Kenzen achieves GDPR Certification for Revolutionary Heat Safety Product
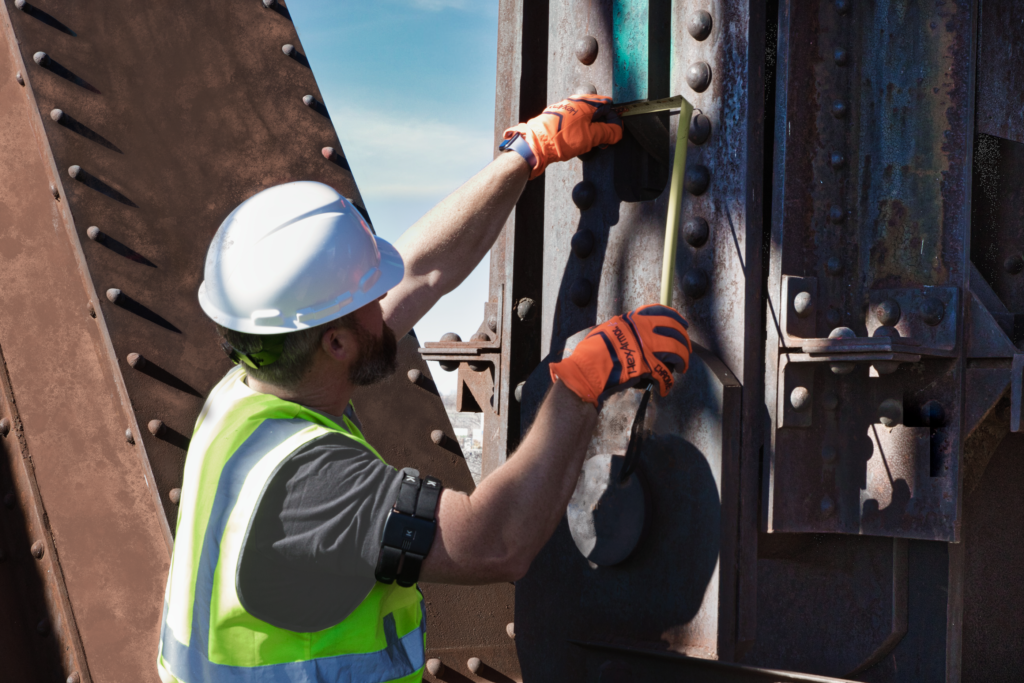
Kenzen, an innovator in the field of heat safety solutions and occupational health, has announced that its flagship product has received GDPR (General Data Protection Regulation) certification, further solidifying its commitment to data privacy and protection. This certification underscores Kenzen’s dedication to ensuring the highest level of privacy and security for its users across the globe and adheres to privacy regulations in the European market. By obtaining GDPR certification, Kenzen ensures the highest level of data protection for its users and adheres to stringent data privacy practices, ensuring the secure collection, storage, and processing of personal information. The GDPR certification is a significant milestone for Kenzen, validating its compliance with the rigorous regulations governing the protection of personal data within the European Union. This achievement reflects Kenzen’s unwavering commitment to data privacy, user rights, and ethical business practices. The certified product represents a breakthrough in heat safety technology, designed to safeguard individuals working in high-temperature environments. By integrating sophisticated algorithms to analyze the physiological data and provide insights, Kenzen provides real-time data and vital signs. These insights enabling proactive, timely intervention and prevention of heat-related injuries or illnesses while improving worksite safety and productivity. Kyle Hubregtse, CEO of Kenzen, expressed his enthusiasm about achieving GDPR certification, stating, “We are thrilled to receive this certification, which further demonstrates our commitment to safeguarding personal data. With this achievement, we aim to improve individual health outcomes for individuals working in high-risk environments while ensuring their privacy and data protection rights are respected.” Kenzen’s GDPR-certified heat safety product is now available for deployment across Europe, offering industries such as mining and metals, manufacturing, energy, and emergency services a robust solution to mitigate heat-related risks.
Wexxar Bel brings high speed Case Forming and Labeling at PACK EXPO 2023
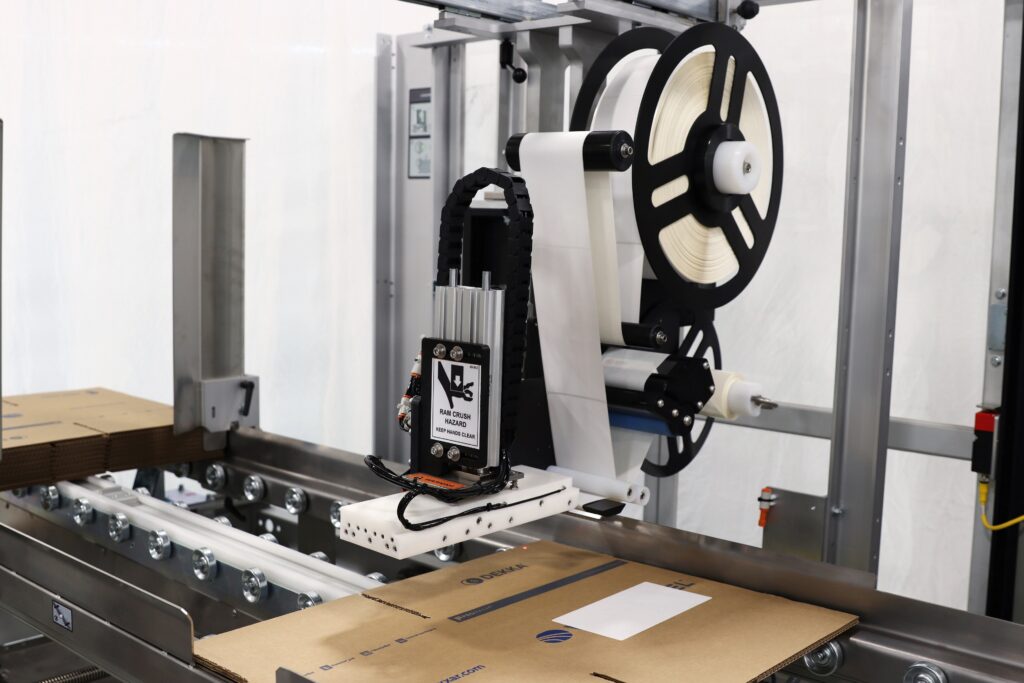
Looking for high speed case forming and labeling all in one efficient solution? Then be sure to add Wexxar Bel to your PACK EXPO 2023 itinerary! The new WLF30T Fully Automatic Case Former, which combines high speed case forming with labeling, will be showcased at booth C-3825 at PACK EXPO 2023, Sept. 11-13, at the Las Vegas Convention Center, Las Vegas, Nevada. The WLF30T incorporates a labeling system from its sister ProMach brand, EPI Labeling. This partnership gives customers the ability to label cases prior to formation at speeds of up to 30 cases per minute. The ability to label the case prior to packing is ideal, particularly for food applications where the case may be going to a cold room after forming. That’s because labeling the case before forming ensures the label is properly adhered and allows the machinery to operate outside the wet or cold area. “Where the WLF30T really proves its worth is in cold storage food applications because it enables customers to label the case before its formed,” said Sander Smith, Product Manager, Wexxar Bel. “What’s unique about the WLF30T is that it merges fast case forming and labeling all housed within one unit. It’s a strong combination we’re bringing to market.” The WLF is based on Wexxar Bel’s reliable WF30 platform with an easy-load bottom pick magazine. It is integrated with an EPI M2 labeler that is located inside the magazine section of the machine, a design that both protects the labeler behind clear Lexan glass doors while also saving valuable floor space. Accessing the labeler is fast and convenient as it easily slides out of the machine for maintenance or reloading labels. As blank cases slide into position, the EPI M2 applies the label; the EPI M2 can be programmed to apply the label at any location on the case. The magazine accepts up to three bundles of cases, totaling about 75 cases depending on thickness. The cases never stop during labeling, providing an uninterrupted smooth flow through the machine. After the label is applied, cases are tipped up and handled by Wexxar’s patented Pin & Dome technology to open the case. Flaps are folded and sealed with a Dekka tape head, and the case advances forward ready to be filled. Features and benefits of the new WLF30T Fully Automatic Case Former include: WISE system with HMI controls Color-coded change handles and textless instructions for easy case changeover Quick and easy case loading even while the machine is in operation Available in tape or hot melt Modular design for greater machine reliability and less maintenance Engineered for IP65 specifications for use in dusty or damp environments
Active intelligence groundbreaking ASTRATM Video Anomaly detection now available
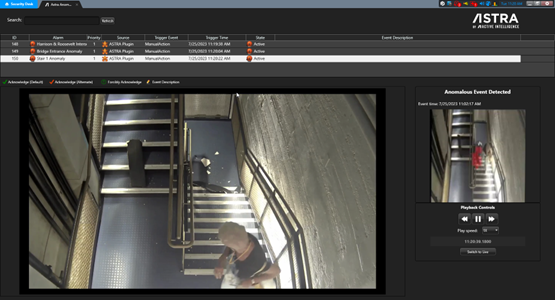
ASTRA™ delivers a true gateway to proactive video security Active Intelligence, pioneer of AI-powered anomaly detection software for physical security just announced that its groundbreaking ASTRA™ Autonomous Video Anomaly Detection solution is now available for sale. The decision to initiate the official availability of ASTRA comes after a series of user trials and evaluations in mission critical applications across multiple vertical markets. “We performed extensive field tests with ASTRA and listened very carefully to scores of respected security professionals over the last 18 months, ensuring that we were bringing the best possible solution to market,” said Ken LaMarca, CEO, Active Intelligence. “The concept of commercially viable autonomous anomaly detection is new to this industry, so it was imperative that we got it right from the get-go. We’re extremely excited to bring this technology to market and help businesses tangibly improve the security of their facilities.” A breakthrough in proactive security technology, ASTRA™ delivers real-time anomaly detection for a virtually unlimited number of security, safety, compliance, and commercial/industrial applications across the enterprise. Unlike conventional video analytics, ASTRA eliminates the need for pre-configured rules to detect virtually any anomaly within a scene. This unique capability allows ASTRA to automatically distinguish acts of violence, individuals in distress, disruptions to assembly lines… the possibilities are limitless. Further, ASTRA detects anomalies using statistical data analysis without any bias or human judgement. A highly cost-effective solution, ASTRA allows for hundreds of video streams to efficiently run on a single server, significantly reducing the cost of implementation compared to conventional video analytics software. The lightweight application also creates little to no load on the user’s network. ASTRA’s anomaly detection transforms any video security system from purely reactive into a truly proactive, automated imaging solution, putting eyes on the entire system 24/7. For ease and speed of deployment, ASTRA integrates with the industry’s leading video management system (VMS) platforms, including Milestone XProtect, Qognify Ocularis, Genetec Security Center and Salient in the near future.
Transient leaders kill culture for reasons you don’t realize
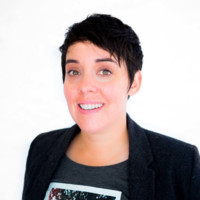
Some organizations go through CEOs and department heads like Kleenex. Today, the average tenure of a CEO is 4.6 years. In other cases, C-Suite leaders rotate out of the organization within 1 or 2 years, and a new leader is installed. And it’s always “This one is the right one – they’re bringing incredible experience/ideas/perspective to the organization.” They try to install a few changes that typically don’t stick, and are moved out in short order. Then the pattern repeats. Why does this happen? Sometimes there are unrealistic expectations that are set. Other times, it actually may be a poor hire. But rotating leaders in and out costs your company much more than simply hiring bonuses. It kills culture in ways you don’t realize. I spoke with a friend recently, who is working in an environment where they’ve had 5 new CEOs in the last 7 years. While some may view this issue as causing pressure, confusion, and constant priority changes for the organization, this wasn’t the core problem. The churn created inertia, where employees simply waited out the new CEO’s tenure, knowing they would be leaving soon, and any new idea or initiative would be killed by the next incoming CEO. My friend’s analogy was spot on, stating, “It’s like a single mom that has another new boyfriend. As a child, you know it’s temporary. You don’t need to respect their authority or become close to them. You do what is necessary to appease them in the short term until they are rotated out by the next one.” This is what kills culture. It’s not that the new hire might not be a great talent, have great ideas, be a great leader, or have a great vision. If there’s a track record in the organization where leaders come and go, the new hire won’t be successful because they are the proverbial “new boyfriend”. Employees will fight to maintain the status quo and resist change, as any time they have in the past those efforts are short-lived, as the next leader upends them. And just like the new boyfriend, the same type of individual is picked every time, and the pattern continues. Leadership might not see it, but employees sure do. So while you may think you just haven’t found the right leader, often it’s the organization’s reaction to historical churn. And that cycle is incredibly hard to break. Do yourself a favor and talk to your employees about what type of leader they want. Find out what has worked in the past and what hasn’t from their perspective. Identify employees internally that have the potential to take a leadership role in a few years, and determine what they need to get there faster. Take a different approach to finding a new leader, whether a temporary employee who is there to prep an internal staff member for the job, or even a totally different leader from outside the industry that signals it’s actually different this time. Otherwise, you’ll just churn through yet another boyfriend. About the Author Andrea Belk Olson is a keynote speaker, author, differentiation strategist, behavioral scientist, and customer-centricity expert. As the CEO of Pragmadik, she helps organizations of all sizes, from small businesses to Fortune 500, and has served as an outside consultant for EY and McKinsey. Andrea is the author of three books, including her most recent, What To Ask: How To Learn What Customers Need but Don’t Tell You, released in June 2022. She is a 4-time ADDY® award winner and host of the popular Customer Mission podcast. Her thoughts have been continually featured in news sources such as Chief Executive Magazine, Entrepreneur Magazine, Harvard Business Review, Rotman Magazine, World Economic Forum, and more. Andrea is a sought-after speaker at conferences and corporate events throughout the world. She is a visiting lecturer and startup coach at the University of Iowa, a TEDx presenter, and TEDx speaker coach. She is also an instructor at the University of Iowa Venture School. More information is also available on www.pragmadik.com and www.andreabelkolson.com.
Reusable Packaging Association set to showcase groundbreaking solutions in the RPA Pavilion at Pack Expo Las Vegas 2023
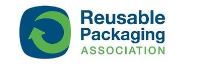
The Reusable Packaging Pavilion is Home to the Technology Hub and Learning Center – The Ultimate Global Gathering of Reusable Packaging Experts, All Under One Roof Leading the way in advancing the circular economy, the Reusable Packaging Association (RPA), has announced the much-anticipated Reusable Packaging Pavilion at PACK EXPO. This exceptional event is set to take place in Las Vegas, September 11-13, uniting the largest assembly of reusable packaging experts and unveiling a diverse range of cutting-edge products and technologies. “For over two decades, RPA has been at the forefront of reusable transport packaging solutions, and the Reusable Packaging Pavilion at PACK EXPO has been a cornerstone showcase of member company innovations in products and services,” said Tim Debus, CEO of RPA. “Attendees at the show can see the latest developments in reusable packaging for the supply chain and learn from the industry’s leading experts in adopting and optimizing reuse systems – all in one place.” The RPA Pavilion will feature over 40-member company exhibitors this September. PACK EXPO attendees are encouraged to check out RPA’s member exhibitors and floorplan to learn where to find each exhibitor in the South Upper Hall at the Las Vegas Convention Center. The adjacent Reusable Packaging Learning Center will host RPA’s education program with 19 sessions over the two days Monday and Tuesday, September 11 and 12, from 10 a.m. until 4:45 p.m. US Pacific Time. Sessions include company presentations and industry panel discussions focused on improving supply chain performance, sustainability, and technology with reusable transport packaging. See the full schedule here. All sessions are open to PACK EXPO Las Vegas attendees. RPA will conclude the Learning Center with the 2023 Excellence in Reusable Packaging Awards on Tuesday at 3:00 p.m. The annual awards celebrate primary (end) users and suppliers that have significant impactful achievements in one of three categories: a reusable packaging system, design innovation, or product technology.
Cabka transforms logistics with circular economy solutions at Pack Expo Las Vegas
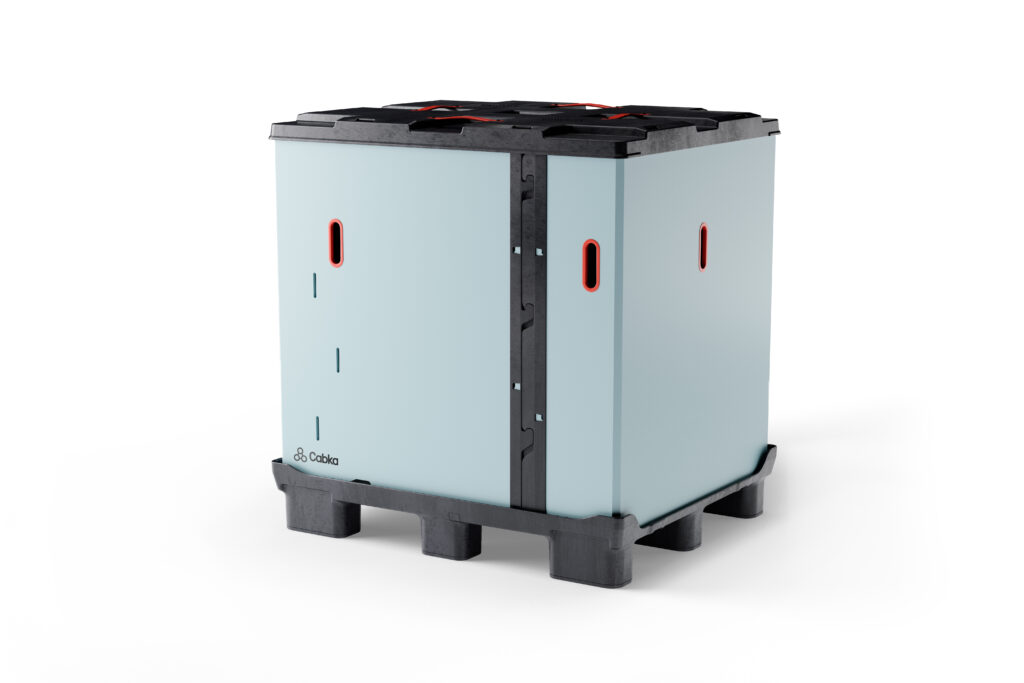
Cabka, a provider of reusable transport packaging made from recycled plastic, has announced its participation in the upcoming Pack Expo Las Vegas (September 11-13, 2023), where it will showcase its innovative products designed for the circular economy at booth N-9403. With a focus on tailor-made solutions and sustainability, Cabka aims to transform storage and transport processes while benefiting customers and the environment. At Pack Expo Las Vegas, Cabka will present its diverse portfolio of large load carriers and pallets, highlighting its commitment to the circular economy. By offering reusable and durable products made from recycled plastics, Cabka not only helps businesses save energy, transportation, and storage costs but also enables them to reduce their scope 3 emissions for Greenhouse Gases (GHG). The company’s development team continuously strives for intelligent product designs that are lightweight, resource-saving, and space-efficient. “At Cabka, we are proud to drive the transformation towards a circular economy”, says Jean-Marc van Maren, Chief Product Officer at Cabka. “By combining our expertise in developing reusable load carriers with our commitment to using recycled plastics, Cabka brings a powerful synergy to our customers: efficiency and sustainability hand in hand.”
Episode 408: Empowering the Blind and Visually Impaired workforce in warehousing with The Austin Lighthouse
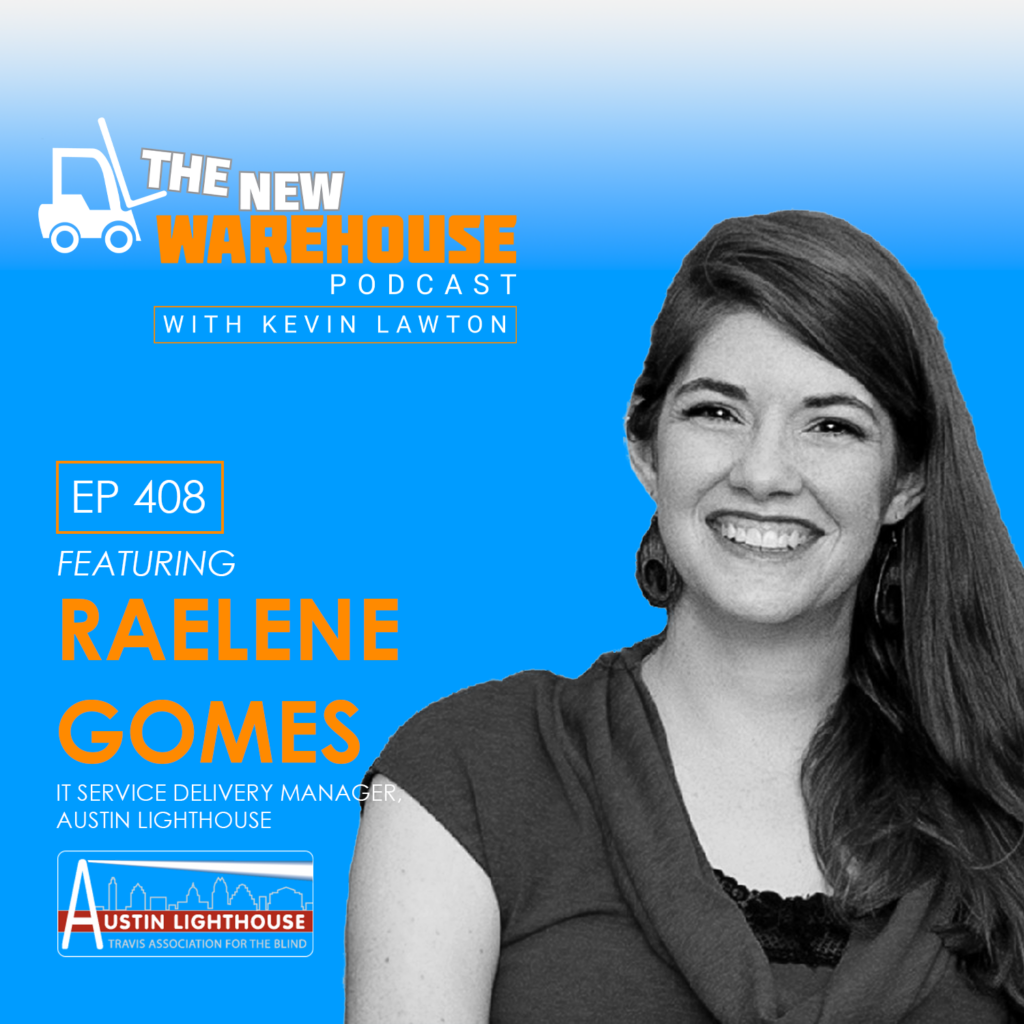
In this episode of The New Warehouse Podcast, Kevin sits down with Raelene Gomes, the IT Manager at the Travis Association for the Blind, also known as The Austin Lighthouse. The Austin Lighthouse, founded in the 1930s, is a warehousing and distribution organization that employs and trains blind and visually impaired workers intending to help them find employment outside the Lighthouse while encouraging upward mobility. Improving Workforce Inclusivity at The Austin Lighthouse through Transformative Technology Raelene discusses how they’ve successfully utilized various technologies, such as screen reading technology, voice picking, and textured tape on the floor, to create a more inclusive and accessible workplace for visually impaired employees. She believes “Technology is so powerful and can be a big equalizer across abilities. With the right technology in place, I cannot limit what I can achieve.” By partnering with technology providers like Zebra and Manhattan Associates, they’ve worked to make software and hardware more accessible, enabling their workforce to thrive. Embracing the Future of Work: Work from Home and Automation Looking to the future of work, Raelene highlights the importance of work-from-home opportunities, especially for individuals with transportation challenges. She also emphasizes the potential of automation as a means to elevate job opportunities rather than replace employees. For example, robots can reduce travel time, making tasks more manageable for employees with specific impairments. She adds “I think automation is going to be a big thing, which, if done right, opens up job opportunities rather than taking them away.” Tapping into an Untapped Workforce in Warehousing Market Raelene urges employers to be open-minded about hiring visually impaired individuals and to inquire about the adaptive technology needed to support them effectively. “I’d like to see more employers ask what kind of adaptive technology is needed. It’s usually not a big ask and can open up job opportunities for people with disabilities.” By doing so, companies can tap into an untapped labor pool, fostering a more diverse and inclusive workforce. Key Takeaways from The Austin Lighthouse By implementing accessible technologies, companies can create a more inclusive and empowering work environment for visually impaired employees. Embracing work-from-home opportunities and automation can enable greater workforce participation and job growth for people with disabilities. Employers should explore adaptive technology and open themselves up to hiring from the visually impaired labor pool, expanding workforce diversity and fostering inclusivity. The New Warehouse Podcast EP 408: Empowering the Blind and Visually Impaired Workforce in Warehousing with The Austin Lighthouse
Brenton appoints Patrick Davis as new Regional Sales Manager
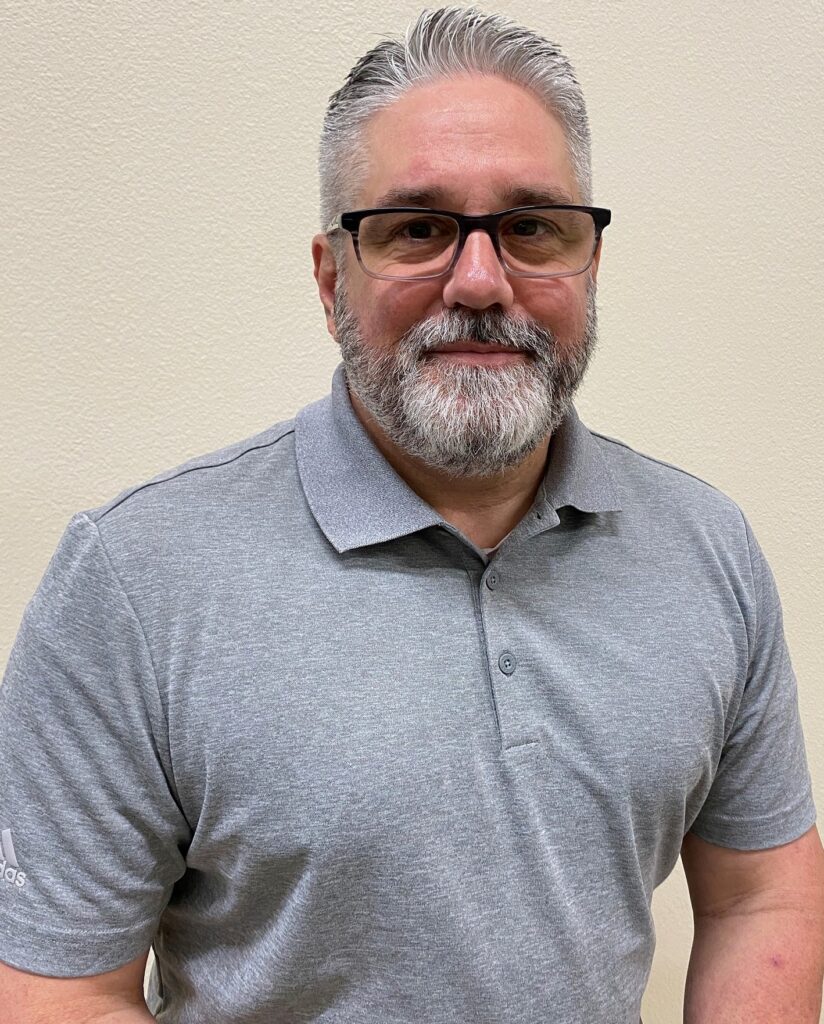
Patrick Davis has been appointed Regional Sales Manager for Brenton, a role in which he will be working with east coast end-user customers and integrators to grow the company’s end-of-line packaging systems. Brenton is a global provider in designing and manufacturing integrated end-of-line case packaging systems and machines, specializing in case packing and palletizing using both robotics and other automation. Davis’s most recent role at ITW Hartness consisted of selling complex integrated systems and individual packaging equipment for food and beverage applications. His resume also includes experience in sales and managerial positions spanning 25 years, including four years of service in the United States Air Force. “I’m excited to put my experience to work developing Brenton’s dependable end-of-line packaging systems for customers,” Davis said. “The team I’m joining has proven to be an industry leader in both technology and customer service, and I look forward to contributing to Brenton’s future.” Davis, who earned a bachelor’s degree from the University of North Carolina, is based in the Charlotte, N.C. area. He can be reached at pat.davis@promachbuilt.com.
Port of Long Beach awards $220,000 in college scholarships
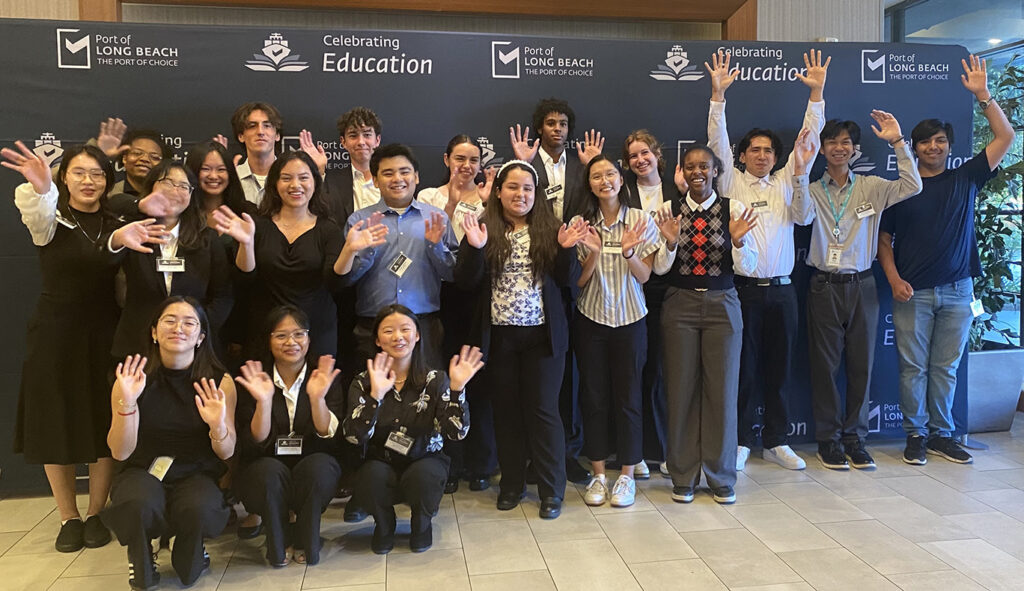
The Port of Long Beach on Wednesday announced $219,500 in scholarships for 154 local college and high school students to assist in their pursuit of higher education degrees in port-related fields from engineering to international business. The students receiving the scholarships were recognized at the Port’s “Celebrating Education” event on Aug. 2. The event also honored the 2023 class of summer high school interns, the first class after a three-year hiatus due to the COVID-19 pandemic. The Celebrating Education event brings together students, educators, public officials and business leaders to highlight the Port’s education outreach programs and recognize the accomplishments of students involved. “The Harbor Commission has a longstanding goal to create and support programs aimed at advancing the development of a skilled workforce in international trade, goods movement and related professions,” said Sharon L. Weissman, President of the Long Beach Board of Harbor Commissioners. “Scholarships are just one of the many ways we work toward that goal.” “We’re proud to provide the college scholarships which will help in guiding our youth toward rewarding careers in the logistics industry,” said Long Beach Mayor Rex Richardson. “These scholarships will play a crucial role in providing essential financial assistance to hardworking students, enabling them to pursue higher education and other training opportunities.” “Our education programs offer training and funding to prepare students for positions at every level within the port industry,” said Port of Long Beach CEO Mario Cordero. “We’re doing our part to make sure our local young people have every opportunity to be part of the goods movement workforce of tomorrow.” Since 2014, the Port has awarded nearly $1.1 million in scholarships to students pursuing careers in international trade and goods movement. This year’s scholarships went to students from local high schools, Long Beach City College and Cal State Long Beach. This fiscal year’s budget for scholarships was $250,000, up from the previous year’s $200,000.
CSX announces departure of Operations Executive Jamie Boychuk
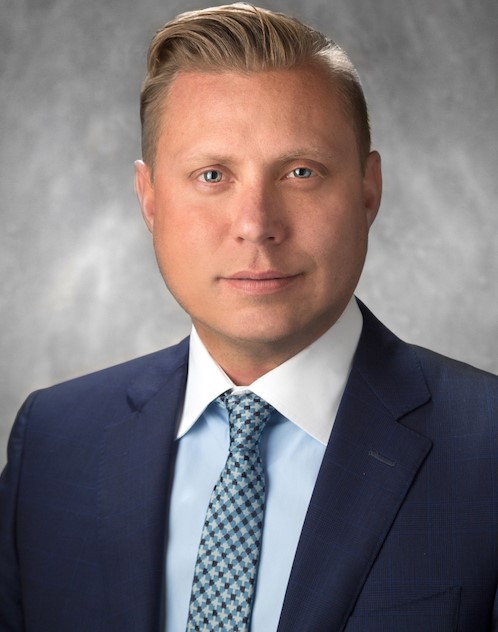
CSX announced today that Jamie Boychuk, executive vice president of Operations, is leaving the company. President and Chief Executive Officer Joe Hinrichs thanked Boychuk for his role in the implementation of scheduled railroading and cited the company’s depth of operational experience that will ensure continuity while CSX searches for a successor. “On behalf of CSX and all our stakeholders, I would like to thank Jamie for his six years of service and contributions to our company, and we wish him all the best in his future endeavors,” Hinrichs said. Hinrichs added, “CSX has an experienced operations leadership team that helped guide our operational transformation into a top-performing transportation company, and who will continue to implement and strengthen the scheduled railroading guiding principles that have been the foundation of our success.” Ricky Johnson, senior vice president of Transportation, and Casey Albright, senior vice president of Network Operations and Service Design, will report directly to Hinrichs as the company conducts an internal and external search prior to naming a new head of all operations functions. Johnson, who oversees all field operations, has over 30 years of experience in the railroad industry, including 22 years of service at CSX. Similarly, Albright has 25 years of service at CSX in various leadership roles. In his current position, he oversees fluid traffic flow across the CSX network, leading the design of service plans that support performance improvement and meet customer needs. “Our seasoned operations leadership team and talented field leaders will remain focused on executing our proven operational plan and drive growth by providing an ever-improving service product to customers. I have the highest confidence in our entire ONE CSX team, which has embraced our culture of working collaboratively to deliver strong safety and service results, positioning us to continue providing enhanced value for our shareholders and other key stakeholders,” Hinrichs said.
Mike Conroy promoted to Kalmar Director Services: Driving growth and exceptional customer experiences
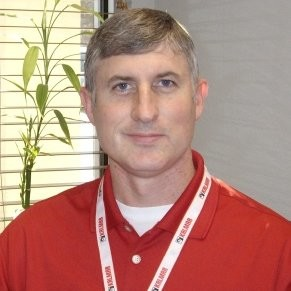
In an exciting development for Kalmar, Mike Conroy has been appointed as the new Director Services, North America. With this promotion, he will take on the responsibility of driving and developing the services business in North America, overseeing both service sales and service operations. Conroy’s extensive experience and remarkable track record within the company make him an ideal candidate for this crucial role. “I am excited and proud to have Mike join the Americas Leadership Team in such a critical role. His product experience, region knowledge and enthusiasm for the challenge are vital to the success of the services division moving forward.” Randy Wingenroth, VP Region Americas Looking back at Conroy’s career, we find a rich history spanning various industries and roles. He spent the first decade of his professional life in the printing industry, gaining valuable experience in customer ser vice and sales. Conroy then transitioned to manufacturing-related positions, including planning, scheduling, production supervision, cost estimating, and sourcing. In 2008, he joined Kalmar, initially working in the Sourcing department, where he managed several categories for Terminal Tractor production in Ottawa. Conroy’s accomplishments within Kalmar continued to grow as he took on more responsibilities. He played a pivotal role in the successful transition of the Princeton Truck Mounted Forklift business from Canal Winchester, OH to Ottawa. In 2010, he became the Sourcing and Supplier Development Manager for the Ottawa MAU, overseeing the Global Axle Category for Kalmar as well. In 2018, Conroy assumed the Terminal Tractor After Sales responsibilities globally, further contributing to the company’s success. With his extensive background and diverse experience, Conroy’s vision for his new role as Director Services, North America is clear. He aims to further propel the North American service and parts business, which has already made a significant impact on Kalmar’s global service division. Conroy is committed to driving profitable growth and ensuring an exceptional customer experience. Inspired by Ken Blanchard’s book “Raving Fans,” he encourages his teams to provide outstanding service, creating satisfied customers who become advocates for Kalmar and generate further business opportunities. In light of the recent promotion, Marques Askins has been named the new Terminal Tractor Parts Manager. Conroy expressed his excitement for Askins and the entire TT sales team, highlighting the growth opportunities available within Kalmar. Having witnessed Askins’ success in previous roles, Conroy believes he is well-deserving of this leadership position. Conroy looks forward to supporting Askins as he leads the TT parts team to new heights. Outside of his professional life, Conroy has made Ottawa, KS his home for the past 26 years, living there with his wife, three children, and a few English Setters. During his leisure time, he enjoys engaging in outdoor activities such as hunting upland game and fly fishing. Additionally, Conroy has developed a passion for perfecting his BBQ skills, adding flavor and creativity to his culinary endeavors. With Mike Conroy’s promotion to Director Services, North America, Kalmar can look forward to continued growth and exceptional customer experiences. His extensive background, dedication, and visionary leadership will undoubtedly contribute to the success of the company and strengthen its position in the North American market.
HC Forklift America introduces the new XE Series Electric Lithium-Ion Pneumatic Forklift
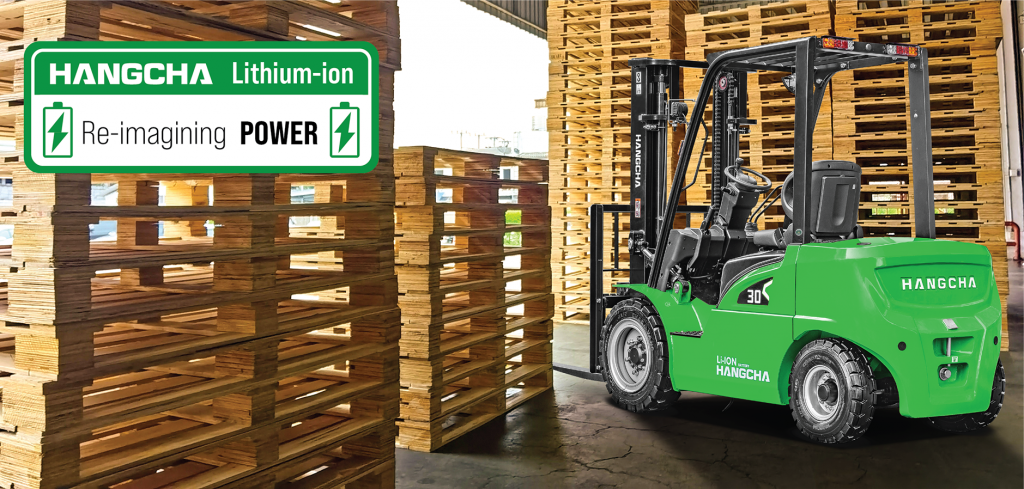
HC Forklift America Corporation (HCFA), a wholly-owned subsidiary of Hangcha Group, has announced the new XE Series Electric Lithium-Ion Pneumatic Forklift with a 4,000-7,600lb capacity. The new XE Series of lithium-ion pneumatic forklifts were designed from the ground up to provide operators with a true lithium-ion alternative to I.C. pneumatic forklifts. Because of this, the integrated 80V lithium-ion forklift features lift speeds, travel speeds, gradeability, ground clearance, and a competitive price point that rivals comparable I.C. pneumatic forklifts. “HCFA is keeping with its plans to continue launching new and updated products. We are proud and pleased to showcase our new XE Series Lithium Iron Phosphate Pneumatic Forklifts. This is not just about a product launch, but about a company (Hangcha) that believes in innovation and market leadership. Our goal is to provide products that bring solutions to our customers at a reasonable cost. Keep watching, because we’re not finished!” said Frank Russo, Vice President of Sales and Dealer Development. The XE Series: A True Lithium-ion Powered Competitor to I.C. Pneumatic Forklifts Hangcha designed the XE Series to include double permanent magnet synchronous motors, reducers in the hydraulic pump, reliable I.C. pneumatic components, and design elements from Hangcha’s well-known I.C. pneumatic forklifts. Hangcha then tested the XE Series Electric Lithium-Ion Powered Forklift to electric and I.C. pneumatic forklift standards. This ensures that the XE Series is a true lithium-ion powered competitor to I.C. powered pneumatic forklifts. Different applications require different equipment. Hangcha designed the new XE Series to complement our existing lithium-ion powered forklifts in the 4,000-7,600lb load capacity range. The XE Series Electric Lithium-Ion Pneumatic Tire Forklift provides operators with a new, integrated lithium-ion forklift that can handle the harsh outdoor applications that I.C. pneumatic forklifts are typically found in. By adding the XE Series, Hangcha now provides solutions for tight indoor applications, compact indoor/outdoor applications, and rugged indoor/outdoor applications with the X Series, XC Series, and the XE Series Electric Lithium-Ion Forklifts respectively. The XE Series: A Lithium-Ion Advantage The XE Series Electric Lithium-ion Pneumatic Forklift features an 80V integrated lithium-ion design. This integrated lithium-ion design provides operators with several key advantages. These advantages include: A Larger, More Ergonomic Operator Compartment Maintenance-Free Battery Packs 3 Different Battery Options for Each Model to Tailor the Forklift to the End-User’s Application A Lower Center of Gravity Up to 11 Hours of Runtime Depending on Battery Pack and Application Easy-Access Charge Ports Heating Elements in the Battery Pack to Ensure Optimal Performance in Cold Weather Applications With the XE Series’ integrated 80V lithium-ion system, I.C. pneumatic forklift design elements, and a competitive price point, end-users now have a true lithium-ion option when replacing I.C. pneumatic forklifts in their rugged outdoor applications.
American Welding Society strengthens support to younger welding professionals with complimentary student membership
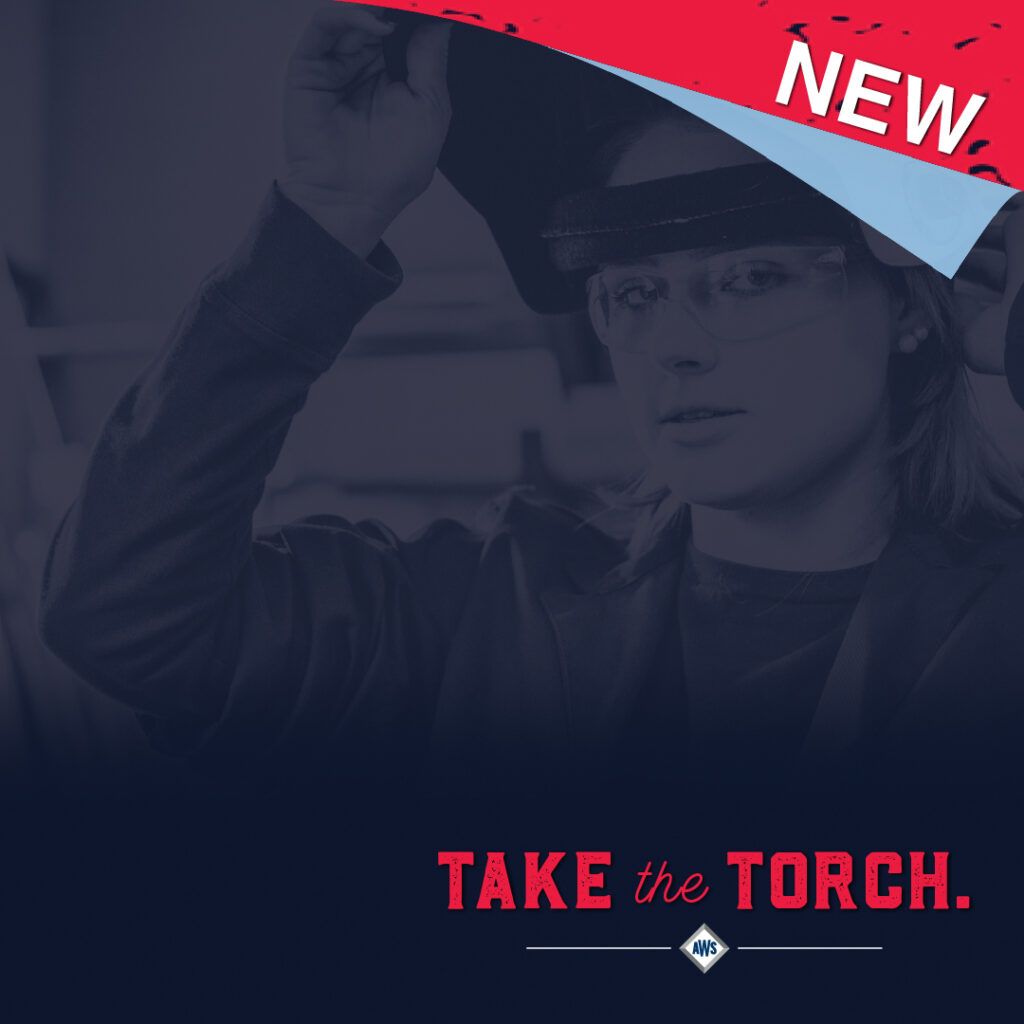
As an organization that recognizes the importance of developing the next generation of welding professionals, the American Welding Society announced today that it’s making its student membership complimentary. “The complimentary student membership is part of the Society’s strategy of supporting the younger generation in the earliest stages of their careers,” said Cassie Burrell, Senior VP, Marketing & Membership Development. “AWS boasts a large portfolio of offerings that will resonate with young people, helping to build a bridge from student to early career to professional membership.” For decades, the annual dues for the student membership were $15. Now, stude nts can obtain a complimentary membership for four years and maintain the same benefits. These include free digital access to the Welding Journal, discounts on publications and educational offerings, and access to the ever-popular Member Network, including a student community. “The complimentary student membership will introduce young people to a vast library of AWS resources and services designed to enhance their education outside the classroom, from scholarships through the AWS Foundation to networking opportunities at local AWS Student Chapter and Section events,” added Burrell. “We’re looking forward to welcoming student members and for them to find career and real-life opportunities they may not have discovered otherwise.” Students looking to elevate their education can apply online at aws.org/membership. They’ll then receive their member ID, giving them instant access to their member benefits.”
Toyota Logistic Design Competition 2024 open to students around the world
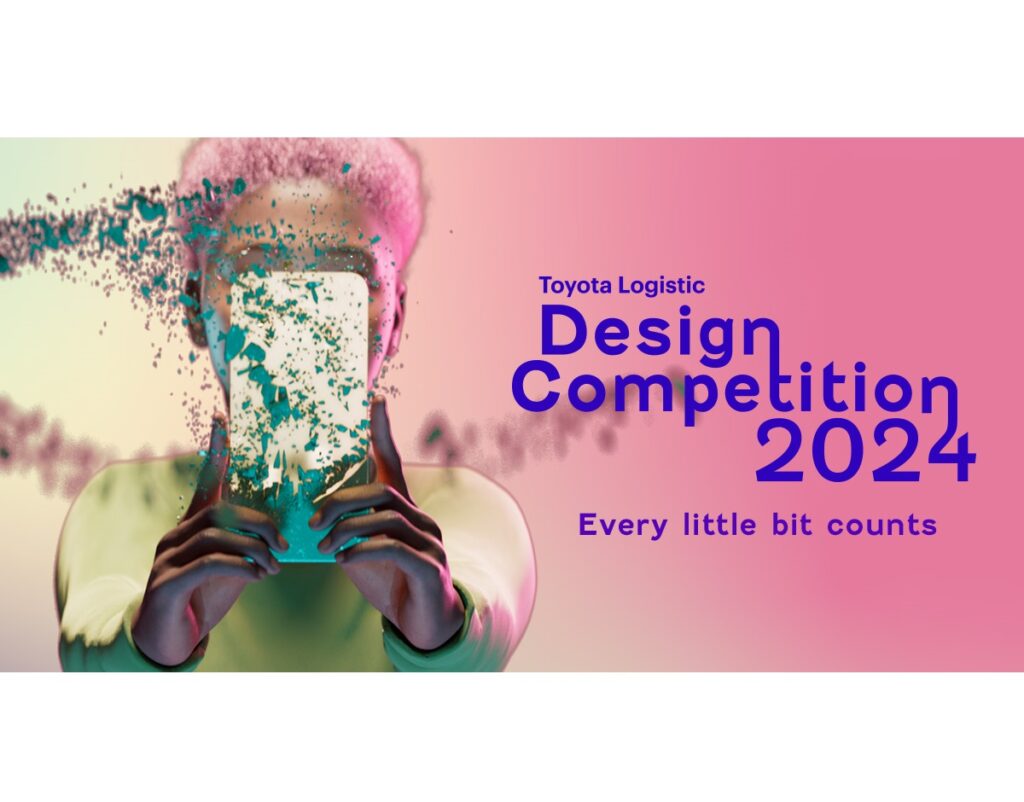
Toyota Material Handling is accepting applications for the Toyota Logistic Design Competition 2024. Undergraduate and graduate students enrolled in university programs from around the world are invited to participate in the competition by submitting groundbreaking inventions and solutions to improve the circular economy through logistics. “The Toyota Logistic Design Competition is a one-of-a-kind opportunity for future innovators to showcase their unique skills in design and engineering and create solutions that will have a long-lasting impact on business and logistics,” said Brett Wood, President & CEO of Toyota Material Handling North America. “The imaginative concepts the participants create each year is always impressive and inspiring.” Toyota, founded on the principle of contributing to society, views this competition as a way of engaging and fostering the next generation of designers and instilling a commitment to serve the communities around them. This year’s participants are challenged to focus on developing solutions for the future that improve lives, minimize waste and use resources in a way that has little impact on the environment. “I was honored to join my colleagues at Logiconomi 2022, [a forum where leaders and experts in logistics gather to discuss current trends and new concepts to improve the industry], concluding our global Toyota Logistic Design Competition with the award ceremony,” said Ian Cartabiano, Vice President of Advanced Design at Toyota Motor Corp. “Although it was a challenge to select our winners from the amazing proposals from all the talented designers of the future, working together, we chose four that represented an innovative future vision of logistics. I had the distinct pleasure to select and bestow the Ian Cartabiano Design Award to Marius Cramer from Umeå Institute of Design in Sweden. This award acknowledges design that is not only innovative and creative but also beautifully executed with an eye towards refined esthetics. Marius’s cargo bike proposal created a solution for last-mile, point-to-point delivery, and looked amazing. Along with this award, Marius was also given the opportunity to experience a design internship at Toyota Europe Design Development. I look forward to this year’s global design competition and working with my global colleagues to find the next generation of creative thinkers.” A panel of professionals working around design and innovation within Toyota will evaluate all entries and determine the finalists. The winner in each category of the competition will receive a cash prize. The winner and finalists’ submissions will be displayed during Milano Design Week and at the 2024 Paris Olympic-Paralympic Event. The deadline to submit is Monday, December 18, 2023. This is the third year the Toyota Logistic Design Competition is welcoming students from universities in the United States. In 2022, two students representing universities from the United States received top awards. Jacob Abraham, a student at the University of Houston, received the Gold Award for Oro, a delivery module that optimizes final-mile delivery vehicles in dense urban environments. Nicholas Orie, a student from California State University, received the Bronze Award for his Toyota Mitsubachi solution, a modular, autonomous drone fleet integrated in warehouses and micro hubs that is designed to streamline the process of handling and organizing goods. “North America was well represented with the Gold and Bronze awards this past year,” noted Greg Smiley, Head of Industrial Design at Toyota Material Handling North America. “Models of the winning designs were on display, and I know it was a great experience and networking opportunity for Jacob to receive his award at Logiconomi 2022 in Antwerp, Belgium.” Learn more about the Toyota Logistic Design Competition and how to submit an entry to compete by visiting https://tldc.toyota-forklifts.eu/.
Orbital wrapper manufacturer appoints sales associate
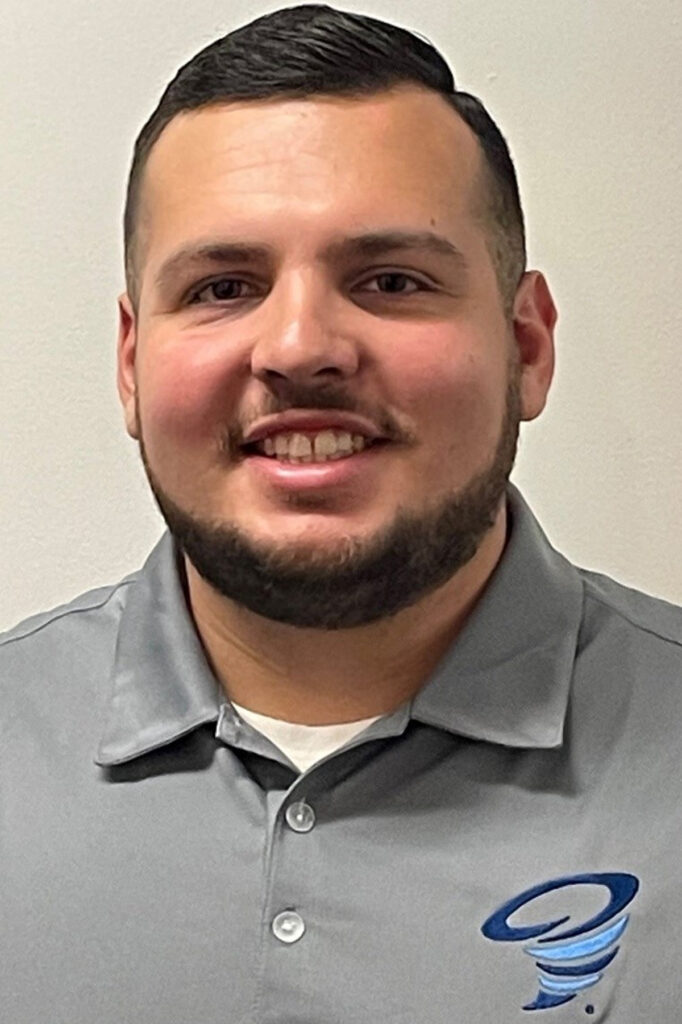
Orbital wrapper manufacturer TAB Industries, LLC, Reading, Pa., has named Kevin Slick sales associate. Bringing nearly five years of business-to-business sales management and technical sales experience to the new position, Slick is responsible for growing sales for the company’s line of patented TAB Wrapper Tornado orbital wrapping machines worldwide. The orbital pallet wrappers enable one operator to automatically apply stretch wrap 360 degrees around and under a pallet and load to create a stable, secure load in one minute or less that withstands shifting in transit and eliminates product damage. This new position was created to accommodate increasing demand for the orbital stretch wrappers, according to Andy Brizek, vice president of sales and marketing for the family-owned company. “We’re committed to providing a high level of personal service and technical expertise with fast lead times even as interest in our orbital wrappers continues to spike,” says Brizek. “Kevin’s proven track record serving both Fortune 500 companies and growing, family-owned manufacturers has helped him become an important part of our team in a very short time.” Slick is currently studying business administration at Millersville University of Pennsylvania, Millersville, Pa., and coaches baseball for Central Mountain High School, Mill Hall, Pa. He resides in Malvern, Pa.
AAR reports Weekly Rail Traffic for the July and the week ending July 29, 2023
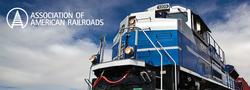
The Association of American Railroads (AAR) has reported U.S. rail traffic for the week ending July 29, 2023, as well as volumes for July 2023. U.S. railroads originated 875,660 carloads in July 2023, down 0.6 percent, or 5,599 carloads, from July 2022. U.S. railroads also originated 967,553 containers and trailers in July 2023, down 5.5 percent, or 56,737 units, from the same month last year. Combined U.S. carload and intermodal originations in July 2023 were 1,843,213, down 3.3 percent, or 62,336 carloads and intermodal units from July 2022. In July 2023, nine of the 20 carload commodity categories tracked by the AAR each month saw carload gains compared with July 2022. These included: motor vehicles & parts, up 6,437 carloads or 13.1 percent; crushed stone, sand & gravel, up 6,079 carloads or 7.5 percent; and primary metal products, up 2,935 carloads or 10.3 percent. Commodities that saw declines in July 2023 from July 2022 included: grain, down 15,585 carloads or 21.0 percent; coal, down 5,709 carloads or 2.2 percent; and pulp & paper products, down 1,631 carloads or 9.1 percent. “As the economy goes so goes rail traffic, and we’re seeing that with the mixed results across volumes being impacted by larger varying market conditions,” said AAR Senior Vice President John T. Gray. “The three non-July 4 weeks in July were the three highest volume intermodal weeks of the year, and carloads of chemicals rose in July for the first time in almost a year. At the same time, July was exceptionally weak for grain carloadings. July rail volumes are always impacted by Independence Day closures, so we are cautious to put too much stock in this month’s exact results, but there are reasons for both optimism and caution.” Excluding coal, carloads were up 110 carloads, or 0.0 percent, in July 2023 from July 2022. Excluding coal and grain, carloads were up 15,695 carloads, or 2.9 percent. Total U.S. carload traffic for the first seven months of 2023 was 6,719,395 carloads, up 0.4 percent, or 26,948 carloads, from the same period last year; and 7,081,148 intermodal units, down 9.6 percent, or 755,112 containers and trailers, from last year. Total combined U.S. traffic for the first 30 weeks of 2023 was 13,800,543 carloads and intermodal units, a decrease of 5.0 percent compared to last year. Week Ending July 29, 2023 Total U.S. weekly rail traffic was 483,481 carloads and intermodal units, down 2.6 percent compared with the same week last year. Total carloads for the week ending July 29 were 230,511 carloads, down 0.0 percent compared with the same week in 2022, while U.S. weekly intermodal volume was 252,970 containers and trailers, down 4.8 percent compared to 2022. Six of the 10 carload commodity groups posted an increase compared with the same week in 2022. They included nonmetallic minerals, up 2,381 carloads, to 34,599; motor vehicles and parts, up 2,331 carloads, to 15,353; and petroleum and petroleum products, up 1,644 carloads, to 10,211. Commodity groups that posted decreases compared with the same week in 2022 included grain, down 5,557 carloads, to 15,032; forest products, down 1,061 carloads, to 7,948; and coal, down 710 carloads, to 67,915. North American rail volume for the week ending July 29, 2023, on 10 reporting U.S., Canadian and Mexican railroads totaled 336,501 carloads, up 0.8 percent compared with the same week last year, and 333,238 intermodal units, down 7.3 percent compared with last year. Total combined weekly rail traffic in North America was 669,739 carloads and intermodal units, down 3.4 percent. North American rail volume for the first 30 weeks of 2023 was 19,360,049 carloads and intermodal units, down 4.1 percent compared with 2022. Canadian railroads reported 88,057 carloads for the week, up 3.0 percent, and 68,604 intermodal units, down 15.9 percent compared with the same week in 2022. For the first 30 weeks of 2023, Canadian railroads reported cumulative rail traffic volume of 4,723,996 carloads, containers and trailers, down 2.8 percent. Mexican railroads reported 17,933 carloads for the week, up 0.5 percent compared with the same week last year, and 11,664 intermodal units, down 3.6 percent. Cumulative volume on Mexican railroads for the first 30 weeks of 2023 was 835,510 carloads and intermodal containers and trailers, up 3.5 percent from the same point last year. To view the weekly rail charts, click here.
Episode 407: Avidbots automates warehouse cleaning
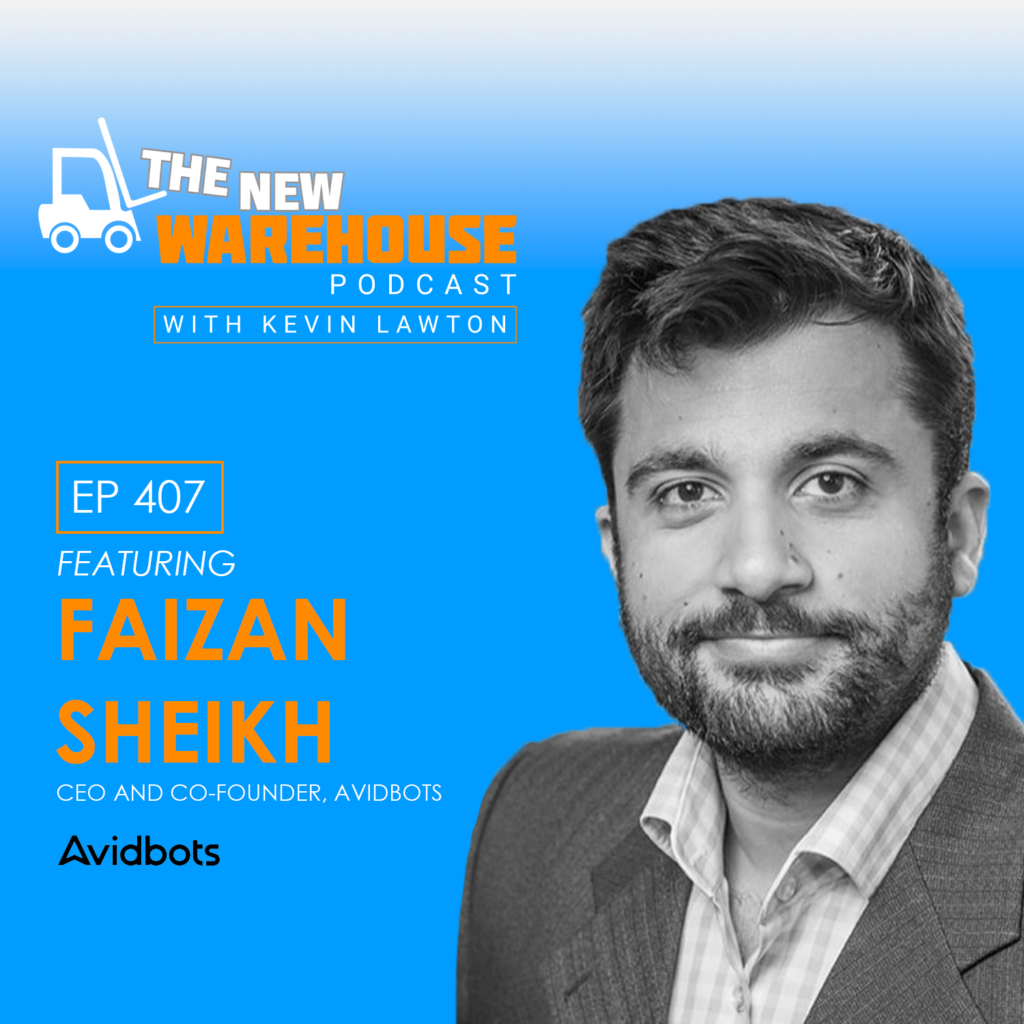
In this episode of the New Warehouse podcast, Kevin is joined by Faizan Sheikh, the CEO and Co-founder of Avidbots, a robotics company specializing in revolutionizing warehouse cleaning with advanced autonomous solutions. Faizan shares insights into their journey, from pivoting away from snow cleaning to developing robots for indoor cleaning, specifically in the warehouse and industrial spaces. Be sure to tune in as Kevin and Faizan discuss the importance of automation in the cleaning process and its impact on safety, employee morale, and warehouse productivity. The Benefits of Automating Warehouse Cleaning Faizan states, “The NEO 2W is a product we recently launched, specifically designed to handle the unique challenges of warehouse cleaning. Its debris diverter prevents choking caused by debris like pallet shrapnel and cardboard boxes, ensuring a more reliable and consistent cleaning process.” Avidbots designed the NEO 2W solution for warehouse and industrial environments with advanced obstacle avoidance and intelligent navigation; the NEO 2W efficiently cleans racking and bulk areas, providing a safer, cleaner work environment. Faizan believes by automating cleaning tasks; warehouses can improve productivity, retain employees, and send a positive message to their workforce. A cleaner warehouse is crucial not only for safety but also for employee morale. “If you can picture working in a warehouse full-time, it’s tough work. On top of that, if your warehouse is like a freaking dump, it creates more mental burden and strain. So people are trying to at least have a clean place for the people who show up and make it a bit more attractive.” The Labor Shortage and the Rise of Automation With a significant labor shortage in warehousing, companies struggle to find and retain workers. Automation of cleaning processes, like Avidbots’ NEO 2W, provides a reliable solution that ensures cleaning tasks are consistently performed. Faizan shares, “People are automating their cleaning because one, they can’t find the labor and retain it, and second, they want to automate their cleaning so that no matter what, the cleaning is getting done. The warehouse doesn’t become a dump, and the people who are already here start getting depressed and leave.” By reducing the reliance on manual labor for cleaning, businesses can focus on more complex tasks, improve employee satisfaction, and retain their workforce. A Vision for the Future of Avidbots Avidbots plans to continue leading the transition from manual to autonomous cleaning in the warehouse and industrial spaces. They are developing more robots and innovative solutions to automate processes. Faizan teases, “We’re cooking up more stuff to help automate the world.” By continuously improving and expanding its robot offerings, Avidbots aims to redefine the automation landscape, making warehouse operations more efficient and environmentally friendly. Key Takeaways from Avidbots Automated cleaning is a low-hanging fruit in terms of automation solutions for warehouses, offering numerous benefits such as improved safety, employee morale, and productivity. The labor shortage in the industry is driving the adoption of automation for critical cleaning tasks, ensuring consistent cleaning and a better work environment for employees. Avidbots’ NEO 2W is a game-changer in warehouse cleaning, equipped with a debris diverter and advanced obstacle avoidance technology, making it suitable for tackling warehouse-specific debris and tight spaces. The New Warehouse Podcast EP 407: Avidbots Automates Warehouse Cleaning
Industrial Batteries Australia Pty Ltd, Inc partners with BSLBATT
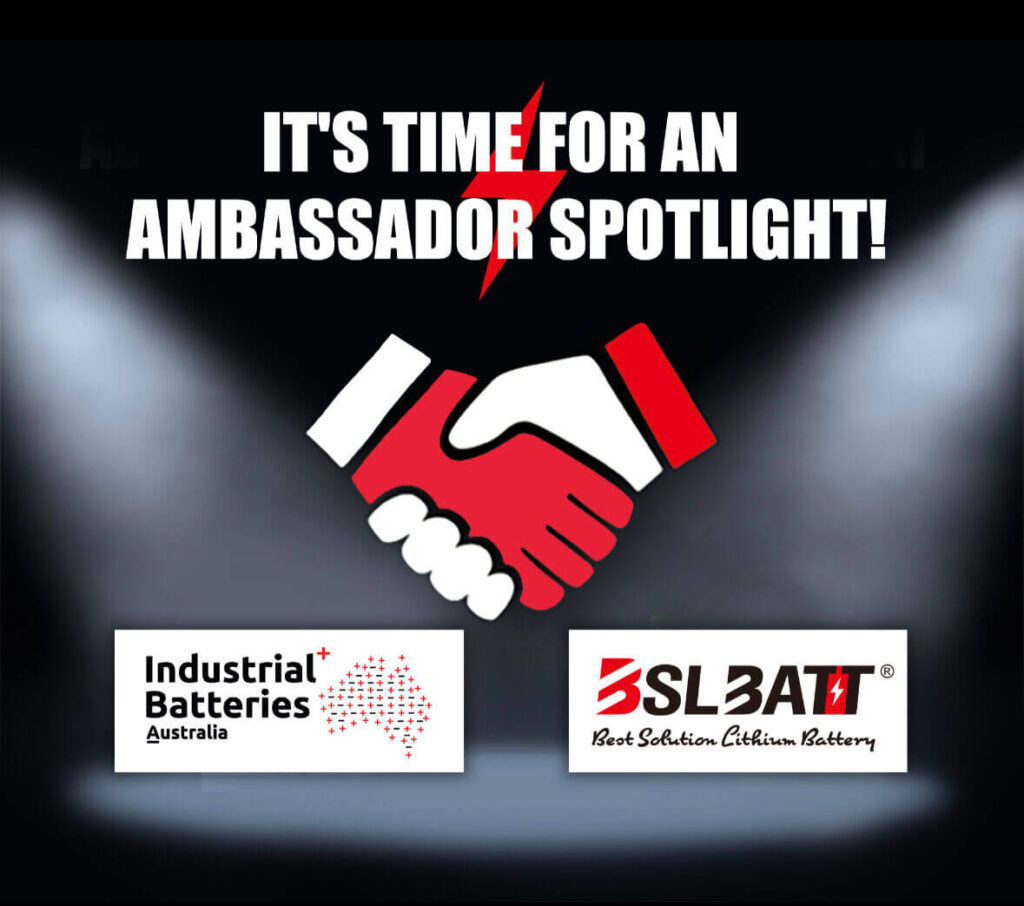
BSL Battery – Industrial, a world supplier of lithium-ion batteries for the material handling industry, just announced a partnership with Industrial Batteries Australia Pty Ltd, Inc., Australia’s largest independent supplier of power/forklift batteries and chargers. The agreement will see Industrial Batteries Australia add BSLBATT’s forklift lithium battery products to its current offering of power solutions for forklift dealers and end users looking to improve their forklift. “As Australia’s nationally leading supplier of power/forklift batteries and chargers, we are always looking for opportunities to form mutually beneficial partnerships, and that’s exactly what BSLBATT provides,” said Managing Director | David Cooper Founder of Industrial BatteriesAustralia Pty Ltd, Inc. “As a leader in lithium iron phosphate battery manufacturing, BSLBATT is looking to partner with local Industrial Batteries Australia Pty Ltd for companies looking to improve material handling, paper and packaging, food and beverage, refrigerated storage, manufacturing, fresh produce, wine and distribution and 3PL application battery customers to provide high-quality lithium battery solutions.” Cooper added. The advantages of BSLBATT’s LiFePO4 forklift batteries include greater power, lighter weight, significantly longer life, longer run times than conventional lead-acid batteries, and the ability to deliver more energy for higher consumption. Another significant benefit is that they are maintenance-free, whereas lead-acid requires active maintenance or a shortened lifespan. Our aim, through our partnership with Industrial Batteries Australia Pty Ltd, is to provide Australia with a trusted source to ensure the highest quality, most compatible power solutions and ultimately expand their business. ” “Our battery reseller program helps partners like Industrial Batteries Australia Pty Ltd build credibility and trust with consumers by leveraging the proven quality and reliability standards of UL Solutions and TUV Rheinland. We are excited to continue our longstanding relationship with Industrial Batteries Australia Pty Ltd, and further demonstrate the value of their lithium solutions.” said Haley Nin, Marketing Manager at BSLBATT. Industrial Batteries Australia Pty Ltd will supply customers with BSLBATT’s most popular lithium products including 24V, 48V and 80V batteries to power all types of equipment. “BSLBATT is a leading manufacturer of Lithium Iron Phosphate batteries across a wide range of applications and their high quality products will fit perfectly with our other power solutions,” said Cooper “BSLBATT’s batteries are great for customers looking to get the most out of their electric forklifts. Lithium batteries are a popular battery in the motorhome market today and Industrial Batteries Australia Pty Ltd is proud to offer the BSLBATT’s long-lasting, reliable power.” To learn more about Industrial Batteries Australia and BSL Battery – Industrial visit industrialbatteries.com.au and lithiumforkliftbattery.com
Yale launches new Power Key option to help warehouses change among lift truck motive power technologies
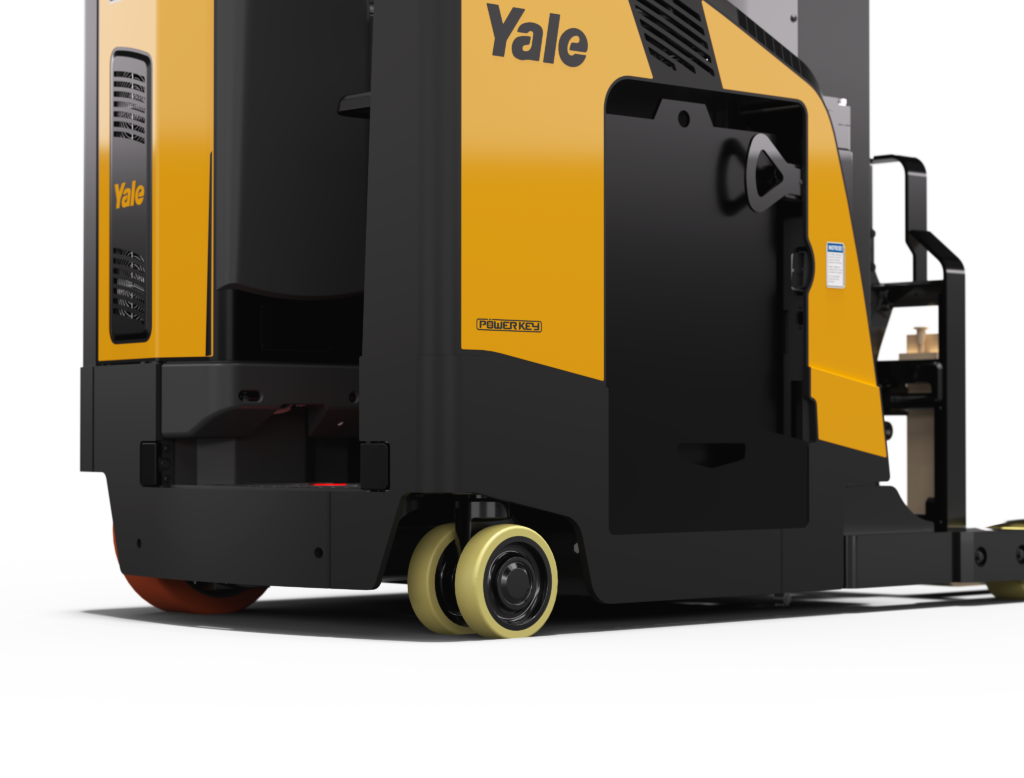
Solution adds thin plate pure lead to roster of power options, enables easy switch among all major battery electric sources Yale Lift Truck Technologies announces Power Key™, a one-of-a-kind solution engineered to provide flexibility in a world of increasing electric power options. Expanding on the previous offering, lithium-ion-ready lift trucks, Power Key allows operations to easily switch among not only lead-acid and lithium-ion, but now also thin plate pure lead (TPPL) battery modes, without external accessories. Like lithium-ion, TPPL produces zero emissions and enables opportunity charging but offers a lower acquisition cost, attributes that make it a strong consideration as a lift truck power option for some warehouses. “From charging and battery maintenance responsibilities to emissions, lift truck motive power has huge implications for warehouse labor, productivity and sustainability,” says Brad Long, Brand Manager, Yale Lift Truck Technologies. “Unrestricted choice is critical for warehouses to get their most efficient power source and supplier. But choice alone is not enough. This solution is a direct answer to customer demand for flexibility, equipping warehouses with seamlessly integrated technology that makes it fast and easy to transition among all three battery types.” Power Key is especially valuable for: Operations that have mixed fleets and need to continue to use lead-acid or are planning to transition to a fully maintenance-free fleet over time. Equipment used at multiple sites within an operation. Companies focused on accomplishing sustainability goals or regulations compliance. Electrification of internal combustion engine (ICE) fleets. Added resale value and broader buyer base for used equipment. Power Key is available on a broad lineup of electric lift truck models, including select narrow aisle rider, walkie pallet jacks, rider pallet trucks and sit-down counterbalanced trucks. Power Key-enabled trucks utilize an electronic Controller Area Network (CANbus) to handshake between the qualified supplier battery and the truck. To switch between power sources and battery suppliers, operators simply use the truck display or controller. When used with qualified lithium-ion and TPPL batteries, Power Key-enabled trucks also feature a battery-state-of-charge display incorporated within the system – no secondary display required – as well as a battery protection system that triggers the truck to engage a controlled shutdown when the battery reaches full discharge. In lithium-ion or TPPL mode, a low battery early warning system (EWS) also provides the operator with multiple warnings that the truck needs to be charged, based on timing that varies according to the approved battery supplier. For additional insight into battery performance and life, operations can access data through Yale Vision, an optional telemetry system.
Carolina Handling supports workforce development with donation of three forklifts to CCCC’s building bridges program
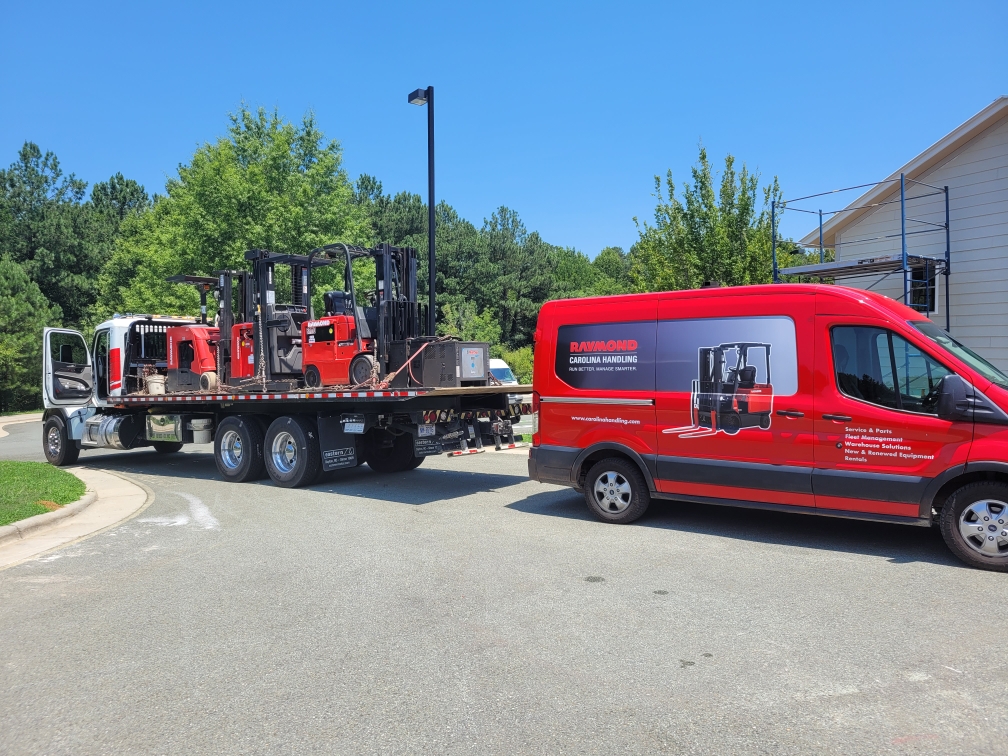
Carolina Handling is assisting workforce development efforts at Central Carolina Community College in Sanford, North Carolina, with the donation of three forklifts to the school’s Building Bridges program. A free, seven-day program for the unemployed, underemployed and those with a criminal record, Building Bridges is a job readiness boot camp that offers soft skills instruction alongside forklift training and OSHA-10 certification to make graduates job ready in a short time. Carolina Handling donated a Raymond sit down four-wheel forklift, Raymond standup counterbalance forklift and Raymond orderpicker to the program to give students well-rounded training on a variety of lift trucks used in manufacturing and distribution center environments. “This equipment was the deciding factor as to whether we could even stand this program up in Chatham County. It was the absolute deciding factor,” said Greg Singleton, Dean of Programs, Workforce Development & Continuing Education at Central Carolina Community College. “When I tell you that the college did not have the funds to even rent equipment, that’s how important this donation is.” For Carolina Handling, the contribution of equipment not only supports education and workforce training in the local community, but it also introduces participants to the company and career opportunities in material handling. “We’re competing for talent like many other companies across the Southeast,” said James Sanders, Director of Operations for Carolina Handling’s North Division. “We welcome opportunities to encourage careers in the material handling industry and to help develop prospective candidates. Building Bridges is a great ministry with a very passionate leader. I see this program making a difference in our community.” To date, CCCC’s Building Bridges program has graduated 74 participants, with 85 percent of them obtaining jobs or job interviews with employers such as Wolfspeed, Vinfast, 3M and the Food Bank of Central and Eastern North Carolina.