MHS wins Product of the Year award for HC-Loop sorter
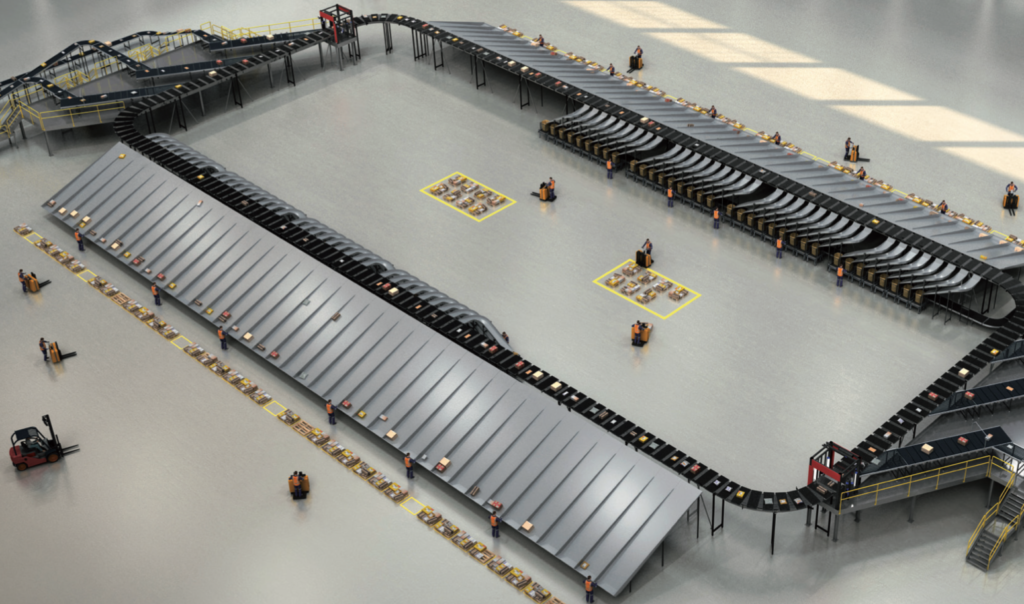
Cross-belt sorter wins conveyors and sortation category in annual product competition MHS a single-source provider of material handling automation and software solutions, took home a product of the year award from Material Handling Product News (MHPN) for its HC-Loop sorter. The company’s cross-belt sortation system won first place in the conveyors and sortation category, triumphing over three other finalists. MHPN readers cast 3,750 votes to decide winning products in 13 categories. The MHS HC-Loop sorter is ideal for operations facing e-commerce challenges like massive order volumes and high package variety, handling everything from flats and bubble mailers to bagged items and corrugate cases. It uses an automatic centering system that precisely locates items in the middle of the conveying surface for consistent divert accuracy, enabling narrower divert chutes that enable greater sortation capacity while maintaining an efficient footprint. “With parcel and e-commerce operations experiencing such extreme growth in order volumes, advanced sortation solutions are critical pieces to enable fast, efficient delivery,” says Rush Fullerton, vice president, business development, MHS. “Our HC-Loop sorter is a solution designed for the needs of today’s economy, and recognition from MHPN readers confirms that.” The sorter’s modular design allows for layout flexibility and uses fewer components to simplify maintenance and improve reliability. It also features the new MHS linear induction motor that offers smooth, consistent operation for precise speed control and a long system lifespan.
Numina Group welcomes Bob Fischer to Warehouse Automation Technology team
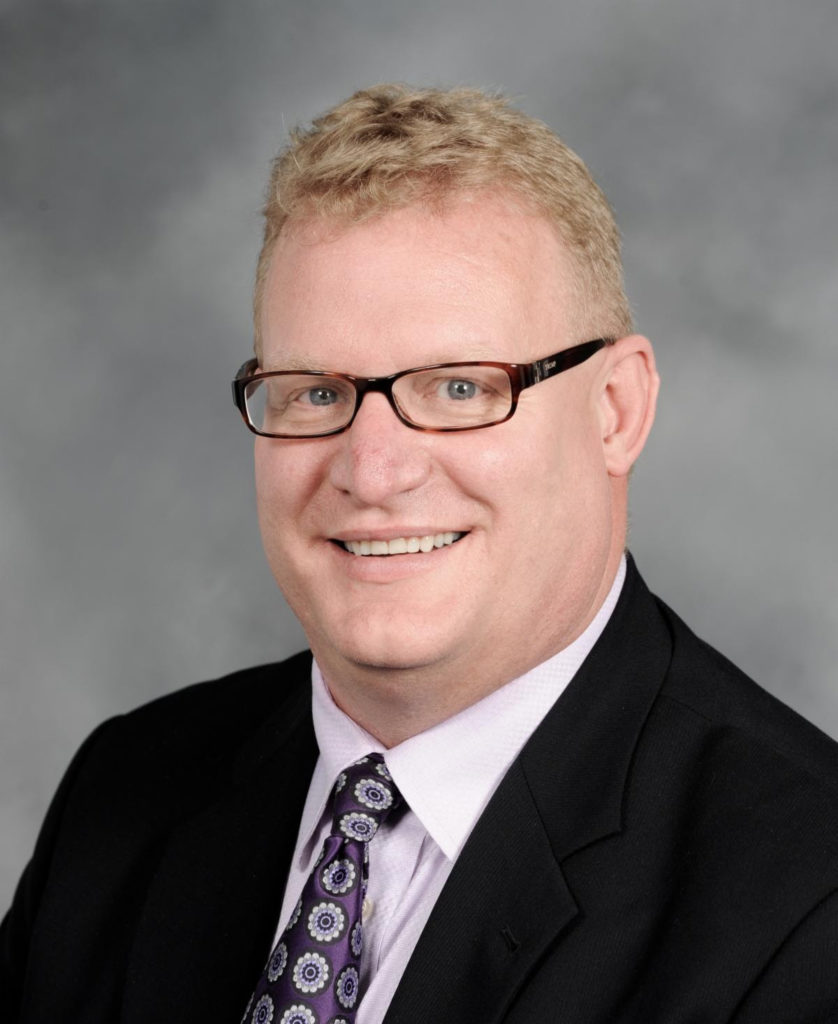
The Numina Group, a supplier of automated warehouse execution and control systems, announced today that Bob Fischer, an industry-recognized leader in logistics technology, will be joining its system engineering and delivery team. Fischer brings more than 30 years of logistics and transportation technology experience to his role at Numina Group. He began his career selling mobile computing solutions and logistics and shipping software in the mid-80’s and 90’s. In 1997, he founded Advanced Distribution Solutions Inc. (ADSI), a company specializing in multi-carrier shipping software, and sold it in 2017. During his career he has helped hundreds of companies solve their supply chain automation challenges by leveraging process and technology improvements. In joining Numina Group, Fischer will focus on expanding Numina Group’s west coast customer install base for the firm’s Real-time Distribution Software (RDS™) pick by voice and family of warehouse order fulfillment automation technologies. Numina Group is a leader in assisting companies to define, design, and implement distribution process improvements that make the business more efficient and profitable. “I’m extremely excited to be joining an industry leader in helping companies achieve measurable financial and labor savings managed with the right blend of warehouse automation,” said Fischer. “Numina Group has earned a stellar reputation with its customers and I’m honored to become part of the team.” “Bob has been a valued partner to Numina Group over the years, and we’re thrilled to add his considerable knowledge to our team,” said Dan Hanrahan, CEO of Numina Group. “His focus has always been on ensuring that a client obtains a tangible value by investing in automation technologies, and his experience will be invaluable to Numina Group’s continued growth.”
Eastey introduces the EXS-100 table top Strapping Machine
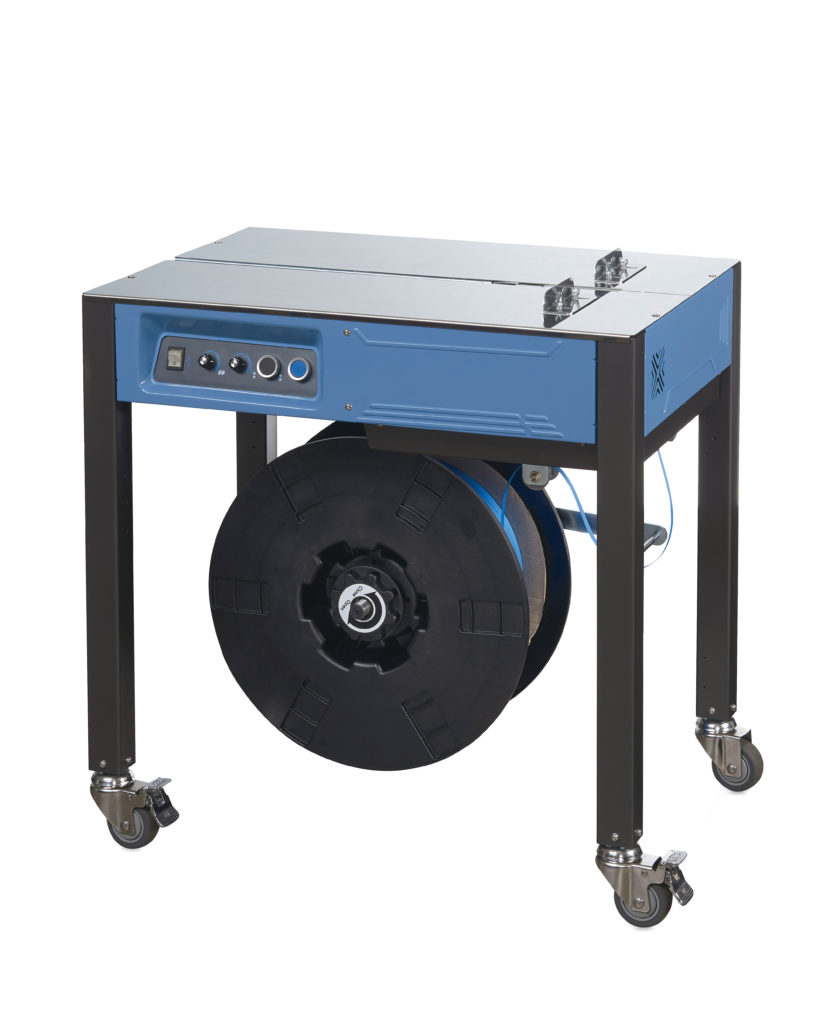
Eastey, a manufacturer of shrink packaging equipment, automated case erectors, tapers, and material handling solutions, introduces the EXS-100 semi-automatic strapping machine designed to efficiently strap and secure over-filled and heavyweight packages. The semi-automatic EXS-100 strapping machine is designed to apply a plastic strap around user’s packages, preventing them from opening during handling and transit. The EXS-100’s bottom seal design is an ideal solution for low to medium volume users that need additional security beyond case taping. Operating the EXS-100 strapping machine is easy and can be learned in minutes. The machine features an open cabinet design, making it easy to view and change the poly strapping. Additionally, the EXS-100 features electronic tension control, allowing the user to adjust the proper tension for a wide variety of packages, and the heated strap-weld sealing system ensures a secure strap. The system comes standard with four locking casters that allow for easy transportation within the facility. The EXS-100 is pre-configured to an industry-standard height of 30”, making a comfortable fit for most packaging environments. The semi-automatic EXS-100 is available now through Eastey’s network of authorized distributors. Sales inquiries can be directed to Joshua Nelson, Eastey, 7041 Boone Avenue, Brooklyn Park, MN 55428, 763 428-4846. jnelson@engagetechnologies.net Eastey, Squid Ink, American Film & Machinery (AFM) and Cogent Technologies are all divisions of Engage Technologies Corporation. Eastey (eastey.com) is a leading manufacturer of heavy-duty shrink packaging equipment and automated case sealing systems for packaging applications. Squid Ink (squidink.com) is a manufacturer of coding and marking systems for product identification and traceability, providing superior quality inks and low maintenance printing equipment. American Film & Machinery (afmsleeves.com) supplies shrink labelers and tunnels, shrink sleeves, and tamper bands. Cogent Technologies (cogent-tech.com) manufactures infrared drying systems used to dry ink in the industrial and graphics industries. Engage Technologies Corporation is headquartered in Brooklyn Park, MN with facilities in Rogers, MN, Spring Lake Park, MN, The Hague, Netherlands, and Shanghai, China. The Company continues to expand sales and services, with authorized distributors strategically located throughout the U.S. and the rest of the world.
Dematic named best and brightest in wellness
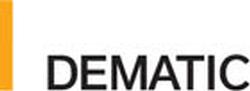
Intralogistics innovator Dematic has been named Best and Brightest in Wellness® for 2019 by the National Association for Business Resources. The Best and Brightest in Wellness Award recognizes and celebrates excellence in health awareness by highlighting organizations that promote a culture of wellness — organizations like Dematic that plan and implement efforts to allow their employees and the community to become a healthier place to live and work. “At Dematic, our employees are the foundation of our organization,” said Michele Longo, Senior Vice President, Human Resources, Dematic. “By investing in wellness programs, we are keeping that foundation strong. When people feel good about themselves, it is reflected in their lives and their work. We’re honored to receive this award as a recognition of our programs.” The programs (known collectively as Optimize Your Wellness) promote a sustainable culture of well-being with engaging resources and services to assist individuals in developing effective, long-term healthy behaviors. This includes encouraging improved physical activity, healthy nutrition and positive lifestyle choices. Programs available to US employees include: Fitness reimbursement Fitness centers and group classes Nutrition consultants Immunizations Wellness challenges Financial planning services
SUN Automation Group announces partnership with Greene House Group
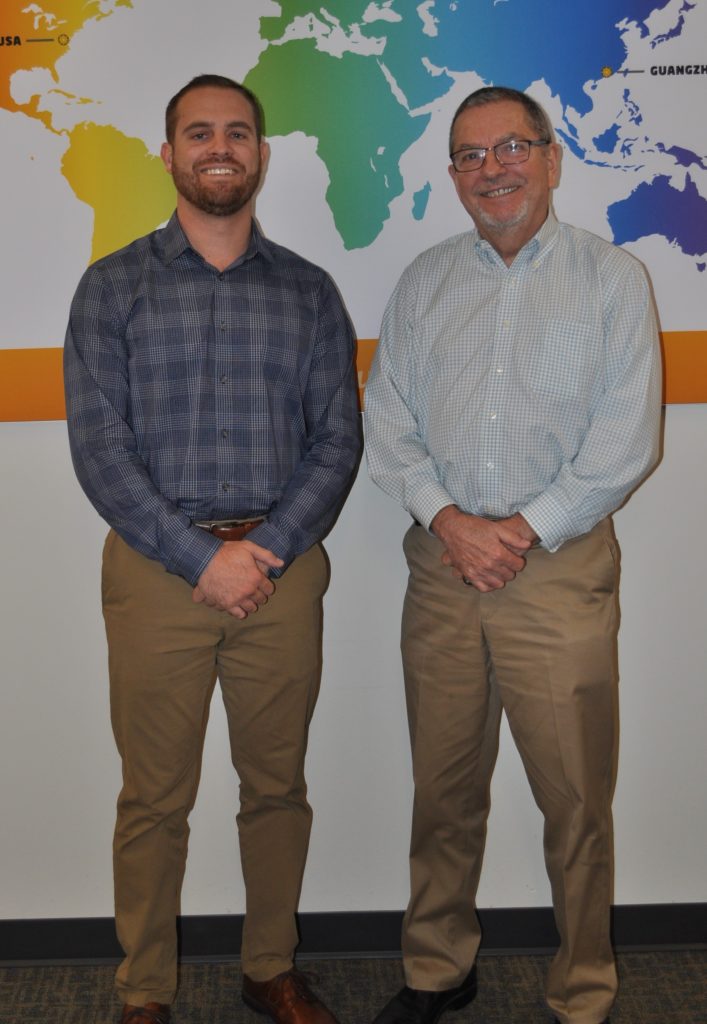
Greene House Group to Represent SUN Automation Group’s Line of Solutions for the Corrugated Industry SUN Automation Group®, a global provider of innovative equipment to the corrugated industry, has announced that the Greene House Group will represent SUN equipment and parts to its customers in California, Oregon, and Washington. Frank Greene, Greene House Group’s founder and President, brings over 30 years of experience in both the corrugated and converting segments of the industry. His vast skill set and knowledge base translates to consistently providing top of the line equipment solutions for box plant corrugators. Working alongside Greene is his son, Hayden Greene, whose industry acumen and sales aptitude further enhance Greene House Group’s capabilities. “I’ve long admired SUN Automation Group’s dedication to innovation and its commitment to listening and responding to customers’ needs. As their newest regional sales representative, I’m excited to share with my customers how SUN’s products deliver efficiencies and maximize ROI,” says Frank Greene. SUN believes this partnership will enhance its presence in these regions, resulting in increased market share. “We’re proud to be represented by Greene House Group, and have full confidence in their ability to convey SUN’s value to customers. Our network of sales partnerships continues to be an integral component of our growth strategy,” says Greg Jones, Vice President of Global Sales & Aftermarket at SUN Automation Group.
Smartrac to sell its RFID inlay business to Avery Dennison
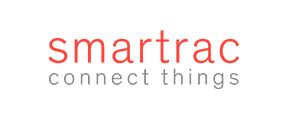
Smartrac Technology Group, a global provider in RFID technology and IoT solutions, has announced that it has reached a definitive agreement to sell its RFID Transponder Division to Avery Dennison Corporation. Headquartered in Glendale, California, Avery Dennison is a global materials science and manufacturing company specializing in the design and manufacture of a wide variety of labeling and functional materials. Its products include pressure-sensitive materials for labels and graphic applications; tapes and other bonding solutions for industrial, medical and retail applications; tags, labels and embellishments for apparel; and RFID solutions serving retail apparel and other markets. Smartrac’s RFID inlay and tags business will complement Avery Dennison’s Intelligent Labels platform, expand its existing product portfolio, enhance the company’s R&D, manufacturing and sales capacity and increase its RFID offerings for a broad variety of customer requirements and applications. The transaction will also provide the opportunity to expand market coverage and to accelerate RFID growth opportunities. “What we are announcing today is a big change in Smartrac’s history. Our people and capabilities are very complementary to Avery Dennison, hence offer a perfect basis to expand market success. We are convinced that our RFID inlays and tags business will face a bright future as part of Avery Dennison’s Intelligent Labels business, which is set to thrive on the rise of the Internet of Things and the growing customer demand for connected products. At the same time, our successful Solutions Business Division will continue to independently build on its offerings supporting the digital transformation,” said Christian Uhl, CEO and Chairman of the Management Board at Smartrac. “We believe in a future where every physical item will have a unique digital identity and digital life, which will transform the visibility of products throughout the supply chain, all the way to the consumer, helping to improve efficiencies, increase sustainability, and enhance consumer experience,” said Francisco Melo, vice president and general manager, intelligent labels for Avery Dennison. “The capabilities of Smartrac will enable us to accelerate our strategy and deliver on this vision across multiple verticals.” As part of the transaction, Avery Dennison will acquire Smartrac’s Transponder business and associated assets, including all manufacturing, R&D, sales and administration facilities, and will take over all affected employees. Avery Dennison will also assume all contractual obligations to employees, customers and suppliers. The acquisition is subject to regulatory approvals and other customary closing conditions.
Sun Automation Group promotes new Director of Sales in N.A.
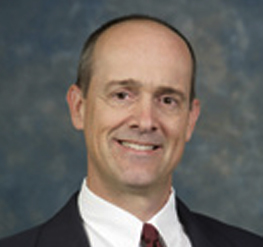
SUN Automation Group®, a global provider of innovative equipment to the corrugated industry, is pleased to announce Frank Reynolds has been promoted to Director of Sales. In this new role, Reynolds will be leading the direct external sales team to drive growth and profitability of core SUN products and new products across the North American market. Reynold’s expanded responsibilities will also include managing the product development cycle and collaborating cross-functionally across the SUN organization to ensure all activities align with bringing value to box plants. He will continue report to Greg Jones, Vice President of Global Sales and Aftermarket. “Promoting Frank to Director of Sales significantly strengthens our pivotal growth around the external direct domestic sales team. His accumulated industry knowledge and leadership skills will empower our sales team to continue to grow our business,” commented Jones. Reynolds has been in the industry over 34 years, and has served SUN in many roles in both the engineering and sales sectors for the past 28 years. “Although I have a strong engineering background, I’ve connected deeply with the sales arm of the business. Cultivating relationships with customers and prospects to address their business needs is tremendously fulfilling,” said Reynolds. “Frank has unequivocally contributed to SUN’s exponential growth for the better part of three decades. He’s proven his abilities as an engineer and sales manager, and we look forward to his team leadership,” said Jones.
MHS doubles the size of its global headquarters
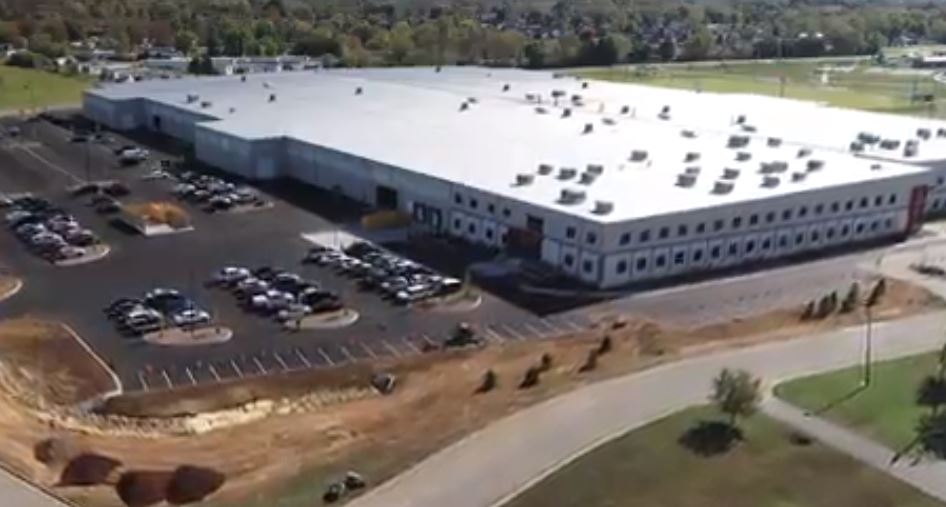
Expansion of existing facility accommodates need for greater manufacturing capacity, headcount MHS, a single-source provider of material handling automation and software solutions, announces the opening of its expanded global headquarters at 131 Griffin Way in Mt. Washington, located just outside of Louisville. The facility now offers over 400,000 square feet of space, enough to house manufacturing, engineering, sales, marketing and executive management functions. “When we moved into the Mt. Washington facility in 2017, it was a big, brand new space. But in just one year, it became apparent we needed more room,” says Greg Judge, president, MHS. “The expansion enables us to continue our rapid growth and further cements our presence in the Mt. Washington community.” The state of Kentucky is providing up to $2.65 million in tax savings through the Kentucky Enterprise Initiative Act and Kentucky Business Investment program, subject to MHS hiring 300 new Kentucky-based employees. Between hiring the new employees and the cost of the headquarters expansion, the MHS investment adds up to more than $20 million. The new construction features a new on-site fitness center for employees and specially commissioned artwork to commemorate the company’s significant milestones and history in the Louisville metropolitan area. For employment opportunities with MHS, interested parties can visit www.mhsglobal.com/who-we-are/careers.
TVH offers a new telematic solution to its customers
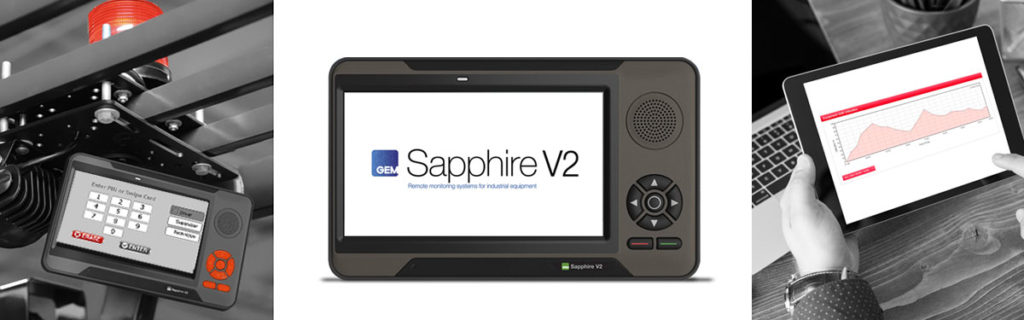
TVH in the Americas (TVH), a global provider of quality replacement parts and accessories for the material handling and industrial equipment industries, is now offering a telematics solution from GEM One. What is telematics? Telematics is the transfer of digital information over long distances using wireless forms of communication to tell you what is going on with the forklift without physically being on it. This monitoring system will allow you to easily track and manage your equipment remotely. You can receive real time updates of incidents, track and record all pre and post operational check lists ensuring you are OSHA compliant, know who is operating the vehicle and so much more! These systems can easily be installed on any make and model of forklift, making it the ideal choice if you have mixed fleets. GEM One offers different types of monitoring solutions, which can be customized with accessories to fit your specific needs.
Strategic Mobility Group, LLC kicks off Breast Cancer Awareness month with second annual Fundraising Campaign
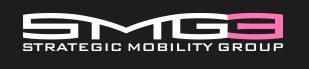
About 1 in 8 U.S. women will develop invasive breast cancer over the course of her lifetime Strategic Mobility Group, LLC (SMG3), a Certified WBENC Women’s Business Enterprise, has launched its second annual Breast Cancer Awareness Fundraiser with the goal of raising $1,000 by October 31st, 2019. SMG3 is asking anyone feeling compelled to finding a cure, to simply share a pinned LinkedIn post on their page. Every contribution brings us one step closer to eradicating this deadly disease. SMG3’s mission is to reduce the incidence of breast cancer, decrease mortality rates, and assist the individuals and families of those who have been impacted by breast cancer. In the United States, a woman is diagnosed with breast cancer every three minutes. Early detection and education are key to breast health and survival rates. “Breast cancer touches the lives of so many women around the world. We wanted to come up with a convenient way for everyone to aid an important cause, and hopefully inspire others to Think Pink while taking action during the month of October. SMG3’s support for breast cancer research reflects a company-wide commitment to bettering the lives of others,” says Nancy Gorski, Presidents & CEO of SMG3. Gorski continues, “Giving back is an integral part of our brand DNA, and we are excited to bring SMG3’s “Be The Good” mantra to life outside of the four walls of our office.” Strategic Mobility Group will donate to a nonprofit committed to breast cancer awareness or research; the beneficiary will be announced at the end of the month. In addition to their support of breast cancer research, SMG3 has been active in numerous community initiatives including an annual coat drive, Toys for Tots, Wounded Warriors, PADS, Children’s Memorial, and Medical Ministry International, among other inspiring organizations. Please visit http://www.linkedin.com/company/strategic-mobility-group to support a breast cancer-free world.
MHS expands in-house sortation portfolio with cross-belt sorter, shoe sorter designed for small items
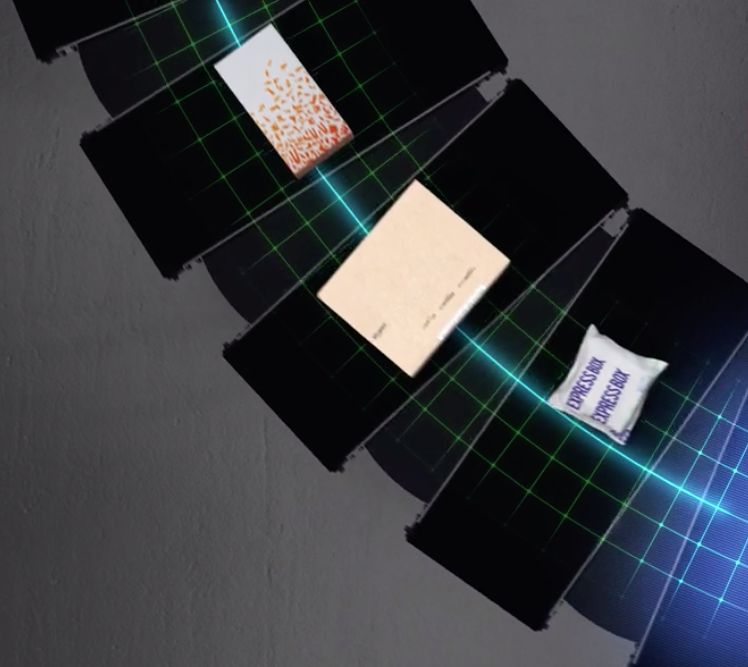
New sorter offerings debut at Parcel+Post Expo MHS, a single-source provider of material handling automation and software solutions, announces two new additions to the company’s in-house sortation portfolio at the Parcel+Post Expo trade show in Amsterdam. At booth #430 in hall 8 until October 3rd, MHS is exhibiting its new HC-Loop cross-belt sorter and HC Smalls sliding shoe sorter. The HC-Loop is the company’s first cross-belt sorter, offering a flat carrying surface to handle the high volumes and package variety of e-commerce with maximum efficiency and accuracy. It includes an automatic centering feature that precisely locates items in the center of the conveying surface for consistent divert accuracy. This level of accuracy allows the system to use narrower divert chutes, boosting sortation capacity while maintaining an efficient footprint. The HC-Loop has a modular design for layout flexibility and space savings, and fewer components for improved reliability and simpler maintenance. The HC-Loop uses the new MHS linear induction motor that avoids contact and vertical attraction, for smooth, constant operation that contributes to long lifespans and precise speed control. The HC Smalls Sorter from VanRiet, an MHS company, is a versatile sortation solution designed for the smallest, lightest parcels, capable of handling items as small as 4-by-2-by-0.02 inches and as light as 0.1 pounds. The advanced sliding shoe design works in tandem with rounded slats to prevent thin products from becoming trapped underneath shoes and causing jams. It offers a high density of exits to maximize capacity in a space-efficient framework, with low noise levels and a maintenance-friendly design to keep operations productive. “These two new sortation products further demonstrate the capability of MHS as one-stop shop for distribution centers looking to handle the challenges of e-commerce with the latest technologies and responsive support,” says Rush Fullerton, senior vice president, business development, MHS. “From electronics and apparel to flats, bagged items and totes, these technologies position us to solve customers’ throughput challenge no matter the product mix they handle.” MHS draws on extensive controls engineering and design experience to offer complete, turnkey control solutions to leverage a variety of automated sortation systems for maximum effect. The company’s Lifecycle Performance Services group provides maintenance, support, modification and optimization services to keep systems running at peak efficiency and maximize long-term value.
Vecna Robotics introduces new line of Autonomous material handling solutions in collaboration with UniCarriers
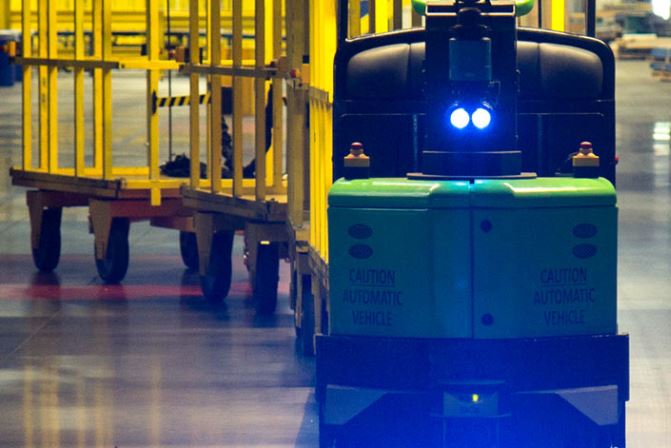
Vecna Robotics, a provider in autonomous material handling solutions, is teaming with UniCarriers Americas (UCA), a manufacturer of material handling equipment and part of the family of one of the world’s largest manufacturing companies, Mitsubishi Heavy Industries. Vecna Robotics and UCA are collaborating on a line of autonomous material handling vehicles for warehouses, distribution centers, and manufacturing environments. Vecna Robotics is integrating its state-of-the-art autonomous navigation technology, learning algorithms, and workflow orchestration software into UCA vehicles turning them into Autonomous Mobile Robots (AMR), capable of moving bulk material through dynamic warehouse environments. The new line will also feature autonomous tuggers and lift trucks capable of vertical and horizontal movements with material up to 10,000 pounds. Renderings of the new autonomous pallet jack will be on display at Vecna Robotics HQ Reveal and Insider Showcase on September 26, 2019. “Vecna Robotics’ collaboration with UCA has come at the perfect time,” said Michael Baier, Director of Hardware Engineering for Vecna Robotics. “Our customer base is rapidly expanding. Companies are no longer asking themselves if they should automate, they are now looking at when to automate and the sooner, the better. Partnering with an industrial vehicle design expert like UCA helps us provide our customers with exceptional products and meet demand without skipping a beat.” The fleet will also feature Vecna Robotic pivot.al™ orchestration system. Pivot.al is an AI-based fleet manager that distributes and redistributes work amongst humans, robots, and standard automation based on capabilities, location, and operational priorities. Pivot.al redesigns workflows, mixing and matching assignments based on the unique capabilities of humans and robots in real-time to ensure current operational processes align with current operational needs. “Customer’s expectations are changing too fast. Companies that restrict themselves to a specific workflow, robot or AGV are not optimizing productivity efficiently,” said Brian Markison, Senior Director of National Accounts and AGV Sale at UCA. “This strategic partnership helps Vecna Robotics and UCA reach a very important shared objective – providing customers flexible and cost-efficient material handling solutions that reliably gets goods out the door no matter how demand or markets change.”
DENSO, Creator of the QR Code, reflects on the technology’s progress 25 years after its invention
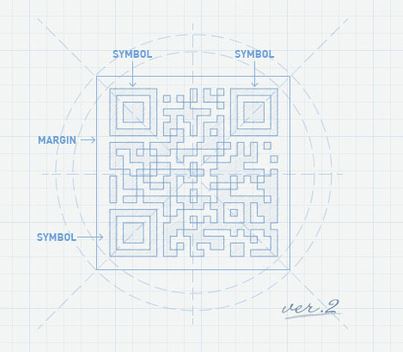
A quarter century after its creation, DENSO’s invention has evolved to become an essential technology across the globe DENSO, the world’s second largest mobility supplier, is celebrating the 25th anniversary of its invention of the QR code. The technology, a machine-readable code used for storing information, was created by DENSO-subsidiary DENSO WAVE with the goal of achieving more detailed production management at manufacturing sites. To commemorate the anniversary, DENSO WAVE has launched a new website that traces the history, future and benefits of this now-ubiquitous technology. In the 1980s, barcodes were widely used for manufacturing and distribution processes. However, within a decade, an industry shift from mass manufacturing to more flexible production required a stronger barcode. A two-person DENSO development team was tasked with the challenge, needing to create a code that could store more information, be read at a higher speed and fit on smaller surfaces. To accomplish this, the team spent nearly two years creating a design with a specific position detection pattern ratio – 1:1:3:1:1. These codes were two dimensional and could hold approximately 7,000 numerals, allowing them to be read more than 10 times faster than a traditional barcode. Though QR codes were originally developed to create efficiencies in manufacturing processes, DENSO encouraged its use more broadly by making the technology license-free. Since its invention, the popularity of QR codes has spread to encompass numerous industries, including: hospitality and tourism, education, and real estate. The codes have contributed to the growth of cashless payment systems, are used to trace foods, pharmaceuticals and other merchandise, and are regularly seen on event tickets and advertisements. “Throughout its development, the QR code represented the type of innovation that DENSO strives for in its efforts to shape the future of mobility,” said Kenichiro Ito, senior executive officer for DENSO Corporation and chief executive officer of DENSO’s North American Headquarters. “Twenty-five years later we can clearly see its vast and impactful results. It is this sort of long-term vision that we look to emulate today to not only improve upon what has already been built, but to create new products and services that will inspire a better future.” Since launching the QR code in 1994, DENSO WAVE has further advanced QR technology to meet social needs with its iQR code, its SQRC code and its Q-revo protection service.
MHS caps off RIA Autonomous Mobile Robot Conference with tour of R&D facility
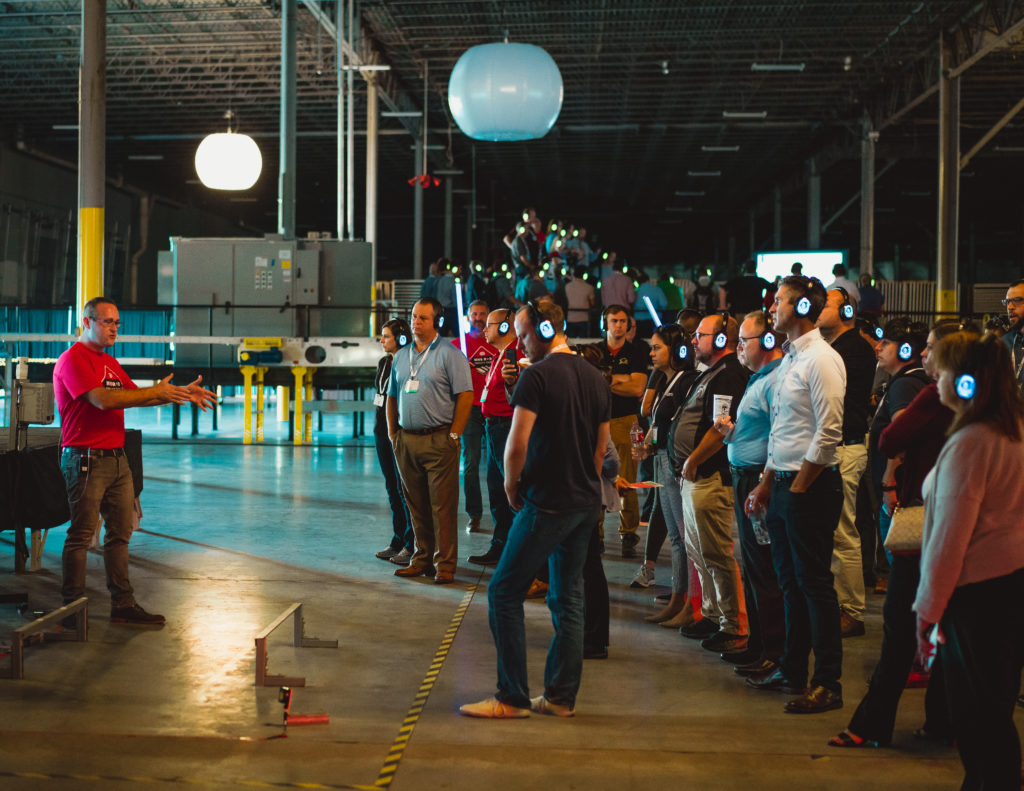
MHS, a single-source provider of material handling automation and software solutions, capped off the 2019 RIA Autonomous Mobile Robot Conference with a tour of its 260,000-square-feet research and development facility. The tour showcased the company’s growing portfolio of next-generation robotic innovations, designed to provide relief from labor challenges and boost productivity for distribution centers. Attendees viewed live demonstrations of: Robotic singulation, using proprietary vision technology, algorithms and end effector to pick individual items from bulk flow in preparation for sorter induction. Large bulk singulator, comprising several conveyor systems to produce consistent, single-file throughput. Autonomous mobile robot, automating the transportation of pallets and heavy loads quickly and efficiently, using advanced navigation to find the most efficient path. Robotic each picking, featuring a robotic arm and gripper on top of a mobile robot to move between pick locations, fully automating the process. “The growth of robotic technology from concept to viable, commercially mature solutions is happening at a faster pace than ever before,” says Brandon Coats, product manager, MHS. “The solutions on display bring together the latest proven robotic innovations to meet some of our customers’ most pressing challenges head on.” MHS solutions featuring mobile robotics come via an agreement with MiR, a Danish company that specializes in collaborative mobile robots.
Energy efficient, intelligent and gentle on resources: KHS to exhibit smart beverage filling systems
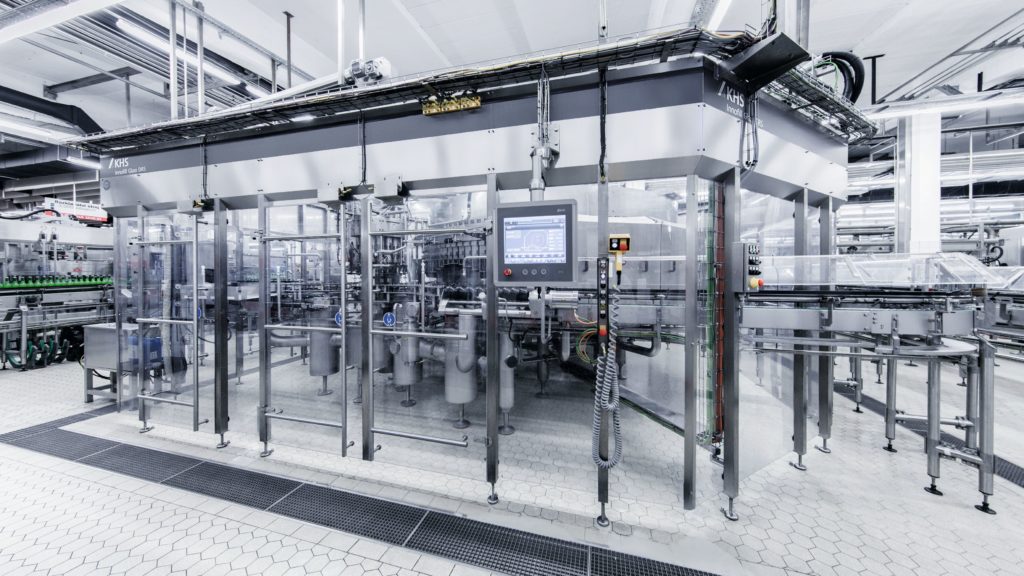
Smart systems which save energy and resources: from November 12 to 14, 2019, KHS is exhibiting intelligent beverage filling technologies at the BrauBeviale trade show in Nuremberg, Germany. One example of the above is the new high-performance KHS glass filler with a capacity of up to 80,000 bottles per hour. With it the German systems supplier is helping the beverage industry move towards more efficient, more sustainable and increasingly digitized beverage production. In November the international beverage industry will again meet in Nuremberg. At this year’s trade show KHS’ main focus will be on process efficiency, digitization and saving resources. “The entire production process is becoming increasingly smarter. As a trusted and reliable partner to the beverage industry we’re applying our extensive experience and line expertise to cater for this development,” says Dr. Johannes T. Grobe, CSO of the Dortmund machine and systems manufacturer. “At BrauBeviale we’re thus presenting intelligent technologies which will map out the direction KHS will take both now and in the future.” Considerable savings in energy and resources One example of this is the new generation of glass bottle fillers KHS will be showing to the public for the first time at the exhibition. With it the turnkey supplier is consistently advancing its aim of continuously reducing the amount of energy and resources consumed within the beverage industry. Among other features the filler has a unique ECO system and special evacuation and CO2 purging process for glass bottles. With this the system uses up to 50% less CO2 compared to conventional methods. KHS has also cut energy consumption by a maximum of 20% thanks to its optimized vacuum pump. “The protection of the environment is one of the determining issues of the moment. We thus offer our customers systems which specifically make their production lines sustainable and efficient,” explains Grobe. Smart KHS systems noticeably optimize production processes Here, an important role is played by smart engineering which noticeably simplifies, optimizes and automates production processes. To quote one example, a diagnostic assistance system monitors the entire filling process with regard to the evacuation and CO2 purging processes, for instance, to considerably minimize the amount of oxygen pickup. Broken bottles are also detected in all filling phases and the containers automatically channeled out of the system. “We’re constantly improving the efficiency of production processes. This in turn brings about a clear improvement in the line performance,” Grobe states. Sustainable in every respect In the future, too, one of KHS’ prime concerns is to significantly reduce our carbon footprint. Service plays a central role in the persistent pursuit of this goal. KHS enables its customers to operate systems for as long as possible and keep them in line with the latest technical, economic and ecological state of the art. Its bottle washing machine optimization program is exemplary in this respect. This aims to successively lower the amount of water and energy the bottle washers use. In this context the Dortmund engineering company provides various smart service packages from the capacity-dependent fresh water controller to weight-optimized bottle pocket carriers. “We take a holistic view of our customers’ production and maintenance processes. With our extensive service program, including line optimization measures to boost efficiency and throughput, together we find the best possible solution and in doing so also help protect the environment,” declares Grobe. KHS is exhibiting its plant engineering in Hall 8.
Selecting a Storage, Logistics or Manufacturing Solution for your facility
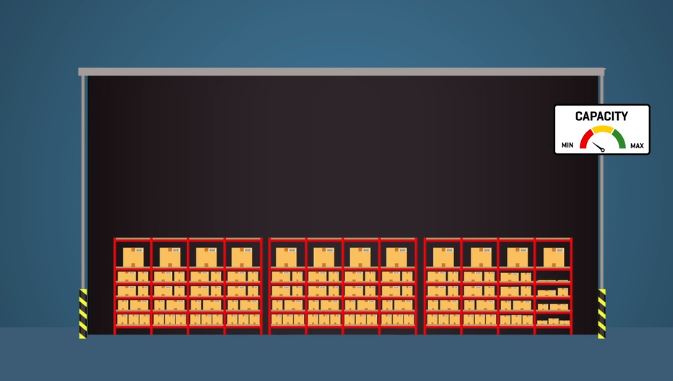
Selecting the right storage system can be a complicated process. Not only are there different options for every unique application, but regulations and compliance codes are changing every year. Your best resource is the Storage Manufacturer’s Association – visit mhi.org/sma to learn more Click here to view video.
Honeywell helps Apparel Logistics Group triple daily output from its e-commerce distribution center
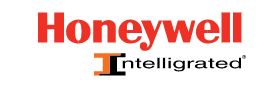
Honeywell has signed an agreement with retail supply chain services provider The Apparel Logistics Group to help the company expand the e-commerce order output at its distribution center in Dallas. Under the agreement, Honeywell Intelligrated will deliver automated material handling solutions to The Apparel Logistics Group, a leading provider of third-party logistics and order fulfillment services for apparel, footwear and accessories. Honeywell Intelligrated’s technology and technical support services will help the logistics provider expand its e-commerce parcel shipping capability, increase productivity at the shipping dock, ensure order accuracy and expand its value-added services capacity, which includes returned merchandise management and product customization. These material handling solutions and services will enable The Apparel Logistics Group to more than triple its daily e-commerce order output. “The third-party logistics (3PL) sector is experiencing unprecedented growth as more retailers require cost-effective order management, reverse logistics and product customization services,” said Pieter Krynauw, president, Honeywell Intelligrated. “In turn, 3PLs need to deploy automation solutions to help them ensure quality control, reduce risks associated with labor availability and deliver on their service-level agreements.” Located in Dallas to support fast shipping throughout the U.S., the 240,000-square-foot facility features an array of dedicated automation solutions including a high-volume sortation system and more than five miles of controlled conveyors. “To keep pace with growing consumer expectations, both traditional retailers and online-only e-tailers need to outsource their order fulfillment, returned merchandise management and product customization. In addition, available warehouse space in North America is at an all-time low,” said Aric Schwab, Senior Vice President, The Apparel Logistics Group. “With these new facility enhancements, we’re able to offer our customers increased volume, faster shipping and more value-added services.” Honeywell Intelligrated will install new material handling solutions to more efficiently move products through nutat The Apparel Logistics Group’s distribution center, which provides retailers with a one-day turnaround on e-commerce orders. In addition, Honeywell Intelligrated will implement and support the facility’s warehouse control system, which operates the production activities and equipment. This provides The Apparel Logistics Group with direct support from Honeywell Intelligrated’s world-class technical services center and 24/7 access to maintenance technicians to maximize facility uptime. Large retail brands and online-only retailers in the U.S. and Canada turn to The Apparel Logistics Group for warehousing, multi-channel order fulfillment and Foreign Trade Zone services to deliver products to distribution centers, stores or directly to individual consumers’ homes.nuts Honeywell Intelligrated is a leading provider of automation solutions for distribution and fulfillment applications with decades of experience helping 3PLs achieve maximum productivity and efficiency by transitioning from manual to automated processes. The Apparel Logistics Group provides multi-channel fulfillment and supply-chain services to clients in the apparel, footwear and accessories industry. The company is a business unit of The Apparel Limited (TAL), a global manufacturer of woven and knit apparel producing more than 50 million garments annually. Honeywell Safety and Productivity Solutions (SPS) provides products, software and connected solutions that improve productivity, workplace safety and asset performance for our customers across the globe. We deliver on this promise through industry-leading mobile devices, software, cloud technology and automation solutions, the broadest range of personal protective equipment and gas detection technology, and custom-engineered sensors, switches and controls.
Kaman Distribution sale to Littlejohn Company LLC is complete
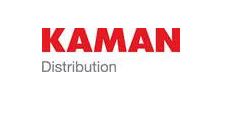
Kaman Distribution today announced the pending sale to affiliates of Littlejohn & Co., LLC (Littlejohn) has been finalized. Following the completion of the transaction, Kaman Distribution will continue to service customers under its three platforms; Automation, Fluid Power and Industrial Technologies. Kaman Distribution provides customers with premium products and integrated solutions through the utilization of its valued and experienced personnel; in conjunction with incorporating today’s most advanced technologies. “Kaman Distribution is looking forward to being a part of Littlejohn with their proven track record of building and growing businesses like ours,” said Al Lariviere, President of Kaman Distribution Group. “They are prepared to continue to invest in the business to accelerate our growth and further enhance KDG’s ability to support our customers. I am excited for the future of the business and the associated opportunities it will bring to our employees.” About Kaman Distribution Kaman Distribution is a leading distributor of more than six million items including electro-mechanical, bearings, power transmission, motion control and fluid power components, as well as automation and MRO supplies, to customers in virtually every industry. In addition, the business provides engineering, design and support for automation, electrical, linear, hydraulic and pneumatic systems and delivers belting and rubber fabrication, customized mechanical services, hose assemblies, repair, fluid analysis and motor management. With over 220 locations across the U.S. and Puerto Rico, Distribution’s 2,200 employees generated $1.1 billion in net revenue in 2018.