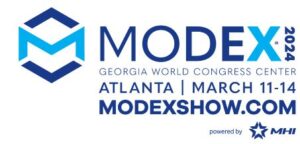
MHI announces The 2024 MHI Innovation Award finalists
MHI has released the list of finalists for the 2024 MHI Innovation Awards. After receiving 192 submissions for this year’s
MHI has released the list of finalists for the 2024 MHI Innovation Awards. After receiving 192 submissions for this year’s
Flex-Line Automation, Inc., a family-owned business in southern Illinois, has been selected to feature on a national television program. For
HWArobotics is making a splash in North America, supplying advanced shuttle ASRS technology to e-commerce logistics specialist Darwynn The North
Warehouse technology innovator, Synergy Logistics, has partnered with leading connected fulfillment solutions specialist, Techdinamics, to provide customers with integrated rate
AGILOX North America has announced its participation in the upcoming MODEX 2024 in Atlanta Booth C7492. The company will exhibit
Haver & Boecker Niagara custom-engineers the largest vibrating grizzly screen in the world. Manufactured with Hardox® steel perforated plates and grizzly
Another year, another record for the patented TAB Wrapper Tornado. Packaging machinery manufacturer TAB Industries, LLC has broken its record for
Sensitive beverages and flexible systems and solutions are the topics in focus at the KHS trade show booth for this
LiuGong North America adds Hamre Equipment to its dealer network. The Chico, California-based company has expanded from material handling equipment
Gamified workplaces entice 84% of warehouse workers Warehouse workers who play together, stay together, according to market study insights released
Cisco-Eagle, a material handling systems integration company has announced the acquisition of Trinity Controls, an innovative controls engineering company located
Seeq, an advanced analytics and industrial AI, announced its 2023 Partners of the Year. These partners have been recognized for
Booth to feature company’s latest machines to maximize profitability and productivity for concrete professionals From battery-powered equipment to portable power
Piab continues the journey to make our foremost cobot tool family available to all end users. We now offer piCOBOT®
Dematic has announced that KION Group AG (KGX.DE) has appointed Michael Larsson as President of Dematic Corp. and Member of
Material handling specialist to lead overall operations throughout the U.S., Canada, and Mexico for the automated forklift safety and fleet
Siemens is extending its drive portfolio in the extra-low-voltage range for 24–48V EC motors with its new SIMATIC MICRO-DRIVE. The
E Tech Group announces the immediate renaming of E-Volve Systems to E Tech Group, following their strategic acquisition on February
Signode, a global manufacturer of a broad range of automated transit packaging equipment, tools, consumables, automation and support solutions, is
As part of its global growth strategy, Leuze in the USA is moving to new premises. The US Leuze Sales,