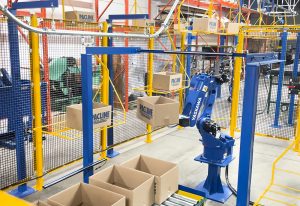
Pacline Conveyors to showcase robotic empty carton handling system at ProMat 2025
Pacline Conveyors has announced its participation in the highly anticipated ProMat 2025 trade show, taking place March 17-20 in Chicago,
Pacline Conveyors has announced its participation in the highly anticipated ProMat 2025 trade show, taking place March 17-20 in Chicago,
New 28,000-square-foot building will focus on machine and system integration activities for various sectors. Norwalt Automation Group has moved to a
This episode of The New Warehouse Podcast features Anthony Jules, Co-Founder and CEO of Robust AI. Anthony shares insights into
Initiative aims for “Widely Recyclable Status” for polystyrene The Plastics Industry Association (PLASTICS) announced the formation of the Polystyrene Recycling Alliance
Two brands, one vision: Revolutionizing logistics automation in North America at ProMat 2025 Murata Machinery USA, Inc. and Cimcorp are set to
Strategic investment aims to accelerate innovation across LG’s commercial, home, and industrial robot solutions LG Electronics has taken a significant
In this episode of The New Warehouse Podcast, Nick Saunders, CEO and co-founder of Hummingbird Systems, discusses a groundbreaking approach
KHS technology boosts value creation in the production process at Schweppes Zimbabwe Limited A big step towards cutting greenhouse gas
Showcases advancements in eco-friendly bagging PAC Machinery will debut several cutting-edge automatic bagging systems at the ProMat Show, including two
Today’s episode of The New Warehouse Podcast features returning guest Mike Myers, now the founder of Lully AI. A seasoned
Helping businesses make smarter decisions about automation Kardex debuted its latest tool – the StoreX Calculator – at the National Retail
ROYPOW has announced the launch of a new fully automated forklift battery module production line, further enhancing its manufacturing capabilities.
In a world that is constantly evolving, technology has taken center stage, changing industries at a pace few could have
TAB offers logos, web addresses, corporate colors on line of stretch wrap Orbital wrapper manufacturer TAB Industries, LLC, has introduced
In this episode of The New Warehouse Podcast, Marin Tchakarov, CEO of Fox Robotics, delves into the groundbreaking advancements his
As gigafactories and recycling plants scale to meet rising demands, the need for innovative solutions that address both safety and
Locus Robotics Warehouse Automation Technology Drives Productivity Gains at GEODIS’ Carlisle, Pa., Location Locus Robotics has announced that its valued
Addressing labor challenges and enhancing operational efficiency are crucial priorities in manufacturing, warehousing, and logistics. Automating the palletized material workflow
The Intelligent Logistics Systems Lab will develop two key areas of research to boost warehouse robot productivity and optimize order
AMR Innovator Excited to Contribute to Industry Advancement Initiatives Seegrid Corporation has announced its membership in the Open Source Robotics