Material Handling Education Foundation, Inc. announces the Liz Richards Scholarship Fund
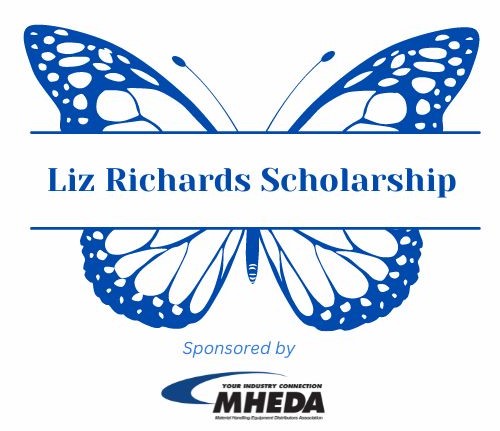
The Material Handling Education Foundation, Inc (MHEFI) an independent charitable organization that was established in 1976, has announced the Liz Richards Scholarship Fund sponsored by MHEDA is now accepting applications. Liz Richards has dedicated much of her 28-year career to growing the awareness and recognition of the material handling industry within the academic community. Liz has worked tirelessly to ensure our industries are a draw for top talent to sustain and strengthen material handling businesses for the future. The Liz Richards Scholarship Fund sponsored by MHEDA offers two to three scholarships per year, each worth $5,000. Family and friends of MHEDA member companies are encouraged to apply. The scholarships are awarded in partnership with The Material Handling Education Foundation, Inc. (MHEFI). The following provides a brief overview of the scholarship program. Please refer to the MHEFI website for complete details. Important Dates! Scholarship Opens – November 15, 2023 Scholarship Closes – January 31, 2024 Scholarships Awarded – April 30, 2024 Dates subject to change. Where to Apply Click here to apply for a scholarship! Note, applications will open in November 2023. Target Programs of Study Undergraduate students from programs listed below that have a focus on material handling, logistics and/or supply chain management are encouraged to apply. Industrial Engineering Industrial Distribution Mechanical & Electrical Engineering Structural Engineering with a focus on cold-formed steel design Engineering Technology Computer Science related to Material Handling & Supply Chain Business & Management related to Material Handling or Supply Chain Management Student Eligibility* For the 2024/2025 academic term, the following students are eligible to apply: Undergraduate students pursuing a material handling, logistics or supply chain career enrolled full time at a qualified college or university in a target program (see list above). Undergraduate students may be classified as freshman, sophomore, junior or senior for the Fall 2024 term to be eligible. Enrolled at any non-profit college or university in the United States accredited by the Council for Higher Education. All applicants must be full-time students with a “B” grade point average or above in their major. Applicants must be enrolled in school for the entire academic year (Fall 2024 and Spring 2025) without interruption barring illness, emergency, or military service. Scholarship awards cannot be used for study abroad programs/semesters or summer school. *Please note, eligibility requirements are subject to change. Scholarship Questions? For scholarship questions, please contact Donna Varner, Executive Director, at 704-676-1190 or email dvarner@mhi.org. Interested in Contributing to the Liz Richards Scholarship Fund? If you would like to help promote the material handling industry by contributing to the Liz Richards Scholarship Fund, click here. Any amount you contribute is tax deductible and will be appreciated and acknowledged.
Movu receives “Supply Chain Excellence Awards 2023” for revolutionary use of robotics in warehousing
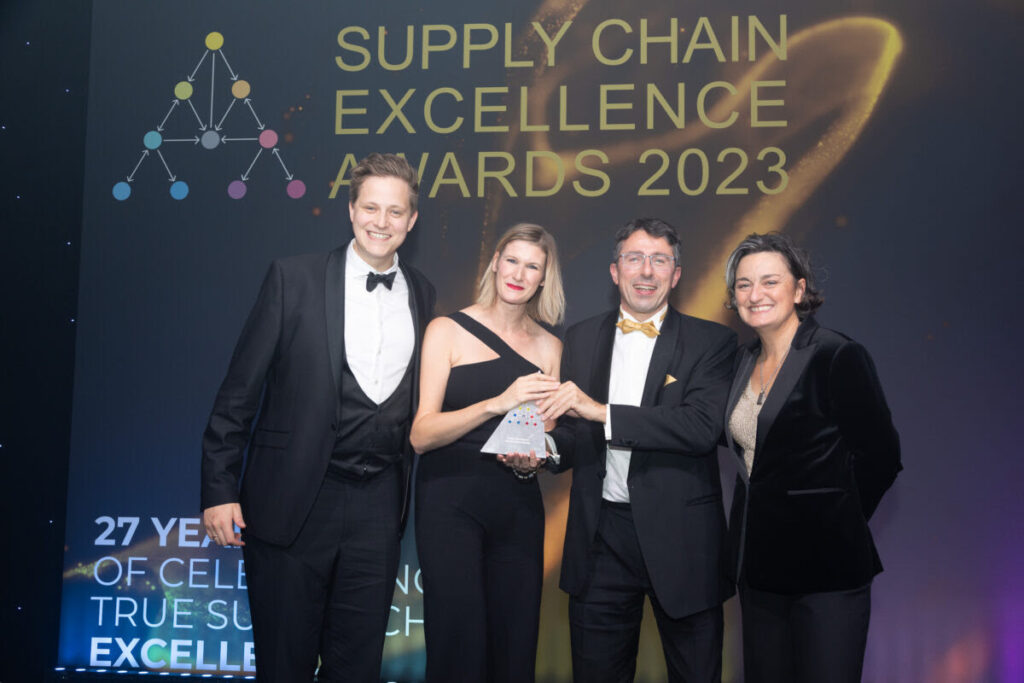
Movu Robotics, one of the industry warehouse automation and robotics suppliers, proudly announces it was exclusively granted “The Best Use of Robotics” award at the “Supply Chain Excellence Awards 2023”. The Awards, recognized as the gold standard for best practices in supply chain management, is bestowed upon organizations that exemplify excellence and innovation in the field. This year, with nearly 300 entries from over 150 unique companies, it had more entrants than ever before. This accolade, presented at the prestigious award ceremony held on November 9th in London, marks Movu’s outstanding contributions to supply chain innovation and excellence. Movu’s achievement underscores its commitment to pushing the boundaries of warehouse automation and robotics. A distinguished jury of internationally renowned experts from the logistics industry awarded Movu for its groundbreaking project for the customer Dematra, a pioneering logistics services company. This visionary project, a shining example of the pinnacle of automated technology in warehousing, showcases a commitment to redefining the future of warehousing and distribution. At the heart of the project stands the awe-inspiring 46-meter-tall stow Silo, a revolutionary fully automated high-bay warehouse. This technological marvel has the capacity to effortlessly house nearly 80,000 pallets and can handle an impressive 12,000 pallet movements within a 24-hour timeframe — an international premiere in warehouse automation. Key to the success of the project are the Movu atlas shuttles, self-powered 2D-pallet carriers ingeniously designed for optimal movement and organization of pallets. These shuttles work seamlessly with the specially designed stow shuttle-rack system and the local controlling system (STC). Jos De Vuyst, CEO of stow Group, expressed his pride in this achievement, stating, “We are truly honored to receive the Supply Chain Excellence Awards 2023. Our collaboration with Dematra and the joint efforts of the stow and Movu teams have resulted in a highly successful project that not only demonstrates the future of warehousing but elevates it to unprecedented heights. The Dematra project exemplifies Movu’s vision to upgrade warehouses globally with easier automation, pushing the boundaries of what is achievable in the world of warehousing”. Movu remains at the forefront of innovation, committed to transforming the warehouse landscape with accessible and easier automation through which it sets new standards in automation and robotics.
Do you have information rot?
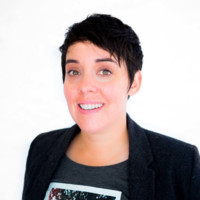
Every organization we’ve worked with has reams of consumer feedback. Often it is utilized to make critical decisions. Sometimes, it’s not. Sometimes, the feedback itself becomes the exercise, where study after study is created multiple times a year, and the insights are simply shared across the organization – nothing more. While customer insight collection is one thing, how companies analyze it is another. Even though we do relentless collection, leaders overlook the fact that consumer stories and insights are subject to decay. Generally, the useful half-life of information is approximately one month. If you gather 1000 stories from consumers, only about 500 will retain their usefulness and actionability after a month. The remaining 500 stories will become outdated and irrelevant as situations evolve and contexts shift. This means that interventions and actions based on perishable data need to be timely. We all have encountered this phenomenon at some point in our lives. Perhaps you observed something about a friend but hesitated to share it, and after some time, the observation lost its significance or relevance. Similarly, we might have a half-drafted email that lingers too long, prompting us to eventually delete it. When companies conduct consumer research, they gather data on their preferences and purchasing habits. This is also subject to decay. As consumer preferences change over time and new trends emerge, the insights collected in previous months or years may no longer be accurate or helpful in making strategic decisions. Recognizing the impermanence and rot of information is crucial, and to mitigate it, you don’t need more studies, but disintermediation. Disintermediation involves removing intermediaries, layers of judgment, and interpretative elements that separate the current state from decision-makers. This process fosters more direct connections between context and decision-makers, allowing for better-informed choices and better responsiveness to changing needs. Consumer problems don’t sit still and wait for solutions, they continuously evolve. This necessitates a more adaptive, fluid, and iterative approach to identifying and responding to consumer needs, where decision-makers must engage directly with the issue, observe patterns and behaviors that emerge, and respond accordingly. Retired General Stanley McChrystal noted a great perspective on the intricacies of changing situations: “For a soldier trained at West Point as an engineer, the idea that a problem has different solutions on different days was fundamentally disturbing. Yet that was the case.” Think of it like surfing or snowboarding, where one must remain vigilant and responsive to ever-changing conditions.As leaders, we need to get out of the old pattern of periodically collecting data and insights, and slowly disseminating it across the organization, hoping change will appear. Instead, we need to focus on shifting our organization’s habits and behaviors towards a fluid, adaptive, and time-bound approach to gathering and responding to consumers’ needs. Otherwise, we’ll just keep collecting a lot of insights that will eventually rot. About the Author: Andrea Belk Olson is a keynote speaker, author, differentiation strategist, behavioral scientist, and customer-centricity expert.As the CEO of Pragmadik, she helps organizations of all sizes, from small businesses to Fortune 500, and has served as an outside consultant for EY and McKinsey. Andrea is the author of three books, including her most recent, What To Ask: How To Learn What Customers Need but Don’t Tell You, released in June 2022. She is a 4-time ADDY® award winner and host of the popular Customer Mission podcast. Her thoughts have been continually featured in news sources such as Chief Executive Magazine, Entrepreneur Magazine, Harvard Business Review, Rotman Magazine, World Economic Forum, and more. Andrea is a sought-after speaker at conferences and corporate events throughout the world. She is a visiting lecturer and startup coach at the University of Iowa, a TEDx presenter, and TEDx speaker coach. She is also an instructor at the University of Iowa Venture School. More information is also available on www.pragmadik.com and www.andreabelkolson.com.
Industrial Labelling Systems continues team growth and celebrates 10-Year partnership with Evolabel
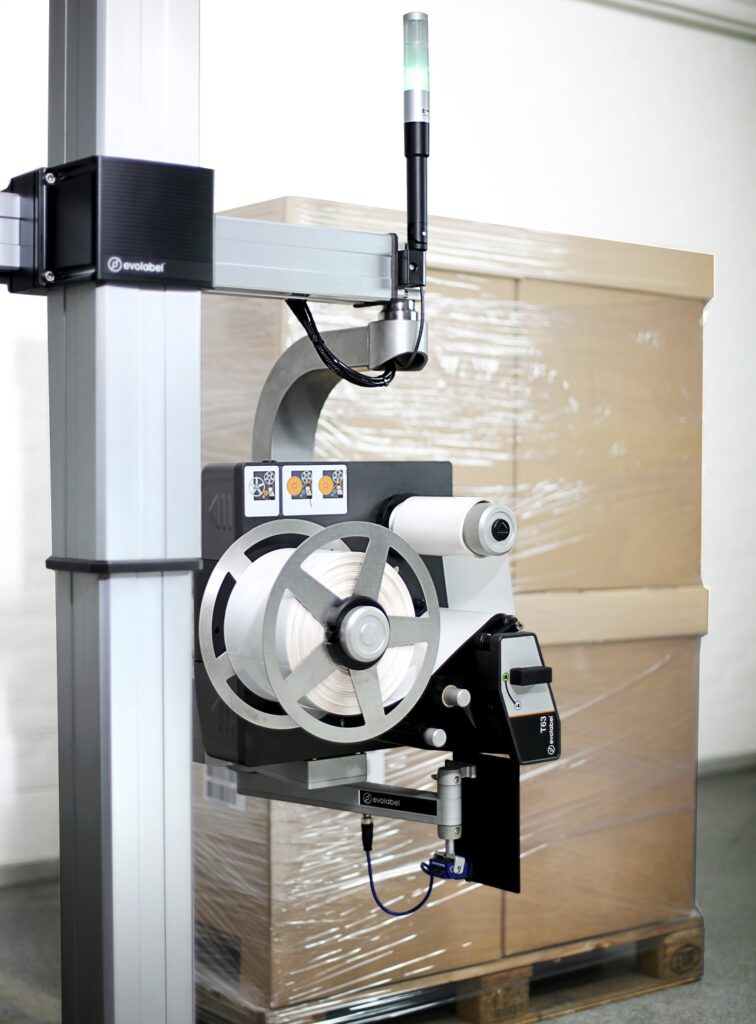
Industrial Labelling Systems (ILS) has marked its tenth year as the longstanding distributor of Evolabel™ products in the UK and Ireland, as the business continues to grow with the addition of two new support team members. Evolabel is a pioneer in print and apply systems, enabling fast and precise automatic labelling in production and warehousing. The company’s extensive range of machines have been distributed worldwide successfully by ILS over the last ten years. Since the partnership began in 2013, ILS has played a pivotal role in supplying Evolabel’s state-of-the-art technologies in North America, Europe and Australia. Food and drink, pharmaceutical and healthcare, automotive, e-commerce and logistics sectors, have all benefitted from the partnership, with countless businesses streamlining their labelling processes, increasing efficiency, and maintaining the highest standards of product labelling. Key to the partnership’s recent success has been the FlexWipe Pallet labeller, the first machine of its kind capable of operating at -28oC without the need for insulation or a heating cabinet. Recognising the importance of a pallet labelling system that performs seamlessly even in extreme conditions, ILS and Evolabel collaborated closely to verify the suitability of the Flexwipe for such demands. With the support of ILS, Evolabel conducted tests on the Flexwipe Pallet labeller within frozen containers, simulating a real cold chain environment. Throughout this two-month testing period, the team monitored the system’s functionality, ensuring the solution would work for customers operating in subzero temperatures. As a result of this trial, ILS and Evolabel’s collaboration brought a pallet labelling solution which is setting new standards in the cold chain industry. With its ability to apply labels non-stop in often harsh operational environments, the FlexWipe Pallet labeller is helping remove employees from these conditions, increasing site safety and production efficiently. To date ILS has successfully deployed more than 80 FlexWipe systems in locations such as North America, France, Germany, Italy, Belgium, Britain, Denmark, Holland and Australia. “Our partnership with ILS has been integral to building sales of Evolabel machines over the past 10 years,” said Martin Selin Dijkstra, Marketing Manager at Evolabel. “The team at ILS are partners in the truest sense, not only selling our machines but also working with us to ensure we develop what our customers want. We are delighted with the success of the first 10 years working together and look forward to the next 10 and beyond.” As one of the UK’s leading suppliers of automatic print and apply labellers, ILS operates from an 11,000sq ft facility in Middleton, near Manchester. Having celebrated its twentieth anniversary in 2022, the company has seen significant growth and appointed two Technical Support Engineers to strengthen its operations. Chris Cheshire joins ILS having previously worked for materials handling software provider, Dematic. In addition, his experience in the use of conveyor systems will prove invaluable for incorporating labelling successfully across clients’ production lines. Kenny Docherty brings his expertise in maintenance engineering to the business, having worked for a global food and beverage manufacturer using Evolabel’s machines for over 10 years. Denis Brett, Managing Director at ILS, concluded; “We are immensely proud of our successful partnership with Evolabel, delivering their market leading print and apply systems across the UK, Ireland and beyond. “By continuing to invest in our team we will make sure that we deliver the service our partners know ILS for, and we look forward to expanding our reach and ensuring that businesses receive the best labelling technology and support.”
AIT Worldwide Logistics unveils Middle Mile Network connecting major US metro areas via strategic gateway city hubs
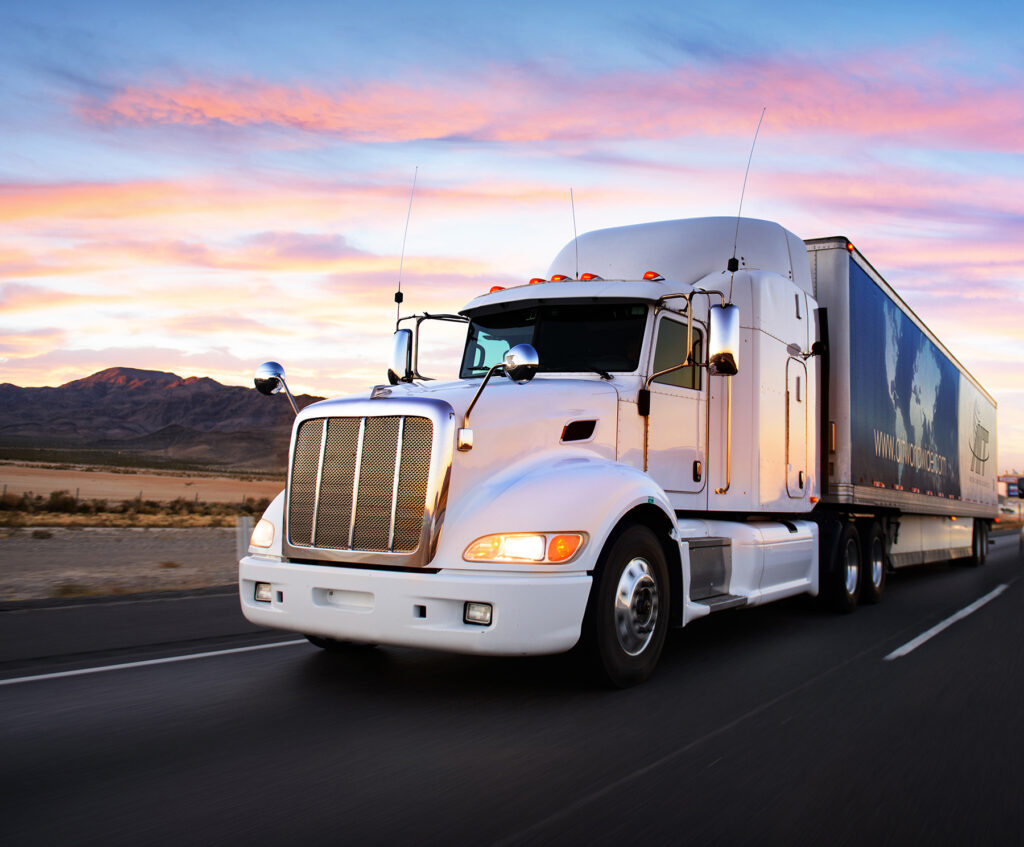
New solution delivers an affordable, more secure, speedier alternative to traditional expedited less-than-truckload service Global supply chain solutions leader, AIT Worldwide Logistics, has announced the launch of its innovative Middle Mile Network, a groundbreaking service in the logistics landscape offering a faster, more secure, and cost-effective alternative to traditional expedited less-than-truckload (LTL) services on vital routes covering more than 90% of major U.S. metropolitan areas. This network, particularly beneficial for customers importing goods to North America, represents the culmination of extensive strategic planning and execution that AIT began in 2021.The service connects major markets across the United States by serving more than 160 lanes every week, with hubs strategically located in import/export gateway cities like Atlanta, Chicago, Columbus, Dallas, and Los Angeles. “In a market where industry consolidation is limiting options and potentially reducing service quality, AIT stands out by offering a robust, internally controlled network,” AIT’s Chief Business Officer, Greg Weigel, said. “This initiative is not about rapid, unchecked expansion; it’s about providing a consistently higher standard of service that connects with AIT’s first and final mile options to deliver a world-class, end-to-end supply chain solution for our customers.” One of the key benefits of this new service is speed and efficiency. The Middle Mile Network significantly reduces dwell time – the number of hours a shipment waits from when it’s dropped off at a hub until beginning the middle mile segment of its lifecycle. By continuously monitoring network efficiency and adjusting to reduce dwell time, the Middle Mile Network’s average transit time is one to two days less in comparison to typical expedited LTL service. “Transparency and precision in our operations set us apart,” said AIT’s Sr. Vice President, Americas, Ryan Carter. “Measuring dwell time at the shipment level is a unique feature of our operation and the Middle Mile Network is making significant cycle time improvements for some of the world’s largest and most discerning supply chain clients. We’re able to ensure exceptional service reliability because our uncompromising dedication to monitoring quality metrics enables us to proactively identify and resolve potential issues.” AIT’s direct handling approach also means there is no comingling of freight from other providers within the hub network. That fact, combined with fewer freight touches, results in a remarkably low claim ratio. Carter adds that the service’s scalability and flexibility are designed to adapt seamlessly to customer demand, because the Middle Mile Network was conceived to quickly redistribute resources as needed to align with shippers’ demands. AIT’s Middle Mile Network is especially effective for transporting heavy, dense freight across various sectors, including automotive parts, healthcare equipment, industrial machinery components, and technology hardware like server racks. In the past year alone, AIT has seen a 60% year-over-year volume increase, with an impressive 98.7% on-time performance for deliveries between hubs. In the near future, AIT will be expanding the Middle Mile Network with new hubs in additional strategic locations across the United States. The company also expects to extend the network into Canada and Mexico to better support cross-border demand from customers who are increasingly relying on nearshoring as part of their sourcing strategy.
H&E relocates branch in Atlanta

Effective November 10, 2023, H&E Equipment Services Inc. (H&E) announces the relocation of its Atlanta, GA, branch. The facility is now located at 3160 Ellenwood Industrial Drive, Ellenwood, GA 30294-3550, phone 678-418-0046. The newly renovated property includes a fully fenced yard area, offices, and a separate repair shop and carries a variety of construction and general industrial equipment. “Our new facility is just 15 miles southwest of our previous address, with more direct access to downtown and job sites across the metro area via I-675 and other major roadways. Moving equipment to customers is now even easier and quicker, and we have a larger, more efficient yard that holds a greater inventory of fleet,” says Branch Manager Justin McKelvey. “Working with our Fairburn, Marietta, and Suwanee branches, we cover all sides of the Atlanta metro area and will pull together to quickly locate available equipment and provide faster response time. We’re in a great position to serve the entire city and surrounding suburbs.” The Atlanta branch specializes in the rental of aerial lifts, earthmoving equipment, telescopic forklifts, compaction equipment, generators, light towers, compressors, and more and represents the following manufacturers: Allmand, Atlas Copco, Bomag, Case, Club Car, Cushman, Doosan, Gehl, Generac Mobile, Genie, Hamm, Hilti, Husqvarna, JCB, JLG, John Deere, Kobelco, Kubota, LayMor, Ledwell, Lincoln Electric, Link-Belt Excavators, MEC, Miller, Multiquip, Polaris, Sany, Skyjack, SkyTrak, Sullair, Sullivan-Palatek, Tag, Towmaster, Unicarriers, Wacker Neuson, Yanmar, and others.
Eagle Mark 4 opens third facility, expanding its national operations
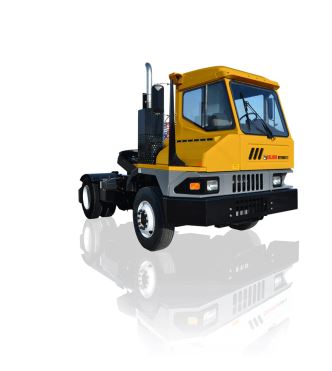
Eagle Mark 4, a Kalmar Ottawa Premier Partner, has announced the opening of a new facility on the West Coast of the United States. The strategic expansion is a testament to their commitment to meeting the evolving needs of their valued customers. The new facility, regionally located in Albuquerque, New Mexico will play a pivotal role in enhancing the company’s ability to serve customers on the West Coast and beyond. It will feature dedicated customer support teams, and a streamlined logistics system to ensure faster delivery times, improved product availability, and exceptional service quality. “Expanding to the West Coast is a significant milestone for Eagle Mark 4,” said Mike Tozzi, Eagle Mark 4 President. “We recognize the growing demand for our products and services in this region, and this new facility will allow us to better support our existing customers while reaching new ones. Our mission has always been to provide top-notch solutions and unparalleled customer support, and this expansion reinforces that commitment.” The new facility at 2108 Candelaria Rd NE, Albuquerque, NM 87107, will extend business hours from 7 a.m. – 7 p.m. EST, servicing multiple time zones with live in-house parts specialists. Customers can order at the Yard Truck Parts Store 24/7, with 95% of products shipped the same day. With Albuquerque being its first location in the West and the third location for the business, following its headquarters in Mansfield, Ohio, and second location in Fayetteville, North Carolina, this is a key milestone for Eagle Mark 4 as a leader of sales, service, rental, and parts in the yard truck industry.
Vertical Cold Storage breaks ground in Kansas City
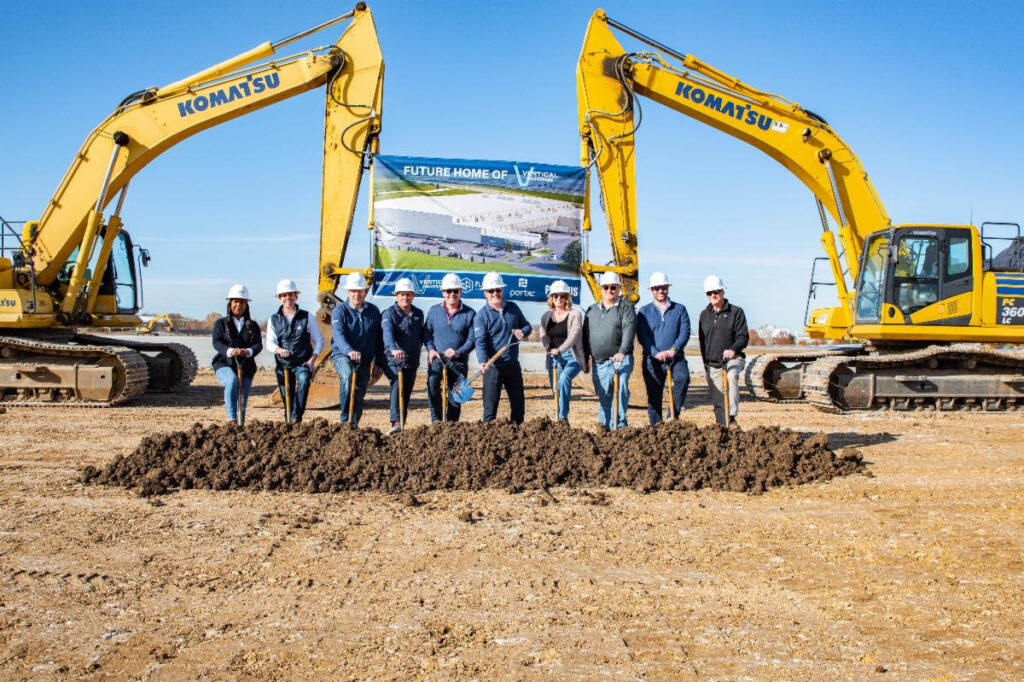
Centrally located Kansas City intermodal distribution center will be company’s eighth Vertical Cold Storage, a developer and operator of temperature-controlled distribution centers sponsored by real estate investment firm Platform Ventures, held a groundbreaking for its Kansas City multi-modal distribution site on November 14th. The facility is scheduled to be operational by the end of 2024 and employ up to 130 full-time team members. “Vertical Cold Storage is excited to deliver the first facility in Kansas City to offer the value-added services of blast freezing, case picking, and expedited intermodal transportation solutions adjacent to the CPKC intermodal terminal. Kansas City is an excellent location for customers interested in reducing their carbon footprint and transportation expense by leveraging new intermodal capacity for import/export or domestic transportation needs,” said West Hutchison, President and CEO of Vertical Cold Storage. “Most cold storage operators are moving away from value added services like blast freezing and case picking, but our team of life-long cold storage operators embrace these complexities and are looking forward to utilizing our best-in-class processes, IT solutions, robotic material handling equipment and AI technology to provide efficient and safe service to our customers.” The site, located adjacent to the CPKC intermodal terminal in south Kansas City, MO, will have 300,000+ sq. ft, ~50,000 pallet positions, state-of-the-art blast freezing technology and four rooms convertible to -20° F. The building design and construction utilize innovative materials and systems that reduce energy consumption. In addition to the site’s adjacency to CPKC’s intermodal terminal, it is centrally located within 30 miles of the BNSF, Union Pacific, and Norfolk Southern terminals, enabling intermodal access to or from anywhere in North America from the heartland of the USA. Primus Builders is the lead contractor for the project, which is expected to employ 150 workers during the construction. “The Vertical Cold team has collaborated closely with our partners and the Kansas City government to develop an advanced multi-modal center, effectively addressing the supply chain challenges of our customers. This facility supports sustainability within the community and environmental friendliness, all while delivering lasting value to our investors. As proud Kansas City natives, we are thrilled to see the initial Vertical Cold build in our backyard,” said Ryan Anderson, Co-President & Co-Founder of Platform Ventures.
ARA’s quarterly forecast shows increased optimism, slower growth and resilient markets
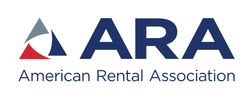
Rental revenue projections increase in U.S. and Canada heading into 2024 In its updated forecast, the American Rental Association (ARA) indicates that United States equipment rental industry’s growth will soften but still grow. Last quarter, the year-over-year growth was expected to be 7.6% in 2023 and 3.1% in 2024. The most current projections indicate 11.8% growth in 2023 totaling $71.5 billion in construction and general tool rental revenue. As for 2024, a 7.1% revenue increase is now expected. This forecast includes both traditional and specialty as the new industry measure. Last quarter the association corrected the forecast that underestimated non-residential construction spending by at least 20% and ‘specialty rental’ in overall rental revenues. “We are more bullish this quarter than last quarter,” says Scott Hazelton, managing director at S&P Global. “We are seeing a decent uptick with inflation moderating and our projections are relatively similar — stagnant but strong. It’s important to note that there will be more growth in construction and industrial equipment (CIE) than in general tool.” Earlier in the year, the forecast predicted a recession that did not materialize. While the first two quarters of the year proved slow, third quarter revenues are very strong, and the quarter four projections appear that way as well. “The biggest change is in the general tool revenue projection,” Hazelton says. “This is probably a function of timing with manufacturing strikes and that the housing market has been more resilient than we thought it would be. People are renovating homes because they are staying in them and home values are trending upwards so there is incentive to invest in their homes.” Canadian equipment rental revenue growth is higher in 2023 compared to last quarter’s projections due to inflation and resilient demand. The CIE outlook in Canada is slower growth with strong levels of activity in 2024, that is a 3.7% revenue increase, making it a $4.5 billion industry with stronger growth anticipated in outbound years, a 7.2% revenue increase in 2025 and 5.7% in 2026. There are some very real issues with Canada’s housing market and that is the primary cause of the revenue decline in 2023, totaling $971 million. In 2024, the projected general tool revenue will total $963 million, a 0.9% decline from 2023. ARA’s quarterly member survey showed conflicting results amongst members with half of respondents saying they expect to see a revenue increase in quarter four and half expecting a revenue decrease. This quarter there was also an increase in members who believe the situation for business is more stagnant. For more in-depth economic data, visit www.ARArental.org/ara-rentalytics, to learn more about RentalyticsTM.
Emerson debuts LED Wall Pack Luminaires for Commercial and Industrial Buildings
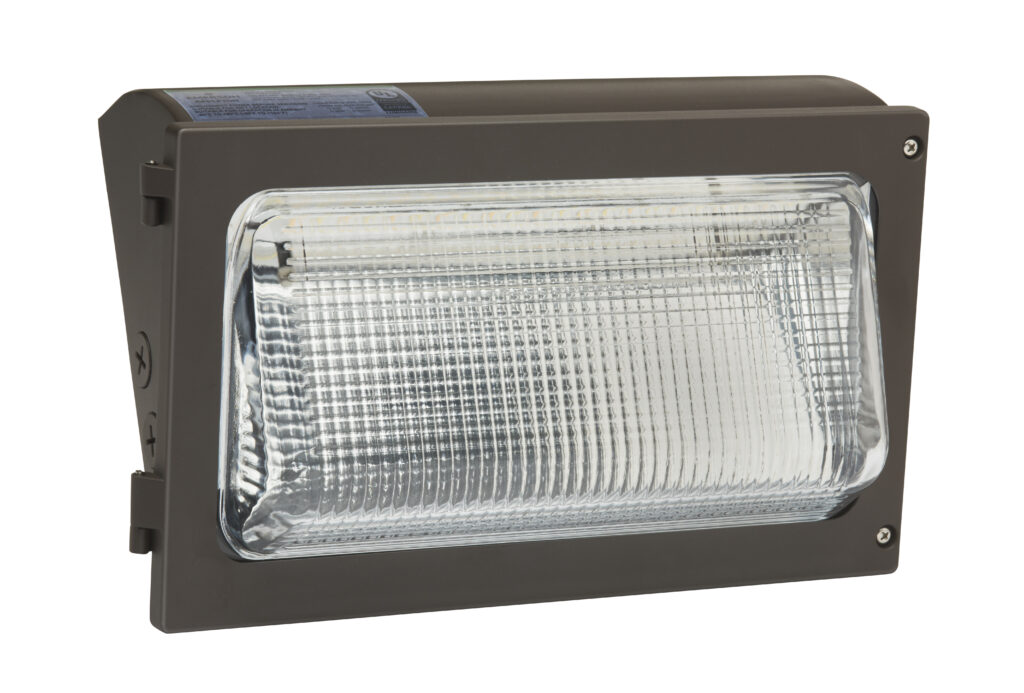
Appleton LED luminaires are ideal for retrofitting legacy HID wall packs to achieve lower energy consumption and reduced maintenance costs Emerson has introduced Appleton™ IWL weatherproof luminaires, a new line of energy-efficient LED wall packs that meet the security, sustainability, and lighting output requirements of modern commercial and industrial facilities. Appleton IWL luminaires ensure safety for people and property by providing up to 15,000 lumens of optimally distributed light when mounted on building exteriors and at outdoor entrances. With the fixture’s nine field-selectable settings, installers can precisely match color temperatures and brightness levels to large or small outdoor areas. When compared to conventional wall pack lighting, Appleton IWL luminaires offer notably better performance and dependability, particularly in applications where condensation and humidity are present. Appleton IWL luminaires are housed in a tough cast aluminum enclosure lined with silicone rubber gasketing and secured by stainless-steel bolts and pins, in contrast to standard wall pack lighting, which is enclosed in plastic. An IP65 ingress certification qualifies IWL luminaires for harsh outdoor areas in power generation plants, steel makers, cement, stone, and sand production sites, shipbuilding and marinas, pulp and paper plants, and foundries. Dependability is further strengthened by a broad temperature range of -40°C to +40°C (-40°F to 104°F). “Wall packs are routinely damaged by outdoor environments, requiring frequent repairs and total fixture replacements. Also, the safety of employees is compromised when a wall pack is non-operational,” explained Frank Cunningham, senior product marketing manager at Emerson. “Appleton IWL weatherproof luminaires are hardened to withstand outdoor environments without needing maintenance, and the housing design keeps water from damaging internal components. Plus, by harnessing LED as a light source, relamping is all but eliminated, reducing labor hours and lowering costs.” Upgrading HID Fixtures to LED Technology Facilities can decrease their energy consumption by up to 75% by replacing outdated HID wall pack fixtures with Appleton IWL luminaires incorporating LED technology. Depending on the model, the new luminaires deliver 5,000, 10,000 or 15,000 nominal lumens with 121 to 165 lumens per Watt (lm/W), equivalent in lighting output to 100-watt to 400-watt HID wall packs. In addition, wall packs are typically mounted several floors high in hard-to-reach areas, therefore requiring electricians to climb into bucket trucks or lifts to perform maintenance. Appleton IWL wall packs offer greater reliability and a much longer lifespan than HID — 130,000 hours versus 20,000 hours on average — translating into virtually zero maintenance, lower labor costs, minimal downtime, and less risk to plant electricians. Appleton IWL Series LED wall packs offer three field selectable color temperatures (CCT): 5000K Cool White, 4000K Neutral White, or 3000K Warm White along with wattage levels of low (5000W), mid (10,000W) and high (15,000W), covering nine possible lumen and color temperature combinations.
Episode 436: E-commerce fulfillment with Brendan Heegan of Boxzooka
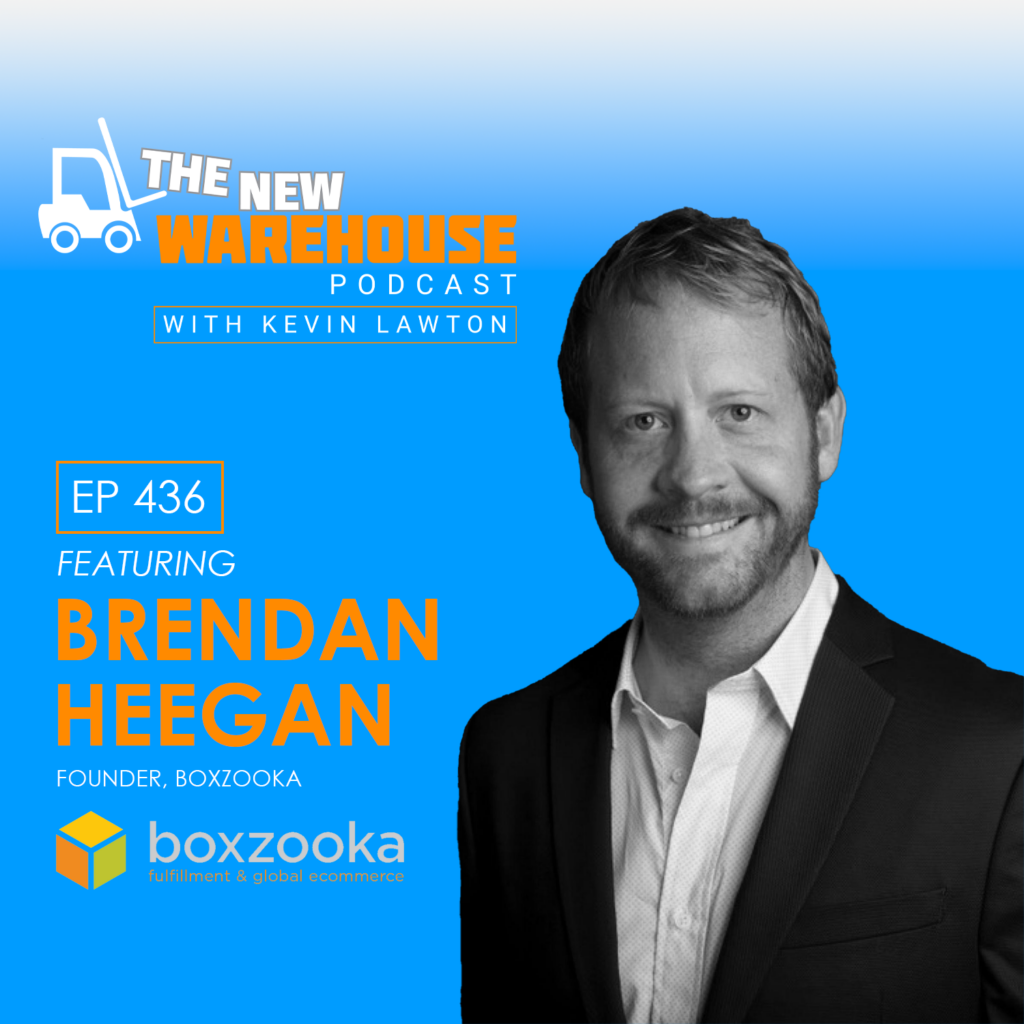
In the latest episode of The New Warehouse podcast, Brendan Heegan, Founder and CEO of Boxzooka, joins the show. With its innovative approach to e-commerce and B2B distribution, particularly in fashion and high-end consumer goods, Boxzooka is redefining the warehousing industry. In this episode, Heegan shares insights into Boxzooka’s unique strategies, their in-house developed Warehouse Management System (WMS), and how they shape the future of e-commerce fulfillment. Listen to the full episode to uncover the cutting-edge practices setting Boxzooka apart in the warehousing world. The Genesis and Evolution of Boxzooka Boxzooka’s journey began with an inventive idea and evolved into a warehousing powerhouse. Heegan’s background in transportation logistics laid the foundation for Boxzooka, initially a software for international landed costs, which organically pivoted into a full-fledged Third-Party Logistics (3PL) provider. Heegan highlights, “We started with software… and evolved into a 3PL.” This transition underscores Boxzooka’s adaptability and forward-thinking approach in the warehousing industry. Innovating with an In-House Developed WMS A pivotal aspect of Boxzooka’s success is its in-house developed WMS. This strategic move provided unmatched flexibility, allowing them to adapt to client needs and technological advancements quickly. “Our in-house WMS is our key to being flexible and nimble,” explains Heegan. This approach not only streamlines operations but also positions Boxzooka as a leader in warehouse technology innovation. Heegan adds, “A lot of 3PLs use out-of-the-shelf systems that are third-party systems that they’re handcuffed to whatever that system can or cannot do. At Boxzilla, engineers sit on-site at our headquarters in New Jersey, constantly enhancing the system.” How Boxzooka Elevates the Unboxing Experience Boxzooka’s commitment to an ‘elevated unboxing experience’ sets them apart in the 3PL industry. This concept goes beyond packaging, focusing on creating memorable experiences for end consumers. Heegan says, “We’re in the brand protection business…ensuring an elevated experience from warehouse to unboxing.” This approach has earned Boxzooka a reputation for excellence and customer satisfaction. Key Takeaways from Boxzooka Adaptive Business Model: Boxzooka’s evolution from a software solution to a comprehensive 3PL provider showcases their adaptability and innovative spirit. Technological Forefront: The development of an in-house WMS by Boxzooka underscores their commitment to technological advancement and operational efficiency. Focus on Customer Experience: Boxzooka’s unique focus on an elevated unboxing experience illustrates their commitment to quality and brand representation in the e-commerce sector. The New Warehouse Podcast EP 436: E-commerce Fulfillment with Brendan Heegan of Boxzooka
A Veteran’s Story: Toyota Material Handling dealer delivers loaded container handler to U.S. Army
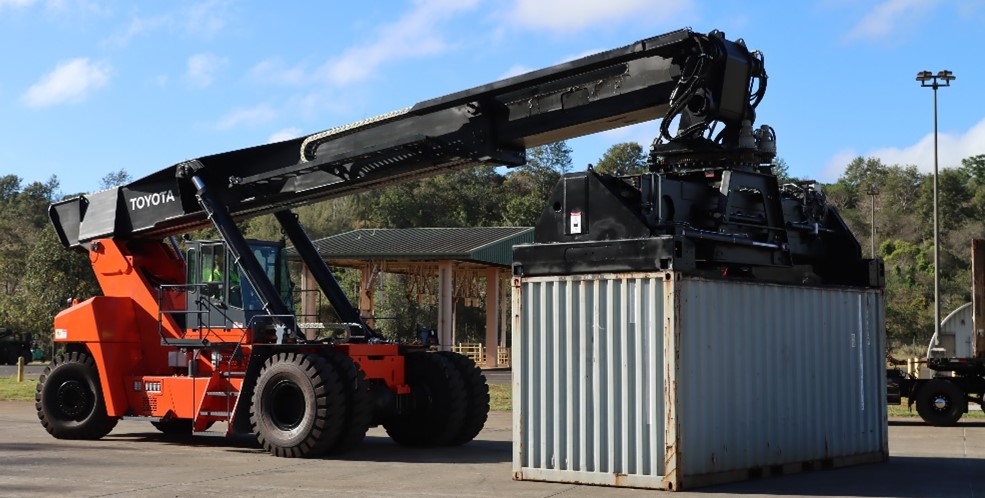
In recognition of Veteran’s Day, Toyota Material Handling is highlighting a special story involving one of its dealers – Toyota Material Handling Northern California – and a U.S. military base in Hawaii. Read the full story about a Vietnam veteran who is still finding new ways to support American troops. Rich Andres knows from experience how important it is for our troops to have the most reliable equipment on the market. Andres, the founder and chairman of Toyota Material Handling Northern California, served in the U.S. Marine Corps during the Vietnam War in the late 1960s. Recently, Andres and Toyota Material Handling Northern California delivered a Loaded Container Handler to a U.S. military base in Oahu, Hawaii, to support contingency operations, local training and deployments for the Army. “This truck will help our operations tremendously and ensure we can make all of our large movements much more efficiently, including fully-loaded shipping containers,” said Melvin Wright of U.S. Army Field Support Brigade LRC 402 Hawaii. “This truck will move all of those important containers, place them on the flatbed truck, and then they’ll be transported down to the port at Pearl Harbor. It’s going to make a big difference for us and save a significant amount of time.” Andres’ story is one centered on family and driven by discipline and sacrifice. His father served in the U.S. Navy before him, and his two sons – Mark and Stephen – now run the successful material handling business he started more than 25 years ago. That’s what made this deal so special. By providing a quality piece of equipment to support the soldiers at Schofield Barracks and Wheeler Army Airfield in Hawaii, Andres says he still wants to do whatever he can to support American troops. “It makes me proud to participate in something with the military,” Andres said. “It’s a great opportunity for us to represent Toyota with the U.S. government. If I was still in the service and I was operating something like this container handler, I would have a high level of confidence in it because of its quality.” Getting the Loaded Container Handler to the Army base in Hawaii wasn’t easy. The product weighs over 175,000 pounds and features a lift capacity up to 90,000 pounds, so it had to be built, disassembled for shipment, and then reassembled once in Hawaii. Several members of the Toyota Material Handling Northern California team traveled to East Chicago, Indiana, where Toyota Heavy Duty forklifts are built, to study, learn, and practice everything needed to know about properly taking the product apart and putting it back together again. Those same professionals traveled to Hawaii to not only reassemble the equipment upon arrival, but fully train the customer on how to use the massive unit. It’s that level of commitment and attention to detail Andres learned during his time in the military and carried with him throughout his material handling career. Andres and his sons instill those same principles into every person that comes to work for them at Toyota Material Handling Northern California. In many ways, those principles connect the military way with the Toyota Way. “There’s definitely an interesting parallel between the two,” Andres said. “They are both driven by processes that have been proven to be successful over a long period of time. In my career, the former military people I’ve hired have had those same values and have been the most successful in the company. The things they brought with them – the things they helped lead with – made the company successful.” Andres joined the Marine Corps with his three best friends in 1967, initially serving as a motor pool mechanic after completing boot camp. But Andres thought he could do even more to serve his country. He tried multiple times to join the troops in Vietnam, and just four months after joining the Marine Corps, Andres succeeded in that effort. After completing his infantry training, Andres was a member of a motor transport unit in Vietnam. His unit joined what is known as the ‘Siege of Khe Sanh’ in early 1968, a 77-day battle in Kasan, Vietnam, that claimed the life of Andres’ unit chief. Andres was thrust into a leadership role as the Motor Transport Chief and successfully led his soldiers until he left the Marine Corps in 1969. Andres initially planned to take some time off after returning from war, but says he wanted to get to work. So Andres started sweeping floors and delivering parts for a local forklift company where he spent five years and worked his way up to a parts manager position. Andres would end up working for two more forklift companies after that, the second beginning in 1985 for the then-called Perin Company, which was founded in 1921 and was the second-oldest Toyota dealer in the country at the time. In 1997, Andres partnered with Toyota Material Handling to buy Perin Company and renamed it Toyota Material Handling Northern California. The Andres family has successfully grown the business in the 26 years since with existing locations in Livermore, Fresno, West Sacramento and Salinas, California. “The whole experience of being in the Marine Corps helped me to get where I am,” Andres said. “It taught me about the determination you need to succeed and showed me what it’s like when somebody always has your back. I wasn’t satisfied just working – I wanted to do something bigger. “I like to lead by example. From being thrust into being the chief of my unit in Vietnam and all throughout my career, I’ve set my sights on specific things and had the determination required to follow through and reach them.” One example Andres leads by is how he treats days of remembrance, like Memorial Day and Veteran’s Day. He doesn’t want the sacrifice of so many men and women to go unnoticed by anyone. “Every year, I send out messages on these special days to let people know the importance of our troops
American Staffing Association celebrates National Apprenticeship Week
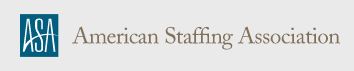
The American Staffing Association celebrates the start of National Apprenticeship Week. “Apprenticeships are a commonsense, cost-effective way for job seekers to learn the skills they need to fill the most in-demand jobs in the labor market,” said Richard Wahlquist, chief executive officer at ASA. “Apprenticeships provide job seekers with unique opportunities to earn while they learn skills that can lead to good-paying careers. “Every year, staffing firms around the country connect job seekers with unique apprenticeship opportunities in sectors all across the labor market. “Our country continues to face a skills gap crisis. Right now, there are 1.5 job openings for every unemployed person in this country. If our nation wants to successfully train the workforces of today and tomorrow, it is imperative that we expand access to apprenticeships.”
H&E opens new branch in Conroe, Texas
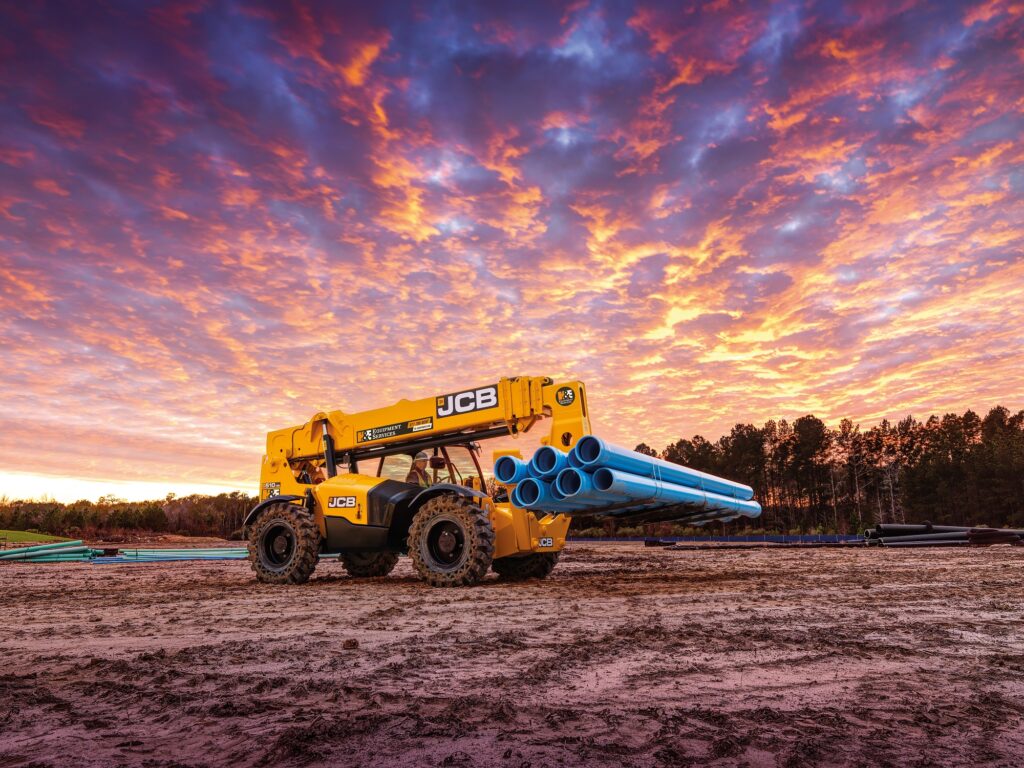
Effective November 13, 2023, H&E Equipment Services Inc. (H&E) announces the opening of its Conroe branch, its fifth rental location in the greater Houston market and the 25th in the state of Texas. Since the beginning of the second quarter of 2023, H&E has opened 14 new branches across the country, with four of those in the Lone Star State. The facility is located at 530 Frazier Commerce Drive, Conroe, TX 77303-5380, phone 936-286-3900. It includes a fully fenced yard area, offices, and a repair shop and carries a variety of construction and general industrial equipment. “The location of our Conroe branch gives H&E total coverage of the Houston area, especially the growing market north of the Woodlands. The new facility covers the territory between our Houston, Katy, and Bryan branches, so customers in outlying areas have more convenient service” says Branch Manager Tesha McGruder. “Our close proximity to I-45, state highways 105 and 75, and other major roadways is ideal for getting our new fleet to job sites quickly.” The Conroe branch specializes in the rental of aerial lifts, earthmoving equipment, telescopic forklifts, compaction equipment, generators, light towers, compressors, and more and represents the following manufacturers: Allmand, Atlas Copco, Bomag, Case, Club Car, Cushman, Doosan, Gehl, Generac Mobile, Genie, Hamm, Hilti, Husqvarna, JCB, JLG, John Deere, Kobelco, Kubota, LayMor, Ledwell, Lincoln Electric, Link-Belt Excavators, MEC, Miller, Multiquip, Polaris, Sany, Skyjack, SkyTrak, Sullair, Sullivan-Palatek, Tag, Towmaster, Unicarriers, Wacker Neuson, Yanmar, and others.
September 2023 Manufacturing Technology Orders down and still above historical averages
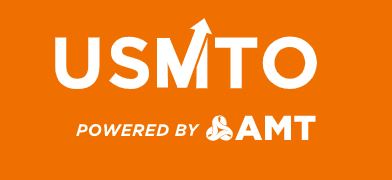
New orders of manufacturing technology totaled $398.9 million in September 2023, according to the latest U.S. Manufacturing Technology Orders Report published by AMT – The Association For Manufacturing Technology. September orders declined 2.8% from August 2023 and 23.4% from September 2022. Year-to-date orders reached $3.64 billion, 13.8% lower than the first three quarters of 2022. “Though 2023 orders are down, activity is still above long-term historical averages, indicating relative health overall,”said Douglas K. Woods, president of AMT. “We are still seeing strength in key industries, with contract machine shops, medical, and automotive continuing to invest heavily in manufacturing technology.” Contract machine shops increased order value by nearly a third while units ordered grew by a much smaller degree. Similarly, manufacturers of medical supplies dramatically increased their overall spending. The automotive sector also continued to increase orders. Because of the longer production horizon as well as a sustained increase in demand for new vehicles, automotive manufacturers made capital spending investments despite labor challenges. “The disparity in manufacturing technology investment across industries indicates that not all are paring back capital spending at once,” said Woods. “Industries that are spending healthily on manufacturing tech appear to be shifting expenditures toward highly automated machinery as evidenced by rising per-unit values.” Though year-to-date orders have declined compared to a strong 2022, order levels are above historical averages, and there are pockets of strength in several industries. “Industries supported by high consumer demand and benefiting from long production timelines continued to be reliable customers of manufacturing technology,” said Woods. “We are detecting a shift in capital goods investment toward improving productivity through adoption of manufacturing technology automation.”
OZ Lifting Launches Davit Crane Wheelbase
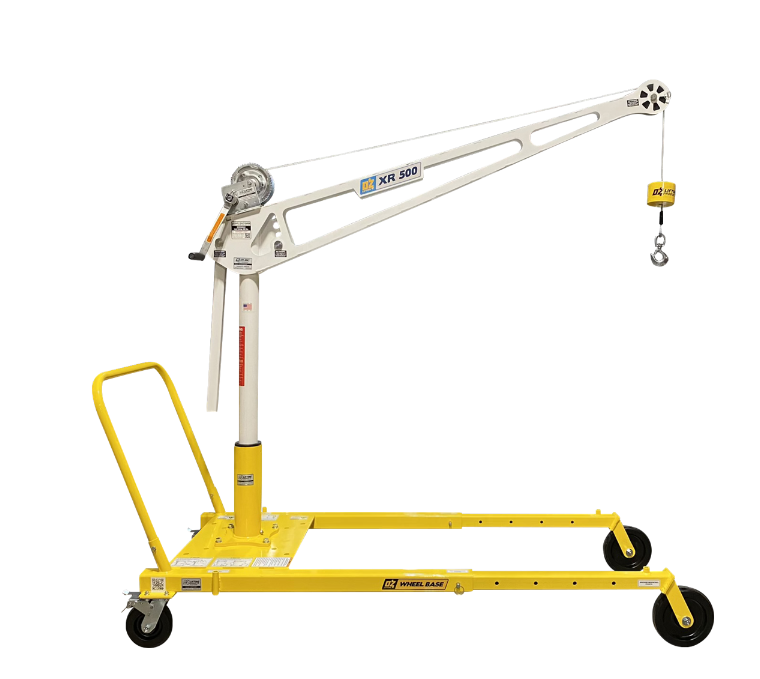
Winona, Minnesota-based OZ Lifting Products LLC has launched a wheelbase that can be used with its full range of davit cranes up to 1,200 lbs. capacity. The USA-made wheelbase is adjustable and has four different length positions: it measures from 56.57” to 77.57” long; 32.44” wide; and 36.87” high. It weighs 140 lbs. when fully assembled, without a crane’s pedestal base, so total weight will depend on the davit being used. Wheelbases will be shipped on a pallet and require assembly at the point of use. Offering durable steel construction with powder-coat finish, oversized casters make rolling the base and moving the crane easy. The wheel base features a patented floor anchoring system, which allows the davit to rotate 360 degrees, even when under load. The manufacturer will part-number and sell the wheelbases with the pedestal base to match the davit crane the user wants. This will make the process straightforward for the customer. Mobile crane Richard Miller, sales manager at OZ Lifting, said: “Demand for such a solution has steadily increased over the last few years. Our customers try to leverage the benefits of our lightweight davit cranes with the ability to use them in different ways and locations. The [wheel] base allows them to move the crane to various points within a facility; the applications are limitless. The main benefit is that users do not have to permanently mount a base at the pick location.” The base will be compatible with the majority of the company’s cranes, including the 500 lbs. and 1,200 lbs. capacity versions of the Tele-Pro, which allows users to leverage the benefits of other lifting technologies in its range while telescoping the boom in and out under load. (This line also features a 2,500 lbs. model, not suitable for use with the wheelbase.) It will also be widely utilized with the Alumi-Lite series of ultra-portable davit cranes, an aluminum series targeted specifically at applications where portability is beneficial; the XR Series; and the steel davit crane. In each of these cases, 500 lbs. and 1,000 lbs. models are available. The CompOZite and CompOZite Elite carbon fiber models, meanwhile, are both offered in 1,200 lbs. capacities. Safe use OZ Lifting will ship the wheelbase with a detailed operator’s manual, which highlights the dos and don’ts when using it. For example, the user must have the legs adjusted to the appropriate length, depending on the crane, so that the end of the boom is in line with the front wheels. The davit crane must also be locked in place using a special locking collar, so the boom doesn’t go outside the width of the legs, causing it to tip over. Miller said: “Only when the wheelbase is anchored using our patented system, can they rotate the davit crane when under load.” New wheels Having previewed the wheelbase at the recent Water Environment Federation’s Technical Exhibition & Conference (WEFTEC) in Chicago, OZ Lifting will show it at the AHR Expo (Booth S10534), which takes place January 22-24, 2024, also at McCormick Place. The wheelbase will be showcased alongside the full range of davits at an expo that attracts a delegation of heating, ventilation, air-conditioning, and refrigeration (HVACR) professionals.
61 New Food and Beverage Industry Planned Projects Continue Downward Slide
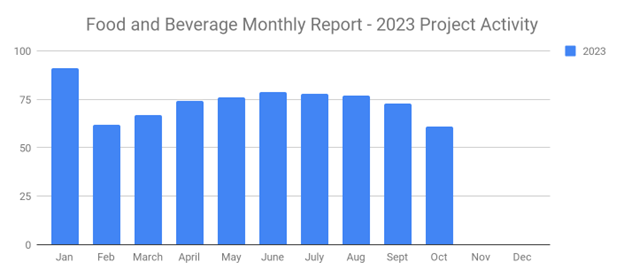
Industrial SalesLeads announced the October 2023 results for the new planned capital project spending report for the Food and Beverage industry. The Firm tracks North American planned industrial capital project activity; including facility expansions, new plant construction, and significant equipment modernization projects. Research confirms 61 new projects in the Food and Beverage sector. The following are selected highlights on new Food and Beverage industry construction news. Food and Beverage Project Type Processing Facilities – 33 New Projects Distribution and Industrial Warehouse – 34 New Projects Food and Beverage Project Scope/Activity New Construction – 27 New Projects Expansion – 25 New Projects Renovations/Equipment Upgrades – 17 New Projects Plant Closing – 1 New Project Food and Beverage Project Location (Top 10 States) California – 7 New York – 6 Texas – 5 Kentucky – 4 South Carolina – 4 Michigan – 3 North Carolina – 3 Wisconsin – 3 Arizona – 2 Florida – 2 Largest Planned Project During the month of October, our research team identified 5 new Food and Beverage facility construction projects with an estimated value of $100 million or more. The largest project is owned by Louis Dreyfus Company, who is planning to invest $500 million for the construction of a soybean processing plant in UPPER SANDUSKY, OH. Construction is expected to start in early 2024. Top 10 Tracked Food and Beverage Projects FLORIDA: Specialty food product MFR. is planning to invest $200 million for the construction of a 400,000 SF processing and distribution facility in ZEPHYRHILLS, FL. They are currently seeking approval for the project. Construction will occur in two phases, with completion slated for late 2024 and 2028 respectively. KENTUCKY: Snack food MFR. is planning to invest $137 million for the renovation and equipment upgrades on a 434,000 SF processing and distribution facility at 1391 Dixie Hwy. in LOUISVILLE, KY. They are currently seeking approval for the project. Completion is slated for Fall 2024. NEW YORK: Produce company is planning to invest $95 million for the construction of a 1.3 million SF warehouse and greenhouse facility at 5222 Junction Rd. in LOCKPORT, NY. They are currently seeking approval for the project. INDIANA: Restaurant chain is planning to invest $74 million for the construction of a processing and warehouse facility on Miami Trail in CHARLESTOWN, IN. They are currently seeking approval for the project. Completion is slated for 2025. NEW JERSEY: Foodservice distributor is planning to invest $29 million for the expansion of their distribution center at 301 Heron Dr Swedesboro in SWEDESBORO, NJ by 141,000 SF. Construction is expected to start in late 2023, with completion slated for late 2024. CALIFORNIA: Global retail chain is planning for the construction of a 900,000 SF distribution center in STOCKTON, CA. They are currently seeking approval for the project. Completion is slated for 2026. PENNSYLVANIA: Snack food MFR. has recently agreed to pre-lease a 650,000 SF distribution center in HANOVER, PA. They will relocate a portion of their operations upon completion in early 2025. TEXAS: Specialty food product MFR. is planning to invest $15 million for the construction of a 77,000 SF processing facility at 696 E. Owassa Rd. in SAN JUAN, TX. Construction is expected to start in late 2023, with completion slated for Summer 2025. MISSISSIPPI: Beverage development company is planning to invest $10 million for the construction of a 50,000 SF processing, warehouse, and laboratory facility in COLUMBUS, MS. Construction is expected to start in early 2024, with completion slated for early 2025. CALIFORNIA: Agricultural co-operative is planning for the expansion of their processing facility at 1300 N Washington Rd. in TURLOCK, CA by 100,000 SF. They have recently received approval for the project. About Industrial SalesLeads, Inc. Since 1959, Industrial SalesLeads, based in Jacksonville, FL is a leader in delivering industrial capital project intelligence and prospecting services for sales and marketing teams to ensure a predictable and scalable pipeline. Our Industrial Market Intelligence identifies timely insights on companies planning significant capital investments such as new construction, expansion, relocation, equipment modernization and plant closings in industrial facilities. The Outsourced Prospecting Services, an extension to your sales team, is designed to drive growth with qualified meetings and appointments for your internal sales team. Visit us at salesleadsinc.com.
NORD DRIVESYSTEMS Product Manager for MAXXDRIVE Industrial Drives receives AGMA Award
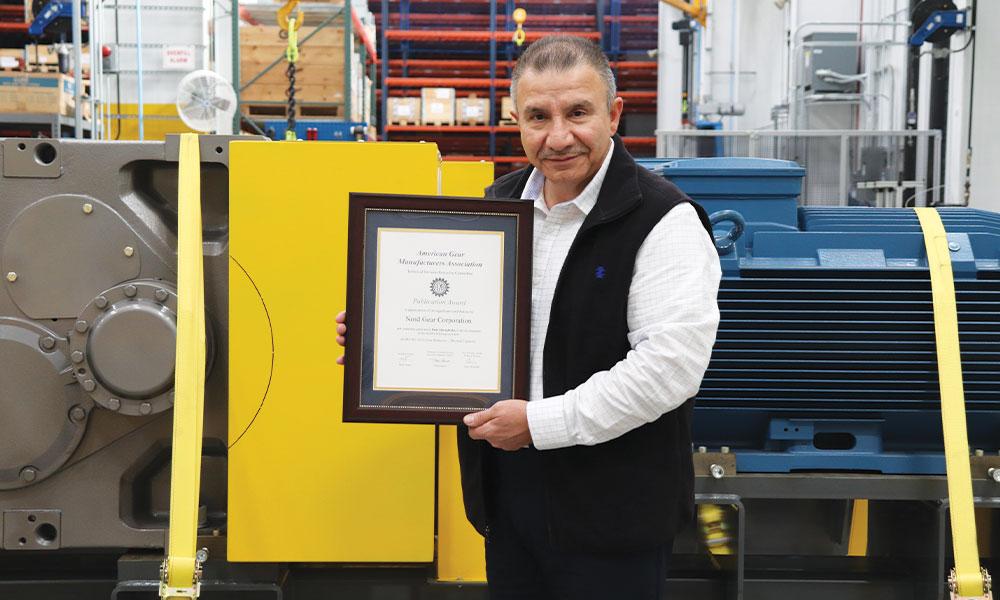
This Fall, the American Gear Manufacturers Association (AGMA) presented various awards during the 2023 Fall Technical Meeting (FTM) Awards Luncheon in Detroit, Michigan. Along with the Chairperson’s Award, awards were presented to AGMA technical committee members who have published a document within the last year. Hani Almoghrabi, Product Manager for MAXXDRIVE Industrial Gear Units at NORD DRIVESYSTEMS, was recognized for his contribution toward publishing AGMA 947-A23, Gear Reducers –Thermal Capacity. Ten other members of the AGMA Drives for Industrial Applications Committee also accepted awards for their work on the piece. “It was a pleasure working alongside my colleagues on the AGMA Enclosed Gear Committee to publish the AGMA 947-A23 Gear Reducers-Thermal Capacity information sheet,” Almoghrabi stated “we hope it will become an informative resource for the gear industry.” The published document utilizes an analytical heat balance model as a means of calculating the thermal transmittable power of a gear unit lubricated with mineral oil. The calculation is based on the standard conditions of 25°C (77°F) maximum ambient temperature and 95°C (203°F) maximum oil sump temperature in a large indoor space but also includes modifiers for calculation in other conditions. The first draft of AGMA 947-A23 was created in April 2019 and approved by the Technical Division Executive Committee in June 2023.
210 New Distribution and Supply Chain Planned Industrial Projects Start Q4 2023 with Familiar Q3 Results
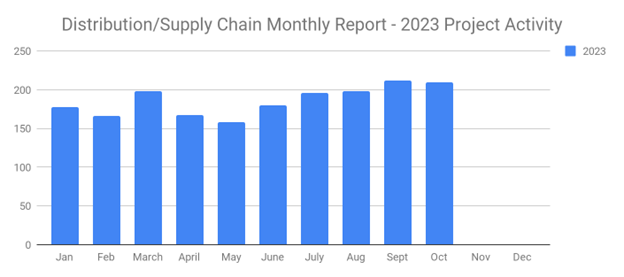
Industrial SalesLeads announced the October 2023 results for the new planned capital project spending report for the Distribution and Supply Chain industry. The Firm tracks North American planned industrial capital project activity; including facility expansions, new plant construction and significant equipment modernization projects. Research confirms 210 new projects in October, as compared to 212 in September. The following are selected highlights on new Distribution Center and Warehouse construction news. Distribution and Supply Chain – By Project Type Distribution/Fulfillment Centers – 24 New Projects Industrial Warehouse – 188 New Projects Distribution and Supply Chain- By Project Scope/Activity New Construction – 106 New Projects Expansion – 51 New Projects Renovations/Equipment Upgrades – 52 New Projects Closing – 8 New Projects Distribution and Supply Chain – By Project Location (Top 5 States) Texas – 17 California – 14 Florida – 14 New York – 14 Illinois – 13 Largest Planned Project During the month of October, our research team identified 6 new Distribution and Supply Chain facility construction projects with an estimated value of $100 million or more. The largest project is owned by Bauducco Foods, Inc., who is planning to invest $200 million for the construction of a 400,000 SF processing and distribution facility in ZEPHYRHILLS, FL. They are currently seeking approval for the project. Construction will occur in two phases, with completion slated for late 2024 and 2028 respectively. Top 10 Tracked Distribution and Supply Chain Project Opportunities OHIO: Battery recycling company is planning to invest $200 million for the expansion and equipment upgrades at their processing and warehouse facility in LANCASTER, OH. They have recently received approval for the project. ILLINOIS: Plastic resin MFR. is planning to invest $180 million for the construction of a 1.3 million SF warehouse complex on Orchard Road in MONTGOMERY, IL. They are currently seeking approval for the project. Construction will occur in 3 phases. KENTUCKY: Snack food MFR. is planning to invest $137 million for the renovation and equipment upgrades on a 434,000 SF processing and distribution facility at 1391 Dixie Hwy. in LOUISVILLE, KY. They are currently seeking approval for the project. Completion is slated for Fall 2024. ARKANSAS: Discount retail chain is planning to invest $100 million for the renovation and equipment upgrades on their 850,000 SF distribution center in WEST MEMPHIS, AR. Completion is slated for Fall 2024. SOUTH CAROLINA: Beverage distributor is planning to invest $100 million for the expansion of their processing and distribution facility in MOORE, SC. They are currently seeking approval for the project. Completion is slated for 2027. NEW YORK: Produce company is planning to invest $95 million for the construction of a 1.3 million sf warehouse and greenhouse facility at 5222 Junction Rd. in LOCKPORT, NY. They are currently seeking approval for the project. WISCONSIN: Biotechnology company is planning to invest $85 million for the expansion of their processing, warehouse, and office facility at 8402 Excelsior Dr. in MADISON, WI. They are currently seeking approval for the project and will relocate a portion of their operations upon completion. INDIANA: Restaurant chain is planning to invest $74 million for the construction of a processing and warehouse facility on Miami Trail in CHARLESTOWN, IN. They are currently seeking approval for the project. Completion is slated for 2025. TENNESSEE: Biotechnology company is planning to invest $65 million for the expansion and equipment upgrades of their processing and warehouse facility in NASHVILLE, TN. They have recently received approval for the project. ILLINOIS: Industrial components mfr. is planning to invest $50 million for a 200,000 SF expansion and equipment upgrades on their manufacturing, warehouse, and office facility in LAKE ZURICH, IL. They are currently seeking approval for the project. About Industrial SalesLeads, Inc. Since 1959, Industrial SalesLeads, based in Jacksonville, FL is a leader in delivering industrial capital project intelligence and prospecting services for sales and marketing teams to ensure a predictable and scalable pipeline. Our Industrial Market Intelligence identifies timely insights on companies planning significant capital investments such as new construction, expansion, relocation, equipment modernization and plant closings in industrial facilities. The Outsourced Prospecting Services, an extension to your sales team, is designed to drive growth with qualified meetings and appointments for your internal sales team. Visit us at salesleadsinc.com.
Ports of Long Beach and Los Angeles to make $60 Million available for Zero-Emissions Trucks
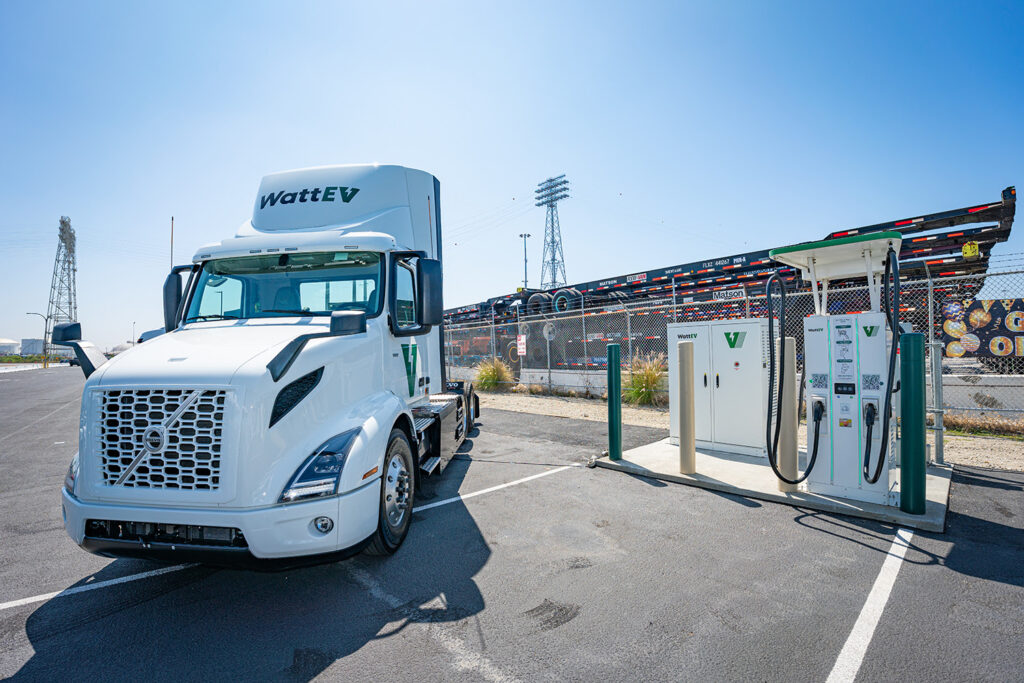
Partnership forged with California Air Resources Board, California Climate Investments and CALSTART incentive program The Port of Long Beach and the Port of Los Angeles will make $60 million in Clean Truck Fund Rate funding available through the California Hybrid and Zero-Emission Truck and Bus Voucher Incentive Project (HVIP) for vouchers toward the purchase of zero-emission, Class 8 drayage trucks that operate at the San Pedro Bay ports complex. The funds will be available to applicants starting at 10 a.m. Tuesday, Nov. 14, at californiahvip.org. Each port is providing $30 million through the Clean Truck Fund (CTF) Rate, which collects $10 per twenty-foot equivalent unit from cargo owners on loaded containers entering and exiting the port complex. The CTF Rate is a key component of the San Pedro Bay Ports Clean Air Action Plan goal of 100% zero-emissions drayage trucks by 2035. The voucher program utilizes the existing HVIP funding application process to provide incentive funding toward eligible zero-emissions truck purchases servicing the port complex. Launched by the California Air Resources Board, HVIP is part of California Climate Investments, a statewide initiative that puts billions of cap-and-trade dollars to work by reducing greenhouse gas emissions, strengthening the economy and improving public health and the environment – particularly in disadvantaged communities similar to those adjacent to the ports. Funding is administered by CALSTART, the current HVIP administrator, on a first-come, first-served basis. Voucher enhancements funded by the ports are $100,000 per truck for fleets with 10 or fewer trucks, and $75,000 for fleets with more than 10 trucks — additional to the HVIP drayage voucher amount of $150,000 per truck and any other applicable HVIP voucher enhancements. The highest potential voucher amount is $250,000 per truck. This funding will support the purchase and deployment of up to 800 new zero-emissions trucks. For a complete list of HVIP funding requirements, including the eligible trucks and dealers, visit californiahvip.org. For drayage purchasers who don’t meet the HVIP requirements for this specific funding – and for other types of vehicles – funds are still available through standard HVIP and other HVIP categories, including over $100 million in other drayage truck funds.