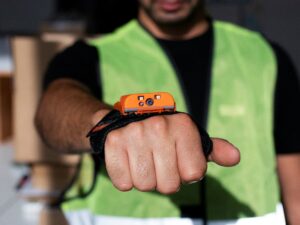
ProGlove and BlueStar partner to expand safe and efficient operations in global warehouses
ProGlove, a company that specializes in smart scanning, has partnered with BlueStar, a global distributor of B2B electronics devices. This
ProGlove, a company that specializes in smart scanning, has partnered with BlueStar, a global distributor of B2B electronics devices. This
Encryption solution safeguards against unapproved internal or external personnel accessing critical or proprietary information. Schreiner Group, Schreiner PrinTrust, and Schreiner
Duravant Establishes Entity in China and Appoints Executive to Lead Local Growth Strategies and Infrastructure Expansion Duravant LLC has announced
Cimcorp has announced its VP of Operations, Anne Happonen, has been named to the “2024 Women in Supply Chain” list
Previously known as the TTL®700 Series, DuraChem labels offer chemical, solvent, abrasion, and smudge resistance for both indoor and outdoor
In this episode of The New Warehouse Podcast, Kevin welcomes Justin Newell, CEO of INFORM, a company with over 55
Today, we’re diving into a fascinating discussion from the New Warehouse Podcast, recorded live at the WERC 2024 conference in
SupplyOne, Inc., the largest independent supplier of custom corrugated and other value-added packaging products, equipment, and services in North America,
Barcoding, Inc. (“Barcoding”), a supply chain automation and innovation company, together with Graham Partners, has announced that an affiliate of
H2 Clipper, Inc. (“H2C”), an aerospace and alternative energy company developing uniquely capable hydrogen-powered dirigibles, has announced that it was
This episode of The New Warehouse Podcast features Jerry Abiog, CEO of Standard Insights, discussing the pivotal role of AI
AGILOX North America has announced its participation in the upcoming MODEX 2024 in Atlanta Booth C7492. The company will exhibit
IDENTCO, a manufacturer of high-performance labeling solutions for the power equipment, electronics, transportation, and general industrial sector, has hired longtime
Industrial Labelling Systems (ILS) has marked its tenth year as the longstanding distributor of Evolabel™ products in the UK and
IDENTCO, a manufacturer of high-performance labeling solutions for the power equipment, electronics, transportation and general industrial sectors will feature its
Kyle Bermel adds to role as Metalcraft president; global ID solutions company CEO to become board chairman Metalcraft announced a
Ideal for applying self-laminating & flag labels to wires, cables & harnesses, company’s durable VortexID can handle up to 20
Welcome to a new episode of The New Warehouse Podcast! In today’s episode, Cliff Hardesty, the Marketing Director at Barcode
Executive brings three decades of automotive, electronics & industrial expertise, and leadership to prominent labeling solutions provider IDENTCO, a manufacturer
Barcoding, Inc., the provider of efficiency, accuracy, and connectivity, announces today the hiring of Michael Tassinari as the firm’s new Chief