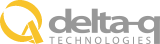
Delta-Q Technologies ships its four millionth battery charger
The milestone represents a carbon emissions reduction of four million metric tons since the company’s founding Delta-Q Technologies (Delta-Q), a
The milestone represents a carbon emissions reduction of four million metric tons since the company’s founding Delta-Q Technologies (Delta-Q), a
UgoWork™, a Canadian manufacturer of lithium-ion battery solutions for industrial vehicles, just announced that it has received $2 million in
As the weather warms, the new 48V lithium battery offers forklift dealers and warehouse owners the ability to power multiple
The company, a partnership between KION GROUP AG and BMZ Holding GmbH, produces lithium-ion batteries for industrial trucks at its
“Lithium batteries made it possible to switch [the company’s forklift fleet] to electric power from propane. Electric [lead-acid] batteries simply
BSLBATT battery is a fast-paced, high-growth (200% YoY ) hi-tech company that is leading the adoption of lithium-ion technology solutions.
UgoWork™, a Canadian lithium-ion battery manufacturer specializing in industrial vehicles and the material handling industry, has announced it has received
In this episode, I was joined by the COO of Concentric, John Winter, at MODEX 2022. Concentric focuses on bringing
OneCharge Inc., a provider of lithium motive batteries for the material handling industry, and Combilift USA, an innovative global manufacturer
NexSys® PURE Thin Plate Pure Lead (TPPL) batteries are helping the company cut carbon dioxide (CO2) emissions and water consumption EnerSys®,
Say “so long” to extension cords Newcastle Systems, a provider of mobile-powered carts designed to make warehouses, manufacturing facilities, and
UgoWork™, a Canadian energy solutions provider specialized in lithium-ion batteries for industrial trucks, today announced it will be featuring its
Chris Wayment, EnerSys® Field Sales Enablement Manager, and NexSys® Battery Specialist, to deliver an educational seminar on Monday, March 28th at
Company to launch Sunlight ElectroLiFe, showcase innovative BMS system KnoWi, and portfolio of lithium-ion and lead-acid products for US market at booth #B7605 during
Green Cubes Technology (Green Cubes) introduces the Lithium SAFEFlex Chargers to complement its market-leading Lithium SAFEFlex Batteries. Green Cubes is
EnerSys®, a global provider in stored energy solutions for industrial applications, will feature its family of virtually maintenance-free NexSys® battery
Flow-Rite has fortified its marketing efforts by filling two newly created positions. Justin McQueen joins the company as product marketing
UgoWork™, a Canadian energy solutions provider specialized in lithium-ion batteries for industrial trucks, announced that its 36V and 48V lithium-ion
EnerSys®, the global provider in stored energy solutions for industrial applications, is taking industrial, electric-powered vehicle safety to the next
Stafl Systems, Idneo, BSLBATT Battery, and American Battery Solutions join Delta-Q Technologies’ compatibility program to facilitate innovation and collaboration among the