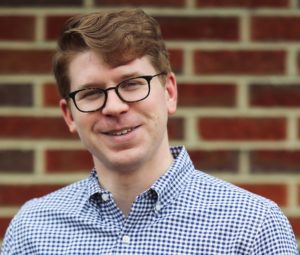
Episode 357: Ouster brings lidar to warehousing
Joining this episode of The New Warehouse is Angus Pacala, Co-founder and CEO of Ouster, a company that provides lidar
Joining this episode of The New Warehouse is Angus Pacala, Co-founder and CEO of Ouster, a company that provides lidar
Ilhan Kolko, Chief Product Officer and President of North America at ProGlove, joins the latest episode of The New Warehouse.
The New Warehouse welcomes Mark Preston, Co-Founder, and Chief Strategy Officer at StreetDrone, to discuss autonomous driving in logistics. Mark
Strengthens Jungheinrich’s intralogistics business with a complementary regional footprint Adds strong growth platform for warehouse automation solutions in the U.S.
The New Warehouse welcomes Vivek Singh, Co-Founder of Hopstack, a software platform that automates and optimizes warehouse operations. Vivek founded
Fast, accurate cross-belt sorter offers a solution for small items with the flexibility to handle larger items, too FORTNA, an
The New Warehouse welcomes Evan Hertafeld, Co-Founder of A2Z Drone Delivery. A2Z Drone Delivery develops cutting-edge technology to provide tailored
The warehouse automation was valued at $36 billion in 2021 Ukraine-Russia war, inflation, and Amazon expected to stunt growth in
Hy-Tek Holdings (Hy-Tek), a portfolio company of Dunes Point Capital, LP (DPC), has acquired Winchester Industrial Controls LLC (“Winchester”). Winchester,
Offering a track with stronger magnets for their linear motors than previously available, ETEL introduces the new MWD+. This magnet-track family is
Nucor Warehouse Systems (NWS) has promoted Reed Reynolds to Commercial Director effective Jan.1, 2023. In this new position, he will
Signode’s Automation and Packaging Technologies division celebrated the opening of their new global flagship facility with the Mayor and other
With the increasing emphasis on sustainability and recycling, Richard S. Burns & Company Inc. invented a patented system to help
Signode will be featuring its “end-to-end” solutions at PACK EXPO 2022, to be held at McCormick Place in Chicago from
Welcome to The New Warehouse podcast. In this episode, Kevin is joined by John Evans, Sr. Customer Success Manager/3PL Team
From the booth at MODEX 2022, Todd Boone, Director of Product Management Robotics and Automation at Zebra, joins Kevin for
AutoScheduler.AI, an innovative Warehouse Management System (WMS) accelerator, announces it will be presenting and exhibiting at the annual CSCMP Conference
PACSystems RXi HMI delivers visualization for the digital age: intuitive graphics, smartphone-like usability, collaboration from anywhere, and industrial ruggedness Machine
We are coming to you live from the Procensis Solution Center for this week’s episode of The New Warehouse. My
Duravant has announced the appointment of Petros Diamantides to the position of Chief Operating Officer – Emerging Markets for Duravant.