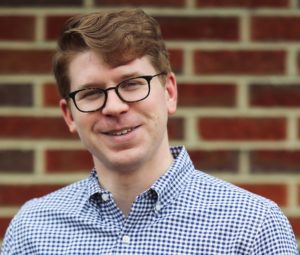
EP 236: ProGlove and the MARK Display
In this episode, I was joined by Ilhan Kolko of ProGlove. Ilhan is the Chief Product Officer and President of
In this episode, I was joined by Ilhan Kolko of ProGlove. Ilhan is the Chief Product Officer and President of
New solutions will combine MiR’s autonomous mobile robot (AMR) navigation and software expertise with Logitrans’ decades of material handling knowledge
Swisslog, a provider of best-in-class warehouse automation and software, has announced that Master Electronics, a global authorized distributor of electronic
Pivotal weekend proves to be the largest on record ever for Tecsys retailers, with key data revealing that brands operating
On this episode, I was hosted by Ed Kennedy at the Procensis Solution Center. Ed is the President and Founder
Located in Atlanta, Georgia, this space will bring capabilities for improved product demos, increased warehousing space for parts, and an
Autonomous mobile robotics provider creates next-generation autonomy platform with humanlike 3D perception Seegrid Corporation, the provider in autonomous mobile robots
AutoScheduler helps warehouse sites Go on “Autopilot” AutoScheduler.AI, an innovative Warehouse Management System (WMS) accelerator, announces that customers gain a
Graham brings more than 20 years of process industry experience, along with demonstrated success driving growth and innovation at Seeq
Tompkins Solutions, a supply chain consulting and services firm, has named Roy Smith vice president of sales of its material handling integration division.
The Industry Group includes 25 of the world’s leading AS/RS suppliers who have installed thousands of systems worldwide, in virtually every
LLumin, Inc., a provider of asset management software has announced that it has released, in partnership with Rockwell Automation, Inc.,
TREW has expanded with an additional new facility! Their existing operations in Mason, Ohio and Milwaukee, Wisconsin have been busting at
The warehouse will be the second Ken’s Food facility to install and streamline operations with Westfalia’s automated storage/retrieval and warehouse
Columbus McKinnon’s First Intelligent Actuator combines Plug-and-Play Control and feedback with Robust Duff-Norton® Hardware Combining intelligent controls with some of
Autonomous Mobile Robotics provider’s industry-leading customers to share insights, capture benefits ahead of widespread deployment Seegrid Corporation, the provider in
Creform has introduced an unusually long version…measuring 17′ L x 30″ W x 39″ T…of its model CA-B50100-NSI, Bi-directional AGV.
Palletizing solution automates double pallet stacking for four SKUs simultaneously At PACK EXPO 2021 in Las Vegas, MHS, a single-source
On this episode, I was joined by the VP of Digital Strategy at Blue Horseshoe, Steve Shebuski. Blue Horseshoe is
GEODIS, a global transport and logistics provider, and Advanced Handling Systems (AHS, LLC), a full-service provider of integrated fulfillment and