Episode 417: Flexible Solutions for Warehousing, Fulfillment, and Distribution with Flexe
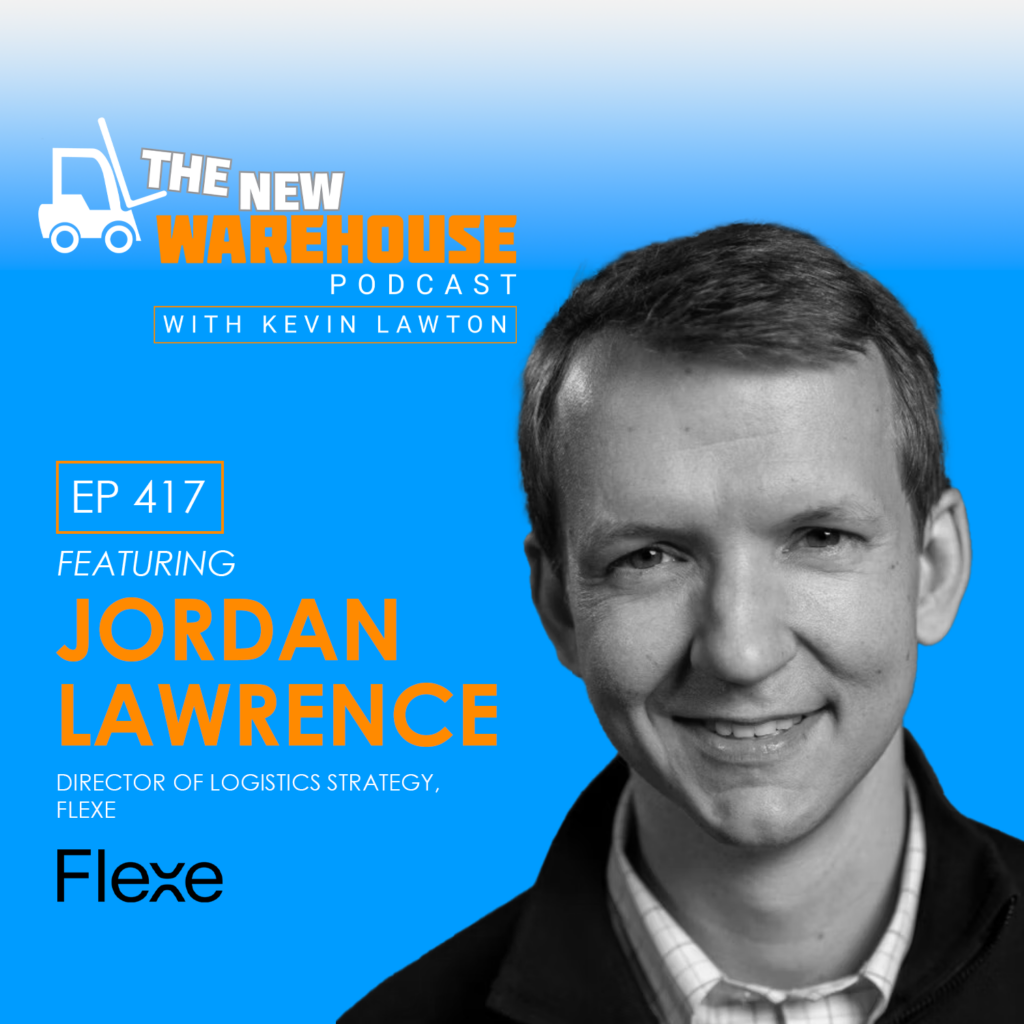
In a recent episode of the New Warehouse podcast, Kevin welcomed Jennifer Dasher, VP of Logistics, and Jordan Lawrence, Director of Logistics Strategy, both from Flexe. Flexe is dedicated to offering innovative solutions to warehousing and fulfillment challenges, bridging the gap between enterprise shippers and a vast network of warehouse operators. Tune in to discover how Flexe’s programmatic logistics is changing the warehousing game, bridging shippers and operators for scalable, flexible solutions. Programmatic Logistics: How Flexe is Transforming Warehousing Solutions Programmatic logistics, or flexible logistics programs, offer a third approach beyond traditional self-run facilities and third-party logistics (3PL) providers. Jordan Lawrence highlighted that the traditional options have fixed costs and scalability limitations. “What Flexe has done with flexible logistics programs is push the envelope on flexibility, get to the bleeding edge of where that cost structure can be, the ability to move up and down, the speed, and the location.” Flexe’s technology platform enables dynamic scalability, empowering enterprise shippers to find the ideal balance between fixed and flexible solutions. This approach allows businesses of all sizes to access warehousing resources tailored to their unique needs. Empowering Warehouse Operators for Success Flexe’s network comprises over a thousand warehouse operators, ranging from small regional players to larger providers. These operators benefit from the partnership with Flexe by filling unutilized space and leveraging their strengths while leaving the technological and customer relationship aspects to Flexe. This collaboration allows operators to focus on execution, enhancing their reputation and increasing business stability. Flexe’s user-friendly platform simplifies onboarding, training, and integration, enabling operators to connect supply and demand seamlessly and in a way that it could not connect previously. The Flexe Institute The Flexe Institute is a hub for data-driven insights and thought leadership in the supply chain domain. By collecting and analyzing data from the spot market in warehousing, Flexe provides valuable information to shippers and industry professionals, helping them make informed decisions. This transparency in pricing and labor trends supports businesses in navigating challenges and optimizing their supply chain strategies. The Flexe Institute showcases Flexe’s commitment to driving innovation and knowledge-sharing within the logistics community. Key Takeaways from the Podcast Flexe’s Innovation: Flexe’s technology platform introduces programmatic logistics, revolutionizing warehousing solutions by providing scalability, flexibility, and efficiency for enterprise shippers. Operator Empowerment: Flexe empowers warehouse operators by connecting them with brands needing additional capacity, helping operators optimize their resources and enhance their reputation. Data-Driven Insights: The Flexe Institute offers valuable data and thought leadership, shedding light on spot market trends and labor dynamics and enabling shippers to make informed supply chain decisions. EP 417: Flexible Solutions for Warehousing, Fulfillment, and Distribution with Flexe
Crowley honored with Corporate Diversity Award from Women’s International Shipping and Trading Association USA
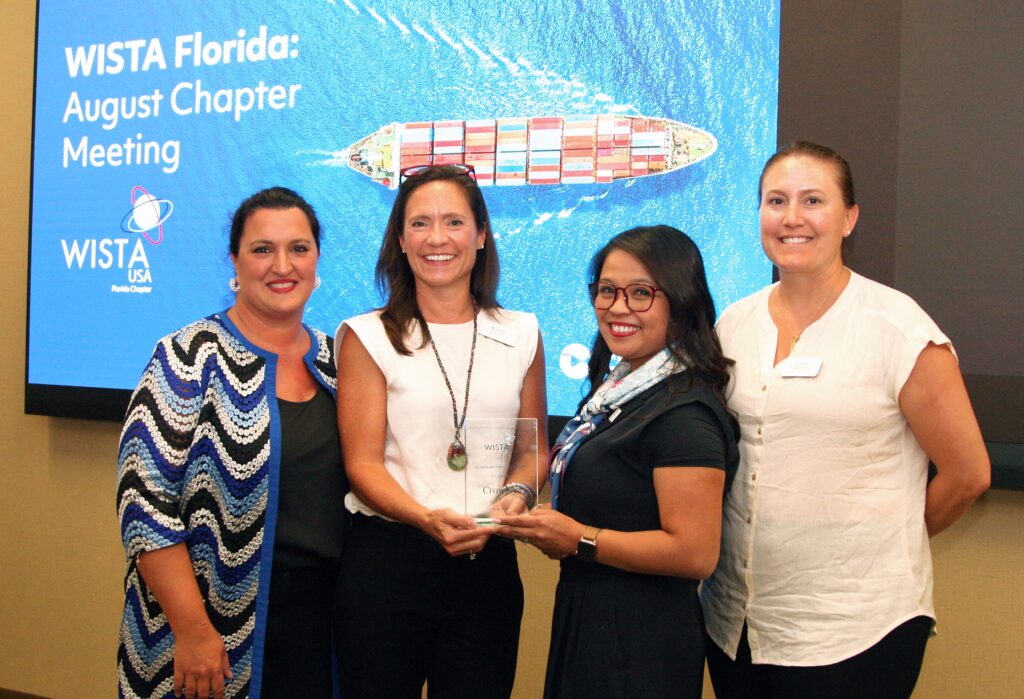
Crowley has been honored for its contributions to diversity and inclusion in the workplace with the Corporate Diversity Award by the Women’s International Shipping and Trading Association (WISTA) USA. Recognized for its efforts to enhance its corporate culture and empower its people through diversity and inclusion programs, Crowley supports its more than 7,000 employees through resources such as employee-led business resource groups, professional development programs, safety training and community engagement. “At Crowley, we value the unique perspectives, talents and ideas of our employees and believe they are what set our organization apart. We know that promoting an inclusive environment helps our people and our business succeed,” said Parker Harrison, Chief Legal and Risk Officer, Crowley. “We are so honored to be recognized for our diversity and inclusion efforts by an organization whose sole purpose is the advancement of women in our industries. We will continue our efforts to foster a workplace that our employees are proud of and feel empowered to drive change within the organization and our industry.” Crowley has taken several steps to promote diversity, equity and inclusion in the workplace: Established the Inclusion, Diversity and Equity in Action (IDEA) Council, led by employees, to create and lead initiatives to drive an inclusive and supportive environment for team members. The employee-led business resource groups support people’s careers and company business success by offering resources, education and a platform to provide Crowley with insights on where to improve. Achieved 37% female representation in the C-Suite leadership through appointments to key positions. Launched the Sexual Assault and Sexual Harassment Prevention Steering Committee to enhance safety measures for all mariners, leading to improvements in communication and technology aboard vessels. Revamped the cadet shipping program resulting in a significant increase in female cadet participation. Recognized as a Top Company for Women to Work For in Transportation by Redefining the Road, a magazine of the Women in Trucking Association annually since 2021. Crowley has also made diversity and inclusion a fundamental part of its overall sustainability commitment, including publicly disclosing and tracking key performance improvement goals in its annual Sustainability Report.
Flexible WMS the efficiency cure for ambitious 3PL
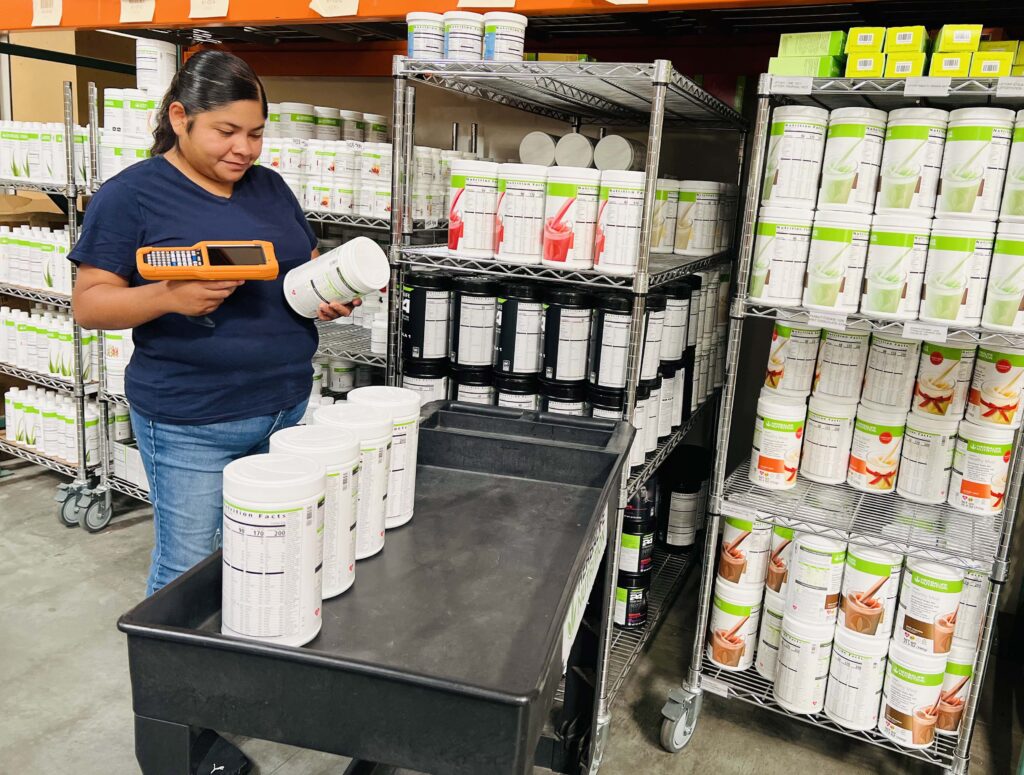
An up-and-coming US 3PL has invested in a cloud-based warehouse management system (WMS) to accelerate expansion and market share Michigan-based Cura Resource Group, which specializes in bespoke turnkey solutions for its dynamic and diverse range of clients, has implemented the award-winning, cloud-based SnapFulfil suite because of its inherent configurability, depth of functionality and multi-site capabilities. Cura successfully went live at their 10,000 sq.ft DC in Riverside, California, recently, after a rapid implementation period – and are quickly enjoying complete inventory visibility, optimized batch consignment and highly accurate image capture. Technologically advanced SnapFulfil replaces an order management system (OMS) that brought constant downtime, a lack of support and inability to adapt to Cura’s fast-paced work environment. Steve Brillati, CEO at Cura Resource Group, said: “The key advantage of choosing SnapFulfil was the immense support and backing we received from their team and the facility to adapt our many procedures into the functionality of the system. “Investing in a highly flexible and scalable WMS like this will optimize our fulfillment processes for much greater efficiency and enhance our labor productivity, as well as providing valuable insight into our operation and supporting us in gaining and retaining clients. SnapFulfil WMS integrates well with our new CIVA e-commerce platform too, which our clients are equally impressed by,” Brillati added. SnapFulfil Project Manager, Charles Thompson, added: “The Cura team were very receptive and we were able to walk them through all the WMS permeations and practice weeks before go live – and this continued into post support because of the increased volumes they were getting out the door. “They can now bulk upload and see their SKU numbers and variations anytime and anywhere, while the automated pick/track/label functionality is a major shortcut in their fulfillment processes.” Cura Resource Group was created to meet the last-mile distribution and warehousing needs of any business that wants a physical presence near where inventory is used, but doesn’t have the time, financial resources, or skills to develop and manage real estate on their own. As business ramps up, the next step is to take advantage of SnapFulfil’s multi-site capabilities and seamlessly implement the WMS into their five other facilities across the US.
Hangcha Forklift Canada strengthens national presence with Mississauga warehouse
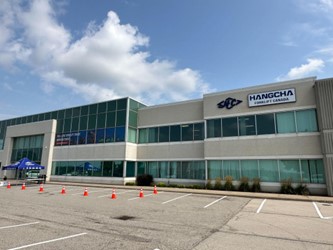
Material handling equipment supplier shows its commitment to the Canadian market with Mississauga grand opening Hangcha Forklift Canada, a provider of material handling equipment, announces the grand opening of its Mississauga warehouse on October 3, 2023. The spacious 30,000 sq ft facility is poised to make a substantial impact in Ontario and extend the Company’s reach throughout Canada. As a wholly owned subsidiary of the esteemed Hangcha Group, Hangcha Canada is uniquely positioned to offer a comprehensive range of material handling solutions tailored to meet the diverse needs of the Canadian market. Strategically located in Mississauga, the warehouse underscores the company’s long-term vision of rapid delivery capabilities to ensure reduced downtime for businesses. The new addition complements the existing warehouses in Vaudreuil-Dorion and Vancouver, allowing the Company to maintain an inventory of 550 units at any given time. “Selling Hangcha Canada material handling equipment allows our staff to offer the Ontario market a full line of high-quality and well-priced Electric and Internal Combustion Forklifts and Reach Trucks,” says Chris DiBerto, Sales Manager at Ri-Go Lift Truck Ltd. “Hangcha Canada offers a broader product range than most Original Equipment Manufacturers (‘OEM’) with stock at three distribution centers in Canada, making it easier than ever for our team to demo and receive quick delivery on equipment.” “With product support, parts support, and technical training that is second to none, the Mississauga warehouse is increasing our ability to support and grow Hangcha Canada’s footprint in Ontario. This is a positive move forward,” says Randy Thistel, Hangcha Canada’s Ontario Sales Representative. The much-anticipated grand opening will be hosted by Hangcha Canada at 3500 Laird Rd #1, Mississauga, ON L5L 5Y4 and welcomes dealers, customers, industry professionals, local businesses, and media representatives. The evening will kick off with a ribbon-cutting ceremony at 4:00 p.m., marking the official inauguration of the Mississauga warehouse. Following the ceremony, a networking session is scheduled from 5:00 to 7:00 p.m. where attendees can enjoy appetizers and refreshments. “Hangcha Canada’s expansion plan signifies our dedication to Canada’s material handling industry. In January 2024, we will be expanding our headquarters in Quebec to include a state-of-the-art, on-site Training Centre and a Parts Department, allowing us to keep up with Canada’s ever-growing demand for our electric [lithium-ion] product line,” adds Robert Pitzul, Vice President of Sales at Hangcha Canada. Combining global expertise with an in-depth understanding of the Canadian market, Hangcha Canada’s customers can experience premium performance and reliability without compromising their budgets, making its products an attractive investment for businesses of all sizes.
FORT Robotics Endpoint Controller for wireless safety and control of machines and robots receives SIL 3 Certification
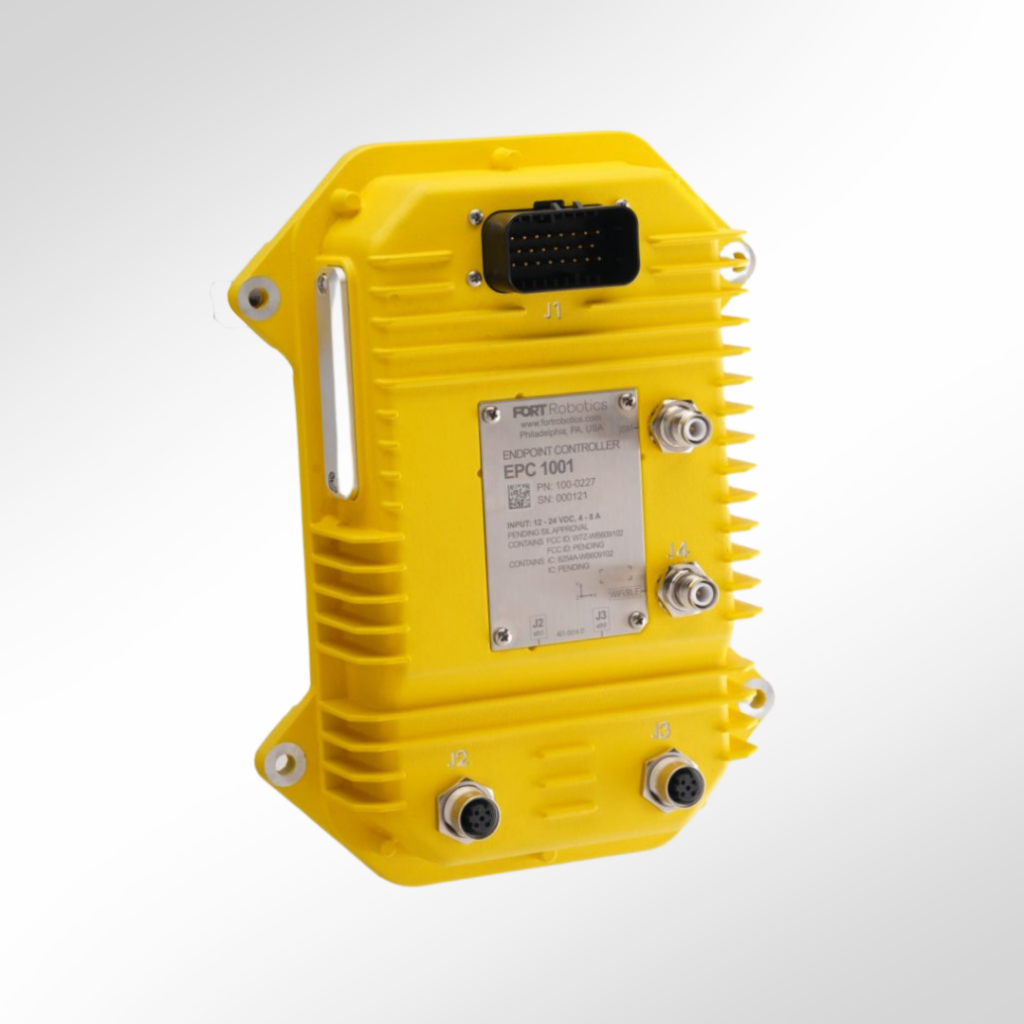
FORT Robotics announced that its Endpoint Controller — which brings safe, secure, dynamic wireless control to mobile, automated, or autonomous machines — has received SIL 3 (safety integrity level 3) functional safety certification, as defined by IEC 61508, from exida. The controller, which is part of the FORT Robotics Control Platform, can send and receive two different SIL 3 safety commands over Wi-Fi or Ethernet and can communicate with up to 30 machines simultaneously. This makes it possible to command and manage machines on- or off-site, delivering scalable, efficient control while protecting people and assets. “In warehousing, manufacturing, heavy equipment, or really any machine environment, there is an increasing need for people and robots to work together,” said Nivedita Ojha, VP of product at FORT. “Our goal is to make that collaboration as productive as possible with minimal risk. With the Endpoint Controller, companies can enhance operational efficiency by commanding multiple machines at once to e-stop, pause, crawl, respond to a fire alarm, and more.” Scalable, Fleet-Wide Robot and Machine Control FORT’s Endpoint Controller functions as both a transmitter and a receiver of SIL 3 safety commands. Deploying an SIL 3–certified product helps users comply with safety regulations and ensures that potential risks have been assessed and mitigated. While in the past, this level of reliability was limited to wired hardware, the evolving automation landscape requires the ability to send functionally safe commands over any network, including wireless communication. FORT’s product is one of only a few certified wireless solutions on the market. “As mobile and autonomous machines become common drivers of productivity, companies must have a reliable means to send safety commands over wireless networks to ensure employees can monitor, respond, or stop machines from a distance if an unsafe scenario emerges,” said FORT CTO Nathan Bivans. “Certification from one of the world’s most trusted safety experts in exida means the device will work as intended, when intended, reducing the risk of harm to people or damage to the equipment.” The Endpoint Controller can be mounted on a machine or integrated with third-party input devices, such as buttons, safety interlocks, light curtains, or fire alarms, allowing users to trigger automatic wireless communications with a fleet of machines or robots. Additional features include a tamper-proof design, an IP65-rated enclosure, and secure firmware to protect against cybersecurity threats. Like other FORT devices in the FORT Robotics Control Platform, the Endpoint Controller is built from the ground up to keep people, assets, and data safe and secure. The controller can be securely configured and managed using the FORT Manager cloud platform, available via a no-code application or through API access for direct integration with an existing system.
Lyko chooses Vanderlande’s FASTPICK to support expansion plans
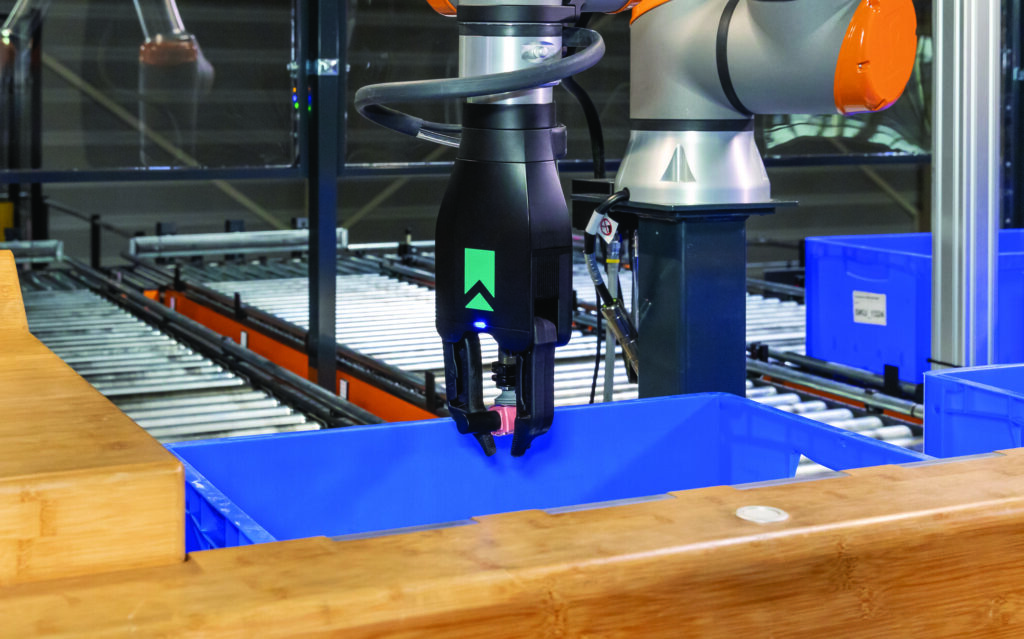
Swedish hair and beauty specialist Lyko has chosen Vanderlande to automate its new warehouse in Vansbro, Sweden. The two companies signed a contract for the installation of Vanderlande’s FASTPICK goods-to-person (GtP) order fulfilment system, including robotic item picking. Lyko needs a new solution to cope with rapid growth and to meet its ambition to break into emerging European markets. Vanderlande’s FASTPICK was selected because it meets the company’s need for greater efficiency and capacity, and can be installed on a limited footprint. The greenfield warehouse is scheduled to open in 2025 and will be Lyko’s largest automation project so far. The scalability and flexibility of Vanderlande’s solution provide the opportunity for further extension. The system includes the ADAPTO automated storage and retrieval system (AS/RS): 216 ADAPTO shuttles will be able to access more than 152,000 product locations across 27 levels and 40 aisles. The innovative system will be capable of handling 45,000 orders every day. The contract also includes 15 GtP workstations, three of which are equipped with robot item pickers from Vanderlande’s portfolio of Smart Item Robotics. In addition, all the manual workstations, including those for decanting, are height adjustable to minimise lifting duties for operators. The system also includes Vanderlande’s POSISORTER shipping sorter. The state-of-the-art solution is driven by Vanderlande’s digital suite of software services. During the entire process, the system handles items as gently as possible, which makes it an ideal solution for Lyko, with its stock of fragile and expensive products, such as bottles of perfume. “This solution gives us the capabilities we need to scale our business in a cost-efficient way – it will therefore support our plans for growth and help us expand into Europe,” says Rickard Lyko, Lyko’s CEO and founder. “By increasing our capacity and providing us with the efficiency we need through integrated robot technology, Vanderlande has shown that it best understands our needs.” “We listened closely to what the Lyko project team needed, and we’re delighted that they chose our state-of-the-art technology to help realise their expansion plans,” says Vanderlande’s Executive Managing Director Warehouse Solutions, James Cotton. “The FASTPICK solution offers the company the flexibility and sophistication it requires to handle an extensive range of products and deliver orders to customers as quickly as possible. We look forward to the installation and forging a long-term partnership with this dynamic company.”
August 2023 Logistics Manager’s Index Report®
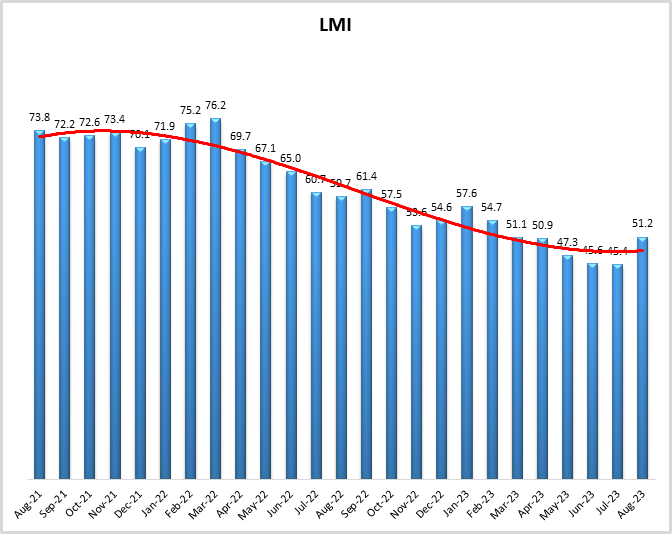
Growth is INCREASING AT AN INCREASING RATE for: Inventory Costs, Warehousing Utilization, and Warehousing Prices Growth is INCREASING AT AN DECREASING RATE for: Warehousing Capacity and Transportation Capacity Transportation Utilization is NEITHER INCREASING NOR DECREASING Inventory Levels and Transportation Prices ARE DECREASING In August the Logistics Manager’s Index read in at 51.2. This is a marked change for the index as before August’s reading the overall index had registered three consecutive months of contraction and five consecutive months of registering new all-time low scores. In contrast, this is the fastest rate of expansion since February. The expansion this month is driven by increased activity across all eight sub-metrics of the index. Inventory Levels are still contracting, but at a much slower rate (+6.0) than July’s reading of 41.9, which was the steepest rate of contraction in the history of the index. This has led to an increase in Inventory Costs (+8.6 to 69.1) and Warehousing Prices (+2.8 to 63.4). We also observe Transportation Utilization moving out of contraction (+8.2 to 50.0) and the rate of Transportation Price contraction slowing considerably (+7.3 to 42.9). It is not yet clear whether this move back towards expansion is a one-off deviation from the contraction we had been seeing or represents a pivot back towards expansion remains to be seen. However, it does appear that the increase in activity we observed in the second half of July has spilled over into August. When taken together with other anecdotal evidence and metrics that will be discussed below, it seems that a move back towards continued expansion is quite possible. Researchers at Arizona State University, Colorado State University, Florida Atlantic University, Rutgers University, and the University of Nevada, Reno, and in conjunction with the Council of Supply Chain Management Professionals (CSCMP) issued this report today. Results Overview The LMI score is a combination of eight unique components that make up the logistics industry, including: inventory levels and costs, warehousing capacity, utilization, and prices, and transportation capacity, utilization, and prices. The LMI is calculated using a diffusion index, in which any reading above 50.0 indicates that logistics is expanding; a reading below 50.0 is indicative of a shrinking logistics industry. The latest results of the LMI summarize the responses of supply chain professionals collected in August 2023. The move back towards a positive overall logistics index was accompanied by other positive economic news in August – particularly in the U.S. For instance, average hourly earnings were up 4.3% year-over-year in August (compared to an increase of 3.2% in the consumer price index over the same period). This is a 0.2% increase from July, giving suggesting that the economy is slowing to a level closer to what the Federal Reserve is looking for[1]. Conversely, the Personal Consumption Expenditures (PCE) index was up 3.3% in July year over year. This is up from the 3% growth rate we saw in June – although it should also be pointed out it is down significantly from the 7% growth we saw a year ago. Core inflation was also up slightly from 4.1% year-over-year in June to 4.2% in July[2]. In addition to the earnings increases, the U.S. added 187,000 jobs in August. This brings the average jobs added over the last three months to 150,000 per month, increasing the chances that the Fed will hold interest rates steady at their September meeting. Despite the overall increase, both warehousing and transportation employers cut jobs in August; although in the case of the latter a large part of that was due to the closure of Yellow[3]. Yellow’s impact was significant. The 36,700 employees that dropped out of the transportation industry marks the largest loss of transportation jobs since the start of lockdowns in April of 2020. Overall, transportation jobs are down 43,800 from their peak of 1.61 million in January[4]. This contrast between the overall market and transportation epitomizes what we have been seeing over the 18 months, during which we have had a freight recession but economic growth otherwise. Ironically, the lost jobs look to be leading to a rebalancing of supply and demand in the freight market, as capacity comes back in line with freight demand, we will continue to see transportation prices come back up. It will be interesting to observe what an increase in logistics prices does to the economy. According to the San Francisco Fed, decreasing supply costs have contributed to slowing inflation in three of the most recent five months[5]. The progress the U.S. has made economically particularly stands out when compared to the situation around the world. Eurozone prices were up 5.3% year over year in August. This is below the peak reached last October, but still well above the levels officials are looking for. While tourism and services have come back in some parts of Europe, manufacturing in places like Germany remains depressed due to the lack of demand for goods[6]. China is of course facing a whole raft of economic issues, including low exports and personal consumption[7]. This progress has led to a positive outlook from both consumers and analysts. The University of Michigan Index of Consumer Sentiment “moved sideways” in August, going from a 71.6 in July to 69.5 in August. This is still the second highest reading in nearly two years and is up 39% from the all-time low consumer sentiment observed in July 2022[8]. Although it should be noted that consumer sentiment could shift with the resumption of student loan repayments in October, with loan beginning to accrue again in September[9]. Additionally, S&P Global Market Intelligence estimated that U.S. GDP will increase by 4% in Q3, which would be a significant increase over what we have seen during the last year and a half[10]. Finally, the overall LMI is up (+5.8) to 51.2, moving back into expansion for the first time since April. This is important as the logistics industry often acts as a leading indicator for the overall economy (before things can be sold in a store or online,
AIT Worldwide Logistics names Chelsea Lamar Global Sustainability Vice President
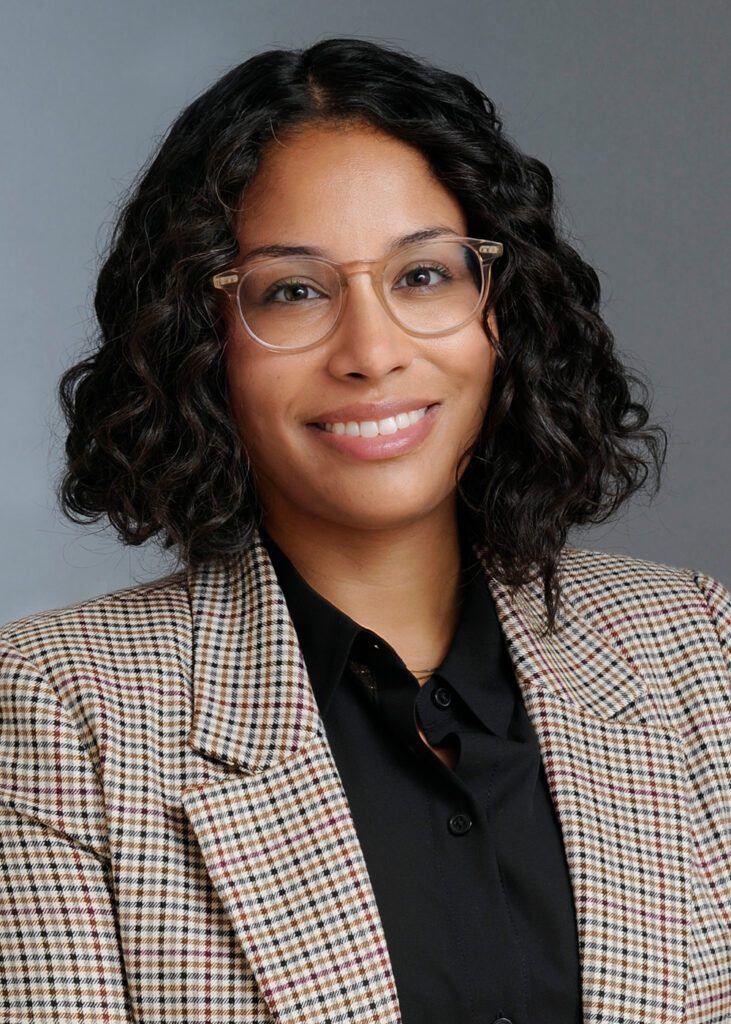
AIT Worldwide Logistics has hired Chelsea Lamar as vice president, global sustainability. In this newly created role, she will lead the company’s sustainability initiatives, furthering AIT’s commitment to environmental responsibility and ethical corporate citizenship, including its goal to reach net-zero carbon emissions by 2035. Lamar is based at AIT’s new global headquarters in Itasca, Illinois, and reports to Executive Vice President and Chief Information Officer, Ray Fennelly, who said her appointment underscores AIT’s dedication to the evolution of its environmental, social and governance strategies. “Chelsea has an incredible track record of bettering our environment by building high-quality sustainability programs,” Fennelly added. “Her leadership will empower AIT to make significant strides towards both our own and our customers’ sustainability goals.” Lamar joins the company with more than a dozen years of experience in sustainability strategy development and execution. In her previous roles, she implemented electric vehicle and renewable fuel pilot programs, introduced energy efficiency initiatives to Illinois public schools, and launched sustainability programs across more than 200 facilities, saving $3 million in annual energy costs. “I’m thrilled to join AIT, a company that shares my passion for sustainability,” Lamar said. “It’s an exciting time in the transportation logistics industry because there are so many opportunities to collaborate across the supply chain. From electric vehicles and alternative fuels to technology solutions – optimizing routes and using digital platforms for enhanced resource management – we will continue pursuing a variety of strategies to attain meaningful carbon emissions reductions.” Fennelly said Lamar will “hit the ground running,” by reviewing AIT’s current sustainability initiatives, planning the program’s next phase, ensuring the company is on track to achieve its 2035 net-zero emissions goal, and meeting with stakeholders and customers. A 2022 Women in Smart Energy Award winner, Lamar holds a degree from Iowa State University in civil engineering with an environmental emphasis. In her free time, she enjoys socializing with family and friends and volunteering for Illinois Green Alliance.
Rotary compactors reduce waste volume by up to 80%
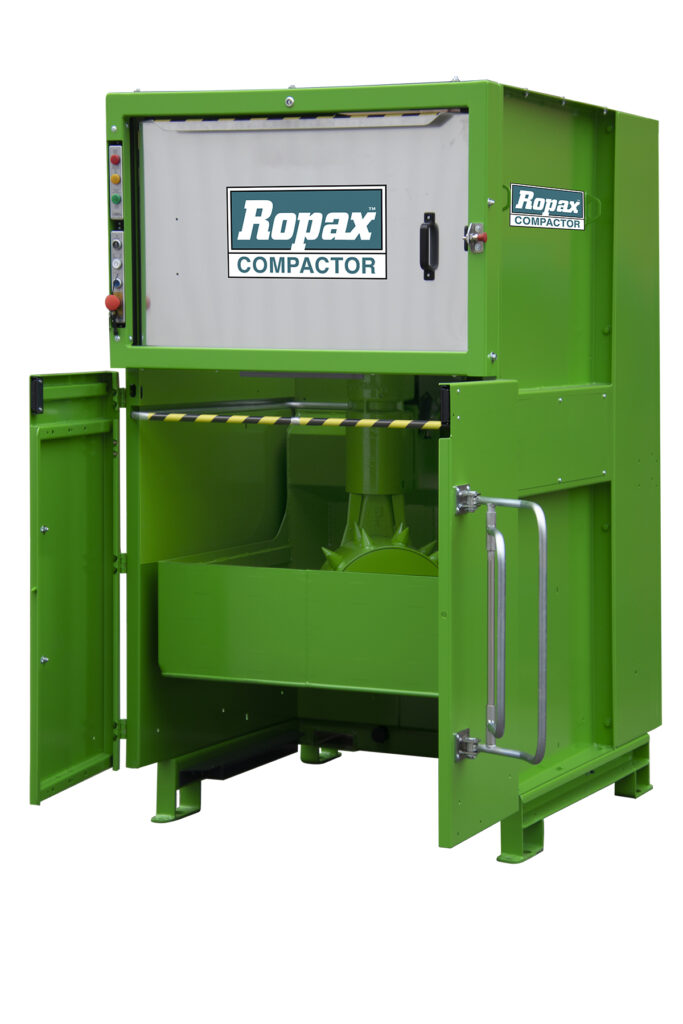
ROPAX Roto-Compactors from Epax Systems compact recyclable material and waste at the source where it is generated. These industrial grade machines use a rotating drum with metal teeth to tear, rip, shred and compact a wide variety of items including cardboard boxes, fruit and vegetable crates, plastic waste, packing filler (polystyrene), and more. As the drum rotates it swivels left and right while keeping items under constant pressure to ensure maximum compaction. Two models are available. Bin Packers compact waste directly into the included 1.5 cubic yard steel container with casters. Built-in fork sleeves on container facilitate easy collection via front loading waste collection trucks. Bag Packers compact and bale waste into large 370-gallon plastic bags that sit on a standard 48” x 40” pallet. When bags are full, they can easily be removed by a hand pallet jack and sealed to create a self-contained bale. Both systems utilize a pull-down mail style feed opening. This design serves the dual purposes of keeping users a safe distance from the compaction drum while also providing a handy shelf from which to feed waste. Items can be fed continuously during the compaction process. Ropax Roto-Compactors have a small footprint (not much larger than a pallet) so they require very little space and no structural alterations to facilities. They are ideal for use in warehouses & distribution centers, supermarkets, department stores, hospitals and medical facilities, hotels, function halls, conference centers and more.
LEDtronics expands its LED Post Top Series for walkway and parking lot lighting
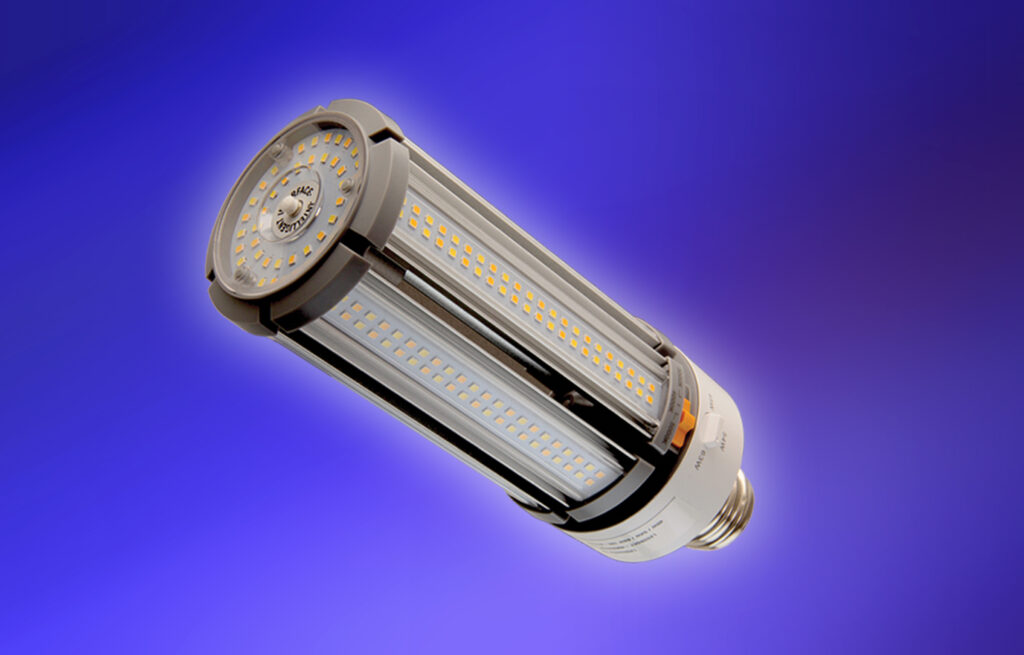
LEDtronics® Inc. announces the latest product in its line of Tunable LED Post Top Lamps with even, omnidirectional lighting that offers energy savings of up to 85 percent over MH and HPS counterparts. Known in the industry as corn bulbs for their shape, this latest high-lumen addition features multi-wattage and multi-color temperature versatility with the ability to choose from three different CCTs — 3000K Warm White, 4000K Natural White and 5000K Pure White, and variable wattage options of 45, 54 or 63 Watts. Customizable to fit any lighting need and with a switchable selection of wattages and CCTs, this lightweight LEDtronics post-top luminaire offers a wide range of features and benefits that make it ideal for a variety of applications, easily replacing E39 CFL bulbs in street post-top lighting, outdoor parking area lighting, driveway and walkway lighting, security lighting, parks, playgrounds, railroad stations, platforms, pendant and globe lighting, among others. The UL-listed LED26GCT series is safe to use in enclosed luminaires, and directly replaces HID lamps with a simple ballast bypass — at 45W it replaces 70W HPS; at 54W replaces 100W HPS, and at 63W replaces 150W MH — all at 5000K and 300W THQ. Reducing additional energy consumption by bypassing the ballast allows the lamp to operate in a voltage input range of 100 to 277 VAC. It comes in E39 mogul screw base, with a wide operating temperature range of -22°F to ~+140°F (~-30°C to ~+60°C). The new LED26GCT lamp directs a uniform, 360 degree beam, with lumens ranging from 6,610 to 9,280, and boasting luminous efficacy of 142 to 163, all depending on wattage and CCT selection. Maximum candela ranges from 663 to 914. It also features outstanding color fidelity with a CRI equal to or greater than 80 that enhances color nuances. The new state-of-the-art lamp maintains over 70 percent or greater of LED lumens for over 50,000 hours or 10 years of operation — a lifespan far longer than the equivalent halogen or HID bulb! The solid-state design renders it impervious to shock, vibration, frequent switching and environmental extremes. In addition, LEDs do not emit large amounts of heat, and little to no ultraviolet or infrared light. Since LED lights are much more energy-efficient than old-technology lighting, this lamp is perfect for operating with an alternative or renewable energy resource such as solar or wind power in cold or warm environments. This versatile LED26GCT omnidirectional, UL-listed LED post-top bulb with tunable wattage and CCT comes with an unconditional 5-year LEDtronics factory warranty, and is available through LEDtronics distributors. Other selectable wattages are available for large quantities and qualified applications.
Wauseon Machine announces consolidation of aftermarket services through merger
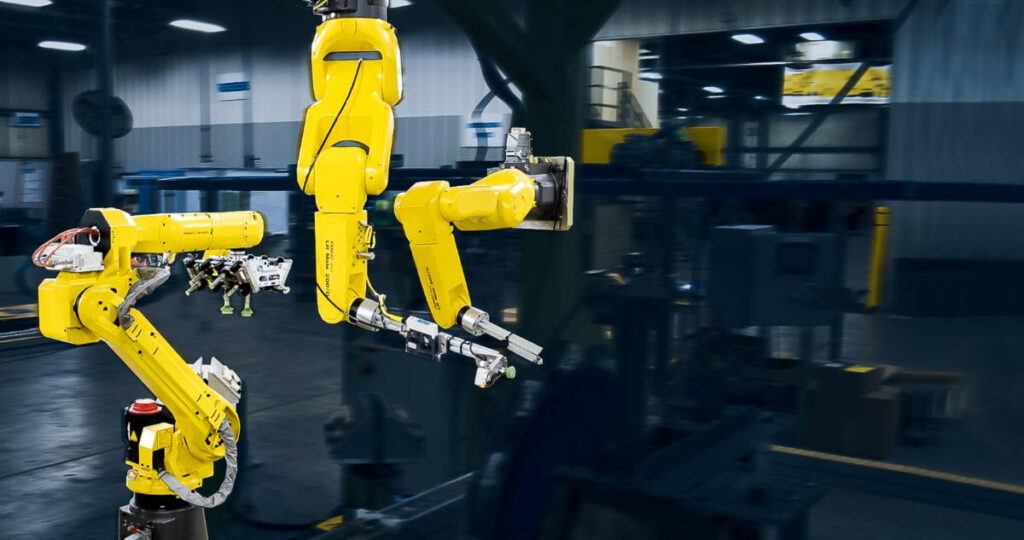
Aftermarket Services by McAlister Design and Automation and Wauseon Machine combine in formal merger Wauseon Machine, Inc. (WM), a provider of robotics automation, tube forming equipment, and built-to-print precision machines parts, announces an increase in the capacity and capability of its Aftermarket Services through the formal consolidation of McAlister Design and Automation (MDA) and WM. This merger will significantly streamline the process for customers to receive goods and services such as preventive maintenance, repair, training, support, and spare parts for automation equipment. In 2022, WM acquired MDA to better meet the needs of its customers by broadening its automation capabilities and geographical footprint. Automation technology is the key to industry transformation across verticals, from aerospace and defense to automotive, consumer products, food and beverage, pharmaceuticals, off road equipment, to warehousing. To enhance and accelerate the adoption of automation for its customers, WM’s capabilities span mobile robot platforms, collaborative robots for human-robot teaming, and a range of other cutting-edge technologies. These forms of ‘flexible automation’ allow organizations to accommodate changes and repurpose automation solutions to fit ever-changing needs. The wide-ranging benefits of flexible manufacturing include augment current labor force, maximized capacity utilization, and improved quality and accuracy. Organizations will also find that safety and ergonomics improve with flexible automation, while also allowing them to create jobs and minimize reliance on global outsourcing. Ultimately, the adoption of flexible automation also significantly increases profitability. Customers that are currently reaping massive benefits from WM’s automation offerings will enjoy an enhanced, streamlined, and simplified experience through the formal merging of WM and MDA.
H&E open new branch in Columbia MO
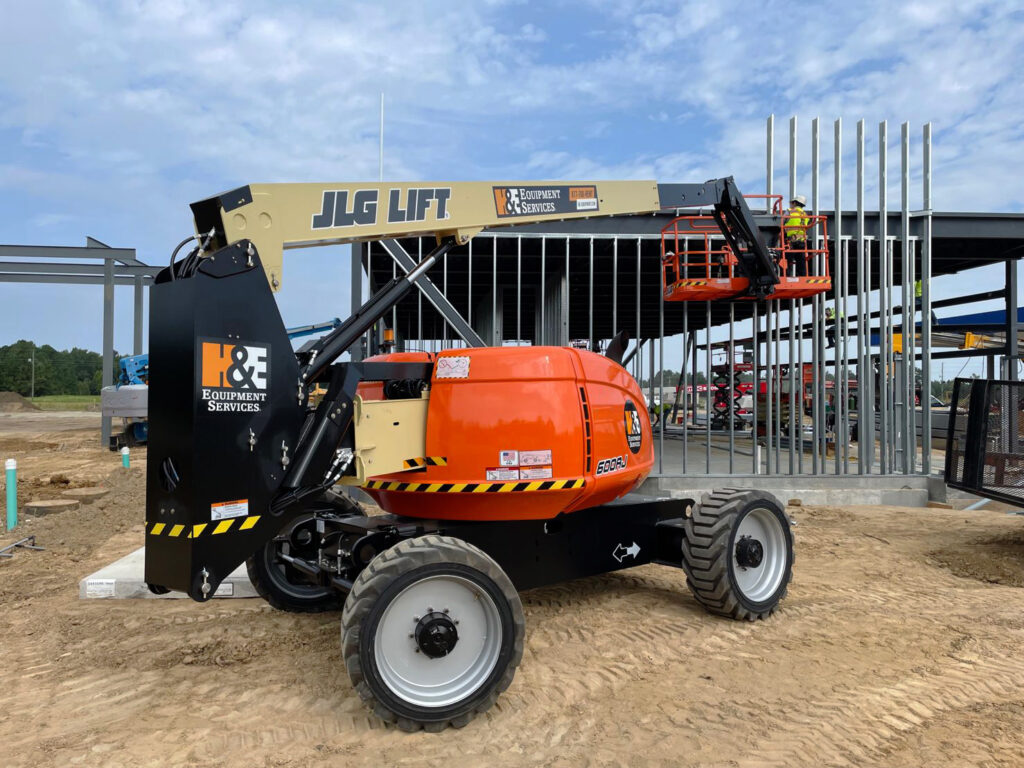
Effective September 5, 2023, H&E Equipment Services Inc. (H&E) announces the opening of its Columbia branch, its third rental location covering the state of Missouri. Since the beginning of the second quarter of 2023, H&E has opened 10 new branches across the country. The facility is located at 5611 Brown Station Road, Columbia, MO 65202-2779, phone 573 615-7101. It includes a large equipment yard, offices, and a repair shop and carries a variety of construction and general industrial equipment. “We expanded into the Midwest just two years ago, and our acquisition of One Source Equipment Rentals last October instantly increased our footprint in the region. We’re maintaining the traction with this new branch in Missouri, which is situated centrally to serve Columbia and the entire state – north to Iowa, south to Arkansas, and areas between our existing locations in the Kansas City and St. Louis markets,” says Branch Manager Robert Kerbo. “We’re continuing to add fleet and efficiencies in the region, and being located close to I-70 and Hwy. 63 means we can source equipment for our customers from nearby branches if needed and move it to their job site quickly and efficiently.” The Columbia branch specializes in the rental of aerial lifts, earthmoving equipment, telescopic forklifts, compaction equipment, generators, light towers, compressors, and more and represents the following manufacturers: Allmand, Atlas Copco, Bomag, Case, Club Car, Cushman, Doosan, Gehl, Generac Mobile, Genie, Hamm, Hilti, Husqvarna, JCB, JLG, John Deere, Kobelco, Kubota, LayMor, Ledwell, Lincoln Electric, Link-Belt Excavators, MEC, Miller, Multiquip, Polaris, Sany, Skyjack, SkyTrak, Sullair, Sullivan-Palatek, Tag, Towmaster, Unicarriers, Wacker Neuson, Yanmar, and others.
Episode 416: Mastering data and inventory with Porter Logic
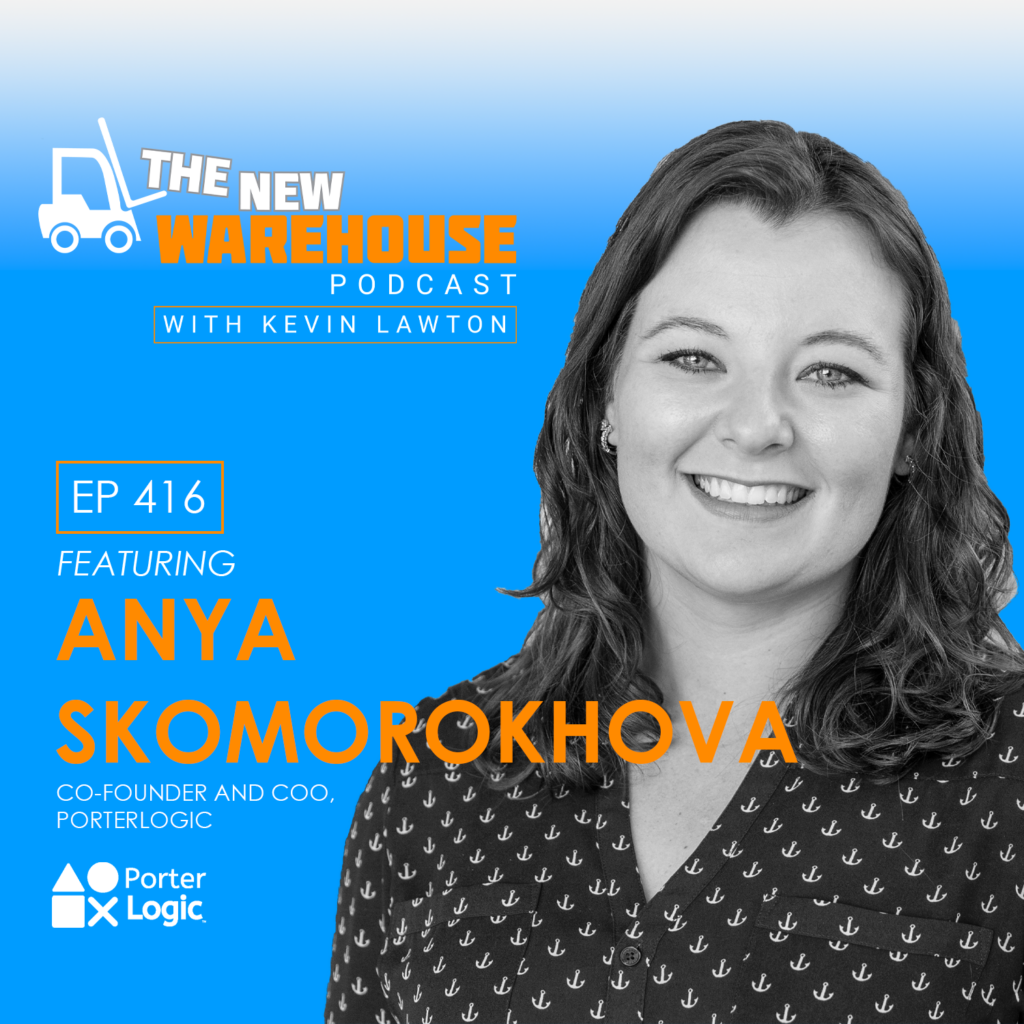
On this episode of The New Warehouse, Anya Skomorokhova, Co-Founder and Chief Operating Officer of Porter Logic joins the show to discuss the significance of data in today’s supply chain and warehousing industry. Be sure to tune in as Anya and Kevin delve into data management’s complexities and challenges, highlighting the increasing demand for comprehensive solutions to solve common problems in warehousing. All Roads Lead Back to Inventory After attending numerous trade shows focused on the supply chain industry over the past year, Anya found one clear lesson that resonated across discussions and pain points: all roads inevitably lead back to inventory. Whether the topic was manufacturing inefficiencies, order management intricacies, or demand planning, inventory stood out as the cornerstone upon which most challenges were built or solved. Common Inventory Challenges Stockouts and Overstocking – Often, companies face challenges at the front end due to inadequate inventory visibility. This can result in stockouts or overstocking, which have financial implications and strain customer relationships. Delayed Shipments – Lack of real-time inventory data often leads to shipment delays. Companies spend countless hours manually tracking goods, causing a ripple effect throughout the supply chain. Lack of Flexibility – Traditional supply chain systems can be rigid, not allowing companies to efficiently adapt to real-time inventory changes. This lack of flexibility can become an Achilles’ heel, affecting responsiveness to market demands. Understanding these issues firsthand, Porter Logic has tailored its technology stack to address them. While the core focus is inventory and warehousing, the platform’s capabilities extend naturally into order management and demand planning. Anya shares that Porter Logic allows customers to “Connect all their different systems together, fill the gaps between operations, and automate workflows across the supply chain.” This holistic approach ensures that you’re not just solving one problem but optimizing your entire supply chain. Leveraging Data for Optimization and Resource Management Anya believes data serves not just as a reflection of the current state but as a predictive tool, acting like a canary in a coal mine to signal upcoming challenges or opportunities. The Role of Data – More than Numbers Leading Indicators – Accurate data and the proper set of KPIs can serve as leading indicators for future market trends, allowing businesses to proactively address potential issues or capitalize on emerging opportunities. Decision-making – While qualitative insights, such as gut feelings or stories, have their place, they lack the empirical evidence that data provides. Only data can validate these intuitions, helping businesses discern between actionable trends and mere noise. Data Quality – Garbage In, Garbage Out The quality of your data will directly impact the quality of your decisions. Timeliness – Data loses value when it isn’t real-time or near-real-time. In an environment where market dynamics shift rapidly, data that is even two weeks old could be irrelevant. Standardization – One of the biggest challenges in data management is the lack of standardized definitions. This absence often leads to mistrust among team members who may be using different data sources or definitions to calculate the same metrics. Clean data and standard definitions yield most of the benefits. Anya believes, “You can get 80, 90% of the benefit just from having good clean data sources and having good, clean standard definitions, and enabling anybody in that organization to access that data or access that, that report or that metric at any time.” Before jumping onto the AI bandwagon, businesses should focus on streamlining their data pipelines and ensuring everyone has access to a ‘single source of truth.’ Making the Most of Data Adopting a tactical approach allows businesses to hone in on specific data elements contributing to these KPIs, mitigating the chaos of conflicting data sources. These KPIs can evolve, providing the organization with a dynamic roadmap for operational improvements. Balancing Metrics and Actions While focusing on specific KPIs, it’s crucial to be mindful of the interconnectedness of metrics. Overemphasis on one metric can inadvertently deteriorate another. Organizations should strive for a balanced portfolio of KPIs that can guide them through operational bottlenecks, avoiding the paralysis of analysis that comes with conflicting data sources. Technology as the Orchestrator Consolidating and streamlining data from various systems can be made easier with technological solutions, especially when companies are struggling with legacy systems and technical debt. Whether you’re a smaller operation using spreadsheets or a large enterprise with multiple data warehouses, choose technology that can grow and adapt with you. Solutions that offer robust connectivity are increasingly vital in today’s interconnected business landscape. Anya shares the example of a sizeable direct-to-consumer food business using varied third-party logistics (3PL) providers. Inefficient data management led them to mark bestselling products as “out of stock,” even when stock was available but not adequately accounted for. By automating the collection and standardization of data from multiple sources, the company achieved $131,000 in direct cost savings and a $250,000 revenue uplift in just a few months. Key Takeaways Achieving 80-90% of supply chain benefits hinges on maintaining good, clean data and standardized definitions accessible across the organization in real time. Modern businesses require software that talks to each other, maximizes competitive advantages, and fills operational gaps. Businesses are investing in systems that offer robust connectivity and API integrations, as these features enable them to quickly adapt to unique operational needs and foster greater efficiency and profitability. The New Warehouse Podcast EP 416: Mastering Data and Inventory with Porter Logic
Panama Canal water levels are likely to remain exceptionally low for months despite forecasted short-term improvements
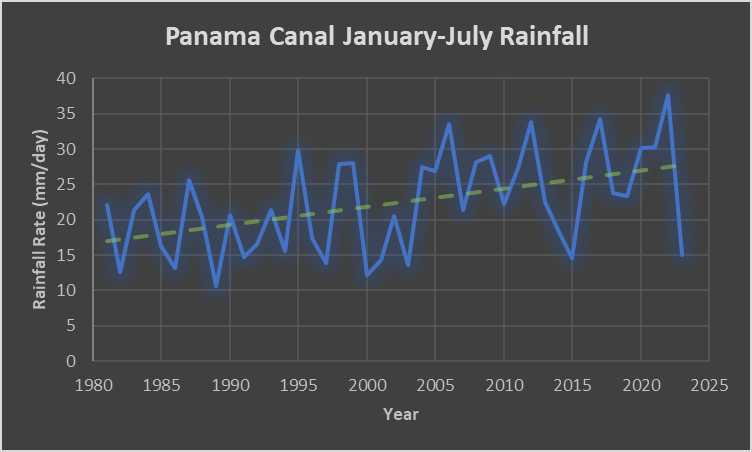
Record year-on-year declines in rainfall ‘likely culprit’ for canal drought “The Panama Canal is experiencing major, ongoing disruptions in the shipping supply chain due to restrictions on traffic related to very low water levels. This is the result of drought conditions that rapidly developed from the beginning of the year through June and have held steady since that time, said Isaac Hankes, Senior Weather Analyst at London Stock Exchange Group. In fact, 2023 is off to the driest start during January-July since 2015, which had a similar rainfall rate (see figure below). Furthermore, this represents a departure from a long-term wetter trend as reflected by data from 1981-present,” added Hankes. While the low rainfall rate itself is not historic in nature over the long-term, 2023 does show the largest decline in rainfall rate year over year on the record. This sudden drying after a wet 2022 is the likely culprit for the rapid drop in canal water levels. There has been a slight improvement in rainfall over the past two months, which has resulted in a stabilization of Panama Cana water levels after months of sharp declines. However, rains have not increased enough to raise water levels or to lessen the drought; rather a worsening scenario was simply avoided. “The forecast through the next two weeks does show a more significant period of high rainfall that could finally start to raise water levels in the canal. Unfortunately, high rainfall is likely to be temporary, as the second half of September is likely to feature widespread dryness once again across Panama. Furthermore, season forecast guidance through the end of the year suggests that dry weather could persist. This means that Panama Canal water levels are likely to remain exceptionally low for months ahead yet despite short-term improvements in the forecast.” said Hankes.
Women In Trucking Association announces its September 2023 Member of the Month
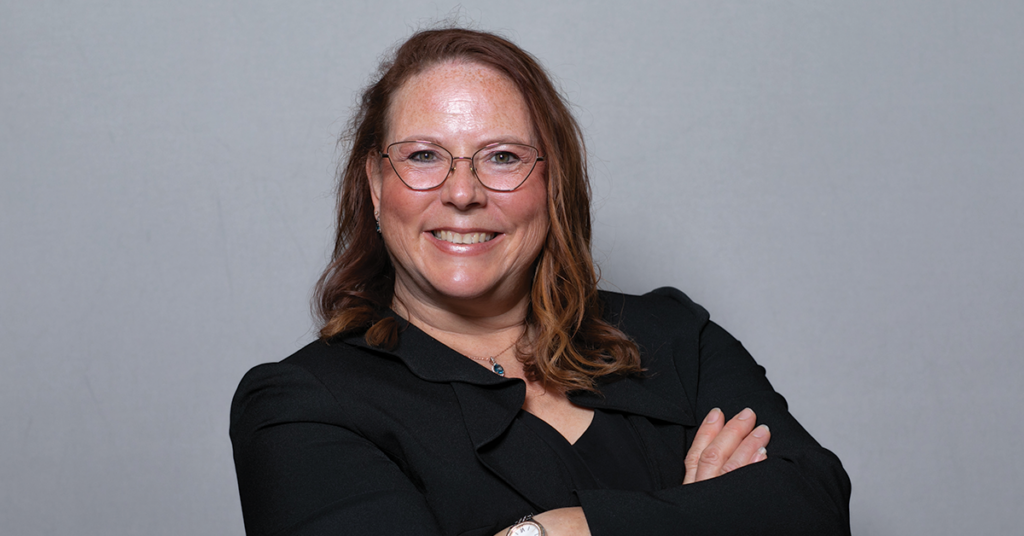
The Women In Trucking Association (WIT) has announced Laura Duryea as its September 2023 Member of the Month. Duryea is the Director of Driver Recruitment and Professional Growth at Boyle Transportation, a specialized transportation logistics provider. Duryea got her start in the transportation industry as a professional driver which was inspired by driving the shuttle bus while attending Carnegie Mellon University. After graduating with a Viola Performance degree and a change of heart, she ultimately decided to attend Pittsburgh Diesel Institute, resulting in a 25-year driving career. The last two of those driving years were spent as a team driver at Boyle Transportation before transitioning to the Manager of Recruiting, Retention, and Driver Development for 5 years. She has been the Director of Driver Recruitment and Professional Growth since July 2023 and believes her 25-year driving career brings a unique perspective to the position. In 2022, Duryea was named as a member newly established Women of Trucking Advisory Board (WOTAB) of the U.S. Department of Transportation’s (DOT) Federal Motor Carrier Safety Administration (FMCSA). The mission of this advisory board is to support women pursuing careers in trucking, expand scholarship opportunities for women in the trucking industry, and enhance trucking training, mentorship, education, and outreach programs for women. She was also recently named as a mentor in the Women in Motion Mentor Program with the American Trucking Association (ATA). Outside of her impressive career in the transportation industry, Duryea is also a member of the Savannah Professional Women for Good which supports local non-profit organizations in her community. She was also the secretary of the Dover Volunteer Fire Department for 10 years and ran LaDa Farms, an organic farm that supplied organic produce to local natural food stores for 15 years. Duryea is a passionate member of WIT and its mission saying, “women are collaborative by nature and when we come together for a cause we can change the world and this industry.”
City, Port of Long Beach welcome ILWU contract ratification
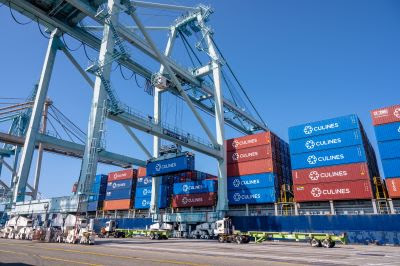
Long Beach Mayor Rex Richardson and Port of Long Beach CEO Mario Cordero congratulated the membership of the International Longshore and Warehouse Union for their ratification of the six-year contract between the ILWU and the Pacific Maritime Association. Long Beach Mayor Rex Richardson “We applaud the ILWU members for approving the new labor agreement with the PMA that will benefit 22,000 workers across 29 ports. This contract ensures the stability and success of our ports, which are a driving economic engine for our city, state and national economy. “This agreement will bolster the global competitiveness of the Port of Long Beach while expanding job opportunities for residents throughout Long Beach and the greater Los Angeles region. We value our port employees and our industry partners, and we are committed to working alongside the ILWU, PMA and our port leadership to make our Port the nation’s leading commercial gateway.’’ Port of Long Beach CEO Mario Cordero “The Port of Long Beach congratulates the International Longshore and Warehouse Union membership on ratifying the new labor agreement with the Pacific Maritime Association. “The contract ratification will have a hugely beneficial impact to the U.S. economy, which depends on our ports and the trade they facilitate. The goods movement workforce and terminal operators provide the top-notch service that brings cargo from around the world to our docks. We’re proud to partner with the ILWU and PMA to move cargo through the nation’s largest trade gateway here in the San Pedro Bay. “This contract will pave the way for the San Pedro Bay ports complex to competitively and sustainably keep the nation’s cargo and the nation’s economy moving.”
Xeneta container rates alert: Long-term ocean freight rates plunge by more than 60% in year of decline
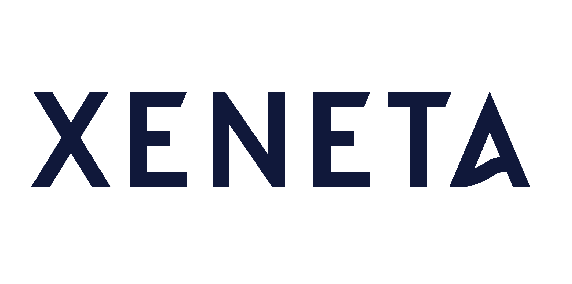
Long-term ocean freight rates slid once again in August, marking the 12th consecutive month of declines for beleaguered carriers. According to the latest real-time data from the Xeneta Shipping Index (XSI®), contracted rates fell 7.8% in August, meaning prices have now dropped 62.7% since this time last year. The world’s busiest routes – exports from the Far East – have endured the most dramatic declines, with Xeneta’s regional sub-index showing a 75% year-on-year fall in the value of valid contracts. On the spot “It’s a torrid time for carriers in the contract market,” comments Peter Sand, Chief Analyst at Oslo-based Xeneta, “with continuing weak demand exacerbated by burgeoning overcapacity as more and more new ships come online. This is driving down the industry’s prized long-term rates, with falls across the board when we assess region by region. The boom period of just one year ago must now seem like a very distant memory. “However,” continues Sand, “the industry needs to bear in mind developments in the spot market. Here carriers have managed to lift the rates on the major trades in the past couple of months. As we know, the long-term market follows spot market movements, albeit with a slight lag. Therefore, regardless of the big plunge here – which shippers should benefit from – the falling rates may not last. So, I don’t think shippers should be complacent; we could be approaching a market shift.” Down time If this is the case, it will be a welcome development for carriers. Sand points to month after month of falling rates since this time last year, with the smallest decline being 0.1% in December 2022, while May 2023 saw a collapse of 27.5%. “And, once again,” he notes, “the data reveals that every major XSI® sub-index lost value in August.” In Europe, the import sub-index fell 3.4% for the month and is now down 60.1% year-on-year. Exports fared slightly better, with a dip of 2.8% from July (down 52.4% since August 2022), despite a significant drop of 13.6% in contracted prices on the export trade from North Europe to China, which has now collapsed 85.4% year-on-year. The US Import XSI® recorded this month’s largest fall, sinking by 14.9% to leave it 65.2% down year-on-year. The biggest monthly rates drops were seen out of China, Japan, Taiwan, and Korea – to both US West and East coasts – with price falls ranging from 19.3% to 62.3%. The XSI® for US exports was this month’s most resilient figure, losing just 0.8% of its value. Xeneta’s data continues to paint a bleak picture for Far East contracted export rates, with the sub-index registering a 14.2% monthly decline for August. The region’s import XSI® fared better, with a decline of 2%, now down 51.1% year-on-year. Long-term perspectives “It’s tough out there,” Sand says, “but carriers will take heart from the fact that spot rates have now moved up above contracted rates on the world’s leading trade corridors. As a result, we may finally see some upward pressure on long-term rates. “Shippers who have been playing the spot market to save money will now be looking at shifting volumes to contracted agreements, which may offer better value. This could elevate prices. So, have we now reached the point where long-term rates have bottomed out? If so, it’s a good time for shippers to negotiate new contracts and lock in favorable rates.” He concludes: “It’s too early to say if there’s a definite market ‘switch’, but I certainly wouldn’t bet on another run of consecutive monthly XSI® falls on the scale we’ve just experienced. I’d advise all stakeholders to keep watching the data for the next market moves.”
Legacy tension fabric buildings feature structural steel frame
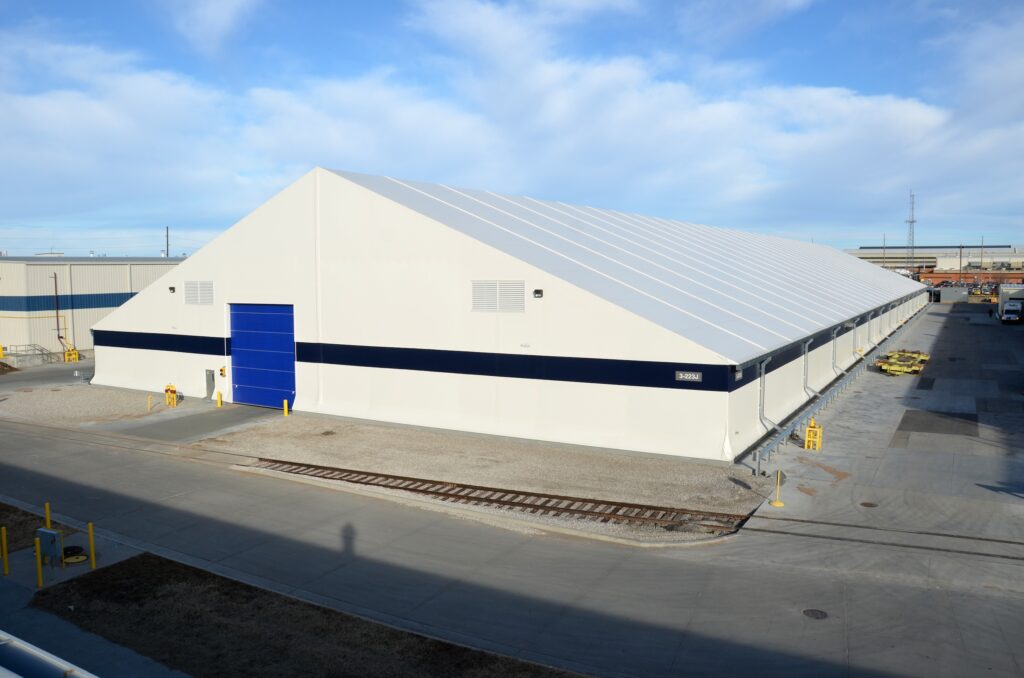
Combining rigid-frame engineering with the proven benefits of tension fabric membranes, Legacy Building Solutions offers superior quality fabric structures that are fully customizable. This design concept provides a high level of flexibility for a wide array of applications and industries, including commercial and industrial warehousing, cold storage facilities, equipment and bulk material storage, treatment plants, and many more. Legacy fabric buildings utilize a durable rigid frame in place of the hollow-tube, open web truss “hoop” framing traditionally used for fabric structures. The strength of the structural steel frame provides several engineering advantages, most notably the ability to easily customize buildings to the exact width, length and height required. In addition to long clear spans, the buildings have straight sidewalls that maximize the useable square footage inside the structure. The design allows for much more structural flexibility than traditional fabric structures, including the ability to add lean-tos, mezzanines, sidewall doors and more. The structures are also engineered to provide desired overhangs or handle additional loads for items such as sprinklers and conveyors. Unlike hollow tube steel, Legacy’s solid structural steel I-beams are not vulnerable to unseen corrosion originating inside a tube. Additionally, there are multiple coating options available for all steel components, including epoxy paint, hot dip galvanizing, primer and powder coat paint. Legacy buildings feature high-quality fabric roofs that eliminate the corrosion concerns associated with metal-constructed facilities. A variety of fabrics are available, including 27-ounce ExxoTec™Elite and 19-ounce ExxoTec Pro, both of which are premium PVC fabrics with superior strength and performance characteristics. The durable fabric allows natural light to permeate the structure during daytime hours, while insulation and liners can be added to meet energy codes or satisfy customer specifications. Installation is up to three times faster than with conventional buildings, and the design can be adjusted for stationary or portable applications. Sidewalls can be customized and built with any desired material — including steel, concrete or stone — and then easily lined with fabric to prevent corrosion to the interior, or to create a seamless look for occupied buildings. Legacy steel components and fabric covers are backed by a comprehensive warranty.
Kito Crosby announces 2023 ‘Lifting for the Troops’ campaign
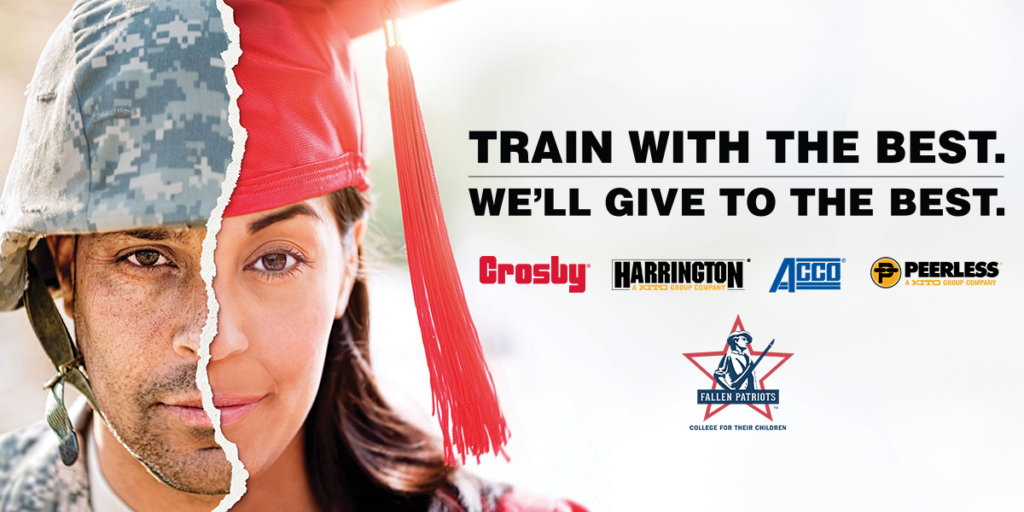
Kito Crosby, a manufacturer of lifting and securement solutions, has announced its Lifting for the Troops campaign for 2023, supporting the Children of Fallen Patriots Foundation. Fallen Patriots provides college scholarships and educational services to military children who have lost a parent in the line of duty. After government programs, the average shortfall in college funding for a student is $25,000. Supported by its loyal channel partners and end users throughout the United States, Kito Crosby looks to raise $50,000 this fall for the Fallen Patriots. From September 1 through October 31, 2023, Kito Crosby will donate $500 for every Crosby, Harrington, Acco, and Peerless training event the company hosts in the US. In addition, all proceeds from the popular Crosby User’s Guide for Lifting online training course during this time will be donated to this honorable cause. Private donations are also welcome. Gifts can be made at liftingforthetroops.com. 100% of the proceeds go directly to the Fallen Patriots and help Kito Crosby reach its goal. Approximately 25,000 children have lost an active-duty parent in the military over the last 35 years. Of those, 96% of casualties are men, leaving behind single mothers to care for their families, and 60% report having trouble making ends meet. The foundation said that $625 million is needed nationwide to cover the gap between government assistance and the actual cost of a degree. Since 2002, Fallen Patriots has provided more than $70 million in total assistance to nearly 3,000 children, including almost 1,400 debt-free graduates. Kito Crosby has trained more than 600,000 people in a wide range of industries since 1991. Every time a worker in the oil and gas, construction, heavy lift, transportation, manufacturing, wind energy, entertainment, and material handling industries attends a Crosby, Harrington, Acco, or Peerless training event, or completes Crosby’s online training course this fall, they can know that they are playing an important part to help secure a better future for military children who have lost a parent. With a US manufacturing footprint that includes plants in Texas, Oklahoma, Arkansas, Pennsylvania, South Dakota, Alabama, and Minnesota, Kito Crosby’s involvement with the country’s military stretches back to its earliest days, supplying lifting hardware for military equipment. Today, more than 50 Veterans work in the company’s facilities designing, manufacturing, and distributing the best rigging hardware and material handling equipment in the world. Melissa King Ruths, Kito Crosby’s senior vice president of marketing and training, said: “We are honored to partner with the Children of Fallen Patriots Foundation again for now the fourth year. Together, with our distributors and end users, we are proud to support such an important cause and help raise enough this year to cover the cost of two college scholarships for young people who have been affected by military casualties.”
Kenco survey: Peak season 2023 expectations for consumer spending, shipping and product availability
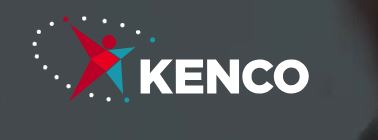
Results indicate that retailers should flatten the peak season curve and look closely at offering slower delivery and more shopping holidays While 58% of consumers are planning to spend approximately the same amount of money during peak season 2023 as they did in 2022, many are still worried about the rising cost of goods and if they will be able to afford gifts this year. This and other findings are reflected in new research from Kenco, one of North America’s third-party logistics (3PL) providers. These outcomes were part of Kenco’s 2023 eCommerce Peak Season Pulse, which surveyed more than 225 U.S. adult consumers to gauge their expected holiday spending, shopping plans and concerns. As inflation pushes up the price of consumer goods, more than half (54%) of respondents worry they will not be able to afford the gifts they want to buy. To counteract, consumers will search for online and in-store deals – 65% of respondents plan to take advantage of a shopping holiday. Specifically, 59% say they will shop on Black Friday and 53% will seek deals on Cyber Monday, while 44% have already taken advantage of goods sold on Prime Day. Additionally, more than one-third (35%) will be taking advantage of post-holiday sales. “Armed with this knowledge, retailers should consider marketing additional sales and creating more shopping holidays to not only spread-out consumer spending, but also flatten the curve of peak season logistics and its respective labor challenges,” said Jason Minghini, Senior Vice President of Operations at Kenco. “By incentivizing consumers to shop on additional days, retailers can also avoid potential shipping delays caused by high order volumes.” Another way that retailers can spread out product shipping and offer a money-saving service to consumers is to incentivize slower delivery. Most consumers (72%) would opt for slower shipping if it meant their packages arrived for free. Nearly three-quarters (74%) will take slower shipping speeds if provided an incentive such as saving on an order (72%), a gift card or store credit (64%) or a free upgrade to faster shipping on a future purchase (25%). Although supply chain kinks have significantly improved over the last three years and 52% of respondents show no supply chain concerns, 60% of consumers still worry about product availability for this year. In fact, 42% of consumers have already started their peak season shopping to get ahead of these concerns. “With many retailers struggling with inventory surpluses, there is an opportunity here to target these early shoppers,” said Dave Hauptman, Chief Commercial Officer at Kenco. “Retailers can pull out and promote their inventory overstock earlier, reducing the amount of products in their warehouses and stores and also potentially reducing order spikes on more traditional shopping holidays.”