TAPPI’s Corrugated Packaging Council elects two new members
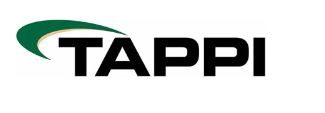
Danny Lopez, VP of New Machinery Sales at The Haire Group, and Tom Staal, Director of Management Systems at Coastal Containers, have been elected to TAPPI’s Corrugated Packaging Council (CPC). The CPC acts as the governing body of TAPPI’s Corrugated Packaging Division, developing strategic plans, press products, and events. Lopez collaborates with Haire’s global customers to develop new products, which is part of his responsibility. He has worked his entire career in the corrugated packaging industry, beginning in 2006 as an application engineer for Alliance Machine Systems International, where he designed corrugated plant layouts in North, Central, and South America before switching to sales, management, and product support for all Alliance customers in the western U.S. and Canada. Staal used his experience as a plant floor supervisor, quality management professional, and now member of the organization’s management team to help Coastal transition from a sheet plant start-up to a full-line corrugated plant. A 30-year TAPPI member, he has long been a member of the Corrugated Board Technical Service Committee (CORBOTEC) and the Fiberboard Shipping Container Testing Committee (FISCOTEC). Staal served as Chair of FISCOTEC and is currently the Vice Chair of CORBOTEC. He previously served as an elected member of the CPC as well as an appointed member. He has served as working group chair on numerous TAPPI Test Methods and TIPs and the Standards Advisory Review Group (SARG). Staal was awarded the Division Technical Award in 2019. The CPC includes appointed members from International Paper, The Haire Group, Menasha Packaging, WestRock, Packaging Corporation of America, Pratt Industries, Arvco Container, Advance Packaging, SMC Packaging, and Greif. The elected positions include BW Papersystems, Kohler Coating, Niagara Sheets, and Fosber members. The Chairs of the Corrugated Division Technical Committees, the YP Division Liaison to Corrugated, and the Supplier Advisory Committee Chair complete the council. Each position is for a three-year term. Lopez and Staal will serve as Member-at-Large. TAPPI’s Corrugated Packaging Division focuses on manufacturing and using corrugated containers and associated packaging materials and products and serves as a forum for knowledge sharing in the industry. The Division comprises members who work for converters, suppliers, consulting companies, and others in the converting industry.
KION Group opens Center of Excellence for automated solutions
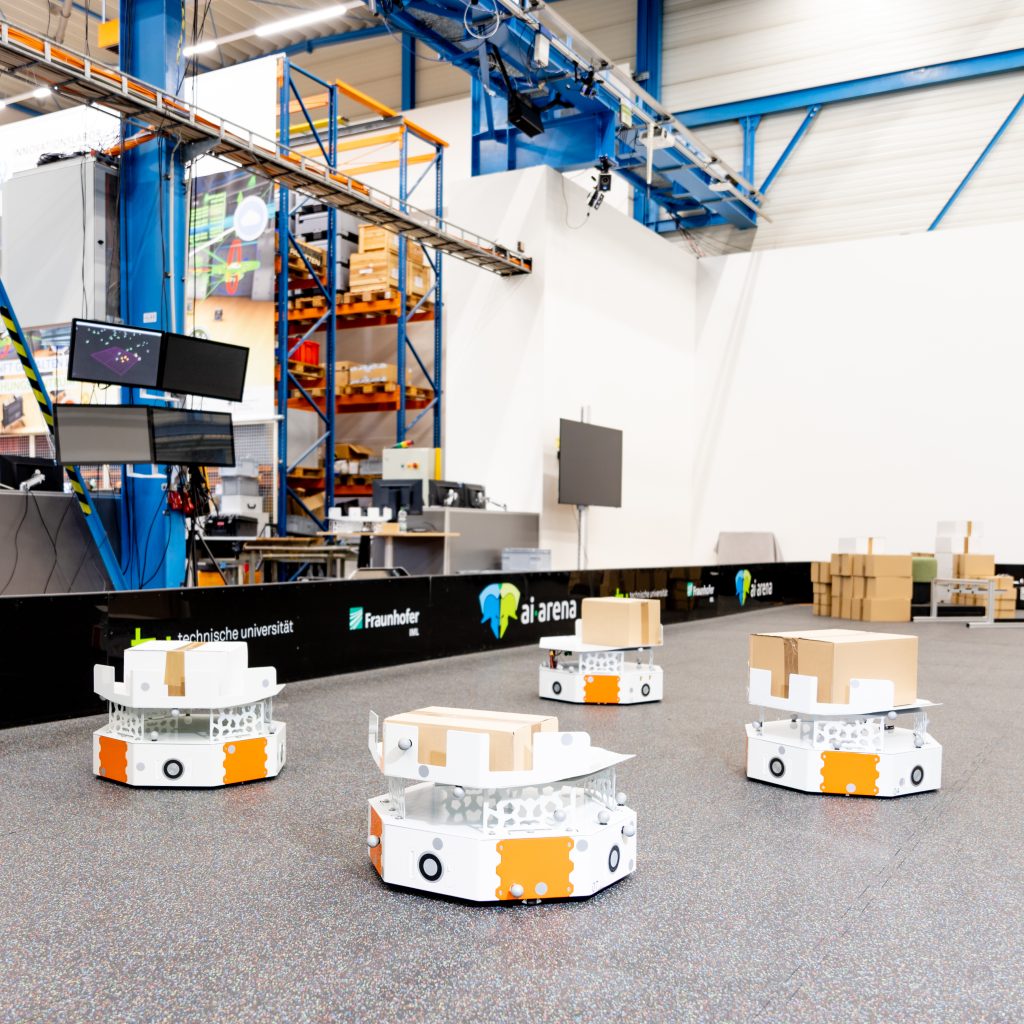
Now under one roof: Automated trucks and software development, customer solutions development, project realization, and production The new facility improves efficiency and fosters collaboration to develop industry-leading automation solutions for KION Group brands Ching Pong Quek, CTO of KION Group: “We can now more efficiently respond to customer needs and deliver innovative automation solutions faster.“ The KION Group has opened the KION Automation Center Antwerp in Belgium, a Center of Excellence facility for automated solutions in EMEA. It is the first of its kind and is now the primary hub for research and development, testing, and customized production of automated solutions in EMEA. Employees from the KION brands will now work and collaborate on automation projects and individual customer requirements. “Automation is the future for our industry, so I’m very excited about the new facility,” says Ching Pong Quek, member of the Executive Board and Chief Technology Officer of KION GROUP AG. “By bringing various capacities under one roof, we can now respond to market needs and deliver automation projects faster, more innovatively, and cost-effectively. The teams design the right automation solutions for our customers and support our regional sales teams.” The new building allows new solutions to be tested and optimized on-site and requirements to be addressed individually and quickly. “The Center of Excellence will enable intensive collaboration across businesses with the aim of serving our customers even better,” says Quek. Approximately 400 employees with diverse professional backgrounds and 40 nationalities work at the KION Automation Center Antwerp. The 11,800-square-meter building is well equipped for collaborative work, with a flexible office concept encouraging creative thinking, learning, testing, and training. The building is located near the port of Antwerp in an industrial area that is set to grow and develop further in the coming years. Cross-departmental collaboration is a critical success factor at the new site The employees who used to work in the two rented locations in Antwerp and Zwijndrecht have now moved into the new automation center. It shortens distances and promotes cross-departmental team collaboration. One of the teams is the KION subsidiary, automation and software specialist Dematic, which has vacated its previous offices and moved less than 100 meters away to the new building. The team provides centralized services on automated solutions for customers across Europe. In addition to Dematic, other operating units of the KION Group are also based in the new building. One of them is KION Industrial Trucks and Services (ITS) EMEA, where a team handles customer projects from planning to delivery, including training sessions conducted in the office and test floors. They also focus on the testing and development of custom hardware and software solutions and the production of customized solutions, particularly for industrial vehicles. Robotic system development will play a major role in the new Center of Excellence for Automation. The team’s mission is to deliver intelligent, driverless, and interoperable robotic products, solutions, and services that are easy to deploy, operate, maintain, and support throughout their lifecycle in brownfield applications. Building design focuses on solutions that support sustainability The KION Automation Center Antwerp features modern standards of sustainable design, such as advanced insulation, solar panels, and a green roof. The goal is to achieve BREEAM sustainable building certification, which is based on a holistic approach to achieving environmental, social, and governance (ESG), health, and net-zero goals. A BREEAM assessment uses recognized performance measures against established benchmarks to evaluate a building’s specification, design, construction, and use from energy to ecology. In addition, the KION Group is working closely with the European agency Encon to obtain a WELL Gold certificate from the US-based international WELL Building Institute. The WELL Building Standard is an evidence-based system for measuring, certifying, and monitoring building characteristics that affect the health and well-being of occupants. The new address of the location: KION Automation Center Antwerp Katwilgweg 3 B-2050 Antwerpen
H&E opens new Dallas South Branch
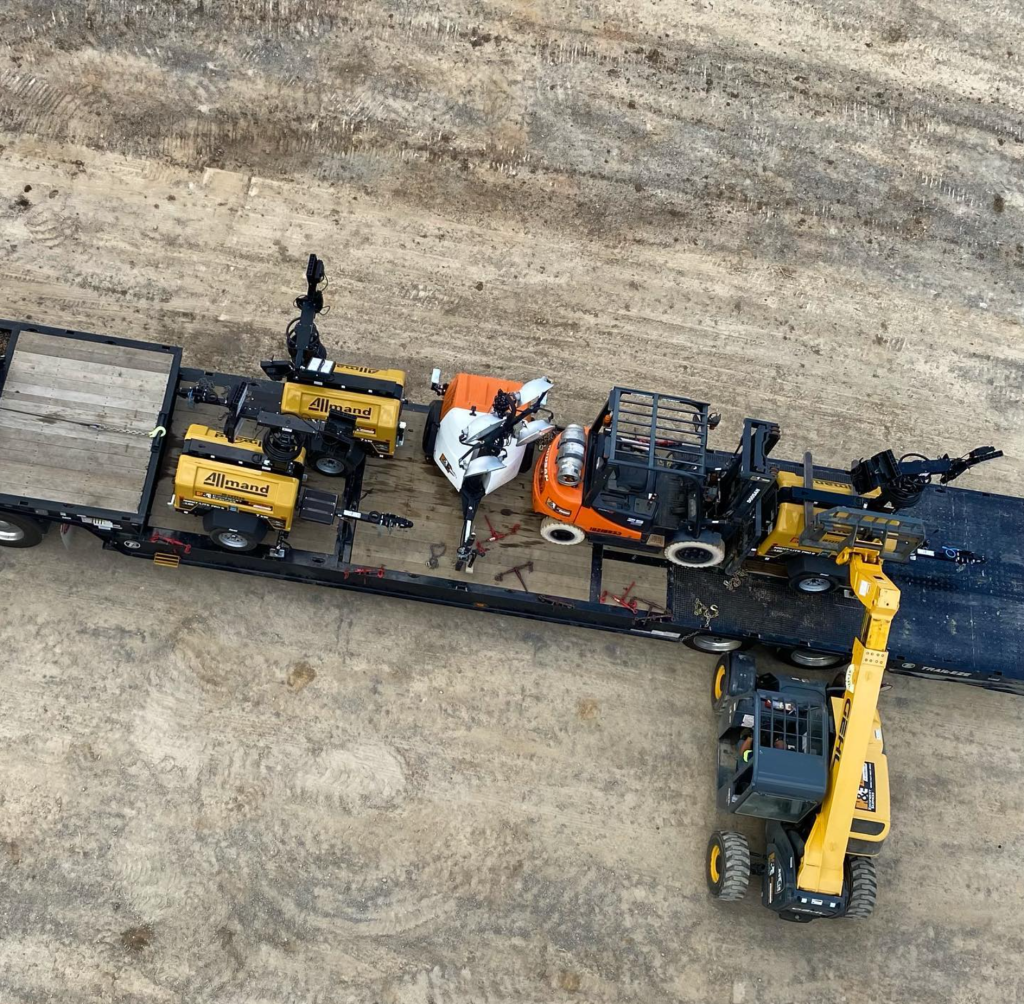
H&E Rentals has announced the opening of its Dallas South branch, the company’s 33rd location in the Lone Star State. It is also the 11 th Texas branch added in just over two years. The facility is located at 9909 South Polk Street, Dallas, TX 75232-5814, phone 469-751-4100. It includes a fully fenced yard area, offices, and a repair shop and carries a variety of construction and general industrial equipment. “The Dallas-Fort Worth area continues to grow, and H&E has it covered. Our eighth and newest DFW general rental location is conveniently situated just southwest of where I-20 meets I-35E and provides even greater service to customers south of the metroplex. Bridging the distance between our Cleburne and Dallas branches, stretching east toward our Mesquite branch and southeast toward our new Lufkin location, we have all of East Texas covered,” says Branch Manager James Kelley. “Sourcing from an expanded local fleet means we can respond quickly and move equipment to your job site in Desoto, Lancaster, Waxahachie, Ennis, Corsicana, Athens, Palestine, Fairfield and all points in between.” The Dallas South branch specializes in the rental of aerial lifts, earthmoving equipment, forklifts, telehandlers, compaction equipment, generators, light towers, compressors, and more. The fleet represents the following manufacturers: Allmand, Atlas Copco, Blue Diamond Attachments, BOMAG, Case, Club Car, Connect Work Tools, Cushman, Gehl, Generac Mobile, Genie, Hamm, Haulotte, Husqvarna, JCB, JLG, John Deere, Kobelco, Kubota, LayMor, Ledwell, Lincoln Electric, Link-Belt Excavators, Manitou, MEC, Miller, Multiquip, Okada, Polaris, Sany, Skyjack, SkyTrak, Sullair, Sullivan-Palatek, Tag, Towmaster, UniCarriers, Vacuworx, Virnig, Wacker Neuson, Yanmar, and others.
AAR reports Rail Traffic for the week ending September 28, 2024
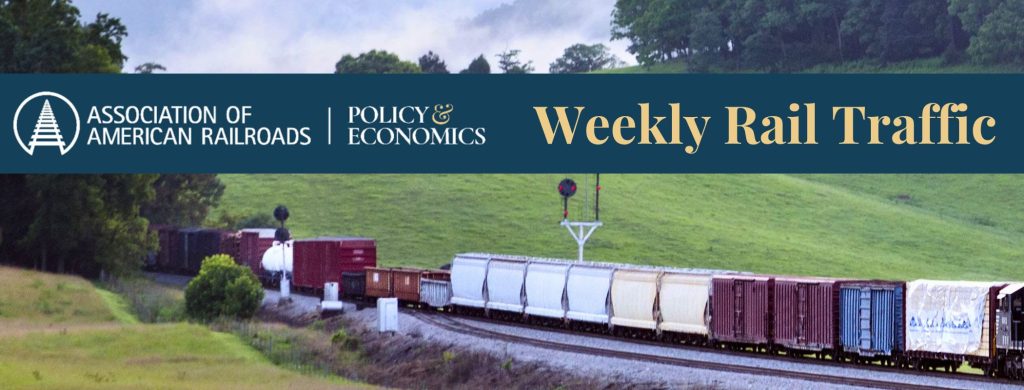
Today, the Association of American Railroads (AAR) reported U.S. rail traffic for the week ending September 28, 2024. This week’s total U.S. weekly rail traffic was 507,537 carloads and intermodal units, up 1.6 percent compared with the same week last year. Total carloads for the week ending September 28 were 227,046, down 3.5 percent from the same week in 2023, while U.S. weekly intermodal volume was 280,491 containers and trailers, up 6.2 percent from 2023. Four of the 10 carload commodity groups posted an increase compared with the same week in 2023. They included grain, up 2,435 carloads, to 20,941; motor vehicles and parts, up 732 carloads, to 16,705; and petroleum and petroleum products, up 617 carloads, to 10,782. Commodity groups that posted decreases compared with the same week in 2023 included coal, down 6,955 carloads, to 60,885; nonmetallic minerals, down 3,168 carloads, to 30,583; and metallic ores and metals, down 1,863 carloads, to 21,213. For the first 39 weeks of 2024, U.S. railroads reported a cumulative volume of 8,472,040 carloads, down 3.3 percent from the same point last year, and 10,211,605 intermodal units, up 9.5 percent from last year. Total combined U.S. traffic for the first 39 weeks of 2024 was 18,683,645 carloads and intermodal units, an increase of 3.3 percent compared to last year. North American rail volume for the week ending September 28, 2024, on nine reporting U.S., Canadian and Mexican railroads totaled 338,087 carloads, down 3.6 percent compared with the same week last year, and 362,754 intermodal units, up 4.2 percent compared with last year. Total combined weekly rail traffic in North America was 700,841 carloads and intermodal units, up 0.3 percent. North American rail volume for the first 39 weeks of 2024 was 25,999,318 carloads and intermodal units, up 2.5 percent compared with 2023. Canadian railroads reported 96,658 carloads for the week, down 1.6 percent, and 70,390 intermodal units, down 0.3 percent compared with the same week in 2023. For the first 39 weeks of 2024, Canadian railroads reported a cumulative rail traffic volume of 6,183,042 carloads, containers, and trailers, up 0.1 percent. Mexican railroads reported 14,383 carloads for the week, down 17.0 percent compared with the same week last year, and 11,873 intermodal units, down 11.4 percent. Cumulative volume on Mexican railroads for the first 39 weeks of 2024 was 1,132,631 carloads and intermodal containers and trailers, up 3.9 percent from the same point last year. To view the U.S. Rail Charts, click here.
IDENTCO is chosen by Prominent Kayak and Watercraft Provider for label durability
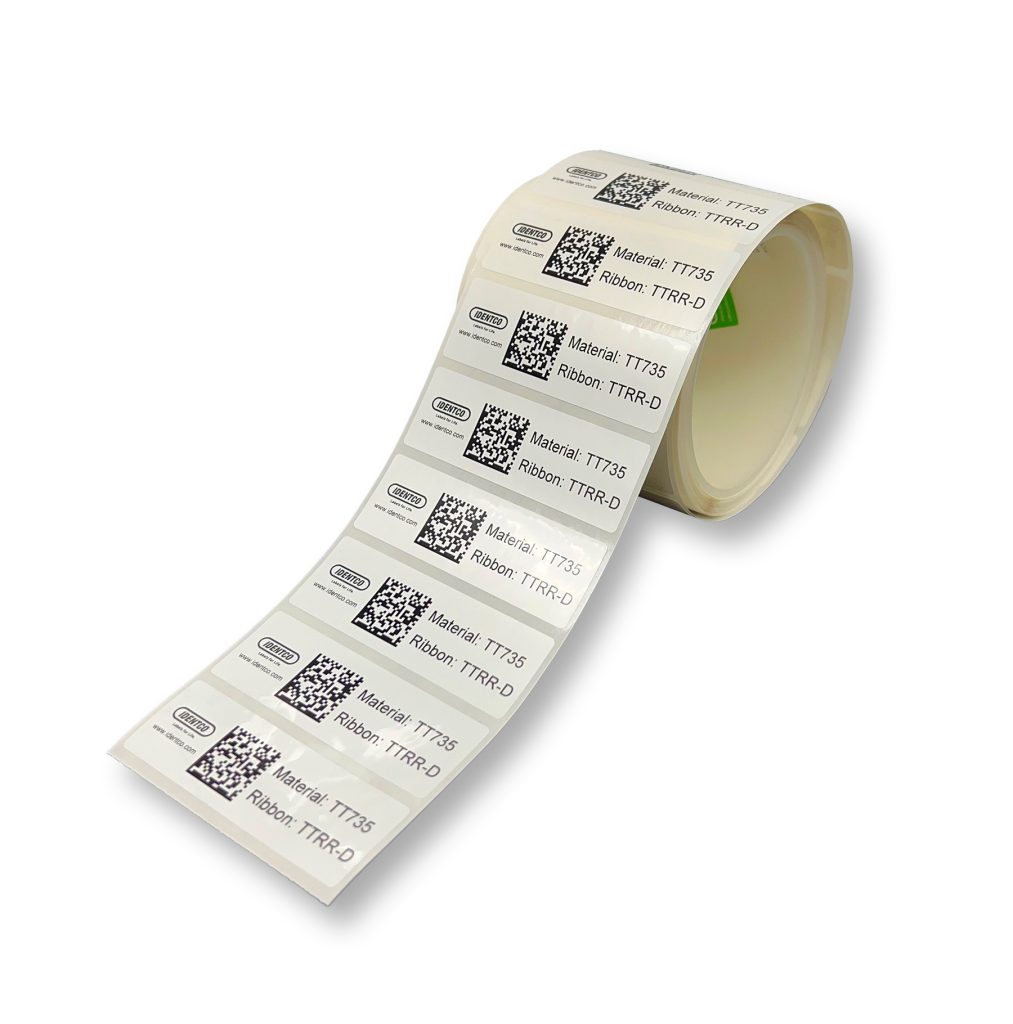
The company’s rugged TT735 Thermal Transfer Labels thrive during thorough comparison tests spanning an exceptionally rare 7,000 hours. IDENTCO has been named label supplier of choice by a prominent North American provider of kayaks and other consumer watercraft. The selection process comprised a comprehensive analysis gauging the durability and legibility of solutions from several labeling suppliers; notably, the thorough testing was conducted over a span of some 7,000 hours, exponentially exceeding the UL testing standard of 750 hours. Deemed the clear-cut winner, IDENTCO’s TT735 Thermal Transfer Labels – part of the company’s DuraChem Series – comprise a 2mil, top coated, gloss white polyester face stock providing excellent resistance to harsh chemicals and abrasion, and designed not to shrink. Its adhesive is a 2 mil, high-performance permanent acrylic with high solvent resistance and an extra thick layering to better adhere to LSE and textured surfaces. A 50# kraft liner offers exemplary performance for both manual and automatic applications. For the watercraft provider, the TT735 Labels are paired with IDENTCO’s TTRR-D Thermal Transfer Resin Ribbon, whose critical bond between ink and topcoat ensures lasting print legibility. Often utilized in rugged settings such as automotive, industrial, aerospace and electronics, the TTRR-D offers heightened resistance to chemicals and abrasion. To ensure the labels’ adhesion durability and enduring legibility across the wide swath of North American climates, tested labels underwent a process that saw temperatures fluctuate between -40° C and 80° C, and at relative humidity from zero to 95%. For its selection process, the watercraft company sought to confirm the functionality and readability of its labels over several years; considering that such simulations equate 375 hours with one year of outdoor exposure, the chosen IDENTCO solution proved durable and legible for well over 15 years. IDENTCO’s DuraChem Series features highly durable labels constructed from white gloss polyester, a versatile material that can adhere to a wide variety of standard smooth surfaces. Offering excellent chemical, solvent, abrasion, and smudge resistance, DuraChem labels have 2-year UL, CUL, and CSA ratings for both indoor and outdoor use and make an ideal choice for a variety of industries including medical, industrial, electronics, military, and automotive.
Episode 525: Healing brand and 3PL relationships with Logistics Resolve
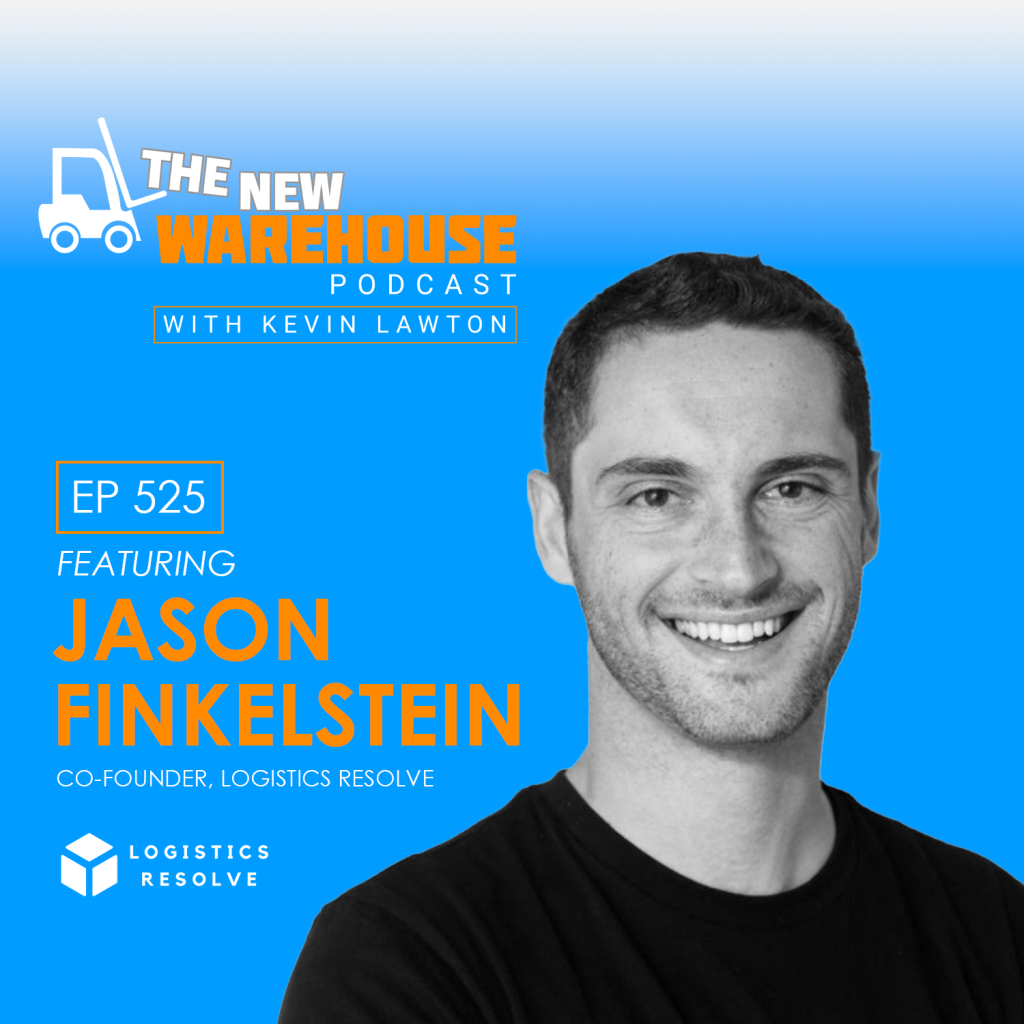
In this episode of The New Warehouse Podcast, Jason Finkelstein, co-founder and partner of Logistics Resolve, discusses an often overlooked yet critical issue in logistics—the relationship between brands and third-party logistics (3PL) providers. Logistics Resolve focuses on repairing broken ties between brands and 3PLs, preventing costly terminations, and enabling long-term partnerships. Drawing from years of industry experience, Finkelstein shares how his team steps in to mediate, heal, and guide these essential relationships. Tune in to hear insights on what causes friction in these partnerships and how businesses can prevent their logistics “marriages” from ending in divorce. The Five Big Issues Facing Brand and 3PL Relationships Finkelstein identifies five common issues that cause relationships between brands and 3PLs to break down. “You always hear people say, ‘I hate my 3PL,’ or ‘3PLs suck,’” he notes. Two issues are on the 3PL side—forecasting problems and scope changes—while two are on the brand side—SLA performance and visibility. A lack of communication, which both sides share, often exacerbates these issues. “Communication is the first and the last issue we work on,” Finkelstein explains, emphasizing how much of the tension can be defused by having consistent and clear conversations between both parties. Why Ending a Brand and 3PL Relationship is a Lose-Lose Terminating a brand-3PL relationship can have significant financial and operational impacts. Finkelstein describes the process as “the biggest lose-lose in the supply chain.” On the 3PL side, the costs include loss of revenue, idle square footage, and potential staff cuts. For brands, switching providers can mean up to a 25% annual increase in fulfillment and small parcel costs. “We really talk a lot about the transition being incredibly risky and incredibly expensive,” says Finkelstein. Many problems brands hope to leave behind by switching often resurface because the root issues never get addressed. How Communication Saves Relationships According to Finkelstein, the key to preventing relationship breakdowns is proactive communication. He encourages brands and 3PLs to shift their mindset from seeking perfection to presuming good intentions and working together to solve issues. “Perfect is not the objective,” he says, adding that regular check-ins can help identify potential problems before they escalate. Logistics Resolve’s mediation process ensures both sides clearly understand each other’s expectations and commitments. “Our job is to get both sides talking in a solution-oriented mindset versus blaming each other,” Finkelstein explains. Key Takeaways Five main issues cause brand and 3PL relationships to break down: forecasting, scope changes, SLA performance, visibility, and communication. Terminating a relationship can result in significant financial and operational costs (10%-25% of fulfillment +)for brands and 3PLs. Proactive communication and regular check-ins can prevent problems from escalating into irreparable conflicts. Logistics Resolve works to mediate and repair relationships, ensuring both sides stay aligned and focused on long-term success. The New Warehouse Podcast Episode 525: Healing Brand and 3PL Relationships With Logistics Resolve
BBI adds Bobby Kehley as new Regional Sales Manager for Northeast Region
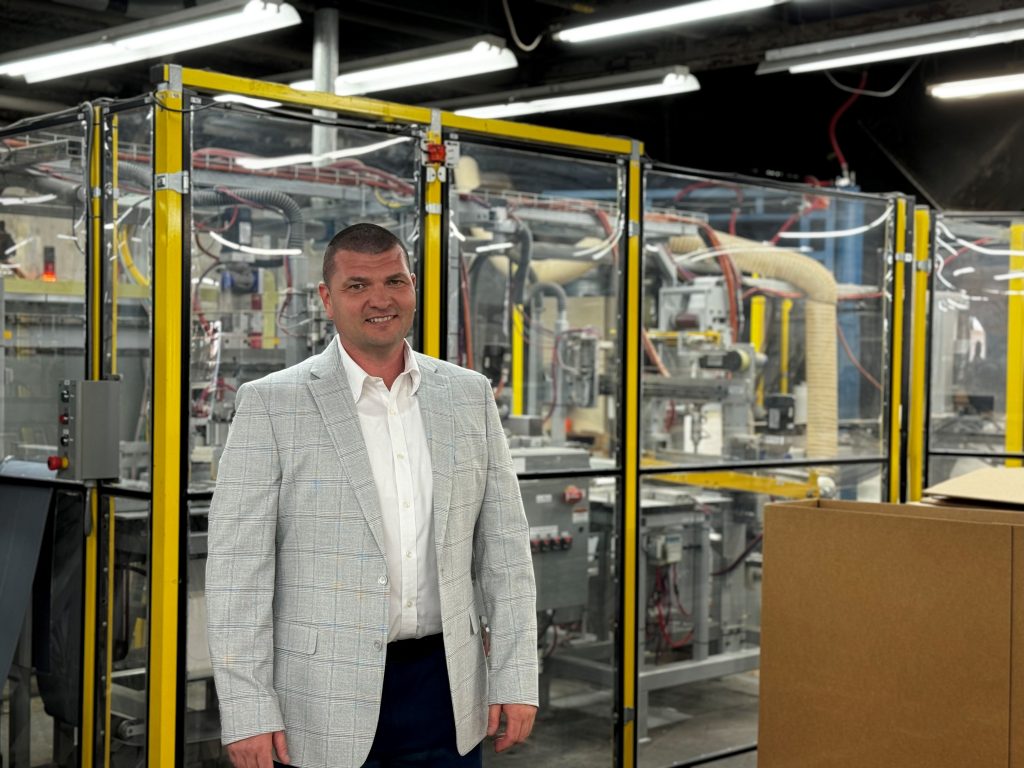
Battery Builders, a manufacturer of lead-acid batteries for the motive power industry, has announced Bobby Kehley’s appointment as the new Regional Sales Manager for the Northeast region. In this key role, Bobby will be the primary point of contact for all motive power-related inquiries and sales initiatives across the area. With over 27 years of experience in the industrial motive power industry, Bobby brings a wealth of knowledge and expertise to BBI. His proven track record in sales and customer relationship management will be instrumental in strengthening our presence in the Northeast and enhancing our commitment to providing exceptional service to our clients – working closely with them to understand their challenges and help them leverage BBI’s innovative products and services to achieve their goals. John Gaughan, VP of Sales, shares, “I was excited to welcome Bobby to the BBI team because his extensive network of contacts in the Northeast is a game changer for us; it’s not just about what you know but who you know – and anyone who knows Bobby knows how driven he is and I’m excited to introduce that drive to our customers. BBI has been the industry’s best-kept secret for far too long, and we’re thrilled to finally reintroduce ourselves to the marketplace. We’re ready to showcase the innovation and expertise that sets us apart, and Bobby will be a key role in this effort.” Bobby has held previous roles at Key Material, Eastern Lift Truck, Alta, and Philadelphia Scientific and is most notably known for helping grow the footprints of the companies in his history. His family has been in the industry for over 70 years, and Bobby holds deep roots in material handling. “I am very happy to be part of a company that has been in the industry for such a long time and thrilled to be part of its growth and rebirth under new leadership,” says Bobby. Bobby is based in New York City and is eager to connect with industry partners and customers throughout the Northeast. He can be reached at bobby.kehley@batterybuilders.com or (646) 510-0626.
ProMach announces the acquisition of HMC Products
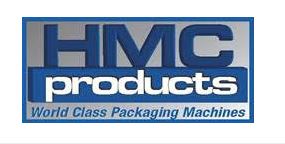
ProMach, a worldwide provider of processing and packaging machinery and related solutions, announced today that it has acquired HMC Products, a provider of machinery and related solutions, announced that it has acquired HMC Products. Adding HMC is ProMach’s fourth acquisition this year, further strengthening its global portfolio of flexible packaging solutions. HMC fabricates and installs new HMC HFFS machines and rebuilt HMC/Bartelt® HFFS machines for flexible packaging solutions across numerous industries, such as snack food, food, cosmetics, healthcare, pharmaceutical, and household goods. The company is also known for its exceptional service and focus on refurbishing or converting existing HMC and Bartelt systems to extend the life of the equipment. Their 60,000-square-foot facility in Machesney Park, IL—just north of Rockford—supports customers with responsive parts distribution and service. “We are very pleased to welcome the HMC Products team to ProMach,” said ProMach president and CEO Mark Anderson. “Their established brand and reputation in the flexible packaging space underscores our ongoing ability to deliver best-in-class packaging solutions while continuing to demonstrate growth within strategic market segments that bolster our business.” Anderson continued, “HMC and their loyal customers will see even further benefits as a result of ProMach’s ability to deliver world-class systems and support around the globe.” Founded in 1979, HMC and its 45 employees will join ProMach’s Systems & Process business unit led by Group president Ryan McCart. This business unit comprises five business lines: Flexible Packaging, Trays, Handling & Sterilization, Systems & Integration, and Process business lines. These business lines provide systems integration, processing, flexible and rigid packaging systems, product handling, retort, and related packaging solutions across 21 distinct product brands. HMC leadership will report to Donald Deubel, Senior Vice President of Flexible Packaging. “The addition of HMC to our Flexible Packaging business line is exciting because of what this means to our current and future flexible packaging customers. Their machining and fabricating expertise that provides quick builds and delivery of new or refurbished equipment, along with their dedicated service and aftermarket support, is exemplary,” said Deubel. “Having these expanded capabilities in our flexible packaging portfolio will equate to even shorter lead times and manufacturing enhancements for our customers,” Deubel added. Dave Kreissler, former president of HMC Products, will remain with the company and continue to lead the HMC team as Vice President and General Manager. “Our desire to join ProMach underscores our continued commitment to our customers by providing them with the best possible solutions and support,” said Kreissler. “In addition to building and installing our own branded HFFS systems, we have been a long-time supplier of parts for ProMach’s Bartelt equipment. The synergies and efficiencies that will come from our addition to the ProMach family of brands will benefit both our and Bartelt’s customers to an even greater level,” Kreissler concluded.
Celebrate Propane’s Versatility and Reliability on National Propane Day, October 7th
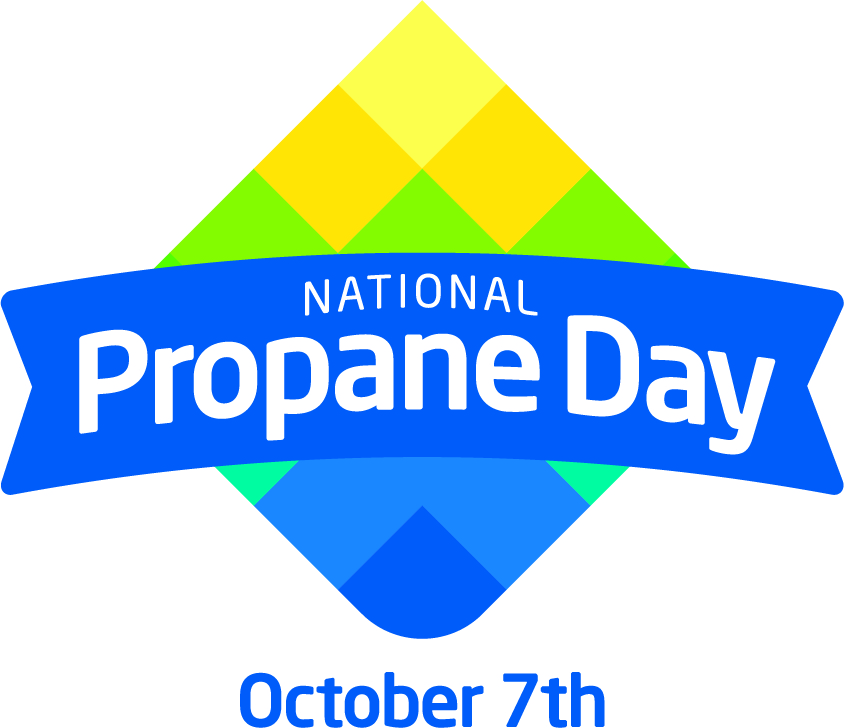
The third annual celebration recognizes propane’s impact on powering Forklifts, Vehicles, and more The Propane Education & Research Council (PERC) has announced the third annual National Propane Day on October 7, 2024 — an opportunity to celebrate propane’s essential role in powering the everyday lives of Americans nationwide. The celebration also honors the hardworking men and women who keep our economy moving with propane-powered forklifts and equipment. “Propane is more than just an energy source; it’s a critical component that helps businesses, homes, and essential services run smoothly, safely, and efficiently,” said Tucker Perkins, president and CEO at PERC. “Whether it’s keeping homes warm, helping farmers during harvest, powering school buses, or providing backup power during emergencies, we are proud to celebrate the many ways propane is a dependable energy solution our country can rely on.” As energy reliability and sustainability remain top priorities for industries and consumers, PERC encourages everyone to explore propane’s benefits — particularly as it complements other renewable energy sources like wind and solar. In addition, the production of renewable propane from sustainable materials like vegetable oils, animal fats, and used cooking oil offers the same reliability as conventional propane but with an even smaller carbon footprint. As more demand is placed on ports, distribution warehouses, and other facilities to remove diesel equipment and/or electrify the entire operation, now is the time to ensure that decision-makers across the U.S. are aware of the benefits and opportunities with propane-powered technology and are selecting that technology for their operation. “Propane generates approximately 52 percent fewer greenhouse gas emissions compared to equivalent electricity from the U.S. grid and provides a versatile option for diversifying the nation’s energy mix,” said Jim Bunsey, senior manager of business development at PERC. “By incorporating propane, Americans can reduce the strain on the electric grid while maintaining a cleaner and more resilient energy infrastructure.” On October 7th, communities, businesses, and propane advocates across the country will join the PERC in celebrating National Propane Day. PERC invites everyone to learn more about propane’s contributions to energy equity, environmental responsibility, and economic savings at Propane.com and Propane.com/NationalPropaneDay.
NRF Calls on Administration to use ‘Any and All Authority’ to end Port Strike
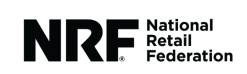
The National Retail Federation released the following statement from NRF President and CEO Matthew Shay after a labor strike was initiated at all U.S. East and Gulf Coast container ports. The strike went into effect after the six-year master contract between the International Longshoremen’s Association (ILA) and the United States Maritime Alliance (USMX) expired on Sept. 30. “NRF urges President Biden to use any and all available authority and tools — including the use of the Taft-Hartley Act — to immediately restore operations at all impacted container ports, get the parties back to the negotiating table, and ensure there are no further disruptions.” “A disruption of this scale during this pivotal moment in our nation’s economic recovery will have devastating consequences for American workers, their families and local communities. After more than two years of runaway inflationary pressures and in the midst of recovery from Hurricane Helene, this strike will result in further hardship for American families. The administration must prioritize our economy — and the millions of Americans who depend on it for their livelihood and well-being — and intervene immediately to prevent further hardship and deeper economic consequences. “It is essential that the ILA and USMX immediately resume negotiations with the intention of finalizing a new master contract without further disruptions and put an end to this stalemate.” Last month, NRF issued a statement urging the parties to immediately resume negotiations. The group also spearheaded a letter signed by nearly 200 organizations to President Biden urging the administration to intervene and avoid a disruption. In June, NRF led a coalition of 158 state and federal trade associations in a letter to President Biden urging the administration to work with the negotiating parties and to reach a new agreement. Earlier this year, NRF also sent a letter to ILA and USMX calling for the resumption of port labor negotiations. As the leading authority and voice for retail, NRF will continue to advocate for policies and solutions that ensure supply chain resiliency.
New JLG® E313 Electric Telehandler for evolving job sites
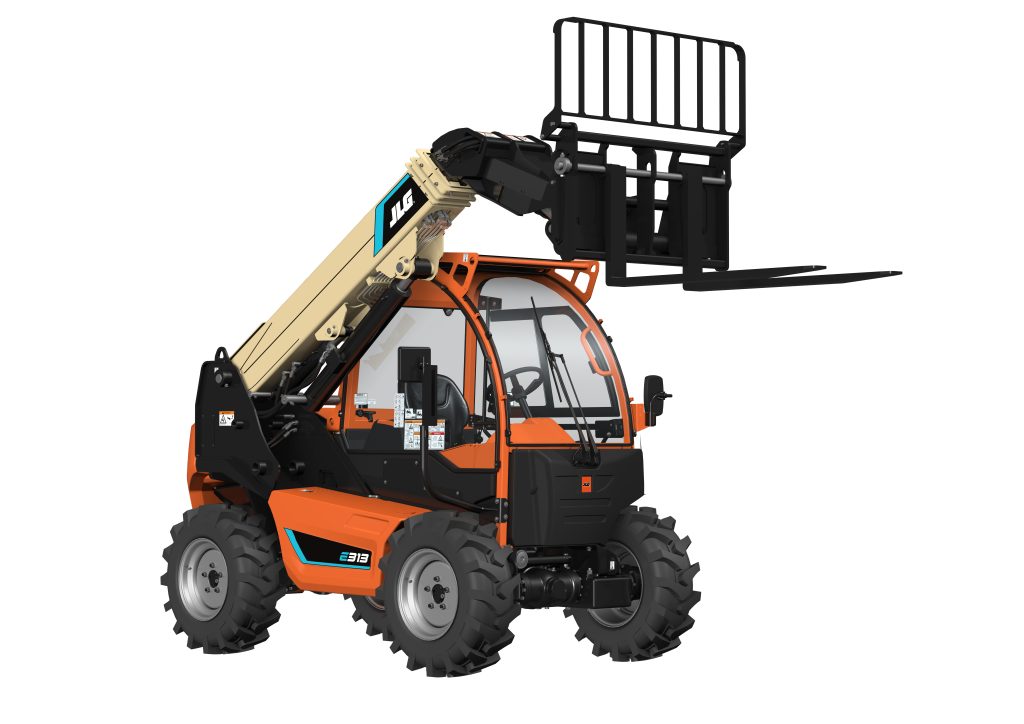
Zero fuel and zero emissions for work in quieter, more sensitive environments JLG Industries, Inc., an Oshkosh Corporation business and a global manufacturer of mobile elevating work platforms (MEWPs) and telehandlers, has unveiled its latest electric innovation: The E313 telehandler. Designed for all-terrain and off-road use, the battery-powered E313 offers zero-emission and low-noise operation for moving materials around indoor construction and urban, residential, and municipal projects. “As job sites evolve, machines need to evolve with them,” said John Boehme, JLG’s senior product manager for telehandlers. “Our new E313 electric-powered telehandler transforms how work is done in emission-free spaces and noise-sensitive environments by delivering a quieter, more efficient working experience.” With a 3,500-lb (1,587.57-kg) maximum lift capacity, a 13-ft 1-in (3.99-m) maximum lift height, 5-ft 8-in (1.73-m) forward reach and 9.3-mph (14.97-km/h) travel speed, this JLG® electric telehandler provides all the advantages of an ultra-compact, electric-powered machine without sacrificing performance for loading and unloading trucks and flatbeds, moving materials around or accessing work at height in single-story buildings. Key features of the new electric E313 include: 6-kW/h electrical system with six maintenance-free 48V lithium-ion batteries for environmentally friendly operation with no emissions Up to four hours of continuous operation, or extended intermittent use, for increased productivity with extended working hours, especially for overnight projects Dual on-board battery chargers with 110V and 220V charging adapters for convenient charging Efficient electric drive motors eliminate the need for fuel or oil and reduce maintenance, lowering operating costs Two-speed electric transmission with high-speed, two-wheel drive and low-speed, four-wheel drive for optimal power management for various job site conditions Two-wheel rear pivot power steering resulting in less ground disturbance Load Stability Indication (LSI) system for enhanced operator confidence, enhancing job site safety by mitigating the risk of accidents during load handling Seatbelt Engagement and Operator Presence system for enhanced safety with the use of visual and audible alarms, as well as limiting machine functions For increased machine versatility, this new electric telehandler from JLG comes standard with a universal skid-steer coupler system. This allows it to attach to various existing telehandler and skid-steer loader attachments, including carriages, forks, and buckets. It also has an integrated hitch for hauling tools around the job, increasing efficiency by reducing the need for additional equipment on-site. The E313 also boasts reduced maintenance requirements and easy serviceability, lowering operating costs. It comes standard with JLG’s ClearSky Smart Fleet™ management system, allowing for true two-way fleet interactivity. A diesel engine model, the JLG 313, is available in addition to this new electric model.
September 2024 Logistics Managers’ Index
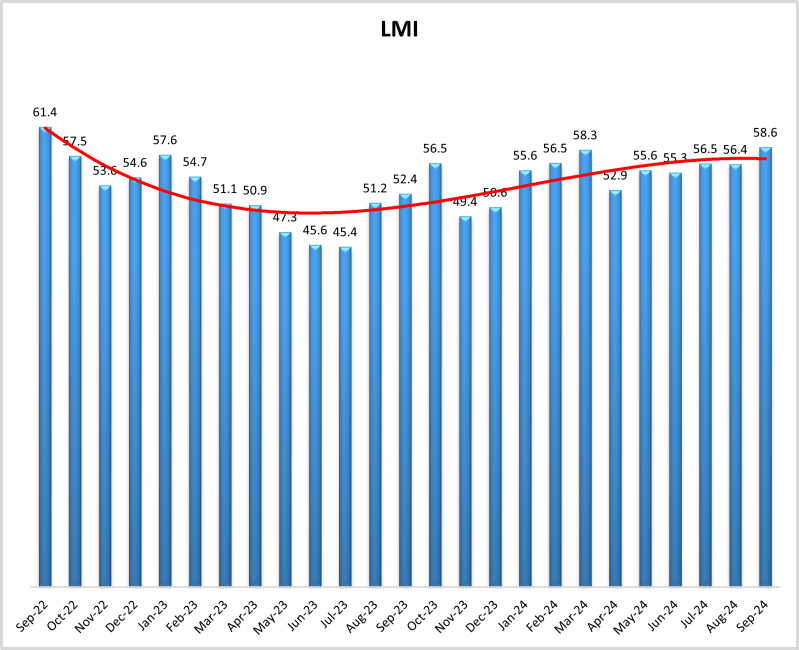
The September Logistics Manager’s Index reads in at 58.6, up (+2.2) from August’s reading of 56.4 and at its highest level since two years ago in September 2022. The overall index has increased for ten consecutive months, proving the logistics industry is back on solid footing. We saw a continuation of August’s trends in September as Inventory Levels increased (+4.1) to 59.8. The long-expected restocking of Downstream retailers primarily drives this. After several months of contraction, Downstream respondents are reporting expansion for Inventory Levels at a rate of 55.7. This represents some modicum of relief for Upstream supply chains, where goods had been building up like rainclouds waiting for the eventual downpour that retailers anticipate as we move into Q4. This shift is reflected in the significantly higher rates of Downstream Warehousing Prices (75.0 to 64.9 Upstream) and Transportation Prices (68.3 to 55.1 Upstream), signaling that retail supply chains are whirring back into motion for peak season. The fact that peak season is happening at all should be a bit of a relief for the logistics industry – and the economy as a whole – since we have not seen a traditional seasonal peak since 2021 (or possibly even 2019, if you don’t consider 2020 or 2021 to be “normal”). This activity resulted in Transportation Capacity moving back down to 50.0 and “no movement,” the second time that happened in 2024. Overall Transportation Capacity has not contracted since March of 2022. However, it is currently contracting at the Downstream level (45.0) due to the movement of goods from vendors down to retailers. It will be interesting to see if the current trajectory continues and it moves back to contraction at any point in Q4. Researchers at Arizona State University, Colorado State University, Rochester Institute of Technology, Rutgers University, and the University of Nevada, Reno, in conjunction with the Council of Supply Chain Management Professionals (CSCMP), issued this report today. Results Overview The LMI score combines eight unique components that comprise the logistics industry, including inventory levels and costs, warehousing capacity, utilization, and prices, as well as transportation capacity, utilization, and prices. The LMI is calculated using a diffusion index, in which any reading above 50.0 indicates that logistics is expanding; a reading below 50.0 indicates a shrinking logistics industry. The latest results of the LMI summarize the responses of supply chain professionals collected in September 2024. The LMI read in at 58.6 in September, up (+2.3) from August’s reading of 56.4, its highest level in two full years. While this is the 24th consecutive reading below the all-time average of 61.8 for the overall metric, the current trajectory suggests that may not be the case for much longer. This reflects the overall economy, which has recovered throughout 2024 and appears poised to expand more forcefully in 2025. Inflation continued to cool down in August, with PCE slowing to 2.2% year-over-year inflation, down 0.3% from July and close to the Fed’s long-term goal of 2% inflation. This number has led some analysts to suggest that the Fed will cut rates again in 2024[1]. The University of Michigan’s Consumer Sentiment Index increased to 70.1 at the end of September, up (+3.2) from August’s reading of 67.9. Forward look sentiment was also up (+2.3) to 74.4 in late September[2]. The percentage of U.S. households below the poverty line was down, and incomes were up 4% in 2023 to $80,610 per household. With this increase, household incomes are nearly on par with their all-time high reading of $81,210 in 2019 before the pandemic[3]. While this is a positive sign for consumers, it should be noted that these are raw numbers and not adjusted for inflation. The fact that U.S. incomes are still not quite back to where they were four years ago demonstrates just how long the economic hangover of COVID-19 has been. This positive economic data contributed to increases in all of the major U.S. stock indices in the last week of September, with the S&P 500 and the Dow, respectively, marking their 42nd and 32nd record high closes of the year[4].As has been the case for most of the last year, the outlook in other parts of the world is more complex and, in many cases, less optimistic than in the U.S. For instance, inflation also declined in France and Spain in September, likely leading to further rate cuts in the EU[5]. Germany has displayed mild improvement in consumer climate but continues to recover more slowly than analysts had anticipated [6]. This is reflected in the European Commission’s aggregate measure of business and consumer confidence, down 0.3% month-over-month, sliding slightly in the post-Olympics period[7]. There were some signs of life in China. In the last week of September, Chinese regulators put forth an economic stimulus package that included interest rate cuts, an allowance for smaller down payments on mortgages, and increased lending rates for firms engaging in stock buybacks. As a result, the Chinese CSI index increased by 15.7%, its most significant weekly gain since 2008[8]. The stock buybacks may be a temporary sugar high, so it will be interesting to monitor the long-term growth of this stimulus package for the world’s second-largest economy. Finally, closer to home, Canada’s GDP was flat in August, following a slight 0.2% uptick in July that had led some analysts to hope the Canadian economy was picking up steam[9]. This has led Bank of Canada officials to push for growth increases and a likely half-point interest rate cut at their October meeting[10]. The EU, China, and Canada are all among the U.S.’s most important trading partners, and the health of those countries will go a long way to determining the potential for supply chain activity. Of course, continued international trade with these countries relies heavily on the continued operation of U.S. ports, which is not as much of a sure thing at the end of September as supply managers would prefer. Port operators and carriers have appealed to the National Labor Relations Board (NLRB) to force
Combilift retained Deloitte’s Best Managed Company Award for the 12th Consecutive Year!
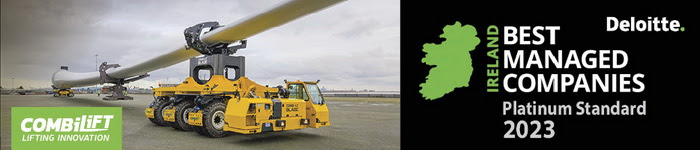
For the 12th consecutive time in the awards’ 16-year history, Combilift has been recognized as a Best-Managed Company, requalifying as a Platinum winner for the sixth time. Their management prowess was rewarded at Deloitte’s prestigious awards ceremony in Dublin on September 19th. The Deloitte Best Managed Company award acknowledges the achievements of management teams and not just individuals. The accolade recognises overall business performance based on the criteria of Strategy, Capability and Innovation, Culture and Commitment as well as Governance and Financial Performance. Judges examine every company based on these four equally weighted pillars to select a winner. The Best Managed Companies Programme originated in Canada in 1993, with Ireland’s program being the second longest-running program, introduced in 2008. In addition to Ireland and Canada, the program is currently run in a total of 48 countries across 4 continents. Founded in 1998 by Martin McVicar and Robert Moffett, Combilift has grown from a small team of 10 to a total staff of over 850 people, selling to 85 countries worldwide. When receiving the award, Martin McVicar said; “It’s a great honor for us as a company to be acknowledged once again by a global brand such as Deloitte’s Best Managed Companies. The credibility of this global award enhances our brand to scale internationally”.
Yale executive recognized as a trailblazing female supply chain leader
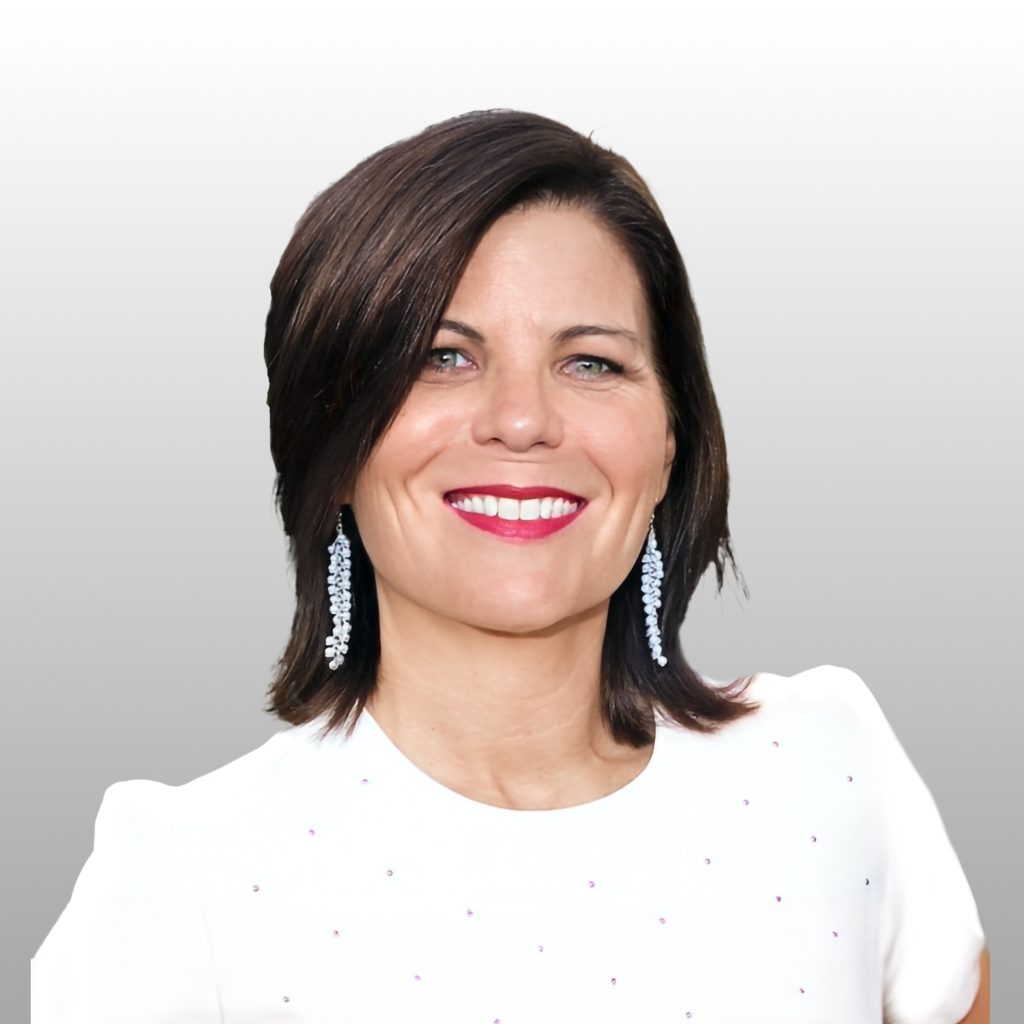
Yale Lift Truck Technologies has announced that Vice President of Global Marketing Strategy and Activation Jill Comer has been selected as a trailblazer in the 2024 Women in Supply Chain awards, presented by industry publications such as Supply & Demand Chain Executive and Food Logistics. The award honors female leaders who continue to pave the way for future women pursuing careers in the supply chain. At Yale, a division of Hyster-Yale Materials Handling, Comer was the first female to hold a sales management position in the brand’s nationwide dealer network. She was instrumental in founding the W4I Women in Leadership Employee Resource Group (ERG), the first ERG at Hyster-Yale Materials Handling. Comer has worked her entire career alongside and with the organization, securing an internship in the Yale dealer network while attending Penn State University and moving into a full-time dealership role immediately after college. During her tenure in the dealer network, she built strong relationships with leaders in the corporate organization, who recruited her to a major account role. After rising to a director role, she exercised her skill and passion for supporting dealer initiatives as a vice president of dealer sales for the eastern U.S. before being selected by leadership to build a new team dedicated to working with large dealer accounts. Now, Comer leads the global brand, emerging technologies, and events teams. “Jill has been the embodiment of a materials handling industry trailblazer here at Yale,” says Brad Long, North America Brand Marketing and Global Activation Manager, Yale. “Under Jill’s leadership, her team has developed a careful focus on the customer industries that are most strongly aligned with Yale and our sister brand, Hyster. She has cultivated strategies that support clear, meaningful brand differentiation to address the distinct needs and challenges of our respective customers, and has helped unite cross-functional teams to work cohesively on executing those strategies.” Comer is also passionate about helping her fellow professionals realize the best versions of themselves, a dedication best captured by her unique goal to someday work for someone who once worked for her. “That would make me so happy,” Comer says. “I have had the opportunity to work with so many talented people, and really believe you’re learning as much from them as they are from you.”
Yokohama TWS announces Elio Bartoli as Company President

Yokohama TWS has announced the appointment of Elio Bartoli as its new company President, effective December 1st. Elio Bartoli succeeds Paolo Pompei, who is stepping down to pursue external opportunities after an impressive tenure with the company. Elio Bartoli brings a strong display of leadership experience, including the last 12 years in various strategic roles at Yokohama TWS. His tenure has included positions such as Commercial Leader of Industrial Tires and, most recently, president of the EMEA Region and Global OE Leader. In these roles, he consistently demonstrated outstanding leadership across commercial and operational functions, driving significant growth and delivering exceptional business results. Elio’s deep expertise spans the entire supply chain, commercial strategy, and customer relations. His people-centric leadership style and his strong track record of fostering collaboration and innovation make him the ideal choice to lead Yokohama TWS into the next phase of its evolution. “We are thrilled to welcome Elio as our new president,” said Nitin Mantri, Co-COO of Yokohama and Head of OHT division. “His deep industry knowledge, strategic vision, and customer focus make him the perfect leader to guide Yokohama TWS into its next phase of growth. We are confident that under Elio’s leadership, the company will continue to deliver exceptional value to our customers, partners, and stakeholders.” Yokohama TWS wishes to extend its heartfelt gratitude to Paolo Pompei for his exceptional leadership and invaluable contributions over the past 25 years. Throughout his tenure, Paolo has expertly navigated the company through key phases of growth, expanded our global footprint, and cultivated a vibrant culture of people and innovation. His legacy will undoubtedly leave a lasting impact on the organization, inspiring us for years to come. Thank you, Paolo!
New partnership to bring “world’s safest hoist” to the US market
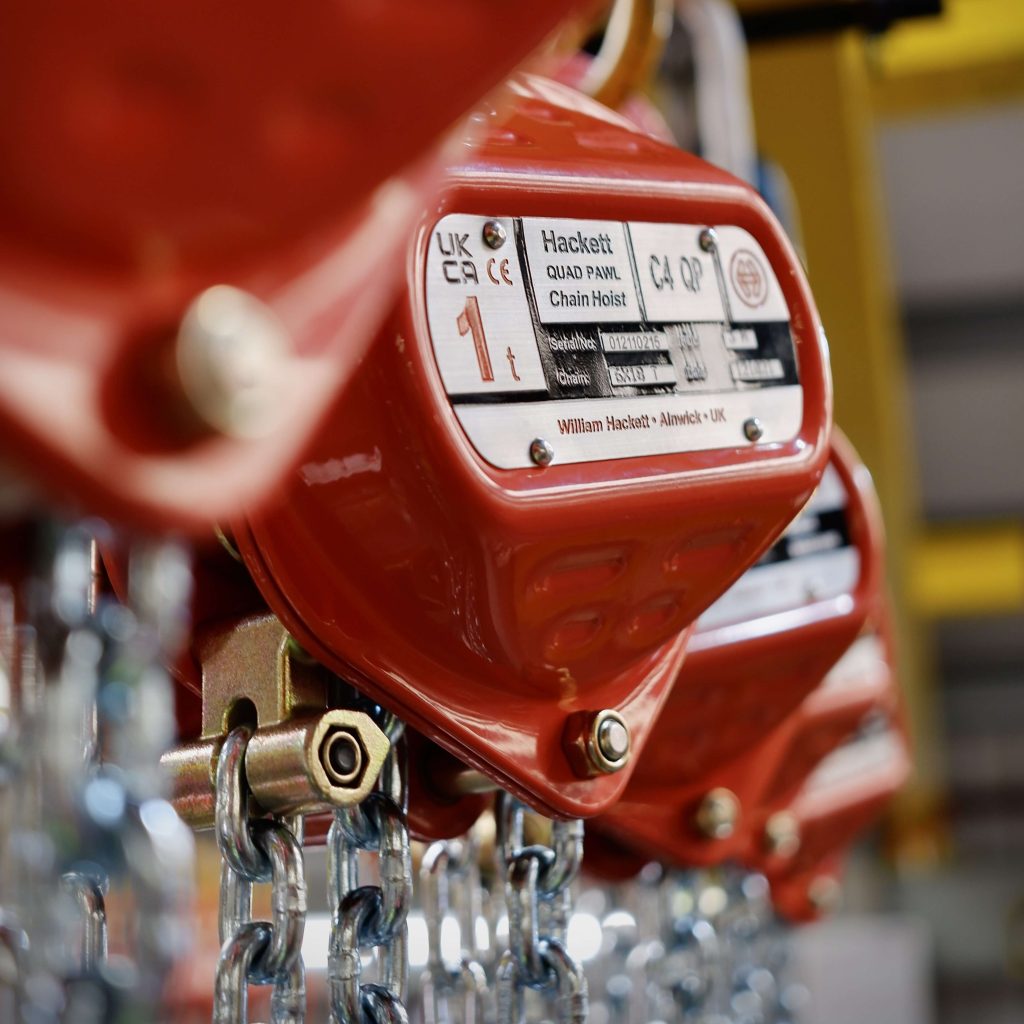
A new transatlantic partnership is bringing the benefits of superior safety hoists to the US market Atlas Lifting & Rigging (ALR) signs partnership deal with William Hackett New agreement brings William Hackett’s Quad Pawl hoist technology to the USA Superior safety hoists designed for offshore, energy, defense, and construction Atlas Lifting & Rigging (ALR) has signed an agreement to import innovative hoists from William Hackett in the UK. The hoists feature William Hackett’s patented Quad Pawl technology, which the company says makes them the safest in the world. Ben Burgess, Director of William Hackett, said: “Our Quad Pawl technology has been a huge success in other markets. We needed the right partner to help us bring the benefits of Quad Pawl to the USA and are delighted to have found that partner in ALR.” William Hackett’s patented pawl design features four-pawl mechanical engagement functionality. This enables all four pawls to engage with the ratchet gear in an offset configuration, reducing the risk of failure. Quad Pawl provides finer adjustment and tensioning ability while maintaining rachet/pawl engagement. Based in Houston, Texas, ALR is a fast-growing manufacturer and wholesaler of premium hoists. It has a nationwide network of distributors serving the American lifting industry. ALR now offers William Hackett WH C4 QP chain hoists and WH L5 QP lever hoists from its Houston warehouse. These hoists are designed for demanding applications in the offshore industry, energy, defense, and construction. Doug Ozolins, Executive Vice President of ALR, said: “William Hackett says that its Quad Pawl hoists have the safest ratchet mechanism in the industry – and we are inclined to agree. “ALR is growing rapidly because we have a reputation for supplying innovative, high quality, robust hoists like these. We are therefore extremely confident that there is demand for the William Hackett range from within our customer base.” Founded in 1892, William Hackett is a respected manufacturer of chains and lifting products. William Hackett hoists are designed, manufactured, and proof load tested in the UK. The new partnership with ALR builds on William Hackett’s growing business in North America. It already sells its market-leading range of HA master links and sub-assemblies—primarily focused on the Gulf of Mexico—along with its Hack10 chain sling components into the USA. “Developing the US market is a cornerstone of our business growth strategy,” added Ben. “We know that our unique QP technology can bring significant benefits to the US lifting industry and provide us opportunities for substantial growth.”
OZ Lifting returns to WEFTEC
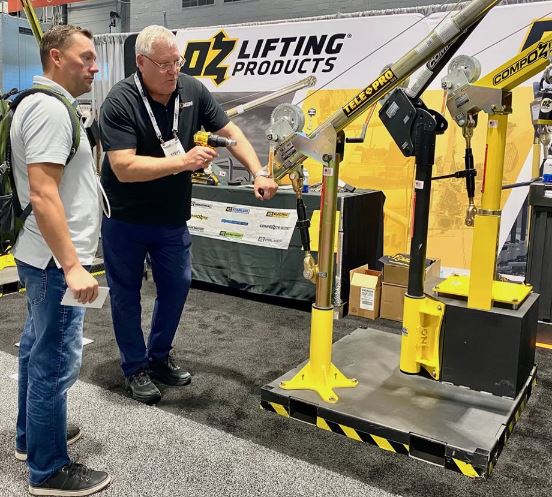
OZ Lifting Products LLC will exhibit at the Water Environment Federation’s Technical Exhibition & Conference (WEFTEC) on October 5-9, 2024, at the Ernest N. Morial Convention Center in New Orleans, Louisiana. The exhibition runs on the final three days of the event. See OZ Lifting at Booth 8229. OZ Lifting returns to the WEFTEC show floor with a 20 ft. by 20 ft. booth, having exhibited on three prior occasions. The center of attention will again be its Tele-Pro Davit crane range, available in 500 lb., 1,200 lb., and 2,500 lb. capacities. It allows users to leverage the benefits of the company’s other davits while telescoping the boom in and out under load. Richard Miller, sales manager at OZ Lifting, said: “The Tele-Pro has been a popular product in this industry because of its ability to make precise adjustments under load. Our customers have found this exceptionally beneficial for raising and lowering water pumps; we will be staging live demonstrations of this application in our booth at the show.” Another popular product is the 1,200-lb. capacity CompOZite davit crane, renowned for being ultra-lightweight and having exceptional corrosion resistance, even in harsh environments where water and treatment chemicals are present. The crane is made from advanced composite material and weighs only 83 lb. A CompOZite boom section will be in the booth to allow WEFTEC attendees to feel the weight difference firsthand. Attendees will see the CompOZite Elite, the world’s most innovative Davit crane, offering the same capacity as the CompOZite, with a total crane weight of only 37 lbs. The booth will also showcase the Steel 500, Alumi-Lite 500, and XR Series 500 davits, plus a new wheelbase, in addition to a full line of stainless steel products, including beam clamps, push beam trolleys, chain hoists, and manual winches. Not forgetting a range of lever hoists featuring the popular dynamometer-equipped Dyno-Hoist. Miller said: “We’ve been seeing a surge in demand for portable cranes in the water and wastewater industry. The ability to quickly move a single crane around a facility using interchangeable bases has been a game-changer for our customers. It’s helped them save time and money and improve overall efficiency. “Expanding our footprint at the show [up from 10 ft. by 20 ft. originally] allows us to showcase better our products, especially the Tele-Pro’s extending boom. With more room, we can comfortably demonstrate the full capabilities of this and other machines. The larger booth also helps us accommodate the increased traffic and provide a more enjoyable experience for visitors.” Miller will be joined in New Orleans by Steve Napieralski, president; Parker Hale, inside sales specialist; and Ashley Blum, marketing manager.
Airfreight soars above the congested ocean freight transport system
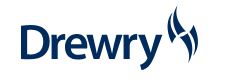
Drewry Airfreight Insight, a new online airfreight market intelligence service launched today by Drewry’s Supply Chain Advisory division, confirms airfreight’s growing popularity among international shippers as cost and congestion issues continue to impede ocean transport. 2024 has been a year of continued supply chain disruption for ocean freight shippers, forcing many to think and act creatively to alleviate the pressures on their global transport networks. With unreliable transit times and myriad problems in ocean transport, airfreight has stepped in and aided procurement teams in a time of need. As congestion has plagued the ocean freight sector, Drewry has seen double-digit growth in airfreight volumes, particularly out of Asia. Still, freighter capacity has remained buoyant enough to sustain this growth, and although rates have gone up, they have not matched the steep increases in ocean spot rates. Despite the demand boom in airfreight between Dec-23 and Sep-24, the cost ratio between airfreight and ocean freight spot rates has narrowed from 25.9x to 5.6x (see below). Drewry Airfreight vs. Maritime Price Multiplier Source: Drewry Airfreight Insight, Drewry Maritime Research, IATA “Procurement teams within global shippers/BCOs and forwarders need access to up-to-date market insights across both ocean and air sectors,” said Chantal McRoberts, director and head of advisory at Drewry Supply Chain Advisors.“This new monthly service provides the timely insights stakeholders need to determine the ‘best fit’ transport mode for their business.” The service will focus on the key drivers of the airfreight market (supply, demand, and load factors) on all key routes and key regional indices, enhanced by spot rate benchmarks against 127 of the most popular air routes. Airfreight Insight is accessed via Drewry’s digital Container Freight Portal, which also provides subscribers with wrap-around content such as Drewry’s World Container Index, Intra Asia Rate Index, Ocean Contract Rate Index, and Port Throughput Index, further enhancing the ocean freight market intelligence offered.
Orange County Business Journal names Toshiba’s Kerstin Woods 2024 Woman in Business Award Nominee
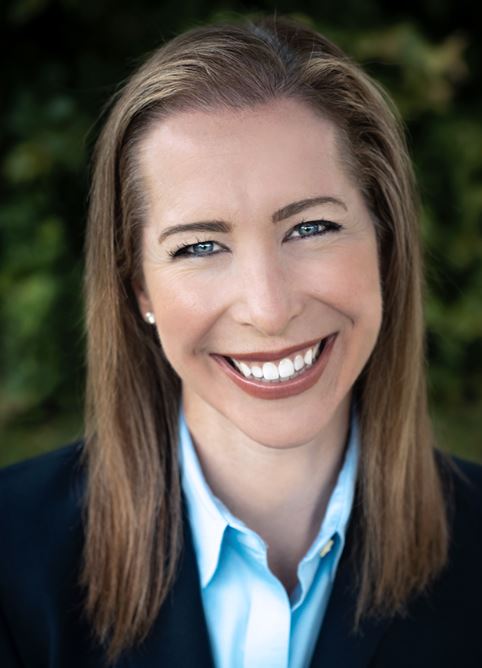
Award Recognizes Women providing positive impacts for their organizations & within the Orange County, California, Community Orange County Business Journal named Toshiba America Business Solutions‘ marketing leader Kerstin Woods a 2024 Woman in Business Award nominee. Award nominees were selected for accomplishing significant success within their respective organizations while benefiting the greater Orange County, California business community. Judges will additionally consider nominees’ contributions to the Orange County community in general, as well as their commitment to philanthropic causes. Sponsors at the Orange County Business Journal’s annual event will present the six awards at the 2024 Women in Business Awards Luncheon & Program on Oct. 30 at the Marriott Irvine in California. “This event is one of the premier contests in Orange County and which last year attracted an audience of about 800,” says Orange County Business Journal Editor-In-Chief Peter J. Brennan. “Toshiba America Business Solutions is one of the most prominent companies with headquarters in Orange County.” Toshiba & Orange County Difference Maker Woods has notched numerous accomplishments as Toshiba’s vice president of solutions and outbound marketing. Upon joining Toshiba in June 2019, she was tasked with acquainting herself to an entirely new industry while shortly thereafter successfully leading her organization’s marketing department through the pandemic. Woods has since led several profitable product launches, defining and adding new product categories for Toshiba, and launching Toshiba’s popular Elevate Sky® cloud platform, which enables organizations’ print productivity and digital automation across the Americas. Woods received the Stevie® Award for Female Executive of the Year for her marketing excellence at Toshiba. She is also an ENX Magazine Difference Maker, 2024 The Cannata Report Best Female Executive of the Year nominee, and leads the company’s AI Task Force. An advocate for diversity and women in business, Woods is the executive sponsor for engagement, diversity, and inclusion at Toshiba, where she mentors many company employees. She also hosts numerous industrywide women’s events annually. Woods also began Toshiba’s first-ever industry-wide giveback while raising more than $20,000 for Orangewood Foundation, a Southern California nonprofit helping foster youth transition into adulthood. Woods additionally serves on the Executive Committee within the Board of Directors for Ocean Institute, a Southern California nonprofit that provides firsthand STEM education to 13,000+ students annually. Moreover, she has a long history of serving in leadership roles within her two children’s local schools and is an enthusiastic advocate for school funding for sports, arts, and hands-on science. Beyond these good works, Woods conducts admissions interviews on behalf of Stanford University’s (her alma mater) Office of Undergraduate Admissions as a member of the university’s alumni ambassador program. “Kerstin is one of the most impressive and dynamic individuals I’ve had the opportunity to collaborate and work beside,” states Toshiba America Business Solutions President and Chief Executive Officer Larry White. “While her impact on our marketing efforts has been transformative, Kerstin also leads and is a mentor for our engagement, diversity, and inclusion program and is a powerful advocate for worthy causes in Orange County.”
Episode 524: Fullstride helps businesses pursue their first WMS
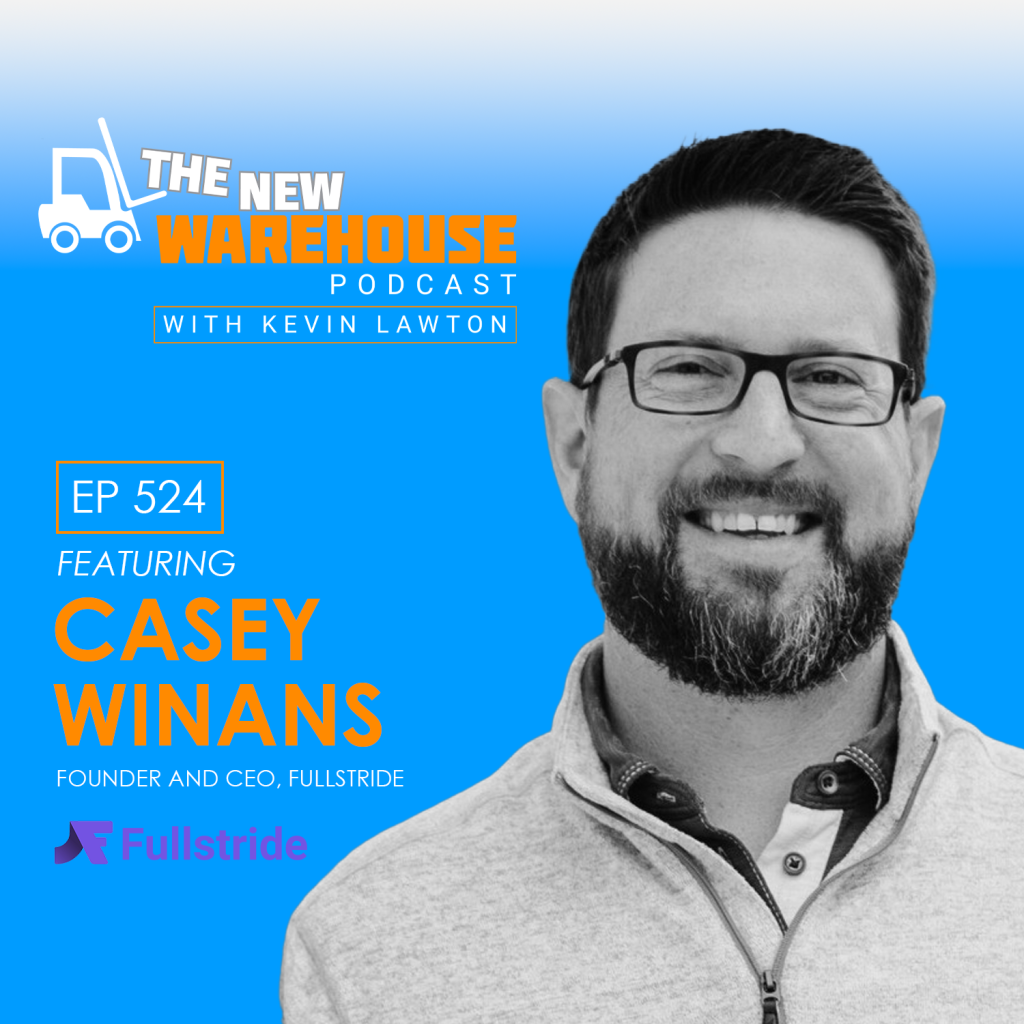
Today, The New Warehouse Podcast welcomes Casey Winans, founder and CEO of Fullstride, a seasoned expert in warehouse management systems (WMS). With over 20 years of experience in supply chain management, Casey brings a wealth of knowledge and a passion for optimizing warehouse operations. In this episode, he shares the story behind Fullstride, a company focused on helping mid-sized businesses navigate the complex world of pursuing their first WMS. We explore the challenges and opportunities in choosing the right WMS and the importance of preparation and process clarity before engaging with vendors. The Journey to Fullstride Casey’s career journey is a testament to the power of persistence and passion. Starting with a management information systems background, he inadvertently immersed himself in supply chain management. His experiences building a parcel manifesting system and working with 3PLs during his time at GE laid the foundation for Fullstride. The company was born out of a desire to do things differently—by focusing on smaller, growth-oriented businesses looking to implement their first WMS. The Importance of Clarity Before Implementation Fullstride’s approach to WMS implementation is rooted in the principle of “clarity first.” Before engaging with vendors, Casey emphasizes that businesses need well-defined processes. “When you start asking questions, it quickly becomes clear that assumptions about process clarity are often misplaced,” Casey explains. He emphasizes the importance of involving both leadership and frontline workers in the conversation. Fullstride helps bridge potential disconnects, ensuring that everyone understands the impact of their contributions. This preparation smoothens the transition and empowers teams to navigate the change more effectively. Navigating the WMS Landscape The current WMS landscape is vast, with numerous options ranging from established giants to innovative startups. Casey points out that while more prominent players have advantages, they often come with “baggage.” This baggage comes in the form of high maintenance costs and complex implementation processes. In contrast, newer vendors, particularly those adopting a SaaS model, offer more flexibility and are often better suited for mid-sized businesses. “The days of long, costly WMS upgrades are fading,” Casey notes, highlighting the shift towards more accessible cloud-based solutions to scale and maintain. However, he advises caution when considering startups, urging businesses to evaluate capitalization, execution ability, and long-term viability. Key Takeaways Preparation is Key: Before selecting a WMS, ensure that your business processes are well-defined and all stakeholders are aligned. Consider Flexibility: Newer, SaaS-based WMS solutions may offer greater flexibility and lower costs, especially for mid-sized businesses. Evaluate Vendors Carefully: Look beyond the technology; consider the vendor’s ability to execute and support your business in the long term. The New Warehouse Podcast Episode 524: Helping Businesses Pursue their First WMS