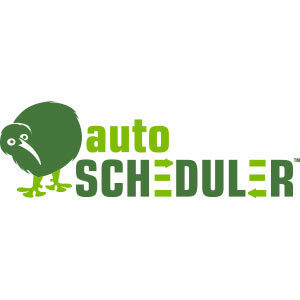
AutoScheduler to discuss Agentic AI Supply Chain on June 18 livestream
Livestream Covers How Every Core Supply Chain Function Can be Managed by Specialized AI Agents that Think, Communicate, and Act
Livestream Covers How Every Core Supply Chain Function Can be Managed by Specialized AI Agents that Think, Communicate, and Act
SUN Automation Group® has announced its 40th anniversary, marking four decades of innovation and industry leadership in corrugated manufacturing technology.
Accelerates cross-business automation strategy DHL will take a more active role in shaping and directing robotics development alongside key partners
Yale Relay solution avoids need for complex coding, enabling fast deployment, lower cost and easier ongoing management Yale Lift Truck
SSE will add complementary services and international exposure to the FOX footprint FOX, led by former Dresser-Rand CEO Vincent Volpe,
Strategic Appointment of Operations Veteran to Lead “Winning Together” Implementation Strategies. Trew, LLC has appointed Cortney Hunt as Chief Operating Officer.
The winning AI-powered solution helps retailers turn returns into revenue opportunities by optimizing product repositioning and minimizing markdown losses Invent.ai
A3 and UL Certifications, ISO Recertification, and employing TUV Certified Engineers Underpin Commitment to Excellence Wauseon Machine has highlighted its
How PepsiCo uses AI and optimization to evolve warehouse decision-making AI and Orchestration Drive More Efficient Warehouse Execution AutoScheduler.AI has
The latest round of tariffs introduced by US President Donald Trump is set to create significant disruptions in global supply
In this episode of The New Warehouse Podcast, Kevin sits down with Ryan Kirklewski, Director of Software Product Management at
Harbor Logistics company receives annual award that recognizes Lineage’s top transportation service providers in North America for high-quality service and
Strategic acquisition expands global reach and unlocks new opportunities in intelligent inventory management Newcastle Systems has announced that it has
Queen City Robotics Alliance FRC teams qualified for the FIRST® World Championships in Houston while at the state tournament last weekend
Inventory accuracy can make or break warehouse efficiency, customer satisfaction, and overall operational performance. In this episode of The New
Bradford Systems has announced a strategic partnership with Rainbow Dynamics. This collaboration aims to revolutionize storage and retrieval systems across
Peak Technologies will exhibit a broad range of smart technologies and powerful analytical tools at ProMat 2025, occurring March 17-20 in
Experience All Your Automation on One Platform at Mujin’s Booth #N6733 and Engage Hands-On in the MujinOS Experience Center Mujin
Appearing at ProMat 2025, a manufacturing and supply chain show, next week, Kardex Solutions and Paccurate have announced a strategic
New solutions from BlueBotics and UBIQUICOM ZAPI GROUP is unveiling its latest solutions for the material handling and logistics sectors at