CanLift achieves 100% growth rate in two years and exhibits scalability in a competitive market
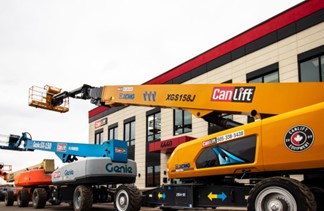
Family-operated enterprise achieves significant milestone powering businesses with aerial lift, material handling, and earthmoving equipment CanLift Equipment Ltd. (“CanLift”), one of Ontario’s largest independently owned lift equipment providers, has achieved a remarkable 100% growth rate in just two years, affirming its status as a scalable enterprise. CanLift operates from two locations based in Burlington and London, Ontario with a dedicated workforce of over 45 employees. They have strategically positioned itself for success with a fleet of over 1,100 machines and substantial investments in its infrastructure including trucks, drivers, and mechanics. CanLift’s growth is a result of a holistic business model that prioritizes workforce development, product diversification, strategic expansion, and logistical efficiency. The Company’s ability to navigate exponential growth while preserving its foundational values that derive from being a family-owned and operated business has drawn in a diverse clientele and veteran industry staff. “I joined CanLift because of its growth-oriented vision,” says Joe Gould, CanLift’s Director of Business Development who has served in various leadership positions at renowned companies within the equipment and machinery sectors. “In a market dominated by multinationals and private equity, our accessibility, hands-on approach, and commitment to customer satisfaction sets us apart from our competitors.” The availability of fleet equipment for both rental and purchase has also been integral to the Company’s success. “Our recent investment in over 100 large boom lifts ranging in size from 80 to 185 ft is a testament to our growth and innovation. We believe that by introducing higher-reaching aerial platforms, we can provide our customers with an alternative to traditional suppliers in this market segment,” comments Johnny Dragicevic, CanLift’s Managing Partner. CanLift prides itself on a service-centric approach, combining a competent and passionate sales team, a highly skilled service team, and a reputable network of partners with a large fleet of new and used equipment.
Long Beach port awards $630,000 in community sponsorships
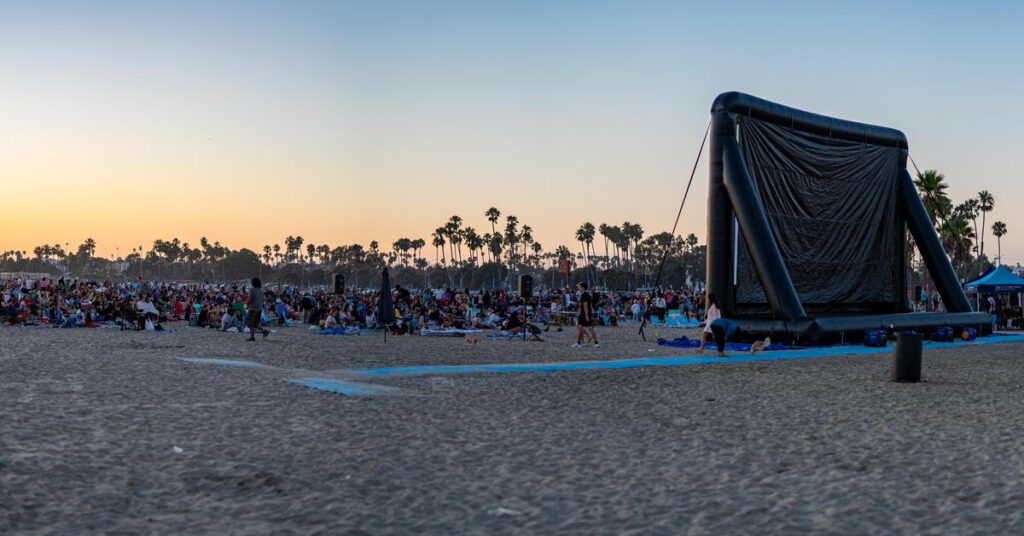
The Long Beach Board of Harbor Commissioners on Monday approved 167 sponsorships totaling $632,150, funding a diverse variety of community events and projects. The sponsorship program helps the Port of Long Beach engage with and inform local community members about Port operations and initiatives. Earlier this year, the Harbor Commission added a third call for the Port of Long Beach’s Community Sponsorship Program, which funds community events and activities that help inform residents about the Port. The events center on the environment, education, social justice, the arts and historic preservation. For this fall 2023 call, the Port received 9% more applications than in fall 2022. Of the applications, 38% were first-time applicants. To satisfy demand for community funding, the Board approved a $2 million sponsorship budget for the 2024 fiscal year that began Oct. 1. A record $1.44 million was awarded to community groups in fiscal year 2023. “We’re very proud of how this program has grown to help even more nonprofit organizations serving our city,” said Port of Long Beach CEO Mario Cordero. “Supporting these important members of our community fabric is part of our longstanding commitment to social responsibility as we provide jobs and drive economic activity across Southern California.” “The Port of Long Beach has an obligation to inform and educate the community about the key role it plays in the local, regional, national and international economy,” said Long Beach Harbor Commission President Bobby Olvera Jr. “The sponsorship program is a great vehicle to accomplish this goal while helping the amazing organizations that make our city a wonderful place to live and work.” Among the events and programs sponsored in this week’s awards are Literary Women of Long Beach’s Festival of Authors, the Hmong Association of Long Beach’s Hmong New Year Festival, Casa Bella Foundation’s Holiday Toys and Meals program, the Historical Society of Long Beach’s Centro de La Raza exhibition and the March of Dimes Baby Showers. A list of the approved sponsorships can be found here. The Port accepts sponsorship applications three times a year, in January, May and September. More information about the Community Sponsorship Program can be found at www.polb.com/sponsorships.
Staffing employment holds steady in November
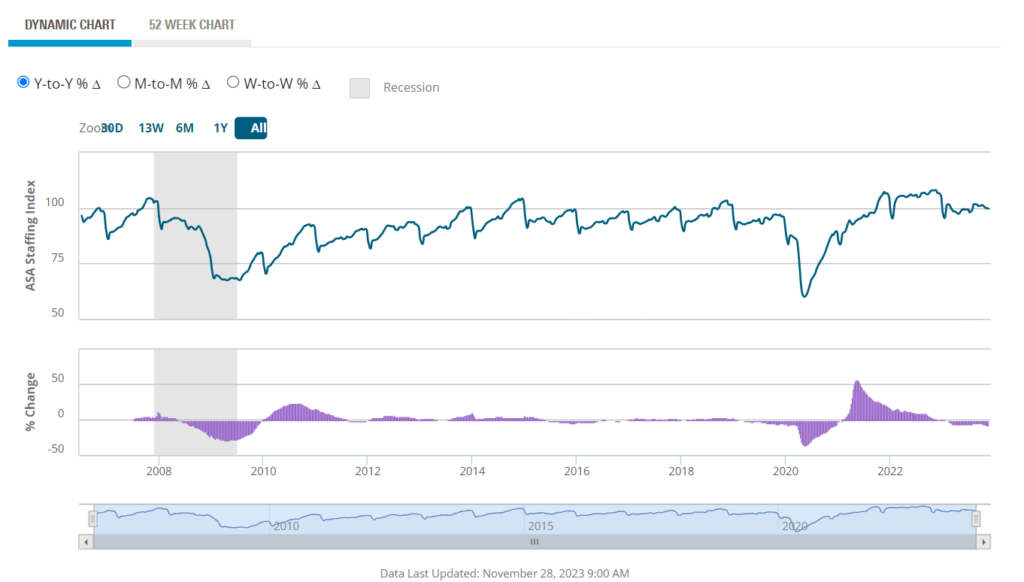
Over four-in-ten staffing firms report gains in new assignments Staffing employment inched up in the week of Nov. 13-19, with the ASA Staffing Index increasing by 0.8% to a rounded value of 100. Staffing companies listed no one primary factor that limited further growth. Staffing jobs were 7.3% below the same week last year. New starts in the 46th week of the year jumped 11.8% from the prior week. Over four-in-10 staffing companies (43%) reported gains in new assignments week to week. The ASA Staffing Index four-week moving average decreased from the prior week to hold at a rounded value of 100, and temporary and contract staffing employment for the four weeks ending Nov. 19 was 7.6% lower than the same period in 2022. “Staffing employment has held steady in November, with no significant dips or fluctuations from the prior month” said Tim Hulley, assistant research director at ASA. This week will be used in the November monthly employment situation report scheduled to be issued by the U.S. Bureau of Labor Statistics on Dec. 8. The ASA Staffing Index is reported nine days after each workweek, making it a near real-time measure of staffing employment trends. ASA Staffing Starts are the number of temporary and contract employees placed in new assignments during the reporting week. ASA research shows that staffing employment has historically been a coincident economic indicator.
Trojan AES battery wins Gold Lift and Access LLEAP Award
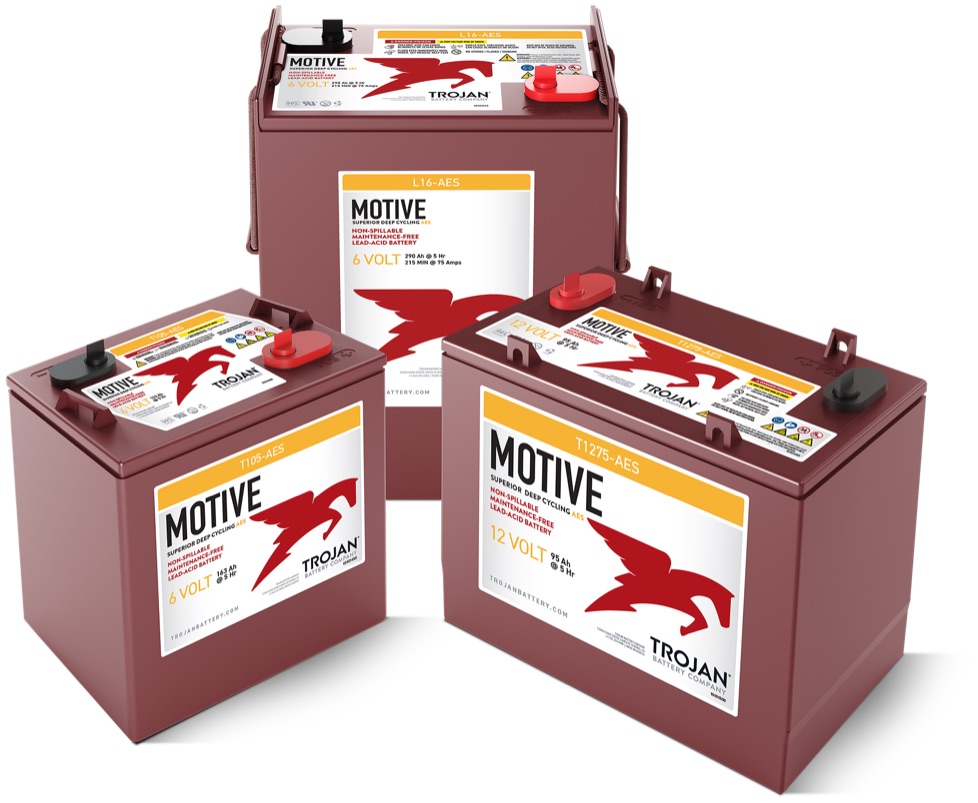
The Trojan AES Battery, which delivers up to 3x the cycle life of standard AGM, was selected as a Gold Award Winner in the 2023 Leadership in Lifting Equipment and Aerial Platforms (LLEAP) Awards presented by Lift and Access magazine. LLEAP Awards recognize innovative equipment and support products and services introduced in the North American market during the previous 12 months. Products were categorized into five categories: Mobile Elevating Work Platforms, Vehicle-Mounted Aerial Lifts, Material Handlers, Features and Components, and Aftermarket Support Products and Services. The LLEAP judging panel includes industry experts involved in operating, renting, selling, and servicing aerial platforms and lifting equipment. In evaluating each entry, the judges look for innovative features and technology, perceived value, productivity, and overall benefit to the industry, owners, and users. The top-scoring entry in each product category received a Gold Award, and the second-highest-scoring entry received a Silver Award. Trojan received a Gold Award in the Features and Components segment. “The Trojan AES battery provides access equipment owners and users with another maintenance-free battery option that overcomes many of the limitations of standard AGM technology. Trojan Battery Company is honored to receive this prestigious award,” says Bob Pigott, vice president of global sales. The product is featured in the 2023 Nov/Dec edition of Lift and Access. The Trojan AES Battery is also used in: Golf, personal transportation (PTV) and utility vehicles Floorcare equipment Material handling equipment Solar Marine and recreational vehicles
ORBIS gives back to local communities
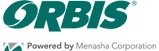
From Make-a-Wish and Blessings in a Backpack, to contributions supporting our nation’s heroes and more, ORBIS team offers participation and donations toward a number of charitable efforts ORBIS® Corporation demonstrated its pledge to give back to local communities and charitable organizations in 2023. From hosting a Walk to End Alzheimer’s summer event at its global headquarters in Oconomowoc, Wisconsin, to gifting charitable donations and sponsoring events with impactful organizations such as local police departments, humane societies, veterans’ groups and more, the ORBIS team supported a number of charitable causes. As a subsidiary of Menasha Corporation, which was founded in 1849, ORBIS has a rich history in packaging – and giving back to support the local communities in which it operates. With funding made available through the Menasha Corporation Foundation, the charitable arm of ORBIS’ parent company, each ORBIS facility has a team that collaborates with nonprofits, coordinates fundraisers and provides volunteers in the local area. “Every year, the ORBIS Community Action team hosts a Giving Reception to celebrate the services nonprofit organizations provide to our communities. Approximately 50 organizations and 80 individuals attended this year’s event,” said Jo Anne Behling, Community Action Team leader at ORBIS Corporation’s Oconomowoc headquarters. “In addition to the donations we make, we work with our nonprofit partners to provide volunteers to help support their great work. I am honored to be a part of the Community Action Team.” ORBIS team members are dedicated to giving back to organizations that are working to make the world a better place for individuals and families in need. “At ORBIS, we firmly believe in making a positive impact in our communities. We aspire to make a difference, enrich lives, foster growth and build a legacy that extends into the community,” said Norm Kukuk, president of ORBIS Corporation. “There is such warmth and kindness that emanates from our beneficiaries; we are grateful to help, and it is an honor to give back to those in need to support their missions.” ORBIS supports a wide variety of organizations throughout southeastern Wisconsin. These organizations are focused on safe and healthy citizens, community betterment, education and environmental sustainability. In addition to financial donations made possible by the Menasha Corporation Foundation, ORBIS was also able to help in additional ways throughout 2023. Here are some highlights from special events where ORBIS impacted the local community: Walk to End Alzheimer’s and Summer Employee Event – Held at the ORBIS Oconomowoc, Wisconsin, location, this event raised nearly $5,000 in 2023 in support of the Alzheimer’s Association. Activities included lunch, an auction and dunk tank contest, with all proceeds benefiting the Wisconsin Chapter of the Alzheimer’s Association. Shorehaven Memory Care provided resources to employees, and fellow ORBIS employee, Linda Patel and her dog, Louie, were on-site as well. Linda and Louie serve as a volunteer therapy team in the memory care unit at Shorehaven Memory Hospital. ORBIS teams were organized in both Waukesha and Madison, Wisconsin. Bread & Roses – ORBIS employees volunteer and donate food two to three times a year at Bread & Roses, helping to provide meals to those in need. During each event, up to 250 dinners are packaged and served for takeout for families in need. Make-A-Wish America Gold Star Donation – As part of ORBIS’ Make-a-Wish America Gold Star donation in 2023, the organization and team made a wish come true for a 16-year-old boy from Menomonee Falls, Wisconsin, who is living with a nervous system disease. With an MLB-wish theme, ORBIS hosted a wish party in late October. The Milwaukee Brewers “pitched” in as well, donating ice cream helmets and other gifts as part of his wish. ORBIS Christmas Family Fundraiser – Supporting 30 children in Wisconsin’s Waukesha and Jefferson counties each year, the ORBIS Christmas Family Fundraiser is brought to life as employees fulfill children’s wish lists. These gifts are purchased, wrapped and delivered before Christmas – making the holidays brighter for families in need. Generosity runs deep within ORBIS; the Christmas Family Fundraiser is fully funded by ORBIS employees. Blessings in a Backpack – For 10 years, ORBIS has supported the Waukesha County Chapter of Blessings in a Backpack. In 2023, about 30 children attending Magee Elementary School in Genesee Depot, Wisconsin, received backpacks filled with nutritious food for each weekend for the entire school year, with support from ORBIS. ORBIS volunteers participate in bag fills and distribution. Rainbow Hospice Care – ORBIS organized a brat fry and donated all proceeds to Rainbow Hospice Care, a local nonprofit providing supportive care management, hospice care, community bereavement support and community health ministry. Police Competition – Now in its third year, the police competition is among three local police departments that compete to be the first to push a squad car to the finish line. In 2023, the Watertown Police Department came in first, Oconomowoc Police Department took 2nd and the Summit Police Department earned 3rd place, with each awarded funds to support their departments. Heroes for Heroes – Heroes for Heroes is a nonprofit advocating for PTSD awareness and support, fundraising for service dogs, and promoting more opportunities for veterans. At its annual summer event to raise money for a local veteran’s service dog, ORBIS employees volunteered their time to support the event. The River Food Pantry – ORBIS volunteers packed lunches and distributed to clients of the River Food Pantry. The River Food Pantry is south-central Wisconsin’s busiest food pantry, providing services that include free groceries and freshly prepared meals for pickup or delivery, online grocery orders, mobile meals and emergency food lockers. Additional Beneficiaries: Bryon Riesch Paralysis Foundation – Run, Walk, Roll Event Watertown Police Department – Donut Dash 5k Event National Alliance on Mental Illness (NAMI) Southeast Wisconsin – NAMIWalks 5k Down Syndrome Association of Wisconsin – Walk at Milwaukee County Zoo Lupus Foundation of America – Charitable golf outing Lake Country Shop with a Cops Waukesha County Green Team – Sustainability event Angelman Syndrome Foundation – ASF Walk shirts LifeStriders – Triple Crown Event Creative Community Living Services Guardians of the Children Humane Animal Welfare Society of Waukesha County Humane Society of Jefferson County Watertown Humane Society Inc Wounded
The first lithium forklift battery that is UL 2580 certified and ISO9001 certified in the industry is BSLBATT® Battery – Industrial
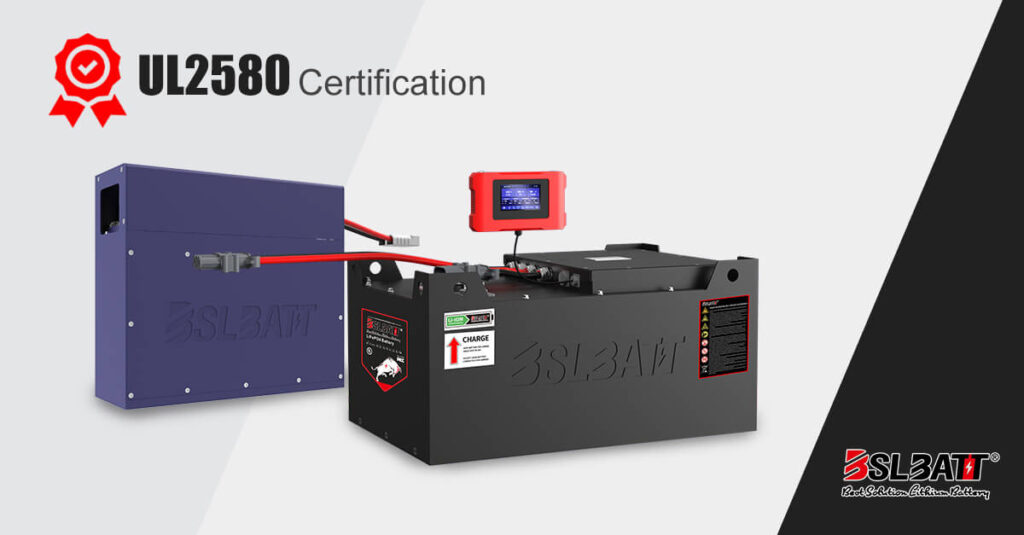
It’s an exciting time for battery innovation whether you own, operate, or lease a forklift. The Underwriters Laboratories (“UL”), a global manufacturer in safety science, has awarded BSL New Energy Technology Co., Limited, a manufacturer of lithium forklift battery systems based in Huizhou, China, North American UL 2580 certification for its 51.2V+ A range of battery models. Forklifts of Class I and Class II can be operated with these models. As a result of this safety certification, BSLBATT® Battery – Industrial’s product line of heavy-duty, over 950 battery models have been approved for use in material handling applications. Certified to UL 2580 UL certification ensures the product meets the highest standards of safety and durability. In UL 2580, batteries are exposed to a range of damaging scenarios to determine their ability to withstand abuse and protect personnel. BSLBATT® forklift lithium batteries recently received the prestigious UL 2580 certification. BSLBATT® forklift lithium batteries represent a breakthrough in safety and reliability in the material handling industry. Nationally recognized safety standards have been met by batteries with UL certification. For material handling applications, BSLBATT® provides safe, reliable, and resilient power solutions. This achievement is significant. BSLBATT® has achieved UL 2580 certification in the North American power industry. What is the significance of this? ❖ In order to determine which batteries are the safest, Underwriters Laboratories (UL) evaluates parameters such as battery chemistry, manufacturing processes, and testing protocols. ❖ Even though lithium technology is extremely unstable and dangerous if it is not monitored/appropriately controlled, you can be assured that your battery meets industry safety and performance standards. ❖ With BSLBATT® forklift lithium batteries, you get the surety of proven technology combined with the benefits of lithium-ion modular technology, delivering high power in a compact design. Capacity of energy. As the first battery manufacturer in China to introduce ISO 9001 compliance to the material handling industry, BSLBATT® is also designed to comply with this standard. To move heavy-duty industrial trucks towards an electric future, safety is key. UL’s certification of BSLBATT®’s forklift lithium battery contributes to this goal by reducing development cycles, enhancing safety, and speeding up time to market. Haley, Marketing Director at BSLBATT®, said. “We are grateful for the outstanding work of the UL team in creating our unique and revolutionary product.” There are several destructive tests involved in UL 2580 testing, including: ❖ Short circuit test ❖ Squeeze test ❖ Multi-axis rotational test ❖ Drop the test ❖ Fire spread test After all the destructive events leading up to the final fire test, the BSLBATT forklift lithium batteries passed all tests and continued to operate and charge rapidly at industry-leading dual-gun 400A continuous rates. As a result of the fire test, the battery self-extinguished in less than an hour, posing no threat to the surrounding area. Fragment of UL test https://www.youtube.com/watch?v=35vKZPJT6kw https://www.youtube.com/watch?v=uWAY9yxi9pc The following are some of the benefits of BSLBATT® lithium-ion forklift batteries: Modular design allows for adaptability to changing needs. As your warehouse business grows and evolves, BSLBATT® provides 43 standard modules in a variety of sizes and configurations. Your investment is protected by durable construction. BSLBATT® uses 6000W laser-welded cells, reliable large-format prismatic cell technology, and lithium iron phosphate chemistry for per-cell stability. BSLBATT® uses the highest quality lithium cells without active balancing. Downtime is minimized by a long cycle life. With BSLBATT® batteries, operators can spend less time charging the battery and more time getting the job done. Modular design allows the system to be expanded to increase capacity. When the module’s power life ends, it can be reused as a backup power source. Employees and the workplace are protected by advanced security features. CE, IEC62619, and UL2580 standards are met by BSLBATT®. In addition, BSLBATT® developed the battery’s innovative battery management system in accordance with ISO 26262:2011 and complies with Automotive Safety Integrity Level C (ASIIL C). In addition to meeting strict automotive functional safety standards, the battery management system protects against over-discharge and provides additional performance benefits. The presence of MINIMAL maintenance (no watering required) further enhances efficiency. Watering lithium-ion batteries is not necessary, saving time and money. The BSLBATT® cloud platform system keeps devices performing at optimal levels throughout their battery life through regular preventative maintenance. “We are very excited about BSLBATT’s achievement, which proves their products are safe and compliant with North American regulatory requirements,” May Hao, director of power sales at UL China South China, said.As a company that supports rapid product innovation and business growth in the growing renewable energy sector, UL understands the challenges faced by battery manufacturers for electric vehicles. To help manufacturers achieve product excellence and gain market access, we will continue to leverage our 100 years of experience and expertise.” The future of electricity is here Lithium-ion batteries have been around for a long time. The challenge has been harnessing their power safely without power surges and fluctuations. BSLBATT® forklift lithium batteries change all that. BSLBATT® is very excited to introduce the first forklift lithium battery. To learn more, contact us today or visit our website.
Komatsu announces plans to acquire American Battery Solutions
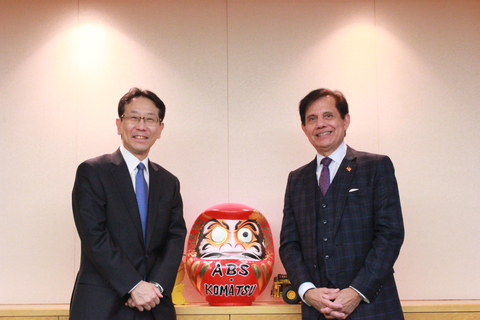
Komatsu, through its wholly owned subsidiary in the U.S., Komatsu America Corp., has agreed to acquire American Battery Solutions, Inc. (ABS), a battery manufacturer headquartered in Detroit, Michigan, U.S. Komatsu is planning to close the acquisition on Dec. 1, 2023, on the condition that all necessary procedures for the closing are completed. The immediate impact on Komatsu’s consolidated business results is estimated to be minimal. ABS develops and manufactures a wide variety of heavy-duty and industrial battery packs, using lithium-ion batteries for commercial vehicles, transit buses and on- and off-road vehicles. The company provides both standard and custom battery systems optimized to each customer’s needs. ABS’ technology, combined with the advanced product development knowledge and expertise of its people, enables the company to develop and manufacture battery packs designed to deliver superior performance and product life, and to enhance safety. The acquisition of ABS will enable Komatsu to develop and produce its own battery-operated construction and mining equipment, through the integration of ABS’ battery technology with Komatsu’s knowledge and network. The first equipment produced with ABS’ batteries will be used to power mining equipment in North and South America, where demand for electrification has been increasing. In the future, Komatsu will aim to expand the use of batteries in construction equipment and to establish a global supply system. Komatsu will continue to support ABS’ battery business to further develop the electrification business post-acquisition. ABS will operate as a stand-alone business entity within Komatsu and will continue its growth plans by executing on its current and prospective customer programs in the commercial vehicle segments. The mining and construction opportunities provided through Komatsu will enable ABS to position itself as one of the world’s leading providers of battery systems in both on-highway and off-highway markets. Through the acquisition, Komatsu will accelerate the development of battery-powered electric vehicles by utilizing ABS’ battery-related technology, along with other initiatives Komatsu is pursuing with its partners, to further contribute to the electrification of construction and mining equipment and the realization of a decarbonized society. These efforts will help Komatsu achieve its management target of 50% reduction of CO2 emissions from the use of its products by 2030 (compared to 2010 levels) as well as the company’s challenge target of achieving its carbon neutrality by 2050. As part of its growth strategy for the mid-term management plan “DANTOTSU Value – Together, to ‘The Next’ for sustainable growth,” Komatsu is working to develop and launch electric equipment to help achieve carbon neutrality, creating new value for customers with the development of new equipment, processes and technologies that will help operations step forward to the next stage for the workplace of the future and provide a more sustainable environment for the next generation.
Motion names new Automation Intelligence GVP
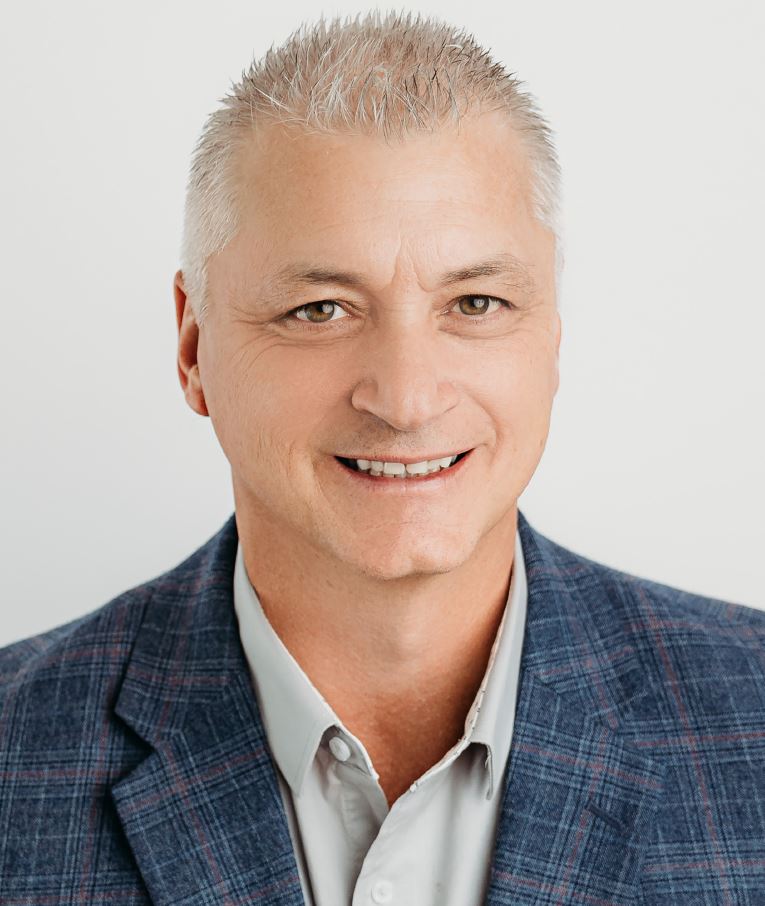
Motion Industries, Inc., a distributor of maintenance, repair and operation replacement parts, and a premier provider of industrial technology solutions, named Mike Esposito to Group Vice President, Motion Automation Intelligence, effective immediately. Most recently, Mr. Esposito served as Director of Motion Automation Intelligence’s Engineering Assembly Solutions (EAS), having joined Motion as part of the Kaman Distribution Group (including Kaman Automation) acquisition. With over 25 years in industrial automation and manufacturing, he has developed a systems approach along with deep, cross-functional experience as an automation consumer, producer and supplier. Mr. Esposito’s experience has enabled the development of solution-driven teams focused on positioning customers and internal stakeholders to be successful. Prior to joining Motion/KDG, he held senior management roles at iAutomation, CDF Corporation, and SencorpWhite. Motion Automation Intelligence solution technologies include robotics, motion control, machine vision, digital Networking/IIoT, industrial framing, pneumatics and custom mechatronic systems. In his new role, Mr. Esposito will lead the Motion Automation Intelligence team, and his responsibilities will include the development and implementation of multi-year strategic business and marketing plans. He will report to Joe Limbaugh, Motion’s Executive Vice President and Chief Operations Officer. “We are thrilled to have Mike at the helm of our automation group. With his diverse yet relevant background and technical expertise, he possesses a unique insight into the industry’s needs and operations. In addition, Mike’s leadership skills and deep passion for automation will certainly spur Motion Automation Intelligence to new heights.”said Limbaugh. Esposito is a graduate of Bridgewater State College (Master of Science in Technology Management – Summa Cum Laude) and New England Institute of Technology (Bachelor of Science in Electronic Engineering Technology – Summa Cum Laude).
CLARK Material Handling Company announces appointment of Jerry Dolan as Aftermarket Regional Sales Manager
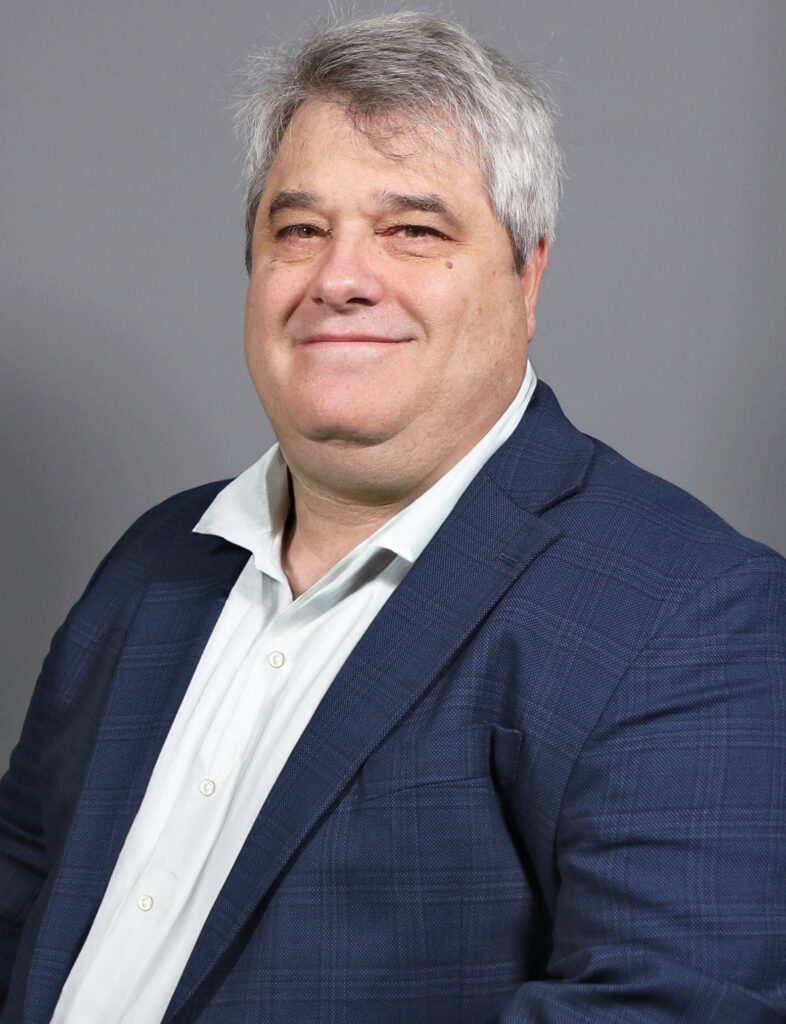
CLARK Material Handling Company has announced the appointment of Jerry Dolan as Aftermarket Regional Sales Manager for CLARK North America. Mr. Dolan will report to Charlie Chwasz, North American Aftermarket Sales Manager. In this role, Mr. Dolan will support the CLARK dealer network on the aftermarket side, assisting dealers as they grow their parts and service departments. Mr. Dolan has over 25 years of experience in the material handling industry, both on the OEM and dealer level. Mr. Dolan served in many roles, including Truck Sales, Aftermarket Sales, Branch Manager, Operations Manager, and General Manager for long-time CLARK dealer Mid-Columbia Forklift in Washington state. Mr. Dolan has a strong background in growing parts and sales business and building lasting relationships with customers built on trust and transparency. “We are pleased to welcome Jerry to the CLARK team, with his extensive industry experience and proven track record of building strong relationships with dealerships and with customers,” commented Charlie Chwasz, North American Aftermarket Sales Manager. “Jerry’s commitment to excellence will be of great benefit to the CLARK team as we collaborate with our dealer network to increase parts and service sales.” “The ability to work for one of the legacy forklift brands, with a strong culture of supporting our dealer network, and one of the broadest product lines in the industry is exciting to me,” added Jerry Dolan, Aftermarket Regional Sales Manager. “I’ve worked with the CLARK brand for many years, and I am thrilled to be working directly with the CLARK team now. CLARK parts maintain the same durability and quality the brand is known for, and I look forward to working with the CLARK dealer network to grow their business in the parts and service departments.” Mr. Dolan resides in Washington state and will be responsible for supporting all northern US and Canadian CLARK dealers.
Episode 440: Electrovaya’s lithium-Ion power solutions for warehousing
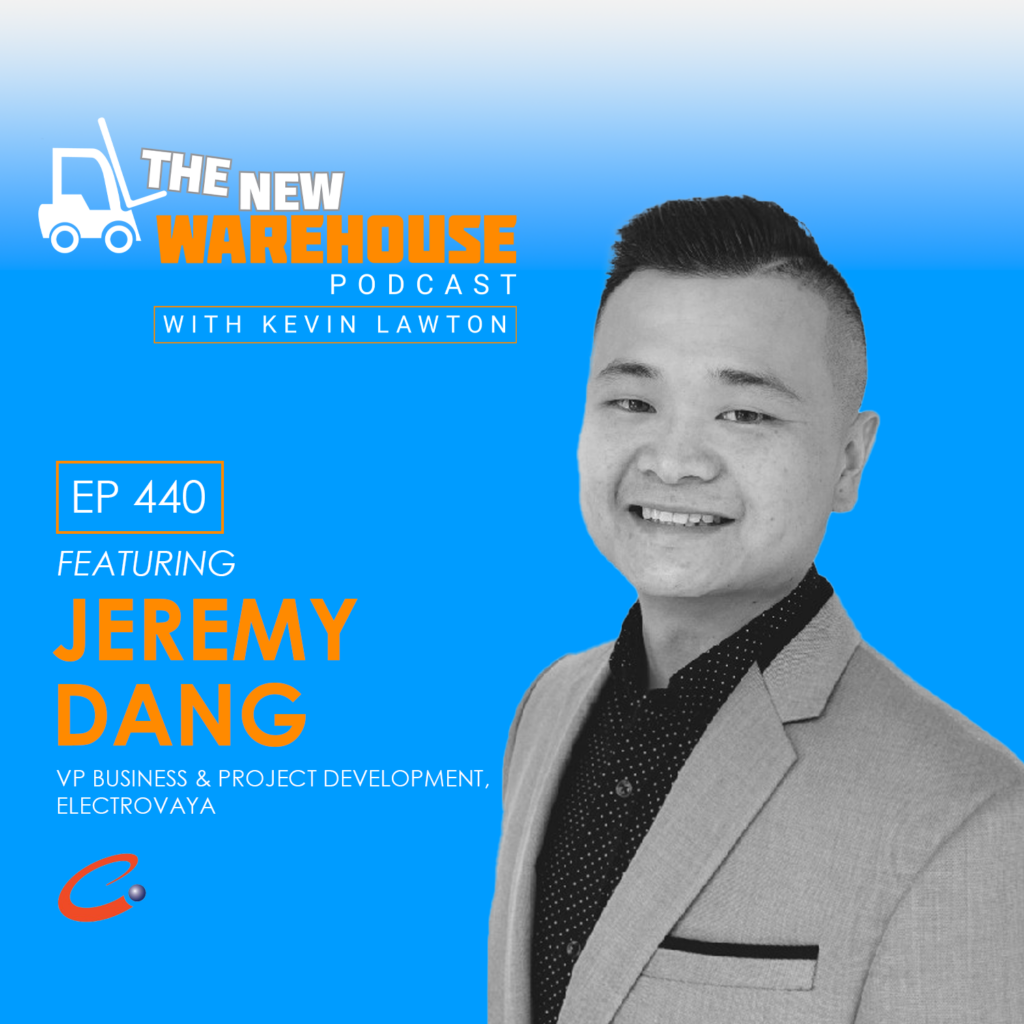
In this episode of The New Warehouse Podcast, Kevin welcomes Jeremy Dang, Vice President of Business Development at Electrovaya, to explore the company’s innovations in lithium-ion power solutions for warehousing. Dang discusses Electrovaya’s journey and its impact on evolving lithium-ion technology in the industry. Lithium-ion Market and ROI: Proven Longevity and Cost-Effectiveness Dang highlights the shift from lead-acid to lithium-ion batteries. “The adoption rate is now at an all-time high, and I expect it to increase over time.” He notes, “With the cost of lithium coming down, it’s becoming a feasible option even for smaller, one-shift operations” to integrate lithium-ion as a common power source for material handling applications and still see a positive ROI. Dang believes, in some cases, lithium-ion batteries are “going to be a 20-year product.” Electrovaya’s Differentiators: Longevity and Safety Focusing on Electrovaya’s unique lithium-ion battery technology, Dang highlights two significant differentiators: longevity and safety. “Our batteries can do up to 14,000 cycles and are thermally stable above 200 degrees Celsius,” he explains, showcasing the exceptional lifespan and safety features. Dang highlights the durability of Electrovaya’s lithium-ion batteries with a compelling example: One of Electrovaya’s oldest customers, a Fortune 500 company, was surprised to find the batteries holding up so well after six years of heavy-duty operations. Dang adds, “They’re at the point where the batteries have started to outlive the life expectancy of the truck.” This capability is a shift from the usual where trucks outlast multiple lead-acid batteries.’ He further notes, ‘This longevity means a “lithium-ion battery is going to be seeing multiple lift trucks within its lifetime.” Relationship with Raymond and Sustainability Dang discusses Electrovaya’s relationship with Raymond, which began primarily with rigorous battery testing and evolved significantly over the years. He highlights the progression of this collaboration, culminating in the Energy Essentials program in December 2020. The strategic agreement between Electrovaya and Raymond Corporation provides Raymond exclusive access to Electrovaya’s advanced NMC Ceramic lithium-ion batteries. In addition to further emphasizing longevity and safety, this battery line collects and transmits valuable data to help customers gain insights. Dang adds, ‘With this integration, data from our batteries, like current, voltage, and odometer readings, is transmitted to Raymond trucks, offering customers critical insights for optimal fleet utilization.’ Three Key Takeaways on Lithium-Ion Power Solutions for Warehousing Industry Shift to Lithium-Ion: Lithium-ion batteries offer extended life cycles and cost savings even in smaller, single-shift material handling operations. Battery Recycling: Collaboration with companies like Raymond Corporation underscores a commitment to sustainable and efficient power solutions. Lithium-Ion Battery Longevity: Lithium-ion batteries last at least six times longer than traditional lead-acid batteries. The New Warehouse Podcast EP 440: Electrovaya’s Lithium-Ion Power Solutions for Warehousing
Toyota Material Handling’s former president and CEO honored with prestigious industry award
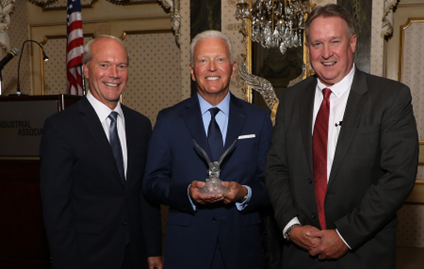
Toyota Material Handling congratulates Jeff Rufener, the company’s former president and CEO, on being honored with the 2023 Meritorious Service Award by the Industrial Truck Association (ITA). The 72-year-old association for industrial truck manufacturers in North America has recognized leaders dedicated to serving the organization and advancing the material handling industry with this prominent award since 1992. “Jeff was an integral part of the material handling industry for over four decades serving in various leadership roles,” said Brett Wood, Toyota Material Handling North America President & CEO. “Not only did he lead Toyota through transformational changes, but with his humble and inspirational leadership, Jeff motivated others to embrace challenges and improve each day. He was always passionate about Toyota’s culture of Kaizen – to continuously improve – and the core purpose of ‘Helping People Carry the Load’.” Rufener contributed to the ITA for more than 20 years, serving as ITA Chairman from 2009-2011, as well as serving on the Executive Committee and as a Board member. He helped found the inaugural National Forklift Safety Day and acted as the first-ever chairman of the task force, laying the foundation for safer operational practices for years to come. Rufener advocated for increased safety in the material handling industry through operator training, educational programs and product and process efficiency improvements. He also recognized the necessity of sustainability and energy efficiency within the industry. Under his direction, Toyota launched more than 20 electric forklift models, strengthening the organization’s position as an industry leader. “I am humbled to receive such a special award from an organization I love so much in the ITA,” Rufener said. “The ITA is so impactful because of its culture, its people and a noble core purpose – the same three tenants that make Toyota great. I’m proud to have been part of both groups and will never forget what we accomplished together.” Rufener emphasized corporate social responsibility as a hallmark of the Toyota brand. One of Rufener’s philanthropic initiatives included the development of Toyota’s partnership with the American Red Cross. Serving as Chairman of the Board of Directors for the Red Cross’ Southeast Indiana chapter, Rufener established a multifaceted initiative of corporate, dealer and associate support. His leadership led to countless donations from Toyota dealerships throughout the country of rental equipment, time, expertise, money and regular blood drives, as a testament to the relationship of the organizations. During his tenure at Toyota which began in 2011, Rufener oversaw the company’s headquarters transition from California to Indiana. Then in 2020, he led the integration of Toyota’s two Columbus-based companies, Toyota Material Handling, USA (TMHU) and Toyota Industrial Equipment Manufacturing (TIEM), creating a single company. Since his retirement in 2021, Bill Finerty, Rufener’s successor, has carried the charge of continuing Toyota’s role as the leader within the material handling industry.
Episode 439: Innovative AGV and AMR Solutions from JLC Robotics
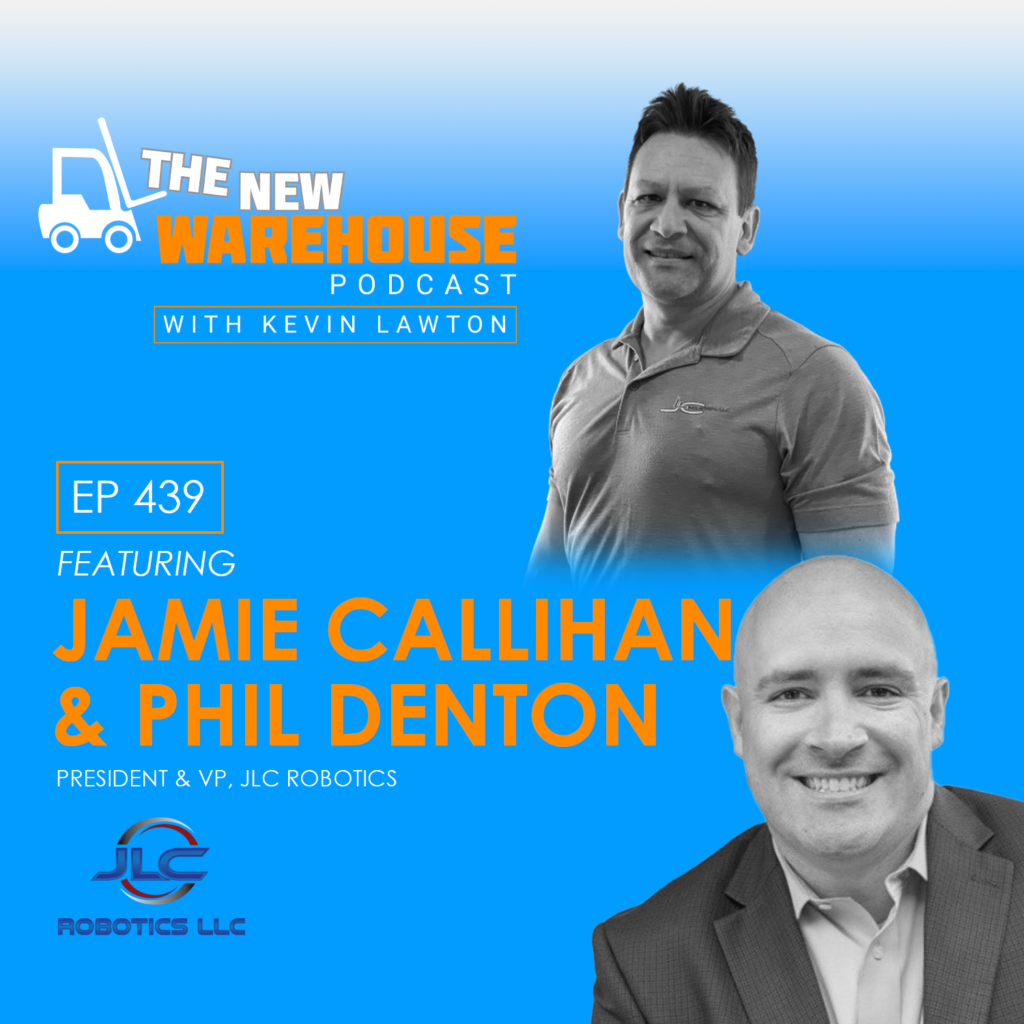
In this pre-Thanksgiving episode of The New Warehouse podcast, we welcome Jamie Callihan and Phil Denton from JLC Robotics. Jamie is the President, and Phil is the Channel Sales Manager at JLC Robotics, a company at the forefront of robotic innovations in the warehousing and manufacturing sectors. Tune in as the guests from JLC Robotics highlight their unique contributions to warehouse automation, featuring Thouzer, a robotic cart with an API, and CaPow, an innovative solution providing perpetual power to AMRs and AGVs. This episode is a treasure trove of insights for anyone interested in the intersection of robotics and warehouse management. JLC Robotics’ Unique AGV and AMR Solutions: Thouzer and Capow Callihan explains the company’s evolution from JLC Industrial to JLC Robotics, emphasizing their shift towards innovative solutions in robotics. Their products, such as Thouzer and CaPow, are designed to enhance efficiency in material handling and quality control in manufacturing, particularly in the automotive sector. Thouzer is a robotic cart designed for simplicity and efficiency in A to B movement. CaPow offers a perpetual power solution for mobile robots, aiming to reduce downtime due to charging. These products highlight JLC Robotics’ commitment to providing practical, user-friendly solutions to common challenges in warehouse operations. Deciphering the Difference Between an AGV and AMR Denton explains, “AGVs always follow a predefined fixed path and will not make independent decisions. On the other hand, AMRs, which are more intelligent, can reroute around obstructions, constantly finding the shortest path from A to B.” Denton highlights the current market trends and the future trajectory of these technologies. “There’s still double-digit demand growth for both AGVs and AMRs,” he states, acknowledging the ongoing relevance of both systems in the industry. However, he points out the increasing edge of AMRs, noting, “As the AMR software collectively gets better and better, the setup time will be less and less. The intelligence is going to grow and grow. They’re going to get smarter and smarter and require less setup, less programming, less maintenance.” The evolving capabilities of AMRs suggest a gradual shift in the industry’s preference towards these more autonomous and flexible solutions despite the sustained significance of AGVs in specific applications. The Challenges and Opportunities in the AGV and AMR Market Denton emphasizes the growing necessity of automation in warehouses, noting that nearly every facility they visit prominently advertises hiring needs. This trend underscores how companies increasingly turn to automation for efficiency and to meet production demands amid labor shortages. Tradeshows, in particular, provide an overwhelming number of choices available to customers, making it difficult to differentiate between robotic solutions. Denton emphasizes the need for custom solutions in a market flooded with options, shedding light on the importance of understanding specific client requirements and the AGV communication standard, VDA 5050. Key Takeaways Innovative Shift in Robotics: JLC Robotics’ transition from industrial solutions to cutting-edge robotics signifies a broader shift in warehouse automation towards more sophisticated and efficient technologies. Navigating Market Complexities: The discussion on the AMR and AGV market challenges sheds light on the importance of custom solutions and the need to understand varied customer requirements. Unique Product Offerings: Introducing products like Thouzer and CaPow illustrates JLC Robotics’ commitment to addressing specific operational challenges in warehousing through innovative technology. The New Warehouse Podcast EP 439: Innovative AGV and AMR Solutions from JLC Robotics
U.S. Rail Traffic for the week ending November 18, 2023
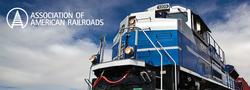
The Association of American Railroads (AAR) has reported U.S. rail traffic for the week ending November 18, 2023. For this week, total U.S. weekly rail traffic was 501,416 carloads and intermodal units, up 4.0 percent compared with the same week last year. Total carloads for the week ending November 18 were 237,416 carloads, up 3.8 percent compared with the same week in 2022, while U.S. weekly intermodal volume was 264,000 containers and trailers, up 4.1 percent compared to 2022. Seven of the 10 carload commodity groups posted an increase compared with the same week in 2022. They included coal, up 3,185 carloads, to 69,630; chemicals, up 2,519 carloads, to 32,295; and motor vehicles and parts, up 1,632 carloads, to 15,260. Commodity groups that posted decreases compared with the same week in 2022 were grain, down 475 carloads, to 24,483; miscellaneous carloads, down 442 carloads, to 7,588; and metallic ores and metals, down 68 carloads, to 20,837. For the first 46 weeks of 2023, U.S. railroads reported cumulative volume of 10,391,997 carloads, up 0.2 percent from the same point last year; and 11,193,010 intermodal units, down 6.5 percent from last year. Total combined U.S. traffic for the first 46 weeks of 2023 was 21,585,007 carloads and intermodal units, a decrease of 3.4 percent compared to last year. North American rail volume for the week ending November 18, 2023, on 12 reporting U.S., Canadian and Mexican railroads totaled 351,368 carloads, up 3.8 percent compared with the same week last year, and 343,001 intermodal units, up 1.7 percent compared with last year. Total combined weekly rail traffic in North America was 694,369 carloads and intermodal units, up 2.8 percent. North American rail volume for the first 46 weeks of 2023 was 30,221,325 carloads and intermodal units, down 3.1 percent compared with 2022. Canadian railroads reported 98,560 carloads for the week, up 3.7 percent, and 66,904 intermodal units, down 8.8 percent compared with the same week in 2022. For the first 46 weeks of 2023, Canadian railroads reported cumulative rail traffic volume of 7,340,071 carloads, containers and trailers, down 3.3 percent. Mexican railroads reported 15,392 carloads for the week, up 3.6 percent compared with the same week last year, and 12,097 intermodal units, up 17.8 percent. Cumulative volume on Mexican railroads for the first 46 weeks of 2023 was 1,296,247 carloads and intermodal containers and trailers, up 4.1 percent from the same point last year. To view the weekly traffic reports, click here.
You are a leader: Whether you know it or not. Whether you want to be one or not
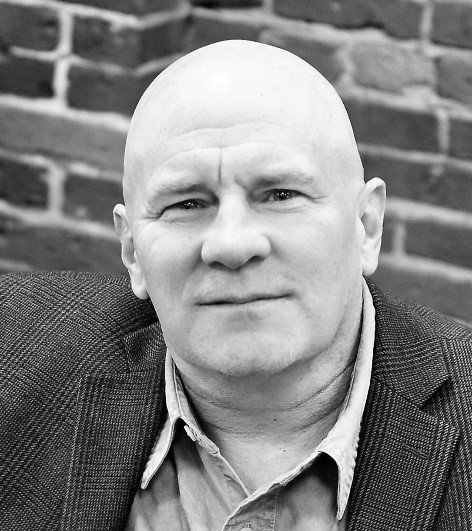
You inspire people–whether you know it or not. You empower people, sometimes even if you’re not trying to. You guide people–whether you want to or not. What is your definition of “leader?” Before you go any further, let’s see if you’re singing in harmony. If not––there’s no point in pursuing this venture any further. Here’s the definition adopted for this article. Let’s see if you fundamentally agree. A leader is simply someone with the ability to attract WILLING followers. And again, whether you know it or not or whether you’re willing or not, there are people who follow your lead of their own free will. The best leaders are people with the will to serve their followers and give them the tools they need to make their lives better. Something else we should make clear is that you need no specific number of followers to be a leader. You can lead one or you can lead millions. And you can change the world for the better or cause incredible damage by your influence on just one person. Leadership is a responsibility. And it’s a responsibility we all share. What defines us as leaders is whether or not we choose to accept or attempt to shirk our responsibility––and in which direction we decide to lead. Let’s dig a little deeper into the fundamentals. These are the Essential Disciplines of the Leader. Inspire… You touch other people’s hearts. Whether you know it or not and whether you want to or not. You can inspire love or fear. You can make someone’s heart or break it. If you’ve been on this planet for any significant time, you’ve probably done both. Empower… You give people tools. Again, whether you know it or want to, you share many things with people. One of the most important ways to empower others is to encourage them––and you do. The bigger question is what, exactly, are you encouraging others to do? Guide… You show the way. Through your words, your actions, and who you choose to take under your wing. It’s a fact. Someone looks to you for guidance––whether you know it or not, whether you choose to or not. Where are you guiding them? You are a leader. You might not be the boss. That’s the excuse heard most often by people who still hesitate or even refuse to accept that they are leaders. That excuse supports the toughest argument still faced when trying to change people’s minds about leadership. The plain fact is that some people cling to one or more of the following beliefs: Leaders are born––not made. Not everyone is cut out to be a leader. Everyone can’t be the leader. There are too many leaders and not enough followers. First of all, you might not be the boss. Leadership has nothing to do with rank, title or position of authority. It has to do with how you Inspire, Empower and Guide others. Everyone knows tremendous leaders who have no title or rank. These people usually have little power or authority in the traditional sense, but they have influence. They inspire, empower, and guide people—sometimes even those at the top. If you doubt that, watch “Undercover Boss” sometime. And of course, you all know people with incredible power and authority who just plain suck as leaders. you all know people who have the rank or the title but little or no respect, trust, or loyalty from the people “below” them. Let’s address some of those excuses: Leaders are born. In fact, everyone is a born leader. Many of the mental health issues faced are due to a significant degree of the real or perceived inability to influence others at any given time. If you don’t make a difference in other people’s lives, you do not feel healthy. Having said that––while everyone is born into this legacy of leadership, it takes a lot of work to be a good leader. And for the best leaders, this work never ends. The most effective leaders are those who accept that perfection is not a destination, but a never-ending process. The best of the best is obsessed with continual self-improvement as a leader and as a person. But “everyone can’t be the leader.” This one can get a little complicated. The traditional model of command and control is dead. It is now understood that the roles of leader and follower are not fixed positions, but rather dynamic roles. In the aforementioned self-directed teams, people flow back and forth in these roles seamlessly depending on the situation and the talents, skills, and experience needed to take charge or manage decisions at any given time. Everyone can’t be “the” leader. But anyone can be “the leader” in the right situation. Some will still say that there are too many leaders. Leaders are people who Inspire, Empower, and Guide others to their very best––people like you. We can never have enough. About the Author: Jim Bouchard is an internationally recognized speaker, Leadership Activist, and founder of The SENSEI LEADER Movement™. He’s the author of 8 leadership books, and hosts Walking The Walk, a podcast highlighting compassionate, engaged leaders from all areas of business, diverse cultures and experiences. Jim’s programs are an inspirational and interactive exploration into the importance of human-centric leadership. To bring Jim to your organization or event, visit www.ArmstrongSpeakers.com.
Lucas Systems and Carnegie Mellon University partner to solve Logistics Industry Packaging and Sustainability challenges

Distribution center technology provider, Lucas Systems, has announced its partnership with Carnegie Mellon University (CMU) on new research with potential significant environmental and commercial impact for the logistics industry. The research is focused on developing new and innovative ways to reduce distribution center and transportation waste by optimizing the way packing and packaging of multiple items in a single order is executed. The outcome of the research work could contribute to significant environmental and commercial impact for thousands of companies in the logistics industry. Worldwide consumption of paper and cardboard has grown steadily over the past 60 years by about 7% year over year, according to a March 2023 report by Statista. Lucas Systems points out that this is five times more paper and cardboard than in 1960. As part of the project, master’s level students in CMU’s Software and Societal Systems Department (S3D) in the School of Computer Science will use 3D visualization frameworks, mobile application development, Core CS and Web/Angular/JS environments and work with Lucas Systems’ data scientists and software engineers on the architecture, user interfaces, and optimization best suited for solving end of supply chain distribution challenges. The joint project will contribute to Lucas Systems’ ongoing development of smart software to help warehouse workers pick products to fulfill an order in the most eco-friendly and financially efficient way. “The entire distribution industry has numerous opportunities to reduce waste and improve sustainability,” says Lucas Systems CTO Mark McCleary. “Consumers already recognize the increased amount of material they throw away with each shipment they receive. Consumers are paying for a lot of that waste – and so is our environment.” Over 90% of items shipped in the U.S. are packaged in cardboard. Lucas Systems’ work with CMU could mean a very large potential economic impact for the distribution industry. Lucas Systems leaders say the solutions to these types of problems are incredibly complex and must lean on a variety of modern technologies and know-how for help. “CMU and S3D are excited to work with Lucas Systems on this critical challenge. Improving the sustainability of packaging using the latest technologies is an area that we’re excited to contribute to,” said Travis Breaux, director of the Master of Software Engineering programs and associate professor of computer science.
AIT Worldwide Logistics plans to increase global footprint with Lubbers Logistics Group acquisition
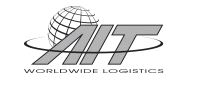
Strategic deal will position AIT as key player in European road transport, energy sectors AIT Worldwide Logistics has entered into a binding purchase agreement to acquire Lubbers Logistics Group, a European logistics company specializing in high-value, complex, and time-sensitive transport services. The purchase will serve as a significant milestone for AIT as the company continues to expand its global reach and enhance its offerings in road transportation, freight forwarding, and project cargo logistics, particularly in the energy sector. Over the past century, Lubbers, headquartered in Schoonebeek, Netherlands, has established itself as a leading provider of top-tier transportation solutions for high-value segments, specializing in road transport, project cargo and global freight forwarding services. With more than 377 employees working across nine road transport hubs and nine freight locations, Lubbers boasts an extensive network of strategically located facilities throughout Europe. “Lubbers’ robust one-stop shop approach and their long-standing relationships with industry-leading customers make them an excellent fit for AIT,” said AIT’s Chief Business Officer, Greg Weigel. “We see significant potential for their broad network by growing freight forwarding operations and energy sector expertise to further enhance AIT’s world-class customer experience. We’re also excited to boost our end-to-end solutions with middle mile service in Europe as a counterpart to our recently launched U.S. Middle Mile Network.” Lubbers’ network will add 18 new offices to AIT’s existing global network of more than 125 locations, while expanding AIT’s footprint to four new countries: Denmark, Norway, Romania and Turkey. Lubbers also has facilities in Germany, Italy and the United Kingdom. “Joining forces with AIT Worldwide Logistics is a strategic move that will allow us to continue providing exceptional service to our clients while expanding our reach on a global scale,” said Lubbers’ CEO, Gary Roche. “AIT’s strong track record and commitment to customer service align with our values, and we look forward to a bright future together.” “We are looking forward to welcoming Lubbers to the AIT network,” said AIT’s Chairman and CEO, Vaughn Moore. “This deal will enhance our position in Europe and bolster our presence in the energy sector, allowing us to better serve current customers while creating new opportunities. Lubbers’ customer-centric approach to business, as well as their reputation for excellent quality aligns perfectly with AIT’s culture.” AIT’s acquisition of Lubbers is expected to be finalized by the end of 2023 and will be subject to obtaining customary regulatory approvals. Terms have not been disclosed. Kirkland & Ellis LLP and NautaDutilh N.V. are both serving as legal counsel to AIT on the acquisition. Nielen Schuman B.V. is serving as the financial advisor to Lubbers. Loyens & Loeff N.V. is serving as legal counsel to Lubbers.
Pat O’Connor announces retirement from Columbia Machine Palletizer Division
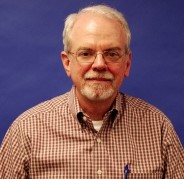
Columbia Machine, Inc has announced the retirement of Pat O’Connor after more than 12 years of distinguished service. Pat joined Columbia in August 2011 as the Business Development Manager for the Palletizer Division before being promoted to the role of President in 2014. Pat has spent his entire career in the conveyor, palletizing and material handling industry. Under Pat’s leadership, Columbia’s Palletizer Division has shown sustained growth, developing the broadest and most advanced palletizer product line in the industry. With more than 40 years of experience in engineering, sales, and product development, Pat’s expertise has been vital in solidifying our position as the market leader in North America. “We are grateful for Pat’s exceptional contributions,” said Rick Goode, Chairman and CEO of Columbia Machine, Inc. “His profound knowledge and extensive experience have played a pivotal role in the transformation and advancement of Columbia’s entire palletizer product line. Pat’s visionary leadership has culminated in the formation of an exceptional team, and his unwavering dedication to our customers, our company, and the industry at large will undoubtedly leave a lasting legacy for generations to come.” “As we approach this transition, we are pleased to announce that Mark MacDonald will take over the role of President of our Palletizer Division.” said Goode. Mark began his career at Columbia in January 2015 as the Applications Engineering Manager and has built a team highly qualified Engineers. Mark has a Mechanical Engineering Degree from the University of Missouri School of Science and Technology and an MBA from St. Louis University. Prior to joining Columbia, Mark has previously held positions as an Applications Engineer (in the Palletizer industry), Sourcing Commodities Manager at GKN Aerospace and Purchasing Manager at Duke Manufacturing. A planned leadership transition has already begun with Pat and will continue over the next few months. “Please join me in thanking Pat for his years of committed service and wishing him all the best in his retirement. Let us also extend a welcome to Mark as he steps into his new role.” added Goode.
NFI’s Brian Webb promoted to President of Port Services Division
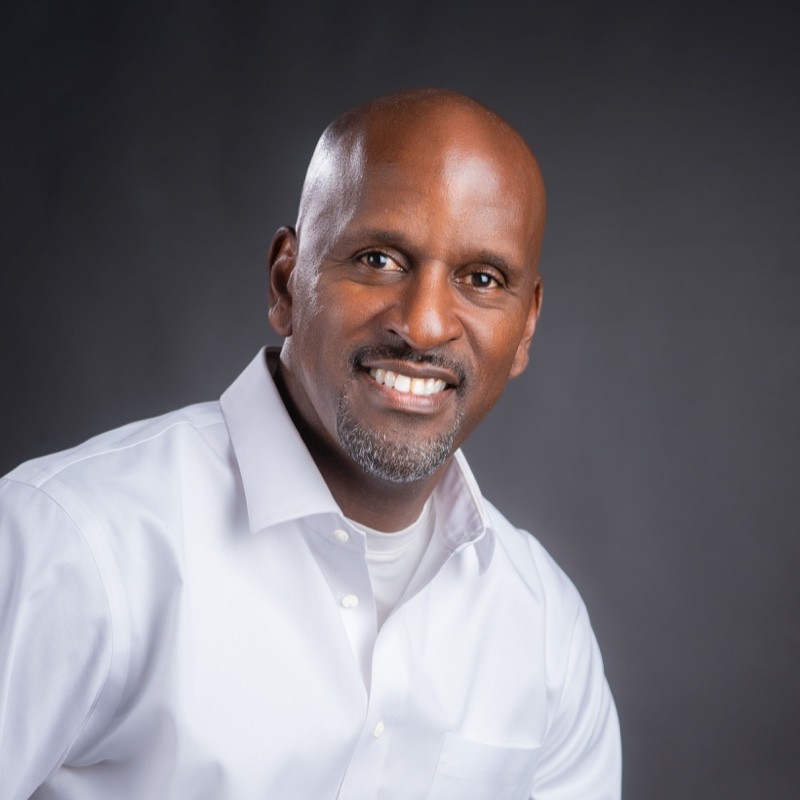
NFI hasrecently announced the promotion of Brian Webb to President of its Port Services solution. With nearly 30 years in the supply chain industry, Brian brings a wealth of experience to support this growing division. “Since the acquisition of Cal Cartage in 2017, NFI has grown tremendously in its Port Services offering,” said NFI CEO Sid Brown. “Brian’s experience leading NFI’s largest region within Distribution and his commitment to operational excellence will be instrumental to the Port Services team as they continue their expansion and growth.” During his career at NFI, Brian brought to his role a history of launching multiple high-volume, dynamic warehouse and distribution facilities across the country. His thorough understanding of the supply chain needs of Fortune 100 companies will bring added value and a fresh perspective to the team. His international experience, navigation of complex supply chains, and distinct track record of creating high-performing teams will pave the way for leading the Port Services team to continued innovation and expansion. Brian was a Sergeant in the US Air Force and transitioned into a role in warehouse operations with DHL. Since joining NFI in 2016, Brian has grown his career to his most recent role of Senior Vice President of the West region, where he was responsible for 26+ million square feet of warehouse space. He also contributes as a Supply Chain Course Instructor at Chaffey College in Rancho Cucamonga, California. From its acquisition of California Cartage to the recent opening of its one-of-a-kind transload facility in the Port of Savannah, NFI’s Port Services division has emerged as a leader in drayage and transloading services across North America. Having proximity to ports and a presence in most major logistics hubs continentally allows the company to connect its customers’ international shipments to their domestic supply chain. NFI’s port service experts have the knowledge to help customers quickly move their products and simplify the shipping process from origin to destination.
What IS NOT strategy and What IS
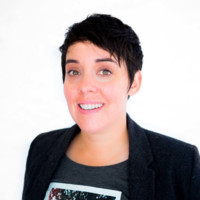
Recruit and retain top talent. Increase market share. Improve customer satisfaction. Expand into new geographic markets. Diversity product offerings. Reduce operating costs. Improve employee satisfaction. Develop and launch new technologies. Improve supply chain management. Increase revenue and profitability. Implement sustainability practices. Improve efficiency and productivity. Develop and maintain strong partnerships. Enhance product quality and reliability. Increase innovation and creativity. Strengthen organizational culture. Build a talent pipeline. Improve the customer experience. Expand into new product categories. Invest in research and development. These are not strategies. These are goals. A goal is what a company wants to accomplish. A strategy is the UNIQUE and DISTINCT WAY by which the goal is achieved. If, as a leader, you don’t design and effectively articulate the strategy by which you’ll achieve those goals, you’ll never reach them. If, as a leader, you throw them over the fence to your leadership team and let them “figure it out, but with the freedom to fail,” you’ll still never reach them. “Human resources will hire five new members of the sales team by the end of September.” is also not a strategy. “The sales manager will be on proposal calls to secure five in-person meetings with prospects by Thanksgiving.” is also not a strategy. “Increase the size of our sales staff.” is also not a strategy. A STRATEGY is much bigger, deeper, and broader. It is core to who you are as an organization. Whether you want to grow, stabilize, retrench, or reinvent, it should easily adapt. It’s your unique value proposition. It’s your unique position. It’s your distinct competitive advantage. That’s it. About the Author Andrea Belk Olson is a keynote speaker, author, differentiation strategist, behavioral scientist, and customer-centricity expert.As the CEO of Pragmadik, she helps organizations of all sizes, from small businesses to Fortune 500, and has served as an outside consultant for EY and McKinsey. Andrea is the author of three books, including her most recent, What To Ask: How To Learn What Customers Need but Don’t Tell You, released in June 2022. She is a 4-time ADDY® award winner and host of the popular Customer Mission podcast. Her thoughts have been continually featured in news sources such as Chief Executive Magazine, Entrepreneur Magazine, Harvard Business Review, Rotman Magazine, World Economic Forum, and more. Andrea is a sought-after speaker at conferences and corporate events throughout the world. She is a visiting lecturer and startup coach at the University of Iowa, a TEDx presenter, and TEDx speaker coach. She is also an instructor at the University of Iowa Venture School. More information is also available on www.pragmadik.com and www.andreabelkolson.com.
20th Annual Cat® Lift Trucks Scholarship Program now open: Mitsubishi Logisnext Americas continues its legacy of educational support in Houston

Houston-based Mitsubishi Logisnext Americas is now accepting applications for its 20th Annual Cat® Lift Trucks Scholarship Program. This long-standing initiative continues its tradition of recognizing an exceptional Houston-area high-school senior interested in pursuing a four-year degree related to the material handling industry. The chosen recipient will be awarded a $5,000 scholarship to support their pursuit of higher education. “Innovation and education are the cornerstones of progress in our industry, and we’re thrilled to celebrate the 2oth anniversary of our Cat Lift Trucks Scholarship Program,” said Ken Barina, president of Mitsubishi Logisnext Americas. “By championing the ambitions of young talent, we are investing in the future of material handling, automation and fleet solutions and helping shape the landscape of our industry.” A Legacy of Support Since its launch in 2005, the Cat Lift Trucks Scholarship Program has awarded a cumulative $140,000 in educational assistance to 27 outstanding students from the Greater Houston area. Past recipients have gone on to enroll in prestigious Texas universities and colleges, including Texas A&M University, The University of Texas at Austin and Texas State Technical College, pursuing degrees in diverse fields, such as mechanical and chemical engineering, welding technology and entrepreneurship. Selection criteria include academic performance, community service involvement, leadership abilities and financial need. Honoring Texas Tradition As the Official Lift Truck Provider of the Houston Livestock Show and Rodeo™ (HLSR), Cat Lift Trucks will announce the winner of the 2024 scholarship during the annual HLSR event, scheduled to take place from February 27 to March 17, 2024, in Houston. “Each year, we witness remarkable academic achievements and a deep dedication to community service among our scholarship applicants,” said Jerry Sytsma, executive vice president, Sales and Aftermarket, at Mitsubishi Logisnext Americas. “Their dedication fuels our commitment to nurture the industry’s future leaders as we celebrate two decades of this program.” How to Apply Applications for the 2024 Cat Lift Trucks scholarship must be submitted online by 11:59 p.m. CST on January 31, 2024. Applicants must be from a Houston-area school district and plan to enroll in a college, university, or technical school in Texas focusing on engineering or a business-oriented or technical trade field related to the material handling industry. For more information on this year’s scholarship program and requirements, or to apply, visit https://www.logisnextamericas.com/en/cat/cat-lift-trucks-scholarship.