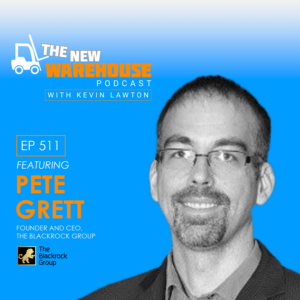
Episode 511: Harnessing AI for Warehouse Optimization
Today’s episode of The New Warehouse Podcast delves into the topic of AI for warehouse optimization with Pete Grett, founder
Today’s episode of The New Warehouse Podcast delves into the topic of AI for warehouse optimization with Pete Grett, founder
Next Generation Manufacturing Canada (NGen) awards Nano One and Worley Chemetics C$2.8 million in non-dilutive non-repayable funding through the Electric
Tele Radio has reminded the industry of the benefits of two handheld radio remote controls specifically for the demands of
SUN Automation Group (SUN) will attend SuperCorrExpo at Booth 1731 at the Orange County Convention Center in Orlando, Florida from
NextGen Supply Chain Conference Awards Recognize Companies Shaping Tomorrow’s Supply Chains AutoScheduler.AI, an innovative Warehouse Orchestration Platform and WMS accelerator,
12 Students Awarded Dematic FIRST® Scholarships to Pursue STEM Education Dematic has announced the winners of the 2024 Dematic FIRST®
With systems integration partner KPI Solutions, Kenco’s new automated storage and retrieval system will shorten click-to-delivery times for the 3PL’s
Cimcorp’s automation boosts storage capacity and enhances operational efficiency, helping the Finnish brewery handle growing production volumes and seasonal demands
Led by Fonds de Solidarité FTQ, the investment will accelerate the company’s growth, expand its global reach, and enhance its
PAC Machinery has announced the new Rollbag® R3200 Fulfillment Paper Automatic Bagger. This innovative model, also available in an XL
The sustainable accessories manufacturer expects to double its sales amidst the expansion of an industry set to reach $500 billion
Customizable Signal Fits a Range of Applications from Control Cabinets to Autonomous Vehicles Pfannenberg, a manufacturer of thermal management and
In this engaging session from Momentum 2024, I was joined by a panel consisting of Adam Kline and Matt Dermody from
Seasoned Sales Executive takes the helm to drive next level growth. ARI Phoenix, Inc. (ARI) is pleased to announce that
Visit Booth #215 to connect with a Wauseon expert and find your next manufacturing solution Wauseon Machine, Inc. (WM) announced
In the latest episode of The New Warehouse Podcast, Kevin sits down with Radu Palamariu, the Managing Director of Alcott
The Seeq platform will be leveraged to maximize production and enhance efficiency across Equinor’s global assets. Seeq and Equinor have announced
High-density system delivers speed and integration flexibility for e-commerce warehouses, retail and grocery fulfillment Urbx launches its robotic inventory storage and
The award recognizes top companies in the Greater Cincinnati region based on employee feedback. Trew, LLC has been recognized as
Motion’s automation market to expand in the Mid-Atlantic Motion Industries, Inc. has signed a definitive purchase agreement to acquire Allied