Episode 456: A deep dive into Technology, Flexibility, and Warehouse resilience
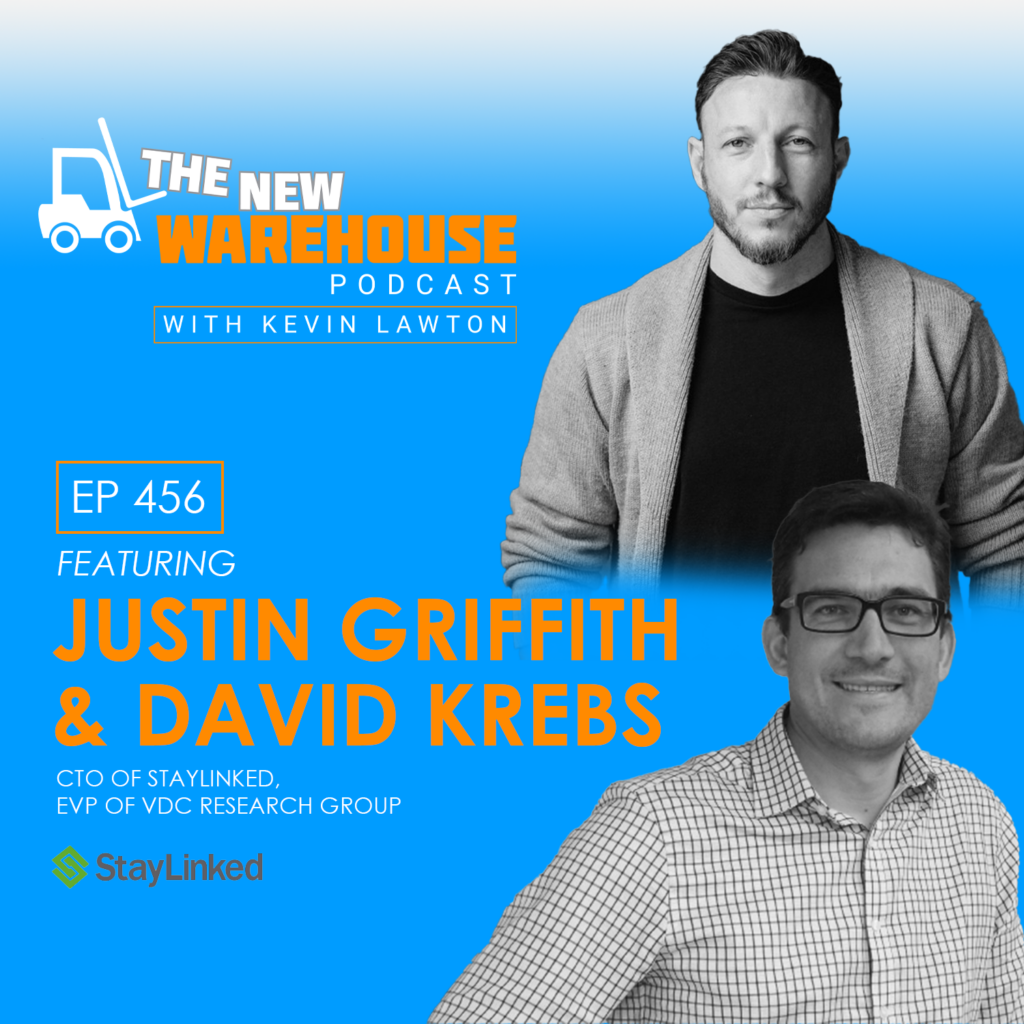
In this week’s episode of The New Warehouse Podcast, Justin Griffith, CTO at StayLinked, and David Krebs, EVP of Enterprise Mobility and AIDC at VDC Research Group, reveal groundbreaking insights from their latest research, “Making Supply Chain Resilience Work: Keeping Up with Ever-Demanding Warehouse Operations.” Discover the complexities and future trends of supply chain operations, warehouse resilience, and technology adoption; an essential listen for those navigating the dynamic warehousing and supply chain management landscape. Redefining Warehouse Resilience with a Shift Towards Agile Infrastructure and Technological Adaptability As David highlights, the notion of supply chain resilience has gained prominence, particularly in the wake of logistical challenges. Companies realize that while they couldn’t have entirely prevented these issues, better preparedness through modernized infrastructure could have mitigated their impact. This realization spurred an accelerated investment in updating underlying infrastructures. There’s a clear correlation between the modernity of a company’s infrastructure and its ability to adopt new technologies effectively. Comparing firms with quasi-modern systems to those lagging in technology versions shows a stark difference in their capacity to integrate new technologies and realize their value faster. The logistics sector, which traditionally held the mindset that if it’s not broke, don’t fix it, is now confronting the reality of outdated legacy Warehouse Management Systems (WMS), highlighting the need for modernization. Justin echoes these sentiments, underscoring the importance of investment in technologies not just for the sake of advancement but for building warehouse resilience and a responsive supply chain. Moreover, the focus has shifted from selecting the perfect technology to creating a system that allows flexibility and choice. It’s about preparing for any necessary technology, whether Automated Mobile Robots (AMRs) or others, as and when needed. The key lies not in committing to one specific technology but in establishing a foundation that supports a mix of different technologies, ensuring adaptability and resilience in ever-changing market conditions. Warehouse Workforce Dynamics: The Synergy of Human Labor and Advanced Technology Labor optimization in warehousing is no longer a one-dimensional pursuit of speed. It has evolved into a multifaceted approach that values the human workforce, emphasizes ergonomic and intuitive technological solutions, and seeks to harmonize both benefits for a more efficient, effective, and resilient supply chain operation. Justin details how the pandemic highlighted the criticality of the human workforce in warehouse operations. Despite advancements in technology like beacons, sensors, Automated Mobile Robots (AMRs), and drones, the absence of human labor could halt operations entirely. This period prompted a reevaluation of existing workflows and a shift from considering full automation to integrating technology that complements the human workforce. David believes frontline workers have been somewhat underserved in technological advancements, often dealing with outdated mobile solutions. He advocates for technology that is as unobtrusive as possible, emphasizing the need for ergonomics, safety, and simplicity in design. These considerations are vital in a labor-intensive environment where worker well-being is paramount. Griffith notes that the focus has shifted from replacing labor with technology to integrating both in a synergistic manner. This integration allows for more inclusive labor practices, such as remote piloting and collaborative robotics, expanding the potential workforce and enhancing operational efficiency. The narrative has evolved from technology as a replacement to technology as a facilitator, working in concert with human labor to achieve better results. Key Takeaways Labor Optimization and Worker Experience: There is a growing emphasis on improving labor optimization and the worker experience. This includes adopting technologies that streamline workflows and reduce warehouse workers’ physical and cognitive load. Adoption of Locationing Systems: There is a growing adoption of locationing systems in warehouse operations to enhance operational visibility. Importance of Warehouse Management Systems (WMS): The study emphasizes the correlation between the age and investment in WMS and a company’s ability to adopt new technologies successfully. Up-to-date systems facilitate better integration and utilization of new technologies. The New Warehouse Podcast EP 456: A Deep Dive into Technology, Flexibility, and Warehouse Resilience (Part 1) https://youtu.be/JZoqC53Nakc?feature=shared
LGH & Rotrex Group announces new LGH Sales Director and Board appointments
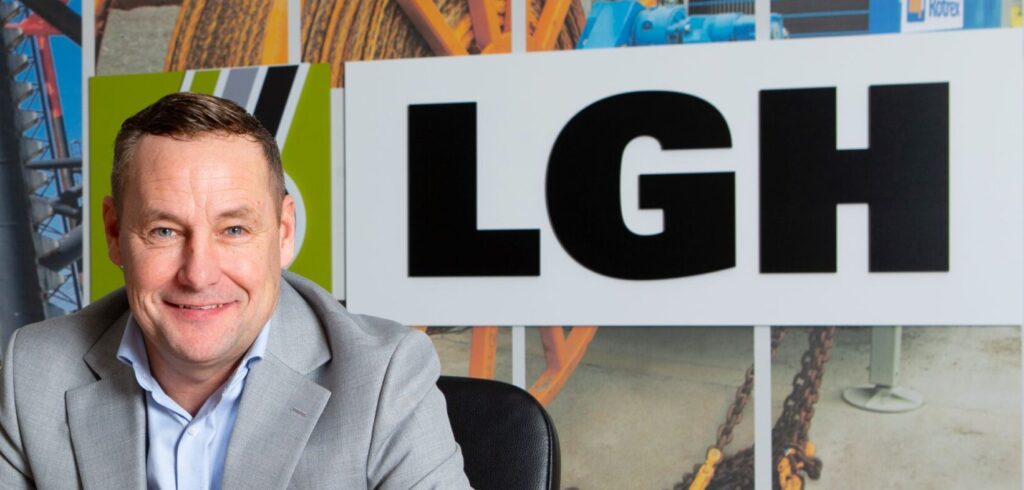
LGH & Rotrex Group has appointed Russell Boswell-Munday as LGH’s new Sales Director for Europe and the UK. Russell has over 25 years of experience in the hiring industry and has managed various sales teams during his career. As well as Russell’s appointment, the group has also announced other changes to the Board. In his new role, Russell will be managing all aspects of LGH’s sales division across the whole of Europe, including continuing its growth in additional territories. He will be leading on strategy and structure as well as budgets and turnover development. Before joining LGH, Russell worked at Andrew Sykes Group as a Major Account Director. Russell commented: “I have long admired LGH, so I am excited to be joining at what is a time of real growth for the business. After my first meeting with Andy Mault – CEO – I quickly realized that our thoughts and ambitions were aligned. I am now looking forward to building on the Group’s strong reputation and adding commercial value by driving sales and our market share right across Europe.” Also joining the LGH & Rotrex Group’s Board of Directors are: Don Wilkinson, who has been promoted to Rotrex’s Sales Director; and Phil Smith, who has been promoted to Group Operations Director. All three now sit on the board alongside Andy Mault, CEO, and Rob Halliwell who was recently been named as Support Services Director. They are responsible for the Group’s entire operations across Europe and the UK. Andy Mault, CEO said: “Russell brings with him a wealth of experience, so we are delighted that he has joined us. I am confident that he will make a real difference and will play a crucial part in driving our sales strategy and its implementation to the next level. Andy added: It has also been fantastic to welcome Don and Phil to the Board alongside Russell and, of course, Rob. Over the past few years, they have both proved themselves to be an asset, and their promotions are richly deserved. I know that this motivated and talented senior leadership team will help me lead the Group to even greater success.” LGH & Rotrex Group is still privately owned by the Parkinson family. LGH is a leading lifting equipment hire company; whilst Rotrex delivers winch hire, sales, and services.
Orion announces Darrin Snarr as new Regional Sales Manager
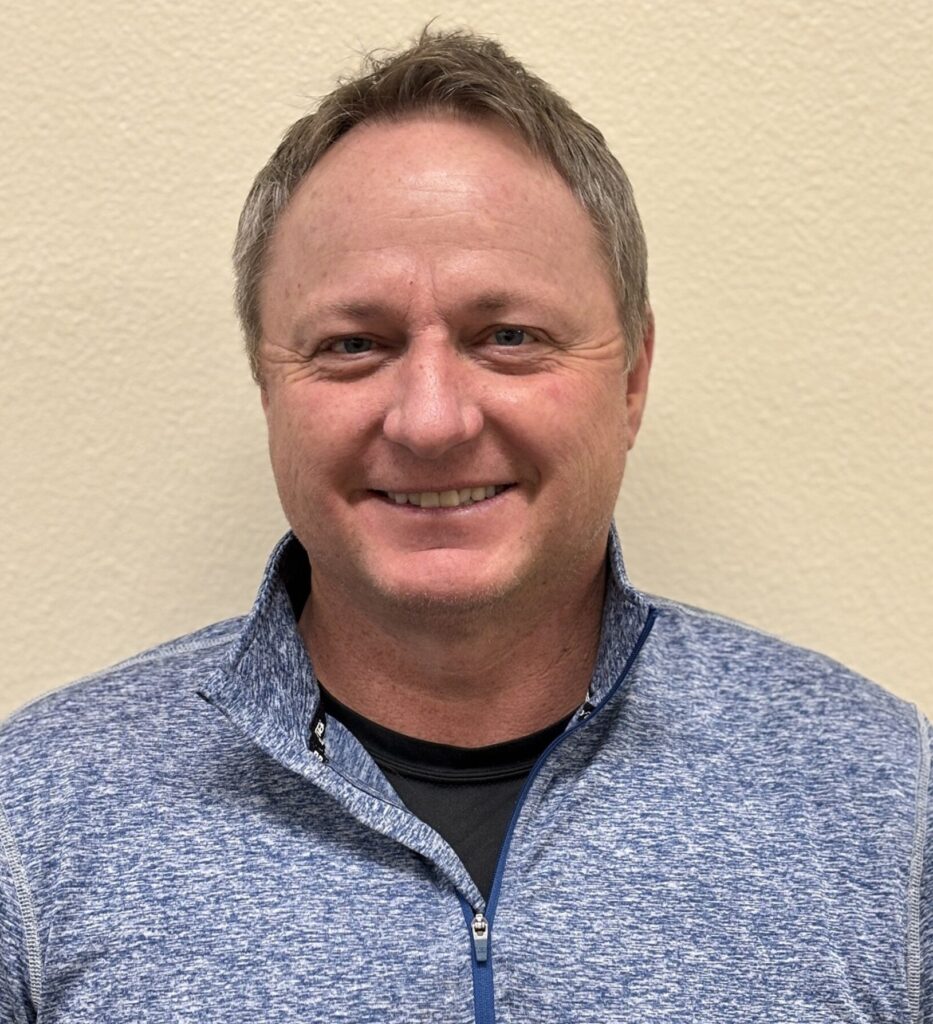
Darrin Snarr has been appointed Regional Sales Manager for Orion, a role in which he will serve as an advisor to end-user customers across 11 states and four Canadian provinces on the West Coast. Orion is a stretch wrapping and pallet unitizing machinery manufacturer of automatic and semi-automatic stretch wrapping equipment, including rotary turntables, rotary towers, and horizontal wrapping systems. Snarr’s resume boasts 15 years in packaging sales, including his most recent position as a packaging consultant for Flexpak where he worked with customers to recommend equipment and training plans. “My new role at Orion offers me so many opportunities to support customers in a variety of ways,” Snarr said. “This company has proven to be an industry leader in stretch wrapping, and I’m excited to join a team that has helped so many users elevate their end-of-line.”
Overcoming Fear and Resistance to create positive change
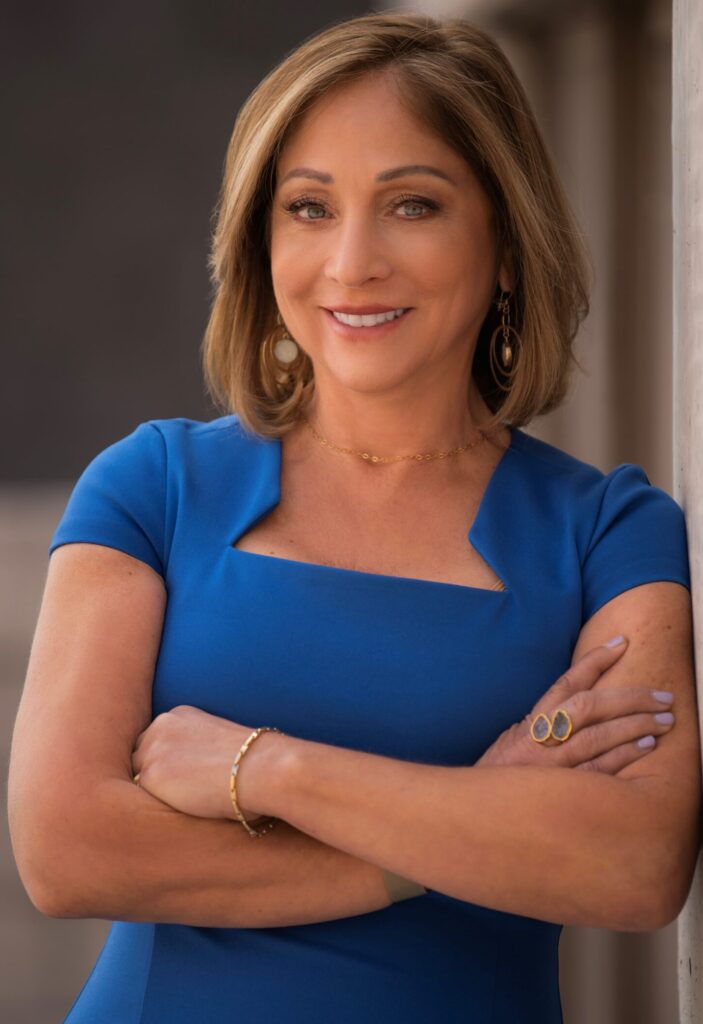
In the dynamic landscape of today’s business world, change is inevitable. However, fear is one of the biggest obstacles to creating positive change. With fear comes resistance and when both of them are at play, your organization becomes stuck in place and unable to overcome new challenges and market shifts. To enable your organization to be agile enough to adapt to and adopt change, it’s essential to understand the necessary steps to overcome and move beyond the inevitable constraints that resistance and fear cause. What’s causing fear? A big problem with having unresolved fear present in your organization is that it’s hard to know where it’s coming from. Most of the time, you won’t even realize you or the people around you are in a state of fear. You can’t fix a problem you don’t even know about. Change management can only be effective when you navigate your fears. Some common fears can include a fear of failure, fear of not being able to manage change, fear of exposing one’s vulnerabilities, and fear of the unknown. These just scratch the surface. Every person and every organization is unique and has different fears that may cause challenges in the workplace. To overcome fear, you must understand what is bringing that fear to the surface. Be conscious of your fears and acknowledge them. Be curious and ask others in the organization what concerns them about impending changes and what makes them uneasy about moving forward. Ask why people are afraid. Getting past fear is much easier when you know what you’re up against. Open your mind Resistance to change is how your organization falls behind. When people fear the uncertainties associated with change, they tend to resist even beneficial transformations, keeping the organization stuck in a frustrated state. One of the most common causes of resistance is close-mindedness, which is often born out of fear. Once you understand what is causing that fear, it’s important to open your mind to the new possibilities and ideas that you may have been resistant to. Just because you’ve gotten by doing things a particular way doesn’t mean there isn’t a better alternative. Being open to diverse perspectives and ideas leads to innovation and market leadership. It’s much easier to gain buy-in and engagement from people when you get curious and include their opinions and perspectives. Hiring people from a variety of backgrounds and areas of expertise can support this. Anyone you hire and engage with about moving the organization forward needs to be committed to your vision or the vision of the company. People who don’t care often resist change because they don’t see how it benefits their personal agenda. Manage your ego Allowing your ego to take charge of your behaviors only leads to a struggle to innovate and grow as an organization. That goes for everyone else in your organization as well. You must take a good look in the mirror and see where you resist doing things differently or moving into unknown territory. If you always must be right, struggle with feedback, blame others for your failures, and/or don’t hire people smarter than you, these may be signs that your ego has too much control over you and is inhibiting your ability to change and keep your organization in a position that makes a positive impact. You may not even realize it. A few ways to remedy this personal and professional challenge include: Encouraging feedback from within the organization – It allows you to better understand what’s working within your company and what can still be improved upon. Practicing Self-Awareness – If you don’t realize your ego is controlling your actions, it’s crucial to look inward to understand why it’s causing you to act in ways that thwart your personal effectiveness so that you can be better at self-managing. Being grounded in who you are – Living true to yourself and understanding your values and goals is key. The ego often overreacts to failure and self-limiting thoughts. Grounding yourself in authenticity fosters consistency and clarity of direction. When your actions align with your true self, you project clarity and certainty because you are being genuine and transparent. Getting out of Frustration and into Courage – It takes courage to be wrong and admit to it. Cultivating your ability to admit missteps and embrace vulnerability is key to effectively managing how much your ego controls your behavior. This transparency also models vulnerability and authenticity for others to follow. Have a direction Being stuck in place can often indicate a lack of specific direction. If you don’t know where you’re going, you’ll never know when you’re there. Your organization, the people within it, and you all need direction. People need to see the vision, and they need to understand why they must feel compelled to act on that vision. Ask questions about yourself and those around you. What is your purpose? What is the vision of your organization? Why is that important? How will it benefit the organization, the people in it, and you? What is the contribution you most want to give? When do you know you’ve given it? Establishing a purpose and defining the contribution your organization aims to make are fundamental aspects of overcoming fear and resistance. Clearly articulated goals and a shared vision provide the necessary guidance for navigating through challenges and driving positive change. When people see and feel the vision, they understand why and how they can contribute. This gives them the positive energy to create and move forward, rather than react and stay complacent. If you don’t have a direction, it’s easy to just stick with whatever you and your organization are doing right now and not change anything. While this approach may keep you afloat for a little while, it won’t enable long-term growth and success for you or your company. Wake up and meet your higher self When you embody the contribution, you aspire to be and make and adjust your behaviors to be
NORD DRIVESYSTEMS delivers efficient, reliable drive solutions to keep the post and parcel industry moving
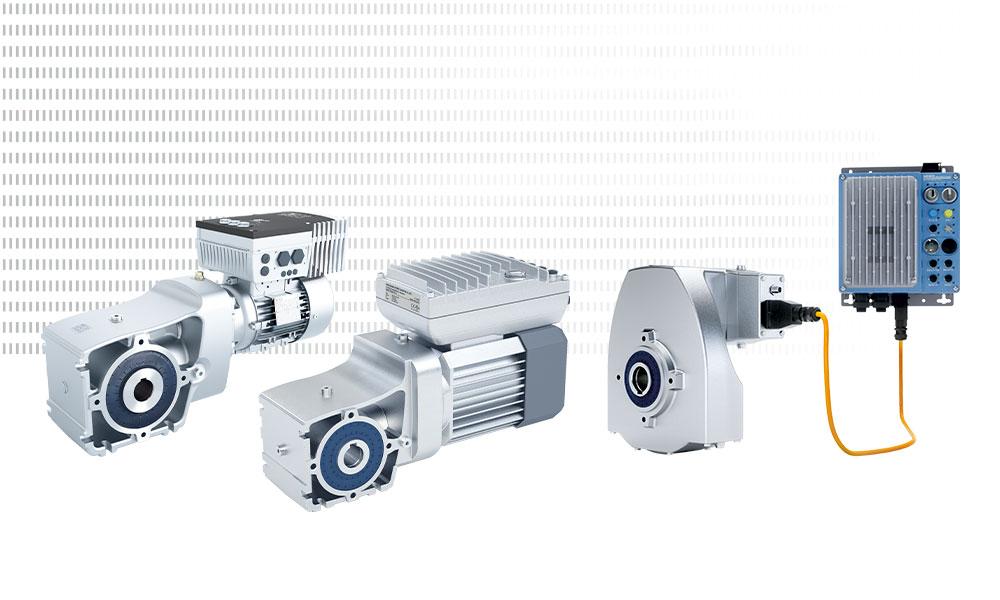
NORD’s drive solutions focus on efficient technology to reduce system variants, lower total cost of ownership (TCO), and reduce energy consumption. NORD DRIVESYSTEMS supports post and parcel distribution centers with modular products adaptable to individual application specifications. Their high-efficiency products increase the energy efficiency of conveyor systems, effectively lowering CO2 emissions and the Total Cost of Ownership (TCO). NORD’s IE5+ product portfolio delivers a complete drive solution with one of the highest operational efficiencies on the market. The line is comprised of the DuoDrive integrated gear motor, IE5+ Permanent Magnet Synchronous Motors, and NORDAC ON/ON+ Variable Frequency Drives. DuoDrive is an innovative solution that combines a single-stage helical gear unit with an IE5+ synchronous motor in one compact housing. Thanks to its optimized system efficiency, high power density, and quiet operation, it is especially suitable for intralogistics applications. The drive also features Plug-and-Play capabilities, allowing for fast commissioning and easy maintenance. IE5+ Permanent magnet synchronous motors are part of NORD’s new generation of high-efficiency motors. The motors are manufactured in-house for quick delivery times and feature a non-ventilated version (TENV) for wash-down applications as well as a ventilated version (TEFC) for intralogistics. These motors have been designed to reduce variants and minimize operating costs due to their consistent efficiency over a wide speed range, even at partial load and low-speed ranges. With two case sizes to choose from, a power range from 0.5 – 5.0 hp, and continuous torque from 14 – 130 lb-in, these motors combine the benefits of NORD’s modular system with highly configurable solutions fitted to customer specifications. NORDAC ON/ON+ variable frequency drives were developed for the special requirements of horizontal conveyor technology with the NORDAC ON made for IE3 motors and the NORDAC ON+ built for combination with IE5+ motors. These VFDs are characterized by an integrated multi-protocol Ethernet interface configurable for each drive parameter, enabling dynamic control and synchronization of conveyor systems. The drives also offer a full Plug-and-Play solution for IIoT environments and thanks to their compact design, can easily be motor or wall-mounted where space is limited. NORDBLOC.1® two-stage helical bevel gear units provide optimized performance for post and parcel conveyor systems. Their high efficiency, low maintenance, and high power density ensure systems operate reliably as well as efficiently. High-strength aluminum alloy housings help maintain a low weight while an open housing design improves heat dissipation for applications with high axial and radial loads. Flexible installation options including various input and output options, solid and hollow shafts, and versatile mounting make the drives highly adaptable to a wide range of applications and environments. NORDAC FLEX variable frequency drives are NORD’s most flexible VFDs with fully scalable functionality and optional modules adaptable to specific application requirements. Their efficient operation and versatility result in a greater Return on Investment (ROI) and lower Total Cost of Ownership (TCO). Full PLC functionality and POSICON integrated positioning mode ensure conveyors move at the correct speeds with precise control. Multiple functional safety options are additionally available to protect users in distribution centers, parcels, and the systems themselves. The LogiDrive® solution from NORD is a competitive drive solution that reduces planning and commissioning efforts through a cost-effective, standardized design. Advanced and basic versions are available to choose from with advanced options including IE5+ synchronous motors, a decentralized frequency drive, and either a two-stage helical bevel gear unit or DuoDrive. Basic versions include an IE3 motor with a motor-mounted VFD and flexible gear unit selection from the modular product line. While LogiDrive advanced solutions focus on energy efficiency, variant reduction, and lower TCO, the basic LogiDrive solutions focus on cost efficiency. Condition monitoring for predictive maintenance replaces time-based maintenance with a status-based maintenance approach to proactively maintain machines and avoid unplanned downtimes. With this system solution, drive and status data are recorded continuously or periodically to use for analysis and optimize the operational safety and efficiency of systems. This status-based approach prolongs the service life of components and machines, increases system availability, and reduces service and material costs. Condition Monitoring can even determine the optimal time to change oil, ensuring drives are always operating at their highest capacity.
United Rentals announces Record Fourth Quarter and full-year 2023 results
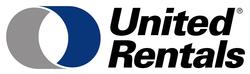
United Rentals, Inc. has announced the financial results for the fourth quarter of 2023 and reported its full-year results on Form 10-K. The company also announced its full-year 2024 guidance and an enhanced capital allocation strategy focused on balancing growth and returns to drive shareholder value that includes a lower targeted full-cycle leverage range, its intention to repurchase $1.5 billion of common stock in 2024 and a 10% increase in its dividend per share. Fourth Quarter 2023Highlights Total revenue of $3.728 billion, including rental revenue2 of $3.119 billion. Net income of $679 million, at a margin3 of 18.2%. GAAP diluted earnings per share of $10.01, and adjusted EPS4 of $11.26. Adjusted EBITDA4 of $1.809 billion, at a margin3 of 48.5%. Year-over-year, fleet productivity5 increased 0.3% as reported and 2.4% on a pro forma5 basis. Full-year net cash provided by operating activities of $4.704 billion; free cash flow4 of $2.306 billion, including gross payments for purchases of rental equipment of $3.714 billion. Full-year gross rental capital expenditures of $3.508 billion. Returned $1.406 billion to shareholders for the full-year, comprised of $1.000 billion via share repurchases and $406 million via dividends paid. Year-end net leverage ratio6 of 1.6x, with total liquidity6 of $3.330 billion. CEO Comment Matthew Flannery, chief executive officer of United Rentals, said, “We entered 2023 with the goal of raising the bar and I’m incredibly pleased with the team’s performance. Our fourth quarter results capped a year of new records across revenue, profits, and returns driven by a relentless commitment to serving our customers while staying laser-focused on safety and operational excellence.” Flannery continued, “We are now excited to deliver on the growth we expect in 2024, supported by our strength on large projects. Our guidance reflects the opportunities we see across our business as we leverage our competitive advantages to support our customers and outpace the market. We continue to execute on our long-held strategy to deliver profitable growth, strong free cash flow and exceptional returns. Our new leverage targets and 2024 capital allocation plans are further evidence of our commitment to driving shareholder value.” _______________ 1. A discussion of the company’s full-year 2023 results of operations is included in its Annual Report on Form 10-K filed with the SEC. 2. Rental revenue includes owned equipment rental revenue, re-rent revenue and ancillary revenue. 3. Net income margin and adjusted EBITDA margin represent net income or adjusted EBITDA divided by total revenue. 4. Adjusted EBITDA (earnings before interest, taxes, depreciation and amortization), adjusted EPS (earnings per share) and free cash flow are non-GAAP measures as defined in the tables below. See the tables below for reconciliations to the most comparable GAAP measures. 5. Fleet productivity reflects the combined impact of changes in rental rates, time utilization and mix on owned equipment rental revenue. The company acquired Ahern Rentals, Inc. (“Ahern Rentals”) in December 2022. Pro forma results reflect the combination of United Rentals and Ahern Rentals for all periods presented. See the table below for more information. 6. The net leverage ratio reflects net debt (total debt less cash and cash equivalents) divided by adjusted EBITDA for the trailing 12 months. Total liquidity reflects cash and cash equivalents plus availability under the asset-based revolving credit facility (“ABL facility”) and the accounts receivable securitization facility. 2024 Outlook The company provided the following outlook for 2024. 2024 Outlook 2023 Actual Total revenue $14.650 billion to $15.150 billion $14.332 billion Adjusted EBITDA7 $6.900 billion to $7.150 billion $6.857 billion Net rental capital expenditures after gross purchases $1.900 billion to $2.200 billion, after gross purchases of $3.400 billion to $3.700 billion $1.934 billion net, $3.508 billion gross Net cash provided by operating activities $4.150 billion to $4.750 billion $4.704 billion Free cash flow excluding merger and restructuring related payments8 $2.000 billion to $2.200 billion $2.314 billion Summary of Fourth Quarter 2023 Financial Results Rental revenue for the quarter increased 13.5% year-over-year to a fourth quarter record of $3.119 billion, reflecting broad-based strength of demand across the company’s end-markets and the impact of the Ahern Rentals acquisition. Fleet productivity increased 0.3% year-over-year, while average original equipment at cost (“OEC”) increased 15.1%. On a pro forma basis, rental revenue increased 7.6% year-over-year, supported by a 6.9% increase in average OEC and a 2.4% increase in fleet productivity. Used equipment sales in the quarter increased 7.1% year-over-year. Used equipment sales generated $438 million of proceeds at a GAAP gross margin of 50.0% and an adjusted gross margin9 of 55.3%, compared to $409 million at a GAAP gross margin of 58.9% and an adjusted gross margin of 61.6% for the same period last year. The year-over-year declines in the GAAP and adjusted gross margins primarily reflect the expected normalization of the used equipment market and the impact of sales of equipment acquired in the Ahern Rentals acquisition. Average fleet age was 52.4 months as of December 31, 2023. Net income for the quarter increased 6.3% year-over-year to $679 million, while net income margin decreased 120 basis points to 18.2%. Net income was a fourth quarter record excluding the fourth quarter of 2017, which included a one-time net income benefit associated with the enactment of the Tax Cuts and Jobs Act of 2017. On a pro forma basis, fourth quarter net income margin declined 40 basis points. The decrease in the company’s reported net income margin was primarily driven by the impact of the Ahern Rentals acquisition on rental and used equipment gross margins, and higher interest expense, partially offset by reductions in selling, general and administrative (“SG&A”) and income tax expenses as a percentage of revenue. While the effective income tax rate of 24.7% for the quarter decreased 390 basis points year-over-year, primarily due to the settlement in the fourth quarter 2022 of non-recurring prior year tax adjustments, the full-year effective income tax rate was largely flat year-over-year at 24.5%. _______________ 7. Information reconciling forward-looking adjusted EBITDA to the comparable GAAP financial measures is unavailable to the company without unreasonable effort, as discussed below. 8. Free cash flow excludes merger and restructuring related payments, which cannot be reasonably predicted for
Toyota Material Handling Solutions announces its relocation to a new facility in Los Angeles
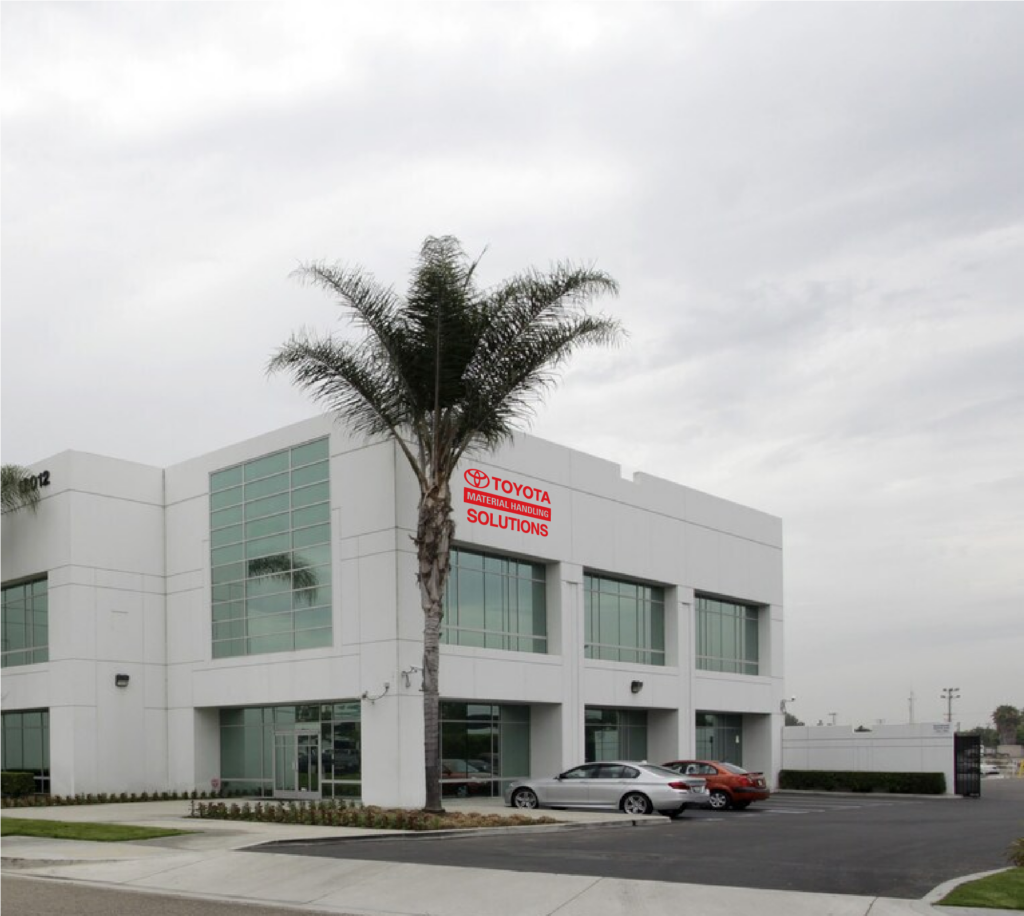
Toyota Material Handling Solutions (TMHS), a provider in the Los Angeles material handling industry, has announced that it has relocated to a new state-of-the-art facility in Santa Fe Springs. The move will enable the company to expand its operations and provide better customer service. The new location features a large warehouse and two buildings in a single structure: a front office at 12012 Burke Street for administrative and sales support and a back office at 12070 Burke Street for aftermarket parts and service support. The 130,000 square feet of modern office and warehouse space will allow TMHS to streamline its operations, enhance its customer service capabilities, and house more new, used, and rental forklifts and other material handling equipment. The new facility is located by the 5, 605, and 91 freeways. “This move represents a significant milestone in our 50-year history,” said President & CEO Dr. Shankar Basu. “As we continue to grow and expand, our new space will enhance collaboration, innovation, and the overall experience for our valued partners and customers.” Current and potential customers are encouraged to contact TMHS for a tour of the new facility.
Carolina Handling receives industry MVP Award
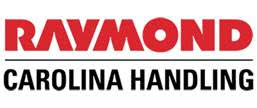
Carolina Handling, a material handling industry, has received the 2024 Most Valuable Partner (MVP) Award from the Material Handling Equipment Distributors Association (MHEDA) for outstanding achievements in 2023. This marks the fourth consecutive year that the company has received the award. The MVP Award is a prestigious accolade within the industry, with fewer than 10 percent of MHEDA’s 600 member organizations earning the distinction. Carolina Handling’s continued recognition as an MVP within the industry underscores a dedication to excellence, professionalism, and responsible stewardship in the business world. To qualify for the award, companies must provide evidence of a commitment to their customers, employees and suppliers, satisfying criteria in the following areas: Industry Advocacy; Customer Service & Safety Practices; Business Networking; Continuing Education; and Business Best Practices. “This award is a testament to our associates and their ongoing commitment to a culture of service and caring in a rapidly evolving industry,” said Carolina Handling President & CEO Brent Hillabrand. “We’re honored to be recognized by our customers, suppliers and industry peers for elite customer service, a commitment to collaboration and teamwork, and a passion of caring for the community.” The MVP Award is significant because it encompasses various facets beyond business achievements, according to Van Clarkson, President of Fairchild Equipment and 2024 MHEDA Chairman. “Achieving this recognition signifies that Carolina Handling has demonstrated exceptional leadership qualities, upheld industry standards, contributed positively to its community, and shown dedication to continuous improvement,” Clarkson said. “This acknowledgment not only elevates the company’s reputation among its peers but also instills confidence in its customers and community members, showcasing it as a leader in the materials handling world.”
Wrapping machinery manufacturer reports record-breaking year
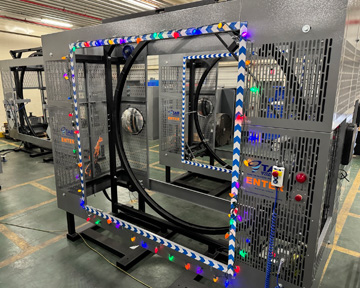
Another year, another record for the patented TAB Wrapper Tornado. Packaging machinery manufacturer TAB Industries, LLC has broken its record for annual revenue for its TAB Wrapper Tornado orbital wrapping systems. Topping $4 million in 2023 for the first time, the annual sales record was broken in large part due to a 180% increase in sales of the TAB Wrapper Tornado Smart Controls orbital wrappers. These wrapping machines enable a single operator to stretch wrap pallet loads automatically by remote control from a forklift seat in 30 seconds or less. In addition, the company introduced a wave of advances during 2023 that garnered substantial interest among new and repeat customers. Its new plastic film cutting system automatically cuts the end of the stretch wrap after wrapping and eliminates the use of blades; its new wrapping ring design both reduces vibrations and speeds lead times; its new laser cut machine guarding sports a powder-coated, anti-scuff finish; and its new preventative maintenance kits help operators keep their wrappers running in peak condition. When forecasting this record sales increase in 2022, the company embarked on a facility expansion that brought 14,000 additional square feet online in its Reading, Pa. headquarters during 2023. This helped increase manufacturing throughput by 20% and cut lead times to as short as four weeks. The company also formally secured two patents for the TAB Wrapper Tornado orbital wrapping technology during 2023 which drew significant attention for improving pallet wrapping speed and efficiency.
KHS systems combine efficiency with safety
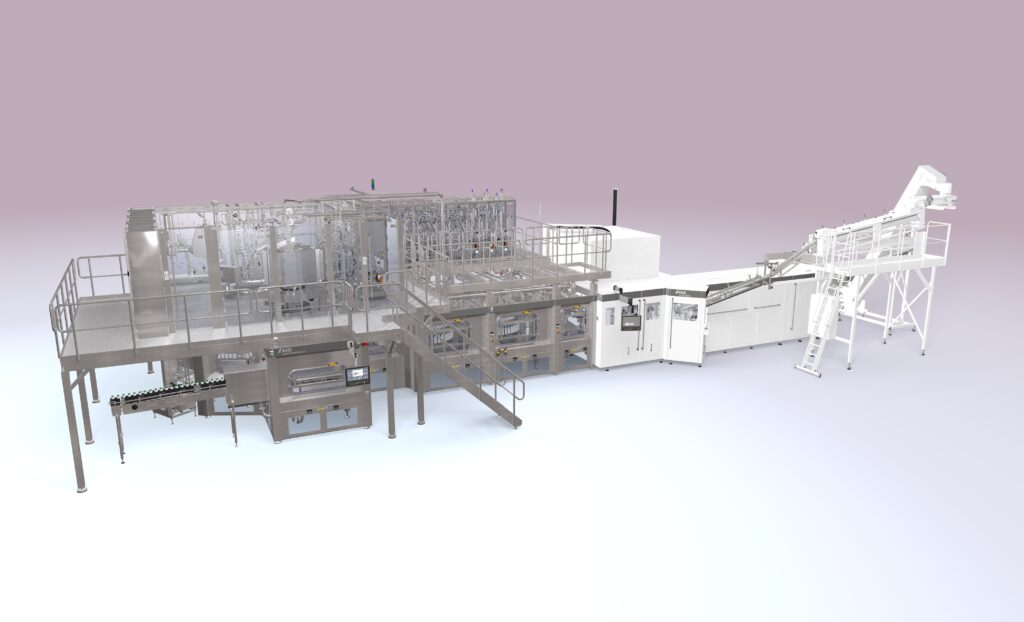
Sensitive beverages and flexible systems and solutions are the topics in focus at the KHS trade show booth for this year’s Anuga FoodTec. With its new InnoPET BloFill ACF-R aseptic block the Dortmund systems supplier wants to set new standards in safety and hygiene when it comes to bottle sterilization. Visitors can also find out all about the latest generation of InnoPET Plasmax barrier technology and the first module in the digital KHS ConnectApp service. “Economic success calls for maximum efficiency and availability in all filling and packaging processes. We provide innovative and resource-saving systems and solutions that fully satisfy all aspects of this demand,” says Tobias Wetzel, CSO of KHS. The most recent example of this is the new rotary InnoPET BloFill ACF-R aseptic block that combines the energy-efficient InnoPET Blomax Series V stretch blow molder with the rotary Innofill PET ACF-R filler for the very first time. Linear filters can process up to 14,000 bottles per hour. In contrast, the rotary aseptic block has a capacity of up to 36,000 1.0-liter bottles per hour and in the future is even to be available with a top output of 48,000 500-milliliter bottles an hour. The new plant engineering achieves a sterility of log 6 inside the bottles – which is equivalent to a reduction in germs of 99.9999%. “Our linear aseptic fillers, also blocked, have long proved themselves in practice in the filling of sensitive beverages into PET bottles, where maximum safety is of the essence. The newly developed rotary aseptic filler in the higher capacity range is thus the next logical step. With this, we also want to set standards regarding the machine’s hygienic properties,” Wetzel promises. Effective protection for sensitive beverages KHS consciously focuses on bottle sterilization that – unlike preform sterilization – can also be combined with the KHS FreshSafe PET coating system and thus offers additional barrier protection for sensitive beverages. In this variant, all potential germs are removed from the containers directly before filling. This process gives bottlers more flexibility and greater availability during format changeovers than preform sterilization, as here changing the stretch blow molds disturbs the sterile state of the block. KHS visitors to the exhibition can also look forward to discovering the latest generation of Plasmax coating technology. With this pioneering technique, a wafer-thin layer of chemically pure glass is applied to the insides of PET bottles, with bottle recyclability nevertheless fully retained. This protects sensitive products such as fruit juice, wine, beer, soft drinks, ketchup, sauces, and other liquid foods from oxidation and loss of CO2, meaning that they keep for considerably longer. KHS has continuously improved this procedure over the years and now brought it up to the next level. The result is better performance, quality and flexibility, and a higher degree of efficiency. Consistent expansion of the digital service portfolio In addition, the turnkey supplier’s range of digital services is now to be supplemented by KHS ConnectApp which provides two major extra benefits: Data-based transparency regarding the key line performance indicators helps with decision-making processes. Support with system operation. The first KHS ConnectApp function is the Guide module that with its interactive work instructions and powerful notification management system helps to ensure trouble-free workflows during inspection and maintenance or when training new employees, for instance. Moreover, all work steps can be documented with the app. “By expanding our digital service portfolio, and especially thanks to the introduction of KHS ConnectApp, we’re laying the foundations for further optimization and efficient organization of the entire system operation and management,” explains Wetzel. The KHS Group will be presenting its plant engineering at Booth B070 C089 in Hall 5.1 at Anuga FoodTec in Cologne, Germany, from March 19 to 22, 2024.
Tompkins Solutions to showcase robotics and warehouse automation at MODEX 2024
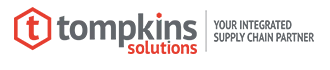
Tompkins Solutions, a supply chain consulting and material handling integration firm, has announced that it will be showcasing some of the industry’s latest warehouse robotics and automation solutions in booth #A11323 at MODEX 2024, March 11-14 at the Georgia World Congress Center in Atlanta. Tompkins Solutions’ newly redesigned state-of-the-art booth will include a technology area where visitors can see live demonstrations of hybrid automation solutions that are flexible and scalable to accommodate a variety of applications and evolving needs. The company’s team of experts will also be on-site to discuss the new solutions and speak with visitors about their unique supply chain challenges. Some of the specific technologies and systems Tompkins Solutions will have on display and in action at the booth include: Soft Robotics mGripAI high-speed picking solution utilizing AI and 3D vision technology Geek+ P800 shelf-to-person picking solution Tompkins Robotics tSort portable, automated unit and parcel sortation system Tompkins Solutions Cornerstone warehouse control system (WCS) “In the past, many companies may have been hesitant to invest in automated material handling systems due to the large capital expense and constantly changing demands,” said David Latona, CEO of Tompkins Solutions. “We’re excited to show how these innovative automation solutions enable logistics operations of all types and sizes to increase efficiency, reduce costs, and remain agile in today’s dynamic environment.” Visit Tompkins Solutions at booth #A11323 in Hall A to learn more about the latest innovations in warehouse automation and supply chain operations.
Brent Poulton appointed as new president of Cromer Material Handling
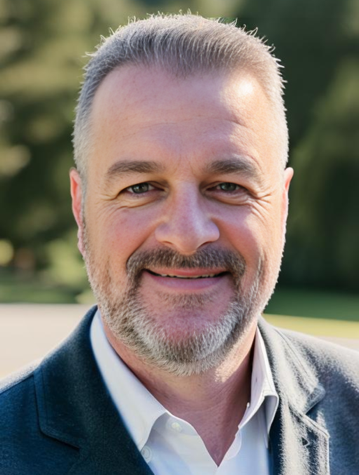
Cromer Material Handling, the West Coast’s trusted material handling provider since 1989, has announced that Brent Poulton has been appointed as President of the business, overseeing all seven dealerships under the Cromer umbrella. Poulton brings a wealth of experience and a proven track record of strategic leadership and business development within the material handling industry. “I’m thrilled to continue my journey with the GNCO organization as the President for Cromer Material Handling,” said Brent Poulton. “I look forward to working with the Cromer team to continue to build on what they’ve already accomplished and continue to grow and develop the business.” Poulton joins Cromer after most recently serving as Chief Operating Officer at Naumann Hobbs Material Handling, following thirteen years at Caterpillar leading the parts & service support operations in the Mid-Atlantic. Poulton’s demonstrated leadership, knowledge of operational efficiencies, and extensive market knowledge will shape the future success of the company.
Hubtex acquires Design Storage and Handling

German forklift manufacturer Hubtex has acquired Design Storage and Handling and will now known as HUBTEX North America. New Managing Director Alexander Baumann is responsible for North and Central America business. For over 30 years, Design Storage and Handling sold the HUBTEX Group’s products in the North and Central American markets with considerable success. The lift truck manufacturer HUBTEX has now acquired all shares in the general importer and will be looking after its North American customers under its own name. “We’re still the partner you can trust for transporting long, heavy, and bulky loads. But now we’re expanding this expertise beyond the confines of the steel industry, taking in the building materials trade and the timber and automotive industries as well – which our products are the perfect fit for. We guarantee users a reliable supply of spare parts, top-quality service, and flawless production processes.” says Alexander Baumann In the USA, HUBTEX aims to further develop the steadily growing market for multidirectional forklifts and special trucks. This includes opening a new depot on the west coast of America – in California, to be precise – alongside our existing major branches in Ohio and Virginia,” explains HUBTEX General Manager Hans-Joachim Finger “We’ve already laid the necessary groundwork and increased the size of our demonstration fleet. Establishing a presence in California is just one of the things we’re doing to get closer to our existing customers, learn even more about what they need, and showcase our products to new users too.” In addition, HUBTEX ensures the rapid availability and on-time delivery of standard machines. Besides the two branch locations, sales and service staff are also active in Washington State, Oregon, New Mexico, Texas and California. HUBTEX North America will sell bespoke material handling technology for the production logistics solutions engineered by Genkinger, a manufacturer of custom-made industrial trucks, as well as specialist airport and air cargo equipment from DIMOS Maschinenbau.
Kadant acquires KWS Manufacturing Company
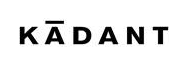
Kadant Inc. (KAI) announced it has completed the acquisition of KWS Manufacturing Company, Ltd. (KWS) for approximately $84 million in cash, subject to certain customary adjustments. The acquisition was financed primarily through borrowings under Kadant’s revolving credit facility. KWS is a manufacturer of conveying equipment for the bulk material handling industry. The company manufactures screw conveyors, screw feeders, slide gates, and bucket elevators for process industries, including the food, chemicals, and wood industries. Located in Burleson, Texas, with approximately 165 employees, KWS had revenue of $45 million for the trailing twelve months ended September 30, 2023. KWS will become part of Kadant’s Material Handling reporting segment. “We are pleased to welcome our colleagues from KWS to the Kadant family,” said Jeffrey L. Powell, president and chief executive officer of Kadant. “Our acquisition of KWS expands our respective product portfolios and enhances our internal capabilities. With our shared focus on bringing highly engineered customer solutions to process industries and our past successes working together, we believe KWS is an excellent fit with Kadant.” William C. Mecke, president of KWS, commented, “We are proud of the leading position KWS has established in the screw conveyor market. Our reputation for quality products and excellent service fits well with Kadant’s culture and values. We look forward to being a part of Kadant and leveraging opportunities to increase value for our customers and other stakeholders.” Conference Call Kadant will hold a conference call and webcast on Monday, January 29, 2024 at 1:00 p.m. eastern time to discuss the acquisition. To listen to the call and view the webcast, go to the “Investors” section of the Company’s website at www.kadant.com. Participants interested in joining the call’s live question and answer session are required to register by clicking here or selecting the Q&A link on our website to receive a dial-in number and unique pin. It is recommended that you join the call 10 minutes prior to the start of the event. A replay of the webcast presentation will be available on the Company’s website through March 1, 2024.
RightHand Robotics introduces the RightPick™ 4 System
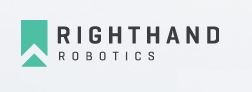
The next-generation autonomous robotic piece-picking system for warehouse order fulfillment. Building on its industry-leading predecessor, the RightPick 4 system can handle items up to 25% larger and 50% heavier, significantly reducing the need for human intervention. RightHand Robotics, a data-driven, autonomous robotic picking solution for order fulfillment, announced the launch of its next-generation solution, the RightPick™ 4 system. The picking system revolutionizes the level of autonomy and reliability of robotic order fulfillment in modern warehouse operations and distribution centers. The RightPick 4 system showcases enhanced AI-based software algorithms, an upgraded sensor suite, and newly designed hardware that enables a larger picking range of item SKUs, advanced item handling capacity, and increased system autonomy. With improved picking and grasping techniques, the RightPick 4 system maximizes reliability and enables faster integration through novel approaches in both software and hardware. “Retailers continue to have challenges with growing demand for faster and more accurate order fulfillment, in part due to ongoing labor challenges. With the launch of the RightPick 4 system, we have created a new piece-picking solution that delivers increased autonomy, reliability, and serviceability,” said Brendon Bielat, VP of Product & Marketing. “We have trained our system by leveraging more than a petabyte of operational data, gathered for over eight years from picking tens of millions of items around the globe. This massive amount of data has helped us create a smarter, more robust solution for real-world fulfillment challenges.” The RightPick 4 system is reducing the need for human intervention by deploying advanced gripping strategies to pick and place more items, even those it has never seen before. With improved smart grasp and suction seal quality detection, RightHand Robotics can enable autonomous piece-picking for market verticals such as general merchandise, office supplies, apparel, pharmaceutical products, cosmetics, and 3PLs. Powered by RightPick™ AI, the RightPick 4 system is continuously learning and improving on the overall range of items that can be picked successfully. “We are thrilled to unveil RightPick 4, a product realized through collaboration with customers and partners. We have hardened our product with a focus on reliability and autonomy so that our customers can increase their operational capacity without being hindered by labor volatility,” said Brian Owen, President & CEO. “The total market potential for the RightPick 4 system is staggering, especially in global, post-pandemic logistics. It’s no longer just early adopters approaching our technology. The general awareness of robotic piece-picking has increased, and omnichannel retailers are realizing it’s a necessity. The RightPick 4 system is a competitive advantage with a quick time-to-value for stakeholders within the supply chain.”To learn more about the RightPick 4 piece-picking system and how it exceeds demand with best-in-class features and capabilities, visit RightHand Robotics at MODEX 2024 in Atlanta, Georgia, at booth #C6479. You can also visit the RightHand Robotics website to learn more.
Doosan Material Handling Solutions moves operations to a new facility
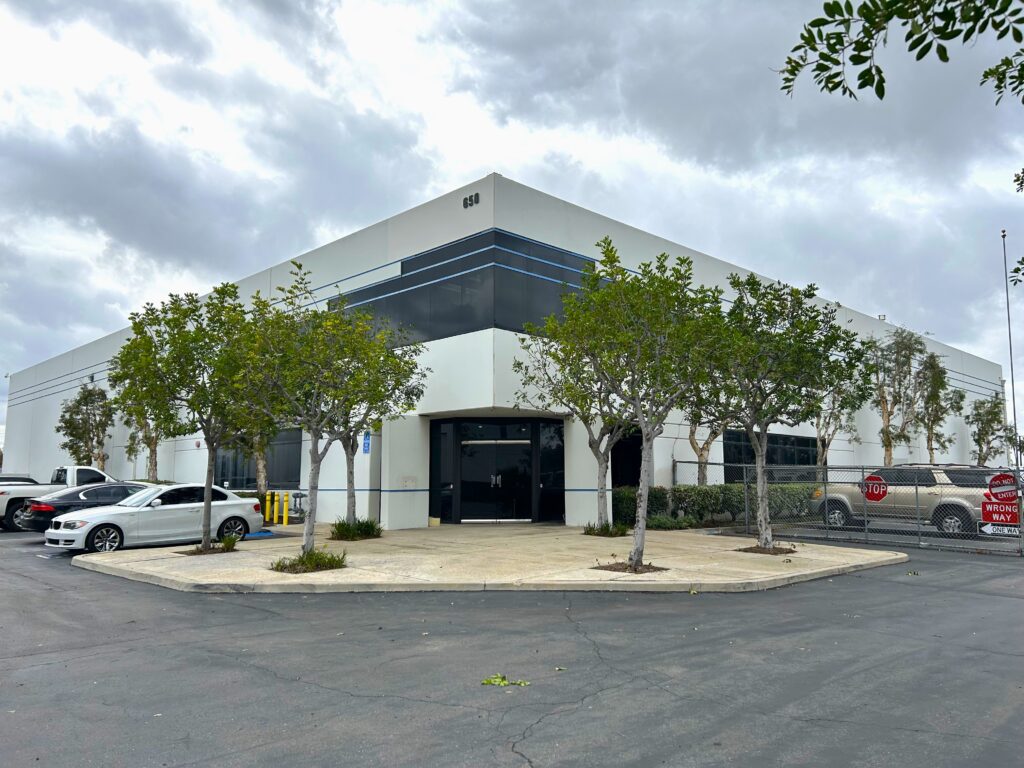
Doosan Material Handling Solutions, a forklift dealership in Southern California, announced that it has moved its business to a larger and more accessible location in Orange County. The new building will allow the company to expand its operations and provide enhanced customer service support. The modern complex, located at 650 W Freedom Ave, has more than twice the space, featuring 31,000 square feet to showcase its comprehensive inventory of new and used forklift and warehouse vehicles available for purchase, rent, and lease during business hours of 8 a.m. – 5 p.m. PST. Expert mechanics are available to provide onsite equipment support for all makes and models within the Los Angeles, Orange, San Bernardino, and Riverside County areas. Shop service is available for large jobs, painting, rebuilds, and more. “We are thrilled to announce our move in efforts to expand business operations and attract top talent to reach our goal of becoming the top dealership in Southern California,” said General Manager Jaime Gomez. “Our focus is to create long-lasting partnerships by providing top-quality service and products that drive profitability for those we serve.”
Thomson Prestress adds a Shuttlelift gantry crane to operation
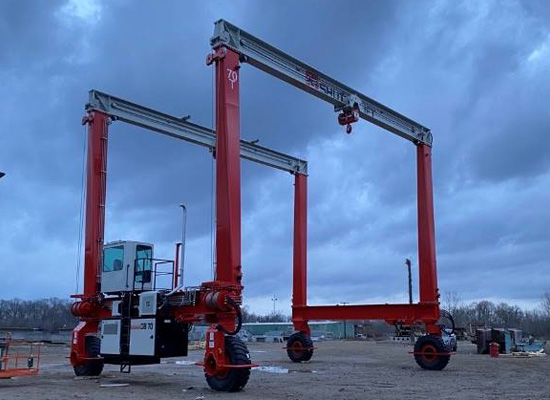
Thomson Prestress, formerly Concrete Products of Tennessee, has added a Shuttlelift DB70 gantry crane to their equipment fleet to enhance the production of their precast and prestressed concrete products. The new double-beam rubber tired gantry crane joins a Shuttlelift SB50 (Single Beam) already onsite and in use since 2011. Thomson Prestress is a family-owned operation located in Jackson, TN and has been in high-quality precast and prestressed concrete products since 1961. They specialize in products for use in bridges, commercial buildings, railroads, and marina construction. They rely heavily on their rubber-tired gantry cranes to move, store, and load out products on their 50-acre facility. With a continued backlog of business, there was a need for another gantry crane onsite to efficiently cast and deliver products on time to customers. The decision to go with Shuttlelift was easy after experiencing the quality and customer service provided with their SB50 gantry crane. “After purchasing our single beam 50 ton from Shuttlelift in 2011, we had decided that our next gantry crane purchase would also be from Shuttlelift”, said Tory Boston, Production Manager at Thomson Prestress. At Thomson Prestress they produce concrete infrastructure products in many shapes and sizes to meet the specific needs of their customers. Due to the many different configurations, there was a need for a custom spreader bar to ensure all products could be lifted. Shuttlelift specializes in customization, including the design and fabrication of spreader beams, and designed a 75’ long beam with sliding lift points to accommodate varying pick points along the product. The new Shuttlelift DB70 is also equipped with a wireless remote control, AVT fuel saver, and work & drive lights for operating at night or early hours of the morning. “With increased technological advancement, there has been a variety of benefits in using this machine compared to what our operators have used in the past”, said Boston of the machine features and options. The wireless remote control comes standard on all Shuttlelift DB and SB series gantry cranes allowing the operator free movement for better line of site and allows the operator to also assist in the rigging process. The Automatic Variable Throttle (AVT) is a built-in engine program that automatically adjusts the engine RPM to draw only the power you need to complete the task at hand, significantly reducing fuel consumption and increasing component life. Shuttlelift and Thomson Prestress have shared a great business relationship for over a decade so the order and delivery process was simple. “It has been a stress-free experience and the process was speedy and effortless”, said Boston. He added, “Our operators are thoroughly satisfied with the quality and functionality of the equipment.”
U.S. Rail Traffic for the week ending January 20, 2024
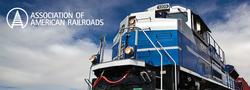
The Association of American Railroads (AAR) reported U.S. rail traffic for the week ending January 20, 2024. For this week, total U.S. weekly rail traffic was 397,553 carloads and intermodal units, down 13.2 percent compared with the same week last year. Total carloads for the week ending January 20 were 173,371 carloads, down 22.4 percent compared with the same week in 2023, while U.S. weekly intermodal volume was 224,182 containers and trailers, down 4.5 percent compared to 2023. None of the 10 carload commodity groups posted an increase compared with the same week in 2023. Commodity groups that posted decreases compared with the same week in 2023 included coal, down 21,055 carloads, to 47,731; nonmetallic minerals, down 11,953 carloads, to 18,628; and grain, down 5,246 carloads, to 15,752. For the first three weeks of 2024, U.S. railroads reported a cumulative volume of 594,824 carloads, down 10.8 percent from the same point last year; and 677,439 intermodal units, up 0.2 percent from last year. Total combined U.S. traffic for the first three weeks of 2024 was 1,272,263 carloads and intermodal units, a decrease of 5.3 percent compared to last year. North American rail volume for the week ending January 20, 2024, on 12 reporting U.S., Canadian and Mexican railroads totaled 265,838 carloads, down 20.3 percent compared with the same week last year, and 289,982 intermodal units, down 6.0 percent compared with last year. Total combined weekly rail traffic in North America was 555,820 carloads and intermodal units, down 13.5 percent. North American rail volume for the first three weeks of 2024 was 1,778,528 carloads and intermodal units, down 5.6 percent compared with 2023. Canadian railroads reported 74,967 carloads for the week, down 21.5 percent, and 54,327 intermodal units, down 15.6 percent compared with the same week in 2023. For the first three weeks of 2024, Canadian railroads reported a cumulative rail traffic volume of 424,647 carloads, containers, and trailers, down 9.8 percent. Mexican railroads reported 17,500 carloads for the week, up 18.1 percent compared with the same week last year, and 11,473 intermodal units, up 24.0 percent. Cumulative volume on Mexican railroads for the first three weeks of 2024 was 81,618 carloads and intermodal containers and trailers, up 17.7 percent from the same point last year. To view the Rail Traffic charts, click here.
Raymond implements energy storage and solar energy generating system

New behind-the-meter storage practice demonstrates potential benefits, including lower costs The Raymond Corporation has finalized its deployment of a full-scale battery energy storage system, solar microgrid array, and warehouse energy management system at its distribution warehouse in Greene, New York. The goal is to demonstrate continuous system benefits of lower energy costs, peak demand management, and resiliency for warehouses. “With the implementation of behind-the-meter storage at our distribution center, we have gained insights into the benefits of the system in material handling applications specifically related to alleviating increased demand associated with charging of advanced power solutions including lithium,” said Jennifer de Souza, vice president, energy solutions, procurement and leasing, The Raymond Corporation. “We are excited to continue to demonstrate a new energy storage process and solution for warehouse energy management that will reduce utility costs for warehouse owners.” This energy storage program began as a joint project in March 2019 with Binghamton University and was partially funded by a $1 million award from the New York State Energy Research and Development Authority. The first phase included the installation of a 200kW Photovoltaic (solar) system and a 250kW/420kWh Battery Energy Storage System at Raymond’s distribution warehouse. The second and third stages of the project developed and demonstrated the installation of advanced lithium-ion battery chargers utilizing proprietary software to balance grid and microgrid charging for power optimization with a priority on renewable energy as the primary goal. The microgrid installation has demonstrated the benefits of behind-the-meter energy generation and storage combined with forklift-to-grid charging systems. “The energy storage solution can help transform warehouses into controllable energy hubs or Virtual Power Plants (VPP), which can be optimized to support the power grid during normal and peak grid conditions while improving sustainability and carbon neutrality,” de Souza said. With insights from this project, Raymond is now deploying the installation of a front-of-the-meter rooftop system at its Syracuse, New York, parts distribution facility. See Raymond Corporation at MODEX 2024 Booth #B5406
Smart Vision Lights introduces RHI200-DO Lightgistics machine vision light
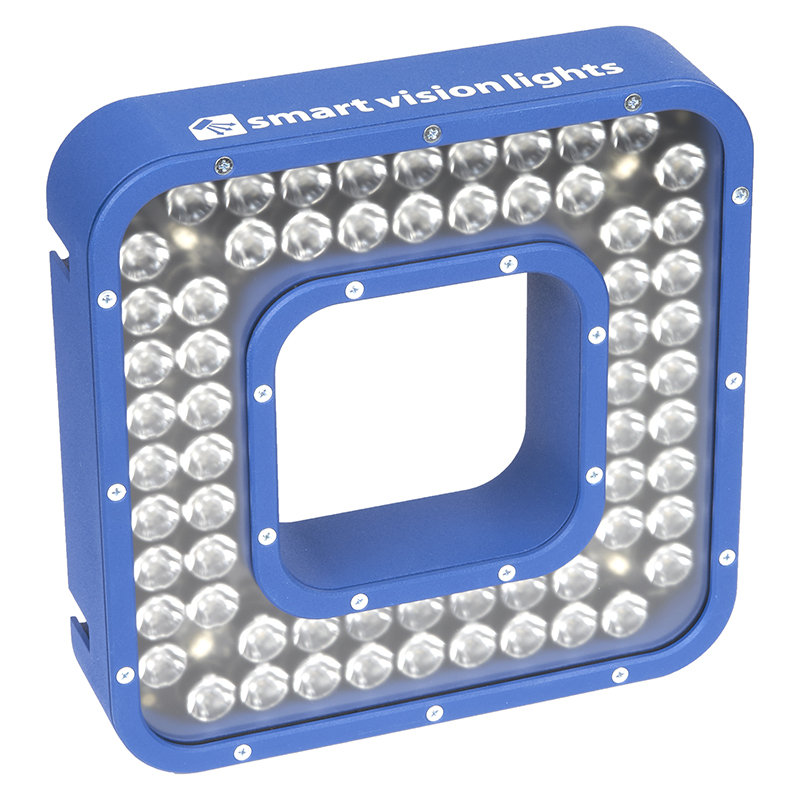
With hidden strobe technology Smart Vision Lights (SVL), a design and manufacture of innovative LED illumination solutions, has introduced the RHI200-DO Lightgistics series light, which features 64 LEDs in a 205 mm x 205 mm ring light for intense uniform lighting at long working distances of up to 2000 mm. Equipped with Hidden Strobe technology, the light delivers all the advantages of strobing without the disturbance and disorientation often linked to LED strobe lights. Hidden Strobe technology allows LEDs to automatically trigger thousands of times per second, pulsating at speeds imperceptible to the human eye and generating the appearance of uninterrupted illumination. The innovative technology helps maximize the abilities of machine vision systems while safeguarding employees from the disorienting effects commonly associated with flashing lights. “Today’s high-speed machine vision systems use LEDs that frequently pulse to capture images of rapidly moving objects, but this strobing effect can generate unpleasant and potentially hazardous work environment conditions,” according to Steve Kinney, director of training, compliance, and technical solutions at Smart Vision Lights. “The RHI200-DO minimizes these drawbacks by utilizing Hidden Strobe technology, which enables high-speed machine vision systems to leverage the power of strobed LEDs without inadvertently creating safety risks or requiring shielding.” Boost Logistics Operations Through Lighting Lightgistics lights specifically address the challenges of accurate high-speed barcode reading and optical character recognition (OCR) on highly reflective plastic wraps and shipping bags. Dual OverDrive™ technology utilizes SVL’s new Deca OverDrive™ and standard OverDrive™ engines, which together allow end users to easily attach polarizers that maximize light output in high-speed conveyor systems. “Logistics and warehousing businesses today cannot afford to sacrifice speed and throughput, which means any machine vision system deployed on the floor must be capable of accurate code reading, even when reading through plastic,” said Kinney. “Lightgistics LEDs help improve logistics operations by delivering lighting that is 10 times brighter than standard continuous mode, which helps improve track-and-trace while maintaining the speeds needed for today.” The RHI200-DO is an OverDrive™–only light source with a high-intensity ring light. Its integrated camera mount fits most common machine vision cameras and can be directly connected and controlled through a camera’s trigger output. The RHI200-DO’s onboard charging capacitors ensure powerful bursts of energy while maintaining a low consistent electrical draw. The IP65-rated bright field operates at working distances between 500 mm and 2000 mm with 10-, 14-, and 30-degree lens options.