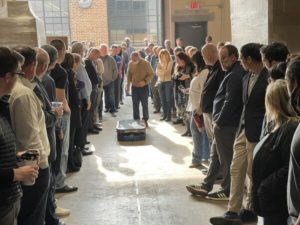
Barcoding Inc. has acquired FRED Automation Inc.
Barcoding, Inc., the provider of supply chain efficiency, accuracy, and connectivity, announced its acquisition of FRED Automation, Inc., an automated guided
Barcoding, Inc., the provider of supply chain efficiency, accuracy, and connectivity, announced its acquisition of FRED Automation, Inc., an automated guided
On this episode, I was joined by the CEO of Coros, Martin Hitch. Coros is bringing visibility to the supply
On this episode, I was joined by Jeff Lem of Portable Intelligence who I recently shared a panel with for Sam Gupta’s
Loftware, Inc., has announced a brand refresh, solidifying the unification of Loftware and Nicelabel into one integrated Loftware global brand.
Softeon, a global supply chain software provider with the industry’s best track record of customer success, has identified a number
More than 1 in 4 manufacturers report over a quarter of products were mislabeled More than three-quarters (76%) of IT directors
More than 66% of US manufacturers report most or all of their IT infrastructures is now in the cloud Nearly
On this episode, I was joined by Avery Dennison’s Vice President of Identification Solutions, Ryan Yost. We discussed Avery Dennison’s
US manufacturers lose more than $1.17M each year on average US manufacturers on average incur losses of around $1,174,000 per year
Products are easy to install and configure, and add safety and convenience in heavy industry, material handling, gas detection &
In this episode, I was joined by Takshay Aggarwal of IBM to discuss barcodes and their evolution. IBM covers a
Bring together 60 years of expertise to deliver customers and partners an expanded choice of solutions and enhanced capabilities Loftware,
The new version of the 3D printing Software 4D_Additive uses artificial intelligence algorithms to achieve an optimal heat distribution. For
2019.3 version also features seamless integrations with Workday and SAP NiceLabel, a global developer of label design software and label
Heatwave Flag and Heatwave Tough offer the automotive and other industries two new heat resistant UHF RFID tags that can
Feeds labelers and metal detectors with room to grow Multi-Conveyor recently built multiple sanitary, precision timed, semi-automatic hand pack conveyor
Customer-Driven LDLA-500-V2® Equipped with Improved Features and Robust Technology Enhancements Signode, a manufacturer of a broad spectrum of packaging consumables,
Empowers resellers to keep customers operating remotely and securely NiceLabel, a global developer of label design software and label management systems,
Episode 59 – Barcoding at MODEX 2020 In this episode, I am joined by Peter Zalinski of Barcoding, Inc in
DataMan 475V ensures quality compliance for every code without slowing down production Cognex Corporation, a provider in industrial machine vision,