Wynright
Viastore Systems
viastore systems Inc.
FMC Corp. Automated Matl. Hndling. Systems
Equipco Corp.
Engineered Storage Solutions
Egemin Automation, Inc.
JLS Automation celebrates 65th Anniversary
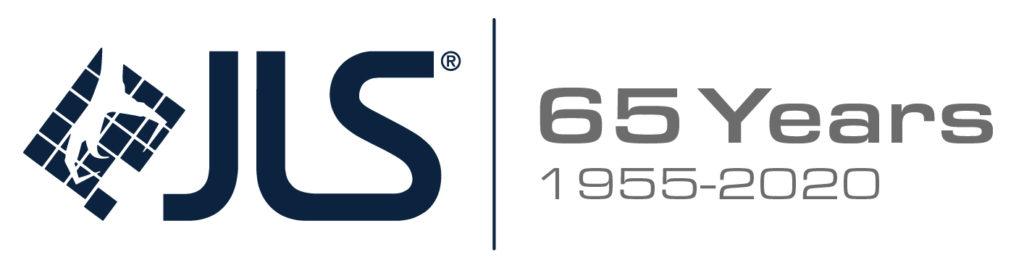
Company’s history shows a culture of innovation and commitment to quality This year marks a major milestone for JLS Automation. The company is celebrating its 65th anniversary and its long-standing commitment to revolutionizing industrial automation with its robotic packaging systems. JLS Automation started as JL Souser & Associates, a manufacturers’ representative firm that sold power transmission equipment in 1955. Since taking over the company, current president and CEO Craig Souser has transformed the company into what it is today—a best-in-class, trusted supplier of hygienic robotic packaging solutions for food handling. “Throughout our 65-year history, JLS has evolved to meet the needs of our customers every step of the way. We have grown with the food packaging industry, and will continue to innovate as the market demands new standards in quality, sanitation, and technical expertise,” said Souser. When he first took the lead of JLS, Souser expanded the product range to include variable frequency drives and started providing application engineering assistance. In 1991, JLS provided systems engineering and shortly after introduced a field service offering to support its engineered systems. In 1993, the company entered the packaging automation segment. Since it’s custom vision-guided primary and secondary robotic packaging systems, high-speed leak detection systems and end-of-arm tooling have been awarded several patents. Just this year, JLS launched its patent-pending Peregrine™, a vision-guided robotic cartoning system that uses a proprietary positive carton transport (PCT) system and game-changing TRAK technology. Also this year, the company developed a high-payload bulk product handling solution for transporting large cuts of protein. Both solutions were the result of customer demand and JLS’s commitment to innovative solutions for hygienic packaging applications. “We are honored that our customers have relied on our commitment to quality equipment and dedication to providing exceptional solutions and service for 65 years,” said Souser. “We take pride in providing leading-edge robotic solutions that in turn help them to work more safely, efficiently and hygienically. JLS is what it is today because of the continued support of our customers along with our innovative culture and talented employees.”
Kardex Remstar displays new Intralogistics Solutions at MODEX 2020
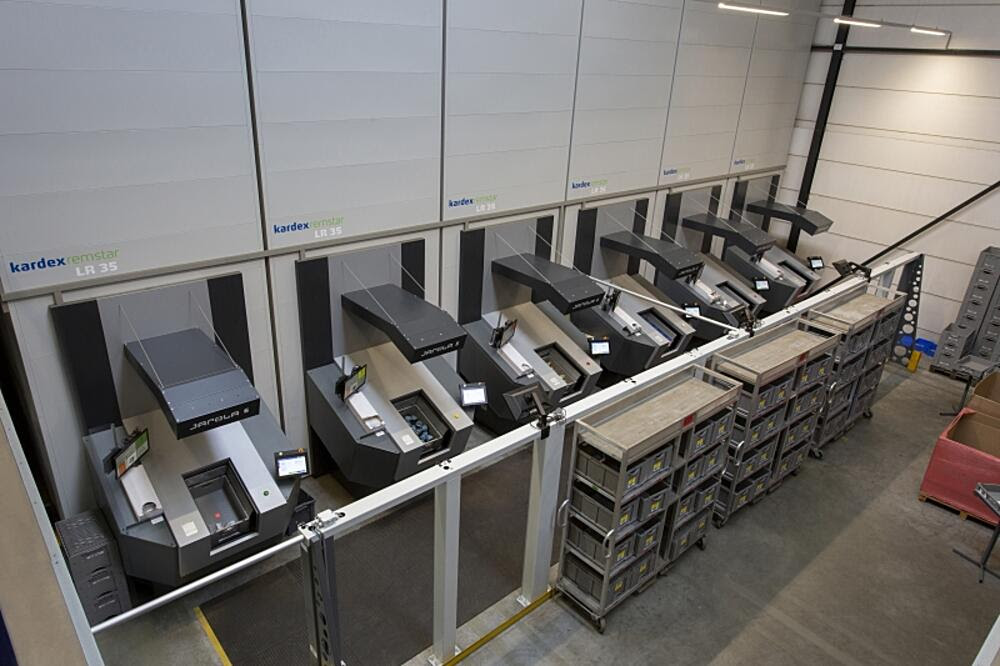
Kardex Remstar is improving eCommerce and distribution operations with new intralogistics solutions. On display will be a new unique solution, FramePick. With this efficient, dynamic and flexible system for fast order fulfillment, companies can drastically reduce the turnaround time of orders. The LR 35 Vertical Buffer Module (VBM) with FramePick and the Shuttle XP Vertical Lift Module (VLM) will be at MODEX in Atlanta, GA March 9-12, 2020 in booth 8811. The new FramePick solution consists of the LR 35 in combination with order picking trolleys for picking articles. These order picking trolleys are simply placed behind a Put Frame with put-to-light displays. The operator can connect the customer order bins on the trolley to the displays with a simple scan. When one of the LR 35 VBMs presents a new storage bin, the displays show how many items should be placed in which bins. When all orders are complete, the trolley with the full bins can be easily transported to the packaging area. And the new trolley with empty bins takes over the position in the Put Frame. This new solution can reduce walking distances by up to 65% and reduce floor space by 80%. In addition to the LR 35, the Shuttle XP integrated with pick to light technology and the new Power Pick OnBoard control will also be in the booth. By utilizing the vertical space from floor to ceiling, vertical storage systems eliminate wasted space commonly found in shelving systems to recover up to 85% floor space. Allowing organizations to create floor space for additional manufacturing or other revenue generating activities can be easily cost justified. Lastly, there will be live demonstrations of the Remote Support platform. There are two features included; first, Remote Assistance, which manages remote diagnostics, allowing for simple maintenance requests to be performed remotely instead of onsite reducing downtime. Secondly, Remote Analytics, which gives users access to machine data anywhere via a Web Browser. This analysis tool guarantees a high level of process reliability for storage unit operations. From vertical carousels to horizontal carousels, software to pick to light technology, Kardex Remstar offers a range of solutions to build your future. In addition, the various life cycle services offered round out the Kardex Remstar product offerings.
Selecting a Storage, Logistics or Manufacturing Solution for your facility
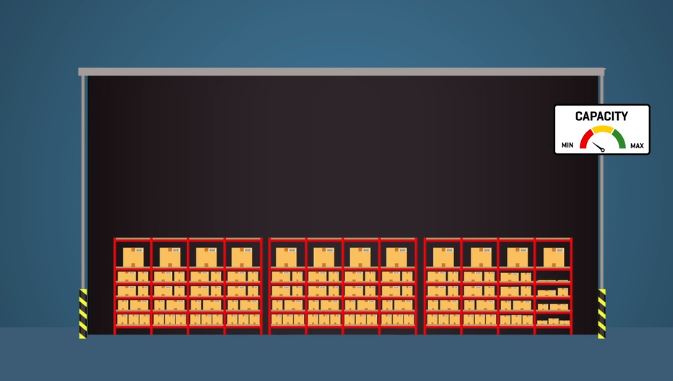
Selecting the right storage system can be a complicated process. Not only are there different options for every unique application, but regulations and compliance codes are changing every year. Your best resource is the Storage Manufacturer’s Association – visit mhi.org/sma to learn more Click here to view video.
Dematic announces strategic partnership with OPEX
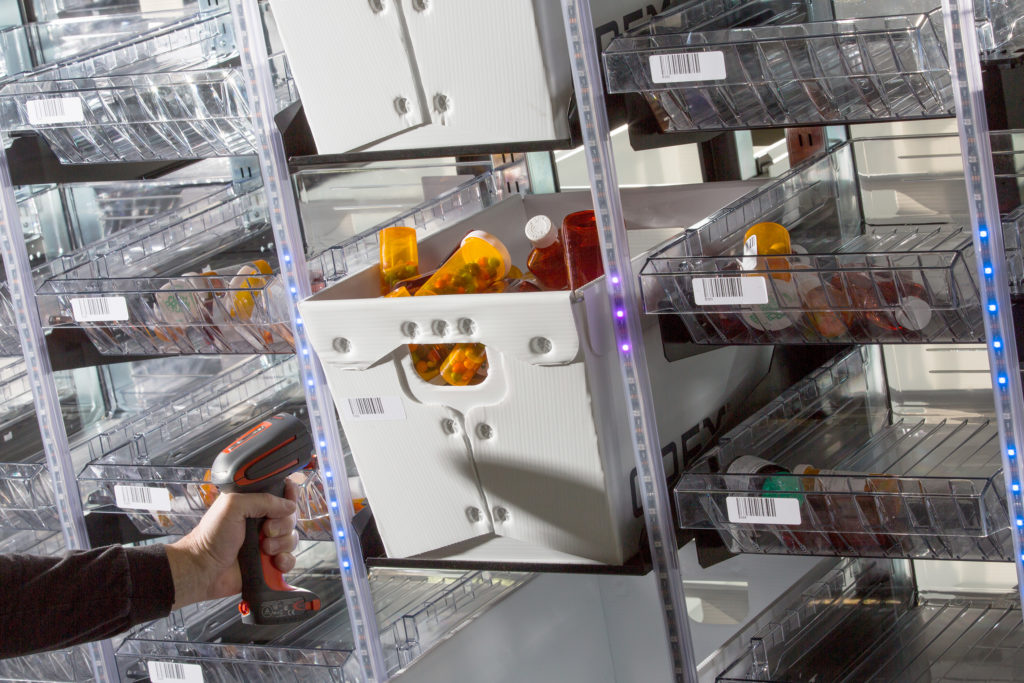
Dematic has announced a partnership agreement with OPEX Corporation that enables Dematic to act as an integrator of Sure Sort™, a small-item sorting system. The agreement expands the omnichannel order fulfillment offering of Dematic and provides customers with more options that bring productivity and efficiency to item order consolidation. As a system integrator/solution provider, Dematic will apply and implement Sure Sort as a subsystem within an overall Dematic system. For OPEX, the agreement will allow more markets and customers to realize the benefits of the Sure Sort solution. The agreement is for systems implemented by Dematic in North America. Sure Sort is a robotic small-item sorter that functions as an automated order consolidation method for batch picked items. The Sure Sort solution is often required for e-commerce order fulfillment and retail store replenishment applications. Sure Sort maximizes efficiency and accuracy during the order consolidation process while minimizing order processing time, labor required and the amount of floor space needed in the distribution center. Dematic iQ Optimize Warehouse Execution System (WES) manages all functional areas of the order fulfillment system, including small-item piece picking and the Sure Sort. This powerful combination of Dematic WES software and Sure Sort automation enables all the operational flexibility necessary to support the high expectations of omnichannel distribution. With Sure Sort in the solution offering, Dematic is further enabled to provide a holistic, integrated system that harmonizes information and material flow from receiving to shipping. “The Dematic suite of modular and standardized solutions is comprehensive — adding Sure Sort to the mix enables users to obtain the ideal small-item piece picking solution,” according to Mike Khodl, Vice President of Global Solutions for Dematic. “The ability to design and implement a wide variety of pre-engineered, standardized system configurations is critical to effectively accommodate the growing demands of omnichannel distribution in this age of acceleration.” “The partnership between OPEX and Dematic leverages both companies’ industry expertise and positions Sure Sort in front of existing Dematic customers and prospective customers,” said Jeff Hedges, President of OPEX Warehouse Automation. “The labor shortage continues to impact warehouse and distribution center operations, and Sure Sort removes the need for additional operators and manually operated put walls. Sure Sort offers an increased number of sort locations without taking up valuable space inside the warehouse.”
SupplyPoint solutions help plants and warehouses take control of handheld assets
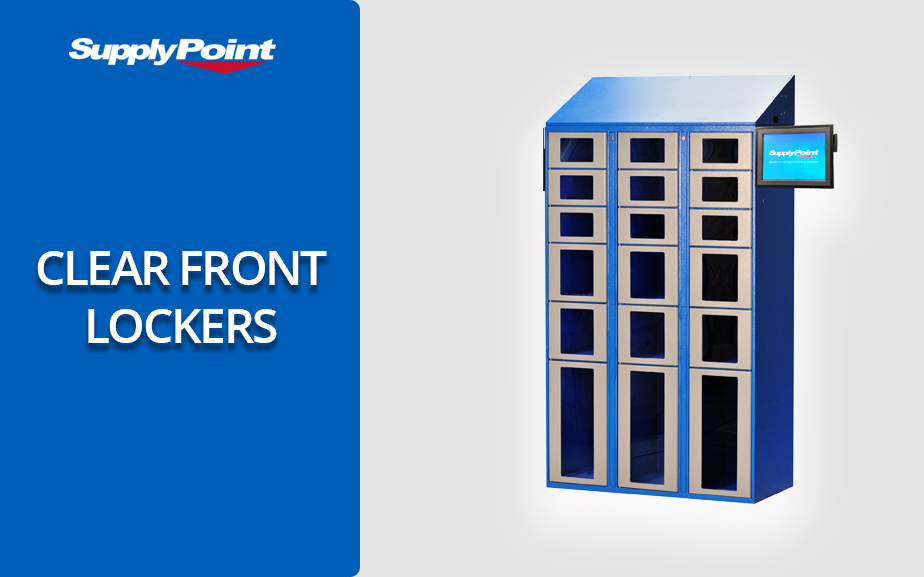
Innovative RotoPoint carousels and Clear Front Locker systems by SupplyPoint ensure that factories and warehouses can achieve both security and user-friendly access to valuable assets such as handheld scanners and mobile devices Inventory and asset management is made easy, reliable and cost effective by removing the worry and cost of important devices becoming misplaced or accidentally damaged. RotoPoint provides a scalable and cost-effective inventory carousel solution for the secure management of a wide range of handheld assets. Running from a standard, single-phase 120V supply, the high capacity of the unit makes it ideal for the management and control of scanners and mobile devices. Available in three sizes offering up to 468 locations with 24/7 availability, the system can be easily reconfigured in line with individual requirements. For instance, every other column divider in RotoPoint is removable, allowing each compartment to be made twice the width to suit larger scanning devices. Access to each compartment is controlled for maximum security, with all transactions logged to a specific user and cost center, thus providing full and accurate audit and reporting capabilities. Importantly, the majority of compartments in RotoPoint are hidden from view behind sturdy sliding doors, while contents can be randomly distributed around the carousel, further reducing the risk of unauthorized removal. SupplyPoint´s Clear Front Locker provides an economic inventory access solution. The system is ideal for larger handheld scanners or mobile devices, with each locker consisting of three vertical stacks which can be configured using three, six or nine electronically controlled clear-front cupboards. These functional and intelligent powered cupboards provide recharging and serial/asset tag tracking via scan in/scan out capability. Convenience, simplicity and security are at the heart of Clear Front Locker, with SupplyPoint software providing a complete audit trail that allows management traceability to know who, what, where and why, with regards to usage. Access to contents is restricted by the use of username, password, biometric identification, card readers, or a combination of these options. The door locks are of a high strength and cannot be forced open in normal or aggressive use. Video recording of each transaction is also an option. John Hook, Business Development Manager Americas at SupplyPoint, says: »When it comes to asset management, handheld scanners and mobile devices can easily be misplaced or accidentally damaged, thereby increasing cost and decreasing productivity. Solutions such as RotoPoint and Clear Front Locker present secure, cost-effective ways of protecting assets and increasing accountability, ultimately reducing replacement costs, damage and downtime looking for devices. These systems can also be managed strategically using our WebSync remote cloud-based service for data management and reporting with real-time visibility.