PTDA welcomes two new members
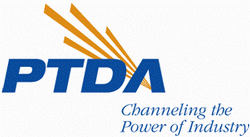
The Power Transmission Distributors Association (PTDA), an association for the industrial power transmission/motion control (PT/MC) distribution channel, welcomes Eastern Sales as a new distributor member and Proton.ai as an associate member. Distributor Eastern Sales, with over 50 years of combined experience, specializes in finding difficult-to-find items. Additionally, through its industrial belt division, the company can install belts as wide as 72 inches. “As a small independent distributor, the opportunity to join PTDA was a no-brainer. The relationships we will build within this network will give us the opportunity for growth,” says owner Grady Burchfield. Associate Proton.ai is an AI-powered customer relationship management program built specifically for distributors. It helps distributors transition from routine check-ins to proactive, consultative conversations. Using AI, the program identifies which customers need attention, locates lapsed accounts, and finds gaps in customer spending so representatives always know the best step to increase revenue. “We’re on a mission to help distributors adopt AI and modernize their sales process. We’ve seen impressive results with PTDA members using our CRM, and we’re excited to continue sharing best practices and drive meaningful revenue growth within the distribution industry and the PTDA community,” says Dasha Shakov, head of marketing.
Two Hyster leaders recognized as influential women in the industry
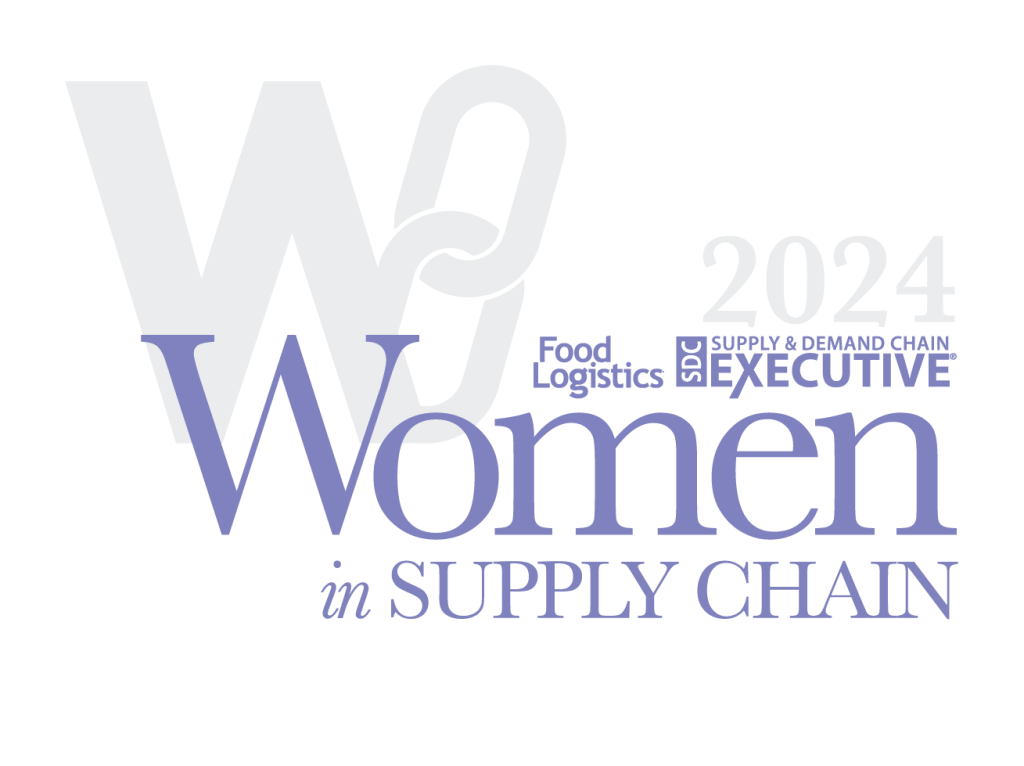
Lorri Lewis was named a trailblazer, Jennifer Timblin was honored as a rising star Hyster Company announces Director of Global Dealer Marketing Enablement Lorri Lewis and Global Big Truck Marketing Strategy and Activation Manager Jennifer Timblin are winners of the 2024 Women in Supply Chain awards, presented by industry publications Supply & Demand Chain Executive and Food Logistics. These awards honor female supply chain leaders whose accomplishments, mentorship, and examples set a foundation for women at all levels of the supply chain. “Lorri and Jennifer’s dedication and leadership at Hyster can’t be overstated,” says Jennifer Meyers, Brand Marketing and Global Activation Manager at Hyster. “Lorri has excelled in every role she’s held in her more than 40 years at Hyster and has paved the way for so many female leaders in our organization, including me. In such a short time, Jennifer has proven herself indispensable and progressed through roles with increasing responsibility, starting as an administrative assistant to now holding a global leadership position for this renowned brand. Both women have had and continue to have a huge impact at Hyster and truly deserve this recognition.” A third-generation Hyster employee with two sons who have followed in her footsteps, Lewis is a true trailblazer in materials handling. Throughout her long tenure, she has applied her tremendous skills in many areas, from graphic design, brand marketing, and event planning to sales, dealer relations, and even inventory analysis. But she is perhaps best known for developing highly successful events, including attention-grabbing booths for the industry’s largest tradeshows and leading hundreds of “roadshows.” During roadshows, Lewis is out in the field herself, helping to host customers at dealer locations or visiting the customer’s own facility to learn more about their specific application. She has been recognized by her peers and leaders for going above and beyond for customer satisfaction, earning the first HYCare award granted by the company’s major accounts team. Timblin is a self-motivated rising star in the supply chain who progressed through the Hyster organization in less than a decade to her current role, in which she manages a team and leads global marketing efforts for the brand’s big truck line of high-capacity forklifts and container handling equipment. She has also managed public relations and communications resources in the Americas, as well as product launch support for the Asia-Pacific region. In recent years, Timblin has organized several high-profile events for Hyster and has championed the brand’s commitment to developing zero-emission solutions that can help even heavy-duty industries make the shift to clean power alternatives for materials handling equipment traditionally powered by diesel and internal combustion engines (ICE). As a manager and mentor, Timblin helps others to identify and act on opportunities to grow their careers. She encourages her employees and mentees to be proactive about their own professional development and is intentional about having conversations with colleagues to understand what work they find fulfilling, outline goals, and pave pathways to help achieve them.
ALAN HURRICANE HELENE SITUATIONAL REPORT for Monday September 30
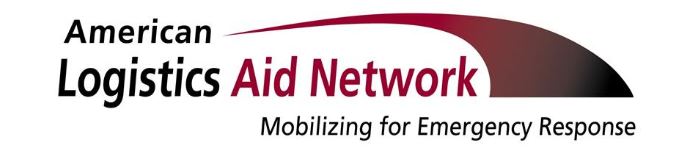
ALAN has been improving logistics response in disasters for 19 years, and the need is greater now than ever. Please donate today to help us continue our work for many more years to come American Logistics Aid Network is mobilized for Hurricane Helene. As part of our response efforts, we are committed to providing you with the latest information and updates on supply chain impacts via our periodic Situation Reports, which can be found below in this email and on our website. A message from ALAN Executive Director Kathy Fulton: Ordinarily, I am a glass-half-full kind of person. But when I look at what’s happened to the residents of Western North Carolina, Florida’s Big Bend, and other parts of the Southeast this past week, I find myself at a loss. The images of Hurricane Helene’s flooding, debris, and devastation are heartbreaking, especially when they are combined with the realization that so many people have lost their lives or remain missing – and that so many still await rescue. Many people have lost their homes, loved ones, pets, or business locations. And there is no sugar-coating how long and difficult the path to recovery will be. There’s so much to do that it’s difficult to know where to start. Thankfully, several great minds can point us in the right direction, including St. Francis of Assisi, who reportedly once advised, “Start by doing what’s necessary, then by doing what’s possible. . . ” Here at ALAN, those words make a lot of sense to us. Looking at our Disaster Micro-Site in the coming weeks, you’ll undoubtedly find numerous tangible examples of “what’s necessary” in the requests we’ll post for donated logistics assistance under our “Active Logistics Needs” tab. I hope that you will consider fulfilling one of them yourself—or that you will pass it along to any of your members, colleagues, or co-workers who might be willing to help. We also have a keen sense of “what’s possible” because, after 19 years of providing disaster relief, we know that when the right people work together to address a challenge efficiently and collaboratively – as so many government and humanitarian relief organizations are doing right now – amazing things can happen. Perhaps most importantly, we understand just how fortunate we are to be part of an industry that can play such a meaningful role in delivering help and hope. In closing, allow me to circle back to the quote I used at the beginning because there’s one part I left out: “Start by doing what’s necessary, then by doing what’s possible; and suddenly, you are doing the impossible.” Things may indeed look like an impossible-to-solve situation right now. But with folks like you in our corner, I know that recovery and resilience will happen. Thank you for being one of the best and brightest parts of my job. My glass wouldn’t be nearly as full without you. CRITICAL MESSAGES North Carolina Business Operations Center: Partners moving people, resources or equipment into western North Carolina, MUST coordinate plans and movements through the NCEM-BEOC. Help us keep critical supply lines open. Please do not self-deploy resources or supply logistics without coordinating with the BEOC. There is a high likelihood that your team(s) will be turned away at various checkpoints. We will prioritize movements and provide safe routes with an escort, as needed. You can email your supply logistics or movement requests to: BEOC@ncdps.gov Begin Subject Line with: Logistics Support Please include the following info: What are you moving? Why you need special access. When do you plan to move and from where? Where are you going? When will they arrive at the “border to Western NC” and where? In summary, until further notice, roads in Western NC (generally anywhere west of Hickory, NC) are closed to all traffic other than emergency services and pre-approved shipments coordinated through the BEOC. ITEMS OF INTEREST PSEMA Tropical Storm Helene Coordination Call via Zoom on Wednesday, October 2, 2024 at 4pm EDT. Join Zoom Meeting https://us02web.zoom.us/j/88943138859?pwd=8IPEcHNNyg0tPrO0R5FdbGY1rh84Hh.1 Meeting ID: 889 4313 8859 Passcode: 046808 OPEN CASES ALAN has begun to receive requests for donated logistics services to support Hurricane Helene response. We are looking to fill the following open cases: Case 9512: Request for Transportation of 120 Pallets – Plywood – from Deerfield Beach, FL 33441 to Ocala, FL 34474 FEDERAL EMERGENCY DECLARATIONS President Biden approved Major Disaster Declaration for South Carolina on September 29, 2024, in response to Hurricane Helene. President Biden approved Emergency Declaration for Virginia on September 29, 2024, in response to Hurricane Helene. President Biden approved a Major Disaster Declaration for Florida on September 28, 2024, in response to Hurricane Helene. President Biden approved Major Disaster Declaration for North Carolina on September 28, 2024, in response to Hurricane Helene. President Biden approved Emergency Declaration for Tennessee on September 28, 2024, in response to Hurricane Helene. President Biden approved Emergency Declaration for South Carolina on September 26, 2024, in preparation for impacts from Hurricane Helene beginning on September 25, 2024, and continuing. President Biden approved Emergency Declaration for Alabama on September 26, 2024, in preparation for impacts from Hurricane Helene beginning on September 22, 2024, and continuing. President Biden approved Emergency Declaration for North Carolina on September 26, 2024, in preparation for impacts from Hurricane Helene beginning on September 25, 2024, and continuing. President Biden approved Emergency Declaration for Georgia on September 26, 2024, in preparation for impacts from Hurricane Helene beginning on September 24, 2024, and continuing. President Biden approved Emergency Declaration for Florida on September 24, 2024, in preparation for impacts from Tropical Storm Helene beginning on September 23, 2024, and continuing. STATE STATE DECLARATIONS Tennessee Governor Lee issued Executive Order No. 105 on September 27, 2024, in response to Hurricane Helene. West Virginia Governor Justice issued Proclamation declaring a State of Preparedness on September 26, 2024, in response to Hurricane Helene. Virginia Governor Youngkin issued Executive Order No. 37 on September 25, 2024 declaring a state of emergency due to Hurricane Helene. South Carolina Governor McMaster issued Executive Order 2024-24 on September 25, 2024, in preparation for impacts from Hurricane Helene. North Carolina Governor Cooper issued Executive Order No. 315 on September 25, 2024, declaring a statewide state of emergency and
Port strike still on schedule, union says
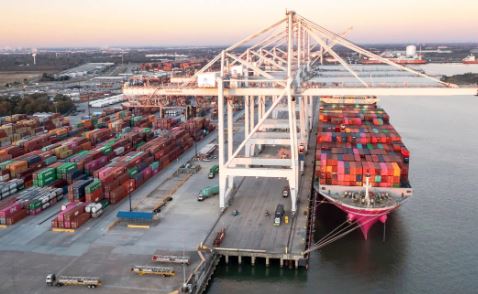
Thousands of dockworkers to walk off the job Tuesday Tens of thousands of dockworkers at East and Gulf Coast ports reaffirmed plans to walk off the job when the current contract with port employers expires as of 12:01 a.m. on Tuesday. The International Longshoremen’s Association in a statement Sunday reaffirmed its plans to set up pickets Oct. 1 at ports from Maine to Texas in a job action that directly involves 25,000 workers in container and ro-ro services. The union charged that the United States Maritime Alliance (USMX) representing terminal operators and ocean carriers “refuses to address a half-century of wage subjugation where Ocean Carriers (sic) profits skyrocketed from millions to mega-billion dollars, while ILA wages remained flat.” The union is reportedly seeking a pay hike of as much as 70% over the six years of a new contract. The International Longshore and Warehouse Union representing West Coast dockworkers in 2023 negotiated wage increases of around 32%. A strike would affect ports handling $92 billion or two-thirds of U.S. trade, idling container handling at the Port of New York-New Jersey, the country’s second-busiest box hub, as well as car and truck imports into Baltimore, the leading gateway for vehicle imports. The USMX did not immediately respond to emails seeking comment. President Joe Biden, who has wooed union support for the general election that is just weeks away, said he would not block a strike. The Taft-Hartley Act gives the president powers to intervene and order a cooling-off period while negotiations resume, but the White House has said it has no plans to force longshore employees back to work. Manufacturers and other shippers spent most of the summer frontloading imports for the end-of-year retail season in a bid to get ahead of a possible strike and global port congestion worsened by rebel attacks on shipping through the Red Sea. Ports in the U.S. saw early peak traffic, and industry observers say a relatively short strike may have little immediate effect. However, industries such as produce importers and others that rely on lean inventories and just-in-time deliveries could see their businesses pressured early on.
ALAN HURRICANE HELENE SITUATIONAL REPORT September 27, 2024
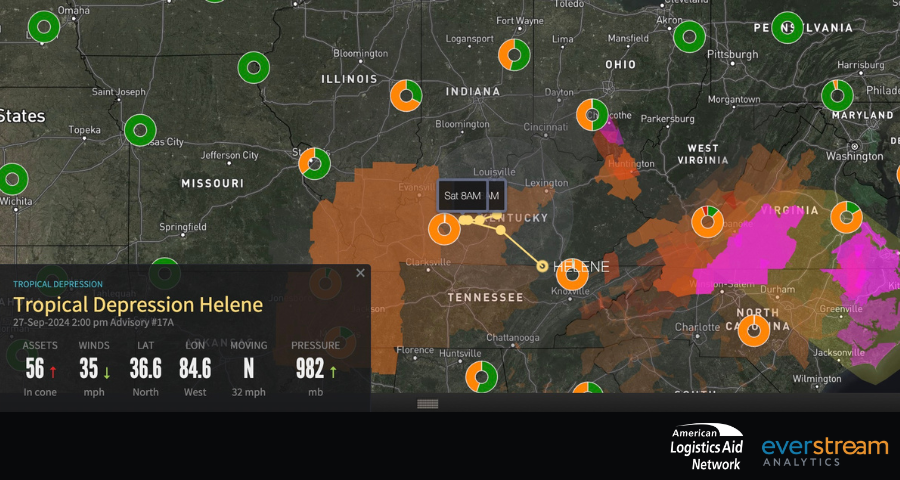
ALAN has been improving logistics response in disasters for 19 years, and the need is greater now than ever before. Please donate today to help us continue our work for many more years to come American Logistics Aid Network is mobilized for Hurricane Helene. As part of our response efforts, we are committed to providing you with the latest information and updates on supply chain impacts via our periodic Situation Reports, which can be found below in this email and on our website. As you know, Hurricane Helene made landfall in Florida’s Big Bend region late Thursday night. Since then, ALAN has heard from many people anxious to know, “What can we do?” (Thank you for all of those questions!) We hope to have specific answers soon because we are working closely with the non-profit community to determine what is needed. As their requests for assistance begin to arrive (some of which we’re vetting now), we will share them via our Disaster Micro-Site and other channels. Meanwhile, there are still many ways we can put our shoulders to the wheel and begin to help—which is why we’d like to pass along the following practical Do’s and Don’ts. DO make sure your employees are safe – and supported. Don’t forget that we’re here for you. Do let us know if you are willing to help. Don’t assume you can’t be of help just because your operations are nowhere near the damaged areas. DO check ALAN’s website and Disaster Micro-Site often over the next few weeks. DON’T host a collection drive for products. DO consider helping in other ways instead. For a full elaboration on these points, please read our latest blog at https://www.alanaid.org/alans-helpful-post-hurricane-relief-dos-and-donts-3/ PSEMA Tropical Storm Helene Coordination Call via Zoom on Saturday, September 28, 2024, at 1 pm EDT. Join Zoom Meeting https://us02web.zoom.us/j/88943138859?pwd=8IPEcHNNyg0tPrO0R5FdbGY1rh84Hh.1 Meeting ID: 889 4313 8859 Passcode: 046808 OPEN CASES ALAN has begun to receive requests for donated logistics services to support the response to Hurricane Helene. We are looking to fill the following open cases: Case 9512: Request for Transportation of 120 Pallets of plywood – from Deerfield Beach, FL 33441 to Ocala, FL 34474 Case 9510: Request for Transportation of 10 Pallets – Tarps – from West Palm Beach, FL 33401 to Winter Haven, FL 33881 FEDERAL EMERGENCY DECLARATIONS President Biden approved Emergency Declaration for South Carolina on September 26, 2024, in preparation for impacts from Hurricane Helene beginning on September 25, 2024, and continuing. President Biden approved Emergency Declaration for Alabama on September 26, 2024, in preparation for impacts from Hurricane Helene beginning on September 22, 2024, and continuing. President Biden approved Emergency Declaration for North Carolina on September 26, 2024, in preparation for impacts from Hurricane Helene beginning on September 25, 2024, and continuing. President Biden approved Emergency Declaration for Georgia on September 26, 2024, in preparation for impacts from Hurricane Helene beginning on September 24, 2024, and continuing. President Biden approved Emergency Declaration for Florida on September 24, 2024, in preparation for impacts from Tropical Storm Helene beginning on September 23, 2024, and continuing. STATE STATE DECLARATIONS Virginia Governor Youngkin issued Executive Order No. 37 on September 25, 2024 declaring a state of emergency due to Hurricane Helene. South Carolina Governor McMaster issued Executive Order 2024-24 on September 25, 2024, in preparation for impacts from Hurricane Helene. North Carolina Governor Cooper issued Executive Order No. 315 on September 25, 2024, declaring a statewide state of emergency and temporary waiver and suspension of motor vehicle regulations. Georgia Governor Kemp issued Executive Order on September 24, 2024, declaring a State of Emergency for Tropical Storm Helene. Florida Governor DeSantis issued Executive Order 24-209 on September 24, 2024, amending Executive Order 24-208. Florida Governor DeSantis issued Executive Order 24-208 on September 23, 2024, in preparation for impacts from potential tropical cyclone nine. ACTIVE TRANSPORTATION WAIVERS Title: Alabama Department of Revenue Commissioner Issued Executive Order Effective: 09/27/24| Expires on: 10/27/24 Description: The Alabama Department of Revenue Commissioner issued an executive order providing temporary suspension of the motor fuel exporter, importer, and transporter licensing requirements associated with the Alabama Terminal Excise Tax for those supporting disaster relief efforts by engaging in the export of motor fuel from Alabama to areas in other states impacted by Hurricane Helene. Title: Alabama Department of Revenue Commissioner Issued Executive Order Effective: 09/27/24| Expires on: 10/27/24 Description: The Alabama Department of Revenue Commissioner issued an executive order providing temporary suspension of the requirements associated with the International Registration Plan and International Fuel Tax Agreement for any motor vehicle engaged in interstate disaster relief that will be traveling through the State of Alabama as part of the disaster relief. Title: Virginia Department of Transportation Secretary issued Transportation Waiver on September 26, 2024 Effective: 09/26/24| Expires on: 10/02/24 Description: The Virginia Department of Transportation Commissioner issued a transportation waiver granting temporary overweight, over width, registration, license, or hours of service exemptions to all carriers transporting essential emergency relief supplies to, through, and from any area of the Commonwealth. The authorization applies also applies to water, food, heating oil, motor fuels or propane, agricultural products, agricultural supplies, livestock, and poultry, forest products and salvaged wood, waste, and trees cut in preparation for the storm, or providing restoration of utilities. Title: South Carolina Governor McMaster issued Executive Order 2024-24 on September 25, 2024 Effective: 09/25/24| Expires on: 10/25/24 Description: In accordance with section 56-5-79(A) of the South Carolina Code of Laws, as amended, during a declared emergency and in the course of responding to the emergency, requirements related to registration, permitting, length, width, weight, and load are suspended for commercial and utility vehicles traveling on non-interstate routes for up to 120 days; and requirements relating to time of service suspensions for commercial and utility vehicles traveling on interstate and non-interstate routes are suspended for up to 30 days, unless extended for additional periods under the FMCSR. Whereas the FMCSR limits the hours of service for operators of commercial vehicles and pursuant to 49 CFR 390.23, the Governor may suspend federal hours of service regulations if the governor determines an emergency condition exists. Title: North Carolina Governor Cooper issued Executive Order No. 311 Effective: 09/25/24| Expires on: 10/05/24 Description: North Carolina Governor Cooper issued Executive Order No. 315 on September 25, 2024, declaring a State of Emergency and temporary waiver and
Green Cubes Technology announced UL Listing with EE Rating for Lithium SAFEFlex PLUS
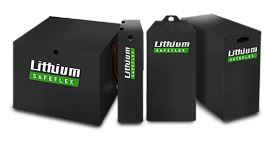
Green Cubes Technology has announced the launch of its Lithium SAFEFlex PLUS batteries based on UL recognized modules and the UL listing for their 48V battery family. This innovative product line continues Green Cubes’ legacy of pushing electrification forward, providing cutting-edge power solutions for material handling, ground support equipment, automated vehicles and other motive products. For many years, Green Cubes has been at the forefront of electrification innovations. The company recently celebrated a decade of leadership in motive power technology for material handling and ground support equipment with its flagship suite of Lithium SAFEFlex Battery solutions; there are more than 10,000 batteries in the field, representing over 300MWh. “We are thrilled to announce the UL listing and EE rating of Lithium SAFEFlex PLUS, which represents a significant advancement in our product offerings, leveraging our 10+ years of experience with the groundbreaking Lithium SAFEFlex product line,” said Michael Walsh, CEO at Green Cubes Technology. “During my 18-month tenure as CEO, we have focused on strengthening our business processes and enhancing customer support while reinvesting in new products and aftermarket service upgrades that better meet the needs of customers.” Key Features of Lithium SAFEFlex PLUS Modular Design: UL recognized module with functional safety facilitates family safety certifications and simplifies ongoing safety approvals. Enhanced Feature Set: Developed based on a decade of experience with Lithium SAFEFlex, PLUS offers superior performance, state-of-charge monitoring and balancing. Reliability and Serviceability: Lithium SAFEFlex PLUS battery systems are designed with modular cell blocks and a battery control module that simplify technician access and field service replacement. Compatibility: Sized to fit standard material handling lead-acid battery compartments and meet truck battery weight requirements. Green Cubes will continue to offer the original Lithium SAFEFlex product line for customers that require the versatility and value it brings. These solutions are designed to meet the cost, performance, efficiency, and durability requirements of rugged warehouse, distribution, and airport environments.
Rennco Launches the EZ20 Vertical Bagger at PACK EXPO 2024
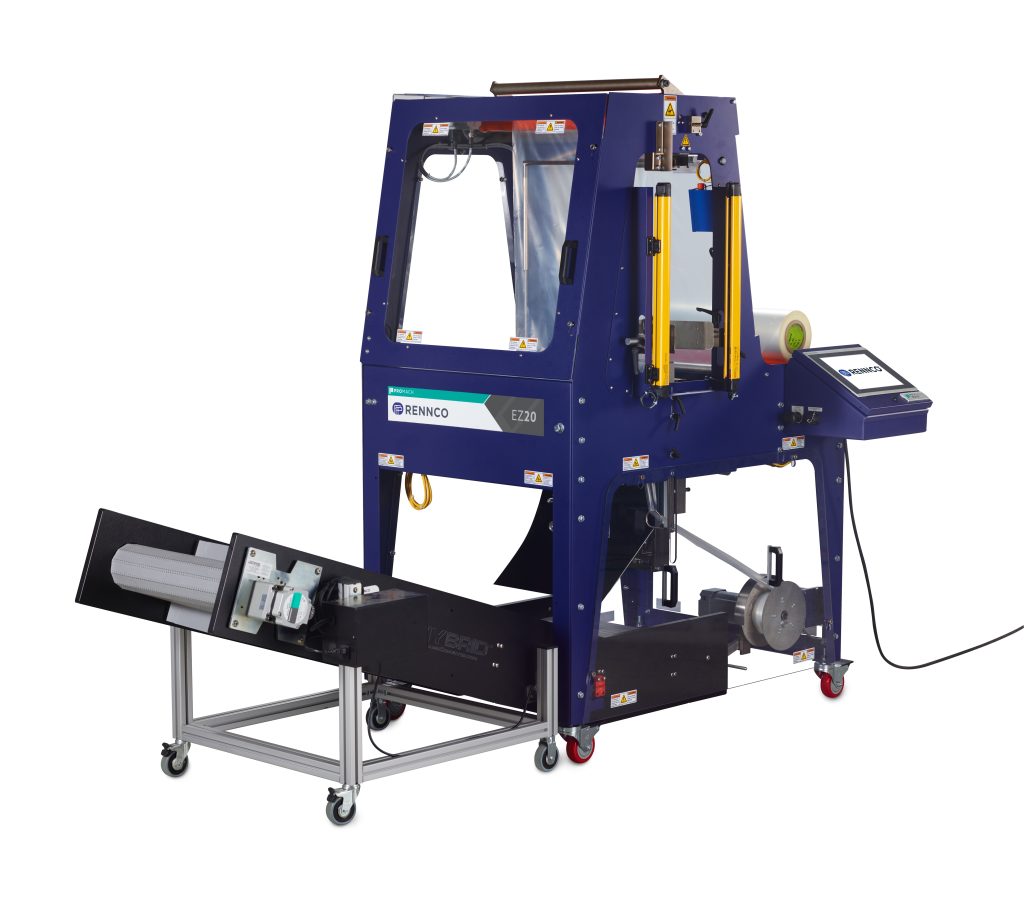
Add Rennco in booth S-3660 to your PACK EXPO 2024 itinerary to see how its vertical bagging solutions can add speed and efficiency to your next packaging application. Looking for a cost-effective way to automate your hand-packing operation? Then look no further than Rennco and its new EZ20 Vertical Bagger, which will be demonstrating its capabilities in booth S-3660 at PACK EXPO 2024, Nov. 3-6, at McCormick Place in Chicago. EZ20 Vertical Bagger Founded in 1969, Rennco has earned a reputation for high-performance bagging solutions that are rugged and durable for 24/7 operation. The new EZ20 brings those high-performance qualities of the Rennco brand to an entry-level model that is competitively priced compared to other similar machines. The all-electric EZ20 is a compact machine with a small footprint. The machine uses centerfolded film to create custom bags tailored to customers’ specific products and needs. The EZ20 represents more than two years of research and development by the Rennco team. Surveyed customers indicated a need for an entry-level machine that incorporates the strengths of Rennco with a cost-effective and easy-to-use bagging solution. Features and benefits of the new EZ20 Vertical Bagger include: Easy to load and operate Centerfolded film, no pre-made bag contracts Compatible with polyethylene and polyolefin (shrink) films User-friendly Allen Bradley HMI All-electric (no air required) – plugs into standard 110V wall outlets Speeds up to 25 packages per minute Pairable with optional discharge conveyor Interlocked perimeter guarding Flexibility to accommodate printers or labelers Ideal for a wide variety of consumer-packaged goods products and e-commerce applications Performance specifications of the EZ20 Vertical Bagger include: 14” standard vertical seal 20” standard horizontal seal 2” x 2” minimum to 14” x 20” maximum bag sizing 5 lb. maximum filled bag weight 4 1/2” – 9” standard jaw opening ProCommerce Vertical Bagging Series In addition to the EZ20, PACK EXPO attendees will see other Rennco bagging solutions in action. This includes the ProCommerce Vertical Bagging Series, which produces custom bags lined with bubble mailing material for e-commerce applications. The ProCommerce bagging solution utilizes flat stock material lined with bubble wrap to create custom right-sized packages in the vertical dimension. ProCommerce eliminates the use of costly pre-made bags that are often oversized for the product, which leads to increased materials and shipping costs. The ProCommerce bagging solution provides added flexibility to users as it can run bubble mailing material or opaque mailing film, covering virtually all aspects of e-commerce packaging and shipping needs. Lift Seal™ Heat Sealer The Lift Seal™ Heat Sealer provides an efficient alternative to impulse, band, and rotary sealers for bagging surgical instruments and supplies. The Lift Seal™ Heat Sealer is easy to maintain and simple to operate. Constant temperature is maintained by a digital temperature control during the sealing process. The lower silicone rubber bar is raised by a rugged mechanical drive to meet the stationary half-inch wide heating sealing bar above. This bar is covered with a special “non-stick” fabric, which is advanced by simply turning a knob as the fabric becomes worn. The fabric roll is ample for months of use and is quickly replaced by snapping the new roll into position. Rennco / Edson Packaging Collaboration Finally, show attendees will see a new packaging solution that merges the best technical expertise Rennco and Edson have to offer. This new packaging solution stars a Micro VCCL (Vertical Cup Counter Loader) from Rennco, feeding packaged stacks of cups to an Edson M1000 to efficiently collate and package paper cups into individual stacks and then load those stacks into cases. The Micro VCCL is engineered to package high volumes of paper cups in a compact unit that reduces floor space by 30 percent over a standard Rennco VCCL unit -all without sacrificing speed or reliability. The Micro VCCL is integrated with the M1000, an all-in-one case erecting and packing system from Edson. The M1000 takes knocked down flats (KDFs) and erects them into cases. The machine then side loads packaged stacks of cups into the newly formed cases, which are sealed and made ready for shipment.
Queen City Robotics Alliance announced New Board Member
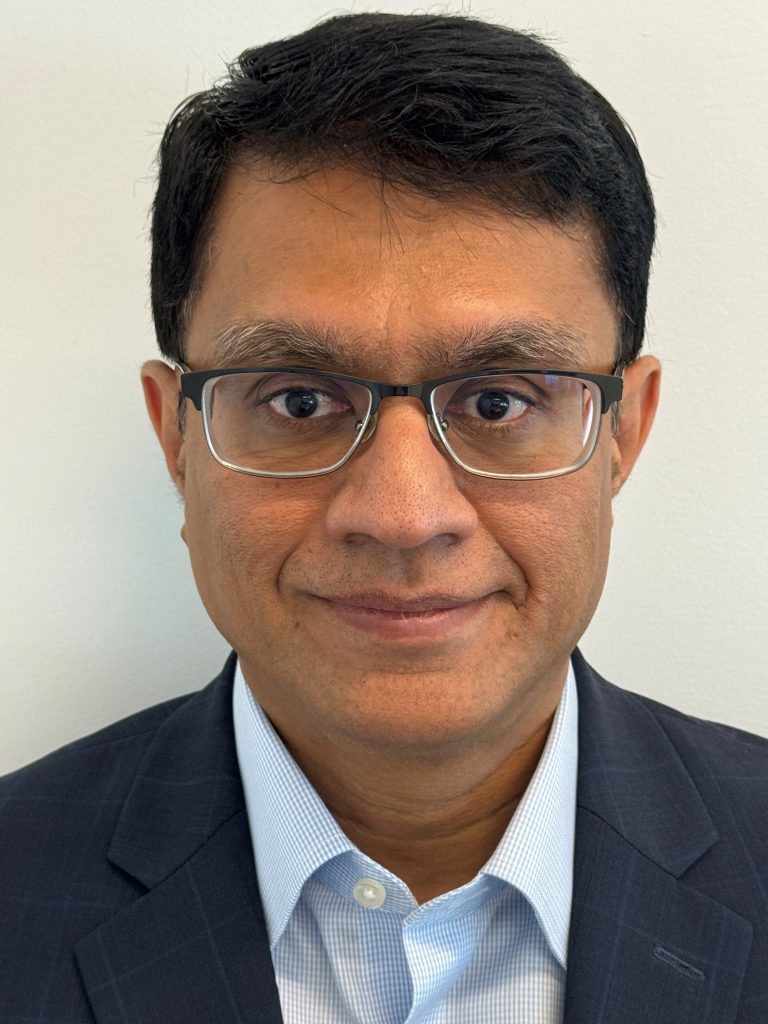
Queen City Robotics Alliance has announced the addition of a new board member – Puneet Mody of Infosys. Mr. Mody is a long-time Charlotte resident having been at Infosys for the last 20 years where he is the Vice President and Regional Head of US Financial Services. He will bring his expertise in both finance and technology to QCRA. Mody has been volunteering in youth robotics for some time including the planning committee for FIRST® North Carolina and as a mentor for area FIRST robotics teams. He also sponsors the Infosys Tech Pioneer program teaching AI to college students. He looks forward to working with QCRA. “QCRA provides an amazing platform for students to explore and excel in robotics,” he says. “Their commitment to providing resources, mentorship, and support across different levels of robotics has helped numerous teams shine at the state, regional, and world stage. Having experienced this commitment firsthand, I am excited to further expand QCRA’s mission.”
SuperCorrExpo® 2024 comes to a close, exceeding expectations
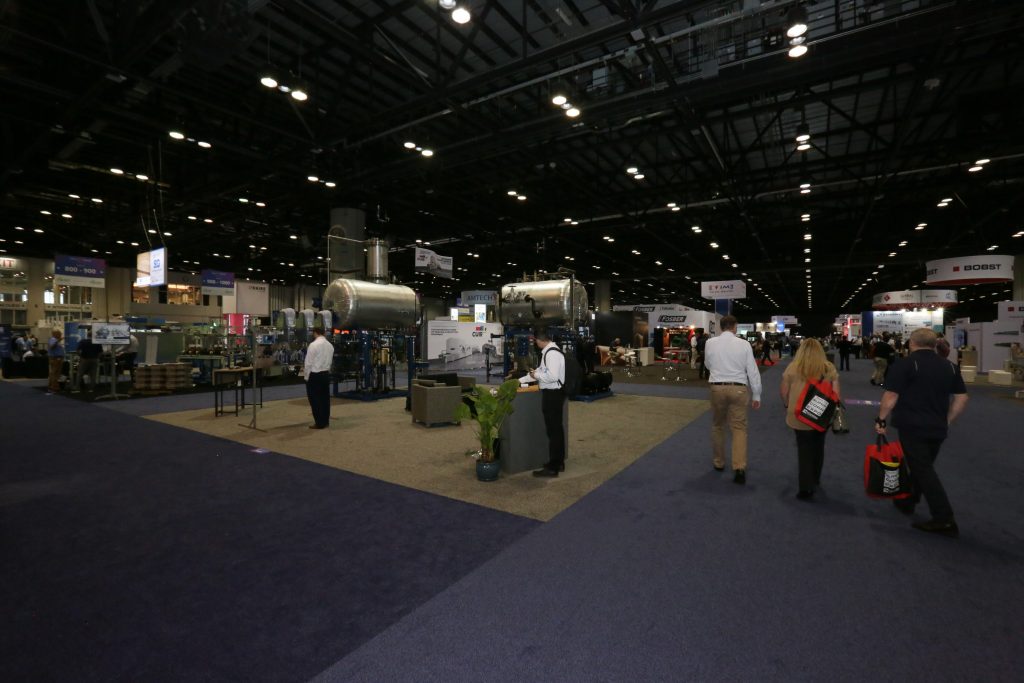
The event succeeds in welcoming the future of the corrugated industry SuperCorrExpo® 2024, one of the most highly anticipated events in the corrugated industry, wrapped up its successful five-day run. From September 8th-12th at the Orange County Convention Center in Orlando, Florida, the event brought together industry leaders, innovators and professionals from across the globe. The event attracted 3,964 attendees, with hundreds of box plant representatives in attendance, all eager to explore the latest technologies, solutions and trends shaping the future of the corrugated industry. SuperCorrExpo® also hosted 276 exhibitors, showcasing groundbreaking innovations in automation, robotics, digital printing, sustainability and more. Exhibitors and attendees alike left the event feeling inspired and energized, highlighting the invaluable connections they formed and deepened: “At SuperCorrExpo®, we are really able to focus down on the machines without the distractions of the factory environment.” –Danny Lopez, Vice President, New Machinery Sales at Haire “As a smaller, growing company, SuperCorrExpo® has been an amazing opportunity to connect with potential strategic partners.” –Brian Zernia, Account Executive at Dynamic Dies, Inc. “SuperCorrExpo® delivers a showcase of technology and advancements in a friendly environment, where catching up with industry friends and discussing business live in person are paramount.” –Brett Kirkpatrick, Director of Trade Business at The BoxMaker. Throughout the event, attendees had the opportunity to engage in insightful sessions covering key topics like artificial intelligence (AI), sustainability and digital transformation, as well as participate in hands-on demonstrations of the latest machinery and software solutions. The show floor was buzzing with activity as participants explored innovations that aim to drive the future of corrugated packaging. SuperCorrExpo® continues to be a hub for industry professionals to connect, collaborate and discover new opportunities that propel their businesses forward. Plans for SuperCorrExpo® 2028 are already underway, promising an even bigger and better experience for the global corrugated packaging community.
ALAN Hurricane Helene situational report September 24, 2024
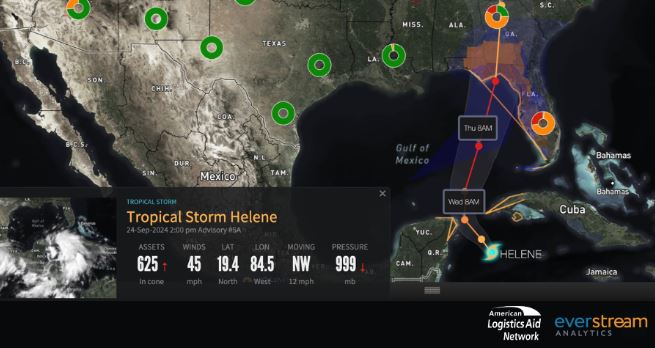
ALAN has been improving logistics response in disasters for 19 years, and the need is greater now than ever before. Please donate today to help us continue our work for many more years to come American Logistics Aid Network (ALAN) is mobilized for Hurricane Helene. As part of our response efforts, we are committed to providing you with the latest information and updates on supply chain impacts via our periodic Situation Reports, which can be found below in this email and on our website. Ahead of Hurricane Helene’s landfall along the Gulf Coast, the American Logistics Aid Network (ALAN) is urging residents in the storm’s path across the southeast to heed evacuation notices and safety advisories – and reminding members of the logistics community that their post-storm help could be needed soon. In addition to working closely with the non-profit and emergency response community, ALAN is providing real-time visibility on the storm’s supply chain impacts—including damages to roads, ports, and airports—via its Supply Chain Intelligence Center, which individuals and businesses can access free of charge. ALAN has also updated its Disaster Micro-Site with helpful Hurricane Helene resources. That site is where ALAN will post requests for donated logistics assistance, most of which will arrive within 24 to 72 hours after the storm’s initial landfall. Logistics businesses that wish to make a financial donation to ALAN instead can do so by visiting https://www.alanaid.org/donate/. ITEMS OF INTEREST PSEMA Tropical Storm Helene Coordination Call via Zoom Join Zoom Meeting https://us02web.zoom.us/j/88943138859?pwd=8IPEcHNNyg0tPrO0R5FdbGY1rh84Hh.1 Meeting ID: 889 4313 8859 Passcode: 046808 FEDERAL EMERGENCY DECLARATIONS President Biden approved Emergency Declaration for Florida on September 24, 2024, in preparation for impacts from Tropical Storm Helene beginning on September 23, 2024, and continuing. STATE STATE DECLARATIONS North Carolina Governor Cooper issued Executive Order No. 315 on September 25, 2024, declaring a statewide state of emergency and temporary waiver and suspension of motor vehicle regulations. Georgia Governor Kemp issued Executive Order on September 24, 2024, declaring a State of Emergency for Tropical Storm Helene. Florida Governor DeSantis issued Executive Order 24-209 on September 24, 2024, amending Executive Order 24-208. Florida Governor DeSantis issued Executive Order 24-208 on September 23, 2024, in preparation for impacts from potential tropical cyclone nine. ACTIVE TRANSPORTATION WAIVERS Title: North Carolina Governor Cooper issued Executive Order No. 311 Effective: 09/25/24| Expires on: 10/05/24 Description: North Carolina Governor Cooper issued Executive Order No. 315 on September 25, 2024, declaring a State of Emergency and temporary waiver and suspension of motor vehicle regulations. Shall waive the maximum hours of service for drivers prescribe by DPS pursuant to N.C. Gen Stat. 20-381 and pursuant to 49 CFR 390.23, waive 49 CFR 395.3 for persons transporting essential fuels, food, water, non-alcoholic beverages, medical supplies, feed for livestock and poultry, persons transporting livestock, poultry or crops ready to be harvested, and vehicles used in the restoration of utility or transportation services. Shall waive enforcement of certain size and weight restrictions and penalties arising under N.C. Gen Stat. 20-86.1 and 20-119 for vehicles supporting emergency relief efforts in the emergency area Title: Kentucky Transportation Secretary issued Declaration of Emergency Order 113789 Effective: 09/24/24| Expires on: 10/08/24 Description: Kentucky Transportation Secretary Gray issued a Declaration of Emergency, Exemption of Hours of Service and Stoppage at Weight Stations. Whereas a state of emergency exists in Florida and the surrounding areas and the Governor of Florida declaring an emergency, pursuant to KRS 189.233 and 49 CFR 390.23, declaring a state of emergency exists requiring relief from hours of service imposed on commercial vehicles providing power restoration within the affected area. Under the authority vested in KAR 189.33 and 49 CFR 390.23, hereby declared a state of emergency exists requiring relief from the hours of service imposed on commercial vehicles providing power restoration, debris removal, and transporting agricultural products and requiring waiver of stopping at all weigh stations for these commercial vehicles responding to the affected area. According to 49 CFR Section 390.23, waive 49 CFR 395.3 for vehicles transporting essential fuels, food, water, non-alcoholic beverages, medical supplies, feed for livestock and poultry, transporting livestock, poultry, and crops ready to be harvested, or the restoration of utility and transportation services. Title: Georgia Governor issued Executive Order 09.24.24.01 Effective: 09/24/24| Expires on: 10/02/24 Description: Georgia Governor Kemp issued an Executive Order on September 24, 2024, declaring a State of Emergency; it justifies the suspension of Part 395 (driver’s hours of service) of Title 49 of the Code of Federal Regulations. Suspension remains in effect for 14 days or until the emergency condition ceases to exist. It is further ordered that commercial vehicles operating outside the normal weight, height, and length restrictions under the authority of this State of Emergency shall be issued permits by the Georgia Department of Public Safety. Title: Florida Department of Agriculture Commissioner Simpson stated on September 24, 2024 Effective: 09/24/24| Expires on: 10/24/24 Description: Florida Agriculture Commissioner Simpson issued a statement temporarily suspending the interstate movement requirements for the transportation of animals that are fleeing the Tropical Storm and the applicable interstate requirements for their return. Title: Florida Highway Safety and Motor Vehicle Executive Director issued Emergency Order 24-05 according to Executive Order 24-208 Effective: 09/23/24| Expires on: 10/07/24 Description: FLHSMV Executive Director issued Emergency Order 24-05 a State of Emergency suspends enforcement of the registration requirements under sections 316.545(4) and 320.0725, Florida Statutes for commercial motor vehicles that enter Florida to provide emergency services or supplies, to transport emergency equipment, supplies, or personnel. Pursuant to 49 CFR 390.23, motor carriers and drivers operating a commercial motor vehicle to provide emergency relief during an emergency are exempt from 49 CFR 393.3 and 395.5. Title: Florida Department of Transportation Secretary Perdue issued Emergency Order 24-08 Effective: 09/23/24 | Expires on: 11/23/24 Description: Pursuant to Executive Order No. 24-208, Secretary Perdue waives and suspends Florida Statutes 316.515(1-3), 316.535(1 and 3), 316.545(2 and 4), and 337.401(1)(a); and Rules 14-28.002(4 and 5), and 14-46.001(2) to allow for alternate size and weight restrictions on any vehicles transporting emergency equipment, services, supplies, or personnel, and agricultural commodities and citrus as recommended by Commissioner of Agriculture. STATE BUSINESS AND INDUSTRY RESOURCES State of Florida Florida Division of Emergency Management Florida ESF 18 Office (Business and Industry) esf18@em.myflorida.com and Private Sector hotline (850) 815-4925 (Daily 7am-7pm EDT). Updates can be found at Florida Disaster Business. Florida 511 Traffic
How a manager can solve conflict between employees: Five steps to use now
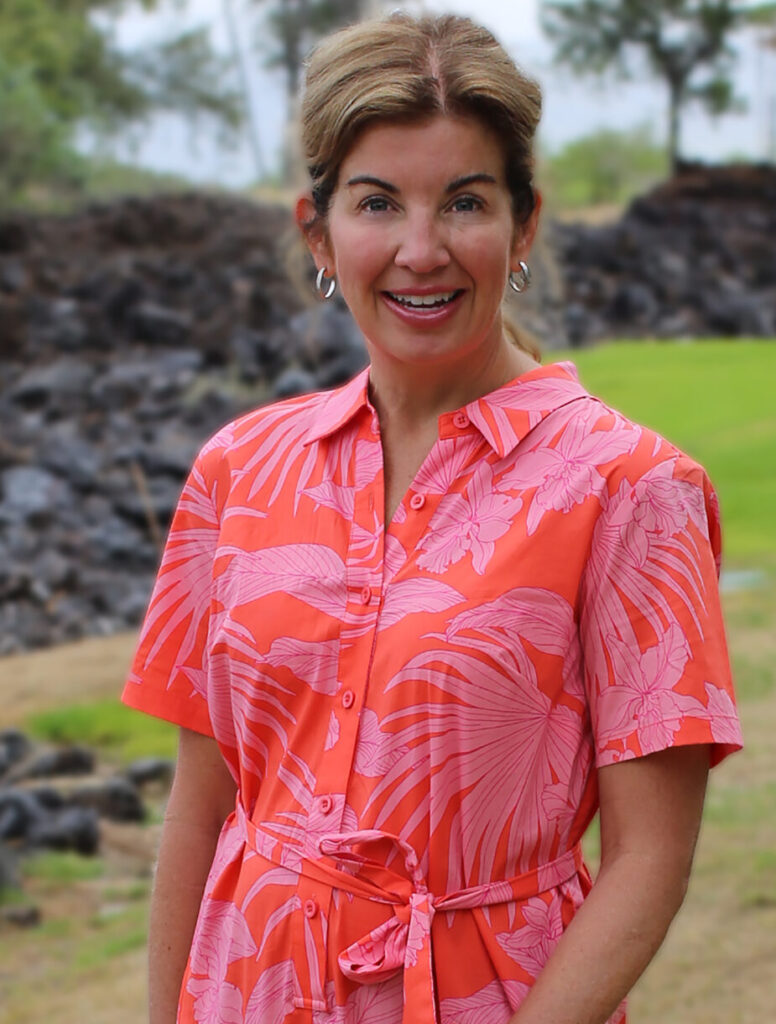
“Sort it out on your own” is no longer an option for businesses when employees are in conflict. Management goals commonly include maintaining harmonious work environments that make employees happy and motivated, but how do you achieve this when people don’t get along? As teams grow and turnover happens, a variety of personalities and experiences become part of the landscape. In other words, conflict between people is inevitable. How do you, the manager, approach disputes between employees? The answer lies in realizing how people perceive conflict with others, which is influenced by many factors, including personality and, associatively, what they have experienced throughout their lifetime. When you look at your business, is someone struggling with others? Perhaps you’ve noticed that what they expect from others differs from what they deliver. You will be unprepared until you think about who you are managing and what they have coped with throughout their lives. This is because how people interpret interactions and conflict depends on what they experienced in the past—before they met their coworkers. Is your business manufacturing, professional service, or retail? No industry is exempt. Jennifer managed a large coffee chain store. She was taught to pay attention to dynamics and observed how employees interacted and communicated. When two employees, Ted and Arlene, who often traveled to work together, became embroiled in a dispute over tips, Jennifer quickly intervened, reminding them of their friendship. Jennifer saw the ineffectiveness of this approach, noticing how Ted ignored Arlene while Arlene made jokes about Ted to another barista. Jennifer worried customers would feel the tension. When district manager Lee stopped into the café for a check-in, she immediately noted the friction. Lee met the employees independently and then jointly. Jennifer watched Ted and Arlene return to work, smiling and conversing lightly. What did Lee do differently than Jennifer? Five Steps to Resolve Conflict Between Employees translates into: Identify the anxiety that blocks resolution. Lee put this into action by talking with the employees about who they were before she waded into the issue at hand. She learned that Ted had been exploited as an adolescent by people he trusted. Lee realized that relationships made Ted feel vulnerable, so she reassured him that Arlene and the company cared for him and there was no intent to harm him. Lee also learned that Arlene was a single parent to two children and feared being unable to provide financially. Lee reassured Arlene that the tip situation would be resolved so she would not experience financial distress. She reaffirmed that work is a safe place. Think like your employee. This effort can be proactive, so you already know your employees when conflict arises. Ask questions like: What do weekends look like for you? Are they busy with obligations, or do you have downtime? Ask these questions with curiosity, not as though you are filling out a questionnaire! This genuine interest builds trust so that when you intervene in an employee dispute, they see that you care about their overall well-being. When conflict happens, effective intervention is directed by empathy. How does your employee think about things based on what you know about them and their lives? For example, Lee knew that Arlene worried about income, so her intervention considered how Arlene needed to feel safe and secure that her finances would not be jeopardized. Cool your jets before taking off into problem-solving. Let’s face it: most managers, owners, and leaders find dealing with employee conflict uncomfortable. This prompts a reactive response, whereby we want the conflict resolved quickly! Unfortunately, this approach leaves people feeling unheard, dissatisfied, and vulnerable to further conflict. Instead, slow down. When your reaction is to quell your anxiety with a quick solution, like separating them and solving what they are upset about rather than why it’s placing a tiny Band-Aid on a gaping wound. Like Lee, take time to meet with them individually. Consider whether the experience has made them feel unvalued or unsafe (physically, emotionally, or financially) and what would need to happen to lower this anxiety. Keep the Relational Goal Paramount. When meeting individually with the employee, don’t lose sight of the goal of healing the employee relationship. Unless they can work in complete silos, it is helpful to think of this relationship as a necessary elastic cord that must be flexible and intact for the relationship to work. Even if you can establish distance between the two, remember that unresolved conflict can ripple across teams like smoke from forest fires. Like Lee, shift from individual meetings to sitting together. As the manager, take the lead with a calm, assertive, and compassionate tone. Reiterate that you understand each of their experiences and the purpose now is to find ground for resolution. Start by highlighting the positives you have heard and that you are pleased with their effort to engage professionally. Set a collaborative direction. In your joint meeting, summarize what you heard from both employees and highlight the same things. For example, “Jill, you mentioned that you have always worked well with Mark and Mark, you complimented Jill for her creativity. While this disagreement has been serious, let’s not minimize the many hours and interactions that have been successful.” Even with resolution, reinforce the collaborative direction of the company. If Mark felt angered by having to take calls for Jill when she took lengthy lunches, and Jill felt Mark’s tone was condescending, demonstrate your commitment to maintaining collaboration. For example, “I understand you can be great workmates. To address this problem, we have created a schedule for phone coverage that does not always rely on Mark and will remind the team that lunches are within designated times.” In other words, make sure you close the loop! About the Author: Julie Gowthorpe, PhD, RSW, is a leading authority in the field of relationships. Renowned for her expertise in simplifying complex concepts, she shares this through a thriving private practice and a weekly radio broadcast; Dr. Gowthorpe speaks candidly with intimate and large groups. She transforms the lives of individuals and business
U.S. Rail Traffic Report for the week ending September 21, 2024
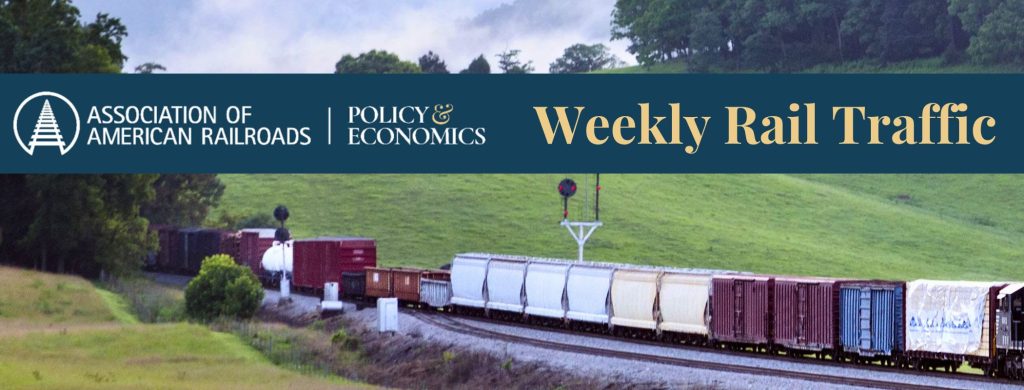
The Association of American Railroads (AAR) has reported U.S. rail traffic for the week ending September 21, 2024. For this week, total U.S. weekly rail traffic was 522,112 carloads and intermodal units, up 6.0 percent compared with the same week last year. Total carloads for the week ending September 21 were 232,818 carloads, down 0.6 percent compared with the same week in 2023, while U.S. weekly intermodal volume was 289,294 containers and trailers, up 12.0 percent compared to 2023. Six of the 10 carload commodity groups posted an increase compared with the same week in 2023. They included grain, up 2,812 carloads, to 20,897; chemicals, up 2,071 carloads, to 33,139; and miscellaneous carloads, up 1,799 carloads, to 10,313. Commodity groups that posted decreases compared with the same week in 2023 included coal, down 4,987 carloads, to 63,164; metallic ores and metals, down 2,699 carloads, to 19,979; and nonmetallic minerals, down 2,382 carloads, to 32,096. For the first 38 weeks of 2024, U.S. railroads reported a cumulative volume of 8,244,994 carloads, down 3.3 percent from the same point last year; and 9,931,114 intermodal units, up 9.6 percent from last year. Total combined U.S. traffic for the first 38 weeks of 2024 was 18,176,108 carloads and intermodal units, an increase of 3.3 percent compared to last year. North American rail volume for the week ending September 21, 2024, on 9 reporting U.S., Canadian, and Mexican railroads totaled 339,514 carloads, down 2.3 percent compared with the same week last year, and 371,529 intermodal units, up 8.0 percent compared with last year. Total combined weekly rail traffic in North America was 711,043 carloads and intermodal units, up 2.8 percent. North American rail volume for the first 38 weeks of 2024 was 25,298,477 carloads and intermodal units, up 2.6 percent compared with 2023. Canadian railroads reported 92,505 carloads for the week, down 4.1 percent, and 69,836 intermodal units, down 4.1 percent compared with the same week in 2023. For the first 38 weeks of 2024, Canadian railroads reported a cumulative rail traffic volume of 6,015,994 carloads, containers, and trailers, up 0.1 percent. Mexican railroads reported 14,191 carloads for the week, down 16.0 percent compared with the same week last year, and 12,399 intermodal units, down 3.0 percent. Cumulative volume on Mexican railroads for the first 38 weeks of 2024 was 1,106,375 carloads and intermodal containers and trailers, up 4.4 percent from the same point last year.
Next-Gen 12,000 lb DriveMod Tugger built at Motrec Facility
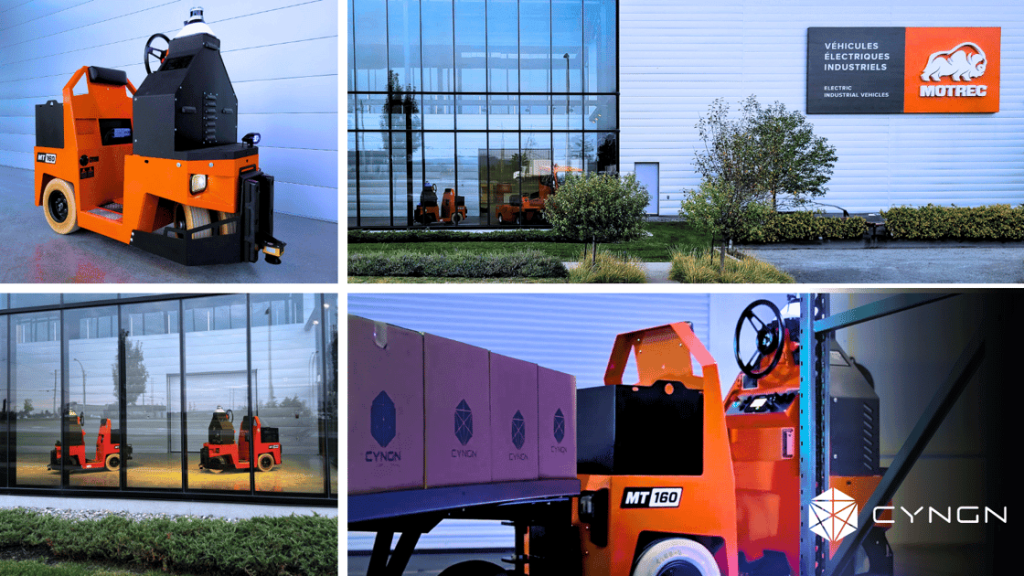
Cyngn announced the first build of the next-generation 12,000 lb DriveMod Tugger has been completed at the facility of its OEM partner, Motrec. Cyngn Inc. has announced the first build of the next-generation 12,000 lb DriveMod Tugger has been completed at the facility of its OEM partner, Motrec International Inc. This key milestone achieves the previously announced upgrade that increases towing capacity from 6,000 lb to 12,000 lb and marks a step forward for integrating Cyngn’s proprietary DriveMod technology with Motrec’s MT-160 tow tractor at scale. The collaboration plays a crucial role in reducing production costs and delivering more streamlined logistics to end customers. By leveraging Motrec’s manufacturing expertise and infrastructure, the DriveMod Tugger can provide exceptional standards of vehicle performance and reliability that Motrec is already known for. “Our partnership exemplifies a synergistic collaboration between a high-tech company and an established OEM,” said Cyngn’s Vice President of Business Development, Ben Landen. “Building the first DriveMod Tugger at Motrec’s facility highlights another positive step of validation for our strategy that includes leveraging complementary strengths between partners to bring the best combination of products, services, and support to the industrial automation market.” “Beginning to build DriveMod Tuggers at our facility reinforces our commitment to innovation and demonstrates our ability to evolve with the needs of our customers who are actively seeking automation solutions,” adds Marc Breton, VP of Sales at Motrec. “We are excited to continue enhancing the vehicles we offer with Cyngn’s cutting-edge technology that builds on our long track record of high-quality, reliable material handling solutions.” Engineered to streamline repetitive hauling tasks such as moving finished goods or delivering supplies, the next-gen DriveMod Tugger features a towing capacity of 12,000 pounds, automatic unhitching, two ruggedized touch-screen user interfaces, safety lights and indicators, and the Cyngn Insight data and fleet management software suite. DriveMod Tuggers are already deployed at customer facilities and are available for sale today.
Combilift retains Deloitte’s Best Managed Company Award for the 12th Consecutive Year

For the 12th consecutive time in the awards’ 16-year history, Combilift has been recognized as a Best-Managed Company, requalifying as a Platinum winner for the sixth time. Their management prowess was rewarded at Deloitte’s prestigious awards ceremony in Dublin on September 19th. The Deloitte Best Managed Company award acknowledges the achievements of management teams, not just individuals. The accolade recognizes overall business performance based on the criteria of Strategy, Capability and Innovation, Culture and Commitment, and Governance and Financial Performance. Judges examine every company based on these four equally weighted pillars to select a winner. The Best Managed Companies Program originated in Canada in 1993, with Ireland’s program, introduced in 2008, being the second longest-running program. In addition to Ireland and Canada, the program is currently run in 48 countries across four continents. Founded in 1998 by Martin McVicar and Robert Moffett, Combilift has grown from a small team of 10 to a total staff of over 850 people, selling to 85 countries worldwide. When receiving the award, Martin McVicar said, “It’s a great honor for us as a company to be acknowledged once again by a global brand such as Deloitte’s Best Managed Companies. The credibility of this global award enhances our brand to scale internationally”.
Fairchild Equipment earns RAVS Plus Certification from ISN
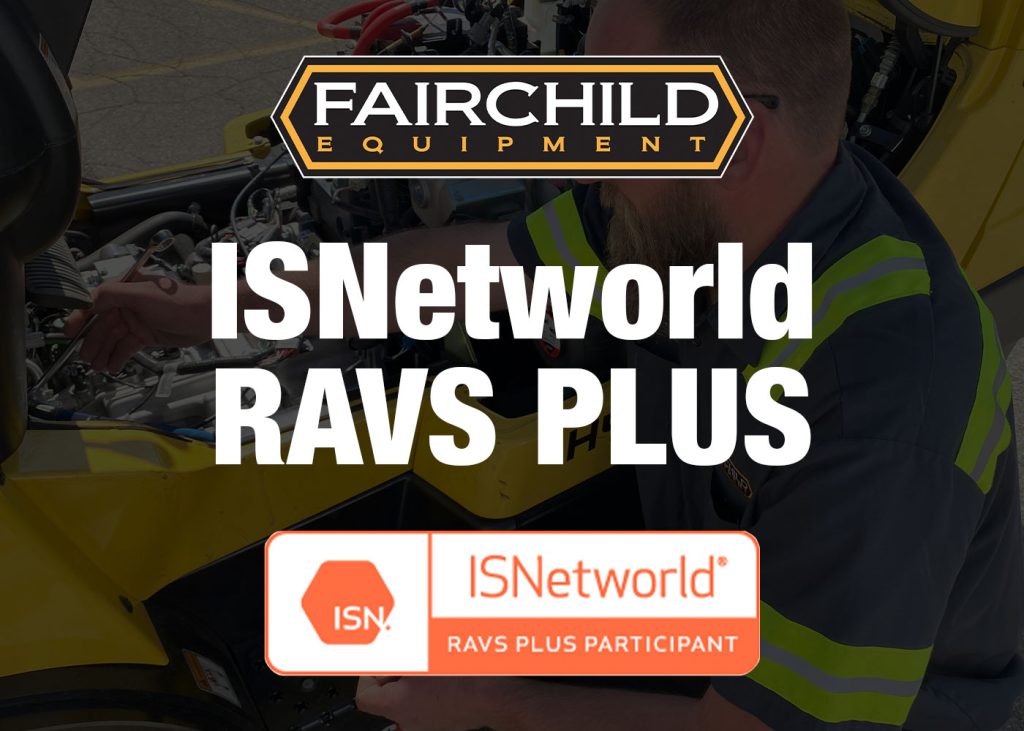
Fairchild Equipment has announced that it has received the RAVS Plus certification from ISN. This recognition places Fairchild Equipment among an elite group of contractors and suppliers out in ISN to meet or exceed the rigorous standards for workplace safety, quality outcomes, and risk management. The ISNetworld Review and Verification Services (RAVS) and RAVS Plus processes assess a company’s health and safety practices and programs. The RAVS Plus process goes beyond a simple desktop review and on-site observations, ensuring that a contractor’s written safety programs are operational in day-to-day activities. This verification process requires documented evidence and in-person interviews by ISN staff to confirm a company’s dedication to occupational health and safety and environmental compliance. “Receiving the RAVS Plus certification is a testament to our unwavering commitment to our ‘Safety Always’ core value” said Marty Schumacher, Corporate Safety Manager at Fairchild Equipment. “At Fairchild Equipment, safety is not just a protocol; it’s an integral part of our culture, emphasizing safety at all times and in all places.” For over 35 years, Fairchild Equipment has consistently provided comprehensive materials handling solutions, including new and used forklifts, aerial lifts, utility vehicles, construction equipment, and professional cleaning equipment, alongside service, parts, rental, fleet management, forklift training, and engineered storage systems. With over 330 employees, including more than 175 technicians, Fairchild Equipment continues to lead the industry with its dedication to safety and quality. “Our top priority is ensuring that our employees return home in the same or better health than when they started the day,” said Van Clarkson, President of Fairchild Equipment. “Achieving RAVS Plus certification reinforces our commitment to not only safeguarding our team but also exceeding our customers’ safety protocols when we are onsite at their locations to keep their teams safe,” Clarkson added.
Nelson-Jameson Executive receives Women in Supply Chain Rising Star Award
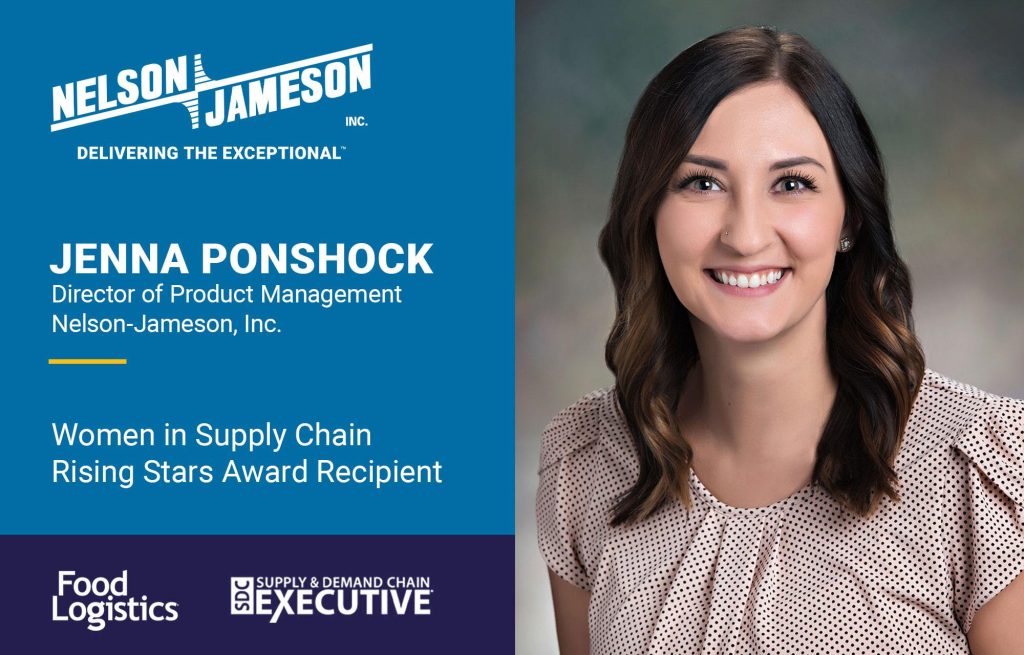
Food Logistics and Supply & Demand Chain Executive honor Director of Product Management Jenna Ponshock Nelson-Jameson has announced that Director of Product Management Jenna Ponshock was honored with a Women in Supply Chain Award. Food Logistics, the only publication exclusively dedicated to covering the movement of products through the global cold food supply chain, and Supply & Demand Chain Executive, the only publication covering the entire global supply chain, named Ponshock as a winner of its annual Rising Stars award. “We couldn’t be more proud of Jenna for receiving this prestigious honor from such well-respected industry publications,” says Mike Rindy, President of Nelson-Jameson. “In her time with Nelson-Jameson, Jenna has made a significant impact across our organization with unwavering kindness and mutual respect. As a rising star within and outside of her work with Nelson-Jameson, Jenna will undoubtedly continue to make a profound impact on supply chain operations.” The Women in Supply Chain Rising Stars award recognizes younger or newer professionals (39 and under) whose achievements, hard work and vision have helped shape the supply chain network. In 2023, two Nelson-Jameson female executives – Dakonya Freis, Vice President of Commercial Development, and Devon Vogel, Vice President of Customer Solutions – were honored with Women in Supply Chain Awards. “Every year, this award continues to amaze me. But this year especially, it’s all about the quality of the submissions. These women are doing remarkable things for their communities, organizations and teams and are paving the way for future young female leaders to be a part of an industry that’s making a difference,” says Marina Mayer, Editor-in-Chief of Food Logistics and Supply & Demand Chain Executive and Co-Founder of the Women in Supply Chain Forum. “New this year, the award was broken down into Rising Stars, Trailblazers, DEI Pioneer and Workforce Innovator. From there, we named an overall winner per category and then four honorable mentions per category. This year’s applications were superb and made it next to impossible just to pick one winner. I’m so proud of these women and their achievements. We’re just getting started.” Sarah Barnes-Humphrey, founder of Let’s Talk Supply Chain podcast and Blended Pledge, both sponsors of the Women in Supply Chain award, added that the winners have been crucial to their industries’ success and innovation. “Women are reshaping the landscape of supply chain management with their unparalleled contributions, igniting growth and fostering innovation across the industry. Their presence not only enriches the workforce but also brings a myriad of perspectives essential for tackling intricate challenges and refining global operations. The Women in Supply Chain award stands as a beacon, celebrating and amplifying their remarkable achievements,” Barnes-Humphrey said. “Congratulations to all the winners, everyone who was nominated and all those making an impact. This recognition honors the courage and dedication of all incredible people who work hard every day. This award is a testament to their unwavering commitment and profound impact on the field.”
Episode 523: Redefining LTL freight logistics with WARP
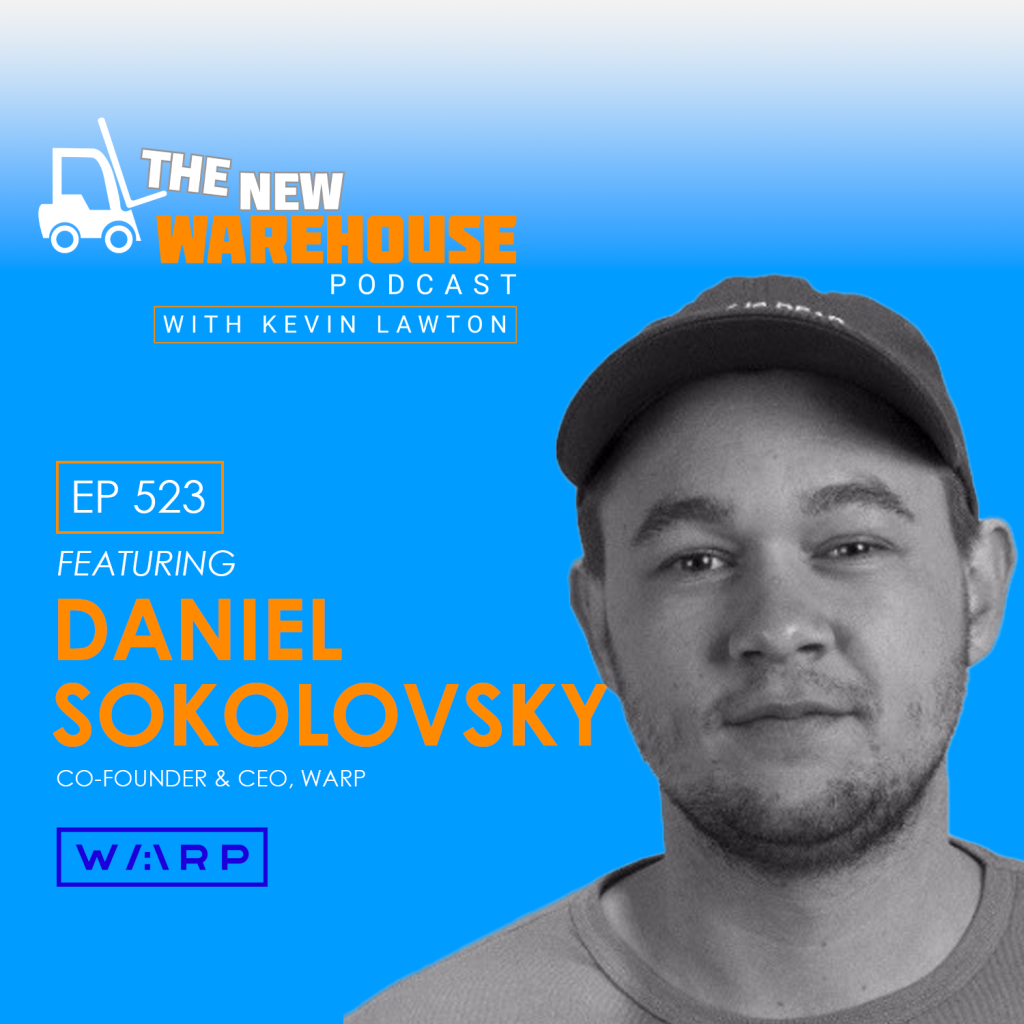
Welcome to this episode of The New Warehouse Podcast, where we dive into LTL freight. We’re joined by Daniel Sokolovsky, the co-founder and CEO of WARP. WARP is leading the charge in innovating Less-Than-Truckload (LTL) freight. In this episode, Daniel shares how WARP is shaking up traditional LTL networks with technology and flexible operations. The company’s mission goes beyond just moving goods; it’s about transforming the entire logistics process to be faster, more efficient, and cost-effective for brands and retailers. Building an LTL Network on Steroids WARP aims to revolutionize the LTL freight market with a powerful network combining cross-docking facilities, optimized routing, and flexible scheduling. As Daniel puts it, “The way we think about it is an LTL network on steroids.” This advanced network allows shippers to choose between speed and cost, offering flexibility that’s rare in traditional LTL logistics. Whether a shipper needs fast delivery or cost savings, WARP’s system allows them to tailor their logistics strategies to fit their unique needs. Bridging Parcel and LTL Freight in the Middle Mile Traditionally, separate networks handle parcel and freight deliveries. WARP, however, is changing the game by integrating these networks, especially in the crucial middle mile. Daniel highlights this innovation: “Where those two networks intersect is specifically in the middle mile.” By connecting these segments, WARP optimizes the movement of goods from regional hubs to final destinations, whether a small package or palletized freight. This strategy cuts costs and boosts efficiency, ensuring goods arrive quickly and reliably. “The flexibility in our network enables a significantly lower price point, quality on par if not higher, and significantly better visibility,” adds Daniel. A Tech-Driven Future for Freight Looking ahead, WARP hopes to unify freight modes—LTL, FTL, and parcel—into one seamless, tech-driven network. Daniel envisions a future where dynamic routing and optimization replace outdated static routing guides. “I think what happens is that we see a merge across all of these different service modes,” he explains. As WARP continues to innovate, they are exploring automation in cross-docking facilities, which could further streamline logistics and set new industry standards. Key Takeaways WARP’s LTL network offers unmatched flexibility, allowing shippers to balance costs and delivery speeds. Integrating parcel and freight networks in the middle mile cuts costs and enhances efficiency. The future of freight lies in a unified, tech-driven network that seamlessly connects multiple service modes. The New Warehouse Podcast Episode 523: WARP is Redefining Freight Logistics
ALAN Tropical Storm Helene Situation report
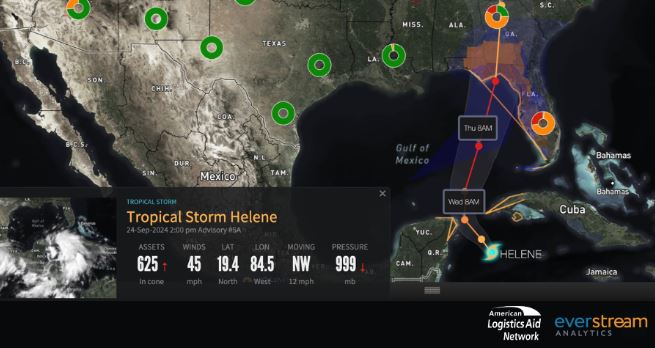
As Tropical Storm/Hurricane Helene approaches landfall on the Florida Gulf Coast, ALAN is busy preparing, and we are encouraging all of our partners to do the same. With that in mind, we’d like to share five pre-storm takeaways that we feel are essential for you and your organizations to be aware of. They’re listed below, and we hope you’ll find them informative. Below these takeaways, you’ll find the current situation report. We’ll update these resources frequently on our Disaster Micro-Site (https://www.alanaid.org/operations/) and will send another situation report as conditions warrant. The Disaster Micro-Site is also where we share key details about ALAN’s storm activation measures and how you can support our relief efforts. Because this storm has the potential to be especially destructive, we encourage you to visit ALAN’s Supply Chain Intelligence Center (https://www.alanaid.org/map/). There, you’ll find resources to keep you in the loop about everything from Helene’s latest path to how local and regional transportation infrastructure is being affected. “As always, all of us at ALAN hope that this storm will be much less severe than predicted and that any damage to life, health, and property will be minimal. At the same time, we are grateful for the many good people like you who continue to invest in our work, said Kathy Fulton, Executive Director of ALAN. ” We ask that you help us prepare to respond by making a financial donation today. Even a seemingly small contribution can go a long way in ensuring we can deliver critical aid to those who need it most. ALAN’s five key takeaways for your organization 1) Make personal safety a priority. If you or your locations are anywhere near Helene’s path, monitor the National Hurricane Center and your local National Weather Service forecast for real-time details. And please, don’t ignore any safety warnings that pertain to you or your personnel. This is expected to be a major hurricane with estimated winds of up to 115 miles per hour, so its potential impact is not to be taken lightly. 2) For the latest detailed information about storm-related road closures, facility closures, and other supply chain impacts, visit ALAN’s Supply Chain Intelligence Center at https://www.alanaid.org/map/. It should tell you most of what you need to know. But should you need additional information, don’t hesitate to contact us at https://www.alanaid.org/contact/. Time permitting, we will do our best to work with our emergency partners to get you an answer. 3) View the latest requests for logistics support by going to the “Active Logistics Needs” section of our Disaster Micro-Site at https://www.alanaid.org/operations/ Over the past few weeks, ALAN has communicated with various emergency management and non-profit partners regarding hurricane needs for Beryl, Debby, and Francine. Although there are no “open” requests for Tropical Storm/Hurricane Helene, this situation could quickly change as the storm makes landfall. In previous years, most of our requests have come several days or weeks after hurricanes. So stay tuned and ready – as requests for transportation, warehousing, volunteers, and material handling equipment come in, we will post them promptly. 4) Request or offer support. If you are a non-profit, please tell us what you anticipate needing by requesting alanaid.org/request-support. If you are a business, tell us how you can help by making a “pre-offer” for transportation, warehouse space, equipment, expertise, or services at https://www.alanaid.org/how-to-help/. Such information is hugely helpful because it helps us better plan our response. Knowing what is needed and who can help allows us to move quickly to support the most urgent needs. We’ll confirm the information with you and match offers with fit needs. 5) Be mindful and demure in your support of disaster relief activities. Don’t self-deploy to disaster-affected sites; please don’t participate in product collection drives. Although the intention behind both of these activities is good, they often create more challenges than they solve because they tend to get in the way of responders who are working to save lives – and add confusion to an emergency supply chain that is already under tremendous strain. If you’re looking for a meaningful way to help, consider making a financial contribution to ALAN or a humanitarian organization. Such donations will be much more helpful and efficient – and far more likely to reach storm survivors.
CKF are best of the bunch with their banana palletising solution for Primafruit
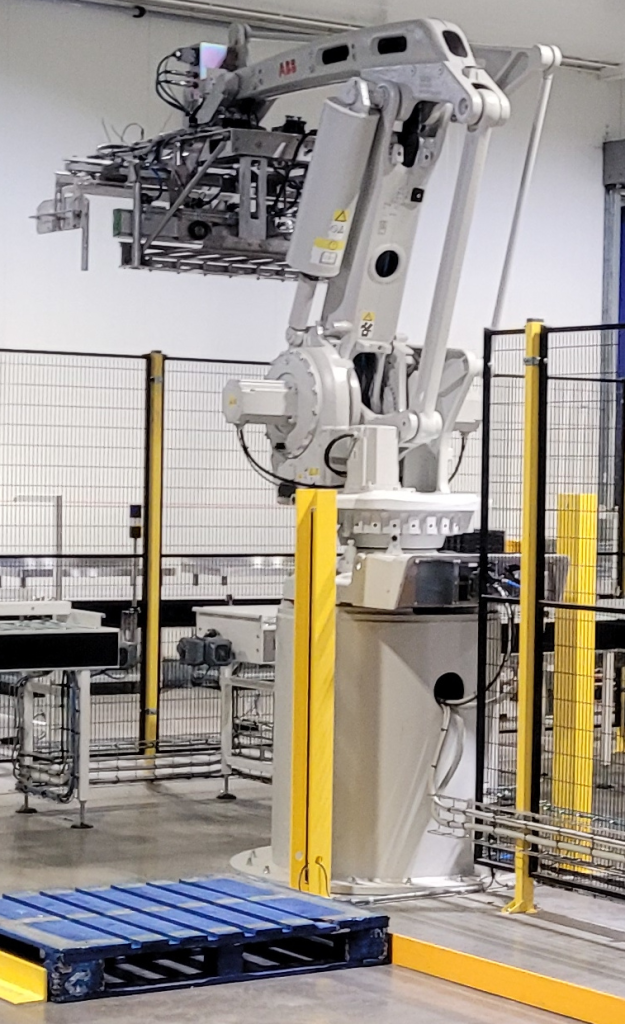
CKF Systems was delighted to have been chosen by Primafruit to develop a new bespoke robotic de-palletising and re-palletising system at their site in the Vale of Evesham. Primafruit is a primary supplier of a broad range of fruit. The challenge The banana inspection and packing lines within Primafruit at their Evesham facility were heavily reliant on manual labor. Imported produce, cardboard trays filled with bananas, were received stacked on pallets, typically to a height nearing 2.5m. The operation for Primafruit was to de-stack the cardboard trays, inspect the produce, and re-pack the fruit into either cardboard trays or collapsible, returnable plastic crates prior to re-palletizing and despatch to their retail customer. Primafruit wanted to automate the process at their state-of-the-art facility which is perfectly located in a central hub for agriculture and have a dedicated pack house, chilled storage, and ripening chambers. The new system was another important step in their automation journey creating a more efficient and safe working environment. Approach CKF has vast experience, designing and building robotic palletizing systems for a wide range of industries. This application demanded that the CKF team fully understand the challenges such that customized solutions could be developed to provide Primafruit with an efficient automated process. The challenges were identified as: De-stack filled cardboard trays from a pallet 2.5m high that could have an inconsistent stack form and deformed cases due to transit. Manage and deliver cardboard trays containing bananas to each inspection and re-packing station ensuring there is always an empty tray or re-useable plastic crate available at each station to enable continuous inspection and re-packing. Re-stack either cardboard or re-useable plastic crates onto the finished pallet ready for despatch. Minimize the system footprint for the efficient use of the existing floor space. For the automation to be cost-effective CKF proposed a single robot for de-stacking and re-stacking. Searches, tolerances, case quality, and stack profiles are all key elements to the success of any robot palletization. To undertake the de-stacking and re-stacking utilizing a single tool would require a bespoke design. The CKF Engineering team also understood the demands on the tool to handle two differing containers i.e. cardboard trays and plastic collapsible, re-useable crates. It was vital that the tooling developed would maintain the integrity of the bananas, without marking or causing any damage. By using a single robot cell, the system would maximize the floor space available to ensure that designated access routes for personnel and the movement of materials would be maintained. The Solution CKF, an experienced ABB value provider for over 13 years, utilized an ABB IRB 660 industrial robot system in the solution design – this dedicated palletizing robot is designed to handle a load of up to 180kg at a reach of up to 3.15m. Its low-weight upper arm, 4-axis design, and parallel rod system mean it delivers optimized speed, reach and payload. This robot is exceptionally fast making it ideal for palletizing bags, boxes, crates, bottles and more. The CKF Engineering team developed the bespoke gripper to pick either two or three cases at a time (dependent on stack orientation.). The single tool was designed to suit both de-stacking and re-stacking, together with handling two case variants of differing dimensions, location points, and material. Based on an anodized aluminum framework to reduce weight, the tool utilizes pneumatically actuated side grippers and base slide plates for transfer of the multiple case format, additionally, a vacuum assist is required to enable lifting of the product trays prior to separation from the stack. Due to the lack of conformity of the pallet stack from the suppliers to Primafruit, the CKF team developed the Robot positioning for de-palletizing using an onboard sensor array to determine the coordinates of height and stack position prior to the pick operation. Once transferred from the pallet, stack cases are transferred to and from the inspection cells on the CKF range of ZPA conveyor sections which utilises the Interroll DC platform. This perfectly matched range of controls, motor rollers, and power units enables the provision of a unique combination of conveyors for this system. This includes CKF accumulation conveyors configured to provide individually controlled zones, allowing zero pressure accumulation of the product trays and the flexibility to be configured to different sizes. The system is driven on a Rockwell platform using a compact GuardLogix 5380 safety controller with a 10” SVGA touch screen for the Operator interface. Troax safety fencing is used around the robot cell to provide the enclosure, with Leuze light guards providing protection for pallet entry and exit.
DURAVANT Expands into China and appoints County Manager
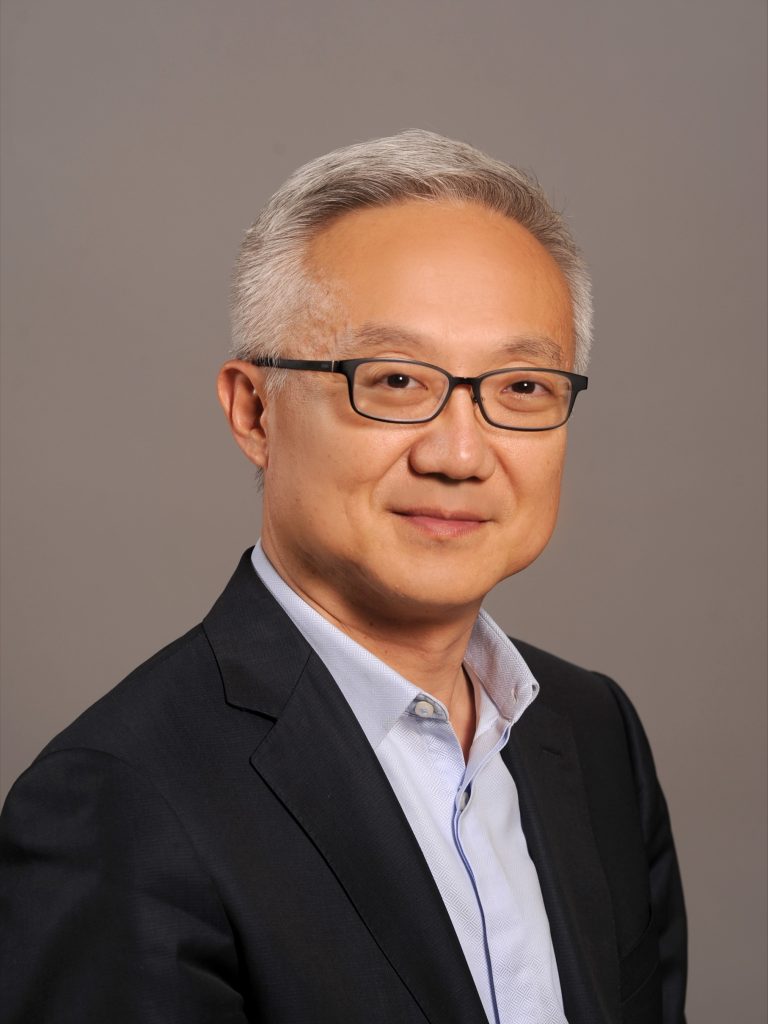
Duravant Establishes Entity in China and Appoints Executive to Lead Local Growth Strategies and Infrastructure Expansion Duravant LLC has announced the appointment of Denver Lu to the position of Managing Director, Duravant China Co Ltd. The announcement follows the company’s recent investments to establish a local sales and service office in Suzhou, China. In this new role, Lu will be responsible for leading business development across the company’s Protein Processing, Food Sorting and Handling, Packaging and Material Handling segments by delivering innovative automation solutions to the Chinese market through Duravant’s world-class brands. Duravant has a long history of supporting global customers who operate in China, and with these investments, the company is advancing their commitment to expand its local sales and service infrastructure to better serve their customers’ expanding automation needs. “China is poised to become the world’s largest consumer market, driven by robust economic growth and rising incomes,” said Petros Diamantides, Duravant’s Chief Operating Officer, Emerging Markets. “As the country shifts its manufacturing focus from speed to efficiency and from quantity to quality, traditional sectors such as food, agriculture and logistics are undergoing a transformative evolution. We see immense potential in the China market to grow our partnerships with multinational customers and regional Chinese powerhouse brands.” Duravant’s comprehensive suite of automation solutions includes hardware and software integration, equipment and technology solutions, and aftermarket parts and services. “Our expansion in China is more than just geographic; it represents our dedication to providing full-service solutions that cater to the unique requirements of the Chinese market,” said Diamantides. “By leveraging our global expertise and local insights, as well as developing capabilities on the ground, we will be well-positioned to support the growth and transformation of the China market.” “We are extremely fortunate to welcome Denver to Duravant,” added Diamantides. As a veteran business leader with almost 30 years of experience in the China market, Lu has held management positions with both food & beverage companies as well as with OEMs. Lu’s extensive industry knowledge stems from leadership roles at Simplot, OSI, and Marel. Lu holds a Master of Commerce degree from the University of New South Wales in Sydney, Australia and a Master of Business Administration degree from Rutgers University in New Jersey, United States. He also has been recognized as a Fellow of CPA Australia.