Global Economic Outlook and Plastics Trade
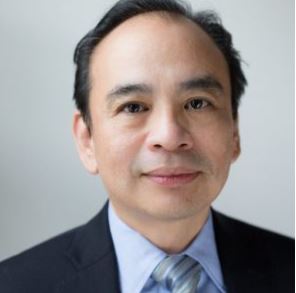
Global trade prospects are significantly influenced by the global economic outlook. The state of the global economy plays a crucial role in shaping international trade dynamics and determining the growth and opportunities for industries and economies around the world. For the U.S. plastics industry, the world serves as the market. With the International Monetary Fund revising its global economic outlook, this has implications for the global plastics trade. The recent revision by the International Monetary Fund (IMF) indicates that world output is expected to grow by 3.0% this year, which represents a 20-basis point increase from its earlier forecast in April. However, it is essential to note that this upward revision still suggests a weaker global economic growth compared to the previous year, 2022. As we enter the second half of 2023, businesses planning for the next six-to-twelve-month cycle must carefully consider the economic outlook for 2024. According to the IMF’s growth revisions, the global economy is anticipated to remain relatively stable from 2023 to 2024 but indicating a sideways movement. This projection has implications for the global plastics trade as well. While the industry can still expect growth opportunities in 2023, the subdued economic outlook for 2024 might pose some trade-related concerns. Global growth matters for trade. The IMF recently revised its forecast for world trade volume for goods and services, lowering it from 2.4% to 2.0% for the year 2023. This indicates that global trade is expected to be less robust than previously projected for this year, suggesting some economic challenges and uncertainties in the international trade landscape. However, there is optimism for the following year, as the IMF anticipates an upturn in global trade volume, revising the forecast for 2024 from 3.5% to 3.7%. This indicates a potential recovery and growth in trade opportunities for industries worldwide, including the U.S. plastics industry. In contrast, the World Trade Organization’s projection in April suggested a slower growth rate of 1.7% for global merchandise trade in the current year, highlighting the cautious outlook for international trade dynamics. The trade data from January to May indicate a decline in the dollar value of plastics materials, resin, and plastics products exports, which decreased by 5.4% compared to the same period last year. Similarly, imports in the same category experienced a more substantial decrease of 20.3% during the same period. These declines align with the trend observed in the monthly Import Price Index for plastics and related articles, which has been consistently decreasing year-on-year during the first half of 2023. It is noteworthy that the Index experienced an increase starting in January 2021 and remained elevated for twelve months before the current decrease. Uneven plastics trade outlook Despite the upward revision in the global economic outlook, the growth of the plastic trade is likely to be uneven. Based on the PLASTICS Global Plastics Ranking®, China, the U.S., and Germany hold the top three positions in the global plastics trade. However, their economic performance is projected to differ in 2023. The U.S. economy is expected to grow by 1.8% this year, while China’s is anticipated to experience stronger growth at 5.2%. In contrast, Germany is projected to face a decline of 0.3% in its economic output in 2023. This variation in economic growth among these key players will impact their respective plastic trade volumes and dynamics. For the U.S. plastics industry, two crucial export markets to watch are Mexico and Canada. Mexico, which is the largest U.S. export market for plastics and plastic products, is now projected to grow by 2.6% this year—an upward revision from the previous forecast of 1.8% growth. Similarly, Canada, the second-largest market for U.S. plastics and plastic products, is expected to grow by 1.7%, up from the previously expected 1.5% output increase. However, looking ahead to 2024, with a flat global growth prospect and Mexico and Canada projected to grow at 1.5% and 1.4%, respectively, the U.S. plastics industry may experience weaker export growth compared to this year. Nevertheless, trade volume could be influenced by lower prices. If the U.S. dollar remains stable but below its highs from 2022, U.S. export, to some extent, could experience a global advantage.
June 2023 Orders of Manufacturing Technology reach $411.3 million; and slide from peak continues but orders remain above historical average
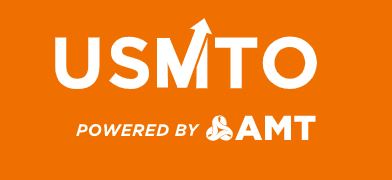
New orders of manufacturing technology totaled $411.3 million in June 2023, according to the latest U.S. Manufacturing Technology Orders Report published by AMT – The Association For Manufacturing Technology. June 2023 orders increased 12.6% over May 2023 but fell 1.7% below orders in June 2022. This brings total orders through the first half of 2023 to nearly $2.5 billion, about 13% below the total for the first half of 2022. “Orders of manufacturing technology have continued their downward trend since peaking in the second half of 2021; however, for perspective, they remain above historical averages,” said Douglas K. Woods, president of AMT. “Even in non-IMTS years, the majority of orders tend to come in the second half of the year. Despite some headwinds, including fears of a recession, it would seem reasonable that manufacturing technology orders could outperform some of the more pessimistic expectations if we return to that historical trend.” Job shops, the largest customer segment, only increased spending by 4.2%, well under the industry growth of 12.6% from May to June 2023. They also decreased the number of units ordered, while the industry remained about flat. “Job shops tend to be smaller to medium-sized businesses, and the effects of economic uncertainty, coupled with higher interest rates, have begun to take a toll, causing some to delay capital investments,” said Woods. There was one surprising bright spot despite high interest rates and the ever-looming fear of a coming recession: Manufacturers of automotive transmissions have been noticeably increasing investment in manufacturing technology. “Investments on this scale show how manufacturers are preparing for a prolonged transitional period from internal combustion engines to electric vehicles,” said Woods. “Moving toward electrification means facing numerous supply and logistical hurdles, from the sourcing of elements to grid reliability. Auto manufacturers recognize that until these challenges are overcome, demand for internal combustion engines will justify further investment.” Year-to-date orders for manufacturing technology from the automotive transmission and powertrain parts manufacturing sector are at the second-highest level since the first half of 2015.
OTTO Lifter wins Gold Stevie® Award in 2023 International Business Awards®
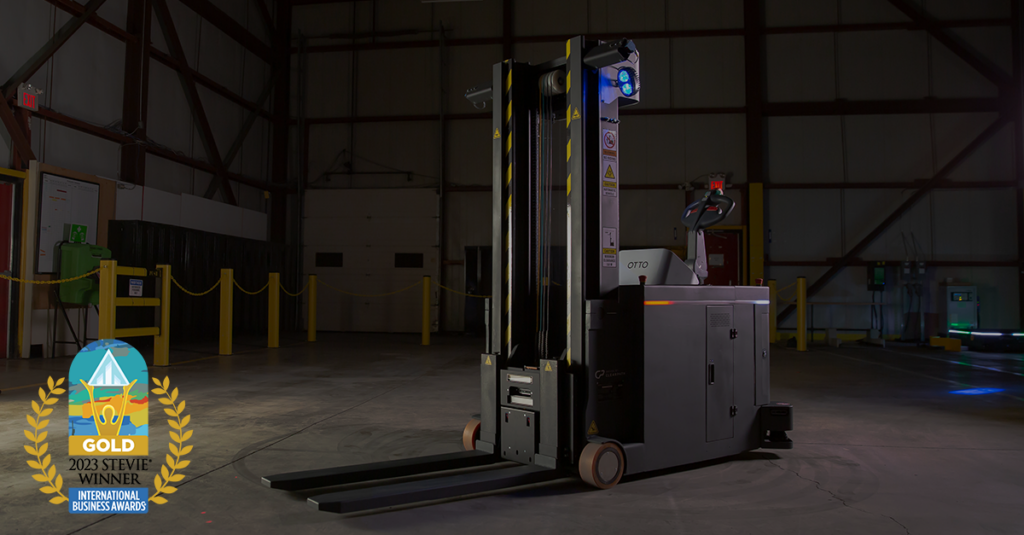
OTTO Motors, a provider of autonomous mobile robots (AMRs), announced that their autonomous forklift, OTTO Lifter, has been recognized as the winner of a Gold Stevie® Award in the Manufacturing Solution category in The 20th Annual International Business Awards®. OTTO Lifter, the world’s smartest autonomous forklift, was awarded for its advancement in autonomous material handling solutions, addressing the challenges of labor shortages, safety, and productivity in manufacturing and warehouse facilities worldwide. Built on OTTO Motors’ fourteen years of industry-leading robotics experience and over four million production hours, OTTO Lifter seamlessly navigates traffic and obstacles, predictably and precisely delivering materials to the right place at the right time. Stevie Award judges commended the solution for its “remarkable innovation, safety, and market performance.” OTTO Lifter was also recently named the SupplyTech Breakthrough Material Handling Solution of the Year as well. “OTTO Lifter was only introduced to the manufacturing industry last year, but it is already transforming and unlocking new material handling workflows, solving top challenges for manufacturers worldwide, and winning prestigious awards,” said Jay Judkowitz, Vice President of Product at OTTO Motors. “We are honored that our autonomous forklift was recognized for its outstanding performance with a Gold Stevie Award.” The International Business Awards are the world’s premier business awards program, recognizing high-achieving organizations and executives from around the world. With more than 3,700 nominations across organizations in over 60 countries, Stevie Award winners were determined by the average scores of more than 230 executives worldwide who participated in the judging process in June and July. “Nominations to the IBAs get better every year, and this year’s class of Stevie winners is the most impressive yet,” said Stevie Awards president Maggie Miller. “The winners have demonstrated that their organizations have set and achieved lofty goals. We congratulate them on their recognized achievements, and look forward to celebrating them on stage in Rome on 13 October.”
Port of Long Beach awarded $2.72 million security grant
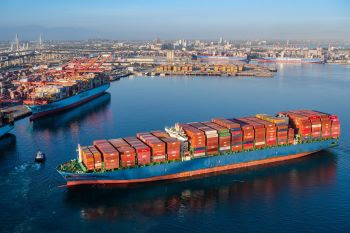
The Department of Homeland Security has awarded a $2.72 million grant aimed at enhancing security at the Port of Long Beach to ensure the safe and efficient movement of cargo in the wake of an emergency. As a recipient of the agency’s Port Security Grant Program, the Port of Long Beach will use the funding to modernize its core security network, strengthen existing security systems and enhance resiliency and business continuity in the event of a disaster. Officials welcomed the grant announcement as an opportunity to improve the Port’s ability to prepare for, respond to and recover from large-scale emergencies. “The ports are the backbone of our local economy, and vital to the nation’s trade,” said Long Beach Mayor Rex Richardson. “By investing in our security measures, we are not only protecting the movement of valuable cargo but also securing the livelihoods of millions of people who depend on the Port’s operations.” “Ports are the economic engine of our community and our country,” said U.S. Rep. Robert Garcia. “As mayor, I saw the threats we face and the importance of federal assistance. This funding will protect our community and our economy, and I will continue to go to bat for our unique needs.” “This grant will strengthen our ability to protect the workforce and critical infrastructure responsible for moving cargo valued at more than $200 billion annually,” said Port of Long Beach CEO Mario Cordero. “We thank the Department of Homeland Security for helping enhance the security and resiliency of our operations in the event of an emergency.” “I would like to thank our federal partners for providing us with the funding to elevate our security measures and enhance our ability to detect and respond to threats within the Port,” said Long Beach Harbor Commission President Sharon L. Weissman. “This grant will help ensure the safe and reliable movement of goods and secure our position as a leader in trans-Pacific trade.” The Department of Homeland Security’s Port Security Grant Program awards funding to state, local and private-sector agencies for security projects that protect port infrastructure from terrorism, improve maritime security risk management and strengthen security mitigation protocols. Specifically, the $2.72 million grant awarded to the Port of Long Beach will be divided across four projects: Maintenance for closed-circuit television and wireless security systems, including more than 750 cameras keeping watch across the Port. Support for existing security access control systems and information-sharing platforms connecting commercial agencies and law enforcement agencies at the federal, state, and local levels. Expansion of a cloud-based resiliency network in the event of terrorism, a cybersecurity attack, a natural disaster or other emergency outages. Modernization of the Port’s core security network to protect the integrity of the systems monitored by its security headquarters, the Joint Command and Control Center.
H&E opens new branch in Kings Mountain NC
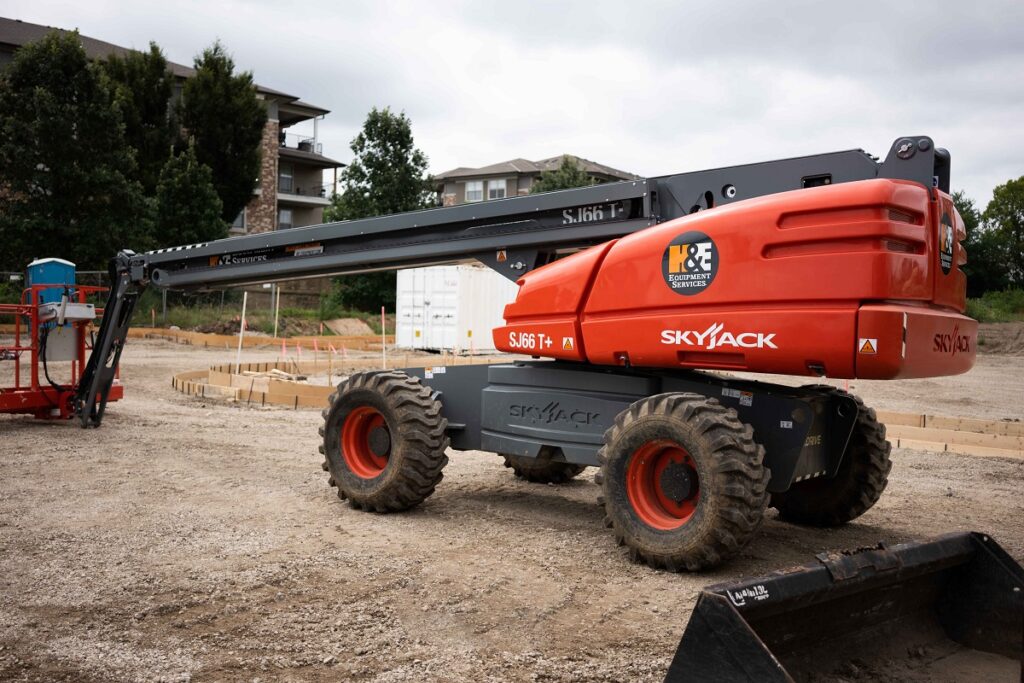
Effective August 14, 2023, H&E Equipment Services Inc. (H&E) announces the opening of its Kings Mountain branch, its ninth rental location in the state of North Carolina and its fourth in the greater Charlotte vicinity. Since the beginning of the second quarter of 2023, H&E has opened eight new branches across the country, with two of those in the Tar Heel State. The facility is located at 612 Canterbury Road, Kings Mountain, NC 28086-9601, phone 980-341-1800. It includes a fully fenced yard area, offices, and a repair shop and carries a variety of construction and general industrial equipment. “The Charlotte metropolitan area is one of the fastest growing regions in the country, and we are bringing additional fleet and resources to serve customers there. Our existing North Charlotte, Charlotte and Statesville branches blanket the eastern and northern portions of the area, so we’ve strategically placed our new branch in Kings Mountain to reach farther west and southwest, including into upstate South Carolina,” says Branch Manager Rob Kendrick. “Our proximity to I-85 and Hwy. 74 is ideal and allows us to deliver equipment to job sites across the metro area quickly and efficiently.” The Kings Mountain branch specializes in the rental of aerial lifts, earthmoving equipment, telescopic forklifts, compaction equipment, generators, light towers, compressors, and more and represents the following manufacturers: Allmand, Atlas Copco, Bomag, Case, Club Car, Cushman, Doosan, Gehl, Generac Mobile, Genie, Hamm, Hilti, Husqvarna, JCB, JLG, John Deere, Kobelco, Kubota, LayMor, Ledwell, Lincoln Electric, Link-Belt Excavators, MEC, Miller, Multiquip, Polaris, Sany, Skyjack, SkyTrak, Sullair, Sullivan-Palatek, Tag, Towmaster, Unicarriers, Wacker Neuson, Yanmar, and others.
AIT Worldwide Logistics debuts new global headquarters in Chicago suburbs
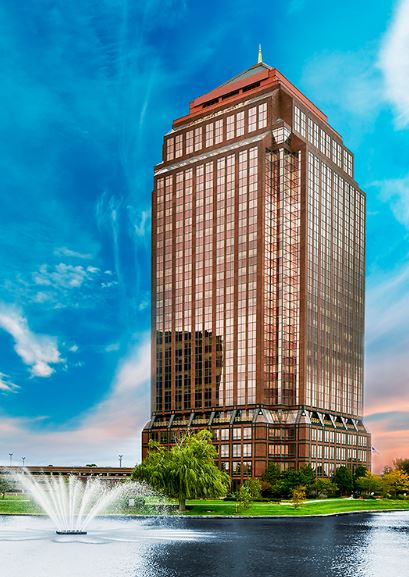
Corporate teammates for supply chain solutions provider AIT Worldwide Logistics recently moved into a new global headquarters at 2 Pierce Place in Itasca, Illinois. Previously, AIT’s shared services teams were based out of multiple Itasca facilities, including 701 Rohlwing Rd., a single-story building and warehouse that had been shared with the company’s Chicago station since 1997. According to AIT’s Chairman and CEO, Vaughn Moore, the move was spurred by the organization’s exponential growth and emergence as a global logistics powerhouse. “After more than 40 years in business, and immense expansion to more than 110 locations across Asia, Europe and North America, we’re fortifying our roots in the Chicago area,” Moore said. “This modern, highly visible location is a true manifestation of our global brand, and it provides our corporate staff with both the space and resources they need to best support our customers and teammates around the world.” Moore added that the new location is a major investment in AIT teammates’ on-site work experience. “Working together in this state-of-the-art office space allows us to be much more collaborative, enabling faster, real-time reactions,” he said. “2 Pierce Place also provides the additional space we need to accommodate the future growth of our shared services teams.” AIT’s global headquarters occupies multiple floors of the iconic 25-story suburban tower. Standing at 395 feet, it is the second-tallest building in Illinois outside the Chicago city limits. From its modern lobby to the tenant lounge, game room and outdoor patio, 2 Pierce Place offers popular on-site amenities, including a fitness center, walking trail, a full-service deli serving breakfast and lunch, grab-and-go dining options, and on-site catering services. Team members from accounting, claims, finance, global business systems, global compliance, human resources, imaging, information technology, legal and marketing are stationed on newly remodeled high-rise floors with conveniences including a private game room, coffee bars, sit-stand workstations, and multiple conference rooms equipped with state-of-the-art audio-visual capabilities. In the coming months, the remaining Chicago area AIT teams in Itasca and Wood Dale (including dedicated food logistics and life sciences locations) are planning to move into a unified multi-service facility in the nearby suburb of Palatine. This new joint office and warehouse space is under construction. Meanwhile, AIT Truckload Solutions will continue to serve customers out of their current location at 55 W. Monroe St. in Chicago. Conveniently located near the intersection of Interstate 290 and the Elgin-O’Hare Expressway, AIT’s new global headquarters is easily accessible from O’Hare International Airport: AIT Worldwide Logistics 2 Pierce Place, Suite 2100 Itasca, IL 60143 Tel: +1 (630) 766-8300
Dorner & Garvey combine expertise to unveil the AquaGard GT Conveyor in booth C-1455 at PACK EXPO 2023
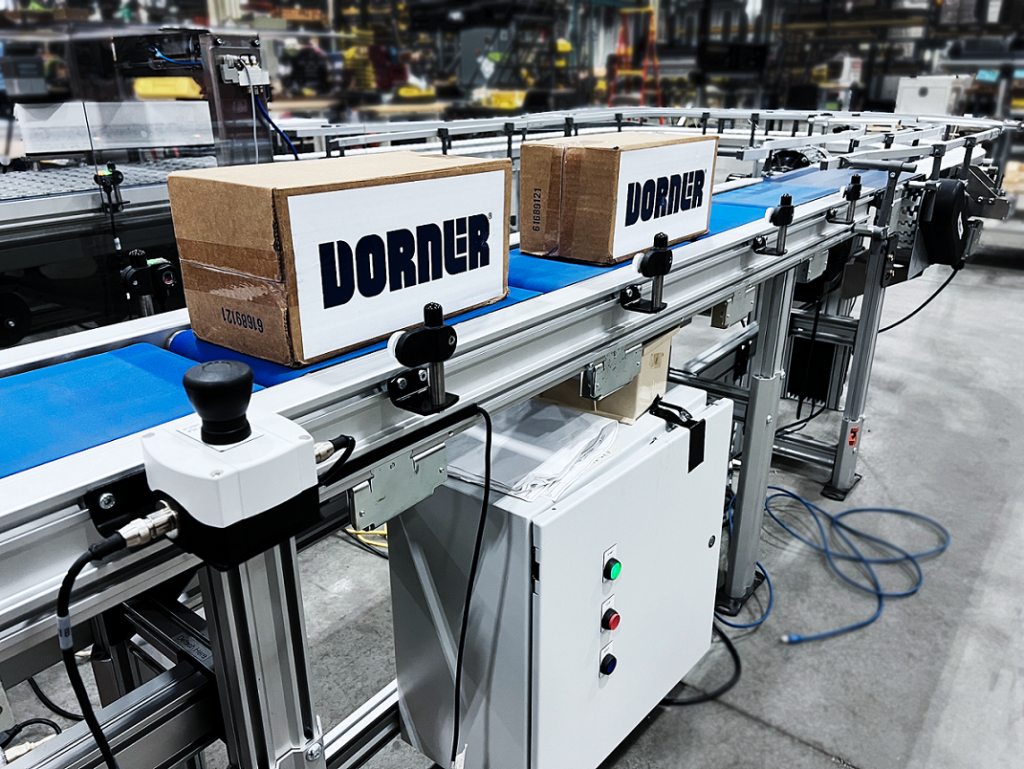
If you are looking for a sure bet in Las Vegas, it’s the AquaGard GT, a new conveyor system that combines the strengths of Dorner and Garvey®, both Columbus McKinnon brands. The AquaGard GT leads an impressive lineup of conveyors in action in booth C-1455 at PACK EXPO 2023, September 11-13, at the Las Vegas Convention Center in Las Vegas. Dorner is a global manufacturer in conveyor automation system design, manufacturing, and integration. Garvey is a recognized leader in the conveyor and accumulation industry, serving customers of all sizes primarily in the food, beverage, pharmaceutical and household product industries. The AquaGard GT is a meticulously designed infeed and outfeed conveyor ideal for accumulation-type applications to prevent bottlenecks in industries such as packaging, bottling, dry food processing, and part handling. All components (except motors) are either stainless steel or FDA-approved plastics, which are ideal for operating in environments that require wipe-down or occasional washdown cleanings of the conveyor. The AquaGard GT integrates features and benefits such as powered transfer units, flush side tails, and pre-engineered transfer modules, among others that in-house machine builders cannot match. The conveyor is competitively priced and comes with a short 10-day lead time. At PACK EXPO 2023, the AquaGard GT will be operating in a fully functional loop with Infinity™ and Bi-Flow™ accumulation tables from Garvey. A versatile machine, the Infinity uses Garvey’s patented technology to accumulate and sort unstable products at high speeds into a single or multi-lane configuration. The Bi-Flow uses opposing conveyor movement to create a buffer for product accumulation in a small footprint. The loop also includes Dorner’s FlexMove Helix and Wedge conveyors which allow vertical product movement to maximize a smaller footprint. This demonstration illustrates the seamless integration Dorner and Garvey can bring to industries worldwide to maximize production in accumulation-type applications. Show attendees will see a second operating loop highlighting the DCMove belted and the 2700 Medium Duty conveyors. DCMove conveyors provide a streamlined approach to conveyance, which more industrial-focused material handling applications call for in their equipment. Helping achieve that goal is the conveyor’s painted steel frame, which includes the right amount of strength and agility for material handling applications. The second portion of this loop is the 2700 Medium Duty Conveyor, which adds an extra boost in load capacity to carry heavier products for various industrial automation and packaging applications including palletizers, multi-lane processing, case- and tray-handling and end-of-line packaging. A third operating loop linking two 3200 Series conveyors with Activated Roller Belt (ARB) technology, a belted Edge Roller Technology (ERT), a FlexMove Side Acting Merge Module and a Powered Side Guide showcases Dorner’s package-handling capabilities. Conveyors with ARB technology are perfect for moving boxes and packages in merging, diverting and aligning applications. They use low- and high-friction angled rollers within the belt to help smoothly guide and align items. ERT platforms employ Dorner’s patented Edge Roller gear-drive technology to move product smoothly for pacing packages, bags and boxes. The FlexMove Side Acting Merge Module is a fully mechanical design to easily merge products from two lanes into one on FlexMove conveyors. Finally, Dorner’s Power Side Guide positions a compact 2200 Series belted conveyor on its side to create a simple pneumatic side plow guide that can pull or eliminate gaps as needed. PACK EXPO attendees can see several other conveyor systems on display, including a fourth operating loop highlighting Dorner’s sanitary platforms. The AquaPruf VBT (Vertical Belt Technology) conveyor, designed to move bulk products in straight-up 90° sanitary applications, features a proprietary staggered sidewall belt designed to increase pocket capacity and improve product release. The AquaGard LPZ Conveyor can be configured with one or two fixed angle points that allow the conveyor to accommodate a variety of height and angle requirements. Lastly, the AquaGard Modular Belt Conveyor features a center bearing to eliminate friction. It can carry a heavier load and allows four curves to be driven by a single motor, which saves valuable floor space as the conveyor can make tight turns around existing machinery and equipment without being hindered by extra motors. Finally, Dorner will feature the versatility of the low profile 2200 Series in its own operating loop. The 2200 Series features a stronger, single-piece frame design that reduces the overall number of needed stands. The frame is a Universal T-Slot compatible with industry-standard hardware, making attaching accessories and guiding fast and simple. The 2200 Series loop moves product through 90° turns as it diverts items quickly and accurately into various lanes with the use of Precison Move technology. For pallet movement Dorner will showcase the Shuttle ERT250, which uses rollers to move pallet conveyors smoothly with no friction. Rounding out the show will be a demo of Columbus McKinnon’s newest acquisition montratec and its intelligent monorail shuttle system which will be expanding in more markets soon.
Olvera announces goals for Port of Long Beach
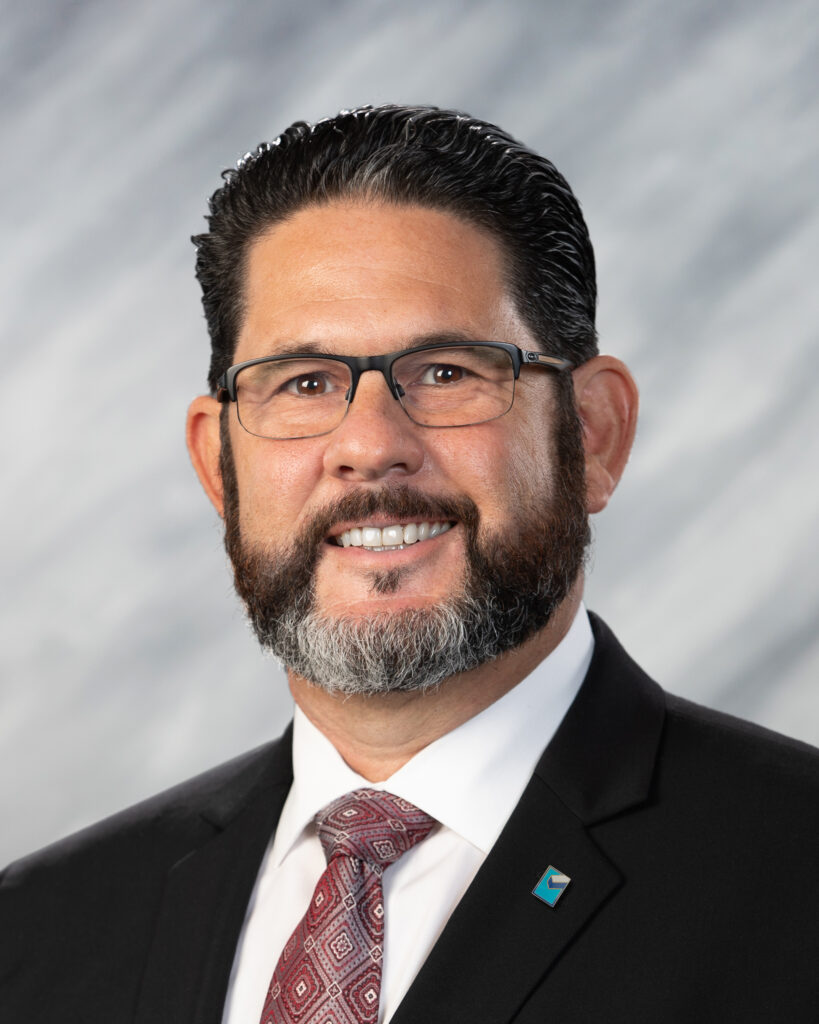
Bobby Olvera Jr. began his term as Harbor Commission President on Monday by accepting the gavel and announcing his goals to increase community engagement and connect industry partners with local schools for the year ahead at the Port of Long Beach. Olvera, a fifth-generation longshore worker currently serving as International Vice President (Mainland) of the International Longshore and Warehouse Union, said he intends to strengthen the Port’s ties to nearby neighborhoods most impacted by port operations, particularly those in West Long Beach and in North Long Beach. He succeeds Harbor Commissioner Sharon L. Weissman, who served as the Board’s president for the past 12 months. “Some of the most important work we do involves community engagement and encouraging students to participate in our education and workforce programs,” said Olvera, who was appointed to the Board in 2020. “I look forward to working with my colleagues on the Harbor Commission and Port staff to build the workforce of tomorrow and secure our role as the premier gateway for trans-Pacific trade.” “I would like to congratulate President Olvera for being selected by colleagues to navigate the Harbor Commission through the year ahead,” said Port of Long Beach CEO Mario Cordero. “We look forward to working with him to improve the lives of people living near the Port and bolstering our education partnerships.” As head of the Board that sets policy for the Port, Olvera said he also wants to increase the Board’s support of the Port’s education outreach programs such as the Academy of Global Logistics at Cabrillo High School in West Long Beach and the ACE Academy at Jordan High School in North Long Beach. Additionally, Olvera said he plans to work with industry partners to donate new tools and equipment for shop classes at local high schools.
Dematic names Mohamed Vaid Senior Vice President Business Solutions P&L, Americas
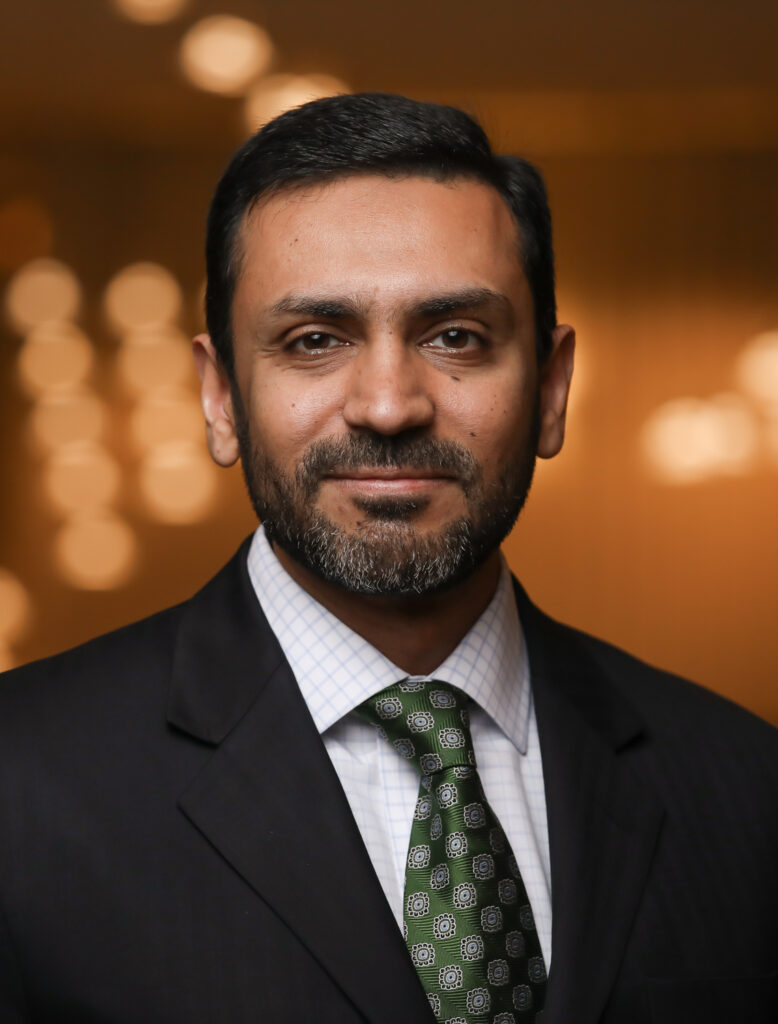
Dematic announced the appointment of Mohamed Vaid to Senior Vice President, Business Solutions Profit & Loss (P&L), Americas. In this role, Vaid will oversee the project execution team for the Americas region, deliver excellence in project execution for customers, and partner closely with all functions within the organization to enable future success for Dematic Americas. “Mohamed was a natural choice for this position, as he’s exemplified strong leadership within the organization over the past four years,” says Mike Larsson, Executive Vice President, Americas. “With a strategic mindset and an unwavering dedication to success, his appointment ensures that Dematic will continue to excel and deliver exceptional projects and solutions for our customers.” Prior to this new role, Vaid served as Dematic Americas’ Senior Vice President, Customer Service, where he facilitated steadfast operational benefits for Dematic customers and ensured support throughout the entire lifecycle of their operations. “I am excited to take this next step in my journey with Dematic, now managing a new team with strategic project execution at the forefront of all my work,” says Vaid. “The execution phase of our work is the lengthiest and most critical part of our duties, and I look forward to further supporting our customers throughout the process.” Vaid joined Dematic in 2019 as Vice President, Global Solution Development. Before joining the organization, he garnered extensive professional experience driving global revenue with cross-functional teams over the course of his career, including executive roles with General Electric, United Technologies, ALJ Toyota, and Saudi Cable Company. A graduate from Harvard Business School, Vaid holds an MBA and a bachelor’s degree in commerce, finance, and management information systems from the University of Virginia. He is a certified Six Sigma Black Belt for excellence in professional leadership. Vaid will continue to be based out of Dematic global headquarters in Atlanta.
Caster Concepts introduces TWERGO® Xtreme Casters for Aerospace and AGV Applications
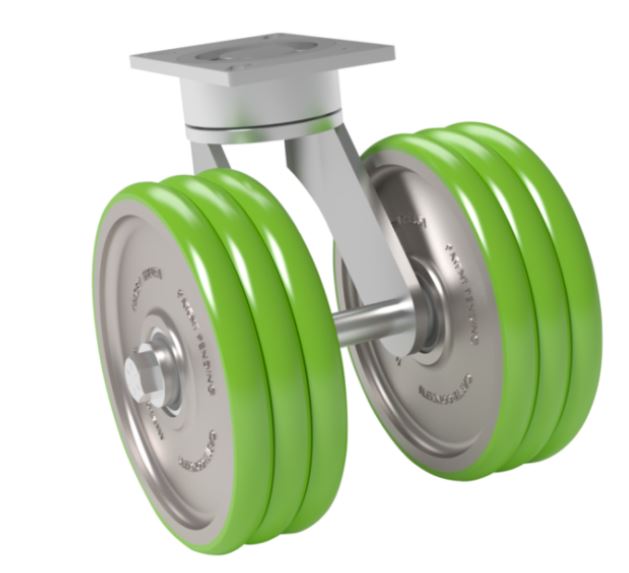
Caster Concepts Inc., a global manufacturer in industrial caster solutions, has introduced the TWERGo® Xtreme caster for heavy duty material handling demands in the Automated Guided Vehicle (AGV) and Aerospace sectors. Tested to move more than 20,000 pounds, these new casters improve safety, maneuverability and workload efficiency in many applications. Based on extensive testing and early customer experiences (example), TWERGO® Xtreme casters are a significant improvement when compared to traditional products used in these applications — reducing push/pull forces by up to 50%. These improvements enable a range of benefits for manufacturers, including significantly expanded operating range for AGVs and reduced push force for manual cart operations at higher loads. “Manufacturers in these sectors are always looking for ways to move heavier loads faster and more efficiently,” said Doug Backinger, vice president of sales at Caster Concepts. “Optimizing productivity while maintaining the highest possible safety standards is a constant challenge. Our new TWERGO® Xtreme casters helps manufacturers boost load factors without sacrificing safety — saving hours each week.” TWERGO® Xtreme casters are the next generation of Caster Concepts’ patented TWERGO® caster blueprint. Its distinct barbell design coupled with a tapered tread is the key to curbing caster wheel friction. This makes a palpable difference in minimizing push/pull forces, whether the application involves manual transportation of assembly components or AGV operations. Additionally, when combined with the company’s HALO Drive AGV solutions, manufacturers can potentially eliminate overhead cranes and benefit from increased cart maneuverability.
US Cutting Tool Orders totaled $217.3 million in June 2023, bringing Year-to-Year total pp 23.5% from 2022
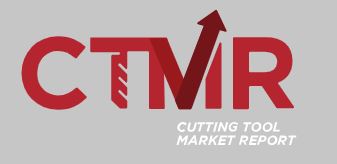
June 2023 U.S. cutting tool consumption totaled $217.3 million, according to the U.S. Cutting Tool Institute (USCTI) and AMT – The Association For Manufacturing Technology. This total, as reported by companies participating in the Cutting Tool Market Report collaboration, was up 3.2% from May’s $210.6 million and up 23.5% when compared with the $175.9 million reported for June 2022. With a year-to-date total of $1.24 billion, 2023 is up 17.4% when compared to the same time period in 2022. These numbers and all data in this report are based on the totals reported by the companies participating in the CTMR program. The totals here represent the majority of the U.S. market for cutting tools. “U.S. cutting tool orders continue to rise after rebounding from a soft April. Second quarter sales were strong versus 2022 sales for the same time period,” commented Jeff Major, president of USCTI. He added, “Hiring pressures appear to have eased, which aids in the reduction in backlogs and drives business. There is optimism that the remainder of the year will remain positive.” “The cutting tool industry continues to record strong sales growth compared to 2022,” stated Bret Tayne, president of Everede Tool Co. “Much of this may be attributable to certain durable goods sectors, such as transportation and defense, that are core drivers of cutting tool consumption. If some of the critical customer categories are outperforming the overall economy, the cutting tool industry may enjoy better-than-anticipated growth.” The Cutting Tool Market Report is jointly compiled by AMT and USCTI, two trade associations representing the development, production, and distribution of cutting tool technology and products. It provides a monthly statement on U.S. manufacturers’ consumption of the primary consumable in the manufacturing process – the cutting tool. Analysis of cutting tool consumption is a leading indicator of both upturns and downturns in U.S. manufacturing activity, as it is a true measure of actual production levels. Historical data for the Cutting Tool Market Report is available dating back to January 2012. This collaboration of AMT and USCTI is the first step in the two associations working together to promote and support U.S.-based manufacturers of cutting tool technology. The graph below includes the 12-month moving average for the durable goods shipments and cutting tool orders. These values are calculated by taking the average of the most recent 12 months and plotting them over time.
Bis Henderson launches “Breathing Space” campaign
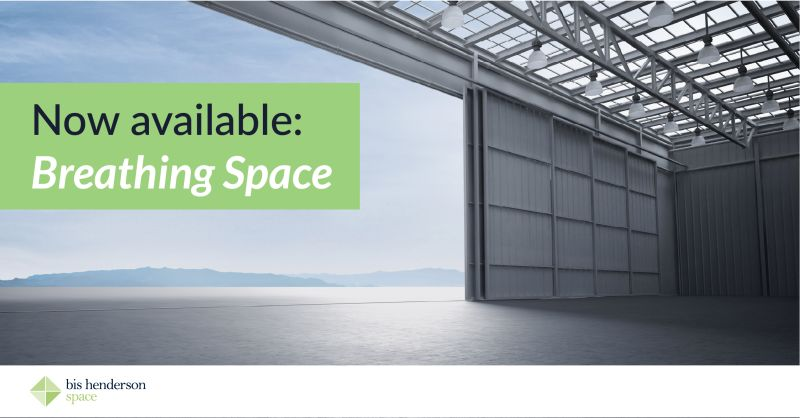
Supply chain and logistics specialist, Bis Henderson Space, has launched “Breathing Space”, a major multi-media campaign promoting its innovative Managed Warehouse Solutions concept. “Breathing Space” reflects the freedom of a ‘Pay-as-you-need’ pallet storage model that allows businesses to flex their storage capacity according to immediate needs – giving organisations the agility to grow and respond swiftly to new opportunities with less exposure to risk. Scaleability is intrinsic to this concept, as anywhere from 5 to 50,000 pallets can be accommodated on a ready-to-go basis. The marketing initiative is aimed at promoting the benefits of flexible storage to businesses of all sizes that require additional storage space to secure growth or to provide greater agility at peak. The model allows businesses to de-risk their operating model by hiring space only as and when they need it – avoiding the commitment and constraints of a long-term leasing agreement. Over 4.5 million sq ft of “Breathing Space” is available and readily accessible across the UK and Ireland – from Greater London, the South West, Wales and the Midlands… to Northern England, Humberside, Yorkshire and Scotland. Space when and where businesses need it. The Breathing Space marketing campaign driving awareness for this concept, is the most extensive multi-media promotion undertaken by Bis Henderson Group to date, involving all the key digital channels, including paid search, LinkedIn, video content and digital advertising – devised and coordinated by award-winning brand development agency, Studio North, and supported by specialist logistics media relations agency, AMA PR. Steve Purvis, Managing Director at Bis Henderson Space, says: “Most industrial, manufacturing or retail businesses now need to be highly agile in the way they respond to changes within their markets, whether that be moving quickly to take advantage of new opportunities as they arise, or scaling back to save on costs. And that means storage space needs to flex with the business. Our solution gives businesses the ability to flex to market needs without major capital commitments to worry about or long-term leases and complex contracts – including stamp duty and dilapidation costs at the end – creating valuable ‘breathing space’ for decisionmakers. With this concept, we provide complete flexibility, in terms of number of pallets to be stored, locations across the country and the length of time they’re on the books – fully managed warehouse solutions, with expert support throughout.” He adds: “Long-leases, big overheads and onerous clauses can stifle growth. Our flexible solution gives businesses the breathing space to grow.”
Add efficiency with Edson’s Case Management Solutions in Booth C-3833 at Pack Expo 2023
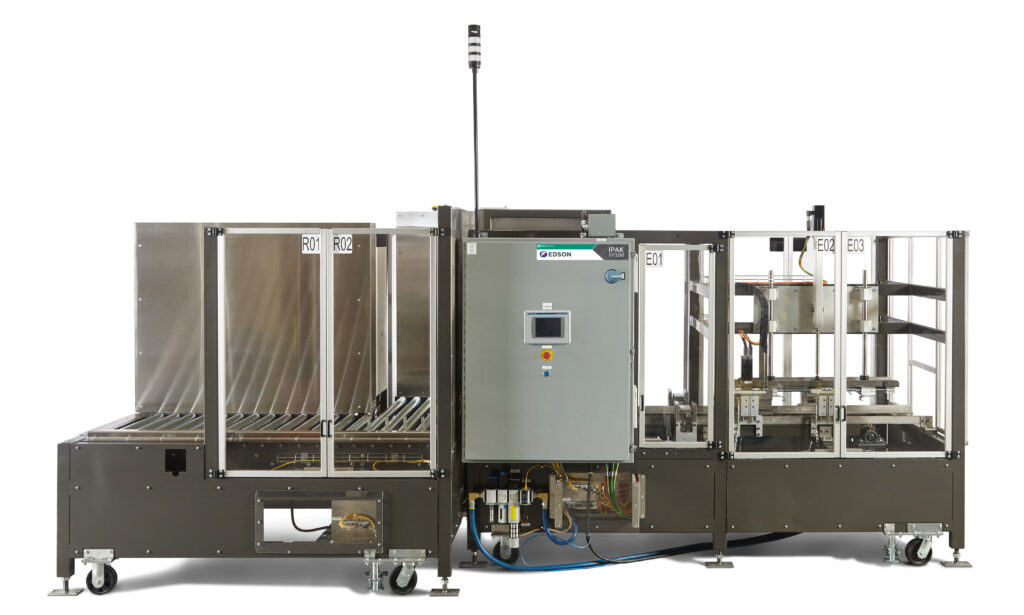
Edson, a ProMach brand, is taking its decades of proven case packing expertise and applying it to help automate other parts of the packaging process. Edson will be demonstrating its strengths with RPC erecting and automatic product settling in booth C-3833 at PACK EXPO 2023, September 11-13, at the Las Vegas Convention Center. Edson has been an industry-leading manufacturer of case and tray packing solutions for the converted paper, diaper, and nonwoven markets for decades. Now, they’re utilizing their automation expertise to help other industries. The RP-200 Fully Automatic RPC Erector uses high speed servos to accurately and consistently form trays, making it an ideal solution for produce, protein, and several other industries that use RPC style trays. The RP-200 is a compact machine that takes up very little floor space. It can be easily moved within a facility or to different locations where the work is centered. This is especially helpful in the produce industry where picking and processing is seasonal and tends to occur in different locales. The machine features an ergonomic easy load, single feed-in magazine to facilitate fast loading with minimal handling. The RP-200 can accommodate both standard and custom tray sizes with speedy, easy changeovers. Edson will also be showcasing their WRC Rotary Case Settling Conveyor, which is designed as an on-the-go settling solution that simultaneously transports and settles cases. The advantage the WRC brings to customers is an all-in-one settling and conveyance solution that can transport up to 100 cases per minute without slowing production. The machine brings added versatility as it can operate as a standard conveyor with the settling function turned off. The compact WRC is available with either a 3 or 6-foot-long option. To see how the RP-200 Fully Automatic RPC Erector and the WRC Rotary Case Settling Conveyor can add speed, efficiency, and safety to your packaging process, visit Edson in booth C-3833 at PACK EXPO 2023, September 11-13, at the Las Vegas Convention Center.
Mitsubishi Logisnext Americas launches next-generation Lift Link® Telematics solution for North American Market
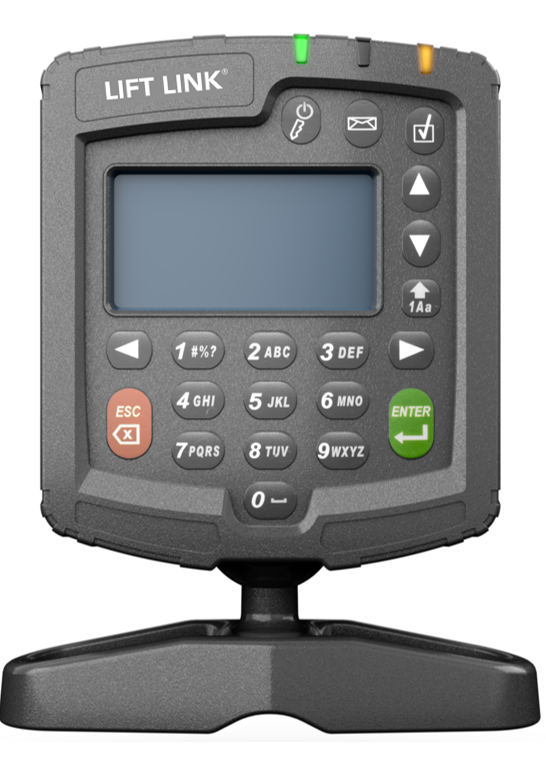
Mitsubishi Logisnext Americas, one of the world’s leading manufacturers and providers of material handling, automation and fleet solutions, announced the launch of Lift Link®, a full-featured telematics solution for material handling equipment. With Lift Link, businesses receive access to precise and actionable data delivered in real-time, allowing them to more effectively operate their fleet, while maximizing uptime and usage. The Logisnext Lift Link telematics solution offers comprehensive fleet-wide insights and is compatible with various types of material handling equipment – from warehouse products to electric and internal combustion forklifts. This versatile solution equips customers with an array of capabilities, including the ability to: Manage/limit forklift usage to only authorized operators. Use existing employee badges (proximity cards) or PIN codes. Enforce the completion of pre-operation forklift inspections. Improve driver behaviors utilizing impact detection and management. Real-time capture of forklift hour meters and usage (engine, travel, lift, etc.). Automated notification of exception events to include failed pre-operation inspections and impacts. Track important planned maintenance milestones to aid on-time planned maintenance service. Communicate with operators with two-way communication. Optional: Speed monitoring (available on select equipment), external alarm, location tracking and load sensing “We are excited to introduce the Lift Link telematics solution, which represents Mitsubishi Logisnext Americas significant advancement in connectivity and fleet management,” said Jerry Sytsma, executive vice president of Sales and Aftermarket Services at Mitsubishi Logisnext Americas. “With Lift Link, our customers can harness the power of real-time data to make informed decisions, improve operational efficiency and ensure a safer work environment.” With Lift Link, customers can choose between a factory-installed or field retrofit option across Logisnext’s material handling equipment – Cat® lift trucks, Mitsubishi forklift trucks, Jungheinrich® warehouse products and UniCarriers® forklifts – in addition to competitive equipment. Customers will benefit from one solution that can be used across their entire fleet.
Felling Trailers adds Larson Cable Trailers to product offering
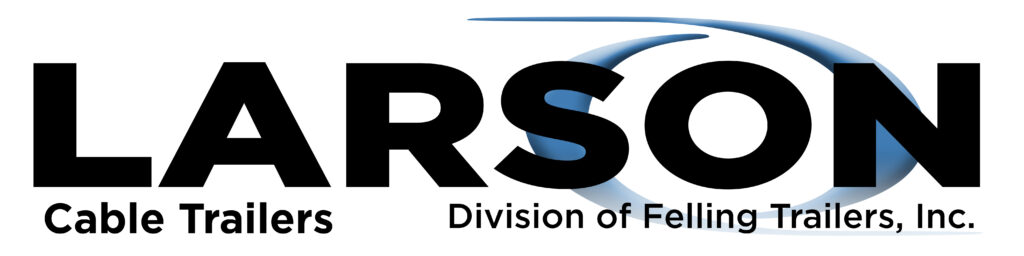
Felling Trailers, Inc. adds Larson Cable Trailers to their product offering with the, LCT-7500, LCT-5620, and LCT-5700. A division of Felling Trailers, acquired in May of 2021, Larson Cable Trailers, Inc. is a known leader in fiber-optic cable-handling trailer products. Effective August 1, 2023, the Felling Trailers sales team is now offering the LCT models as part of their expansive product line. “We feel this move will allow us to provide enhanced regional dealer support, providing training and product support,” said Nathan Uphus, Felling Trailers sales manager. With the two companies working together with seven regional sales managers, we can now provide sales and product support nationwide. This will, in turn, allow more time for Larson’s Tech Training Specialists, Rick Larson, and Mike Young, to focus on end-user support. The two companies will be exhibiting in tandem at this year’s Utility Expo, taking place in Louisville, KY, Sept. 26th-28th. Located in the K-Lot, Felling Trailers, Inc., in booth K125, will display a selection of utility underground products from their drill series and utility telecom model lines. Located next door to Felling in booth K123, Larson Cable Trailers, Inc. will provide product demonstrations with their core models, LCT-7500 and LCT-5620. Regional Sales Support Contacts North Central – Jeff Swartz 605-481-4005 Great Lakes – Joel Lindmeyer 320-309-3833 South Central – Joe Pessen 913-249-1766 Northeast – Jim Capobianco 774-991-3613 Southeast – Jason Worley 803-415-2742 Northwest – Mike Pitts 208-546-1504 Southwest – Michael Wilwerding 209-429-7110
Cargo volume dips in July at Port of Long Beach
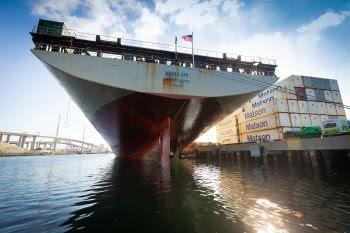
Summer lull continues amid shift in consumer spending Trade dipped at the Port of Long Beach in July due to adjusted trade routes, full warehouses and a shift in consumer spending to travel, entertainment and other experiences. Dockworkers and terminal operators moved 578,249 twenty-foot equivalent units (TEUs) last month, down 26.4% from July 2022, which was the Port’s busiest July on record. Imports declined 27.9% to 271,086 TEUs, while exports decreased 17.6% to 90,134 TEUs. Empty containers moving through the Port were down 27.7% to 217,030 TEUs. “I am confident we will see our numbers improve as we work with industry partners to rebuild our market share,” said Port of Long Beach CEO Mario Cordero. “Looking ahead in the near term however, we anticipate a modest ‘peak season’ for shipping as consumers spend a little less this year on back-to-school supplies and gifts through the holiday season.” “Our facilities, longshore labor, marine terminal operators and all of our industry partners continue to make this the premier gateway for trans-Pacific goods movement,” said Long Beach Harbor Commission President Bobby Olvera Jr. “We are ready for a rebound in cargo volume based on our ability to move cargo reliably, quickly and sustainably.” The Port has moved 4,310,925 TEUs during the first seven months of 2023, down 25.6% from the same period last year. Cargo flows are now closer to pre-pandemic levels, when the Port of Long Beach moved 4.3 million TEUs through the first seven months of 2019. For complete cargo numbers, visit polb.com/statistics.
Episode 410: The collaborative success of Vanderlande and RightHand Robotics
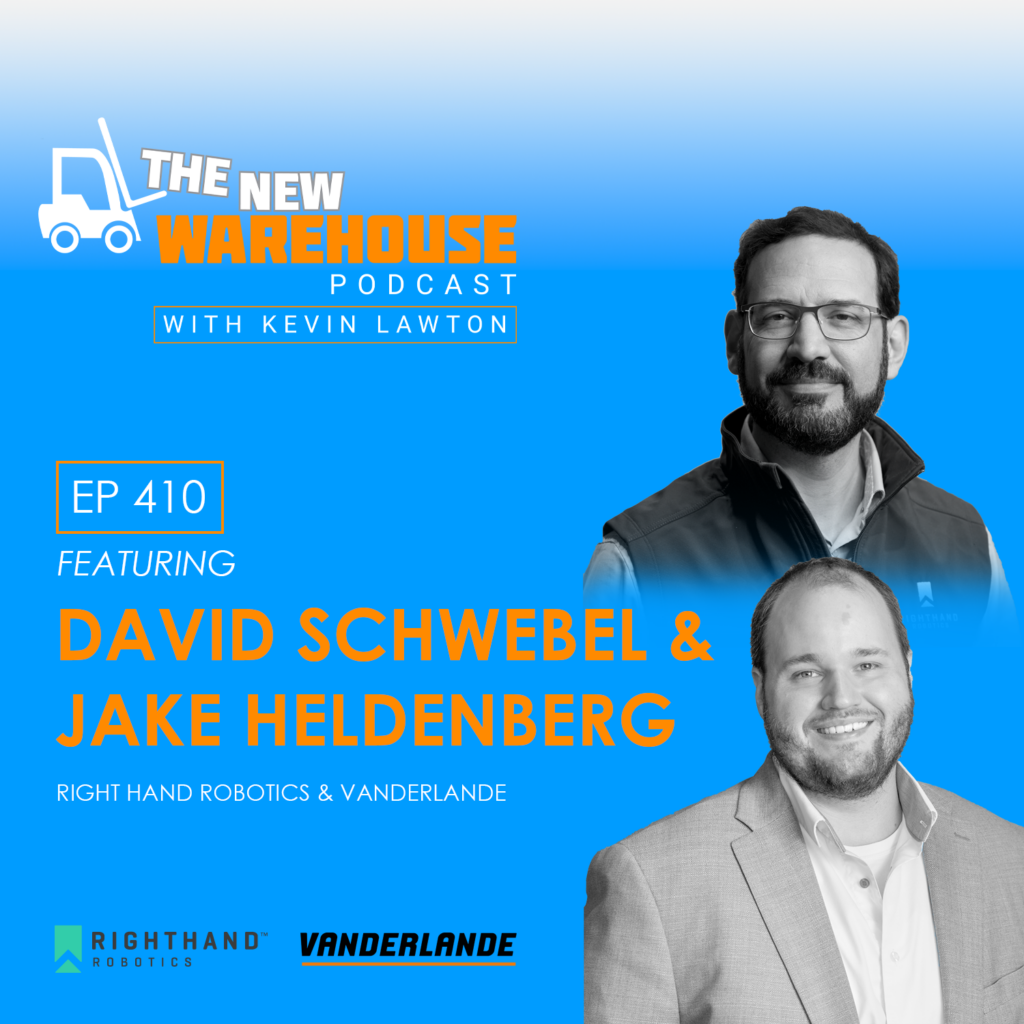
Welcome back, avid listeners of The New Warehouse Podcast! In today’s exciting episode, we’re diving into the fascinating world of warehousing innovation with two exceptional guests. The dynamic duo joining us today: Jake Heldenberg, Head of Solution Design for Warehousing in North America at Vanderlande, and David Schwebel, Head of Sales and Business Development at RightHand Robotics. Get ready to uncover the secrets behind their groundbreaking partnership, where integrator expertise meets cutting-edge robotics technology, reshaping the landscape of modern warehousing. In this blog post, we’ll explore the highlights of their conversation, focusing on three key topics that shed light on the warehousing industry’s evolution and the crucial role these companies play. Tailored Automation Solutions: Vanderlande’s Approach to Warehousing Excellence Let’s start by delving into Vanderlande’s role as a leading solutions provider in the warehousing industry. Jake gives us insights into Vanderlande’s core mission: “The number one thing that we focus on working with our customers is finding the right solution for them to make their business better, stronger, more profitable.” Vanderlande specializes in optimizing supply chain processes and distribution center operations to enhance businesses’ efficiency, accuracy, and overall success. As Jake explains, it’s not just about automation—it’s about identifying what makes each customer unique and creating tailor-made solutions that empower them to outshine the competition. Robotics Revolution: Unleashing the Potential of RightHand Robotics David Schwebel introduces us to the world of RightHand Robotics, a pioneering force in robotic piece-picking technology. Founded in 2014, the company’s ingenious solution involves “the hand, which is how we pick things, the eye, how we observe it and see it in the arm that moves it.” RightHand Robotics’ innovation lies in its ability to replicate human-like dexterity and precision, offering seamless solutions for various fulfillment needs. “Ultimately, it is all about picking and placing the eaches that delight the consumers and end users.” David emphasizes that their partnership with Vanderlande has been instrumental in expanding their capabilities and enhancing the customer experience. Bridging the Gap: The Integrator-Robotics Synergy The heart of this engaging conversation revolves around the unique partnership between Vanderlande and RightHand Robotics. Jake provides valuable insights into this collaboration: “Through looking at all these various companies, we found that with RightHand, they had all three segments covered.” He refers to vision and grasping, hardware, and robot control—as essential components in successful automation. David elaborates on how this partnership has allowed RightHand Robotics to focus on its core strength, robotic picking, while leveraging Vanderlande’s expertise in system integration, program management, and design. Together, they’re tackling the challenges of order completeness and process optimization to drive their customers’ success. Key Takeaways from Vanderlande and RightHand Robotics Customization is King: Vanderlande’s mission centers on crafting tailored automation solutions that align with each customer’s unique needs and competitive advantage. Robotics Revolutionized: RightHand Robotics’ mastery of robotic piece-picking technology unlocks unprecedented accuracy and efficiency, enhancing fulfillment operations. The Power of Synergy: The partnership between Vanderlande and RightHand Robotics demonstrates how integrator expertise and robotics innovation come together to fill gaps and deliver seamless, optimized solutions. The New Warehouse Podcast EP 410: The Collaborative Success of Vanderlande and RightHand Robotics
Weekend lane closures for Long Beach Bridge
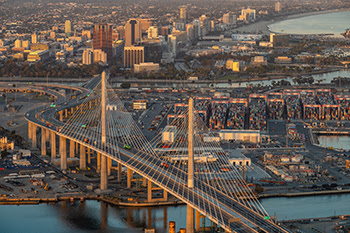
Roadwork will result in intermittent lane closures on the Long Beach International Gateway Bridge this weekend, Aug. 12-13. Vehicles will be restricted to the right lane of traffic on both the eastbound and westbound directions of the bridge from 6 a.m. to 6 p.m. Saturday and Sunday. The Mark Bixby Memorial Bicycle-Pedestrian Path and Ocean Boulevard Connector will not be affected by the roadwork. Motorists should exercise caution while driving through the work zone and heed the direction of officers. If additional work is required, the bridge will be narrowed to one lane of traffic from 6 a.m. to 6 p.m. the following Saturdays, Aug. 19 and Aug. 26. The Long Beach International Gateway Bridge opened to vehicles in October 2020 with three traffic lanes in each direction.
ALERT: American Logistics Aid Network (ALAN) mobilizes for Hawaiʻi fires
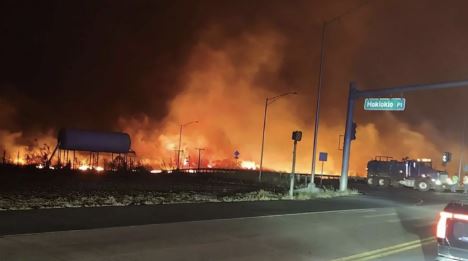
As fires on Maui and Big Island continue to burn, the American Logistics Aid Network (ALAN) is gearing up to provide support – and calling on members of the logistics community to be on long-term alert for opportunities to do the same. Effective immediately, the organization has expanded its Disaster Micro-Site (www.alanaid.org/operations/) to include key details about the fires and their related logistics needs. And late yesterday the organization received its first request for logistics assistance – moving communications equipment to support shelter facilities near Lahaina. “We are heartbroken and devastated for the residents of both islands, especially those who have lost a loved one, a home or – in the case of Lahaina – most of their hometown,” said ALAN Executive Director Kathy Fulton. “Today we are officially channeling that heartbreak into action. “Although the need for our supply chain assistance for post-fire relief efforts in Hawaiʻi hasn’t been extensive yet, the operative word is yet, because as Hawaiʻi Lieutenant Governor Sylvia Luke said, the full impact of the fires won’t be known for weeks or months. As assessments are made, we’ll undoubtedly be getting more requests, including many that could come in several weeks or months down the road. That’s why we hope members of the logistics community will visit our Disaster Micro-Site often to view the latest lists of requests – or consider making a pre-offer (https://www.alanaid.org/offerinkind/) of any space, services and equipment they’d be willing to donate to assist with fire relief efforts.” Fulton also reiterated a request from many members of the non-profit relief community: Please don’t self-deploy to Maui or Big Island – and refrain from participating in product collection drives. “Although the intention behind these efforts is good, they often create more challenges than they solve, including getting in the way of rescue efforts. So please don’t add to an already difficult situation,” she said. “If you truly wish to help, send funds. Cash donations allow non-profits to buy what they need, when and where they need it. And that will help survivors faster.” Fueled, in part, by Hurricane Dora’s strong offshore winds, the fires on Maui have claimed 36 lives and destroyed more than 271 structures, many of which were in the historic town of Lahaina. “This devastating disaster is a good example of just how unpredictable hurricanes and their impacts can be,” said Fulton. “However I hope that – like other recent disasters we’ve been working on – it will also serve as an example of just how generous the logistics community can be, because the donated transportation, warehousing, shipping supplies, forklifts and logistics expertise we provide can truly be game-changers and make a considerable difference for disaster survivors.”
Hyster-Yale Materials Handling announces second quarter 2022 results
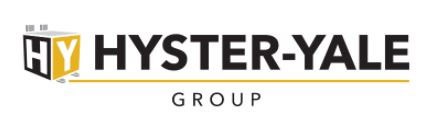
Q2 2022 consolidated revenues increased 17.0% over Q2 2021 due to an 11.5% increase in shipments, primarily as a result of a 32.2% increase in EMEA lift truck shipments Q2 2022 consolidated and Lift Truck gross margins improved from the historically low Q4 2021 levels, but, as expected, decreased modestly compared with Q1 2022 gross margins due to additional commodity inflation resulting from the Russia/Ukraine conflict and adverse product mix Q2 2022 consolidated results were better than expected, but remained unprofitable with an operating loss of $15.7 million and a net loss of $19.4 million due to material and freight cost inflation, unfavorable manufacturing variances resulting from component shortages and the absence of $6.3 million of income recorded in 2021 associated with a favorable court ruling Manufacturing inefficiencies at the Lift Truck and Bolzoni segments associated with normal Q3 seasonal plant shutdowns combined with cuts in production volumes due to continued supply chain constraints, as well as unfavorable currency effects, are expected to lead to a significant consolidated Q3 2022 operating loss As the Lift Truck segment works through its low-margin backlog in the second half of 2022, margins are expected to improve again in the fourth quarter, which in turn is expected to lead to a substantially lower operating loss than in the first half of 2022, mainly driven by the expected strong operating profit in the fourth quarter of 2022 in the Americas segment. Results for the remainder of 2022 and in 2023 are expected to be below what was expected in the Q1 2022 earnings release due to lower than previously planned productions levels as a result of continued supply chain constraints Q2 2022 Bolzoni operating profit improved over Q1 2022 and Q2 2021, but 2022 second half improvement over 2021 is expected to be lower than the improvement in the first half of 2022 Nuvera operating results for the second half of 2022 are expected to improve due to the absence of impairment charges recognized in 2021 and expected lower production costs Hyster-Yale Materials Handling, Inc. has announced consolidated revenues of $895.4 million, an operating loss of $15.7 million and a net loss of $19.4 million, or a loss of $1.15 per share, for the second quarter of 2022 compared with consolidated revenues of $765.6 million, operating profit of $5.9 million and net income of $1.9 million, or $0.11 per share, for the second quarter of 2021. Segment Financial Results Summary results for the Company’s three business segments were as follows for the second quarter of 2022 and 2021: (in millions) *Hyster-Yale Group *Bolzoni *Nuvera Q2 2022 Q2 2021 Q2 2022 Q2 2021 Q2 2022 Q2 2021 Revenues $ 846.3 $ 719.2 $ 86.4 $ 84.8 $ 0.3 $ 0.3 Gross Profit (Loss) $ 81.3 $ 103.2 $ 18.9 $ 15.8 $ (1.6) $ (2.5) Operating Profit (Loss) $ (11.7) $ 15.4 $ 3.4 $ (0.4) $ (7.9) $ (9.0) *For purposes of this release, Hyster-Yale Group refers to the Company’s Lift Truck business, Bolzoni is the Attachment business and Nuvera is the Fuel Cell business. Hyster-Yale Group Results Hyster-Yale Group unit shipments, bookings and backlog were as follows: ($ in millions) Quarter Ended June 30, 2022 Quarter Ended March 31, 2022 Quarter Ended June 30, 2021 Unit Shipments 25,300 23,900 22,700 Unit Bookings 23,200 35,900 46,900 Unit Bookings $ Value $760 $950 $1,070 Unit Backlog** 112,000 114,100 84,900 Unit Backlog $ Value** $3,530 $3,170 $2,070 ** June 30, 2022 and March 31, 2022 Unit Backlog has been reduced by 2,700 units and 3,200 units, respectively, and Unit Backlog $ Values have been reduced by $45 million and $54 million, respectively, due to suspended orders from Russian dealers which the Company currently has no defined plans to fill. The global lift truck market grew in the first quarter of 2022, but appeared to decline significantly in the second quarter compared to the high levels of both the second quarter of 2021 and first quarter of 2022. As a result of the market decline, as well as the Company’s focus on accepting only orders with expected sound margins and in the context of long lead times in a still very large market, bookings in the second quarter of 2022 decreased substantially from the robust levels of the 2022 first quarter and 2021 second quarter. The Company is focused on pricing new bookings close to target margins based on anticipated costs at the time of expected production. The average bookings sales price per unit increased 23.8% in the 2022 second quarter over the 2022 first quarter and 43.6% over the prior-year quarter because the Company continued to increase prices to offset material and freight cost inflation, a shift in sales mix to higher-priced lift trucks and a focus on accepting only orders with expected sound margins. These increased prices in turn translated into a substantial increase in the current average sales price per unit of backlog in the 2022 second quarter over the respective prior periods as well. The Company expects improved margins as prices and costs come into line, which in turn is expected to lead to a return to profitability in the 2022 fourth quarter. Second-quarter unit shipments increased compared with the prior-year second quarter and the 2022 first quarter due to increased production rates from prior year levels facilitated by a moderately reduced impact of component shortages from the ongoing global supply chain and logistics constraints. However, current supply chain constraints of certain critical components continued to negatively affect second-quarter 2022 production rates. Nevertheless, with higher shipments and lower bookings than in the 2022 first quarter, the Company’s high backlog level with its associated less than fully competitive lead times, began to decrease in the second quarter of 2022 for the first time since the beginning of the pandemic. The favorable effect of price increases put in place to mitigate the impact of material and freight cost inflation, as well as higher unit and parts volumes in the Americas and EMEA, mainly from a