Digital tool boosts cargo visibility at Port of Long Beach
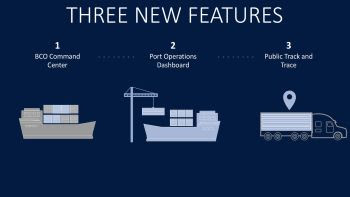
Supply chain information highway maximizes efficiency and connectivity The Long Beach Board of Harbor Commissioners on Monday received an update about the capabilities of the Supply Chain Information Highway, a robust digital tool created to maximize the efficiency and visibility of cargo shipments moving through the Port of Long Beach. Now in its second phase of development, the Supply Chain Information Highway is undergoing field testing to refine its ability to deliver aggregated data that will help logistics partners to better plan, schedule and track cargo movement in real time from origin to destination. “We are merging technology and collaboration to enable information sharing and connectivity across every link of the supply chain,” said Port of Long Beach CEO Mario Cordero. “By increasing cargo visibility, the Supply Chain Information Highway will deliver a more accurate record of container movement through the port complex, reduce delays and aid the entire goods movement industry from end-to-end and coast-to-coast.” “The Supply Chain Information Highway maximizes efficiency by enabling our industry partners to schedule and plan for the arrival of cargo through our Port, as well as expedite deliveries to consumers and retailers,” said Long Beach Harbor Commission President Sharon L. Weissman. “This is truly a game-changer for the 200,000 shippers who move their goods through the Port of Choice.” All six marine terminals at the Port are using a beta version of the Supply Chain Information Highway. Three new features were introduced at a public meeting of the Board of Harbor Commissioners on July 24, features created to significantly enhance the digital platform’s functionality while meeting the key objectives this initiative was designed to achieve: A dashboard designed for beneficial cargo owners allows customers to access information about the location of their containers within the Port complex, highlighting which containers have arrived, which are undergoing inspection by the U.S. Customs and Border Protection, and which are ready to be picked up. A public “track and trace” page allows users to access the most up-to-date information about the status of containers moving through the Port of Long Beach. After inputting a unique tracking number, the user will be presented with a detailed list tracing every step the container goes through from the time it is loaded onto a vessel until it is unloaded on the docks. A public port operations dashboard that contains much of the information currently found in the Port’s Weekly Advance Volume Estimate, or WAVE Report, including projected container volumes, vessel calls and turn times for trucks accessing marine terminals. The Supply Chain Information Highway is anticipated to be compatible with similar data-sharing platforms across the maritime logistics industry, with a goal of using the tool at other seaports across the nation. The Port of Oakland, the Northwest Seaport Alliance, the Utah Inland Port Authority, PortMiami, the South Carolina Ports Authority and the Port of New York/New Jersey have previously agreed to collaborate with the Port of Long Beach and participate in the project. Read more and sign up for updates about the Supply Chain Information Highway here. Watch the presentation to the Harbor Commission here.
Yellow exec tells sales staff Friday is their last day and Monday the company will file for bankruptcy
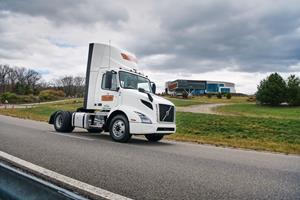
Media reports this afternoon have reported that a Yellow senior vice president informed their staff on Wednesday, July 26th, that their last day would be Friday and that the Yellow less-than-truckload (LTL) carrier will file for bankruptcy on Monday, July 31st, according to three employees who attended a video call. The sales employees were approved to tell customers of the bankruptcy plans and to take paid time off for the rest of the week. According to a video of the meeting viewed by industry publication FreightWaves and two employees present, the senior vice president told employees to backtrack on the bankruptcy statement. She said to “correct” any customers that were previously told there would be a bankruptcy and to share the following statement: When Material Handling Wholesaler asked company officials for comment they responded, “Talks with the International Brotherhood of Teamsters are ongoing. As previously stated, in keeping with the fiduciary responsibility of the company’s executives, the company continues to prepare for a range of contingencies.” A Yellow representative shared the same statement when FreightWaves reached out for comment to learn more about the message that the trucking company may file for bankruptcy on Monday. Yellow’s vice president of technology services also told her team the above statement Wednesday afternoon, according to one Yellow employee. That employee said, previously in the day, their boss advised their team that a bankruptcy could happen at any time and to send out resumes. This story is developing. Check back here for updates. Are you a Yellow employee with a story to share? Email rpremack@freightwaves.com.
AAR Reports weekly rail traffic for the week ending July 22, 2023
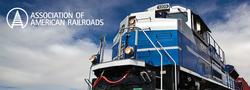
The Association of American Railroads (AAR) has reported U.S. rail traffic for the week ending July 22, 2023. For this week, total U.S. weekly rail traffic was 473,736 carloads and intermodal units, down 3.2 percent compared with the same week last year. Total carloads for the week ending July 22 were 222,454 carloads, down 1.3 percent compared with the same week in 2022, while U.S. weekly intermodal volume was 251,282 containers and trailers, down 4.8 percent compared to 2022. Six of the 10 carload commodity groups posted an increase compared with the same week in 2022. They included motor vehicles and parts, up 2,150 carloads, to 14,641; nonmetallic minerals, up 1,780 carloads, to 34,583; and metallic ores and metals, up 886 carloads, to 21,354. Commodity groups that posted decreases compared with the same week in 2022 included grain, down 4,417 carloads, to 14,981; coal, down 3,251 carloads, to 64,474; and forest products, down 852 carloads, to 7,748. For the first 29 weeks of 2023, U.S. railroads reported cumulative volume of 6,488,884 carloads, up 0.4 percent from the same point last year; and 6,828,178 intermodal units, down 9.8 percent from last year. Total combined U.S. traffic for the first 29 weeks of 2023 was 13,317,062 carloads and intermodal units, a decrease of 5.1 percent compared to last year. North American rail volume for the week ending July 22, 2023, on 12 reporting U.S., Canadian and Mexican railroads totaled 330,062 carloads, up 0.4 percent compared with the same week last year, and 331,880 intermodal units, down 6.3 percent compared with last year. Total combined weekly rail traffic in North America was 661,942 carloads and intermodal units, down 3.0 percent. North American rail volume for the first 29 weeks of 2023 was 18,690,310 carloads and intermodal units, down 4.2 percent compared with 2022. Canadian railroads reported 89,701 carloads for the week, up 4.8 percent, and 68,972 intermodal units, down 11.6 percent compared with the same week in 2022. For the first 29 weeks of 2023, Canadian railroads reported cumulative rail traffic volume of 4,567,335 carloads, containers and trailers, down 2.7 percent. Mexican railroads reported 17,907 carloads for the week, up 1.9 percent compared with the same week last year, and 11,626 intermodal units, down 3.3 percent. Cumulative volume on Mexican railroads for the first 29 weeks of 2023 was 805,913 carloads and intermodal containers and trailers, up 3.7 percent from the same point last year. To view the weekly rail traffic report, click here.
TAPCO launches extension to LegendViz product line
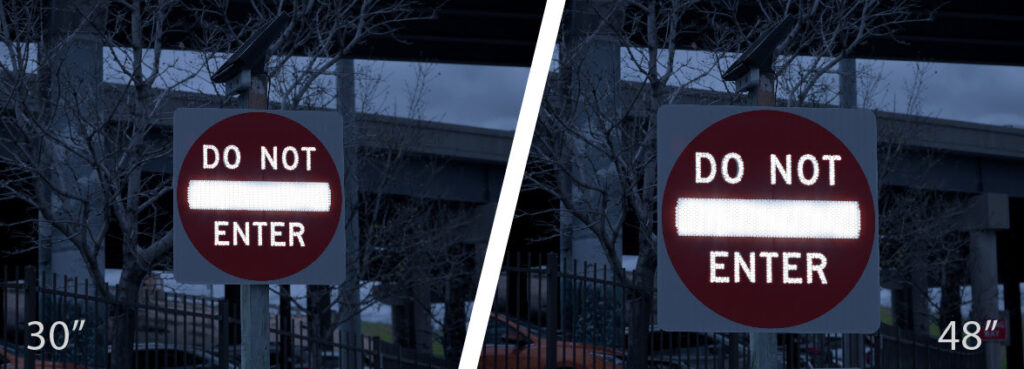
Traffic and Parking Control Co., Inc. (TAPCO), manufacturer, distributor and service provider of roadway safety innovations is excited to announce the launch of a LegendViz® line extension. The new additions to the LegendViz® line are the 36-inch-by-36-inch Stop and 48-inch-by-48-inch Do Not Enter signs. The new sizes are MUTCD-compliant and suitable for use on multi-lane roads, expressways and in states where oversized sign applications are desired. LegendViz® technology can also be applied to private roadways. Initially launched in 2021, the LegendViz® line was driven by customer feedback requesting traffic signs that motorists could see without headlights. Ever since, the innovative, LED-illuminated design has quickly become a popular addition to TAPCO’s range of traffic sign offerings. The latest extension is designed to address the growing need for larger-sized traffic signs that are highly visible regardless of factors such as speed or traffic volume. “We are excited to expand our product line to align with state standards and regulations nationwide,” said Amanda Schulz, TAPCO’s Director of Sales. “By providing larger signs that comply with Federal and State MUTCD standards, we are meeting the demands of our customers and continuing to increase safer roadways for all.” The new 36-inch-by-36-inch Stop and 48-inch-by-48-inch Do Not Enter signs are now available to purchase. As with all LegendViz® signs, the new sizes are designed for simple, single-person installation and offer the flexibility of AC or solar power options.
Fairchild Equipment announces new location in Rockford
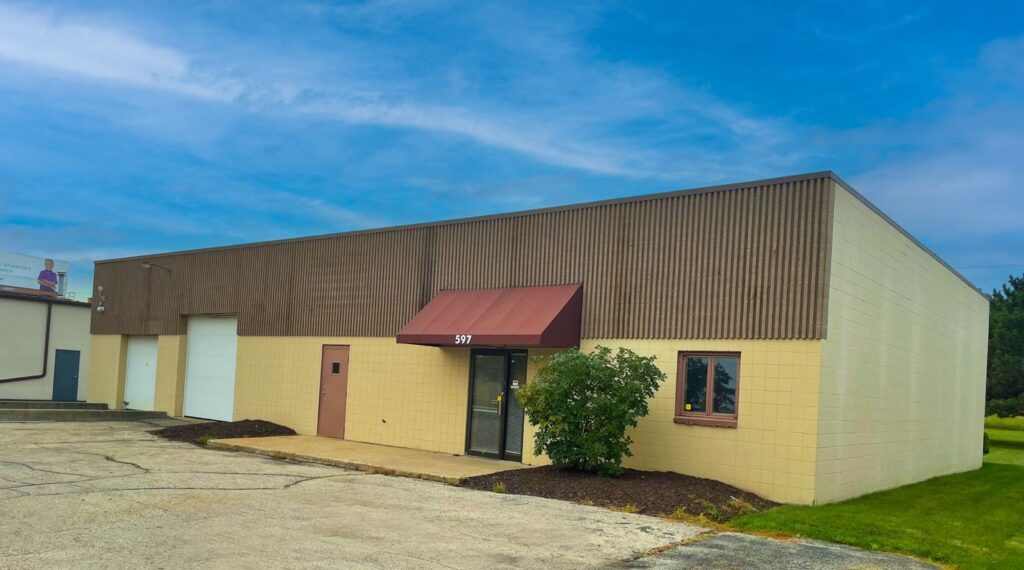
Van Clarkson, president of Fairchild Equipment, has announced a new location in Rockford, Illinois, which has just opened. “We are extremely excited to have moved into this new facility in Rockford,” Clarkson said. “It brings us closer to some of our larger customers in our Illinois region which will greatly reduce delivery costs for them. The area of Illinois from Rockford down to Rochelle has also seen significant growth in distribution due to its proximity to several major interstates and intermodal rail. This better positions us to serve this important market” he further explained. The new facility, which is located off of Highway 20 and Kishwaukee Street at 597 Grable Street in Rockford, is now home to a growing team and replaces Fairchild Equipment’s Beloit location at 755 East Philhower Road. The new Rockford branch offers triple the space, enabling Fairchild Equipment to add shop technicians, plus provide additional office space for service writers, customer care and sales teams to support customers. “This move gives us a presence in Northern Illinois which will enable us to better service our customers in this area to our full potential,” Brent Maurer, the Branch Manager for the Rockford branch, stated. “We are thrilled to have substantially more space in this new facility and be able to bring our portfolio of leading material handling equipment brands, in-shop service, parts and rental equipment closer to our customers in Illinois,” he continued. This new facility marks the third facility expansion since 2020 in Fairchild Equipment’s network of locations throughout the Midwest. It will better accommodate the expansive product line Fairchild Equipment offers, which includes warehouse and materials handling equipment as well as engineered storage solutions and fleet management services. Its diverse line of materials handling equipment brands provide a holistic approach to solving all of organizations’ operational challenges related to moving, stacking and storing materials. Fairchild Equipment is committed to providing outstanding service and innovative goods and solutions to become a valued business partner for its customers and create customers for life.
Episode 405: Sustainable Packaging Solutions with Cory Connors
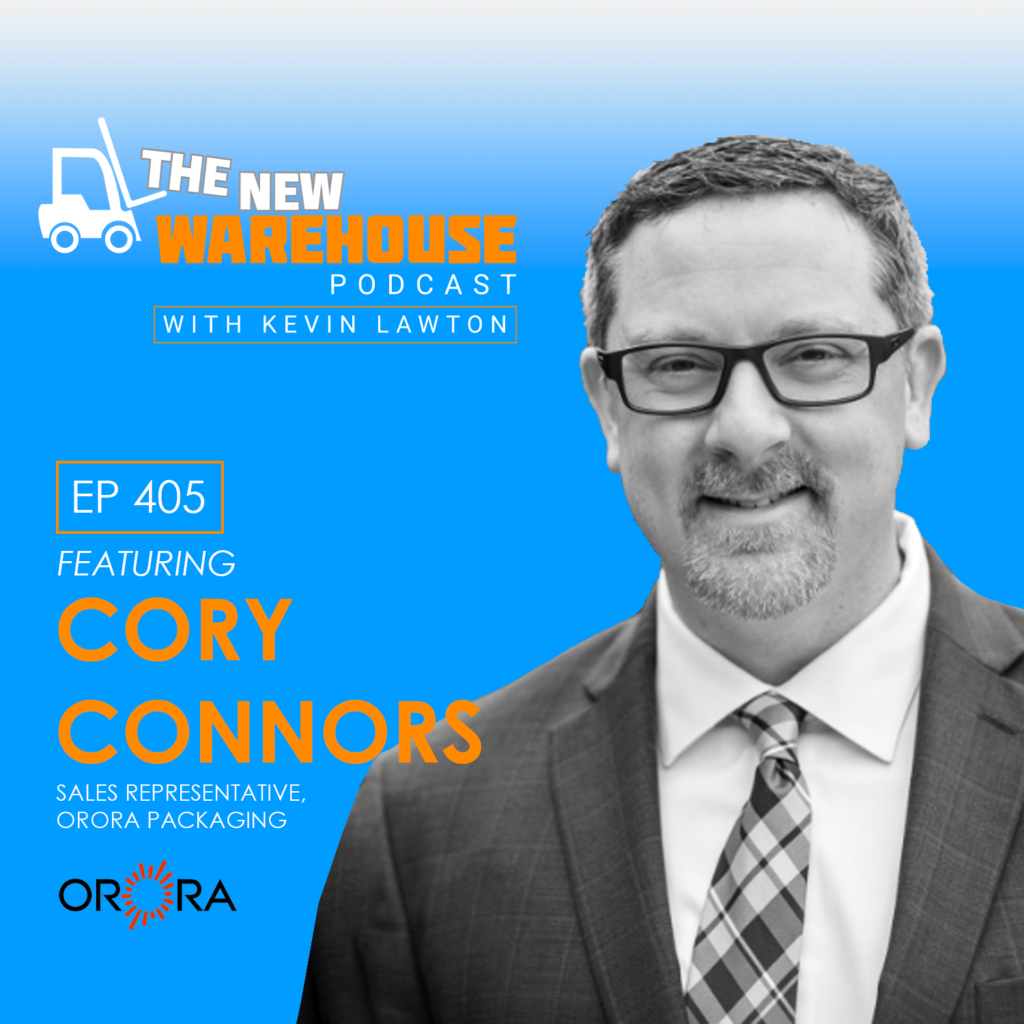
In today’s episode of the New Warehouse podcast, we have a special guest, Cory Connors, the Director of Sustainable Packaging at Orora Packaging. Cory is also the host of the Sustainable Packaging Podcast, which reflects his passion and love for sustainable packaging solutions. He grew up in the environmentally conscious Northwest region of the United States, where recycling and sustainability were ingrained in his upbringing. Orora Packaging is a global packaging company headquartered in Melbourne, Australia, with around 70 locations in North America, including 55 distribution centers and production facilities. The company is committed to being a global leader in sustainability and aims to offer more eco-friendly packaging solutions to its customers. The Role of Packaging in the Sustainable Movement Packaging plays a critical role in the global push toward sustainability. As Cory Connors rightly pointed out in the podcast, “Packaging is a trillion-dollar industry that people don’t fully understand its importance in their daily lives.” The sustainable movement starts with packaging, as it’s one of our lives most tangible and widespread components. Whether at home, at work, or shopping, we interact with various types of packaging daily. The key focus of the sustainable movement in the packaging industry is to create eco-friendly packaging solutions that are easily recyclable and reusable, thus promoting a circular economy. Brands and businesses must take the lead in adopting sustainable packaging practices and encourage consumers to make more conscious choices. Sustainable Packaging Solutions in E-commerce and Warehousing With the e-commerce and online shopping boom, warehouses have become hubs for processing and shipping products. As a result, the demand for packaging, especially corrugate, has exponentially increased. Sustainable packaging practices in the e-commerce and warehousing sectors are critical for reducing waste and environmental impact. Companies like Orora Packaging are working towards providing more sustainable packaging solutions to the e-commerce industry to address this. These solutions include reusable packaging options, eco-friendly materials, and innovations like the Box Latch, a reusable clip for temporarily closing boxes, which can significantly reduce the need for tape. The Path to Sustainable Packaging Solutions Starts with Consumer Behavior While brands and businesses play a vital role in offering sustainable packaging options, it’s equally important for consumers to embrace sustainability as a part of their daily lives. As Cory Connors mentioned in the podcast, “Sustainability is a luxury for some, but a choice for others.” Consumers must make conscious decisions and support brands that prioritize eco-friendly packaging. Sustainable choices made by consumers will drive brands and businesses to adopt more sustainable packaging options. For instance, consumers can choose products with minimal packaging, opt for reusable or refillable containers, and recycle packaging materials correctly. By collectively making these small changes, we can pave the way for a more sustainable future. Key Takeaways Sustainable packaging is a vital component of the global sustainability movement. Brands, businesses, and consumers must work together to embrace and implement eco-friendly packaging solutions. E-commerce and warehousing industries play a significant role in promoting sustainability by adopting reusable and recyclable packaging practices. Innovations like the Box Latch can reduce waste and enhance the circular economy. Consumers’ choices matter the most. Consumers can drive positive change and create a more sustainable world by consciously supporting brands with sustainable packaging initiatives and recycling properly. The New Warehouse Podcast EP 405: Sustainable Packaging Solutions with Cory Connors
EnerSys® expands NexSys® iON battery offering with addition of 80 volt model
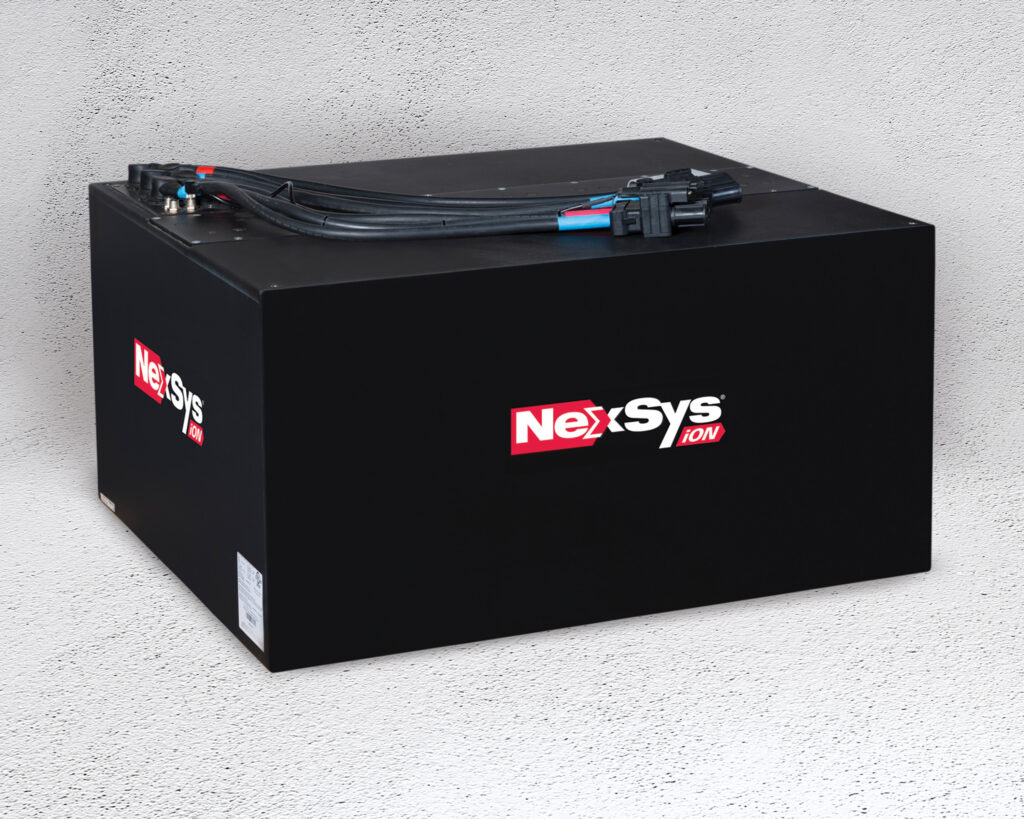
EnerSys®, the global provider of stored energy solutions for industrial applications, has expanded its line of virtually maintenance-free, high-performance NexSys® iON Lithium-ion batteries with the addition of its 80 Volt model. Engineered for fast recharge, long run times and to deliver high energy capacity in a smaller footprint, the latest NexSys® iON battery model provides customers with a premium power solution catered to meet the energy demands of a variety of heavy-duty applications, including those converting from LP- and diesel-fueled equipment to fulfill sustainability requirements. “We strive to provide our customers with solutions that are tailored to their unique operational demands,” said Harold Vanasse, Senior Director of Marketing, Motive Power Global at EnerSys. “Sometimes that can include a large warehouse that’s operating on a 24/7 basis and requires the utilization of a variety of heavy-duty equipment to keep up with their business schedule. It’s important that we can offer these operators a complete range of power options that provide high productivity and lower Total Cost of Ownership. We are excited to be able to support our customers with the addition of our NexSys® iON 80V battery.” Other notable design features of the NexSys® iON 80V battery include: Capacity: 17.8 to 35.7 kWh (222-444 Ah) Can maintain a high State of Charge (SoC) as a result of its fast recharge capability and longer forklift truck run time Eliminates battery changes for peak productivity Maintenance free – no watering, battery cleaning or long equalize charges Integrated Battery Management System (BMS) is designed to Automotive Functional Safety Standard ISO 26262 BMS supports greater safety, reliability and battery life by performing auto-diagnosis, voltage limitation (charge and discharge) and communication of performance data Optional forklift truck integration via CAN protocol Engineered with multiple layers of safety CE certified to meet EU safety, health and environmental protection requirements EnerSys® NexSys® iON batteries are available in multiple voltages, including 24V, 36V, 48V and now 80V. Additionally, fast- and opportunity-charging NexSys® iON batteries with high output NexSys®+ chargers provide added user convenience and enhanced fleet efficiency. Utilizing a proprietary EnSite™ modeling software, EnerSys can work directly with the customer to right-size a NexSys® iON battery and NexSys+ charger to their vehicle fleet, helping to eliminate the unwanted downtime and unnecessary stress associated with premature battery failure from improper installation, equipment fitting or charging practices.
JLG publishes new Accessories Resource Guide on #DirectAccess
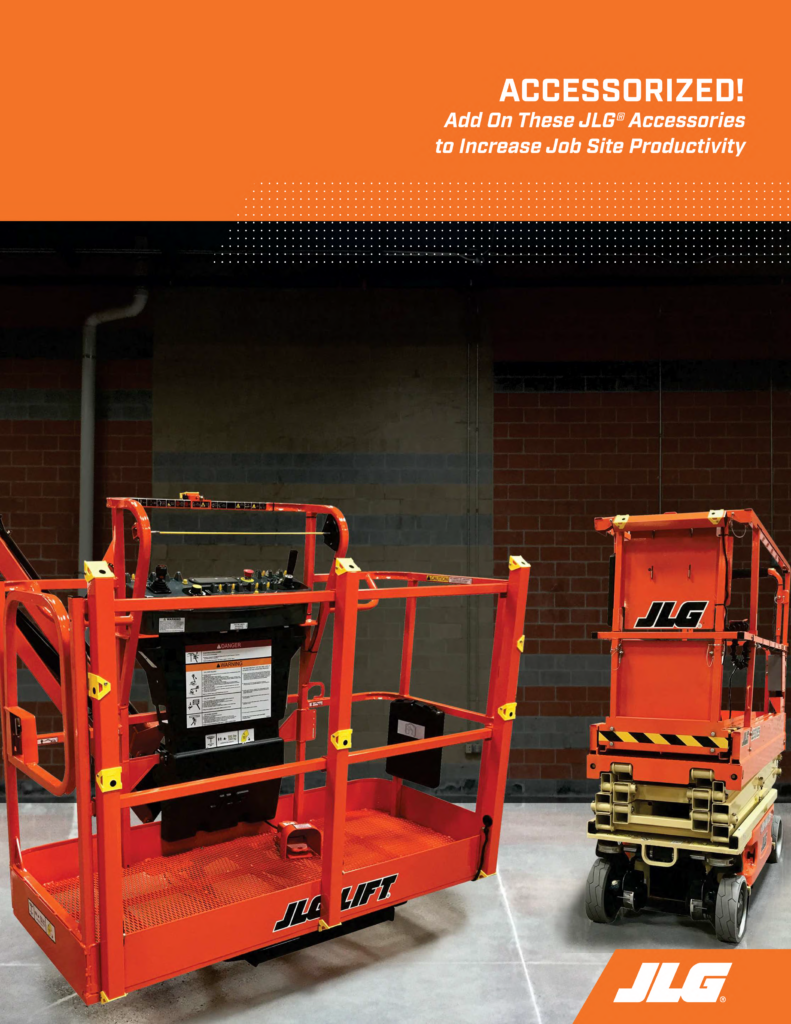
JLG Industries, Inc., a global manufacturer of mobile elevating work platforms (MEWPs) and telehandlers, has released its new resource guide Accessorized on #DirectAccess to provide customers with information about add-on JLG® accessories that can increase operators’ job site productivity, provide additional safety measures and/or extend the machine’s efficiency in certain applications. “When a crew needs to get work done at height, a JLG scissor lift or boom lift equipped with the right accessories can be one of the most effective tools to help them get the job done,” says Nancy DeZarn, Senior Marketing Manager – Aftermarket, JLG. “For example, some accessories are designed to conserve platform space, while others improve job site working conditions or help complete overhead work in welding, electrical, plumbing and maintenance applications.” In this whitepaper, JLG outlines the different options for accessories available for equipment owners and operators and provides information on how to purchase these equipment add-ons. Get your free copy of the Accessorized whitepaper, available for download now, on #DirectAccess by clicking here.
Tompkins Solutions names Dan Bryan Vice President of Sales
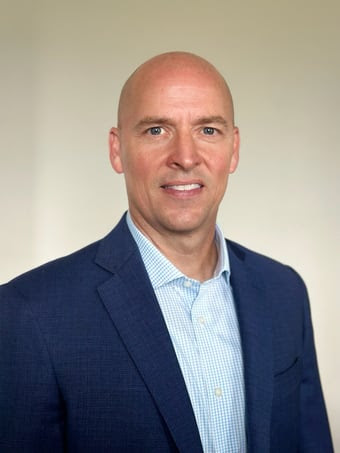
Tompkins Solutions, a supply chain consulting and material handling integration firm, just announced that Dan Bryan has joined the company as vice president of sales. In this role, Bryan will be responsible for driving sales growth and identifying opportunities to deliver value to existing and prospective customers. Bryan has more than two decades of experience leading sourcing and logistics initiatives and business development efforts for organizations ranging from small startups to Fortune 500 companies. Prior to joining Tompkins, Bryan was partner and vice president for Blue Spring Partners, and also held senior management positions with Overstock.com, iFit (formerly Icon Health & Fitness) and UPS Supply Chain Solutions. “Dan’s extensive background in supply chain and logistics and demonstrated success helping companies achieve revenue targets and reduce costs will be invaluable to both our clients and our organization,” said David Latona, CEO of Tompkins Solutions. “We’re excited to have him on board and help us continue to deliver results-driven supply chain solutions to our customers.”
Women In Trucking measures Gender Diversity in leadership roles
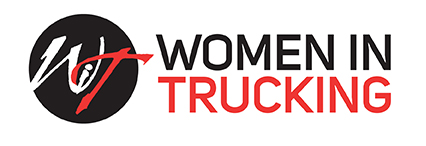
New data from the 2023 WIT Index recently released by the Women In Trucking Association (WIT) has provided a new measurement of percentages of women in corporate leadership within the commercial freight transportation industry. The WIT Index is the industry barometer that benchmarks and measures each year the percentage of women who make up various critical roles in transportation. Included are percentages of women who are in leadership roles, in the C-suite, and serving on boards of directors of companies within the transportation industry. The 2023 WIT Index found that an average of 36.9% of company leaders, defined as professionals with supervisory responsibilities, are women. The 2023 WIT Index also found that an average of 31.6% of C-suite executives are women. In addition, the 2023 WIT Index indicated that women comprise 28.4% of boards of directors of responding companies. Initiated in 2016, the index is based upon reported statistics by companies in transportation, including for-hire trucking companies, private fleets, transportation intermediaries, railroads, ocean carriers, equipment manufacturers, and technology companies. Data involving the 2023 WIT Index was confidentially gathered from January through April of 2023 from 350 participating companies of various sizes operating in the trucking industry. Percentages are reported only as aggregate totals of respondents rather than by individual company. “The presence of female leaders in transportation is critical because they bring a broader range of diverse thought, skill sets, and experiences to the workplace,” said Jennifer Hedrick, president and CEO of WIT. “Companies that boast a higher representation on their boards notably outperform organizations that do not,” she continues. “Research has shown that companies with greater gender diversity, not just within their workforce but directly among senior leadership, are significantly more profitable than those without.” For more information on the WIT Index and to download a full executive summary of the 2023 WIT Index findings, visit https://www.womenintrucking.org/index. Click here for Company Leaders – Percentage of Women Click here for C-Suite Executives – Percentage of Women Click here for Females Serving on Boards of Directors
Herc Holdings reports strong Second Quarter 2023 results and reaffirms full-year 2023 Guidance
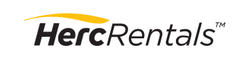
Record equipment rental revenue of $702 million, an increase of 16% Record total revenues of $802 million, an increase of 25% Net income increased to $76 million, or $2.66 per diluted share, an increase of 12% Adjusted EBITDA of $352 million increased 24%; adjusted EBITDA margin at 43.9% Rental pricing increased 7.8% year-over-year Common stock repurchases of approximately 520,000 shares Herc Holdings Inc. has reported financial results for the quarter ended June 30, 2023. Equipment rental revenue was $702 million and total revenues were $802 million in the second quarter of 2023, compared to $605 million and $640 million, respectively, for the same period last year. In the second quarter of 2023, the Company reported net income of $76 million, or $2.66 per diluted share, an increase of 12% compared to $73 million, or $2.38 per diluted share, in the same 2022 period. “We continue to generate strong, double-digit growth as a result of sound strategies and an unmatched team of product and logistics experts that embody a customer-first mindset,” said Larry Silber, president and chief executive officer. “In the second quarter, Team Herc increased equipment rental revenue by 16% on 7.8% higher pricing, despite continued supply chain inefficiencies and labor disruptions in the film and television industry, which has all but halted our studio entertainment business. Growth in national account revenue and local market expansion through acquisitions and greenfield locations drove rental revenue higher, while strong returns on fleet sales represented an incremental benefit to total revenue. This, coupled with cost efficiencies, supported a 24% increase in Adjusted EBITDA year over year. “Our non-residential and industrial markets are healthy and growing with outsized opportunities coming from federally funded, large-scale infrastructure and mega projects. The favorable market environment coupled with our expanding branch network, broad selection of premium equipment, leading customer experiences, comprehensive fleet management services and advanced technologies position us to continue to capture above-market growth in 2023 and over the long-term,” said Silber. 2023 Second Quarter Financial Results Total revenues increased 25% to $802 million compared to $640 million in the prior-year period. The year-over-year increase of $162 million primarily related to an increase in equipment rental revenue of $97 million, reflecting positive pricing of 7.8% and increased volume of 17.3%. Sales of rental equipment increased by $64 million during the period. Dollar utilization was 40.3% compared to 42.5% in the prior-year period. The change is primarily due to a slowdown in the studio entertainment business as a result of labor disruptions in the film and television industry, as well as the continued supply chain challenges that have disrupted the normal cadence of deliveries. Direct operating expenses of $282 million increased 14% compared to the prior-year period. The increase was primarily related to strong rental activity and associated additional headcount, in addition to higher maintenance and facilities expenses as we increase our fleet size and expand our branch network. Depreciation of rental equipment increased 24% to $161 million due to higher year-over-year average fleet size. Non-rental depreciation and amortization increased 22% to $28 million primarily due to amortization of acquisition intangible assets. Selling, general and administrative expenses was $111 million, or 14% higher primarily due to increases in general payroll and benefits, credit and collection expense, and selling expenses, including commissions and other variable compensation increases. Interest expense increased to $54 million compared with $25 million in the prior-year period due to higher interest rates on floating rate debt and increased borrowings on the ABL Credit Facility primarily to fund acquisition growth. Net income was $76 million compared to $73 million in the prior-year period. Adjusted net income increased 3% to $77 million, or $2.69 per diluted share, compared to $75 million, or $2.47 per diluted share, in the prior-year period. The effective tax rate was 26% in both periods. Adjusted EBITDA increased 24% to $352 million compared to $284 million in the prior-year period and adjusted EBITDA margin was 43.9% compared to 44.4% in the prior-year period. A decline in the Company’s studio entertainment revenue year over year, as well as sales of used equipment, which more than quadrupled over last year’s second quarter sales, impacted the margin performance in the latest quarter. 2023 First Half Financial Results Total revenues increased 28% to $1,542 million compared to $1,208 million in the prior-year period. The year-over-year increase of $334 million was related to an increase in equipment rental revenue of $224 million, reflecting positive pricing of 7.4% and increased volume of 20.0%. Sales of rental equipment increased $107 million during the first half of 2023. Dollar utilization decreased to 40.0% compared to 42.0% in the prior-year period. The change is primarily due to a slowdown in the studio entertainment business as a result of labor disruptions in the film and television industry, as well as the continued supply chain challenges that have disrupted the normal cadence of deliveries. Direct operating expenses of $563 million increased 19% compared to the prior-year period. The increase was primarily related to strong rental activity and associated additional headcount, in addition to higher fuel, maintenance and facilities expenses as we increase our fleet size and expand our branch network. Depreciation of rental equipment increased 26% to $313 million, due to higher year-over-year average fleet size. Non-rental depreciation and amortization increased 23% to $54 million primarily due to amortization of acquisition intangible assets. Selling, general and administrative expenses was $217 million, or 17% higher primarily due to increases in selling expenses, including commissions and other variable compensation, credit and collections expense, and general payroll and benefits. Interest expense increased to $102 million compared with $48 million in the prior-year period due to higher interest rates on floating rate debt and increased borrowings on the ABL Credit Facility primarily to fund acquisition growth. Net income was $143 million compared to $131 million in the prior-year period. Adjusted net income increased 9% to $146 million, or $5.03 per diluted share, compared to $134 million, or $4.41 per diluted share, in the prior-year period. The effective tax rate was 20% in the first half of 2023 compared to 21% in the
Hyster receives green award for developing clean power solutions for materials handling equipment
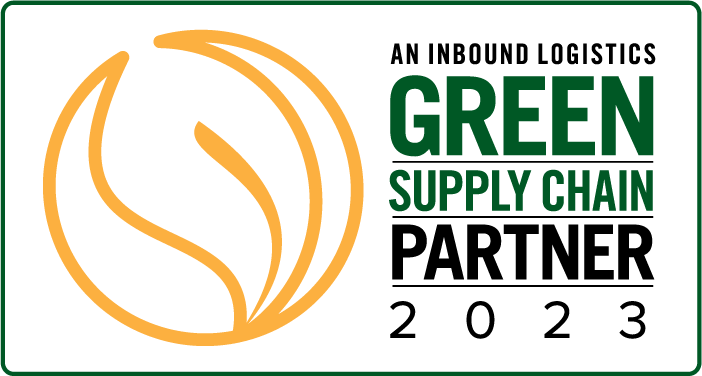
Hyster Company announces its selection as a 2023 Green Supply Chain Partner by Inbound Logistics magazine. The award honors Hyster® for innovating clean power solutions that help operations in intensive industries like ports and manufacturing mitigate environmental impact and meet growing sustainability regulations and goals. In keeping with its commitment to develop industry-first solutions, Hyster is at the forefront of electrifying higher-capacity equipment that has traditionally relied on internal combustion engine (ICE) power. The company’s innovations in hydrogen fuel cell-powered (HFC) port equipment resulted in the first-ever real-world pilot of an HFC-powered top-pick container handler, located at Fenix Marine Services in the Port of Los Angeles. The container handler is designed to provide the zero emissions benefits of a battery electric option, but with enough energy capacity to keep operations moving for a full shift, avoiding the need to interrupt productivity by stopping to recharge or refuel. This single truck is expected to reduce carbon emissions by 127 tons and reduce criteria pollutants by half a ton over the course of a year, according to the Center for Transportation and the Environment. Hyster also has planned pilots for an HFC-powered reachstacker at the Port of Valencia in Spain, an HFC-powered empty container handler and terminal tractor in Hamburg, Germany and is working with Capacity Trucks to develop electric and hydrogen-powered terminal tractors. In developing these solutions, Hyster draws on a wealth of experience in electric forklift design with the company’s line of smaller, lighter-capacity equipment, for which Hyster offers extensive electric power options. This recognition as a Green Supply Chain Partner is its fourth honor in a row and follows on the heels of the company’s selection by the Sustainable Energy Council (SEC) as one of four finalists in the industrial application category of the World Hydrogen 2023 Awards. “Increasingly, companies and government bodies are grappling with the task of limiting emissions and pursuing sustainability,” says Herman Klaus, Director, Big Truck Application Solutions, Hyster Company. “As we continue to expand green options, we’re helping our customers obtain the right clean power solution to help them meet their emissions reduction targets, even in applications where electrification might not have seemed possible before.”
CSX commits $10 Million donation to the University of Florida Graduate Center Project in Jacksonville
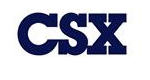
Historic investment reinforces CSX’s dedication to serving its hometown community CSX has announced a landmark $10 million contribution to the University of Florida (UF) to support the future graduate center, which is poised to redefine the landscape of downtown Jacksonville. The charitable investment will be distributed over five years and solidifies CSX as the leading private funding partner of this transformational project. “We are proud to partner with the University of Florida and the City of Jacksonville on this ambitious project to establish a world-class graduate center in the city’s urban core,” said Joe Hinrichs, CSX president and chief executive officer. “Investing in education is an investment in the future, and we believe this contribution will have a lasting impact on the region by fostering innovation, economic development, and creating bold new opportunities. This project will yield countless benefits for our community, including an influx of top-talent, which will help shape the future of Northeast Florida for generations to come.” Earlier this year, the University of Florida and local city leaders announced a partnership to explore creating a new graduate center in Jacksonville. This graduate center will create a space in Jacksonville that will shape the state’s future workforce and build a pathway for high-skilled, high-tech employees. “Gator Nation is excited and grateful to be engaged in this work with our extraordinary state, local, and philanthropic partners,” UF President Ben Sasse said. “We’re putting our shoulder to the wheel and pushing hard in the same direction to create a space in Jacksonville that will shape the state’s future workforce and build a pathway to prepare the high-skilled, high-tech employees of tomorrow. UF is ready for the next phase of this work and to lead the way toward making this shared vision a reality.” Service is a guiding principle for CSX, as evidenced through the company’s commitment to its customers, current and future employees, and the communities where it operates. CSX’s signature philanthropic initiative, Pride in Service, supports hundreds of thousands of military, veteran and first responder service members across 26 states, while also representing the pride the company takes in serving its own local community. Supporting the economic growth and educational advancement of Jacksonville is a natural extension of this mission. “Jacksonville is a city on the move, and my administration is honored to continue to build on that momentum with one of the best public universities in the nation,” said Jacksonville Mayor Donna Deegan. “We are excited to continue the work of the previous administration that invited UF to expand its presence here in Jacksonville, and we know there are numerous ways this center will support and bolster our city’s strengths in fintech, health care innovation, and other key industries. It’s a new day in Jacksonville, and both UF and vital partners like CSX will be a critical part of our important work to make Jacksonville a technology and innovation hub.” This historic $10 million donation showcases CSX’s commitment to Jacksonville and is a key component in a public-private partnership that includes support from Gov. Ron DeSantis, the Florida State Legislature, and other Northeast Florida civic, community and industry leaders. The proposed center received $75 million in the state’s 2023-2024 budget signed into law June 15 by Gov. DeSantis. The state’s contribution has been amplified by a $50 million pledge from the City of Jacksonville and $62.5 million in gifts from key industry and philanthropic supporters from across the region. By providing significant financial support to this transformative graduate center, CSX exemplifies its role as a corporate leader and catalyst for progress. The university is moving forward with raising funds for the center’s next phase, which will include project development, potential site selection and programmatic evaluation. Mori Hosseini, chair of the UF Board of Trustees, said the university community is excited about the support of CSX, Gov. DeSantis, the Florida Legislature, and community leaders across the First Coast and looks forward to a rewarding partnership that will address critical statewide workforce demand. “UF is ready for the next phase of this work and to lead the way toward making this shared vision a reality,” Hosseini said. “On behalf of the entire UF community, we are grateful to CSX and all those who are helping us advance this impactful and innovative opportunity in Northeast Florida. Our vision for this center is to leverage UF’s strengths in professional development and graduate education to future-proof Florida’s workforce. We are thrilled to partner with the State of Florida, the City of Jacksonville, and pioneering companies like CSX to bring this to life.”
Staffing employment rebounds after Holiday
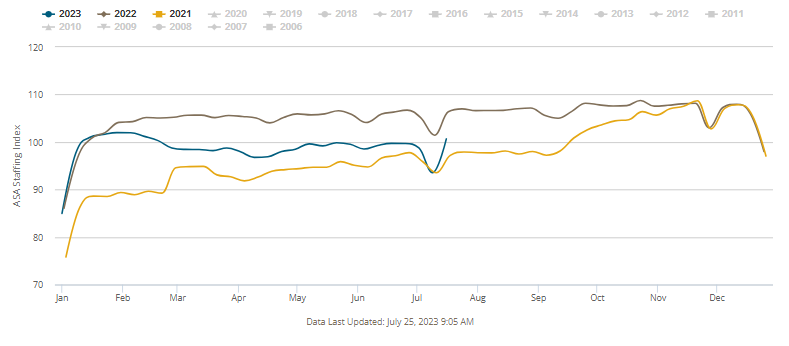
Following a sharp decline the week prior due to the Fourth of July holiday, staffing employment surged in the week of July 10-16, with the ASA Staffing Index increasing by 7.6% to a rounded value of 101. A few staffing companies listed a holiday as a barrier preventing further growth. Staffing jobs were 5.4% below the same week last year. New starts in the 28th week of the year grew 26.1% from the prior week as nearly two-thirds of staffing companies (63%) reported gains in new assignments week to week. The ASA Staffing Index four-week moving average held steady at a rounded value of 98, and temporary and contract staffing employment for the four weeks ending July 16 was 6.4% lower than the same period in 2022. “While temporary and contract hiring has fallen since last year, it’s still above pre-pandemic levels,” said Tim Hulley, ASA assistant director of research. This week, containing the 12th day of the month, will be used in the July monthly employment situation report scheduled to be issued by the U.S. Bureau of Labor Statistics on Aug. 4. The ASA Staffing Index is reported nine days after each workweek, making it a near real-time measure of staffing employment trends. ASA Staffing Starts are the number of temporary and contract employees placed in new assignments during the reporting week. ASA research shows that staffing employment has historically been a coincident economic indicator.
NAW endorses Rep. Smucker’s Main Street Tax Certainty Act
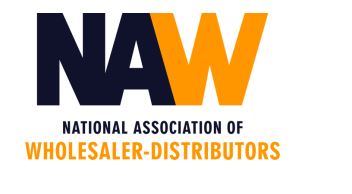
Legislation would make the Section 199A 20 percent pass-through deduction permanent, providing tax certainty for main street businesses across the country The National Association of Wholesaler-Distributors (NAW), which is the voice of the 8.2 trillion-dollar wholesale distribution industry, and employs more than 6 million U.S. workers, released the following statement endorsing H.R. 4721, the Main Street Tax Certainty Act introduced by Congressman Lloyd Smucker (R-PA): “NAW is proud to endorse the Main Street Tax Certainty Act,” said NAW CEO Eric Hoplin. “The wholesale distribution industry extends our appreciation to Congressman Smucker for introducing this vital piece of legislation, and we urge Congress to pass this bill into law,” concluded Hoplin. “Millions of main street businesses across the country including wholesaler-distributors face a tax increase if the 199A pass-through deduction is allowed to expire at the end of 2025. The looming deadline threatens the ability of businesses to continue to make payroll, hire, and invest in their local economies, “ said NAW Associate Vice President for Government Relations Alex Hendrie. “Congressman Smucker’s Main Street Tax Certainty Act stops this harmful tax increase and we urge all members of Congress support it,” concluded Hendrie. In an effort to create some level of parity between C-Corporations and smaller businesses that file taxes as pass-through entities, Congress included a provision known as Section 199A in the Tax Cuts and Jobs Act of 2017. Section 199A created a 20% deduction for pass-through businesses. However, unlike the corporate tax cuts that were made permanent, Section 199A is set to expire at the end of 2025. Pass-through business represent 95 percent of all businesses across the country and employ more than 78 million Americans. This includes the majority of wholesaler-distributors, which pay generous wages and benefits, as well as some of the highest effective income tax rates, even after the enactment of Section 199A. Many NAW members report paying an average effective rate of 30% in combined federal and state taxes, while operating with an average profit margin of just 2%, and many below 1%. A return to pre-TCJA tax rates punishes these companies that are our nations supply chain and an important engine of economic growth threatening their ability to hire, expand and invest in their employees and their communities. Read our full letter endorsing the Main Street Tax Certainty Act here. You can view other groups who are endorsing this legislation here.
Olvera elected Long Beach Harbor Commission president
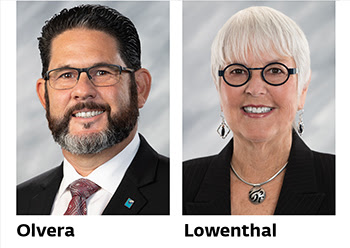
Harbor Commission Vice President Bobby Olvera Jr. was elected Monday as president of the Long Beach Board of Harbor Commissioners, the five-member panel that oversees the Port of Long Beach. The board also selected Bonnie Lowenthal as Vice President and Frank Colonna as Secretary. Each July, Commissioners select a President and two board officers for one-year terms. The Commission’s new officers will begin their terms at the next regularly scheduled meeting, on Monday, Aug. 14, when outgoing President Sharon L. Weissman will hand the gavel to Olvera. Olvera is a fifth-generation longshoreman and serves as International Vice President (Mainland) of the International Longshore and Warehouse Union. He began his 30-year history with the ILWU in 1989 and has held numerous leadership roles, including three terms as president of Local 13. In 1991, Olvera took a leave of absence to serve in the U.S. Marine Corps. In addition to his work as a labor leader and his military service, Olvera has served on the boards of the Miguel Contreras Advocacy Foundation and the United Way of Greater Los Angeles, Labor Community Services. He is also a former member of the Long Beach Economic Development Commission. Appointed to the Harbor Commission in 2020, Olvera was elected as Vice President of the Board in July 2022. “It’s an honor to be chosen as president by my colleagues,” said Olvera. “We are at a critical juncture in our Port’s history as we accelerate our progress toward zero emissions. I look forward to collaborating with fellow Commissioners, CEO Mario Cordero, staff and all of our industry partners to build a more efficient, sustainable and equitable port.” Under the City Charter, the Board sets policy for the Port and directs the Port’s CEO, who leads about 530 employees in developing and promoting the Port of Long Beach.
Toyota Material Handling promotes Jimenez to Vice President
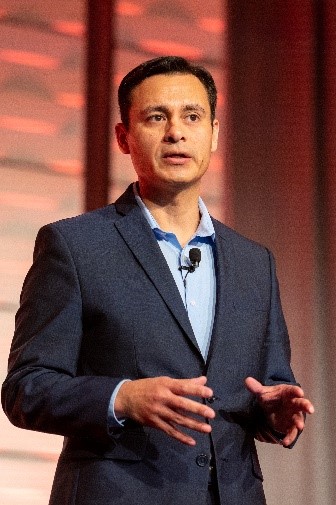
Longtime Toyota leader to oversee Regulatory Affairs, Product Planning, & Product Assurance Toyota Material Handling (TMH) has recently announced the promotion of Cesar Jimenez to Vice President of Regulatory Affairs, Product Planning, and Product Assurance. In this new role, he is responsible for Toyota’s industry-leading product line throughout its life cycle, including pre-development, launch, warranty and ongoing resolution of any technical problems. “Cesar’s knowledge of our products, commitment to our customers and dedication to quality make him the ideal person for this position,” said Tony Miller, Toyota Material Handling’s Senior Vice President of Operations, Engineering and Strategic Planning. “Cesar lives out Toyota’s commitment to ensuring all the products and solutions we produce make our customers’ work more efficient while prioritizing quality and innovation. I am honored to work alongside him to ensure our products continue meeting our high standards and solving our customers’ problems.” Jimenez began his career at Toyota as a college intern in the summer of 1996. Over the last 27 years, he has worked in various capacities, including product planning engineer, product marketing manager, and joined the Toyota executive team in 2015. Jimenez has played an instrumental role in the successful launch of over 50 material handling products. His efforts have contributed significantly to making Toyota the number one manufacturer of material handling products and solutions in North America. Jimenez is also a respected leader in the material handling industry. As a member of the Industrial Truck Association for over 10 years, Jimenez has served as the Vice Chair and Chair for both the Energy Storage Systems Subcommittee and the General Engineering Committee, which works on industrial truck performance oriented safety standards and supplies which is provided to national safety organizations. “I am humbled by this opportunity and grateful to have spent my entire career with Toyota,” Jimenez said. “This organization has given me so much, and I come to work every day driven to represent Toyota in the best possible way. Throughout my career, I’ve been inspired by Toyota’s commitment to excellence and the company’s mission to contribute to society in meaningful ways. I am excited to embrace the challenges of this new role and to contribute to Toyota’s continued success by providing products and solutions that solve our customers’ evolving problems.”
Briggs Industrial Solutions announces Mark Piccirillo as new Chief Financial Officer
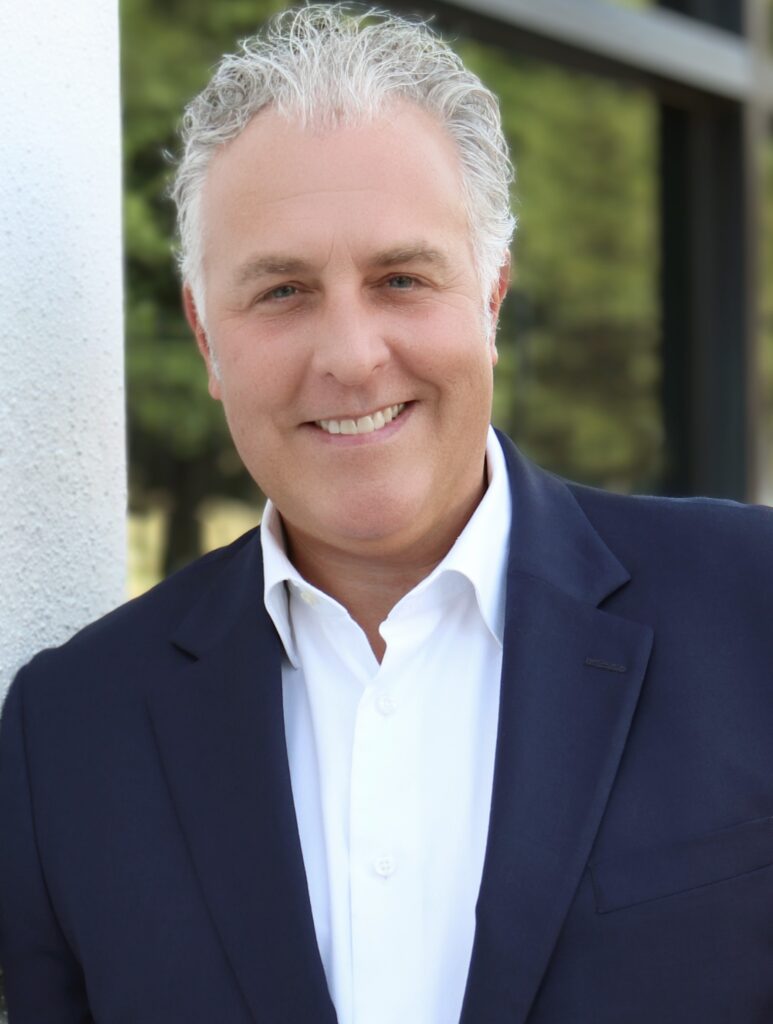
Briggs Industrial Solutions, a Sammons Industrial company, announced Mark Piccirillo as the new Chief Financial Officer. A proven strategic leader, with more than 25 years of experience, Piccirillo has held roles with responsibilities in the US and abroad that included mergers & acquisitions, P&L ownership, growth initiatives, and profitability improvements. Piccirillo has a proven record in leading complex finance organizations across multiple industries and driving change. “I am excited to have Mark join our executive team and bring his breadth of experience to our organization. Mark’s approach to leadership and team development and strong values aligns with our company values and will help us to continue to grow in the future.” Dan Lister, President, Briggs Industrial Solutions. Piccirillo joins Briggs from Lennox International, where he most recently served as Vice President, Finance & Chief Financial Officer for Lennox’ Commercial HVAC and Refrigeration businesses. During his nearly 12 years with Lennox, Mark served as the CFO for four different business segments guiding the U.S. and Internationally based businesses through various stages of turn-around, growth and expansion. Mark is a Certified Public Accountant and graduated cum laude from Babson College.
Episode 404: Slip Robotics optimizes truck loading and unloading
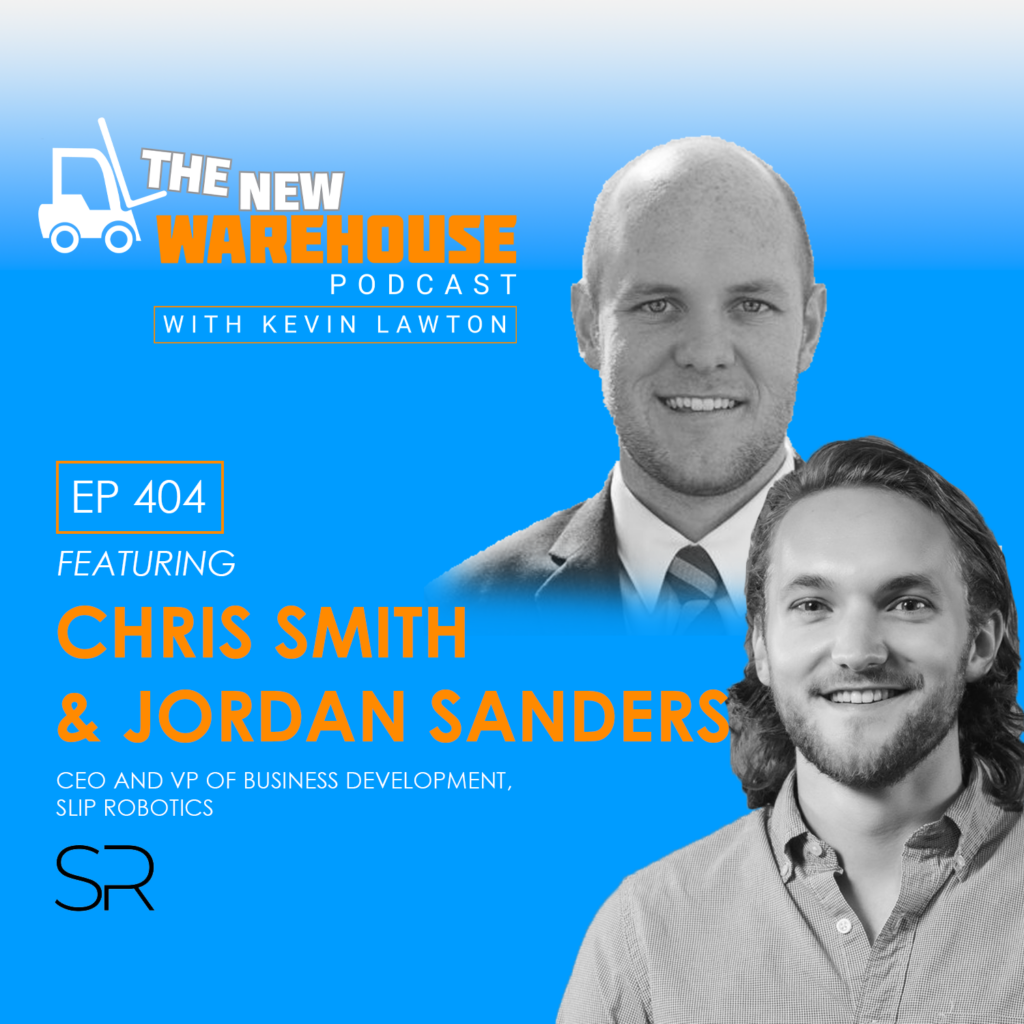
In this exciting episode of the New Warehouse Podcast, Kevin welcomes two guests from Slip Robotics: Chris Smith, the Founder and CEO, and Jordan Sanders, the VP of Business Development. Slip Robotics is a company that automates truck loading and unloading with the help of its innovative platform. Chris Smith, a supply chain veteran with experience in companies like Cummins and Tesla, shares the inspiration behind founding the company. The Eureka Moment and the Birth of Slip Robotics After observing numerous short-haul, high-frequency routes within supply chains, Chris realized the need for a better way to optimize truck unloading, leading to the birth of Slip Robotics. He adds, “We’re always looking to optimize the robot, making it better, shorter, and lighter. We also want to expand use cases, increase capabilities, and handle more different types of freight.” Jordan believes their business model as Robot as a Service (RaaS) facilitates more complex physical or operational interactions, which makes it easier for Slip to integrate with different players in the market. Unleashing the Power of the Slip Platform: Fast, Efficient, and Flexible Unloading The Slip Robotics solution centers around a large flat AMR (Autonomous Mobile Robot) that fits into a standard 53-foot trailer. Freight is loaded onto the AMRs in the staging lane, and upon the truck’s arrival, the robots go onto the truck, remain during transport, and come off on the other side. This ingenious approach ensures faster and more efficient loading and unloading, significantly reducing labor costs. Beyond Labor Savings: Key Benefits and Future Outlook Slip Robotics’ solution offers a host of benefits beyond labor savings. By automating loading and unloading, truck drivers spend less time waiting at docks, which boosts overall trucking productivity. Chris adds, “Truck drivers spend 23% of their time sitting at loading docks waiting to get loaded and unloaded. Instead, we can turn a truck through a door, fully unloading and loading it in about eight minutes.” Jordan highlighted the complexity, risk, and time-consuming nature of loading and unloading trailers. He emphasizes that their clients are reaping significant benefits, observing labor savings and substantial productivity enhancements in trucking operations and within the facility itself. Additionally, reduced forklift traffic leads to improved safety, decreased freight damage, and higher productivity within the facility. Key Takeaways Optimized Loading and Unloading: Slip Robotics’ platform revolutionizes truck unloading, significantly reducing loading times and streamlining the entire process. Enhanced Productivity: Slip Robotics helps facilities maximize their space and resources by increasing dock throughput and minimizing forklift traffic. Future Innovation: Slip Robotics plans to continuously improve and expand the platform, catering to various use cases and industries. The New Warehouse Podcast EP 404: Slip Robotics Optimizes Truck Loading and Unloading
A Light of Hope, Felling Trailers announces 2023 Trailer for a Cause Auction dates
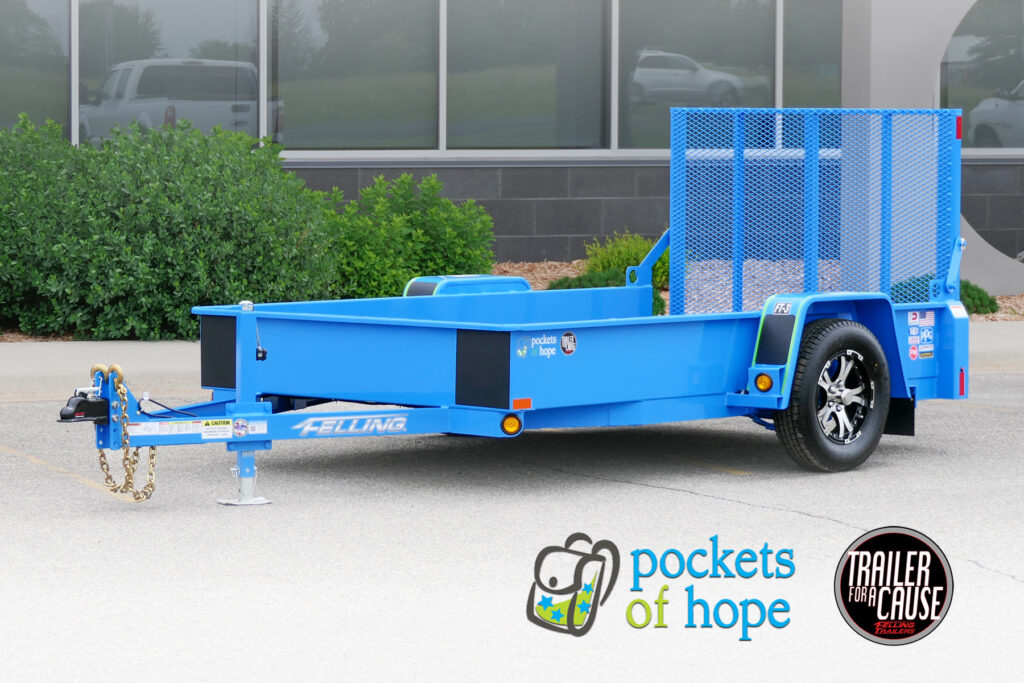
Felling Trailers, Inc. is conducting its eleventh annual online auction of an FT-3 drop deck utility trailer to benefit a non-profit organization. Pockets of Hope is the 2023 recipient. Every day, children are rescued from abuse, neglect, and abandonment. These children are confused, scared, and desperate for security and comfort after being separated from family, home, and possessions. Pockets of Hope provides backpacks filled with essential and comfort items like socks, blankets, combs, etc., for these children as they enter foster care. Felling Trailers wants to help generate awareness about Pockets of Hope, the work they do, the children they serve, and the hope and security their backpacks provide to children. Thus, Felling Trailers manufactured and painted one of its most popular trailers, custom “Hope Blue” with custom green pinstriping and bares the Pockets of Hope emblem. An online auction of the trailer will run for five days: September 11th through September 15th. Several Felling Trailers’ suppliers have joined to support Pockets of Hope by sponsoring the trailer build, from lighting to tires to decking. The 2023 Trailer for a Cause sponsors are Trans-Texas, PPG, Dexter, Sealco, Peterson, Industrial Wood (Blackwood), Demco, and Pacific Rim. One hundred percent of the winning bid will benefit Pockets of Hope! Pockets of Hope provides children, teenagers, and young adults (ages birth-21) with comfort items they can call their own. These are everyday items that many of us take for granted, such as pajamas, shampoo, a tooth brush, and more. For the recipients, these are more than a backpack; they represent hope and comfort that there are people who care. Whether received when going to a new foster home in the midst of the night or after an incident that has brought them to the CAC (Central Minnesota Child Advocacy Center), they provide each recipient a light of hope that there is good out there. “3/17: One of my favorite work memories is giving an older youth a backpack from Pockets of Hope. This specific youth told me that it was the first time in a really long time that he felt anyone cared about him (& a simple backpack with a few goodies gave him that message!) I love organizations that make a difference. If you have ever thought about children/youth in the foster care system, this is an amazing way to give them some comfort and hope!” (The Impact, www.pocketsofhope.org/the-impact.html). The Trailer for a Cause auction will start on Monday, September 11th at noon, running for five days, ending Friday, September 15th at noon. The online auction can be viewed at https://www.felling.com/our-company/trailer-for-a-cause/. Arrangements are to be made for pick up at Felling Trailers’ manufacturing facility or delivery (freight extra).