KION Group and Eurofork sign strategic partnership
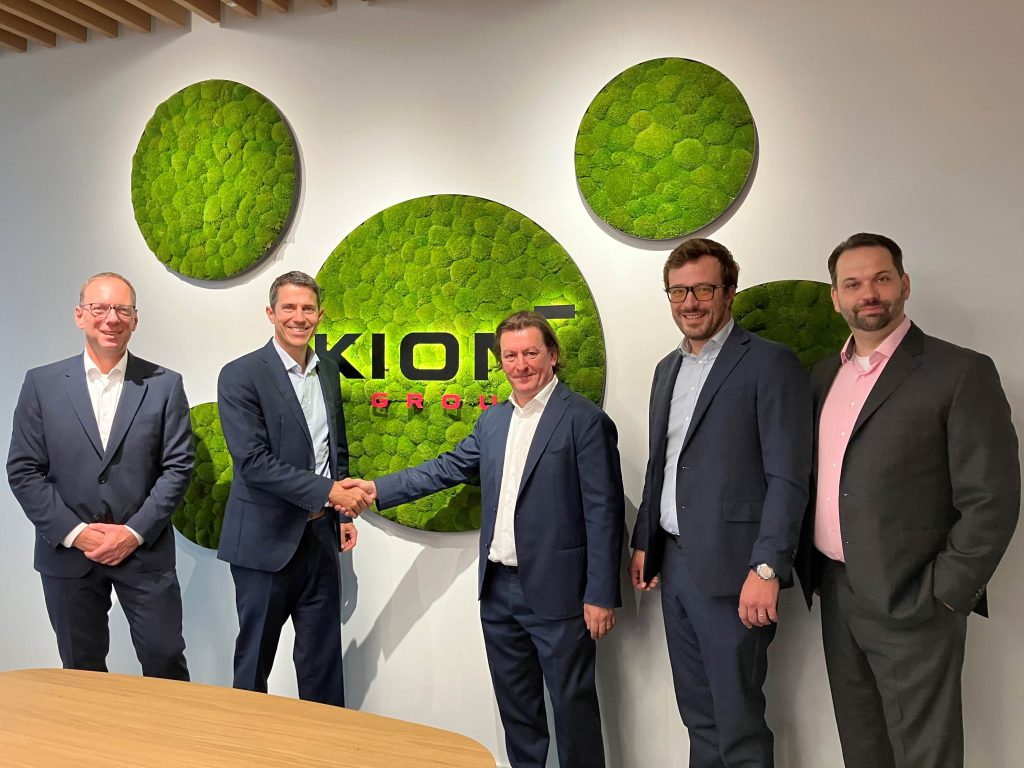
KION Group has signed a cooperation agreement with a manufacturer of pallet shuttle systems, Eurofork, in Frankfurt am Main, Germany Eurofork solution E4CUBE® to be distributed through KION Group’s sales networks Andreas Schneider, SVP of Product Management at KION: “With this partnership, we are strengthening our product portfolio in the area of automated solutions” Maurizio Traversa, CEO of Eurofork: “Our partnership will open opportunities for numerous companies to leverage the latest automation technology with our pallet shuttle solution E4CUBE® The KION Group has entered into a strategic partnership with Eurofork S.p.A., a manufacturer of pallet shuttle systems. The two companies have signed a cooperation agreement at KION GROUP AG headquarters in Frankfurt am Main, Germany. Under the agreement, Eurofork’s E4CUBE® solution will be distributed through the sales and service networks of the KION brands in the Industrial Trucks & Services segment in the EMEA region with immediate effect. Andreas Schneider, Senior Vice President of Product Management at KION, said: “We are very pleased to enter this strategic partnership with Eurofork, one of the leading players in the market for pallet shuttles. This will enable us to offer our customers an even more comprehensive product portfolio of automated solutions and further strengthen our position.” Pallet shuttle systems are an efficient form of storage with high flexibility, continuous material flow, and high throughput rates. Automated shuttles travel independently on rail systems through the racks and transport palletized goods to the picking station. E4CUBE® can be easily configured with standard modules for individual customer solutions and is operational within a few months. In addition, the system ensures the traceability of goods and offers high operational safety. Maurizio Traversa, CEO of Eurofork, said: “We are proud to enter this strategic partnership agreement, which marks a new high of our long-standing cooperation with the KION Group. Our pallet shuttle automation adds substantial value for customers and having KION teaming up with us for the distribution of the E4CUBE® will enable access to easy automation for a wide array of companies. This solution delivers value without unnecessary complexity, including from a financial perspective, thanks to our partner’s leasing solutions.” Eurofork was founded in 2000 in Roletto near Turin, Northwest Italy. The company specializes in producing material handling devices such as pallet shuttle systems and telescopic forks made in Italy. Eurofork products and solutions are used worldwide in industrial automation and intralogistics thanks to their quality and efficiency.
EasyHeat Snow Melt System prevents dangerous ice dams and icicle formations on roofs
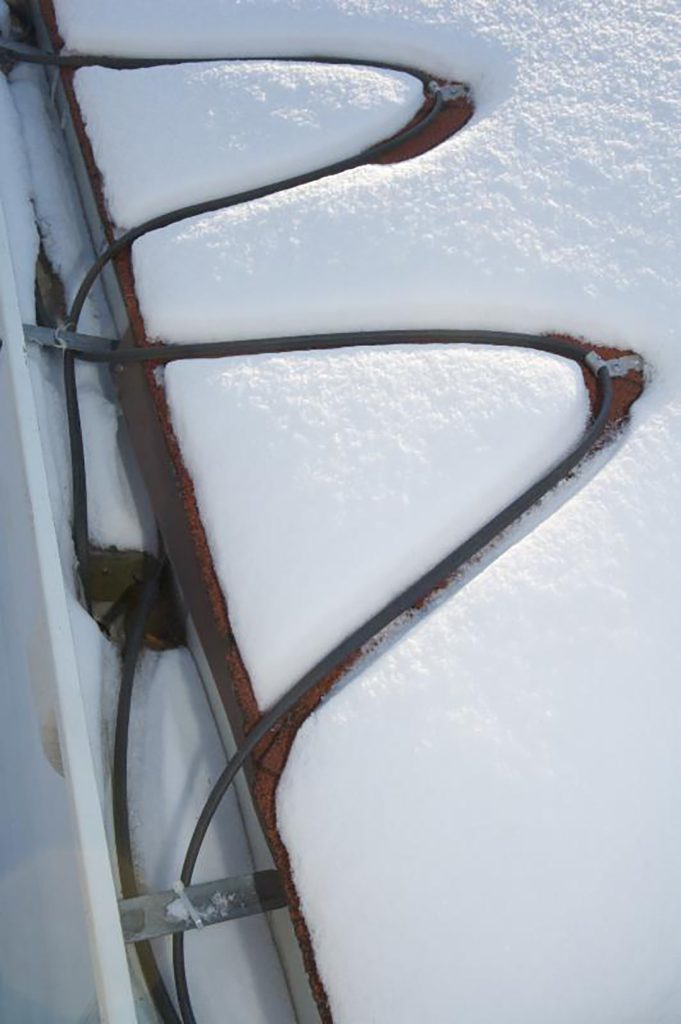
Although winter weather evokes images of warm fires, icy wonderlands, and snowball fights, it can also be highly destructive to roofs. Ice accumulation on the edge of roofs, also known as ice dams, can create a blizzard of problems for property owners, from minor inconveniences to severe structural damages. If left untreated, water from melting ice migrates and accumulates, which can cause leaks, mold growth, structural damage, and, in extreme cases, total roof collapse. The melted water then refreezes as temperatures drop, restarting the cycle again. EasyHeat, an Emerson brand, is helping building owners avoid costly problems with its RG Trace Cable De-Icing System. Simple and inexpensive, the RG Trace Cable De-Icing System includes everything necessary for a complete, hassle-free installation: Cut-to-length RG Trace heating cables, delivering 12 watts per foot output needed to accommodate larger commercial gutters and downspouts; EasyHeat Controls to sense both moisture and temperature, optimizing power consumption; Downspout hangers, power connection kits, and end-seals are necessary to complete the system safely. Being self-regulating, EasyHeat RG Trace Cables automatically varies its heat output as temperature changes. The cable’s outer jacket is both waterproof and UV resistant to withstand harsh weather conditions for years, while a tinned copper braid installed over two protective inner jackets provides a continuous ground path. EasyHeat RG Trace Cable De-Icing System is available on reels up to 1,000 feet for cut-to-length convenience in the field. It is suitable for use on asphalt or wood shingles, metal roofing, synthetic rubber, thermoplastic, modified bitumen (“membrane”), and virtually every other type of roofing material. AVOID REPAIR COSTS Repairing a roof is expensive. Even a minor repair typically costs several thousand dollars. Larger repairs or work on membrane, slate, or metal roofs run exponentially higher. Industry estimates put roof replacement on a 10,000-square-foot commercial building at approximately $70,000. By safeguarding the roof line, gutter, and downspouts of buildings from damaging ice and snow accumulation, the EasyHeat RG Trace Cable De-Icing System is an investment that pays dividends every winter, year after year. ICICLE DANGERS As if ice dams aren’t enough to deal with in the winter, another danger often hangs over our heads: large icicles can fall from multi-story buildings, causing lacerations, broken bones, head trauma, or worse. Icicles have also been known to shatter the windows of cars parked nearby when they’ve broken free. Icicles are visual evidence of ice dam formation and are the primary cause of leaky and overloaded roofs. EasyHeat RG Trace Cable Systems prevent icicles from forming, providing protection to property and people. EasyHeat RG Trace Cables are UL and CSA-approved for roof application to existing structures and new construction.
Hyster receives green award for demanding industrial materials handling applications
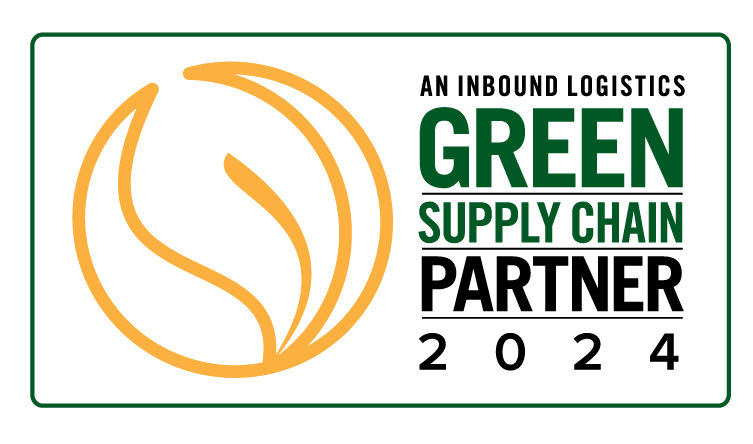
Hyster Company announces its selection as a 2024 Green Supply Chain Partner by Inbound Logistics magazine. The award honors Hyster for innovating clean power solutions that are helping to electrify materials handling applications in industries that have traditionally only been powered by internal combustion engines (ICE), providing the opportunity for those businesses to maintain high productivity levels while supporting sustainability initiatives from governments and corporations alike. Among the company’s most notable innovations in this space are a hydrogen fuel cell-powered (HFC) ReachStacker currently being piloted at the Port of Valencia in Spain, battery-powered terminal tractors that will be shipped to the Port of Mobile, Alabama, and the world’s first HFC-powered top-pick container handler, currently engaged in a pilot program at the Port of Los Angeles, California. The company will also ship an HFC-powered empty container handler and terminal tractor to Hamburg, Germany. In developing these solutions, Hyster draws on a wealth of experience in electric forklift design from the company’s line of smaller, lighter-capacity equipment, for which Hyster offers extensive electric power options. The lineup includes forklifts powered by lead-acid batteries and those with factory-integrated lithium-ion battery packs, enabling ergonomic advantages that help increase operator productivity while providing operations with several power-related benefits. Among these benefits are fast charging times, zero emissions, and productivity comparable to ICE equipment. This is the fifth year Hyster has been recognized as a Green Supply Chain Partner. The company’s HFC-powered ReachStacker was also recently recognized with a BIG Sustainability Product of the Year Award, a Green GOOD DESIGN Award, and an innovation to watch by the Global Good Awards. The HFC-powered top-pick container handler was also named a finalist in the 2023 Fast Company Innovation by Design Awards. “As companies and government bodies grapple with the need to limit carbon emissions, the pursuit of sustainability and clean power in materials handling is becoming less of an option and more of a requirement,” says Lucien Robroek, president of Global Technology Solutions, Hyster Company. “As businesses navigate the growing need for a shift to electric equipment, we’re expanding our green options to include operations where electrification has not previously been possible and are continuing to help customers find the right power solution for their particular application.”
Bobcat introduces the premium and feature-rich TL623 Telehandler
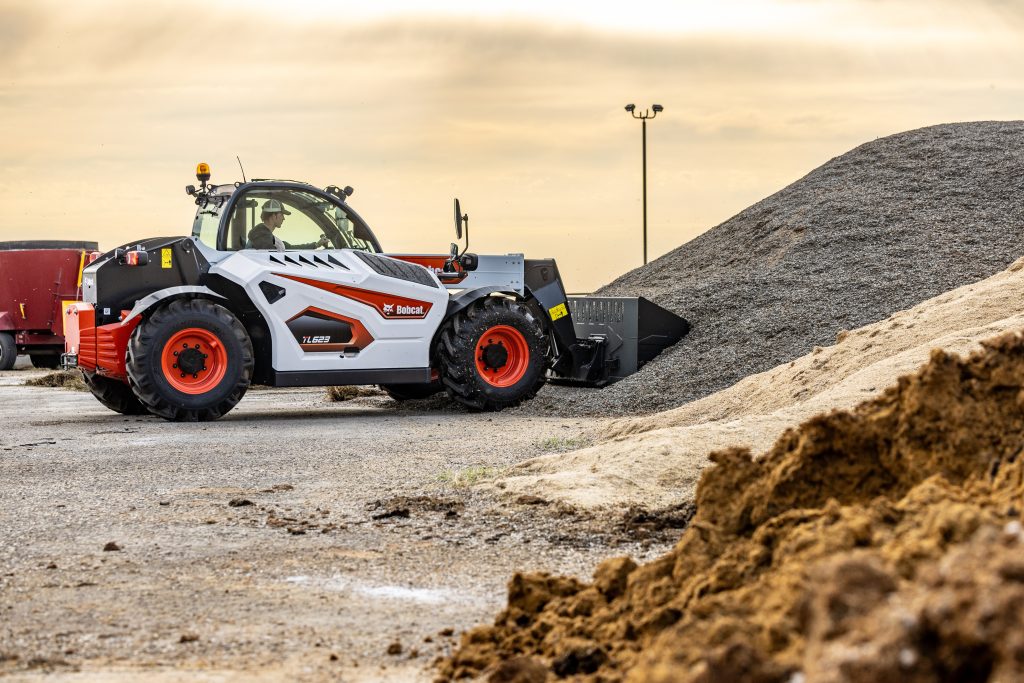
Bobcat Company, a global brand of compact equipment, innovation, and worksite solutions, introduces its all-new TL623 telehandler. This telescopic tool carrier is loaded with premium performance and comfort features not found on other standard-equipped telehandlers. The TL623 offers the extended reach and superior lift capacity of a heavy-duty telescoping boom combined with Bobcat’s leading multi-attachment versatility, enabling operators to tackle a wide range of jobs with one machine. Reach high and stack, then quickly change attachments to take the TL623 telehandler’s productivity beyond pick-and-place tasks. “The TL623 gives operators the flexibility to accomplish a variety of demanding tasks with superior precision and efficiency,” said Jamison Wood, Bobcat product development specialist. “It’s ideal for agriculture, construction, landscaping, snow removal, and many other applications that require a high-performing and versatile tool carrier.” Exceptional Performance The TL623 has a lift capacity of 6,000 pounds and a lift height of 23 feet, ensuring exceptional power and productivity during every demanding lift cycle. The advanced Tier 4 turbo-charged engine delivers powerful, high-torque performance, excellent efficiency, and emissions compliance without the use of a diesel particulate filter (DPF) or selective catalyst reduction (SCR). Operators will also appreciate the engine’s reliable cold-weather starting and a variety of features that make maintenance and service more convenient. Five operation modes give operators the versatility needed for a wide variety of applications: ECO mode allows operators to maintain hydraulic performance without using the engine’s full power, working at lower rpm, less noise, and lower fuel consumption. Smooth drive mode is ideal for maneuvering across job sites with mild acceleration and deceleration while carrying loads. Dynamic drive mode increases the responsiveness of the telehandler’s acceleration and deceleration for traveling between tasks. Flex drive mode allows the operator to manage the engine speed independently from travel speed. Advanced attachment control mode allows for full auxiliary hydraulic performance. More Standard, Performance-Boosting Features The TL623 has performance and comfort features designed to increase operators’ productivity. Along with the five operation modes, this workhorse also comes standard with the following performance-enhancing features: Four steering modes for application-matched maneuverability The Bobcat Smart Handling System for tailored boom movements via controls on the joystick Power Bob-Tach® mounting system for quick and easy attachment changes A spacious, high-visibility cab with an efficient HVAC system, an easy-to-read control panel, simple and intuitive controls, an air-suspension seat, and an LCD screen that provides full-featured machine interaction and monitoring capabilities Automatic Ride Control for reduced material spillage and faster travel speeds 7-Pin Attachment Control Device (ACD) for additional control and functionality in select attachments Outstanding Comfort and Operability The cab builds upon the Bobcat tradition of operator-centered design. It comes standard with high visibility, excellent ergonomics, a comfortable air suspension seat, an efficient HVAC system, and an easy-to-read 5-inch LCD display panel. Bobcat telehandler cabs are designed and tested to Roll-Over Protection Structure (ROPS) and Falling Object Protective Structure (FOPS) level II standards. A single, intuitive joystick controls the travel direction, lift and tilt functions, boom extension, and auxiliary hydraulics. This gives the operator fine adjustment for lifting loads with care. It also allows operators to manage several machine functions simultaneously, enabling more precise control and higher productivity without removing their hands from the joystick. Fingertip control access makes operation smooth, comfortable, and easy. The directional switch for forward, neutral, and reverse can be operated with the index finger on the front side of the joystick. The 2-speed travel switch, lift-arm float, boom extension, machine function settings, and auxiliary hydraulics are located on the rear of the joystick. The low-profile boom sits below the operator’s eye level to provide an open view of the surroundings. Front, top, and rear window wipers help keep windows free of debris and precipitation. Mirrors on the operator’s left and right provide added visibility when working in confined areas. An optional rear mirror, rearview camera, and boom work light kit are also available. Unbeatable Uptime, Serviceability, and Versatility The TL623 is built with a robust box-welded frame for enhanced rigidity and a low center of gravity for optimal stability. The shielded bottom plate protects vital components, while the engine, cooling system, and critical components are well-protected within the center of the chassis, ensuring minimal wear and tear due to job site obstacles or harsh terrain. Engine compartment accessibility puts routine maintenance checks, filters, and other engine components, as well as the oil filter and other service points, within easy reach. The Bob-Tach mounting system allows operators to share select attachments with other Bobcat equipment for even greater versatility. From pallet forks and buckets to grapples and snowblowers, operators can conquer a variety of tasks without the need for specialty attachments. The TL623 will be available at Bobcat dealerships across North America in Q4 2024. To find a local dealer, visit bobcat.com/dealer.
Hy-Brid Lifts announces Director of Sales for Western United States
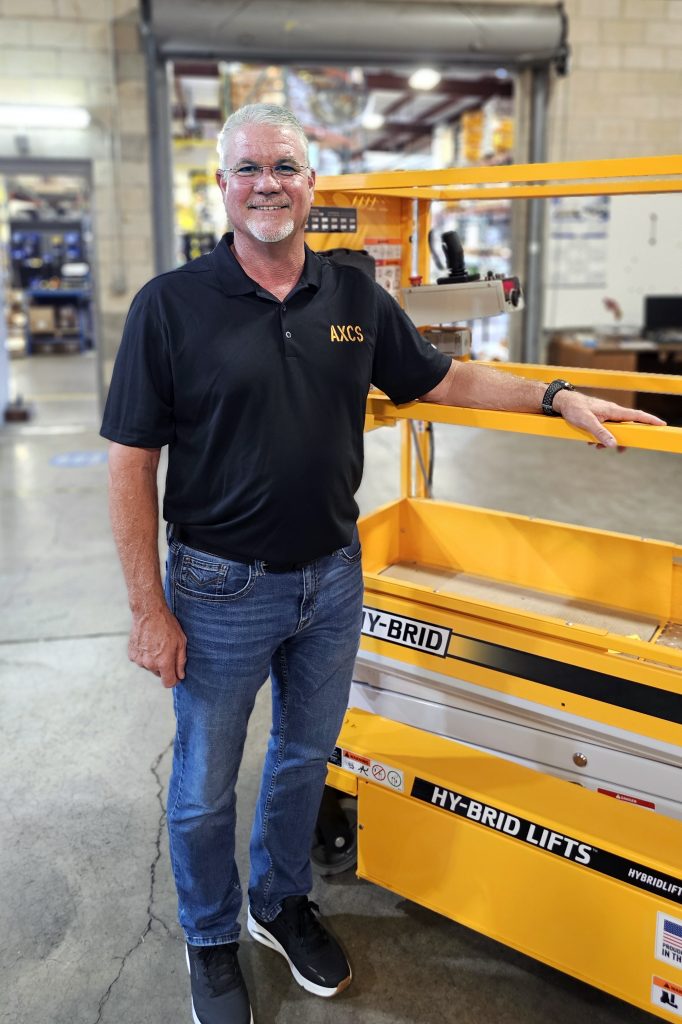
Hy-Brid Lifts announced that Charlie Haskin will be the director of sales covering the western United States. Haskin’s responsibilities include providing customer support as well as continuing the growth and channel development of the Hy-Brid Lifts line of low-level scissor lifts. “I’m excited to join this team and to be part of the growth for the Western Region by building upon my existing customers and boosting new relationships,” Haskin said. “After visiting our manufacturing facility in Wisconsin, I’m confident in the quality of our equipment and solid support of our service and leadership teams. With over 20 years of experience split in equipment manufacturing sales and general rental, I understand the importance of quality and support for our customers. Along with the new product launching in 2025, I have no doubt in our success for the future.” Haskin brings 20 years of industry knowledge and experience to his new role, primarily derived from his time in equipment sales, dealerships, and the equipment rental industry. During his time in these sectors, he strongly emphasized customer relationships. “We’re thrilled to welcome Charlie to the Hy-Brid Lifts team as he takes on the western United States region. His extensive knowledge in sales and the rental industry will enhance our ability to serve our customers,” said Eric Liner, CEO of Custom Equipment LLC. “Charlie Haskins is a great addition, and we’re excited about the valuable contributions he will make toward our company’s continued growth.”
Episode 526: AI in Warehouse Management with Chat WMS
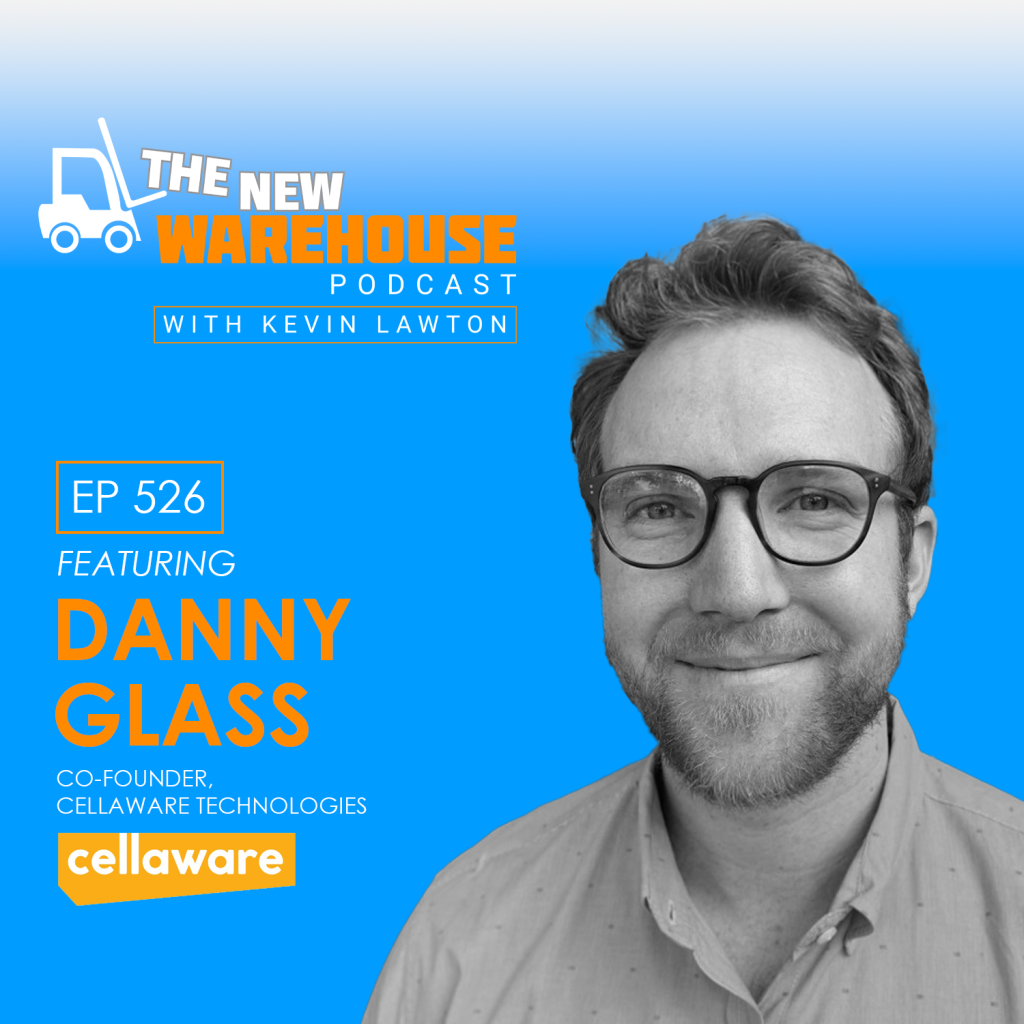
In this episode of The New Warehouse Podcast, Danny Glass, co-founder of Cellaware Technologies, explores the innovative ways artificial intelligence (AI) is applied to warehouse management systems (WMS). Danny shares his background in logistics and systems and how his experience led to the development of ChatWMS. This natural language interface allows users to interact with their warehouse management systems using AI. They dive deep into the practical use of AI in streamlining operations and the challenges of AI adoption in the warehousing industry. From Operations to AI: The Birth of ChatWMS Danny’s journey into AI and warehouse management started with his early career at DHL. His operational experience and passion for systems led him to co-found Cellaware Technologies. He recalls, “We decided that we wanted to found Cellaware Technologies with the primary aim of applying artificial intelligence in the supply chain and specifically in the warehouse in a practical way.” The breakthrough came in 2023 when AI, particularly ChatGPT, became mainstream, inspiring the creation of ChatWMS, a system designed to enhance WMS through natural language processing. AI’s Role in Improving Warehouse Efficiency ChatWMS takes AI further by enabling users to interact with their WMS through a simple chat interface. Danny explains, “Using the latest large language model capabilities and technology, you can effectively converse with your warehouse management system in the most comfortable way to derive insights from it. In my experience in operations, there’s a lot of value in that because I know how much smarter I became with respect to my operation when I could interact with the data at that level.” This innovative approach allows managers to access critical data without relying on pre-built reports or complex SQL queries. ChatWMS empowers managers to make informed decisions quickly by simplifying data extraction, enhancing operational efficiency, and reducing errors. Challenges of AI Adoption in Warehousing Despite the benefits of AI, adoption in the warehouse industry has been slow. “There’s a lot of hype around AI,” Danny notes, but actual implementation has lagged. Many companies are cautious about the disruption AI could cause to daily operations. The key, Danny emphasizes, is making AI solutions “minimally invasive” and ensuring that they integrate seamlessly with existing systems. ChatWMS, for instance, works with any WMS that stores its data in a relational database management system, making it adaptable and easy to implement. Key Takeaways on AI in Warehouse Management ChatWMS enables natural language interaction with warehouse management systems. AI adoption in warehousing is slow due to concerns about disruption, but tools like ChatWMS offer minimal implementation risks. Danny Glass highlights the importance of making AI solutions practical and adaptable for real-world warehouse environments. The New Warehouse Podcast Episode 526: Leveraging AI in Warehouse Management with Chat WMS
ALAN HURRICANE MILTON SITUATIONAL REPORT: Sunday, October 6, 2024
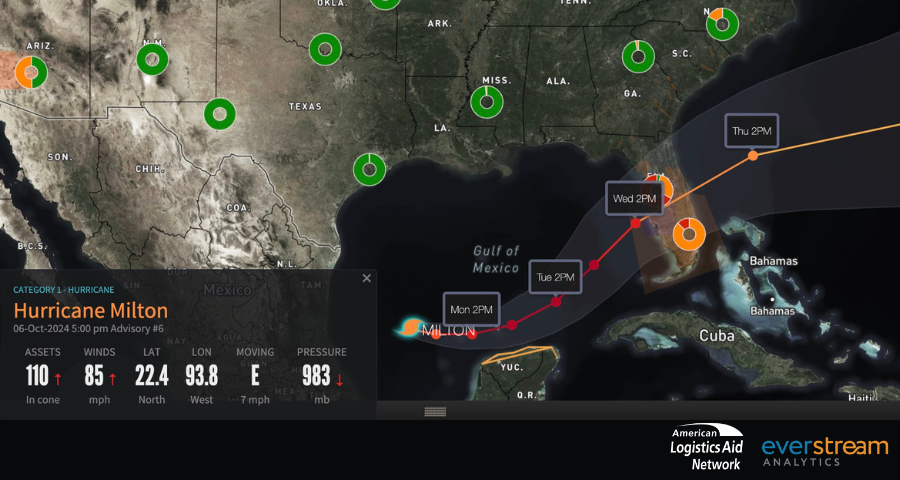
American Logistics Aid Network is mobilized for Hurricane Milton. As part of our response efforts, we are committed to providing you with the latest information and updates on supply chain impacts via our periodic Situation Reports, which can be found below in this email and on our website. ALAN has been improving logistics response to disasters for 19 years, and the need is greater now than ever. Please donate today to help us continue our work for many more years to come. ACTIVATION UPDATE ALAN is monitoring the National Hurricane Center forecast for Hurricane Milton and stands ready to support our members and partners if needed. As of Sunday, October 6, at 5 pm EDT, Hurricane Milton is forecast to quickly intensify while moving eastward to northeastward across the Gulf of Mexico. It will be a major hurricane when it reaches the west coast of the Florida Peninsula mid-week. “In an ideal world, we’d have plenty of time to focus all of our efforts on Hurricane Helene clean-up and recovery,” said Kathy Fulton, ALAN’s Executive Director. “But in the real world, major hurricanes don’t always wait for their turn. As a result, we are officially activating for Hurricane Milton.” While it is too soon to specify the exact magnitude and location of the greatest impacts, portions of the west coast of the Florida Peninsula, beginning Tuesday night or early Wednesday, face an increasing risk of life-threatening storm surge and damaging winds. Areas of heavy rainfall will impact portions of Florida Sunday and Monday ahead of Milton, with heavy rainfall more directly related to the system expected later on Tuesday through Wednesday night. For more information on evacuation zones in Florida, go to Know Your Zone Map. No evacuations have been ordered as of Sunday, October 6, 2024. STATE EMERGENCY DECLARATIONS Florida Governor DeSantis issued Executive Order 24-215 on October 6, 2024, amending Executive Order 24-214. Florida Governor DeSantis issued Executive Order 24-214 on October 5, 2024, in preparation for Tropical Storm Milton’s impact on Florida. ACTIVE TRANSPORTATION WAIVERS Title: FMCSA Regional Emergency Declaration No. 2024-008 and Extension of Emergency Declarations Pursuant to 49 CFR 390.23 and 390.24 Effective: 10/04/24 | Expires on: 10/27/24 Description: The United States Department of Transportation (USDOT), Federal Motor Carrier Safety Administration (FMCSA) declares that an emergency exists that warrants the issuance of a Regional Emergency Declaration and extension of emergency declarations issued by State Governors to continue emergency relief granted from certain regulatory requirements in Parts 390-399 of the Federal Motor Carrier Safety Regulations (FMCSRs). This Declaration is in response to Hurricane Helene and its effects on people and property, including immediate threats to human life, public safety, and public welfare from heavy rains, strong winds, storm surge, high surf, and flooding. This Declaration addresses the emergency conditions creating a need for immediate transportation relating to restoring essential supplies and services and providing necessary relief. Affected States included in this Declaration are Alabama, Florida, Georgia, North Carolina, South Carolina, Tennessee, Virginia, and West Virginia. The Presidential Declarations issued provide regulatory relief for up to 30 days of emergency relief from Federal regulations in 49 CFR 390 through 399. FMCSA issuing this Declaration and granting regulatory relief in accordance with 49 CFR 390.23 and 390.25, as set forth herein. STATE BUSINESS AND INDUSTRY RESOURCES State of Florida Florida Division of Emergency Management Florida ESF 18 Office (Business and Industry) esf18@em.myflorida.com and Private Sector hotline (850) 815-4925 (Daily 7am-7pm EDT). Updates can be found at Florida Disaster Business Florida Public Radio Florida Storms Mobile App Florida 511 for real-time traffic conditions
Fairbanks Scales unveils FB1150 Industrial Scale Instrument: A breakthrough solution for Optimizing Weighing in Transportation & Warehousing
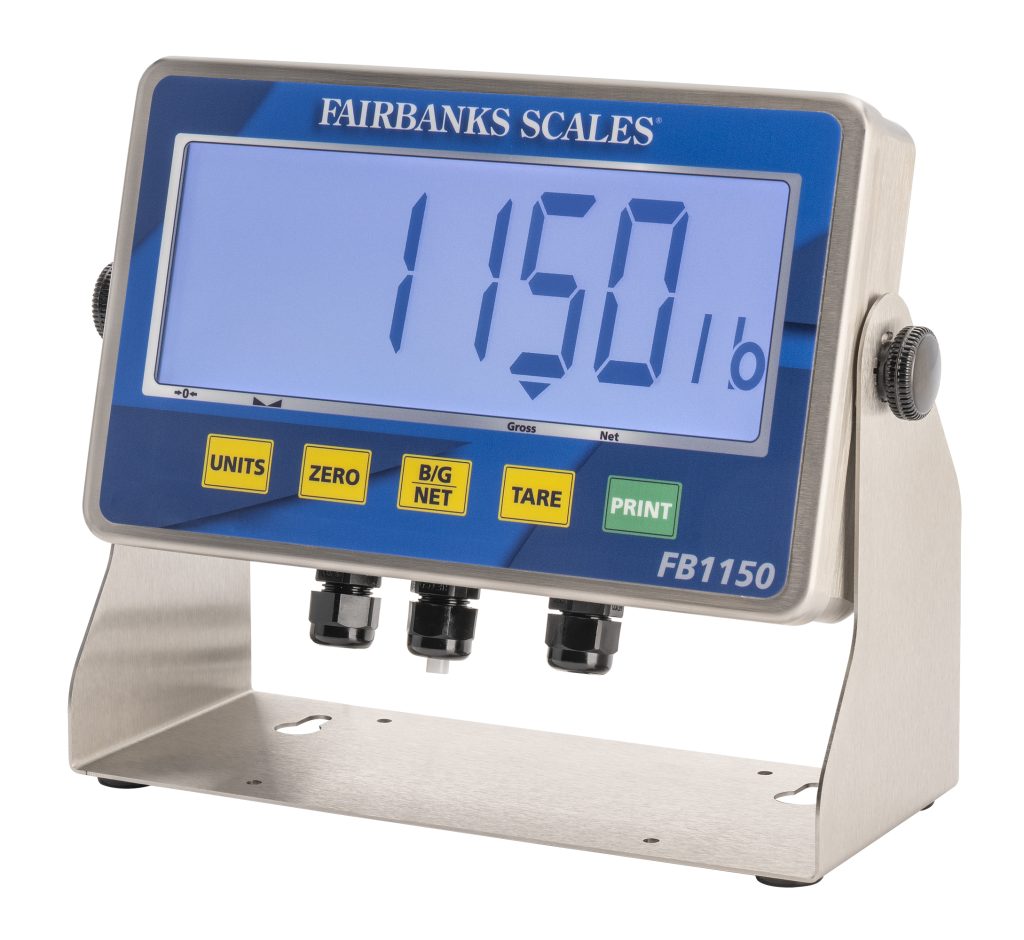
Fairbanks Scales Inc. has introduced the FB1150 industrial scale instrument. This robust and reliable solution is designed specifically to enhance weighing accuracy and efficiency in the transportation and warehousing industry. The FB1150 offers precision technology and ease of use, setting a new standard for performance, durability, and cost-effectiveness in the sector. Key Features of the FB1150 for Transportation & Warehousing: Large, High-Visibility Display: The FB1150 features a 2-inch-tall LCD display, providing clear, legible readings from up to seventy-five feet away. This makes it perfect for fast-paced loading and unloading operations in warehouses or logistics hubs, where quick access to weight data is essential for maintaining smooth workflow. Configurable Backlight Options: The FB1150 has seven backlight color settings, allowing users to customize visibility based on their lighting environment. Whether working in dimly lit docks or under bright warehouse lights, the display remains sharp, reducing errors and improving throughput. Versatile Connectivity Options: With an RS-232 serial port, the FB1150 enables seamless integration with ticket printers, PCs, and warehouse management systems (WMS). It can also serve as a remote display for other Fairbanks instruments, providing an interconnected solution for managing multiple scales at various locations. Remote Display Functionality: The FB1150 can be used as a remote display for other Fairbanks instruments. It allows operators to easily monitor weights from a central location, streamlining processes in busy environments and improving overall operational efficiency. Designed to withstand demanding environments, the FB1150 delivers exceptional reliability and performance without the high cost often associated with industrial-grade instruments. Its rugged construction and innovative features make it the ideal choice for businesses in the transportation and warehousing industry looking to enhance throughput, improve operational efficiency, and optimize their weighing capabilities.
Combilift Triple Crowned at the Exporter of the Year Awards for 2024
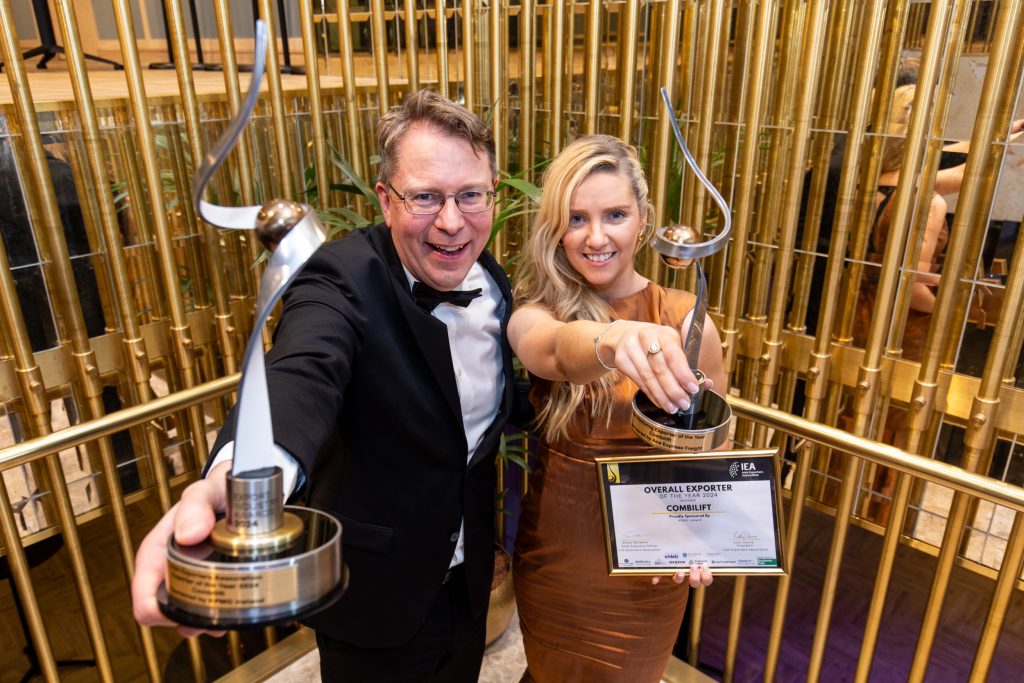
Combilift, the Irish manufacturing giant, celebrated a landmark achievement at the prestigious Irish Exporter of the Year Awards 2024, becoming the first Irish firm in history to win the coveted Exporter of the Year title three times! The IEA (Irish Exporters Association) event hosted at the Dublin Royal Convention Centre, saw Combilift not only secure the title of Manufacturing Exporter of the Year, sponsored by Ace Express Freight, but also claimed the ultimate honor of being named Overall Irish Exporter of the Year 2024, sponsored by KPMG. This extraordinary accomplishment further solidifies Combilift’s reputation as a leader in both the manufacturing and export arena. A Legacy of Success Combilift’s victory at this year’s Irish Exporter of the Year Awards is the latest in a long line of accolades. The company previously won the Irish Exporter of the Year award in 2008 and again in 2015, making this their third time receiving the prestigious title. These successes reflect Combilift’s ongoing commitment to innovation, growth, and quality in a highly competitive global market. These awards acknowledge Combilift’s significant contribution to the international marketplace, its innovative approach to engineering, and its relentless focus on fostering a culture of creativity and forward-thinking within the industry. Combilift is the leading global provider of innovative material handling solutions, offering a portfolio of award-winning, custom-engineered multidirectional forklifts, heavy handling equipment, and warehouse management systems. Established in 1998, the company now distributes to over 85 countries through a global network of dealers dedicated to meeting customer needs. This international reach and strategic growth were key factors in securing Combilift’s top honors at the event. Speaking at the Export Industry Awards, Simon McKeever, Chief Executive of the Irish Exporters Association, remarked: “I am thrilled to honor Combilift with the 2024 Exporter of the Year award. Their success in global markets is a testament to their team’s hard work and dedication. Combilift’s focus on innovation is at the core of its global success. Since its inception, the company has fostered a strong ethos of innovation and engineering solutions that push the boundaries of what’s possible in material handling. Their customized forklifts and warehouse solutions enable businesses to maximize space, reduce costs, and enhance safety, a key driver of their international growth.” Combilift’s CEO, Martin McVicar, shared his pride in the achievement, saying: “We are absolutely delighted with this recognition. To win two major awards, including Overall Winner, is a testament to the dedication, hard work, and innovative mindset of the entire Combilift team. Winning the Exporter of the Year in our market is the equivalent of winning a Gold medal at the Olympics – we are all competing at the highest level, and this award reflects that. I would also like to thank our customers and dealers around the world; your continued support and partnership have been key to our continued success. Our commitment to delivering cutting-edge solutions globally is stronger than ever, and it’s fantastic to have that recognized on such a prestigious platform.” A Remarkable September September 2024 has been an extraordinary month for Combilift, with a winning streak of 7 awards, highlighting the company’s leadership and innovation: UK EMA – Design Team of the Year for the Combi-BLADE UK EMA – Industry Leader Award, recognizing Martin McVicar’s exceptional leadership UKMHA Archies – Ergonomics of the Year Award for the Combi-CB70E UKMHA Archies – Product of the Year Award for the Combi-BLADE Deloitte Best Managed Company – Platinum Award, for the 12th consecutive year Irish Exporter of the Year – Manufacturing Exporter of the Year Irish Exporter of the Year – Overall Winner – Irish Exporter of the Year 2024 These accolades underscore Combilift’s ability to deliver outstanding products and services, unwavering commitment to excellence, and leadership in international markets. Looking Forward As Combilift celebrates its numerous successes, the company remains focused on the future. With a continued emphasis on innovation and sustainability, Combilift is well-positioned to expand its global presence further and continue leading the way on the international stage. Martin comments: “I’m excited about the future of our company. To support our continuous growth, we are actively seeking to expand our team of national account specialists across export markets.”
Raymond inspires next generation of talent with 10th National Manufacturing Day events
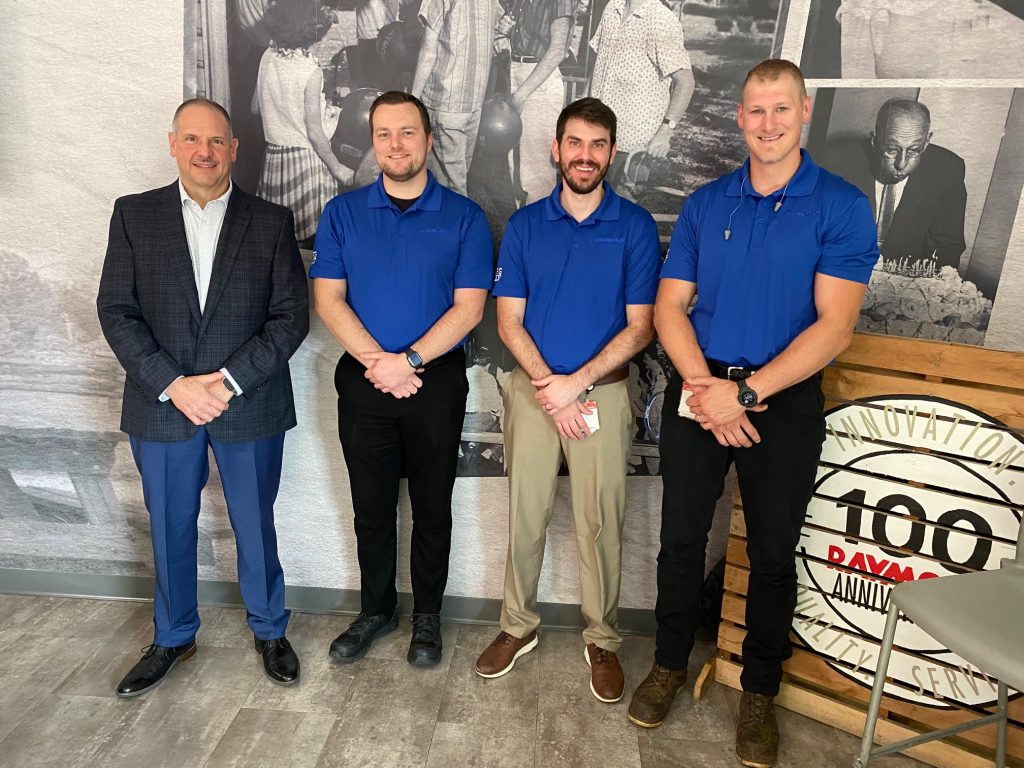
The Raymond Corporation hosts students for onsite tours and demonstrations on National Manufacturing Day, highlighting the importance of skills development and innovation in the manufacturing industry The Raymond Corporation kicks off its tenth annual celebration of National Manufacturing Day with both on-site and online events today. National Manufacturing Day is an annual celebration of the manufacturing industry organized by the National Association of Manufacturers (NAM) since 2012. The Raymond Corporation’s 2024 Manufacturing Day onsite event was held today at the Greene, NY facility. This year’s in-person event focused on showcasing innovation to high school students through interactive displays, hands-on activities, and firsthand insights from professionals working in these fields. Students had the opportunity to learn about building skills for the future through a manufacturing facility tour and demonstrations of forklifts, welding, and paint simulators. Students also had the chance to talk with Raymond employees who work in manufacturing. Students attending Raymond’s onsite Manufacturing Day event learned about the exciting and highly skilled careers available in manufacturing, including: A presentation from Tony Topencik, vice president of operations, quality, environmental health and safety An interactive employee presentation Interactive demonstrations provide a hands-on experience with forklift, welding, paint simulators, and Raymond technology products, including the iWAREHOUSE® suite of products, Virtual Reality simulator, and automation A tour of Raymond’s world-class, award-winning manufacturing facility Opportunities to learn about available job opportunities in manufacturing at Raymond Lunch with Raymond employees who work in manufacturing Raymond will also host an online Manufacturing Day program to help teachers and high school students learn more about future careers in modern manufacturing. Students will be able to learn about building skills for the future through a virtual manufacturing facility tour, highlights of industry technology, and various online activities. Schools can register to attend this event at www.raymondcorp.com/2024ManufacturingDayRegistration, which will be available from Oct. 4-31, 2024. “We’re excited to showcase the advancements happening at both Raymond and in material handling. We hope to spark curiosity in the next generation and encourage them to pursue a career in this growing industry,” said Tony Topencik, vice president of operations, quality, environmental health, and safety at The Raymond Corporation. “Skilled workers will always be in demand to ensure the smooth operation of our supply chains. That’s why Raymond is committed to creating a supportive environment where employees can thrive and shape the future of manufacturing.” For over 100 years, Raymond has been a leader in manufacturing, engineering, and the material handling industry, recognized for its leadership and innovation through various awards over the years, including: Forbes Best Midsize Employer, 2021, 2022, 2023 and 2024 Plant Engineering Product of the Year Award, 2020, 2023 and 2024 Food Shippers of America Top Food Chain Technology Award, 2023, 2024 “By prioritizing innovation and development of the next generation of manufacturing leaders at Raymond, we provide them with the necessary resources to effectively drive change within the supply chain,” said Randy Wolken, president and CEO at Manufacturers Association of Central New York. “We’re proud to support their journey as they shape the future of this dynamic industry in our state.” “As technology evolves, particularly with advancements in AI, big data, and sustainable practices, engaging and investing in students is increasingly crucial for our industry,” said Michael Field, president and CEO The Raymond Corporation. “By inspiring these young minds with a passion for innovation and equipping them with skills in these growing areas such as big data, AI advancements, and sustainable practices early on, we’re able to ensure a pipeline of skilled talent that’s ready to drive our industry forward with both technological and environmental responsibility.” For more than 100 years, Raymond has built a reputation as an innovative and future-forward organization. Raymond is actively contributing to developing next-generation energy resources, shaping the future for modern manufacturing, and leading the industry in sustainability and cutting-edge technology.
PLASTICS recognizes Manufacturing Day
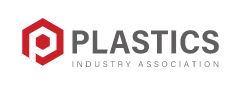
The Plastics Industry Association (PLASTICS) recognizes and celebrates Manufacturing Day, the largest annual event to promote manufacturing in the United States. Manufacturing Day works to show the reality of modern manufacturing careers by encouraging thousands of companies and educational institutions around the nation to open their doors to students, parents, teachers, and community leaders. The plastics industry is the eighth largest U.S. manufacturing industry, employs over one million workers and generates $519 billion. “Manufacturing Day is an excellent platform to highlight the exciting career opportunities and innovations throughout the plastics industry,” said PLASTICS’ President and CEO, Matt Seaholm. “Our manufacturing members are continually investing in new technologies and processes to make products more lightweight, durable, and sustainable, and those innovations call for a skilled and forward-thinking workforce. Plastics play a vital role in almost every aspect of daily life, and I encourage job seekers and students to consider the rewarding career paths in this essential industry.”
Intella Parts Company declares a winner in its “Oldest Toyota Forklift Competition”
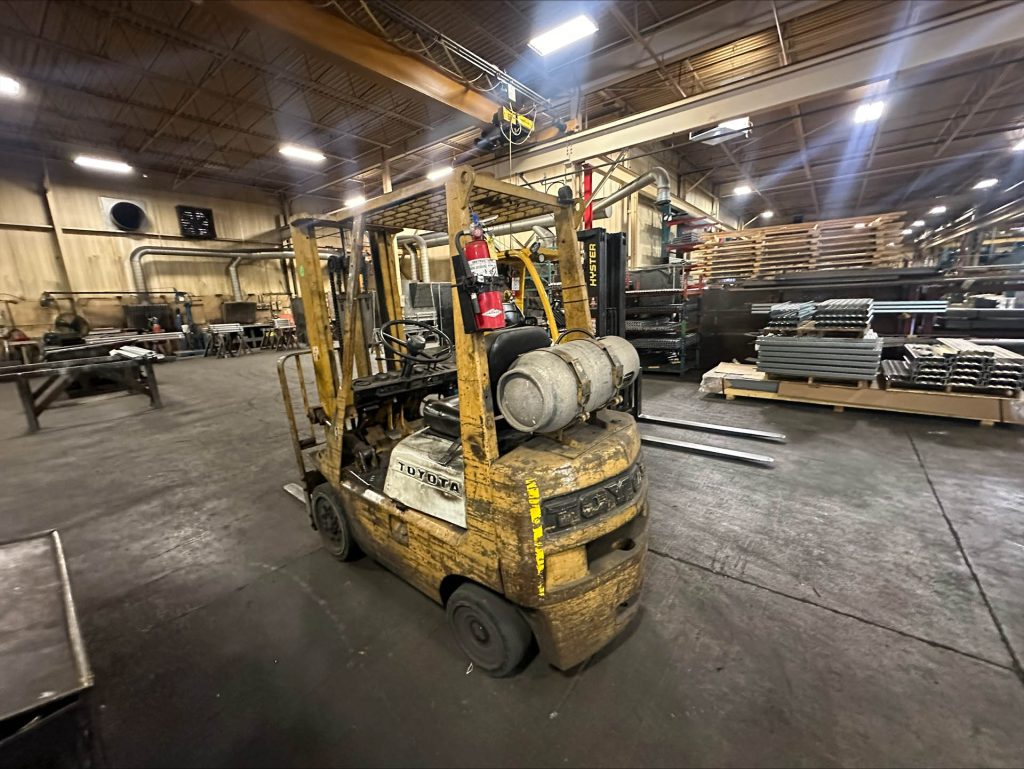
Intella Parts Company declared a winner in its contest to find the oldest operating Toyota forklift. Alexander Toolsie from Burlington, Ontario, submitted the winning entry for a 1978 Toyota model 42-3FGC20 forklift. Mr Toolsie was awarded a $100 gift certificate to be used on Intella’s website and a $100 Visa gift card. Intella offers aftermarket parts for most all brands of forklifts and most ages, even the old models. “Even if customers are operating older forklifts, Intella can supply the aftermarket parts they need to keep these older models running,” says Marcel VandenTop, president of Intella Parts Company. This is the second year Intella has run its ‘oldest forklift’ competition. In 2023, a multi-month competition resulted in the finding of a 1945 KD model in Amarillo, Texas.
Registration now open for Women in Industry Conference 2024
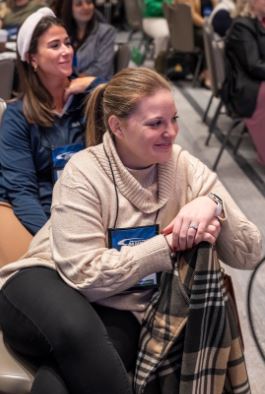
MHEDA has announced that the Women in Industry Conference registration is now open! Join MHEDA, MHI, and WERC for the 2024 Women in Industry Conference at the Loews Chicago O’Hare Hotel on November 6-7, 2024, and gain tools to prepare yourself for all the future has in store for YOU! Learn how to increase your status, build your network, connect through life’s pivot points, and uncover the new rules of influence with AI. This interactive conference is designed to inspire you to lead the way in evolving and preparing for the business landscape of tomorrow. Event Highlights: Connect with like-minded peers and expand your professional network. Gain practical skills and insights on leadership, technology, and personal development. Participate in roundtable discussions with others in similar roles. Enjoy several interactive networking activities and engage with fellow attendees. Learn practical AI hacks that will dramatically increase your productivity. And more! For full details and to register, visit https://www.mheda.org/events/wii2024/.
Syntegon complete packaging system solutions at Pack Expo 2024
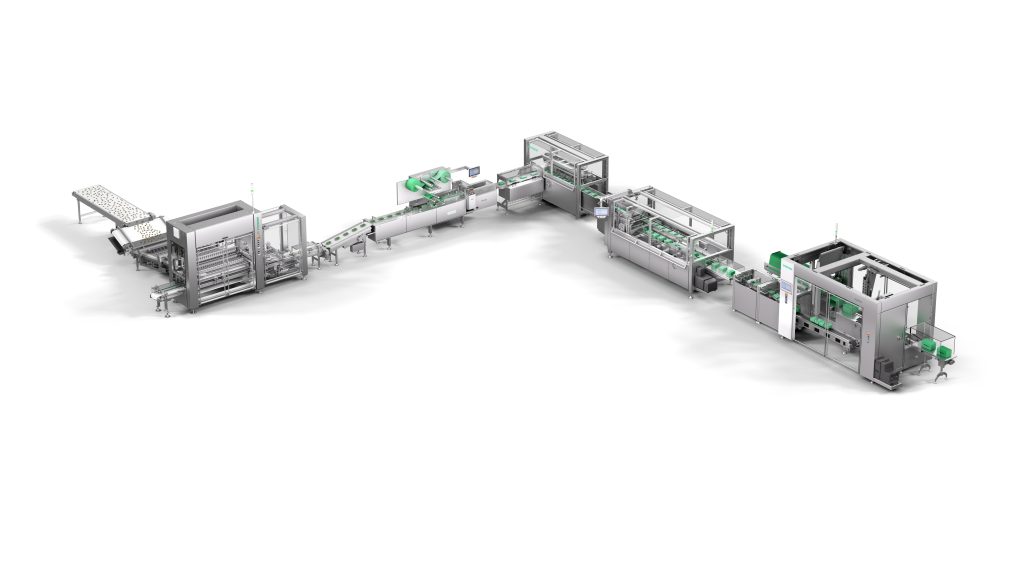
Visit Booth S-2914 to explore seamless processes, innovative technologies, and sustainable solutions for the food industry Syntegon will highlight its latest innovations and comprehensive system solutions at PACK EXPO International, to be held November 3-6, 2024, at McCormick Place, Chicago, IL, Booth S-2914. Experience highly automated systems for cookies, as well as fresh, chilled, and frozen food, along with the debut of the SVX Compact, part of Syntegon's VFFS SVX series, for snacks. “Syntegon is a one-stop supplier for seamless solutions with high levels of automation and efficiency,” says Brad Baker, Senior Sales Director North America at Syntegon. “Whether food manufacturers are looking for stand-alone primary, secondary or case packing equipment – or fully integrated turnkey systems – we provide sustainable and flexible solutions as well as comprehensive support services to future-proof their investment while maintaining impressive levels of operational efficiency.” System Solution for Sandwich Cookies Syntegon’s system solution for sandwich cookies offers a highly automated packaging line that prioritizes speed, flexibility, and efficiency. Central to this solution is the all-new FGCT high-speed count feeder, which efficiently groups cookies and loads them into trays, minimizing damage and waste. This aligns with Syntegon’s commitment to sustainability. The FIT linear motor infeed and Pack 202 flow wrapper provide a compact solution for overwrapping trays. The Pack 202 is a versatile flow-wrapping machine, that handles various formats at different speeds. Following the primary packaging process, the new MagTRAC collating unit, which uses linear motor technology for quick format changes, is seamlessly integrated into the compact BEC endload cartoner. This setup enhances flexibility and reduces changeover times. The BEC endload cartoner supports high-speed operation and flexible format handling, minimizing downtime and resource consumption. The Elematic 1001 side load case packer optimizes floor space with its compact design and user-friendly interface, integrating smoothly into existing lines. This system solution for sandwich cookies addresses industry challenges like labor shortages and cost pressures. Syntegon also offers Service Agreements, including remote support and Synexio software for data analysis, helping optimize production efficiency. System Solution for Fresh, Chilled, and Frozen Food Syntegon’s solution for fresh, chilled, and frozen food features new wash-down RPP pick-and-place robots integrated with a Pack 403 HE flow wrapper, designed for harsh environments with essential cleaning capabilities for food safety. The stainless-steel frames and motors of the RPP meet NEMA4X standards for durability. RPP robots efficiently load products into the flow wrapper infeed chain. In addition to the primary packaging process, the system includes a Kliklok ACE carton erector and a second RPP cell for loading the flow-wrapped products into cartons. Kliklok ACE allows quick transitions between carton sizes, reducing downtime and enhancing flexibility. Its ergonomic design improves operator efficiency and safety. This solution showcases Syntegon's dedication to innovative and seamless packaging processes. By integrating advanced technologies, Syntegon offers manufacturers a robust system that meets demanding hygiene and efficiency standards while future-proofing operations. The system’s hygienic design, stainless-steel construction, and wash-down capabilities ensure high food safety standards and increased automation. SVX Compact The SVX Compact by Syntegon revolutionizes the snack industry with its innovative design, offering the fastest cycle times for snack manufacturers, achieving up to 300 cycles per minute. The drive system is positioned on the sealing mechanism, reducing frame size, making the machine ultra compact and a perfect fit for this industry. Modular design and quick format changes accommodate various product types and packaging styles enhancing future-proof flexibility and production output. The SVX Compact features a patent-pending cross-seal drive for reliable seals that enhance product integrity and extend shelf life. It supports the use of sustainable packaging materials. The hygienic design enables easy cleaning and compliance with food safety standards. Digital real-time monitoring boosts efficiency through data analysis. Remote service capabilities enable proactive maintenance, minimizing downtime.
SupplyOne showcases packaging equipment and services
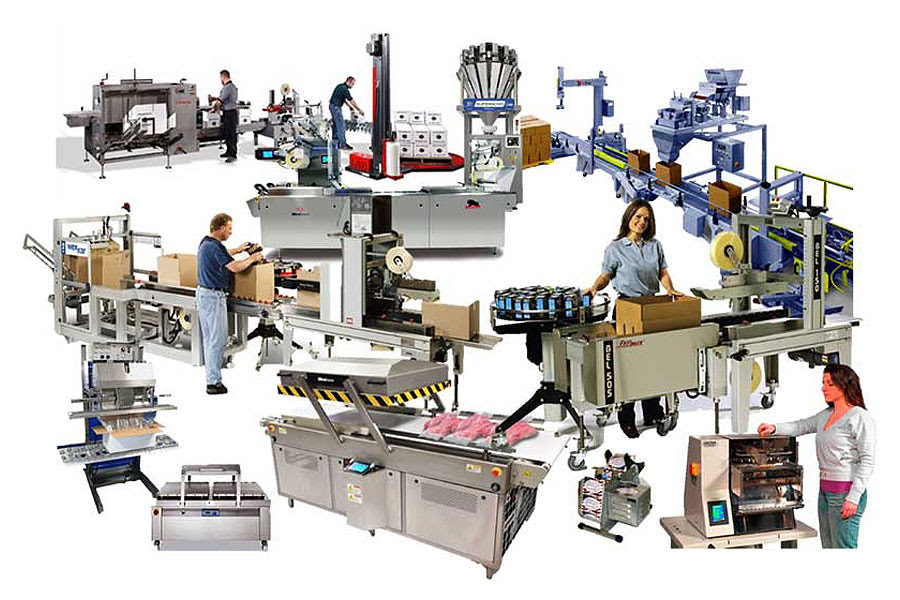
Versatile solutions for diverse industry needs SupplyOne, Inc. spotlights its expansive range of packaging equipment and support services. These offerings enhance productivity, efficiency, and overall packaging performance across various industries. SupplyOne offers a diverse catalog of packaging automation equipment that caters to a wide range of applications. Their solutions include carton sealing, conveying, strapping, and handling systems that ensure secure and efficient packaging processes. They also provide specialized equipment for food packaging, such as thermoformed trays, vacuum chambers, and steam tunnels. Additional offerings include palletizing and stretch-wrapping equipment, shrink-wrapping machines, blister packaging, and bag and pouch-filling systems. SupplyOne’s equipment ensures product safety and quality with options like induction sealing and metal detection, and their systems integration and robotics enhance automation and efficiency. SupplyOne’s factory-trained technicians and seasoned equipment engineers are dedicated to reducing downtime and increasing productivity. Their comprehensive support services include operator training to ensure the safe and efficient use of equipment, as well as equipment rentals and financing to offer flexible solutions to meet operational needs. The company provides demo systems that allow customers to evaluate equipment before purchase, and strategic recommendations from experts to optimize packaging processes. Maintenance and repair services ensure the long-term reliability and performance of equipment. With multiple locations across North America, SupplyOne’s team of experts is always available to provide tailored solutions that meet specific industry requirements. The company represents best-in-class manufacturers, ensuring unbiased recommendations and top-quality equipment. SupplyOne’s Packaging Management Program (PMP) and Management Services Agreement (MSA) are designed to deliver significant savings by optimizing packaging operations. These programs help reduce direct costs, improve working capital, and enhance operational efficiency, ultimately lowering the total cost of packaging ownership.
LEDtronics expands low bay lighting solutions
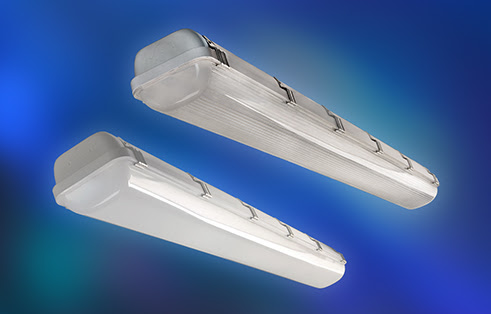
Tunable, Dimmable LED Linear Luminaires LEDtronics® has announced its latest line of LED Linear Low Bay Luminaires. These new luminaires offer multi-wattage and multi-CCT tunable units, versatile dimming capabilities, and a wide range of features, making them ideal for a variety of lighting applications. With options to select from three different color temperatures—3000K Medium White, 4000K Natural White, and 5000K Pure White—and wattage options of 32W, 40W, and 50W, these 4-foot luminaires are highly customizable to fit any lighting need. Additionally, they are available with a choice of diffused frosted white or clear lenses. The LLL04-MW unit is dimmable when wired to an external 0-10V dimmer, while the LLL04-MWS model comes equipped with a built-in microwave motion sensor offering programmable dimming with daylight harvesting capabilities. Available with five mounting options and suitable for wet locations with an ingress protection rating of IP66, these luminaires are a great solution for various applications, including production areas, canopies, stairwells, warehouses, workshops, food processing facilities, equestrian parks, farmyards, parking areas, garages, tunnels, and bridges. With a stainless steel heatsink and included mounting hardware (silicone gasket and closure clips for secure, even sealing), the units are perfect for wall, ceiling, or suspended mounting. These ETL-listed lighting solutions operate on a 120-to-347 AC voltage range, providing a wide 120-degree beam of uniform lighting with a high color rendering index of 80. For the clear lens models, luminosity ranges from 4,839 lumens at 32W/3000K to 7,397 lumens at 50W/4000K. For the frosted lens models, luminosity ranges from 4,905 lumens at 32W/3000K to 6,851 lumens at 50W/4000K. A power factor of 0.98~0.99 supplies constant-current power at any wattage selection. Both the clear and frosted units feature a polycarbonate lens integrated with crystals that enhance even light distribution. The luminaires have an integrated design where the LED plate is bonded to the polycarbonate cover. The lightweight yet durable white polycarbonate housing with a stainless steel heatsink resists vandalism, high impact, and shock. The rugged construction, along with an IK08 Impact Rating and a wide operating temperature range of -40°F to +122°F (-40°C to +50°C), makes these luminaires ideal for harsh environments. They have an extended lifespan of up to 50,000 hours with lumen maintenance of over 70 percent. At the 50W/5000K setting, these luminaires can replace 35W LPS, 100W HPS, and 300W tungsten halogen (TH) quartz lights. Thanks to their solid-state design, the LED lights are impervious to shock, vibration, frequent switching, and environmental extremes. Unlike traditional halogen, metal halide, or high-pressure sodium bulbs, these ETL-listed LEDs do not emit excessive heat or ultraviolet and infrared light, contributing to energy savings and enhanced safety. The new LEDtronics LLL04-x-MW and LLL04-x-MWS series of linear low bay luminaires, featuring tunable color temperatures and wattages, are available through LEDtronics distributors and come with a five-year warranty. Quantity discounts and custom options are available for volume orders, including mounting options for wire/chain suspension, 90-minute emergency battery backup, and 8-foot linear luminaires.
ALAN HURRICANE HELENE SITUATIONAL REPORT for Wednesday, October 2, 2024
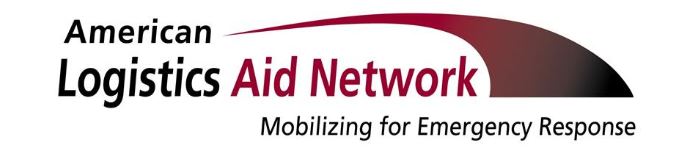
American Logistics Aid Network is mobilized for Hurricane Helene. As part of our response efforts, we are committed to providing you with the latest information and updates on supply chain impacts via our periodic Situation Reports. ALAN has been improving logistics response to disasters for 19 years, and the need is greater now than ever. Please donate today to help us continue our work for many more years to come. CRITICAL MESSAGES North Carolina Business Operations Center: Partners moving people, resources or equipment into western North Carolina, MUST coordinate plans and movements through the NCEM-BEOC. Help us keep critical supply lines open. Please do not self-deploy resources or supply logistics without coordinating with the BEOC. There is a high likelihood that your team(s) will be turned away at various checkpoints. We will prioritize movements and provide safe routes with an escort, as needed. You can email your supply logistics or movement requests to: BEOC@ncdps.gov Begin Subject Line with: Logistics Support Please include the following info: What are you moving? Why you need special access. When do you plan to move, and from where? Where are you going? When will they arrive at the “border to Western NC,” and where? In summary, until further notice, roads in Western NC (generally anywhere west of Hickory, NC) are closed to all traffic other than emergency services and pre-approved shipments coordinated through the BEOC. ITEMS OF INTEREST 2:00pm EDT North Carolina BEOC Coordination Call Teams Meeting Meeting ID: 259 218 205 140 Passcode: uyvDTB 4:00 pm EDT PSEMA Tropical Storm Helene Coordination Call via Zoom https://us02web.zoom.us/j/82147633838?pwd=hiay24IsxMe84PbrImyZtSlTdq60Vv.1 Meeting ID: 821 4763 3838 Passcode: PSEMA FEDERAL EMERGENCY DECLARATIONS President Biden approved Major Disaster Declaration for Virginia on October 2, 2024, in response to Hurricane Helene. President Biden approved Major Disaster Declaration for Georigia on October 1, 2024, in response to Hurricane Helene. President Biden approved Major Disaster Declaration for South Carolina on September 29, 2024, in response to Hurricane Helene. President Biden approved Emergency Declaration for Virginia on September 29, 2024, in response to Hurricane Helene. President Biden approved a Major Disaster Declaration for Florida on September 28, 2024, in response to Hurricane Helene. President Biden approved Major Disaster Declaration for North Carolina on September 28, 2024, in response to Hurricane Helene. President Biden approved Emergency Declaration for Tennessee on September 28, 2024, in response to Hurricane Helene. President Biden approved Emergency Declaration for South Carolina on September 26, 2024, in preparation for impacts from Hurricane Helene beginning on September 25, 2024, and continuing. President Biden approved Emergency Declaration for Alabama on September 26, 2024, in preparation for impacts from Hurricane Helene beginning on September 22, 2024, and continuing. President Biden approved Emergency Declaration for North Carolina on September 26, 2024, in preparation for impacts from Hurricane Helene beginning on September 25, 2024, and continuing. President Biden approved Emergency Declaration for Georgia on September 26, 2024, in preparation for impacts from Hurricane Helene beginning on September 24, 2024, and continuing. President Biden approved Emergency Declaration for Florida on September 24, 2024, in preparation for impacts from Tropical Storm Helene beginning on September 23, 2024, and continuing. STATE STATE DECLARATIONS Tennessee Governor Lee issued Executive Order No. 105 on September 27, 2024, in response to Hurricane Helene. West Virginia Governor Justice issued Proclamation declaring a State of Preparedness on September 26, 2024, in response to Hurricane Helene. Virginia Governor Youngkin issued Executive Order No. 37 on September 25, 2024 declaring a state of emergency due to Hurricane Helene. South Carolina Governor McMaster issued Executive Order 2024-24 on September 25, 2024, in preparation for impacts from Hurricane Helene. North Carolina Governor Cooper issued Executive Order No. 315 on September 25, 2024, declaring a statewide state of emergency and temporary waiver and suspension of motor vehicle regulations. Georgia Governor Kemp issued Executive Order on September 24, 2024, declaring a State of Emergency for Tropical Storm Helene. Florida Governor DeSantis issued Executive Order 24-209 on September 24, 2024, amending Executive Order 24-208. Florida Governor DeSantis issued Executive Order 24-208 on September 23, 2024, in preparation for impacts from potential tropical cyclone nine. ACTIVE TRANSPORTATION WAIVERS Title: Virginia Department of Transportation Secretary issued Transportation Waiver on September 26, 2024 (extension signed 10/01/24) Effective: 09/26/24| Expires on: 10/25/24 Description: The Virginia Department of Transportation Commissioner issued a transportation waiver granting temporary overweight, over width, registration, license, or hours of service exemptions to all carriers transporting essential emergency relief supplies to, through, and from any area of the Commonwealth. Authorization applies also applies to water, food, heating oil, motor fuels or propane, or agricultural products, agricultural supplies, livestock and poultry, forest products and salvaged wood, waste, and trees cut in preparation for the storm, or providing restoration of utilities. Title: Tennessee Governor Lee issued Executive Order No. 105 for Hurricane Helene Effective: 09/27/24| Expires on: 10/11/24 Description: Tennessee Executive Order No. 105 provides exemption to Tennessee Code Annotated Sections: 55-4-401 through Section 55-4-413; Section 55-7-201 through Section 55-8-209, and Tenn. Comp. R. & Regs. 1680-07-01 through 1680-07-01-.25 that set forth maximum weight, height, length, and width limitations are suspended in the case of vehicles providing relief efforts in response to severe weather. In accordance with 49 CFR 390.23, provide a temporary exemption from 49 CFR Part 395 limiting the hours of service for the operator of a commercial vehicle providing supplies, equipment, personnel, and other provisions to assist persons affected by severe weather. Title: Alabama Department of Revenue Commissioner issued Executive Order Effective: 09/27/24| Expires on: 10/27/24 Description: Alabama Department of Revenue Commissioner issued executive order providing temporary suspension of the motor fuel exporter, importer, and transporter licensing requirements associated with the Alabama Terminal Excise Tax for those supporting disaster relief efforts by engaging in the export of motor fuel from Alabama to areas in other states impacted by Hurricane Helene. Title: Alabama Department of Revenue Commissioner issued Executive Order Effective: 09/27/24| Expires on: 10/27/24 Description: Alabama Department of Revenue Commissioner issued executive order providing temporary suspension of the requirements associated with the International Registration Plan and International Fuel Tax Agreement for any motor vehicle engaged in interstate disaster relief which will be traveling through the State of Alabama as part of the disaster relief. Title: Virginia Department of Transportation Secretary issued Transportation Waiver on September 26, 2024 Effective: 09/26/24| Expires on: 10/02/24 Description: Virginia Department of Transportation Commissioner issued a transportation waiver granting temporary overweight, over width, registration, license, or hours of service exemptions to all carriers transporting
MHI offers support for the victims of Hurricane Helene
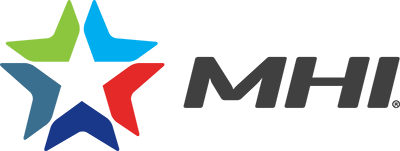
The sights of Hurricane Helene’s flooding, debris, and destruction are incredibly saddening, particularly when we consider the lives lost and those who are still missing or awaiting help. The road to recovery will be long and arduous, with overwhelming work ahead. The American Logistics Aid Network (ALAN) is actively responding to these needs, as it has done for over 19 years. To help support the relief efforts, the MHI Board of Governors has approved a resolution to donate $200,000 to ALAN. “It is hard to know where to even begin in the face of such massive devastation,” said John Paxton, MHI CEO. “We are confident that the donation to ALAN will get relief to those who need it as swiftly as possible.” MHI encourages you to check in frequently for ALAN’s latest updates and needs. If you’d prefer, you can also make a donation to support our ongoing humanitarian efforts. Every dollar truly helps. You can also provide support by providing the specifically requested material handling equipment. Please be on the lookout for additional material handling equipment donation needs from the ALAN network. In addition to ALAN, these organizations also assist Helene victims. American Red Cross World Central Kitchen United Way The Salvation Army
Plastics: The global nature of an indispensable industry
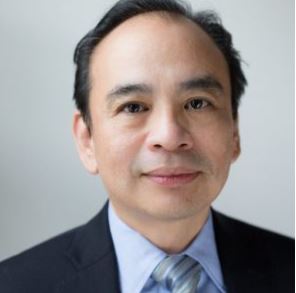
Each year, the Plastics Industry Association releases one of our flagship publications, the Global Trends Report. Written from the U.S. plastics industry perspective, the report provides a detailed assessment of the plastics trade during the previous year and the first six months of the current year. Last year’s report highlighted a $1.0 billion U.S. plastic trade surplus for the first six months. It also projected that the U.S. would return to a plastics trade surplus in 2023, which appears to be confirmed in this year’s forthcoming Global Trends Report. However, trade challenges can arise at any point, and unlike any global industry, the plastics industry’s supply chain is no exception. For instance, the dockworkers’ strike along the East and Gulf Coasts, which began on October 1, could create significant supply chain disruptions if not resolved promptly, and its overall impact on the macroeconomy could be inflationary. During a roundtable discussion this week, led by U.S. Department of Commerce Assistant Secretary Grant Harris, the Plastics Industry Association expressed concerns about the state of trade. It noted that plastics imports totaled $38.7 billion in the first half of 2024, while exports reached $38.6 billion. Given the wide range of industries plastics serve, plastic trade has far-reaching implications for the U.S. economy. Perc Pineda, PhD, Chief Economist of PLASTICS, shared his concerns during the discussion: “From a broader supply chain perspective, we hope the issue is resolved soon,” Pineda said, adding that “in the meantime, the U.S. plastics industry, by and large, can address potential supply gaps in manufacturing inputs due to the ports strike, just as it did during the COVID-19 pandemic – to keep the U.S. economy moving.” Although the U.S.’s free trade partners, Mexico and Canada, accounted for 45.1% of total U.S. plastics industry exports and 30.3% of imports year-to-date through July 2024, with trade primarily moving by rail or truck, trade with other countries also plays a significant role. As of July 2024, the estimated total exports of plastics materials and products, excluding plastics machinery and molds for plastics, originating from The East and Gulf ports were $17.9 billion, while imports were $17.0 billion. Since PLASTICS began tracking global plastic players in its annual Global Plastics Rank®, the U.S. has consistently ranked second to China, surpassing Germany, which holds the third position, as a key global player in plastics trade. This year’s annual Global Trends Report edition will be released on October 16, 2024, at the inaugural National Plastics Conference in Houston, TX. For more information on the event, visit: https://nationalplasticsconference.org/
Wolter Inc. expands national presence with new region & strengthened executive leadership

Wolter Inc. just announced significant developments in our national growth strategy, including creating a new region and appointing key executive leaders. These changes, driven by our February 2024 partnership with BBH Capital Partners, mark a major expansion of our footprint across the United States. Creation of the Southeast Region Wolter Inc. is strategically expanding beyond its Midwest roots into the Southeast with the recent acquisition of Dedicated Material Handling Solutions in Atlanta, GA. This expansion enables Wolter Inc. to reach new customers and tap into the thriving markets from Arkansas to Florida. Tony Jones, the former CEO of Doosan Industrial Vehicles Americas, has been named President of Wolter Southeast. Based in the Atlanta, Georgia, area, Tony will spearhead growth initiatives and acquisitions throughout the Southeast, seamlessly integrating them into our existing operations. Strengthening the Midwest Leadership As we expand into new regions, Wolter Inc. remains committed to strengthening our core operations in the Midwest. Ross Jeremiah has been promoted from Executive Vice President to President of Wolter’s Midwest region. Ross’s leadership will be essential in overseeing our Midwest operations and ensuring seamless integration and collaboration with the newly established Southeast region. Stu Pineda has been promoted to Chief Financial Officer of Wolter, Inc., where he will spearhead financial strategies that support our expansion and ongoing success. Wolter Leadership Team Overview A dedicated and experienced executive team drives Wolter Inc.’s expansion and success: Wolter Inc. Otto Wolter – Owner, Chairman of the Board Jerry Weidmann – CEO, Board Member Steve Kletzien – Board Member Ross Jeremiah – President, Midwest Tony Jones – President, Southeast Stu Pineda – CFO Martin Park – COO & Chief of Staff Kristin Lelewicz – CMO Julie Williams – CIO Kim Wachs – CHRO Jan Plenke – Assistant to Chairman of the Board Martin Park, our Chief Operating Officer, will also serve as the CEO’s newly appointed Chief of Staff. Martin will oversee operations coordination across our corporate departments, including Human Resources, Finance, IT, Marketing, and the newly created regional divisions in this role. His leadership will ensure that all facets of our expanding business are aligned with Wolter Inc.’s strategic goals.