Titan Machinery Inc. announces strategic acquisition of O’Connors
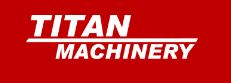
Australia’s leading Case IH dealership group with strong presence in high horsepower equipment – Accretive acquisition generated approximately $0.40 in annual proforma earnings per share – Acquisition includes strong management team with track record of solid financial performance through a combination of organic and acquisitive growth Titan Machinery Inc., a network of full-service agricultural and construction equipment stores, announced that it has entered into a definitive purchase agreement to acquire J.J. O’Connor & Sons Pty. Ltd. (“O’Connors”), the largest Case IH dealership group in Australia, for $63 million in cash, subject to final working capital and other closing adjustments (the “Transaction”). In the unaudited full fiscal year period ended June 30, 2023, O’Connors generated revenue of $258 million and EBITDA of $21.4 million, as translated to USD. O’Connors, founded in 1964, is the largest Case IH dealership group in Australia, and a market leader in high horsepower equipment. O’Connors delivers a wide range of new and used equipment, parts, and services through its 15 dealerships and 1 parts location located in the Australian southeastern grain belt, which includes the regions of Victoria, New South Wales, and South Australia. In addition, O’Connors is a distributor for more than 25 leading short-line equipment brands, providing an impressive range of complementary offerings to its core Case IH line of products, and has a strong parts and service business that provides a reliable recurring revenue stream. On a consolidated basis, O’Connors achieved a gross margin of approximately 18.7% in the full fiscal year 2023, and generated a total pre-tax margin of approximately 7.2%, representing a margin profile that is consistent with Titan’s. David Meyer, Titan Machinery’s Chairman and Chief Executive Officer, stated, “We are pleased to announce our definitive agreement to acquire O’Connors, Australia’s leading Case IH dealership group. This transaction marks our entry into the Australian agriculture market, as we continue to seek opportunities for Titan to expand its reach, both domestically and abroad. O’Connors’ operating metrics, core values, and customer-centric focus align with our own, making them a great partner for our entry into the Australian agriculture market, which is benefiting from strong fundamentals that are being driven by enhanced productivity, economies of scale, and farmer profitability.” Mr. Meyer continued, “We are very impressed with the O’Connors senior management team, led by CEO Gareth Webb, who have been operating the business exceptionally well over the last five years after succeeding the retiring major shareholders Dennis and Mark O’Connor. It’s this strong management team, along with their great track record of retailing and supporting the high horsepower CaseIH product line up that makes this a very compelling acquisition. O’Connors has established itself as a respected leader in the region, earning a reputation for its deep expertise and employee and customer-centric focus. Their long-term business relationships, built over nearly six decades, demonstrates their commitment to excellence. The O’Connors team has a proven track record of driving organic growth, M&A execution, and profitability, and we believe that there is additional opportunity to build upon their growth formula and capitalize on operational synergies across Titan’s global footprint as we integrate the business.” Strategic and Financial Highlights Largest Case IH agriculture equipment dealership in Australia with leading market share positions in key offerings – O’Connors is a distributor of Case IH agricultural equipment in Australia, with a primary focus on high-horsepower cash crop production equipment. Throughout its 16 locations in the grain belt region in southeastern Australia, O’Connors provides an end-to-end offering to customers including new and used equipment, parts and services, and other value-added service offerings. Key similarities to Titan’s domestic agriculture business, which will allow for seamless integration and unique synergy opportunities – O’Connors’ focus on high-horsepower cash crop production equipment in Australia’s grain belt region is being supported by the combination of increasing precision ag technology adoption and farm expansion. These trends are similar to what Titan is experiencing in its domestic agriculture business and coupled with the O’Connors’ strong management team, Australia’s native English language, and comparable legal system, this transaction is expected to allow for a seamless integration that carries over into our shared values and customer-centric focus. The Company believes it also provides Titan with unique operational synergy opportunities to expand its global customer service capabilities and capacity across the network. Titan to enhance and expand upon O’Connors’ proven M&A strategy – O’Connors’ growth accelerated in 2018 following a focused acquisition strategy that resulted in acquiring nine additional locations in the subsequent five year period. The Australian market is in the early stages of dealer consolidation and through a combined approach – leveraging O’Connors’ existing leadership team and Titan’s broader capabilities and resources – the Company believes is it well positioned to capitalize on continued acquisition opportunities to unlock network synergies while driving market share gains. Immediately accretive transaction with long-term growth opportunities – O’Connors’ base unaudited fiscal 2023 business, ended June 30, 2023, produced revenue of $258 million, pre-tax income of $18.7 million and EBITDA of $21.4 million. Adding estimated financing and integration expenses for the first twelve months of ownership to these results provides for run rate pro forma profit before tax of $13.0 million, or $0.40 earnings per share. The combined Titan Machinery enterprise, along with the O’Connors proforma run rate results, would equate to approximately $2.9 billion in revenue, and $5.20 in diluted earnings per share an annualized basis, based on the midpoint of Titan’s full fiscal year 2024 guidance ending in January 2024. The combined Company exhibits strong pre-tax margins and builds upon Titan’s growth strategy. Additional Transaction Details The definitive agreement to acquire O’Connors contemplates an acquisition price of $63 million, subject to final working capital and other closing adjustments, and will be funded with cash and Titan’s existing credit facility. The O’Connors organization is represented by a strong, capable and professional leadership team that spearheaded its growth acceleration over the past five years. It is anticipated that Titan Machinery will retain O’Connors’ management team following the integration, who will be responsible for the region’s operating performance and report into Titan’s executive team. The Transaction is subject to customary closing conditions and is expected to close in the fourth quarter of calendar 2023. Fiscal 2024 Modeling AssumptionsUpon closing, the Company
OHAUS introduces new Courier™ Series scales
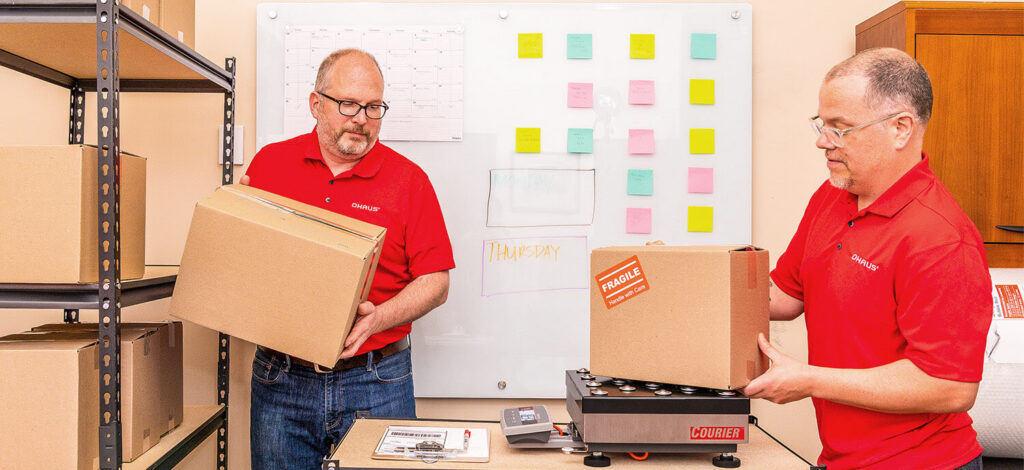
OHAUS’s Courier line of precise standard scales for dedicated shipping applications are designed with intuitive features and fast and easy connection created with your business in mind. No matter what your business, it can carry the weight. The new Courier 7000 and Courier 5000 Series scales specifically meet the demands of distribution, office shipping, and manufacturing. Durable, fast and reliable these scales feature intuitive integration with PC-based shipping software allowing data to be captured accurately every time. In addition, the Courier 7000 and Courier 5000 are equipped with special applications like Display Hold, which keeps measurements visible long after large, display-obscuring packages are weighed and moved, and Totalization, which gives users the ability to quickly and efficiently access a sum total of weighing results from a given project. The Weight Alert™ mode will also alert you to packages that may be too heavy in relation to defined values – saving your business from potentially costly errors. Multiple connection options and power options mean the Courier 7000 will be ready to get to work for you 24/7.
FedEx announces 2024 shipping rates, fees and surcharge increases
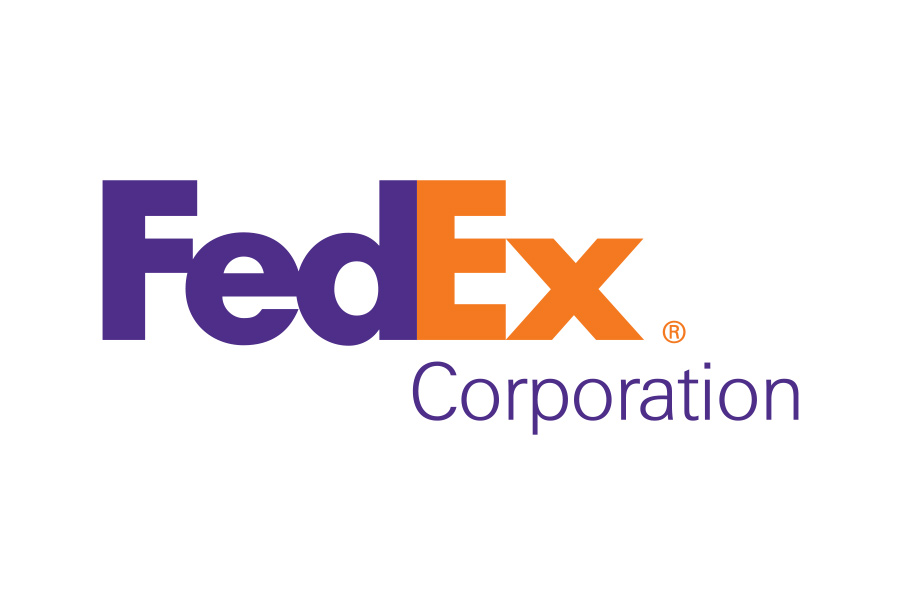
FedEx Express, FedEx Ground, and FedEx Freight, subsidiaries of FedEx Corp. will adjust shipping rates on January 1, 2024. • FedEx Express shipping rates will increase by an average of 5.9% for U.S. domestic, U.S. export, and U.S. import services. • FedEx Ground and FedEx Home Delivery shipping rates will increase by an average of 5.9%. FedEx Ground Economy shipping rates will also increase. • FedEx Freight shipping rates will increase by an average of 5.9%-6.9% dependent on the customer’s transportation rate scale. This change applies to shipments within the U.S. (including Alaska, Hawaii, Puerto Rico, and the U.S. Virgin Islands) and between the contiguous U.S. and Canada. The average annual rate increases are one percentage point lower than last year’s general rate increase. The price adjustments reflect incremental costs associated with the current operating environment, while enabling FedEx to continue investing in service enhancement, fleet maintenance, technology innovations, and other areas to serve customers more effectively and efficiently. The following FedEx Express and FedEx Ground surcharges will also take effect in January 2024: • Effective January 1, 2024, FedEx will be increasing customs clearance service fees on imports. • Effective January 15, 2024, FedEx will assess the Additional Handling Surcharge and Oversize Charge per eligible package for international multi-piece shipments, instead of per shipment. The affected surcharges are the Additional Handling Surcharge (Dimension, Weight, Packaging, Freight, and Non-Stackable) and the Oversize Charge. Details of all changes to rates, surcharges, and fees will be available on fedex.com on September 7, 2023. Demand surcharges for the 2023 holiday shipping season Formerly known as “peak” surcharges, the demand surcharges that will be in effect for the 2023 holiday shipping season are available on fedex.com.
Hamilton Casters VP of Sales Jim Lippert passes at age 62
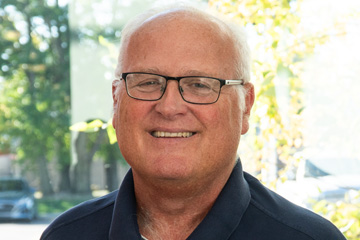
Hamiliton Caster has sadly announced that Jim Lippert, Vice President of Sales died on August 11th. He was born on February 3, 1961 to the parents of Mary and Bob Lippert. In a company statement they said Jim was beloved by everyone who knew him. Admired for his easy-going, warm and extroverted personality, Jim was the type of man who made you feel important when he spoke with you. He was so personable, in fact, that his high school friends created a fan club for him that’s still going strong today, with 450 members and counting. In an article in the Journal-News, Steve Lippert was quoted in the article saying he wasn’t the best player on the team ― he had a lot of “bench time” ― but Jim had his fans. And actually, it was a fan club that had grown to 450 members strong more than four decades after he graduated. Steve isn’t sure about the origin of the fan club, but he suspects it had to do something with his exuberant and extroverted personality. A natural with customers, Jim started in Hamilton sales back in 1990. “He was THE guy you wanted to work for,” recalled Marty Wilson, Hamilton’s Director of Business Development. No matter what, Jim had your back.” “He demonstrated an incredible empathy for his team—always a good listener and never confrontational,” added Hamilton President Mark Lippert. “If he ever needed to share difficult feedback, he did it in a way that the person on the receiving end was so grateful and appreciative by the end of the conversation!” One of the hallmarks of Jim’s personality was his “booming voice” and the way he expressed “growls of approval” when anyone on his team achieved a sale. Mused Hamilton Sales Engineer Joe Ford, “His voice was rich and full, and you could hear him speaking from 50 yards away—you could hear him laugh from 100 yards away. He would have made a wonderful sportscaster. I will miss him greatly.” An alumni and avid sports fan of the University of Michigan, Jim attended college on an ROTC full ride scholarship. He served seven-and-a-half years as an Army field artillery officer and was awarded the Meritorious Service Medal and Army Commendation Medal. Devoted to both his family and community, Jim served on the Wyoming Booster board, coached his three sons’ baseball and basketball teams and was named the 2003 Wyoming Citizen of the Year for his leadership. He was also active in two Wyoming churches, where he served as a reader, lector, choir member and eucharistic minister. Jim recently celebrated 40 years with his high school sweetheart, Carrie, and is survived by his four children and five grandchildren. “He was the consummate family man,” said Lippert. “Twice a week, he and Carrie would host family dinners at his house. Their love and fellowship were something straight out of a Norman Rockwell Thanksgiving.” Jim is survived by his wife of 40 years, Carrie, his children Christopher (Tarra) Lippert, John (Kelly) Lippert, Patrick (Ashley) Lippert, and Marie Lippert (and fiancé Keegan Hodge); and his siblings, Dave (Teresa) Lippert, Steve (Joan) Lippert, Debbie Bellman, Jennie (Tom) Ruehlmann, and Mike (Molly) Lippert; as well as his five grandchildren and many nephews and nieces. In lieu of flowers, the family requests donations be made to St. James of the Valley Catholic Church in Wyoming in Jim Lippert’s memory. Their address is 411 Springfield Pike, Wyoming, OH 45215. The phone number is (513) 948-1218.
Budgeting: A declaration is not a strategy
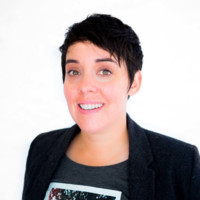
Budgeting season is coming soon for many companies, and this usually includes the review of major initiatives, costs, resources, and activities for the coming year. Sometimes, it’s also the time to re-evaluate the organizational strategy or even create a new one. And while creating a strategy can be a daunting task, many leaders actually go through long and convoluted processes to create one, only to shelve it in a matter of months. This can be incredibly frustrating. Why go through weeks and months of effort to create a so-called strategy that you aren’t even used to guide decisions during budgeting and planning? Why have a strategy that never gets implemented, or just becomes that “document we made a while back” which is periodically referred to but no one understands what it really means to their department? There are usually many factors at play in these situations, but more often than not, the strategy isn’t a strategy – it’s a declaration. In short, a strategy is created in a bubble by upper leadership, a document is created that is extensively wordsmithed and then thrown over the fence to the organization in a big town hall meeting. A declaration isn’t a strategy. Crafting a strategy – especially a corporate strategy – is just the beginning, not the end of the process. Thinking that the organization will understand the nuances and thought processes behind something that took you months to create, will be digested and translated in 20 minutes is folly. Your declaration that “this is the strategy, go forth”, doesn’t equip your department leaders with anything other than a 50,000-foot, general idea of what the organization is trying to achieve. That idea must be translated into department-specific business strategies to turn it into action. This doesn’t mean you tell your teams, “Hey, now that you have the corporate strategy, put together your budgets and activity plans and make sure they align with the strategy.” The magic of a strategy comes with taking that strategy you’ve defined and determining how each department can creatively amplify it. In short, this means they need to craft their own supporting strategy. For example, say your corporate strategy includes a component declaring, “Our people are our most important asset, and we will focus on attracting the right talent and building a culture of execution.” What does that mean for HR? What does that mean for product development? What does that mean for project management? The declaration is so broad and lofty, it has very little meaning. How should this get translated into a competitive advantage? Or is this really just frustration about launches missing their deadlines and current attrition numbers? Then it’s not really a strategy at all. Strategies fall flat for a variety of reasons but don’t fall into the declaration trap. Even if you’ve spent countless hours creating your strategy, it will be useless without taking the next step in helping each of your departments translate it. This doesn’t mean telling HR to “improve the application process”. It means discussing in depth what types of talent you need and why, what those people are looking for, where they can be found, and what other organizational elements need to change to meet their needs. Only then might your “declaration” actually become a strategy that creates real outcomes. About the Author Andrea Belk Olson is a keynote speaker, author, differentiation strategist, behavioral scientist, and customer-centricity expert.As the CEO of Pragmadik, she helps organizations of all sizes, from small businesses to Fortune 500, and has served as an outside consultant for EY and McKinsey. Andrea is the author of three books, including her most recent, What To Ask: How To Learn What Customers Need but Don’t Tell You, released in June 2022. She is a 4-time ADDY® award winner and host of the popular Customer Mission podcast. Her thoughts have been continually featured in news sources such as Chief Executive Magazine, Entrepreneur Magazine, Harvard Business Review, Rotman Magazine, World Economic Forum, and more. Andrea is a sought-after speaker at conferences and corporate events throughout the world. She is a visiting lecturer and startup coach at the University of Iowa, a TEDx presenter, and TEDx speaker coach. She is also an instructor at the University of Iowa Venture School. More information is also available on www.pragmadik.com and www.andreabelkolson.com.
Board revises standard on Employers’ Duty to bargain before changing terms and conditions of work
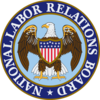
Today, the NLRB issued two full-Board decisions, Wendt Corporation and Tecnocap, LLC, (both decided on August 26, 2023), addressing the statutory duty of employers to bargain with unions before making changes in terms and conditions of work. In Wendt, the Board overruled Raytheon Network Centric Systems (2017), which had given employers greater latitude to make unilateral changes affecting a unionized workforce during a contractual hiatus or during negotiations for a first contract. The Board explained that allowing employers to justify discretionary unilateral changes during such time periods as a “past practice” was both inconsistent with the Supreme Court’s decision in NLRB v. Katz, 369 U.S. 736 (1962) and undermined the pro-bargaining policies of the National Labor Relations Act. The Board in Wendt also reaffirmed the longstanding principle that an employer may never rely on an asserted past practice of making unilateral changes before employees were represented by a union (when the employer had no duty to bargain) to justify unilateral changes after the workers select a bargaining representative. In Tecnocap, the Board overruled a different aspect of Raytheon that had not been addressed in Wendt. The Board held that an employer’s past practice of unilateral changes that was developed under a management-rights clause in a collective-bargaining agreement cannot authorize unilateral changes made after the agreement expires and while bargaining for a new agreement is under way. The Board explained that the Raytheon holding harmed the collective-bargaining process in two ways: It forced unions to bargain to regain terms of employment lost to post-expiration unilateral changes, and it discouraged unions from agreeing to management-rights clauses in the first place. “Our decision today returns to a more faithful application of Supreme Court precedent. By protecting employees who have chosen a union representative from being subject to discretionary unilateral changes in their terms and conditions of employment without bargaining, the policy we announce today better promotes the collective-bargaining process that lies at the core of the National Labor Relations Act,” said Chairman Lauren McFerran. Members Wilcox and Prouty joined Chairman McFerran in issuing the decisions. In Wendt, Member Kaplan concurred in finding that the employer acted unlawfully but but did not agree with the majority’s decision to reach the validity of Raytheon upon remand. In Tecnocap, Member Kaplan dissented.
Columbia/Okura launches miniPAL+ ™ with a 20kg lifting capacity
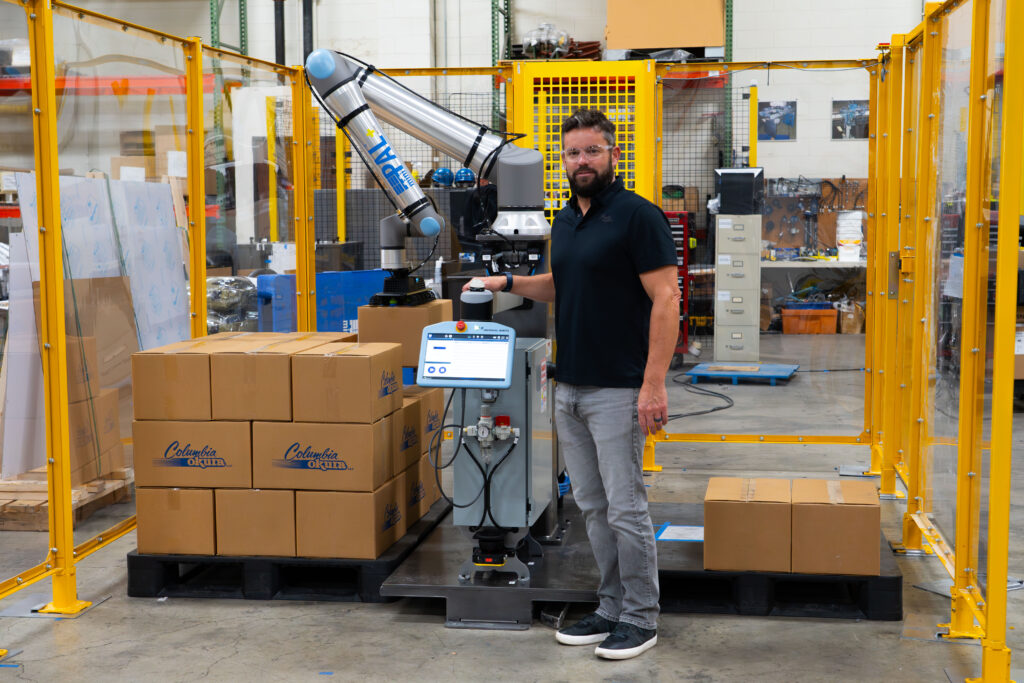
Columbia/Okura LLC just announced the miniPAL+ ™, a new collaborative solution utilizing Universal Robot’s UR20 cobot arm, providing a 44 lbs. (20kg) lifting capacity. This new palletizing solution enables handling heavy payloads at higher rates than previous collaborative systems and with flexible tooling allow for multi-pick options. The design features a 10’ x 11’ footprint, and an intuitive pattern building software by Rocketfarm for ease of use. Columbia/Okura will debut the miniPAL+ ™ at Pack Expo Las Vegas 2023. Stop by booth # C-2838 on Monday, September 11th, at 10AM for the official unveiling and to see the miniPAL+ ™ in action! “The unveiling of the miniPAL+ ™ collaborative palletizer at Pack Expo in Las Vegas is a testament our belief in the transformative power of automation. This new palletizer was designed specifically to improve efficiency, safety, and productivity in businesses of all sizes. It is a welcome addition to the Columbia Okura lineup of innovative end-of-line automation solutions”. Columbia Okura’s Director of Sales, Michael Stuyvesant Optimal Design for Palletizing with the miniPAL+ ™ Columbia/Okura’s newest solution features the all new UR20 cobot arm, providing a load height of 2032mm (80”). Cobots are designed to interact directly with human operators, keeping users safe through limited force and speeds. The miniPAL+ ™ safety features include area scanners and radar, both of which monitor the palletizing cell and slow the robot to ‘collaborative speeds’ should a person enter. Additionally, it includes guarding to create a physical barrier while also optimizing the footprint of 10’ x 11’. The dual pallet building locations allow for reduced downtime when one pallet load is completed and needs to be removed from the cell. The system uses 110V AC power which is achieved through a standard power outlet. The system is very quick to integrate. It can be set-up and running within a day of deployment. With over 25 years of robotic palletizing experience, Columbia/Okura is ready to assist in providing the best automated solution for our client’s needs. Visit our website to learn more about the miniPAL+ ™ https://columbiaokura.com/products/cobots/
BSLBATT®completes delivery of lithium-ion batteries to distribution and 3 PL in the Philippines
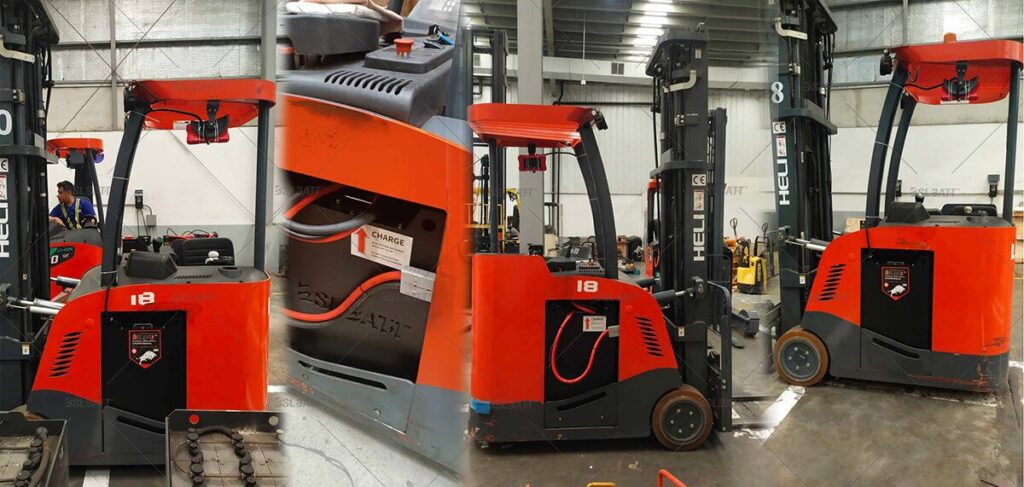
A BSLBATT® Filipino client consolidated its small warehouse in Manila into two large distribution centers and replaced the fleet of forklifts at both locations from previously using lead-acid batteries to lithium-ion batteries. And make their facilities safer and cleaner. A detailed cost analysis shows that lithium batteries offer significant cost savings compared to LPG (propane) and lead-acid batteries. After more than half a year of impeccable performance of BSLBATT® lithium-ion batteries, the company’s forklifts have switched from lead-acid batteries to lithium batteries as the main power source for forklifts, which is an important step in improving distribution and sustainable development of 3PL. Founded in 2012, Lazada Group is Southeast Asia’s leading eCommerce platform. With a presence in six countries –Indonesia, Malaysia, the Philippines, Singapore, Thailand and Vietnam– BSLBATT® connected this vast and diverse region through our technology, logistics and payments capabilities. Today, they have the largest selection of brands and sellers, and by 2030, BSLBATT® aims to serve 300 million customers. In 2016, Lazada became the regional flagship of the Alibaba Group, and is backed by Alibaba’s best-in-class technology infrastructure. In early March 2023, Lazada Philippines consolidated some of its smaller existing warehouses across the Philippines into two large warehouses in Manila and Cebu, totaling 1.5 million square feet. “By consolidating our current footprint into two large fulfillment centers, we are gaining efficiencies to serve our customers more effectively,” Lazada Philippines said in a company PR press release at the time.
Toyota Material Handling earns Green Supply Chain Partner recognition
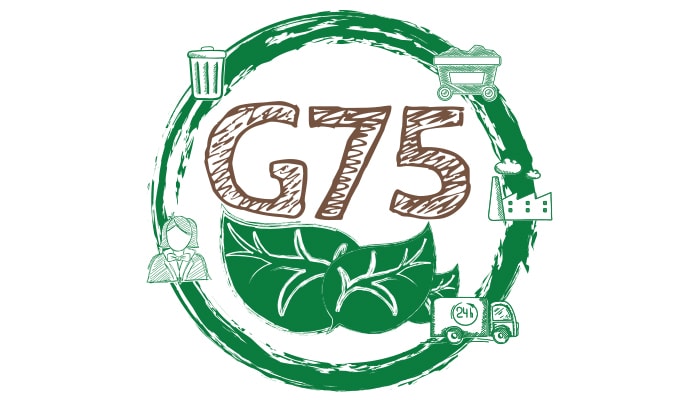
Toyota Material Handling was named a 2023 G75 Green Supply Chain Partner for leading the way in sustainability programs. The G75 list, curated annually by the editors of Inbound Logistics, recognizes 75 companies that go above and beyond to prioritize green initiatives and help global supply chains become more sustainable. “Being named a Green Supply Chain Partner is an honor for Toyota. One of our guiding principles is our commitment to creating a sustainable tomorrow. That commitment is part of our contribution to society, the communities we work in and our industry,” said Bill Finerty, Toyota Material Handling President and CEO. “Through our parent company, Toyota Industries Corporation, we have committed to contributing to Environmental Vision 2050, an ongoing company-wide leadership initiative to create a carbon-neutral society, a recycling-based company, harmony with nature and the promotion of environmental management.” In 2021, Toyota was recognized with the Indiana Governor’s Award for Environmental Excellence for its CO2 reduction projects. Since 2018, the company has reduced its CO2 emissions by 34% at its Columbus, Indiana, manufacturing facility through the implementation of energy reduction projects including LED lighting, air leak detection and repair, energy monitoring, weld fume collection systems, investment in wind energy certificates, and equipment upgrades and replacement. Collectively, these projects have contributed to an estimated CO2 savings of more than 13,000 tons since 2018, the equivalent of 3,000 gasoline-powered passenger vehicles driven for a full year. Toyota also recently increased its renewable energy ratio to 30% – through wind energy credits – to support the local renewable energy market. Toyota Material Handling has held zero-landfill status since 2004. Last fiscal year, the company diverted 579 tons of waste from landfills and sent 7,545 tons of materials to be recycled, recovered and reused. Local sustainability efforts, such as the company’s annual Environment Week, are planned and implemented by the Toyota Environment team. Through this team’s efforts, over 2,500 trees and 2,000 butterfly garden seed packets were planted in the local community last year to protect the local butterfly population and support biodiversity.
Bobcat Backyard Makeover contest winner announced with plans to include a wheelchair accessible garden
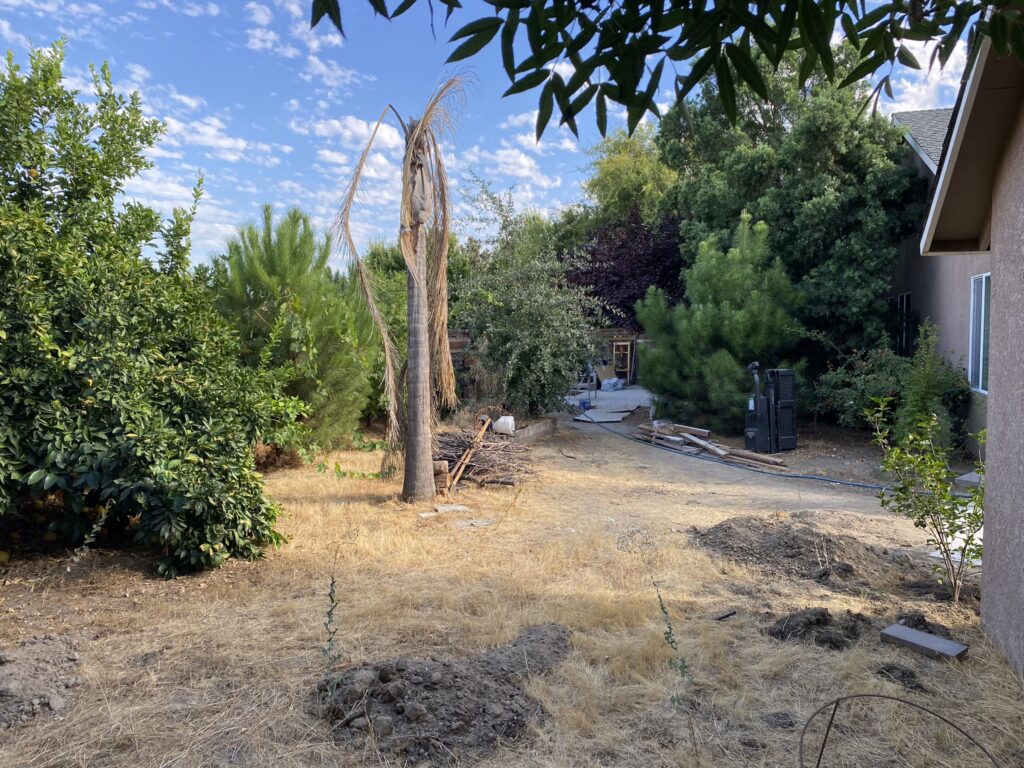
Bobcat fans voted to decide the winner of the $25K backyard makeover, and the opportunity to meet country music superstar Justin Moore The votes are tallied, and Bobcat Company is thrilled to announce the winner of the Bobcat Backyard Makeover Contest is Julie Rummer from Turlock, Calif. Julie will receive a $25,000 backyard makeover using Bobcat equipment to transform her backyard and garden. She will also have the opportunity to meet country music superstar – and Bobcat enthusiast – Justin Moore. Five finalists were selected based on the originality and creativity in their contest entry submission, as well as sharing the impact of how a backyard makeover would empower them to accomplish more. Julie’s powerful story received the most votes from the public. Julie survived an auto accident in 1995 that left her paralyzed as a quadriplegic. She is now wheelchair dependent, and often encounters challenges maneuvering in her backyard. While she loves to garden, the dirt and weeds often get stuck in her wheelchair. She would like to makeover her backyard and make it wheelchair accessible so she can be outdoors more often, which she says helps her forget her mobility limitations. “We are thrilled to announce Julie Rummer as the winner of the Bobcat Backyard Makeover Contest and can’t wait to bring her backyard dreams to life,” said Laura Ness Owens, vice president of global brand and communications and North American marketing. “At Bobcat, we are committed to empowering people to conquer their biggest challenges, and we are proud to help Julie in her pursuits by enhancing her backyard.” Julie and her husband love to entertain family, friends and neighbors at their home. They have dreamt of making improvements to their yard – both visually and to make it more wheelchair-friendly – but haven’t had the time or money. “Gardening is one of my biggest passions and being outdoors makes me forget my daily limitations. I am so incredibly grateful to Bobcat for this opportunity to create a completely accessible yard that will allow me the garden of my dreams,” said Julie. “I’ve been brought to tears at the thought of winning this contest. The kindness, love and support from my family, friends, neighbors and total strangers has filled my heart.” In addition to the backyard makeover, Julie will have the opportunity to meet Justin Moore as he joins the Bobcat team in the renovation project. Moore has been a brand ambassador for Bobcat Company since 2021. As an owner and operator of multiple pieces of Bobcat equipment, including a compact loader and compact tractor, Moore keeps busy on his 80-acre property in Arkansas. In addition to meeting Moore, Julie will work with an area landscape contractor and her local Bobcat dealer to plan and create her dream backyard. “Bobcat is known for empowering people and in my case, they are helping me to enjoy more sunshine and time in my happy place – my backyard,” said Julie. “Thank you for your generosity and commitment to lifting people up and helping me find a new path.”
Episode 415: Navigating the Future of Warehouse Automation with Rueben Scriven of Interact Analysis
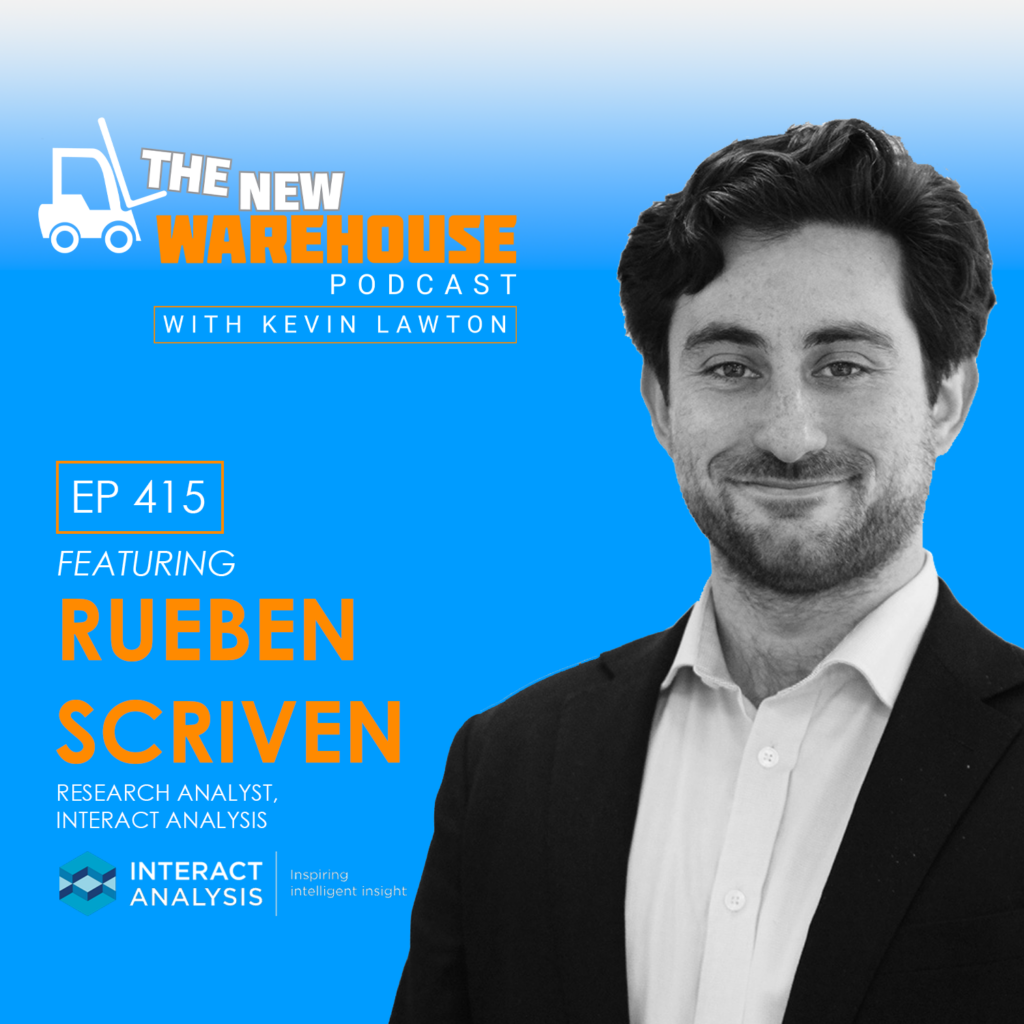
For this episode of The New Warehouse, we have the pleasure of hosting Rueben Scriven, Research Manager at Interact Analysis, an organization at the forefront of market intelligence for supply chain automation. Rueben delves deep into what’s happening in the warehouse automation market, the dynamics of orchestration platforms, and the emerging trends shaping the future. From the big behemoths like Amazon to small and medium enterprises (SMEs), automation touches every facet of the supply chain. This episode offers a treasure trove of insights for anyone invested in warehousing, so you don’t want to miss it. The Current State of the Warehouse – The Interact Analysis Perspective The warehouse, often seen as the backbone of the supply chain, has undergone a remarkable transformation over the past few years. According to Rueben, we’re at an interesting crossroads in 2023. Surge and Slowdown – The initial pandemic-induced boom in e-commerce led to a surge in new, large-scale automated warehouses. However, as interest rates rise and e-commerce growth stabilizes, new warehouse construction is slowing down and is expected to decline by 35% in 2023 compared to 2022. Focus on Efficiency – Rather than building new facilities, operators are now more interested in maximizing the efficiency of existing warehouses. This has increased demand for point solutions or automation technologies that solve specific operational challenges. The Rise of Modular Systems – Technological advancements have developed more modular systems. The separation between Original Equipment Manufacturers (OEMs) and system integrators is becoming increasingly prominent as fast-paced technological developments have led to partnerships to harness both strengths. SMEs Entering the Fray – While large corporations have been the traditional investors in warehouse automation, there’s a significant uptick in smaller and medium-sized businesses embracing automation. Innovative financial models like “Robotics-as-a-Service” (RaaS) and leasing options are making it more accessible for them. The American vs. European Landscape – While the U.S. market is highly concentrated, with the top eight investors accounting for more than 55% of automation investments, the European market presents a more diversified landscape. The bottom line? The warehouse of the future is undergoing a seismic shift. It’s not just about size or scale; it’s about innovative, efficient, and flexible operations. A Deep Dive into Labor Trends, ROI Shifts, and Software-Centric Strategies Automation is not just a buzzword; it’s a necessity. Staying ahead means understanding the latest trends, technologies, and market shifts in today’s rapidly evolving supply chain landscape. The increasing integration of robotics and automation within warehouses has led to discussions around the return on investment (ROI) and the impact of labor availability on operations. Labor Availability and ROI Shift – The focus shifted from traditional ROI calculations to labor availability during the pandemic. With labor becoming scarcer due to various factors, warehouse operators were more concerned with maintaining operations than optimizing cost savings. Rather than seeking immediate cost savings, warehouse operators placed a premium on ensuring that operations could continue unfettered. Rueben believes, “ROI became less of a factor, and continuing operations became the central thesis of investing in automation.” Labor Trends – The conversation also touched on labor trends, highlighting the dramatic increase in warehouse labor during the pandemic, followed by expectations of gradual declines and fluctuations in the coming years. Rueben adds, “During the pandemic, warehouse labor in the U.S. nearly doubled, going from 1.3-1.4 million to an increase of about a million. We expect a decline of 200,000 FTEs in 2023, things to remain flat in 2024, followed by a significant increase of 250,000 FTEs in 2025.” This labor availability dynamic plays a role in shaping automation adoption strategies. Software’s Role in Automation – While the visual impact of automation hardware is striking, the conversation underlines that software is at the core of automation systems. Software, specifically WES, is vital for coordinating and optimizing the movement of goods through automated systems. This shift in perspective from pure hardware to software-centric approaches highlights the importance of intelligent decision-making in warehouse operations. Rueben believes, “At the end of the day, the value of your software you generate is how intelligent it is. It’s how many decisions your software makes. The more decisions your software makes, the more intelligent it is, the more valuable it is, and the more profitable it is.” ROI: Don’t Call it a Comeback Rueben revealed an emerging trend. “ROI is creeping back into the picture,” he explains. While the urgency of labor availability reshaped ROI considerations, the tide seems to be shifting once again. Rueben shares, “Companies are still looking at how do I continue my operations, but they want to do so in a cost-effective way.” The pendulum swings back, albeit with an altered perspective on what constitutes a justifiable ROI. Rueben’s nuanced assessment points to a potential turning point. “We’re at a correction or a year,” he states, cautioning against viewing the shift as a mere return to pre-pandemic norms. The recalibration of ROI thresholds suggests a new era where companies are willing to invest more to embrace automation’s benefits. This metamorphosis prompts intriguing reflections on the ROI concept—what it means, what it means now, and the evolving strategies it shapes. Key Takeaways from Interact Analysis Automation, the Future’s Imperative: Understanding warehouse automation trends is crucial in a rapidly evolving supply chain landscape. Interact Analysis provides insights into the integration of robotics, ROI shifts, and labor dynamics, shaping the future of warehousing. Labor Dynamics and ROI: Labor availability now drives automation investment. Pandemic-induced labor shortages shifted the focus from traditional ROI calculations to ensuring operational continuity. Software’s Vital Role: Automation’s core lies in software, especially Warehouse Execution Systems (WES). Embrace software-centric strategies for intelligent decision-making. The New Warehouse Podcast EP 415: Navigating the Future of Warehouse Automation with Rueben Scriven of Interact Analysis
AAR reports Rail Traffic for the week ending August 26, 2023
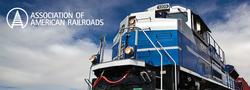
The Association of American Railroads (AAR) has reported U.S. rail traffic for the week ending August 26, 2023. For this week, total U.S. weekly rail traffic was 472,525 carloads and intermodal units, down 5.9 percent compared with the same week last year. Total carloads for the week ending August 26 were 226,679 carloads, down 3.9 percent compared with the same week in 2022, while U.S. weekly intermodal volume was 245,846containers and trailers, down 7.7 percent compared to 2022. Four of the 10 carload commodity groups posted an increase compared with the same week in 2022. They included motor vehicles and parts, up 1,500 carloads, to16,113; petroleum and petroleum products, up 1,373 carloads, to 9,921; and nonmetallic minerals, up 507 carloads, to 33,254. Commodity groups that posted decreases compared with the same week in 2022 included coal, down 5,449 carloads, to 68,828; grain, down 4,767 carloads, to 13,312; and miscellaneous carloads, down 887 carloads, to 8,789. For the first 34 weeks of 2023, U.S. railroads reported cumulative volume of 7,621,657 carloads, up 0.1 percent from the same point last year; and 8,074,700 intermodal units, down 9.2 percent from last year. Total combined U.S. traffic for the first 34 weeks of 2023 was 15,696,357 carloads and intermodal units, a decrease of 4.9 percent compared to last year. North American rail volume for the week ending August 26, 2023, on 12 reporting U.S., Canadian and Mexican railroads totaled 327,192 carloads, down 3.4 percent compared with the same week last year, and 327,499 intermodal units, down 8.9 percent compared with last year. Total combined weekly rail traffic in North America was 654,691carloads and intermodal units, down 6.2 percent. North American rail volume for the first 34 weeks of 2023 was 22,009,485 carloads and intermodal units, down 4.1 percent compared with 2022. Canadian railroads reported 83,877 carloads for the week, down 4.8 percent, and 69,342 intermodal units, down 15.8 percent compared with the same week in 2022. For the first 34 weeks of 2023, Canadian railroads reported cumulative rail traffic volume of 5,357,780 carloads, containers and trailers, down 3.2 percent. Mexican railroads reported 16,636 carloads for the week, up 12.9 percent compared with the same week last year, and 12,311 intermodal units, up 15.3 percent. Cumulative volume on Mexican railroads for the first 34 weeks of 2023 was 955,348 carloads and intermodal containers and trailers, up 5.1 percent from the same point last year. To view the traffic charts, click here.
Dematic announces 2023 STEM scholarship winners
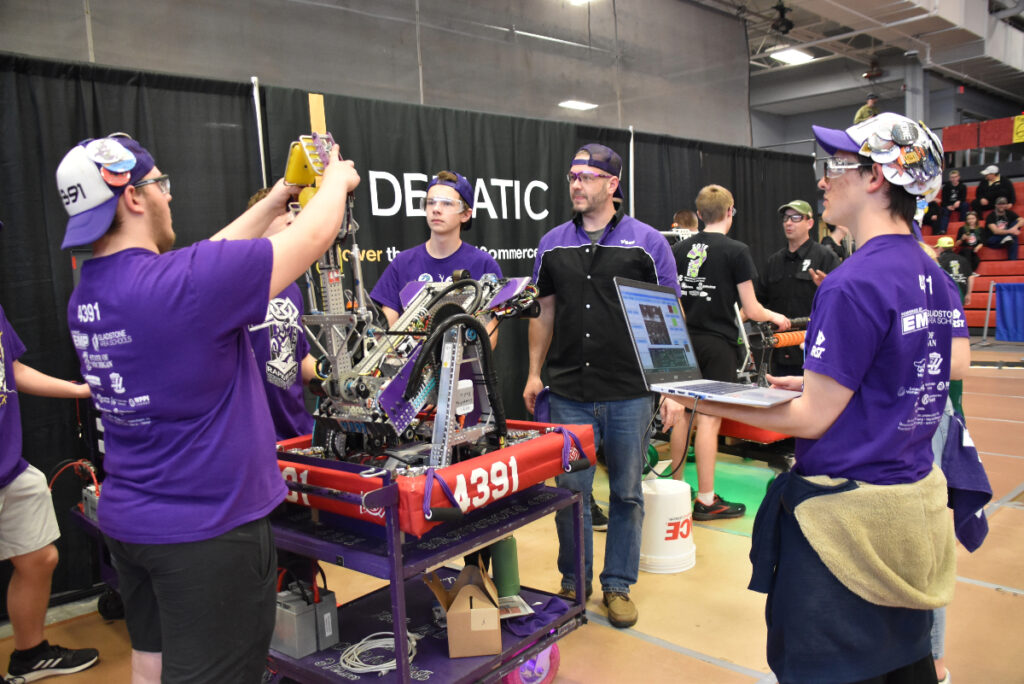
Dematic FIRST® Scholarships support students pursuing STEM (science, technology, engineering, and math) educations Dematic announces the 2023 recipients of its Dematic FIRST® Scholarship program, which honors students pursuing careers in STEM-related industries. Now in its third year, this scholarship program further demonstrates Dematic’s commitment to future leaders and innovators in supply chain and logistics by supporting corporate nonprofit, FIRST (For Inspiration and Recognition of Science and Technology). Scholarship honorees include students Jace Flansburg from Ramsey, Minnesota, and Lukas Goodworth from Goleta, California, who were each awarded $5,000 to put toward a post-secondary degree or technical certification. Dematic also awarded 10 additional $1,000 scholarships to Matthew Carroll, Miles Frewert, Rajat Gupta, Alydia Jura, Richard Louvar, Jack Meyer, Sebastian Romna, Navya Swali, Tanush Vanarase, and Andrew Yellin. “Each year, I am impressed by the remarkable talent showcased by these scholarship recipients,” says Mike Larsson, executive vice president, Americas, Dematic. “I’ve seen firsthand the impact that FIRST has on future STEM leaders, and this real-world experience is vital as they begin their careers. This was the most competitive group of applicants in the scholarship’s history, and the increased interest in the program underscores the importance of investing in STEM education to empower the next generation.” This year’s scholarship program received a 25% increase in applications from last year. Dematic executives reviewed all applications, selecting honorees based on their academic excellence and commitment to pursuing a future in STEM. The program requires applicants to provide their transcripts, a one-page essay discussing a future where humans and machines interact in the warehouse, and a letter of recommendation. In addition, they must have previously competed in a FIRST Robotics Competition or FIRST Tech Challenge. “My experience learning and competing with FIRST during high school is what cemented my interest in pursuing a STEM degree during college,” says Lukas Goodworth, mechanical engineering student at Westmont College. “I’m extremely honored to be awarded the Dematic FIRST Scholarship, and I’m grateful for the opportunities it provides as I continue my education at Westmont College and start my career.” Dematic employees volunteer their time and talent to local FIRST teams, providing mentorship and guidance to students. Within the last year, Dematic sponsored 17 FIRST teams throughout the country and donated $65,000 to the nonprofit to support students as they prepare for competitions and careers in STEM. Scholarship Winners (Name, Hometown, College/University Attending, Scholarship Amount): Jace Flansburg Ramsey, Minn. University of Minnesota at Twin Cities $5,000 Lukas Goodworth Goleta, Calif. Westmont College $5,000 Matthew Carroll Waukesha, Wis. University of Wisconsin at Platteville $1,000 Miles Frewert Carson City, Nev. University of Nevada at Reno $1,000 Rajat Gupta Cincinnati, Ohio Georgia Institute of Technology $1,000 Alydia Jura Ann Arbor, Mich. University of Michigan $1,000 Richard Louvar Redmond, Ore. Oregon State University $1,000 Jack Meyer Rogers, Ark. Texas A&M University $1,000 Sebastian Roman West Islip, N.Y. Purdue University $1,000 Navya Swali Prosper, Texas University of Texas at Austin $1,000 Tanush Vanarase Norwalk, Conn. University of Connecticut $1,000 Andrew Yellin Zelienople, Pa. University of Illinois Urbana-Champaign $1,000
H&E opens new branch in Wilmington
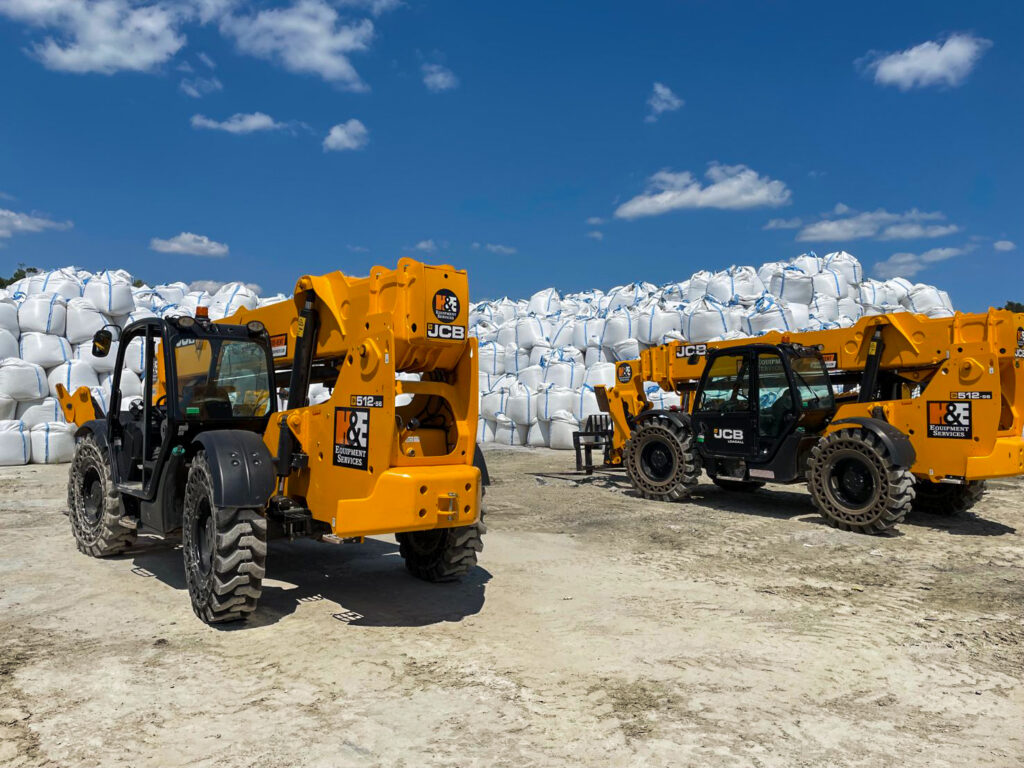
Effective August 30, 2023, H&E Equipment Services Inc. (H&E) announced the opening of its Wilmington branch, its 10th rental location in the state of North Carolina. Since the beginning of 2023, H&E has opened nine new branches across the country, with three of those in the Tar Heel State. The facility is located across from the Port of Wilmington at 851 Sunnyvale Drive, Wilmington, NC 28412-1151, phone 910 756-4100. It includes a fully fenced yard area, offices, and a repair shop and carries a variety of construction and general industrial equipment. “The location of our newest North Carolina branch gives us greater reach along the Atlantic coastline, both north and into South Carolina, and covers the southeastern portion of the state below our existing Raleigh facility. Adding more fleet in this area allows us to supply customers in Wilmington and up to Elizabethtown, Lumberton, and New Bern, to name just a few cities well within our service area,” says District Manager Justin Gnagy. “Our proximity to I-40 and highways 17, 74, and 421 is ideal and allows us to deliver equipment to job sites across the area quickly and efficiently.” The Wilmington branch specializes in the rental of aerial lifts, earthmoving equipment, telescopic forklifts, compaction equipment, generators, light towers, compressors, and more and represents the following manufacturers: Allmand, Atlas Copco, Bomag, Case, Club Car, Cushman, Doosan, Gehl, Generac Mobile, Genie, Hamm, Hilti, Husqvarna, JCB, JLG, John Deere, Kobelco, Kubota, LayMor, Ledwell, Lincoln Electric, Link-Belt Excavators, MEC, Miller, Multiquip, Polaris, Sany, Skyjack, SkyTrak, Sullair, Sullivan-Palatek, Tag, Towmaster, Unicarriers, Wacker Neuson, Yanmar, and others.
ORBIS to showcase integrated reusable packaging products at Pack Expo
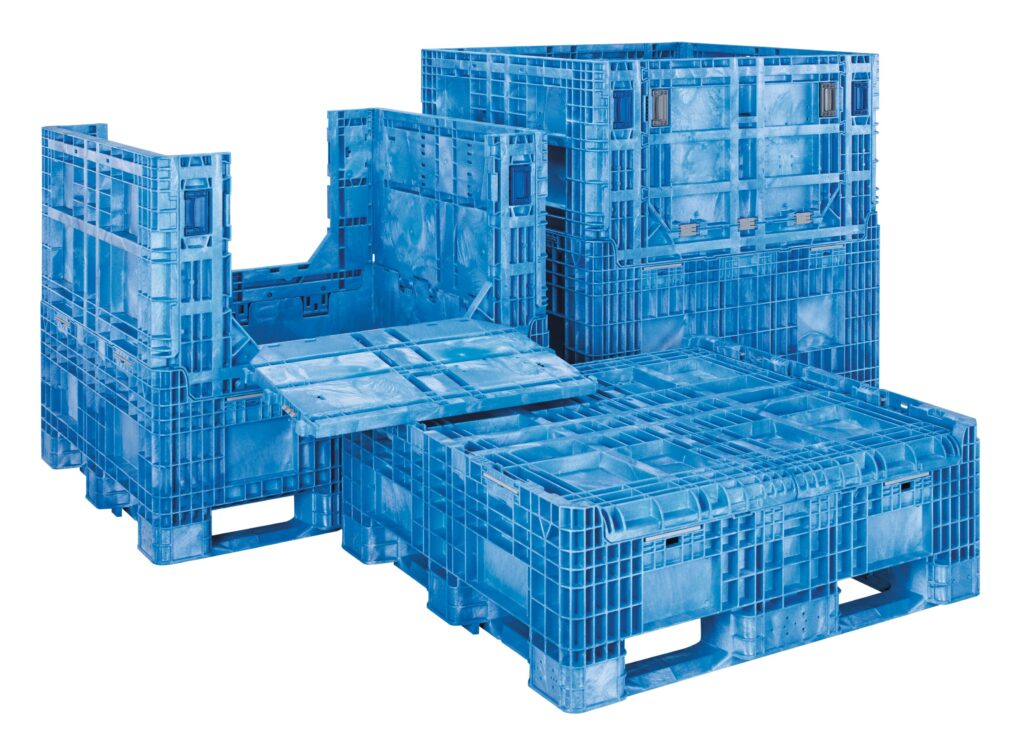
ORBIS® Corporation, an international provider in reusable packaging,will highlight the latest in reusable packaging solutions for a sustainable supply chain at this year’s PACK EXPO, Booth SU-8001. ORBIS offers a variety of packaging solutions, including reusable plastic pallets, totes, bulk containers and metal solutions, as well as services that help supply chains find efficiencies, improve the flow of product, increase sustainability and reduce costs. ORBIS is exhibiting at this year’s show held in Las Vegas, Sept. 11-13. The booth will highlight the role reusables play in driving the circular economy and will feature the importance of increasing supply chain sustainability by showcasing reusable packaging solutions that can be manufactured, used, reused and reprocessed without impacting the solid waste stream. With a diverse portfolio of integrated packaging, ORBIS looks to help its customers drive efficiency at every point along the supply chain, no matter the industry. ORBIS also offers a range of services to support companies as they make the switch from single-use packaging to reusable packaging. ORBIS Reusable Packaging Management offers a full range of packaging management services that extend the useful life of packaging for a more sustainable supply chain. Services include management, cleaning, sorting, asset tracking and analytics. Additionally, ORBIS has an engineering services team that conducts analysis and provides expertise needed to ensure a smooth conversion to reusable packaging, as well as a rapid return on investment. “We understand that industries are constantly evolving, and with this evolution comes new opportunities to add supply chain efficiency and sustainability,” said Lynn Hediger, vice president of product management at ORBIS Corporation. “Our integrated portfolio of products and solutions are designed to solve the unique challenges our customers face. From enhancing product flow to reducing costs, we’re here to provide tangible results. At this year’s PACK EXPO, we’re excited to showcase our unwavering commitment to shaping a more efficient, sustainable and resilient supply chain for industries around the world.” With sustainability, e-commerce and automation top of mind for today’s supply chain managers, the ORBIS booth will showcase a variety of packaging solutions and programs for primary packaging, retail, automotive and industrial operations, including: 280-trip 40×48 P3 pallet The 40-inch-by-48-inch P3 pallet is a durable, lightweight, stackable hygienic packaging solution that integrates seamlessly with manual and automatic material handling equipment. Designed with a low-profile 5.1” height, the P3 pallet optimizes truckload space and can be double-stacked in racking systems to maximize space. Optional steel reinforcements and grommets provide strength and improved stability to reduce load shifting and product damage. The plastic flow-through design reduces contaminant spaces and allows for easy cleaning. In FasTrack life-cycle analysis, the P3 reusable pallet completed 280 cycles, giving the P3 pallet over 25 times the life span of a standard whitewood stringer pallet. 44 x 56 food can pallet, sheets and top frame Streamline food and beverage can distribution with pallet systems. ORBIS offers a system that is comprised of a plastic pallet, divider sheets to layer between product, and a top frame for load stability. This system is compatible with many palletizers, depalletizers, automatic strapping/banding systems, conveyors, and pallet washing systems. All components are hygienic, easily cleaned and recyclable at the end of its service life. Attached-lid FliPak® containers ORBIS offers the largest selection of attached-lid totes used for split-case picking and distribution. ORBIS totes offer generous internal capacity, with streamlined designs for efficient transportation. These reusable plastic attached-lid containers take the place of corrugated shipping boxes for long-term packaging savings. In addition, all FliPak containers offer warehouse cleanliness by eliminating fiber and dust. FliPak totes stack when full and nest when empty, for the most efficient use of available space. BulkPak® HDMP Extended Height container system Based on the standard Automotive Industry Action Group footprint, these containers are designed and constructed to efficiently move, store and ship automotive, appliance and transportation equipment components. With weight capacities from 1,500 to 2,000 pounds, they are ideal for all types of product loads. The heavy-duty 48×45 HDMP Extended Height series offers 28 positions in a standard 53’ truck, enabling a gain of up to 20% in shipping efficiency and warehouse utilization. Reusable Packaging Management In today’s complex supply chains, it’s critical that packaging is available where and when you need it. ORBIS RPM services significantly reduce the time and effort required to track, retrieve, clean and inventory packaging assets in a wide variety of industries, including industrial, food and beverage products, and consumer packaged goods. The ORBIS RPM team works to analyze supply chains holistically to determine the best management program. By using data, ORBIS handles inspection, sorting and even product refurbishment to ensure the supply chain is as efficient as possible. Packaging Life-Cycle Assessments ORBIS helps companies calculate the impact reusable packaging can have on the environment. Using life-cycle assessments to compare reusable and single-use packaging, ORBIS applies data-driven analysis to help customers reduce their overall environmental impact in terms of greenhouse gas emissions, solid waste and energy usage. ORBIS will conduct packaging assessments at the booth during the show. At PACK EXPO 2023, ORBIS will offer two presentations: Measuring the Environmental Impacts of Reusable Packaging in the Circular Economy, using Packaging Life-Cycle Assessment (PLCA) Data; Sept. 11; 11:00 a.m. Speaker: Breanna Herbert, product manager Location: RPA Pavilion (South Upper Hall) Best Practices for Making the Switch to Reusable Pallets in Your Supply Chain; Sept. 12; 10:30 a.m. Speaker: James Riegleman, product manager Location: RPA Pavilion (South Upper Hall)
Port of Long Beach again exceeds Small Business Enterprise goals
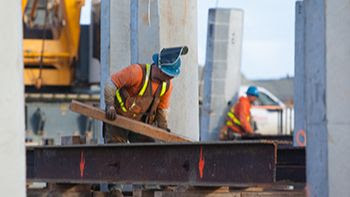
Efforts by the Port of Long Beach to include more small businesses among its contractors and vendors are raising awareness of opportunities in doing business with the Port. Nearly half of Port funds spent on contracts applicable to the Port’s Small Business Enterprise Program goals in the most recent fiscal year went to buy services and materials from companies defined as “small business enterprises” and “very small business enterprises.” The 48.9% participation by small and very small businesses in contracting for which small business enterprise participation is measured translates to $54.2 million in spending on construction projects, consulting services, event planning, and other supplies and services for the Port, which is the Harbor Department of the City of Long Beach. The Port’s goal for small business enterprise participation in applicable contracting is 27%. The Port’s utilization of small businesses for which participation is measured has risen steadily in recent years. Fiscal year 2018 saw a 30.2% rate, 2019 was 33.2%, 2020 was 34.4%, and 2021 was 40.8%. “We are demonstrating our commitment as a public agency to offer more opportunities to small businesses to provide the goods and services necessary to operate the Port,” said Bonnie Lowenthal, Vice President of the Long Beach Board of Harbor Commissioners. “This practice diversifies the contractor pool and increases competition for Port contracts, resulting in additional value to the public.” “In the course of improving and operating the Port, we offer significant contracts every year. We need to ensure every qualified company, large or small, at least has the opportunity to participate and grow with us,” said Port of Long Beach CEO Mario Cordero. The thresholds of annual receipts and number of employees for classification as a small business enterprise vary widely by industry, as determined by the U.S. Small Business Administration. Very small business enterprise eligibility is equivalent to the state of California’s microbusiness designation: businesses with $5 million or less in annual gross sales, averaged over the last three fiscal years, or manufacturers with 25 or fewer employees. All aspiring contractors for the Port apply for posted contracts on the Port’s “Planet Bids” online system, where the businesses can pre-register and check back for posted bids. Go to polb.com/businessopportunities and click on “Access the POLB Vendor Portal.” The complete small business enterprise utilization report for fiscal year 2022 is available at www.polb.com/sbe.
Creating a Resilient Company Culture: Navigating change and thriving amidst challenges
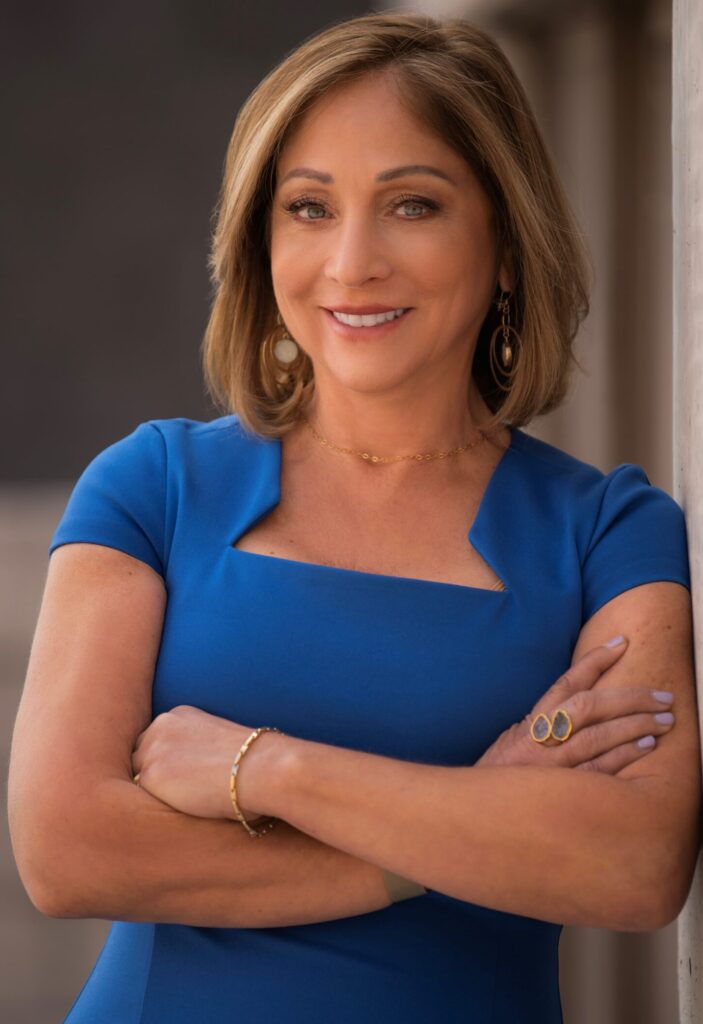
In an era marked by immense volatility and complexity, characterized by technological advancements, business consolidations, fierce competition, and economic fluctuations, you may find yourself in an unprecedented time of change. The aftermath of the pandemic continues to linger, with burnout, stress, and overwhelm persisting among individuals and teams. Amidst this tumultuous landscape, the challenge is this: How can organizations emerge stronger from the trials of recent years? How can they cultivate a culture that thrives, adapts, and responds effectively to the unpredictable? The answer lies in fostering an emergent culture – one characterized by change management prowess, response agility, and a positive environment with fulfilled employees. Understanding Culture When more than two people come together, whether as a couple, a family, or a company, they form a human system. Within this system, culture serves as the driving force or energy. Culture possesses the power to create and destroy, providing guidelines for interaction, conflict resolution, motivation, and progress. The objective of examining and shaping organizational culture is to channel the collective energy of individuals into a productive force – one that mirrors the synchronicity found in natural phenomena, such as the coordinated movements of a school of fish or flock of birds. This is called an emergent culture. Influencing Culture Effective impact on company culture entails understanding and influencing the energy inherent within the human system. To initiate this process, focus on the following areas: Start With The Leader All culture begins with the CEO; the leader of the organization. What is their vision? Who are they as a leader? What are their values? Are they operating and living congruent with all of those markers, no matter how challenging or stressful the circumstances may be? Having a CEO who can answer those questions clearly and can live in alignment with them consistently is the foundation on which a company’s culture gets built. If the CEO is frazzled, overwhelmed, and in survival mode, that is going to set the tone for the entire organization. Whatever energy the CEO brings to the company and to their life will be the energy that other people pick up on and assimilate to in order to fit in and make it. Thus, the CEO must be conscious. They must be awake and aware of what they’re emanating through their words and their actions. They must ensure that they have a clear vision, bolstered by positive moods and inspiring language that rallies people around their vision and engages them into action. Human systems are guided by behaviors, beliefs, actions, what’s said, what’s unsaid – all of that equates to the energy of the human system, and energy is culture. So, what kind of culture is the CEO creating? Cultivate the Leadership Team The leadership team further propagates cultural attributes throughout the organization. Behaviors exhibited by this team tend to cascade down to various departments. Similar to the CEO, leadership must demonstrate consciousness and accountability for their actions. This includes acknowledging their role in shaping the culture and undertaking personal growth to support a healthy, high-performance human system. By focusing on the following key elements, the leadership team can contribute to a thriving culture: Achievement. The company knows what they’re here to do, why they’re doing it, and how they’re measuring it. Organizational achievements are individual achievements, and vice versa. Achievements are specific, measurable, attainable results that are bound in time. Self-actualization. Each person is conscious. They know what their strengths and weaknesses are, and they’re responsible for them and the impact they have on others. They’re doing their own development and personal work just like the CEO is. Affiliation. People are partnering, collaborating, sharing ideas, and problem solving on an interdepartmental level. Cross-functional teams are committed to the noble cause and vision for the organization and are coming up with ways to problem solve together to fulfill the vision. Humanistic Managers. Managers authentically care about their people. They are aware of what’s going on in their employees’ lives, what their goals are, and how they want to grow. When an employee knows to their core that their manager has their best interests at heart and they want them to thrive, difficult conversations to improve performance can happen. Mentorship, coaching, and caring for people comes with humanistic management, and it supports employees who grow and thrive. Assess Environment and Employees Employee behavior provides insights into the prevailing environment. Key considerations include whether they experience autonomy, trust, and support in their roles. Ask these questions to assess the environment that your employees are navigating: How well do employees handle changes and upsets and challenges in the market? Do people feel the freedom and trust to share new ideas, take risks and have space to fail? Is there space in the time at work to ideate, innovate and co-create? Are the meetings inspirational and motivating or just a laundry list of getting things done? Is everyone clear on what the noble cause is? Is the right architecture or systems in place for people to work effectively together? Is the leadership team dismantling anything getting in the way of employees taking the ball and running with it? If there’s a problem, are the employees the ones to solve it? Are people being given the autonomy they need? Are people held accountable to their agreements and promises and measures? Can you have difficult conversations? Achieving Resilience Through Emergent Culture In times of uncertainty, organizations with the ability to adapt and pivot harness their power. Such resilience hinges on a healthy human system and a shared commitment to the company’s purpose. Leadership needs to exemplify responsibility, optimism, and collaborative problem-solving across departments to overcome obstacles and realize the company’s vision. This approach cultivates an emergent culture, capable of navigating challenges effectively. While creating an emergent culture demands considerable dedication, care, and focus, the rewards are boundless. With a culture founded on change management skills, response agility, and employee fulfillment, organizations can not only weather storms but also soar to new heights. About
ASSP recruiting presenters for Safety 2024 in Denver
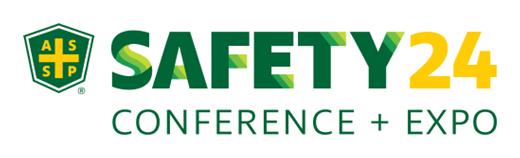
The American Society of Safety Professionals (ASSP) is seeking a diverse group of occupational safety and health professionals to join its team of presenters now being formed for its Safety 2024 Professional Development Conference and Exposition. The world’s oldest professional safety organization is an industry leader in promoting best practices that make safety an integral element of business. Safety 2024 will be held Aug. 7-9 in Denver. Presentations should address key occupational safety and health issues as well as emerging matters and innovations relevant to the profession. Speakers have until Sept. 13 to submit their proposals to contribute to next year’s event. “Our annual conference is a dynamic learning and networking experience that helps attendees expand their knowledge, find solutions to challenges and learn about the latest trends,” said ASSP President Jim Thornton, CSP, CIH, FASSP, FAIHA. “Whether you’re an industry newcomer or seasoned practitioner, there’s always something more to learn to better protect workers at your organization.” All speaker proposals for Safety 2024 will be reviewed by ASSP’s Conference Planning Committee. The group’s evaluations consider a range of factors such as a speaker’s presentation skills and experience, desirability of the topic, and alignment with conference objectives. Presentations are in person for one hour, including 15 minutes for questions. The committee will consider no more than two proposals per speaker. “Presenting at our conference is a terrific opportunity to contribute to the career development of your colleagues while advancing our profession,” Thornton said. “It’s truly a rewarding experience.” Successful applicants will be notified by March 1, 2024. For more information on submitting a proposal to present at Safety 2024, please visit http://www.assp.org/call-for-presenters.
CASSEL Inspection exhibits Shark MultiSense Metal Detector at PACK EXPO
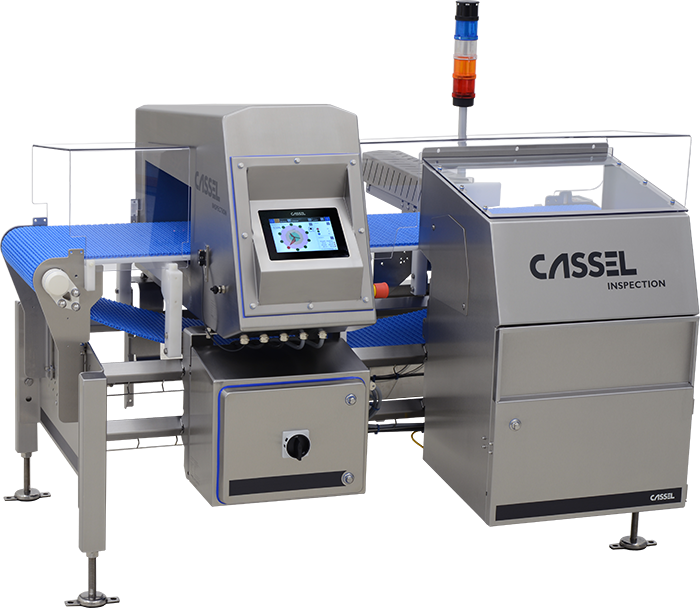
CASSEL Inspection, a custom provider of inspection solutions for food production, plastics, pharmaceuticals and more, will be on the exhibit floor at PACK EXPO Las Vegas 2023 with booth highlights featuring the breadth and depth of the company’s line of inspection products, including configurable and customizable solutions in metal detection, X-ray inspection, and checkweighers. Among the inspection system highlights included will be a demonstration of the latest technology advancements in detection capabilities – the Shark MultiSense Metal Detector. CASSEL Inspection booth highlights will include: Shark MultiSense Metal Detector – Preview of the innovative new metal detection technology featuring: Simultaneous multi-frequency High sensitivity Automated operation Intelligent signal processing Automated set-up Auto-learn capabilities Improved probability of detection in challenging applications METAL SHARK BD Metal Detector + C80 Checkweigher Combo – Technically-advanced inspection system built to meet demands for accuracy and data transmission for requirements of the food industry. High-sensitivity metal detection in dry, moist, salty, or frozen goods with 3D detection, easy set-up, and intuitive operation for packaged and unpackaged goods.Easy-to-use settings, low maintenance conveyors, and see one of our reject variants live at the show. METAL SHARK GF Metal Detector – A gravity-feed, small drop-through metal detector. XRAY SHARK XD38: X-ray inspection for packaged food or non-food products to detect high-density materials like metal, ceramic, stone, and some plastics. CASSEL Inspection representatives will be available throughout the show to discuss the latest inspection technologies and how they make quality assurance processes safer and more efficient. PACK EXPO Las Vegas 2023 kicks off on Monday, September 11, and runs through Wednesday, September 13, at the Las Vegas Convention Center in Nevada. CASSEL Inspection will exhibit in booth 6378. “Our team is eager to meet with PACK EXPO attendees to learn about their individual challenges and requirements, and explain how our package inspection solutions can help enhance quality control to safeguard our customers’ investments and brand reputation,” said Paul Payerle, US Commercial Leader for CASSEL Inspection. “This year holds particular excitement for us as we will offer an exclusive demonstration of the next generation of detection technology, the Shark MultiSense Metal Detector.”
Jungheinrich acquires all shares in robotics company Magazino
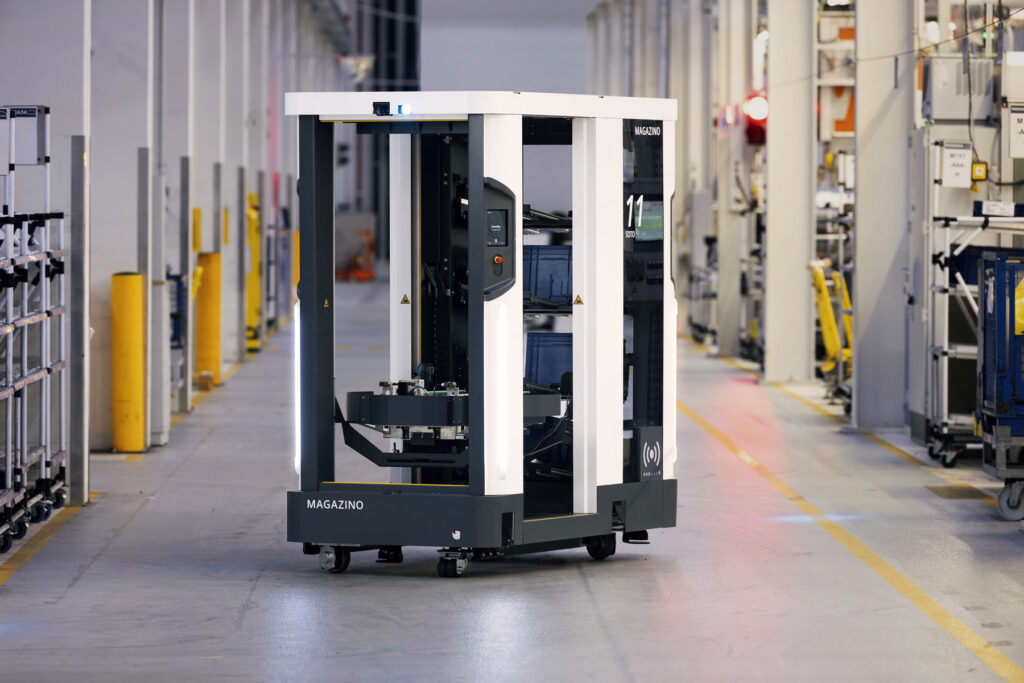
Hamburg-based intralogistics pioneer Jungheinrich is fully taking over Magazino, a Munich-based robotics specialist. In addition to its shareholding, which has existed since 2020 and was increased to 21.7 percent in 2022, Jungheinrich is acquiring all shares held by the founders as well as the previous co-shareholders, a.o. Cellcom, Fiege Logistik, and Körber. The transaction took effect immediately upon signing this week. The parties have agreed not to disclose the purchase price. Magazino will continue to grow as an independent company within the Jungheinrich Group and also in particular make use of the Group’s global sales and service network. The company will remain under the management of both Co-Founders Frederik Brantner and Lukas Zanger as well as Dr. Moritz Tenorth. For Jungheinrich, the full takeover of Magazino is another strategically important step towards strengthening its automation expertise. Founded in 2014, Magazino employs around 130 people and has one of the largest mobile robotics development teams in Europe. The company offers a powerful technology platform that enables logistics robots to also operate in a mixed human-machine environment. As a result, robots are able to intelligently navigate in the warehouse as well as selectively pick up and transport needed objects. Magazino’s system and robots are already in use in warehouses of various industrial customers, online retailers and logistics service providers. The control software for robots in complex logistics environments is also already integrated in Jungheinrich’s EAEa, a fully automated low-lift truck that was initially presented at this year’s LogiMAT intralogistics trade fair. For Jungheinrich, the merger is an ideal addition as part of the expansion of its business with automated and autonomous vehicles. Going forward, Magazino’s software and development expertise will be even more closely integrated into Jungheinrich’s product development. Magazino gains access to Jungheinrich’s international sales and service network and becomes part of a broad portfolio of intralogistics products and solutions. The Magazino brand will be retained and the company will continue to work with external integration partners and customers. “We’ve been working closely with Magazino for several years now, we are on par with each other and communicate well. The chemistry is simply right. Now we are taking the next logical step in our cooperation and acquire Magazino in full”, said Dr. Lars Brzoska, Chairman of the Board of Management of Jungheinrich. “Magazino is a successful company with a very good management and top experts in the market. It has outstanding software competencies and has developed solutions that have the potential to shape the future of intralogistics in the long term. In the Group, we will leverage these competencies to jointly drive the further development of innovative automation and robotics solutions.” Frederik Brantner, CEO and Co-Founder of Magazino: “The need for warehouse automation is growing constantly. By steering robots in this complex environment, we have developed a unique expertise that we want to further expand. We would like to thank our previous investors for the trust they have placed in us and for the many years of successful cooperation. They have supported us strategically and financially to date and have made a significant contribution to the further development of our business. Together we have laid the foundation for the next chapter in Magazino’s success story. With Jungheinrich, we will continue to extend our intralogistics technology leadership and expand internationally.”