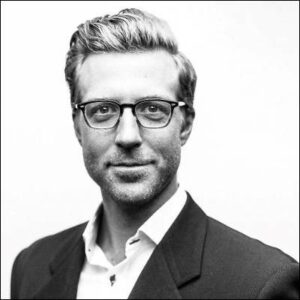
Ampure appoints D.J. Gregory to newly created President of Industrial PosiCharge position
Gregory to oversee the Material Handling and Ground Service Equipment business units Ampure, an innovative provider of electric vehicle (EV)
Gregory to oversee the Material Handling and Ground Service Equipment business units Ampure, an innovative provider of electric vehicle (EV)
Material-handling electric vehicles use two types of batteries: lithium-ion (Li-ion) and lead-acid batteries. The main deciding factors when choosing the right battery
Forklift battery chargers are essential for ensuring the top performance and longevity of lithium batteries. Understanding how to use and
Video from Power Tool Institute details correct procedures The Power Tool Institute, an organization for power tool safety resources, information, and
Forklifts are essential workplace vehicles that offer immense utility and productivity boosts. However, they are also associated with significant safety
China Huizhou, BSL Battery-Industrial a provider in designing and manufacturing smart lithium-ion batteries (up to 50% more efficient than its
EV Industry veteran brings extensive experience in accelerating growth AMPURE, formerly Webasto Charging Systems, appoints John Thomas as Global Head
Innovation, quality, and safety have always been fundamental factors in the design and manufacture of BSL Battery – Industrial’s Lithium Iron Phosphate
Reliable paralleling switchgear ideal for emergency backup power Russelectric, A Siemens Business, offers its robust and reliable Emergency Power System
PosiCharge, the industrial charging division of Webasto Charging Systems Inc., a subsidiary of Webasto Group, its divestment of the charging business to
Delta has recently obtained Federal Communications Commission (FCC) approval and METus* certification. The M∞Vair 30 kW model boasts 95% contactless
EnerSys ® has outlined its commitment to providing customers with solutions to achieve true optimization during an onsite press conference
The M-Series Li600 available in Class I, II and III is the latest addition to Stryten Energy’s portfolio of motive
As electrification of material handling equipment continues to gain traction, Green Cubes offers modular battery technology to ensure safety and
Slim, rugged portable pack is UL-certified to power multiple devices at different voltages with built-in DC adapters. Green Cubes Technology (Green
Forklift International.com and Material Handling Wholesaler will have a booth at MODEX 2024 on March 11 –
EnerSys® will premier its latest NexSys® charging innovations at MODEX 2024 – the NexSys® AIR wireless charger and the NexSys®+ Outdoor charger. Engineered
Veteran Financial Leader to Fortune 500 Technology Companies to Lead Next Phase of Company Growth Flux Power Holdings, Inc., a
Battery Builders is excited to announce several new additions to our Field Sales team: Trey Hitson, Director of Sales Trey
Company to Showcase its New G2 Product Line of Heavy-Duty Battery Packs and SkyBMS® Telematics Solution Flux Power Holdings, Inc.,