Industrial Construction News: Labs, and Power, Energy and Oil & Gas with Noticeable Increases in October 2023
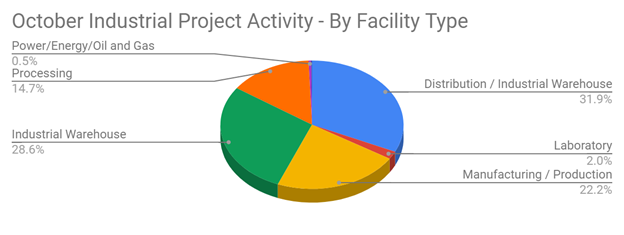
Research by Industrial SalesLeads experienced industrial market research team, shows 419 new planned industrial projects tracked during the month of November. Planned industrial project activity decreased by 4% from the previous month, however, there were noticeable increases in laboratory, Power / Energy / Oil & Gas. The following are selected highlights of new industrial construction news and project opportunities throughout North America. Planned Industrial Construction – By Project Type: Manufacturing Facilities – 146 New Projects Processing Facilities – 97 New Projects Distribution and Industrial Warehouse – 210 New Projects Power/Energy/Oil and Gas – 3 New Projects Laboratory Facilities – 13 New Projects Mine – 1 New Projects Terminal – 0 New Projects Pipeline – 0 New Projects Planned Industrial Construction – By Scope/Activity New Construction – 181 New Projects Expansion – 116 New Projects Renovations/Equipment Upgrades – 125 New Projects Plant Closing – 27 New Projects Planned Industrial Construction – By Location (Top 10 States) Texas – 28 New York – 26 Ohio – 21 Florida – 20 Indiana – 20 North Carolina – 20 Michigan – 19 Illinois – 17 Georgia – 13 Pennsylvania – 13 Largest Planned Industrial Construction Project During the month of November, our research team identified 31 new General Industrial facility construction projects with an estimated value of $100 million or more. The largest project is owned by Northvolt AB, which is planning to invest $5 billion in the construction of a manufacturing facility in MCMASTERVILLE, QC. They have recently received approval for the project. Completion is slated for late 2026. Top 10 Tracked Industrial Construction Projects ARKANSAS: Specialty gas company is planning to invest $3.5 billion for the construction of a gas-to-liquid processing plant in PINE BLUFF, AR. They are currently seeking approval for the project. Construction will occur in multiple phases, with completion slated for 2029. INDIANA: Automotive MFR. is planning to invest $3.2 billion for the construction of an EV battery manufacturing facility in KOKOMO, IN. Completion is slated for early 2027. MICHIGAN: Battery MFR. is planning to invest an additional $3 billion for the expansion of its manufacturing facility in HOLLAND, MI. They are currently seeking approval for the project. CALIFORNIA: University is planning to invest $2 billion for the construction of a 1.4 million SF space research and development center in MOUNTAIN VIEW, CA. They are currently seeking approval for the project. Completion is slated for 2027. LOUISIANA: Fertilizer MFR. is planning to invest $2 billion for the construction of a processing facility in ASCENSION PARISH, LA. They are currently seeking approval for the project. QUEBEC: Specialty steel MFR. is planning to invest $1.7 billion for the construction of a manufacturing facility in SEPT-ILES, QC. They are currently seeking approval for the project. Construction is expected to start in 2026, with completion slated for 2029. MASSACHUSETTS: Consumer goods mfr. is planning to invest $1 billion for the expansion, renovation, and equipment upgrades at its manufacturing facility in ANDOVER, MA. They will relocate their manufacturing operations from BOSTON, MA upon completion. The project includes the renovation of their corporate campus in BOSTON, MA. INDIANA: Solar panel MFR. is planning to invest $800 million for the construction of a manufacturing facility in JEFFERSONVILLE, IN. Completion is slated for late 2025. OHIO: Agricultural processing company is planning to invest $500 million in the construction of a soybean processing plant in UPPER SANDUSKY, OH. Construction is expected to start in early 2024. MICHIGAN: Hydrogen technology company is planning to invest $400 million for the construction of a 510,000 sf manufacturing facility in PLYMOUTH TOWNSHIP, MI. They are currently seeking approval for the project. About Industrial SalesLeads, Inc. Since 1959, Industrial SalesLeads, based in Jacksonville, FL is a leader in delivering industrial capital project intelligence and prospecting services for sales and marketing teams to ensure a predictable and scalable pipeline. Our Industrial Market Intelligence identifies timely insights on companies planning significant capital investments such as new construction, expansion, relocation, equipment modernization, and plant closings in industrial facilities. The Outsourced Prospecting Services, an extension to your sales team, is designed to drive growth with qualified meetings and appointments for your internal sales team. Visit us at salesleadsinc.com.
Emerson’s new edge solution for faster digital transformation
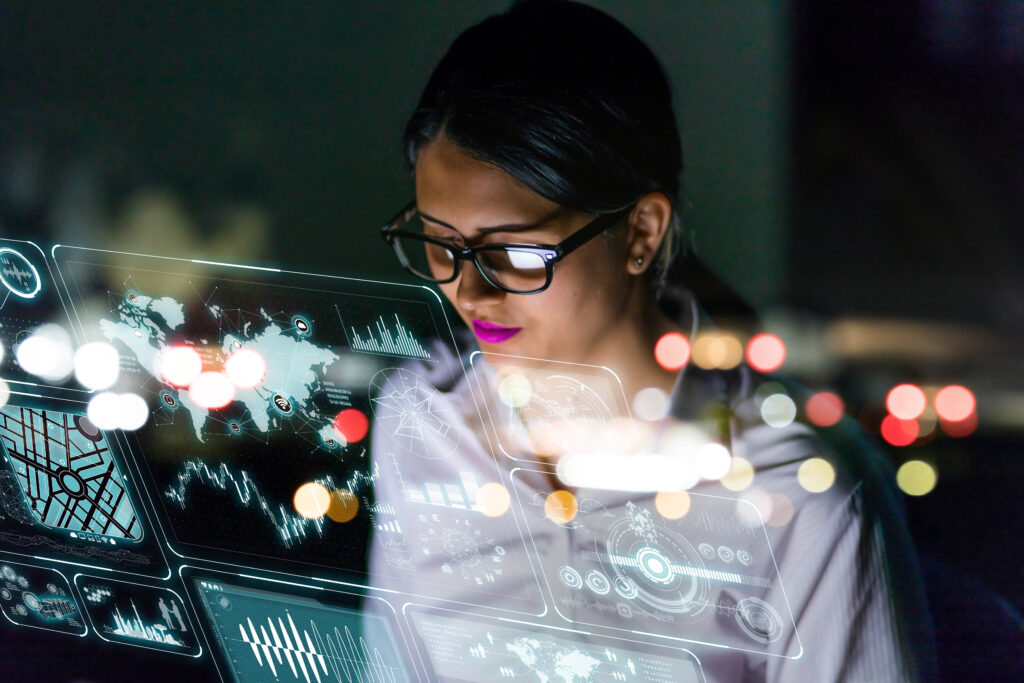
DeltaV Edge Environment provides a sandbox to deploy and run applications with easy, secure, contextualized data access Global technology and software provider Emerson has launched the DeltaV™ Edge Environment, a first-of-its-kind integrated software solution that expands the capabilities of the evolving DeltaV automation platform to provide an operational technology (OT) sandbox for data manipulation, analysis, organization, and more. Teams can deploy and execute applications to run key artificial intelligence (AI) engines and analytics close to the data source with seamless, secure connectivity to contextualized OT data across the cloud and enterprise. The DeltaV Edge Environment empowers teams to deliver operational improvements tied to productivity, sustainability, and other business objectives. Valuable data in intelligent devices, machines, and systems helps enable enterprise-wide analytics, expands operational insight, and feeds the AI engines catalyzing innovation. However, OT data is often trapped beneath layers of systems and networks, adding complexity and removing meaningful context. The DeltaV Edge Environment expands the horizons of the distributed control system (DCS), creating a secure data superhighway where users can seamlessly socialize contextualized data directly with cloud and enterprise applications while also leveraging a built-in execution sandbox—a testing environment for critical innovation tasks such as generating dashboards, running applications and training AI tools. “Operations and IT increasingly rely on data from the control system to optimize production and increase intelligence for OT improvements, sustainability, and other digital transformation initiatives,” said Claudio Fayad, vice president of technology for Emerson’s process systems and solutions business. “The DeltaV Edge Environment is the first step in defining the control system of the future, extending the DeltaV DCS with the capability to move data and configuration easily and securely while simultaneously empowering users to drive innovation as they safely run applications and scripts inside the DCS.” The DeltaV Edge Environment helps production teams meet their need to more easily and securely engage with automation data and manipulate it into actionable information to steer digital transformation. A single, encrypted, outbound-only flow of data helps authorized users ensure they have constant access to near real-time data without the risk of users accessing the control system—a common risk with traditional custom-engineered solutions. Users can run applications for visualization, analytics, alarm management, digital twin simulations, and other needs with the contextualized data available on the DeltaV Edge Environment. OT teams will know the rich data they use is a precise replica, always up to date and fully reflective of the current operating condition. The DeltaV Edge Environment leverages open, common protocols such as OPC Unified Architecture (OPC UA) to provide contextualized data while standard application programming interfaces like representational state transfer architectural style (REST API) and scripting tools like Python provide the sandbox environment in which users can design and run applications.
The Devil is in the detailing
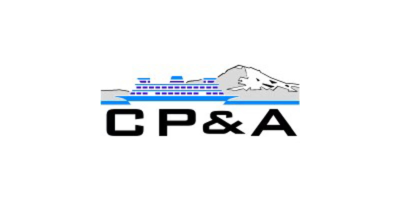
In the crane design world, how beams are joined together is called connection detailing and getting these details right can literally make or break a crane. Besides reducing a crane’s potential for collapse, proper connection detailing can also extend a crane’s service life by up to 400%. As we know, cranes experience their full rated load much more often than other structures, such as buildings and bridges. While an engineer might not be surprised that cranes see their rated load as often as they do, what is not so obvious is the consequences of millions of cycles at the full rated load. These consequences are known as “fatigue”. Fatigue is the term used to describe the failure of a steel member below its yield stress due to cyclic loading. By understanding fatigue and implementing fatigue design strategies and concepts, the crane engineer can go a long way in removing the “devil” from the detailing. Effect of weld contour details on stress flow and fatigue behavior. Poor fatigue detailing increases the risk of cracking, which can lead to sudden connection and member failures. The long-term benefits of good fatigue detailing are longer inspection intervals and less repair work, resulting in reduced maintenance and repair costs. Smooth transfer In the structural crane design world, fatigue detailing is a special class of connection design. Fatigue detailing improves the smooth transfer of loads from one beam to another by reducing stress concentrations. Stress concentrations—also called stress risers—are created when one area of a connection is more highly stressed than adjacent areas. This condition is usually the result of an abrupt change in geometry, especially around sharp corners. Good fatigue detailing reduces stress concentrations by limiting the effects of geometry changes when connecting one beam to another. Many crane design codes address fatigue detailing by separating connection types into classes based on the severity of their stress concentrations. Historically, stress concentration factors have been found using experimental techniques though advances are being made in finite element analysis (FEA) to approximate the initiation and propagation of fatigue cracks more accurately. This is also true in many of the experimental sensors, such as strain gauges. Modern-day technology is relevant here, as it is with everything else. The improvements of computer chips have been remarkable. They allow engineers to run very computationally demanding calculations that take a computer the same amount of time to complete as it takes for the engineer to grab a cup of coffee from the office kitchen. We can run multiple design iterations and compare results much more quickly than before. This allows engineers to consider more connection details than they could have previously. However, properly setting up and verifying the results of the FEA model is now the bottleneck. An important complement to connection detailing is proper fabrication. On-site inspection during all phases of a crane’s construction is a must to ensure the as-designed fatigue detailing is properly implemented. Inspectors help make sure plates are properly fit up and clean before welding. Weld inspectors review weld geometry for proper setup and carry out non-destructive testing. Misaligned transfer Good fatigue detailing extends to mechanical components as well. Engineers must maintain proper alignment of machinery for power transfer to occur efficiently and consistently. For a hoist-on-trolley arrangement, if the hoist machinery is not designed for the flexing of the trolley frame as the crane picks up a load, then the hoist machinery is likely to become misaligned during the pick. At best, misaligned mechanical components are less effective—brake pads do not contact properly, leading to reduced brake torque, shafts become misaligned, leading to larger loads and accelerated wear, and gears may no longer mesh correctly—leading to shortened service life and increased maintenance costs. At worst, a coupling, gearbox, or other component can fail, putting the load at risk of dropping and requiring the crane to be immediately removed from service for costly and time-consuming repairs. Do you know your crane? Knowing that proper connection detailing alone can be the difference between a 10-year service life and a 40-year service life, do crane owners really “know” the life of their cranes? As a crane completes its first decade of service, do owners know the service life of their cranes and can they confidently say how much service life remains? The answers can typically be found in the crane purchase specifications and the crane maintenance/service log. The purchase specifications state the number of moves for which the crane needs to be designed. By comparing the design moves to the actual moves in the service log, a fairly good idea of the remaining service life can be extrapolated. Of course, this approach assumes the crane’s actual service life will meet the specified design life. However, some of these cranes have design lives of 20 years or more so it takes a long time to see if the design is successful. Sometimes design life is measured in cycles. A crane may perform over two million lifts during its useful life. If the connection designs are susceptible to cracking, the crane is more likely to have higher maintenance costs and may even fail much earlier, than a crane with proper connection detailing. Tired viewpoint Many people think of fatigue as the “wearing out” of steel but this is not quite right. Fatigue failure occurs in components subjected to a high number of cycles of fluctuating stresses. Under these dynamic conditions, failure can occur at a stress level that is significantly less than that of a static load. However, if the fluctuating stresses are low enough and in an ideal environment, steel can have an infinite fatigue life. A crack appears at a welded connection. Cracks are a common mode of fatigue failure and originate from initial flaws in the steel. They can propagate from many sources, including high cycle fatigue, poor manufacturing, corrosion, and overload events such as snags, earthquakes, or storm winds. The initial flaws may be microscopic or macroscopic. Growth rate increases with crack size so
Kassow Robots establishes U.S. Sales and Support team
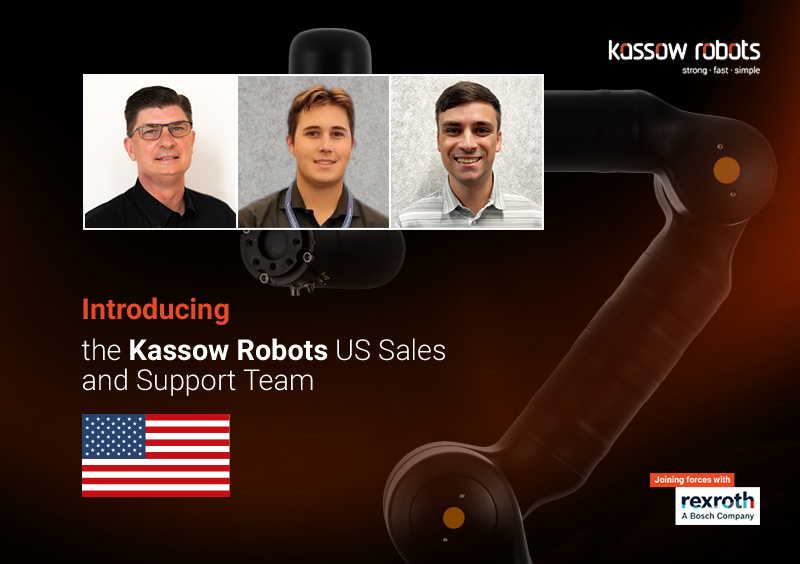
Kassow Robots, a developer of 7-axis industrial cobot solutions for machine tending, material handling, dispensing, and various other applications, has established a U.S.-based team focused on sales and support. Regional Channel Partner Managers Jim Adamski and Collin Ayres and Technical Support Engineer Chris Hapsias will support Kassow Robots’ sales partners, system integrators, and distributors in the U.S. Kassow Robots is part of Bosch Rexroth, which has been its majority owner since 2022. “This team will allow us to work closely with our system integrators and distributors in the United States. They will also extend our reach to new sales partners and markets,” said Dieter Pletscher, Global Sales Manager at Kassow Robots. Jim Adamski is focused on working with the U.S. partner network east of the Mississippi River and in Iowa. He joined the Kassow Robots team earlier this year and has previous experience with Bosch Rexroth. He’s worked in the factory automation industry for more than 30 years. Adamski looks forward to helping U.S. companies automate their operations efficiently and manage labor challenges. “Kassow Robots has a great lineup of 7-axis robots that are easy to set up and program,” Adamski said. “There is vast array of potential applications, such as machine tending, welding, dispensing, and palletizing, that these cobots are equipped to handle because of their flexibility.” Collin Ayres recently joined the Kassow Robots team after receiving his mechanical engineering degree from the University of Nebraska, Lincoln. As Regional Channel Partner Manager, he focuses on helping Kassow Robots expand its presence in North America and supporting sales partners in the western part of the U.S. “It’s an exciting time to be working in automation, and I’ve enjoyed seeing users’ response to interacting with the Kassow Robots cobots at events over the past several months,” Ayres said. “The 7-axis lightweight robots were made for industrial use and enable automation for operations even in the most confined spaces.” The latest addition to the U.S. team is technical support engineer Chris Hapsias. He is responsible for providing technical support and training for Kassow Robots’ U.S. distributor network. He brings four years of factory automation experience, specifically in the autonomous mobile robot (AMR) space. “The added range of motion the seventh axis provides for the KR Series robots is impressive,” Hapsias said. “They are user-friendly, with an intuitive tablet-based user interface that allows beginners to program these cobots with little training and robotics pros to dive deeper to program complex operations.” Kassow Robots’ 7-axis lightweight cobots offer small footprints and increased maneuverability. The unique seventh axis, or “wrist joint,” enables continuous dispensing, welding, and material removal applications, regardless of access angle, without the need to reorient the arm. The cobots are easy to program and operate after a short introduction, allowing small and medium-sized enterprises (SMEs) without robotics specialists to implement automation cost-effectively and independently.
PLASTICS Industry Association releases Global Trends Report, underscores strong global demand for plastics
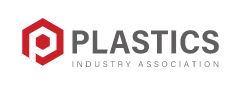
The Plastics Industry Association (PLASTICS) released its annual Global Trends report today during a press briefing and keynote address at PLASTIMAGEN ® MÉXICO. “According to the World Trade Organization (WTO), global trade volume expanded by 2.7% in 2022. The remarkable 9.7% growth in the U.S. plastics industry’s trade volume for 2022, surpassing global merchandise trade, underscores the strong global demand for plastics,” said Dr. Perc Pineda, PhD, PLASTICS’ Chief Economist. “As we look ahead to 2023, the WTO anticipates a 0.8% increase in world merchandise trade volume. Data from the first half of this year indicates a decline in plastics trade volume compared to the same period last year. However, during this time, the U.S. trade balance shifted from a deficit (-$5.2 billion) to a surplus ($1.0 billion). It would not be surprising to see the U.S. plastics industry’s trade volume in 2023 once again outpacing the growth in total global merchandise volume,” Pineda added. “The decelerating economic growth in China may pose a challenge for the U.S. plastics industry, given that China ranks as the third-largest export market for U.S. plastics. Although the U.S. maintains an overall trade deficit with China in the plastics sector, it’s worth noting that the U.S. enjoys a $3.1 billion trade surplus in resin, making it the second-largest country in terms of resin trade surplus, trailing only Mexico,” said Pineda. “The U.S. plastics industry remaining a key player in the global plastics trade shows the importance of our industry and the essential nature of plastics,” said PLASTICS President and CEO, Matt Seaholm. “Our members continue to innovate and invest in new ways to make products even better and more sustainable, while continuing to provide essential materials that improve lives across the globe.” Among the highlights found in the Global Trends report: U.S. plastics industry exports rose 11.8% and imports rose 7.2%. The overall plastics trade deficit fell to $7.4 billion in 2022 from $10.0 billion in 2021 as the global economy continued to recover from the pandemic in 2020. According to the Global Trends, the apparent consumption of plastics industry goods in the U.S., an indicator of demand, increased 13.7% to $393.3 billion, up from $345.9 billion in 2021, which underscores the benefits that plastics and plastics products on the economy. Global plastics trade volume is estimated to have reached $1.7 trillion with China, the United States, and Germany ranked the top three players in the global plastics trade, based on PLASTICS’ annual Global Plastics Ranking®. The U.S. plastics industry had its largest trade surplus with Mexico of $11.0 billion, followed by Belgium ($2.9 billion), Brazil ($2.4 billion), the Netherlands ($881 million), and Singapore ($854 million). “The trade connections among the U.S., Mexico, and Canada are robust and deeply embedded, largely owing to the United States-Mexico-Canada Free Trade Agreement. These three nations stand out as key trade partners across the entire spectrum of the plastics industry, evident from the substantial $258.8 billion trade volume in resin and plastics products in 2022,” concluded Pineda. Interested parties worldwide will find the Global Trends report and its accompanying dataset provide a comprehensive account of U.S. plastics exports and imports worldwide in each of the four categories of the plastics industry – resin, products, machinery and molds. The report is also the only plastics trade report that includes trade analysis outlining the movement of resins and plastics that are embedded in goods that the U.S. both exports and imports. An executive summary and the full PLASTICS’ Global Trends report is available to Plastics Industry Association members online at: https://www.plasticsindustry.org/data-report/global-trends-2023/
Kinetic Technologies unveils HT Headstock-Tailstock Positioners to Revolutionize Cobot Welding Automation
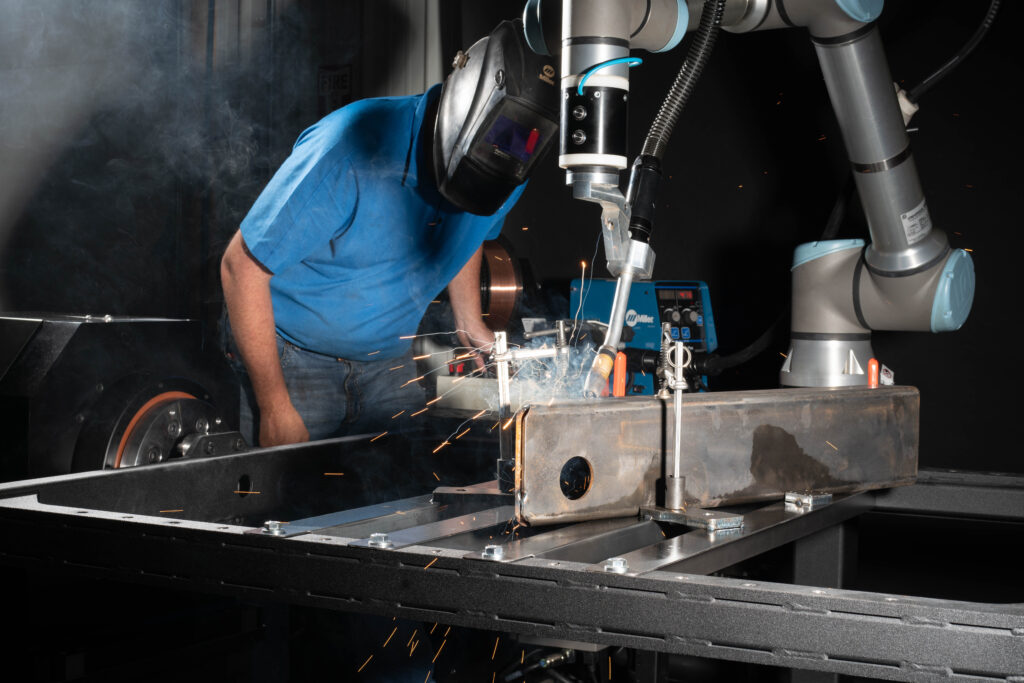
Kinetic Technologies, an innovator of positioners, fixtures, and tooling for industrial automation cells, has announced the launch of their newest positioning system for cobot welding, the HTheadstock-tailstock positioner family, a transformational addition to their product portfolio. The positioners will disrupt the world of cobot welding and offer performance, quality, and efficiency improvements for welding operators and production managers. The HT product family delivers a remarkable level of versatility to welding automation. Unlike traditional flat tables, the servo-driven headstock rotating positioners with a fixed tailstock allow for part positioning accuracy down to 0.01 degrees, offering nearly infinite jog table locations and the ability to rotate during welding. This flexibility maximizes arc-on time and ensures superior part quality at the same time. The industry needs for the HT Positioners are clear. Mark Barglof, Owner of Kinetic Technologies, said, “Industrial robot cells have employed positioning systems for decades, and very few industrial welding cells out on manufacturing floors today do not include a positioner, however, very few cobot welding cells utilize positioning systems today.” With the HT1, manufacturing leaders can realize the full potential of cobot welding, providing more consistent, higher-quality welds. This approach provides a distinct competitive advantage over companies using industrial automation, but not positioning. Mr. Barglof said, “We are excited to release the HT product family to our customers. We have heard from many customers that their parts would be best handled using a headstock-tailstock configuration. We have found that our ability to provide customers with turn-key welding automation cells has increased tenfold by adopting the HT configuration.” Moreover, Kinetic Technologies is launching its new RT Lite rotary welding table in addition to the HT positioners. The RT Lite is a modified version of their RT1 turntable, which was launched back in November 2022 at FABTECH. The RT Lite features the same load capacity as the RT1 at a lower price point for those who don’t need the cobot fixed to the table. Kinetic’s RT rotary positioners are specially designed cobot-controlled rotary tables that help to optimize welding capacity for cobots. With a range of advanced features and the ability to optimize part positioning, Kinetic Technologies’ positioners ensure high weld quality, consistency, and production efficiency, making them an invaluable addition to their cobot welding operation.
Hy-Brid Lifts announces Director of Sales for Southeast United States
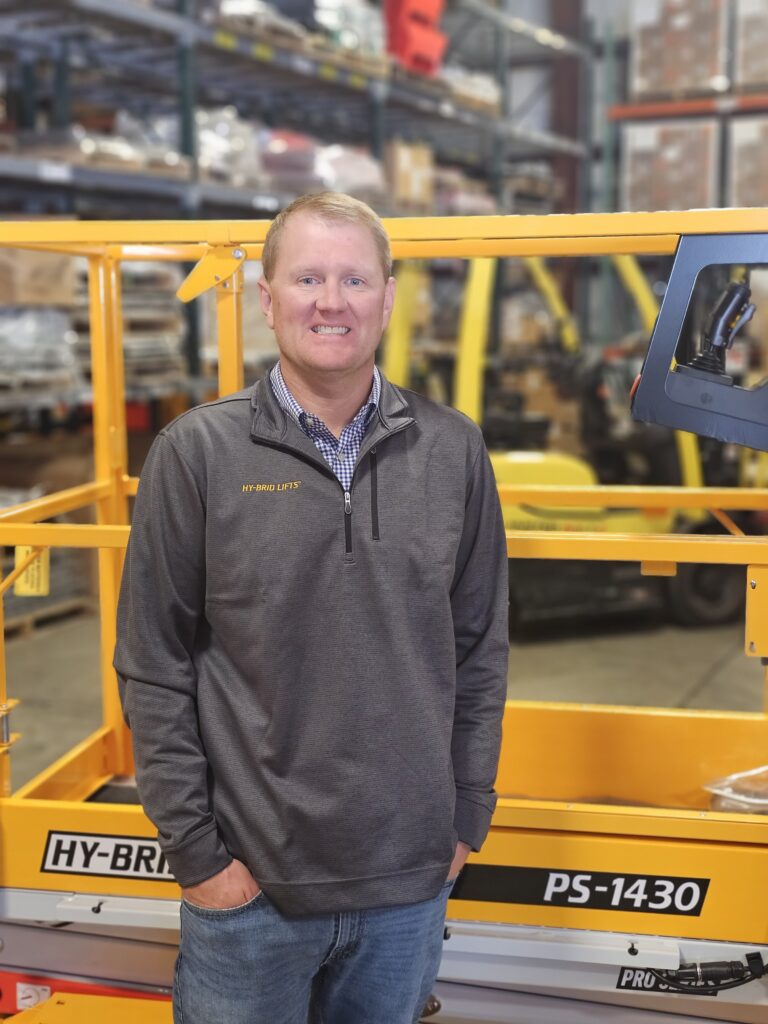
Hy-Brid Lifts announces David Price as director of sales covering the southeast United States. Price’s responsibilities include providing customer support as well as continuing the growth and channel development of the Hy-Brid Lifts line of low-level scissor lifts. “I am excited to join this team and look forward to the opportunity to work with our customers. Coming from the rental industry, I understand the importance of quality equipment and customer service backed by a solid service department,” said Price. “After touring the production facility and meeting the Hy-Brid Lifts family, it’s no surprise that this company is continuing to grow, and I look forward to being a part of that growth.” Price brings 12 years of industry experience to his new role, largely derived from his time in the rental equipment industry with United Rentals, Blueline Rentals and Equipmentshare. He spent a majority of his time in sales management with a strong emphasis on customer service and going above and beyond for every customer. “The entire Hy-Brid Lifts team is excited to have David on board to serve the southeast United States. David has a wealth of sales and rental industry knowledge that will strengthen our ability to serve our customers,” said Dave Wanta, Custom Equipment LLC vice president of sales. “David is a valuable addition to the team, and we look forward to the contributions that he will provide for our company’s continued growth.”
U.S. Rail Traffic for the week ending November 4, 2023
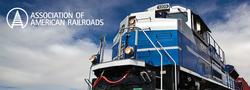
The Association of American Railroads (AAR) has reported U.S. rail traffic for the week ending November 4, 2023. For this week, total U.S. weekly rail traffic was 484,757 carloads and intermodal units, down 1.7 percent compared with the same week last year. Total carloads for the week ending November 4 were 224,415 carloads, down 5.2 percent compared with the same week in 2022, while U.S. weekly intermodal volume was 260,342 containers and trailers, up 1.5 percent compared to 2022. Three of the 10 carload commodity groups posted an increase compared with the same week in 2022. They were motor vehicles and parts, up 357 carloads, to 14,841; farm products excl. grain, and food, up 274 carloads, to 17,101; and petroleum and petroleum products, up 267 carloads, to 9,527. Commodity groups that posted decreases compared with the same week in 2022 included grain, down 3,655 carloads, to 21,395; coal, down 3,017 carloads, to 65,298; and nonmetallic minerals, down 2,562 carloads, to 31,218. For the first 44 weeks of 2023, U.S. railroads reported cumulative volume of 9,920,836 carloads, up 0.1 percent from the same point last year; and 10,665,407 intermodal units, down 7.0 percent from last year. Total combined U.S. traffic for the first 44 weeks of 2023 was 20,586,243 carloads and intermodal units, a decrease of 3.7 percent compared to last year. North American rail volume for the week ending November 4, 2023, on 12 reporting U.S., Canadian and Mexican railroads totaled 337,189 carloads, down 2.0 percent compared with the same week last year, and 339,433 intermodal units, down 0.5 percent compared with last year. Total combined weekly rail traffic in North America was 676,622 carloads and intermodal units, down 1.2 percent. North American rail volume for the first 44 weeks of 2023 was 28,833,863 carloads and intermodal units, down 3.4 percent compared with 2022. Canadian railroads reported 97,307 carloads for the week, up 2.5 percent, and 67,421 intermodal units, down 10.7 percent compared with the same week in 2022. For the first 44 weeks of 2023, Canadian railroads reported cumulative rail traffic volume of 7,008,124 carloads, containers and trailers, down 3.4 percent. Mexican railroads reported 15,467 carloads for the week, up 24.2 percent compared with the same week last year, and 11,670 intermodal units, up 29.6 percent. Cumulative volume on Mexican railroads for the first 44 weeks of 2023 was 1,239,496 carloads and intermodal containers and trailers, up 3.4 percent from the same point last year. To view the rail traffic charts, click here.
Episode 435: Velostics – Streamlining warehouse scheduling with AI
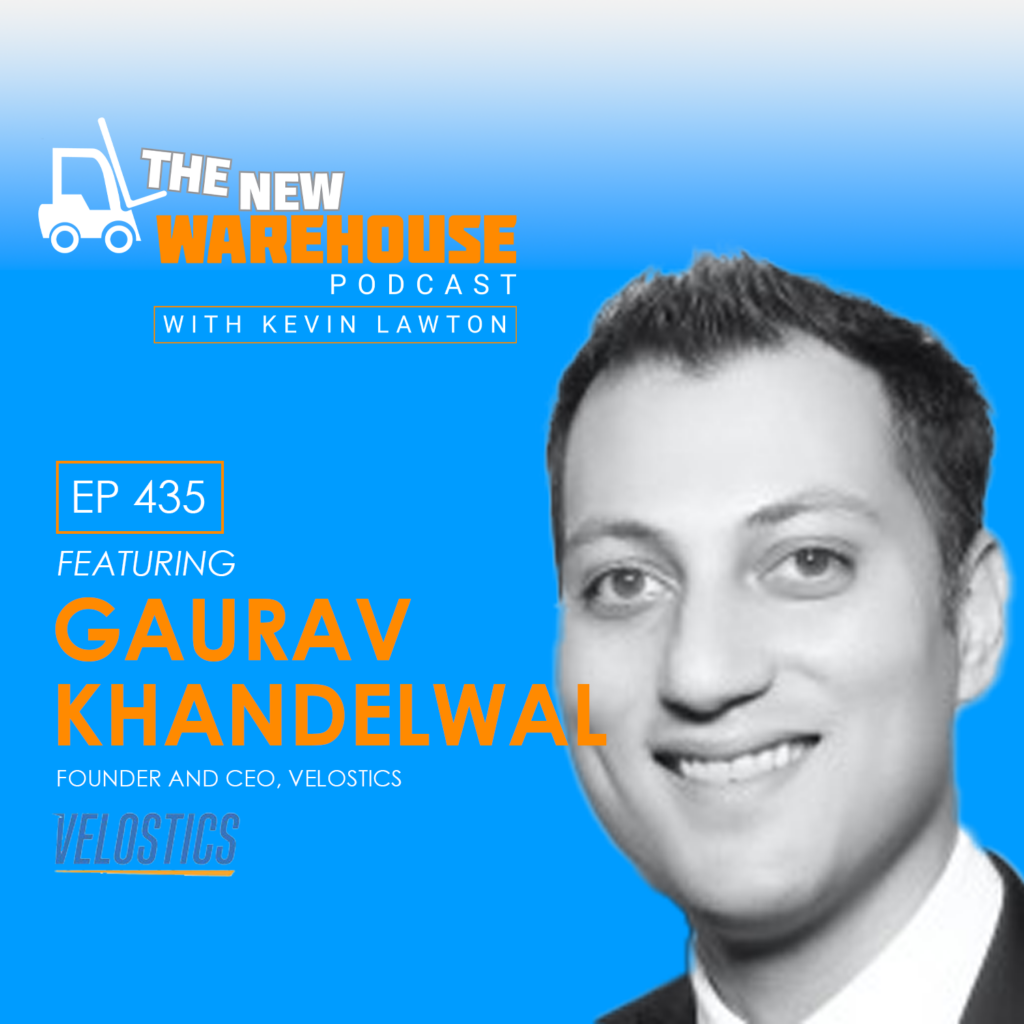
In the latest episode of The New Warehouse podcast, Kevin sits down with Gaurav Khandelwal, CEO and founder of Velostics, to shed light on the revolutionary strides his company is making in the industry. Velostics has been carving its niche by creating custom logistics software for heavyweight industries, ranging from oil and gas to e-commerce, delivering solutions that transcend the typical boundaries of operational efficiency. Whether it’s the lines of trucks waiting outside plants, driver fatigue, detention frustrations, or rigorous compliance with ELD mandates, Velostics provides a novel approach to automate the traditionally manual scheduling processes, a solution poised to transform how plants and warehouses operate. But Velostics is more than just about automation; it’s a story of delayed disruption in the critical relationship between shippers and brokers and the intricate check-in and check-out operations. Please tune in to uncover how Velostics drives the warehousing industry forward and the potential impacts of its AI-powered solutions on your operations. Streamlining Warehouse Scheduling: Lessons from the Digital World The traditional approach to warehouse scheduling, as Khandelwal analogizes, resembles “the old school Craigslist” – a one-size-fits-all solution buried within warehouse management systems (WMS), yard management systems (YMS), or transportation management systems (TMS) that treated scheduling as an afterthought. This has led to a cumbersome process, with “20 clicks to get an appointment or change an appointment,” hardly aligning with the agility needed in modern logistics. Khandelwal’s company leaps forward, offering a “branded website” for shippers, where appointments for pickups and deliveries can be automated based on various factors, streamlining what was once a labyrinthine task. This digitization of scheduling extends beyond mere convenience. As Khandelwal underlines, it’s also about optimizing dock usage and labor management, reducing detention times, and, ultimately, cost savings. “It’s all set around optimization,” he stresses, ensuring that “the truck in and out as fast and as safely as possible” is the norm, not the exception. Harnessing AI for Enhanced Warehouse Scheduling Khandelwal captures the essence of this advancement, “Where our customers want it, we can integrate with their visibility provider… we can let the customer know… Do you want me to move this appointment automatically?” Warehouses are no longer static spaces but intelligent hubs that react and adapt in real time. Khandelwal’s insight into the power of predictive analytics in anticipating delays is a testament to the evolving landscape, “We started to notice…certain lanes, certain brokers, certain type of shippers, those trucks are like, you know, 10 percent late, 20 percent late.” Such data-driven foresight enables warehouses to mitigate the domino effect of delayed shipments, which can ripple through the supply chain, causing significant operational disruption. It’s this level of detail that AI captures and analyzes, providing recommendations to ensure warehouses stay a step ahead. For instance, he elucidates the benefits of this intelligent system, “…70 percent of the time, this truck’s not shown up when it said it would. Do you want to keep an opening for later in the day?” The potential of AI to actively suggest operational changes ensures warehouses aren’t just receivers of goods but proactive players in a larger, interconnected supply chain. Key Takeaways Innovation Through Customization: Velostics is setting a new standard in logistics software by offering tailored solutions that cater to the unique demands of industries as varied as oil and gas to e-commerce. Their innovative approach redefines the efficiency of check-in and check-out operations in warehouses and plants. Digital Transformation of Scheduling: By creating an automated, customizable “branded website” for shippers, Velostics is revolutionizing the appointment setting process. This leap forward not only enhances dock utilization and labor management but also significantly cuts down on detention times, leading to substantial cost savings. Predictive Power of AI: Integrating AI with real-time data provides unprecedented predictive analytics, enabling warehouses to adjust to delays and maintain smooth operations proactively. This shift from reactive to proactive management positions warehouses as pivotal players in a responsive and integrated supply chain. The New Warehouse Podcast EP 435: Velostics – Streamlining Warehouse Scheduling with AI
Hyster-Yale Group recognizes National STEM Day with manufacturing engineering and innovation programs
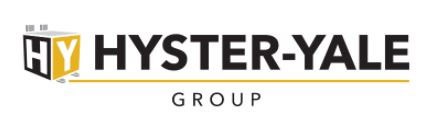
Major manufacturer of forklifts and related technologies collaborates with non-profit, universities across the country to foster opportunity and innovation among students pursuing careers in engineering Coinciding with National STEM Day, Hyster-Yale Group announces several milestones and opportunities for engineering students through its longstanding collaborations with academic and career development programs from coast to coast. The company is sponsoring dozens of senior capstone projects, providing mentorship and internship opportunities, opening a new innovation lab and lending industry perspective to new university engineering programs. Innovation Lab at the University of Portland The Hyster-Yale Group Innovation Lab will resume in January 2024 at the new Shiley-Marcos Center for Design and Innovation at the University of Portland. The lab was paused due to the COVID-19 pandemic and construction of the new facility. The lab, which has been a model for other industry-university cooperation, immerses student interns in real engineering and product development projects. Four interns have already been hired into development and innovation roles with the company. The lab is led by Chief Technologist of Innovation for Hyster-Yale Group, Ed Stilwell, who created and taught an innovation course for several years at the university. Internships and advisory councils The company works with other colleges in the communities where it operates to provide internship opportunities, including East Carolina University, Berea College, Eastern Kentucky University and the University of Kentucky. Hyster-Yale Group also serves alongside companies such as Lockheed Martin and Lexmark on the Eastern Kentucky University engineering advisory council. Anthony Wasson, Value Stream Manager, and Ken Deters, Director of Service Operations, are active on the council, which was established to provide industry perspective to the development and operation of the school’s new degree program in manufacturing engineering. At East Carolina University, the Warranty and Quality Improvement Manager for Hyster-Yale Group, John Roberson, also serves on an engineering advisory council. Hyster-Yale Group’s Counterbalanced Development Center (CBDC) in Oregon is in the planning process for 2024 internships with the Multiple Engineering Co-Operative Program (MECOP), a non-profit that works with member companies and universities in the Pacific Northwest to cultivate the highest level of engineering and business graduates by bridging academic theory with industry reality. Since 2000, more than 95 interns across mechanical, electrical, computer engineering and computer science disciplines have worked at the CBDC supporting various product development projects. At least 15 former MECOP interns are employed across the development team, working in design, validation, program management, software and simulation or virtual testing. Hyster-Yale Group posts internship opportunities for fall, spring and summer semesters at several locations. To learn more about all available internship opportunities or to apply, visit https://hyster-yalecareers.com/. University capstone projects Each year, the CBDC sponsors capstone projects for 35 to 40 seniors from local universities. The students work in teams on eight to 10 real-world and often multi-discipline engineering problems provided by Hyster-Yale Group. In Greenville, North Carolina, the company’s Warehouse Product Development Center and manufacturing facility also host engineering students from East Carolina University completing their capstone projects. In both cases, students are guided through the process of developing viable solutions by mentors from the company, accessing valuable experience and insight to the field and developing relationships in the industry as they progress. Student teams have created specialized test equipment, innovative human-machine interfaces, improvements to forklift operator comfort, new sensing methods and other innovations at the leading edge of the materials handling industry.
Gebrüder Weiss announces strategic partnership with PartsCloud
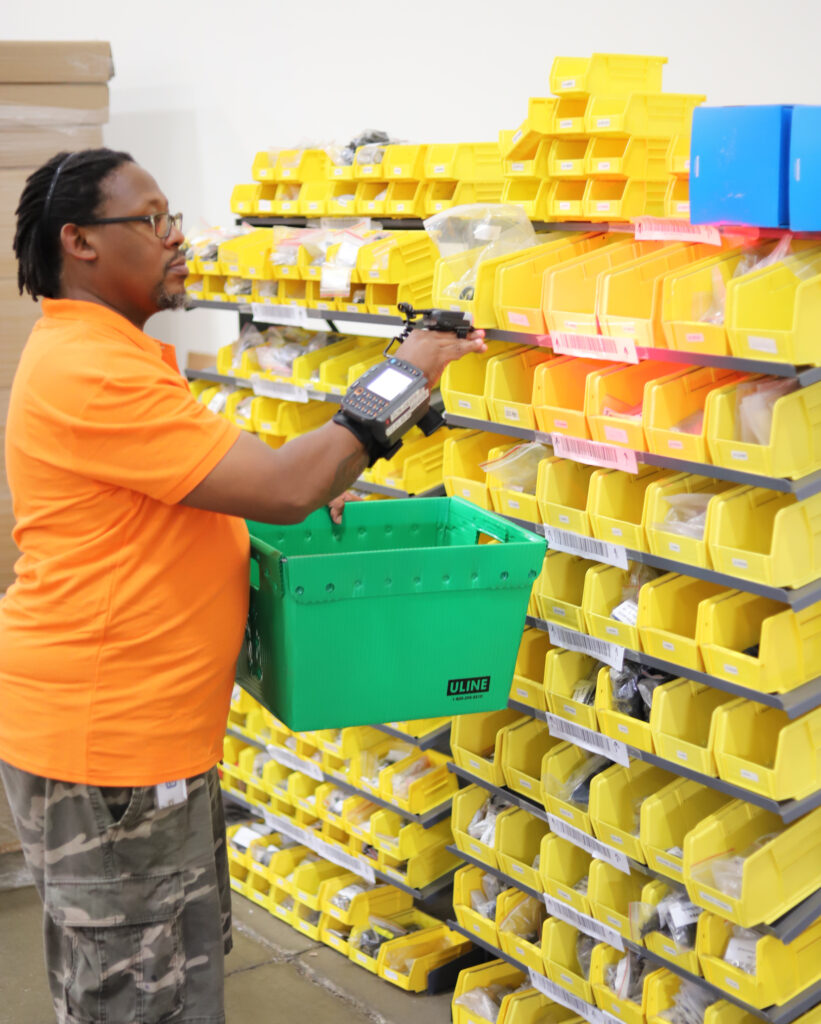
Gebrüder Weiss, an international transport and logistics company with a 500-year history, announced a new strategic partnership with PartsCloud, a LaaS (Logistics-as-a-Service) start-up that digitizes spare parts logistics for engineering and plant construction. PartsCloud is based in Stuttgart, Germany, and the grand opening of its new Chicago warehouse represents its first entry point into the U.S. market. “Spare parts logistics in engineering and plant construction is very complex, and Gebrüder Weiss can provide support based on our many years of logistics know-how,” says Lothar Thoma, Managing Director Air & Sea at Gebrüder Weiss. Moreover, we believe in the business model of PartsCloud, and there is still immense potential for standardization and digitization in industrial spare parts logistics.” PartsCloud co-founders Benjamin Reichenecker and Fabian Gemmecke founded the company in 2021 with the mission to create a global logistics network that people can use through a simple interface. Engineering and plant construction is one of their native Germany’s leading export and innovation sectors, but lack of digitization has created procurement challenges. Machine downtime in production plants costs these businesses an average of 13.5 million euros per month. The cooperation with Gebrüder Weiss enables PartsCloud to smoothly transfer its established standard operating model and its fulfillment processes in Germany to the U.S. “Our LaaS platform puts our customers in full control and offers standardized interfaces for efficient logistics,” says Reichenecker, CEO of PartsCloud. “We are proud to work with a logistics provider as experienced and reputable as Gebrüder Weiss as we partner to bring this interface to customers in North, Central, and South America.” In addition to its US expansion, PartsCloud plans to open markets in Asia, Mexico, the UK and the Middle East.
Bobcat expands in new facility in Monterrey, Mexico
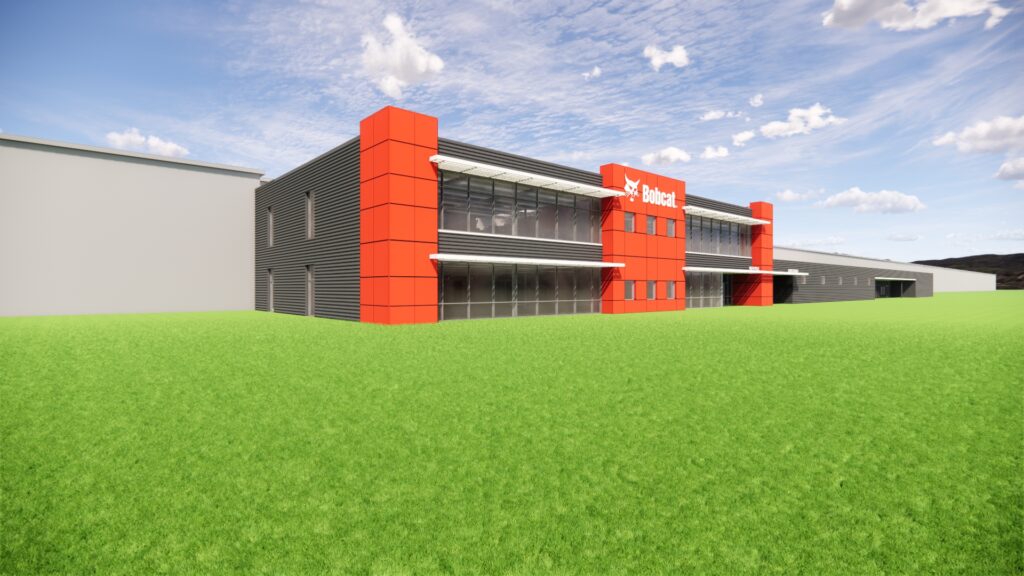
$300 million investment aims to boost production capacity to support customer demand and company growth Bobcat Company has announced their intentions to expand its footprint with a new manufacturing facility in Monterrey, Mexico, anticipated to begin production in early 2026. The investment, planned for approximately $300 million, will expand Bobcat’s existing global footprint to create additional production capacity and manufacturing capabilities for select compact track and skid-steer loader models. The new facility is expected to create an additional 600 to 800 jobs in the region. “As a global company with manufacturing facilities, offices, dealerships and customers across the globe, we have seen tremendous growth and increased demand for our products,” said Scott Park, Doosan Bobcat CEO and vice chairman. “We are excited to continue growing our footprint to meet demand for Bobcat solutions worldwide.” The 700,000-square-foot manufacturing facility is expected to increase Bobcat’s North American compact loader production capacity by 20%. The facility will feature areas for welding, painting and assembly, as well as an on-site warehouse and office space. Bobcat will implement state-of-the-art technology with an emphasis on quality, precision and energy efficiency. The Monterrey location will manufacture Bobcat M-Series compact loaders for North American distribution. This strategic manufacturing capacity alignment will allow Bobcat to focus its industry-leading R-Series compact loader production at its Gwinner, N.D. facility, and its Dobris, Czech Republic facility will continue to manufacture M-Series loaders for the Europe, Middle East and Africa regions. Bobcat will continue to focus on talent retention and hiring at all locations in support of continued expansion and growth. “This new facility allows us to design a manufacturing space for maximum efficiency, quality and production output,” said Mike Ballweber, Doosan Bobcat North America president. “By growing our manufacturing footprint, we can also further optimize our other global facilities to improve our operational efficiency and enhance employees’ workspaces.” This new location was selected after extensive review and consideration of expansions at existing Bobcat locations, along with the potential for new developments at locations across the globe. Monterrey was selected for its well-established industrial sector, skilled workforce, proximity to the U.S., cost competitiveness and strong business environment, among other factors.
Juno Jones wins prestigious national award from NSC
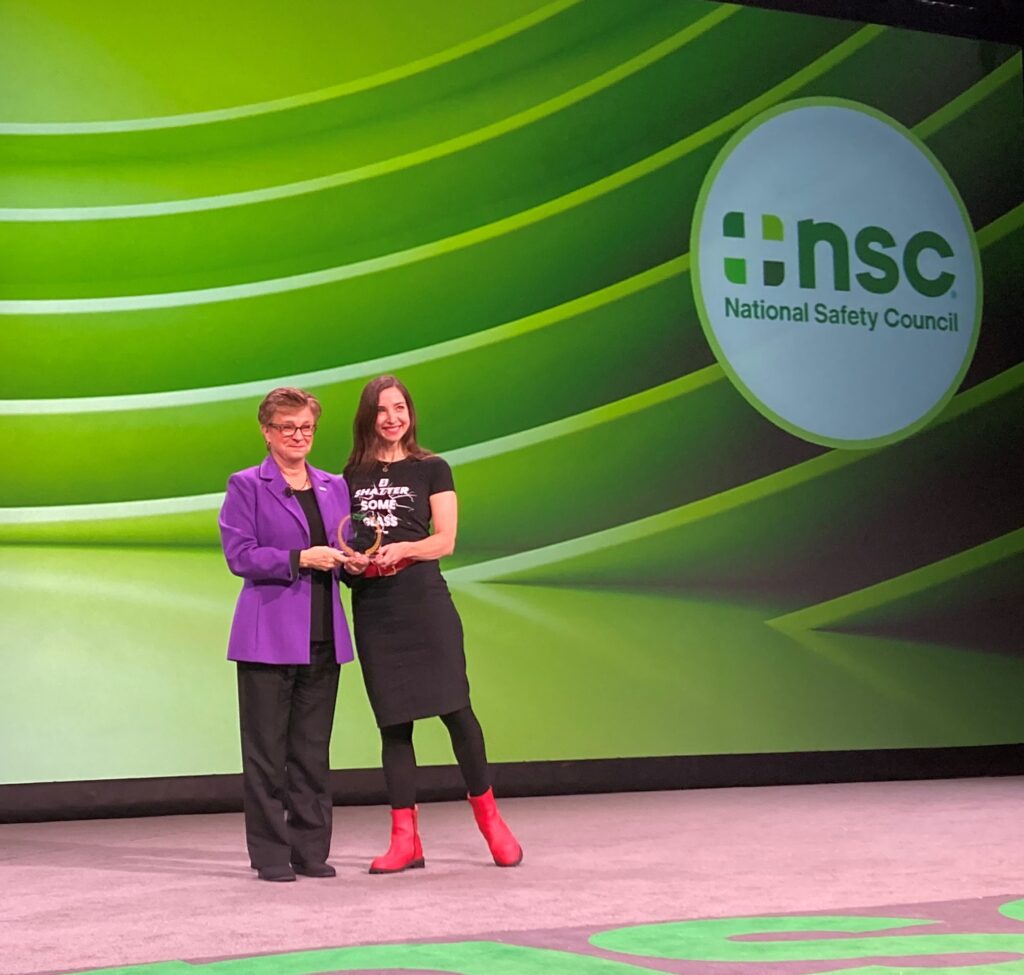
The National Safety Council, the nation’s leading nonprofit safety organization, has honored Juno Jones boots with a prestigious Best in Show Award at the 2023 Safety Congress and Expo held in New Orleans, Louisiana. The National Safety Council held its annual conference, which is the world’s largest annual gathering of safety professionals, at the Ernest N. Morial Convention Center from October 22-24, 2023. Prior to the Wednesday morning keynote, the winners were announced before an audience of thousands. Of over 70 new safety products, the Juno Jones Women’s Steel Toe Meti II Boot was declared a winner and called onto the stage. Juno Jones Founder and CEO Emily Soloby was on hand to accept the award from NSC CEO Lorraine M. Martin. Juno Jones specializes in ASTM safety footwear made especially for a woman’s foot shape, creating a safer, more comfortable, and more stylish boot. “This is a win for women’s safety in the workplace, and a win for inclusion in the workplace. It shows that the tides are turning. Pink it and shrink it is out, and inclusion is in,” said Juno Jones Founder Emily Soloby. You can find Juno Jones at retailers like Duluth Trading Company, as well as on their website at www.junojones.com. Juno Jones partners with leading distributors to help bring women’s PPE to female employees at corporations and organizations around the country. To learn how to bring Juno Jones boots to your company, email info@junojonesshoes.com.
DHL Supply Chain and AutoStore™ announce partnership expansion to further automate global warehousing
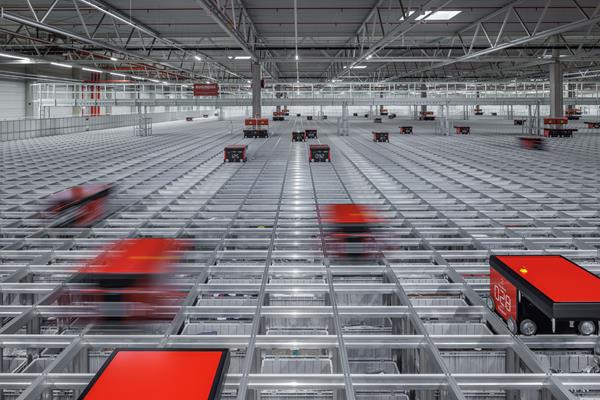
DHL Supply Chain is currently involved in nine AutoStore projects across Singapore, the U.S. and Germany, with four more in planning Through this partnership, a fleet of over 1,000 robots has significantly boosted operational efficiency and throughput in DHL’s fulfillment warehouses This automated storage and retrieval system (AS/RS) technology is a preferred solution for businesses handling smaller products and items DHL Supply Chain, global provider in contract logistics, and AutoStore, a pioneering robotic technology company specializing in automated storage and retrieval systems, are expanding their partnership in a move set to further automated warehouse operations on a global scale. DHL Supply Chain, already involved in nine operational AutoStore warehouse projects with four more in the planning stage, is poised to become one of AutoStore’s largest 3PL clients, reinforcing their commitment to digitalization and automation. The nine existing Systems effectively operate 800,000 bins, with the forthcoming four Systems elevating the total number of bins to a remarkable 1.2 million. In the future, DHL also intends to construct five further facilities in addition to those already in operation or planning. This innovative automated storage and retrieval system (AS/RS) technology has been developed to efficiently manage and optimize inventory using vastly reduced space within warehouses. Its highly modular and scalable design makes it a preferred solution for e-commerce and businesses handling smaller products such as fashion and tech items. The strategic aim of DHL and AutoStore through this partnership is to accelerate the implementation of this ground-breaking technology that enhances abilities to meet diverse client needs. Fleet of more than 1,000 robots will enhance operational efficiency and throughput Markus Voss, COO and CIO at DHL Supply Chain, emphasizes the importance of this collaboration: “We are pleased to expand our existing relationship with AutoStore as we continue to implement our digitalization and automation strategy in a growing number of warehouses, allowing us to better and faster serve our customers. AutoStore’s standardized and modular technology perfectly aligns with our aim to make our operations more efficient, enabling swift scalability and adaptability across various use cases and end-markets – a crucial factor for us as a third-party logistics provider. Through a standardized approach and dedicated stock availability we will be able to significantly drive down implementation times. Additionally, AutoStore’s network of partners is invaluable in supporting our growth strategy across multiple geographies.” Watch a video with DHL’s Marcus Voss discussing the partnership here. Since 2012, DHL Supply Chain and AutoStore have partnered to implement cutting-edge solutions across sites in Singapore, Poland, Germany, Australia, and the U.S. The ongoing collaboration has already led to expansions at all operational sites, resulting in a fleet of more than 1,000 Robots worldwide that significantly increase operational efficiency and throughput. Mats Hovland Vikse, CEO of AutoStore, expressed excitement about the expansion: “Our longstanding collaboration with DHL Supply Chain has showcased the strength, reliability, and efficiency of AutoStore’s technology. We are thrilled to further expand this valued partnership, supporting DHL Supply Chain’s global deployment of automated warehouse solutions. We are excited about the significant growth opportunity that this represents for AutoStore, as we continue to drive innovation in the world of logistics.” This expanded partnership between DHL Supply Chain and AutoStore promises to redefine the future of warehousing, offering scalable, adaptable, and efficient solutions that cater to the ever-evolving needs of customers worldwide.
Women In Trucking Association names Shelley Simpson as 2023 Influential Woman in Trucking
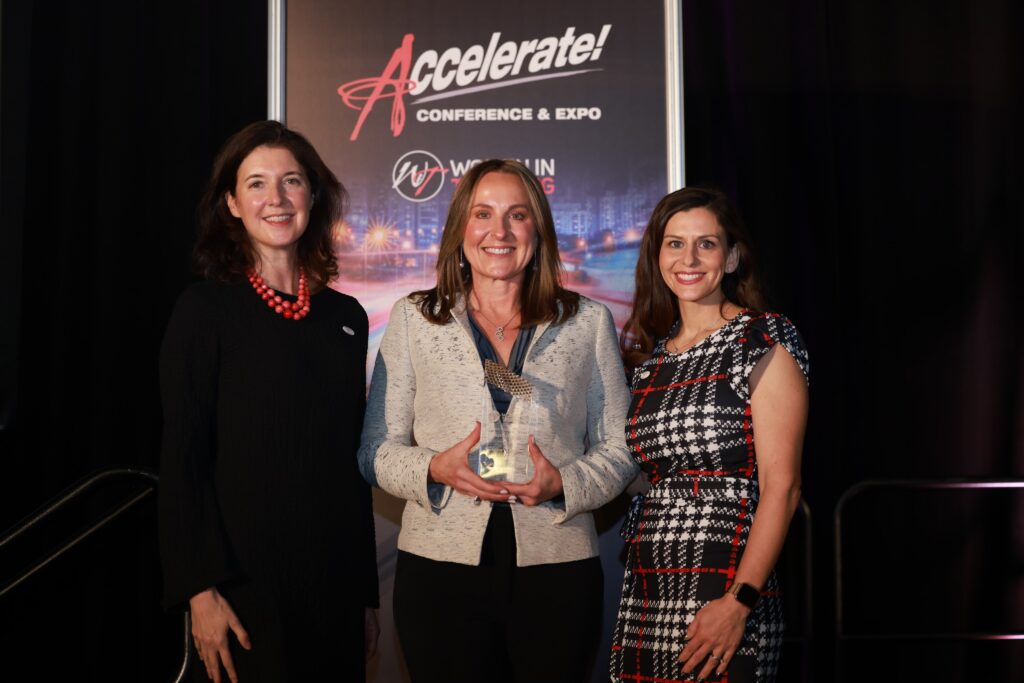
The Women In Trucking Association (WIT) presented Shelley Simpson, President, J.B. Hunt Transport Services, Inc. with its 2023 Influential Woman in Trucking award. The award is sponsored by Daimler Truck North America (DTNA), a manufacturer of Class 6-8 commercial vehicles in North America, and recognizes the achievements of female role models and trailblazers in the trucking industry. The winner was announced during the WIT Accelerate! Conference & Expo in Dallas. The announcement followed the panel discussion Unstoppable Women in Trucking You Must Know About, facilitated by Tracy Mack-Askew, Chief Engineer of Chassis, Propulsion, and Vocational Engineering, DTNA. Finalists for the 2023 award included Tori Blake, Chief Financial Officer and Co-owner, Western Logistics Express and WLX, and Megan Ferguson, Vice President of End-to-End Delivery Acceleration, Walmart. “It’s a privilege for Women In Trucking to recognize Shelley Simpson as our 2023 Influential Woman in Trucking award winner,” said Jennifer Hedrick, WIT President and CEO. “Shelley’s passion and leadership for this field, including her commitment to expanding gender diversity in transportation, have been evident throughout her nearly 30-year career.” “On behalf of Daimler Truck North America, our congratulations to all of the remarkable finalists for the 2023 Influential Woman in Trucking award who have and continue to work tirelessly to create expanded opportunities for women in our industry,” said Angela Lentz, Chief People Officer, DTNA. “In addition, I want to congratulate Shelly Simpson for being named the 2023 Influential Woman in Trucking. Her amazing and vast career, commitment to others and impact on trucking are all impressive accomplishments worthy of this unique recognition.” Simpson’s career at J.B. Hunt reflects the company’s continued progression as an innovative leader in the transportation and logistics industry. Since joining J.B. Hunt as an hourly customer service representative, she has held multiple positions for business segments across the company, including most recently serving as Chief Commercial Officer and Executive Vice President of People and Human Resources. In 2007, Simpson was named President of Integrated Capacity Solutions (ICS), a business unit she helped create. While continuing to develop ICS, Simpson assumed sales and marketing executive responsibilities in 2011 and was appointed Chief Marketing Officer. She took on additional leadership in 2014 as President of J.B. Hunt’s Truckload business segment, helping improve the efficiency of the company’s fleet. Simpson was named Chief Commercial Officer in 2017, leading strategic direction of marketing, sales, customer experience, and external product development, including J.B. Hunt 360°, the company’s technology platform for freight matching and operational efficiency. As the company evolved J.B. Hunt 360 and its technology-driven services, Simpson was also responsible for commercializing them on a global scale as the leader of International Services. In 2020, she was named Executive Vice President of People and Human Resources, leading the company’s efforts to create a more inclusive culture and work environment. Simpson was named President in 2022, and currently provides management and performance oversight for all company business units, in addition to emerging technology, developing services and People and Human Resources. Simpson serves on the board for multiple organizations, including the Mercy Health Foundation and the Dean’s Executive Advisory Board for the Sam M. Walton College of Business at the University of Arkansas, in addition to serving on the DSA Selection Committee for the Council of Supply Chain Management Professionals. In 2016, she received the Distinguished Woman in Logistics award by Women In Trucking and was named 2017 ATHENA Woman of the Year at the NWA Business Women’s Conference. In 2020, she received the Power50 Award by the National Diversity Council and was named a 2020 Top Influencer by Arkansas Money & Politics. In 2021, she was named one of the Top 100 Women in Supply Chain by Supply Chain Digital and has been named one of the top 100 HR Professionals by the National Diversity Council in 2022. She recently received the 2022 Woman of the Year in Innovation award by the Women’s Foundation of Arkansas and the Excellence in Free Enterprise Award from Economics Arkansas. Originally from Russellville, Arkansas, Simpson graduated from the University of Arkansas with a bachelor’s degree in marketing. She lives in Rogers, AR with her husband David and three children.
What is a Lithium Battery Digital Passport?
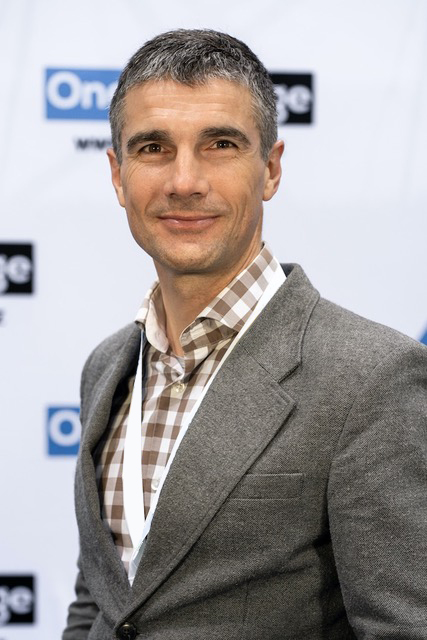
A digital battery passport provides easy access to structured, reliable, and complete information about the battery. This fresh initiative in the U.S. lithium battery landscape aims to simplify the choice and use of batteries for consumers. The U.S. government agencies are working on battery passport requirements, centralizing battery specifications and pertinent details, making it user-friendly for the everyday buyer. This digital battery passport offers a streamlined gateway to trustworthy and comprehensive battery data. Its widespread embrace is important for battery industry growth, pioneering products, safety, and environmental stewardship. As U.S. government bodies shape this directive, those in the electric industrial equipment sector can reference the EU’s recent regulations for insight. But, what exactly is a digital battery passport? Digital Battery Passport provides transparency, rewards responsibility A digital battery passport is a unique file created for each battery that contains complete information about the battery, its components, technical specifications, telemetry data, service history, expected life, etc. It is provided by the manufacturer to authorized operators. For companies operating electric industrial equipment, easy access to complete battery data translates into higher efficiency in their fleet management and equipment utilization. It also makes corporate ESG and emissions reporting easier. Supporting the development of a competitive, innovative battery market Structured and complete information helps operators increase battery serviceability and take the guesswork out of decisions on whether a battery is compatible with particular equipment. The data about installed integration protocols provides easier market access for new battery products, and fosters competition and innovation. Access to BMS data and software can help update CAN integration protocols with a charger and host vehicle or repurpose a battery for a subsequent application. Equipment utilization, reusing, and repurposing of lithium batteries The current lack of transparency in any battery’s actual state of health (SOH), expected cycle life, maintenance, and service history is a barrier to improving equipment utilization. This data can also help to define battery compatibility with secondhand equipment or repurposing. Reliable and easily accessible battery data will reduce the cost of testing and evaluation and help recover the residual value of a used battery. Ensuring a high level of environmental protection in the USA Manufacturer and user ESG claims can be substantiated with verified information on battery key specifications, such as cell chemistry, the origin of the core battery materials, the share of recycled materials used in manufacturing, and the full cycle carbon footprint. Supporting the growth of renewable energy sources, reducing CO2 emissions Testing and evaluating cells in used Li-ion battery packs is a bottleneck in the emerging business of re-manufacturing EV batteries for solar energy storage applications. Accurate battery data helps solve the problem of battery evaluation, reducing the cost of repurposing batteries for solar energy storage, and supporting the growth of renewable solar-generated electricity. With fewer batteries to recycle, the energy usage for recycling and waste management is reduced, resulting in fewer CO2 emissions. What are the main requirements of the recent EU “battery passport” regulations? The new EU “digital battery passport” regulation came into effect on 08/17/2023, with a planned start date of 02/18/2024. It introduces a few major demands for the batteries sold in the EU and is a good precedent for the US business community to study and learn from. All battery packs having a capacity over 2 kWh will need to have a digital battery passport to carry a disclosure of the CO2 footprint over the battery’s full life cycle, and to allow for user access to data on the battery’s state of charge and the number of cycles left in the battery before end-of-use. New rules have been introduced for repurposing and recycling, as well as a requirement for a minimum content of recycled metals used in manufacturing (cobalt, nickel, lithium, and lead). We wrote about how the data capabilities of forklift lithium batteries in the US can provide a solution to help EV car buyers and sellers deal with the current obscurity of battery health. Digital battery passports are a big step forward in solving this issue. Sustainability and Safety All rechargeable industrial batteries with a capacity of more than 2 kWh must have a “clearly legible and indelible” carbon footprint declaration and a label indicating (amongst other information) the levels of recycled cobalt, lead, lithium, and nickel used in the production of that battery. Digital battery passport EV batteries and rechargeable industrial batteries with a capacity of more than 2 kWh will need a “digital battery passport,” with information on the battery model, the specific battery, and its use. More generally, all batteries must have labels and QR codes detailing their capacity, performance, durability, and chemical composition and show the “separate collection” symbol. For batteries using a battery management system, the end-user should be able to determine the state of health and expected lifetime of such batteries at any time based on the data stored in the battery management system. This data should be updated at least daily, or more frequently where that is required for a specific purpose. Recycling / End-of-Life Management The battery management system of EV batteries shall include a software reset function, in case enterprises carrying out preparations for the re-use, repurposing, or re-manufacturing of EV batteries need to upload different battery management system software. Benefits of a mandatory digital battery passport for US users and dealers of industrial equipment A unique “digital passport” can reduce the complexity and minimize the risks of choosing, buying, and servicing an industrial battery for US customers. On the other hand, excessive regulation runs a risk of stymied product development and price increases. Some US battery manufacturers, like OneCharge, have already developed digital passports for their batteries giving users access to the battery data. What are the data points they can provide today? Digital Battery Passport Datapoints Each OneCharge battery is Wi-Fi-enabled and provides authorized users with complete, up-to-date battery data, including the following data points: battery model and serial number—these help consumers identify the battery and to find information about it online or in
Strategy is also about People and Culture Dynamics
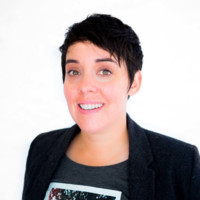
When organizations design strategies, the focus is typically on crafting an approach to achieve key organizational goals.These plans usually take hundreds of hours collectively, and once complete, are presented to the organization in a series of town halls, beautifully illustrated documents, and leadership meetings. Yet while we believe the strategy itself is the path to success, it’s the people and culture that make a strategy work. Yeah, yeah. “Culture eats strategy for breakfast”. But it doesn’t have to. Culture and strategy can work together in harmony, and even complement each other in a way to compete more effectively. This starts with crafting your strategy with your culture and people in mind. What I mean by this is by examining and deeply understanding what you’re genuinely good at, where you are today, and the behaviors inherent across the organization. Here’s why: What You’re Good At – Many strategies focus on big, aspirational goals, while ignoring what can be leveraged as differentiators today. This doesn’t mean your strategy shouldn’t look towards the future – it just means your strategy needs to consider what advantages you have today that you can capitalize on. For example, your company might be excellent at customer service, so your strategy should consider how this can be leveraged in a way to compete more effectively. Instead of thinking of it as a basic requirement and looking for alternative ways to grow, consider how this advantage can be amplified, accelerated, and further differentiated. Where You Are Today – For instance, a strategy may center on leveraging advanced technology to better engage customers and compete against new entrants. On its face, this sounds like a smart approach. Yet, if your organization is in the proverbial technology stone age, simply declaring this strategic goal won’t get you anywhere. Instead, understand where your organization is today, and articulate within your strategy the key steps you’ll take to get from here to there. In this scenario, becoming technologically advanced may seem like an unreasonable leap, especially if teams are struggling today to convert Word documents into PDFs. This is why knowing where you are today provides you with a clear starting point for articulating your strategy in a way that the organization can see a clear, plausible path forward. Behaviors Inherent In The Organization – Strategies often declare major behavior changes while ignoring how those changes should occur. For instance, a company might claim in its strategy that the goal is to be customer-centric. Arguably, an admirable objective. However, if there’s an undercurrent of doing what’s in the best interest of the organization rather than the customer, it will take a lot more than a strategy to change long-standing habits. Instead, examine organizational behaviors and identify specific ones that may undermine your strategy. Then, use those key behaviors that need to change as the infrastructure to support your customer-centric strategic goal. In short, don’t declare that you simply want change, but illustrate the key things that need to change to make it happen. Granted, there are cases where an organization has become so toxic and internally focused, that a major overhaul is in order. But these are the exceptions – most companies have gotten to the level they’re at by doing something right. And many of those people who helped the organization get there are still employed with the company. Don’t throw yet another strategy over the fence, hoping and praying this time it’s so compelling people won’t be able to resist making it happen. People need to not just understand where you want the company to go, but that you see the realities of today and have a clear path to getting the organization to its destination. Because people are the only thing that will bring a strategy to life. About the Author: Andrea Belk Olson is a keynote speaker, author, differentiation strategist, behavioral scientist, and customer-centricity expert.As the CEO of Pragmadik, she helps organizations of all sizes, from small businesses to Fortune 500, and has served as an outside consultant for EY and McKinsey. Andrea is the author of three books, including her most recent, What To Ask: How To Learn What Customers Need but Don’t Tell You, released in June 2022. She is a 4-time ADDY® award winner and host of the popular Customer Mission podcast. Her thoughts have been continually featured in news sources such as Chief Executive Magazine, Entrepreneur Magazine, Harvard Business Review, Rotman Magazine, World Economic Forum, and more. Andrea is a sought-after speaker at conferences and corporate events throughout the world. She is a visiting lecturer and startup coach at the University of Iowa, a TEDx presenter, and TEDx speaker coach. She is also an instructor at the University of Iowa Venture School. More information is also available on www.pragmadik.com and www.andreabelkolson.com.
Episode 434: The pivotal role of Propane in sustainable warehousing
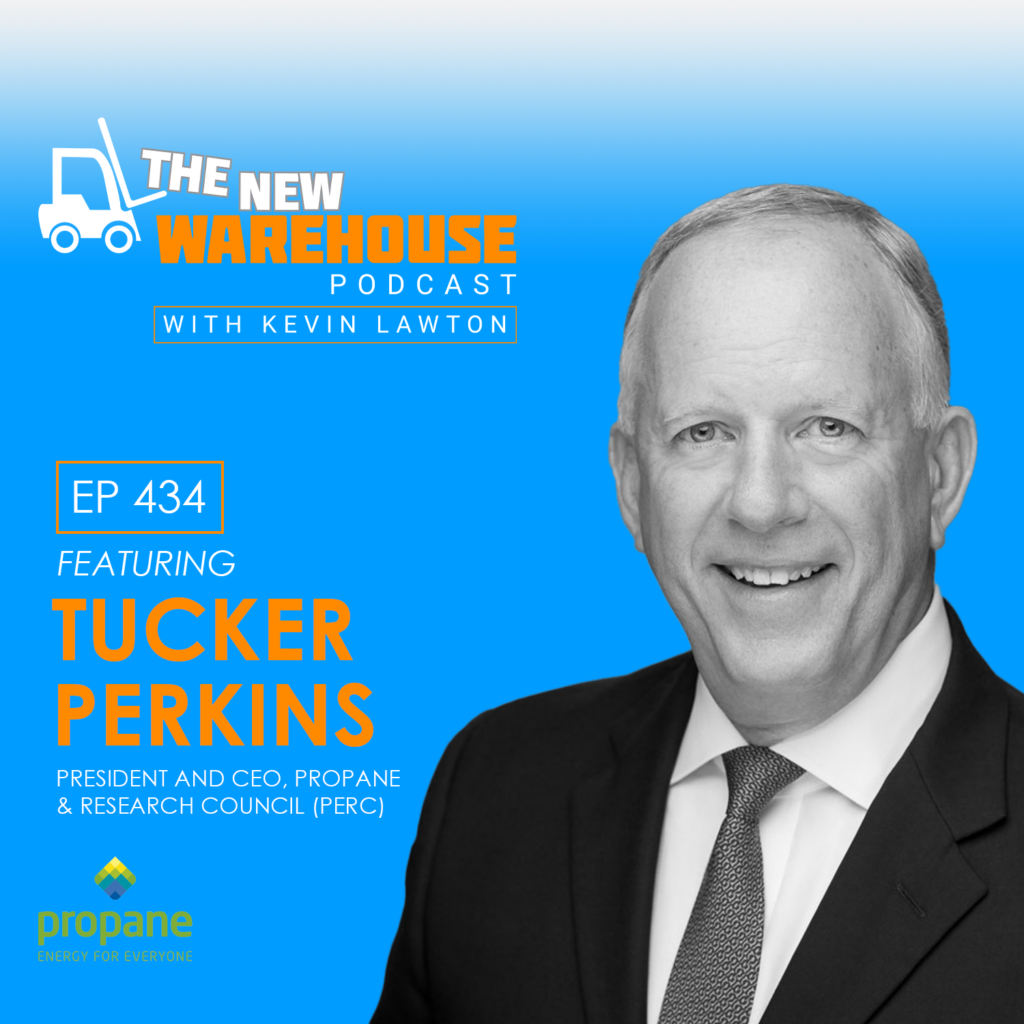
In the latest episode of The New Warehouse podcast, Kevin welcomes an influential figure in the energy sector—Tucker Perkins, CEO of the Propane Education and Research Council (PERC). Perkins leads an organization at the forefront of educating users and promoting the safe, innovative use of propane across various industries, including material handling and warehousing. PERC distinguishes itself by focusing not on lobbying or codes but on the end-users of propane. Whether it’s for farmers, builders, homeowners, or forklift operators, PERC’s mission is to optimize the use of propane, ensuring that machines operate efficiently and sustainably. Safety and training are pillars of their work, as they strive to ensure that industry professionals and consumers alike are well-versed in handling propane with the utmost care. But what exactly does PERC do beyond safety and training? How does propane hold up against other energy options in the industry’s shift toward sustainability? Tune in to the full episode as they unpack these questions, revealing insights that could reshape how the warehousing industry thinks about energy. The Role of Propane in Modern Material Handling Perkins notes, “We’re quickly becoming a two-fuel society regarding material handling.” Its benefits—economic and environmental—pose a compelling case for its increased adoption. In distribution centers, particularly those operating at ports or locations with limited access to electricity, propane is more than just a fuel—it’s a solution. Perkins states, “Five years ago, I think we identified that distribution centers probably just didn’t have adequate access to electricity for what some of their needs are going to be.” This foresight has led to an innovative approach where propane not only powers traditional equipment but also supports the infrastructure for electric vehicles (EVs). The introduction of renewable propane bolsters the sustainable narrative of propane. Perkins points to its potential to reach zero or even harmful carbon emissions, providing a “great story to tell about using conventional propane in a material handling application.” Furthermore, the application of propane goes beyond mobility. Perkins shares insights into power generation: “We’re involved around the country now in using what I think is at least far better than using diesel generators—using propane power generators.” Whether stationary or mobile, these generators are crucial in powering electric vehicle infrastructure without diesel. Harnessing Propane for Sustainable Warehouse Operations Perkins challenges the conventional narrative that fossil fuels are inherently detrimental to the environment, suggesting that the efficiency and cleanliness of propane, particularly in internal combustion engines like forklifts, often outperform electricity derived from coal-dependent grids. “In vast parts of the country, you would better serve the environment by directly using propane,” he asserts. This insight is crucial for warehouse operators assessing their carbon footprint and energy strategies. In collaboration with industry giants such as Hyster-Yale, Toyota, and Mitsubishi-Cat, PERC is innovating for the future. Perkins shares, “We’re working on hybrid forklifts that combine the best of electric powertrains and internal combustion powertrains,” which signifies a leap towards optimizing efficiency and sustainability. The transformative work of PERC focuses not only on current solutions but also on the future of renewable energy sources. Perkins envisions a shift toward renewable propane, especially in states with stringent environmental standards, offering “zero carbon” alternatives. This forward-thinking approach places propane as a versatile and potentially game-changing fuel in the material handling industry, securing its role not just for the present but for decades. The Rise of Renewable Propane in Warehousing Perkins is not just advocating for a greener option; he’s showcasing a shift in the industry towards a zero-emissions goal. He highlights the vast potential of renewable propane, made from diverse feedstocks, including used cooking oils, agricultural oils, and even recycled plastics. His narrative is not limited to hypotheticals; he describes how these processes have moved “from the lab into pilot scale and commercial scale.” The increasing adoption of renewable propane in states like California, Washington, and Oregon is paving the way for its wider acceptance across the warehousing industry. Perkins’ vision is clear: to harness the potential of propane as an energy source that ticks all the boxes for warehouses striving to stay ahead in a competitive, cost-sensitive, and environmentally-conscious market. His parting insight speaks volumes about the future trajectory of energy use in material handling and distribution, making propane not just a specialty but a strategic asset for the warehousing sector. Key Takeaways on Propane in Warehousing Propane is a versatile solution in material handling, with innovation pushing it from a traditional fuel to a key player in sustainable energy. Perkins challenges the environmental impact of fossil fuels, proposing propane, mainly renewable propane, as a cleaner alternative to coal-dependent electricity. Renewable propane is gaining traction as a strategic asset for zero-emission goals in warehousing, with industry collaborations fostering hybrid forklift technologies. The New Warehouse Podcast EP 434: The Pivotal Role of Propane in Sustainable Warehousing
Modular Automation Products for the automotive industry
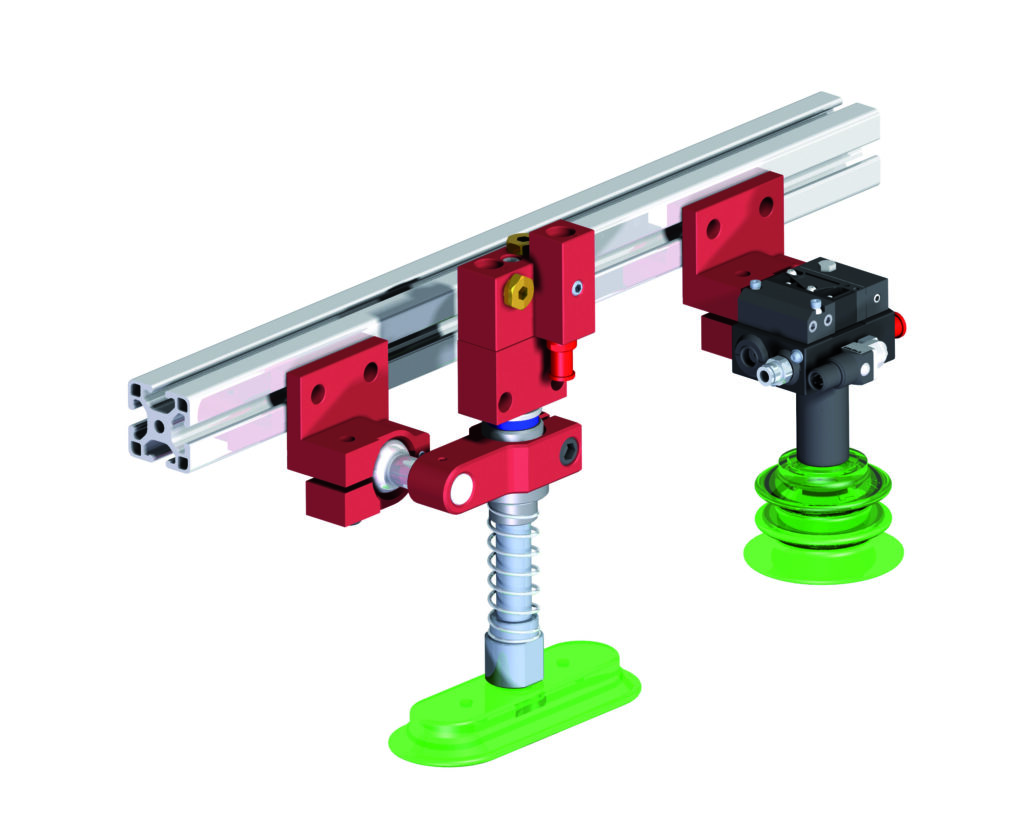
Material handling system features revolutionary vacuum technology The new tooling system allows auto manufacturers to construct vacuum-end effector tools with minimal design time to meet their exact needs for critical applications, such as sheet metal stamping, die-casting, injection molding, thermoforming and glass handling. Made of hard-coat anodized aluminium, Piab Modular Automation Tooling (PMAT) is lightweight and easy to assemble on-site without welding or use of special tools, making it ideal for handling materials in both the raw and finished stages of production. The PMAT is highly flexible and can be quickly configured to handle large metal parts or small plastic components with equal ease and success. PMAT features a swivel arm assembly with a choice of various functional attachments, including a PIAB vacuum pump. The air-driven vacuum pump provides vacuum pressure through Piab’s patented COAX® technology, a revolutionary design based on Piab’s multi-stage concept for creating vacuum pressure with compressed air. The result is a smaller, more efficient, more reliable and highly flexible technology that allows users to design a modular system. The vacuum pump can also be equipped with a check valve feature, a Piab innovation that “traps” vacuum pressure for an indefinite period in a leak-free system. This feature allows parts to be handled safely in case of system interruption or failure.
Hyster recognized by Fast Company for world’s first hydrogen-powered top-pick container handler
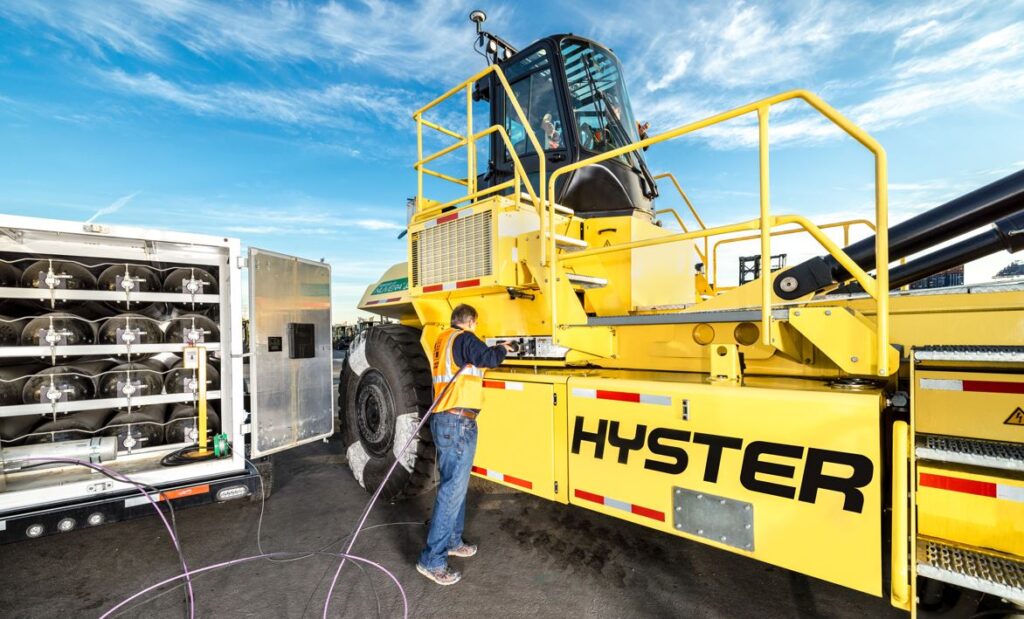
The solution, which is being piloted at the Port of Los Angeles, was named a finalist in the Innovation by Design Awards Hyster Company announces that the business publication Fast Company recognized the hydrogen-powered top pick as a finalist in its Innovation by Design Awards. The port equipment was named among the best sustainable projects of 2023 for its use of design to meaningfully reduce harm to the environment. The top-pick container handler, which is expected to provide emissions savings of 127 tons of carbon dioxide and almost half a ton of criteria pollution per year, is the first of its kind and is currently being piloted at the Fenix Marine Services terminal at the Port of Los Angeles. The truck is powered by two Nuvera® 45kw hydrogen fuel cells working in tandem with an on-board lithium-ion battery, with the fuel cells able to power the equipment directly or charge the battery. This allows operators to refuel the truck in about 15 minutes and then operate for 8 to 10 consecutive hours all while producing no harmful emissions – only heat and water. “With supply chains often accounting for more than 90% of an organization’s emissions, the pressure is on for ports to find sustainable solutions for their heavy-duty applications while still producing at the level they require,” said Jan Willem van den Brand, Director, Global Market Development, Big Trucks, Hyster. “This recognition joins a growing list of accolades that distinguish Hyster for this solution in particular, but also for our broader commitment to developing zero-emission solutions that push the boundaries of what is possible in electrifying intensive industries.” The top-pick container handler is one of several clean power-focused port equipment projects that Hyster is currently working on. Recently, the company shipped a hydrogen fuel cell-powered ReachStacker to Spain’s Port of Valencia, where it will undergo a pilot program of its own at one of Europe’s largest container terminals. Hyster will also supply an empty container handler and a terminal tractor, both powered by hydrogen fuel cells, to a port terminal in Germany, and is working with Capacity Trucks to develop electric and hydrogen-powered terminal tractors.