August Manufacturing Technology Orders fall short of 2023; Outlook optimistic for remainder of 2024
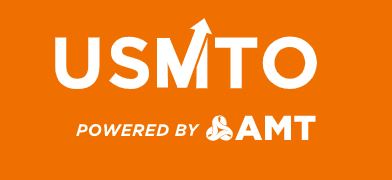
Orders of manufacturing technology, measured by the U.S. Manufacturing Technology Orders (USMTO) report published by AMT – The Association For Manufacturing Technology, totaled $360.8 million in August 2024. These orders for metalworking machinery increased 22.7% from July 2024 but fell 12% short of August 2023 orders. Year-to-date orders reached $2.81 billion, a decline of 11.5% compared to the first eight months of 2023. While orders continue to lag behind those placed in 2023, the level of order activity remains above historical levels. August 2024 orders are 3.8% above those placed in a typical August. This trend indicates the industry is still undergoing a period of normalization following the COVID disruptions rather than an actual decline. Historically elevated capacity utilization rates across durable goods manufacturers indicate a genuine need for additional investment in manufacturing technology. Contract machine shops, the largest manufacturing technology customers, increased the number of units ordered and the value of their orders for the first time since March 2024. This growth in a key customer segment is a welcome sign after a sluggish July, which saw the lowest value of orders since May 2020 and the fewest units ordered since July 2010. Since job shops typically absorb elevated capacity needs from OEMs, this buying trend indicates that production could continue to grow. Manufacturers in the aerospace sector increased the value of their orders by 13% from July to August 2024, but the number of units increased by nearly 27% at that same time. This indicates their purchases are for additional capacity, which is confirmed by the sector’s persistently rising capacity utilization rates. While machinery orders from aerospace parts manufacturers have been strong in the past few months, the ongoing strike of Boeing machinists has the potential to dampen this demand. It would be tempting to compare this to the 2023 United Autoworkers strike, which almost had no impact on manufacturing technology orders from the automotive sector. However, the automotive industry had already been pulling back orders at that time after a historically elevated buying cycle over the summer of 2023. Additionally, capacity utilization rates were falling, and inventories were growing leading into the strike. The aerospace sector is in a decidedly different position, with increased orders, a buying cycle on an upswing, and capacity utilization rising for the past three years. Only time will tell how the Boeing strike could impact machinery orders. Although August 2024 orders fell short of those placed in 2023, the outlook for the remainder of the year remains optimistic. The electric atmosphere at September’s IMTS, the largest manufacturing technology trade show in the Western Hemisphere, was a welcome sign that manufacturers need additional capacity as well as solutions to improve quality and efficiency. With the upcoming U.S. presidential election and the Federal Reserve beginning to reduce interest rates and signaling additional reductions, two of the major issues giving pause to further capital investment will be alleviated by year’s end. Given these factors and the coming expiration of bonus depreciation of capital equipment, the momentum of order activity in the last four months of 2024 will likely accelerate. It could carry over into 2025, as forecast by experts at AMT’s annual MTForecast conference. # # # The United States Manufacturing Technology Orders (USMTO) Report is based on the totals of actual data reported by companies participating in the USMTO program. This report, compiled by AMT – The Association For Manufacturing Technology, provides regional and national U.S. orders data of domestic and imported machine tools and related equipment. Analysis of manufacturing technology orders provides a reliable leading economic indicator as manufacturing industries invest in capital metalworking equipment to increase capacity and improve productivity. USMTO.com.
Episode 528: Streamlining Inventory and Warehouse Management with Cin7
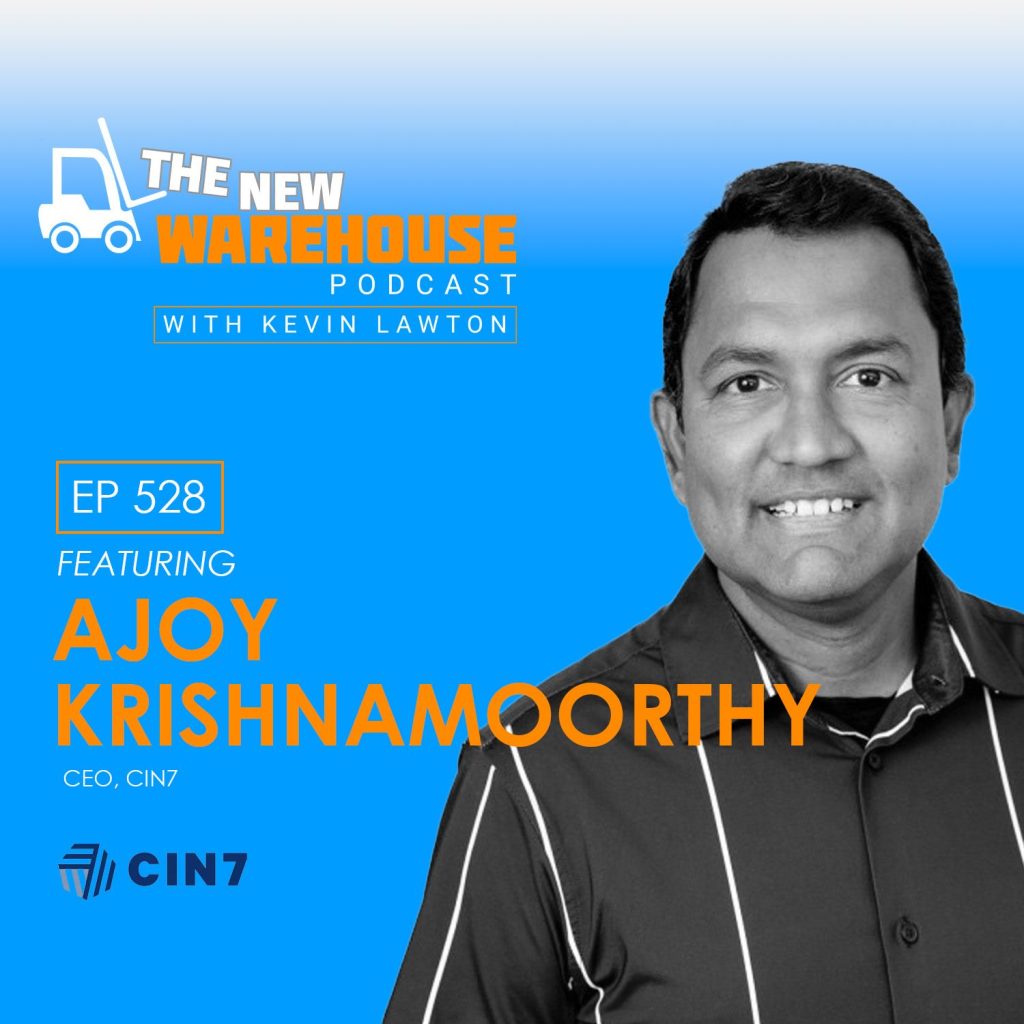
In this episode of The New Warehouse Podcast, Ajoy Krishnamoorthy, CEO of Cin7, discusses how their platform transforms operations by integrating software solutions for inventory, order, and warehouse management. Cin7’s mission is to streamline processes and foster a better workplace culture by simplifying software systems for their users. The conversation dives into how Cin7’s powerful integrations, efficient onboarding, and broad platform capabilities can eliminate operational silos, ensuring visibility and control over supply chain functions. Streamlining Inventory with Unified Platforms A significant challenge in the supply chain is operating without visibility across different systems. Cin7 aims to fix that. Ajoy explains, “Our customers come to us over ERP because it’s super easy to onboard.” Cin7’s platform offers comprehensive solutions, integrating over 700 systems like Shopify, Amazon, and QuickBooks to ensure smooth workflows and real-time data alignment. This level of integration helps eliminate guesswork in supply chain operations, allowing teams to stay synchronized and efficient. Optimizing Warehouse Efficiency Through Streamlined Processes Warehouse efficiency often hinges on clear visibility and intuitive processes. Ajoy points out that Cin7’s platform allows users to set up various picking mechanisms, such as batch or zone picking, which can drastically reduce the time spent on order fulfillment. He notes, “The purpose of good software is to make the user a superhero.” By ensuring that employees can find products quickly and with confidence, Cin7 enhances both employee satisfaction and operational efficiency. Leveraging Data to Drive Smarter Decisions Cin7 doesn’t just uncover inefficiencies; it actively helps businesses address them. Ajoy shares results from a recent cohort, “Our average customers in that 30 cohort had $500,000 in overstock.” Cin7’s inventory forecasting tools analyze sales patterns and supplier lead times to predict demand more accurately. Ajoy elaborates on how Cin7 tackles overstock issues, explaining, “We’re now starting to surface that information up to our customers to get them to be smarter regarding replenishment.” This approach helps businesses avoid unnecessary reorders and direct their capital toward products in demand, ultimately reducing overstock and stockouts. Key Takeaways Cin7 eliminates operational silos by integrating inventory, order, and warehouse management on one platform. The platform’s efficiency tools, like batch and zone picking, enhance employee productivity and operational speed. Data-driven insights help companies avoid costly overstock and stockouts, leading to better financial outcomes. The New Warehouse Podcast EP 528: Streamlining Inventory and Warehouse Management with Cin7
IRS provides Hurricane Milton relief; May 1 deadline now applies to individuals and businesses in all of Florida; many businesses qualify for deposit penalty relief
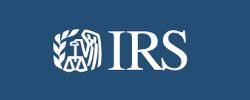
The Internal Revenue Service today announced relief for individuals and businesses in 51 counties in Florida due to Hurricane Milton. Individuals and businesses in six counties that previously did not qualify for relief under either Hurricane Debby or Hurricane Helene will receive disaster tax relief beginning Oct. 5, 2024, and concluding on May 1, 2025. They are Broward, Indian River, Martin, Miami-Dade, Palm Beach, and St. Lucie. In addition, individuals and businesses in 20 counties previously receiving relief under Debby but not Helene will receive disaster tax relief under Hurricane Milton from Aug. 1, 2024, through May 1, 2025. They are Baker, Brevard, Clay, DeSoto, Duval, Flagler, Glades, Hardee, Hendry, Highlands, Lake, Nassau, Okeechobee, Orange, Osceola, Polk, Putnam, Seminole, St. Johns, and Volusia counties. As a result, affected taxpayers in all of Florida now have until May 1, 2025, to file various federal individual and business tax returns and make tax payments, including 2024 individual and business returns normally due during March and April 2025 and 2023 individual and corporate returns with valid extensions and quarterly estimated tax payments. The IRS is offering relief to any area designated by the Federal Emergency Management Agency (FEMA). Individuals and households that reside or have a business in any one of the localities listed above qualify for tax relief. The current list of eligible localities is always available on IRS.gov’s Tax Relief in Disaster Situations page on IRS.gov. Filing and payment relief Hurricane Milton-related tax relief postpones various tax filing and payment deadlines that occurred beginning on Oct. 5, 2024, and ending on May 1, 2025 (postponement period). As a result, affected individuals and businesses will have until May 1, 2025, to file returns and pay any taxes that were originally due during this period. This means, for example, that the May 1, 2025, deadline now applies to: Any individual or business with a 2024 return is normally due in March or April 2025. Any individual, C corporation, or tax-exempt organization with a valid extension can file their calendar year 2023 federal return. The IRS noted, however, that payments on these returns are not eligible for the extra time because they were due last spring before the hurricane occurred. 2024 quarterly estimated tax payments are normally due on Jan. 15, 2025, and 2025 estimated tax payments are normally due on April 15, 2025. Quarterly payroll and excise tax returns are normally due on Oct. 31, 2024, Jan. 31, 2025, and April 30, 2025. In addition, for localities affected by Hurricane Milton, penalties for failing to make payroll and excise tax deposits due on or after Oct. 5, 2024, and before Oct. 21, 2024, will be abated as long as the deposits are made by Oct. 21, 2024. Localities eligible for this relief are Alachua, Baker, Bradford, Brevard, Broward, Charlotte, Citrus, Clay, Collier, Columbia, DeSoto, Dixie, Duval, Flagler, Gilchrist, Glades, Hamilton, Hardee, Hendry, Hernando, Highlands, Hillsborough, Indian River, Lafayette, Lake, Lee, Levy, Madison, Manatee, Marion, Martin, Miami-Dade, Monroe, Nassau, Okeechobee, Orange, Osceola, Palm Beach, Pasco, Pinellas, Polk, Putman, Sarasota, Seminole, St. Johns, St. Lucie, Sumter, Suwannee, Taylor, Union and Volusia counties. Deposit penalty relief and other relief were previously provided to taxpayers affected by Debby and Helene. For details, see the Florida page on IRS.gov. The Disaster Assistance and Emergency Relief for Individuals and Businesses page also has details and information on other returns, payments, and tax-related actions qualifying for relief during the postponement period. The IRS automatically provides filing and penalty relief to taxpayers with an IRS address of record in the disaster area. These taxpayers do not need to contact the agency to get this relief. It is possible that an affected taxpayer may not have an IRS address of record located in the disaster area because they moved to the disaster area after filing their return. In these unique circumstances, the affected taxpayer could receive a late filing or late payment penalty notice from the IRS for the postponement period. The taxpayer should call the number on the notice to have the penalty abated. In addition, the IRS will work with any taxpayer who lives outside the disaster area but whose records are necessary to meet a deadline occurring during the postponement period and are located in the affected area. Taxpayers qualifying for relief living outside the disaster area must contact the IRS at 866-562-5227. This also includes workers affiliated with a recognized government or philanthropic organization who assist in relief efforts. Disaster area tax preparers with clients outside the disaster area can choose to use the Bulk Requests from Practitioners for Disaster Relief option, described on IRS.gov. Additional tax relief Individuals and businesses in a federally declared disaster area who suffered uninsured or unreimbursed disaster-related losses can choose to claim them on either the return for the year the loss occurred (in this instance, the 2024 return normally filed next year) or the return for the prior year (the 2023 return filed this year). Taxpayers have extra time – up to six months after the due date of the taxpayer’s federal income tax return for the disaster year (without regard to any extension of time to file) – to make the election. For individual taxpayers, this means Oct. 15, 2025. Be sure to write the FEMA declaration number – 3622-EM – on any return claiming a loss. See Publication 547, Casualties, Disasters, and Thefts, for details. Qualified disaster relief payments are generally excluded from gross income. In general, this means that affected taxpayers can exclude from their gross income amounts received from a government agency for reasonable and necessary personal, family, living, or funeral expenses, as well as for the repair or rehabilitation of their home or for the repair or replacement of its contents. See Publication 525, Taxable and Nontaxable Income, for details. Additional relief may be available to affected taxpayers participating in a retirement plan or individual retirement arrangement (IRA). For example, a taxpayer may be eligible to take a special disaster distribution that would not be subject to the additional 10% early distribution tax, allowing the taxpayer to spread the income over three
ALAN HURRICANE MILTON SITUATIONAL REPORT: Thursday, October 10, 2024
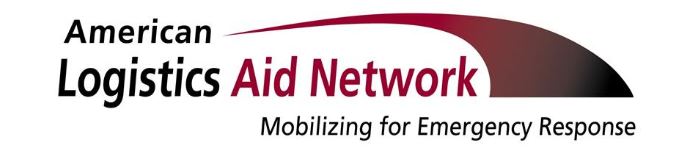
American Logistics Aid Network is mobilized for Hurricane Milton. As part of our response efforts, we are committed to providing you with the latest information and updates on supply chain impacts via our periodic Situation Reports, which can be found below in this email and on our website. ALAN has been improving logistics response to disasters for 19 years, and the need is greater now than ever. Please donate today to help us continue our work for many more years to come. ACTIVATION UPDATE As Floridians struggle with the aftermath of Hurricane Milton, the American Logistics Aid Network (ALAN) has begun supporting relief efforts and reminding members of the supply chain community that sharing their logistics know-how, space, equipment, and services is one of the most vital ways they can help. “The devastation Hurricane Milton and its many tornadoes have caused is heartbreaking. We mourn for those who have lost family members, pets, and homes, and we are already working hand-in-hand with various non-profit partners to deliver help,” said Kathy Fulton, ALAN’s Executive Director. ALAN received its first request for Hurricane Milton-related logistics assistance earlier this week. In the coming weeks, Fulton anticipates it could receive dozens more, just as it has since Hurricane Helene struck various parts of the Southeast two weeks ago. “During the first 48 to 72 hours after a hurricane, most of the work on the ground is focused on search and rescue efforts,” Fulton said. “Because of this, ALAN usually doesn’t receive the first substantial wave of donated logistics requests until after that, when humanitarian organizations can get in, conduct their initial assessments, and determine what’s most needed.” “We know that can be frustrating for organizations that want to do something tangible as soon as possible. But we hope they will still be willing to provide their logistics help when the need arises, whether it’s in a few days, a few months – or even beyond that,” Fulton added. ALAN encourages organizations interested in joining its Hurricane Milton relief efforts to visit its Disaster Micro-Site at https://www.alanaid.org/operations/ frequently in the weeks and months ahead. That’s where ALAN will post any unfilled requests and currently features several open needs for Hurricane Helene and other ongoing disaster relief efforts. Those who wish to help ALAN by making a financial contribution instead can do so by going to https://www.alanaid.org/donate/. “Logistics professionals may not be first responders, but ensuring that relief supplies reach those in need is indeed a life-saving activity,” Fulton said. “We’re thankful to be part of a community that can play such a meaningful role under the most challenging of circumstances.” Please read the full news release, along with ALAN’s Ten Post-Hurricane Relief Takeaways, on the Breaking News section of our website. ITEMS OF INTEREST PSEMA Hurricane Milton Coordination Call via Zoom daily at 4 pm EDT Join Zoom Meeting https://us02web.zoom.us/j/86737741797?pwd=hAg1zTWdsbHKYRvnWIbbMAyKuJNWyZ.1 Meeting ID: 867 3774 1797 Passcode: 106474 FEDERAL EMERGENCY DECLARATIONS President Biden approved an Emergency Declaration for the Seminole Tribe of Florida on October 8, 2024, in preparation for Hurricane Milton’s impacts. President Biden approved an Emergency Declaration for Florida on October 7, 2024, in preparation for Hurricane Milton’s impacts. STATE EMERGENCY DECLARATIONS Florida Department of Health Surgeon General issued Emergency Order No. 24-003 on October 8, 2024, suspending statutes, rules, and orders pursuant to Executive Order 24-214 made necessary by Hurricane Milton. Waivers related to procurement, emergency medical licensure requirements, practitioner licensure requirements, prescription drug monitoring reporting, and mobile pharmacies. Florida Governor DeSantis issued Executive Order 24-215 on October 6, 2024, amending Executive Order 24-214. Florida Governor DeSantis issued Executive Order 24-214 on October 5, 2024, in preparation for Tropical Storm Milton’s impact on Florida. ACTIVE TRANSPORTATION WAIVERS Title: Florida Commissioner of Agriculture Simpson issued Executive Order 2024-016, suspending Florida Statutes relating to liquid fuel Effective: 10/08/24 | Expires on: 12/08/24 Description: Pursuant to Executive Order 2024-015, suspension of sections of Florida Statutes 527.0201, 527.021, 527.04, and 527.11, only for persons performing work of Category I Liquified Petroleum Gas Dealers in furtherance of emergency recovery efforts directly related to Hurricane Milton. Title: Florida Commissioner of Agriculture Simpson issued Executive Order 2024-015, suspending Florida Statutes relating to liquid fuel Effective: 10/07/24 | Expires on: 12/07/24 Description: Pursuant to Executive Order 2024-015, suspension of sections of Florida Statutes 526.02, 526.04, 526.05, and 526.07, relating to the sale, offer for sale, delivery, distribution, or storage of liquid fuels; all other provisions of chapter 526, Florida Statutes, shall remain in effect. Title: FMCSA Regional Emergency Declaration No. 2024-008 and Extension of Emergency Declarations Pursuant to 49 CFR 390.23 and 390.24 Effective: 10/04/24 | Expires on: 10/27/24 Description: The United States Department of Transportation (USDOT), Federal Motor Carrier Safety Administration (FMCSA) declares that an emergency exists that warrants the issuance of a Regional Emergency Declaration and extension of emergency declarations issued by State Governors to continue emergency relief granted from certain regulatory requirements in Parts 390-399 of the Federal Motor Carrier Safety Regulations (FMCSRs). This Declaration is in response to Hurricane Helene and its effects on people and property, including immediate threats to human life, public safety, and public welfare from heavy rains, strong winds, storm surge, high surf, and flooding. This declaration addresses the emergency conditions that create a need for immediate transportation relating to the restoration of essential supplies and services and provides necessary relief. Affected States included in this Declaration are Alabama, Florida, Georgia, North Carolina, South Carolina, Tennessee, Virginia, and West Virginia. The Presidential Declarations issued provide regulatory relief for up to 30 days of emergency relief from Federal regulations in 49 CFR 390 through 399. FMCSA issuing this Declaration and granting regulatory relief in accordance with 49 CFR 390.23 and 390.25, as set forth herein. Title: Florida Department of Transportation Secretary Perdue issued Emergency Order 24-12 Effective: 10/06/24 | Expires on: 10/21/24 Description: Pursuant to Executive Order No. 24-213, Secretary Perdue waives and suspends Florida Statutes 316.515(1-3), 316.535(1 and 3), 316.545(2 and 4), and 337.401(1)(a); and Rules 14-28.002(4 and 5), and 14-46.001(2) to allow for alternate size and weight restrictions on any vehicles transporting emergency equipment, services, supplies, or personnel, and agricultural commodities and citrus as recommended by Commissioner of Agriculture. Title: Florida Highway Safety and Motor Vehicle Executive Director issued Emergency Order
Forklift-International.com expands U.S. Market Presence, Celebrates major milestone with 150 dealer locations and over 10,000 equipment listings
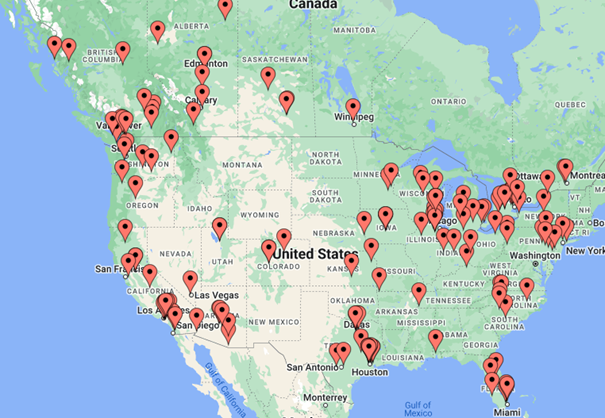
Forklift-International.com, the online marketplace for material handling equipment, has announced a major milestone for its U.S. operations. The platform currently features over 10,000 forklifts, telehandlers, and other equipment from more than 150 dealer locations across North America. This achievement reflects the company’s rapid growth and its commitment to serving the needs of the U.S. material handling industry. “Reaching 150 dealer locations in the U.S. marks a significant step in our journey to becoming the most innovative marketplace for material handling equipment in North America,” said Chris Schmid, CEO of Forklift-International.com. “Our goal is to create the most efficient platform, where both dealers and buyers can easily find the right equipment to meet their needs.” With this rapid expansion, the marketplace allows U.S. dealers to showcase their inventory to a wide audience, providing buyers with a convenient and efficient way to find the right equipment. As part of its ongoing commitment to supporting dealers, Forklift-International.com continues introducing new tools and services to enhance the buying and selling experience further. “We are proud to offer over 10,000 pieces of equipment across the United States,” said Johannes Mueller, head of U.S. Business Development. “This milestone reflects the trust our dealers place in us, not only in terms of delivering leads but also in the numerous tools we provide to help them improve their daily operations.” Forklift-International.com’s growth is driven by a range of tools designed specifically for material handling dealers. These include inventory synchronization, lead generation, and easy quote management, all designed to streamline daily operations. Dealers can also take advantage of the app for iPhone and Android, which makes managing stock and creating quotes on the go effortless. The latest addition is a feature allowing dealers to showcase their inventory directly on their websites, complete with built-in SEO optimization to attract more local leads. By integrating these capabilities into one cohesive platform, dealers can maximize efficiency and manage their listings in less time, ultimately helping them drive more sales. To learn more about how your dealership can list your material handling equipment or if you want a no-obligation demonstration of the Forklift platform, email sales@MHWmag.com or call 563 557-4495.
American Logistics Aid Network (ALAN) begins Post-Hurricane Milton response
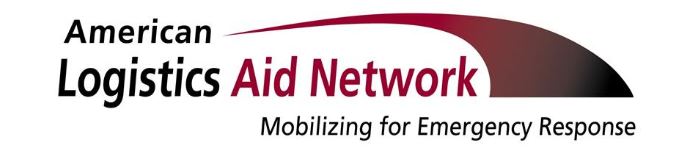
“Right now, The ability for Logistics Professionals to get relief items stored, transported, organized, and delivered to disaster sites can be a game-changer.” As Floridians struggle with the aftermath of Hurricane Milton, the American Logistics Aid Network (ALAN) has begun supporting relief efforts and reminding members of the supply chain community that sharing their logistics know-how, space, equipment, and services is one of the most vital ways they can help. “The devastation Hurricane Milton and its many tornadoes have caused is heartbreaking. We mourn for those who have lost family members, pets, and homes, and we are already working hand-in-hand with various non-profit partners to deliver help,” said Kathy Fulton, ALAN’s Executive Director. ALAN received its first request for Hurricane Milton-related logistics assistance earlier this week. In the coming weeks, Fulton anticipates it could receive dozens more, just as it has since Hurricane Helene struck various parts of the Southeast two weeks ago. “During the first 48 to 72 hours after a hurricane, most of the work on the ground is focused on search and rescue efforts,” Fulton said. “Because of this, ALAN usually doesn’t receive the first substantial wave of donated logistics requests until after that, when humanitarian organizations can get in, conduct their initial assessments, and determine what’s most needed.” “We know that can be frustrating for organizations that want to do something tangible as soon as possible. But we hope they will still be willing to provide their logistics help when the need arises, whether it’s in a few days, a few months – or even beyond that.” ALAN encourages organizations that are interested in joining its Hurricane Milton relief efforts to visit its Disaster Micro-Site at https://www.alanaid.org/operations/ frequently in the weeks and months ahead. That’s where ALAN will post any unfilled requests it has – and where it currently features several open needs for Hurricane Helene and other ongoing disaster relief efforts. Those who wish to help ALAN by making a financial contribution instead can do so by going to https://www.alanaid.org/donate/ “Logistics professionals may not be first responders, but ensuring that relief supplies reach those in need is indeed a life-saving activity,” Fulton said. “We’re thankful to be part of a community that can play such a meaningful role under the most challenging of circumstances.”
Yale wins 2024 Green GOOD DESIGN Award for fully integrated lithium-ion lift trucks
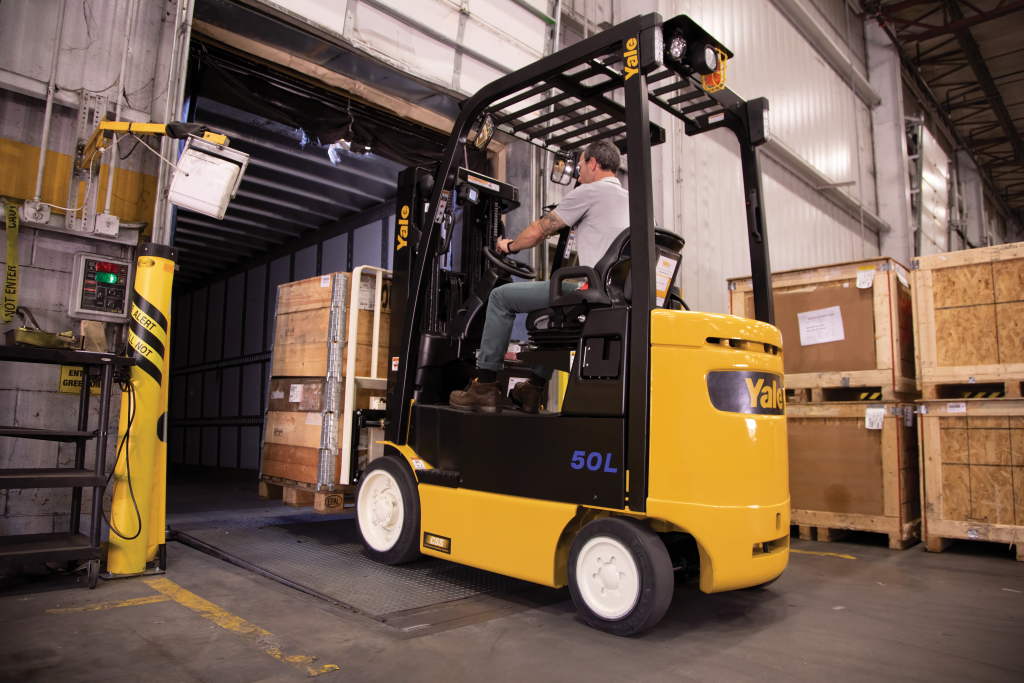
Yale Lift Truck Technologies announces that the ERC050-060VGL series of lithium-ion-powered lift trucks has received a 2024 Green GOOD DESIGN® award. The line of 5,000- to 6,000-pound load capacity cushion tire lift trucks is designed to bring warehouse operations the benefits of factory-integrated lithium-ion power, including improved productivity, ergonomics, and zero emissions. While operations have traditionally utilized a battery box replacement to convert counterbalanced lift trucks from lead-acid to lithium-ion battery power, the ERC-VGL series is completely designed around a fully integrated, space-saving lithium-ion battery pack. This design helps free space in the operator compartment, combining ergonomic benefits with the advantages of lithium-ion technology—including zero emissions during operation and no off-gassing during the charging process—to maximize comfort, convenience, and performance. “The ERC050-060VGL is an example of our commitment to customer-driven design, helping warehouses not only meet sustainability targets but address critical labor and productivity challenges,” says Brad Long, Brand Manager, Yale Lift Truck Technologies. “Designing this truck around integrated lithium-ion power presented an opportunity to make significant changes to the operator compartment that make adopting this zero-emission technology even more appealing.” The slim form factor of the lithium-ion battery pack enables a lower floor plate, enabling more accessible entry and exit from the truck, with open space below the seat that gives operators more freedom to position their feet. It also allows additional headroom, accommodating a taller seat with air suspension for a more comfortable ride. Lithium-ion batteries charge faster and more simply than lead-acid alternatives – no maintenance, off-gassing, or watering is required. The ERC-VGL can fully charge in just over an hour and weigh less than the equivalent lead-acid-powered model, reducing energy consumption for extended run times in demanding applications. The Yale lineup of integrated lithium-ion lift trucks includes the award-winning ERP040VTL and ERP040VFL. The brand has won numerous awards for sustainability-friendly products, including 13 consecutive placements on a leading industry publication’s list of the top 75 green supply chain partners.
ZAPI GROUP to exhibit unparalleled range of Charging Solutions at The Battery Show North America 2024
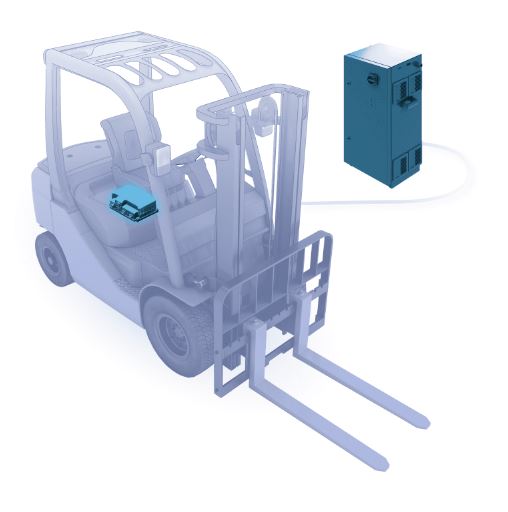
ZAPI GROUP, a global provider of electrification headquartered in Italy, aims to grow North American awareness of its brand’s solutions at the upcoming Battery Show North America in Detroit (October 7-10). Technical personnel from ZIVAN Srl (ZIVAN), Delta-Q Technologies (Delta-Q), and ZAPI GROUP will feature and support the full range of ZAPI GROUP’s on-board (OBC) and off-board charging solutions, from 350 W to 36 kW, from ZIVAN Srl (ZIVAN), Delta-Q Technologies (Delta-Q), and ZAPI GROUP. “We are committed to delivering electrification enablement to our customers,” said Rod Dayrit, Global Director, Business Development for ZAPI GROUP’s charging solutions. “Our comprehensive charger lineup is designed for seamless integration with other electrification system components and battery technologies offered through our extensive partner network. With our global presence, we streamline sourcing, manufacturing, logistics, compliance, and OEM support across various industries, ensuring that our customers receive the best possible service no matter where they are.” The new 9 kilowatt ZIVAN-branded SG9 industrial charger will be displayed at the ZAPI GROUP booth 5622. This highly flexible off-board fast charger can be configured for various AC input sources for global deployment (single and three-phase voltages) and offers multiple charge voltages (36 to 96 volts DC) to support a wide array of battery packs. “We are thrilled to showcase our latest product, a portable, powerful, and ruggedized off-board charging solution, distinct in the market at The Battery Show North America,” said Simone Paterlini, Chief Operating Officer of ZIVAN. “The SG9 charger is IP-rated to withstand the harshest environments, providing portable high-power opportunity charging at construction and other outdoor industrial sites.” ZAPI GROUP invites The Battery Show attendees to booth 5622 to see the SG9 and explore its broader portfolio of battery charging solutions, including the recently released 3.3 kW onboard chargers offered under the Delta-Q and ZIVAN brands. The team will also showcase other electric drivetrain solutions, including motors and controllers. This event is an excellent opportunity for engineers, designers, and product managers to engage with our technical experts, discuss challenges, request samples, and explore ideas for their electrification.
Bobcat Company wins prestigious Red Dot Design Award for RogueX2 Concept
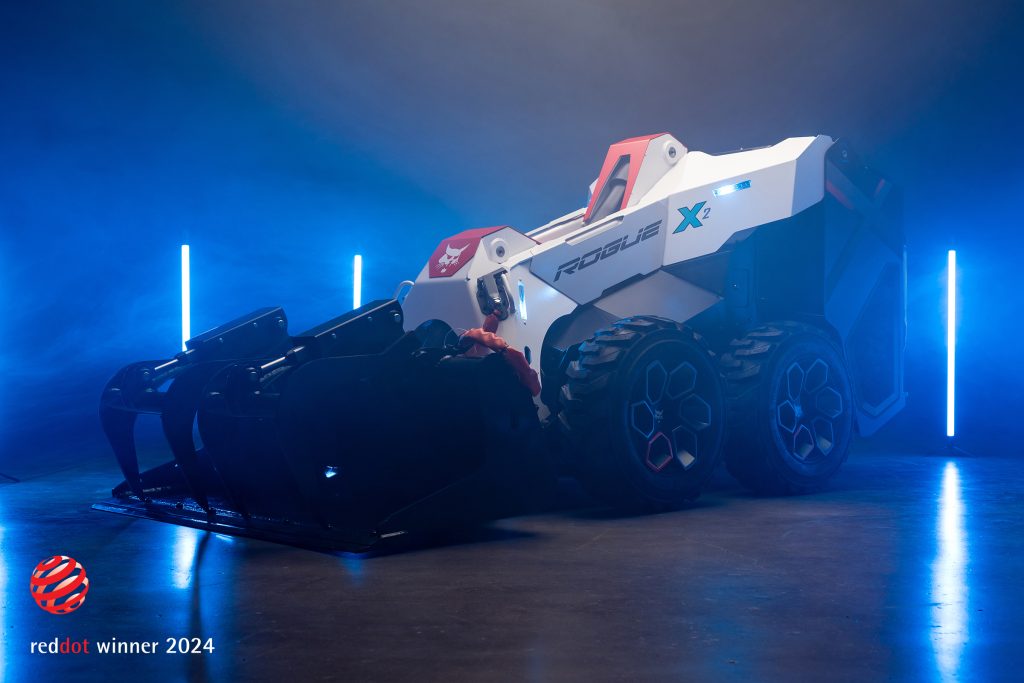
Bobcat Company has been selected as a Red Dot Award: Design Concept winner for RogueX2, an all-electric, fully autonomous concept loader. The Red Dot Design Award is one of the most respected design awards in the world. Its Design Concept category identifies and celebrates new design concepts and innovations as the precursors of tomorrow’s great products. “We are honored to win the world-renowned Red Dot Award for Design Concept in recognition of the groundbreaking design of the RogueX2,” said Joel Honeyman, vice president of global innovation at Doosan Bobcat. “This award is a testament to the dedication of the Bobcat teams, who are passionate about pushing design limits and advancing innovation to redefine the machines of tomorrow.” Key to the machine’s development was the Bobcat Global Design Studio, which supported the project in collaboration with the Bobcat Global Innovation team. On display at CES 2024, the RogueX2 is a powerful, smart machine that produces zero emissions. It features a lithium-ion battery, electric drive-actuated lift, and tilt kinematics, and no hydraulics. Specifically designed and built without a cab, RogueX2 explores the idea of how work machines of the future can be designed and optimized for new technologies and enable an entirely new work experience. Designed with wheels to optimize the electric battery run time, the RogueX2 features axial flux motors, which give the machine incredible tractive effort. The RogueX2 was built as a proving ground to advance Bobcat’s innovation leadership and has garnered many new patents pending. “To build a smarter, more sustainable, and connected future, we must ask the questions no one else has thought to ask before and invent new solutions that previously did not exist,” continued Honeyman. The award-winning RogueX2 is not commercially available in the research and development stage. The Red Dot Design Award is an annual international competition recognizing design and business excellence. With around 20,000 entries per year, it is one of the biggest design competitions in the world. The Design Concept category features projects in varying stages of development, from concepts to prototypes to almost fully developed products ready for market. For more information on the 2024 Red Dot Awards, visit www.red-dot.org.
HexcelPack to showcase expanded line of Eco-Friendly Packaging Solutions at PackExpo
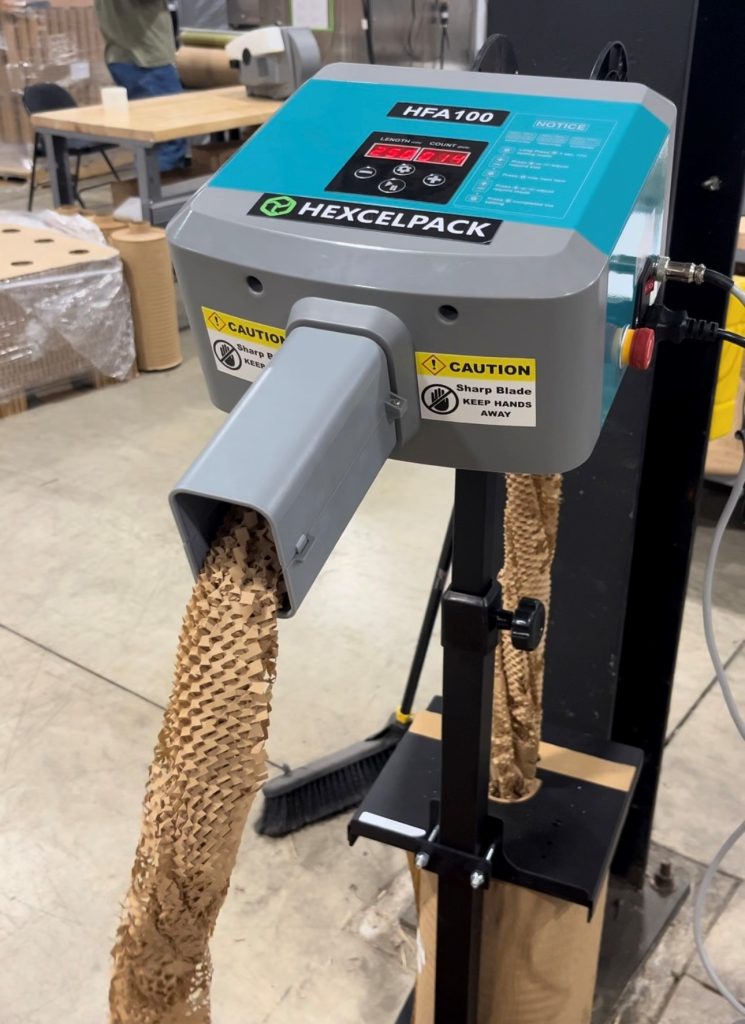
HexcelPack, an innovator in paper-based protective packaging designed to replace bubble , air pillows, and other plastic or foam materials, is set to unveil a range of new sustainable packaging products at PackExpo International 2024. The company will debut its expanded lineup of cost-effective, eco-friendly solutions at Booth W-24105 from November 3-6 in Chicago. Among the featured products at this year’s show will be the AutoHexaFil™, a cutting-edge automatic dispensing system, a Wide Wrap™ version of HexcelPack’s signature HexcelWrap™ cushioning paper, Hexcel’ope, the company’s eco-friendly mailer, and new protective Hexcel Pads™. Key products highlighted at this year’s show include: AutoHexaFil™: HexcelPack’s fully automatic dispensing system for HexaFil™ void fill material. The AutoHexaFil™ machine uses a unique cutting technology, delivering sustainable void-fill material up to three times faster than traditional methods. The system is fully electric, operable via a foot pedal, and features a programmable screen for preset length dispensing. AutoHexaFil™ is adjustable to fit over packaging conveyors and includes wheels for mobility, providing a highly efficient and safe solution for high-volume packaging environments. Wide Wrap™: A new, wider version of HexcelPack’s HexcelWrap™, available in widths from 20” to 40” (unstretched). Ideal for larger and heavier items, Wide Wrap™ offers greater flexibility in protecting oversized products during shipping. It can be used with a tabletop brush dispenser or an orbital wrapper, making it a versatile solution for businesses looking to minimize waste while maximizing protection. Hexcel’Ope™: HexcelPack’s sustainable alternative to traditional bubble mailers. The Hexcel’Ope™ is made using the same patented slit-paper technology as HexcelWrap™, providing a curbside-recyclable solution for shipping that eliminates the environmental impact of plastic-based mailers. Hexcel Pads™: Offering superior protection for fragile items, Hexcel Pads™ are available in sizes up to 48” long and 16” wide, with three thickness options, including a double-layer version for enhanced crush protection. These pads provide reliable cushioning without the need for interior openings, making them ideal for a wide range of products. “We are very excited to have the opportunity to highlight and demo these eco-friendly innovations at PackExpo, showcasing our commitment to sustainable, cost-effective packaging solutions,” said Lorne Herszkowicz, Partner at HexcelPack. “In addition to our new products, we continue to invest in our operations with the expansion of our manufacturing footprint in 2025.”
Container market on the edge: Election uncertainty and global volatility to persist well into 2025
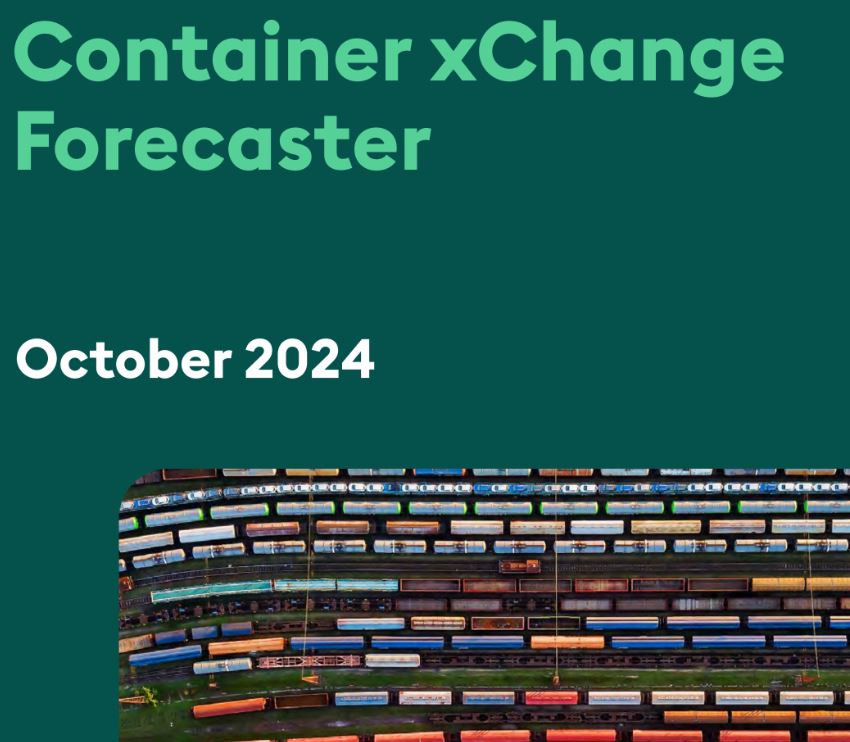
As we enter October 2024, the U.S. container trading market is experiencing heightened volatility due to several influencing factors. The recent strikes at East Coast ports, which began on October 1 and have since concluded, have left a lasting impact on supply chains while the focus shifts to the U.S. elections scheduled for November 5. ” The recent strikes may have ended, but the storm is far from over. With unresolved issues surrounding automation, we are on the brink of another disruption come January 2025.,” shared Christian Roeloffs, cofounder and CEO of Container xChange. Looking ahead, Roeloffs highlighted potential future challenges: “Given the unresolved issues around automation, I believe there are strong chances of another disruption in January. The unions strongly oppose any form of automation, and this unresolved matter raises the likelihood of another strike in January.” Roeloffs urged U.S. container traders to prepare: “As we approach the peak season and the Chinese New Year, expect another wave of frontloading as importers seek to secure cargo ahead of potential disruptions. Container traders should begin contingency planning now- —this includes securing inventory, diversifying supplier networks, and considering alternative shipping routes to mitigate delays. Proactive steps like these will be crucial for navigating the challenges anticipated in January.” Conversely, China is facing significant domestic challenges, with weak consumer spending and slowing income growth. While exports have shown resilience, broader economic concerns could impact supply chains, including a slowdown in domestic consumption and property investment. Reduced demand for goods within China, coupled with U.S. retailers and wholesalers holding considerable inventory, is creating a more challenging environment for container trading and leasing companies, as lower shipping volumes and excess container capacity put pressure on both demand and leasing rates. The Middle East is contributing to increased volatility in global container shipping, particularly in October 2024. Tensions have escalated between Israel and Iran, with Iran launching missiles at Israel and Hezbollah carrying out rocket attacks from Lebanon. These developments continue to disrupt operations in the Red Sea, where Houthi rebels are actively targeting vessels, intensifying shipping capacity strains with no immediate resolution in view. xCPSI Rises: Increased Expectations for Container Price hikes The Container Price Sentiment Index (xCPSI) for September and October indicates a notable rise in the number of supply chain professionals globally anticipating an increase in container prices. This expectation is driven by limited supply and steady demand. Country-level findings No impact of U.S. East Coast strikes on average container prices In September, average container prices in the U.S. remained relatively stable. However, on a global scale, Asia and Europe experienced the most significant price hikes, while the Middle East and the Indian Subcontinent (ISC) saw a 6% decline. An interesting development is that the Middle East experienced a 7% price surge in early October, indicating market volatility in that region. In China, average prices have consistently decreased, reflecting diminished factory output and reduced U.S. and European exports. Additionally, supply is still coming offline from container factories, contributing to the overall price decline. Region-wise average price development in September 2024 Currently, average container prices are highest in China, followed by the U.S. and then Europe. Prices have consistently fallen in both China and the U.S. while remaining relatively stable in Europe at a considerably lower level. What lies ahead for container traders in the U.S.? Key Factors influencing Q4 (Oct-Dec) 2024 container prices Impact of strikes and elections in November: Although the strikes have concluded, the possibility of renewed labor disputes in January 2025 is a concern. Additionally, the upcoming U.S. elections introduce uncertainty, as trade policies could shift significantly depending on the outcome. Demand-Supply Dynamics: In the short term, demand for U.S. containers appears stable. However, in the mid-to-long term, retailers and wholesalers are managing considerable inventory levels, which diminishes the need for significant imports unless demand significantly bounces. The extent of inventory refilling required for the next cycle—aligned with the Chinese New Year—will primarily depend on the performance of peak season demand in the U.S. Cyclic Nature of Demand in Q4: Traditionally, Q4 sees increased container demand due to the holiday season. While some stabilization in demand is anticipated as retailers work through their inventories, the full effects of peak season demand will likely become evident only in early 2025. Much will depend on how ongoing inventory adjustments unfold. Roeloffs stated, “U.S. retailers are managing significant inventory levels, but the real challenge lies ahead. As we enter the holiday season, the dynamics between demand and supply will shift dramatically, revealing whether these inventories can maintain a healthy market or indicate deeper issues.” Customer Insights Conversations with U.S. container traders reveal cautious optimism regarding improving market conditions should Trump win the elections, potentially leading to policy changes that favor trade growth. Conversely, many container traders express concerns about ongoing global trade uncertainties and the residual effects of labor disputes, particularly as negotiations with the International Longshoremen’s Association (ILA) may resume in January 2025. Will Frontloading Persist into Q4’24? As we near the end of 2024, the U.S. container trading market is characterized by a blend of uncertainties, from post-labor strike adjustments to peak season, hurricane threats, and upcoming elections. While supply remains tight, demand may experience significant fluctuations based on inventory levels, trade policies, and broader economic indicators. Traders and industry stakeholders should remain alert, especially with January 2025 negotiations on the horizon, reintroducing discussions about automation and future labor relations. “With the Chinese New Year as the next key shipping season and fears of another strike looming, we’re entering a critical phase for importers. The rush to secure cargo now could shape the market well into 2025. How we navigate this will define our resilience as an industry.” Concluded Roeloffs. 2025 Outlook Looking ahead to 2025, the U.S. container market will likely be shaped by the resolution of labor disputes and the broader geopolitical landscape. The outcome of the U.S. election will significantly influence trade and domestic fiscal policy, subsequently affecting container prices. The topic of automation will remain prominent,
SupplyOne expands Southeastern Region with acquisition of Gulf Packaging, Inc.
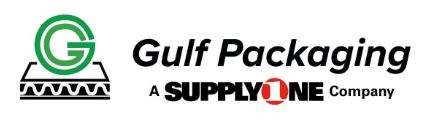
SupplyOne, Inc., a distributor of custom corrugated and value-added packaging solutions in North America, is strengthening its presence in the Southeast with the acquisition of Gulf Packaging, Inc. (“Gulf”). Gulf is a premier converter and supplier of custom corrugated boxes and displays serving Alabama, Florida, Georgia, Tennessee, Mississippi, and Louisiana. Founded in 1990, Gulf Packaging operates out of production facilities in Bay Minette and Tallassee, Alabama. The company produces a wide range of custom corrugated products with fast turnaround times and exceptional customer service. Gulf’s comprehensive offerings and commitment to quality have established it as a trusted partner for businesses across diverse industries in the Southeastern United States. “Welcoming Gulf Packaging into the SupplyOne family enhances our ability to deliver customized, high-quality packaging solutions to our customers in the Southeast and fills what was a large geographic opening for SupplyOne,” says Todd Renehan, president and CEO of SupplyOne. “Gulf’s reputation for excellence and customer-centric approach aligns perfectly with our mission to provide unparalleled service and innovative packaging solutions nationwide.” “As a privately owned company for over three decades, finding a partner that values our legacy of superior service and dedication to our employees was paramount,” says Larry Taylor, CEO of Gulf Packaging, Inc. “SupplyOne shares our commitment to customer satisfaction and offers the resources and support to expand our capabilities and reach across the country. We are excited about the opportunities this partnership brings to our customers and team members.” “Joining SupplyOne marks an exciting new chapter for Gulf Packaging,” says Paul Morris, President and General Manager of Gulf. “Their extensive network, industry expertise, and packaging supplies offering will allow us to enhance our services while maintaining the personalized attention our customers have come to expect. We look forward to continued growth and success as part of SupplyOne.” This acquisition represents the 42nd addition to the SupplyOne portfolio since its founding 25 years ago, reinforcing the company’s strategic growth and commitment to serving customers with comprehensive packaging solutions across North America.
AAR reports Rail Traffic for the week ending October 05, 2024
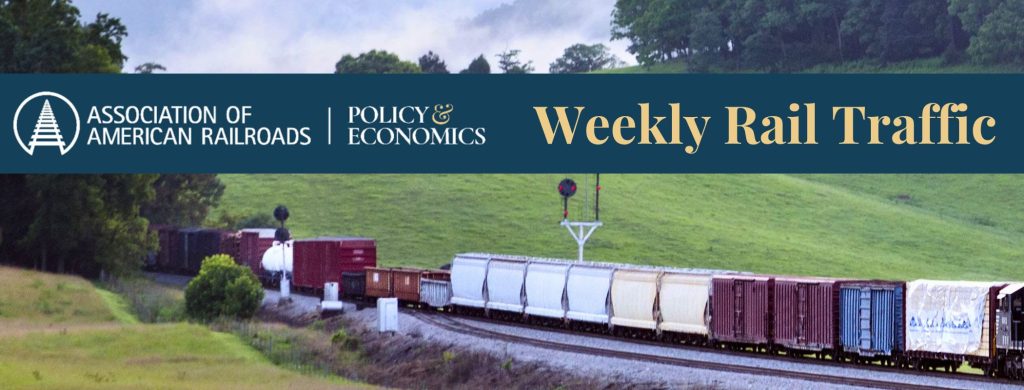
Today, the Association of American Railroads (AAR) reported U.S. rail traffic for the week ending October 5, 2024. This week’s total U.S. weekly rail traffic was 486,187 carloads and intermodal units, down 2.5 percent compared with the same week last year. Total carloads for the week ending October 5 were 225,280, down 3.5 percent from the same week in 2023, while the U.S. weekly intermodal volume was 260,907 containers and trailers, down 1.7 percent from 2023. Four of the ten carload commodity groups posted an increase compared with the same week in 2023. They included farm products excl. grain, and food, up 1,553 carloads, to 18,019; chemicals, up 1,140 carloads, to 31,059; and metallic ores and metals, up 828 carloads, to 20,908. Commodity groups that posted decreases compared with the same week in 2023 included coal, down 5,458 carloads, to 61,304; nonmetallic minerals, down 3,937 carloads, to 29,645; and grain, down 1,300 carloads, to 21,933. For the first 40 weeks of 2024, U.S. railroads reported a cumulative volume of 8,697,320 carloads, down 3.3 percent from the same point last year, and 10,472,512 intermodal units, up 9.1 percent from last year. Total combined U.S. traffic for the first 40 weeks of 2024 was 19,169,832 carloads and intermodal units, an increase of 3.1 percent compared to last year. North American rail volume for the week ending October 5, 2024, on nine reporting U.S., Canadian, and Mexican railroads totaled 331,587 carloads, down 4.5 percent compared with the same week last year, and 341,107 intermodal units, down 3.0 percent compared with the previous year. Total weekly rail traffic in North America was 672,694 carloads and intermodal units, down 3.7 percent. North American rail volume for the first 40 weeks of 2024 was 26,678,777 carloads and intermodal units, up 2.4 percent compared with 2023. Canadian railroads reported 94,571 carloads for the week, down 2.0 percent, and 68,805 intermodal units, down 4.7 percent compared with the same week in 2023. For the first 40 weeks of 2024, Canadian railroads reported a cumulative rail traffic volume of 6,346,418 carloads, containers, and trailers, down 0.0 percent. Mexican railroads reported 11,736 carloads for the week, down 31.7 percent compared to last year, and 11,395 intermodal units, down 19.3 percent. Cumulative volume on Mexican railroads for the first 40 weeks of 2024 was 1,162,527 carloads and intermodal containers and trailers, up 3.6 percent from last year. To view the weekly rail charts, click here.
Episode 527: Digital Transformation with Labeling
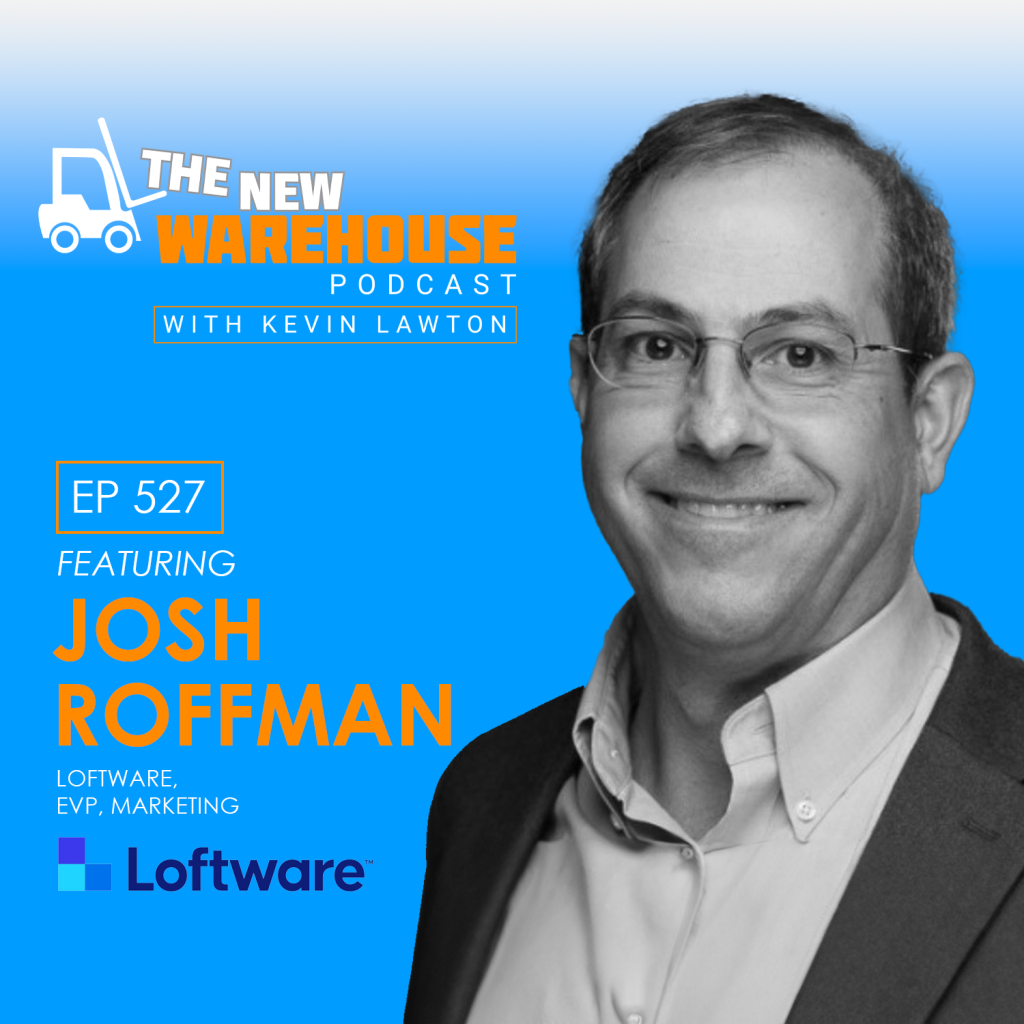
In this episode of The New Warehouse Podcast, Josh Roffman, EVP of Marketing at Loftware, explores the pivotal role labeling plays in today’s supply chain. Loftware, a pioneer in the labeling industry with nearly 40 years of experience, assists over 12,000 companies globally in navigating the complexities of product labeling. The conversation delves into how labeling has evolved, the intersection of digital transformation with labeling processes, and the integration of AI and cloud technologies. Roffman highlights the importance of labels in ensuring compliance, traceability, and efficiency within an increasingly complex and globalized supply chain. The Evolution of Labeling and Supply Chain Complexity Labeling has long been a crucial aspect of supply chains, but as technology advances, so too has the function of labels. Roffman states, “The ability to have that label be a connection point between the physical and digital is where things are evolving.” The growth of regulations and the need for traceability have pushed labels beyond basic product identification. Now, labels carry vital information that supports both businesses and consumers in understanding a product’s journey. From tracking pharmaceuticals in the life sciences to providing detailed information in retail, labeling continues to evolve alongside the growing demand for transparency and compliance. Digital Transformation with Labeling: A Path to Efficiency The digitization of labeling processes is central to modernizing supply chains. Roffman explains, “Manual processes have given way to automation, integrating systems of truth like SAP to trigger labeling downstream.” This shift toward digital transformation has automated the creation and management of labels, helping companies address the complexities of geography, regulations, and evolving industry standards. By leveraging cloud-based technologies, companies can centralize their labeling processes, enabling supplier networks to adhere to specific standards, ultimately reducing errors and improving efficiency. AI and Cloud: A Powerful Combination for the Future AI and cloud technologies are transforming supply chain operations. Roffman shared that 76% of supply chain professionals believe AI will transform their operations within three years, but only 17% have begun implementing it. He acknowledges that large organizations face challenges in adopting new technologies but emphasizes the potential: “We’re right at the cusp of what AI can do… It will streamline next-generation labeling solutions.” With AI automating complex labeling changes and ensuring compliance and cloud offering centralized control, companies can unlock new levels of efficiency and accuracy in their supply chains. Key Takeaways Labels have evolved from basic product identifiers to carriers of critical supply chain data. Digital transformation in labeling automates previously manual processes, improving efficiency. AI and cloud technologies offer new opportunities to streamline labeling processes and ensure compliance. The New Warehouse Podcast Episode 527: Digital Transformation with Labeling
Universal Lithium Battery Supply (ULBS) celebrates grand opening
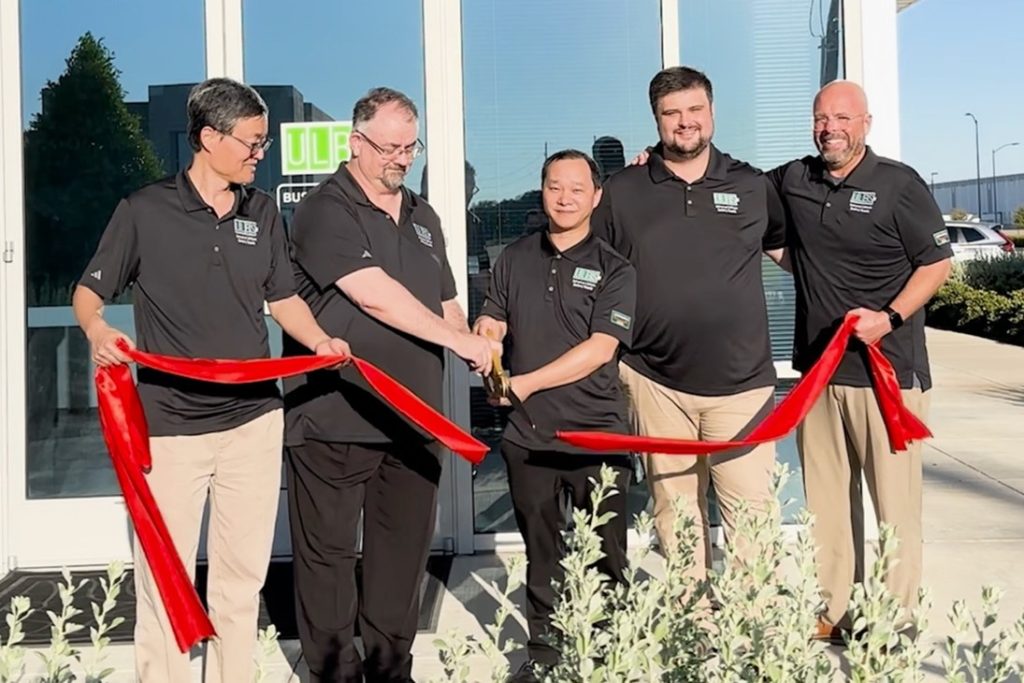
Universal Lithium Battery Supply (ULBS) opened its headquarters with a grand opening on September 26, 2024. Located in Brookshire, TX, ULBS aims to transform the material handling industry with its cutting-edge Lithium Iron Phosphate (LiFePO4) battery packs. These packs allow users to upgrade their new or existing lead-acid-powered material handling equipment while enhancing its performance, efficiency, and sustainability. At the heart of ULBS’s offerings are innovative maintenance-free lithium-ion battery packs designed as direct replacements for any OEM’s electric material handling equipment. These 24V, 36V, 48V, 72V, and 80V lithium-ion batteries not only provide rapid/opportunity charging capabilities but also boast extended lifespans, superior run times, and a substantial return on investment. “Our mission at ULBS is to empower companies with the tools they need to optimize their operations while minimizing downtime,” said Chadd Smith, Senior Business Development Manager of ULBS. “With our state-of-the-art Lithium Iron Phosphate batteries, we are setting a new standard for performance in the material handling market. Our products are designed not just to meet the demands of today but to prepare our customers for the future.” In addition to high-quality lithium-ion batteries, ULBS offers a comprehensive range of chargers and aftermarket support services. This commitment to customer satisfaction ensures clients can confidently run their equipment while maximizing productivity and reducing operational costs. The grand opening and ribbon-cutting event took place on September 26th, 2024. ULBS hosted dealers and select attendees at our new facility in Brookshire, Texas. This event featured the ribbon cutting, guided tours of the facility, live demonstrations of ULBS’s battery technology, and opportunities for attendees to engage with the ULBS team. The day also included networking sessions and discussions about the future of ULBS and its role within the logistics and manufacturing sectors. Want to see a video recap of the grand opening? Click the link below. https://ulbspower.com/resources/vf/id/15.html
ASSP revises key standard to elevate motor vehicle safety
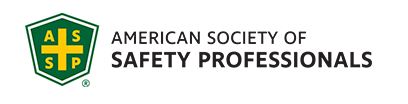
The American Society of Safety Professionals (ASSP) has revised a national voluntary consensus standard that defines core elements of a fleet safety program to help organizations protect workers on the road. There are 3.5 million fleets in North America, and 32 million commercial vehicles are used. ANSI/ASSP Z15.1-2024 Safe Practices for Motor Vehicle Operations outlines industry best practices for the safe management and use of motor vehicles owned or operated by an organization. The standard provides guidance to fleet managers and safety professionals on creating written programs and policies, enhancing safety through speed management and driver training, addressing impaired and distracted driving, implementing routine vehicle inspections and maintenance, and conducting proper incident reporting. “This safety standard is significant because motor vehicle crashes are the leading cause of work-related fatalities,” said ASSP President Pam Walaski, CSP, FASSP. “These tragic incidents are avoidable. Employers need expert guidance on identifying and managing risks their workers face on the road.” The revised standard strengthens incident reporting and analysis requirements and includes modifications that address today’s vehicles, technologies, and operating environments. “The best way to manage workplace hazards and keep workers safe is to incorporate a structured, proactive approach that assesses risks, identifies system gaps, and implements best practices,” Walaski said. Organizations that make fleet safety a core value also help reduce the economic and reputational costs of crashes involving their workers. That may include medical care, vehicle repair, liability, lost productivity, environmental impacts, and damage to the company’s reputation. The Z15.1 subcommittee that revised the standard comprised 11 safety and health experts from insurance, academia, government, and other fields. The inclusive process took 2½ years. Voluntary consensus standards provide the latest expert guidance and fill gaps where federal standards don’t exist. Companies rely on them to drive improvement, injury prevention, and sustainability. Government regulations are slow to change and often outdated, so federal compliance is insufficient to protect workers. ASSP leads the development of voluntary consensus standards for the workplace. In its last fiscal year, ASSP created, reaffirmed, or revised 15 standards, technical reports, and guidance documents, engaging 1,400 safety experts representing 500 organizations. The Society also distributed more than 14,000 copies of standards. To obtain Z15.1-2024 or other workplace safety standards, visit the online ASSP Store.
NEW Rollbag® Brand returnable Poly Shipping Mailers ideal for E-Commerce
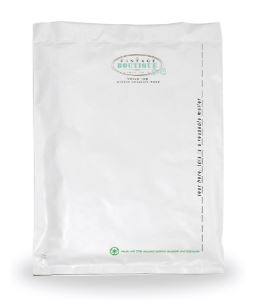
PAC Machinery has announced the new Rollbag® brand, Returnable Poly Mailer Bags, for mail order fulfillment. These bags are available for use on PAC Machinery Rollbag automatic baggers. PAC’s Rollbag Returnable Poly Shipping Mailers simplify the return process for customers while promoting eco-friendly practices. These mailers feature a self-seal adhesive closure liner on the inside of the bag, allowing customers to quickly return unwanted or incorrectly shipped items in the same convenient bag. Resealable poly mailers can be ordered from PAC Machinery Bags and Materials as pre-opened bags on a roll or fan-folded in a box. Customization options allow businesses to print their brand, message, or logo on the bags to enhance customer experience. Ideal for e-commerce retail shipping of non-fragile items such as apparel and soft goods, Resealable Poly Mailers features: 2-4 Mil thickness Exceptional puncture resistance and tear strength Made using at least 25% recycled resin Allows items to be returned in the same mailer Complies with shipping requirements of all major carriers Works on Rollbag brand automated bagging machines Eco-Friendly Features Rollbag Returnable Poly Shipping Mailers are recyclable and made with 25% recycled resin as standard. The adhesive strip benefits customers and supports companies in their sustainability efforts by enabling the reuse of packaging. By utilizing these bags for both initial orders and returns, companies help reduce plastic waste. Choose the PAC Machinery Rollbag brand of Returnable Poly Shipping Mailers for a seamless return process and a commitment to eco-friendly practices in your automated label, load, and seal process. Learn more about these bags and other PAC Machinery products at the PACK Expo International Show, which will take place at McCormick Place in Chicago from November 3 to 6, 2024, exhibit S-2130.
ProMat 2025 returns to Chicago March 17-20
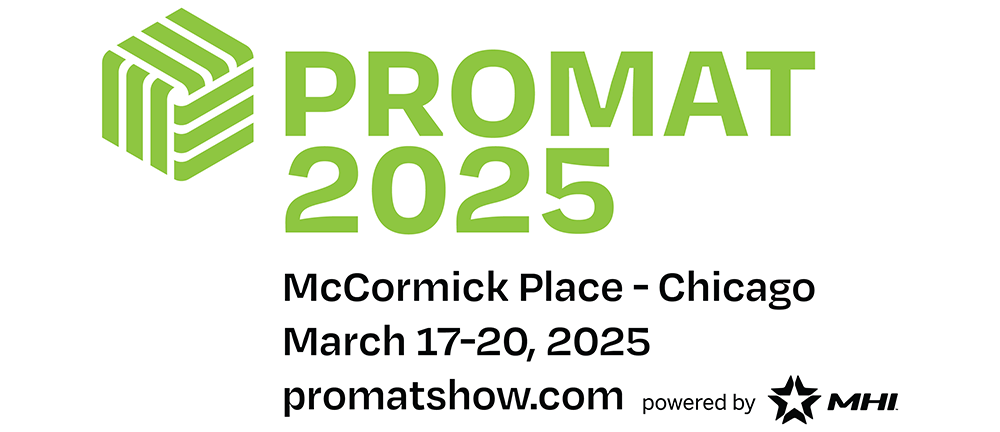
When the premier manufacturing and supply chain trade event of 2025, ProMat, returns to Chicago on March 17, it will include over 1,100 exhibits from leading solution providers and a comprehensive Educational Conference of nearly 200 sessions focusing on best-in-class solutions for manufacturing and supply chain operations. ProMat exhibits will represent all material handling, logistics, and transportation segments, from traditional, manual equipment to automated systems and smart, connected supply chain technologies. “ProMat offers manufacturing and supply chain professionals the unique opportunity to witness in person, in action the vast array of technology and innovations impacting this industry,” says John Paxton, CEO of MHI. “We are thrilled to offer the supply chain community this chance to come together and experience all that ProMat has to offer.” “From hands-on demonstrations to unparalleled education experiences, attending ProMat is your best opportunity in 2025 to gain the tools you need to innovate your supply chain operations for the next level of success,” adds Daniel McKinnon, Chief Exhibitions Officer, MHI. “If it’s your job to innovate your manufacturing and supply chain operations, you can’t afford to miss ProMat.” ProMat 2025 Conference In addition to the exhibits, the ProMat Conference will include four keynotes and nearly 200 educational seminars covering leading trends, best practices, and state-of-the-art equipment and technology solutions that can make manufacturing and the entire supply chain work more resiliently, efficiently, and profitably. March 17 Keynote: The Data Effect: The Price of Not Knowing Paul Zikopoulos, VP of Technology Unit Skills & Enablement at IBM March 18 Keynote: The AI Opportunity for Supply Chains Azeem Azhar, host of Bloomberg’s “Exponentially” March 19 Keynote: From Prime Time to Coach Prime A Conversation with Dion Sanders March 19 Keynote Panel: Preview of MHI 2025 Annual Industry Report John Paxton, CEO, MHI, and Wanda Johnson, Deloitte Consulting LLP March 19: MHI Industry Night with Jay Pharoah ProMat will feature the announcement of the 2025 MHI Innovation Award winners during an evening of food, drinks, and entertainment from comedian Jay Pharoah on Wednesday, March 19. Tickets to this event are $50. This event’s door prize will be a lifetime vacation trip. Trip Value: $30,000. See official rules. Women in the Supply Chain Industry Forum on March 17 at ProMat MHI has partnered with the Material Handling Equipment Distributors Association (MHEDA) and the Warehousing, Education, and Research Council (WERC) to bring an afternoon of discussion, education, and networking for women in our industry. The event includes a keynote by Taylor Elyse Morrison. MHI Young Professionals Network Reception on March 17 at ProMat This event provides attendees to network and connect with young professionals in the handling and supply chain industry. ProMat Student Day on March 19 MHI, in partnership with WERC, MHEDA, the College Industry Council on Material Handling Education (CICMHE), and the Material Handling Education Foundation (MHEFI), presents Student Day at ProMat 2025. This event features guided show floor tours to attract future talent to our industry. ProMat is the largest manufacturing and supply chain expo in North and South America. It will be held March 17-20, 2025, at Chicago’s McCormick Place.
American Logistics Aid Network (ALAN) activates for major Hurricane Milton
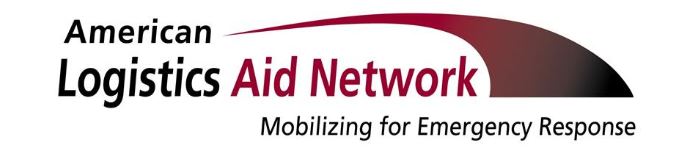
Less than two weeks after Hurricane Helene made landfall, the American Logistics Aid Network (ALAN) is mobilizing for another major hurricane – reminding supply chain professionals to take the 13th named storm of the season as seriously as they took the first. “In an ideal world, we’d have plenty of time to focus all of our efforts on Hurricane Helene’s clean-up and recovery, especially because the needs are so extensive,” said Kathy Fulton, ALAN’s executive director. “But in the real world, hurricanes don’t always wait for their turn. As a result, we are officially activating for Hurricane Milton. “All signs point to Hurricane Milton being an extremely destructive and dangerous event for the west coast of Florida, including many parts that are still struggling with rescue and recovery efforts from Hurricanes Helene and Debby. As a result, ALAN is consolidating its resources for preparedness and response efforts – and calling upon its network to help.” Late yesterday, ALAN expanded its Disaster Micro-Site (www.alanaid.org/operations/) with a Situation Report that includes specifics about Milton’s projected path and impacts and links to transportation waivers and state business/industry resources. It will continue to provide these reports as circumstances change in the days ahead. “The bad news is, we’ve had to use this site several times already because there have been so many hurricanes this year,” said Fulton. “The good news is it’s allowed us to do a better job of providing the industry with critical hurricane-related information – and helped us connect humanitarian organizations with the logistics help they need more quickly.” ALAN encourages those who want to help with Hurricane Milton relief efforts to visit the “Active Logistics Needs” portion of its Disaster Micro-Site often in the weeks ahead – bearing in mind that the vast majority of its requests tend to arrive after a storm has made landfall and initial assessments have been made – or to consider fulfilling some of the many Hurricane Helene logistics needs that are already showcased there. Organizations that would prefer to support ALAN’s relief efforts by making a financial donation instead can do so by going to https://www.alanaid.org/hurricane-helene/. Meanwhile, ALAN urges businesses with operations in Hurricane Milton’s cone of concern to focus on keeping themselves and their employees safe. This includes allowing plenty of time for their area employees to make preparations and either evacuate or shelter in place. “We hope this will be the last time this year that we have to send out a hurricane APB like this because each one represents terrible circumstances that we wouldn’t wish on anyone,” said Fulton. “However, we’re thankful for the overwhelming response we’ve received from members of the logistics community throughout this hurricane season so far. It is allowing us to make a considerable difference for disaster survivors.”
Seegrid’s Lift RS1 AMR looks to the future of Autonomous Material Handling
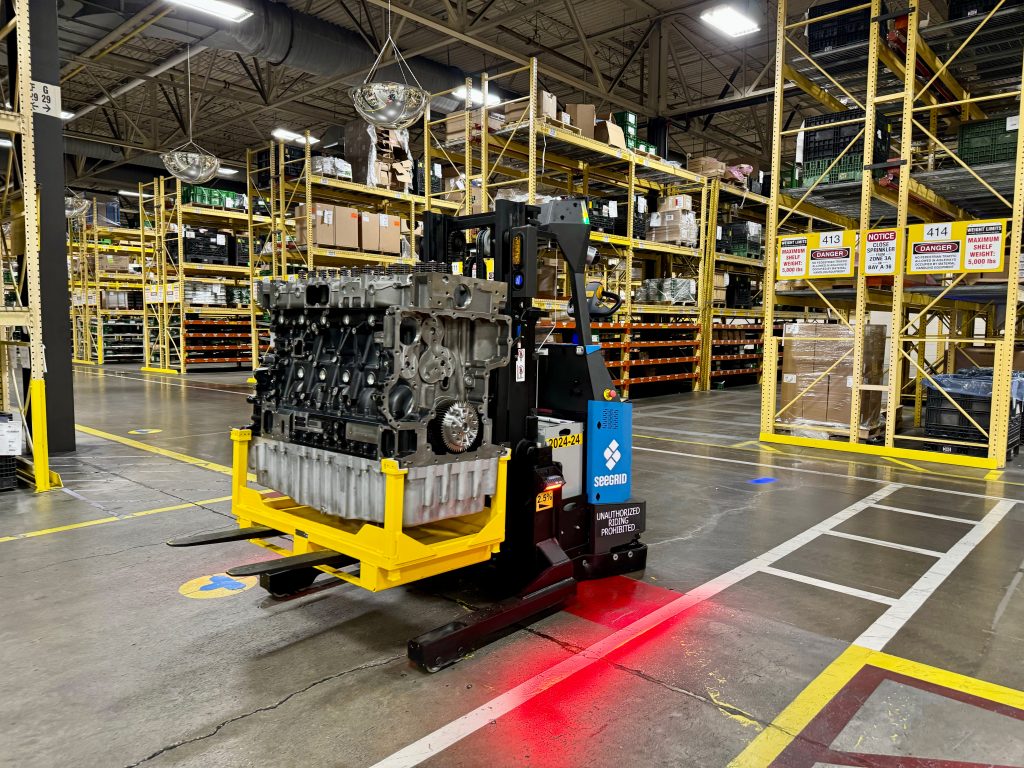
Seegrid manufactures autonomous mobile robot (AMR) solutions for palletized material handling, highlighting its Lift RS1 AMR. This autonomous lift truck is designed to transform material handling workflows, providing unmatched productivity, efficiency, and safety to manufacturing, warehousing, and logistics operations. Seegrid’s Lift RS1 AMR is capable of a 6-foot lift height, making it ideal for low-lift processes across the most prevalent industrial facility applications. A payload capacity of 3,500 pounds enables facilities to handle heavy loads more efficiently, boosting overall operational productivity. The RS1 demonstrates exceptional reliability, consistently performing tasks with precision and minimal downtime, ensuring seamless material handling operations. The RS1 has been built with the same proven technology stack, enabling Seegrid AMRs to log over 15 million autonomous production miles in customer facilities. With its vision-guided technology, Seegrid’s Lift RS1 can safely and reliably navigate even the most dynamic environments without requiring infrastructure such as magnets or reflectors. Moreover, the RS1 helps simultaneously address staffing shortages and respond to customer demands by providing facilities with a dependable autonomous solution. The RS1 features Seegrid’s pioneering Sliding Scale Autonomy, a unique-to-Seegrid innovation that blends the agility of autonomous mobile robots (AMRs) and the predictability of automated guided vehicles (AGVs). This allows the truck to navigate differently based on what is best suited for the specific customer application at hand. Whether performing long-haul routes or dynamically executing picks and drops, the RS1 excels by providing both the predictability and agility required by modern manufacturing, warehousing, and logistics environments. Equipped with LiDAR-based SLAM technology, the RS1 plans dynamic routes based on real-time perception feedback, ensuring reliable picks and drops without explicit training. Sliding Scale Autonomy offers a level of capability unmatched by competitors, empowering customers to optimize their material handling workflows in ways traditional AMRs and AGVs cannot. Safety is a top priority for Seegrid, and the Lift RS1 offers 360° safety coverage. The truck has primary and secondary safety sensing capabilities, which is a standout feature in the industry. While many systems rely solely on primary obstruction detection, which can only sense objects within 6 inches of the ground, Seegrid’s secondary obstruction detection technology precisely scans the drop area before payload release. This guarantees an extra layer of safety, ensuring accurate pallet drops and further reducing the risk of errors. Seegrid continues to deploy its proven and trusted AMRs in live customer environments—with hundreds of successful deployments and thousands of AMRs—transforming how customer facilities operate without a reportable or recordable safety incident. Beyond offering pioneering autonomous solutions, Seegrid prides itself on its ongoing service and support, proven implementations, and industry-leading ROI. Supporting more than 50 global brands, Seegrid continues revolutionizing how facilities operate. As seen in one customer manufacturing facility, more than a hundred Seegrid AMRs are responsible for nearly 80% of their non-conveyed material moves, cutting inventory levels by up to 30% and expected to deliver positive ROI in less than 18 months. With fast deployment times of weeks, not months, the RS1 can be fully integrated into facility operations without disrupting existing workflows, allowing its benefits to be experienced almost instantly. The Lift RSI AMR is designed to meet and exceed the ever-increasing demands of today’s modern manufacturing, warehousing, and logistics industries that rely heavily on palletized material handling. Seegrid’s pioneering autonomous lift trucks continue to bring real value to customers today. As industry innovators, they will continue developing new technology to enable their customers to automate their material handling workflows more than ever.