Episode 461: HeroWear exosuits enhance warehouse safety and productivity

Welcome to the latest episode of The New Warehouse Podcast, where we sit down with Mark Harris, the visionary CEO and Co-founder of HeroWear. This episode takes us on a deep dive into HeroWear’s groundbreaking exosuit technology, designed to empower workers by minimizing injury risks and amplifying productivity. We explore the inception of HeroWear, the transformative impact of their suits in the logistics industry, and a revealing study that underscores the significant benefits of adopting this technology. Innovating Exosuits for Worker Well-being Mark shares the compelling origin story of HeroWear, rooted in the everyday experience of co-founder Carl’s struggle with back pain from carrying his young children. Carl wondered, “How is this 20-pound person destroying my back?” sparking a quest into the biomechanics of back pain and the genesis of HeroWear’s exo suits. This personal inquiry led to the development of a low-profile, lightweight suit designed to offload back strain and reduce injury risk. He discusses how HeroWear’s technology can mitigate the risk of musculoskeletal injuries, a common concern in physically demanding jobs. The narrative extends beyond invention, delving into HeroWear’s dedication to enhancing workers’ lives on and off the job through innovative wearables. A Groundbreaking Study on Exosuit Productivity In a recent productivity study, HeroWear’s exo suits boosted productivity by 8% and reduced the effort required for tasks by 39%. Mark adds, “This study validates our technology’s impact on reducing injury risk and highlights its role in driving productivity.” He emphasizes the dual benefits of their suits: safeguarding workers’ health and bolstering operational efficiency, making a solid case for integrating exo technology in the workplace. Exosuits are Where Safety Meets Productivity As HeroWear gears up for an expansive future, Mark Harris outlines their strategic steps toward normalizing exo-suit technology in the workplace. “We’re building out our infrastructure and expanding into more facilities, which includes enhancing our manufacturing capacity and moving to a larger space for pick, pack, and fulfillment,” Harris shares. HeroWear is also diving deeper into productivity studies through partnerships that share data to validate the long-term benefits of their technology. “It’s about proving over time the dual benefits of safety and productivity gains,” Harris explains, emphasizing the importance of tangible evidence to support their mission. Looking to the future, Harris draws an analogy with the evolution of power tools, predicting a similar trajectory for exosuits. Just as power tools transitioned from a niche B2B technology to a ubiquitous household item, HeroWear envisions a world where exo suits are a standard tool for physical tasks, reducing strain and enhancing efficiency. Key Takeaways HeroWear’s exo suits are at the forefront of enhancing worker safety and productivity. Recent studies confirm the significant positive impact of exo technology in the workplace. HeroWear is shaping a future where technology and human well-being coalesce to redefine labor. The New Warehouse Podcast EP 461: HeroWear Exosuits Enhance Warehouse Safety and Productivity
Slimline swiveling-rotary modules for large workpieces
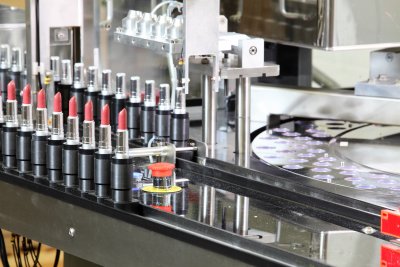
The slimline infinite rotary units are suitable for the highly dynamic rotation of large workpieces and eccentric grippers as well as for use in screwing and coiling technology. Miniature drives and microdrives can be found in virtually all areas of automation technology and have a correspondingly wide variety of applications. These range from medical technology and laboratory automation as well as general machine construction and intralogistics to aerospace applications. In all areas, the small drive systems play a role in ensuring that the associated automation solutions function with optimum process safety, reliability, and cost-effectiveness. This also applies to handling applications. In slimline, yet high-torque swiveling-rotary modules, these drives ensure that even large workpieces are moved precisely, both in the case of fast screwdrivers and also in automatic rotary handling, assembly, and testing systems. Anyone looking for an efficient and space-saving solution for typical movement sequences that occur in handling and assembly technology, such as turning, swiveling, screwing, rolling, or coiling, may be interested in the swiveling-rotary modules of the ForTorque series from the kinematics specialist JA². This is because the slimline infinite rotary units are ideal for the highly dynamic rotation of large, high-inertia workpieces and eccentric grippers as well as for use in screwing and coiling technology. Turning, swiveling, screwing, coiling A typical application case for the miniature swiveling-rotary modules is, for example, screwing the caps on small cosmetics or pharmaceutics containers in constrained spaces on fully automated packaging lines. The modules are also suitable in cases where grippers or workpieces need to be swiveled, e.g. when assembling or separating products. Designed as a modular system, six sizes with diameters of 16, 20, 25, 35, 40 and 45 mm are available. This covers peak and continuous torques of 0.3 and 0.14 Nm to 4.0 and 2.6 Nm respectively. The inertia of the load may be between 2.0 and 200 kgcm². This provides the most suitable solution for accurately angled movement and positioning for a wide range of different handling and assembly tasks. To reduce the load on the output shaft of gearheads in the case of high external moments of inertia, the output plate of the four larger module models has an extremely rigid bearing consisting of two thin-section bearings. Furthermore, the swiveling-rotary module with 40 mm diameter can additionally be equipped with a fluidic rotary joint for pneumatics or vacuum, e.g. to supply a pneumatic gripper with compressed air. The kinematics specialists push the modular concept even further: An interesting possibility is to combine the fast rotary units with linear axes, e.g. of the QuickLab series. Matching adapter plates are available as accessories. The result is compact lift-rotary or lift-swiveling systems through to five-axis handling systems. High dynamics and precision “The drives are the heart of our modular automation system and the requirements placed on them are very high,” explains Wilhelm Jung, Managing Director at JA². “The motors must operate highly dynamically, be precisely controllable, and have suitable dimensions.” In the case of the ForTorque modules, for example, the brushless DC-motors of the B and BX4 series from FAULHABER proved convincing. The motors with their two-pole and four-pole technology are extremely compact. The used variants of the B series with diameters of 16, 20, and 35 mm are just 28, 36, and 68 mm long respectively, but deliver continuous torques of up to 168 mN in the case of the largest variant. Similar also applies to the BX4 series. “Here we use motors with 22 mm or 32 mm diameter and continuous torques of 18 and 53 mNm respectively,” reports Wilhelm Jung. The motors are used in the ForTorques up to speeds of 8,000 rpm. Different gearheads, including zero backlash planetary gearheads from FAULHABER, provide gear reduction. Ultimately, the gearhead technology with the respective maximum input speed determines the limit for the maximum motor speed. “We then select the reduction ratio according to the application,” continues Wilhelm Jung. “In this way, we can influence the extent to which the external moment of inertia is reduced by the square of the reduction. The motor can then be precisely regulated unaffected by the lever. When selecting the gearheads, we paid particular attention to the efficiency of the gearheads. Because the better the efficiency is, the more precisely the torque applied at the gearhead output can be determined from the motor current. This is a key feature, particularly in the case of screwing applications where delicate (plastic) parts need to be screwed on with a defined torque.” Single-cable technology for fault-free control All swiveling-rotary modules are connected and controlled using a standardized bayonet connector, single-cable technology, and a motion controller. In automation systems, however, the switch cabinet is usually some distance from the actual drive. “Between the motor and the controller in the separate switch cabinet, there can then be 10, 20 or more meters,” says Wilhelm Jung. There is therefore a special, multi-shielded cable that transfers the motor power and the position sensor signal between the motor and controller up to 30 m without interference. The cable is fastened with strain relief, can be plugged in, and is also designed for use with cable chains, i.e. for mobile use. Moreover, thanks to the available preassembled cable sets, the single-cable technology simplifies installation. With the motion controllers, the user has the choice because the used motors are compatible with different controllers. “We also offer motion controllers from FAULHABER,” adds Wilhelm Jung. The two companies have, after all, enjoyed successful collaboration for many years. In the above-mentioned QuickLab linear axes, for example, the DC linear drives LM2070 and LM1247 are used. They are not designed as classic “surface rotors” with carriages and guides. Instead, the forcer rod is guided within a 3-phase self-supporting coil. “This design produces an exceptionally good relationship between linear force and current and high dynamics. In addition, there are no cogging torques, thereby making the linear motors ideal for use in our modular QuickLab system,” concludes Wilhelm Jung. About the Author JA² (Jung Antriebstechnik u. Automation, see
BlueBotics to showcase AGV/AMR interoperability and share usage trends at MODEX 2024
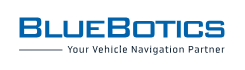
BlueBotics, a natural feature navigation and part of ZAPI GROUP, will be at MODEX 2024 to showcase the complete ‘ANT driven‘ ecosystem of interoperable AGVs and AMRs and to provide unique industry insights on the adoption of these burgeoning technologies to visitors. The company’s partner-focused exhibit on booth C6092 will feature a full multi-brand AGV/AMR fleet demo managed by the BlueBotics ANT server fleet management software. In addition to this live example of vehicle interoperability, the stand will include six vehicle-brand kiosks staffed by BlueBotics’s AGV partners and associated materials. In addition to this info-packed stand experience, senior BlueBotics staff will host a uniquely educational seminar in which they will share industry insights from the company’s recent global AGV/AMR usage survey. “BlueBotics research validates that the automated vehicle market is thriving, with many companies planning both to adopt AGVs or AMRs and then grow these fleets in the coming years,” said BlueBotics CEO Dr. Nicola Tomatis. “The visitors attending our seminar will learn more about how the AGV market is advancing, what vehicle types companies are buying, how users integrate them on-site, ROI calculations, and much more. Plus, attendees can then visit our stand to explore the primary autonomous navigation technology that is driving this growth with our ANT server fleet demo.” Live interoperable fleet demo On the BlueBotics stand (C6092), the team will host a live multi-brand AGV/AMR fleet demonstration. This will feature six separate brands of vehicle – ranging from a full-size counterbalanced forklift AGV to a small turn-on-the-spot AMR and a floor cleaning robot – all of which will run in one connected fleet, managed by BlueBotics’ ANT server fleet management software. Participating brands include AND&OR, Bastian Solutions, Cleanfix, FlexQube, Kivnon, and Oceaneering Mobile Robotics. Global AGV/AMR insights Meanwhile, in Theatre C on Wednesday, March 13, BlueBotics CEO Nicola Tomatis will join VP of Marketing Matt Wade to guide visitors through the evolving global usage of automated vehicles by digging into the findings from the company’s first-ever AGV/AMR usage survey. These findings will cover a wide range of topics, including how AGV/AMR fleets are evolving in different regions, which vehicle types are most popular, user fears when adopting this technology, and how firms measure the success of their mobile robotics investments. MODEX 2024 runs from March 11 to 14 at the Georgia World Congress Center, Atlanta. Visit BlueBotics on stand C6092.
Tompkins Solutions names Bryan Perkins Senior Vice President of Engineering
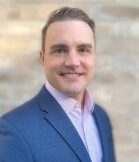
Tompkins Solutions, a supply chain consulting and material handling integration firm, has announced that Bryan Perkins has joined the company as senior vice president of engineering. In this role, Perkins will be responsible for all engineering functions, including consulting engagements, controls and hardware implementations, and field customer service. Perkins has nearly two decades of experience in supply chain, logistics, manufacturing and engineering, and is also a certified Six Sigma Black Belt, Lean Champion and Lean Practitioner. Before joining Tompkins, Perkins served as senior vice president of operations for DeliverOL, where he led a network of delivery stations for DHL, and also held senior management positions with ADVATIX, Walmart, and Amazon. “Bryan’s widespread expertise across supply chain operations and strong background in engineering and business methodologies make him a great addition to the Tompkins team,” said David Latona, CEO of Tompkins Solutions. “We are excited to have him on board and help us continue to deliver innovative solutions that meet our clients’ evolving needs.”
TVH receives the Most Valuable Supplier Award
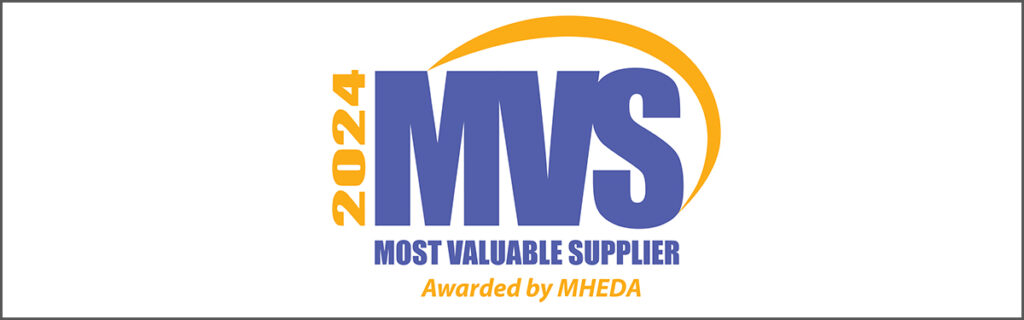
TVH Americas, a global provider of quality replacement parts and accessories for the material handling, industrial, and construction equipment industries, has been awarded the prestigious MVS (Most Valuable Supplier) Award for its outstanding achievements in 2023 by their industry trade association, Material Handling Equipment Distributors Association (MHEDA). This achievement marks the 9th consecutive year that TVH has achieved the Award. The MVS Award is a coveted accolade within the industry, with fewer than 10% of MHEDA’s member organizations earning this distinction. TVH’s continued recognition as a valued partner within the industry underscores a commitment to excellence, professionalism, and responsible stewardship. To qualify for the MVS Award, TVH was required to meet a series of criteria in several areas important to the companies that do business with them. In addition to confirming an ongoing commitment to safety and employee training, award recipients must provide documentation of active participation in a program that gives back to the community. MVS Award winners have demonstrated an overall commitment to business excellence by documenting activity in the following areas: Industry Advocacy Distributor Advocacy Business Networking Continuing Education Business Best Practices “The MVS Award is a significant recognition in the materials handling industry, encompassing various facets beyond just business achievements. Achieving such recognition signifies that TVH has demonstrated exceptional leadership qualities, upheld industry standards, contributed positively to its community, and shown dedication to continuous improvement. This acknowledgment not only elevates the company’s reputation among its peers but also instills confidence in its customers and community members, showcasing it as a leader in the materials handling world.” Van Clarkson, President of Fairchild Equipment and 2024 MHEDA Chairman.
MODEX attendees bring big spending plans to the biggest supply chain event of 2024
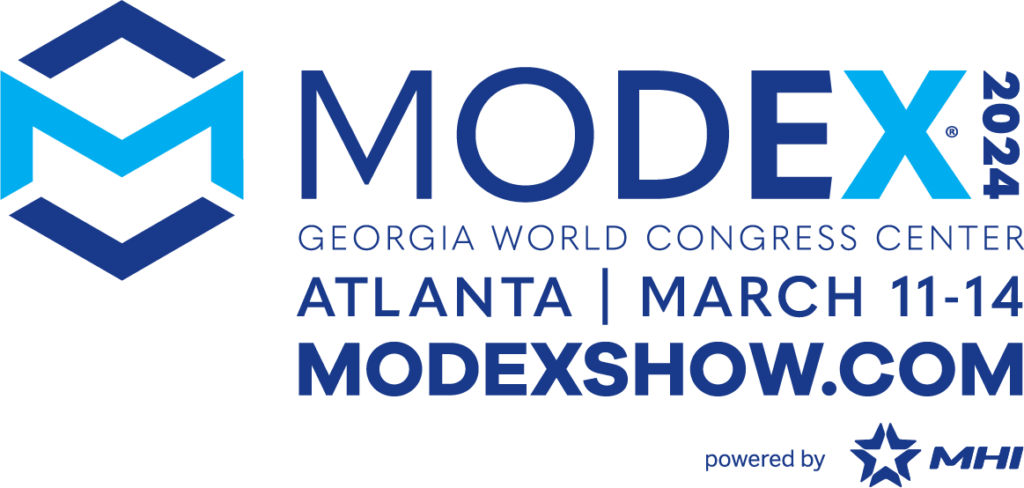
Attendees are looking to invest in automation, robotics, and tech solutions to improve the speed and resiliency of their supply chain operations With MODEX 2024 just over one month away, attendee registrations are tracking well above the last in-person MODEX event. Looking at attendees that have registered to date, they are high in quality as well and represent the majority of the Fortune 1000, top 100 retailers, and top 100 consumer goods firms. We are also seeing record numbers of buying teams from these firms planning to attend. When attendees register, they are asked to answer a variety of demographic questions indicating their industry, product interest, buying authority, and spending plans. Below are some highlights from current MODEX attendee demographics. 85% have buying power 81% are coming to see new products and innovations 62% are coming to network and learn 35% plan on spending over $1 million over the next 18 months 47% are corporate or senior management 32% are middle management or IT/Engineering 69% are looking for solutions for distribution centers or warehouses supporting manufacturing 23% are looking for solutions for manufacturing facilities When it comes to the solutions, MODEX 2024 attendees are looking for a wide range of equipment and technologies for their supply chain operations. However, there is a heightened interest in automation, robotics, autonomous vehicles, and emerging technologies. The top product interest categories for attendees currently are: Automatic Guided Vehicle Systems Artificial Intelligence/Machin Learning Automated Storage/Retrieval Systems Autonomous Fork Trucks Conveyors Robotics Autonomous Mobile Robots Forklift Trucks Distribution & Warehousing Software Sustainability and Alternative Energy Solutions including Batteries Racks Pallets and Palletizers Order Picking and E-commerce Fulfillment Packaging and Parcel Shipping Solutions These statistics are an early indication of growth of the MODEX event and the high interest attendees in investing in the manufacturing and supply chain equipment and systems that will be showcased at MODEX. MODEX will be held March 11-14 at Atlanta’s Georgia World Congress Center and will be the most important week in 2024 for the manufacturing and supply chain industry. The event will feature over 1,175 exhibits, 200 educational seminars and 5 keynotes. For more information and to register for free admission to attend MODEX, visit modexshow.com.
MHI announces The 2024 MHI Innovation Award finalists
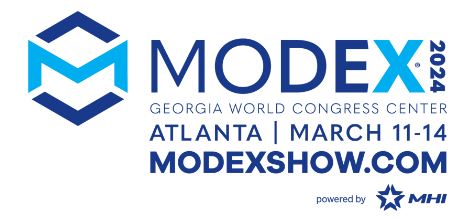
MHI has released the list of finalists for the 2024 MHI Innovation Awards. After receiving 192 submissions for this year’s awards, seven independent judges comprised of professionals from the material handling and supply chain industry completed the initial review process. Three finalists were chosen as the most innovative products in each category based on concept, value, and impact, including the inaugural Best Innovation in Sustainability category. Here are the finalists in no particular order. BEST NEW INNOVATION Dexory Product: Dexory View | Booth Number: B708 Slip Robotics Product: Automated Loading Robots (ALRs)for 5-minute truck loading/unloading | Booth Number: A11318 Geekplus America, Inc. Product: Pallet-to-Person | Booth Number: C6076 BEST INNOVATION OF AN EXISTING PRODUCT Verity AG Product: Autonomous inventory drones featuring coexistence | Booth Number: C3692 Schneider Electric Product: Ecostruxure Expert Twin for Logistics | Booth Number: B7232 ForwardX Robotics Product: Apex C1500-L | Booth Number: B3209 BEST IT INNOVATION Optimal Discovery, LLC Product: Optimal Slotting | Booth Number: B8056 Configura, Inc. Product: CET Material Handling | Booth Number: B7853 Exotec Product: Deepsky from Exotec® | Booth Number: B4202 BEST INNOVATION IN SUSTAINABILITY PAC Machinery Product: PAC FW 650SI INVERTED FLOW WRAPPER | Booth Number: C4488 WAGNER Fire Safety Product: OxyReduct Fire Prevention System | Booth Number: B7845 Avery Dennison Smartrac Product: Logistics Grade Linerless | Booth Number: A10123 The MHI Innovation Award serves to educate and provide valuable insights on the latest manufacturing and supply chain products and services to MODEX attendees. MODEX 2024 exhibitors were called to submit a new product, product line, technology or service or new application of existing products or technology that create quantifiable and sustainable results in terms of ROI, cost savings, customer satisfaction, etc. On Monday, March 11, 2024, finalists move onto the next round of judging and will present their unique solutions to a panel of independent judges on the show floor at MODEX 2024. The winners in each category will be announced at MODEX 2024 on March 13th during MHI Industry Night with Colin Jost. MHI would like to thank the seven industry professionals for graciously volunteering their time as Innovation Award judges. To see more information and learn more about all the Innovation Award entries, visit modexshow.com/innovation-awards. For questions, contact Greg Baer at 704-714-8725.
Yale expands UX lift truck line with two new integrated lithium-ion models
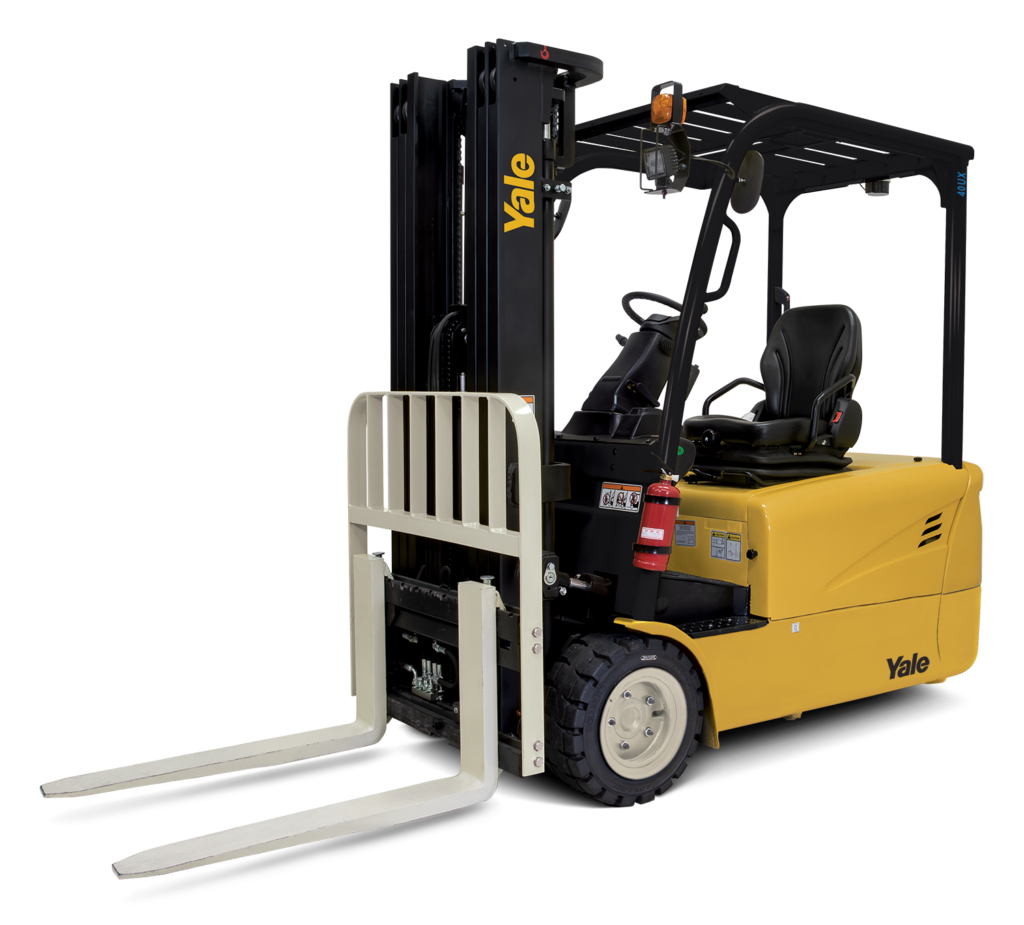
Yale Lift Truck Technologies has announced the launch of two new integrated lithium-ion counterbalanced lift trucks, the three-wheel ERP32-40UXTL and the four-wheel ERP30-70UXL, as part of its cost-effective UX product line. The budget-friendly models are an appropriate fit for applications in retail stores, warehouses, and home centers to take advantage of the benefits of lithium-ion power. “While warehouses have a long history of utilizing electric lift trucks, lead-acid battery power has typically been the default option for occasional to average duty cycle applications, where usage simply did not justify the investment in lithium-ion,” said John Santiago, Director, of Counterbalance Product Planning and Solutions, Yale. “With these new UX models, Yale is making lithium-ion more accessible, and in doing so, delivering on our mission to engineer lift truck solutions that seamlessly integrate advanced technologies and address the demands of today’s warehouses.” The trucks provide reliable performance and the advantages of lithium-ion power in a value-driven package. The lithium-ion battery eliminates the need for a battery changing room, can fully charge in about two-and-a-half hours, and can be opportunity charged during operator breaks to maximize equipment availability during shifts. Lithium-ion produces zero tailpipe emissions and also supports productivity by providing consistent power delivery and requiring zero battery maintenance. While some competitive offerings may rely on third-party battery suppliers or face support and warranty limitations, Yale and its robust dealer network provide service and warranties on the truck, battery, and charger for maximum uptime, productivity, and customer satisfaction. The two models are available with lift capacities in the 3,200-to-4,000-pound and 3,000-to-7,000-pound range, respectively. The trucks also offer several ergonomic features, including a low step height, a small, adjustable steering wheel, and a wide view mast that helps maximize visibility and supports operator comfort. The Yale UX line initially launched in 2020, expanded in 2021 with the addition of electric walkie-trucks, and earlier in 2023 with multiple lead-acid battery-powered models.
Forklifts Group celebrates milestone with opening of its new headquarters
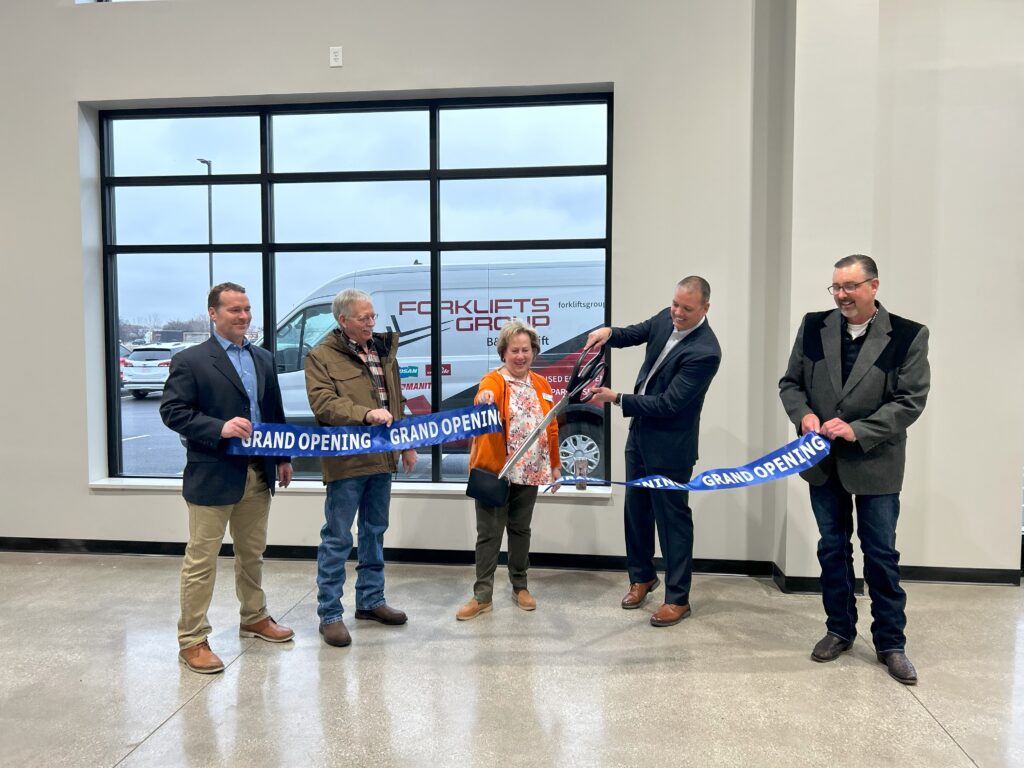
Forklifts Group celebrated the opening of its newly constructed headquarters at 5966 Haughn Road, Grove City, OH 43123, with a ribbon-cutting ceremony and grand opening on January 29, 2024. Forklifts Group welcomed the Grove City Area Chamber of Commerce, community members, employees and the building’s contractors to the new building for a ribbon-cutting ceremony to commemorate the company’s significant milestone. “Thank you to our community partners Grove City, Jackson Township, and the Grove City Area Chamber of Commerce,” said Bill St. John, Forklifts Group President. “You all have been a joy to work with throughout this process. I want to thank our contractor partners, Frazier General Contractors, for all their efforts, all our employees who have worked so hard over the past 18 months and our customers who have allowed us to get to this point. We’re excited about the opportunity this new building presents to be able to grow within the community and on a national scale.” Shawn Conrad, Grove City Area Chamber of Commerce President and CEO, partnered with Forklifts Group to conduct the ribbon-cutting ceremony. “The Grove City Area Chamber of Commerce was honored to participate in the grand opening and ribbon cutting of the Forklift Group’s new headquarters on Haughn Road,” Conrad said. “A perfect location, a beautiful new building and lots of guests made the event very special. Welcome to Grove City, we are very happy to have you as part of our business community.” The 20,480-square-foot Forklifts Group headquarters serves the greater Columbus area for new and used equipment sales, rentals, parts, and service. The facility houses a fully stocked parts department and over 11,000 square feet of space designed for its factory-trained, skilled technicians to service equipment from leading brands such as Bobcat, Linde, Clark, Snorkel, Manitou, Sellick and more.
HexcelPack to debut upgraded automatic dispensing solution for void fill at E-Commerce Packaging & Labeling Expo in London
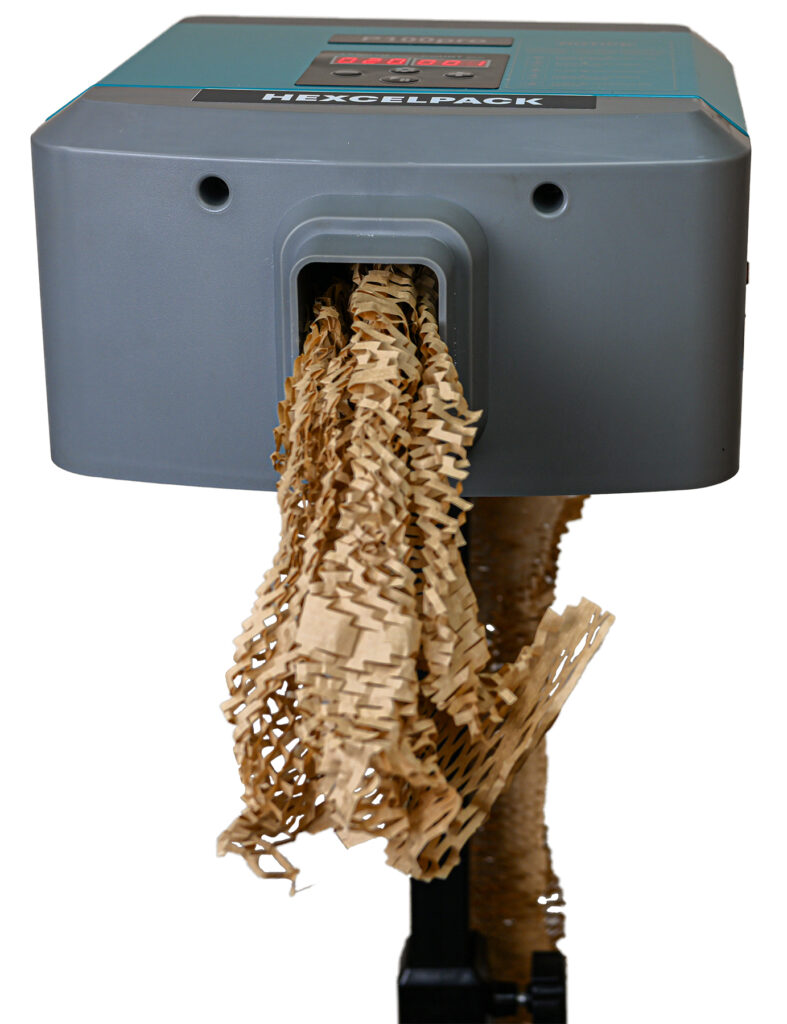
Enhancements include faster packing speeds and several new programming modes. HexcelPack, a developer of eco-friendly, paper-based protective packaging solutions to replace bubble and air pillow packaging and other plastic, paper or foam-based materials, will introduce its upgraded AutoHexaFil™, a fully automatic dispensing solution for its HexaFil™ void fill, at E-Commerce Packaging & Labeling Expo, February 27-28 in London. At Booth PE2501, HexcelPack will showcase the latest iteration of its automatic dispenser, which incorporates several enhancements such as faster packing speeds and several new programming modes. The company’s AutoHexaFil™, which uses a novel cutting technique to dispense the sustainable void fill material into corrugated shippers, now offers packing speeds up to 16% faster than alternative methods. With a programmable screen and electric operation via a foot pedal, the machine quickly dispenses HexaFil™ to the desired length. Four new programming modes are available to ensure supreme cushioning, blocking, and bracing: Cut-to-length bulk bin filling Cut-to-length with a preset quantity Cut-to-length – hold until pulled by the operator Manual continuous length – cut when the foot pedal is released The AutoHexaFil™ is adjustable in height to fit atop packaging conveyor systems and has wheels for easy maneuvering. Recently tested for heavy-duty work cycles, the AutoHexaFil™ is durable, allows for quick and easy paper reloading, and – evidenced by one million cycles of testing – is virtually jam-free. Aside from its enhanced product introduction, the company has been selected as a finalist for the show’s Sustainable Packaging Award, which recognizes companies breaking boundaries across various sectors of the e-commerce, packaging, and labeling sectors. HexcelPack is one of four nominated companies whose products, services or strategies have been recognized for outsized impact and influence in their specific marketplace. “At HexcelPack, our team is dedicated to sustainable packaging solutions that offer unsurpassed product protection while minimizing environmental impact,” said Lorne Herszkowicz, Partner at HexcelPack. “We are thrilled to be introducing our newly enhanced AutoHexaFil™ at the E-Commerce Packaging & Labeling Expo, and look forward to connecting with many like-minded industry professionals.”
Schneider Electric delivers next-generation, open automation infrastructure in collaboration with Intel and Red Hat
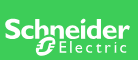
New Distributed Control Node (DCN) software framework to help drive open automation The solution helps replace vendor-specific hardware with plug-and-produce offer Interoperability and portability support industrial innovation, reduce obsolescence Schneider Electric, a digital transformation of energy management and automation, in collaboration with the technology companies Intel and Red Hat, has announced the release of a Distributed Control Node (DCN) software framework. An extension of Schneider Electric’s EcoStruxure™ Automation Expert, this new framework enables industrial companies to move to a software-defined, plug-and-produce solution, allowing them to enhance their operations, ensure quality, reduce complexity, and optimize costs. Next generation of industrial control Aligned with the goals of the Open Process Automation Forum (OPAF), which is dedicated to driving interoperability and portability, the three collaborators have worked together to create a modern, network-based experience that will lead the way to the next generation of industrial control. “This project is the culmination of two years of co-innovation to create efficient, future-proof distributed control systems,” said Nathalie Marcotte, Senior Vice President of Process Automation at Schneider Electric. “The DCN framework is key to fostering an open automation approach, enabling industrial businesses to grow and innovate for the future. Its interoperability and portability help our customers enjoy the freedom of shaping technology around their business needs – and not the other way around.” Red Hat, in collaboration with Intel, has announced the creation of a new industrial edge platform that helps provide a modern approach to building and operating industrial controls. Since implementing this platform, Schneider Electric has now deployed Red Hat Device Edge in the new DCN software, in addition to Red Hat Ansible Automation Platform and Red Hat OpenShift at the compute layer for DCN deployments, combined with a control infrastructure from Schneider Electric and reference architecture from Intel. The framework consists of two main components: an advanced computer platform (ACP), which supervises the control workload by providing the content control and automation capabilities needed to deploy workloads securely and programmatically, along with virtualization and monitoring functionalities; and the DCN, which are low-power, industrial systems using Intel Atom x6400E series processors, dedicated to running controls and designed for workloads f mixed-criticality. “Open and interconnected commercial solutions will help usher in the transition from fixed function proprietary devices to flexible and dynamic software-based infrastructures,” said Christine Boles, Vice President of Intel’s Network and Edge Group and General Manager for Federal and Industrial Solutions. “Intel has a long history of driving open system approaches across its ecosystem. This collaboration with Schneider Electric and Red Hat to develop a software-defined control system showcasing next-generation distributed control nodes built on general-purpose compute and operating systems brings about this transition to the industrial sector.” “Red Hat is committed to helping manufacturers implement autonomous operations on the shop floor,” said Francis Chow, Vice President and General Manager of In-Vehicle Operating System and Edge at Red Hat. “By working closely with our partners like Schneider Electric and Intel, we can help build scalable, software-defined factories and operations capable of advanced automation and interoperability by utilizing a consistent platform approach. We’re excited about this collaboration, and this is only the beginning. By taking these steps now, we can help set the industrial sector up to explore all the possibilities AI, edge computing and more have to offer.”
How to select a proper dock lift for your operation
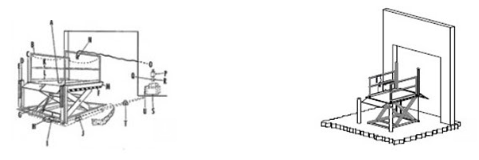
Hydraulic Dock Lifts have two advantages over other means of unloading trucks: Level unloading from the bed of a truck is safer than any other alternative, and Loading Dock Lifts are the only type of equipment that can reach from ground level to all sizes of trucks ranging from low step vans to large refrigerated reefers. There is no vehicle size that dock lifts cannot service. Once you realize the benefits of level loading with dock lifts, the next question is which type of loading dock lift system best fits your application and what options should you consider. Top of Ground Style or Pit Mounted Recessed Lift The first consideration is which of these hydraulic truck lift alternatives is best for your application. Top of Ground Advantages These units can be mounted on any flat concrete slab (units will sink into blacktop during the summer) and require no pit work. This not only avoids the cost of a pit, but also drainage issues and potential interference with underground utilities. If you decide to move the unit later (we have reports of units providing as many as 35 years of continuous service) it is an easy matter to unbolt the unit and move it with no pit left to fill in. Capacities range from 4,000 lbs. up to 15,000 lbs. and platform sizes range from 6’ X 6’ up to 8’ X 12’. The cost of top-of-ground units are always higher than the cost of recessed units, however, when the cost of pit construction is added to the equipment prices, top-of-ground units can be competitive. Recessed or Pit Mounted Advantages The equipment costs for these units are always less expensive than top-of-ground units. The biggest advantage is the fact that these hydraulic dock lifts are mounted flush with surrounding surfaces so they do not become an obstacle to drive over traffic. This is especially important if the unit is being mounted in a doorway. Top-of-ground units have ramps that transition loads from the platform to ground level which is fine for offloading operations but can be tiring if heavy loads must be pushed up the ramps for loading trucks. Standard capacities of recessed units range up to 20,000 lbs. Recessed units offer level loading both at ground level and at truck height. If recessed units are mounted within the face of docks they can provide easy dock-to-ground access, although top-of-ground units can do the same if the approach ramps are shortened and the units are mounted immediately adjacent to the dock. Platform Size The platform size is primarily determined by the type of transport equipment that will be used to load or unload trucks. The minimum suggested platform width is 6’. Guardrails use 4” to 8” of usable platform width on some models and there should be at least 4” of clearance on each side of the widest load such as a 48” wide pallet for ease of maneuvering. In some cases, the loads may be wider and some users like to unload two pallets side by side so 7’ and 8’ wide platforms are common options. If the loads are four-wheeled carts or baskets, or the loading equipment is limited to two wheeled hand carts, then a 6’ platform length is sufficient. For manual pallet jacks, 8’ platform lengths are considered minimum. Powered pallet jacks work best with 10’ lengths to comfortably fit the load, powered pallet jacks and operator all in line. Straddle stackers also fit well on 10’ platforms. Fork trucks are much longer so they generally require platforms in the 10’ to 12’ range. The size range mentioned above covers 99% of all applications and is now available as standards in both top-of-ground and recessed styles of loading lifts. Unusual loads may require custom-designed units with platform widths of 10’ or 12’ and platform lengths of up to 65’. If you have special requirements, a full-service supplier can help you design a perfect fit. Capacities Lifting Capacity Once a platform size has been determined, it is a simple matter of adding up the maximum weight of the goods being transferred, the weight of the transport equipment and the weight of an operator to arrive at a lifting capacity. Axle Rating Capacity The axle loads on manually propelled carts and pallet jacks are too light to be of concern. Manual pallet jacks divide payload weight evenly between two axles, but powered pallet jacks and straddle stackers often concentrate 60% of the combined payload and equipment weight on their rear axle and they can move heavier loads than manual equipment. Fork trucks usually concentrate 80% of the maximum payload plus fork truck weight on the front axle, but some unusual trucks may run as high as 90% concentrations. Most manufacturers have appropriate end load axle ratings for corresponding maximum lifting capacities, but there is always the danger that you have unusual equipment and/or if your application requires traveling over the side of the lift in anything other than the fully lowered position, there is a possibility that the side axle rating is marginal. It is wise to compare the axle loads produced by your equipment vs. the rating of the dock lifts to be safe. Roll Over Capacity This only applies to recessed units and refers to the maximum axle load allowable for vehicles driving over a fully lowered lift. Most recessed dock lifts are rated for 10,000# axle load slow speed drive over. This is usually more than adequate because of state mandated limits on truck axle loads. However, large specialty vehicles and high capacity fork trucks with small hard wheels can exceed these limits. In those cases, warn the lift manufacturer and they can modify the lifts to accommodate larger loads with thicker deck plates and other forms of reinforcement. Power units and controls The up-down controls must be controlled by the operator riding on the lift. Any other scenario is a sure recipe for an accident. Standard controls for most companies are NEMA 4 pushbuttons. These are
B&B Attachments travels to the Big 5 Construct Saudi
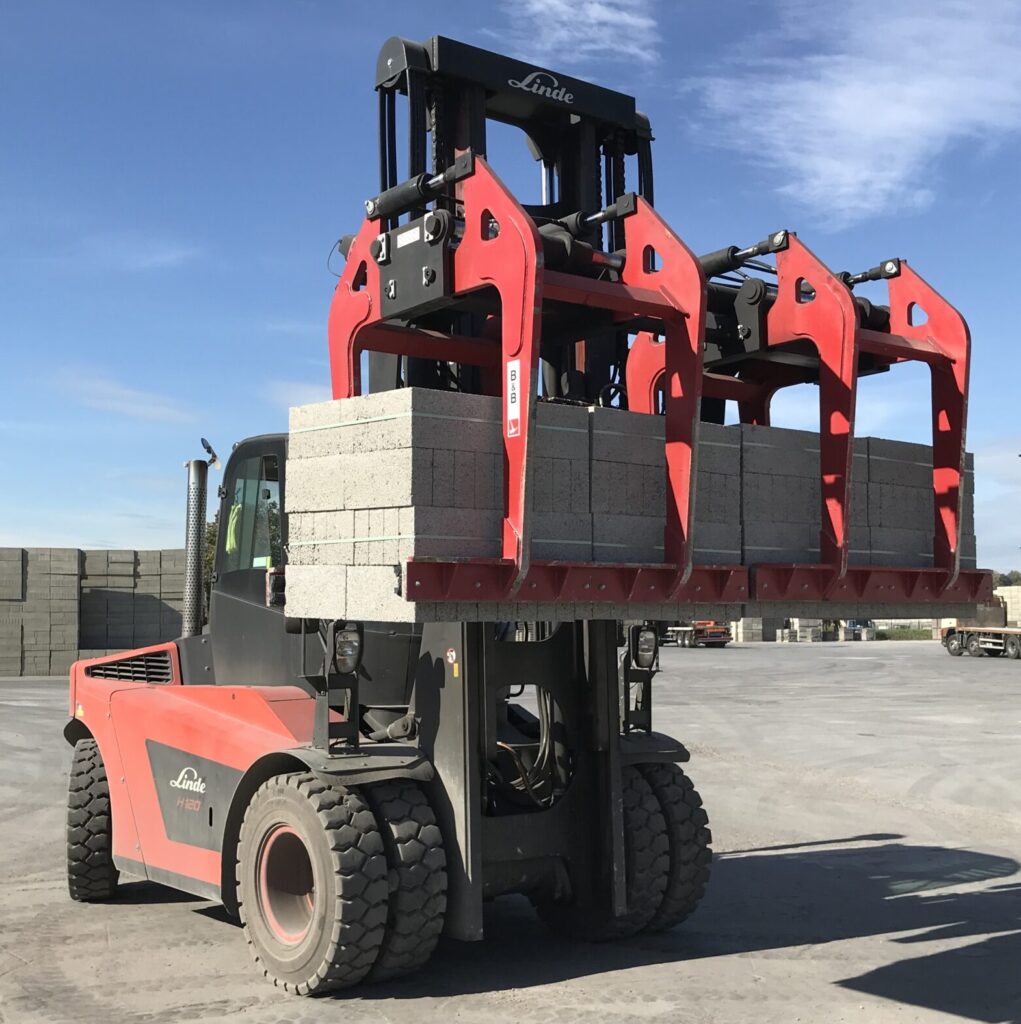
Big 5 Construct Saudi, returns for its 12th edition to the Riyadh Front Exhibition and Conference Center, February 26th to 29th 2024. Exhibiting for the first time in Saudi is a UK-based manufacturer of material handling solutions, B&B Attachments, supporting its official dealer for the region; GOTRADE of the GORICA GROUP. “We are excited to participate in BIG 5 Saudi Construct, Saudi Arabia’s largest construction event. This event provides the ideal platform for us to showcase our material handling solutions to a global audience. Our BlockMaster range, manufactured in our UK facility, comprises a collection of specialist forklift truck attachments designed for material handling within the building products industry.” Comments Mike Barton, Managing Director at B&B Attachments. Mike continues, “The development of the construction industry in the Middle East presents an abundance of opportunities for us to expand further into this ever-growing market. Our (BlockMaster) range offers a unique, cost-effective, solution for handling brick, block, and concrete products.” Founded in 1980, B&B Attachments has grown to become the UK’s leading independent supplier of forklift truck attachments and masts, offering the widest range of products available from a single source.
Mitsubishi Logisnext Americas group showcases Jungheinrich® and Rocrich AGV Solutions™ at MODEX 2024

Mitsubishi Logisnext Americas group (Logisnext), a North American provider and manufacturer of material handling and innovative automation and fleet solutions, has announced its participation in MODEX 2024, one of the world’s leading manufacturing and supply chain shows. The conference will take place March 11 – 14 at the Georgia World Congress Center in Atlanta, GA. At this year’s event, Logisnext will showcase its cutting-edge Jungheinrich® warehouse products and introduce Rocrich AGV Solutions™ the exclusive provider of Jungheinrich and Rocla® AGVs and AMRs in North America. Attendees will discover how to maximize their material handling operations through advanced solutions, like automated guided vehicles, semi-automation technology, e-mobility, and digital fleet management tools, including Logisnext’s Lift Link® telematics solution. “We’re excited to showcase our latest innovations in warehouse solutions at MODEX 2024,” said Jerry Sytsma, executive vice president, sales and aftermarket services at Mitsubishi Logisnext Americas. “Logisnext remains dedicated to providing state-of-the-art material handling, mobile automation and fleet management solutions to meet the industry’s changing needs. We invite attendees to join us at the show and discover the future of logistics.” Schedule of Events Product Demonstrations at Jungheinrich Booth #B9019 Jungheinrich EKS 215a Automated Guided Vehicle Pallet Stacker Rocla ART Automated Reach Truck Product Exhibit at Jungheinrich Booth #B9019 EKX 516 Turret Truck with Warehouse Navigation EKS 314 High-Level Order Picker Lift Truck Solutions Fleet Management Tool Lift Link Telematics Live Demonstration Exclusive Educational Seminar at Emerging Technologies Theater A Roadmap to Mobile Automation Success: Your Journey from Idea to Operation Led by Rocrich AGV Solutions President, Brian Spradlin, and Director of Integrator and Direct Sales, Brian Markison Tuesday, March 12: 12:30 – 1:15 p.m.
NOBLELIFT® AGV technology wins significant award
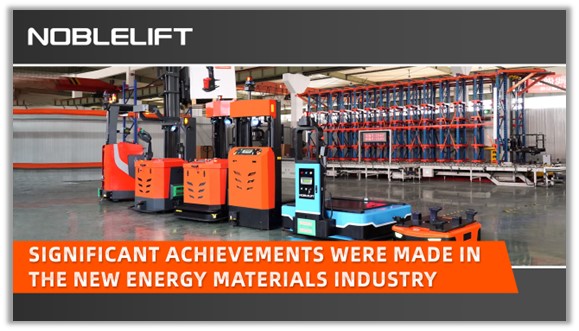
NOBLELIFT wins the High-Tech Golden Globe Award for their AGV Technology at the 2023 High-Tech Mobile Robot Annual Conference held in Hefei China. NOBLELIFT‘s dedication and proactive attitude in the new energy materials industry have been recognized by various organizations and partners and they have achieved numerous accomplishments. At the High-Tech Mobile Robot Annual Conference and High-Tech Golden Globe Awards Ceremony, NOBLELIFT’s AGV technology of “High-Precision Positioning and Control Technology for Omni-directional Movement of Mobile Robots” stood out and won the “2023 Technology” High-Tech Golden Globe Award. This award highly affirms NOBLELIFT’s achievements in the field of heavy-duty AGVs in the new energy materials industry. During the event, Mr. Mao, the General Manager of NOBLELIFT AGV division, delivered a speech as an outstanding representative of the mobile robot industry and participated in roundtable discussions with industry experts to envision the future. Through innovation in six key areas, namely “distribution of coil materials for new energy material production equipment,” “distribution of coil materials for baking equipment,” “distribution of coil materials for cutting equipment,” “automatic threading of copper foil rolls,” “automatic packaging of foil roll products,” and “three-dimensional warehousing of copper foil products,” NOBLELIFT supported the new energy materials industry and improved the efficiency for production, material handling, packaging, and warehousing systems. As a result, it successfully secured purchase requests from Smart Factories logistics solution worth nearly ¥100,000,000. The project will produce 50,000 tons of new energy materials annually. NOBLELIFT has invested many years, significant finances, and team resources in their AGV technology. We have developed various types of AGVs and intelligent logistics software, including forward-type, counterbalance-type, and narrow-aisle side-insertion-type AGVs, which are widely used globally in various industries. We are proud of our AGV team and our most recent award. Through innovation in six key areas, namely “distribution of coil materials for new energy material production equipment,” “distribution of coil materials for baking equipment,” “distribution of coil materials for cutting equipment,” “automatic threading of copper foil rolls,” “automatic packaging of foil roll products,” and “three-dimensional warehousing of copper foil products,” NOBLELIFT supported the new energy materials industry and improved the efficiency for production, material handling, packaging, and warehousing systems. As a result, it successfully secured purchase requests from Smart Factories logistics solution worth nearly ¥100,000,000. The project will produce 50,000 tons of new energy materials annually. NOBLELIFT has invested many years, significant finances, and team resources in their AGV technology. We have developed various types of AGVs and intelligent logistics software, including forward-type, counterbalance-type, and narrow-aisle side-insertion-type AGVs, which are widely used globally in various industries. We are proud of our AGV team and our most recent award.
TAPPI/AICC announce Shawn DuBravac to Keynote at SuperCorrExpo® 2024
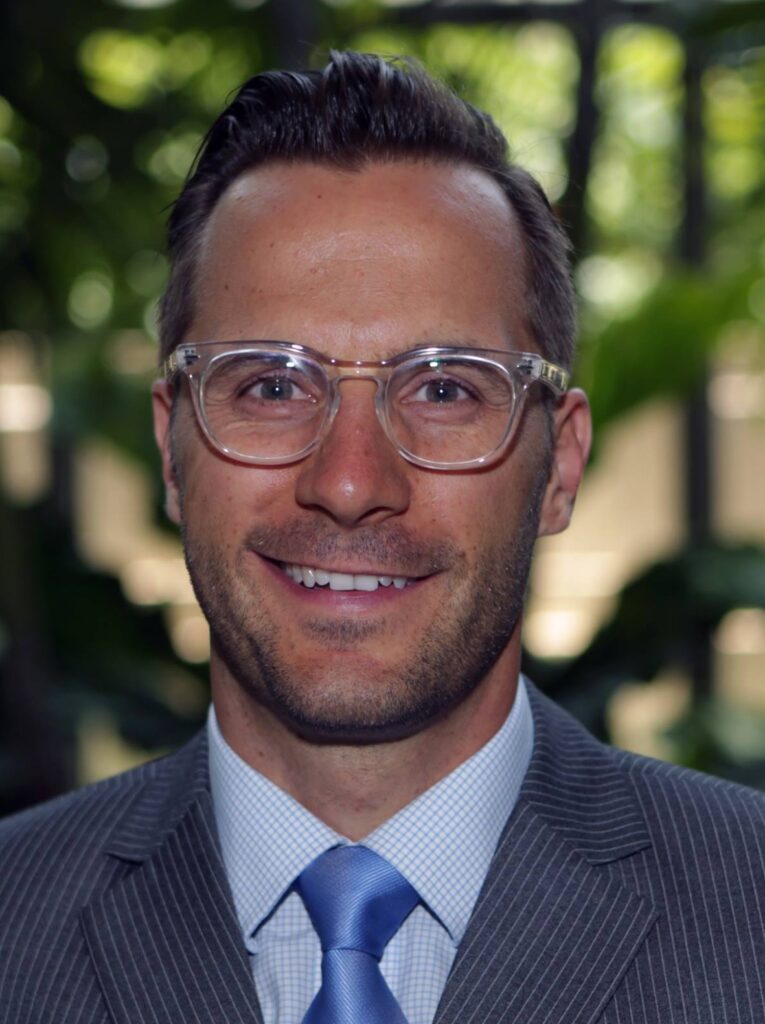
TAPPI and AICC, co-producers of the mega corrugated event SuperCorrExpo® (SCE) 2024, has announced Shawn DuBravac will be the opening keynote speaker at the corrugated industry’s quadrennial event taking place September 8-12, 2024 in Orlando, FL. Acclaimed futurist and trendcaster Dr. Shawn DuBravac is the author of the New York Times Best Seller Digital Destiny: How the New Age of Data Will Transform the Way We Work, Live, and Communicate, which explores how the world’s mass adoption of digital technologies portends the beginning of a new era for humanity in the realms of business, healthcare, finance, transportation, and culture. DuBravac is an internationally recognized thought leader and top-rated keynote speaker, delivering pragmatic and provocative insights on the trends, technologies, and paradigms transforming the globe. His research focuses on the forces shaping tomorrow that are percolating on the periphery of society and business today. By providing an elevated view of developing trends, DuBravac empowers leaders and their organizations to improve strategic decision-making capabilities by understanding the changing landscape and identifying the opportunities that lie ahead. Shawn is joining a distinguished group set to keynote at SuperCorrExpo®, including Emmy Award-winning sports broadcaster Greg Gumbel and Jake Hall, known for his industry-leading platform The Manufacturing Millennial. “We are incredibly excited for Shawn DuBravac to join us at SuperCorrExpo®,” said TAPPI CEO and President Larry N. Montague. “He offers expertise and insights relevant to the future of our industry and adds a valuable perspective to our well-rounded keynote program.” “SuperCorrExpo® is the rare opportunity we get every four years to hear from expert thought leaders in our industry, and also sit next to them in sessions to ask questions and share ideas.” said TAPPI President and CEO Larry N. Montague. “Conversations and commerce both happen at SuperCorrExpo. That’s what makes it such a success for attendees and exhibitors.” SuperCorrExpo® 2024 takes place at the Orange County Convention Center in Orlando, FL. Considered one of the most influential corrugated packaging-focused trade shows in the Western Hemisphere, SCE brings together more than 6,000 producers and suppliers from over 70 countries. A record number of representatives from corrugated manufacturers from around the world are expected to attend in 2024. “SuperCorrExpo® 2024 is on track to be a must-visit event.” said AICC President Michael D’Angelo. “With an exceptional lineup of speakers and exhibitors from around the globe, we are eagerly anticipating robust learning opportunities, exciting networking, and unparalleled prospects for growth.”
BigRentz surpasses 14,000 supplier locations
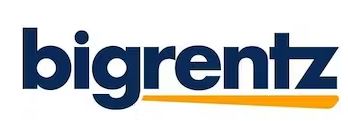
The company reaffirms its commitment to improving customer experience by developing & investing in new technology, capabilities & features BigRentz has announced the significant achievement of surpassing 14,000 construction rental equipment supplier locations nationwide, further cementing the company’s position as a trusted industry leader and partner to equipment rental houses of all sizes. These new and existing locations make up one of the sector’s largest networks of suppliers and ensure that builders, technicians, developers, contractors, and others have access to the equipment they need, regardless of project size, location, or complexity. In addition to affirming its dedication to providing every industry professional with the equipment they need to complete projects on time and budget, BigRentz is also doubling down on its commitment to invest in and develop new technology to consolidate rental management in one, easy-to-use platform. The company’s strategic outlook introduces new capabilities and features both to improve the supplier experience and to meet the evolving needs of the broader industry. “We are grateful to our valued supplier partners who’ve helped us achieve this milestone and made BigRentz the go-to platform for construction equipment rentals,” said BigRentz CEO Scott Cannon, CEO. “We have big goals at BigRentz and we don’t plan to stop at 14,000 supplier locations. In addition to our goals of supporting our suppliers and growing our network, we’re doubling down on developing and improving technology needed to not only simplify the equipment rental process but also help clients solve other complicated challenges, be those related to staffing, finances or any other problem they may face.” Founded in 2012, BigRentz boasts a network of more than 6,000 equipment partners throughout the USA, giving renters access to 14,000 equipment yards through their platform. The company’s digital platform has helped redefine the rental sector, simplifying equipment procurement and project management, providing customers access to real-time data and reporting, and making costs and budgets easy to track across multiple projects. BigRentz offers an expansive range of equipment categories including aerial platforms like scissor lifts, material handling such as forklifts, heavy and earthmoving equipment, and cranes as well as job site services like dumpsters, generators, and light towers. This comprehensive offering distinguishes BigRentz from competitors, allowing customers to secure all necessary equipment from a single source. The milestone of surpassing 14,000 supplier locations is a prelude to the era of BigRentz as the go-to construction technology solution and rental provider. As the industry undergoes digital transformation, BigRentz reinforces its role in reshaping how construction businesses approach technology and resources.
Point of Rental Software acquires Record360
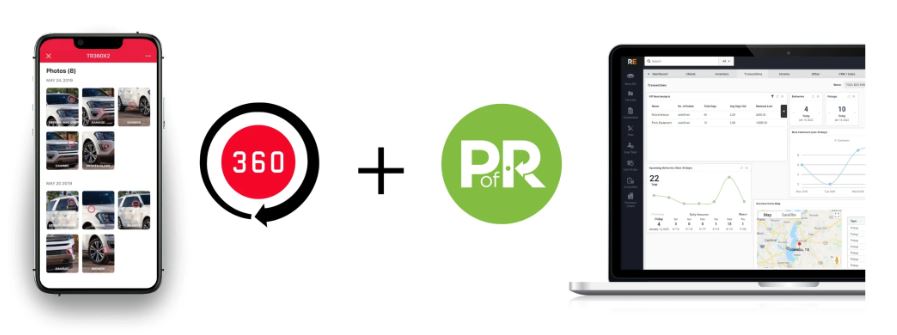
Acquisition to Expand Rental Inspection Software’s Reach Worldwide Record360, a rental inspection software solution, has been acquired by Point of Rental Software, the largest company globally in rental management software. The acquisition is designed to fuel Record360’s product development and growth, allowing the team to accelerate the pace of product innovation, increase its global footprint, and continue setting the standard for mobile digital documentation tools. “Point of Rental aligns with our values of bringing innovative products to market while focusing on responsible long-term growth and customer service,” said Record360 CEO Abby Chao. “Because our products are complementary, Record360 customers will benefit as we discover new features we can build into our product.” Record360 will continue to operate as its own business entity, adding inspection software to Point of Rental’s valuable suite of RMS-independent solutions, which also include e-commerce, consumer portal, electronic signature collection, and integrated payments. “We see immense potential in the abilities of Record360 to transform the industry and we’re excited to combine our resources to realize that potential,” said Point of Rental CEO Wayne Harris. “We’ll continue to prioritize Record360’s autonomy and increase integration points through the Open API so that any ERP system can fully integrate with Record360.” Leadership from both organizations will talk about the future of the united business at Point of Rental’s pre-ARA Show happy hour in New Orleans on Feb. 18. For those not able to attend, they’ll also host an online webinar to share the vision for Record360 in the weeks after the show.
Episode 460: Meet Squid, a most unique end-to-end warehouse automation solution from BionicHive
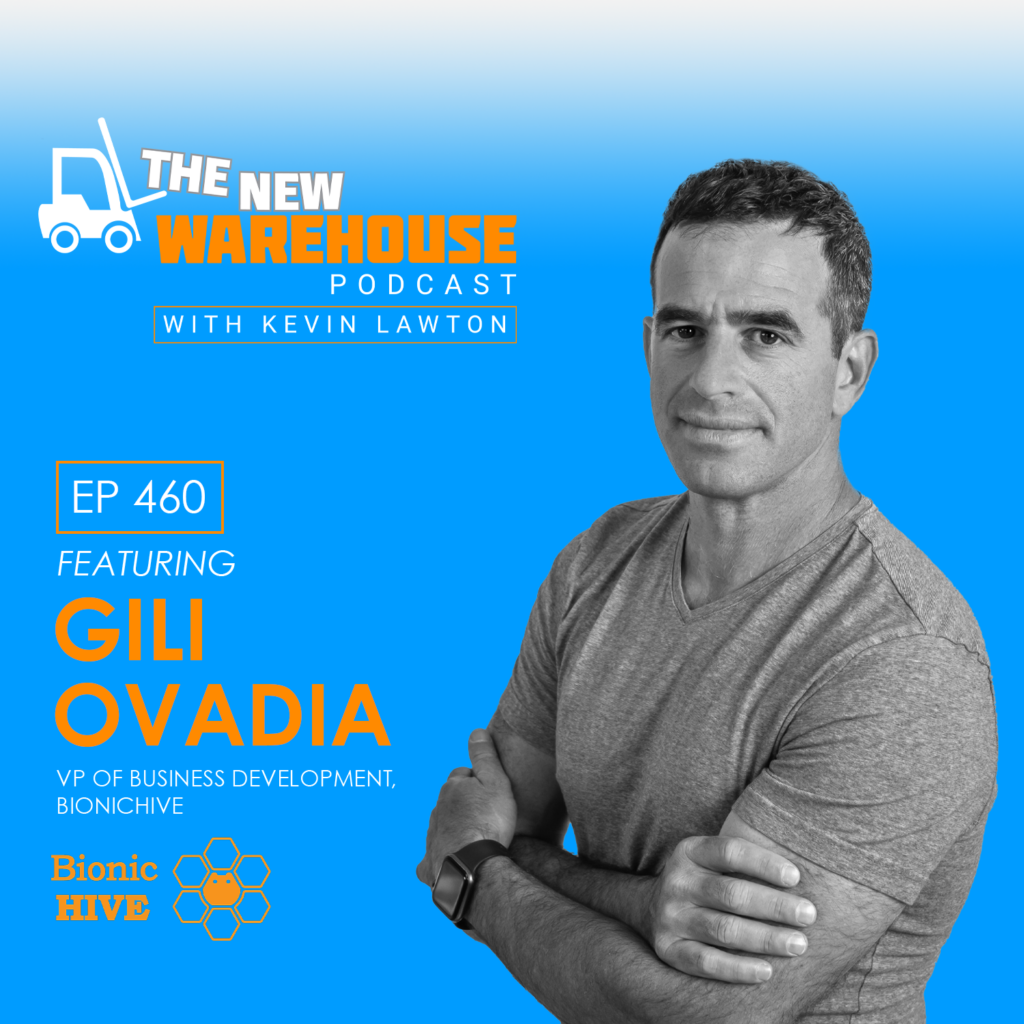
When is it good for things to be crawling around your warehouse? You’ll find out on this episode of The New Warehouse Podcast featuring Gili Ovadia, VP of Business Development at BionicHive. Gili discusses their innovative robotic solution, Squid, which uniquely navigates warehouses in three dimensions. Established in 2016, BionicHive aims to provide a flexible automation solution to warehouses, enhancing efficiency and adaptability. This episode delves into Squid’s origin, design, and potential, highlighting recent achievements, including investments and pilot programs with industry giants. Origin and Design of Squid Gili Ovadia explains Squid’s development, which is rooted in a blend of defense industry expertise and innovative technology. “The original idea came from… the defense industry,” Ovadia shares, describing Squid’s capability to move vertically and horizontally across warehouse racks, offering unparalleled flexibility. This multidisciplinary approach resulted in a robot that enhances operational efficiency without needing warehouse modifications. Flexibility and Efficiency in Automation Discussing Squid’s advantages, Ovadia emphasizes its flexibility and utility in various warehouse tasks, from replenishment to returns. “We’ve combined [elevation and horizontal movement]… it’s the flexibility,” he notes. Squid’s design allows for dynamic adaptation to warehouse demands, showcasing its potential to streamline operations across different sectors. Future Directions and Impact Ovadia outlines BionicHive’s ambitions to scale their technology, focus on commercial deployments, and enhance the product. “We want to… deploy three commercial deployments throughout 2024,” he states, highlighting the importance of adapting to customer needs and integrating seamlessly with existing warehouse management systems. This forward-looking perspective underlines BionicHive’s commitment to revolutionizing warehouse automation. Key Takeaways BionicHive’s Squid offers a novel approach to warehouse automation, capable of navigating in three dimensions. Flexibility and adaptability are core to Squid’s design, enabling it to work with existing infrastructure and meet various warehouse operational needs. BionicHive is poised for significant growth, focusing on commercial deployments and continuous innovation. The New Warehouse Podcast Episode 460: Meet Squid, a most unique end-to-end warehouse automation solution from BionicHive
Episode 459: Managing Rapid 3PL growth and insights into the 3PL landscape with Renewal Logistics
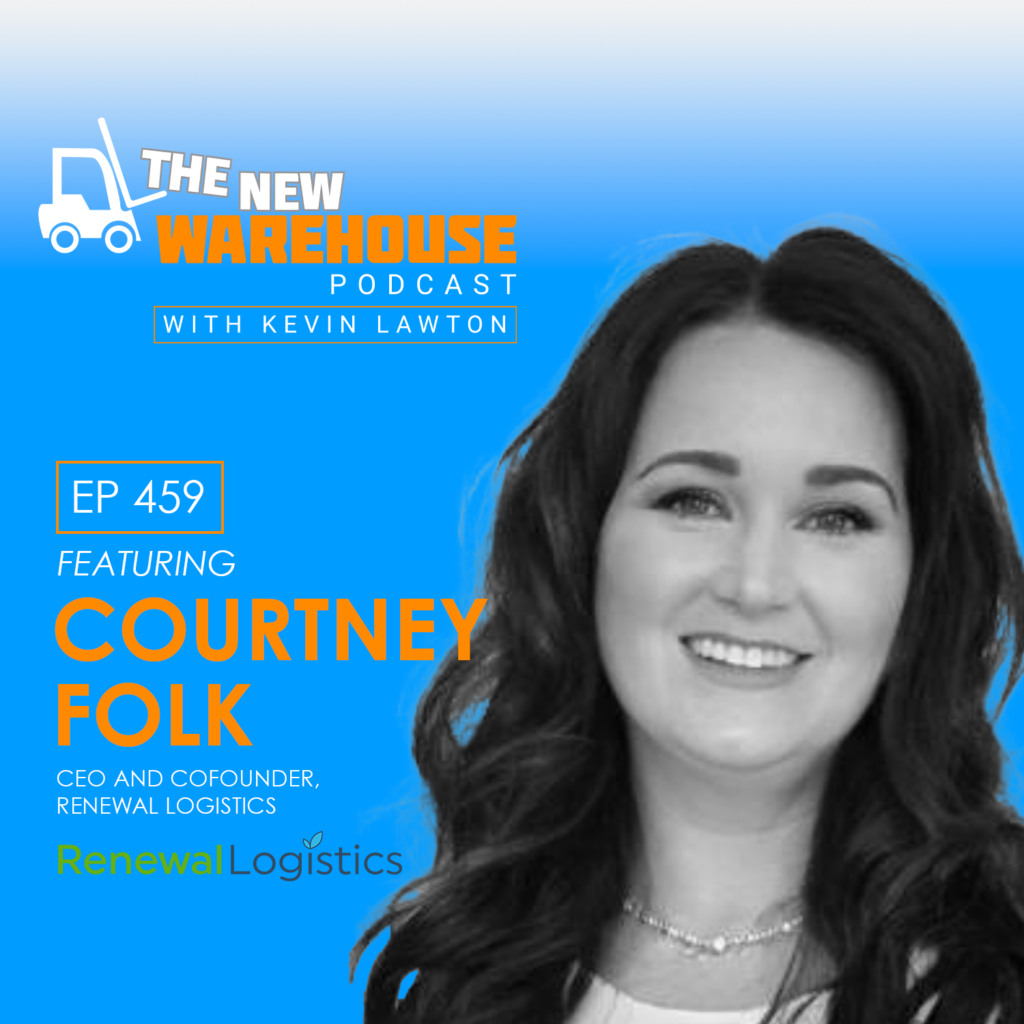
In this episode of The New Warehouse Podcast features Courtney Folk, CEO and Co-Founder of Renewal Logistics. We delve into Courtney’s intriguing journey in the logistics industry and the unique challenges and innovations of Renewal Logistics. Courtney brings a wealth of experience and insights into the evolving landscape of third-party logistics (3PL) and offers a fascinating perspective on the industry’s future. The Adventurous Beginnings of Renewal Logistics Courtney details the transition from a dry-cleaning business to a significant player in logistics thanks to their successful handling of a challenging project involving 300,000 mold-contaminated jeans. They completed this task two days early, demonstrating impressive scaling capabilities and operational efficiency. This achievement earned them a reputation for excellence in the logistics industry and led to a substantial increase in business volume and a deeper partnership with a major global brand. Renewal Logistics’ growth continued through word-of-mouth, establishing a dedicated facility adjacent to their client’s site. Managing Rapid 3PL Growth at Renewal Logistics Courtney discusses the rapid growth of Renewal Logistics and the challenges of managing sudden business expansion. She attributes their success to the synergistic partnership with her husband, Brian, and shares some key points she learned along the way: Leveraging Personal Strengths – Combining Courtney’s business acumen and Brian’s math and process planning expertise. Strategic Delegation – Utilizing relationships and delegating to experts for efficient operations scaling. Adaptability in Crisis – Embracing business challenges with a resilient mindset developed through personal experiences. Focus on Teamwork – Recognizing the importance of collaborative efforts in achieving rapid growth and overcoming obstacles. Their mindset and skill in cultivating connections and entrusting tasks to specialists empowered them to expand operations and conquer intricate logistical obstacles effectively. Navigating the Evolving 3PL Landscape and Embracing Automation Courtney discusses the complexities and future of the 3PL industry, emphasizing the challenges and opportunities it presents. She highlights the importance of identifying a specific customer profile, particularly in the apparel sector with high return rates. Courtney points out the critical role of managing property inflation and labor costs in this evolving landscape. She also touches on the strategic use of automation, mentioning Renewal Logistics’ approach to integrating software for process planning rather than extensive on-floor automation, tailoring their services to each client’s unique needs. This approach allows for a more integrated solution, combining returns, outbound fulfillment, and other services under one roof. Key Takeaways Targeted Customer Focus: Courtney emphasizes identifying a specific customer niche in the 3PL industry, particularly those requiring specialized services like high-return rate management in apparel. Navigating Economic Challenges: She highlights the impact of inflation on property and labor costs, stressing how these factors critically affect the 3PL business strategy. Balanced Automation Approach: Courtney discusses Renewal Logistics’ strategic use of software for process planning, allowing them to manage diverse client needs efficiently without over-reliance on physical automation. The New Warehouse Podcast EP 459: Managing Rapid 3PL Growth and Insights into the 3PL Landscape with Renewal Logistics