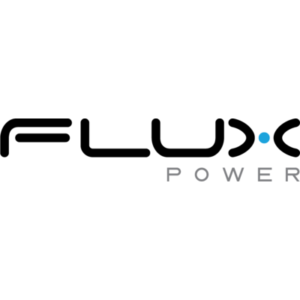
Flux Power’s FY 2021 Revenue increased by 56% to $26.3M; Gross Margins improved to 22.1%
Flux Power Holdings, Inc., a developer of advanced lithium-ion battery packs for commercial and industrial equipment, today reported financial results for
Flux Power Holdings, Inc., a developer of advanced lithium-ion battery packs for commercial and industrial equipment, today reported financial results for
Combilift is revolutionizing the way companies handle and store goods. March Huang, the Senior Sales Specialist, explained what makes BSLBATT
Nano One Achieves Milestone 2 of the Scaling Advanced Battery Materials Project with Support from Sustainable Development Technology Canada and
Nano One® Materials Corp., a clean technology company with patented processes for the low-cost, low-environmental footprint production of high-performance cathode
100% recyclable wrap solution exceeds SAE G27 lithium battery packaging performance standards PACT, LLC, an innovator of packaging and crating
Choosing industrial batteries can be complicated—there are just so many options that it can be difficult to decide which factors
Battery Water Technologies has announced that Jack Elliott has been promoted to the position of Business Development Manager. As a
On this episode, I was joined by a previous guest, Harold Vanasse of Enersys®. Harold is the Senior Director
East Penn is proud to announce that the company ranks as one of America’s Best Employers for Women 2021 by
OneCharge Inc., a provider of lithium batteries for the material handling industry, announced that it has appointed David Suarez as
Flux Power Holdings, Inc., a developer of advanced lithium-ion industrial batteries for commercial and industrial equipment, announced on July 30th
Ken Johnson adds manufacturing and supply chain expertise to global operations Green Cubes Technology (Green Cubes), the provider in producing
VARTA empowers technologies of the future: VARTA supplies energy in the form of primary lithium button cells to the Norwegian
Flux Power Holdings, Inc., a developer of advanced lithium-ion industrial batteries for commercial and industrial equipment, has announced that on
Green Cubes Technology (Green Cubes), a provider in producing Lithium-ion (Li-ion) power systems that facilitate the transition from lead-acid batteries
The recent advances in lithium industrial batteries and their use in manufacturing are remarkable. So much so, that it may
SolaHD SDN-D Power Supplies Generate Significantly Less Heat in Cabinets SolaHD, an Emerson brand and one of the world’s most
EnerSys®, a global provider in stored energy solutions for industrial applications, is transforming material handling operations with the addition of
Yale Materials Handling Corporation announces the launch of its new ERC050-060VGL series, a 5,000 to 6,000-pound capacity cushion tire lift
Lithium-ion battery technology pairs well with the wine industry, like a good Cabernet with a lamb chop. The wine business