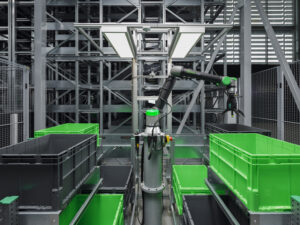
Movu Robotics launches a gripping innovation to transform robotic piece picking
Movu Robotics, a supplier for designing, developing, and implementing innovative and easier warehouse automation solutions, announces the launch of the innovative Movu eligo