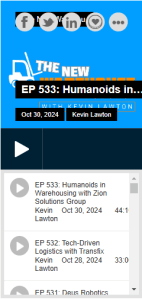
Hellmann advances innovation with AI-RobotX MEA and Geekplus to enhance eCommerce fulfillment operations
Hellmann Worldwide Logistics continues its journey of innovation with the successful implementation of Geekplus robotics automated storage solutions at its