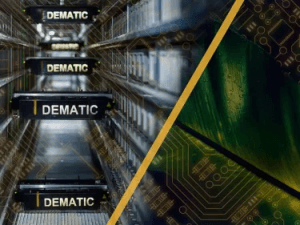
Dematic to feature innovative supply chain solutions at ProMat 2025
Attendees to learn how to enhance their operations at booth #S2303 Dematic, a global leader in supply chain automation, will
Attendees to learn how to enhance their operations at booth #S2303 Dematic, a global leader in supply chain automation, will
MAHLE Aftermarket turned to Kardex for an automated storage and retrieval solution following a shift in orders from large pallets
NextGen Supply Chain Conference Awards Recognize Companies Shaping Tomorrow’s Supply Chains AutoScheduler.AI, an innovative Warehouse Orchestration Platform and WMS accelerator,
Today’s episode of The New Warehouse Podcast features Anna Farberov, the General Manager at PepsiCo Labs. Anna is at the
Kardex appeared at MODEX 2024 where it unveiled its FulfillX solution, specially designed by expert automation engineers to maximize the capabilities
Process Safety Industry Leader Chet Barton, P.E. of Hargrove Controls & Automation achieves a prestigious Functional Safety (FS) Expert Certificate
CKF Systems are delighted to have started the installation of another Robotic Central Palletising system for a world leading snack
AutoScheduler.AI, an innovative Warehouse Management System (WMS) accelerator, announces that its warehouse resource planning and optimization platform, AutoScheduler, is now available
Hai Robotics US, the recent winner of the MHI Innovation Award for Best Innovation of an Existing Product, is making
PeakLogix announced that Pat Peplowski has joined the company as VP of Business Development. Peplowski is a data-driven leader who
The new Kardex Compact Buffer utilizes warehouse space from top to bottom and from side to side for long-term partner
Joining me for this week’s podcast from the booth at MODEX 2022 is Mark Hasler, Business Development Manager at Autostore.
In keeping with the belief to deliver adaptive, flexible, and portable solutions, Tompkins Robotics introduces the new tSort3D. tSort3D is
Kardex, a world manufacturer of automated storage and retrieval systems (ASRS) will display solutions digitally at MODEX 2022 for a
Effective January 13, 2022, Darein Gandall has been named CEO and Chairman of the Board of Cisco-Eagle, a Dallas-based material
Cisco-Eagle has promoted Bryan Gauger to Vice President of Systems Integration according to Cisco-Eagle President Darein Gandall. Gauger brings decades
Surgere, a supply chain solutions company brings visibility to parts inside trailers making the supply chain more efficient by verifying
Company’s history shows a culture of innovation and commitment to quality This year marks a major milestone for JLS Automation.
Kardex Remstar is improving eCommerce and distribution operations with new intralogistics solutions. On display will be a new unique solution,
Selecting the right storage system can be a complicated process. Not only are there different options for every unique application,