Episode 455: NetLogistik connects the dots for more efficient supply chain operations
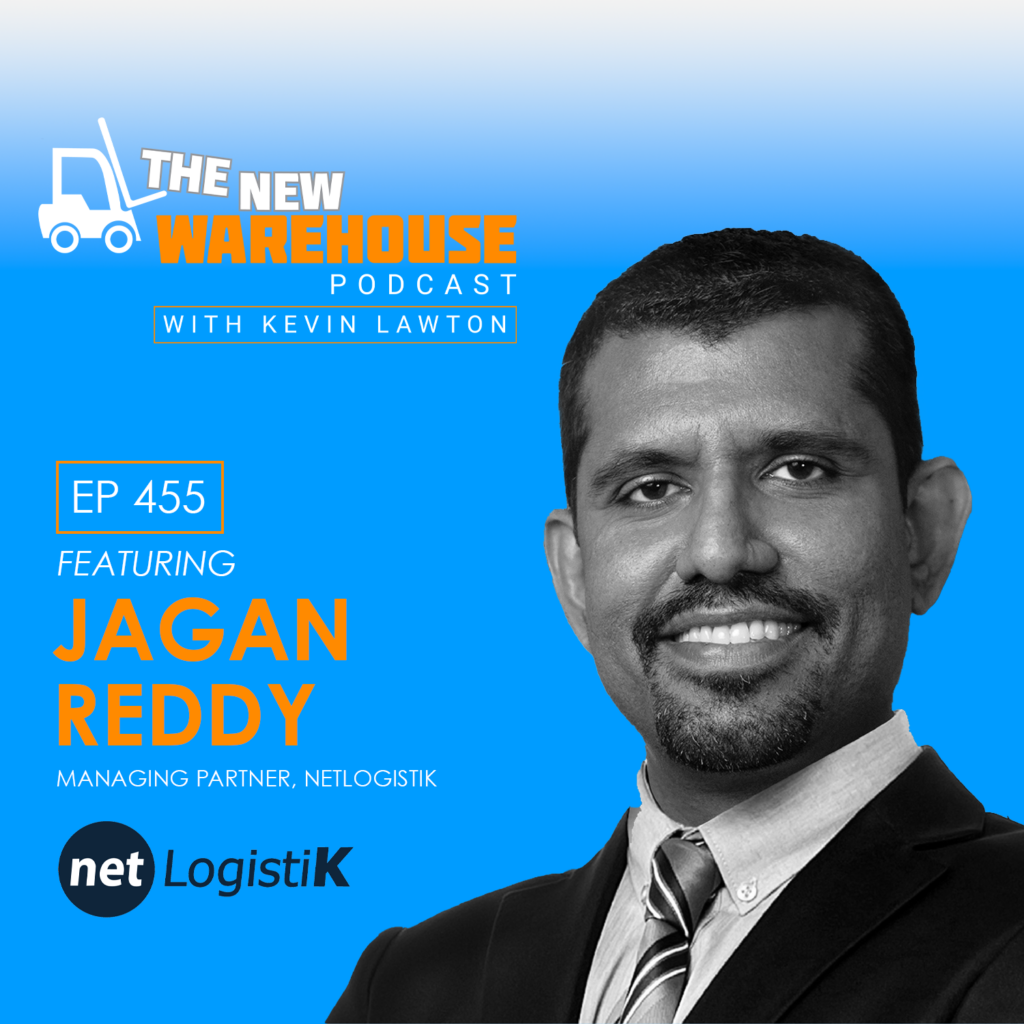
In this episode of The New Warehouse Podcast, Jagan Reddy, the Managing Partner at NetLogistik US, joins the episode to discuss how NetLogistik is tackling the industry’s current challenges. NetLogistik specializes in creating innovative solutions for Warehouse Management Systems (WMS). Tune in as Kevin and Jagan discuss NetLogistik’s recent Innovation Day and nearshoring, providing valuable insights into the evolving landscape of supply chain technologies and what the future holds in this dynamic field. Innovation Day: A Forum for Future Supply Chain Trends Reddy highlighted the company’s commitment to fostering a neutral and objective platform for discussing the future of supply chain management. Unlike typical events run by software companies, NetLogistik’s Innovation Day aims to provide a broad perspective on industry trends and necessary investments. The event focused on three key areas: Understanding near-term supply chain trends Innovating at the intersection of traditional software boundaries Exploring automation advancements Reddy elaborates on the changing landscape, noting the overlap of systems like WMS, TMS, and OMS and the increasing need for cohesive solutions. “There’s a lot of need for innovation so that the supply chain can function like a single organism,” he says, underlining the significance of companies like NetLogistik in connecting these dots for more efficient operations. A significant takeaway from the event was the shift towards mobile automation in warehouses, such as mobile robots for picking and other tasks, offering more flexible and scalable solutions than traditional fixed infrastructure. Reddy also touched on the growing trend of process automation through software bots, transforming routine tasks and streamlining transportation processes. He concludes, “We’re seeing a lot of interest in process automation and mobile goods-to-person systems.” Leveraging Data Insights for Smarter Warehouse Management The emerging trend now focuses on enhancing WMS features with additional layers of intelligence. Reddy emphasizes the importance of utilizing the data within a WMS to extract actionable insights. He states, “It’s about how you take the data within a WMS and draw insights from it, then layer it with intelligence so that WMS can sense and adapt to changes in operations.” This layer of intelligence in WMS enables the system to recommend changes in configurations or processes, adapting to day-to-day variations or long-term shifts within warehouse environments. The integration of such intelligence layers doesn’t necessarily require substantial investments. Reddy describes these as microservices, allowing for cost-effective and swift implementation. Reddy also discusses the evolving landscape of inventory management, noting the rise of micro fulfillment centers and smaller footprint operations. These newer operations have distinct requirements that differ from larger, national, or regional distribution centers. “There’s a proliferation of micro fulfillment centers… and they need a different footprint of a solution,” says Reddy. These smaller operations require tailored solutions that work hand in hand with the core WMS, sharing data and insights without competing with the primary system. This approach signifies a shift towards more versatile and responsive WMS solutions capable of catering to the diverse needs of modern warehouse operations. Navigating the Complexities of WMS Implementation Reddy explains, “A successful WMS deployment is less about quick implementation and more about getting it done right.” He outlines several vital strategies for successful implementation: Prioritize Effective Change Management: Emphasize guiding the organization through the transition rather than rushing the implementation process. Establish Clear Objectives: Clearly define the goals of the WMS deployment, whether for technology upgrade, labor efficiency, or inventory accuracy. Realistic Planning and Communication: Focus on thoroughly capturing requirements and ensuring clear communication with the implementation team. Prepare for the Unexpected: Plan for unforeseen challenges and approach them calmly and collaboratively. Support Employee Transition: Provide employees with the necessary support and space to adapt to the new system, recognizing its long-term role in business operations. Reddy’s approach highlights the importance of a strategic and thoughtful implementation process to ensure the successful integration of a WMS into an organization’s operations. Key Takeaways Trends show a shift towards a unified supply chain ecosystem, emphasizing solutions for the overlap between WMS, TMS, and OMS for seamless operations. WMS data intelligence is pivotal for operational adaptability, enabling systems to anticipate changes and optimize processes in real time. WMS implementation success hinges on meticulous planning, clear objectives, and robust change management, ensuring a seamless transition and operational efficiency. The New Warehouse Podcast EP 455: NetLogistik Connects the Dots for More Efficient Supply Chain Operations
Tranzonic names Joe Vitale Chief Corporate Development Officer
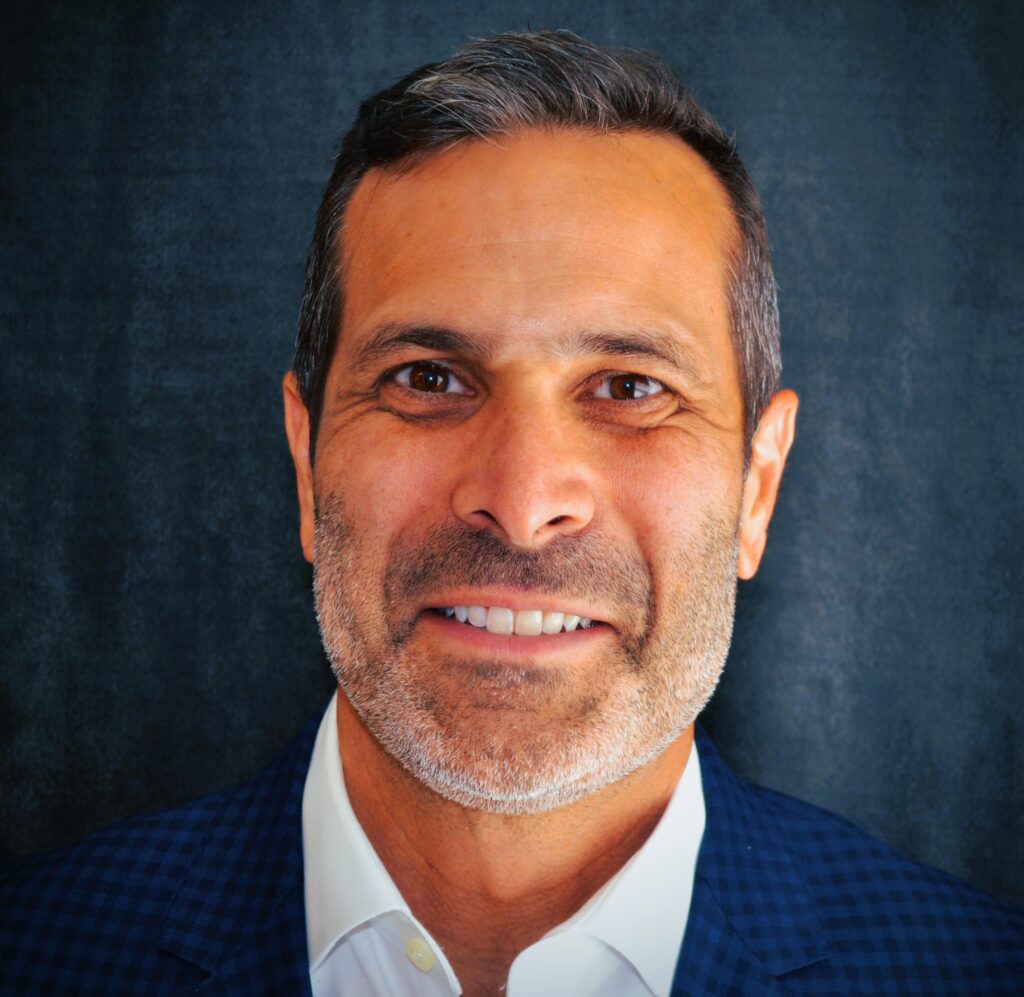
Newly created position to pilot strategic growth via M&A The Tranzonic Companies, a manufacturer of personal care and protection, contamination control, and cleaning products, has named Joe Vitale to the newly created role of chief corporate development officer. Vitale will provide strategic direction and leadership as the business expands through acquisitions, investments, and partnerships, and will collaborate with executive leadership on company strategy. M&A is central to the growth strategy of Tranzonic, which has increased sales five-fold in the past decade via acquisitions of diverse companies including Monarch Brands, Acute Care, Adenna, Chemcor, NILodor, Innocore, High-Tech Conversions, and others. Each investment has strengthened Tranzonic’s position as a leader in helping businesses protect, clean, and care for shared spaces where we work, stay, and gather — businesses across manufacturing, food service, healthcare, retail, transportation, hospitality, and other target industries. Vitale’s mission is to optimize Tranzonic’s origination, acquisition, and integration processes to more efficiently identify and partner with new companies to achieve greater growth. He is well-suited to lead the company’s growth efforts, with more than 25 years of professional experience in corporate banking, large and mid-cap industrial, and sponsor-backed portfolio companies. Vitale most recently led M&A and Treasury for Brook + Whittle, before which he spent over a decade with Ferro Corporation, where he helped transform the company through M&A to outperform peer group public companies. He has successfully completed acquisition, partnership, and carve-out transactions in the U.S. and across the world, and his collaborative approach allows for efficient transactions that minimize disruption to the business and preserve value for all stakeholders. “Joe’s values and the engaged culture he creates are well-aligned with Tranzonic and what we plan to achieve as we grow,” said Tom Friedl, CEO of The Tranzonic Companies. “We already have exciting new investments planned for 2024, and Joe’s energy and focus will further our goals as we look to the next decade and beyond.” Vitale earned his MBA in finance from UCLA Anderson and his bachelor’s degree from Vanderbilt University.
CLARK Material Handling Company announces leadership appointments
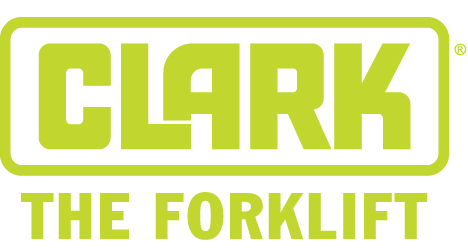
CLARK Material Handling Company has announced its plans for upcoming leadership appointments in the North American company. 2023 was a record sales and revenue year for CLARK Material Handling since the purchase of the company by the Young An company in 2003. Dennis Lawrence, President and CEO of CLARK commented on the business’s success, “Our team has worked tirelessly for the past 20 years to rebuild a brand that we can all be proud of. We have endured many challenges with the downturn in the market between 2009 to 2011 and COVID-19 in 2020. Through it all, we have been successful in building a strong team with dedicated employees, dealers, and customers.” Additionally, Mr. S.S. Baik, Chairman of CLARK Material Handling Board remarked, “We had a vision for this business when we acquired the company, and we could not be more pleased with its growth. As we look to the future, we are now making plans to welcome the third generation of the family into this business. They will begin to shape the vision of the business for future generations.” To prepare for this growth, Mr. Dennis Lawrence, President and C.E.O. of CLARK Material Handling Company, has been appointed to the Board of Directors for CLARK Material Handling and will step down as President and C.E.O. on July 1, 2024. He has made strong contributions as a key figure to YoungAn and the Baik Family for over 40 years. In this new role, he will work with the owners on various new strategic projects within the business. Mr. S.S. Baik commented, “We are excited to have Dennis as part of this new team and look forward to growing the business together.” With the above changes, CLARK Material Handling Company is pleased to announce the appointment of Mr. Michael (Mike) Binnie as C.E.O. effective July 1, 2024. Mr. Binnie is currently serving as C.O.O. of CLARK Material Handling and comes to CLARK with decades of experience leading dynamic teams. Mr. S.S. Baik commented, “Mr. Binnie brings a wealth of business experience to the team, and we are looking forward to the continued growth of the brand.” Mr. Lawrence commented, “Mr. Binnie has proven his business acumen and leadership strength as C.O.O. of CLARK. As the business continues to grow, we have full confidence in Mr. Binnie’s ability to build on the success of the company.”
Staffing employment begins to rise in January
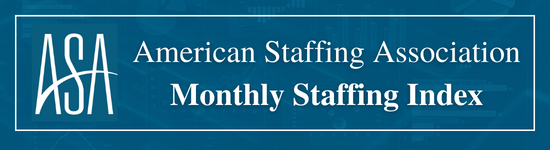
Almost half of all staffing firms report gains in new assignments After the seasonal end-of-year dip in December, staffing employment rose in the week of Jan. 8-14, with the ASA Staffing Index increasing by 4.0% to a rounded value of 88. Some staffing companies mentioned a holiday and inclement weather as primary factors that limited further growth. Despite two straight weeks of growth, staffing jobs were 12.5% below the same week last year. New starts in the second week of the year were up 19.2% from the prior week. Almost half of all staffing companies (48%) reported gains in new assignments week to week. The ASA Staffing Index four-week moving average decreased from the prior week to a rounded value of 86, and temporary and contract staffing employment for the four weeks ending Jan. 14 was 9.6% lower than the same period in 2023. “Staffing employment is rising in line with seasonal patterns of expansion, but its momentum is lagging behind prior years due to accelerated economic headwinds within the broader labor market,” said Noah Yosif, chief economist at ASA. This week will be used in the January monthly employment situation report scheduled to be issued by the U.S. Bureau of Labor Statistics on Feb. 2. The ASA Staffing Index is reported nine days after each workweek, making it a near real-time measure of staffing employment trends. ASA Staffing Starts are the number of temporary and contract employees placed in new assignments during the reporting week. ASA research shows that staffing employment has historically been a coincident economic indicator.
New Mobile APP for risk and safety professionals launched by Origami Risk
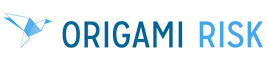
New solution helps engage operations and reinforce safety culture by streamlining safety inspections, audits, incident reporting and analytics, corrective actions Origami Risk, a risk, safety, and insurance Software as a Service technology firm, today announced the launch of a new mobile application with enhanced user experience to support the environmental, health, and safety (EHS) and risk management functions. The new app, Origami Mobile, empowers safety and risk professionals, employees, and contractors to quickly conduct audits and inspections; make observations; and report incidents from anywhere in the field via mobile phone or tablet – even when Wi-Fi or mobile connectivity is unavailable. Used in conjunction with Origami’s integrated platform for risk, safety, and compliance, the new app helps risk and safety professionals drive visibility into their data and initiatives through a single, centralized system. “As risk and EHS professionals look to be both more proactive and efficient in their efforts to drive safety, reduce risks, improve productivity, and achieve operational excellence, new technology-driven solutions are helping them raise the bar on their performance and results,” said Sean Salvas, senior market strategy lead-EHS at Origami Risk. “Working closely with our risk and safety clients, we designed the new mobile app to give those professionals an easy way to engage operations in the safety process, share in the success, and strengthen the safety culture across the enterprise.” “Mobile applications are an essential technology adopted by the vast majority of EHS leaders, with real-time data and offline functionality key to proactively identifying risks and hazards before incidents occur and ultimately sending workers home safe,” noted Bill Pennington, VP of Research, EHS and Risk Management at Verdantix, “Origami Risk continues to solidify its role in the EHS marketplace as an innovator with the introduction of its next-generation mobile app with modern performance and consumer-like navigation, filtering, and searching capabilities.” Origami Mobile enables risk and safety team members, operations managers, supervisors, and other users to perform multiple safety-related tasks, including: Complete standard checklists based on best practices or forms designed by risk and safety team members for specific departments, functions, operations, or locations. Detect and report workplace and operational hazards and behavior trends, including photo uploads to illustrate issues. Trigger the development of corrective actions and monitor their effectiveness. Gather real-time incident and near-miss data from specific operations or worksites, enabling risk and safety teams to instantaneously assess risk and hazards. Leverage data to create opportunities for early intervention and quicker resolution, preventing injuries and claims before they occur. Identify, report, and analyze safe/unsafe employee behaviors and conditions. Provide timely coaching to encourage and reinforce safe behaviors. Among its many features, the app includes offline capabilities that enable remote workers with limited internet access to input data offline and submit it when Wi-Fi or mobile connectivity becomes available. An autofill capability instantly matches employee and location data, streamlining the reporting process and eliminating the need for manual and repetitive data entry. Furthermore, with voice-to-text functionality, the app can be operated hands-free, promoting active note-taking and reporting. All input from the mobile app is automatically captured in a single web-based repository, giving risk and safety team members ready access to incident and claims data, dashboards, checklists, and metrics, while facilitating easy reporting and analytics.
Creform picking cart provides a versatile solution for wholesale distribution workflow
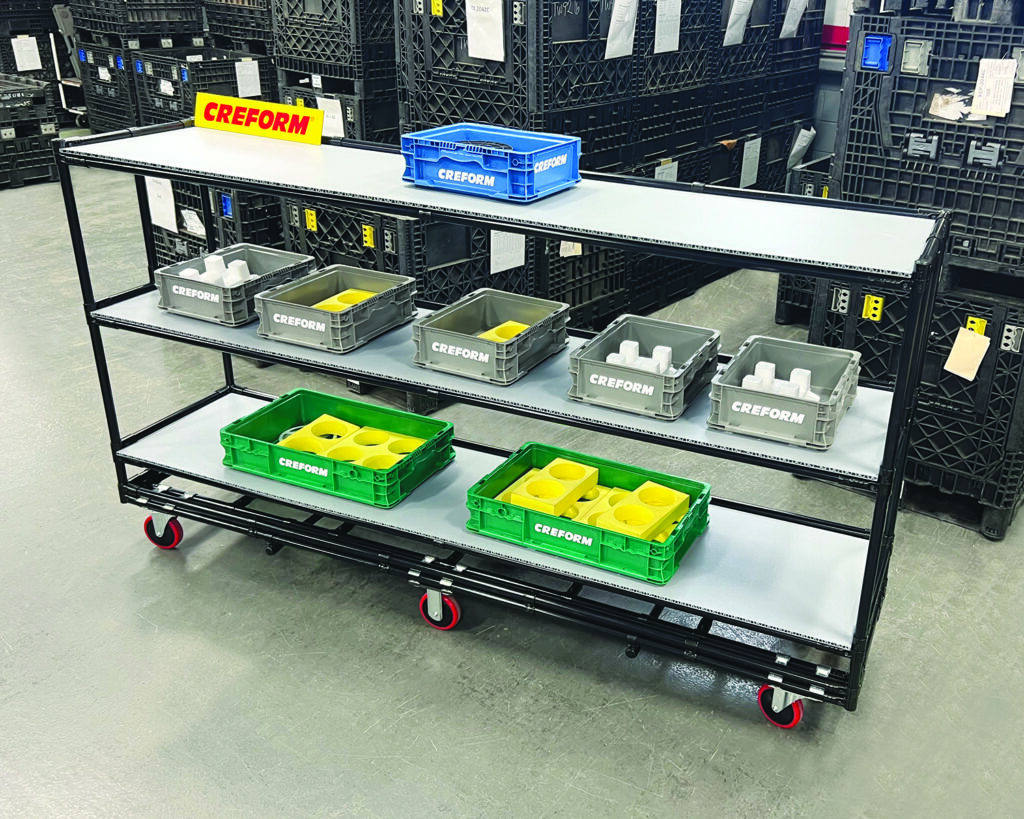
Creform Corporation, a manufacturer of unique products, has designed and built a picking cart for a healthcare services company that specializes in wholesale pharmaceutical distribution. The cart provides an innovative and versatile solution for in-process workflow. The engineering team at Creform collaborated with the healthcare services company and provided several prototypes to arrive at the best possible form, fit, and function, as well as the optimum shelf height and space utilization. The warehouse picking cart features three horizontal picking shelves for totes. Each shelf features a low-weight, high-stability polypropylene surface which is 50% lighter than wood. Each shelf can hold up to seven standard-sized boxes and the cart is well suited for E-commerce order fulfillment, as each shelf can be used to hold full boxes of parts or open boxes/totes that can be filled through piece picking. The shelves are flat for easy load/unload access as well as visibility from all sides. Should the need arise, each of the cart’s shelves can be repositioned or the whole cart can be customized with only simple tools. The modular construction of a Creform structure means easy customization and scalability. The cart’s dimensions are 91″ W x 22″ L x 51″ T and features six 5″ diameter bolt-on casters with urethane wheels for easy, stable, and safe rolling. The cart is designed to hold up to 600 lb. It also features two fixed casters in the center for easy directional control along with four corner swivel casters. The bolt-on casters are a durable solution for the high number of “miles” that the carts travel. As the cart will be pushed all day every day, it is important to keep the cart’s weight as low as possible while maintaining the necessary strength and durability. Creform’s 28mm plastic-coated steel tubing and clamping metal joints provide the necessary strength and durability yet retain flexibility. As with all Creform carts, higher capacity and custom cart sizes and configurations are possible with the Creform system of 28 mm and 42 mm plastic-coated steel pipes and metal joints. When needed, they can be configured for ESD (anti-static) applications. Further, Creform carts provide minimal maintenance requirements for prolonged durability. The surfaces are easy to clean to help maintain a hygienic environment. The color of the pictured cart shown is black, but a wide variety of pipe color options are available and upgrade hitches are available for AGV or tugger delivery. Accessories include hooks, label holders for shelf levels or even shelf positions, pockets for paperwork, and a writing surface with clipboards just to name a few. Creform carts are available as a kit, assembled structure or in component form for a complete DIY solution. Adaptability is a fundamental principle of Creform. The long-term, component nature of Creform ensures that if there are any damaged or worn components replacement parts are readily available. The Creform System is used to create an array of material handling and efficiency-enhancing devices and is a proven component in continuous improvement and lean manufacturing programs. The company partners with customers in developing and enhancing these programs.
Compact IDEC XA/XW emergency stop switches enable improved safety
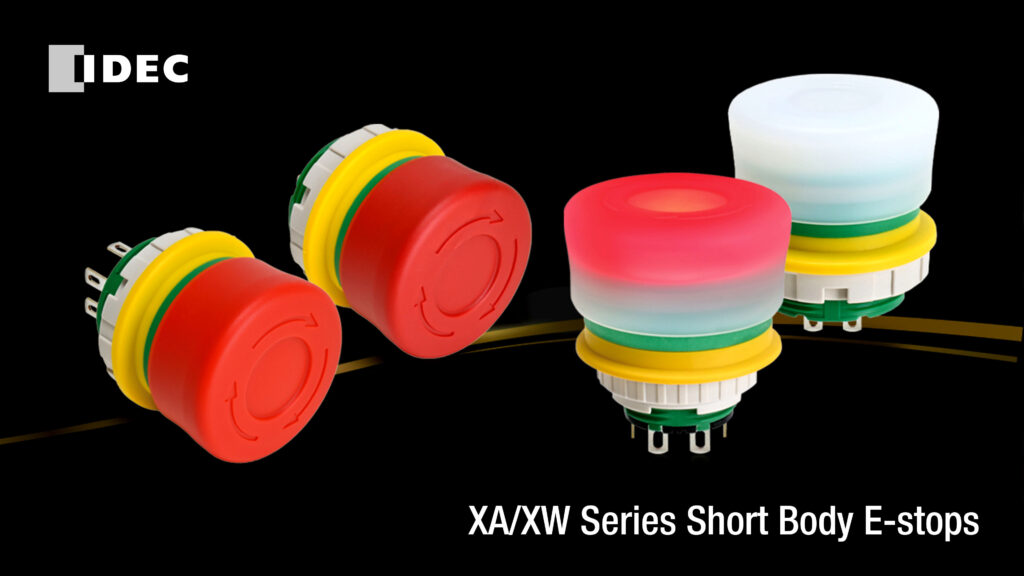
Expanding robotic and industrial equipment applications call for small form factor emergency stop switches. IDEC Corporation has expanded its line of emergency stop (E-stop) switches with new XA/XW series short-body models. These industrial-grade and outdoor-rated models are designed in the space-saving size essential for robotic and industrial equipment applications, with innovative features to meet the increased requirements of international safety standards. Modern E-stop challenges While E-stop switches have been a fundamental design and safety element of automated systems for decades, two factors have prompted an update of these devices. The first factor relates to the proliferation of smaller-scale automated equipment with increasingly limited onboard space but a need for E-stop functionality. Examples are robot teach pendants, mobile robotics, production machines, and industrial vehicles. The second-factor concerns revisions to safety standards. Safety standard ISO3691-4 (2020) requires E-stops to be accessible from both ends and both sides of industrial vehicles, which can be difficult or impossible to achieve without compact devices. In addition, any detachable or cableless control stations—such as pluggable portable teaching pendants or wireless controllers—are now required by ISO13850 (2015) to incorporate measures for avoiding user confusion regarding whether the E-stop is active or inactive. While there are various ways to achieve this, the XA/XW E-stops change color through illumination to indicate if they are active or inactive, which is a leading way to comply with the standard. Addressing new E-stop requirements IDEC has designed the XA/XW series to minimize the installation depth behind the mounting surface. Available in industry-standard diameters of 16mm for the XA and 22mm for the XW, these new E-stops now require only an industry-leading 12.6mm of space behind the mounting surface for solder terminal styles and just 18.0mm for tab terminal styles. All devices are rated IP67/69K and UL Type 4X for outdoor installation, and they can be specified with or without illumination. Operating temperatures range from -25 to +55 or +70 °C, depending on the model. When users select the active/inactive version for compliance with ISO13850, the E-stop cap color is opaque white when the device is inactive and red when the device is active. This unique feature is designed so that users will recognize the device is plugged into equipment and usable only when the E-stop is red. If the device is white, then the E-stop is not connected. The E-stops follow a standard push-lock and pull or turn to reset action, and the top cap uses cap-color direction arrows to comply with ISO13850. The body base is high visibility yellow with an angled “escape structure” design so debris will not hinder operation, and a green ring acts as a secondary visual indication of the E-stop pressed or not-pressed status. The E-stop physical mechanism uses IDEC’s unique and patented “reverse energy structure” for an additional degree of safety, with a spring arranged to operate the E-stop if it is physically damaged in certain ways. Competitive devices can fail to drive equipment to a safe state under these conditions. Even though the XA/XW series features a compact body, the non-illuminated version offers two NC contacts for integration with safety circuits and one NO contact for illumination and/or monitoring. Contacts are rated for an industry-leading 250,000 operations at 24V and 100mA, ensuring exceptional durability. Improved safety for any application The IDEC XA/XW series is designed to meet the latest safety standards in an industry-leading small form factor rated for challenging environmental conditions. Space-saving E-stops are needed for robotics, AGV/AMR, medical devices, tabletop machines, and other industrial applications. EV chargers, power generators, outdoor conveyors, and specialty industrial vehicles all need robust E-stops that are easily installed in limited spaces. As designers are increasingly using wireless controllers and detachable pendants for these applications, the active/inactive capability of associated E-stops is a key requirement.
Coast Guard Captain named Port Security Director
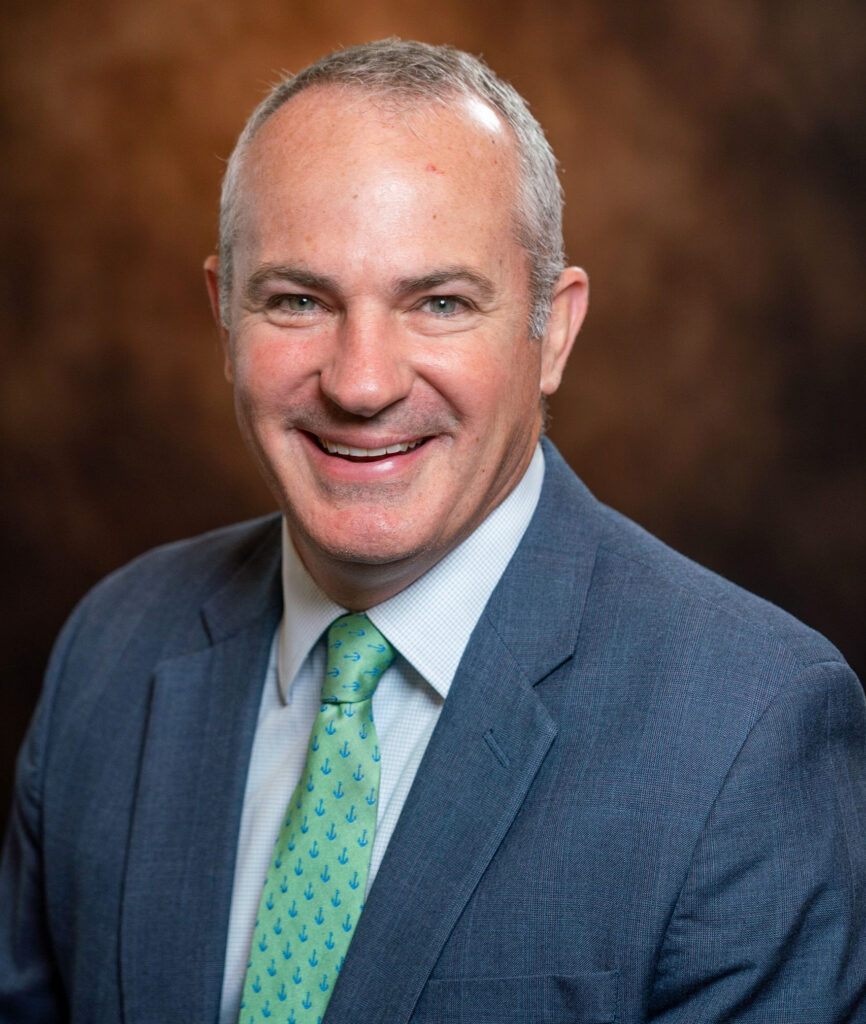
Manning to assume role following March retirement The Long Beach Board of Harbor Commissioners approved the appointment of U.S. Coast Guard Capt. Ryan Manning to lead the Security Division at the nation’s second-busiest seaport. Manning, currently Captain of the Port of Los Angeles-Long Beach and Commander of Coast Guard Sector Los Angeles-Long Beach, will join the Port of Long Beach following his retirement at the end of March. In his present role, Manning leads a team of 550 active duty, reserve, and civilian personnel and a 750-member volunteer auxiliary workforce. This team facilitates regional partnerships and conducts federal maritime safety, security, law enforcement, and environmental protection operations along the coast from Orange to San Luis Obispo County and within the United States’ largest container port complex. Before his current assignment, Manning most recently served as the Commanding Officer of Coast Guard Activities Europe, located in Brunssum, the Netherlands. In this position, he directed U.S. Coast Guard vessel inspection and port security assessments throughout Europe, Africa, and the Middle East. Manning received his commission from the United States Coast Guard Academy in 1994 and has served in a variety of port safety and security-related positions throughout his career. He has earned master’s degrees in mechanical engineering, joint campaign planning, and strategy. He is also a registered professional engineer in mechanical engineering. The Port of Long Beach Security Division’s top priority is to provide safety and security throughout the Port of Long Beach. The Port takes a leadership role in the development of strategies to mitigate security risks in the port complex, working closely with multiple partner agencies to plan and coordinate security measures.
Alta Equipment Group appoints Jeff Hoover as Chief Legal Officer and General Counsel
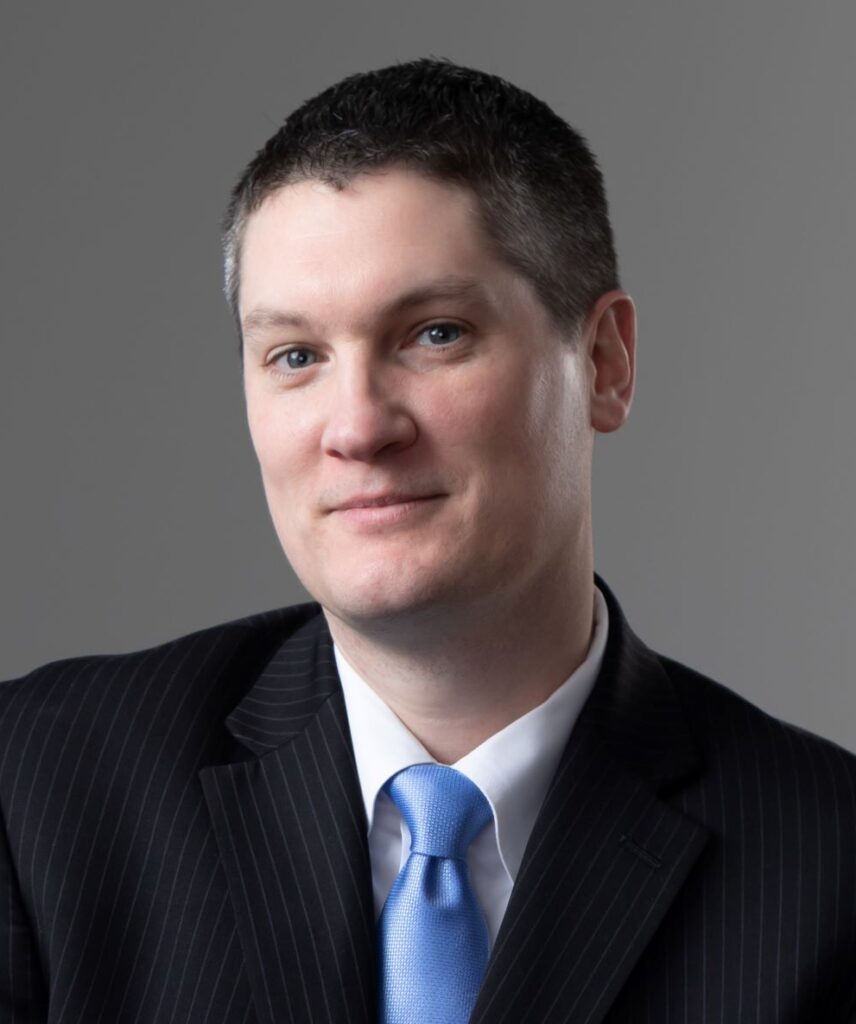
Alta Equipment Group Inc., a provider of premium material handling, construction, and environmental processing equipment, appointed Jeff Hoover as Chief Legal Officer and General Counsel effective immediately. Hoover came to Alta via Dinsmore & Shohl LLP, a national law firm, and before that Howard & Howard Attorneys, PLLC where he was a Partner at both firms and specialized in mergers and acquisitions, corporate finance, commercial lending, and real estate transactions. Hoover holds a Master’s of Business Administration in Finance from Eastern Michigan University and a Doctorate of Law from Cooley Law School. As Chief Legal Officer, Hoover will report to Alta’s Chief Executive Officer, Ryan Greenawalt, and take on the role of leading and coordinating Alta’s legal affairs, corporate governance, and Board relations, as well as being a business partner to our operational leaders from an administrative and compliance perspective day to day. “We are pleased to announce the appointment of Jeff Hoover as Chief Legal Officer and General Counsel. In Jeff’s previous roles, he was an integral partner to Alta where he supported our growth and development since 2016 as external legal counsel. Jeff has tremendous knowledge of Alta, our history, how we do business, and most importantly our culture,” said Ryan Greenawalt, Chief Executive Officer. “I look forward to the contributions he will make as part of the Alta family.” “I am excited to step into my new role as Chief Legal Officer and General Counsel and look forward to using my experience to continue to support the growth and success of Alta. I am thrilled to be joining the Alta family,” said Hoover.
Dorner appoints new Business Development Manager
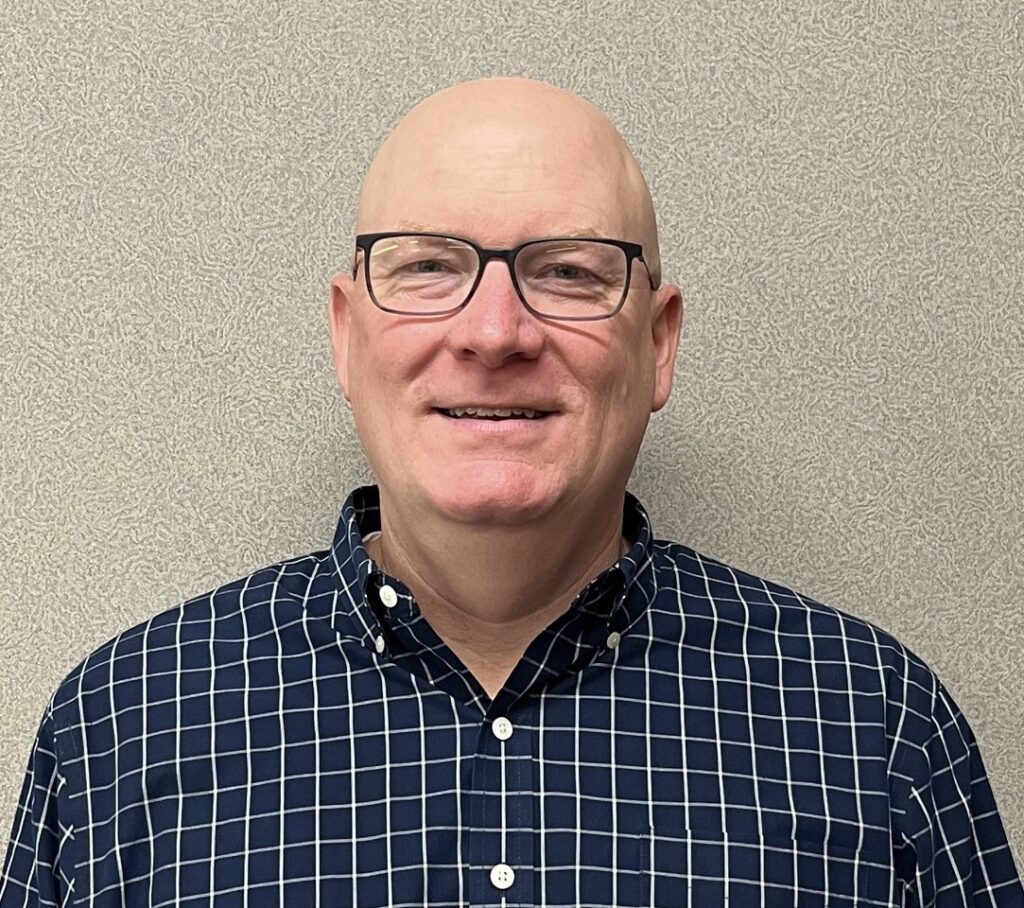
Dorner has hired Dave Giffels as Business Development Manager. Giffels will be working with the sales team to grow Dorner’s industrial and automation conveyor business into new markets and customer bases. Giffels joins Dorner after spending most of his career in automation sales, including 12 years with Bosch selling palletized conveyor systems. His experience spans across the material handling industry including work with manufacturers, integrators, channel partners, and customers. “Dorner has a long, distinguished history and has developed a reputation as a company that knows how to make conveyor systems the right way,” Giffels said. “I look forward to getting to work with this well-established brand on the manufacturer side again and get out into the field with customers and salespeople.” One of the first initiatives Giffels will be working on is incorporating a solutions-based sales approach in which salespeople will work with customers and channel partners to understand their operations before making recommendations based on each user’s specific goals.
Episode 454: Innovating Asset Management in Warehousing with Traka
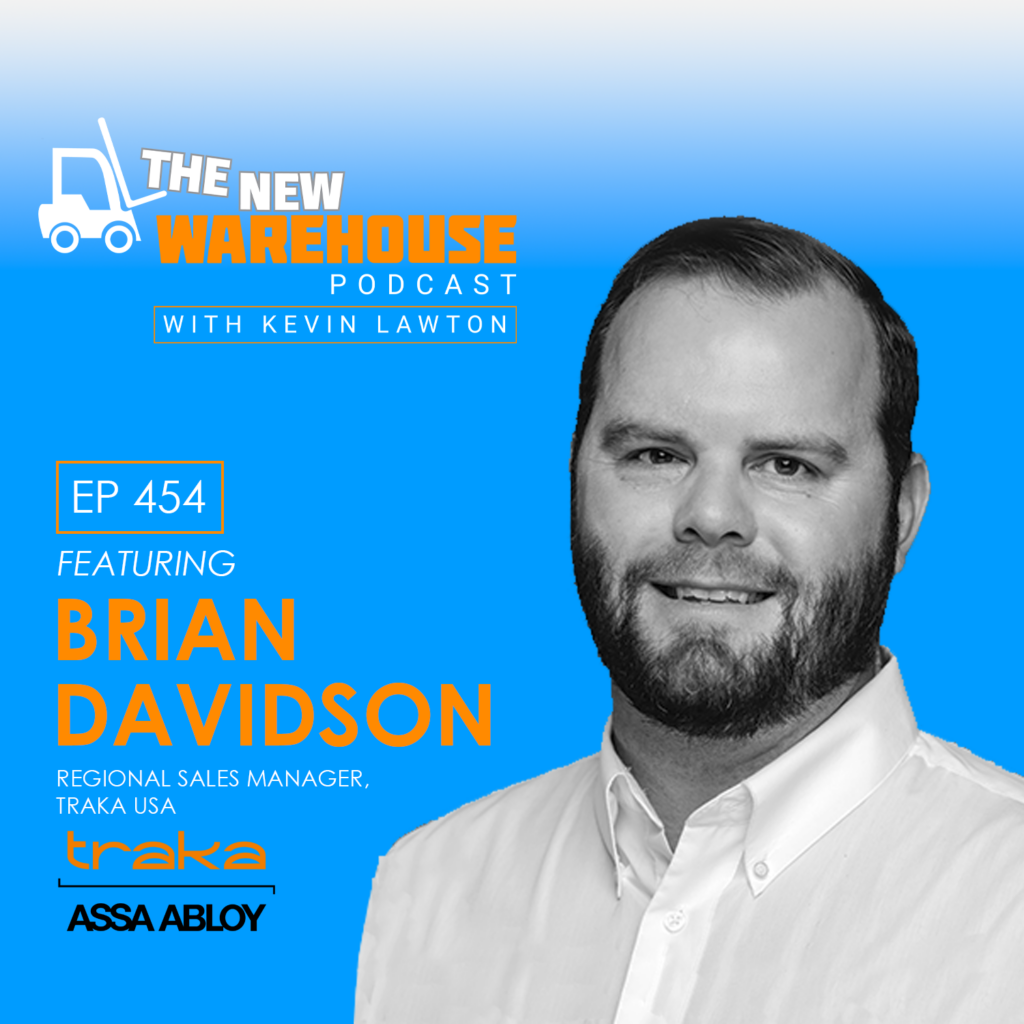
In this episode of The New Warehouse Podcast, Brian Davidson, Regional Sales Manager at Traka Americas, joins the show to discuss asset management in Warehousing. Traka Americas, a part of the Assa Abloy Group, specializes in asset storage and management solutions, mainly focusing on key and equipment management in various industries. This episode delves into how Traka’s innovative solutions address common pain points in warehouse operations and asset management. The Growing Need for Asset Management in Warehousing Davidson outlines the journey of Traka Americas, beginning with a software solution for a major airline in the early ’90s and evolving into a key and asset management company. Their initial focus on key management for fleet vehicles expanded over time, introducing locker management in 2007 to accommodate growing demands for diverse asset control, like managing radios. Davidson emphasizes, “The product continuously evolved, and as devices became more and more prevalent, now device management. Facilities are growing larger and larger, placing these scanners and keys in a place easily accessible within a facility has proven very valuable for many organizations.” Asset Management Accountability in Warehousing Davidson discusses Traka’s significant impact in the warehouse sector, especially in managing forklift keys and device management. He highlights the importance of placing devices and keys strategically within facilities for accessibility and efficiency. Davidson explains, “Our system enforces the process that employees need to follow, ensuring instant accountability and efficiency.” Curfew Feature and Fault Logging for Improved Management Traka’s system includes a ‘curfew feature’ for timely asset return and a ‘fault logging’ feature allowing users to report issues with equipment. Davidson explains, “If someone hasn’t returned their device, an email alert is sent out to their manager within a minute of the item going past curfew.” Access schedules in Traka’s system offer a critical feature for enhancing security and compliance within warehouse operations. They enable administrators to restrict vehicle or equipment use outside business hours, ensuring assets are only accessed during designated times. Traka’s fault logging feature offers a practical solution for recording and managing equipment issues. Upon returning an item, users can log any faults they encounter, such as a flat tire on a vehicle or a cracked screen on a scanner. These features prevent loss of productivity and ensure timely repair and maintenance of equipment. Davidson notes, “It helps ensure that these items are being returned within a designated timeframe.” Key Takeaways Traka Americas has evolved from software solutions to comprehensive key and asset management in warehousing. Their systems improve efficiency and accountability in warehouse operations. Innovative features like curfew alerts and fault logging enhance equipment management. The New Warehouse Podcast EP 454: Innovating Asset Management in Warehousing with Traka
Zion Solutions Group secures 2024 MHEDA Most Valuable Partner Award
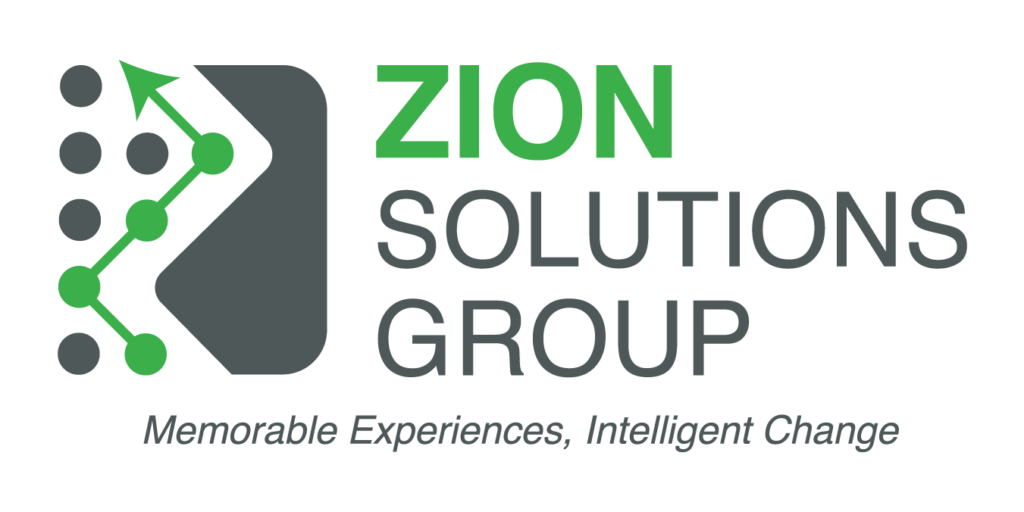
Zion Solutions Group has been awarded with the 2024 Most Valuable Partner (MVP) Award by the Material Handling Equipment Distributors Association (MHEDA). The MHEDA MVP Award recognizes companies that stand out for their industry excellence, commitment to education and community, and innovation. “Receiving the MVP Award for another year is more than just an honor for us; it’s a reflection of our unwavering commitment to excellence and the tireless efforts of our team. This award celebrates our 2023 focus on innovative strategies and strong relationship-building,” remarked Jim Shaw, President of Zion Solutions Group. The company has intensified its commitment to social responsibility in the past year, particularly in enhancing environmental sustainability and expanding educational outreach. These initiatives are part of its ongoing mission to enact positive change within the material handling sector and beyond. Looking ahead, Zion Solutions Group is set to continue its trajectory of growth and innovation, with plans to expand its technological capabilities and further solidify its position as a market leader. This award catalyzes our future endeavors, inspiring us to set new benchmarks in the industry.
H&E opens a new branch in SanAngelo,TX
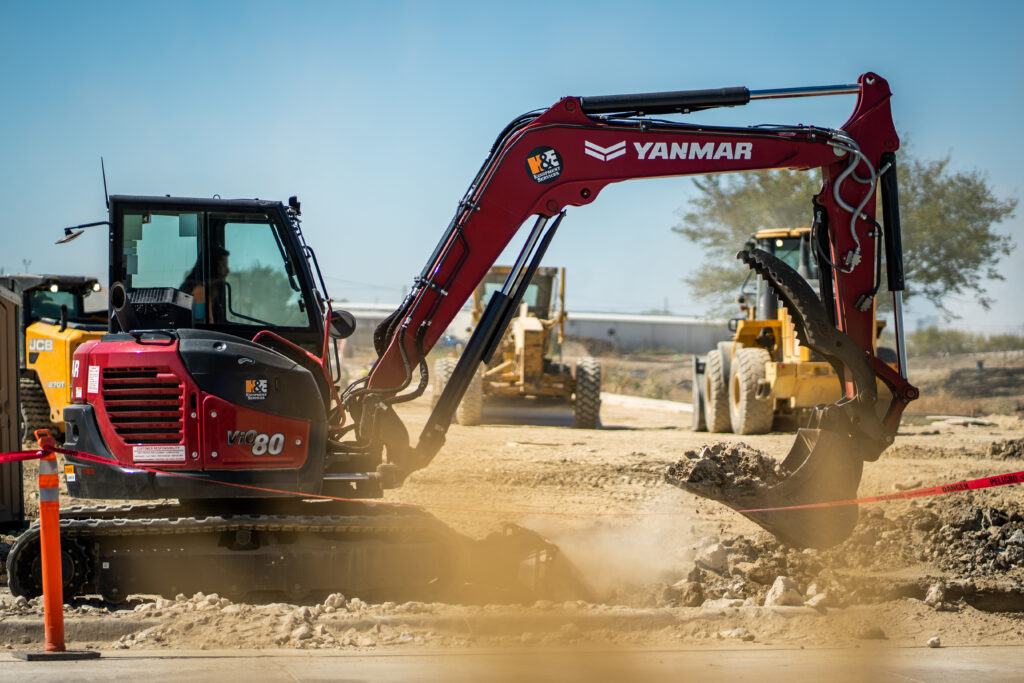
H&E Rentals (H&E) announces the opening of its San Angelo branch, the 26th rental equipment location in the state of Texas. Since this time last year, H&E has opened 15 new branches across the country, five of which are in the Lone Star State. The facility is located at 6728 Highway 853, San Angelo, TX 76901-9745, phone 325-222-1100. It includes a fully fenced yard area, offices, and a repair shop and carries a variety of construction and general industrial equipment. “The location of our San Angelo branch complements our existing facility in Midland and now provides even greater coverage to West Texas. Our territory reaches above I-20 and down to I-10, and we’re excited to serve customers in San Angelo as well as Abilene, Sterling City, Barnhart, Ozona, Brady, Brownwood, and points in between,” says Branch Manager Jason Blackman. “By having several H&E branches to our east within reach as well, we can source equipment from an expanded fleet and provide the specific unit that is needed. We’re just off Highway 67 and near other major roadways, so we’re able to get equipment to customer job sites quickly.” The San Angelo branch specializes in the rental of aerial lifts, earthmoving equipment, telescopic forklifts, compaction equipment, generators, light towers, compressors, and more and represents the following manufacturers: Allmand, Atlas Copco, Bomag, Case, Club Car, Cushman, Doosan, Gehl, Generac Mobile, Genie, Hamm, Hilti, Husqvarna, JCB, JLG, John Deere, Kobelco, Kubota, LayMor, Ledwell, Lincoln Electric, Link-Belt Excavators, MEC, Miller, Multiquip, Polaris, Sany, Skyjack, SkyTrak, Sullair, Sullivan-Palatek, Tag, Towmaster, Unicarriers, Wacker Neuson, Yanmar, and others. Founded in 1961, H&E Rentals is one of the largest equipment rental companies in the nation, providing a higher standard in equipment rentals, sales, parts, and service. Branches are located throughout the Pacific Northwest, West Coast, Intermountain, Southwest, Gulf Coast, Southeast, Midwest, and Mid-Atlantic regions.
Hamre Equipment joins LiuGong North America dealer network
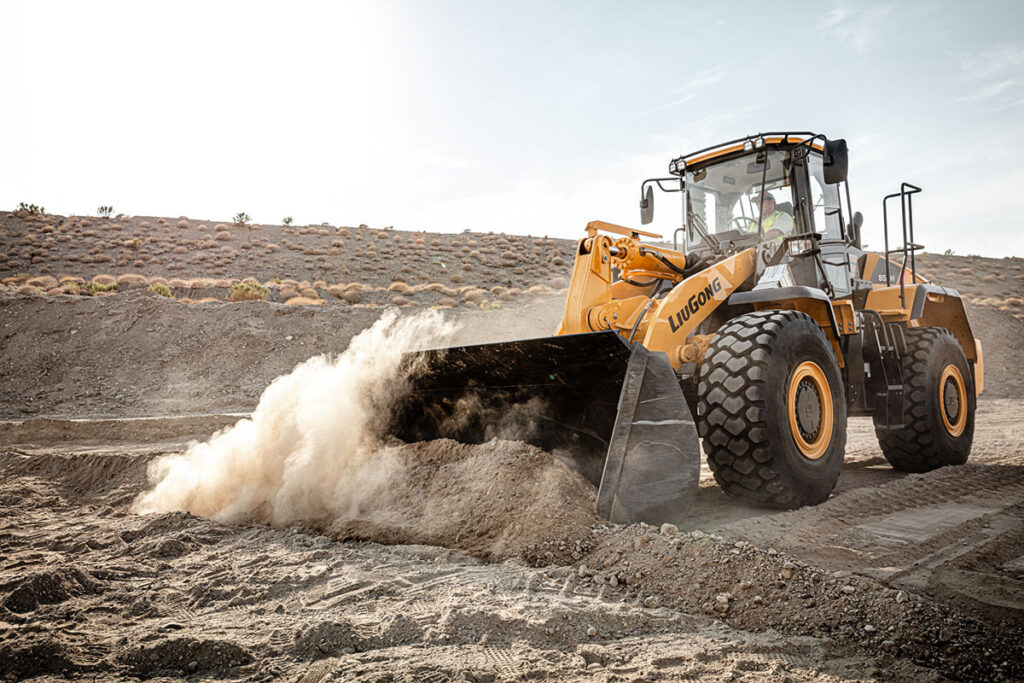
LiuGong North America adds Hamre Equipment to its dealer network. The Chico, California-based company has expanded from material handling equipment (MHE) into construction equipment (CE) since being founded in the late 1980s and has established a foothold in the region. Hamre Equipment also has international roots, as company CEO Lee Hamre met AmeraMex International in Mexico when Hamre Equipment worked to expand into international markets. AmeraMex International has three business units: Hamre Equipment Inc., Hamre Heavy Haul, and Hamre Parts & Service. After starting as a dealer of forklifts and compact truck loaders, Hamre Equipment began adding construction equipment to its range of offerings. It serves the industrial construction, intermodal, sales, forestry, and transportation industries. Hamre Equipment President Brian Hamre noted the opportunity to join the LiuGong dealer network has come in two stages, starting in the material handling equipment space six months ago and adding construction equipment products two months ago. A customer has already acquired a medium-size LiuGong wheel loader from Hamre. “It’s pretty fresh, but we’re happy to add LiuGong products to our dealership,” Brian Hamre said. “We’re just getting our feet into it. We’ve had some good acceptance on the forklift side in the Northern California market. Now that we’ve added the construction equipment side, we’re just now ramping that up to get noticed.” Andrew Ryan, President, LiuGong North America, hailed the Hamre group’s longtime standing within the region. “We’ve added the Hamre group in Northern California, a longstanding equipment dealership network with a really strong forklift presence in that part of the world. We’re excited to have them as part of the LiuGong team,” Ryan said. “The Hamre group has a great history with material handling equipment,” added Jared Ward, Vice President, Material Handling, LiuGong North America. “We look forward to growing with them as they join the LiuGong family.” LiuGong North America continues to grow its footprint in the North American market by providing high-performance and high-value machines.
2024 PTDA Foundation Board ready to pioneer new programs
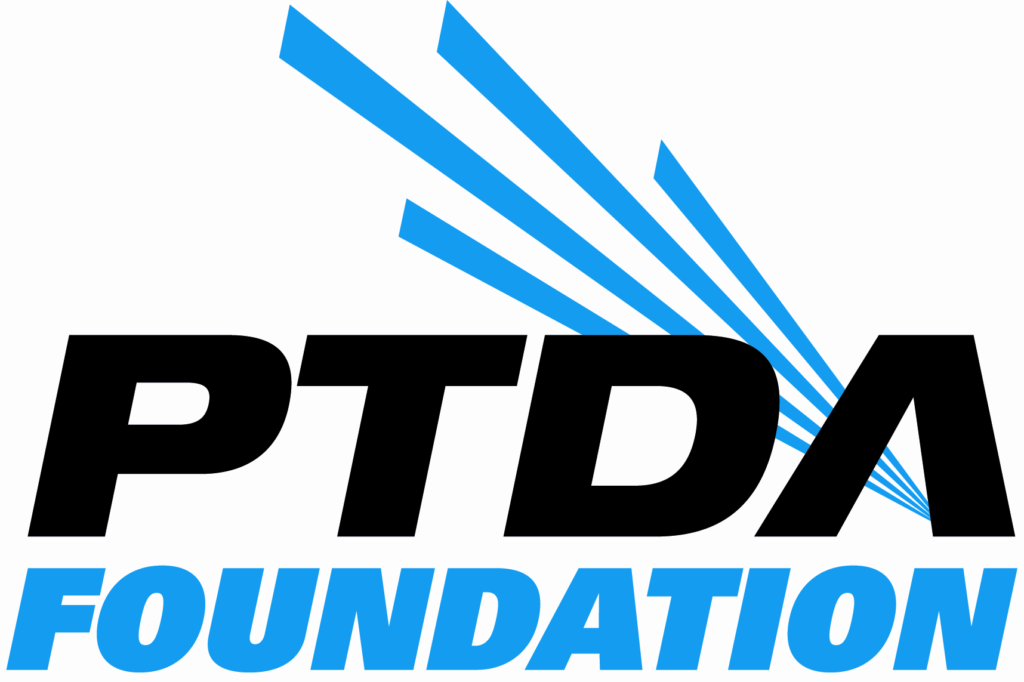
The Power Transmission Distributors Association (PTDA) Foundation Board of Trustees begin their leadership terms. Matt Pavlinsky, director of power transmission products, at Applied Industrial Technologies (Cleveland, Ohio) assumes the role of president. Pavlinsky has been involved with the PTDA Foundation since 2018. Most recently he served on the Board of Trustees and the PT WORK Force® Education, Research and Knowledge committee. “I am excited for the collective expertise and acumen the 2024 board brings to our efforts as we look in a new direction,” says Pavlinsky, “The Foundation is shifting its efforts to where it can have the most impact. Namely, building awareness of rewarding careers in the power transmission and motion control (PT/MC) industry and developing initiatives focused on providing vital educational and financial support for those interested in pursuing PT/MC careers or who already are working in the industry.” Joining Pavlinsky on the board are: Vice President Mike McLain, vice president, Allied Bearing Supply (Harahan, La.) PTDA President Brian Nowak, president & CEO, Kurz Industrial Solutions (Neenah, Wis) PTDA Treasurer JP Bouchard, vice president, General Bearing Service (Ottawa, Ontario, Canada) Keith Nowak, president, MPT Drives, Inc. (Madison Heights, Mich.) Ajay Bajaj, president, Rotator Products Limited (Woodbridge, Ontario, Canada) Rex Davis, VP operations, MAXCO Chain Ltd. (Marietta, Ga.) Hafeez Hameer, national distribution manager, Hercules OEM (Des Plaines, Ill.) Barbara Ross, director channel & representatives, Pfannenburg USA (Lancaster, N.Y.) Scott Taylor, vice president & general manager, Schaeffler Canada Inc. (Stratford, Ontario, Canada) JT Wubbolding, VP sales, NORD Drivesystems (Waunakee, Wis.) Newly appointed PTDA Foundation Director Kevin Koreman will support the board in its execution of plans and programs. Most recently, Koreman was member services specialist with PTDA. He began his career with PTDA as an operations & administrative assistant in 2018. The PTDA Foundation, whose work is funded solely by donations, was founded in 1982 to champion education, outreach and research initiatives relevant to the power transmission/motion control (PT/MC) industry that enhance the knowledge and/or professionalism and productivity for industry stakeholders. The Foundation is a not-for-profit, tax-exempt 501(c)(3) corporation; contributions are tax-deductible to the full amount allowed by law.
HyLite LED NexGen lotus lamps
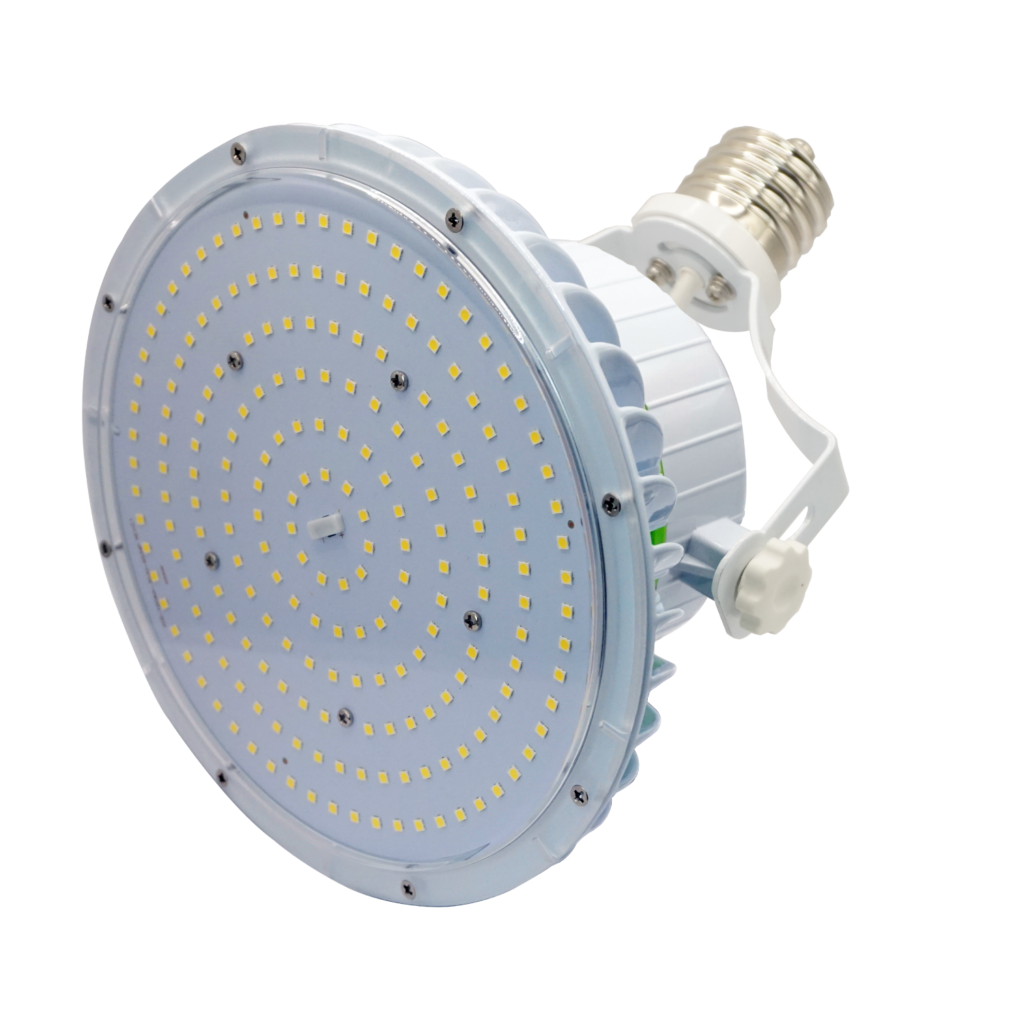
No Need to Replace Traditional Fixtures, Simply Plug N’ Play! The new NexGen Lotus Lamp is available in 40, 60 & 100 watt options to replace 300, 500 & 1,000 watt incandescent and halogen lamps. The 100w lotus lamp is the world’s only triac dimmable LED lamp. The proprietary & patented diecast heat-sink design provides excellent thermal management and heat dissipation. The IP-65 design provides complete ingress protection against contact, dust infiltration, and water splashes. All the lotus lamps are DLC-listed and are eligible for utility rebates, providing greater savings from your energy provider. The lotus lamp easily fits into existing PAR cans which makes retrofitting easy. No need to replace traditional fixtures, simply plug n’ play. The lotus lamp is ideal for stages & theaters, houses of worship, auditoriums, convention centers, exhibits & banquet halls, studios, arenas, and low & high bay lighting. The lotus lamp offers 3 customizable options to best suit your application. 3 Power Connection Options GX16D – for the 2-Prong PAR Lamp Connection E39 Socket – as a Mogul Base Screw-in Option WC2 – for a Hardwire, In Line Power Connection 3 Beam Angle Options 25° for Narrow Flood Beam 40° for Flood Beam 120° for Wide Flood Beam 2 Color Temperature Options 3,000K for Warm Light 5,000K for Daylight See how the Lotus Lamp can be your Lighting Solutions
Hyster-Yale Group and PortxGroup enter exclusive agreement to elevate materials handling solutions in Asian Sea Ports & Terminals
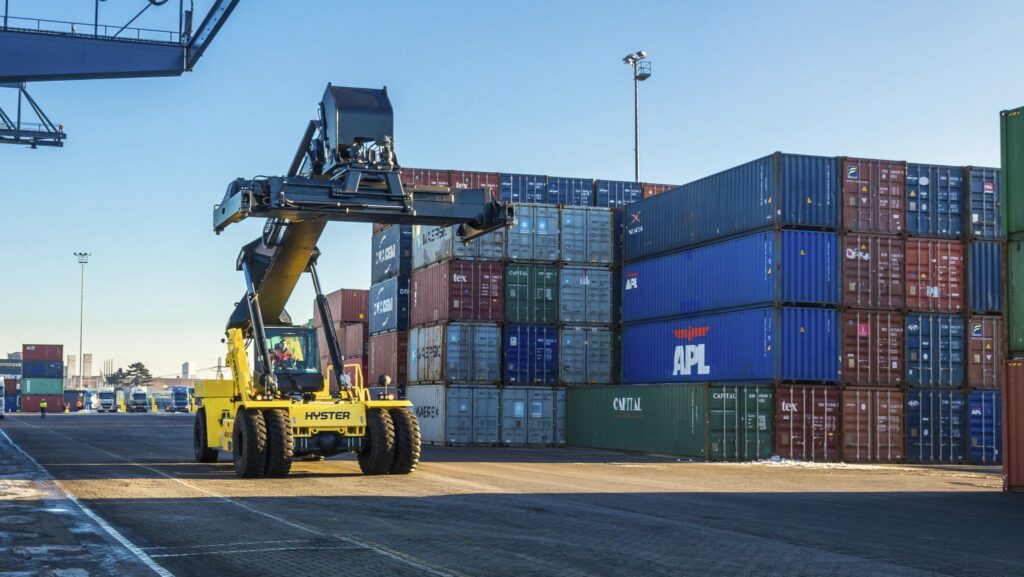
Hyster-Yale Group, an integrated full-line lift truck manufacturer, announced a strategic partnership with PortxGroup, a logistics solution, to exclusively distribute Hyster® products in key Asian sub-regions. The agreement positions PortxGroup as the sole Hyster dealer for seaports and terminals in Thailand, Malaysia, Indonesia, and South Korea, adding to PortxGroup’s earlier appointment as a Hyster dealer for the Pacific region. PortxGroup has been a representative for Hyster in the Pacific Islands for the past two years, demonstrating unparalleled success in challenging environments and port development projects. Leveraging its extensive experience and robust networks in the seaports and container terminals across Asia, PortxGroup will focus on expanding the presence of Hyster’s container handling equipment in the region. Simon Munn, Vice President, Dealer Development, JAPIC, Hyster-Yale Group, expressed enthusiasm about the exclusive partnership, stating, “PortxGroup’s proven track record, extensive experience, and commitment to customer satisfaction make them the ideal partner to represent Hyster exclusively for seaports and terminals in these key Asian markets. We believe that their dedication to excellence aligns perfectly with the values of Hyster-Yale Group.” In response to the appointment, Peter McLean, Principal at PortxGroup, shared his excitement about becoming an exclusive Hyster dealer for seaports and terminals in Asia. He stated, “I am honored to be allowed to be a Hyster dealer for seaports and terminals. Asia is one of the most dynamic and diverse regions — a territory that requires a business that is fiercely committed to customers.” McLean emphasized the strategic importance of the partnership, highlighting the comprehensive range of high-quality tier-one materials handling equipment and sophisticated engineering solutions that PortxGroup will now offer to seaports and terminals in the region. “This exclusive dealership enables us to provide one-stop-shop solutions, delivering the renowned quality of the Hyster brand combined with our long-term partnership approach to business,” he said. Effective 1 December 2023, PortxGroup serves as the exclusive Hyster dealer in the designated seaport and terminal areas, and Munn is confident in the success of this new venture. He added, “We are excited about the potential that this exclusive partnership with PortxGroup holds. With their strong industry presence and our commitment to innovation, we aim to further elevate Hyster’s business in the key markets of Thailand, Malaysia, Indonesia, and South Korea, solidifying our position as a leader in materials handling solutions for seaports and terminals in Asia.”
136 new Industrial Manufacturing Planned Industrial projects to finish out December 2023

Industrial SalesLeads has announced the December 2023 results for the new planned capital project spending report for the Industrial Manufacturing industry. The Firm tracks North American planned industrial capital project activity; including facility expansions, new plant construction and significant equipment modernization projects. Research confirms 136 new projects a drop from 161 in both October and November in the Industrial Manufacturing sector. The following are selected highlights on new Industrial Manufacturing industry construction news. Industrial Manufacturing – By Project Type Manufacturing/Production Facilities – 119 New Projects Distribution and Industrial Warehouse – 80 New Projects Industrial Manufacturing – By Project Scope/Activity New Construction – 42 New Projects Expansion – 38 New Projects Renovations/Equipment Upgrades – 63 New Projects Plant Closings – 11 New Projects Industrial Manufacturing – By Project Location (Top 10 States) Michigan – 13 Indiana – 9 California – 8 New York – 8 North Carolina – 6 Ohio – 6 South Carolina – 6 Texas – 6 Ontario – 5 Tennessee – 5 Largest Planned Project During the month of December, our research team identified 12 new Industrial Manufacturing facility construction projects with an estimated value of $100 million or more. The largest project is owned by Powerco Canada Inc., who is planning to invest $5 billion for the construction of a manufacturing facility in ST. THOMAS, ON. They have recently received approval for the project. Completion is slated for 2027. Top 10 Tracked Industrial Manufacturing Projects ARIZONA: Semiconductor MFR. is planning to invest $2 billion for the construction of a 500,000 sf manufacturing facility in PEORIA, AZ. They are currently seeking approval for the project. TEXAS: Solar panel MFR. is planning to invest $1 billion for the construction of a manufacturing facility in BROOKSHIRE, TX. They are currently seeking approval for the project. Completion is slated for late 2024. SOUTH CAROLINA: EV battery MFR. is planning to invest an additional $810 million for the expansion of their currently under-construction manufacturing facility in FLORENCE, SC. Completion is slated for 2026. ONTARIO: Tire MFR. is planning to invest $550 million for the expansion of their manufacturing facility at 388 Goodyear Rd. in NAPANEE, ON by 420,000 SF. They are currently seeking approval for the project. SOUTH CAROLINA: Magnetic product MFR. is planning to invest $500 million for the construction of a manufacturing facility in SUMTER, SC. They have recently received approval for the project. Completion is slated for Fall 2025. CALIFORNIA: Mobility technology innovation center is planning to invest $300 million for the construction of a 200,000 SF laboratory and manufacturing facility on Ramona Ave. in SACRAMENTO, CA. They are currently seeking approval for the project. They will relocate their operations upon completion. ARIZONA: Semiconductor equipment MFR. is planning to invest $300 million for the construction of a 250,000 sf manufacturing, warehouse, laboratory, and office facility in SCOTTSDALE, AZ. They will relocate their operations upon completion in 2026. OHIO: Biotechnology company is planning to invest $229 million for the expansion, renovations, and equipment upgrades on their processing facility in HAMILTON, OH. They are currently seeking approval for the project. ONTARIO: Medical supplies MFR. is planning to invest $165 million for the construction of a 140,000 SF manufacturing facility on Bonder Road in LONDON, ON. They are currently seeking approval for the project. Completion is slated for 2026. OREGON: Paper product MFR. is planning to invest $150 million for the renovation and equipment upgrades on their manufacturing facility in HALSEY, OR. Completion is slated for 2025. About Industrial SalesLeads, Inc. Since 1959, Industrial SalesLeads, based in Jacksonville, FL is a leader in delivering industrial capital project intelligence and prospecting services for sales and marketing teams to ensure a predictable and scalable pipeline. Our Industrial Market Intelligence identifies timely insights on companies planning significant capital investments such as new construction, expansion, relocation, equipment modernization and plant closings in industrial facilities. The Outsourced Prospecting Services, an extension to your sales team, is designed to drive growth with qualified meetings and appointments for your internal sales team.
Does CRM really “help” make the sale? Depends on which one you use
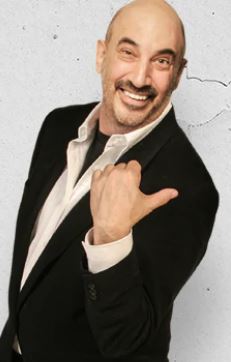
Are you using some form of database management to “control” your customer data? Customer Relationship Management or CRM has been around in one form or another for nearly 30 years. But in the last five years it’s become more sophisticated, more of a sales necessity, and a lot more competitive. The main multiple-user programs include Salesforce, Pipedrive, Zoho, Oracle, and Hubspot. Since I am often asked “which one” I recommend, I think it’s best to develop criteria for what I feel needs to be included (you should do the same) and go from there. Logging on to your CRM application gets you to your opening desktop dashboard. At a minimum there has to be an eyeful of “now.” You want to see hot prospects, top proposals, a forecast, their report card, and today’s appointments. You want a quick path to contacts, emails, and calendar – and maybe a motivational quote. From there, it should only be one click to new leads, current accounts, opportunity accounts, activity lists, phone book, email, contacts, tasks, a daily to-do report, a won-loss report, and/or a lead analysis report. And just a double click away from account detail, key issues, key people, and a sales plan to close each deal. ALERT: CRM is MISSING sales coaching. Coaching helps the salesperson make the sale, either internally with product knowledge, or externally with sales answers by means of online coaching when you demand it. If I’m a salesperson using CRM, and I am, I want to have access to better questions, a way to follow-up, pathways to decision makers, strategies to close my sales AS I progress through each sales cycle, and a way to build a relationship once a sale is made. Monitoring a sales cycle is one thing – that’s what databases are designed to do. But assisting salespeople with each step in the sales cycle is the missing element. Now with the domination of e-mail communication to single and multiple customers, PDF proposals, video chat and AI, a new dynamic has emerged in CRM: Monitoring all social and face-to-face activity. REALITY: The tragic flaw in CRM is that salespeople (maybe even you) avoid entering sales data even though it could help them. Yes, salespeople are reluctant to enter data for one silly reason or another, pain in the butt, EVEN though it’s for their own good. Me? I look for what I need and the user-friendliness of the application. Me? I look for what I use every day and how efficient it is. That’s why I chose Pipedrive, ease of use (I programmed it myself to my sales cycle), and amazing sales oriented and sales friendly functions. You? Do the same as I do. Figure out what’s best for you and do that. BUT do something. If you don’t have a CRM application in your life, get one. If you don’t, you’ll find yourself at a technological and informational disadvantage. And in sales, that’s no place to be. If you want the Pipedrive info and a free 30-day demo, go to www.gitomer.com/crm and get the offer. About the Author: Jeffrey Gitomer is the author of seventeen best-selling books including The Sales Bible and The Little Red Book of Selling. All of Jeffrey’s sales and personal development training programs, including his coaching program and a sales skills assessment, are available at www.gitomer.com. Gitomer’s NEW 3-day sales certification program is now available LIVE – go to www.GitomerTraining.com/coach. For information about keynote speaking, customized training and seminars visit www.gitomer.com, or email Jeffrey personally at helpme@gitomer.com.
Are you embracing the electrification of forklift fleets?
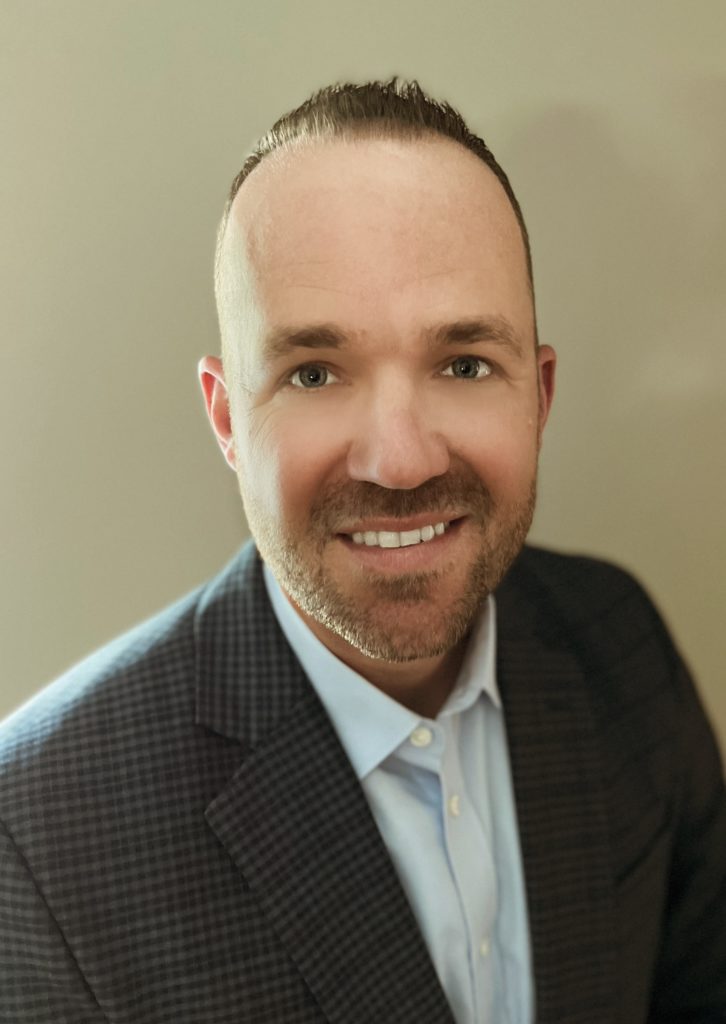
This time last year, in February 2023’s edition, I asked the question, ‘who owns the end-customer and their customer experience’ when it comes to the dealership and the battery agent? Electrification in the material handling industry, electrified equipment, and fleets, continue to be business trends within our industry and into the future. According to Transparency Market Research, they estimate the global forklift battery market will reach US $43.1 billion by the end of 2031. Warehouse operations continue to grow and expand within your service areas. This expansion has of course increased the requirement for forklifts, concurrently driving an increased demand for forklift batteries, battery service, technical support, battery monitoring and battery management. The growing trend towards electric forklifts can be attributed to their environmental benefits, lower operating costs, and advancements in battery technology. As we continue to see the electrification of forklift fleets across our industry, many dealers and independent service providers have embraced this as part of their business strategy. If you are considering adding forklift battery service and maintenance to your service offering, let’s take a closer look around some of the topics surrounding this trend and how it can be a new avenue of profitability for your dealership. Sustainability More and more dealers and suppliers I talk to are adding sustainability initiatives and incorporation of Environmental, Social, and Governance (ESG) strategies into their businesses. They are also being asked by their customers on what they are doing in regard to ESG, especially as many forklift users are embracing 100% zero-emission forklifts which is being driven by their own corporate sustainability initiatives. Implementing a battery service program into your ESG strategy aligns with the broader goals of environmental responsibility, social impact, and governance excellence. By prioritizing sustainability in your operations, your dealership not only contributes to a greener future but also positions itself as a leader in the industry, attracting environmentally conscious customers and employees. This also reflects a commitment to responsible business practices and long-term value creation. An additional part of a comprehensive battery service program is the inclusion of battery reconditioning services as part of your service offering, which further emphasizes your business’s commitment to sustainability. Instead of outright replacements, reconditioning offers a cost-effective alternative that resonates well with your budget-conscious customers. It’s not just about saving money – it’s about presenting environmentally friendly options that align with the sustainability goals of many businesses as noted previously. Extending the life of forklift batteries through reconditioning conserves resources and helps minimize waste of batteries that would otherwise end up in garbage landfills. Also, this eco-friendly service offering not only mitigates environmental impact but also presents a competitive advantage for your business to further market itself with the sustainability initiative. Technicians and Technology As the complexity of forklift battery systems increases, many of your customers opt to outsource maintenance services to specialized providers. This trend is driven by the need for expertise in handling advanced battery technologies and ensuring compliance with manufacturer specifications. Therefore, investing in your service staff through training and certification programs is an investment in the success of a battery service program. Well-trained technicians equipped with the latest knowledge and skills instill confidence in your customers. Certification adds a layer of credibility, assuring your customers that their forklift battery service and management is being serviced by experts. Customers value transparency and expertise and investing in state-of-the-art diagnostic tools and technologies is a strategic move. Outfitting your technicians with these tools will not only enable your technicians to identify battery issues with precision but also showcases your commitment to provide advanced services. Incorporating fleet management software and battery monitoring systems into your service program also enhances efficiency. Real-time monitoring allows your service team to be proactive, which ensures the reduction of unexpected breakdowns for your customer. This not only adds value to your service but positions your dealership as a leader in technology, which is also good for attracting the younger generation of technicians entering the workforce. Customer Satisfaction Establishing a battery service program isn’t just about meeting a market demand – it’s about positioning your dealership for long-term success in our ever-evolving industry. Offering solutions that go beyond a conventional service department, your dealership can not only stay ahead of the competition but also become a driving force for the future of forklift battery services. Your customers prefer streamlined services, and offering forklift service alongside dedicated battery services positions your dealership as a convenient and reliable partner. A forklift battery service program is a strategic investment that can boost your service department’s profits. The increasing emphasis on sustainability and cost-effectiveness in business operations will continue to fuel the demand for extensive battery services. The ongoing shift from conventional internal combustion forklifts to their electric alternatives, driven by a commitment to sustainability and reduced carbon footprint, underscores the importance of cleaner and more energy-efficient solutions. This transformative transition has elevated the need for maintenance, reconditioning, and replacement services for forklift batteries. By aligning with this trend, your dealership can solidify its position as a comprehensive, one-stop solutions provider for customers seeking forward-thinking and environmentally conscious options. About the Author: Chris Aiello is the Business Development Manager at TVH Parts Co. He has been in the equipment business for 17-plus years as a service manager, quality assurance manager, and business development manager. Chris now manages a national outside sales team selling replacement parts and accessories in various equipment markets such as material handling, equipment rental, and construction/earthmoving dealerships.