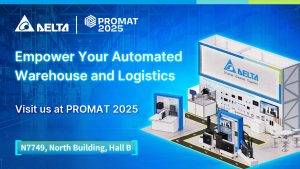
Delta’s Wireless Charging and Industrial Automation Solutions for Smart Warehouses at ProMat 2025
Delta attends ProMAT 2025 with its cutting-edge wireless charging and industrial automation solutions. These innovations, which are designed to boost
Delta attends ProMAT 2025 with its cutting-edge wireless charging and industrial automation solutions. These innovations, which are designed to boost
First solution of the cooperation with NVIDIA and Accenture demonstrates AI-powered industrial trucks and their digital twin. Rob Smith, CEO
Celebrate four decades of collaboration in Canada Since the 1980s, Arrow Speed Controls and Mitsubishi Electric Automation have delivered automation solutions
In this episode of The New Warehouse Podcast, Kevin sits down with Andre Luecht, Global Strategy Lead at Zebra Technologies;
Welcome to this episode of The New Warehouse Podcast featuring Jackie Wu, Founder and CEO of Corvus Robotics. Corvus Robotics
Users can query logistics operation data, create reports, and generate dashboards via chat. Requests such as releasing orders or unblocking
Smart solution for energy-efficient, high-precision panel bending with robotic automation Prima Power highlights its BCe Smart 2220 panel bending machine, designed to
Gorbel® is set to celebrate the 25th anniversary of its groundbreaking G-Force® Intelligent Lifting Device. This device marked a significant
AutoStore has just announced CarouselAI™, an AI-powered robotic piece-picking solution designed explicitly for AutoStore that brings the latest advancements in
Leading warehouse automation provider Brightpick now independent company with plans to expand using deal proceeds Photoneo Brightpick Group, a 3D
Permanent lubrication system reduces maintenance costs A large beverage producer in Mexico invested in an automated system for packing and
OSARO’s researchers have developed an innovative AI-powered technique that enables robots to accurately determine graspable object positions through physical interaction,
To strengthen market leadership and scale global growth Verity, an AI-powered mobile intelligence that enables complete warehouse operational visibility through
Attendees to learn how to enhance their operations at booth #S2303 Dematic, a global leader in supply chain automation, will
Welcome to another episode of The New Warehouse Podcast, where we dive into a unique solution for evaluating warehouse employee
SUN to Serve as Exclusive U.S. and Canada Agent and Distributor for Kolbus Machinery and Aftermarket Support SUN Automation Group,
The world of warehouse automation is evolving rapidly, but one persistent challenge remains: transparency. Many businesses looking to implement automation
Signode, a manufacturer of a broad range of transit packaging equipment, tools, consumables, automation, and support solutions, is highlighting its
Giraffe raises the Brightpick solution to new heights, reaching 20 feet (6 meters) to maximize warehouse density E-commerce leader The
Muratec USA & Cimcorp NA: 100 years of innovation, one transformative experience ProMat 2025 is just around the corner. Did