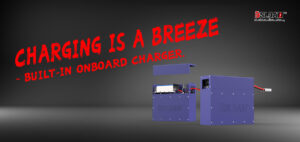
BSL touts lithium-ion technology
BSL New Energy Technology Co., LTD. is a fast-paced, high-growth (200% YoY) high-tech company leading the adoption of lithium-ion technology solutions. Mr.
BSL New Energy Technology Co., LTD. is a fast-paced, high-growth (200% YoY) high-tech company leading the adoption of lithium-ion technology solutions. Mr.
In the latest episode of The New Warehouse Podcast, Michael Marcum, the General Manager at Bastian Solutions, and Matthieu Ebert,
EnerSys is honoring breast cancer awareness month with a special battery donation to ProLift Toyota Material Handling for its rental
Milestone marks a decade of manufacturing safe and reliable Li-ion technology for motive equipment with its Lithium SAFEFlex Battery solutions
Motive power batteries for forklifts and other material handling equipment typically look very similar, with no differentiation of design or
Ground support equipment (GSE) is traditionally powered by internal combustion engines (ICs), just like the aircraft they support. The burning of
Innovative software platform enhances fleet performance, operator safety, and sustainability UgoWork™, a Canadian lithium-ion energy solutions provider specialized in the
Intralogistics Group’s batteries now being recycled by strategic partner Li-Cycle in Magdeburg, Germany Sustainable process recovers up to 95 percent of
The electric forklift rental business model benefits greatly from switching the equipment to lithium batteries from widespread lead-acid batteries. Lithium
Commencing shipment of samples for partners to validate tonne scale LFP in Q4 Repeated One-Pot LFP trials demonstrates technology at
The New Warehouse Podcast is excited to bring insights from Kevin Kushman, CEO at Electrada. Kevin is a leading authority
A BSLBATT® Filipino client consolidated its small warehouse in Manila into two large distribution centers and replaced the fleet of
UgoWork®, a Canadian energy solutions provider specialized in the material handling industry, has announced that it has signed a pan-Canadian
Back in February’s edition of Wholesaler, I wrote about ‘forklift battery management’ to your dealership’s services offering as a one-stop
BSL Battery just announced that it has joined the Compatibility Program of SPE Industrial Electronics Charger Manufacturer in Crevalcore, Bologna, Italy,
BSL Battery – Industrial, a world supplier of lithium-ion batteries for the material handling industry, just announced a partnership with
Green Cubes Technology to provide Lithium SAFEFlex batteries to power Doosan electric forklifts as sole Lithium-ion battery supplier of choice
BSLBATT Battery has announced that it has joined Fronius Perfect Charging’s new partner program “Charger Compatibility”. The program provides BSLBATT
EnerSys®, the global provider of stored energy solutions for industrial applications, has expanded its line of virtually maintenance-free, high-performance NexSys®
Hyster Distributor – Yale Distributor Panama Grupo El Iman is a supplier of a full line of industry award-winning lift