AutoScheduler wins big at BGSA
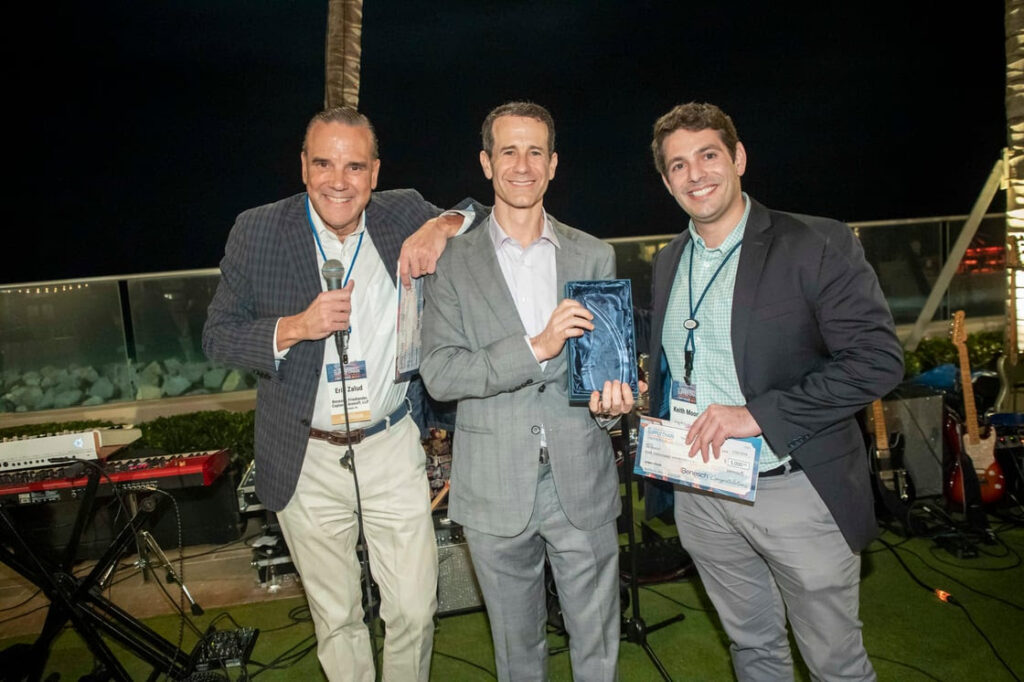
Named the next big winner in the Supply Chain Industry; clean sweep of both categories – Judge’s Choice and People’s Choice AutoScheduler.ai, an innovative Warehouse Management System (WMS) accelerator, has announced the company has won the BG Strategic Advisors (BGSA) Supply Chain “Shark Tank” competition. Selected from a record number of applicants representing many high-caliber companies, the six finalists presented their concepts to three judges and over 350 industry decision-makers proactively looking for innovative investment opportunities. AutoScheduler took home both the Judge’s Choice and the People’s Choice Awards. Awards included $5,000 in cash provided by former Shark Tank Winner Venti and $10,000 in services by Benesch. “Being recognized by peers and top industry leaders from all segments of the supply chain as a top supply chain technology is a testament to all the team’s hard work for creating this innovative technology. We were thrilled to be named a finalist in the BGSA 2024 Supply Chain ‘Shark Tank’ competition, but we were blown away with our clean sweep of both the Judge’s Choice and People’s Choice categories. Many thanks to all the wonderful people at BGSA.” Keith Moore, Chief Executive Officer, AutoScheduler.AI The BGSA 2024 Supply Chain “Shark Tank,” sponsored by G&P, is the ultimate platform for innovative startups to showcase their potential. This exciting event features six finalists handpicked by a panel of esteemed supply chain leaders, each vying for the top spot. Each startup was able to present its story and field questions about its business model, innovation, and strategy. It’s not just about impressing the judges; the audience played a pivotal role, too. Both the “Sharks” and audience members had the opportunity to vote for the startup they believe is most deserving of the title of the next big winner in the supply chain industry, and AutoScheduler was named the winner!
Haver & Boecker Niagara engineers the Largest vibrating grizzly screen
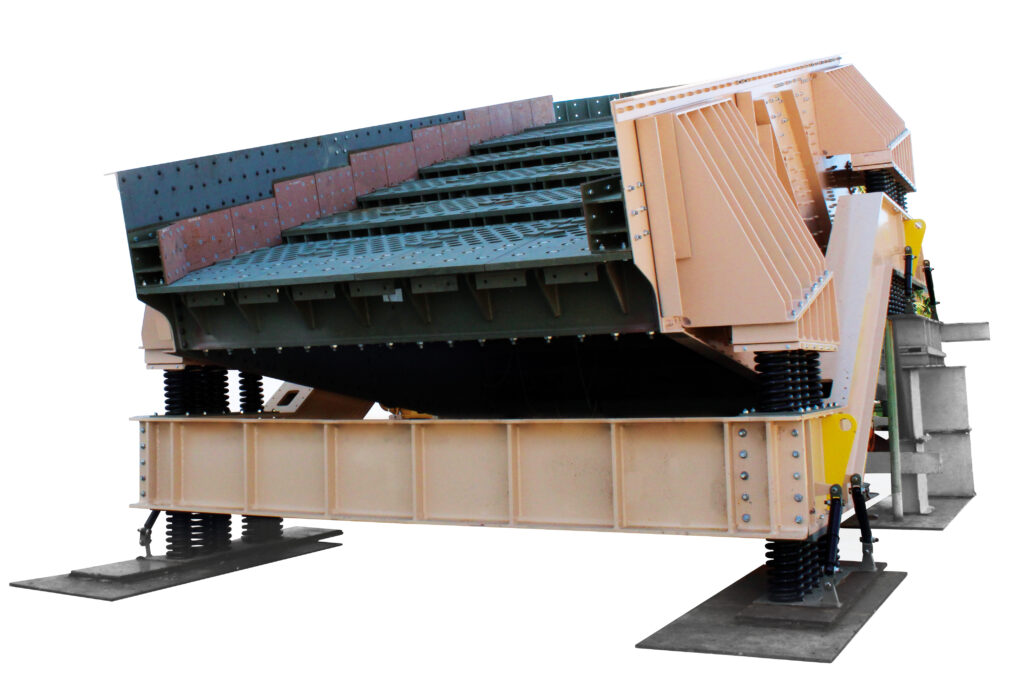
Haver & Boecker Niagara custom-engineers the largest vibrating grizzly screen in the world. Manufactured with Hardox® steel perforated plates and grizzly bars for a large Brazilian iron ore operation, the Niagara XL-Class vibrating grizzly screen boasts a capacity of 8,000 tph and a cut size of 200 mm. As the largest exciter-driven machine in the industry, the XL-Class provides the operation with high-capacity screening while maximizing uptime and production. Combined with the grizzly technology, the XL-Class offers the necessary ability to remove large stones, relieving pressure on the primary crusher. At 120 tons, the machine’s size required a modular approach, so Haver & Boecker Niagara engineered the XL-Class vibrating grizzly screen as two bodies. With this customization, the 1.3-meter particles did not allow for the normal placement of exciters, resulting in adjusting the design to place three exciters beneath each body rather than the standard overhead location. Effectively screening material top sizes of 1.3 meters, the XL-Class grizzly vibrating screen removes oversized materials to relieve the crusher. “We recognize that no two operations are the same, which is why Haver & Boecker Niagara takes the time to understand each of our customers and their needs for every new quarry or mine location,” said Denilson Moreno, sales manager at Haver & Boecker Niagara. “We have worked with this customer for many years, but as they began production at what is the largest iron ore operation in the world, we realized to truly maximize output, it would require a durable and extremely efficient primary screen. That’s what led us to engineer and manufacture this XL-Class, which is now the largest vibrating grizzly screen on the market.” Haver & Boecker Niagara listened to the operation’s challenges and employed their signature NIAflow plant simulation software to address them. The software analyzed the proposed plans, processes, goals, and material for plant optimization, providing information to the customer and Haver & Boecker Niagara to design and custom engineer the one-deck vibrating grizzly screen. To maximize uptime, the customer opted to equip the XL-Class vibrating grizzly screen with Haver & Boecker Niagara’s signature Pulse condition monitoring (Pulse CM) system. The advanced technology provides the producer with 24/7 access to the health of its vibrating screen. Pulse CM includes up to 20 sensors placed on the bearings and bodies, which continually assess the acceleration of the machine and provide a forecast of the equipment’s dynamic condition in intervals of 48 hours, five days, and four weeks. Additionally, the sensors capture real-time information on the monitored equipment and send e-mail alerts to the producer at the first sign of system anomalies. The collected data provides insights into preventive maintenance opportunities, the ability to catch possible issues before they cause unplanned downtime and the peace of mind that the machine is running at peak efficiency. “Our goal is not only to provide our customers with top-tier equipment but to act as a true consultant and partner to them,” said Clayton Carvalho, managing director of Haver & Boecker Niagara’s Brazil operation. “With more than 150 years of experience in the mining and aggregates industry, we are proud of the equipment and technology that we can offer as well as the knowledge and expert service we bring to our customers.”
Midwest Association of Rail Shippers welcomes new officers and announces summer meeting dates
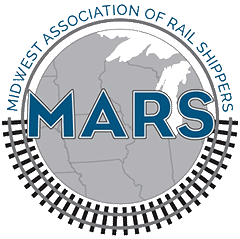
The 2024 Executive Committee was introduced at the recent Winter Meeting of the Midwest Association of Rail Shippers (MARS). The Winter Meeting set a record for MARS with more than 980 attendees. Among the many topics covered was how North American railroads—functioning as a more efficient network—can gain market share of North American freight. The 2024 MARS elected officers are: President Matt O’Kray, Transtar; First Vice President, Steve Blinn, Norfolk Southern Railroad; and Second Vice President, Luke Jones, GATX Corporation. The Immediate Past President is Kathy Bathurst. “It’s an honor to step into my new role,” says O’Kray. “I look forward to building on the momentum that Kathy and the board established this past year. It made MARS stronger than ever. We have an excellent team in place, and plans are already underway for a memorable Summer Meeting.” There is one new member of the MARS Executive Committee: Tony Kazakevicius, Director of Sales & Marketing, Chicago South Shore & South Bend Railroad. The next gathering will be the Summer Meeting on July 8-9 and will be held in conjunction with the MARS Scholarship Golf Outing at the Grand Geneva Resort in Lake Geneva, Wisconsin.
Nucor reports results for the Fourth Quarter and Full Year 2023
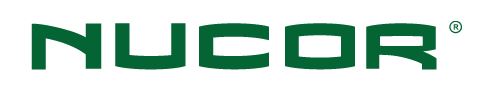
Fourth quarter and full year 2023 diluted EPS of $3.16 and $18.00, respectively. Fourth quarter and full year 2023 net earnings before noncontrolling interests of $872.8 million and $4.91 billion, respectively; EBITDA of $1.36 billion and $7.41 billion, respectively. 2024 is expected to be another strong year as Nucor executes its strategy to grow the core and expand its portfolio of solutions. Capital deployment is expected to increase in 2024 with planned capital expenditures of $3.5 billion, continued evaluation of acquisitions, and share repurchases set to outpace the prior year. Nucor Corporation has announced consolidated net earnings of $785.4 million, or $3.16 per diluted share, for the fourth quarter of 2023. By comparison, Nucor reported consolidated net earnings of $1.14 billion, or $4.57 per diluted share, for the third quarter of 2023 and $1.26 billion, or $4.89 per diluted share, for the fourth quarter of 2022. For the full year 2023, Nucor reported consolidated net earnings of $4.52 billion, or $18.00 per diluted share, compared with consolidated net earnings of $7.61 billion, or $28.79 per diluted share, in 2022. “The Nucor team delivered a strong finish to 2023, which represents the third-most profitable year in our Company’s history. Nucor’s strategy to grow our core steelmaking capabilities and expand beyond into steel-adjacent business lines continues to deliver strong results,” said Leon Topalian, Nucor’s Chair, President, and Chief Executive Officer. “Over the past four years, Nucor has generated an average annual ROE of 33% and has returned approximately $9.7 billion to its shareholders through dividends and share repurchases. We remain optimistic that Nucor’s best days are ahead of us, with a resilient U.S. economy and steel-intensive megatrends driving increased demand for our products. With our strong balance sheet and a broad array of sustainable steel solutions, we believe Nucor is unparalleled for its ability to leverage these market drivers for continued growth.” Financial Review Nucor’s consolidated net sales decreased 12% to $7.70 billion in the fourth quarter of 2023 compared with $8.78 billion in the third quarter of 2023 and decreased 12% compared with $8.72 billion in the fourth quarter of 2022. Average sales price per ton in the fourth quarter of 2023 decreased 8% compared with the third quarter of 2023 and decreased 15% compared with the fourth quarter of 2022. Approximately 5,934,000 tons were shipped to outside customers in the fourth quarter of 2023, a 5% decrease from the third quarter of 2023 and a 3% increase from the fourth quarter of 2022. Total steel mill shipments in the fourth quarter of 2023 decreased 4% compared to the third quarter of 2023 and increased 8% compared to the fourth quarter of 2022. Steel mill shipments to internal customers represented 20% of total steel mill shipments in the fourth quarter of 2023, which was unchanged from the third quarter of 2023 and the fourth quarter of 2022. Downstream steel product shipments to outside customers in the fourth quarter of 2023 decreased 11% from the third quarter of 2023 and decreased 14% from the fourth quarter of 2022. For the full year 2023, Nucor’s consolidated net sales of $34.71 billion decreased 16% compared with consolidated net sales of $41.51 billion reported for the full year 2022. Total tons shipped to outside customers in 2023 were approximately 25,205,000 tons, a decrease of 1% from 2022, while the average sales price per ton in 2023 decreased 15% from 2022. The average scrap and scrap substitute cost per gross ton used in the fourth quarter of 2023 was $397, a 4% decrease compared to $415 in the third quarter of 2023 and a 7% decrease compared to $427 in the fourth quarter of 2022. The average scrap and scrap substitute cost per gross ton used in the full year 2023 was $421, a 14% decrease compared to $492 in the full year 2022. Pre-tax, pre-operating and start-up costs related to the Company’s growth projects were approximately $127 million, or $0.39 per diluted share, in the fourth quarter of 2023, compared with approximately $101 million, or $0.31 per diluted share, in the third quarter of 2023 and approximately $73 million, or $0.22 per diluted share, in the fourth quarter of 2022. In the full year 2023, pre-tax, pre-operating and start-up costs related to the Company’s growth projects were approximately $400 million, or $1.21 per diluted share, compared with approximately $247 million, or $0.71 per diluted share, in the full year 2022. Overall operating rates at the Company’s steel mills were 74% in the fourth quarter of 2023 as compared to 77% in the third quarter of 2023 and 70% in the fourth quarter of 2022. Operating rates for the full year 2023 increased to 78% as compared to 77% for the full year 2022. Included in the results for the fourth quarter of 2022 was an after-tax net benefit of $60.4 million, or $0.24 per diluted share, related to state tax credits and an after-tax net benefit of $88.0 million, or $0.34 per diluted share, related to a change in the valuation allowance of a state deferred tax asset. Also included in the fourth quarter of 2022 results was a pre-tax $96.0 million, or $0.29 per diluted share, write-off of the remaining carrying value of the Company’s leasehold interest in unproved oil and gas properties that is included in the raw materials segment. Financial Strength At the end of the fourth quarter of 2023, Nucor had $7.13 billion in total liquidity, not including the Company’s $1.75 billion revolving credit facility. Nucor continues to have the strongest credit ratings in the North American steel sector (A-/A-/Baa1) with stable outlooks at Standard & Poor’s, Fitch Ratings and Moody’s. Commitment to Returning Capital to Stockholders On December 14, 2023, Nucor’s Board of Directors declared a cash dividend of $0.54 per share. This represents a 6% increase over the prior cash dividend, and is payable on February 9, 2024 to stockholders of record as of December 29, 2023. Nucor has increased its regular, or base, dividend for 51 consecutive years – every year since it first began paying dividends in 1973. During the fourth quarter of 2023, Nucor repurchased approximately 1.0 million shares of its common stock at an average price of $177.18 per share (approximately 9.75 million shares during the full year 2023 at an average price of $159.34 per share). As of December 31, 2023, Nucor had approximately $3.32 billion, or 26 million shares, remaining authorized and available for repurchases under its share repurchase program. This share repurchase authorization is discretionary and has no scheduled expiration date. For the full
Episode 458: Elevating E-Commerce Operations – An insightful journey with Linnworks
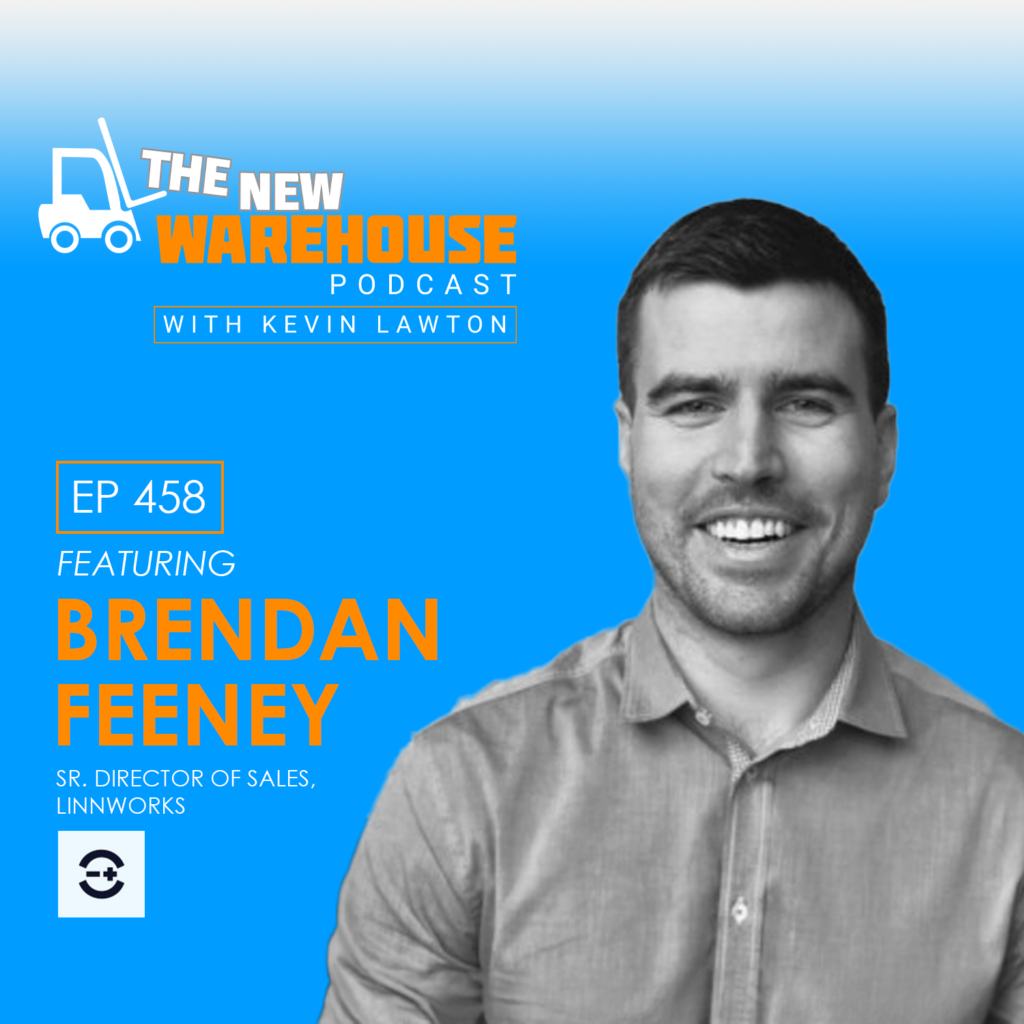
Welcome to Episode 458 of The New Warehouse Podcast, featuring an in-depth discussion with Brendan Feeney, Director of Sales for North America at Linnworks. Linnworks serves as an orchestration layer, enabling brands to connect with multiple sales channels, including websites, marketplaces, and retailers. Linnworks specializes in synchronizing inventory levels, managing orders, and assisting with forecasting. Dive into a world of e-commerce operations, where Linnworks’ innovative approaches are revolutionizing brand and shipper experiences across various platforms, including social commerce. Get ready for an enlightening session exploring the intricacies of today’s e-commerce landscape and find out how to enter for a chance to fund your Super Bow parth with SkuBowl. The Evolution and Impact of Linnworks Brendan describes Linnworks as more than just a software solution; it’s an essential tool for e-commerce businesses navigating the complexities of online sales. “Linnworks really becomes the central nervous system of a company’s e-commerce operations,” he explains. The platform offers a seamless integration of inventory and order management across multiple channels, ensuring that businesses can keep up with the fast-paced, ever-changing demands of the online retail world. Essentially, they manage the backend activities from the point of purchase to fulfillment, incorporating elements of IMS (Inventory Management System), OMS (Order Management System), and WMS (Warehouse Management System), along with capabilities in product listing and management. Brendan emphasizes the importance of having a system that manages these processes and provides valuable insights into sales trends and consumer behavior. SkuBowl: A Revolutionary Marketing Approach The SkuBowl is an innovative marketing initiative by Linnworks to engage the e-commerce community. Brendan elaborates on this unique concept, “It’s a way for us to connect with our customers and the wider e-commerce community in a fun, interactive way.” Participants engage with industry-related videos, earn badges, and enter raffles. It’s a unique way for the e-commerce community to engage in a light-hearted, interactive experience while gaining valuable insights. Mastering Warehouse Fulfillment and Inventory Challenges Discussing the complexities of warehouse management and inventory control, Brendan highlights Linnworks’ role in streamlining these critical aspects of e-commerce. He points out, “Effective inventory management is crucial. You need to know what you have, where it is, and how quickly it needs to move.” Linnworks helps businesses overcome these challenges by providing tools for efficient multichannel fulfillment, ensuring that orders are processed and shipped promptly. This aspect of Linnworks proves indispensable for businesses looking to maintain high customer satisfaction and operational efficiency in an increasingly competitive online marketplace. Key Takeaways from Linnworks Central Nervous System for E-commerce Operations: Orchestration and execution systems are integral tools for e-commerce, effectively managing backend activities and serving as a central hub for inventory, order, and warehouse management systems. SkuBowl – Engaging Marketing Strategy: The SkuBowl initiative highlights Linnworks’ innovative approach to marketing and education, blending fun and interactive ways to connect with the e-commerce community. Efficiency in Fulfillment and Inventory Management: Streamlining warehouse management and inventory control is crucial for maintaining high customer satisfaction and operational efficiency in the competitive online marketplace. The New Warehouse Podcast EP 458: Skubowl with Linnworks
Raymond President and CEO accepted into Fast Company Executive Board
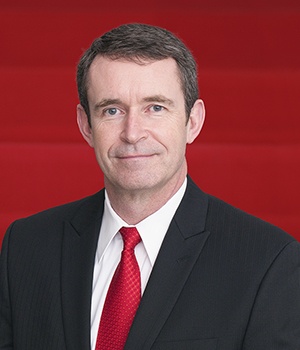
Mike Field, president and CEO of The Raymond Corporation, a provider of material-handling products and intelligent intralogistics solutions, has been accepted onto the Fast Company Executive Board, a professional organization of company founders and senior executives passionate about technology and design. Field was selected to join the board based on his proven technology expertise in the manufacturing industry. As a member, Field joins industry-leading peers in technology, marketing, advertising, social impact, media, entertainment, corporate leadership, creative design, nonprofit, and social responsibility. “I am honored to have been selected to join the prestigious Fast Company Executive Board, a community synonymous with innovation, leadership, and forward-thinking excellence,” Field said. “I look forward to contributing to this community of leaders embracing the spirit of innovation. I am honored to lead a company with a legacy of innovation spanning over a century and eager to share and gain insights from other leaders on Raymond’s journey to continuous improvement as we look to the future beyond Industry 4.0.” Founded in 2021, the Fast Company Executive Board gives members access to a curated network of company founders and senior executives through a private online platform. They help one another solve business challenges, make connections, and share information through lively discussions, virtual events, and online chats.
Cyclonaire Corp welcomes Jason Hablitzel as Application Engineer Supervisor
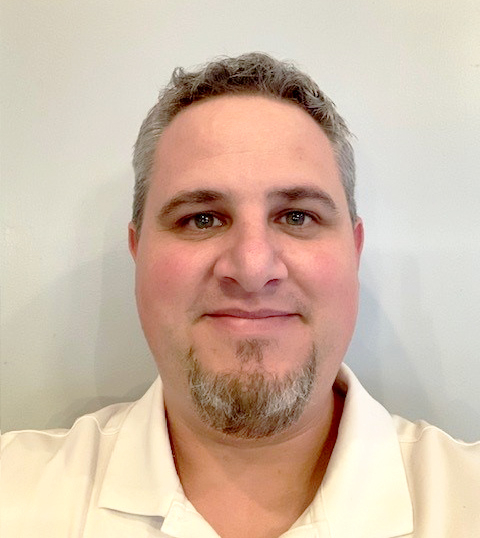
Cyclonaire Corporation, a provider of innovative material handling solutions, has announced the appointment of Jason Hablitzel as the Application Engineer Supervisor. Jason will bring his extensive expertise to lead the application engineering team, ensuring the delivery of high-quality solutions to our valued clients. With a Bachelor’s degree in Mechanical Engineering from the University of Nebraska, Jason possesses a strong academic background that aligns seamlessly with Cyclonaire’s commitment to excellence. Notably, Jason returns to Cyclonaire with prior experience, having been a valuable member of our team from 2006 to 2016. His previous contributions and in-depth knowledge of our products and industry dynamics make him an invaluable asset to our organization. “We are thrilled to welcome Jason back to Cyclonaire as the Application Engineer Supervisor. His proven track record, coupled with his engineering acumen, will undoubtedly strengthen our team’s capabilities,” said Mike Colella, Vice President Sales and Marketing at Cyclonaire. Jason’s role as Application Engineer Supervisor will involve overseeing the application engineering department, collaborating with cross-functional teams, and driving innovative solutions for our clients. His return signifies a commitment to maintaining and enhancing the high standards of engineering excellence for which Cyclonaire is renowned. Jason will also be responsible for Cyclonaire’s state-of-the-art Test Lab providing oversight for customer material testing and reporting. Cyclonaire looks forward to the positive impact Jason will undoubtedly bring to the organization and anticipates continued growth and success under his leadership.
New battery test & assembly system from McAlister Design & Automation
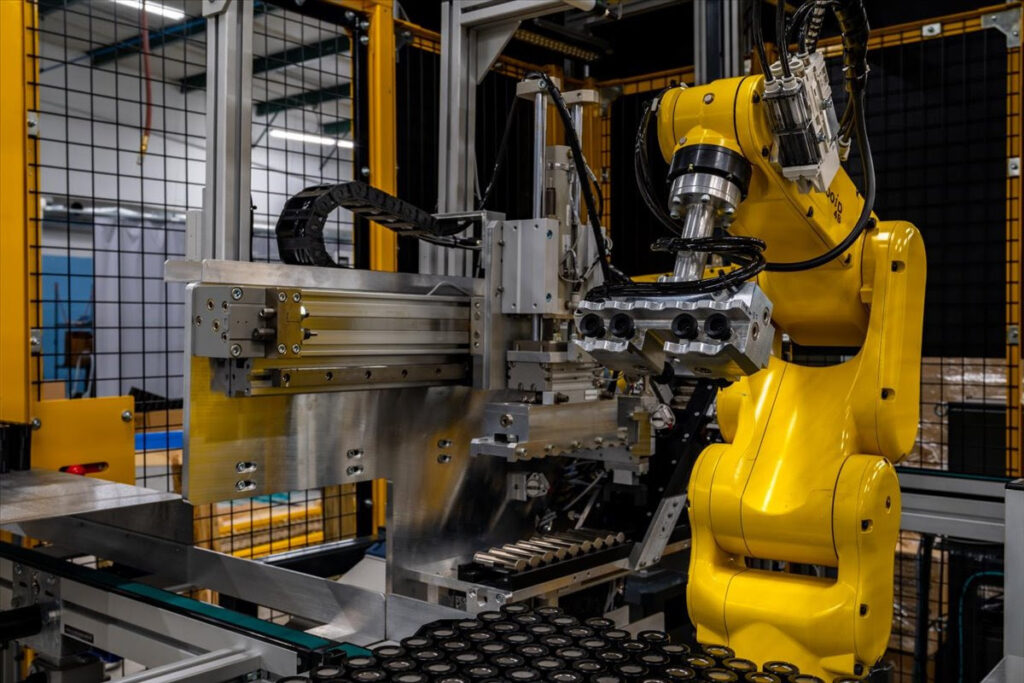
The system enables pre-pack manufacturing testing of battery cells and battery cell performance data storage capabilities McAlister Design & Automation, a subsidiary of Wauseon Machine, revealed its new Battery Test and Assembly System. This battery system enables the inspection and testing of battery cells and assembly of battery packs, commonly used in electric vehicles and consumer products. The system has been developed to support market changes and future growth. The Battery Test & Assembly system allows battery pack manufacturers to ensure the quality of their product meets or exceeds the requirements for its design. The Battery Test and Assembly System tests each battery cell before incorporating it in the pack, mitigating the number of packs that falter because of a potential issue with a single battery cell. McAlister Design & Automation designed this system in response to the rapid increase in demand for electric vehicles, power tools, and electronic residential equipment. The system utilizes industry-standard battery cell packaging, minimizing the amount of operator handling during the introduction to the testing and assembly process. Additionally, McAlister Design & Automation modeled the Battery Test & Assembly System around the 2170 battery for broader application benefits, including the many industries previously mentioned. In today’s market, data tracking and storage enables traceability and is a critical aspect of manufacturing operations. This Battery Test & Assembly system features the capability to capture, store, and analyze battery cell and pack data. This grants manufacturers the ability to trace battery pack and cell performance over the entire life cycle of their product—enabling manufacturers to manage incoming supplier quality and trace defects across their value stream. The system has a unique focus on flexibility—using vision guidance for robotic components, six-axis robots, and conveyors—allowing the system to be modified or reconfigured for varying battery sizes or battery pack configurations. The system design also features asynchronous testing and assembly stations, maximizing its throughput and minimizing the amount of time it takes to assemble a battery pack. Plus, its pre-engineered software makes for an easily scalable and adaptable system to accommodate hazardous lithium-ion batteries. The system offers integrated dunnage inspection, providing fire hazard mitigation and a safer working environment for system operators.
New dimmable BackLit LED flat panel lights offer selectable wattage & color temperature
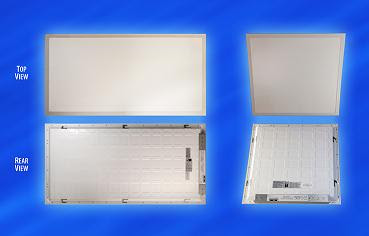
Introducing a breakthrough in lighting technology: LEDtronics® unveils its series of Backlit LED Ceiling Panel Lights. These multi-mode, dimmable flat panels feature tunable wattage and white color temperature options. The UL-listed panels feature continuous dimming and directly replace fluorescent troffers in most standard recessed T-bar ceilings. In addition, the luminaire series can also be surface mounted with optional aluminum surface mounting frames, or ceiling-suspended with optional steel wire cables. “This new backlit technology makes the flat panel much more efficient and gives it a longer life,” says LEDtronics president Pervaiz Lodhie. “It keeps it cooler with better heat dissipation, more stability of color, intensity, and lumens.” The Torrance, California-based company recently celebrated its 40 years of LED lighting research, marketing, and production. Available in 2×2 and 2×4 ft sizes, the lightweight CLLxCTxDBL series of tunable LED flat panel lights are ideal replacements for fluorescent fixtures and tube lights in recessed luminaires. Their ultraslim profile fits seamlessly into standard dropped troffer and parabolic fixtures in most T-bar ceilings. Offering the flexibility to customize wattage in 5 or 10-watt increments and adjust color temperature from 3000 Kelvin (warm white) to 5000K (pure white), these thin panels can provide the desired ambiance in a multitude of industrial or commercial spaces in offices, retail and convenience stores, hotels, resorts, conferences rooms, classrooms, and healthcare environments, among others. The Title 24 compliant panels offer continuous dimmability with external 0-10V dimmers, with no flicker. They feature a white-trim plastic frame and a frosted white polystyrene diffuser plate that offers high light uniformity and transmission. The 2×2 foot LED panel light offers variable wattage in 5W increments, from 20W to 35W, and programmable white color temperatures: 3000K, 3500K, 4000K or 5000K. The 2×4 foot LED panel light has a variable wattage of 30W, 40W, or 50W, with a tunable choice of 3500K, 4000K or 5000K white colors. They all operate within a voltage range of 120 to 277VAC, delivering a total light output ranging from 2603 lumens at 20 watts/3000K, to 6422 lumens at 50 watts/5000K. This translates to lighting efficacies averaging 145 lumens per watt. The luminaires offer energy savings of up to 75 percent over fluorescent fixtures and tubes. As an example, a LEDtronics 2×4 ft panel light at 50W/5000K replaces 75W T12CWFL; 85W T12 (800mA) FL; 59W and 65W-T8FL. Additionally, the minimal lamp heat output of LEDs over that produced by fluorescent tubes keeps temperatures in offices and hallways optimally lower, saving building air-conditioning costs. The LEDtronics panel lights boast a long lifespan, with lumen maintenance over 70 percent at more than 50,000 hours. The solid-state design of the “CT” LED panel lights renders them impervious to shock, vibration, frequent switching, and environmental extremes, while their LM80-rated superbright SMD2835 LED chips provide high-lumen and greater than 80 CRI uniform illumination in a 120° wide beam-free of ultraviolet radiation or RF interference, low infrared, no glass, no lead or mercury. The LEDtronics CLLxCTxDBL series of tunable and multimode LED flat panel lights come with an unconditional 5-year U.S. factory warranty, and they are available through LEDtronics distributors. Quantity discounts are available, and other product options, such as a 90-minute/10W emergency power pack or a 1×4 panel size, are available for qualified volume orders.
Omega Design Corp. hires New Regional Sales Manager
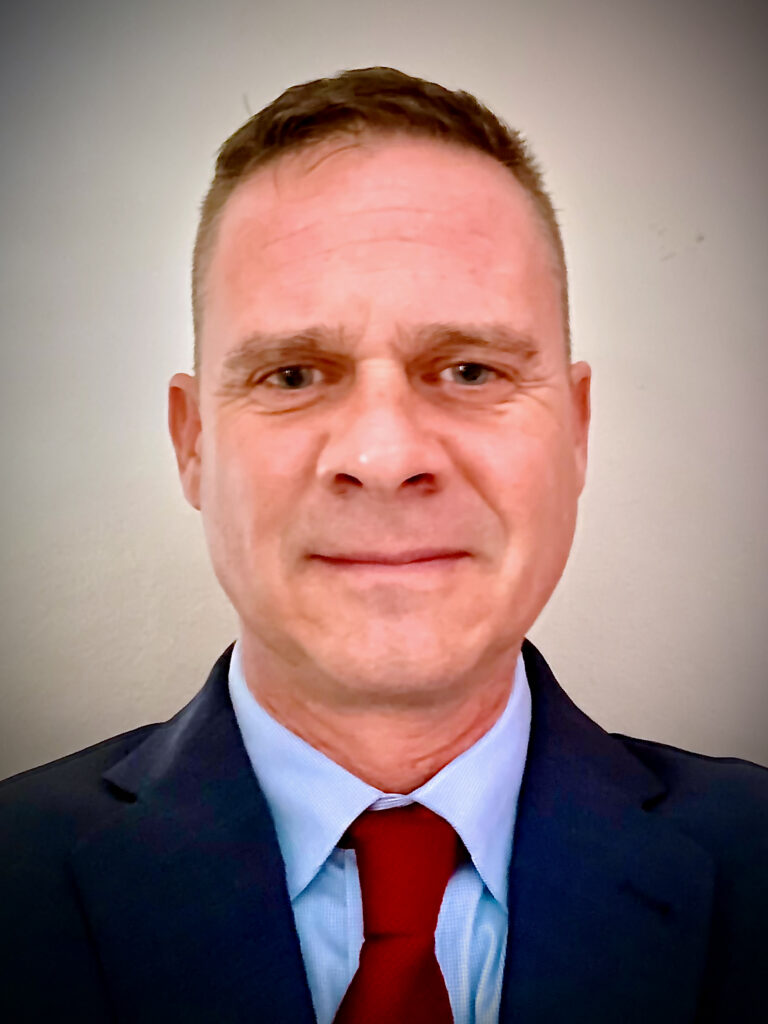
Experienced sales executive Matthew Powers will lead sales efforts for prominent packaging machinery provider throughout the North-Central United States Omega Design Corporation has hired industry veteran Matthew Powers as its newest Regional Sales Manager. Reporting directly to the Director of Sales Operations, Powers will be responsible for developing and maintaining customer relationships, expanding overall sales, and extending Omega Design’s market share in the North Central US region. Powers brings a wealth of sales and entrepreneurial experience to his role with Omega Design. Among other positions, he served as Western US Sales Manager for pharmaceutical solid-dose equipment supplier Freund-Vector Corp., National Sales & Business Head for packaging and coding machinery company Pharmapack North America Corp., and Senior Global Sales Engineer for tableting equipment manufacturer Thomas Engineering. Earlier in his career, he owned a successful water filtration and purification company. Powers joins Omega Design at a promising time. The company is rolling out several new solutions aligning with growing market needs, including desire for increased automation. For example, Omega Design recently introduced an Automatic Robotic Bottle Unscrambler, which provides smarter sorting with a pick-and-place robot module that separates, orients, and positions bottles onto a conveyor or into stabilizing pucks. The versatile module is ideal for applications running complex or multiple bottle shapes, including a broad array of containers, bottles, tottles, jars, vials, jugs and tubes. “Matthew has an impressive record of sales generation and customer relationship building – and an equally impressive roster of established, executive-level contacts at an array of pharmaceutical and nutritional companies,” said Glenn Siegele, President of Omega Design Corporation. “His diligence and people skills will serve him well at Omega Design, as we continue to introduce new solutions for an ever-evolving pharma and nutritional manufacturing landscape.” Powers earned degrees in mathematics and molecular biophysics at the University of Illinois. He resides in Wisconsin.
Keen Utility Kenton for Spring 2024
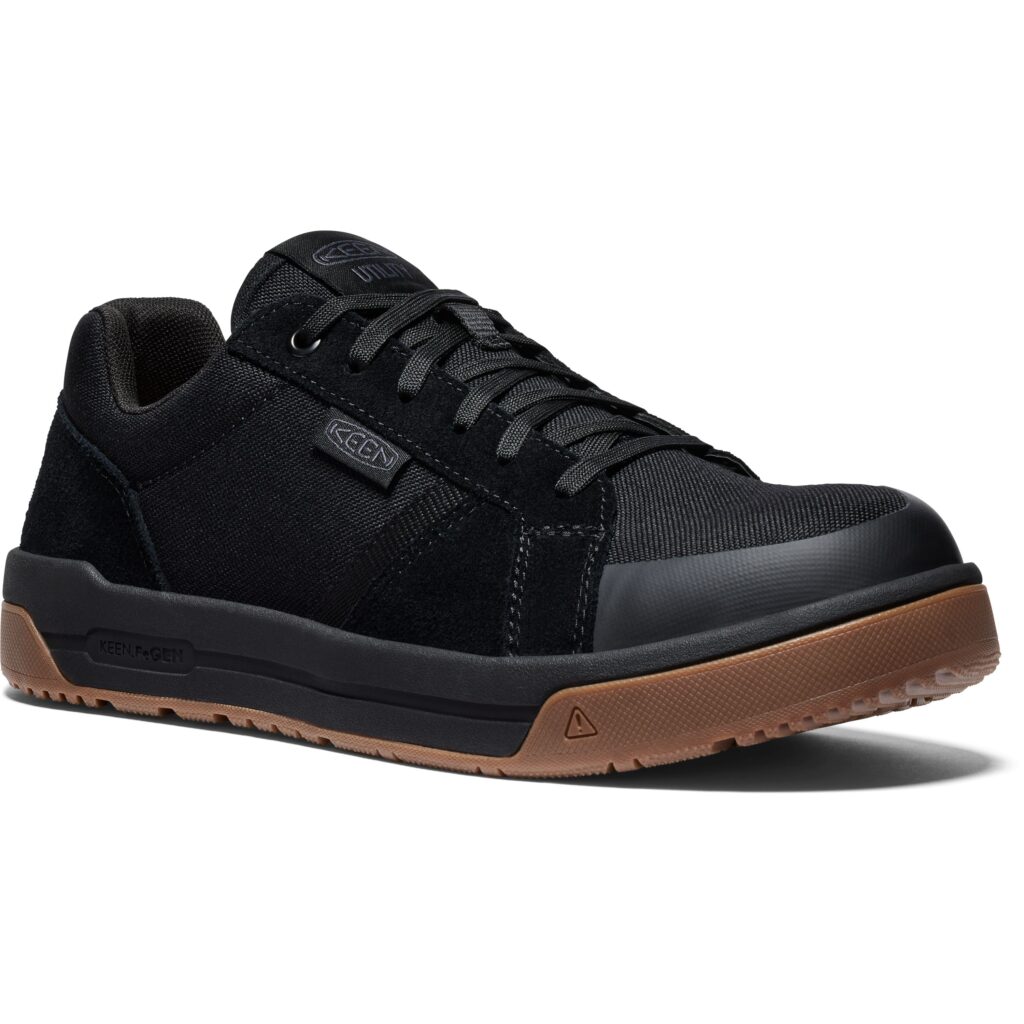
From KEEN Utility for Spring ‘24, the Kenton is a retro-inspired work sneaker reinvented with lightweight protection for all-day workflow. With a wide toe and snug heel, the Kenton boasts a responsive KEEN.ReGEN cushioning provides up to 50% energy return, to help keep your feet and legs feeling fresh, even during long workdays. In addition to all-day energy-returning comfort, the Kenton features low-profile protection including carbon-fiber safety toes 15% lighter than steel and a slip-resistant rubber outsole to help you stand strong through all the movement of your workday. Made to move, the Kenton is available in several colorways and collar heights for men.
AIT Worldwide Logistics acquires Global Transport Solutions Group
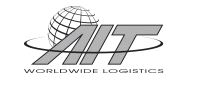
European-based marine spare parts logistics specialist with more than 600 teammates in 11 countries AIT Worldwide Logistics has acquired Global Transport Solutions Group (GTS), a prominent international freight forwarder specializing in time-critical marine spare parts logistics. Headquartered in the Netherlands, GTS and its more than 600 teammates across 16 locations in Asia, Europe, the Middle East, and North America, serve over 2,000 ports around the world. The GTS network also includes nine consolidation hubs totaling more than 45,000 square meters of warehouse space. AIT Chairman and Chief Executive Officer, Vaughn Moore, said, “I’d like to welcome our new GTS teammates to the global AIT network. This is the largest acquisition in our company’s history and GTS’ marine spare parts business is an excellent complement to AIT’s time-critical supply chain solutions.” The company’s business is divided into two sub-brands: Marinetrans (founded in 1991), excelling in “door-to-deck” spare parts logistics for ship owners and managers, and Best Global Logistics (founded in 2007), providing time-critical solutions and general forwarding for other industries, including life sciences shippers. According to AIT’s Chief Business Officer, Greg Weigel, the acquisition provides the company with a new geographic presence in Greece, Japan, and the Nordic region while adding significant capacity and subject matter expertise to existing AIT networks in China, the Netherlands, and Singapore. The deal also provides a strong foundation to expand GTS’ world-class marine spare parts solutions via AIT’s expansive global freight network. “The acquisition of GTS creates an incredible portfolio of solutions serving the maritime industry with delivery of time-critical spare parts across all geographies. This is a perfect complement to AIT’s vertical strategies focused on expedited mission-critical services like our Critical Solutions Group, government and AOG team, and Life Sciences Division,” Weigel said. “We plan to rapidly invest and expand GTS’ North American operations by capitalizing on AIT’s robust salesforce in the United States and offering maritime customers a world-class spare parts logistics solution in every port.” AIT President and Chief Operating Officer, Keith Tholan, noted that the GTS core values – customer first, operational excellence, and partnership and collaboration – closely mirror AIT’s core values. “We are delighted to welcome GTS teammates to AIT,” Tholan said. “Their deep marine logistics expertise and three decades of proven on-time performance in a very demanding segment will complement the diverse solutions we offer across our vertical sector strategy. We also expect our best-in-class global air freight procurement will instantly benefit their time-critical operations.” According to GTS co-CEO John Burgstra, the acquisition is an opportunity for GTS to further expand its worldwide operations. “We aim to provide our clients an unrivaled experience when it comes to global visibility, transparency, and on-time performance, fully unburdening them of the required logistical handling of their vessels’ spare parts,” he said. “We are excited about becoming part of a larger group and the global development opportunities this acquisition will provide for our teammates.” “Because of the highly fragmented and international nature of our client’s requirements, they need a trusted partner with a vetted and effective global network,” added GTS co-CEO Vegard Prytz. “GTS will gain enormous benefits from leveraging the global AIT infrastructure, creating an even more integrated and seamless solution for clients around the world.” Terms of AIT’s agreement to acquire Global Transport Solutions Group have not been disclosed.
U.S. Rail Traffic for the week ending January 27, 2024
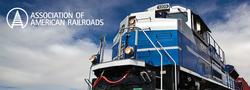
The Association of American Railroads (AAR) today reported U.S. rail traffic for the week ending January 27, 2024. For this week, total U.S. weekly rail traffic was 467,222 carloads and intermodal units, up 0.7 percent compared with the same week last year. Total carloads for the week ending January 27 were 208,131 carloads, down 9.0 percent compared with the same week in 2023, while U.S. weekly intermodal volume was 259,091 containers and trailers, up 10.1 percent compared to 2023. Two of the 10 carload commodity groups posted an increase compared with the same week in 2023. They were petroleum and petroleum products, up 688 carloads, to 10,660; and motor vehicles and parts, up 2 carloads, to 13,757. Commodity groups that posted decreases compared with the same week in 2023 included coal, down 11,014 carloads, to 57,231; nonmetallic minerals, down 5,919 carloads, to 23,370; and grain, down 2,316 carloads, to 21,025. For the first four weeks of 2024, U.S. railroads reported a cumulative volume of 802,955 carloads, down 10.4 percent from the same point last year; and 936,530 intermodal units, up 2.8 percent from last year. Total combined U.S. traffic for the first four weeks of 2024 was 1,739,485 carloads and intermodal units, a decrease of 3.7 percent compared to last year. North American rail volume for the week ending January 27, 2024, on 12 reporting U.S., Canadian, and Mexican railroads totaled 313,288 carloads, down 7.2 percent compared with the same week last year, and 339,611 intermodal units, up 7.4 percent compared with last year. Total combined weekly rail traffic in North America was 652,899 carloads and intermodal units, down 0.1 percent. North American rail volume for the first four weeks of 2024 was 2,431,427 carloads and intermodal units, down 4.2 percent compared with 2023. Canadian railroads reported 87,086 carloads for the week, down 7.3 percent, and 67,580 intermodal units, down 4.2 percent compared with the same week in 2023. For the first four weeks of 2024, Canadian railroads reported a cumulative rail traffic volume of 579,313 carloads, containers, and trailers, down 8.8 percent. Mexican railroads reported 18,071 carloads for the week, up 21.8 percent compared with the same week last year, and 12,940 intermodal units, up 25.5 percent. Cumulative volume on Mexican railroads for the first four weeks of 2024 was 112,629 carloads and intermodal containers and trailers, up 19.2 percent from the same point last year. To view the Rail Traffic charts, click here.
Hyster introduces Power Cellect™, providing forklift operations freedom and flexibility
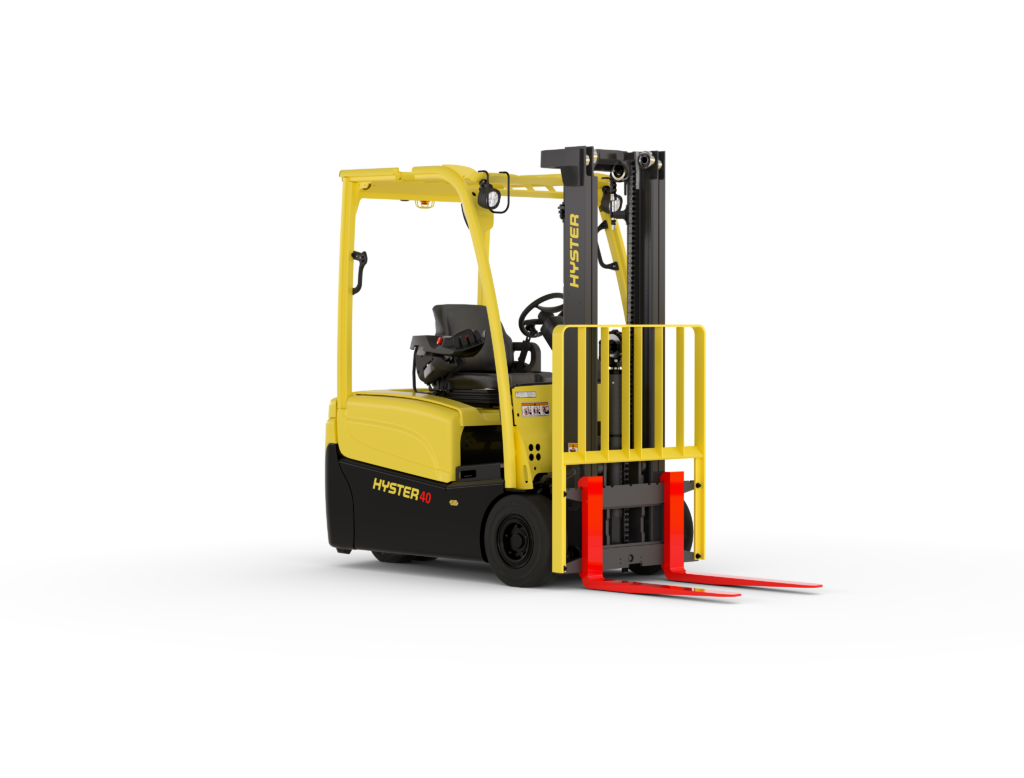
The new Hyster Power Cellect option enables users to easily change among major battery sources with no external accessories, software downloads, or integrations required Hyster Company has announced the launch of Power Cellect, an optional package available on 27 Hyster® electric forklift models. Power Cellect empowers users to easily switch power sources in electric trucks between traditional lead acid and low-maintenance battery solutions like thin plate pure lead (TPPL) and lithium-ion. The solution provides a straightforward path for customers to change the truck’s battery type, and it is particularly effective for fleets transitioning to low-maintenance battery solutions over time as well as for equipment that will be used for different applications with varied battery availability throughout its life. Hyster previously offered a lithium-ion-ready option on electric trucks, which enabled a smooth switch between lead-acid and lithium-ion batteries. Power Cellect expands on the compatibility of lithium-ion ready by adding TPPL batteries to the mix and uses an electronic Controller Area Network (CANbus) for communication between a qualified battery and the truck. Once the battery is changed out, truck settings can be easily changed to switch power sources. “Whether sustainability goals, regulations compliance or other forces are driving electrification decisions, the common thread is that operations need flexibility. Power Cellect avoids locking operations into a single power option for the life of their equipment, and eliminates the complications and compromises of third-party setups,” says James Nielson, Hyster Senior Business Product Manager for Motive Power and Electrification. “Facilitating this fluidity across battery types is the latest example of Hyster powering possibilities for forklift fleets working in all our customers’ applications, even the toughest, most demanding jobs.” In addition to providing a convenient shift in motive power sources, Power Cellect offers major functional benefits. The truck-side battery early warning system includes lift interrupt and traction performance cutback capabilities, and the truck’s battery discharge indicator (BDI) accurately portrays a state of charge across approved battery types, thereby eliminating the need for secondary displays and indicators. An internal battery protection function triggers a controlled shutdown when the battery reaches complete discharge, and operations can view additional battery data, such as battery state of health and lifetime discharge when the Hyster Tracker telemetry system is added.
Cattron introduces Remtron PatriotPro industrial remote control system
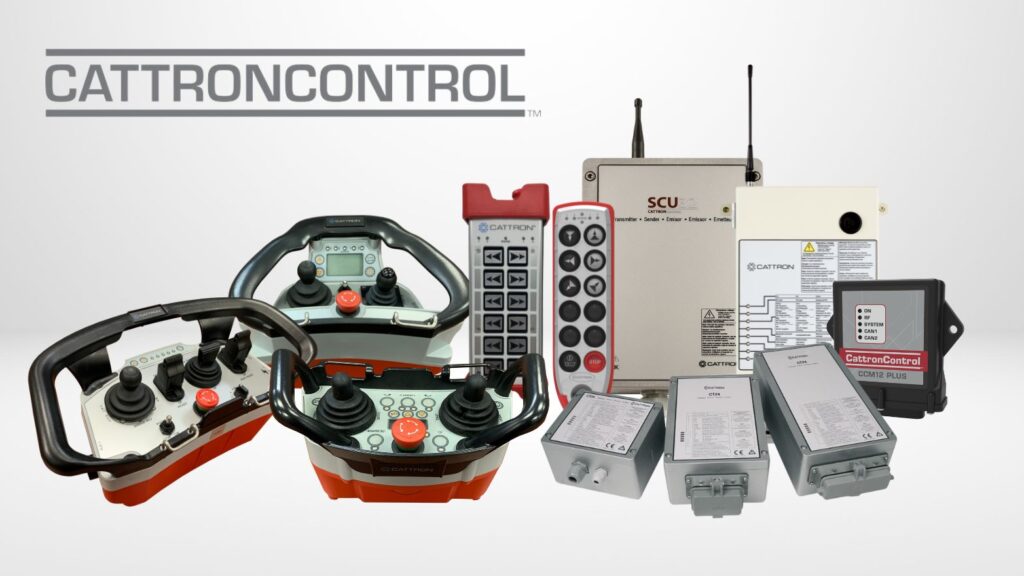
Cattron’s Remtron PatriotPro comes with a distinctive yellow control unit Cattron, a radio remote control, engine and generator control panels, and cloud-based monitoring and control solutions, has announced that its next generation of Remtron has arrived with the release of the PatriotPro industrial remote control system. The PatriotPro retains the rugged design and distinctive feel of the time-tested and proven legacy Patriot product and now boasts a new look and an advanced, future-ready technology platform. The company also announced that a limited edition patriotic, flag-inspired version of the controller will also be offered from March through July 4th, 2024. The operator control unit is available in standard configurations and can be engineered to meet specific application requirements. The transmitter can support up to 18 commands with an engineered system. New systems work with the CBMCU, 10R/17R, or 11R receivers. PatriotPro transmitters are also backward compatible with Remtron’s existing Patriot and CommandPro systems, providing a path for upgrading existing systems. Premium features of the PatriotPro radio remote control system include: Distinctive click-click indication between steps Illuminated PL-d stop switch Wireless closed-box Bluetooth configuration for the deployment of spares Logging of essential data and diagnostics Signals are secured with black channel communication protocol Private label options for OEMs and select distributors CattronLink wireless programming tool for system updates Up to a 600-foot operating range “PatriotPro combines our premium radio remote control features into a single, flexible solution that supports operators with advanced technology and security features,” said Brian Fette, vice president of Product Management for Cattron. “With all it has to offer, PatriotPro will quickly become the hero of our Remtron portfolio of industrial remote control solutions.” The PatriotPro Industrial Remote Control System is positioned to cater to the specific needs of industries reliant on precise and efficient remote-control systems applications such as those in industrial automation, material handling, and mobile equipment. With its rugged design and advanced technology platform, the PatriotPro is a remote control system built for tomorrow’s demanding industrial environment. One of the standout benefits of the PatriotPro is its flexibility and versatility. The operator control unit can be customized to meet specific application requirements, making it adaptable to a wide range of tasks. Whatever it’s controlling, the PatriotPro’s tailored, user-defined configurations ensure seamless integration into diverse industrial settings. Control units can even be privately labeled with a customer’s branding and trade dress. Safety and security are paramount in industrial settings, and the PatriotPro addresses these concerns with its innovative features. The distinctive click-click indication between steps ensures that operators have clear feedback, enhancing their ability to make accurate decisions. The illuminated PL-d stop switch adds an extra layer of safety, making it easy to halt operations in emergencies. Additionally, the use of black channel communication protocol ensures signal security and integrity during remote control operations. The PatriotPro boasts an impressive 600-foot operating range, providing operators with the freedom to control machinery from a considerable distance. This extended range not only increases operational efficiency but also enhances safety by allowing operators to maintain a safe distance from potentially hazardous equipment.
ProVeyance Group debuts new conveyor pulley solutions at MODEX 2024
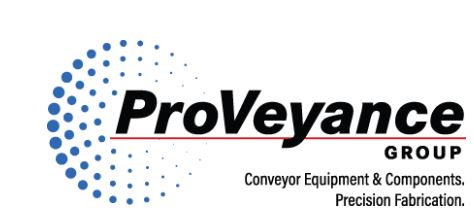
ProVeyance Group will be exhibiting at MODEX 2024 from March 11th through March 14th at Georgia World Congress Center in Atlanta, Georgia BOOTH #13818. ProVeyance is a North American manufacturer of advanced conveyance components and subsystems for package and material handling applications that go to market through its Woodsage and Ashland brands. The company will be introducing its new Conveyor Pulley product line at the event. ProVeyance’s Woodsage is a supplier of high-quality, precision-manufactured rollers for conveyor and sortation systems. The brand manufactures specialty steel rollers and roller assemblies, including tapered, grooved, motor-driven, sleeved, and precision-fabricated tube products for niche applications. The Ashland brand manufactures and assembles conveyor systems, sub-systems, and related parts and accessories. Ashland offers a standard line of gravity rollers, skatewheel, telescoping gravity, flexible gravity and powered belt conveyors, ball transfers, and tables, along with a complete selection of accessories. “Along with our well-established product lines, I am excited to have the opportunity to introduce Conveyor Pullies as the newest addition to our component products offering stated Tim Carpenter, President & CEO. “Our focus is to deliver the highest quality, conveyor pullies, at industry-best lead times, while ensuring maximum customer satisfaction through our streamlined customer service process.” Visit ProVeyance at Modex Show 2024, where we have more conveyor solutions than ever before. You’ll get a sneak peek at our new Conveyor Pulley offering and the ability to speak with an experienced representative.
Dialight unveils award-winning battery backup model LED High Bay
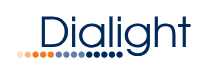
Dialight, a hazardous and industrial LED lighting innovation, has announced an all-new battery back-up model for its iconic LED High Bay. These state-of-the-art fixtures now offer even greater peace of mind for enhanced safety in harsh industrial environments, such as Oil and Gas Refineries, Metal and Steel, Petrochemical Plants, Pulp and Paper Mills, Water/Wastewater Treatment Plants, General Manufacturing facilities, and more. Proper lighting is one of the most important ways to ensure safety for workers in harsh and hazardous industrial work sites. These applications are often hampered by extreme conditions, including dust, debris, high temperatures, vibration, and power outages. In particular, power outages pose a significant safety risk by instantly plunging areas into darkness. Workers must remain safe and have adequate egress lighting to safely exit a potentially dangerous area. Dialight’s solution ensures that the fixture will stay illuminated throughout the emergency loss of power. “Since 2009 the Dialight High Bay has been the flagship of our Solid State Lighting division,” said Dialight CEO Fariyal Khanbabi. “Over the years, this fixture has received numerous awards for advancements in energy efficiency, longevity, and specialized protections for harsh industrial environments. Integrating our all-new battery backup system into the High Bay gives our customers operating in challenging conditions even greater peace of mind and demonstrates our continued dedication to innovation in the field of Industrial Lighting and safety.” Dialight’s new auxiliary battery backup solution comes factory-installed with premium NiMH battery technology making installation quick and easy. It boasts the widest operating temperature range for any industrial battery backup LED lighting fixture from -20°C to +55°C (-4°F to +131°F) and can provide illumination for a field-selectable duration from 60 minutes to 180 minutes to meet Life Safety Codes by National Fire Protection Association (NFPA) 101® guidance on emergency lighting. Available with either permanent maintained or switch-maintained operation and 10W and 20W battery options, the Dialight Battery Backup LED High Bay covers a wide range of lighting needs in industrial and hazardous locations and has been certified to UL1598/A, UL924, UL844, CID2, CIID1, and CIIID1&2. The fixture’s self-testing and diagnostics functionality removes the need for push-button tests or costly installation of a separate wire run from the High Bays to a switch or button on the ground for testing. Red and Green indicator lights on the fixture make visual inspection easy, and automatic weekly and yearly testing offers peace of mind, ensuring the battery is charging and operating properly on an ongoing basis. The new Dialight Battery Backup LED High Bays are compatible with advanced sensors and controls, including microwave occupancy sensors and Dialight IntelliLED™ wireless controls. Best of all, Dialight’s LED High Bay products are backed by an industry-leading 10-year warranty (excluding batteries) and are recognized by the National Lighting Bureau’s Trusted Warranty Program. The all-new Battery Backup LED High Bay is currently available for sale in North America.
Raymond Headquarters in New York celebrates 100,000 kaizens submitted

Cross-functional kaizen approach empowers the organization and demonstrates that voices are valued Taking continuous improvement and employee empowerment to heart, The Raymond Corporation facility in Greene, New York, is celebrating 100,000 employee-submitted kaizens in operations since introducing the program in 2006. Kaizen is based on the idea that small ongoing changes over time will result in significant improvements. “Demonstrating pure initiative and a collaborative nature, the Greene, New York, operational team deserves great recognition for 100,000 kaizens submitted,” said Tony Topencik, vice president of operations, quality and EHS at The Raymond Corporation. “Raymond encourages its employees at all levels and tenure to submit kaizens they believe will help improve their departmental processes. With each kaizen that is selected and acted upon, it further demonstrates to team members that their voices are valued.” Submitting kaizens is not mandatory at Raymond, but they continue to see employee engagement with this process. Kaizen submissions even withstood the challenging times of COVID-19 and continue to foster connectivity and culture within the organization. The Greene, New York, operation consists of 28 departments and over 2,900 employees who submitted at least one kaizen. More than 80% of kaizens submitted have so far been implemented. In total, 5,427 days were saved by eliminating waste and improving processes through kaizens. In total, across Raymond, which consists of 110 departments spanning three locations, the company has secured 19,883 days saved, with 4,384 employees having submitted at least one kaizen since 2006. The Raymond Corporation is tracking toward hitting 150,000 kaizens enterprise-wide within the year and sees, on average, 843 kaizens submitted monthly. “Kaizen is a foundational part of Raymond Lean Management (RLM), which is built on the proven foundation and principles of the world-renowned Toyota Production System. The program teams up with associates across the organization — from the manufacturing floor to office departments, dealerships and more — to coach them on continuous improvement concepts,” says Topencik. “All associates are given the opportunity for hands-on learning and mentorship. The process empowers employees to find opportunities for improvement and instills a culture of continuous improvement.” Employees receive well-deserved recognition during a monthly review, where four implemented kaizens are selected. Implemented kaizens shine a light on the employees who submitted their work, with a presentation by Raymond’s president & CEO, VP of operations, director and senior manager for the area, and direct supervisor. The kaizen winner talks about their work and receives both a monetary award and a certificate of recognition. “At Raymond, we believe in celebrating excellence at every level. Our monthly kaizen reviews recognize our employees’ hard work and innovation and exemplify our commitment to continuous improvement. Implemented kaizens are a testament to our collective dedication to excellence, and through these moments of recognition, we illuminate the path to continuous success,” said Topencik. “Of all the data measured by organizations, moral metrics are of great importance to us. This is a critical part of our culture and encourages peer-to-peer positivity. It confirms that together, we are going in the right direction.”
Bobcat Company donation supports University of Mary
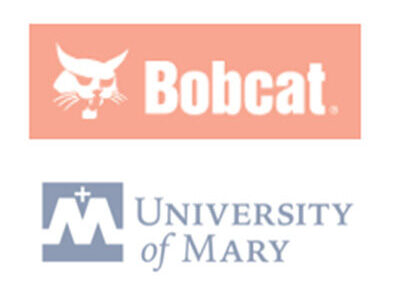
Sustaining STEM education ensures students are ready for innovative careers Bobcat Company is donating $250,000 to the University of Mary in Bismarck, N.D., in support of the Hamm School of Engineering. “Supporting STEM-based education is a key component of Bobcat’s foundation of innovation – a longstanding belief that has generated community progress and fueled the curiosity needed to build the technology of tomorrow,” said Mike Ballweber, president of Doosan Bobcat North America. “We are proud to support University of Mary as they advance educational opportunities for the next generation of groundbreaking engineers.” Headquartered in West Fargo, N.D., Bobcat is the state’s largest manufacturer and a major employer with more than 3,800 North Dakota-based employees at facilities in Bismarck, Gwinner, Fargo, West Fargo and Wahpeton. Bobcat’s donation will support the engineering school through the University of Mary’s Vision 2030 Capital Campaign, a comprehensive strategic planning initiative to enhance and transform the university campus and offerings. The Hamm School of Engineering facility opened in 2020 and is state-of-the-art designed to encourage collaboration and hands-on learning. The school offers ABET accredited degrees in mechanical, electrical, and civil engineering. The Hamm School of Engineering also offers computer science, environmental engineering, construction engineering and construction management. “We are extremely humbled and grateful for this gift from Bobcat Company, an innovative and industry leader throughout the world,” said Jerome Richter, executive vice president at the University of Mary, and the person leading the Vision 2030 Capital Campaign. “We appreciate Bobcat’s continued commitment to our Hamm School of Engineering students. Our students are highly sought after, recruited by firms well before they graduate, and not only are they trained in technical skills, but also well-formed servant leaders who are culturally prepared for the workplace.” As the largest employer of engineers in North Dakota, Bobcat understands firsthand the tremendous need right now for engineers locally, regionally, and globally. Data shows, 70% of the students in the Hamm School of Engineering are from out of state, and last year, 67% of its graduates stayed in North Dakota to work for engineering firms. Therefore, this donation exemplifies the strong partnership between the University of Mary and Bobcat, and just as important, the collaboration for continued growth and prosperity in the state. Over the years, several Bobcat team members have served as advisor committee members for University of Mary engineering students. Bobcat also supports classroom presentations and senior design projects and recruits University of Mary students every year for full-time employment, co-op, and intern experiences throughout various departments. “As a company based in North Dakota, we are committed to nurturing the state and region’s future innovators, engineers, and technology leaders,” said Scott Schuh, Doosan Bobcat chief technology officer, and senior vice president. “That requires investment in the initiatives that will create the next generation of STEM professionals, whose technology and engineering expertise will ensure our state’s businesses continue to grow and thrive.”
Statement from Brotherhood of Locomotive Engineers and Trainmen First Vice President Mark Wallace on Breakthrough Agreement reached today with Norfolk Southern to improve Rail Safety through the adoption of a close call confidential reporting program
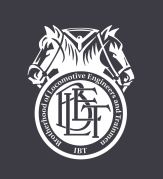
The following statement from Brotherhood of Locomotive Engineers and Trainmen (BLET) First Vice President Mark Wallace references a breakthrough agreement signed in Washington today between Norfolk Southern, the BLET and another union for joint participation in a Federal Railroad Administration Confidential Close Call Reporting System (C3RS) pilot program. C3RS is designed to enhance railroad safety by enabling covered BLET members employed at the railroad to report safety issues without fear of retaliation or punishment. In addition to the statement below, more details can be found at: https://blet.link/42gye78 BLET members who work in the cabs of Norfolk Southern’s locomotives welcome this agreement. Our union has had years of experience with close call reporting programs at Amtrak and other passenger railroads, along with a handful of smaller freight carriers, but only 23 out of the nation’s 800 railroads have adopted C3RS. For far too long the large railroads and their trade association, The Association of American Railroads, have paid lip service to safety. The AAR prefers to spend millions of dollars on television commercials bragging about safety while backtracking on safety agreements. Rather than adopt programs like C3RS, that enable an organization to continually improve and take corrective actions, the Class I railroads engaged and continue to engage in finger pointing. This close-call reporting system, which is like safety programs successfully used in commercial aviation, will help put an end to the blame game and place Norfolk Southern’s trains on safer journeys. We fervently hope that it will be a model for other Class I freight carriers. Norfolk Southern and its CEO, Alan Shaw, should be commended for showing leadership on this issue. Our union’s National President, Eddie Hall, and our General Chairmen who represent BLET members at NS, Scott Bunten, Dewayne Dehart, and Jerry Sturdivant, have joined me in telling Norfolk Southern’s managers that if they’re serious about improving this railroad they must both prioritize safety and value railroad employees. This agreement on C3RS does both. Mark Wallace is First Vice President of the Brotherhood of Locomotive Engineers and Trainmen, the union’s second-highest office. He began his career in railroading at Norfolk Southern where he worked as a carman and as a conductor before becoming a locomotive engineer. The Brotherhood of Locomotive Engineers and Trainmen represents 51,500 professional locomotive engineers and trainmen throughout the United States. It is the nation’s oldest labor union. The BLET is the founding member of the Rail Conference, International Brotherhood of Teamsters. More information can be found on the BLET website: https://ble-t.org/