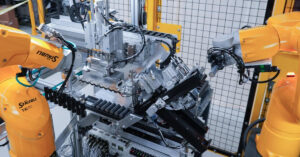
Wauseon Machine to showcase integrated automation solutions at Automate 2024
Visit Booth #1257 to learn more about robotic and custom-tailored automation solutions Wauseon Machine, Inc. (WM) has announced its participation
Visit Booth #1257 to learn more about robotic and custom-tailored automation solutions Wauseon Machine, Inc. (WM) has announced its participation
Product bundle combines trailblazing Pick-by-Voice solution with best of breed wearable scanners ProGlove is joining forces with topsystem, a division
XR2 sets a new benchmark in RFID technology with unmatched speed, accuracy and affordability Janam Technologies, a provider of rugged
PosiCharge, the industrial charging division of Webasto Charging Systems Inc., a subsidiary of Webasto Group, its divestment of the charging business to
OSR Shuttles Technology released for sale across North American Cold Chain KNAPP has announced that they will commence the sale and
Veteran leader provides extensive international legal and management expertise Fortifi Food Processing Solutions (“Fortifi”) has appointed Robert Gibson as General
TAB Wrapper Tornado option extends life of cutting system A new Thermal Cutting System from orbital wrapper manufacturer TAB Industries,
TerraSource Global has announced the election of CEO Kevin Hambrice to the Board of Directors of the Conveyor Equipment Manufacturers Association
Automation Guidance, a service proven to save customers on average more than $2.5m annually, joins the Kenco MHE Solutions™ portfolio Kenco
The Movu 3D shuttle system “escala” has been awarded “Product of the Year 2024” by the readers of the logistics
Dorner and Garvey are well-established brands with decades of proven success. But now, they are combining their strengths to write
Kardex appeared at MODEX 2024 where it unveiled its FulfillX solution, specially designed by expert automation engineers to maximize the capabilities
In this episode of The New Warehouse Podcast, Lee Rector, CEO of Embassy Data Logistics, joins Kevin for an informative
Delta, a power management and provider of IoT-based smart green solutions, is showcasing high-efficiency wireless charging systems and smart industrial
Discover end-to-endless solutions to set the tempo of an optimized warehouse floor The Raymond Corporation continues to build on its
Mobile robots and software integration automate labor-intensive sorter destination changeover tasks in eCommerce and sortation facilities FORTNA, an automation and
Attendees can experience the ELOshield forklift safety and pedestrian detection system, the new ELOshield module for automated guided vehicles/autonomous mobile
Slamcore launches Visual Intelligence Localization solution for manually driven intralogistics vehicles at Modex Slamcore Aware combines the power of
Rockwell Automation, Inc. plans to expand its presence at MODEX 2024 in Atlanta, GA., March 11-14. The company will showcase the
Signode, a manufacturer of a broad range of automated transit packaging equipment, tools, consumables, and automation solutions, has announced the