Toyota Material Handling’s King and Douglass honored with 2023 Women in Supply Chain Award
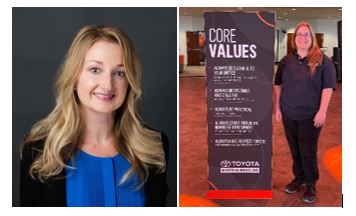
Lea Ann King, Kim Douglass recognized for their leadership and contributions to the industry Toyota Material Handling has announced Lea Ann King and Kim Douglass are recipients of the 2023 Women in Supply Chain Award. The award, given annually by Food Logistics and Supply & Demand Chain Executive, honors female supply chain leaders and executives whose accomplishments, mentorship and actions set a positive example for women at all levels of the supply chain network. “Lea Ann and Kim are exceptional leaders who are paving a path for women in the supply chain and material handling industries,” said Bill Finerty, Toyota Material Handling President & CEO. “These women embody Toyota’s founding principle to contribute positively to society and make the world a better place for all while encouraging others to do the same.” King, Toyota’s Vice President of Legal and General Counsel, is a dynamic leader who inspires others. King founded the Toyota Women’s Impact Network (T-WIN), the company’s women’s initiative that ensures Toyota has an inclusive culture and attracts diverse talent. She is a champion for women in all roles and creates mentorship and teaching opportunities for female professionals. King also showcases her commitment to the supply chain industry by serving on the board of the Industrial Truck Association (ITA), including her most recent position as chair of the ITA’s lawyer’s committee from 2016-2019. She continues to advocate for women in the legal field, regardless of the industry. Douglass, an Assembly Team Leader at Toyota, is a trailblazer and role model in the material handling and supply chain industry. Last year, Douglass became the first woman to medal in the Toyota Material Handling Group’s Global Skill Competition, earning the gold in the 2022 competition for Assembly. Since her historic win, Douglass has committed to advocating for other women within the organization. She represents Toyota’s commitment to encouraging more women to pursue careers in the material handling industry. She also serves as an ambassador for the Toyota Women’s Impact Network. Douglass advocates for women to receive the skills training, professional development, mentoring and coaching they need to have successful careers in the material handling manufacturing world. Food Logistics and Supply & Demand Chain Executive received over 400 submissions for this year’s award, which set the publication’s record for any of its award categories. Of that number, 118 were submitted by male counterparts, and 39 women were self-nominated.
Lauren Mollencupp named recipient of 2023 Women in Supply Chain Award

This award honors female supply chain leaders and executives whose accomplishments, mentorship and examples set a foundation for women in all levels of a company’s supply chain network TA Services, a premier full-service third-party logistics provider, has announced Lauren Mollencupp a winner of the 2023 Women in the Supply Chain award presented by Food Logistics, the only publication exclusively dedicated to covering the movement of product through the global cold food supply chain, and Supply & Demand Chain Executive, the only publication covering the entire global supply chain. Mollencupp is one of three TA Services female leaders to be honored this year. “This year, we received over 400 submissions, the highest amount of applications not only for this award, but also for all of our awards. This shows hope that one day, we won’t need an award like this because men and women in the supply chain will be equal,” says Marina Mayer, Editor-in-Chief of Food Logistics and Supply & Demand Chain Executive. “While there’s still more work to be done, what we’re doing is working. From truck drivers to CEOs, what these winners are doing matters to the future of all supply chains.” Mollencupp, who formerly served as site leader for TA Services’ largest warehouse site in Indiana with 250+ employees, was recently promoted to Implementation Manager. Because of her extensive warehouse supply chain knowledge, she now supports all of TA’s warehouse sites in her new role. A testament to her abilities as a leader in warehouse management and innovator in the industry. In her former role as site leader at TA Services’ largest warehouse facility, Lauren’s main objectives were to successfully lead the TA Services warehouse team and deliver a high level of service to her customers while maintaining TA’s position as a cost-effective provider. She also made it her top priority to ensure that employees, primarily warehouse workers, were recognized for their value at the full service 3PL. One way Lauren drove value and recognition, while also boosting morale in the warehouse, was by creating and implementing a point system program—the Extra Mile program—that rewards employees with points that can be redeemed for various prizes like apparel, company branded swag, and additional PTO days. Employees can even redeem points to have their manager dress up in funny costumes, making it an experience for all to enjoy. Lauren and her team have invested in being a family-inclusive environment and hosted an inaugural event in which all employees’ family members were encouraged to attend. This has been a very successful initiative and will now be an annual tradition going forward. This initiative is one of Mollencupp’s favorite achievements as the event brought a family atmosphere to the workplace and helped invest in employee engagement and retention. “Being a woman in the supply chain, especially warehousing, is currently a bit of an anomaly,” said Mollencupp. I hope to help other women excel and discover a passion for the logistics and warehousing industry. I truly believe in a people-first approach, and I have found this method not only creates loyalty from customers, but loyal employees as well.” “Women have been making a significant impact in supply chain management, contributing to the growth and innovation of the supply chain industry. As more women join the supply chain workforce, they bring diverse perspectives that can help address complex supply chain problems and improve global supply chain operations. It is important that we empower, recognize, and elevate these achievements through initiatives like the Women in Supply Chain Award, as seen through the overwhelming response. Congratulations to all the winners, those who nominated others and the bravery of those who nominated themselves,” adds Sarah Barnes-Humphrey, founder of Let’s Talk Supply Chain podcast and Blended Pledge project, both exclusive sponsors of the Women in Supply Chain award.
Episode 420: Intelligent Warehouse Automation with Exotec
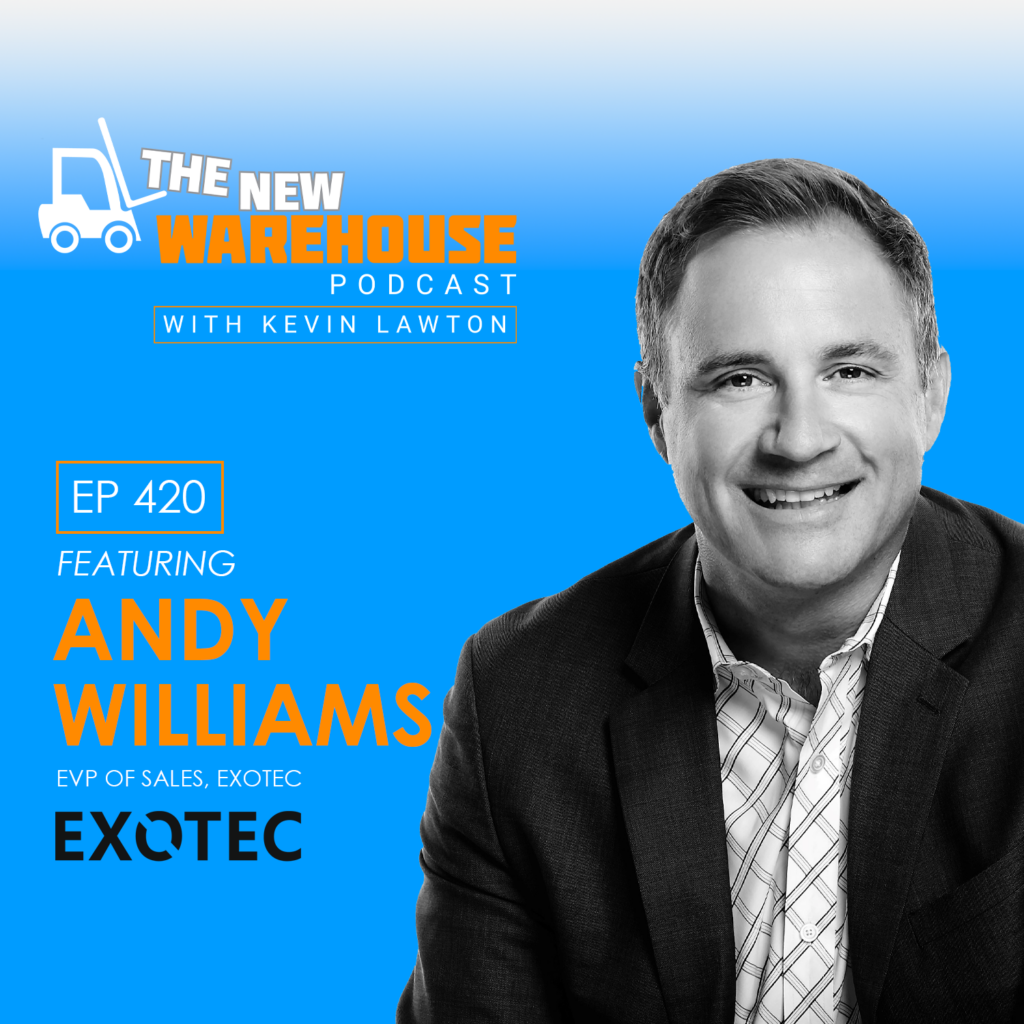
Today, on The New Warehouse Podcast, we welcome Andy Williams, Executive Vice President of Sales North America of Exotec, to discuss intelligent warehouse automation. Exotec specializes in innovative Automated Storage and Retrieval Systems (ASRS), leading the way in creating a more efficient, flexible, and responsive fulfillment system. If you’re keen on understanding the intricacies of intelligent warehouse automation and how it could redefine your operations, this episode is an essential listen. The Role of Robotics in Intelligent Warehouse Automation Andy Williams emphasized robotics’s pivotal role in shaping the future of warehouse automation. He noted, “It became evident that robotics was really the future of automation and warehousing. For many different reasons, but just robotics in general and warehousing is much more flexible; you can kind of build for capacity as you go.” This observation serves as a compass for companies contemplating investments in automation technologies, pointing to the flexibility that robotics inherently bring to the warehouse environment. From ASRS to AMR in Intelligent Warehouse Automation Delving into Exotec’s core technology, the Skypod, Andy Williams explained what sets their systems apart: “What makes Exotec different is purely from a technology standpoint, we have an incredibly dense system. But it’s really more so the flexibility of the design,” he said. The Skypod is unique in its ability to function as an Automated Storage and Retrieval System (ASRS) and quickly transition into an Autonomous Mobile Robot (AMR), showcasing its innovative approach to intelligent warehouse automation. The system’s dynamic capability allows it to complete a small e-commerce order with two or three order lines in less than five minutes, regardless of the system’s size. Driving Innovation in Intelligent Warehouse Automation The company’s culture has a direct influence on its innovative capabilities. Andy Williams shed light on this by stating, “First and foremost, the culture of Exotec is probably the number one reason I came. That group was able to create a set of really revolutionary technologies for warehousing automation.” Andy emphasizes that at Exotec, the company’s culture has enabled them to set new standards in intelligent warehouse automation. “One of the mantras inside Exotec is almost pass is fail. And I think that’s how the company established a really successful solution.” This phrase encapsulates the company’s ethos of striving for perfection, underlining the stringent standards that Exotec sets for its products and services. Key Takeaways Guaranteed Reliability – Exotec guarantees system reliability through intelligent warehouse automation features like no single point of failure, ensuring uninterrupted access to goods even if a robot encounters an issue. This makes it a reliable and efficient solution for goods-to-person picking across various industries. Simplifying the Complex – Exotec simplifies complex warehouse challenges by providing a fail-safe, highly reliable system. Intelligent warehouse automation enhances internal efficiencies and opens up transformative possibilities for the entire supply chain, from location flexibility to gaining a competitive edge. Space Efficiency and Supply Chain Innovation – Exotec systems allow for high throughput and dense storage, enabling warehouses to operate effectively in smaller footprints. This results in cost savings and provides the flexibility to position warehouses closer to manufacturing hubs or consumer bases, revolutionizing supply chain strategies. The New Warehouse Podcast EP 420: Intelligent Warehouse Automation with Exotec
United Rentals announces departure of Dale Asplund, EVP & Chief Operating Officer
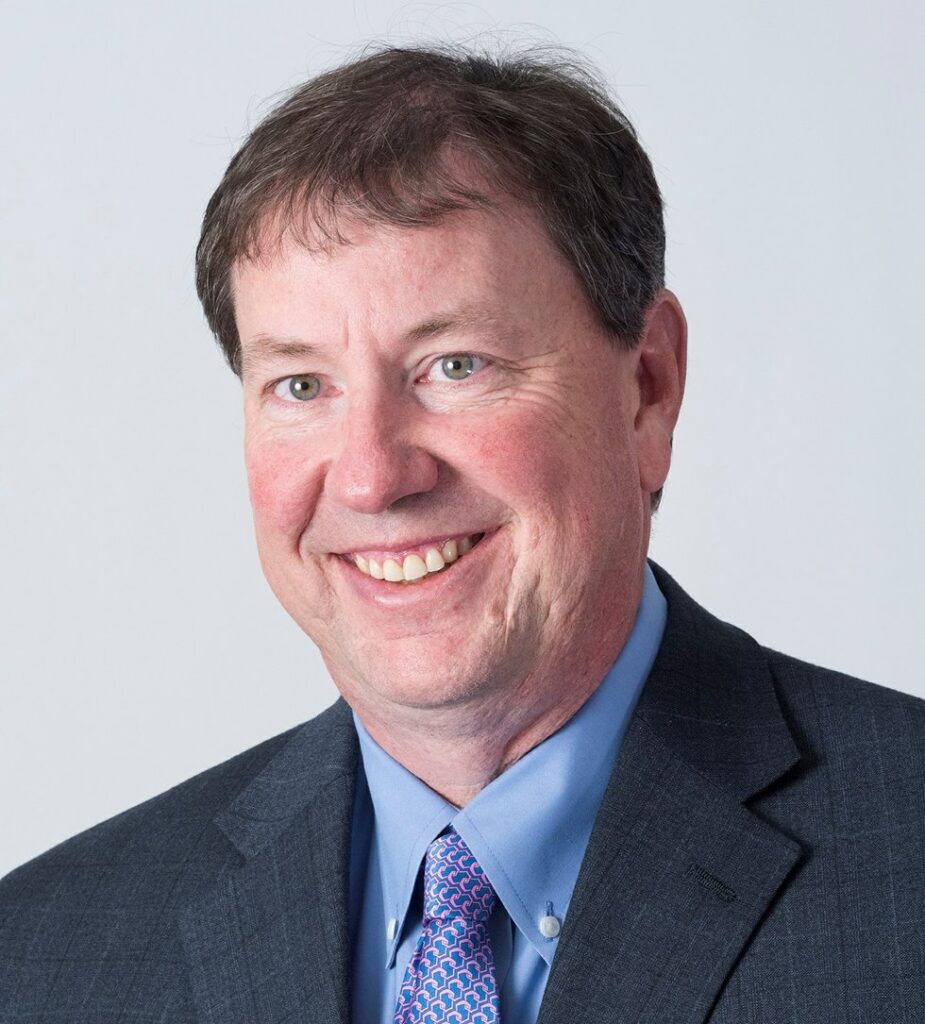
Michael Durand, SVP of Sales & Operations promoted to EVP & Chief Operating Officer United Rentals, Inc. has announced that Dale Asplund, executive vice president and chief operating officer, will be leaving the company on September 29, 2023, to take the role of president and chief executive officer at another public company outside of the equipment rental industry. Mr. Asplund joined United Rentals in 1998, and was named chief operating officer in 2019. He will remain in an active role with United Rentals through September 29 to ensure a smooth transition to Michael Durand, who is being promoted to chief operating officer. Mr. Durand joined United Rentals in 2002 as a branch manager and has held roles of increasing scope through the present day, including district manager, region vice president, and his current role of senior vice president of sales and operations. Mr. Durand has been an integral leader across all aspects of sales and operations at United Rentals, including the company’s go-to-market strategy, large acquisition integrations, operations strategy, and operational excellence. He has built strong and enduring relationships within United Rentals and its customer base over his more than two decade career, making him the ideal choice to follow Mr. Asplund as chief operating officer. Matthew Flannery, chief executive officer of United Rentals, said, “We expect this to be a seamless transition between two seasoned leaders who have worked closely together for many years. Mike is a proven leader whose numerous contributions have delivered strong results across the company. I’m confident that his operational expertise and demonstrated ability to lead our business will play a key role in our continued focus to drive profitable growth and generate shareholder value.” Flannery continued, “We deeply appreciate Dale’s truly extraordinary contributions to making United Rentals the company it is today. On a personal note, I want to thank Dale for his incredible partnership, leadership, and commitment to our employees and shareholders. We wish him the very best as he assumes a new career opportunity.”
TAWI announces new Mobile Lifting and Conveying solution for freight container unloading
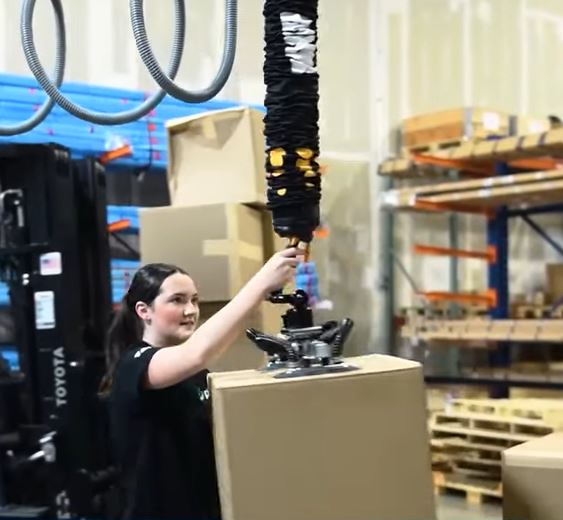
TAWI, the inventor of the vacuum lift (also known as a vacuum tube lifter) has launched a new, portable vacuum lifter designed to be used inside of any ocean freight or box truck to reduce manual lifting of materials during the unloading process. This solution enables a more flexible workforce by reducing the need to team lift heavy objects while also minimizing the opportunity of injury. This is a faster, safer, and easier material handling method when compared to individual or team lifting of materials by hand. Capable of lifting materials up to 110 lbs (50 kg), TAWI’s Container Unloader is comprised of a vacuum lifter integrated with an operator platform and conveyor. With its trigger style controller, the operator can lift and move product without exerting any lifting force and at a faster rate than performed manually. The Container Unloader features a patented jib arm for low overhead spaces which is capable of horizontally gripping packages or materials to remove them from the top of a container or box truck. The unit is free-standing, completely mobile, and powered by either 3-phase electrical or optional battery pack for cordless mobility. Operators can use the remote control to drive the unit as well as the controls on the control panel. This mobilization makes it so that operators can maneuver the Container Unloader in and out of docks and shipping containers as well as to move around your facility or to other facilities in your organization,. “Many businesses are seeing workforce issues in today’s complex economy. This can include locating, training, and retaining qualified material handling employees,” states Nick Hajewski, Global Marketing Director for TAWI. “A vacuum lift reduces this issue of locating human capital by reducing the number of material handlers needed to perform an existing task – especially when team lifting is required. It also opens these heavy lifting applications up to employees not physically capable of manual handling such weights, as the lift does the lifting for the operator – all the operator needs to be able to do is squeeze the control handle. So that’s the secret –less labor required, faster performance due to a lack of physical fatigue, and at the end of the day, everyone is safer because they are not physically lifting the materials themselves. In trials we are seeing a reduction of employees in container unloading operations by 25%, while cutting the time to unload containers in half. This doubles the capacity of existing loading docks and reduces the dependence on hard to find labor”
Lance Reed promoted to Cisco-Eagle Central Texas Director of Sales
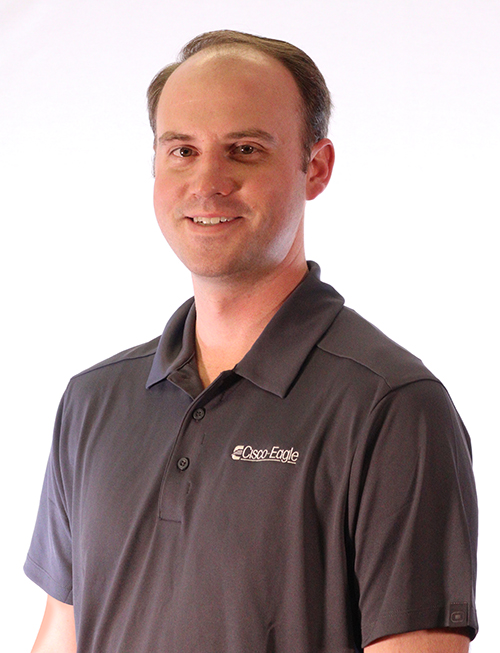
Effective September 1, 2023, Lance Reed has been named Central Texas Director of Sales for Cisco-Eagle, according to Vice-President of Sales James Murphy. Reed has been a successful account executive in the company’s San Antonio office, where he was responsible for significant growth, including multiple large clients in the distribution and manufacturing sector. Reed developed successful automation, storage and material handling systems for a large variety of clients in the area. In his new role, Reed is responsible for market and sales force development in Austin, San Antonio and other areas of the region. His role includes sales leadership and corporate strategy.
Cisco-Eagle promotes Greg Bates to Eastern Director of Sales
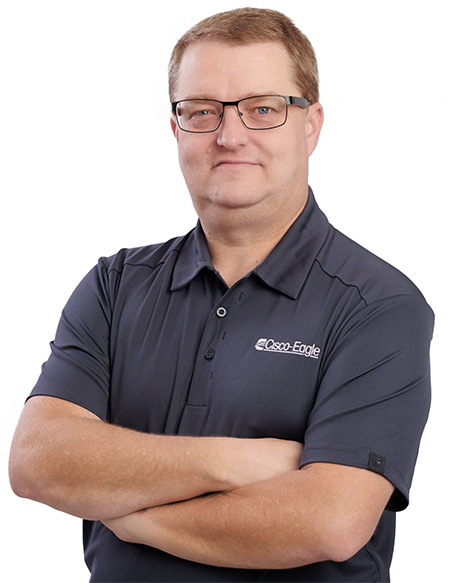
Effective September 1, 2023, Greg Bates has been named Cisco-Eagle East Central Director of Sales for the company’s Charlotte office according to Vice-President of Sales James Murphy. Previously, Bates has worked in the Carolinas market as a successful account executive, responsible for growth in the region. He founded the Charlotte office in 2021. In his role as sales director, Bates will develop a sales force to serve industrial customers of all types throughout the region. Bates has helped a growing customer base of warehousing, manufacturing and distribution companies operate better, faster, safer and more efficiently by assisting with material handling, automation, safety and storage projects.
Rockwell Automation and Infinitum announce agreement to make high-efficiency low voltage drives and motors
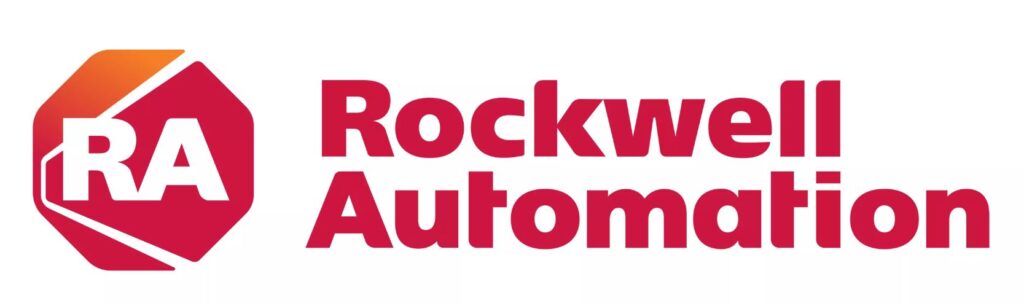
Partnership will deliver market-leading integrated drives and motors giving manufacturers the ability to deliver sustainable outcomes with less consumed energy, raw materials, and waste Rockwell Automation, Inc., the world’s largest company dedicated to industrial automation and digital transformation, and Infinitum, creator of the sustainable air core motor, has announced an exclusive agreement to jointly develop and distribute a new class of high-efficiency, integrated low voltage drive and motor technology. This solution will significantly save energy and cut costs for industrial customers globally, while helping them reduce their carbon footprint and become more sustainable. As companies grow more energy conscious and look to reduce greenhouse gas emissions, variable frequency drives (VFDs) with high-efficiency motors have increasingly come into focus. According to the International Energy Agency (IEA), electric motors consume approximately 40% of the electricity consumed globally, with the percentage rising to nearly 70% for industrial companies. Under this agreement, Rockwell’s market-leading PowerFlex® drive technology will be combined with Infinitum’s high-efficiency Aircore EC motor system. This powerful package will help companies reduce their carbon footprint with a motor system that is 50% smaller and lighter, uses 66% less copper, and consumes 10% less energy than traditional iron core motors. “We’ve long recognized the benefits of Infinitum’s integrated motor and drive system because of its class-leading energy efficiency, sustainability, and ease of operations,” said Barry Elliott, vice president and general manager of Power Control, Rockwell Automation. “We’re excited about the powerful impact that our new joint solution will have on improving sustainability, energy-efficiency, and productivity for our customers around the world.” Rockwell and Infinitum have collaborated since 2021, when Rockwell made an initial investment in Infinitum as part of the company’s Series C funding. “We’re excited to extend our successful partnership with Rockwell Automation. This agreement opens new customer channels for our sustainable motors that can power the world with less energy, material, and waste,” said Ben Schuler, founder and CEO, Infinitum. “Working with Rockwell will enable a direct and widespread impact on industrial companies, reducing electricity consumption and increasing sustainability for this energy-intensive sector.” The integrated VFD and motors will be available in late 2024 exclusively through Rockwell and its partners.
Will labor costs and consumer confidence crash the holiday hiring season?

As the 2023 holiday season kicks off, the labor market is starting to cool and employers are hiring at a slower clip. As labor costs and interest rates rise, seasonal employers may rein in their typical hiring sprees, as both consumers and employers feel the crunch, according to one workplace authority. “With inflation slowing, companies, particularly Retailers, won’t be able to pass increased labor costs to the consumer as easily. This could lead to more cuts, rather than more added positions, as evidenced by the increase in job cuts in this sector,” said Andrew Challenger, workplace and labor expert and Senior Vice President of global outplacement and executive and business coaching firm Challenger, Gray & Christmas, Inc. Retailers have announced 55,755 job cuts through August, according to the latest Challenger Report. This is up 524% from the 8,940 job cuts announced in the sector through August 2022. Due to the current environment, Challenger predicts Retailers will add 410,000 seasonal positions, the lowest number of jobs added in the final quarter since 2008, according to an analysis of non-seasonally adjusted data from the Bureau of Labor Statistics (BLS) by Challenger. The 2022 holiday hiring season saw Retailers add 509,300 jobs, revised down from 519,400, according to the BLS. That is down 27% from the 701,400 jobs added during the holiday season in 2021, and the lowest since Retailers added 495,800 seasonal positions in 2009. Retail employment has surpassed pre-pandemic levels, but is lower than 2018, when 15,713,500 people were employed in the sector in August. This year, Retail employment in August is 15,530,000, according to preliminary non-seasonally adjusted data from the BLS. Peak employment for the sector in August occurred in 2016, when 15,809,900 workers were employed. The highest employment in Retail recorded in a single month occurred in December 2016, when 16,338,300 workers were employed. Meanwhile, Transportation and Warehousing, which saw its highest employment on record last December with 7,049,500 has fewer workers this August than in the same month in 2022. In August, the BLS reported 6,556,200 workers, down 24,000 jobs from August 2022. So far this season, seasonal hiring announcements are slow to occur. US-based companies have announced just 38,000 seasonal hiring plans so far this year, according to Challenger tracking. By this point in 2022, employers had announced 258,201 seasonal hiring plans, up 36% from the 190,000 seasonal hiring plans announced by the same time in 2021 and down from 301,700 hiring plans companies announced at this point in 2020. 1-800-FLOWERS.COM will hire 8,000 workers for the 2023 holiday season, the same number as last year. Bed, Bath & Beyond plans to hire 30,000 for the holiday season. Kroger announced it would hire “thousands,” but did not specify a number. Job posting sites have ads for seasonal employment for companies such as Crate & Barrel, Macy’s and UPS, but no other employers have announced major hiring plans as they have in past years. Notably, UPS not announced seasonal hiring plans after negotiations with the union led to higher wages for current members and avoided a strike. The transportation company has announced 100,000 new hires for the holidays in each of the last three years. “Seasonal employers have a few issues to grapple with in the coming months. One is the cost of labor limiting desire to add workers. Another is whether consumers continue to spend at the same clip. Another is one that has been fairly constant since the pandemic: can they attract workers?” said Challenger. JOBS ADDED IN RETAIL TRADE October, November, December Oct Nov Dec TOTAL % Change 2005 122,300 392,700 196,600 711,600 0.20% 2006 150,600 427,300 169,000 746,900 5.00% 2007 87,900 465,400 167,600 720,900 -3.50% 2008 38,600 213,600 72,700 324,900 -54.90% 2009 45,100 317,100 133,600 495,800 52.60% 2010 149,800 339,200 158,600 647,600 30.60% 2011 134,200 390,600 154,500 679,300 4.90% 2012 138,700 485,400 99,600 723,700 6.50% 2013 159,600 443,100 184,100 786,800 8.70% 2014 182,800 412,200 154,100 749,100 -4.80% 2015 183,300 399,300 125,700 708,800 -5.38% 2016 149,400 359,400 132,200 641,000 -9.57% 2017 146,400 462,700 59,300 668,400 4.27% 2018 115,900 494,800 14,900 625,600 -6.40% 2019 160,900 431,900 79,500 672,300 7.47% 2020 239,200 356,800 140,300 736,300 9.52% 2021 224,400 348,600 128,400 701,400 -4.74% 2022 143,700 263,200 102,400 509,300 -27.39% Average* 142,933 389,072 126,283 658,317 *Since 2005 JOBS ADDED IN TRANSPORTATION & WAREHOUSING October, November, December Oct Nov Dec TOTAL % Change 2011 11,200 25,900 62,200 99,300 -2.93% 2012 14,000 28,300 103,900 146,200 47.20% 2013 11,300 57,500 96,300 165,100 12.39% 2014 39,100 56,800 135,800 231,700 40.34% 2015 13,900 70,600 144,000 228,500 -1.38% 2016 28,000 85,500 152,800 266,300 16.54% 2017 41,400 88,600 135,200 265,200 -0.41% 2018 52,900 111,200 95,400 259,500 -2.15% 2019 36,300 119,400 139,300 295,000 13.68% 2020 117,900 254,200 121,700 493,800 67.39% 2021 121,600 239,800 190,900 552,300 11.85% 2022 86,800 166,900 122,700 376,400 -31.84% AVERAGE* 47,867 108,725 125,017 281,608 *Since 2011 Source: Challenger, Gray & Christmas, Inc., with non-seasonally adjusted data provided by the U.S. Bureau of Labor Statistics
Felling Trailers names Capobianco as Northeastern Regional Sales Manager
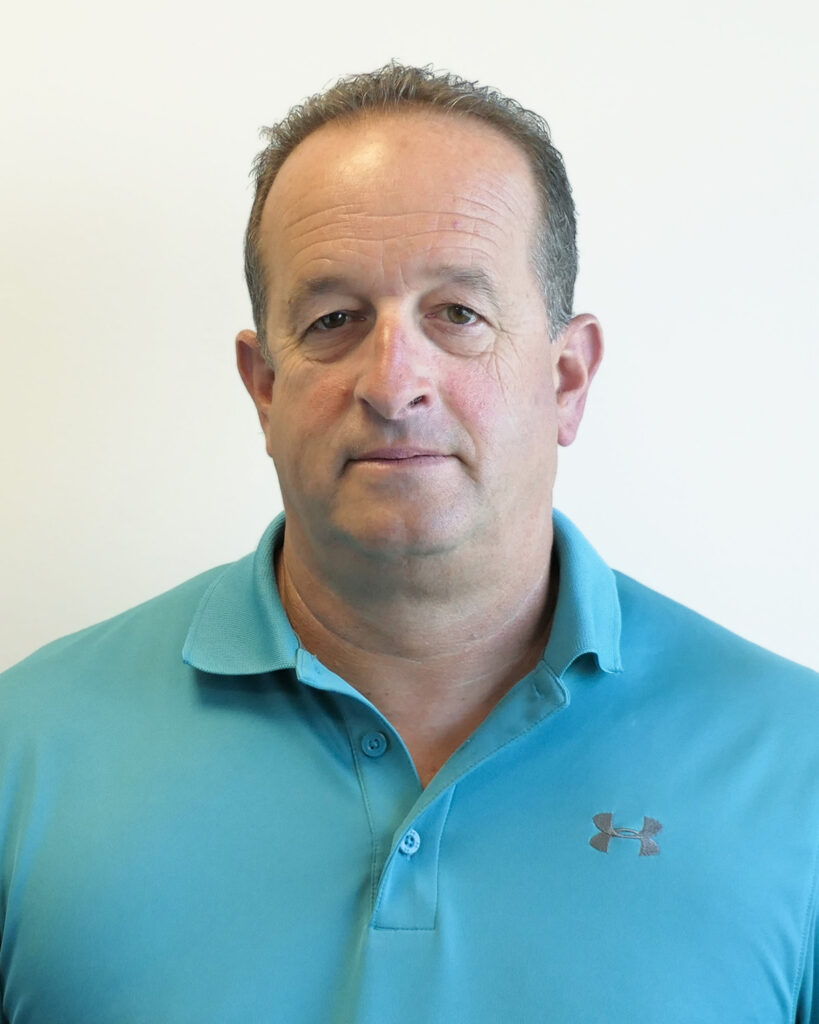
Felling Trailers Inc., a manufacturer of industrial and commercial trailers, has appointed Jim Capobinaco as their Northeastern Regional Sales Manager. In his new role, Jim will be responsible for all sales development, activity, and dealer support within Maine, New Hampshire, Vermont, New York, Rhode Island, Massachusetts, New Jersey, Maryland, Delaware, Connecticut, Pennsylvania, and Washington D.C. Jim will be taking over the Northeastern region once served by Mike Flynn, who retired in January of 2023 after 22 years with the company. Capobianco brings a wealth of knowledge with twenty-five years in the heavy equipment and aggregate industries. Before joining Felling Trailers, Jim Capobianco held several key positions, each contributing to his extensive knowledge and expertise. Most recently, Jim was a territory sales rep for C.N Wood Co., Inc.; it was here that he became familiar with the Felling Trailers’ quality product line. “I had sold a few of the Felling trailers while with C.N. Wood Co., as they were a Felling dealer. All the customers knew of the Felling quality, and the reviews were always good. It made sense to me that this should be the place to go if I was going to work in the trailer industry,” said Capobianco. Nathan Uphus, sales manager for Felling Trailers, believes Capobianco’s specialized experience in the heavy equipment and aggregate markets will be an asset when working with dealers/end-users to find the best trailer solution for their transport needs. “We at Felling Trailers consider ourselves trailer experts because of our real-world experience that many of our team members possess. Jim’s comprehensive knowledge of the heavy equipment and aggregate industries adds to our sales teams’ diverse knowledge base,” said Uphus. Jim expressed his enthusiasm for his new role: “I am honored to join the Felling Trailers family and contribute to the company’s continued success. Felling Trailers has a long-standing reputation for manufacturing top-quality trailers, and I am excited to help our customers find the perfect solutions for their hauling needs.” .
OZ Lifting chain hoists, trolleys lift floating docks
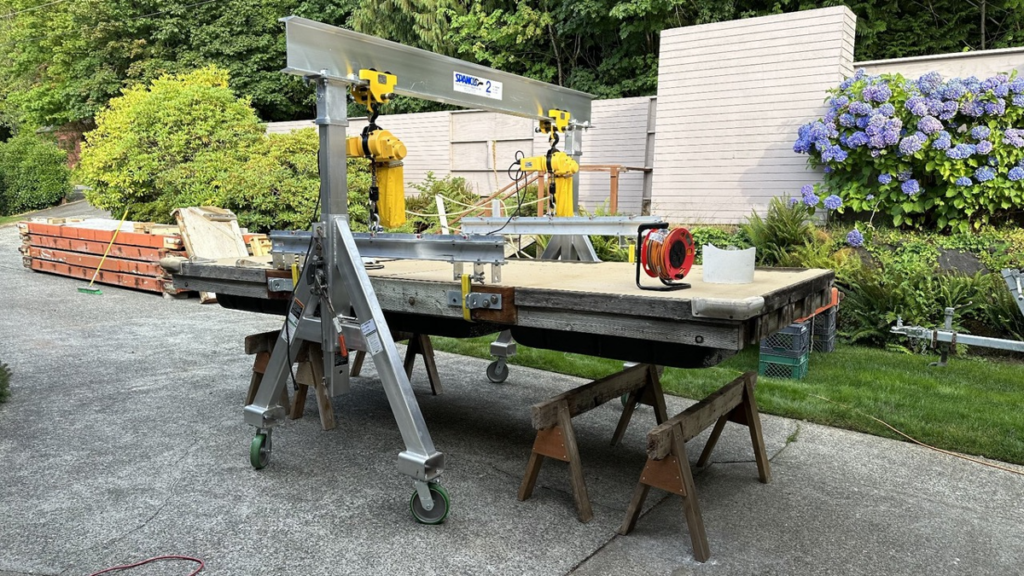
OZ Lifting Products LLC has provided two 1-ton capacity electric chain hoists and trolleys to lift floating docks, manufactured at a residential property. The Winona, Minnesota-based manufacturer provided the equipment via distributor Global Industrial, delivering it to the end user’s yard in Seattle, Washington. The hoists and trolleys were sourced along with a 2-ton capacity, adjustable aluminum gantry crane and lifting slings. The customer was looking for a method to lift, move and rotate 20 ft. by 8 ft. floating docks, which weigh between 600 lbs. and 1,600 lbs. He completed the material handling solution with a pair of aluminum lifting beams that he manufactured himself. He said: “The dock sections are too big and heavy to move, even with two people. Usually, I need six people to lift a single section and I don’t have that type of manpower readily available. The overall solution has proved to be very helpful; it is super easy to raise, lower and move my dock sections—and other heavy objects—around the property.” The hoists, operated by ergonomic pendant control, offer overload protection; a high-performance friction clutch is integrated with the load brake. Each hoist features a forged carbon steel load hook with a heavy-duty latch. The bottom hooks, meanwhile, feature a thrust bearing to allow 360-degree rotation to prevent twisting of the load chain; the top hook is rigid. The load sheave provides better distribution of the floating dock load, and smooth lifting with reduced vibration and wear, while the precision-machined gears are heat treated for strength and durability. Oil bath lubrication on all bearing rotating points presents the end user with quieter, smoother, and cooler operation, and 110v power (115/1/60) means the hoists can be used virtually anywhere. The trolleys boast lightweight robust construction, and fit most I-, S-, and W-beams. They are protected by baked enamel paint and feature precision ball bearing trolley wheels, anti-drop plate, and stainless steel identification tags. All OZ products are delivered with individual test certificate and serial number. The customer added: “I made the lifting beams from aluminum and included hooks for the lifting straps. I can use the gantry on wheels to move it around the property, but it can also transport the docks while under load. [The equipment] allows me to also upend and rotate the load.”
Mitsubishi Logisnext Americas Group launches new UniCarriers® Forklift SCX N2 Series of Electric Stand-Up Counterbalanced Lift Trucks
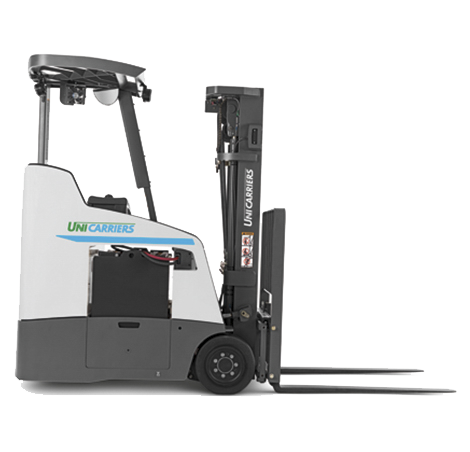
Mitsubishi Logisnext Americas, the exclusive manufacturer and provider of UniCarriers Forklifts across North, Central and South America, announced the launch of the new cutting-edge SCX N2 Series of Electric Stand-up Counterbalanced Lift Trucks. This addition further enhances the company’s comprehensive portfolio of warehouse products, offering customers an array of benefits that redefine efficiency and flexibility in material handling operations. The SCX N2 Series is distinct with its improved turning radius, reducing minimum aisle requirements and enabling more efficient maneuverability within crowded warehouse spaces. With simultaneous multi-function controls and user-friendly ON-OFF machine functionality, the SCX N2 Series ensures a seamless multitasking experience. It excels in operations requiring extensive product shuffling or frequent maneuvering in and out of trailers, making it a versatile and indispensable asset for business. Key benefits of the SCX N2 include: Industry-leading efficiency and runtimes – 16 hours on a single charge Quick acceleration, higher productivity and industry-leading lift and travel speeds Excellent all-round visibility Adjustable anti-fatigue floorboard with multiple weight adjustment settings for all operator sizes High stability during travel 1000-hr maintenance intervals 2-year unlimited hour warranty “The introduction of the SCX N2 Series represents a significant advancement in our commitment to delivering state-of-the-art material handling solutions to our dealers and customers,” said Niels Tolboom, Director of North AmericaDealer Sales for UniCarriers Forklift at Mitsubishi Logisnext Americas.“This series of Electric Stand-Up Counterbalanced Lift Trucks is a game-changer, offering unmatched efficiency and flexibility in warehouse operations.” The SCX N2 also features an impressive range of features and additional options: 3,000, 3,500 & 4,000 lbs. base capacity @ 24-inch load center 36V AC Electric system with 6th generation AC induction motors Max fork height of 276” Integrated diagnostic system 3 customizable performance modes Passive sway control and industry-exclusive “Intelligent Curve Control” Electronically adjustable padded armrest and backrest (4” travel) Additional option Telematics Lithium-Ion technology Lighting packages Freezer options Lower overhead guard Several in-cab accessories (USB ports, operator fan & mirror)
Metalcraft announces October succession for CEO Steve Doerfler
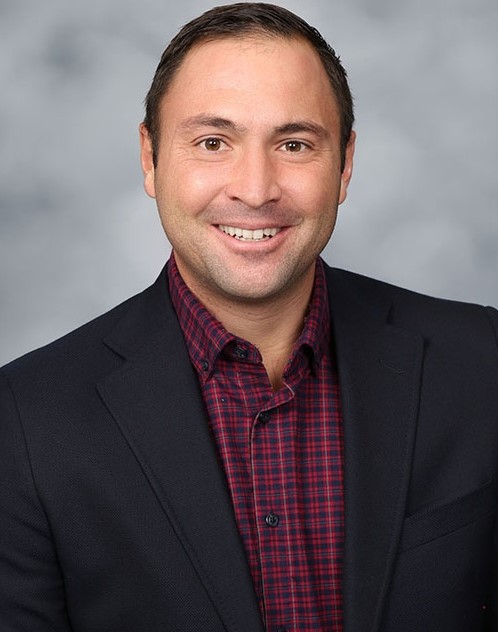
Kyle Bermel adds to role as Metalcraft president; global ID solutions company CEO to become board chairman Metalcraft announced a planned leadership transition reflecting the ongoing elevation of the employee-owned company’s dedicated team. Effective October 1, president Kyle Bermel will add Chief Executive Officer to his title, succeeding Steve Doerfler, who will become board chairman. This transition reflects Metalcraft’s commitment to a customer-centric team inspiring customers to unleash the power of their data with the most effective identification products. Doerfler joined Metalcraft in 1990 and served as CEO since 2012. His leadership championed a culture that prioritizes employee well-being, nurturing a thriving work environment that propelled the Iowa-based manufacturer to a global leadership position in identification products. As Chairman, Steve will continue guiding Metalcraft University, an initiative empowering member-owners’ personal development, cultivating leadership potential, and enhancing skill sets to ensure Metalcraft remains at the forefront of ID technology. “Steve Doerfler’s leadership is central in shaping Metalcraft’s identity and success,” said Bermel. “His transition to Chairman leverages his unparalleled experience to navigate the company’s future. Together with the entire Metalcraft team, we will continue to thrive on challenges to make the complex simple for our customers, showing a better way and delivering as promised.” Bermel brings a background in innovation and technology to his leadership responsibilities. He joined Metalcraft as an RFID engineer in 2012, becoming Metalcraft’s first Chief Operating Officer in 2019. Bermel led development of subsidiaries ARK Business Systems and Inlay Innovation, offering software and the Iowa-based design and manufacture of custom RFID inlays, respectively. “Metalcraft has a culture of employee-led innovation,” said Doerfler. “From our beginning, we’ve always been problem solvers, and our member-owners rally around change. I am confident that Kyle’s passionate leadership of innovative technology development demonstrates we have the experience and expertise company-wide to sustain the growth of our dedicated team.”
Big Joe boosts automation capabilities with new AMR features and key personnel
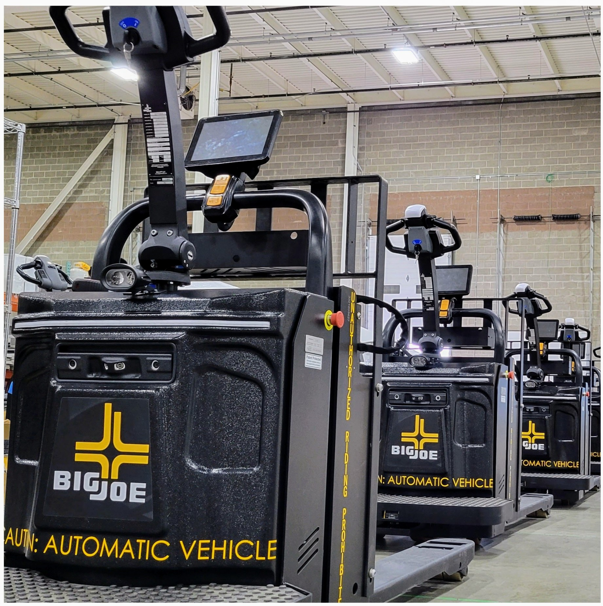
Big Joe Forklifts in partnership with Thoro.ai continues to rapidly advance the features on their flagship AMR and invest in key staff to help deliver easy to deploy automation for their customers. At Pack Expo, visitors could see and experience the latest Big Joe Pallet Mover AMR first-hand including several new features such as dynamic on-the-fly rerouting, onboard viewable maps and configurable zone rules to further enhance productivity, ease of operation and control for users. Additionally, Big Joe will be showcasing other unique vehicles in its standard lineup that are ideal for supporting packaging operations in manufacturing, warehousing or logistics environments. With the introduction of the Pallet Mover’s dynamic rerouting capability the unit can now autonomously navigate to a destination on an alternative path should an aisle or area of travel become blocked, improving productivity and reliable completion of user-directed tasks. With visual maps of an operating area now included on the Pallet Mover’s user interface, operators can now easily validate that they are sending the AMR to an intended location as a visual reference. Lastly but perhaps one of the most powerful updates on the Pallet Mover to be introduced at Pack Expo, is a host of configurable zone rules which users can employ within areas of operation. These zone rules instruct the Pallet Mover as to how a user wants it to behave in a specific location. Slower travel speed areas, continuous horn use areas, prohibited areas and areas intended for automated side-by-side pallet unload are but a few examples of the increased control provided with the new zone rules feature. In addition to advancements in its AMR, Big Joe is announcing that it has hired the Director of Strategic Partnerships for its Autonomous Division, Brendan Brett. Brett will be leveraging Big Joe’s core strengths of developing affordable, reliable, easy to use and deploy autonomous vehicles to foster additional collaborations within or aligned with the material handling industry. Brett’s vision is to evolve the company’s strategic autonomous roadmap ahead of market trends to sustain Big Joe’s competitive advantage throughout both its distribution and service network and those of partners. “The global pandemic accelerated the need and uptake of autonomous vehicles, paving the way for the material handling industry to become educated on how simple, yet effective solutions could be every day, not just to solve its pain points during a crisis,” said Brett. “I look forward to helping provide growth and development opportunities for our current fleet as well as adding additional options for our customers as we continue to focus on innovation and automation.” Brett studied Supply Chain Management and Information Systems at Penn State and has 15 years of Supply Chain Operations experience specifically in the food and beverage industry. He was globally recognized by Nestle’s High Performance Logistics Team for projects such as setting up a configurable WMS fully integrated with AGV-MS, semi-automated Pallet Mole® systems and YMS software. “Big Joe is committed to bringing smart simple automation solutions to market which by nature requires innovation and collaboration. We welcome Brendan and look forward to working together on helping others empower workers and eliminate the need for complicated systems integration,” said Big Joe’s Chief Marketing Officer, Bill Pedriana. The rest of the Big Joe lineup of demos in booth #N-10028 will include the PDSR Walkie Reach Truck which features power steering and flexible operational advantages in numerous material handling applications. The Big Joe CB30/CB35 Counterbalanced Walkie Stackers will illustrate a safe and productive alternative to traditional rider forklifts, and the iconic Big Joe J1 “Joey” Task Support Vehicle will be on hand to help attendees ponder how they might improve the performance of elevated work at their facilities.
LFP from Nano One’s commercial size reactors lead to fast-tracking customer samples
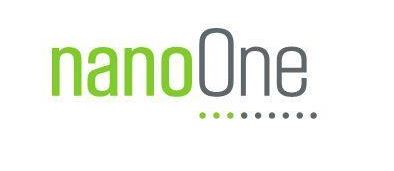
Commencing shipment of samples for partners to validate tonne scale LFP in Q4 Repeated One-Pot LFP trials demonstrates technology at commercial size reactors Accelerated retrofit of Candiac for continuous production of LFP 200 tpa reactors installed and optimization underway Building pipeline of potential customers for LFP product orders Nano One® Materials Corp is a clean technology company with patented processes for the production of lithium-ion battery cathode materials that enable secure and resilient supply chains by driving down cost, complexity, energy intensity, and environmental footprint. The Company is pleased to report that One-Pot trials over the past few months in the existing reactors at the Candiac plant have produced lithium iron phosphate (LFP) at commercial scale with performance results consistent to lab scale. Nano One has leapfrogged to full commercial size reactors and its LFP can be shipped to select customers in Q4 for evaluation. Additionally, the 200 tonne per annum (tpa) reactors have been installed and optimization is underway for scale-up. “We are ready to send qualified LFP materials to our partners for evaluation at tonne scale from our commercial scale reactors.” said Nano One’s Chief Commercialization Officer Mr. Denis Geoffroy, “These reactors performing are an important milestone in our commercialization strategy, to provide tonne scale samples to strategic partners and boost the confidence in our technology’s scalability. I am very proud of our team who achieved these results in a very short timeframe.” 2,000 tpa Commercial Reactors (existing): Nano One has continued to optimize trials in the existing commercial scale reactors, reproducing lab and development results. This demonstrates the One-Pot process can scale to commercial volumes and advances the de-risking of the technology at commercial scale. This rapid advancement allows commercial scale LFP samples to be sent to qualified customers, ahead of schedule, for thorough evaluation and validation for the purposes of entering binding offtake agreements for both the existing Candiac plant and the first full commercial line to be built next door. Optimization will continue and the results have helped identify key processing parameters and will expedite the commercial scale-up process. Successful repeatable LFP trials in the existing commercial scale reactors will lead to an accelerated refurbishment of the plant to automatize the use of the existing reactors for the One-Pot process. This will enable continuous production capabilities up to 2,000 tpa level toward the end of 2024. 200 tpa Pilot Reactors (new): In parallel, the team has continued to work on the reception, installation, and commissioning of the 200 tpa One-Pot reactors. These reactors will provide important information to improve the processes and support validation in a cost-effective manner as the Company continues to innovate. They also allow Nano One to have a baseline automated production capacity of 200 tpa, ready to deliver to customers once they have validated the product. “The experience of our team has been invaluable in achieving these important milestones.” said Alex Holmes, COO, “Working concurrently with both the 200 tpa reactors and existing commercial scale reactors has fast tracked our commercialization efforts. We are setting the foundation for growth that can secure market share and enhance shareholder value. This couldn’t have been achieved without the unwavering dedication of our team and showcases the amazing talent we have at Nano One.” “Being ahead of schedule and producing high-quality LFP cathode material is what we needed to fast-track Nano One’s progression to profitability.” said Andrew Muckstadt, VP Business Development, “While attending The Battery Show in Novi Michigan this week, we are able to talk to select customers about taking orders and potentially supplying them with LFP for their business plans in the future. As major players are still determining their supply chain and partners, we are demonstrating we have a viable product that can be produced in North America and replicated around the world.”
Plastics Industry Association launches Recycling is Real Advocacy Campaign
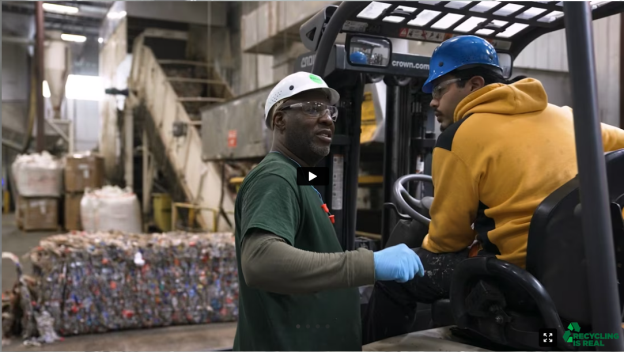
The Plastics Industry Association (PLASTICS) has launched a new advocacy campaign called Recycling is Real, dedicated to promoting and defending plastic recycling in America. The campaign will provide content to help elected officials and policymakers understand that recycling is a vital link of the sustainability and circularity chain, enabling them to make more well-informed decisions about recycling resources for their constituents. The campaign has also been created in an effort to put an end to false narratives claiming that recycling doesn’t happen or is a “myth.” Anti-recycling organizations and their allies have created a coordinated campaign against plastic recycling in an effort to advance their anti-plastics agenda and it is eroding faith in our nation’s ability to recycle. “Plastic recycling is very real, and it happens every single day across America,” said PLASTICS’ President and CEO Matt Seaholm. “The Recycling is Real campaign allows both the public and lawmakers to see for themselves the extraordinary role recycling plays in the circular economy, making it undeniable that recycling is not only effective but is a feasible and economical way to achieve our shared sustainability goals.” PLASTICS, on behalf of the entire plastics industry supply chain, is committed to sustainability and ensuring plastic material remains in our circular economy, and out of the environment. Recycling is an integral part of achieving this goal, and the industry knows America needs to recycle more. Recently, recycling has come under attack from those who wish to reduce or eliminate the production of plastic altogether. Recycling is Real will show how recycling happens, where it happens and introduce the people who make it happen. This initial launch will spotlight recycling efforts taking place at Ultra-Poly, Placon, Novolex and MAAG, with additional videos launching in the coming weeks and months. To view videos, click here.
SupplyOne streamlines and optimizes packaging operations for maximum productivity and savings
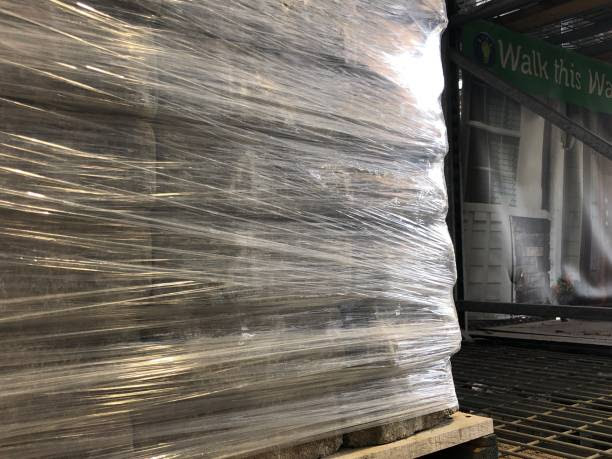
SupplyOne’s innovative end-of-line packaging equipment promises increased productivity, reduced labor costs, and improved consistency for manufacturers SupplyOne Inc. is highlighting its comprehensive state-of-the-art transit packaging automation solutions. Guided by a mission to give manufacturers more control over their packaging expenses, the company is set to redefine operational efficiency in the manufacturing industry with their packaging equipment solutions for the bundling, grouping, sealing and shipping of products to optimize transportation logistics and warehouse operations. End-of-line packaging simplifies handling and storage by consolidating larger quantities of products while keeping them stable and undamaged in transit. SupplyOne supports end-of-line packaging operations with the full gamut of automatic and semi-automatic case erecting and case sealing systems, strappers, banders, palletizing and wrapping equipment, as well as associated consumable including custom or stock corrugated, films, tapes, strapping, and other materials. In addition to enhanced product protection and security, this technology reduces the need for manual labor, thereby improving packaging consistency, reducing human error and labor costs and increasing productivity. “Our goal is to simplify and optimize our clients’ operations,” says Chip Reavley, SupplyOne’s SVP of Packaging Automation. “Our end-of-line packaging solutions not only streamline the packaging processes but also significantly improve efficiency and consistency of output.” SupplyOne builds packaging programs that streamline processes, guarantee savings, and increase efficiency while maximizing flexibility and scalability to meet challenges such as product mix variability, market demand fluctuation and labor shortages. SupplyOne packaging equipment specialists, packaging engineers and designers create custom solutions that are purpose-built to address each customer’s needs. SupplyOne offers comprehensive end-of-line packaging solutions from a range of recognized best-in-class manufacturers. Manufacturers who have already adopted SupplyOne’s end-of-line packaging solutions report impressive results. A recent case study reveals a 30% increase in productivity, reduction in labor costs, and a notable improvement in the consistency and quality of packaged goods. SupplyOne offers packaging demonstration facilities around the country to provide manufacturers, food processors, and e-commerce companies with live demonstrations of state-of-the-art primary, secondary, and end-of-the-line packaging machinery. Virtual demonstrations are also available. SupplyOne is a value-added packaging company committed to uncovering hidden costs within customers’ packaging expenses and reducing their total cost of packaging ownership. With access to the broadest range of packaging supplies and equipment available and suite of services that take cost, waste and complexity out of packaging management, SupplyOne helps manufacturer’s streamline operations, improve efficiency, and empower manufacturers to compete at the highest levels. For manufacturers looking to elevate their packaging operations and enhance their business, SupplyOne is the partner of choice. Discover how our packaging automation solutions can transform your manufacturing processes and drive success.
The A4 Glove for cut resistance and much more
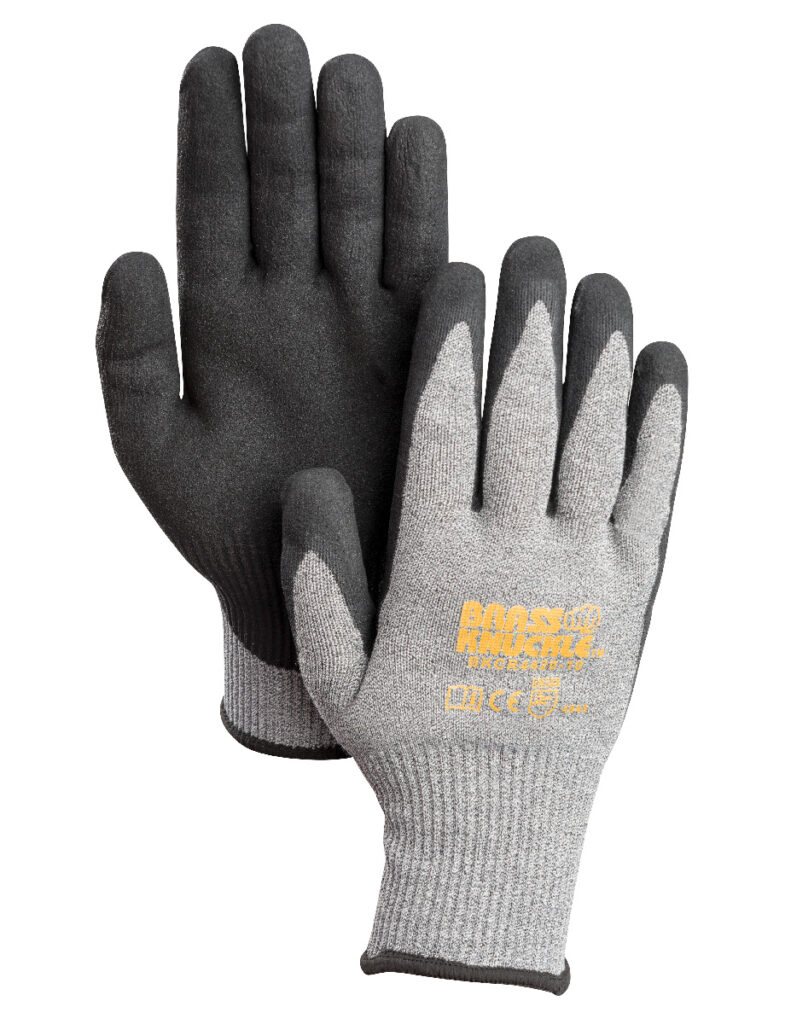
Brass Knuckle® SmartCut™ (BKCR4420) adds grip, moisture protection, and high dexterity Application specific cut standards remain the only way to specify cut-resistant protective gloves; however, A4 cut resistance has quickly become the de facto minimum standard for work gloves used in many applications. Foremen and plant managers alike trust its performance and feel confident putting their people in it when setting out for another hard day at work. Brass Knuckle® SmartCut™ (BKCR4420) offers this highly desirable A4 cut resistance PLUS a whole lot more, making it a value-added glove with plenty of upside. SmartCut starts with a high-density polyethylene (HDPE) knit shell to provide ANSI cut level A4 protection without bulk, with a strength-to-weight ratio 8 to 15 times higher than steel. But then SmartCut adds superior grip, moisture protection, and a high degree of dexterity. Come for the cut protection; stay for the comfort and grip. To achieve this winning combination, SmartCut has a water-based polyurethane (WBPU) coating as a palm and finger base coat. This helps reduce penetration of liquids, including light oil. Then it secures grip with a foam nitrile top coat, perfect for working with oils, petrochemicals, fuels, and most acids. Then, a sandy grip finish further enhances abrasion resistance and cut protection. It’s why SmartCut is the choice of so many industries, from metal work and stamping to automotive, oil and gas – and any application that needs a sturdy, hardy safety glove. It provides excellent medium-to-high cut resistance with layered protection that is the most breathable and flexible in its class.
Port of Long Beach sees cargo lull in August
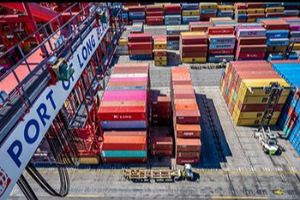
Overstocked warehouses, consumer spending shift contribute to decline The Port of Long Beach saw a modest start to the traditional “peak” shipping season as warehouses remained overstocked and consumers continued to pivot toward travel and other summertime activities. Dockworkers and terminal operators moved 682,312 twenty-foot equivalent units last month, a 15.4% decline from August 2022. Imports decreased 15.4% to 325,436 TEUs, while exports were down 23.1% to 93,402 TEUs. Empty containers moving through the Port declined 12.5% to 263,474 TEUs. “We anticipated a modest peak season as our cargo numbers continue to stabilize at pre-pandemic levels,” said Port of Long Beach CEO Mario Cordero. “Over the long term we are strengthening our competitiveness by investing in digital and physical infrastructure projects that will keep goods moving efficiently for decades to come.” “We are collaborating with our industry partners to grow market share while moving goods reliably and sustainably,” said Long Beach Harbor Commission President Bobby Olvera Jr. “We intend to close the year on a positive note that focuses on our efforts to improve cargo flow and secure our position as the premier gateway for trans-Pacific trade.” The Port has moved 4,993,237 TEUs during the first eight months of 2023, down 24.4% from the same period last year. Cargo flows this year have been on pace with pre-pandemic levels, when the Port of Long Beach moved more than 4.9 million TEUs through August 2019. For complete cargo numbers, visit polb.com/statistics.
Millwood’s CORE division adds co-packing location
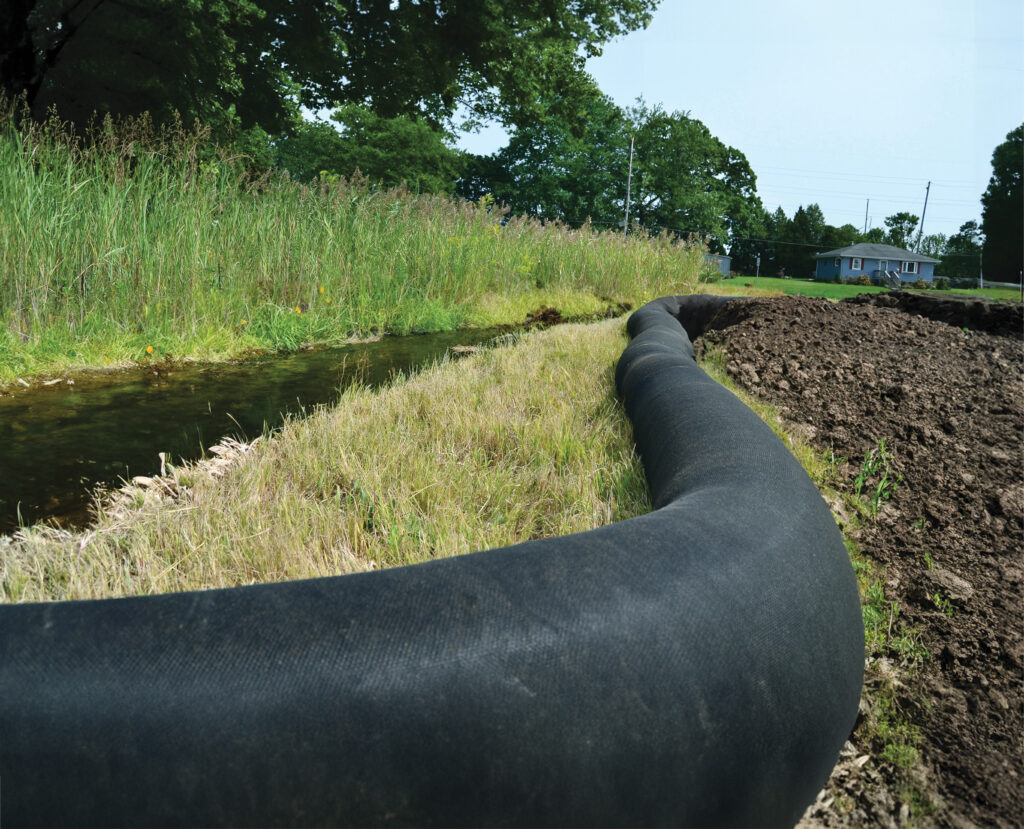
Millwood, Inc.’s CORE Erosion Control Services division has added a co-packing location in Bridgeville, DE. “We’re excited about partnering with the team at Pallet Masters to supply CORE filter socks to this area of the country,” Chris Verbosky, CORE regional operations manager, said. “The opportunity to bring them on is a true testament to teamwork within Millwood.” As a current and valued pallet supply partner for Millwood, Pallet Masters’ Bridgeville location fit the mold to act as a co-packing location for Millwood’s CORE filter socks in this region of the country, said CORE Sales Director Chris Sztenderowicz. “Not only was their operation designed to manufacture the filter sock, Pallet Masters is already a trusted supply partner for Millwood and their core values and quality of standardization align with Millwood,” Sztenderowicz said. The agreement reached allows both parties to work together to ensure success. Millwood supplies the equipment and filter sock mesh needed to manufacture the filter sock, and Pallet Masters supplies the labor and recycled wood chips from unusable pallets to manufacture and ship the CORE filter sock from their operation to various CORE customers in this region of the U.S. The wood chips used in these CORE filter socks went through various testing to ensure it meets all regulations. A Millwood team, also, traveled to Bridgeville to train the Pallet Masters team on the machinery and packing methods. “We made sure that their particle-size distribution met the criteria of the compost filter sock,” Sztenderowicz said. “After [Pallet Masters] installed new wooden screens into their grinder, we were able to get the medium at usable levels for the filter sock.” Customers and prospects in this region of the U.S. will now be able to take advantage of lower shipping costs with the addition of this co-packing location. “We have customers in this region of the country and nationwide, so we’re trying to keep adding more co-packing locations across the country to better service them,” Verbosky said. “One of our biggest pinch points is transportation, so developing relationships with co-packing locations across the country is vital to the success of our area of the business.” As this area of Millwood’s business continues to grow, so will the number of co-packers. Contracts with additional co-packing locations are already moving forward, Verbosky said. “With the resources that CORE can tap into from Millwood, we are able to stay ahead of some of our competitors and give assistance to our customers,” Verbosky said. “Our goal is to eventually be able to services customers across the continental U.S.”