m/s and acceleration of 2 m/s, the SLS300 has a single-machine capability of up to 120 boxes an hour. Alongside the SLS300, HWArobotics also launched the SLS400 series variable tote shuttle system to the North American market. Offering strong compatibility and flexibility, the robot ASRS solution can mix and store containers of different sizes and can be configured to meet different efficiency requirements. Reliable, economical, and flexible, HWArobotics’ SLS600 3D tote shuttle system meets the needs of low-traffic, high-efficiency environments, such as spare parts, publishing, and e-commerce sites. It has excellent warehouse-sharing capabilities as shuttles can realize any change of lane operation, while system capacity can be easily adjusted by increasing or decreasing the number of shuttles to meet local short-term demand peaks. Also on display at MODEX 2024 was the highly controllable FPSS1500 series pallet robot shuttle system designed for warehouses and distribution centers. The four-directional solution is an advanced ASRS designed for efficient pallet handling and storage, with global standard CE and UL certification. Specialized all-electric shuttle devices are capable of moving in four directions within the racking structure, providing enhanced versatility and operational efficiency. The FPSS1500A is designed for room temperature environments across the manufacturing, distribution, food & beverage, and industrial sectors, and the FPSS1500B has been created specifically for cold storage, such as food, medicine, and cold chain businesses. Using AI scheduling algorithms, it has achieved swarm intelligence within the PSR system to automatically adjust efficiency based on the number of vehicles and the rack structure. Alongside its high-performance shuttle devices, HWArobotics has a wide portfolio of goods lifts, racking, and picking workstations (including robotic picking), for maximum performance and conveying capacity, high positioning accuracy, and sturdy, high tolerance storage. HWArobotics General Manager, Sky Chen, explains, “We are delighted to have been at Modex 2024 demonstrating the exceptional range of benefits our tote and pallet shuttle ASRS solutions can deliver. Thank you to the many visitors who visited our stand to learn more about the possibilities our innovative automated warehousing and logistics technology offers to reduce the workload of personnel and deliver efficient and accurate order execution. “At HWArobotics, we are enormously proud of the 20 years’ of experience we have as a pioneer in the field of shuttle robot systems and our exceptional customer service. We have established a base in the US and are excited to enhance the competitiveness of North American businesses with our shuttle ASRS technology. “The recent deployment of HWArobotics shuttle systems by Darwynn demonstrates how our technology can be up and running quickly and effectively, automating and optimizing logistics and storage processes. Our strong global customer base, including Bosch UAES, Hisense Hitachi, SONY, iCOOP, Shein, Joyson Safety Systems, JD.com, and Forvia, is a testament to the capabilities we offer to companies seeking intelligent upgrading of their warehouses and manufacturing plants.”
Yale expands availability of award-winning Yale Reliant forklift operator assist solution at MODEX 2024
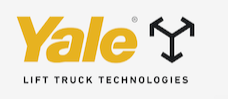
Technology designed to support warehouse safety initiatives now available on 59 Yale forklift models Yale Lift Truck Technologies announced the availability of its Yale Reliant™ forklift operator assist solution on an additional 16 Yale® models. The new entrants to the Yale Reliant lineup are predominantly warehouse lift trucks and expand the technology’s availability to a total of 59 models covering a wide range of applications, including those common in retail and e-commerce fulfillment, wholesale distribution, and third-party logistics operations. The lineup expansion includes several models that were not previously available for standard order with Yale Reliant enabled, as well as additional capacities or configurations of models for which only select variations were available previously. Very narrow aisle (VNA) turret trucks, narrow aisle reach trucks engineered with a smaller frame for tight retail environments like stockrooms, and the straddle, furniture, and standard order picker models are all newly available with Yale Reliant. Center riders, tow tractors, enclosed end riders, and reach trucks were already available with Yale Reliant, but the latest portfolio expansion extends availability to additional capacities and configurations of those models. The operator assist technology is the focus of the Yale booth #B3810 at the MODEX trade show in Atlanta this week. In addition to providing a deeper understanding of the solution’s underlying advanced dynamic stability (ADS) technology, personalized demonstrations at the booth also feature other technologies in the Yale Reliant suite like object detection, proximity detection and real-time location sensing. Yale Reliant keeps the operator in ultimate control of the lift truck, but depending on the package selected, automatically applies interventions in response to compromised stability, obstacles detected in the path of travel or nearby, and even based on rules specified for certain areas of the warehouse. “The interest that this technology continues to attract, whether at the industry’s leading tradeshows or reflected in the thousands of trucks commercially deployed with it, speaks to forklift accident prevention as a critical priority for today’s warehouses,” says Joe Koch, Emerging Technology Sales Manager, Yale Lift Truck Technologies. “Just yesterday, we introduced a standalone ADS option to empower operations with greater choice and opportunity to incorporate this tool in their safety initiatives, and this announcement takes another step in that direction, broadening our Yale Reliant lineup to help warehouses and retailers access the truck that is most appropriate for the job and technology that can help them support inexperienced operators and proper operating practices.”
Manufacturing Technology Orders down 31% from December: contract machine shops decrease orders
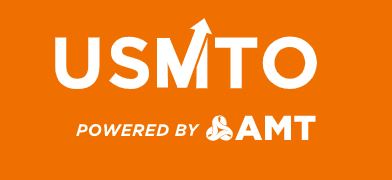
Orders of manufacturing technology, measured by the U.S. Manufacturing Technology Orders Report published by AMT – The Association For Manufacturing Technology, totaled $338 million in January 2024, a 31% decline from December and a 3.7% decline from January 2023. The value of orders in January 2024 was at the lowest level for January 2021, yet the unit count was the lowest since 2016. This indicates the demand for manufacturing technology is still being driven by orders of highly specialized, automated machinery. Contract machine shops, the largest customer of manufacturing technology, decreased orders in January 2024 to the lowest level since July 2023, a 27.1% decline from December 2023. These shops have been ordering below their typical share for some time now. Should business conditions improve for these manufacturers, there is a large upside potential for future orders of manufacturing technology. Contract machine shops are expected to continue experiencing subdued order activity shortly. Despite a minor improvement in February 2024, the Gardner Metalworking Index – compiled by Gardner Business Media and predominantly based on responses from contract machine shops – indicates that the downturn in business activity is likely to persist for at least another month. Outside of the aerospace and automotive sectors, OEMs in many other industries are generally small consumers of manufacturing technology in any given month relative to the size of orders from contract machine shops. However, for some time now, this has inverted, as OEMs across several industries have increased orders at a pace that has nearly offset the decline in orders from contract machine shops. Manufacturers of oil and gas field machinery were among the OEMs increasing orders in January 2024. According to data published by the Texas Oil and Gas Association, 2023 set records in both the extraction and refining of oil and natural gas in the state. In recent years, elevated orders for manufacturing technology from this sector have typically been placed in the fourth quarter of the year. The early uptick in 2024 could indicate an appetite to expand capacity and modernize equipment to compete with recent regulatory hurdles. January is typically the slowest month for manufacturing technology orders in any given year, and 2024 may prove to be no different. Forecasters at Oxford Economics have predicted that global industrial production will increase 2.7% in 2024. This bodes well for manufacturing technology, as even non-durable goods producers require machinery that is built using the metalworking equipment tracked by USMTO. Indeed, Oxford Economics also presented a forecast at AMT’s Winter Economic Forum, predicting that manufacturing technology orders in the United States would increase nearly 8% in 2024.
Delta showcases innovative wireless charging solutions and machine vision solutions for Smart Logistics at MODEX 2024
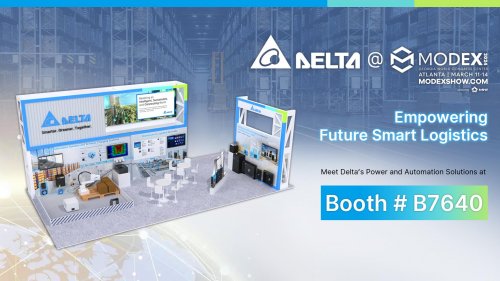
Delta, a power management and provider of IoT-based smart green solutions, is showcasing high-efficiency wireless charging systems and smart industrial automation solutions for AGVs, e-forklifts, and conveyors to foster autonomous logistics operations. Key features include a 30kW Wireless Charging System, which offers up to 95% efficiency for a broad range of industrial logistics vehicles, and a Machine Vision Solution with 3D ToF Smart Cameras to enable AGV smooth navigation even in completely dark logistics conditions. Dave Morse, Vice President of Industrial and Automation at Delta Americas, said, “Delta’s leadership in high-efficiency power solutions and prowess in smart manufacturing derive from our commitment to innovation and energy conservation. With more factories adopting autonomous equipment such as AGVs and AMRs, we have developed advanced industrial automation and innovative wireless charging solutions to accelerate the application of unmanned industrial vehicles and enhance the productivity and energy efficiency of our customers’ warehousing and logistics operations.” During the event, Delta will present a live AGV demonstration to showcase: Delta’s wireless charging systems, adopt industrial wireless charging technology developed by WiTricity®. The 1kW Wireless Charging System is composed of a primary unit for AC supply attachment and a secondary for vehicle battery connection. The two units can transfer power wirelessly within a gap of up to 20 mm with a maximum of 93% power conversion efficiency. The M∞Vbase single-phase model features 3-5 charging modules with each providing 1350W power output to meet various charging demands. It also supports ethernet communication for energy management. The 3D ToF Smart Camera DMV-T integrates imaging, sensing, and computing in a compact design and supports 6W ultra-low power consumption, which is perfect for integration in a mobile robot with limited space. Featuring a built-in dual-core CPU, the DMV-T can process the depth maps in real-time and leverage Delta’s Machine Vision Platform DIAVision for AGV navigation and collision avoidance. In addition, the AGV servo system adopts the Integrated Brushless DC Gearmotor for locomotion, with the integration of the servo motor, servo drive, magnetic encoder, and planetary reducer in one package. This coupling-free gearmotor design is a compact solution for the space-saving demand of the AGV chassis. Delta will also showcase a forklift-shaped demo to present the latest M∞Vair 30kW Wireless Charging System. This system also features a primary and a secondary unit and enables fully autonomous charging over a gap of up to 150 mm. Its up to 95% contactless power transmission greatly reduces energy waste for large e-vehicles such as forklifts. A fully integrated Warehouse and Logistics solution with a visualized SCADA System VTScada for remote control of diverse subsystems. The control span covers various applications, such as door and dock, conveyors, sorting, picking, and scanning. Visit Delta’s booth B7640, Hall B at the Georgia World Congress Center in Atlanta during MODEX 2024 from March 11th – 14th.
VisionNav’s VNST20 PRO world premiere showcases 45-minute trailer truck loading/unloading at MODEX 2024
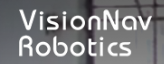
VisionNav Robotics launched its latest automatic trailer truck loading and unloading solution, featuring the newly unveiled VNST20 PRO AGV robotics, at MODEX 2024, the full spectrum supply chain expo in Atlanta. The world premiere of the pioneering solution from the materials handling robotics specialist saw demonstrations of how it is capable of loading and unloading trailer trucks in just 45 minutes. Combining VisionNav’s high-performance autonomous forklift VNST20 with an advanced Robot Control System (RCS) for fleet scheduling and 3D LiDAR SLAM deep learning positioning technology for market-leading accuracy, the flexible solution has been designed specifically for trailer trucks, automating loading, unloading, and manual handling tasks. At MODEX 2024, VisionNav featured an immersive display allowing a technologically advanced exploration of the capabilities of VNST20 PRO, which marks an evolutionary step in the development of trailer truck loading and unloading. Powerful 3D perception, state-of-the-art mapping, and market-leading accuracy Fitted with a powerful RCS that utilizes state-of-the-art mapping, 3D perception, localization, and routing technologies, the VNST20 PRO generates efficient loading and unloading strategies, devises optimal delivery routes, and maximizes loading rates. Featuring 3D LiDAR SLAM positioning, the dedicated, proprietary system delivers increased space utilization, high scenario adaptation, high compatibility, and reliable solution redundancy to provide fast, safe, and efficient cargo handling. Available in the US from 2025 the VNST20 PRO can adapt to diverse trucks, goods, and environments, utilizing self-adaptive perception for unstructured environments and dynamic mapping for dynamic routing in containers. It is compatible with a wide range of trucks in North America and Europe and can be tailored to a variety of pallets, including EPAL and CHEP. VNST20 PRO is easily switched into manual mode to prevent delays. Key features of VisionNav’s VNST20 PRO: Rated load capacity of 2000 kg Cargo top clearance of 150 mm Gap between goods of 0-30 mm Minimum turning radius of 1,431 mm 45 minutes loading/unloading. Don Dong, VisionNav Robotics VP of Global Sales, says, “Boosting overall work efficiency and safety, the VNST20 PRO is at the cutting-edge of AGV robotics technology, revolutionizing cargo handling to enable loading or unloading a trailer truck in as little as 45 minutes. This is a new approach to trailer truck loading and unloading. “We demonstrated VNST20 PRO at work at our stand at MODEX 2024, alongside 4-sided LED hanging screens. This immersive experience provided visitors to the show with the opportunity to see the full capabilities of our trailer truck loading and unloading solution and how it can work for them. This is the first time VNST20 PRO has been demonstrated anywhere in the world and the response has been very positive.”
PS Logistics Acquires Yordy Transport
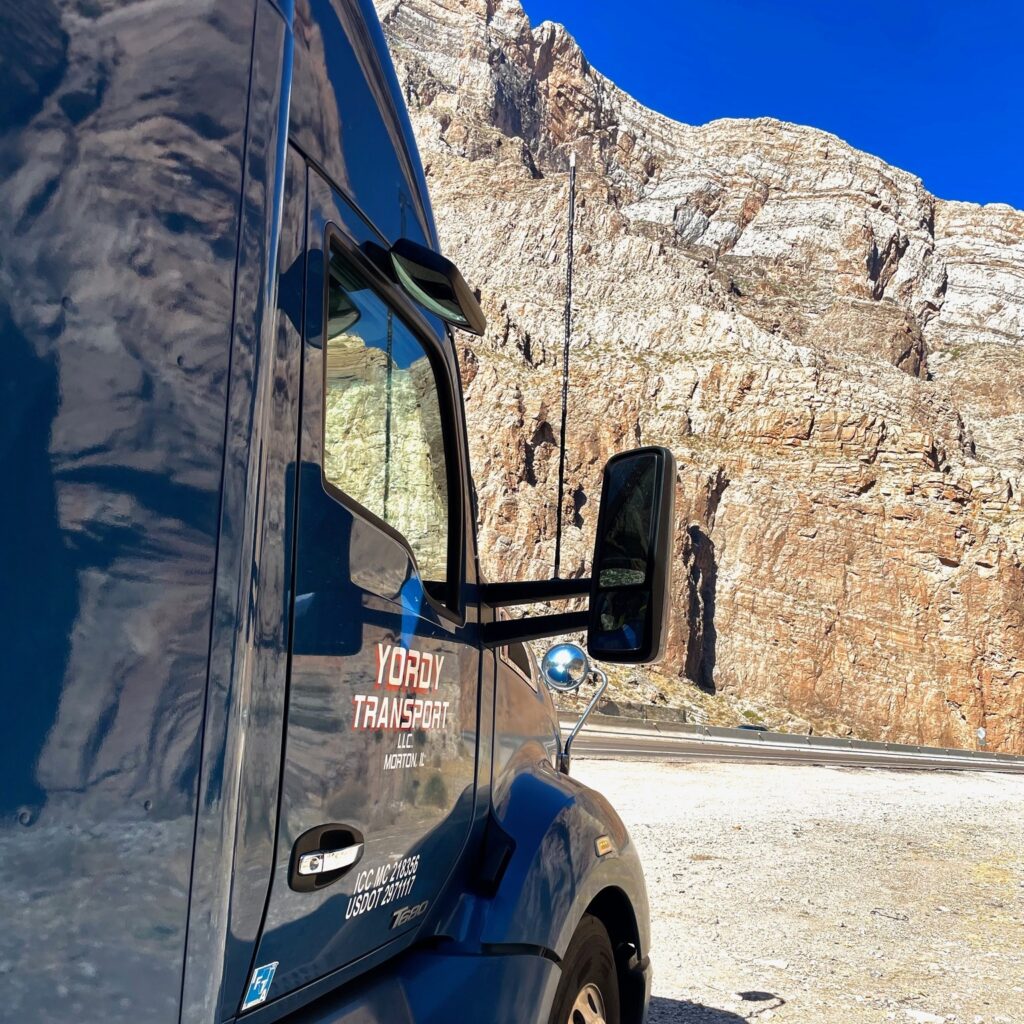
PS Logistics, a transportation and logistics company in the United States, has announced that its subsidiary Diamond State Trucking & Logistics (“Diamond State”) has acquired Yordy Transport, a trucking company that specializes in flatbed shipping. Financial terms of the transaction were not disclosed. Headquartered in Morton, Illinois, Yordy Transport was founded in 2018 by Avery Yordy and primarily hauls railroad, steel, lumber, and building materials freight across the central and southeastern United States. Yordy Transport’s freight mix and geographic coverage are complementary to the Diamond States’ and are expected to provide immediate opportunities to realize operational synergies. Yordy Transport will now operate under the Diamond State name. “We are excited to welcome Yordy Transport’s flatbed drivers and employees to the PS Logistics family,” said Scott Smith, chief executive officer and co-founder of PS Logistics. “This acquisition aligns nicely with our desire to partner with founder- or family-owned trucking companies that put their drivers first while also providing quality service to their customers, and PS Logistics is looking forward to the growth opportunities that will result from this acquisition.” Avery Yordy, founder and owner of Yordy Transport, said, “Diamond State will be a great partner for my business. Throughout the process of working with them, it became evident that they are committed to the drivers’ success, and I’m excited that Yordy Transport will now be a part of a larger organization that will provide greater freight choices to Yordy’s drivers and operational expertise to the business.” The transaction continues PS Logistics’ acquisition strategy of partnering with families and quality owners within the transportation and logistics industry. Since 2016, PS Logistics has successfully acquired 26 trucking operations and five non-asset logistics operations across the United States.