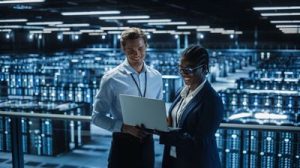
Exide Technologies to present latest energy storage solutions for data center applications at Data Centre World Frankfurt
Exide to exhibit at Data Centre World Frankfurt on 4th and 5th June Comprehensive energy storage solutions and
Exide to exhibit at Data Centre World Frankfurt on 4th and 5th June Comprehensive energy storage solutions and
EnerSys is one of the world’s leading manufacturers and providers of material handling, automation, and fleet solutions to provide Fleet,
That lithium battery powering your equipment seems simple, right? Until it reaches its end. Tossing it isn’t just careless; it’s
Cimcorp has announced its entry into the electric vehicle (EV) battery industry with its end-to-end automated material handling solution for
Ampure is set to attend the 2025 EV Charging Summit & Expo, the largest infrastructure event for transportation electrification in
Nano One® Materials Corp. has announced updates to its senior technology leadership team. After nearly a decade of guiding Nano
Green Cubes Technology has announced the launch of its latest Lithium Iron Phosphate (LFP) battery designed specifically for Material Handling
Ampure, an electric vehicle (EV) and industrial charging solutions company, has announced the appointment of Manoj Karwa as its Chief
EnerSys, an in stored energy solutions for industrial applications, will preview their new NexSys™ BESS energy storage system and Synova™
IFS, a provider of enterprise cloud and Industrial AI software, has appointed Matt Breslin president of North America. Breslin joins
Minit Charger announces four new charging solutions powered by Silicon Carbide (SiC) technology, designed to transform electric fleet operations across
Powering equipment is a key component of any material handling organization, and batteries’ role in the industry continues to evolve.
New service will deliver transformative performance for battery systems by providing access to Brill Power’s Innovative BMS+ Power Conversion hardware,
ROYPOW has announced the launch of a new fully automated forklift battery module production line, further enhancing its manufacturing capabilities.
Minit Charger announced four new charging solutions powered by Silicon Carbide (SiC) technology, designed to transform electric fleet operations across
When it comes to securing your products for shipment, selecting the right strapping materials is critical. This decision impacts not
Nano One® Materials Corp. has announced the allowance and/or issuance of 7 new patents to its portfolio, bringing its 2024
Bluewater Battery Logistics, a provider of battery lifecycle management, has announced an official partnership with HazMat Consulting. Bluewater is helping
Navigating the world of battery transportation can feel like trying to solve a puzzle with pieces that don’t seem to
Bluewater Battery Logistics has announced that Max Khabur has joined the team as the Director of Marketing. With extensive expertise