Episode 432: Wireless charging solutions in warehousing with Bastian Solutions and PULS
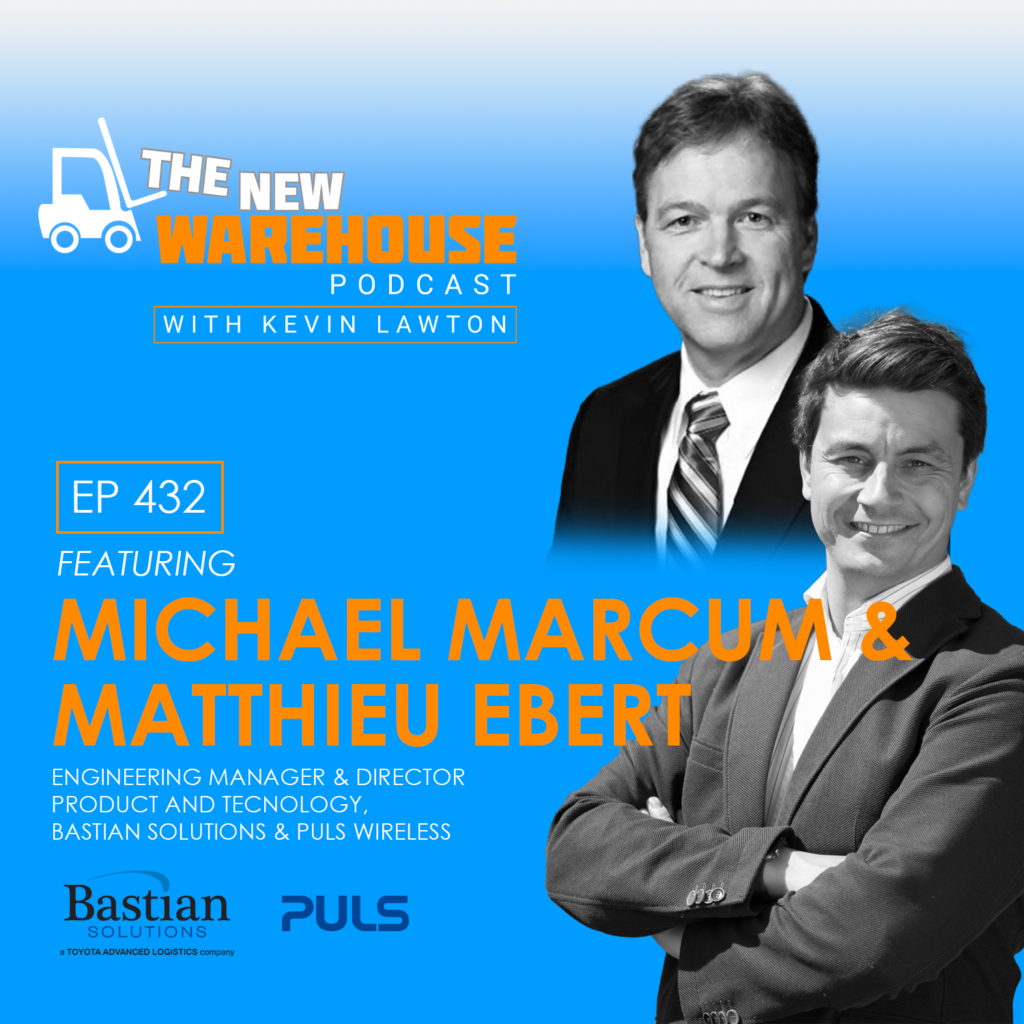
In the latest episode of The New Warehouse Podcast, Michael Marcum, the General Manager at Bastian Solutions, and Matthieu Ebert, the Director of Product and Technology at PULS Wireless, join the show to discuss the future of wireless charging in warehousing, power management, and automation. Bastian Solutions specializes in providing advanced logistics in material handling, such as automatic storage and retrieval systems and conveyor systems. PULS is a market leader in industrial DIN Rail power supplies. With the acquisition of Wiferion’s industrial charging business, PULS aims to expand its footprint to include mobile energy supplies. The conversation takes several fascinating turns as both guests discuss their experiences with mergers and acquisitions and how these corporate changes have set the stage for innovation. What is driving the demand for autonomous vehicles in manufacturing and warehousing? What are the challenges that slow down the adoption of AGVs in warehouses? Stay tuned as Michael and Matthieu provide deep insights into these burning questions. Challenges in Adoption of AGVs in Warehouses Introducing AGVs into a warehouse environment is not without its challenges. Let’s examine some of these challenges briefly: Lack of On-Site Maintenance – Unlike manufacturing setups, which often have robust maintenance teams, many warehouses rely on external services for equipment maintenance. Infrastructure Readiness – Warehouses may lack the necessary infrastructure to support AGVs, especially when compared to manufacturing environments. Safety Concerns – AGVs require robust safety measures to prevent accidents, which can be challenging to implement in a warehouse setting. Power Management – Traditional power solutions can have issues of wear and tear and may not offer the robustness required for seamless AGV operation. Skill Gap – The technical skill required to manage and maintain AGVs may not be readily available within the warehouse staff. Understanding these challenges is crucial for businesses considering the adoption of AGVs in their warehouses, as it informs the preparation and planning needed for successful implementation. According to Matthieu, the value proposition of wireless charging stations for warehouse environments is multi-faceted and significant. He outlines these advantages in a detailed conversation reflecting the challenges and opportunities in the current logistics landscape. The Case for Wireless Charging Solutions in Warehousing Matthieu emphasizes that his company’s wireless charging solutions are essentially “plug-and-play kits” that automate power management. “The problem with customers is that they don’t value some robust or fancy charging or power management technologies,” he explains. This is crucial because it allows AMR manufacturers to focus on their core value propositions, like smart navigation and complex load handling, instead of grappling with power management issues. In essence, these wireless charging systems streamline operations, allowing manufacturers to concentrate on optimizing performance areas that directly affect the bottom line. Matthieu’s second key point concerns the “necessity to design robust solutions.” He observes that many AMR builders begin with prototypes and then scale up but often overlook the limitations of their charging systems until they become problematic at higher volumes. By adopting robust, wireless charging solutions from the get-go, companies can sidestep these pitfalls. “A robust charging technology is not recognized on a small scale. It is recognized on large scale,” he says. This aspect is essential as AMRs are adopted in traditionally low-tech industries like warehousing, which may not have the expertise to manage complex systems. Integrating Wireless Charging Solutions in Warehouses Michael explains, “You do need to plan… it’s just design work, but you do need to do that design work upfront.” He further emphasizes the necessity of compatibility between the charger and the existing energy storage solutions, asking, “Whose battery do you have on your vehicle?” Matthieu also touches on this, highlighting the complexities of retrofits and stating, “I think there would even be the chance for a good ROI… the Brownfield business needs to be assessed case by case.” While it’s clear that integrating new technology comes with its challenges, both experts agree that the work is necessary and rewarding. Matthieu aptly refers to it as “the homeworks of the OEMs,” and suggests that as long as the “pain, or let’s say the cost in operations is high enough, they will invest in doing the retrofit.” Key Takeaways Wireless charging solutions offer “plug-and-play” convenience, allowing warehouses to focus on core operational efficiencies rather than power management. Implementing robust, scalable wireless charging technologies from the outset can help companies avoid issues as they scale up their automation efforts. Despite the challenges of integrating new technologies, both experts agree that the investment is worthwhile for significant operational improvements and potential ROI. The New Warehouse Podcast EP 432: Wireless Charging Solutions in Warehousing with Bastian Solutions and PULS
Henry Puhl to become new CEO of TGW Logistics
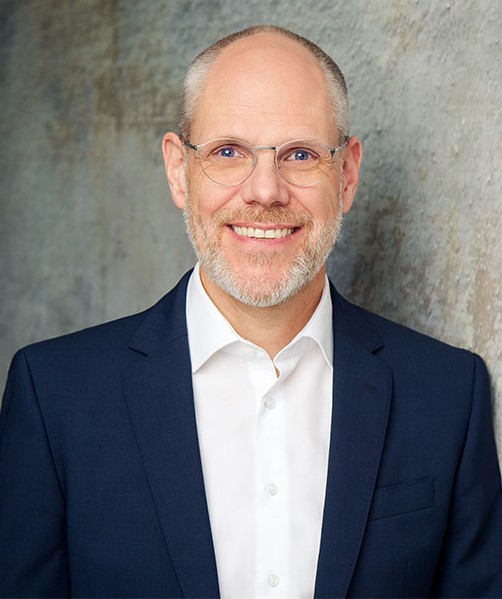
Dr Henry Puhl is moving from KION Group to the Upper Austrian intralogistics specialist and will become the new CEO of TGW Logistics in February 2024 Current CEO Harald Schröpf is leaving the company at his own request and will retire in calendar year 2024 The company wide transformation program will be continued and will give the company a new upswing The Board of Directors of TGW Future Private Foundation, the sole owner of TGW Logistics, has announced the appointment of Dr. Henry Puhl as the new Chief Executive Officer. Puhl will take over as CEO from February 2024, succeeding Harald Schröpf, who has led TGW Logistics as CEO for the past six years and has been instrumental in the company’s growth and success. The search for a new CEO was an intense process. Henry Puhl’s track record and leadership experience in the automation industry – most recently as CTO of the KION Group – as well as his strong identification with the company’s values stood out and made him the ideal choice to lead TGW Logistics into the next phase. The TGW Future Private Foundation, owner of TGW Logistics, is responsible for the selection of the new CEO. Chairman of the Board of Directors of TGW Future Private Foundation Martin Krauss on the selection. With Henry Puhl, we have been able to gain a highly qualified and empathetic leader who has a deep understanding of the industry and an impressive track record. His competence and the high level of identification with our foundation’s philosophy “Focusing on people – learning and growing” testify to the right mix of heart and mind. These qualities, together with his strong customer orientation, make Henry Puhl the ideal leader for TGW Logistics and we look forward to working with him“, says Krauss. In addition to his experience as CTO of the KION Group, Henry Puhl has an international track record in industrial technology and automation, and has extensive knowledge covering the entire value chain. He is a charismatic leader with a deep understanding of the customer perspective, broad technical know-how and a lot of transformation experience. The 52-year-old’s professional career includes well-known global companies such as the CLAAS Group and John Deere (Deere & Company). Intralogistics is looking forward to a very positive growth market. TGW Logistics has state-of-the-art technology and unique know-how, already has a very good business base in Europe and a lot of potential to position itself more strongly in the USA as well. We will use the transformation that has already begun in the company to elevate TGW Logistics to the top league of international players and make optimal use of market potentials.” adds Puhl. TGW Future Private Foundation is convinced that TGW Logistics will further strengthen its global position in intralogistics and logistics automation under Puhl’s leadership and looks forward to a promising future. Outgoing CEO Harald Schröpf, who was instrumental in paving the way for today’s TGW Logistics, will retire in 2024. His commitment to TGW Logistics and his successful work are deeply appreciated. He will play a critical role in preparing the company for the transition and facilitating a smooth transition over the next few months. To ensure this he will continue to be available as an advisor to the company after February 1st.
EnerSys honors Breast Cancer Awareness Month with battery donation to ProLift Toyota Material Handling
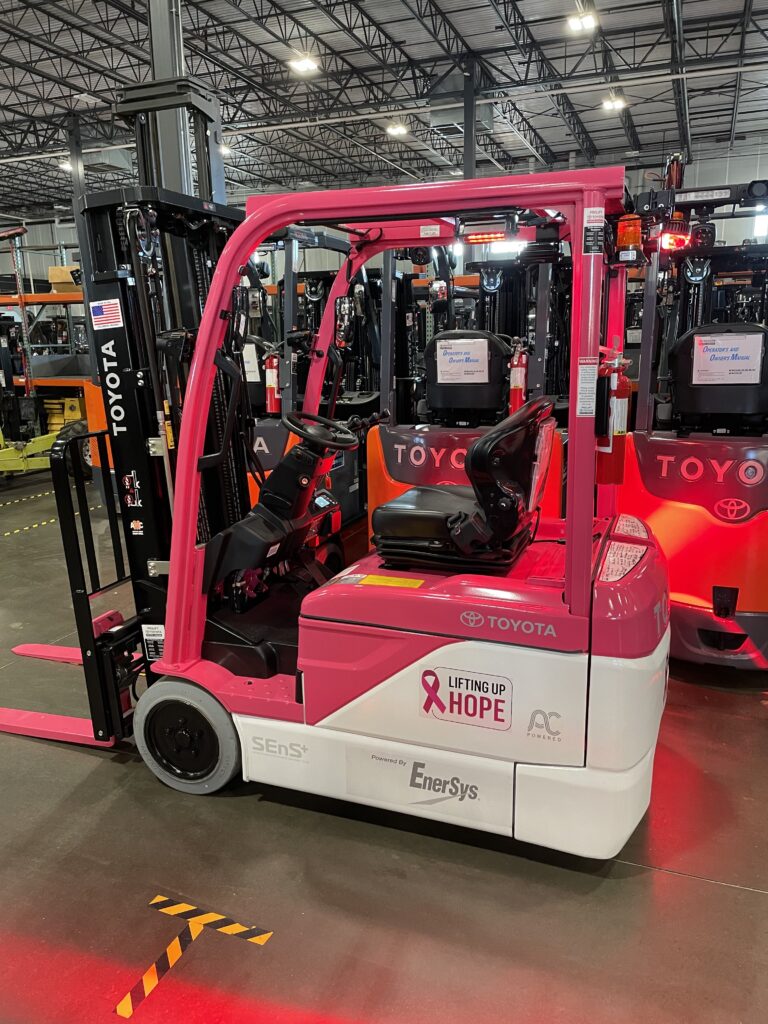
EnerSys is honoring breast cancer awareness month with a special battery donation to ProLift Toyota Material Handling for its rental truck campaign. Specifically, EnerSys has donated an IRONCLAD® Deserthog battery, which will be used to power a pink Toyota FBE20U 3-wheel electric forklift vehicle. All the proceeds from the rental truck will be donated to support the Susan G. Komen® foundation and its ongoing efforts to assist breast cancer patients and fund continuing research for a cure. “While EnerSys has partnered with Toyota and its subsidiaries for several years on various charitable programs, this is the first time we’ve been able to support patients and families affected by such a devastating disease,” said Rick Losacker, Senior OEM Manager, Motive Power at EnerSys. “Millions of women and their loved ones have been affected by breast cancer, so it’s deeply humbling to be able to help power a campaign with such heartfelt meaning and purpose. We hope this helps broaden awareness of this important topic within our industry and beyond.” The customized hot pink forklift, adorned with the tagline, “Lifting Up Hope,” provides an opportunity to help build awareness about breast cancer and the importance of early detection as well as the latest research, resources and treatment options available to women and men within the material handling industry. The vehicle was officially unveiled during 2023 Toyota Week in September. Founded in 1978, ProLift Toyota Material Handling provides new, used, and rental forklifts and other warehouse solutions, as well as training. With headquarters in Louisville, Kentucky, it serves customers in Kentucky, Indiana, Ohio and West Virginia. The rental truck will be available to customers across ProLift’s entire service territory.
AutoStore launches new R5 Pro Robot
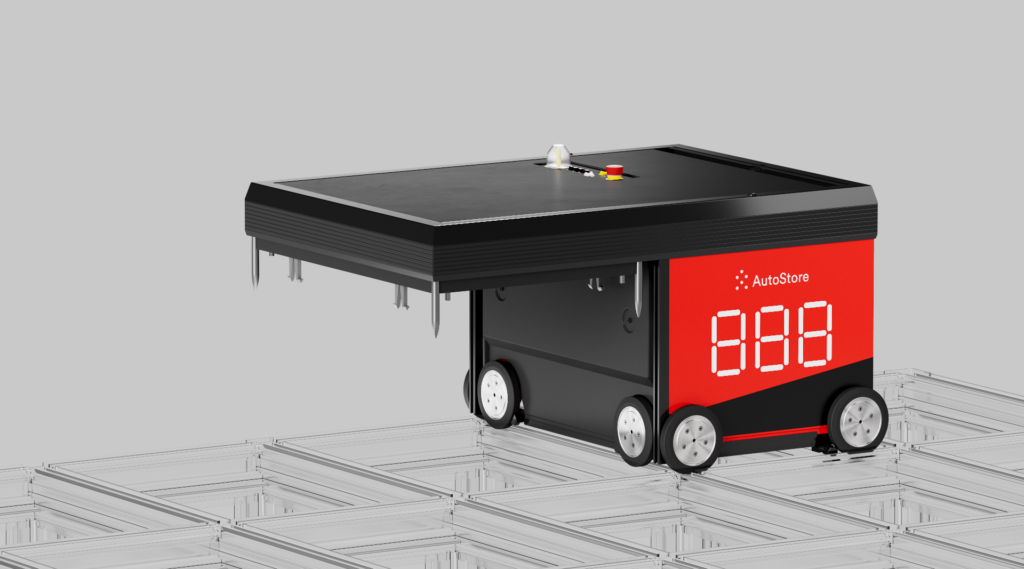
AutoStore’s new R5 Pro Robot for large-scale operations frees up space for additional products in the warehouse and improves Robot efficiency at a reduced total cost of ownership AutoStore™, a robotic technology company, has introduced the R5 Pro Robot, the latest version of the company’s field-proven R5 Robot. This new robotic solution is designed to address the specific demands of large-scale e-commerce operations, emphasizing better space usage, higher performance, and reduced total ownership costs for companies running multi-shift operations at scale. Carlos Fernandez, Chief Product Officer at AutoStore, points to the growing demand for large, high-throughput systems in the e-commerce sector: “The R5 Pro offers an edge by augmenting productivity per Robot during extended operations, optimizing space usage, and reducing the total cost of ownership, ultimately enhancing the customer experience while boosting profitability.” The R5 Pro is designed to meet the needs of e-commerce organizations with large-scale multi-shift operations. Key features and benefits of the R5 Pro Robot include: Enhanced productivity: By deploying the R5 Pro at a large AutoStore site, customers can reduce the number of Robots required on the same grid by up to 15%, when compared to using the R5 Robot, enabling better routing and enhanced system efficiency. Continuous operations: The use of an LTO (Lithium-Titanium Oxide) battery in the R5 Pro allows rapid charging, improving individual Robot availability during multi-shift operations. Space and Cost Optimization: Up to 86% fewer chargers required with the LTO battery allows for more efficient use of warehouse space, accommodating additional SKU storage or reducing the required footprint. In addition, customers achieve significant cost savings related to electrical infrastructure. AutoStore’s Chief Product Officer Fernandez continues, “The introduction of the R5 Pro improves both our market position and the value proposition for customers managing very large systems and high-throughput operations, typically characterized by extended operating hours and a substantial robot count.” One prominent AutoStore customer, Tobias Sjölin, CTO, Fulfillment and logistics at Boozt, shares the customer perspective: “As a leading e-commerce company, we are always looking for new ways to optimize warehouse operations. We are excited about the R5 Pro, the latest addition to the AutoStore R5 series, which will bring tangible benefits to customers with large AutoStore systems that require speed.” “Being able to reduce charging time during multi-shift operations offers great potential for improved productivity. The projected higher productivity per robot means we would need significantly fewer robots and chargers to achieve our required throughput – and also enable us to fit more SKUs within our existing Grid. But in the end, it’s all about the total cost of ownership. All these incremental savings add up over time and allow us to remain competitive.”
Staffing employment edges down in October
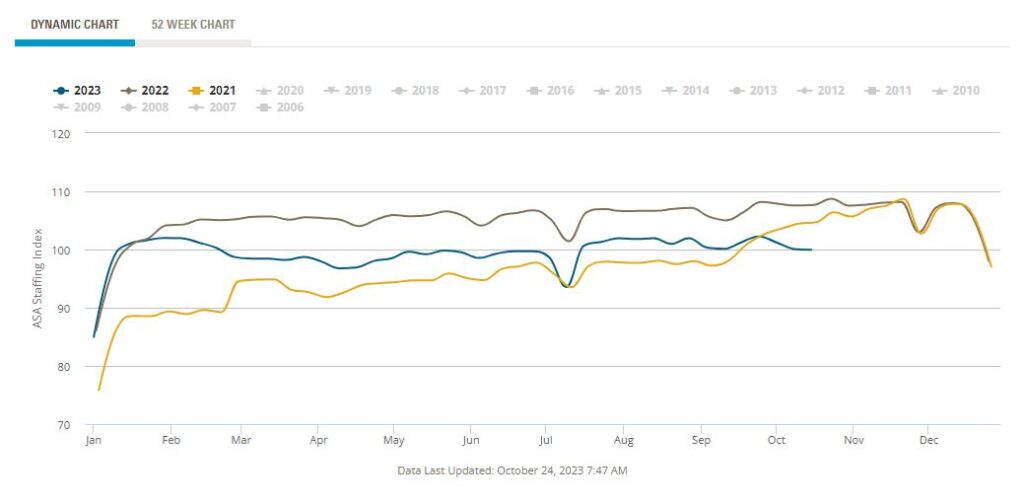
Staffing employment edged down in the week of Oct. 9-15, with the ASA Staffing Index decreasing by 0.1% to a rounded value of 100. Staffing companies listed no one primary factor that limited further growth. Staffing jobs were 7.2% below the same week last year. New starts in the 41st week of the year inched up 0.9% from the prior week. Close to half of all staffing companies (45%) reported gains in new assignments week to week. The ASA Staffing Index four-week moving average decreased from the prior week to hold at a rounded value of 101, and temporary and contract staffing employment for the four weeks ending Oct. 15 was 6.4% lower than the same period in 2022. “Staffing employment has eased in October, though it remains above the lows we saw in the second quarter of the year,” said Tim Hulley, assistant research director at ASA. This week, containing the 12th day of the month, will be used in the October monthly employment situation report scheduled to be issued by the U.S. Bureau of Labor Statistics on Nov. 3.
U.S. rail traffic for the week ending October 21, 2023
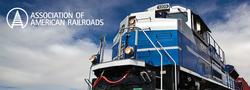
The Association of American Railroads (AAR) has reported U.S. rail traffic for the week ending October 21, 2023. For this week, total U.S. weekly rail traffic was 505,985 carloads and intermodal units, up 1.8 percent compared with the same week last year. Total carloads for the week ending October 21 were 234,893 carloads, up 1.5 percent compared with the same week in 2022, while U.S. weekly intermodal volume was 271,092 containers and trailers, up 2.1 percent compared to 2022. Six of the 10 carload commodity groups posted an increase compared with the same week in 2022. They included metallic ores and metals, up 3,855 carloads, to 22,463; nonmetallic minerals, up 1,595 carloads, to 33,966; and chemicals, up 1,076 carloads, to 31,517. Commodity groups that posted decreases compared with the same week in 2022 included grain, down 2,374 carloads, to 20,367; coal, down 1,442 carloads, to 67,459; and forest products, down 390 carloads, to 7,805. For the first 42 weeks of 2023, U.S. railroads reported cumulative volume of 9,468,896 carloads, up 0.3 percent from the same point last year; and 10,133,251 intermodal units, down 7.4 percent from last year. Total combined U.S. traffic for the first 42 weeks of 2023 was 19,602,147 carloads and intermodal units, a decrease of 3.8 percent compared to last year. North American rail volume for the week ending October 21, 2023, on 12 reporting U.S., Canadian and Mexican railroads totaled 348,134 carloads, up 0.3 percent compared with the same week last year, and 355,428 intermodal units, down 0.1 percent compared with last year. Total combined weekly rail traffic in North America was 703,562 carloads and intermodal units, up 0.1 percent. North American rail volume for the first 42 weeks of 2023 was 27,452,637 carloads and intermodal units, down 3.5 percent compared with 2022. Canadian railroads reported 96,761 carloads for the week, down 1.0 percent, and 72,717 intermodal units, down 5.0 percent compared with the same week in 2022. For the first 42 weeks of 2023, Canadian railroads reported cumulative rail traffic volume of 6,677,072 carloads, containers and trailers, down 3.5 percent. Mexican railroads reported 16,480 carloads for the week, down 8.3 percent compared with the same week last year, and 11,619 intermodal units, down 13.8 percent. Cumulative volume on Mexican railroads for the first 42 weeks of 2023 was 1,173,418 carloads and intermodal containers and trailers, up 2.4 percent from the same point last year. To view the rail traffic charts, click here.
E Tech Group to showcase Oligonucleotide Automation Advancements at Rockwell Automation Fair 2023
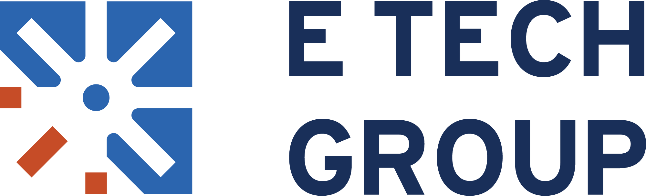
Rockwell Automation Gold Partner E Tech Group to present three educational sessions and demonstrate oligonucleotide automation in booth #232 at Automation Fair in Boston, MA November 6-9, 2023 E Tech Group, a provider in high-quality automation, control, and engineering services for industrial clients and Gold Certified Rockwell Automation Partner, has announced the company will be leading three separate presentations at the 2023 Rockwell Automation Fair and exhibiting in booth #232. Automation Fair will take place November 6-9, 2023, in Boston, MA at the Boston Convention and Exhibition Center. E Tech Group will host three different educational sessions at the show. On Tuesday, November 7 at 11:00 am ET, Vivek Puthezath, E Tech Vice President of Northeast Operations, will be presenting “Oligonucleotide Production Automation Improves Yield and Consistency for a Pharmaceutical Manufacturer”, a case study on manufacturing oligonucleotide pharmaceutical drugs, converting a highly manual process into a fully automated system. On Tuesday, November 7, at 1:00 pm ET, “PlantPAx 5.0 Makes Oligos Go Go Go! Accelerating the Pace of Life Science Research” will be presented by Umar Karim PMP, P.E., TUV FSE, E Tech Senior Automation Engineer I, where he will instruct attendees on how PlantPAx 5.0 was used for a new oligonucleotide production facility. The third presentation will be given twice by Jeff Allen, E Tech Application Engineering Manager, and Steve Scheffler, E Tech Engineering Manager, both Tuesday, November 7 at 1:00pm ET and Thursday, November 9 at 11:00am ET. Jeff and Steve will share insights on gaining value in Industry 4.0 through edge and cloud computing during “Leveraging the Power of Industry 4.0.” “As one of the largest Rockwell partners in the life sciences space, E Tech Group is thrilled to be presenting during three different sessions at the 2023 Rockwell Automation Fair showcasing our commitment to innovation and excellence across the industry,” said Matt Wise, Chief Executive Officer of E Tech Group. “Our passion for automation and our dedication to improving processes have allowed us to lead the way in transforming oligonucleotide production and accelerating life science research. Join us at Automation Fair to experience firsthand how E Tech Group is shaping the future of pharmaceutical manufacturing and Industry 4.0.” Visit E Tech at Booth #232, to connect with the E Tech team and see their oligonucleotide automation demonstration on display at the front of the booth. The demo will be a high level look at how automation can provide the ability to replicate a traditionally manual process over and over, track production, and lessen operator interaction with caustic chemicals. Automation Fair is an opportunity to learn about new innovations in the industry, network with professionals, and understand steps to achieving digital transformation. Register for Automation Fair here.
PLASTICS: Break free act lacks collaboration needed to achieve real sustainability goals
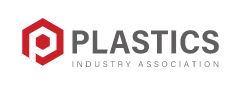
The Plastics Industry Association (PLASTICS) announced its strong opposition and disappointment in the Break Free from Plastic Pollution Act of 2023, as reintroduced in the U.S. Congress. “Instead of working towards compromise and common-sense policies, this new iteration of the Break Free from Plastic Pollution Act is even worse and less collaborative than previously, moving further from a realistic proposal,” said Matt Seaholm, President and CEO of PLASTICS. “The plastics industry stands ready to work with both sides of the aisle to develop real solutions to the environmental concerns this measure supposedly addresses. We believe there are answers to the environmental challenges we face, such as investments in recycling infrastructure and greater demand for recycled content through minimum requirements and stronger end-markets. “Plastics is the preferred material in many applications because it uses less energy and fewer resources to manufacture and transport, in addition to its ability to be reused and recycled—but this misguided legislation overlooks scientific facts and would likely unintentionally lead to an increase in greenhouse gas emissions. “The Break Free from Plastic Pollution Act would negatively impact the American economy, harm the over one million men and woman who are employed by the plastics industry and hurt other industries reliant upon them as an essential part of the supply chain. “Instead of one-sided proposals that don’t move us forward, we need to work together to craft sound policy that will actually help our environment,” concluded Seaholm. Facts about plastic: Of the materials used for consumer products, plastic has the lowest GHG impact; An independent study from McKinsey & Co. found plastics help reduce greenhouse gas emissions by 10-90%. The overwhelming majority of plastic waste will not be addressed by this legislation; more than 90% of plastic in the oceans comes from 10 river systems in Southeast Asia and Africa—not from the U.S and not subject to this legislation. Plastics only make up 12% of municipal solid waste, and packaging only makes up 5%. Thousands of facilities across the United States are involved in the manufacturing of plastics; this legislation could prompt many to shutter and move offshore to countries with less environmental safeguards.
Hope Floats with Kostreba’s winning bid for the 2023 Trailer for a Cause
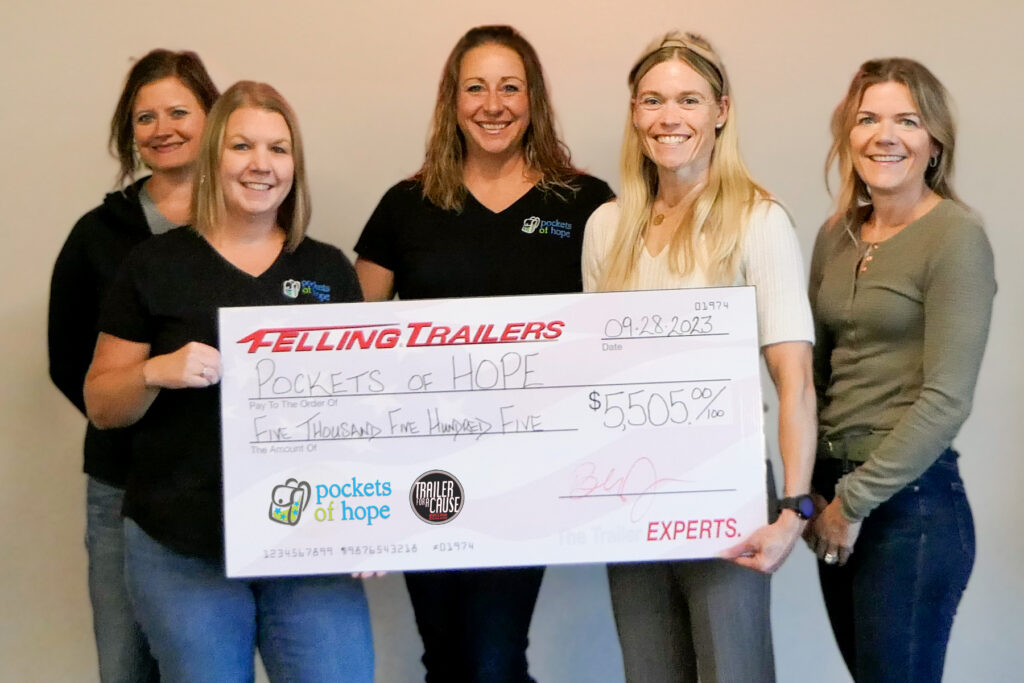
Felling Trailers, Inc. conducted its eleventh annual online auction of an FT-3 drop deck utility trailer to benefit a non-profit organization: Pockets of Hope. A winning bid of $5,505.00 won the auction that ended at noon on Sept. 15th. The bid winner was Joe Kostreba of Sauk Centre, MN. Joe, a local contractor, has participated in previous Trailer for a Cause auctions and was the bid winner in the 2021 Trailer for a Cause auction that benefitted the Minnesota Fire Fighters Foundation (MNFFF). Like in years prior, Joe had been watching the auction as the week went along. By chance, he had some downtime just before the auction was set to close, and within the last 2 minutes, he captured the winning bid. A week after the auction closed, arrangements were made for Joe to come and pick up his new trailer. “I have been fortunate enough that my construction business has been good and busy, and I am grateful for that. As a small business owner, I want to spread that around, bidding on this trailer is one way to do that.” said Kostreba. The 2023 Trailer for a Cause FT-3 utility trailer was painted custom “Hope Blue” and bared the Pockets of Hope emblem. Several Felling Trailers’ suppliers joined to support Pockets of Hope by sponsoring the trailer build, from lighting to tires and paint. The 2023 Trailer for a Cause sponsors are Trans-Texas, PPG, Dexter, Sealco, Peterson, Industrial Wood (Blackwood), Demco, and Pacific Rim. Felling Trailers wants to help generate awareness about Pockets of Hope, the work they do, the children they serve, and the hope and security their backpacks provide to children. The online auction ran for five days, from Monday, Sept. 11th at noon CST through Friday, Sept. 15th at noon CST, ending with Joe’s winning bid of $5,505. One hundred percent of the $5,505 went to benefit Pockets of Hope! One week after Joe had picked up the 2023 Trailer for a Cause FT-3, the Pockets of Hope team made the trip to Sauk Centre to accept the donation check. Founders Lisa Schroers, Briana Sjodin, and Jennifer Bruzek met with Felling Owners Brenda Jennissen and Bonnie Radjenovich to present them with the check for $5,505. “Thanks for an amazing trailer for a cause! We just got this message today from a social worker. The money you raised gives us the opportunity to keep giving out these backpacks!” said Lisa. The message read, “I met with a few children at the Child Advocacy Center earlier this week. They have been experiencing chronic homelessness and allegations of physical abuse. When the children saw the bags, their eyes got big, and they had the biggest smiles. They were so excited as they took items out of the bag, one at a time. Each item they took out, the more excited their voices became. When one of the boys took out the bag of shampoos and soaps, he held it up high and exclaimed, “Now I have my own stuff; that’s all mine!” Another child ran to me with a blanket and pressed it against my face, saying, “Feel this; it’s so soft. I’m going to sleep on it tonight.” The children shared, “This is better than Christmas.” Thank you for Pockets of Hope. The bags genuinely make a difference for so many children in our community.” “Hope gives each person, young and old, the strength to overcome the difficulties and hardships in their life. We are honored to support Pockets of Hope and witness the difference they are making in young people’s lives. God’s work, their hands, keeping hope afloat,” said Brenda Jennissen Felling Trailers CEO/President.
KION Group delivers strong earnings and free cash flow in the first nine months of 2023 and raises outlook
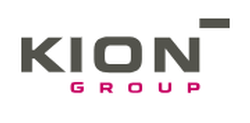
Revenue at €8.347 billion (Q1–Q3 2022: €8.243 billion) Adjusted EBIT more than doubles to €571.9 million (Q1–Q3 2022: €210.6 million) Adjusted EBIT margin at 6.9 percent (Q1–Q3 2022: 2.6 percent) Strong free cash flow at €329.3 million (Q1–Q3 2022: minus €971.9 million) Sustainability: MSCI increases KION Group’s ESG rating to AAA Outlook raised for the Group’s adjusted EBIT and free cash flow KION Group strengthens leadership team The KION Group achieved a strong increase in its profitability and free cash flow in the first nine months of this year. These results were mainly driven by a continued momentum in the Industrial Trucks & Services (ITS) segment. The primary reasons for this impressive performance were the stabilization of the supply chain enabling higher production volumes, and the positive effects of the measures initiated in 2022 to boost commercial and operational agility. “The significant upward trajectory of KION Group is once again underscored by these strong results for the first nine months of this year”, says Rob Smith, Chief Executive Officer of KION GROUP AG. “This strong momentum reinforces our leading position in intralogistics solutions for customers worldwide.” Consolidatedrevenue amounted to €8.347 billion in the first three quarters of 2023, a year-on-year rise of 1.3 percent (Q1–Q3 2022: €8.243 billion). The proportion of consolidated revenue attributable to the service business increased to 44.6 percent (Q1–Q3 2022: 41.7 percent). Total revenue in the Industrial Trucks & Services segment increased by 16.5 percent to €6.160 billion (Q1–Q3 2022: €5.288 billion). The systematic processing of the sizeable order book built in 2022 had a positive impact on revenue in the segment. In addition, price increases implemented in the previous year made a substantial contribution to revenue growth. At 48.1 percent, the proportion of the segment’s external revenue attributable to the service business was lower than in the prior-year period (Q1–Q3 2022: 51.7 percent). In the Supply Chain Solutions segment, total revenue contracted by 25.4 percent to €2.216 billion (Q1–Q3 2022: €2.970 billion). Whilst the stable and higher-margin service business (customer services) registered a proportionate increase to 34.9 percent (Q1–Q3 2022: 23.9 percent) of total revenue muted customer demand in the project business (business solutions) in the preceding quarters led to a drop in revenue. Moreover, the projects secured in the reporting period were predominantly of a long-term nature, from which the revenue will be recognized over an extended period. Adjusted EBIT for the nine-month period increased to €571.9 million (Q1–Q3 2022: €210.6 million). Price adjustments introduced in 2022 and, on the supply side, the general improvement in the availability of materials and stable costs contributed to these strong earnings. Reflecting this, the KION Group’s adjusted EBIT margin significantly increased to 6.9 percent (Q1–Q3 2022: 2.6 percent). The adjusted EBIT of the Industrial Trucks & Services segment more than doubled to €613.6 million (Q1–Q3 2022: €300.4 million). This was partly due to the earnings effect from increases in volumes and prices and the efficiency gains in production. The ITS segment’s adjusted EBIT margin returned to double digits to 10.0 percent for the first nine months of the year (Q1–Q3 2022: 5.7 percent). Adjusted EBIT for the Supply Chain Solutions segment was €30.7 million in the first three quarters of 2023 (Q1–Q3 2022: € minus 32.2 million). The segment’s earnings improved in the third quarter with the successive completion of lower-margin orders. The adjusted EBIT margin for the first nine months of 2023 turned positive to 1.4 percent (Q1–Q3 2022: minus 1.1 percent). The Group’s net incomefor the period amounted to €228.3 million, which was up by €161.4 million year on year (Q1–Q3 2022: €66.9 million). Basic earnings per share attributable to the shareholders of KION GROUP AG came to €1.70 (Q1–Q3 2022: €0.48) based on a weighted average of 131.1 million no-par-value shares (Q1–Q3 2022: 131.1 million). The Group generated free cash flowof €329.3 million (Q1–Q3 2022: € minus 971.9 million) during the reporting period. MSCI, one of the leading index providers, raised the KION Group’s sustainability rating to AAA at the end of September, putting the KION Group in the top 10 percent of its sector. Outlook In the third quarter of 2023, the KION Group once again significantly increased its earnings and margins compared with the corresponding quarter of 2022. The ongoing positive effects of the measures taken to enhance operational and commercial agility led to a particularly noticeable improvement in the financial performance of the Industrial Trucks & Services segment and thus of the Group compared with the first half of 2023. Having already updated it in July 2023, the KION Group has once again raised its 2023 full-year outlook for the key performance indicators adjusted EBIT, free cash flow and return on capital employed (ROCE) because the earnings of the Industrial Trucks & Services segment in the third quarter of 2023 were better than expected. This was primarily due to the continued improvement in the availability of materials and the easing of material prices on the supply side. The 2023 full-year outlook for revenue and adjusted EBIT in the Supply Chain Solutions segment has been lowered. This is because the customer orders received in the reporting period were predominantly for long-term projects, which means that only a small volume of revenue from these projects will be recognized in 2023. Furthermore, customers are continuing to postpone the placement of orders. In light of this situation, the Executive Board of KION GROUP AG decided on October 13, 2023 to update the outlook for 2023, both for the Group and for the Industrial Trucks & Services and Supply Chain Solutions segments. The outlook had originally been published on March 2, 2023 and was most recently updated in July 2023. The new outlook is shown below: Outlook for 2023 KION Group Industrial Trucks & Services Supply Chain Solutions Outlook July 2023 Outlook October 2023 Outlook July 2023 Outlook October 2023 Outlook July 2023 Outlook October 2023 Revenue1 minimum €11.4 billion minimum €11.2 billion minimum €8.2 billion minimum €8.2 billion minimum €3.2 billion minimum €3.0 billion Adjusted EBIT1 minimum €680 million minimum €780 million minimum €730 million minimum €830 million minimum €65 million minimum €55 million Free cash flow minimum €615 million minimum €660 million – – – – ROCE minimum 6.0% minimum 7.0% – – – – 1 Disclosures for the Industrial Trucks & Services and Supply Chain Solutions
Seagull Scientific appoints Kendall Hyatt as new Director of Business Development and Strategic Alliances
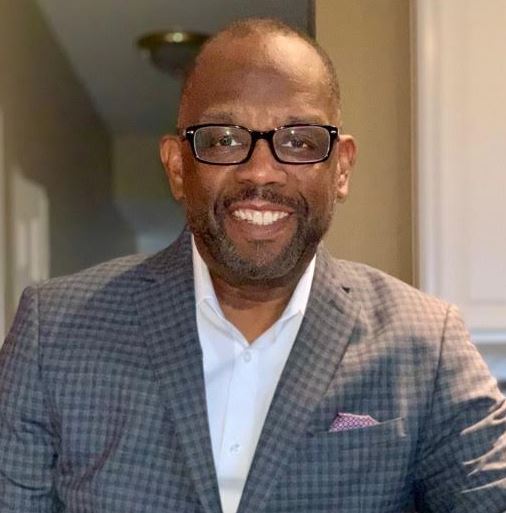
Seagull Scientific, maker of BarTender® software, the global leader in software to print, mark and code labels, RFID tags, products, and packaging, has announced the appointment of Kendall Hyatt as the company’s new Director of Business Development and Strategic Alliances. “Kendall Hyatt has made significant contributions to the growth of Seagull Scientific’s business over the past 18 months as our Americas’ Business Development Manager of Channel Sales”, said Matthew Brine, Chief Revenue Officer of Seagull Scientific. “We are thrilled to welcome Kendall Hyatt to the role of Director of Business Development and Strategic Alliances. His skills and competencies across multiple technology sectors make him an excellent fit for this role. We look forward to his continued contributions and leadership.” Kendall’s appointment as Director of Business Development and Strategic Alliances is timely, coinciding with the creation of Seagull Scientific’s new Business Development and Strategic Alliances Sales Team. “I’m excited to work closely with my colleagues and our partners, to deliver value that meets the dynamic needs and business goals of our mutual customers,” said Kendall Hyatt, Director of Business Development and Strategic Alliances at Seagull Scientific. “As we continue to expand our digital transformation offerings, we are dedicating time and resources to positively impact customers along their modernization journey.” BarTender is the first labeling, marking and coding solution to offer full integration with the entire Microsoft Dynamics 365 ERP product suite. Click here to learn more about how BarTender customers can harness BarTender’s trusted, proven, label printing and management solutions for the Microsoft Dynamics 365 Supply Chain Management or Business Central.
Robroy Industries® Enclosures Division announces promotion of Roger Schroder to Operations Manager
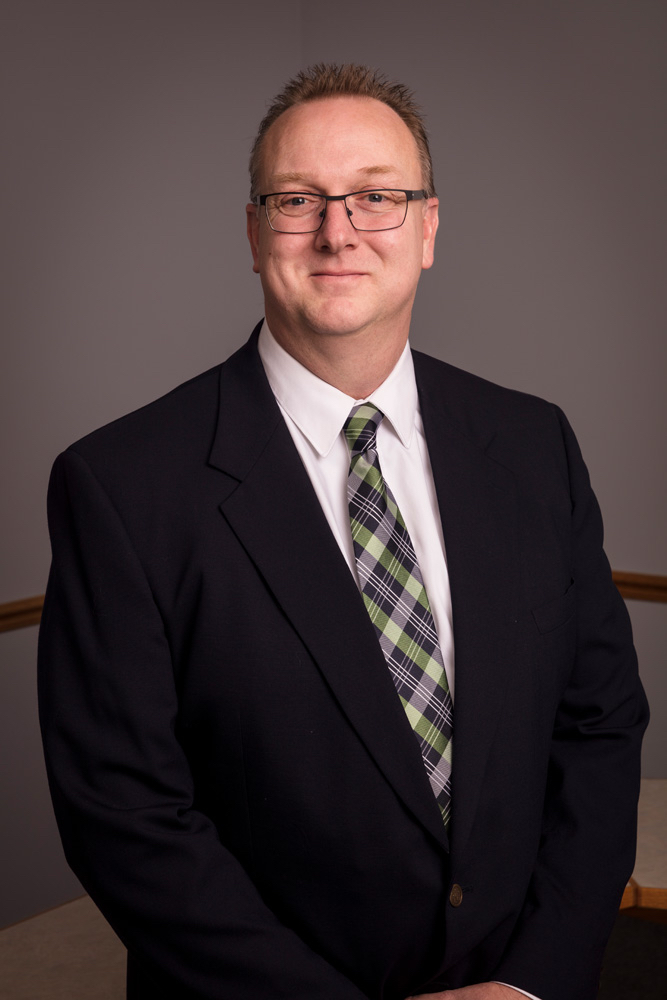
Robroy Industries has announced that Roger Schroder has been promoted to Operations Manager for the company’s enclosure manufacturing facility in Belding, Michigan. Mr. Schroder will be responsible for all engineering and operations functions of the organization. He provides extensive experience from nearly 14 years with Robroy Industries where he has served as Engineering Manager, Product Manager, and Business Development Manager. His professional history includes expertise in electrical, electronic, and automotive manufacturing. “Roger knows enclosures inside-and-out, top-to-bottom,” says Craig Mitchell, President of Robroy Industries Enclosures Division. “For many years we have relied on his strong engineering management and cross-functional team leadership. Among his many strengths, Roger is skilled in product development and quality assurance, as well as the intricacies of thermoplastic materials and compression molding of thermoset polymers. He will help us continue to lead the way in the production and availability of the highest quality non-metallic enclosures.”
MARTINS announces the launch of three new sub-brands
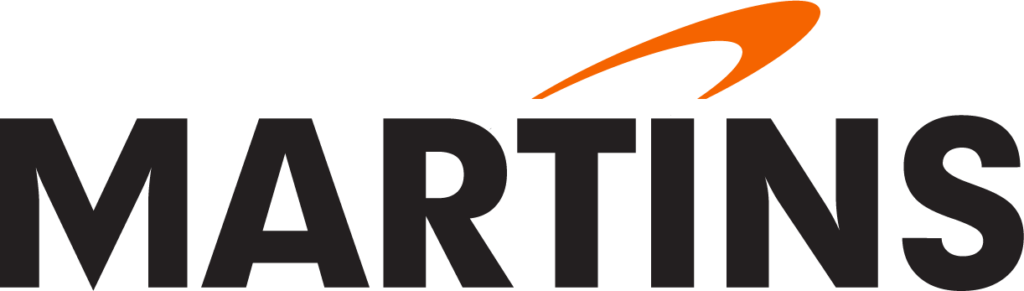
MARTINS has announced the launch of its three new sub-brands: tiretools, tirestow, and tiresupp. This expansion marks a significant milestone in the company’s ongoing commitment to providing top-notch solutions and services to its clientele. tiretools is dedicated to providing smart and innovative tire equipment solutions. Focused on quality, safety, and user-friendly design. tirestow represents MARTINS’ commitment to addressing the need for effective tire storage solutions. Designed to optimize space and streamline tire storage for businesses of all sizes, tirestow aims to offer a seamless and efficient experience for its users. Complementing these offerings, tiresupp presents itself as an expert in tire supplies. With a dedication to quality and reliability, tiresupp aims to serve as a trusted partner for businesses seeking premium solutions for their tire-related needs. Martin Depelteau, President of MARTINS, expressed his enthusiasm about the launch, stating, “These new sub-brands testify to our relentless pursuit of innovation and customer-focused solutions. We are determined to provide the tire industry with the tools and supplies necessary to thrive in an ever-evolving market.” As MARTINS continues to expand its global presence, the introduction of tiretools, tirestow, and tiresupp reflects the company’s unwavering commitment to providing businesses with cutting-edge solutions, quality products, and unparalleled customer service.
KEEN Utility introduces the Lansing Chelsea with pull-on convenience
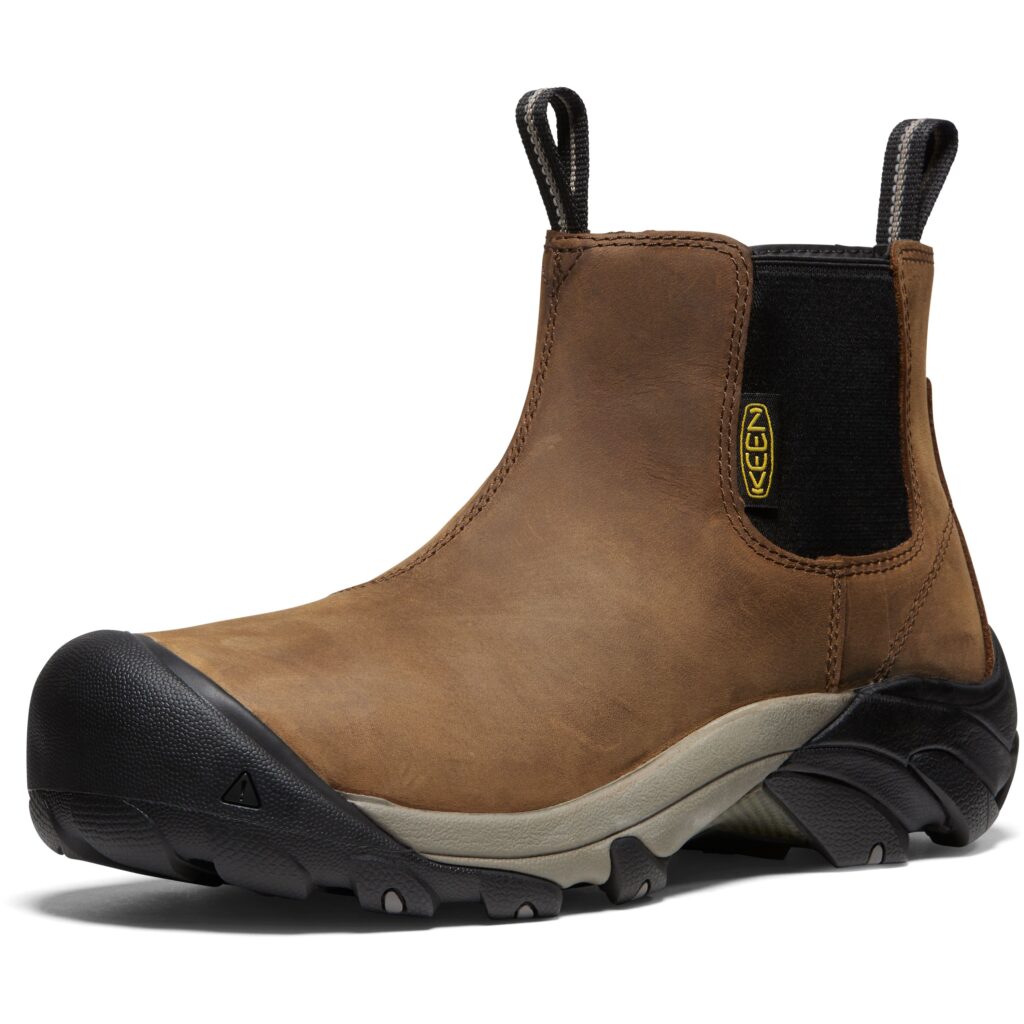
With the release of the Lansing Chelsea, KEEN Utility brings its go-to work hiker with pull-on convenience while still providing essential protection and support. Made with a durable, water-resistant leather upper that’s as good-looking as it is hard-working, the Lansing Chelsea steel-toe boot offers elastic panels in the ankle area that make it easy to pull on, while a reflective safety feature runs from heel to toe for added visibility on the job. Other product highlights include an EH-rated outsole to provide a secondary source of protection when accidental contact is made with live electrical circuits and an oil- and slip-resistant, non-marking, multidirectional lugged rubber outsole. New for Fall 2023, the Lansing Chelsea is available for men.
Episode 431: Breaking down fulfillment software, warehouse management systems & AI with Logiwa
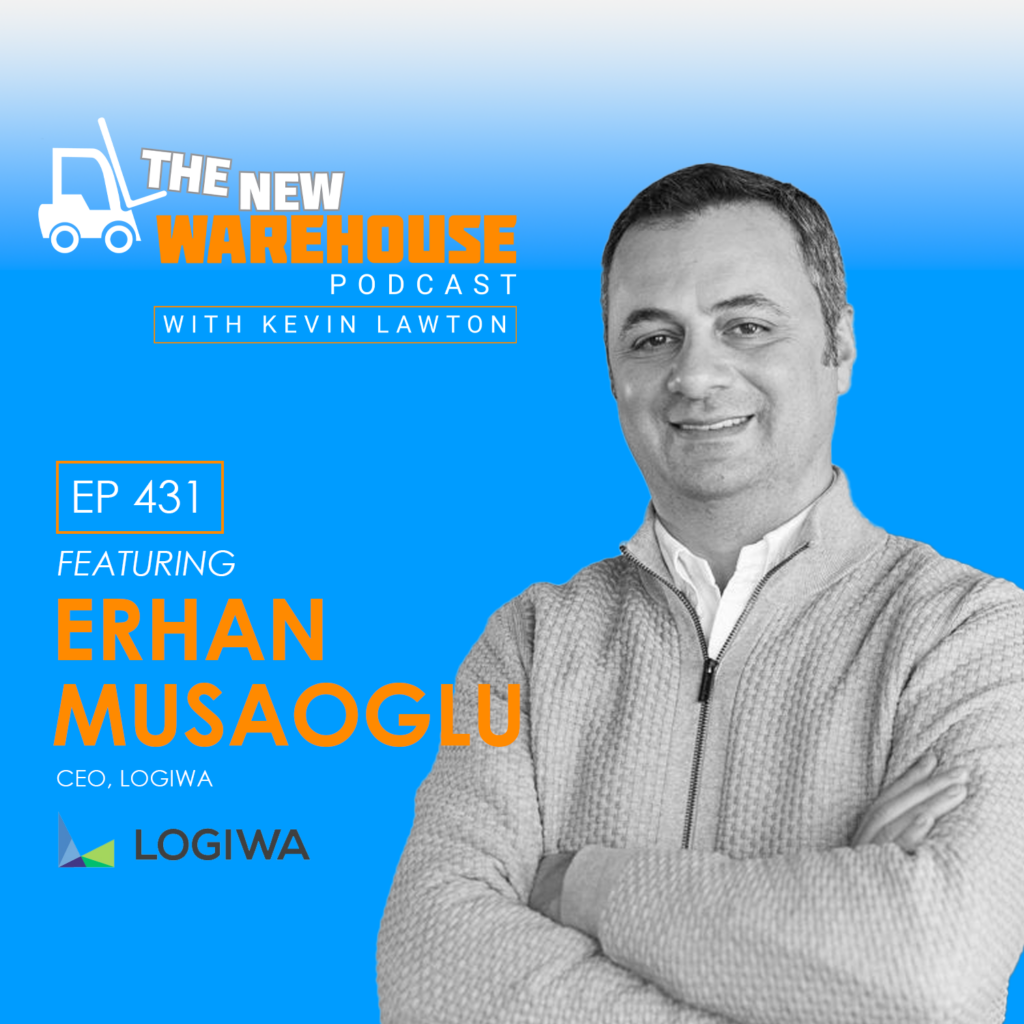
Logiwa positions itself not as a traditional WMS but as a modern fulfillment software specifically designed for high-volume, direct-to-consumer operations On today’s episode of The New Warehouse podcast, Kevin welcomes Erhan Musaoglu, the CEO and Founder of Logiwa. Erhan launched Logiwa two decades ago, initially implementing tier-one legacy WMS systems for large B2B companies. However, he noticed a gap in the market when it came to e-commerce companies. Traditional WMS solutions designed decades ago were inefficient for today’s direct-to-consumer models, which require processing thousands of small, individual orders. The inefficiencies of using old systems led him to create Logiwa, a solution that addresses the distinct needs of e-commerce and direct-to-consumer businesses. Be sure to tune into this episode to discover more about how Logiwa is revolutionizing the world of warehousing and what the future holds for AI in this sector. More than Just a WMS, Logiwa Provides Fulfillment Software Logiwa distinguishes itself from traditional WMS solutions by being highly adaptable to the requirements of modern e-commerce. As Erhan explains, shipping 10,000 pens in a B2B environment might involve a single forklift and two pallets, but in a direct-to-consumer scenario, it involves thousands of different orders, shipping labels, and a much larger workforce for picking, packing, and shipping. This real-world example illuminates the company’s focus on creating a product tailored to the labor-intensive nature of e-commerce fulfillment. Erhan stresses the importance of distinguishing between traditional WMS and fulfillment systems. The difference lies in their core objectives: while WMS focuses on storage, fulfillment systems are all about speed. “You don’t want to store anything in the fulfillment center. You just want to ship faster and faster,” Erhan states. Exploring the Diverse Landscape of Fulfillment Software and Warehouse Management Systems Erhan describes various types of technology powering WMS solutions, from on-premise legacy systems to cloud-based offerings. This diverse range of options reflects the changing needs and challenges businesses face today. One Size Fits All: According to Erhan, some providers are transitioning from a one-size-fits-all model to more targeted solutions. This change aligns with a broader industry trend toward specialized solutions that offer quicker time to value. User Experience: Erhan points out that modern WMS solutions are increasingly user-friendly and intuitive, reflecting a broader shift in how technology is designed and interacted with. Connectivity: easily integrating with other platforms is becoming more critical than ever, as Erhan notes. This development is part of a more significant trend of increasing interoperability in the industry. Emerging Focus on Fulfillment: Erhan suggests a growing focus on fulfillment over storage in some corners of the industry, illustrating the array of strategic choices that businesses now have. Erhan adds, “Eighty-two percent of Logiwa’s customers are shipping in less than 20 hours. And if your old legacy system is causing you to ship slower, you are losing your money.” The Transformative Impact of AI on Fulfillment Software and Warehouse Operations Erhan highlights the transformative potential of Artificial Intelligence (AI) in actively optimizing warehouse operations, particularly in outbound flow. AI uses algorithms for complex tasks that the human brain or even mathematical models find challenging—such as order batching, walking path optimization, and employee assignment. These algorithms capture every user activity and motion in the warehouse to establish labor standards, thereby efficiently matching employees to tasks. The real-world application of AI in Logiwa’s systems reflects the future-forward focus of the company, where predictive analytics and real-time adjustments can enhance labor productivity and operational efficiency. Furthermore, Erhan believes AI will play an increasingly central role in planning and coordinating warehouse operations. The future vision includes a “big AI machine” that runs continuously and can forecast demand, inventory management, and even immediate employee assignments based on their skill set and patterns. He points out that the advancements in AI technology could eventually lead to humanoid robots efficiently picking from bins and packing orders, something not yet fully realized. Key Takeaways Modern fulfillment software is moving towards high-volume, direct-to-consumer operations, differing significantly from traditional Warehouse Management Systems (WMS) that focus on storage. The landscape of WMS and fulfillment software is diverse and evolving, featuring everything from on-premise legacy systems to user-friendly, cloud-based platforms. Artificial Intelligence (AI) is poised to revolutionize warehouse operations, specifically optimizing outbound flow. Through sophisticated algorithms and predictive analytics, AI can optimize labor assignments, enhance operational efficiency, and even forecast demand. The New Warehouse Podcast EP 431: Breaking Down Fulfillment Software, Warehouse Management Systems & AI with Logiwa
Smart Vision Lights launches JWL150-DO Lightgistics Machine Vision Light with hidden strobe technology
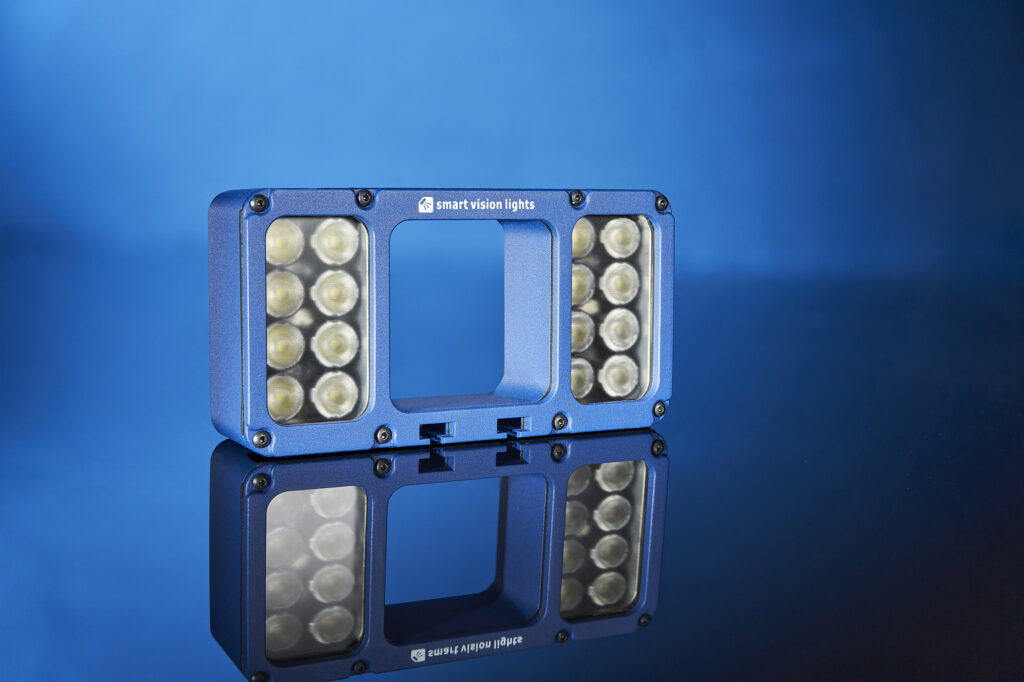
Smart Vision Lights (SVL) has introduced the JWL150-DO Lightgistics Series light, now with Hidden Strobe technology, which delivers the benefits of strobing without the distraction and disorientation associated with LED strobe lights. Hidden Strobe technology allows LEDs to internally self-trigger thousands of times per second, pulsing faster than the human eye can perceive and creating the illusion of continuous light. The technology maximizes machine vision systems while protecting employees from the disorientation caused by flashing lights. “In high-speed machine vision systems today, LEDs are pulsed to freeze images of fast-moving objects, but the strobing effect can create an uncomfortable and potentially unsafe working environment,” says Steve Kinney, director of training, compliance, and technical solutions at Smart Vision Lights. “Designed specifically to address these issues, the JWL-150-DO with Hidden Strobe technology helps high-speed machine vision systems capture the right images without causing unintended environmental hazards and without shielding.” Improve Track-and-Trace through lighting Designed specifically for performing challenging high-speed, accurate barcode reading and optical character recognition (OCR) with packages in highly reflective plastic wraps or shipping bags, Lightgistics lights feature Dual OverDriveTM technology — which combines SVL’s Deca OverDriveTM and standard OverDriveTM engines and allows end users to attach polarizers that retain exceptional light output while handling any speed. “Automation applications in logistics today require high speeds and high accuracy, and when difficult applications such as reading through polybags and plastic wraps slow down the process, throughput slows down,” says Kinney. “Lightgistics LED lights address these issues head on by offering greater than 10 times brighter light pulses compared to standard continuous mode. This capability improves overall logistics and track-and-trace. The JWL-150-DO delivers an intense, compact light source with an integrated camera mount that can be directly connected and controlled through a camera’s trigger output. The JWL150-DO features an onboard charging capacitor designed to ensure powerful bursts of energy with a low consistent electrical draw. The IP65-rated bright field operates using a working distance of 500 mm up to 2000 mm; 10-, 14-, and 30-degree lens options; and built-in Multi-Drive technology that provides both continuous operation and OverDriveTM mode.
Episode 430: The Evolution of WMS Implementation with Tryon Solutions

In the latest episode of The New Warehouse Podcast, special guest Adam Downing, President of Tryon Solutions, dives into the intricate world of Warehouse Management Systems (WMS). With 14 years of specialization in Blue Yonder WMS implementations, Tryon Solutions provides a comprehensive suite of services spanning consulting and operational improvements to upgrades and support. Based in Raleigh, North Carolina, and boasting a global presence, the company completed an impressive thirty-nine go-lives just last year. Adam offers invaluable insights into how WMS providers are evolving to keep pace with rapidly advancing technologies, including automation and robotics. Don’t miss the chance to gain these insights; tune in to the episode for the full discussion. Robotics, Labor Issues, and the Rise of SaaS in Warehouse Management Systems In an industry as dynamic as warehousing keeping up with technological advancements and labor market shifts is crucial. Adam sheds light on some of the most pressing issues and changes currently affecting the warehouse management landscape. “A lot of our products right now are centered around either robotics or automation,” Adam mentions, highlighting the increased focus on these technologies to drive efficiencies, with labor remaining a significant concern. One of the most noteworthy shifts is moving from on-premise solutions to Software as a Service (SaaS). “There’s this big push to move to SaaS,” Adam notes. This change, though sometimes met with resistance from large enterprise IT departments, is becoming increasingly accepted. It allows operational folks to take more ownership of the systems, bypassing the need to rely solely on internal IT teams. “SaaS WMS solutions are not a new thing, but certainly from the enterprise level, they are becoming more and more adopted,” Adam adds. WMS Implementation and Integration in an Age of Robotics and Automation Adam emphasizes the integration challenges of the proliferation of robotics: “You’re just automating things that are in your work queue, and rather than assign it to a person, you’re assigning it to a robot. Much of that still boils down to how you implement it and do the industrial engineering to build that into your operation.” This becomes particularly pertinent as warehouses strive for seamless coordination between human labor and automation technologies. As warehouses increasingly adopt robotics and other automation technologies, one critical hurdle is how these new tools integrate with existing WMS platforms. “The biggest challenge our customers see is how you integrate these various technology solutions with your existing WMS system?” Adam points out. He notes that while older WMS systems might still be able to handle new technologies via middleware, there’s a growing push toward SaaS solutions. The transition to SaaS offers better reliability and eases the integration of additional microservices that can optimize operations further. The Value of Test Automation in Streamlined Warehouse Operations Test automation is pivotal, especially as the warehouse ecosystem becomes more complex. “Test automation, for example, doesn’t necessarily make your go-live easier, but it makes your ongoing maintenance more robust and reliable. It’s always about mitigating risk,” Adam shares. He notes that while test automation is most effective in a large ecosystem where WMS is just one part of a broader IT infrastructure, its value is undeniable in maintaining long-term operational integrity. “We look at automating those tasks of the high priority things…the picking, the put-away, those sorts of tasks,” says Adam. By focusing on automation for these tasks, warehouses can better mitigate risk and reduce the need for manual interference, which can be especially critical during system upgrades or other changes. Key Takeaways on WMS Implementation Robotics and automation are increasingly essential in warehouse management, necessitating seamless integration with existing WMS platforms. The transition from on-premise to Software as a Service (SaaS) solutions accelerates, allowing operational teams to take greater ownership and improve system reliability. Test automation is pivotal for mitigating risks and streamlining operations, particularly in larger ecosystems where WMS interacts with a broader IT infrastructure. EP 430: The Evolution of WMS Implementation with Tryon Solutions
Women In Trucking Association announces finalists for 2023 Influential Woman in Trucking Award
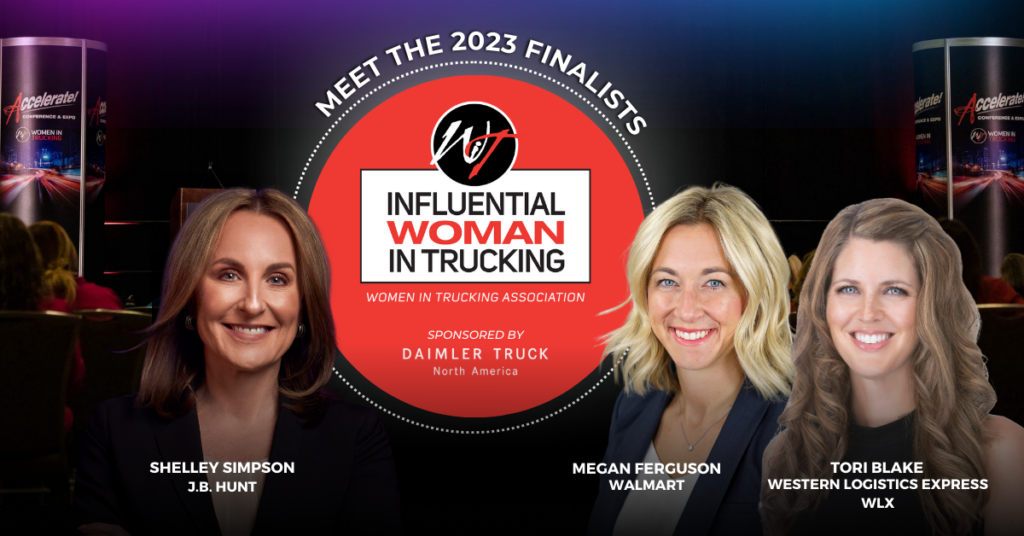
The Women In Trucking Association (WIT) just announced the three finalists for the 2023 Influential Woman in Trucking award sponsored by Daimler Truck North America (DTNA), the leading manufacturer of Class 6-8 commercial vehicles in North America. This award was developed in 2010 to recognize female leaders and to attract and advance women in the trucking industry. The award highlights the achievements of female role moles and trailblazers in the trucking industry. The 2023 Influential Woman in Trucking finalists are: Tori Blake, Chief Financial Officer and Co-owner, Western Logistics Express and WLX Megan Ferguson, Vice President and of End-to-End Delivery Acceleration, Walmart Shelley Simpson, President, J.B. Hunt Transport Services, Inc. Tori Blake, Chief Financial Officer and Co-Owner of WLX and Western Logistics Express “WLE”, has made it her mission to mentor women in all facets of her business. In her role, she is responsible for financial management, talent acquisition, employee development and strategic visioning. WLX|WLE have been recognized as one of Kansas City’s fastest growing companies each year Tori has been on the team, as well as one of Kansas City’s best places to work. She was also named Kansas City Business Journal’s 2023 CFO of the year. At the start of her career, Tori was an auditor at Ernst & Young, one of the four largest accounting firms in the world. Over her 16-year career as an executive leader, she has led startup companies and has a true passion for entrepreneurial endeavors. Tori has a heart for serving others. She was instrumental in supporting Children’s Mercy Hospital in Kansas City through “Sunshine Taggie” blankets for patients, handmade by WLX|WLE employees. She has also served as chairwoman of her church board, has been a children’s church teacher for over a decade, and is serving as the church mission trip leader. Tori is also a coach of two youth sports teams where she has the honor of coaching and guiding 25 young female athletes and leaders each year. Megan Ferguson, Vice President of End-to-End Delivery Acceleration at Walmart, holds over 15 years of experience at Walmart and Sam’s Club, with a deep background in transportation operations and strategy and merchandise operations. Megan joined Walmart in 2007 as a Private Fleet Strategy Intern and moved into the role of Project Manager of Walmart’s Private Fleet Strategy upon obtaining a degree in Supply Chain Management at Michigan State University. During her career at Walmart, she has filled transportation leadership roles in sourcing and procurement, inventory management and optimization as well as merchandise operations. In her current role, Megan brings Walmart’s delivery strategy to life, across first, middle, and last mile, and always prioritizing the customer’s needs. Megan is a passionate mentor and leader to her teams. She co-leads Walmart’s Women of Supply Chain Council as well as hosts educational sessions and mentorship circles while continuing to grow herself as an active member in the Walmart’s Women’s Officer Caucus. While her passions lie in advocating for women in the transportation and supply chain industries, her mentorship extends to all associates seeking guidance in managing relationships, peer collaborations, and various business topics. Megan prioritizes volunteering her time to train and participate in fireside chats and panel discussions to inspire other women to take on leadership roles. Shelley Simpson is President of J.B. Hunt Transport Services, Inc. Her 29-year career at J.B. Hunt reflects the company’s continued progression as an innovative leader in the transportation and logistics industry. Since joining J.B. Hunt as an hourly customer service representative, she has held multiple positions in business segments across the company, including leading Integrated Capacity Solutions, Truckload, Customer Experience, Highway Services and most recently serving as Chief Commercial Officer and Executive Vice President of People and Human Resources. While leading the strategic direction of marketing, sales, customer experience, and external product development, Shelley also led the development of the company’s freight matching technology platform J.B. Hunt 360°®. As the company evolved the platform and its technology-driven services, Shelley was also responsible for commercializing them on a global scale as the leader of International Services. In 2021, she was named one of the Top 100 Women in Supply Chain by Supply Chain Digital and has been named one of the top 100 HR Professionals by the National Diversity Council in 2022. She recently received the 2022 Woman of the Year in Innovation award by the Women’s Foundation of Arkansas and the Excellence in Free Enterprise Award from Economics Arkansas. There will be a panel discussion at the WIT Accelerate! Conference & Expo held in Dallas, TX, Nov. 5-8, 2023. The winner will be announced after the panel discussion on Tues, Nov. 7 at 10:15 a.m. CST.
Toyota Material Handling receives Manufacturing Excellence Award for community impact
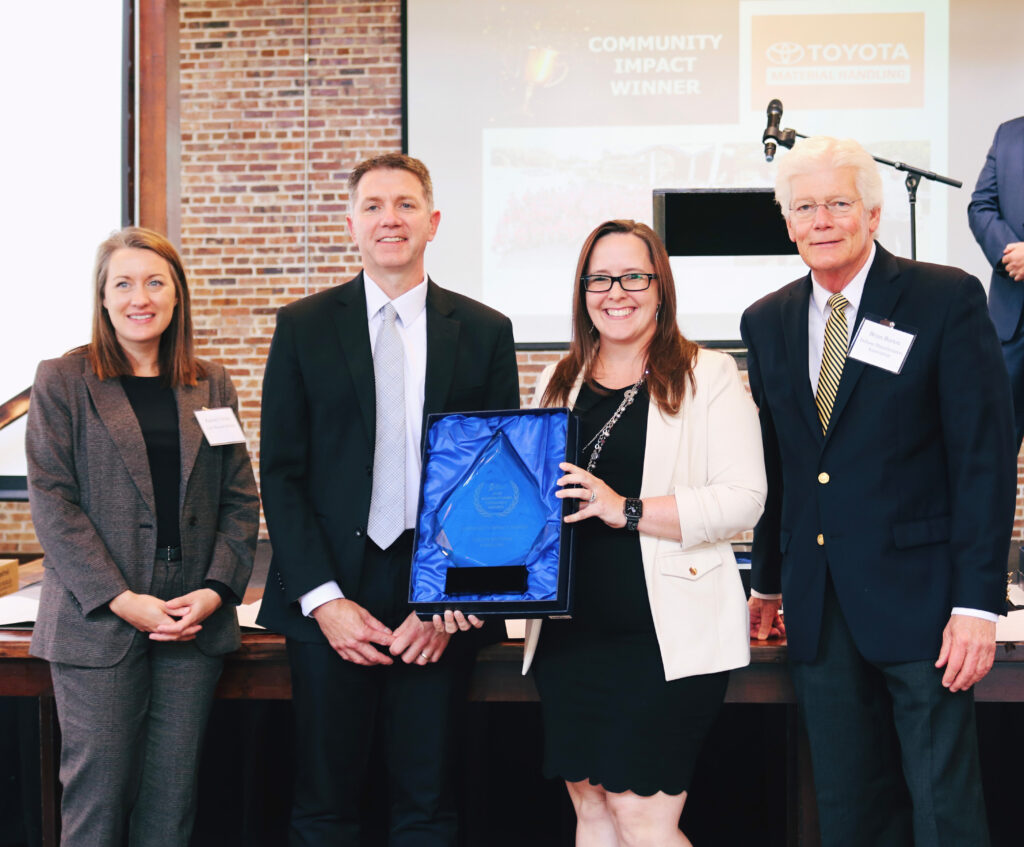
Toyota Material Handling (TMH), the North American leader in material handling innovation, received the 2023 Manufacturing Excellence Award for Community Impact during the Indiana Manufacturers Association’s (IMA) Hall of Fame Luncheon last week at Indianapolis’ Bitwell Event Center. The awards, given annually by the IMA, recognize manufacturers that make important contributions to the customers and communities they serve and set an example for other companies to follow. Toyota Material Handling was selected from a large group of applicants for showing exemplary leadership and a strong commitment to community service as reflected in its company policy, resources and employee participation. “At Toyota, we believe it is our responsibility to contribute to society in meaningful ways and make a real difference in the communities in which we live and work,” said Tony Miller, Toyota Material Handling Senior Vice President of Operations, Engineering & Strategic Planning. “We take that responsibility seriously, and it’s an honor to be recognized with this award by the IMA. I’d like to thank every one of our associates for their unwavering commitment to making our community a better place. This award is not about the contributions of a few; it’s only possible because of the efforts of everyone at Toyota. We will always seek opportunities to invest in the communities we serve and dedicate our time and resources to continuously improve the lives of those around us.” Corporate social responsibility is integral to Toyota’s culture. Toyota has cultivated numerous community-focused relationships, including corporate partnerships with the American Red Cross, United Way and Anchor House, a local nonprofit focusing on investing in neighbors through housing, employment resources and nutritional assistance. Throughout the year, Toyota sponsors and organizes volunteer activities on and off Toyota’s campus. In 2022, Toyota associates donated 12,000 hours of their time to support local organizations, contributing to a total economic impact of $750,000. “We instituted the Indiana Manufacturers Hall of Fame Awards in 2015 to help bring awareness and recognition to the many positive contributions of Hoosier manufacturers, and added the Manufacturing Excellence Awards in 2019 to focus and honor companies in specific areas of achievement,” said IMA President and CEO Brian Burton. “We congratulate Toyota Material Handling for their outstanding work and continued dedication to making Indiana manufacturing a positive and driving force for the state.”
Terex announces leadership succession plan
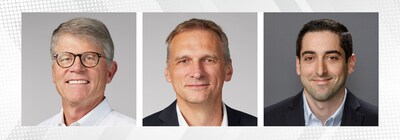
John L. Garrison, Jr. to retire as Chairman and CEO effective January 1, 2024 Simon Meester, current President Terex Aerial Work Platforms, named next CEO Joshua Gross named next President Genie Raises Full Year 2023 Outlook Terex Corporation has announced that John L. Garrison, Jr. is retiring as Chairman and Chief Executive Officer and a member of the Board of Directors, effective January 1, 2024. Garrison will be succeeded by Simon Meester, current President Terex Aerial Work Platforms, as the Company’s President and Chief Executive Officer. Meester will also join the Company’s Board. Garrison will work closely throughout the remainder of 2023 with Meester to ensure a seamless and orderly transition of responsibilities. Joshua Gross, current Genie Vice President of Global Strategy and Product Management, will be promoted to President Genie. Garrison will continue as a consultant for Terex after January 1, 2024 through June 30, 2024. David Sachs, currently lead independent director of the Terex Board will become Non-Executive Chairman of the Board effective January 1, 2024. Garrison said, “Leading Terex has been the highlight of my career. Without a doubt, our success and achievements have been driven by our dedicated, engaged team members who live our Terex Way Values and Zero Harm Safety culture each and every day. Terex is in as strong a position as it has ever been in and now is the right time to begin the transition to Terex’s next leader. I have had the privilege of working closely with Simon for a number of years and he has proven to be a global, strategic thinker with a natural ability to lead teams and drive results. I have great confidence that he is the right leader for Terex as the Company focuses on delivering long-term value for its stakeholders.” Sachs said, “On behalf of the entire Board, I want to thank John for his significant contributions, leadership and dedicated years of service to Terex. Since his appointment as CEO, he has been instrumental in transforming our Company into the Terex of today which comprises a very strong portfolio of market leading businesses. Under his leadership, Terex has experienced remarkable success and remains well positioned for continued growth. The naming of Simon as the next CEO is the culmination of a thorough and orderly succession planning process undertaken by the Terex Board, that included the evaluation of internal and external candidates, to ensure continuity of leadership. The Board is confident that Simon is the right choice to lead Terex in its next phase of growth and value creation for our shareholders.” “I am excited and humbled to be named the next CEO of Terex,” said Meester. “It is an honor and privilege to represent our dedicated and hardworking team members. We are in a great position for the future given our strong foundation, and I look forward to continuing to work closely with John to ensure a seamless transition. In the months ahead, I also will continue to work closely with Josh Gross to ensure a smooth transition at Genie. Josh has been a critical member of the Genie leadership team and is the right person to successfully drive Genie’s strategic initiatives going forward.” Gross said, “I look forward to working alongside Simon and our leadership team as we continue to provide our customers with industry leading products and services. This is an exciting time for our business and an incredible opportunity to build the future together with our customers.” Raises Full Year 2023 Outlook Terex expects its full year 2023 earnings per share results to be approximately $7.05. The Company will provide a detailed full year 2023 outlook when it releases its third quarter 2023 financial results on October 26, 2023. About Simon Meester Simon Meester has been President Aerial Work Platforms since May 2023. He was appointed President, Genie, on August 1, 2021. Previously, Mr. Meester had been serving as Chief Operating Officer of Genie since June 2020. He joined Terex in 2018 as Vice President, Global Sales and Marketing Administration for Genie. Prior to joining Terex, he was VP and General Manager of the Industrial Control Division at Eaton Corporation. Earlier, he spent 14 years in progressively senior roles at Caterpillar, Inc., before becoming President, Sandvik Mining and Construction in India. He has managed global teams and operations for more than 20 years, based in seven countries, including 11 years in the United States. He holds an MBA from the University of Surrey, England and a Bachelor of Science in automotive engineering, Apeldoom, Netherlands. About Josh Gross Josh has been Genie’s Vice President Global Strategy and Product Management since July 2022, and prior to that was Vice President Global Commercial Operations since August 2020. Josh joined Genie in 2019 and has led areas including strategy, product management, Genie Operating System, marketing, pricing and sales, inventory and operations planning (SIOP). He has worked closely with Simon in reimagining Genie’s brand positioning, resulting in the launch of Genie’s updated brand promise, “Quality by Design.” Before joining Genie, Josh spent almost 11 years with Eaton, where he served in a variety of roles in increasing levels of responsibility including Plant Operations Manager and Multi-Site Leader, Global Product Line Manager (P&L Leader), Product Manager, and Senior Sales Engineer. Josh holds BS degrees in Aerospace Engineering and Mechanical Engineering from West Virginia University, and an MBA from Marquette University.