ASSP welcomes new chief financial officer
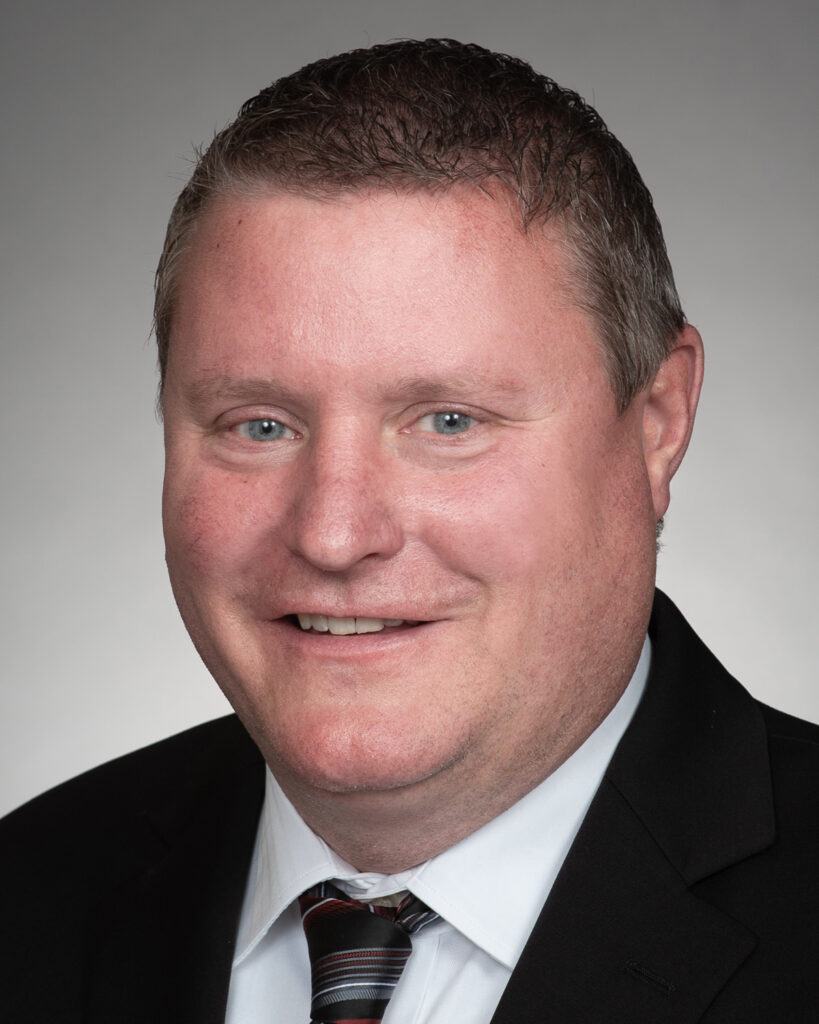
The American Society of Safety Professionals (ASSP) has welcomed a new chief financial officer. Steven M. Lothary, MBA, will lead the Society’s finance team as of Nov. 1. He will replace Bruce Sufranski, who is retiring at the end of October after more than 14 years of service. Lothary joins ASSP’s leadership team, working with the CEO and Board of Directors to align resources with the organization’s strategic direction. He will oversee all financial functions of ASSP and the ASSP Foundation. His responsibilities include accounts payable and receivable, cash management, annual budgets and audits, financial and tax reporting, risk management, insurance, and headquarters office building operations and maintenance. Lothary brings more than 20 years of experience in the not-for-profit and association industry. “We’re excited to bring Steve on board to continue the competent work and valuable contributions that Bruce has provided for many years,” said ASSP President Jim Thornton, CSP, CIH, FASSP, FAIHA. “Steve will play a significant role as we continue to grow post-pandemic and strengthen our position as a global leader in occupational safety and health.” Lothary will create and manage a long-term financial sustainability plan and work to increase reserves. He also will oversee human resources, which includes compensation and benefits, organizational planning and talent management. “This is a terrific opportunity that is meaningful to me because it helps protect worker safety and health,” Lothary said. “My background and career experiences align well with ASSP’s objective of increasing its financial health and stability. I look forward to helping the Society build on its history of success.” Lothary most recently served for six years as senior director of finance at the Emergency Nurses Association in Schaumburg, IL. The professional medical association provides education for more than 50,000 emergency department nurses. He led the redesign of their budget process and implemented an automated budget system. Prior to that, Lothary was director of finance and facilities for the American Society of Anesthesiologists – also in Schaumburg – from 2008 to 2012 and again from 2014 to 2017. The professional medical association provides education and lobbying support for more than 50,000 members. He implemented monthly dashboard reporting that focused on major revenue sources to better enable the organization’s leaders to pursue strategic initiatives.
Episode 428: Speeding up grocery fulfillment with Adam Gurga of Cimcorp
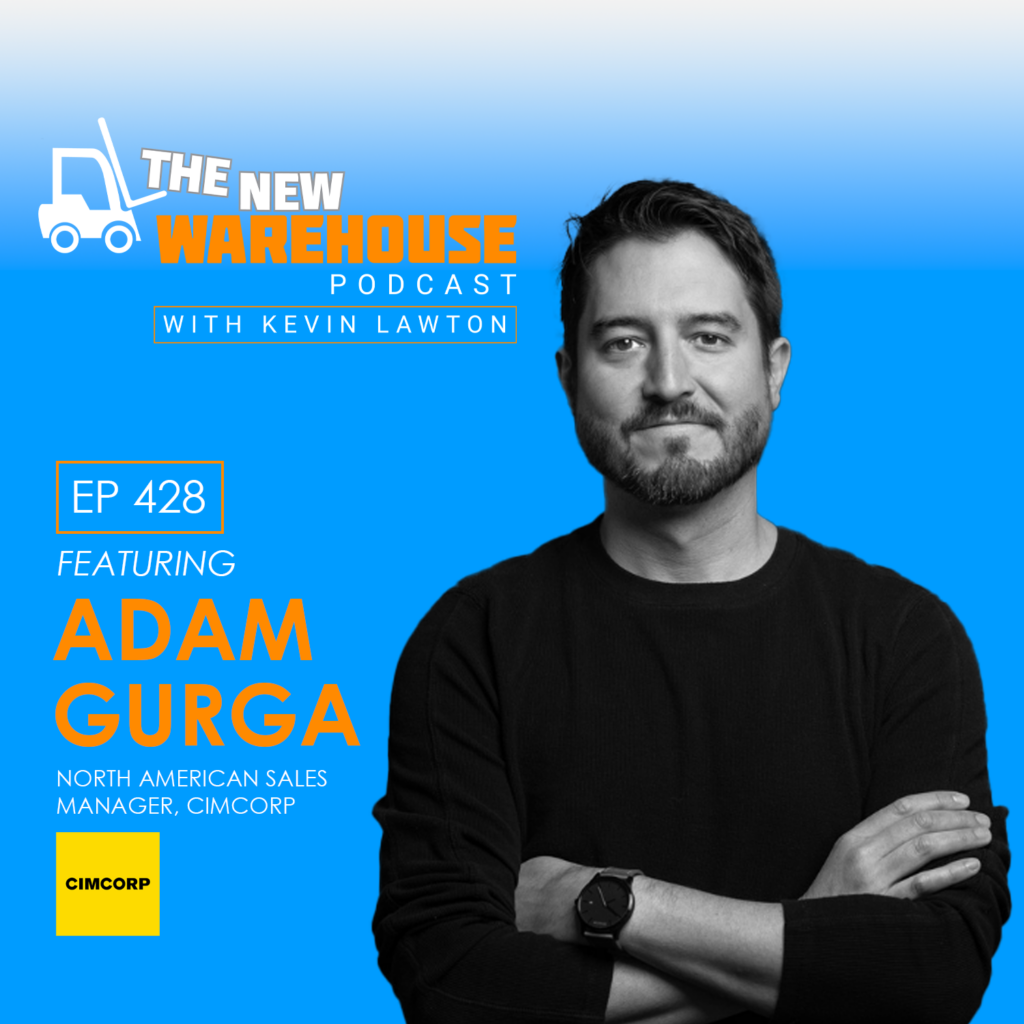
Welcome to The New Warehouse Podcast, where our guest is Adam Gurga, the National Manager for Grocery and Retail Partnerships at Cimcorp. Cimcorp specializes in providing automation solutions within the fulfillment space, including tire manufacturing, grocery, and retail industries. What sets Cimcorp apart is its unique approach to automation, specifically through its overhead gantry robots. Be sure to tune in to learn how automation is shaping grocery fulfillment. Challenges in Grocery Fulfillment and Distribution Centers Adam’s insights paint a vivid picture of grocery fulfillment and distribution centers’ complex challenges. These hurdles shape the industry’s present and future, from labor shortages to network capacity. As technology evolves, new opportunities emerge, but these come with their own set of challenges. Labor Pool Constraints – Adam identifies labor issues as one of the most significant challenges in the industry. The labor pool is dwindling due to factors like the aging population and younger generations seeking different types of work. He notes, “You’ve got fewer younger people who want to do that work. They tend to have higher levels of education than previous generations, leading them to seek out those white-collar jobs.” Network Capacity – Another challenge Adam highlights is the strain on network capacity. He says, “Feedback right now is a lot of the network capacity from a distribution standpoint from our customers is nearly maxed out, but there’s still desires, especially for publicly traded companies, for growth.” Automation Challenges – Adam also discusses the difficulties in retrofitting older buildings with modern automation solutions. While building a new warehouse might seem like a logical solution, “Retrofitting is typically less expensive. With new buildings, you’ve got rising costs of land acquisition to deal with, not to mention infrastructure, lead times, logistical remapping, and zoning challenges.” Temperature-Controlled Environments – Adam addresses the complex issue of maintaining automation solutions in temperature-controlled environments, especially for perishable goods. He notes, “There’s some limitations, not just with our automation, but in automation in general, once you start to push below that freezing level.” Navigating these challenges requires a multi-faceted approach encompassing technological innovation, strategic planning, and an in-depth understanding of market trends. Accelerating the Grocery Fulfillment Pick Process to Address Last-Mile Challenges The conversation shifts focus to the speed of delivery, a critical factor in customer satisfaction in grocery fulfillment. Adam emphasizes the importance of accelerating the picking process as much as possible to meet the demands of quick delivery. Cimcorp utilizes systems like ASRS (Automated Storage and Retrieval Systems) and gantry robots to swiftly bring products into storage, reprocess them, and build orders for delivery. He adds, “We have produce systems with six pick modules, and they’re pushing 120,000 cases in 24 hours.” Such speed is essential in a market where consumers have come to expect same-day delivery for groceries. The last mile—delivery from the distribution center to the customer’s doorstep—is another hurdle even advanced in-house automation can’t solve independently. Adam points out that grocery retailers often lose money on this crucial part of the supply chain, with losses ranging from seven to twenty-five dollars per order. This economic pressure further emphasizes the need for speed and efficiency in every preceding step, making automation even more indispensable. Overall, the challenges of grocery fulfillment are many, and the solutions are complex. However, companies like Cimcorp are taking steps to address these hurdles as technology evolves. Key Takeaways Labor Pool Challenges – Adam highlights a significant challenge concerning the labor pool, particularly in sectors requiring manual labor, such as warehouses. A declining or aging population and changing career aspirations of younger generations are making labor-intensive jobs less attractive. Need for Flexible Solutions – There is a trend of developing modular and scalable solutions to tackle immediate challenges like labor shortages and maxed-out network capacities rather than building entirely new distribution centers. Automation and Cold Storage – Automation in cold storage environments has specific challenges tied to temperature and condensation. The New Warehouse Podcast EP 428: Speeding Up Grocery Fulfillment with Adam Gurga of Cimcorp
Kito Crosby unveils new corporate brand

Kito Crosby, a global manufacturer of the lifting and securement industry, has announced the launch of its new, unified corporate brand. The strategic business combination of KITO Corporation and The Crosby Group, announced in January this year, has combined the expertise and heritage of two industry leaders, creating a stronger organization equipped to further drive innovation and elevate industry standards. The Kito Crosby brand unites the best of both companies, amplifying their shared commitment to safety, quality, and technology advancements. “We are thrilled to unveil our new brand, a symbol of our two legacy businesses combining as one team with a single mission and vision,” said Robert Desel, CEO of Kito Crosby. “This corporate identity serves as the focal point for all of us as we come together to best serve our valued channel partners and end users.” The brand embodies a dedication to reliability, innovation, safety, and quality, serving as a hallmark for the industry. Kito Crosby supports customers with a wide range of products and services used to make lifting, rigging, transporting, and securing operations safer and more efficient. The new brand fortifies the company’s position as a one-stop solution provider for all lifting needs. While unveiling the new brand, Kito Crosby has also launched a new mission, vision, and corporate values for the company’s 4,000 employees. The corporate brand serves as an umbrella for Kito Crosby’s leading product brands such as Kito, Crosby, Harrington, Gunnebo Industries, Peerless, and others. The product brands remain unchanged and Kito Crosby will continue to invest in these for a safer and more productive lifting and securement industry. “The unveiling of our new brand, mission, vision, and values marks a pivotal moment in our journey,” continued Desel. “With this strong corporate identity, our portfolio of powerful product brands can flourish – continuing to build on our long-standing legacy of pioneering technologies and solutions. We are proud to join together with our employees, channel partners and the entire industry to ‘raise your world.’”
Cheap industrial batteries: Where’s the catch?
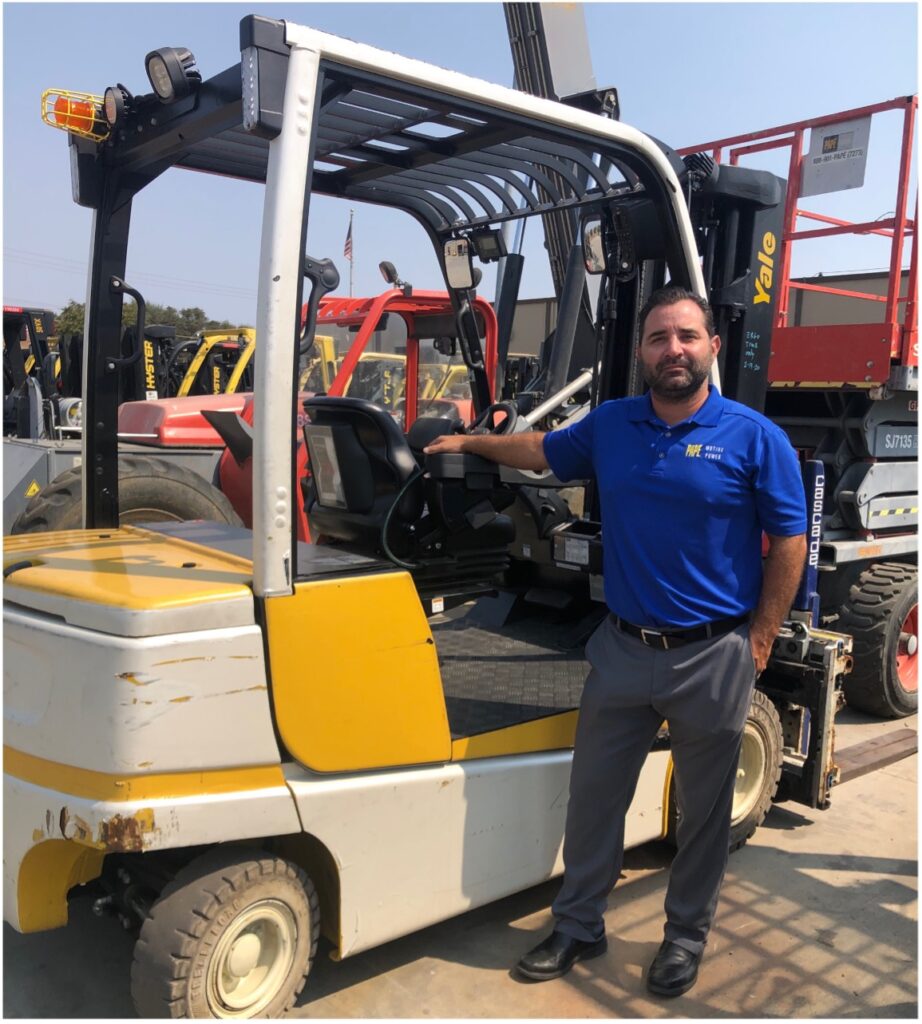
Motive power batteries for forklifts and other material handling equipment typically look very similar, with no differentiation of design or exterior features. Their technical specifications, like voltage and Ah capacity, are required to comply with the standard requirements of the host vehicles. However, there is often a significant price difference between different brands, which stems from the functionality of the battery management system (BMS), but also from other parts of the “total product”: delivery and installation; options for integration with the forklift and charger; and the availability of support, service, and parts. What helps cheaper batteries stay cheap? Cheap overseas labor can be a major factor in the US retail price when the production volume is large, but this is not the case for the relatively niche forklift lithium battery market. Transportation costs and longer lead times are leveling out this advantage. What is it, then? First and foremost, it is the limited functionality provided by a basic-level BMS. In our latest article focusing on the key factors extending the cycle life of a lithium battery, we argued that an advanced BMS plays a major role in preventing battery degradation by providing real-time diagnostics, equalizing the charge of individual cells, and safeguarding and optimizing the charge and discharge processes. A standard, off-the-shelf BMS with no adjustment for use in material handling and no advanced functions may give a price advantage, but also cause a lot of headaches to battery users. An inexpensive battery bought online from overseas, as you’ll see in the real-life example provided by PAPÉ’s Motive Power Regional Manager and top expert John Perazzo below, arrives at your door as if a forklift battery is as easy to install as a AAA battery in a TV remote. It is not. Not only does it require a second forklift or crane to remove the old battery, but a trained technician is required to properly connect and run tests on the battery, including connectivity, safety, and operation checks. On the other hand, installation and setup costs are typically included in the price of a US battery brand. Taking into account the potential service needs, the labor costs of initial installation will add up going forward. What is not included in the lower price, is the cost of downtime: in the best-case scenario, it equals the rental costs while you wait for spare parts to arrive. In the worst case, when the replacement is not quickly available, it equals the cost of business operation downtime. An online purchase of a lead-acid battery that went wrong Here is the story as it was told by John Perazzo, the motive power expert. PAPÉ had a customer in San Francisco for whom they quoted a replacement battery for a 5000-pound electric forklift. The customer called in to say PAPÉ’s offer was $2,000 higher than “the internet guy” and so PAPÉ lost the bid. A month later, the customer received a battery via a common carrier and was unable to install it because the old battery in his forklift was dead. Had he placed the order through PAPÉ, the new battery would have been delivered and installed, and the old battery would have been removed and properly disposed of, all included in the price. Instead, the customer needed to pay PAPÉ $450 for the installation. About 90 days later, this customer had a cell failure, contacted the manufacturer, and a replacement cell was shipped to him. This was another $500 service call for PAPÉ to come and have the cell installed. Meanwhile, the customer’s only forklift was down again while he waited for the cell. He ended up paying $900 for a rental. Not to mention the headache and downtime he experienced and the time spent overcoming these hurdles. “So we were $2000 more expensive up front, so he bought (a battery) from the internet,” says John Perazzo. “Once it was all said and done, the customer expressed the understanding of having local support for a product and that he wouldn’t make that mistake again.” Conclusion The technical specifications, size, weight, connectors, controls, and exterior design may be almost identical for industrial batteries from different brands. However, it is risky to treat industrial batteries as a commodity. The key differences are in the mechanical and electrical design, electronics and software, as well as in the level of local support and parts availability. To choose an industrial battery, operators need to understand the benefits and trade-offs of the total product to avoid painful losses with potential downtime and extra labor costs. About the Author: Maxim Khabur is a Director of Marketing at OneCharge, one of the US leading manufacturers of lithium industrial batteries, and a Chairman of the Advanced Energy Council, representing a group of companies – members of the MHI.org (Materials Handling Industry) Association.
Crossover at Kinnick Iowa Hawkeyes Women’s Basketball Bobblehead unveiled
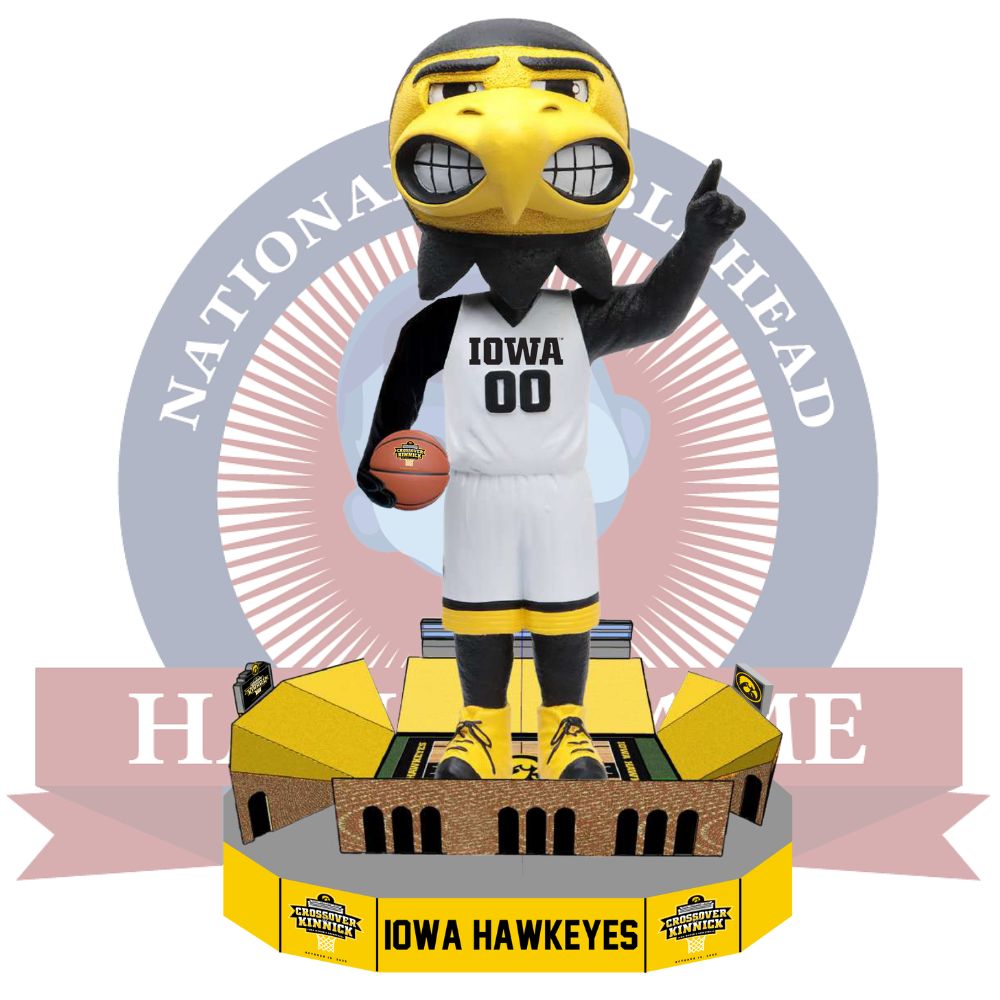
This morning, the National Bobblehead Hall of Fame and Museum unveiled an officially licensed, limited-edition bobblehead commemorating the “Crossover at Kinnick” women’s basketball game that is set to take place this Sunday, October 15th at Kinnick Stadium in Iowa City, Iowa. The bobblehead features University of Iowa mascot Herky the Hawk holding a “Crossover at Kinnick” basketball while standing on a basketball court inside a replica of Kinnick Stadium. The special edition bobblehead is being produced by the National Bobblehead Hall of Fame and Museum, an official licensee of the University of Iowa. Iowa will look to set the all-time women’s basketball attendance record when it hosts DePaul at Kinnick Stadium on Sunday. The women’s basketball attendance record of 29,619 was set in the 2002 National Championship game between Connecticut and Oklahoma in San Antonio’s Alamodome, and over 47,000 tickets have already been presold for Sunday’s game. Holding a basketball with the “Crossover at Kinnick” logo and standing on a basketball court inside a replica of Kinnick Stadium, the Herky the Hawk bobblehead is wearing his white Iowa Hawkeyes basketball jersey. The stadium base reads IOWA HAWKEYES across the front along with the “Crossover at Kinnick” logo on the sides. Each bobblehead will be individually numbered to only 2,023 and they are currently available exclusively through the National Bobblehead Hall of Fame and Museum’s Online Store. The bobbleheads, which are expected to ship in January, are $40 each plus a flat-rate shipping charge of $8 per order. With more than 47,000 tickets sold 10 days prior to the big event, the “Crossover at Kinnick” featuring the Iowa Hawkeyes, last year’s national runner-up, and DePaul is certain to shatter the all-time women’s basketball attendance record. “This is a once in a lifetime opportunity for our women’s basketball program and the sport,” 24th-year Iowa coach Lisa Bluder said in a statement. “I look forward to seeing all of our closest friends inside Kinnick Stadium for a historic day.” All proceeds from “Crossover at Kinnick” game will go to the University of Iowa Stead Family Children’s Hospital. Excitement is high for the 2023-24 women’s basketball season in Iowa City after the Hawkeyes went on a memorable and historic run last season. Three starters, including All-American point guard and reigning National Player of the Year, Caitlin Clark, return from a team that went 31-7 and finished as the national runner-up. In August, the program announced that season tickets were already sold out. The state of Iowa has a long history of supporting girls and women’s basketball. The Hawkeyes were second nationally in attendance last season with an average of 11,143 at Carver-Hawkeye Arena. In addition to appearing in the title game of the NCAA Tournament for the first time in program history where they lost to LSU, 102-85, the Hawkeyes finished as the runner-up in the Big Ten Conference behind Indiana with a 15-3 record and won the Big Ten Conference Tournament title for the second consecutive season. Earning a No. 2 seed in the NCAA Tournament, the Hawkeyes recorded victories over Southeastern Louisiana, Georgia, Colorado, and Louisville to advance to their first Final Four since 1993. In the national semifinals, Iowa knocked off defending champion, previously undefeated and top-seeded South Carolina, 77-73, before a sellout crowd of 19,288 at American Airlines Center in Dallas in one of the most anticipated matchups in women’s Final Four history. “We are excited to release this very special bobblehead in celebration of the Iowa women’s basketball team’s ‘Crossover at Kinnick’ event,” National Bobblehead Hall of Fame and Museum co-founder and CEO Phil Sklar said. “After the excitement created by the Hawkeyes last season and the anticipation for another memory-making season, this bobblehead will be a must-have for fans of the Iowa Hawkeyes and especially for those that will attend this historic event!”
Combilift’s CB15-5E wins the Italian Terminal and Logistics Award
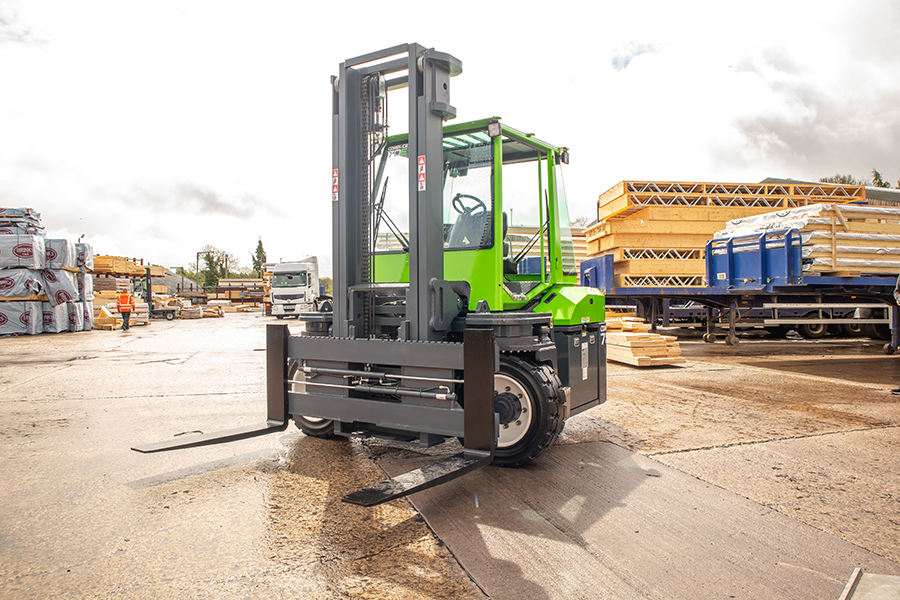
Combilift pick up award while attending GIS Expo in Italy Combilift, the largest global manufacturer of multidirectional trucks, articulated forklifts, and straddle carriers has announced that the Combi-CB15-5E has been honored with the coveted Italian Terminal and Logistics Award. This prestigious accolade recognizes the innovation in the operational field and its commitment to operator training and safety. The Italian Terminal and Logistics Award is a significant industry recognition, presented annually to highlight the skills of operators in port, intermodal, and logistics terminals both in Italy and abroad. The new Combi-CB15-5E is a further addition to Combilift’s ever-growing range of electric models which offers powerful performance, extensive battery life, and unrivaled ergonomics. This model, in the vibrant Combi-green livery, boasts the distinction of being the shortest 15,500lbs capacity counterbalance truck on the market whilst also benefitting from multidirectional ability, enabling the versatile space-saving handling of both long and bulky loads. Martin McVicar – CEO and Co-Founder of Combilift accepted the award alongside their EA Group partners and said: “We are honored to receive the Italian Terminal and Logistics Award for the CB155E. This recognition validates our unwavering commitment to innovation, safety, and training in the material handling industry. The CB15-5E is a perfect example of our dedication to providing our customers with efficient, eco-friendly, and safe solutions.”
Global Mobile Robotics Market Survey indicates widespread acceptance and significant growth
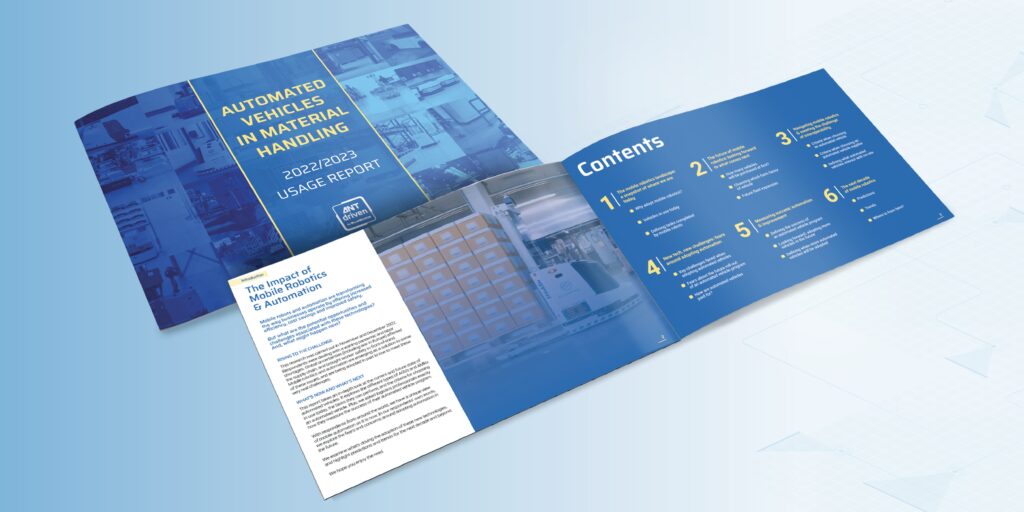
BlueBotics, the global reference in natural navigation for automated guided vehicles (AGVs) and autonomous mobile robots (AMRs), has released results of a new survey indicating significant growth in automated guided vehicle (AGVs) on its educational website, ANTdriven.com. Conducted in collaboration with Logistics Business magazine, the report “AUTOMATED VEHICLES IN MATERIAL HANDLING 2022/2023 USAGE REPORT indicates a bright outlook for the future of AGVs. Between November 28th and December 14th, 2022, the independent research firm Logistics Business interviewed 180 respondents from 29 different countries, 87 percent of whom were involved in purchasing automated vehicles. Virtually all respondents used some automated vehicle to improve their operations, and most planned to expand use soon. The results also indicated increasing acceptance and trust in automated vehicle technologies, high adoption of natural navigation methods, and significant interest in interoperability. Key findings: Widespread use of automated vehicles. More than 70 percent of the respondents have adopted or plan to adopt AMRs or AGVs and 21 percent were using self-driving forklifts. The average fleet size was 7.7, consisting mostly of AMRs or AGVs; only 17 percent used more than one type of vehicle. Diverse uses. Respondents used AGVs to compensate for staff shortages but generally not to reduce headcount. Applications included moving payloads to or from conveyors, palletizers, and wrappers; packaging or other end-of-line applications; pallet toting and retrieval; and picking. About a third cited on-site safety as a reason for adopting automated vehicles. Natural navigation is the most popular guidance method. About 3 out of 4 respondents were using vehicles guided by natural navigation methods, with others using laser triangulation, inductive wire, magnetic tape, and QR code or tag-based systems. Market growth. 91 percent of respondents plan to extend their AGV or AMR fleets, with 81 percent planning to do so within the next two years. Most will purchase between 3 and 10 vehicles. Interoperability trending. The need for new purchases to interoperate with each other and other plant technology showed as important as brand reputation and payload capacity, as respondents seek to avoid single vendor reliance. The need to measure ROI remains. But how they will measure that return remains of concern. The two most cited approaches include comparing cost savings to manual or automated vehicle technologies and productivity increases, with break-even time, accident reduction, and staff acceptance. “This survey confirms our belief that the adoption of automated vehicles will continue strongly for many years, driven by the challenge of hiring and retaining material handling workers, the continued need for increased efficiency and cost savings in challenging global conditions. We are especially gratified to see such strong current use of natural navigation as users see the value of automating material handling operations,” said BlueBotics CEO, Dr. Nicola Tomatis. For more details on survey results, read the complete survey report here.
AutoScheduler now available on SAP® Store
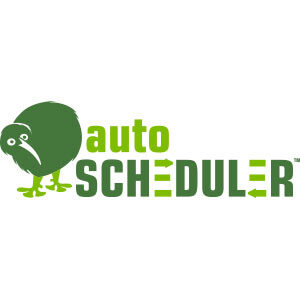
AutoScheduler.AI, an innovative Warehouse Management System (WMS) accelerator, announces that its warehouse resource planning and optimization platform, AutoScheduler, is now available on SAP® Store, the online marketplace for SAP and partner offerings. AutoScheduler takes data from SAP ERP solutions and uses capacity-constrained schedules to create plans and schedules that optimize the warehouse. “Adding AutoScheduler to the SAP Store will be an invaluable resource for companies needing to speed fulfillment operations, optimize warehouse resources, and better manage inventory. Many of our customers and prospects use SAP ERP solutions and are searching for ways to improve supply chain operations. AutoScheduler will help them orchestrate warehouse operations to drive value and efficiencies through the supply chain.” said Keith Moore, Chief Executive Officer, AutoScheduler AutoScheduler.AI enables organizations to: Combines disparate data from multiple systems, converges supply chain activities, and prescriptively creates fulfillment plans that orchestrate campus operations for optimized efficiency. Properly orchestrated facilities work harmoniously to get inventory shipped on time and in full. Prescribe the optimal workflow for operations using constraint-based mathematics and digital twins to minimize touches and ensure on-time, in-full fulfillment. Crossdock more frequently to keep inventory and activities steady so everything is on time and available for fulfillment. Minimize the number of transfer shipments by automatically shifting dock locations to reduce the number of moves among warehouses, which helps to speed fulfillment. SAP Store, found at store.sap.com, delivers a simplified and connected digital customer experience for finding, trying, buying, and renewing more than 2,300 solutions from SAP and its partners. There, customers can find the SAP solutions and SAP-validated solutions they need to grow their business. For each purchase made through SAP Store, SAP will plant a tree. AutoScheduler.AI is a partner in the SAP PartnerEdge® program. The SAP PartnerEdge program provides the enablement tools, benefits, and support to facilitate building high-quality, disruptive applications focused on specific business needs – quickly and cost-effectively.
Four Hargrove Controls & Automation Trailblazing Engineers named among CFE Media and Technology’s Engineering Leaders Under 40

Hargrove Controls & Automation, an industrial automation system integrator and a subsidiary of global EPC firm Hargrove Engineers & Constructors, announced that four of their engineers have been listed along with 30 other engineering professionals as rising stars of innovation in the CFE Media and Technology class of 2023 Engineering Leaders Under 40. This achievement recognizes individuals in automation, industrial manufacturing, and system integration who have made substantial contributions to the control engineering and plant engineering professions. “We are so proud of each teammate representing Hargrove Controls & Automation in the class of 2023 Engineering Leaders Under 40,” said Karen Griffin, Vice President of Hargrove Controls & Automation. “These outstanding individuals are following a legacy of excellence that previous Hargrove Teammates have achieved while forging their own that will be tough to match.” The four engineers representing Hargrove Controls & Automation include Matthew Bailey and Megan McIntosh from Mobile, Alabama and Chase Beard and Elliot Miller from Atlanta, Georgia. “Matthew’s, Chase’s, Megan’s, and Elliot’s commitment to Hargrove’s core values and their dedication to excellence and growth is the reason they are top performers within our company,” said Uwe Kurfurst, Hargrove Controls & Automation Industry Engineering Leader. “It is an impressive feat for Hargrove Controls & Automation to have continued representation in the program each year and demonstrates our commitment to engineering excellence.” Last year, the Engineering Leaders Under 40 class of 2022 featured five Hargrove Controls & Automation engineers – from technical consultants to controls and automation engineers – including the Control System Integrators Association (CSIA) 2023 Rising Star Award recipient Sean Phillips. Learn more about the Engineering Leaders Under 40 program.
Plastic alternative now available for flow wrapping
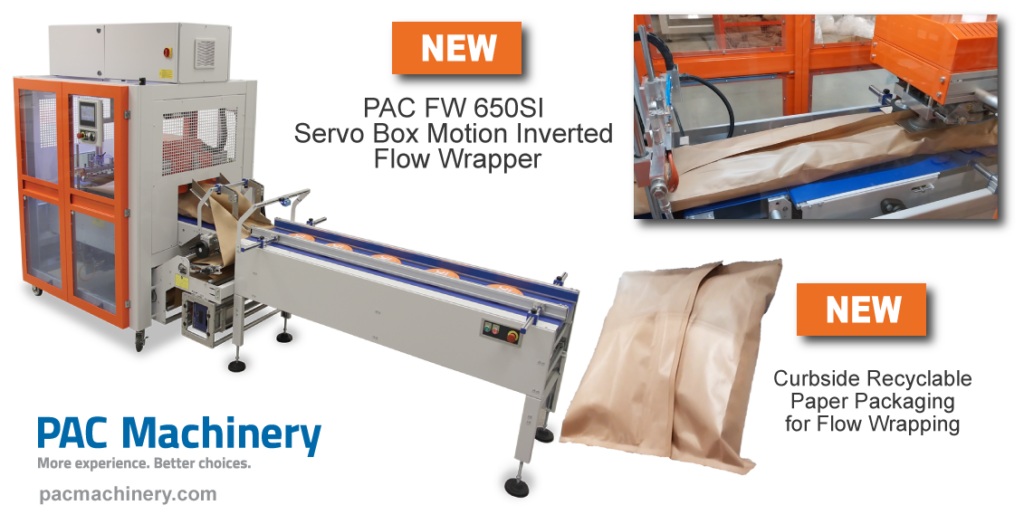
PAC Machinery (PAC) introduces the PAC FW 650SI Servo Box Motion Inverted Flow Wrapper that runs new curbside recyclable paper. This innovative new technology gives industries that flow wrap with an alternative to plastic packaging on horizontal flow wrappers. The FW650SI runs with a new eco-friendly, curbside recyclable paper mailer that for the first time, eliminates plastic packaging for industries that flow wrap including food, electronics, bakery, candy, industrially manufactured parts, and even medical devices. “We are thrilled to continue to provide new, innovative packaging equipment and materials to the industry that helps businesses grow and meet their customer’s demands that also prepares them for a plastic-free packaging future, which is the way this industry is moving,” said Greg Berguig, Vice President, PAC Machinery. “We were thrilled with the attention this machine received when it debuted at the historic, record-breaking Pack Expo show in September that directly showcased this new sustainable packaging option to our target audience,” Berguig said. The FW 650SI Servo Box Motion Inverted Flow Wrapper makes bags to product length at high speed using PAC’s NEW Curbside, Recyclable Paper. The FW 650SI has a 13.75” wide end seal jaw to accommodate products up to 12” wide or 8” high. It has the ability to print directly on the package or on a label that is applied to the package and is ideal for apparel and other soft, delicate products packaged with a continuous motion. It comes standard with a 6.5 ft. infeed conveyor belt with adjustable guides for multiple loading stations which provides flexibility when packing products of various length. For those not ready to make the move to paper, the FW 650SI is flexible enough that it can also run plastic-based films. The packaging machine has a 7” HMI touchscreen interface that displays key packing statistics, including production rate and efficiency for a quick changeover with 50 recipe memory. Safety features include enclosed electrical interlocked guarding that ensures operator safety, a CE-compliant design for improved safety and troubleshooting and accessible emergency stop button.
MHI sets date for ProMat 2025 and expands to three halls
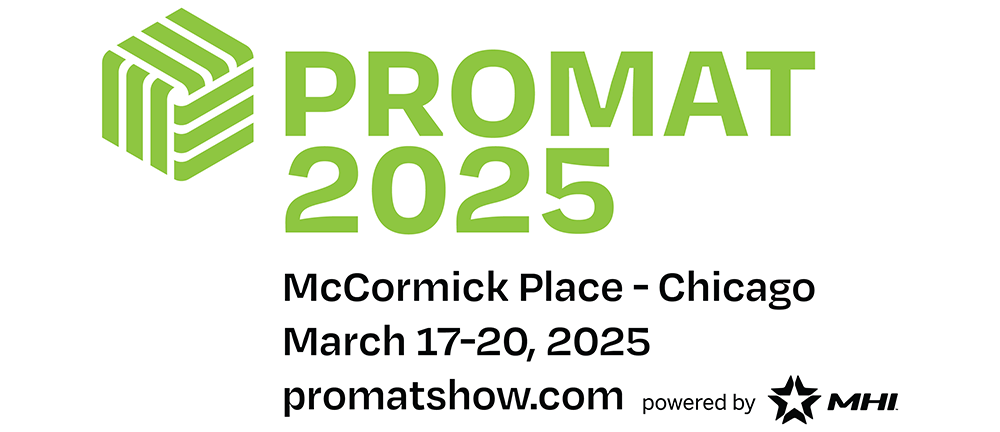
MHI recently announced the dates for ProMat 2025. ProMat 2025 will be held March 17-20, 2025 at Chicago’s McCormick Place. ProMat is the largest international manufacturing and supply chain show and conference held in the United States. The 2025 event will be the biggest ProMat ever and will include an expansion into McCormick Place’s Lakeside Hall. ProMat brings together solution providers who demonstrate their equipment, systems and services to over 50,000 manufacturing and supply chain professionals from around the globe, seeking productivity solutions for their operations. Over 1,100 exhibitors will showcase their solutions on ProMat’s three show floors totaling over 700,000 square feet of manufacturing and supply chain solutions. ProMat exhibits will represent all segments of the material handling, transportation, and logistics industry, from traditional, manual equipment to computerized, automated systems. To make it easier for attendees to find the solutions they need, ProMat’s three hall’s will be solution-focused: South Hall Manufacturing, Planning & Sourcing Fulfillment, Workforce & Labor Data Capture, Analytics & Information Management North Hall Automation and Robotics Emerging Supply Chain Technology Lakeside Hall Sustainability & Risk Management Transportation, Distribution & Warehousing Last Mile ProMat 2025 will also feature a comprehensive educational conference including keynotes and show floor educational seminars led by industry experts and leading authorities. ProMat 2025 will again include its highly regarded and prestigious International Buyer Program. The Program provides matchmaking for interested buyers and sellers through an International Business Center located near the show hall. Exhibit Space Draw Lease Deadline is November 1, 2023. The ProMat 2025 Exhibit Space Draw will be held November 14-16, 2023. This will be the first opportunity for organizations to secure exhibit space at this event. The deadline for leases for the Space Draw is 5pm ET on November 1, 2023.
Movu Robotics launches new brand to strengthen robotics unit
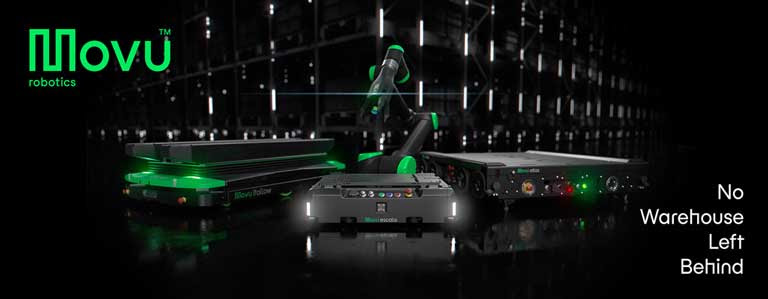
Movu Robotics makes warehouse automation easier. No warehouse left behind! stow Group, a globally recognized provider in the design, manufacturing, and implementation of advanced storage solutions and automated warehouse systems, has launched the new ‘Movu Robotics‘ brand, developed to strengthen its ‘Robotics’ business unit and to meet the strongly increasing demand for Automation and Robotics solutions. Movu Robotics stands out by bringing easier Logistics automation solutions to the world’s warehouses and ensuring that, when it comes to opportunities for automation, no warehouse is left behind. Movu tackles automation with easier, modular, scalable, and efficient solutions that customers need and helps them upgrade their warehouses. In this way, Movu brings automation and robotics opportunities to companies that would otherwise find them hard to attain. The higher simplicity of Movu Robotics’ range of innovative sub-systems reduces risk for customers and speeds roll-out to help them meet the challenges of labor shortages, cost increases, storage density, growing volumes, and improving accuracy. Movu Robotics provides a full range of warehouse solutions for every requirement: The Movu atlas, a self-powered 2D pallet shuttle. The Movu escala 3D robotic bin storage and fulfilment system. The Movu eligo piece picking arm robot. The Movu ifollow Autonomous Mobile Robots (AMRs). The portfolio’s technologies can be integrated into a single autonomous sub-system as a solution, with components including racking, shuttles or AMRs, software, wi-fi and commissioning. This enables easy installation, adaptability to new business needs through simple integration of new applications and a minimal Total Cost of Ownership (TCO) approach.
Episode 427: Digital Twins in warehousing with Meta Logic
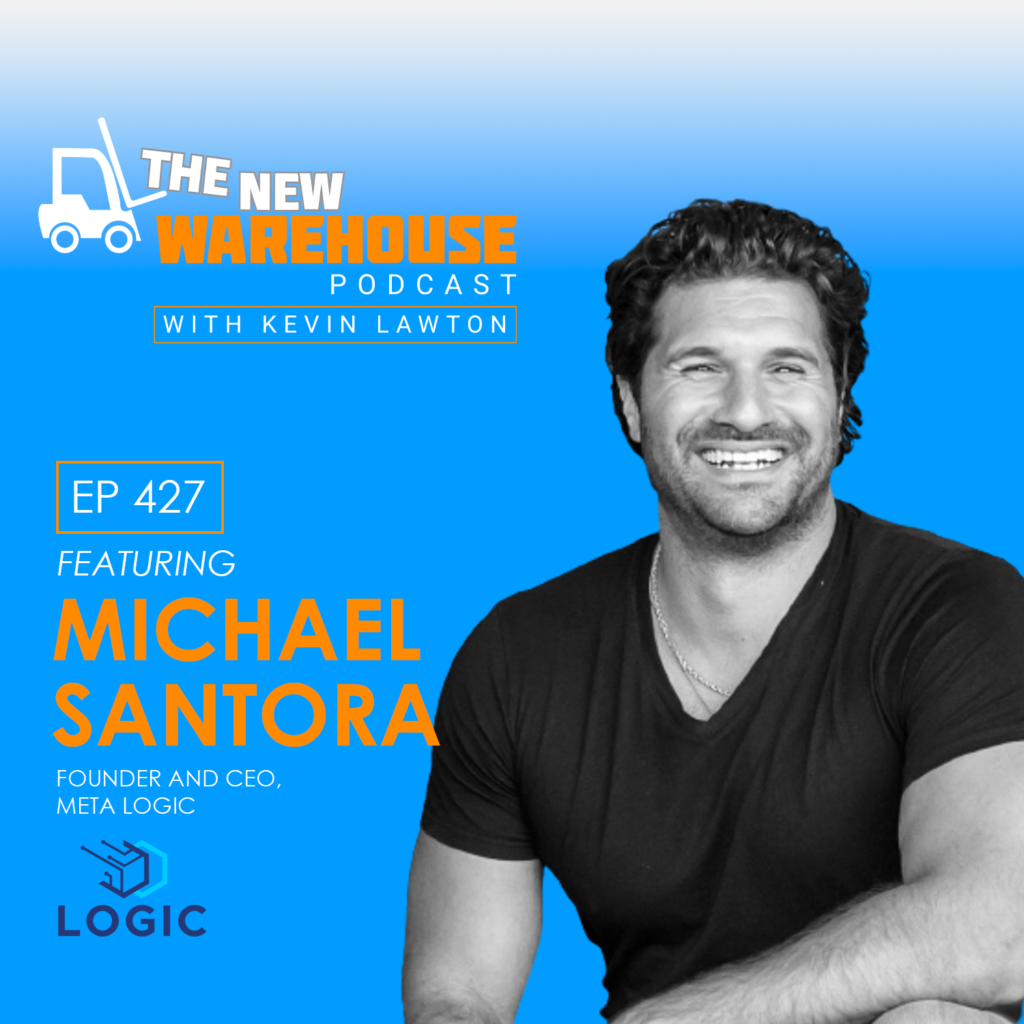
Welcome to a brand-new episode of The New Warehouse Podcast as we welcome Michael Santora, CEO of Meta Logic. Meta Logic is revolutionizing the warehouse landscape by creating a metaverse focused on digital twin technology and then translating that to their robotic solution, like their Logic Palette. We met at an ABCO event recently, so be sure to tune in as we dive into Meta Logic’s fresh approach to automation in warehousing. Understanding the Power of Digital Twins in Warehousing with Meta Logic According to Michael, a digital twin is “a virtual representation of a space… an exact, highly accurate 3D environment of a space and the equipment within that space.” The digital twin is a virtual replica of the physical world, capturing critical data that can influence operational decisions. Meta Logic’s digital twin technology goes beyond mere representation; it integrates physical properties like the weight a robot is carrying, the type of floor it’s driving on, or the temperature and humidity levels in the space. This allows for a simulation-controlled environment that is highly predictive. Michael elaborates: “What we’re doing with our system is we are controlling through simulation…we are integrating into that digital twin [the physical properties] to predict how something is going to behave.” The use of digital twins in warehousing generally revolves around optimizing workflows, facilitating real-time monitoring, and minimizing errors. Where Meta Logic disrupts the norm is in how it leverages its digital twin technology to control robotic operations. “We’re using this digital twin to get the best of both worlds to create a robust, inexpensive mobile robot that can move without the limitations of fixed infrastructure within the facility,” says Michael. By fusing the capabilities of traditional AGVs (Automated Guided Vehicles) and cutting-edge AMRs (Autonomous Mobile Robots), Meta Logic’s digital twin technology facilitates a new breed of robotic solutions. These are neither restricted by fixed infrastructure like AGVs nor limited by the high costs associated with the sensory and perception systems of AMRs. The result is a more agile, cost-effective, and highly adaptable robotic system that promises to redefine automation in warehousing. Revolutionizing the Supply Chain Through Digital Twins and Mobile Robots Michael explains that the concept involves creating a digital twin that supplements the hardware typically found in robots. This strategy dramatically reduces the costs and increases the flexibility of deploying a fleet of robots. The result is an innovative approach to supply chain automation, making it accessible not just to giants like Amazon and Walmart but also to companies that don’t have enormous capital expenditure budgets. Meta Logic’s digital twins allow these robots to operate with far less onboard infrastructure, thus reducing setup and operational costs. The robots look and function much like Automated Guided Vehicles (AGVs), but without the hefty price tag of building an entire infrastructure for them to run on. These mobile robots also possess the unique ability to go on and off vehicles, paving the way for new automation sectors within the supply chain. The approach alleviates common bottlenecks like truck waiting times at loading docks, thereby increasing the efficiency of the entire supply chain process. Multi-Warehouse Operations and Workflow When dealing with multiple warehouses not under a single controlling entity, Meta Logic still offers a seamless workflow. The system accommodates manual and automatic control, employing technology like Bluetooth “follow me” modes and digital joysticks for remote control. These features are helpful when products move between partner facilities not part of the Meta Logic network. Built-in weight sensors on the pallets help verify loads, enhancing the reliability of the shipping process. The system’s mission planner coordinates the robots’ activities upon their arrival at a warehouse under Meta Logic control. This advanced system considers factors like box size, weight, and stacking order to optimize the operation. In this way, Meta Logic serves as a highly adaptive layer that integrates smoothly with existing Warehouse Management Systems (WMS) or Enterprise Resource Planning (ERP) systems. The end goal is simple: to convert what would have been human tasks into automated, robotic ones, thereby streamlining operations and reducing costs. The End of Traditional Pallet Racking: Embracing Intelligent Space Utilization The traditional warehouse storage notion has long relied on pallet racking systems to organize and manage goods. However, innovative advances in warehouse technology have begun to challenge this approach. “I don’t think you’ll need the racks anymore,” says Michael. Integrating AI and automated systems has increased density that outperforms conventional methods. For example, intelligent systems allow workflows to manage up to “six levels of warehouses on a single floor,” greatly maximizing space and throughput. What sets this new system apart is its focus on urban logistics, bringing warehouses closer to dense population centers instead of being located “a hundred miles away because that’s where we found space for it.” This shift doesn’t just benefit storage density and can revolutionize transportation logistics, solving issues like the last mile and enabling greener transportation methods for short trips. This intelligent system can map and adapt to any space, making it perfect for non-traditional warehouses with challenging conditions. “Our AI figures out workflows that you wouldn’t be able to see yourself by looking at,” highlighting the way forward for what could very well be the future of logistics and warehousing. Key Takeaways: Meta Logic’s digital twin technology goes beyond merely replicating a warehouse space, integrating physical factors like weight and temperature to predict behavior. By fusing traditional AGVs and cutting-edge AMRs, Meta Logic’s system delivers a new, cost-effective breed of mobile robots not restricted by fixed infrastructure. The company’s approach maximizes warehouse space and brings operations closer to urban centers, revolutionizing storage and transport logistics. The New Warehouse Podcast EP 427: Digital Twins in Warehousing with Meta Logic
Over-The-Dock Racking: Special considerations for busy loading zones
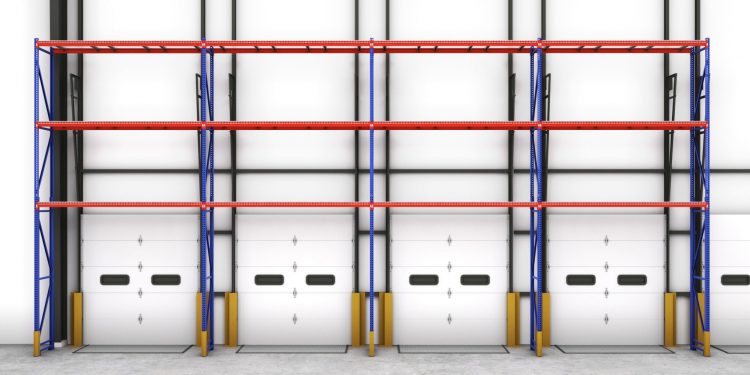
When it comes to optimizing space in a warehouse, distribution center, or production facility, safety should always be the top priority. One often overlooked area that can provide a cost-effective solution for the need for additional storage is above the dock doors. Although inbound and outbound dock areas are a hub of activity, a properly engineered and protected rack structure can leverage the unused area above the dock doors to free up floorspace. For operations thinking of using over-the-dock racking, here are a few special considerations for their safe application in busy loading zones Consideration # 1: What Are the Stored Items Many operations utilize over-the-dock racking to store items that are useful to have near the dock. Often, this is an ideal place to put empty pallets, said Dawn Bigbee, Design Supervisor at NUCOR Warehouse Systems, a member of the Rack Manufacturers Institute (RMI). “We often see over-the-dock racking used to hold pallets that are waiting for a return trip to a customer or a vendor,” she said. “This helps open up floorspace in the dock area by allowing them to be stored overhead.” Likewise, other operations use over-the-dock racking to store excess inventory of packing and shipping materials, Bigbee continued. “I’ve also seen operations use this as the spot to store facility-related items, like extra lightbulbs. It’s a good location for long-term storage of items that don’t require frequent access or movement.” Consideration # 2: Structural Capacity of the Rack Configuration As with every rack installation, safety is paramount when implementing over-the-dock racking. Bigbee urged operations considering this solution work with a qualified rack design engineer to ensure the safest structure. There are three typical over-the-dock storage rack solutions available. Conventional single-deep selective pallet rack with uprights located on either side of the dock doors. The first level of storage beams and decking are immediately above the doors. However, because of the heavy forklift traffic passing in and out of the dock doors when loading and unloading trailers, many operations prefer to minimize impact risk. There are two rack design alternatives that can accomplish that goal in busy loading zones, said Bigbee: single-leg pallet rack and suspended pallet rack. “In both of these situations, however, the rack must tie in to the building wall,” she explained. “That makes the design of these two types of over-the-dock racking more complicated structurally, because now the loading forces will be applied to the wall. That additional load can damage the building’s structure.” To safely and properly design these styles of rack requires consultation with the building’s original structural engineer. That can be challenging when working with an existing building, she said. “It may not always be possible to locate the facility’s structural engineer — particularly in an older building,” Bigbee noted. “If you can find that person, they need to confirm that the building’s walls can handle the applied loads imparted by the rack. But it’s often challenging, particularly in older facilities.” For that reason, the optimal time to plan for single-leg or suspended over-the-dock racking is during the design phase of a new facility. Regardless of whether using over-the-dock racking in a new building or as a retrofit, the rack structure will need permits issued by the local jurisdiction. Consideration # 3: Protecting Uprights and Personnel Installing safety and containment accessories will help protect the racking from forklift impacts and prevent items from falling into the busy loading area. Pallet rack column guards — offered in a variety of configurations — deflect impacts. Bollards and guardrails are free-standing versions of these protective guarding devices. They are installed on the floor a few inches in front of the uprights. Other column protection options are either bolted or welded to the column. Outfitting over-the-dock racking with flexible safety nets or rigid steel mesh panels protects personnel working in the area from falling items. These containment accessories capture any items before they tumble to the floor. “Like all other industrial steel storage rack installations, plan for routine inspections of over-the-dock racking for damage,” added Bigbee. Because these racks will be in a high-traffic area, inspections should occur daily to identify dents, missing safety pins, loose anchor bolts, and more. Immediately isolate the area until repairs are complete. Want More Pallet Rack Safety Guidance? RMI offers multiple resources detailing both standards and best practices that enhance people and pallet rack safety. This includes a series of videos, presentations, publications, case studies, frequently asked questions, and an MHI Cast podcast recording about rack safety. TAGS BEAMOVER-THE-DOCK RACKINGPALLET RACKPROTECTIVE GUARDINGRACKRACK DAMAGERACK GUARDINGRACK INSPECTIONRACK MANUFACTURERS INSTITUTERACK SAFETYRMI
MODEX-The biggest manufacturing and supply chain event of 2024 is coming to Atlanta March 11-14
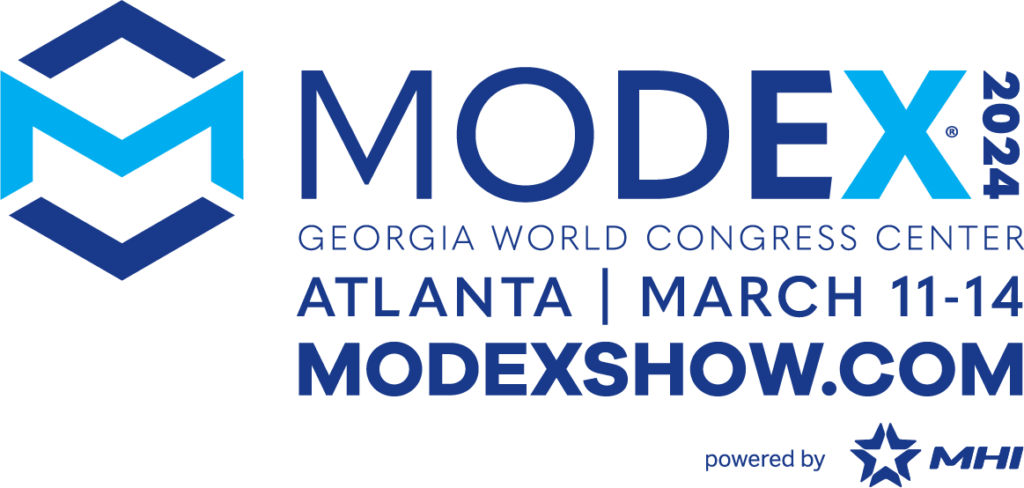
Trade show and conference to feature over 1,000 exhibitors, 165 sessions and keynotes from Jeremy Renner, AI expert Gerd Leonhard, and UPS’s Bill Seward When the largest manufacturing and supply chain trade event of 2024, MODEX, returns to Atlanta on March 11 it will include over 1,000 exhibitors from leading solution providers and a comprehensive Educational Conference focusing on best-in-class solutions for manufacturing and supply chain operations. MODEX 2024 exhibits will represent all segments of the material handling, logistics and transportation industry, from traditional, manual equipment to computerized, automated systems and smart, connected supply chain technologies and last mile logistics. “Only at MODEX, can you engage in face-to-face business interactions and gain immersive firsthand experiences with cutting-edge supply chain equipment, technology, and solutions,” says John Paxton, CEO, MHI. “The value of witnessing these solutions in-person, in-action on the exhibition floor, participating in informative educational sessions, and connecting with industry leaders and innovators all in one place is invaluable to taking your operations to the next level of excellence. MHI is excited to offer this market access and knowledge-sharing opportunity to their entire industry.” “Supply chains are essential to the health of the overall global economy.” says Daniel McKinnon, EVP of Exhibitions, MHI. “By exploring the diverse range of solutions, engaging with industry-leading suppliers, and networking with peers, manufacturing and supply chain professionals can unlock opportunities to identify essential solutions that will pave the way for their future success.”MODEX 2024 Conference In addition to the exhibits, the MODEX Conference will include four keynotes and over 165 show floor educational sessions covering leading trends, best practices and state-of-the-art equipment and technology solutions that can make manufacturing and the entire supply chain work more resiliently, efficiently and profitably. March 11 Keynote: Lessons Learned from the Supply Chain Front Line Bill Seward, President, UPS Supply Chain Solutions March 12 Keynote: Exponential Change in the Age of AI: Digitization, Decarbonization and Reformation Gerd Leonhard, CEO, The Futures Agency and Founder, The Good Future Project March 13 Keynote: A Conversation with Jeremy Renner The Heart of An Avenger March 30 Keynote Panel: Preview of MHI 2024 Annual Industry Report John Paxton, CEO, MHI and Wanda Johnson, Supply Chain Specialist Leader, Deloitte Consulting LLP March 13: MHI Industry Night with Colin Jost MODEX will feature an evening of music, food, drinks and entertainment by comedian Colin Jost on Wednesday, March 31. Tickets to this event are $50 and include beer, wine and hors d’oeuvres. The door prize for this event will be a trip of a lifetime vacation. Women in the Supply Chain Industry Forum on March 11 at MODEX MHI has partnered with Material Handling Equipment Distributors Association and the Warehousing, Education and Research Council (WERC) to bring an afternoon of discussion, education, and networking for women in our industry. MHI Young Professionals Network Reception on March 11 at MODEX This event provides attendees with an opportunity to network and connect with young professionals in the material handling and supply chain industry. MODEX 2024 Student Day on March 13 MHI in partnership with Warehousing Education and Research Council (WERC), College Industry Council on Material Handling Education (CICMHE), Material Handling Equipment Distributors Association (MHEDA) and the Material Handling Education Foundation (MHEFI) presents Student Day at MODEX. More than 300 students will have the opportunity to tour the exhibition and gain first-hand experiences of the latest supply chain technologies. MODEX is the largest manufacturing and supply chain expo held in North America and South America. The event will be held March 11-14, 2024 at Atlanta’s Georgia World Congress Center. MHI also announced the dates for ProMat 2025 in Chicago. ProMat will be held March 17-20, 2025 at McCormick Place.
Rail traffic for the week ending October 7, 2023
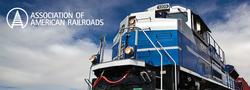
The Association of American Railroads (AAR) has reported U.S. rail traffic for the week ending October 7, 2023. For this week, total U.S. weekly rail traffic was 499,217 carloads and intermodal units, up 3.0 percent compared with the same week last year. Total carloads for the week ending October 7 were 233,768 carloads, up 3.6 percent compared with the same week in 2022, while U.S. weekly intermodal volume was 265,449 containers and trailers, up 2.5 percent compared to 2022. Seven of the 10 carload commodity groups posted an increase compared with the same week in 2022. They included motor vehicles and parts, up 2,618 carloads, to 16,495; grain, up 1,403 carloads, to 23,235; and petroleum and petroleum products, up 1,326 carloads, to 10,139. Commodity groups that posted decreases compared with the same week in 2022 were miscellaneous carloads, down 440 carloads, to 8,745; farm products excl. grain, and food, down 124 carloads, to 16,461; and forest products, down 1 carloads, to 7,937. For the first 40 weeks of 2023, U.S. railroads reported cumulative volume of 9,008,598 carloads, up 0.4 percent from the same point last year; and 9,594,783 intermodal units, down 7.9 percent from last year. Total combined U.S. traffic for the first 40 weeks of 2023 was 18,603,381 carloads and intermodal units, a decrease of 4.1 percent compared to last year. North American rail volume for the week ending October 7, 2023, on 12 reporting U.S., Canadian and Mexican railroads totaled 346,637 carloads, up 2.6 percent compared with the same week last year, and 349,627 intermodal units, down 1.5 percent compared with last year. Total combined weekly rail traffic in North America was 696,264 carloads and intermodal units, up 0.5 percent. North American rail volume for the first 40 weeks of 2023 was 26,066,184 carloads and intermodal units, down 3.6 percent compared with 2022. Canadian railroads reported 96,488 carloads for the week, up 2.6 percent, and 72,277 intermodal units, down 11.8 percent compared with the same week in 2022. For the first 40 weeks of 2023, Canadian railroads reported cumulative rail traffic volume of 6,344,008 carloads, containers and trailers, down 3.4 percent. Mexican railroads reported 16,381 carloads for the week, down 10.2 percent compared with the same week last year, and 11,901 intermodal units, down 15.4 percent. Cumulative volume on Mexican railroads for the first 40 weeks of 2023 was 1,118,795 carloads and intermodal containers and trailers, up 3.4 percent from the same point last year. To view the traffic charts, click here.
September 2023 Logistics Manager’s Index Report® LMI® at 52.4
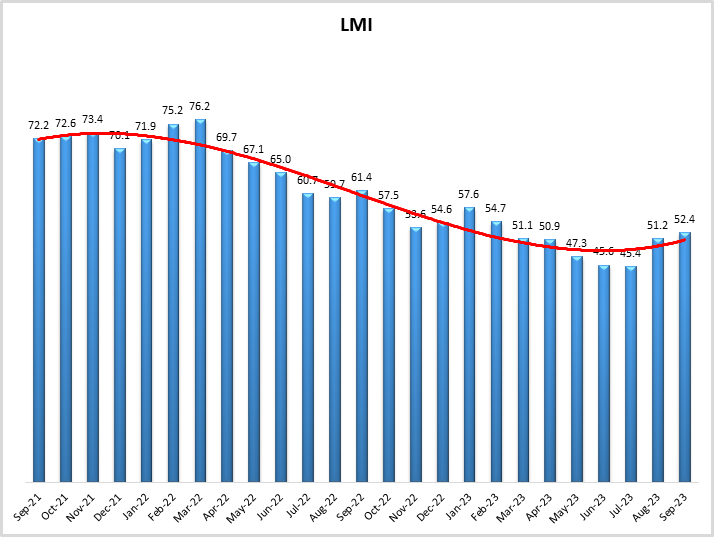
Growth is INCREASING AT AN INCREASING RATE for: Warehousing Utilization, Warehousing Prices, Transportation Capacity, and Transportation Utilization. Inventory Costs, Warehousing Utilization, and Warehousing Prices Growth is INCREASING AT AN DECREASING RATE for: Warehousing Capacity and Inventory Costs Inventory Levels and Transportation Prices ARE DECREASING In September the Logistics Manager’s Index read in at 52.4, up (+1.2) from August’s reading of 51.2. This is the second consecutive month of expansion following three straight readings of contraction from May-July. While this is the fastest rate of expansion since February, a reading of 52.4 is still well below the all-time average of 62.9 and represents a very moderate level of expansion. The largest contributor to September’s expansion is our three warehousing metrics. The rate of expansion has slowed for Warehousing Capacity (-3.4) while rates of expansion for Warehousing Utilization and Warehousing Prices (+3.1 and +7.9 respectively). We also observe Transportation Utilization moving from no change to expansion (+3.5) and a slight slowdown in the decline of Transportation Prices (+0.6). Conversely, we do observe a slight increase in the contraction of Inventory Levels (-4.5) and Inventory Costs (-4.5). This second consecutive expansion provides further evidence suggesting that the move towards growth in August was not a one-off occurrence and may have marked a turning point back towards growth in the logistics industry. It is possible we could see the index slide back into contraction in the face of a potential government shutdown and the UAW strikes. However, we have generally observed strong rates of growth in the fourth quarter, so seasonally speaking, it would be unusual to see a move back towards contraction through the rest of 2023. Researchers at Arizona State University, Colorado State University, Florida Atlantic University, Rutgers University, and the University of Nevada, Reno, and in conjunction with the Council of Supply Chain Management Professionals (CSCMP) issued this report today. Results Overview The LMI score is a combination of eight unique components that make up the logistics industry, including: inventory levels and costs, warehousing capacity, utilization, and prices, and transportation capacity, utilization, and prices. The LMI is calculated using a diffusion index, in which any reading above 50.0 indicates that logistics is expanding; a reading below 50.0 is indicative of a shrinking logistics industry. The latest results of the LMI summarize the responses of supply chain professionals collected in September 2023. The overall LMI is up slightly (+1.2) to 52.4, which represents a very moderate level of expansion. Moderate expansion might be an apt description of the U.S. economy overall. Labor force participation is increasing as the U.S. added 187,000 new jobs in August. While this is slightly above the pre-pandemic average from 2019, it is down from the explosive growth observed throughout 2022 and early 2023. This move towards more sustainable levels of growth may take some pressure off the Federal reserve to raise interest rates again in 2023[1]. Feelings of optimism continue around the U.S. economy as indicated by the University of Michigan’s consumer confidence measure reading it at 68.1 in September – up 16.2% from this time a year ago. When combined with the “Current Economic Conditions” reading of 71.4[2], it is clear that consumers are optimistic about the state of the economy. This optimism is partially due to the continued slowing of inflation. Personal consumption expenditures were up 0.4% in August due to energy and fuel prices. Core inflation rose by only 0.1% over the same period[3]. Wall Street is not quite as confident, as the S&P fell more than 4% in September, making it the worse month for stock prices in 2023. This may be partially due to money moving over to Treasury bonds, where returns have increased with the anticipation that higher interest rates could stick around for longer than had been expected[4]. That being said, the U.S. is still in better shape than many other places around the world. China continues to struggle with consumer sentiment and a crash in their exports and construction industries. A survey by the U.S.-China Business Group does not paint a rosy picture regarding a potential Chinese turnaround, with 43% of respondents stating the Chinese business environment has deteriorated in the past 12 months due to stop-start lockdowns, and restrictions on trade and technology transfer between the U.S. and China[5]. Germany, which has long been the economic driver of the EU, is struggling as well. Europe’s economy may have contracted in Q3 as interest rates continue to take a toll. Conversely, it appears as though there may be growth in places like Australia and Japan. Many central banks are now pulling back on interest rate increases, but it remains unclear if or when any countries could slide into recession[6]. Consumer spending remained strong through the summer as well. While this provides a hope that holiday spending will increase the movement of goods, there are a few potential obstacles on the horizon in the form of the resumption of student loan payments, the UAW strike, and a potential U.S. government shutdown. While a government shutdown was avoided in the last few hours of September, the matter will likely come up again in another 45 days, which could potentially coincide with the runup to black Friday and Cyber Monday. Beyond any potential damage a shutdown could do to sectors of the economy, it would also delay the publication of the economic statistics that the Fed partially bases their interest rate decisions on[7]. While a shutdown remains theoretical, the UAW strike is very real and is increasing in scale in its third week at the end of September, with more walkouts focusing on Ford and GM facilities[8]. Goldman Sachs estimates that annualized economic growth will decrease 0.05 to 0.1 percentage points every week that the strike goes on[9]. Inventory metrics were a somewhat mixed bag in September. Inventory Levels declined (-0.5) at a rate of 47.4, marking the fourth consecutive month that inventories have declined. There is some nuance to this however, as large firms with over 1,000 employees actually saw
The ARA Show 2024 returns to The Big Easy in February
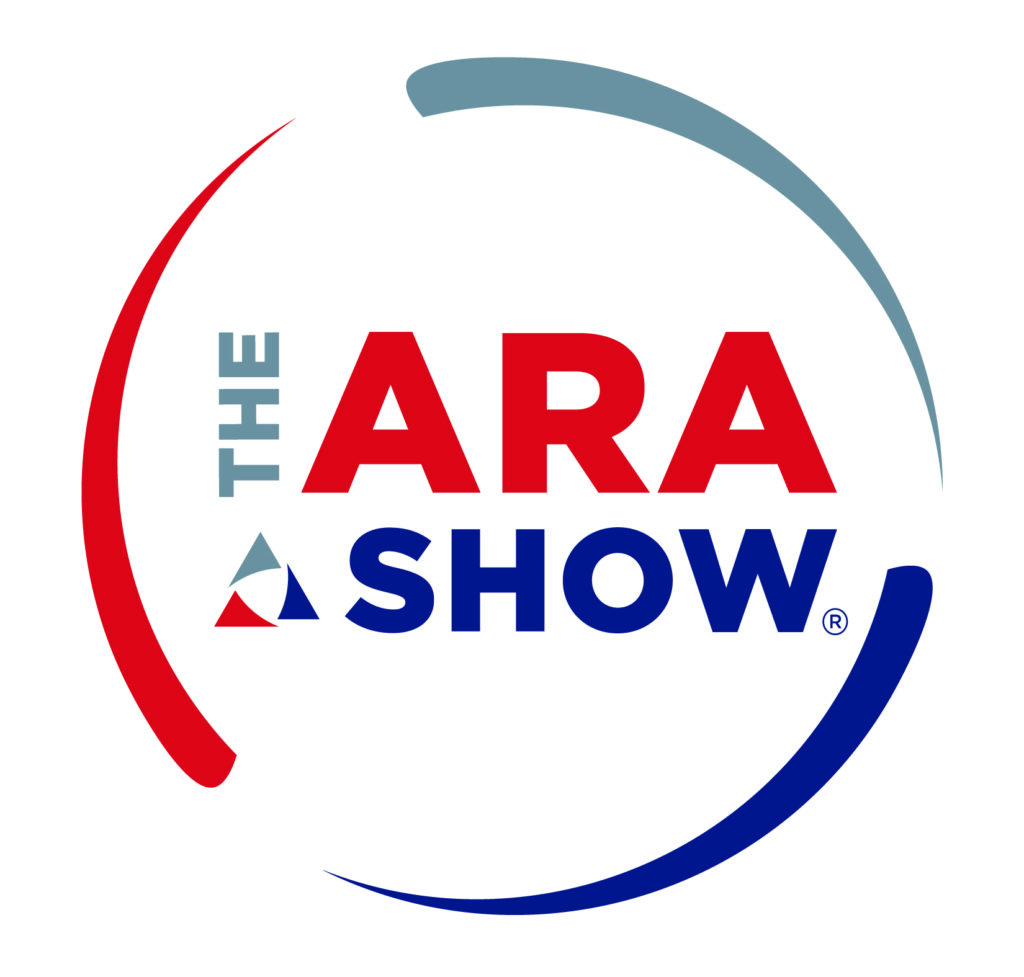
The ARA Show™ returns to The Big Easy when the world’s largest equipment and event rental trade show makes its way to the Ernest N. Morial Convention Center in New Orleans, Louisiana, February 18 – 21, 2024. The American Rental Association’s (ARA) annual trade show is a can’t-miss event with nearly 40 hours of education and more than 19 hours of trade show excitement over three days with more than 630 exhibitors. Registration for The ARA Show 2024 opens Tuesday, October 17. Both current and prospective ARA members can take advantage of incentive pricing through October 31, and advance pricing through February 15. “We are thrilled to bring The ARA Show 2024 back to New Orleans for an engaging, insightful and fun week for our members. Last year’s show set the bar high and we’re excited to carry that momentum forward with a mix of educational programs, professional networking and our popular social gatherings throughout the week,” says Tony Conant, ARA CEO. The excitement begins on Saturday, February 17, with the return of EventsU. Designed specifically for event rental professionals, the one-day program gives attendees an opportunity to hear from industry leaders on topics including event rental safety, tenting and the latest trends, plus exclusive networking with their event rental industry peers. The ARA Show 2024 officially kicks off with a full day of education sessions on Sunday, February 18. An unmatched array of exceptional sessions will feature professional speakers, industry experts and rental peers. Content on a variety of relevant and timely topics will be offered that appeals to rental professionals at every level. The keynote address — sponsored by ARA Insurance — will be delivered by John Taffer on Monday, February 19. Host and executive producer of Paramount Network’s “Bar Rescue,” Taffer relies on four decades of hospitality, entertainment and nightlife industry experience to advise companies on resetting their business models to ensure future success. Taffer is the best-selling author of three books, in addition to being featured in Forbes Magazine, Rolling Stone and the New York Times. As part of his keynote presentation, Taffer will share the business management expertise he has offered to thousands of businesses and Fortune 500 companies. Immediately following Taffer’s keynote session, the trade show floor will open for two and a half days of product introductions, the latest innovations and Show-Only Specials that allow attendees to fit more equipment and services into their budgets with exclusive deals. “There is a lot of excitement about The ARA Show 2024 being back in New Orleans and that is evident with more than 630 exhibitors confirmed and limited booth space remaining,” says Christine Hammes, ARA Vice President Association Services/Events. “That presents a great opportunity for our members and prospective members to prepare for a successful year ahead by bringing together the education, products and services tailored to their business needs.” Other featured networking events during The ARA Show 2024 include the ARA Young Professionals Network Reception, ARA’s Industry Awards Lunch, Regional Receptions, Women in Rental Breakfast, ARA’s Tuesday Night Event at House of Blues New Orleans featuring Mitchell Tenpenny and more. Advanced registration and ticket requirements may apply. The ARA Show 2024 registration opens Tuesday, October 17. For complete show details, including registration and pricing information, visit ARAshow.org.
August orders of Manufacturing Technology grow 16.1% from July
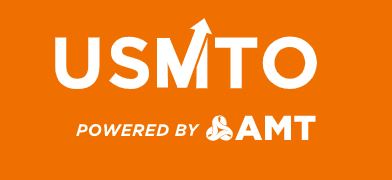
New orders of manufacturing technology totaled $404.2 million in August 2023, according to the latest U.S. Manufacturing Technology Orders Report published by AMT – The Association For Manufacturing Technology. August orders increased 16.1% from July 2023 but were down 12.2% from August 2022. Year-to-date orders reached $2.23 billion, 12.6% lower than the first eight months of 2022. “We are seeing industries focused on shorter-term projects reduce their spending, but at the same time, OEMs focused on longer-term production timelines have been increasing their spending, keeping orders at an elevated level,” said Douglas K. Woods, president of AMT. “The net result is that for the third consecutive month, the gap between year-to-date orders in 2022 and 2023 has narrowed, falling from a 14.6% deficit in May to the 12.6% difference we see today.” Job shops continued to order machinery below their typical monthly share. The value of orders was well below their historical trend despite their share of unit orders remaining elevated. This indicates that while job shops are continuing to buy to increase capacity, OEMs are increasing their purchases of specialized machinery to make more complex, higher-value parts. Of those OEMs increasing orders, manufacturers of automotive transmissions have increased for yet another month. This marks the highest three-month streak of orders since June to August 2017. Manufacturers of engines, turbines, and other power transmission technologies are also increasing orders at a rapid pace. The current upward trend is the largest sustained increase in orders since the increase that peaked in summer 2008, which was driven by the transition from coal-fired power plants to electricity generated by natural gas turbines. “Much of the spike in demand for manufacturing technology over the last few years can be traced back to elevated consumer demand. To gauge the probable path of manufacturing technology orders in the future, we should keep an eye on the health of consumer spending,” said Woods. “Between mortgage payments becoming a larger share of discretionary income, wages in many industries not keeping pace with inflation, and ongoing labor disputes shuttering production lines, there are still several headwinds that face both consumers and the manufacturing technology industry.”
When going for gold isn’t good enough
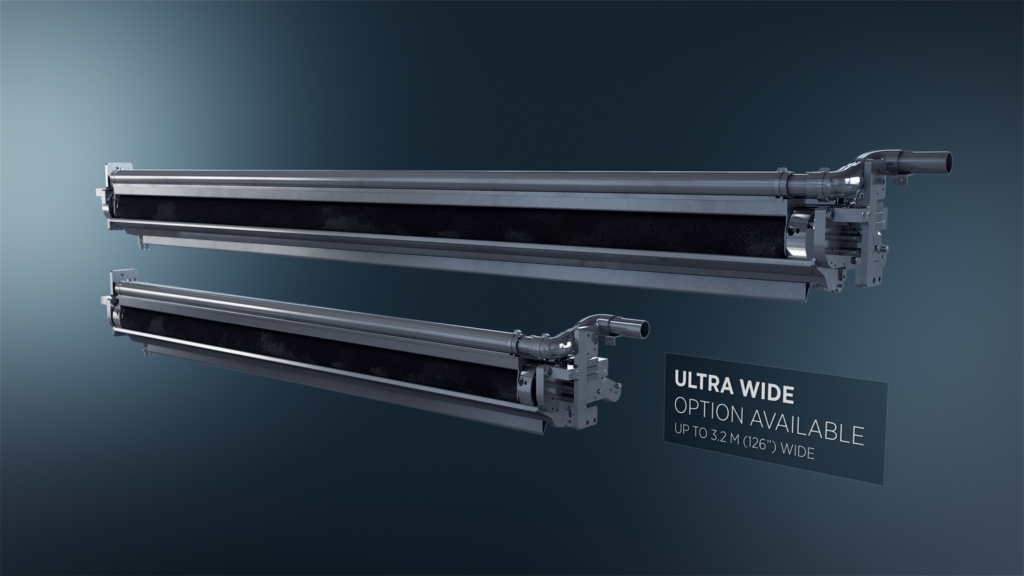
Baldwin Technology experts to highlight “Diamond Standard” for corrugated production efficiency at FEFCO Technical Seminar Spotlight Baldwin, the global manufacturer and supplier of innovative process-automation equipment, parts, service and consumables for the printing, packaging, textile, plastic film extrusion and corrugated industries, will be demonstrating its corrugated-industry leadership by sharing a “Diamond Standard” on cleaning and drying revelations at the forthcoming FEFCO Technical Seminar (Centre de Congres de Lyon, Lyon, France, October 25-27, 2023). During its October 25 Spotlight Spot at FEFCO, Baldwin will present a provocative technical presentation entitled “Fool’s Gold. Why All That’s Gold Doesn’t Glitter. – Adopt the ‘Diamond Standard’ for Efficiency,” led by Dennis Behnisch, Baldwin’s Germany-based Engineering and R&D Leader. FEFCO is the European Federation of Corrugated Board Manufacturers, the non-profit organization representing the interests of the industry across Europe and addressing a wide range of issues, from technical topics to economic considerations. Baldwin’s presentation will be centered on its how the users of its combination of Diamond IR and FlexoCleanerBrush can glean value from these technology advancements Baldwin’s recently-introduced Ultra Wide FlexoCleanerBrush has garnered wide market favor and adoption. It is a fully automated flexo plate-cleaning system that can be up to 126 inches (3.2 meters) wide. As Baldwin’s flagship solution to enhance print quality and improve worker safety in corrugated printing, the system automatically removes dust and contamination from the plate in seconds during production, without stopping the press. It also performs full end-of-job plate cleaning and drying in under four minutes, enabling increased capacity, improving operator injury and saving thousands of dollars per year in consumables spending. Baldwin will also explore its FlexoDry Infrared (IR) drying system. Developed to maximize press throughput, boost production speeds and reduce energy consumption, the FlexoDry system utilizes Diamond-IR lamps to focus powerful IR radiation. These lamps use a unique ceramic reflector that directs all light to the substrate, resulting in 30% energy savings when compared with other IR lamps. In addition to these technological advancements, to further support the overall corrugated industry Baldwin has launched www.printenomics.com. A corrugated-specific Ebook featuring a dedicated resource center, it houses discrete industry organization and trade publication links and a host of podcasts and instructional guides to maximize profitability in the corrugated space. In consultation with its customers, industry experts, and in-house engineering team – along with a review of the latest reporting – “From Beast to Beauty” explores four primary trends that will impact box-making facilities: E-commerce, Brand Protection, Sustainability, and Labor Challenges.“With the incredible explosion in demand for corrugated materials, it’s no secret that box plants are being squeezed to get more capacity and quality out of their existing equipment. When you add to this the scarcity of qualified operators to run production, the entire industry requires smart automation that enables efficiency,” said Behnisch. “Here at Baldwin ,we possess a long-held knowledge of the corrugated industry – we have pioneered technologies that our customers demand, and that is what the audience can learn more about at our spotlight talk.”