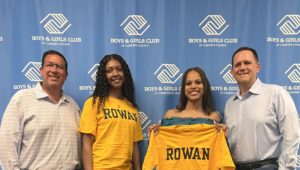
MHS Lift sending two Camden Sisters to Rowan University through Fourth-Annual Scholarship
Boys & Girls Club of Camden County members are 2022 scholarship winners MHS Lift, a national provider of warehousing and
Boys & Girls Club of Camden County members are 2022 scholarship winners MHS Lift, a national provider of warehousing and
inVia Robotics, a provider of eCommerce fulfillment automation systems –– has been awarded this year’s Best Practices Technology Innovation Leadership
Packaging machinery manufacturer TAB Industries, LLC has reported that 90 percent of the TAB Wrapper Tornado orbital wrapping systems purchased
Warehouse Management and Warehouse Execution Systems deliver throughput, Operating Cost Reduction, and ROI Softeon, a global supply chain software provider
SRSI (Slate River Systems, Inc.) and Dematic signed an integrator relationship agreement. SRSI will now be a certified integrator of
In this episode, I was joined by Monty McVaugh of OPEX Corporation at MODEX 2022. OPEX is a family-owned automation
On this episode, I was joined by Mike Stein of Signode at MODEX 2022. I first spoke to Signode at
One of the UK’s leading supermarket chains, Asda, has renewed its site-based, life-cycle services contract with Vanderlande for the next
Rick Goode, Chairman and CEO of Columbia Machine Inc., announced the acquisition of Control Design & Manufacturing (CD&M) assets on
In this episode, I was joined again by Ryan Clifford and Ryan Chesterfield of Phantom Auto at MODEX 2022. Phantom
AMR provider delivers reliable material flow with rapid ROI for automotive component manufacturer’s expanding facilities Seegrid Corporation, a provider of
At Booth #B7632A/B, Cimcorp and Murata Machinery will showcase their end-to-end automation solutions designed to bring speed, efficiency, and peace
On this episode, I was joined by the previous guest Justin Griffith of StayLinked. Justin is the CTO at StayLinked
MotionAi offers a tech-savvy, methodical approach to custom needs Motion Industries, Inc., a distributor of maintenance, repair, and operation replacement
Connected Industrial Mobility provider, SIERA.AI, announced the completion of a $6.8 million-dollar seed funding round. The funding round was supported
PAC Machinery, a provider in packaging with one of the most diverse ranges of machinery, has entered the Rollbag® R3200
Demand for industrial products has risen considerably over the past two decades — and with that, we’ve seen an increase
Sustainability report: Quantron AG has an excellent ESG rating and is a very sustainable business Strong environmental management, high sustainability
On this episode, I was joined by Dan Gilmore who is the CMO at Softeon. Dan was previously on the
The digital universe is doubling in size every two years, growing from 4.4 trillion gigabytes in 2013 to 44 trillion